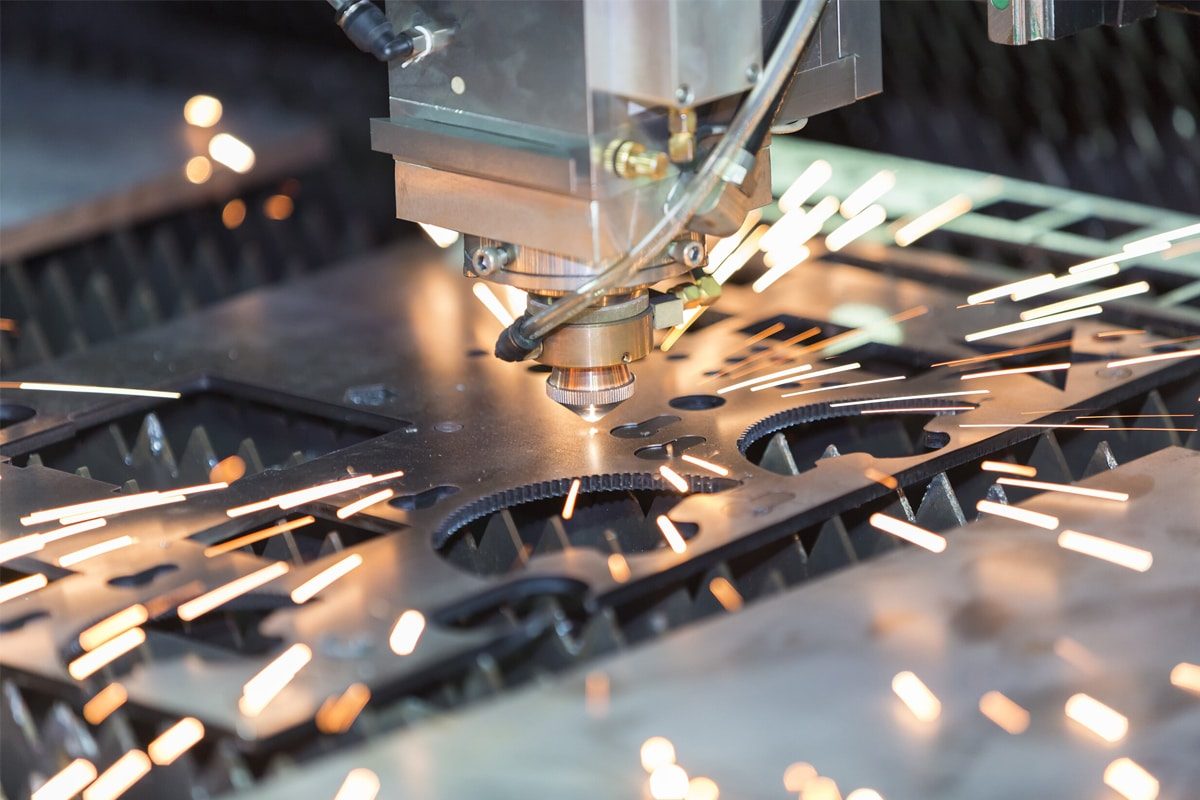
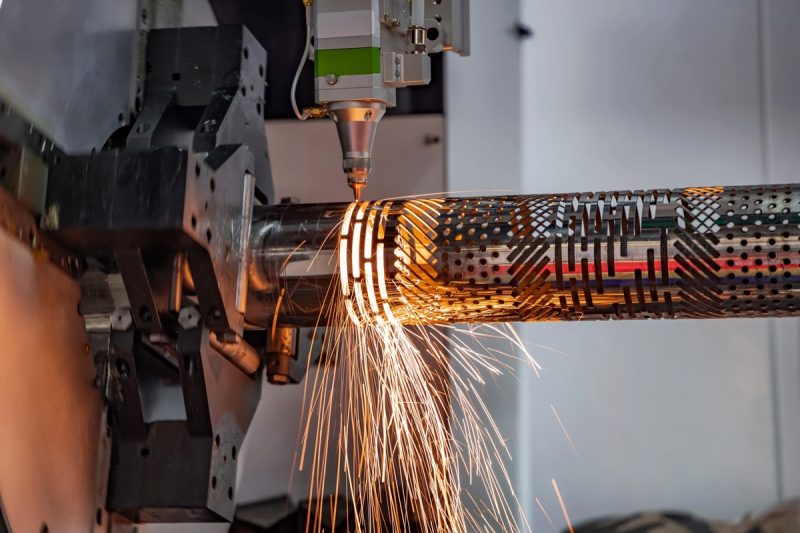
Understanding Laser Power
What is Laser Power?
