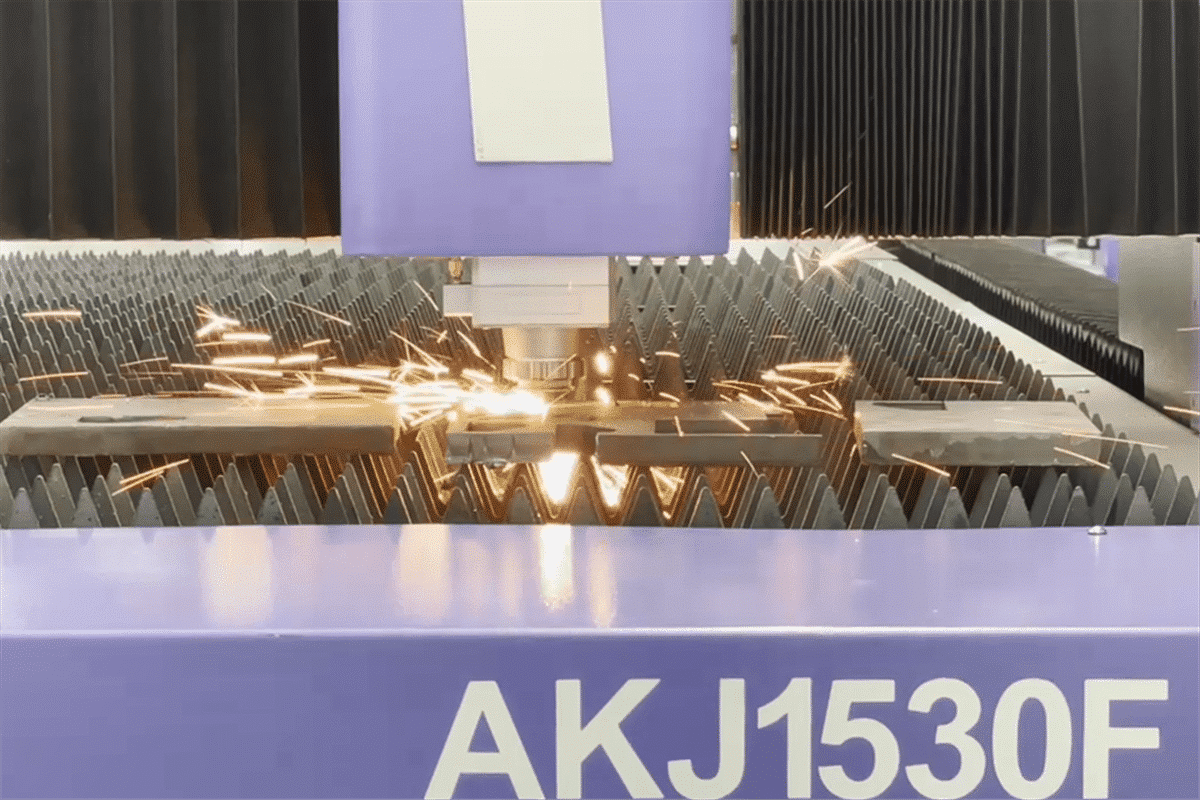
How to Improve The Quality of Laser Cutting?
Laser cutting machine is increasingly popular in the industrial field due to their high precision, good surface quality, low processing noise, and fast cutting speed. The basic principle of laser cutting is the interaction between laser and matter. This interaction involves many phenomena such as the absorption, reflection, refraction, energy conversion and transmission of the material to the laser light, as well as the state of the material and the composition of the surrounding gas. This series of processes makes the factors that affect the quality of laser cutting very complicated.
In addition to the processed materials, other factors that affect the quality of laser cutting include beam characteristics, cutting speed, laser power, nozzle height, focus position, auxiliary gas, etc. So how to improve the quality of laser cutting, this is a problem that needs to be considered comprehensively.
