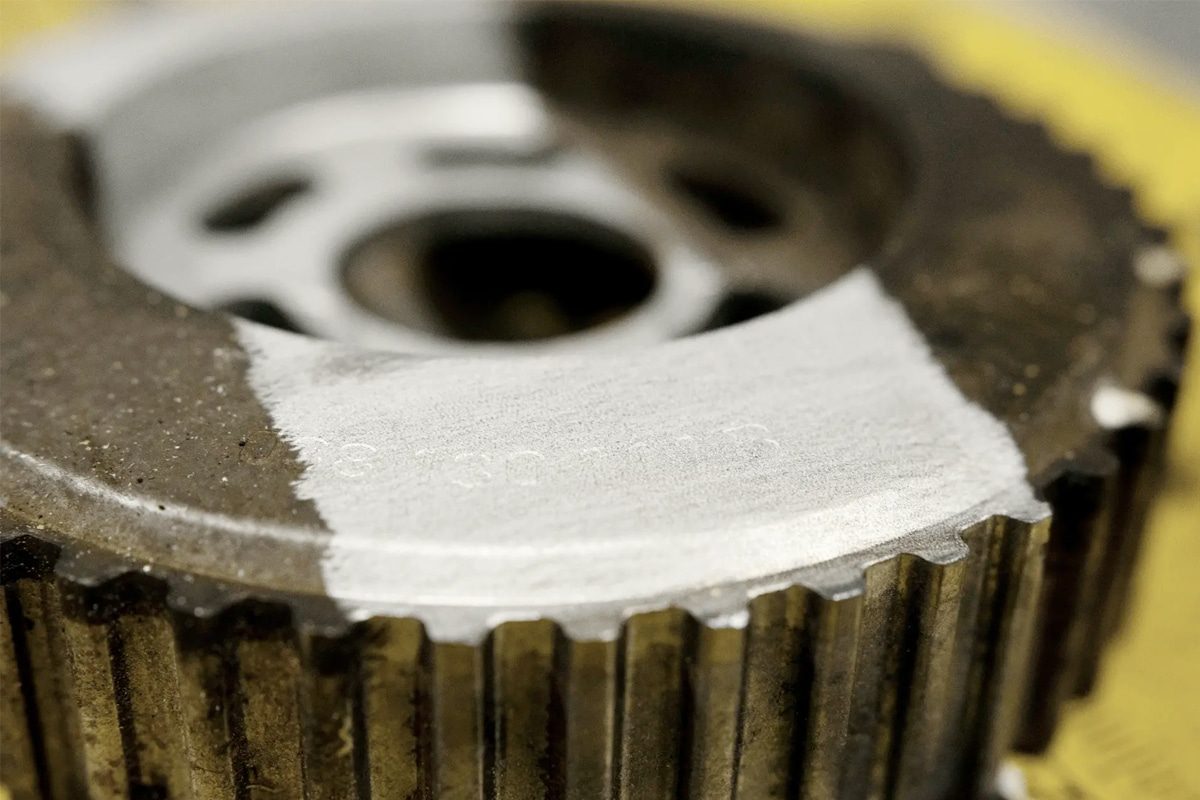
How to Maintain The Laser Cleaning Machine?
Maintaining a laser cleaning machine is critical to ensure consistent performance, long service life, and maximum efficiency. As a sophisticated and versatile tool, laser cleaning machines excel at removing rust, paint, and contaminants from a wide range of surfaces with unmatched precision and minimal environmental impact. Proper maintenance not only protects your investment but also guarantees the safety and productivity of your operations. This guide offers a comprehensive overview of essential maintenance practices, from daily inspections and cleaning of optics to scheduled servicing and component replacements. By adhering to recommended maintenance protocols, you can minimize downtime, reduce costly repairs, and maintain the optimal functionality of your laser cleaning system. Whether you’re an operator or technician, understanding and implementing these best practices will ensure your machine continues to deliver top-tier results in even the most demanding applications.
Table of Contents
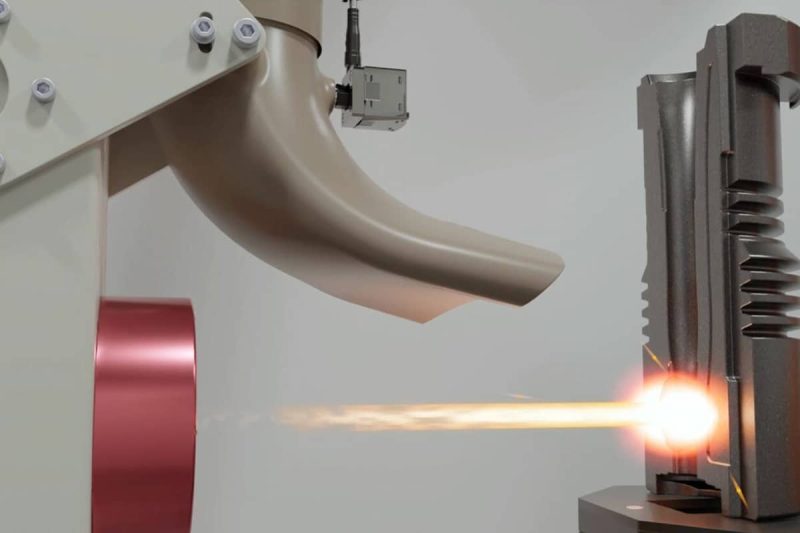
Understanding the Importance of Maintenance
Regular maintenance of a laser cleaning machine is crucial for ensuring its optimal performance, longevity, and safety. These machines are valuable assets in industries ranging from automotive to aerospace, and maintaining them properly yields significant benefits while neglecting maintenance can lead to serious consequences.
