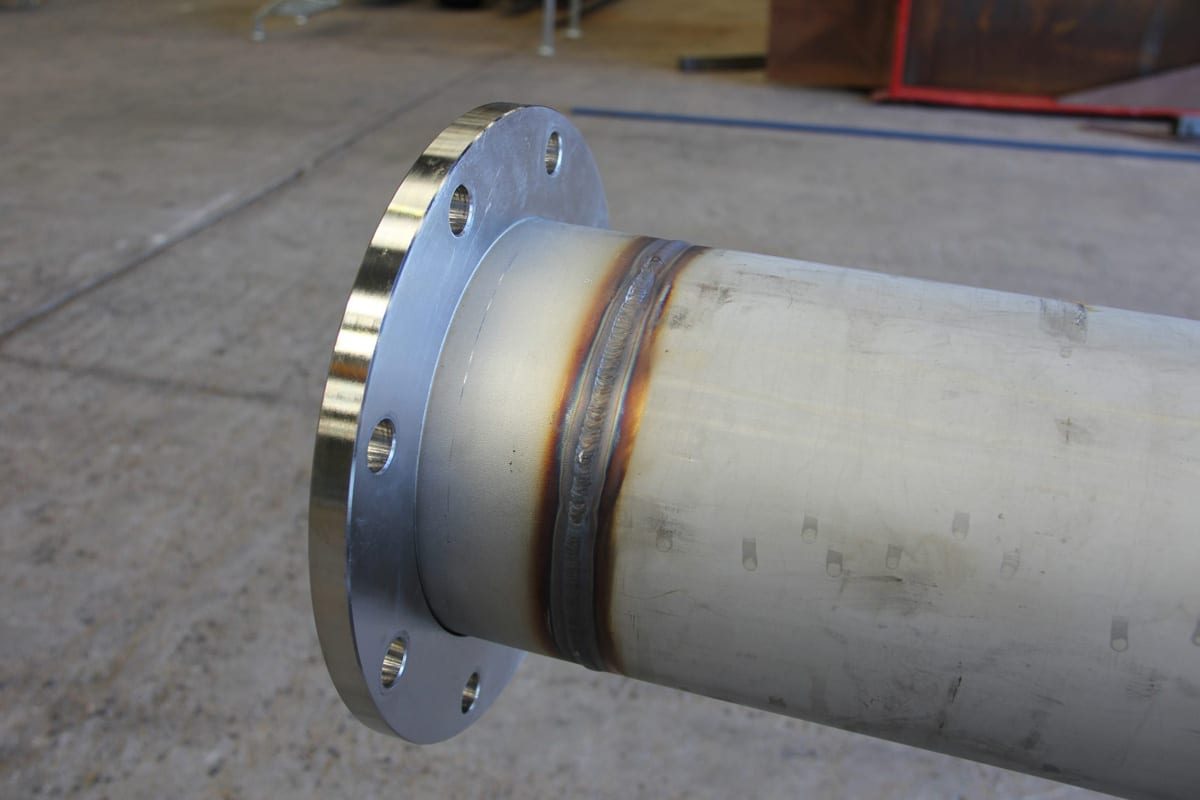
How to Improve the Strength of Laser Welded Joints
Laser welding has been widely used in automobile manufacturing, aerospace, and electronics industries as an efficient and precise welding technology due to its low heat input, deep penetration welding, and excellent automation capabilities. This technology can greatly improve production efficiency while ensuring welding quality, and reduce material deformation and processing steps. Therefore, laser welding has become an indispensable and important means in modern manufacturing.
However, the strength of welded joints is directly related to the performance and reliability of products, especially in applications subject to high-stress or complex working environments. How to optimize materials, processes, and designs to further improve the strength of welded joints is a key issue in technology research and development and industrial applications. This article will start with the main factors that affect weld strength, analyze in detail the advanced technologies for improving strength, explore the importance of post-weld treatment, and provide solutions to common challenges.