Table of Contents
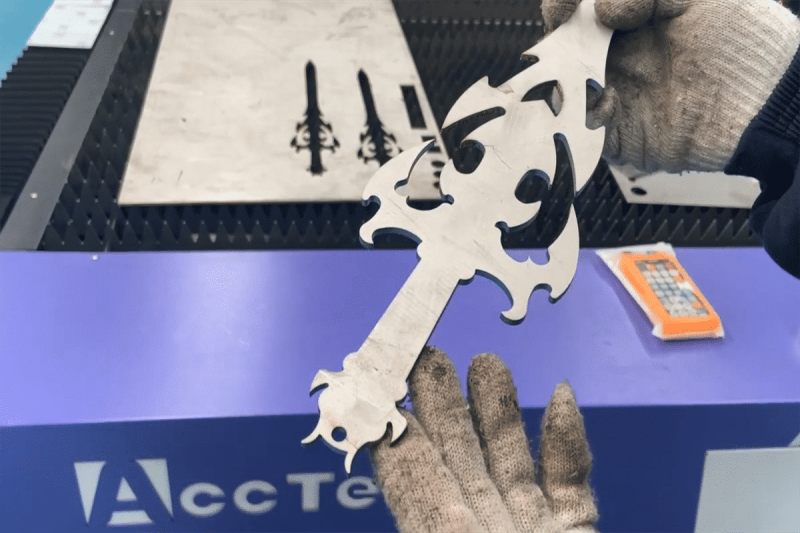
The right sheet material can improve the quality of laser cutting
Different materials have different effects on them. Whether any material is suitable for laser cutting depends on the material’s interaction with the laser wavelength and energy. Different materials produce different cutting capabilities, cutting speeds and cutting qualities. Therefore, in order to improve the quality of laser cutting, the following factors need to be paid attention to in the selection of plates.
Sheet Thickness
The same laser cutting machine can achieve different cutting effects when cutting materials of different thicknesses. Each machine has a max cut thickness, normal cut thickness and hi-speed cut thickness. Only by ensuring that the thickness of the plate is within the reasonable range that the laser cutting machine can cut can a higher cutting quality be obtained. Conversely, when the material exceeds the applicable cutting thickness, the cutting quality will deteriorate.
Sheet Type
When the same laser cutting machine cuts different materials with the same thickness, the cutting effect obtained is different. For example, when the same 2000W laser cutting machine cuts 10mm carbon steel, not only the cutting quality is high, but also the cutting speed is fast. However, if cutting 10mm stainless steel, problems such as burrs and slag will appear. Therefore, if you want to obtain high-quality laser-cutting effects, you must ensure that the material type matches the power of the laser-cutting machine.
Sheet Quality
Rust, coating, painting, etc. on the surface of the material usually have a negative impact on laser cutting. At this time, if you want to improve the quality of laser cutting, you need to clean the surface of the material first, and then cut the surface after cleaning. A flat and smooth material surface will contribute to better cut quality.
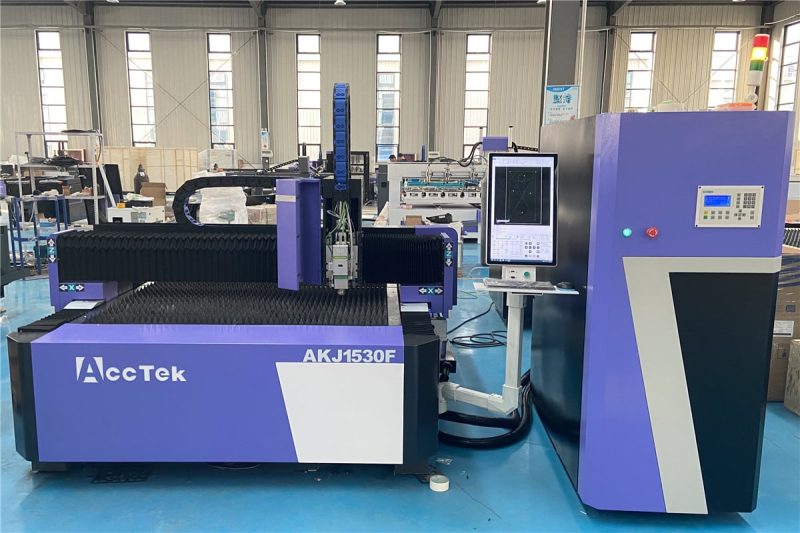
High quality laser cutting machine can improve laser cutting quality
The laser cutting machine is used as a tool for cutting plates, and its quality will directly affect the cutting quality of the workpiece. Machines assembled with high-end components not only have higher cutting quality, but also have faster cutting speed and longer service life. If users want to improve the quality of laser cutting, they need to choose a high-quality machine and equip it with parts that match the cutting material.
Laser Generator
The laser generator is the “heart” of the laser cutting machine, and the quality of the laser generator will affect the final laser cutting quality to a certain extent. There are many trustworthy laser generator brands on the market, such as IPG, Raycus, Max, JPT, etc. When choosing a laser cutting machine, you must choose a laser generator with stable performance and long service life in order to better control the quality of laser cutting.