Benefits of Regular Maintenance
- Optimal Performance: Consistent maintenance keeps the machine running at peak efficiency, ensuring precise cleaning results and stable laser output.
- Extended Lifespan: Proper care and upkeep prevent premature wear and tear on critical components, ultimately prolonging the life of the machine.
- Minimized Downtime: Routine inspections and timely servicing help identify and resolve potential issues before they escalate, reducing downtime and maximizing productivity.
- Cost Savings: Preventative maintenance lowers the risk of costly repairs or unexpected replacements by catching small issues early.
- Enhanced Safety: Regular maintenance ensures all safety features are operational, reducing the likelihood of accidents or hazardous malfunctions during operation.
Consequences of Neglecting Maintenance
- Reduced Efficiency: Poor maintenance can lead to inconsistent cleaning results, degraded laser output, and inefficient operation, impacting productivity.
- Equipment Failure: Ignoring maintenance tasks can result in component malfunctions, damage to the laser source, or complete system breakdowns, potentially halting production.
- Higher Costs: Neglected maintenance often leads to expensive repairs or the need for early replacement of key components, significantly increasing operational expenses.
- Safety Risks: Failing to maintain safety-critical components, such as cooling systems or interlocks, can expose operators to laser radiation hazards, electrical issues, and mechanical failures.
- Environmental Impact: Poorly maintained machines can produce excess waste, fumes, or emissions, undermining environmental benefits and compliance with industry standards.
Maintaining your laser cleaning machine is not just about keeping it operational, it’s about ensuring consistent performance, safeguarding investments, and maintaining a safe work environment. Regular maintenance translates into reliability and cost-effectiveness, while neglect can lead to disruptions and hazards.
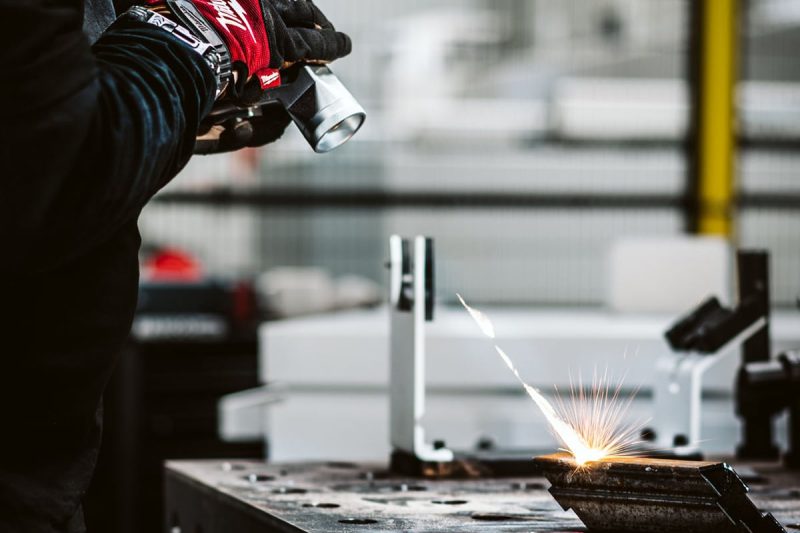
Safety Precautions Before Maintenance
Maintaining a laser cleaning machine involves specific safety protocols to protect both the operator and the equipment. Failure to adhere to these precautions can lead to serious accidents, damage, and downtime.
Personal Protective Equipment (PPE)
Proper PPE is essential for anyone performing maintenance on a laser-cleaning machine. This equipment reduces exposure to laser radiation, hazardous debris, and electrical risks.
- Laser Safety Glasses: Always wear laser-rated safety glasses to shield your eyes from harmful laser radiation, even when the machine is turned off, as residual energy may be present.
- Gloves: Use gloves made of appropriate material to prevent contact with sharp edges, hot surfaces, and potentially harmful chemicals.
- Protective Clothing: Wear long-sleeved clothing, lab coats, or coveralls that are non-reflective and flame-resistant for maximum protection.
- Face Shields: If there is a risk of debris or splash, a face shield provides an additional layer of facial protection.
Safety Guidelines
- Authorized Personnel Only: Maintenance should only be performed by trained and authorized personnel familiar with laser equipment and its associated risks.