Table of Contents
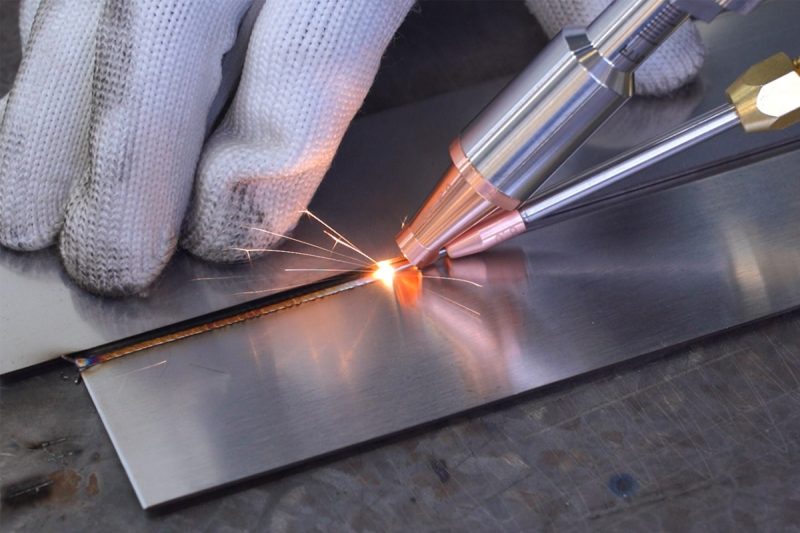
Learn About Laser Welding
Laser welding uses a high-energy laser beam as a heat source, which can be focused into a very small spot to achieve low heat input and deep penetration welding effects. The unique advantages of this technology are its accuracy and flexibility, making it particularly suitable for complex geometric structures, high-precision requirements, and difficult-to-access welding areas. Compared with traditional welding methods, laser welding can not only significantly reduce thermal deformation and residual stress, but also improve processing speed and production efficiency.
In addition, laser welding machine can be applied to the connection of a variety of materials, including various metals and alloy materials, and plays a vital role, especially in the context of the increasing demand for lightweight and high-strength components in the manufacturing industry. However, while achieving efficient welding, the strength of the welded joint remains a key issue affecting product performance and reliability. This requires continuous improvement of welding quality by optimizing materials, processes, and designs to meet the needs of high-standard industrial applications.
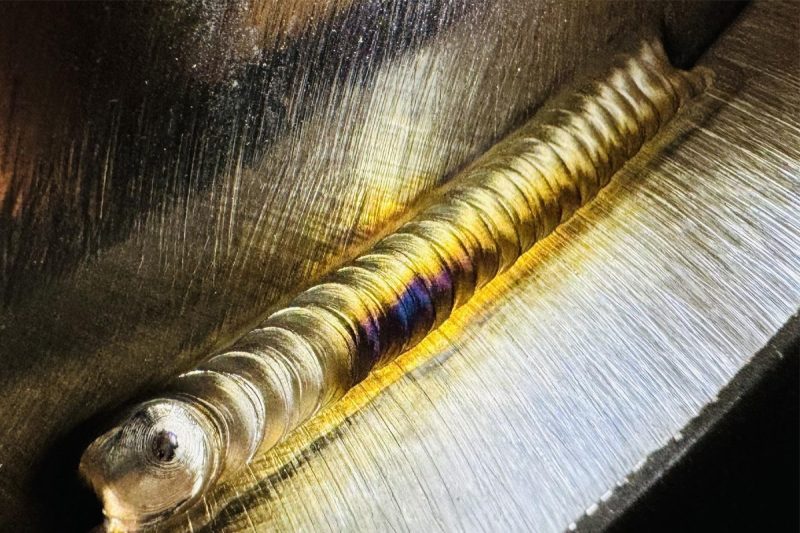
Factors Affecting Welding Strength
The strength of laser-welded joints is affected by a combination of factors, including material properties, laser parameters, joint design, and welding environment. To achieve high-quality welded joints, it is necessary to have a deep understanding of the specific role of these factors and their mutual influence, to optimize each link in practical applications. The following will analyze these factors in detail.