How Laser Power Affects the Cutting Process
Laser power plays a key role in the laser-cutting process, affecting several key aspects:
- Cutting Speed: Higher laser power allows for faster cutting speeds. This is because more energy is available to melt, vaporize, or burn through the material, allowing for faster cutting. For industrial applications where high productivity is critical, selecting a higher laser power can significantly reduce production time.
- Edge Quality: The quality of the cut edge is affected by the laser power. The optimal power setting produces a smooth, clean edge while minimizing burrs and thermal distortion. However, too high a power can result in edge burns, over-melting, and a wider heat-affected zone (HAZ), which can compromise edge quality.
- Material Penetration: Laser power determines the ability to cut different material thicknesses. Thicker materials require higher powers to ensure that the laser beam can penetrate the full depth of the material. For thin materials, lower power settings are often sufficient and can prevent unnecessary heat buildup and material damage.
- Material Removal Rate: The material removal rate is affected by laser power. Higher powers result in higher material removal rates, which is beneficial for thicker materials but can result in over-melting or burning of thinner materials.
- Precision and Detail: For intricate designs and fine details, lower laser powers are often a better choice. This allows for precise control of the laser beam, reduces the risk of over-cutting, and ensures that detailed features are accurately rendered.
- Thermal Effects: Excessive laser power can result in noticeable thermal effects, such as warping or discoloration, especially in heat-sensitive materials. Proper power calibration can minimize these adverse effects.
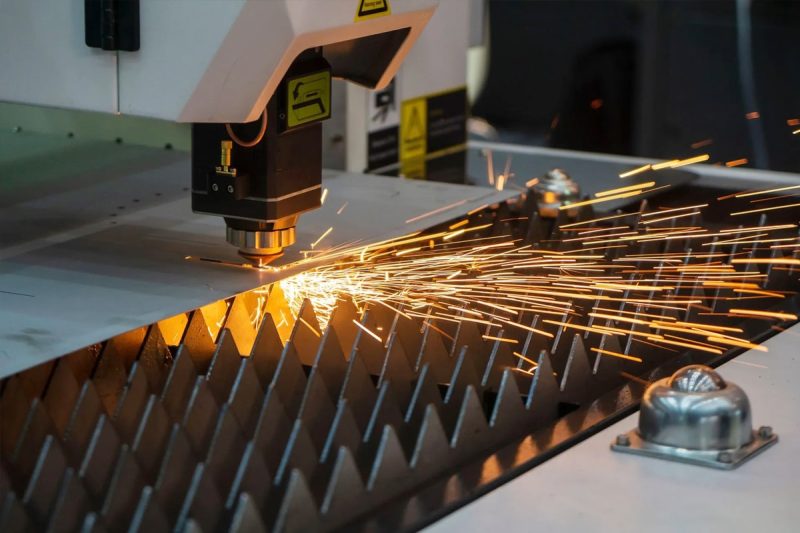
Types of Laser Cutting Machines
Fiber Laser Cutting Machine
Main Features
- Wavelength: Typically around 1.06 microns, making it ideal for cutting metals.
- Efficiency: High electro-optical efficiency, typically over 30%, resulting in lower operating costs and energy consumption.
- Beam Quality: Superior beam quality enables finer, more precise cutting, especially on thin materials.
- Maintenance: Since there are no moving parts in the laser source, maintenance requirements are low.
Applications
- Material: Ideal for cutting metals, including steel, stainless steel, aluminum, brass, and copper.
- Thickness: Suitable for high-precision cutting of thin to medium-thick materials.
- Industries: Widely used in aerospace, automotive, electronics, and metal manufacturing industries.
Advantages
- Speed: Faster cutting speeds compared to CO₂ and Nd lasers, especially when cutting thin materials.
- Precision: High precision and high edge quality due to the thin beam.
- High Electro-Optical Efficiency: Higher efficiency, resulting in lower energy consumption and operating costs.
- Cost-Effectiveness: Long service life and low maintenance requirements.
Disadvantages
- Initial Cost: Higher initial investment compared to CO2 laser generators.
- Material Limitations: Less effective on non-metallic materials such as wood and plastic.
CO2 Laser Cutting Machine
Key Features
- Wavelength: Approximately 10.6 microns, ideal for cutting a wide range of materials, including non-metals.
- Efficiency: Electrical efficiency is lower compared to fiber lasers.
- Beam Quality: Good beam quality, suitable for a wide range of cutting and engraving tasks.