- Work Area Safety: Ensure that the maintenance area is free of flammable materials and that the workspace is clean and organized.
- Warning Signs: Display warning signs around the machine being serviced, indicating that maintenance is in progress.
- Ventilation: Confirm that there is adequate ventilation, especially if there is a risk of fumes or gases during maintenance procedures.
- Follow Manufacturer Guidelines: Adhere strictly to the manufacturer’s recommended maintenance procedures and safety protocols.
Power-Off Procedures
Before performing any maintenance, ensure that the machine is powered off and all energy sources are properly isolated.
- Turn Off the Machine: Switch off the machine using its main power button and wait for the system to completely shut down.
- Disconnect from Power Supply: Unplug the machine from the electrical supply or switch off the circuit breaker to completely isolate it from any power source.
- Discharge Residual Energy: Allow sufficient time for any residual electrical or laser energy to dissipate before starting maintenance tasks. This minimizes the risk of accidental exposure or electrical shock.
- Lockout/Tagout (LOTO): Use lockout/tagout procedures to ensure the machine cannot be powered on by anyone else during maintenance. Apply locks and tags to the main power switch, indicating that maintenance is in progress.
- Release Pressure and Cool Down: If applicable, release any built-up pressure in the cooling system and allow components to cool to a safe temperature before handling.
By following these safety precautions, you can ensure a secure environment for maintenance tasks, protect personnel from potential hazards, and preserve the integrity of your laser cleaning machine.
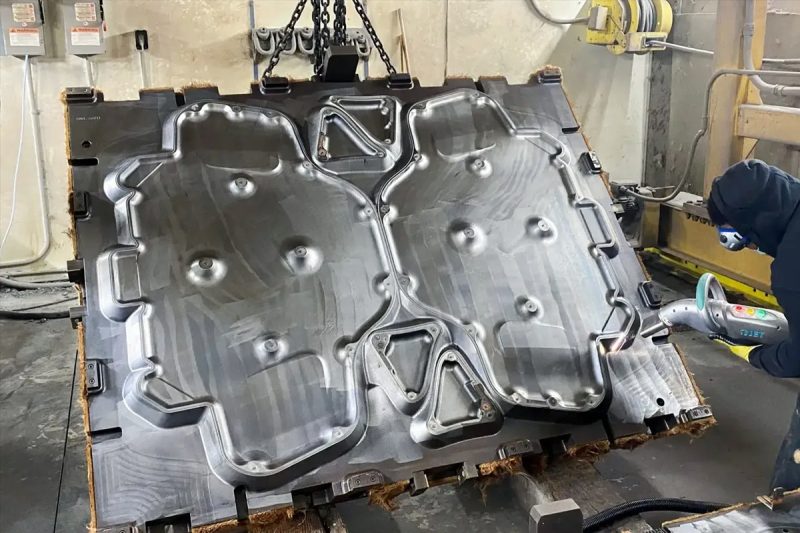
Daily Maintenance Tasks
To ensure your laser cleaning machine operates efficiently and maintains its longevity, it’s crucial to perform daily maintenance. These routine tasks are simple yet essential for detecting and addressing potential issues early, reducing downtime, and maximizing performance.
Exterior Cleaning
- Remove Dust and Debris: Use a soft, lint-free cloth or a vacuum cleaner to remove dust, dirt, and debris from the exterior surfaces of the machine. This prevents the accumulation of contaminants that can interfere with performance or cause overheating.
- Wipe Down Surfaces: Clean the machine’s exterior with a mild, non-abrasive cleaning solution to remove stains, grease, or grime. Avoid harsh chemicals that could damage paint or plastic components.
- Keep Vents Clear: Ensure that ventilation openings are free from dust or obstructions. Proper airflow is critical to maintain cooling and prevent internal components from overheating.
Visual Inspection
- Overall Condition: Conduct a visual scan of the machine’s components to identify any signs of wear, cracks, or corrosion. Pay close attention to the laser head, lenses, and mirrors to detect any dirt, scratches, or debris that might impact performance.
- Check for Leaks: Inspect hoses, coolant lines, and other components for any signs of leakage, as coolant leaks can compromise machine safety and efficiency.
- Moving Parts: Examine moving parts, such as guide rails and mechanical joints, for smooth operation. Note any unusual noises, vibrations, or resistance, which could indicate misalignment or wear.
Checking Connections and Cables
- Electrical Connections: Verify that all electrical connections are secure and free from signs of damage or corrosion. Loose or worn connections can lead to malfunctions or pose safety risks.
- Cable Integrity: Inspect cables and wiring for any signs of fraying, pinching, or wear. Damaged cables should be replaced immediately to avoid electrical hazards or signal disruptions.
- Connection Ports: Ensure that connection ports, plugs, and sockets are clean and firmly connected. Dust or loose connections may disrupt communication between components or impact machine performance.
By incorporating these daily maintenance tasks into your routine, you can help maintain the performance and reliability of your laser cleaning machine. Regular exterior cleaning, visual inspections, and checking connections will minimize the risk of malfunctions, extend the lifespan of your equipment, and ensure safe operation.