Material Properties
Material properties are an important basis for determining welding results, which are mainly manifested in base material composition, material thickness, and surface condition.
- Substrate composition: Different materials have different absorption rates for lasers. For example, highly reflective metals (such as aluminum and copper) have low absorption rates for laser energy, which can easily lead to insufficient penetration. It is necessary to improve the welding effect by adjusting laser parameters or coating the surface with absorbing materials.
- Material thickness: Material thickness directly affects the energy distribution of the laser. Too thick materials may cause insufficient laser penetration, resulting in incomplete penetration welds; while too thin materials are prone to burn through due to excessive laser energy, requiring careful adjustment in parameter settings.
- Surface condition: The cleanliness, oxide film, and roughness of the material surface will affect the transmission and absorption of the laser. Surface contamination or oxidation may lead to uneven molten pool formation and reduce weld strength. Therefore, pre-welding cleaning and proper surface treatment are essential.
Laser Parameters
Laser parameters directly determine the heat input and molten pool formation during welding.
- Laser power: Too low power may lead to insufficient penetration and weakened weld strength, while too high power may easily cause material burn-through or form an excessively large molten pool, thereby weakening the strength of the weld joint. Therefore, it is necessary to select the appropriate power level according to the material properties and thickness.
- Welding speed: Too fast welding speed may lead to insufficient molten pool formation, and pores or cracks may appear in the weld; while too slow speed may cause excessive heat input, causing overheating or even deformation of the material.
- Focus position: Accurate positioning of the laser focus helps to maximize the effective use of energy and ensure the depth and uniformity of the molten pool. Focus deviation will lead to reduced welding efficiency and may cause quality defects.
- Pulse parameters: For pulsed laser welding, the setting of pulse width and frequency directly affects the formation and solidification process of the molten pool. Optimizing pulse parameters can reduce the generation of cracks and pores and improve welding strength.
Connector Design
The joint design not only affects the ease of welding but is also directly related to the mechanical properties and reliability of the weld.
- Joint configuration: Different types of joints (such as butt joints, lap joints) are suitable for different structural requirements and mechanical performance requirements. For example, butt joints are suitable for high-strength welding, while lap joints are better suited for thin plate welding.
- Assembly and Alignment: Poor joint assembly or alignment errors can cause weld pool migration or weld defects, reducing weld strength. In actual operations, the use of precision fixtures or automatic alignment systems can significantly improve assembly accuracy.
- Edge preparation: The quality of edge preparation is critical to the welding effect. Uneven or burred edges may cause cracks or inclusion defects, so precision machining equipment is required to handle the edges.
Welding Environment
The welding environment is an external factor that affects the welding quality, including the selection of shielding gas and the control of environmental conditions.
- Shielding gas: The right type and flow of shielding gas can prevent oxidation of the molten pool and improve the compactness and corrosion resistance of the welded joint. For example, argon and helium are commonly used shielding gases, and too much or too little flow will affect the protection effect.
- Environmental conditions: An environment with high humidity, too much dust, or a sharp temperature difference may have an adverse effect on the welding process and even cause the performance of the weld to deteriorate. Therefore, maintaining good environmental control in the welding area is an important measure to ensure welding quality.
The factors that affect the strength of laser welded joints are complex and diverse, involving all aspects of material properties, laser parameters, joint design, and welding environment. In practical applications, these factors need to be considered comprehensively, and high-quality, high-strength welded joints can be achieved through reasonable process optimization and equipment adjustment.