Laser Power
The laser power represents the cutting ability of the laser cutting machine, and the higher the laser power usually means the stronger the cutting ability of the machine. Materials of the same thickness but different types may require different laser powers to cut effectively. Even for the same metal material, different thicknesses require different laser powers. For example, a 2000W laser cutting machine can cut 14mm carbon steel and 6mm stainless steel, and if cutting 14mm stainless steel, you need to choose a 6000W laser cutting machine to get better cutting quality. The correct laser power can not only help users save costs, but also ensure higher cutting quality.
Nozzle
The role of the nozzle is to control the injection area of the auxiliary gas to control the quality of laser cutting. So the structure, size and height of the nozzle will affect the final cutting quality. Different cutting thicknesses are suitable for different nozzle diameters. For example, the Φ1.2 nozzle is suitable for 1-6mm stainless steel plate. Φ2.0 nozzle is suitable for 6-10mm stainless steel plate. If the nozzle part is damaged, it will cause uneven airflow and affect the cutting quality. Therefore, it is necessary to pay attention to the quality of the nozzle, and when it is damaged, the nozzle needs to be replaced in time.
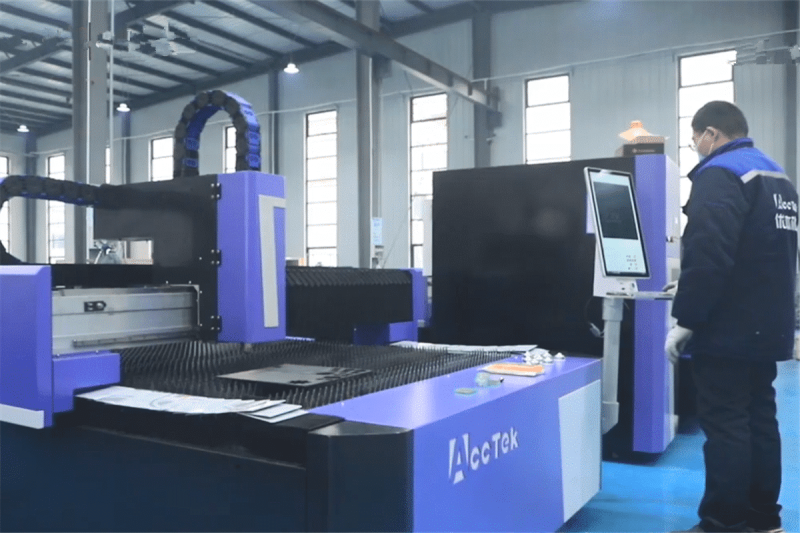
Proper machine operation improves laser cutting quality
The quality of laser cutting is affected by many factors, among which the correct operation of the machine plays an important role in improving the cutting quality. These operations include pre-cutting preparations and parameter settings during cutting. Users need to analyze according to the specific cutting situation, adjust the parameters and check the machine parts to achieve the best laser cutting quality.
Material Fixation
When placing the plate, it is necessary to check the level of the machine tool and whether the steel plate is flat. Make sure the board is not tilted on the work surface and there are no other obstructions.
Operator Training
After receiving the laser cutting machine, the user should first read the machine instruction manual carefully to understand the normal operation process of the machine. If necessary, relevant operators can be trained professionally before operating the machine. Operators learn how to properly set up, operate and maintain equipment during training courses. Through training, the problem of poor cutting quality caused by operating errors will be reduced and avoided, and the quality of laser cutting will be improved.
Cutting Speed
Cutting speed plays an important role in cutting quality, the optimal cutting speed can produce smooth cutting surface and eliminate bottom dross. If the cutting speed is too fast, the plate may not be completely cut, resulting in sparks and slag in the lower half, and even damage to the lens. If the cutting speed is too slow, it may cause excessive melting, widening of the kerf, expansion of the heat-affected zone, and even burning of the workpiece. Therefore, the quality of laser cutting can be improved by setting the best cutting speed.
Focus Position
The focused point of the laser beam has the highest energy density. The smaller the spot, the better the cutting effect. The focus position of the laser beam directly affects the quality of laser cutting, including kerf size, kerf roughness and taper. Before operating a laser cutting machine, users need to ensure that the laser beam is focused on the correct position. For carbon steel laser cutting, the focus position is on the surface of the workpiece, the thicker the workpiece, the higher the focus position. For stainless steel laser cutting, the focus position is below the surface of the workpiece, and the thicker the workpiece, the lower the focus position. In addition, a focus test can be carried out before cutting to check whether the laser focus position is shifted, and adjust according to the laser focus shift.