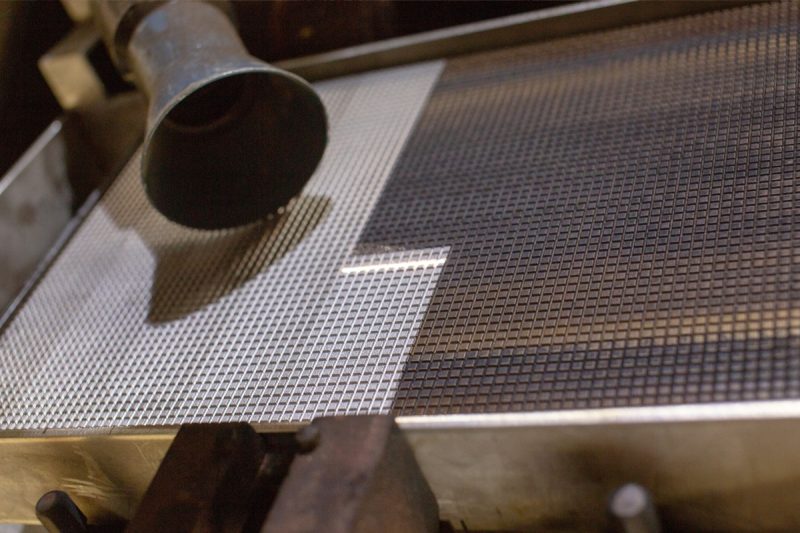
Weekly Maintenance Tasks
In addition to daily maintenance, performing a more detailed weekly inspection and cleaning of your laser cleaning machine is essential for ensuring long-term efficiency and optimal performance. Weekly maintenance focuses on critical components that influence the precision and reliability of the machine.
Inspecting Optical Components
- Check for Damage: Inspect the machine’s optical components, including lenses, mirrors, and beam path elements, for signs of wear, scratches, cracks, or contamination. Any damage to these components can significantly affect laser performance, reducing cleaning accuracy and power output.
- Alignment Verification: Ensure that the optical components are properly aligned according to the manufacturer’s specifications. Misalignment can lead to reduced laser efficiency, inconsistent cleaning results, and potential component damage.
- Dust and Contamination: Look for any dust, dirt, or other contaminants on the optical surfaces. Even small particles can scatter the laser beam, reducing its effectiveness.
Cleaning Lenses and Mirrors
- Use Appropriate Cleaning Tools: Clean lenses and mirrors using specialized optical cleaning solutions and lint-free wipes or swabs. Do not use regular cleaning products, as these may scratch or damage the delicate surfaces.
- Handle with Care: When cleaning, avoid touching optical surfaces with your fingers, as oils and residue from skin contact can degrade optical clarity and cause damage over time.
- Inspect After Cleaning: Once cleaning is complete, inspect the lenses and mirrors for any remaining residue or streaks. Repeat the cleaning process if necessary to ensure all optical surfaces are clear.
Checking the Cooling System
- Coolant Levels: Verify that the coolant reservoir is filled to the manufacturer’s recommended level. Low coolant levels can lead to overheating and may cause damage to the laser source and other components.
- Coolant Quality: Check the coolant for any signs of contamination, discoloration, or sediment buildup. Replace the coolant if necessary to maintain optimal heat transfer and system efficiency.
- Inspect Hoses and Connections: Examine all cooling hoses, connections, and fittings for leaks, cracks, or wear. Ensure that all connections are secure to prevent coolant leaks and potential malfunctions.
- Cooling Fan and Vents: Clean the cooling fan and vents to ensure unobstructed airflow. Dust or debris buildup can impede cooling efficiency, causing overheating.
By performing these weekly maintenance tasks, you can significantly enhance the reliability and performance of your laser cleaning machine. Regular inspections of optical components, thorough cleaning of lenses and mirrors, and checking the cooling system will help to prevent costly repairs, ensure consistent results, and extend the lifespan of your equipment.
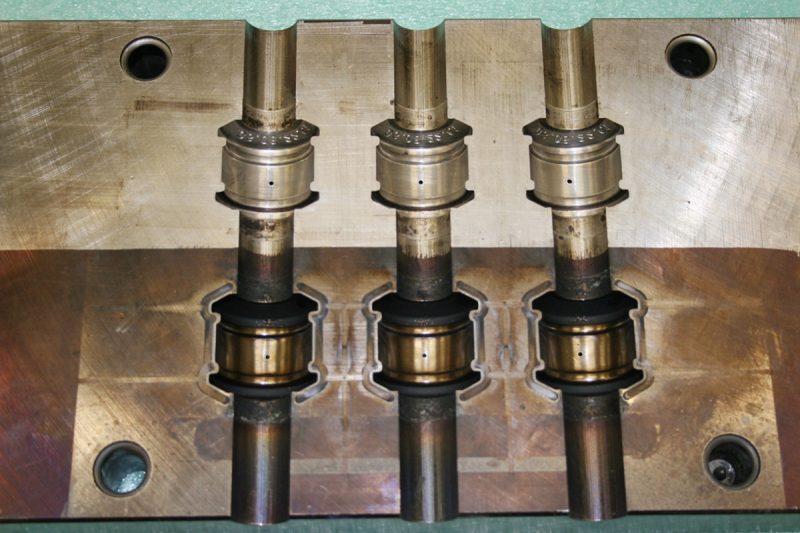
Monthly Maintenance Tasks
In addition to daily and weekly upkeep, monthly maintenance tasks for your laser cleaning machine focus on inspecting critical components, ensuring precise calibration, and maintaining the integrity of software systems. These steps are necessary for maintaining optimal performance, reducing downtime, and preventing unexpected failures.