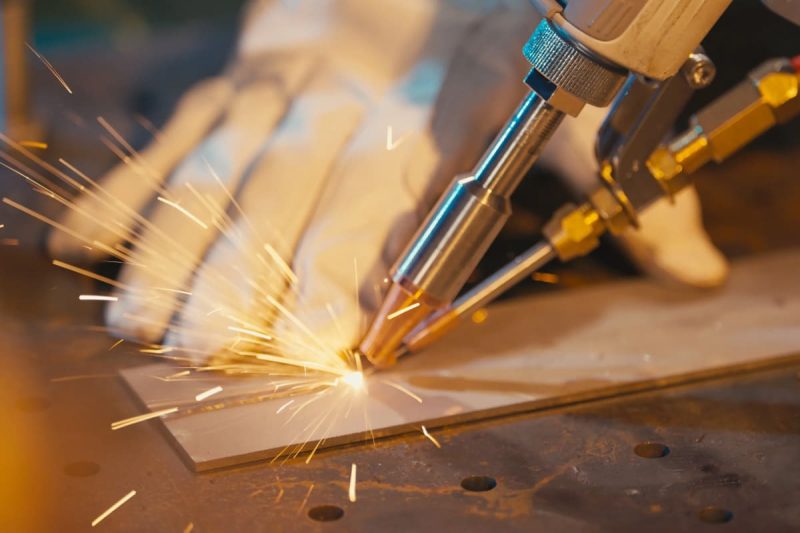
Technology to Improve Welding Strength
In order to improve the strength of laser-welded joints, it is necessary to optimize the material properties, laser technology, welding process control, and post-weld treatment. This includes not only the selection and preparation of welding materials, but also the precise adjustment of laser parameters, the design of reasonable joint shapes, and the use of advanced process control technology. By comprehensively optimizing these links, the mechanical properties and reliability of the weld can be significantly improved. Specific technical methods to improve welding strength will be elaborated below.
Material Selection and Preparation
Materials Are the Basis of Welding Performance and Play a Vital Role in the Strength of Welded Joints.
- Alloy Optimization: By selecting high-strength materials suitable for laser welding and adjusting the alloy composition, welding results can be significantly improved. For example, by adding specific elements to improve the weldability and fatigue resistance of the material, the weld can maintain stability in harsh environments.
- Surface cleaning: Thoroughly clean the material surface before welding to remove grease, oxide layers, and other contaminants, ensure efficient transmission of laser energy, and reduce weld defects. Common methods include mechanical cleaning, chemical cleaning, and laser cleaning.
- Preheating: For highly heat-sensitive materials or materials that are prone to cracking, appropriate preheating can reduce the thermal gradient during the welding process and reduce thermal stress, thereby improving the welding quality.
Laser Optimization
The adjustment of laser parameters directly determines the forming quality and mechanical properties of the weld.
- Power density control: Precisely adjust the laser power density to ensure uniform distribution of the molten pool, thereby improving the density and strength of the weld. Lower power density may result in insufficient penetration, while too high a power density may easily cause burn-through or metal splashing.
- Beam shaping: Optimizing the shape of the laser spot can improve heat distribution during the welding process. For example, changing the circular spot to an elliptical or linearly distributed beam shape can significantly reduce the occurrence of weld pores and improve the stability of the weld.
- Focus adjustment: Precisely positioning the laser focus is the key to improving welding quality. A focus that is too deep may result in insufficient penetration, while a focus that is too shallow may cause surface ablation problems. Optimum penetration of the weld is therefore ensured through automatic focus or precision mechanical adjustment.
Process Control
Advanced process control technology provides a strong guarantee for the stability of welding quality.
- Adaptive control system: Use real-time monitoring equipment (such as cameras and sensors) to monitor key parameters in the welding process, and automatically adjust laser power, welding speed, etc. to ensure that the weld quality is always in the best state.
- Closed-loop feedback: The sensor obtains data such as molten pool shape and temperature, and feeds back to the control system in real-time, which can dynamically optimize welding parameters and reduce welding defects.