- Maintenance: Requires regular maintenance, including gas replenishment and mirror calibration.
Applications
- Materials: Capable of cutting a wide range of materials, including metals, wood, acrylic, glass, textiles, and plastics.
- Thickness: Effective for cutting thin and thick materials.
- Industries: Used in signage, packaging, woodworking, automotive, and textile industries.
Advantages
- Versatility: Can cut a wide range of materials, in addition to metals.
- Cost: Lower initial cost compared to fiber lasers.
- Availability: Mature technology, available in a variety of models and configurations.
Disadvantages
- Speed: Slower for cutting metals compared to fiber lasers.
- Maintenance: Maintenance requirements are high, including gas replenishment and regular mirror adjustments.
- Energy Consumption: Energy consumption is high due to low electrical efficiency.
Nd Laser Cutting Machine
Main Features
- Wavelength: Approximately 1.064 microns, similar to fiber lasers, suitable for metal cutting.
- Operation Modes: Can operate in both continuous wave (CW) and pulsed modes, providing flexibility for cutting and engraving applications.
- Beam Quality: High beam quality for precision cutting and drilling.
- Maintenance: Typically low maintenance, rugged design, and long life.
Applications
- Material: Suitable for cutting metals, ceramics, and some plastics.
- Thickness: Suitable for precision cutting and drilling of thin materials.
- Industries: Commonly used in electronics, medical device manufacturing, jewelry, and aerospace industries.
Advantages
- Accuracy: High accuracy, capable of producing fine details.
- Pulsed Operation: Capable of pulsed operation, ideal for drilling and fine engraving.
- Material Compatibility: Effective for a wide range of materials, including hard and brittle materials.
Disadvantages
- Speed: Slower cutting speeds compared to fiber laser generators.
- Cost: Higher initial cost and lower efficiency compared to CO2 lasers.
- Cooling Requirements: Requires an efficient cooling system to manage heat dissipation.
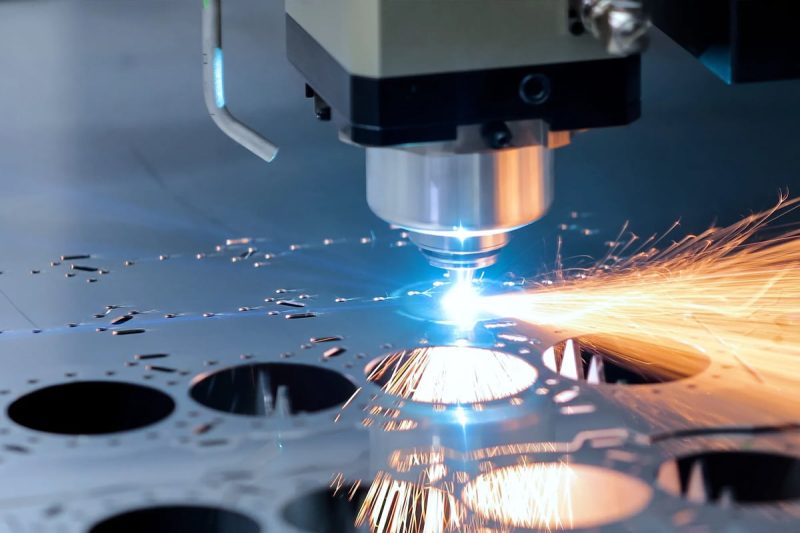
Factors Affecting Laser Power
Material Type
Metals
- Steel: Due to its high melting point, it generally requires higher laser powers. Mild steel, stainless steel, and other steel alloys may have different power requirements.
- Aluminum: Due to its high reflectivity and thermal conductivity, it requires high laser powers.
- Copper and Brass: These materials are highly reflective and conductive and require higher power levels or specialized laser generators, such as fiber laser generators, to ensure efficient cutting.
Non-Metals
- Plastics and Acrylics: Generally require lower powers than metals. The power required can vary depending on the type and thickness of the plastic.
- Wood: Moderate power is required, but the power required can vary greatly depending on the type of wood and its moisture content.
- Fabric and Paper: Since these materials are thin and flammable, they require lower powers when cutting.
Material Thickness
The thickness of the material is directly proportional to the laser power required. Thicker materials require more power to cut because the laser must penetrate deeper and remove more material.
- Thin Materials (≤ 1 mm): Lower power levels are sufficient. Lower powers allow for high precision and fine detail.
- Medium Thickness (1-5 mm): Medium power levels are required. The exact power required depends on the material type and the desired cutting speed.