Inspecting the Laser Source
- Visual Inspection: Carefully examine the laser source for any visible signs of wear, damage, or discoloration. Dust, debris, or oxidation around the laser housing can impact performance and should be cleaned as needed.
- Check Performance Metrics: Measure the laser output power to ensure it is operating within the specified range. Any noticeable decline in power or beam quality may indicate an issue with the laser source or internal optics.
- Inspect Electrical Connections: Ensure that all electrical connections to the laser source are secure and free from corrosion. Loose or damaged connections can lead to inconsistent performance or system failures.
- Cooling System Functionality: Verify that the laser source is adequately cooled during operation. Check for signs of overheating, which may require immediate attention.
Calibrating the Laser
- Beam Alignment: Check the alignment of the laser beam relative to the optical path. Misalignment can lead to inconsistent cleaning results and reduced efficiency. Use calibration tools or follow the manufacturer’s guidelines to adjust as necessary.
- Power Calibration: Perform a power calibration to ensure that the laser output is consistent and accurate. Use a power meter to verify the actual laser output matches the machine settings.
- Recalibration Schedule: Follow the manufacturer’s recommended recalibration schedule or make adjustments if any discrepancies in performance are detected during operation.
Software Updates and Backups
- Update Firmware and Software: Check for and install any software or firmware updates provided by the manufacturer. Regular updates can improve performance, fix known issues, and enhance the machine’s capabilities.
- Configuration Backup: Create a backup of your current machine settings and configurations. This ensures that if any software issues arise or if a reset is needed, you can quickly restore the system to its previous state.
- Verify Software Integrity: Test and verify that all software features are functioning correctly after updates. Address any potential compatibility issues or bugs immediately by consulting with technical support.
By conducting these monthly maintenance tasks, you will keep your laser cleaning machine operating at peak performance while minimizing the risk of unexpected downtime. Regular inspection of the laser source, precise calibration, and timely software updates ensure consistent and accurate cleaning results while safeguarding the machine’s long-term health.
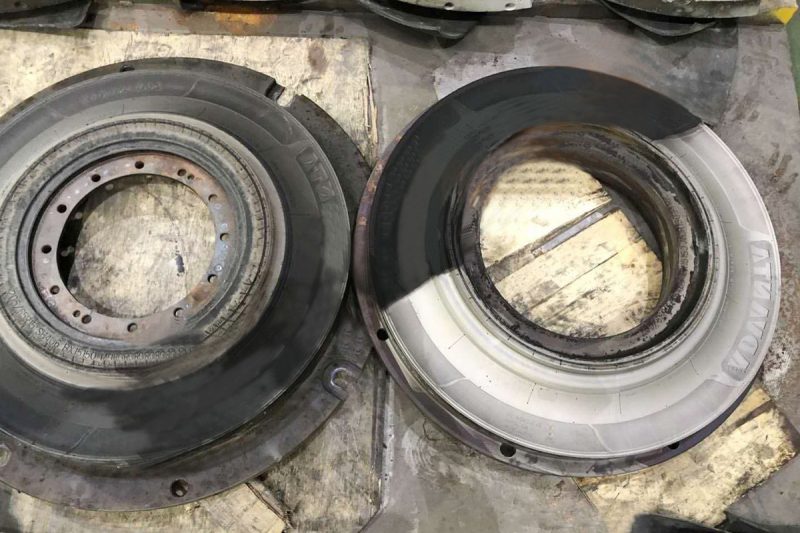
Annual Maintenance Tasks
Annual maintenance of your laser cleaning machine is critical for ensuring long-term performance, safety, and reliability. These tasks involve comprehensive system checks, the replacement of worn components, and professional servicing to address deeper issues that may not be evident during daily or monthly maintenance routines.
Comprehensive System Check
- System Diagnostics: Perform a full system diagnostic to assess the health and performance of all major components, including the laser source, optics, cooling system, electrical connections, and mechanical parts. This helps identify potential issues that may not be visible during routine inspections.
- Calibration Verification: Confirm that all previously calibrated components, such as the laser alignment and power output, remain within manufacturer specifications. If necessary, recalibrate the system to maintain peak performance.