- Machine learning algorithm: Introduce artificial intelligence and machine learning technology to analyze a large amount of welding data, predict the best parameter combination, further optimize the welding process, and improve the level of automation.
Joint Design and Preparation
Joint design and edge preparation plays an important role in the strength of welded joints.
- Optimized joint geometry: The joint shape is designed according to the welding process and structural requirements. For example, butt joints are suitable for high-strength welding, while lap joints are more suitable for thin plate connections. By optimizing the joint geometry, the mechanical properties of the weld can be significantly improved.
- Precise assembly and alignment: Use high-precision fixtures and automatic positioning equipment to ensure the alignment accuracy of the joints, thereby avoiding welding offsets and poor joints, and improving the overall strength of the welds.
- Edge preparation: Use precision equipment to process the welding edge to make it smooth and burr-free, which can effectively reduce the tendency of cracks and improve the consistency and reliability of the weld.
Post-Weld Treatment
Post-weld treatment can further release welding residual stress and improve the mechanical properties and service life of the weld.
- Heat treatment: Release welding stress through annealing or tempering, improve the microstructure of the weld and surrounding materials, and improve the toughness and strength of the material.
- Surface finishing: Remove rough parts and defects on the weld surface by grinding or polishing, thereby improving its fatigue resistance and aesthetics.
- Nondestructive testing: Use nondestructive testing methods such as ultrasonic and radiographic testing to ensure that there are no hidden dangers such as cracks and pores inside the weld, further improving the reliability of the product.
- Mechanical processing: Improve the residual stress distribution on the weld surface through methods such as shot peening, and use rolling technology to improve the density and fatigue resistance of the weld through mechanical pressure. These mechanical processing methods can provide additional strengthening measures for the weld.
Improving the strength of laser welded joints requires comprehensive optimization of many aspects, from material selection and preparation to precise adjustment of laser parameters, to advanced process control and post-weld treatment, each link is crucial. Through scientific and reasonable process combinations, not only can the mechanical properties of welded joints be improved, but also the overall welding quality and reliability can be improved, providing strong support for high-standard industrial applications.
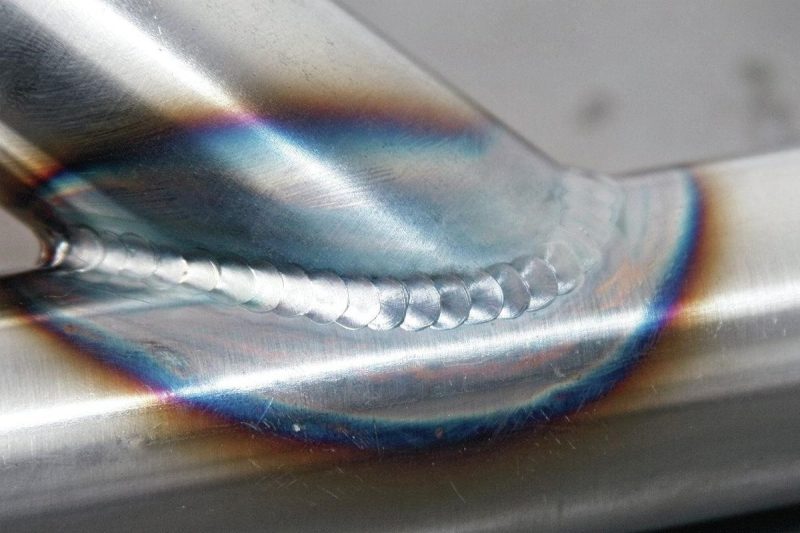
Challenges and Solutions
In the laser welding process, although the efficiency and precision of the technology provide strong support for multi-industry applications, there are still some challenges in practical applications, which directly affect the quality and stability of welded joints. To address these challenges, effective solutions can not only improve welding quality but also broaden the application scope of laser welding. The following will discuss in detail the three key challenges of thermal management, material compatibility, and process stability and their solutions.