- Thick Materials (> 5 mm): High power is required to ensure complete penetration and efficient cutting. For extremely thick materials, a multi-pass approach or a specialized high-power laser generator may be required.
Cutting Speed Requirements
The desired cutting speed significantly affects the choice of laser power. The faster the cutting speed, the higher the power is usually required to maintain the cut quality and prevent incomplete cuts or excessive burrs.
- High-Speed Cutting: For applications where speed is critical, such as mass production, higher laser powers are required. Higher power ensures that the laser can cut the material quickly without sacrificing quality.
- Medium-Speed Cutting: In scenarios where cutting speed is not as important, medium power settings can be used. This is often the case for small-batch production or custom manufacturing.
- Slow-Speed Cutting: For very detailed or complex cuts, lower cutting speeds and lower power settings can be used. This allows for greater precision and control.
Required Cut Quality
The required cut quality will also affect the laser power setting. Different applications have different standards for edge quality, accuracy, and finish.
- High-Quality Cutting: For applications that require smooth edges, high quality, and minimal post-processing, higher laser powers, and slower cutting speeds are usually required. This ensures a clean cut with minimal dross and burrs.
- Standard Quality Cutting: For applications where minor imperfections are acceptable, medium power levels are sufficient. This is often the case in heavy industrial applications where speed takes precedence over aesthetic quality.
- Rough Cutting: When speed is the primary concern rather than edge quality, higher powers, and faster cutting speeds can be employed. This approach is often used in the preliminary cutting stages or for materials that will undergo further processing.
Complexity of Design
The complexity of the design or pattern to be cut also affects the laser power required. Intricate and detailed designs generally require more precise control of the laser, which affects the power setting.
- Complex Designs: Complex patterns with sharp angles, small holes, and detailed features require precise control of the laser power. Lower power settings combined with slower speeds help achieve high precision and avoid overheating or deforming the material.
- Medium Designs: Designs of moderate complexity can be cut with balanced power settings. These designs may include curves and varying line thicknesses but do not require extreme precision.
- Simple Designs: Straightforward cuts with minimal detail, such as simple shapes and straight lines, can be performed with higher power settings and faster speeds.
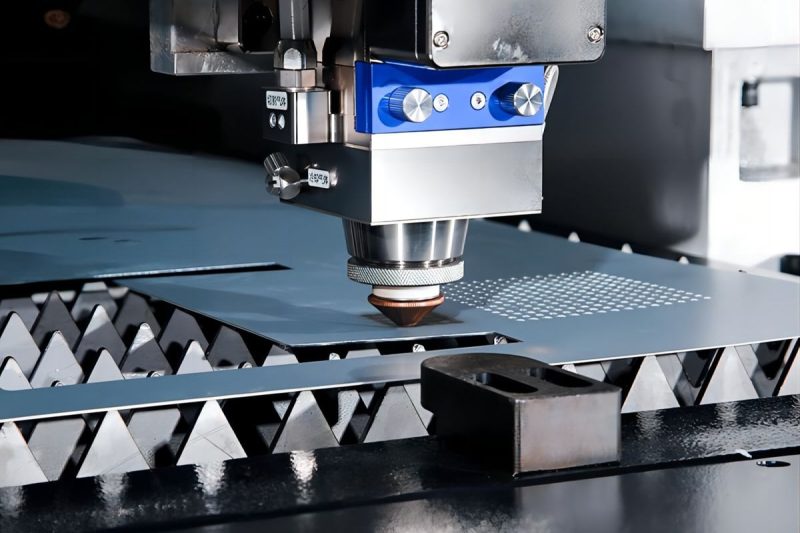
Laser Power Ranges for Different Materials
Metals
Mild Steel
- Thin Plate (up to 3 mm thick): 1,000-2,000 Watts
- Medium Thickness (3-6 mm): 2,000-4,000 Watts
- Thick Plate (6-12 mm): 4,000-8,000 Watts
- Extra Thick Plate (over 12 mm thick): 8,000-12,000 Watts
Stainless Steel