- Inspecting Safety Systems: Check the functionality of safety interlocks, emergency stop buttons, and any other safety mechanisms built into the machine. Ensure they are fully operational and compliant with safety standards.
Replacing Worn Components
- Optical Components: Replace any lenses, mirrors, or other optical components that show signs of wear, scratches, or degradation. Worn optics can significantly impact the efficiency and precision of the cleaning process.
- Mechanical Parts: Inspect and replace mechanical components, such as bearings, seals, and moving parts, that have reached their end-of-life cycle. This helps prevent mechanical failure and ensures the smooth operation of the machine.
- Consumable Items: Replace consumables such as filters, gaskets, and seals according to the manufacturer’s recommendations. Regular replacement of these items ensures that the machine operates efficiently and minimizes the risk of contamination.
Professional Servicing
- Certified Technician Inspection: Schedule an annual visit from a certified technician for an in-depth inspection and servicing. Professional servicing often includes advanced diagnostics and maintenance procedures that may not be feasible during routine maintenance.
- Component Upgrades: Consider any recommended hardware or software upgrades to enhance the performance, efficiency, or safety of the machine. Upgrades can offer new capabilities or improve existing functionality.
- Documentation and Recommendations: Ensure that the servicing team provides detailed documentation of the maintenance performed, along with recommendations for any additional improvements or preventive measures.
By performing these annual maintenance tasks, you can ensure that your laser cleaning machine continues to operate at its best for years to come. Comprehensive system checks, timely replacement of worn components, and professional servicing are key to maximizing machine longevity, preventing costly breakdowns, and maintaining a safe working environment. Regular annual maintenance demonstrates a commitment to precision, reliability, and efficiency in all laser cleaning tasks.
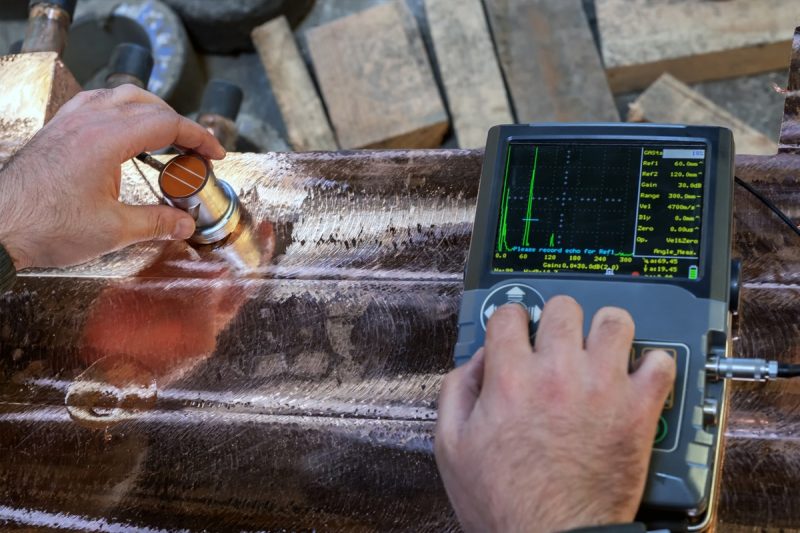
Troubleshooting Common Issues
Even with regular maintenance, laser cleaning machines may encounter occasional issues that can impact performance. Promptly identifying and addressing these issues is crucial to minimizing downtime and maintaining operational efficiency.
Laser Power Fluctuations
Power fluctuations can occur due to unstable electrical supply, dirty or damaged optical components, or issues with the laser source itself.
Troubleshooting Steps
- Check Electrical Supply: Ensure that the machine is receiving a stable power input without fluctuations. If needed, use a power stabilizer or UPS (uninterruptible power supply).
- Inspect Optics: Clean the lenses, mirrors, and other optical components to ensure they are free from dirt, dust, or scratches that could impact power levels.
- Laser Source Inspection: If the issue persists, inspect the laser source for any signs of wear or damage. Contact a professional technician if needed for a detailed assessment.
Overheating Problems
Overheating can result from inadequate cooling, blockages in the cooling system, or high ambient temperatures.
Troubleshooting Steps
- Check Coolant Levels: Ensure that the coolant reservoir is filled to the recommended level and that the coolant is free from contaminants.
- Inspect Cooling System: Examine hoses, pumps, and other cooling components for leaks, blockages, or malfunctions. Clean or replace as necessary.
- Improve Ventilation: Make sure that the machine is operating in a well-ventilated area. Ensure that vents and cooling fans are unobstructed and functioning correctly.
Laser Beam Misalignment
Misalignment of the laser beam can lead to inconsistent cleaning results and reduced efficiency. It can be caused by mechanical shocks, vibrations, or worn optical components.
Troubleshooting Steps
- Realign the Laser Beam: Follow the manufacturer’s guidelines to realign the laser beam. Use alignment tools as needed to ensure proper focus and orientation.
- Inspect Mechanical Components: Check for loose mounts, brackets, or other parts that could affect alignment. Tighten or replace components as necessary.