Thermal Management
Thermal management is an important issue that needs to be addressed during laser welding. Laser welding can easily lead to local overheating of the material due to concentrated heat input, which can cause deformation, thermal cracks, or residual stress, all of which may reduce the strength and life of the welded joint.
Challenge Analysis
- In high heat input environments, uneven expansion and contraction of materials can cause deformation, especially in the welding of thin materials and precision parts.
- Excessively high temperatures may cause cracks or intergranular corrosion in the weld, affecting the welding performance.
Solution
- Optimize welding path: Optimize welding path through computer-aided design (CAD), disperse heat input, and reduce the temperature of heat accumulation area.
- Cooling device: Introducing a cooling water fixture or air cooling equipment during welding can effectively control the heat input intensity of the welding area and reduce the probability of thermal deformation and cracks.
- Pulse laser mode: Using pulse laser welding instead of continuous laser welding can better control heat input, reduce the range of heat-affected zones, and thus improve welding quality.
Material Compatibility
In industrial production, welding of dissimilar materials is becoming more and more common, such as steel and aluminum, copper and stainless steel, etc. The differences in physical properties and chemical properties of these materials can bring about welding difficulties.
Challenge Analysis
- Welding of dissimilar materials is prone to poor fusion, brittle phases, or interface cracks, which seriously affect the strength and reliability of the welded joint.
- The difference in expansion coefficient between the materials may cause large residual stress in the weld during cooling, increasing the risk of cracking.
Solution
- Select compatible alloys: By optimizing the material formula, select alloys with higher compatibility as the base material to reduce the occurrence of poor fusion and cracks.
- Use filler materials: Adding specific filler materials (such as master alloys or welding wires) during the welding process can improve the fusion performance of the two materials while reducing the complexity of the interface reaction.
- Laser parameter optimization: Precisely adjust the laser power, welding speed, and focus position to meet the specific needs of dissimilar material welding and ensure the stability and uniformity of the molten pool.
Process Stability
Laser welding is a highly parameter-dependent process. Fluctuations in welding parameters may lead to inconsistencies in weld quality, thus affecting production efficiency and product performance.
Challenge Analysis
- Unstable laser power or welding speed can result in uneven weld depth, width, and strength.
- Vibration in the welding equipment or loose material clamping can cause weld defects such as lack of fusion, porosity, or offset issues.
Solution
- Adaptive control: Introduce an intelligent adaptive control system to dynamically adjust the laser power and welding speed according to the real-time monitored welding parameters (such as temperature, molten pool shape, etc.), thereby ensuring high stability of the process.
- Closed-loop feedback system: Use high-precision sensors to collect key data in the welding process and feed the data back to the control system for automatic adjustment. For example, the focus position is dynamically adjusted by real-time monitoring of the shape changes of the molten pool to ensure the consistency of the weld.
- Artificial intelligence optimization: Introduce an algorithm based on machine learning to achieve automatic optimization of the laser welding process through big data analysis and parameter prediction, reduce the impact of parameter fluctuations, and improve the reliability and repeatability of welding.
In laser welding applications, thermal management, material compatibility, and process stability are the three key challenges that affect welding quality. These problems can be effectively solved by adopting optimized welding paths, compatible alloys, filler materials, and intelligent control technology to improve the mechanical properties and process stability of the weld. These solutions can not only meet the high requirements of current industrial production but also provide a solid foundation for the further development of laser welding technology.