- Thin Plate (up to 2 mm thick): 1,000-2,000 Watts
- Medium Thickness (2-5 mm): 2,000-4,000 Watts
- Thick Plate (5-10 mm): 4,000-6,000 Watts
- Extra Thick Plate (over 10 mm thick): 6,000-12,000 Watts
Aluminum
- Thin Plate (up to 2 mm thick): 1,000-2,000 Watts
- Medium Thickness (2-6mm): 2,000-4,000 Watts
- Thick Plate (6-10 mm): 4,000-8,000 Watts
- Extra Thick Plate (over 10 mm): 8,000-12,000 Watts
Copper and Brass
- Thin Plate (up to 1 mm thick): 1,000-2,000 Watts
- Medium Thick (1-3 mm): 2,000-4,000 Watts
- Thick Plate (3-6 mm): 4,000-6,000 Watts
- Extra Thick Plate (over 6 mm): 6,000-8,000 Watts
Non-Metals
Plastics (e.g. polycarbonate, polypropylene, PVC)
- Thin Sheets (up to 2 mm thick): 25-40 Watts
- Medium Thickness (2-5 mm): 40-100 Watts
- Thick Sheets (5-10 mm): 100-150 Watts
- Extra Thick Sheets (over 10 mm thick): 200-600 Watts
Acrylic
- Thin Sheets (up to 2 mm thick): 60-100 Watts
- Medium Thickness (2-5 mm): 100-200 Watts
- Thick Sheets (5-10 mm): 200-400 Watts
- Extra Thick Sheets (over 10 mm thick): 400-600Watts
Wood (e.g. plywood, MDF, hardwood)
- Thin Sheets (up to 3 mm thick): 100-150 Watts
- Medium Thickness (3-6 mm): 150-300 Watts
- Thick Sheets (6-12 12 mm): 300-500Watts
- Extra Thick Sheets (over 12 mm): 500-600 Watts
Textiles and Leather
- Thin and Medium Thickness: 60-150 Watts
- Thick Materials: 150-300 Watts
Composites
Carbon Fiber Reinforced Polymer (CFRP)
- Thin Sheet (up to 1 mm thick): 100-200 Watts
- Medium Thickness (1-3 mm): 200-400 Watts
- Thick Sheet (3-6 mm): 400-600 Watts
Glass Fiber Reinforced Polymer (GFRP)
- Thin Sheet (up to 1 mm thick): 100-200 Watts
- Medium Thickness (1-3 mm): 200-400 Watts
- Thick Sheet (3-6 mm): 400-600 Watts
Other Composites (e.g., Kevlar, Boron Composites)
- Thin Sheet (up to 1 mm thick): 100-200 Watts
- Medium Thickness (1-3 mm): 200-400 Watts
- Thick Sheet (3-6 mm): 400-600 Watts
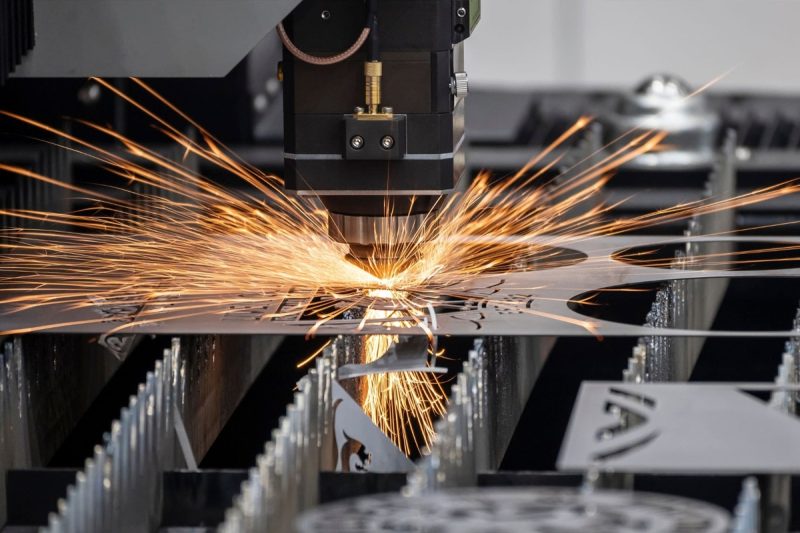
Methods for Determining Laser Power
Material Compatibility Charts
Material compatibility charts are a valuable resource that provides general guidance on the laser power settings required for different materials.
- Purpose: These charts help users quickly identify starting power settings for various materials based on material type and thickness.
- Structure: Compatibility charts typically list the materials in one column, followed by the recommended power settings, cutting speeds, and other relevant parameters.
- Sources: These charts can be found in user manuals, laser cutting software, and manufacturer websites.
Advantages
- Quick Reference: Provides immediate guidance without the need for extensive calculations or experimentation.
- Standardized Settings: Provides standardized power settings based on industry best practices.
Disadvantages
- General Information: This may not account for specific variations in material quality or environmental conditions.
- Starting Point Only: This should serve as a baseline for further adjustments and optimizations.
Materials Testing
Material testing involves conducting actual tests to fine-tune laser power settings for specific materials and applications.
