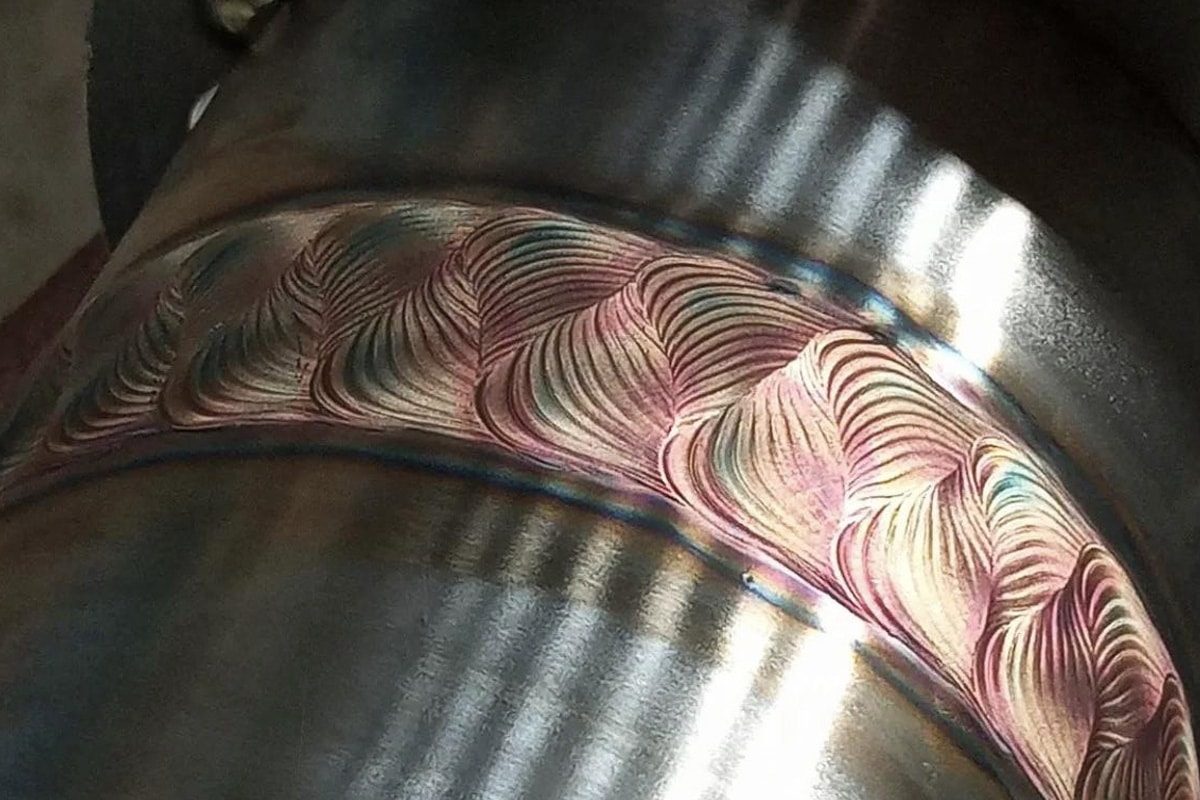
How to Minimize Laser Welding Distortion and Warpage?
Laser welding has revolutionized modern manufacturing, offering unmatched precision, efficiency, and versatility across industries. From automotive and aerospace components to medical devices and electronics, laser welding provides a high-speed, high-quality solution for joining metals. However, despite its many advantages, laser welding is not immune to common welding challenges, such as distortion and warpage. These issues, caused by uneven heating and cooling during the welding process, can compromise the dimensional accuracy, mechanical integrity, and aesthetic appeal of welded components.
Minimizing distortion and warpage is crucial for ensuring product quality, reducing material waste, and maintaining manufacturing efficiency. Achieving this requires a deep understanding of the factors contributing to thermal stresses, as well as the implementation of optimized techniques and advanced technologies. This article explores the causes of laser welding distortion and provides practical strategies for manufacturers to mitigate these challenges, delivering distortion-free welds for high-performance applications.