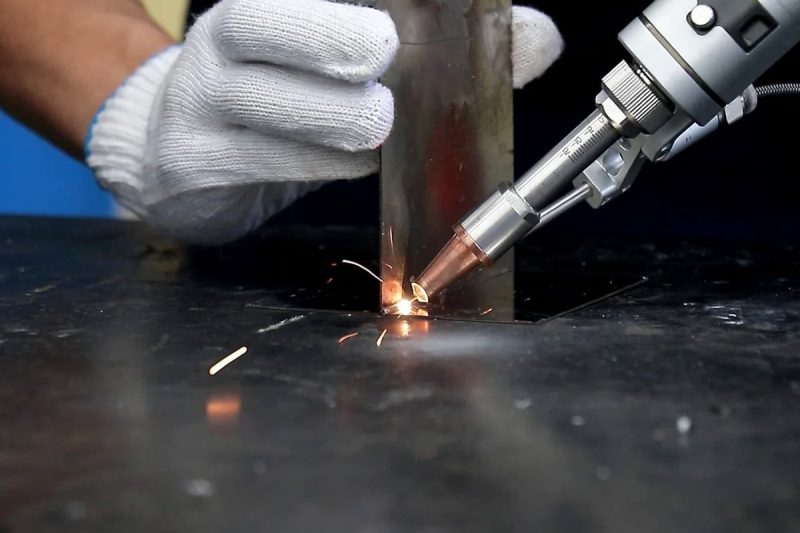
Summarize
As an efficient and precise welding method, laser welding technology has great potential to improve joint strength. By optimizing material selection, laser parameters, joint design, and post-weld treatment, the strength and reliability of welded joints can be effectively improved. Precise laser power control, proper surface cleaning, suitable joint geometry design, and post-weld heat treatment during welding can help reduce thermal deformation and enhance the fatigue resistance of welded joints. In addition, with the advancement of process control technology, especially the application of machine learning and adaptive control systems, the stability and quality of laser welding have been unprecedentedly guaranteed. The integration of all these technologies makes laser welding more competitive in industrial applications and brings more efficient and reliable welding solutions to various industries.
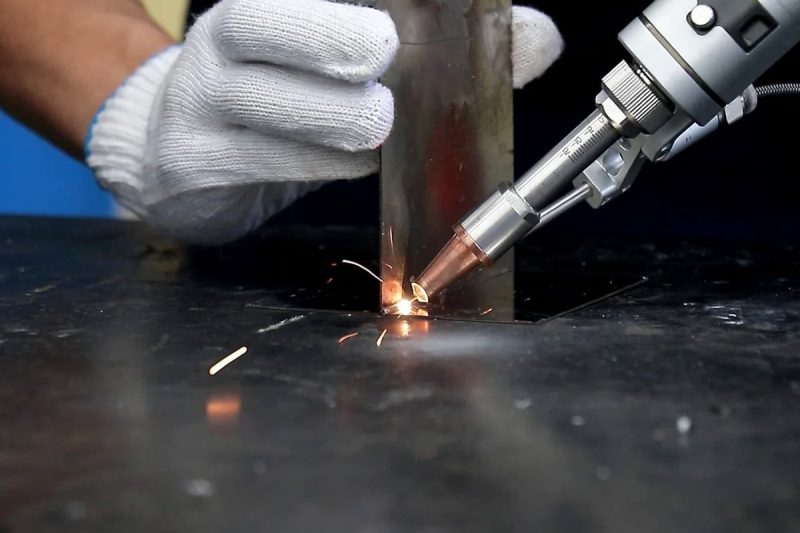
Get Laser Solutions
As a leader in the field of laser welding, AccTek Laser laser generators provide high-strength and high-stability welding solutions with excellent performance and precision technology. We focus on tailoring solutions for our customers to ensure that each device can perfectly adapt to your specific needs. Whether it is material compatibility, control of the welding process, or post-weld processing, our laser technology can help you achieve the best welding effect, and improve production efficiency and product quality. We are committed to providing comprehensive technical support and solutions to every customer to ensure that your welding process is always at the leading level in the industry. If you have any questions or needs about laser welding technology, please feel free to contact us. We will provide you with the most professional consultation and services to help you succeed on the road to laser welding!
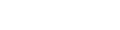
Contact information
- [email protected]
- [email protected]
- +86-19963414011
- No. 3 Zone A, Lunzhen Industrial Zone,Yucheng City , Shandong Province.
Get Laser Solutions