Optimizing Laser Parameters
- Parameter adjustment for plates with different thicknesses: When laser cutting the corners of thin steel plates, overheating of the laser will produce melted corners. At this time, the sharp corners can be modified to acceptable rounded corners, so as to maintain high-speed laser cutting and achieve better cutting quality and save cutting time. When laser cutting thicker plates, in order to obtain better cutting quality, a transition line can be drawn at the start and end of the cutting, called the lead-out line. It should be noted that the connection between the lead wire and the groove must adopt a circular arc transition. Reasonable adjustment of the gap between parts according to the thickness of the plate can prevent thermal influence, improve the quality of laser cutting, and avoid damage to parts.
- Cut width: Generally speaking, the kerf width does not affect the cutting quality. Only when a particularly precise contour is formed inside the workpiece, the cut width has an important impact, because the cut width determines the minimum inner diameter of the contour. As the thickness of the sheet increases, the cutting width also increases. Therefore, in order to ensure the same high precision, no matter how large the incision width is, the workpiece should be constant in the processing area of the laser cutting machine.
- Laser power: If the output power of the laser is insufficient, there will be quality problems with cutting burrs. At this time, you should check whether the laser generator is working normally. If it is normal, observe whether the output value of the laser control button is correct and need to be adjusted.
Auxiliary Gas Selection
The auxiliary gas can assist the laser beam to cut the workpiece better, and at the same time quickly blow away the slag, which also plays an important role in improving the quality of laser cutting. Both the type of gas and the level of pressure affect edge roughness and burr formation. The gases commonly used in laser cutting are oxygen, nitrogen and air, and different auxiliary gases have different effects.
- Air cutting is the lowest cost method, but the metal cutting surface may produce burrs, and as the thickness of the sheet metal increases, the burrs will be more obvious. In addition, the metal cutting surface will be blackened, and the quality of the workpiece will be poor. In order to obtain higher cutting quality under air cutting, it is necessary to choose a high-power laser cutting machine. For example, a 12000W laser cutting machine can cut carbon steel below 10mm by air and still have good cutting quality. To ensure cutting quality and avoid any damage to the laser generator when cutting with air, the compressed air must be pure and constant.
- Oxygen cutting: Oxygen is often used to cut thick carbon steel, because the chemical reaction between iron element and oxygen helps the metal absorb heat and promote its melting, which can improve the cutting ability. But cutting with oxygen increases the risk of oxidation of the material. In general, oxygen is used to assist carbon steel plate cutting, low-pressure punching, and low-pressure cutting.
- Nitrogen cutting: When nitrogen is used as the auxiliary gas of the metal laser cutting machine, the nitrogen will form a protective atmosphere around the molten metal to prevent the material from being oxidized, thereby ensuring the quality of the workpiece. Generally, nitrogen gas is used to cut stainless steel, galvanized sheet, aluminum, aluminum alloy, brass and other materials, through low-pressure perforation and high-pressure cutting. When cutting with nitrogen, the change of gas flow has a great influence on the cutting performance. In order to obtain good cutting quality, the gas flow should be sufficient and constant.
Auxiliary Gas Control
The pressure of the auxiliary gas will affect the slag blowing effect, thus affecting the final laser cutting quality. Different metal materials require different optimum gas pressures. If the air pressure is too low, the molten material cannot be blown off in time, and it will stick to the back of the cutting edge. If the gas pressure is too high, it will weaken the cutting ability of the laser beam, making the cutting seam larger and rougher. Therefore, it is necessary to set different air pressures when cutting different materials to obtain better laser cutting results.
Trial Cutting and Prototyping
Before mass production of workpieces, trial cutting of plates can effectively reduce the scrap rate of workpieces. Prototyping is carried out through the control software of the laser cutting machine, and then the prototype is tested to ensure that it meets the cut quality requirements and necessary adjustments are made. Prototyping can help users identify design flaws and functional issues before investing in mass production, saving a lot of money and resources.
Reduce Back Reflection
Excessive back reflections can heat the nozzle and cutting head to critical levels, affecting cut quality and even causing damage to the workpiece. Therefore, when performing laser cutting, it is necessary to avoid excessive back reflection by measuring the reflection and optimizing the process. When the back reflection is too high, the cutting head feed speed can be reduced.
Real-time Monitoring and Quality Control
Through the real-time monitoring system of the laser cutting machine, the laser cutting quality can be effectively paid attention to, and the parameters can be adjusted to obtain the best cutting effect.