- Initial Setup: Start with the recommended settings found in a materials compatibility chart or manufacturer’s guide.
- Incremental Adjustment: Gradually adjust laser power, speed, and other parameters while monitoring results.
- Evaluation: Evaluate the cut quality, edge smoothness, and any signs of material degradation or overheating.
Advantages
- Accuracy: Allows for precise calibration based on specific material properties and cutting requirements.
- Optimization: Allows for fine-tuning for optimal cutting performance, improving efficiency and quality.
Disadvantages
- Time-Consuming: Requires time and resources to conduct multiple tests and evaluations.
- Material Waste: Involves using some material during testing.
Manufacturer Recommendations
Following the manufacturer’s recommendations is a key method for determining the appropriate laser cutting power.
- Source: Recommendations can be found in user manuals, technical support documents, and official communications from laser-cutting machine manufacturers.
- Content: These guides typically include detailed power settings, cutting speeds, and other parameters based on extensive testing and real-world applications.
Advantages
- Reliability: Manufacturer recommendations are based on comprehensive testing and are tailored to the specific capabilities of the laser-cutting machine.
- Support: Technical support is available from the manufacturer for any questions or concerns.
Disadvantages
- General recommendations: While these recommendations are reliable, they may still need to be fine-tuned based on specific use cases and material conditions.
- Dependency: Over-reliance on manufacturer recommendations can limit the exploration of optimized settings for unique applications.
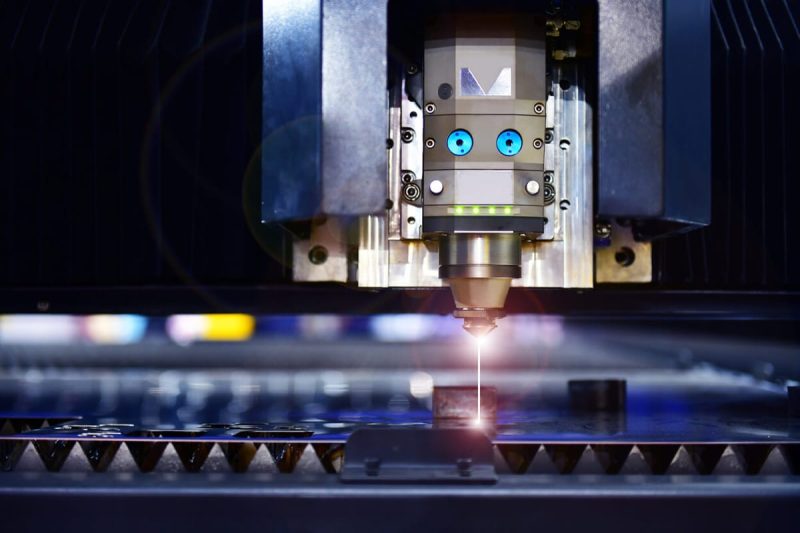
Practical Considerations for Selecting Laser-Cutting Power
Machine Specifications
Maximum and Minimum Power Output
- Range: Make sure your machine can handle the power settings required for your material. Fiber lasers typically range from 1,000 to 12,000 watts (for metals), while CO2 lasers range from 60 to 600 watts (for non-metals).
- Flexibility: Machines with a wide power range offer greater flexibility for cutting different materials and thicknesses.
Beam Quality
- Focus Size: The quality of the laser beam affects the accuracy of the cut. High beam quality and smaller focal size allow for finer, more precise cuts.
- Stability: Consistent beam quality ensures even cuts and reduces the need for frequent adjustments.
Cutting Speed and Acceleration
- Speed Capability: Higher laser power allows for faster cutting speeds, but the machine’s mechanical components must support these speeds without compromising accuracy.
- Acceleration: A machine with high acceleration capabilities can handle rapid changes in cutting direction, which helps achieve complex designs.
Control System
- Software: Advanced control software can optimize cutting paths and power settings, improving efficiency and quality.
- Integration: Ensure that the control system can be seamlessly integrated with other production equipment and software to simplify operation.
Cost and Energy Efficiency
Operating Costs
- Power Consumption: Higher laser power settings consume more electricity. Evaluate the energy requirements and operating costs associated with different power levels.
- Auxiliary Gas: The type and amount of auxiliary gas used (e.g., oxygen, nitrogen, compressed air) can affect total cost. Higher power settings may require more auxiliary gas to maintain cut quality. If you want to learn more about auxiliary gases, check out the “Effect of Auxiliary Gas Selection on Laser Cutting” article.