- Check Optical Path: Verify that all optical elements are correctly aligned and secure within the beam path.
Software Glitches
Software glitches may arise due to outdated software, corrupted files, or compatibility issues.
Troubleshooting Steps
- Restart the System: A simple restart may resolve minor software issues.
- Check for Updates: Ensure that you have the latest software and firmware updates installed. These often address known bugs and improve system stability.
- Restore Backup Settings: If settings have been corrupted, restore them from a previously saved backup. This can help revert the machine to a stable configuration.
- Contact Technical Support: For persistent issues, contact the manufacturer’s technical support team for guidance or troubleshooting assistance.
By understanding and addressing these common issues, you can quickly restore your laser cleaning machine to optimal performance. Proactively troubleshooting laser power fluctuations, overheating problems, laser beam misalignment, and software glitches will minimize downtime, maintain consistent results, and ensure that your machine continues to perform at its best.
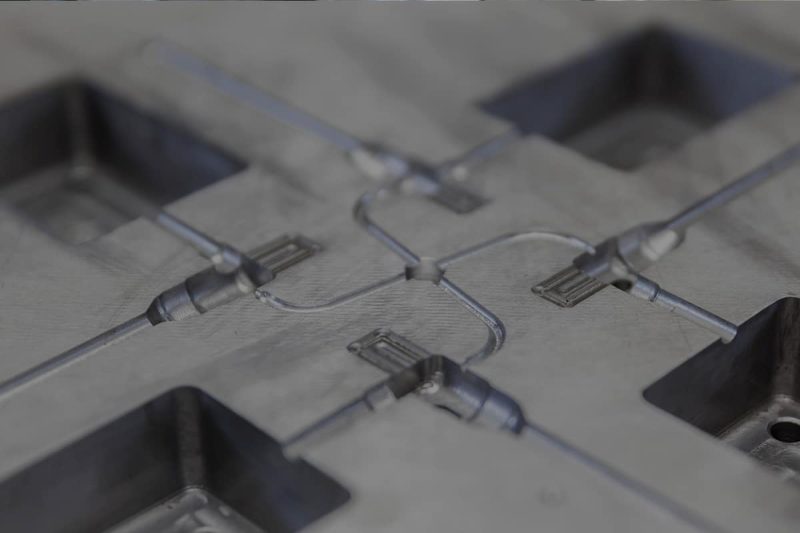
Best Practices for Prolonging Machine Life
To ensure the long-term performance and reliability of your laser cleaning machine, it is important to follow best practices that go beyond regular maintenance. Proper operation, a suitable environment, comprehensive training, and diligent record-keeping all contribute to the longevity and efficiency of your equipment.
Proper Operation Techniques
- Follow Manufacturer Guidelines: Always operate the machine according to the manufacturer’s instructions and recommendations. Adhering to prescribed settings and procedures minimizes the risk of damage and ensures optimal cleaning performance.
- Avoid Overloading: Do not exceed the recommended power output or workload for the machine. Overloading can strain the laser source and mechanical components, leading to premature wear or system failure.
- Monitor Performance: Regularly monitor the machine’s performance indicators, such as laser output power, temperature levels, and cleaning effectiveness. Promptly address any anomalies to prevent small issues from escalating.
Environmental Considerations
- Clean, Dust-Free Environment: Ensure that the machine is operated in a clean, dust-free environment. Accumulation of dust and debris can interfere with optics, cooling systems, and other critical components.
- Temperature Control: Maintain a stable ambient temperature within the recommended range for the machine. Excessive heat or cold can affect laser performance, lead to overheating, or cause condensation.
- Humidity Control: Avoid operating the machine in environments with excessive humidity, as it can lead to moisture buildup on optical components and electrical systems, increasing the risk of damage.
- Proper Ventilation: Ensure adequate ventilation around the machine to dissipate heat and prevent overheating of internal components.
Operator Training
- Initial Training: Ensure that all operators undergo comprehensive training on the machine’s operation, safety protocols, and basic maintenance procedures. A well-trained operator is less likely to make mistakes that could lead to equipment damage.
- Ongoing Education: Provide periodic refresher training and updates on new machine features, maintenance techniques, and industry best practices to keep operators informed and competent.
- Safety Emphasis: Emphasize the importance of safety measures, including the use of personal protective equipment (PPE), adherence to lockout/tagout procedures during maintenance, and awareness of laser hazards.
Record Keeping
- Maintenance Logs: Maintain a detailed log of all maintenance activities, including daily, weekly, monthly, and annual tasks. This log helps track the health of the machine and ensures that no essential tasks are missed.
- Service Records: Document all professional servicing and repairs, including dates, issues addressed, and components replaced. This information provides a comprehensive history of the machine’s upkeep.
- Performance Tracking: Keep records of performance metrics, such as laser output power and cleaning efficiency, to detect gradual changes over time. This can help predict when servicing or component replacement may be needed.