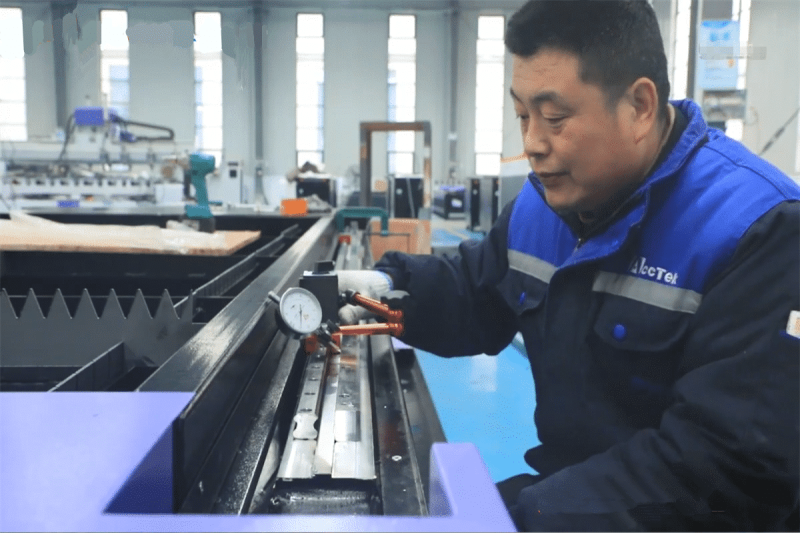
Regular machine maintenance improves laser cutting quality
As a high-precision CNC cutting equipment, the laser cutting machine can only maintain high-efficiency and high-quality cutting capabilities during long-term use only by maintaining good daily maintenance. And correct maintenance can also reduce the maintenance cost of the machine and prolong the service life of the machine.
Lens Maintenance
The maintenance of the lens of the laser cutting machine is very important, and a clean lens is essential to ensure the quality of the beam. The lens of the laser cutting machine is easily polluted by smoke and dust. It is recommended to check the lens cleanliness every day before starting work. If dust is found on the lens, it needs to be cleaned in time, and the machine can only be started after making sure the lens is clean. When using the lens, be careful not to directly touch the surface of the focusing lens, protective lens, QBH head and other optical components with your hands to prevent scratching or corroding the lens.
Nozzle Maintenance
The coaxially between the center of the nozzle exit hole and the laser beam is a key factor affecting the cutting quality. If the nozzle is deformed or melted, it will directly affect the coaxial. The shape and dimensional accuracy of the nozzle is very high, so care should be taken to maintain the nozzle to avoid deformation caused by collision.
Chiller Maintenance
The chiller is used as the cooling equipment of the laser cutting machine to ensure the normal operation of the machine at a constant temperature. Pay attention to the water temperature when the machine works for a long time, it is recommended to keep the water temperature below 35°C. In order to prevent the circulating water from freezing when using the fiber laser cutting machine in winter, antifreeze can be added. The water inside the laser cutting machine chiller needs to be replaced regularly. Because long-term use is easy to scale, which affects the cooling effect. Generally, the chiller is cleaned 1-2 times a month, and the internal circulating water is replaced. Use distilled water without impurities, such as pure water or mineral water, and be careful not to use tap water.
Rail Maintenance
The rail frame of the laser cutting machine needs to be cleaned regularly to remove dust and other debris to ensure that the equipment can maintain a good cutting effect. Racks should be wiped and lubricated frequently to ensure the lubrication is free of debris. In addition, the steel belt should be checked frequently to ensure that the steel belt is tight.
Check Machine Parameters
Check some parameters of the machine every six months, such as the straightness of the track and the verticality of the machine. If any abnormality is found, perform maintenance and adjustment in time, otherwise the cutting effect will be affected.
Check Exhaust System
A good laser exhaust system will help reduce fumes and dust and create a safe working environment. Having a system like this can improve laser cut quality while reducing fume residue on the workpiece and the need for cleaning inside the laser system. Therefore, you should check that exhaust system for any blockages. Also, you should check that the ventilation fans are functioning properly.
Summarize
The quality of laser cutting is affected by many factors. First of all, improper setting of parameters will affect the cutting effect, such as laser power, cutting speed, air pressure, etc. Also, sometimes problems can occur even when the parameters are set correctly. This is usually because the gas is not pure enough, or the nozzles and lenses are contaminated or damaged. Therefore, users need to check whether the nozzle and laser head are working properly before cutting, and then set appropriate parameters. The user needs to analyze the cause according to the specific laser cutting effect, adjust the parameters and check the machine parts to achieve the best laser cutting quality. Follow AccTek Laser to learn more about laser cutting.
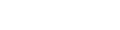
Contact information
- [email protected]
- [email protected]
- +86-19963414011
- No. 3 Zone A, Lunzhen Industrial Zone,Yucheng City , Shandong Province.
Get Laser Solutions