Initial Investment VS Long-Term Savings
- Initial Cost: A higher-powered laser cutting machine generally requires a higher initial investment. However, it can provide long-term savings by increasing cutting speeds and efficiency.
- Efficiency Gain: A more powerful laser can reduce cutting time and increase production throughput, saving labor and operating expenses.
Energy Efficiency
- Laser Efficiency: Fiber laser generators are generally more energy-efficient than CO2 laser generators. Consider the energy efficiency of the laser generator type when selecting a power setting.
- Cooling System: An efficient cooling system can reduce energy consumption and extend the life of the laser generator.
Maintenance and Downtime
Routine Maintenance
- Frequency: Higher power settings accelerate wear on machine components. Create a regular maintenance schedule to inspect and replace parts as needed.
- Parts: Critical components such as lenses, mirrors, and nozzles require frequent cleaning and replacement to maintain optimal performance.
Downtime Management
- Planned Downtime: Plan maintenance activities during planned downtime to minimize disruption to production.
- Preventive Maintenance: Implement a preventive maintenance strategy to identify and resolve potential issues before they cause machine failure.
Manufacturer Support
- Service Agreements: Consider service agreements and support packages offered by manufacturers. These can provide peace of mind and reduce the risk of extended downtime.
- Technical Assistance: Ensure access to technical support to troubleshoot and optimize machine performance.
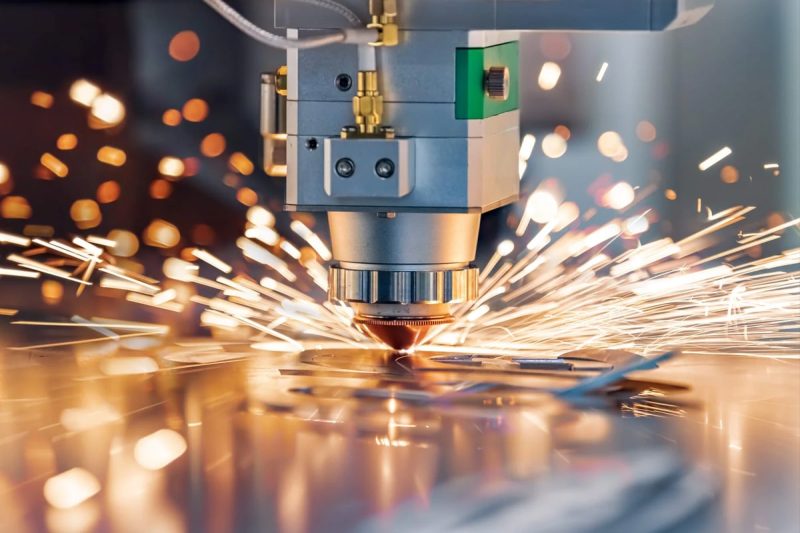
Troubleshooting Laser Power Issues
Not Cutting Deep Enough
Insufficient Power
- Cause: The laser power setting may be too low to cut the material.
- Solution: Increase the laser power gradually and make test cuts until the desired depth is reached. Make sure the power level is within the safe operating range of the machine.
Cutting Speed Too High
- Cause: The cutting speed may be too fast, not allowing enough time for the laser to fully penetrate the material.
- Solution: Reduce the cutting speed to allow more energy to focus on the material. Balance the speed and power settings to optimize the cutting depth.
Missed Focus
- Cause: The laser beam may not be properly focused on the material surface, reducing cutting efficiency.
- Solution: Adjust the focus height to ensure the laser beam is properly focused on the material. Use the machine’s focusing tool or adjust manually as needed.
Material Thickness
- Cause: The material may be thicker than expected, requiring more power or multiple passes.
- Solution: Verify the material thickness and adjust the power setting accordingly. For very thick materials, consider multiple passes or using a higher-powered laser.
Excessive Burning or Melting
Excessive Power
- Cause: The laser power setting may be too high for the material being cut.
- Solution: Gradually reduce the laser power until burning or melting is minimized. Make sure the power setting is appropriate for the material.
Slow Cutting Speed
- Cause: The cutting speed may be too slow, causing excessive heat buildup and burning.
- Solution: Increase the cutting speed to reduce heat exposure time. Find the right balance between speed and power to achieve a clean cut without burning.
Incorrect Focus
- Cause: The laser focus may be too concentrated, causing overheating in a small area.
- Solution: Adjust the focus height so that the laser energy is more evenly distributed across the cutting area. Make sure the beam is properly aligned and focused.
Material Sensitivity
- Cause: Some materials are more sensitive to heat and tend to burn or melt.