- Issue Documentation: Record any problems encountered, along with the steps taken to resolve them. This helps operators quickly troubleshoot similar issues in the future and contributes to an overall understanding of the machine’s behavior.
By implementing these best practices, you can prolong the life of your laser cleaning machine, ensure consistent performance, and protect your investment. Proper operation, maintaining an optimal environment, continuous operator training, and meticulous record-keeping form the foundation of effective machine management. This proactive approach minimizes downtime, reduces repair costs, and maximizes productivity.
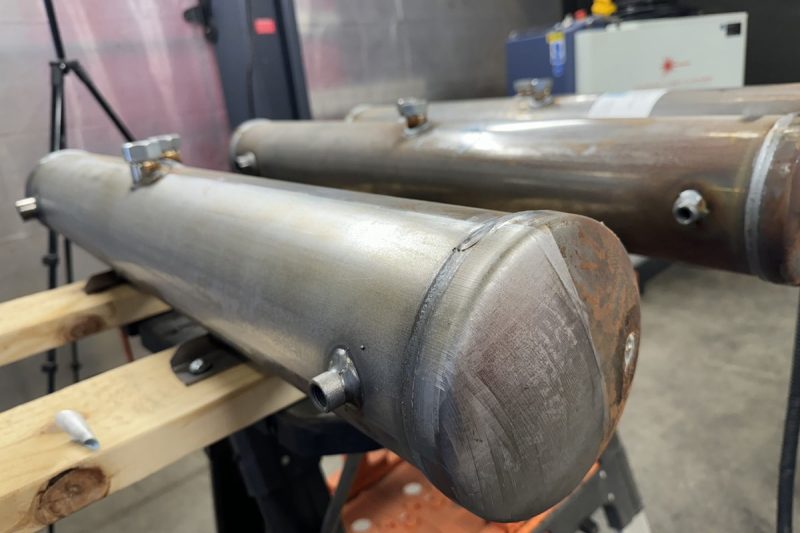
Summary
Maintaining your laser cleaning machine is essential for optimal performance, safety, and extended service life. Regular upkeep, including daily tasks like exterior cleaning and visual inspections, weekly checks of optical components, and monthly calibration and software updates, ensures consistent and reliable operation. Annual comprehensive system checks, professional servicing, and timely replacement of worn components further safeguard the machine’s efficiency and longevity. By adhering to proper operation techniques, controlling the machine’s environment, providing thorough operator training, and maintaining detailed maintenance records, you can minimize downtime, reduce costs, and maximize productivity. Effective maintenance not only protects your investment but also ensures consistent cleaning results in even the most demanding applications.
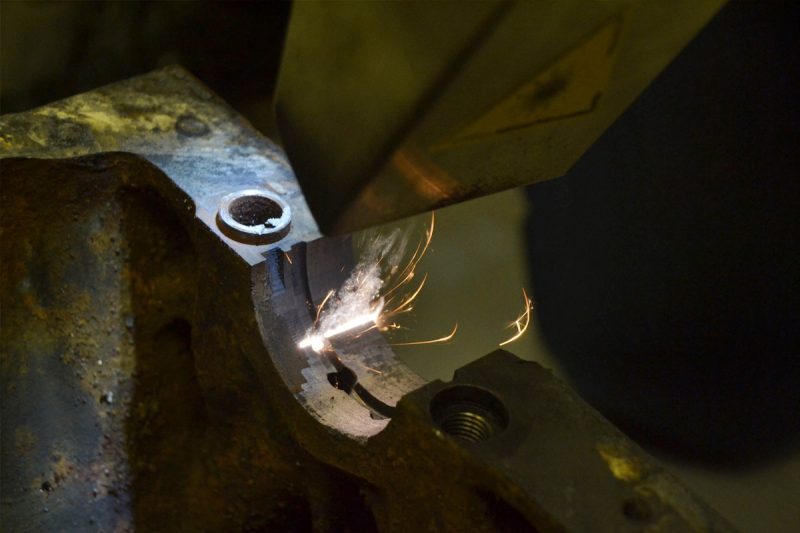
Get Laser Cleaning Solutions
Maintaining your laser cleaning machine is vital for consistent performance and extended service life. However, even with regular upkeep, there may be times when you need expert support or customized solutions to address unique cleaning challenges. At AccTek Laser, we offer comprehensive laser cleaning solutions designed to optimize your operations. Whether you need advanced troubleshooting, replacement components, or guidance on best maintenance practices, our experienced team is here to assist you every step of the way. We provide tailored maintenance programs, professional servicing, and access to the latest upgrades and enhancements, ensuring your laser cleaning machine continues to operate at peak efficiency. Our commitment to precision, safety, and innovation means you can rely on AccTek Laser for top-tier service and support. Contact us today to learn how our laser cleaning solutions can keep your equipment in perfect working condition and maximize your operational success.
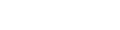
Contact information
- [email protected]
- [email protected]
- +86-19963414011
- No. 3 Zone A, Lunzhen Industrial Zone,Yucheng City , Shandong Province.
Get Laser Solutions