- Solution: Use materials with better heat tolerance whenever possible. Also, consider using an assist gas such as nitrogen, which can help reduce burning by displacing oxygen around the cutting area.
Inconsistent Cutting Results
Variable Power Output
- Cause: The power output of the laser generator can fluctuate, resulting in inconsistent cutting performance.
- Solution: Check the laser generator for stability issues and ensure it is operating properly. Regular maintenance and calibration can help maintain consistent power output.
Material Variations
- Cause: Variations in material properties, such as thickness or composition, can lead to inconsistent cutting.
- Solution: Use high-quality, uniform materials to ensure material consistency. Perform test cuts on different batches of material to adjust settings as needed.
Improper Machine Calibration
- Cause: The machine may not be properly calibrated, affecting cutting accuracy and consistency.
- Solution: Calibrate the laser cutting machine regularly according to the manufacturer’s guidelines. Check for mechanical issues or misalignments that may affect cutting performance.
Dirty or damaged optics
- Cause: Dirty or damaged optics can scatter the laser beam, resulting in inconsistent cutting results.
- Solution: Clean the optics regularly and inspect them for damage. Replace any damaged components to ensure optimal beam quality and consistency.
Environmental Factors
- Cause: Changes in ambient temperature, humidity, or airflow can affect the cutting process.
- Solution: Maintain a controlled environment for your laser cutting machine. Ensure consistent temperature and humidity levels to reduce the impact of environmental factors on the cutting process.
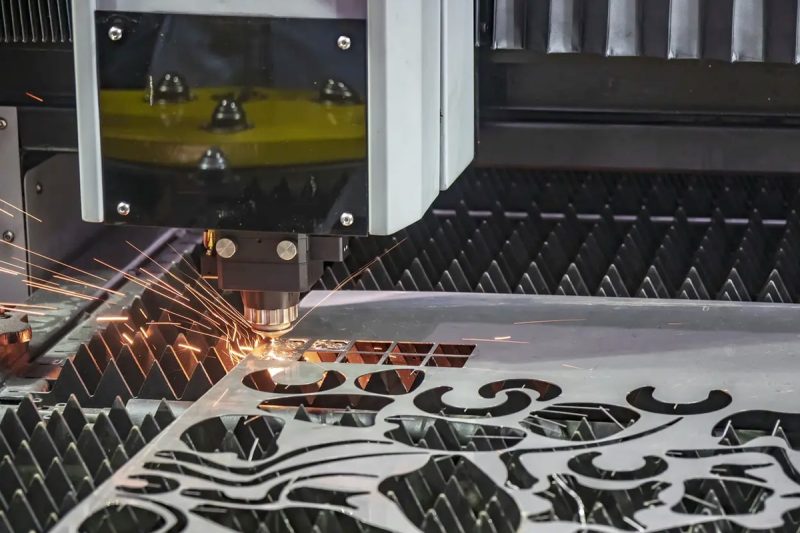
Summary
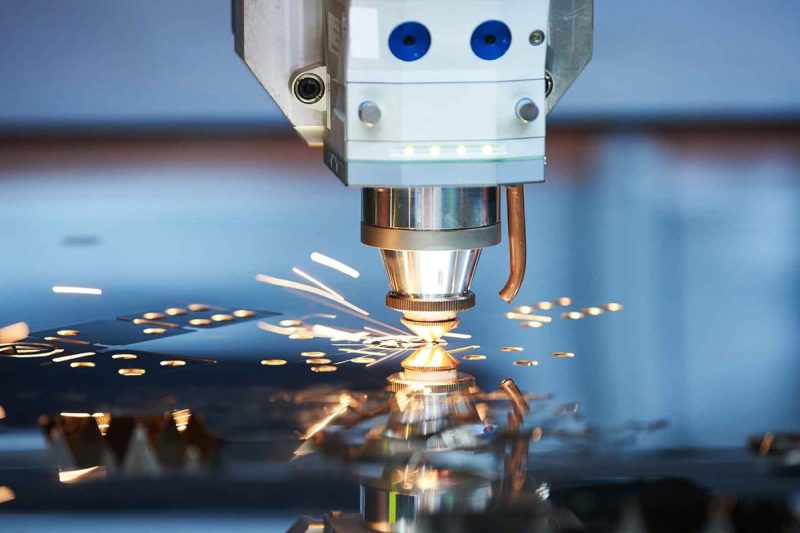
Get Laser Cutting Solutions
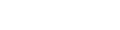
- [email protected]
- [email protected]
- +86-19963414011
- No. 3 Zone A, Lunzhen Industrial Zone,Yucheng City , Shandong Province.