Table of Contents
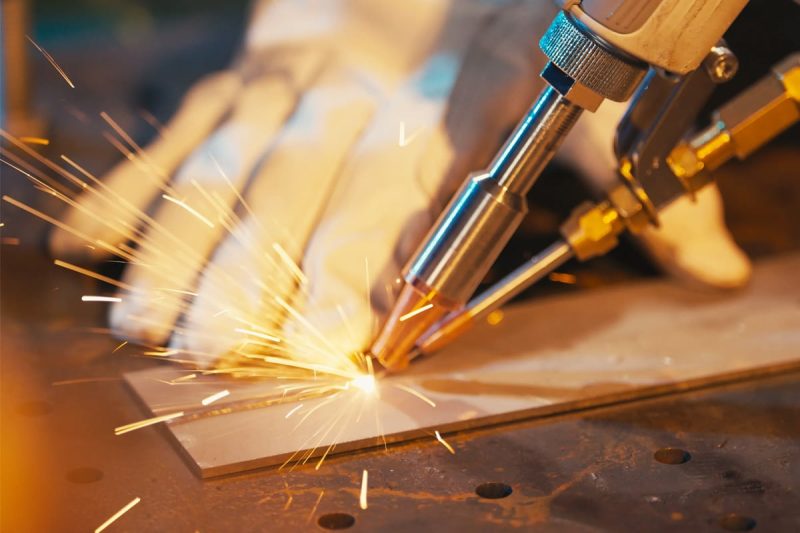
Understanding Laser Welding Distortion and Warpage
Laser welding, known for its precision and efficiency, can still produce distortion and warpage, challenging the structural integrity and quality of welded components. These deformations stem from various factors, including thermal effects, material properties, and the type of distortion experienced during the welding process. Understanding these aspects can help minimize distortion and ensure high-quality welds.
Thermal Effects During Welding
Laser welding involves the rapid application of concentrated heat to a localized area, creating steep thermal gradients. As the material heats, it expands, and during cooling, it contracts. The localized nature of this process often causes uneven thermal expansion and contraction, leading to residual stresses within the material.
Key thermal effects include:
- Thermal Expansion and Contraction: Rapid heating expands the material unevenly, while quick cooling creates contraction forces that distort the workpiece.
- Heat-Affected Zone (HAZ): The area surrounding the weld is subjected to thermal cycles that alter its microstructure, often causing additional stresses.
- Cooling Rates: Faster cooling rates can result in more significant warpages due to abrupt thermal shrinkage.
Material Properties Affecting Distortion
The behavior of materials during laser welding is largely influenced by their physical and thermal properties. These properties dictate how heat is absorbed, conducted, and dissipated, impacting the extent of distortion and warpage.
Key material properties include:
- Thermal Conductivity: Materials like aluminum, with high thermal conductivity, dissipate heat quickly, reducing thermal gradients but requiring higher laser power.
- Coefficient of Thermal Expansion (CTE): Materials with a higher CTE, such as aluminum alloys, experience greater expansion and contraction, increasing the likelihood of distortion.
- Elastic Modulus: Materials with a lower elastic modulus are more prone to deformation under thermal stress.
- Specific Heat Capacity: High heat capacity materials absorb more energy before changing temperature, affecting heat input distribution.
Types of Distortion in Welding
Distortion during laser welding manifests in several forms, depending on the material, joint design, and welding parameters. The most common types include:
- Longitudinal Shrinkage: Occurs along the weld seam due to contraction during cooling, shortening the material lengthwise.
- Transverse Shrinkage: This happens perpendicular to the weld seam, causing the material to contract sideways.
- Angular Distortion: Caused by uneven heat distribution between joint edges, resulting in an angular displacement.
- Buckling: Thin materials may warp or buckle due to excessive heat input, leading to an unstable workpiece.
- Rotational Distortion: Found in circular or curved parts where thermal stresses induce twisting.
By analyzing and understanding the interplay of thermal effects, material properties, and distortion types, manufacturers can implement strategies to mitigate these challenges and produce high-quality, distortion-free welds.
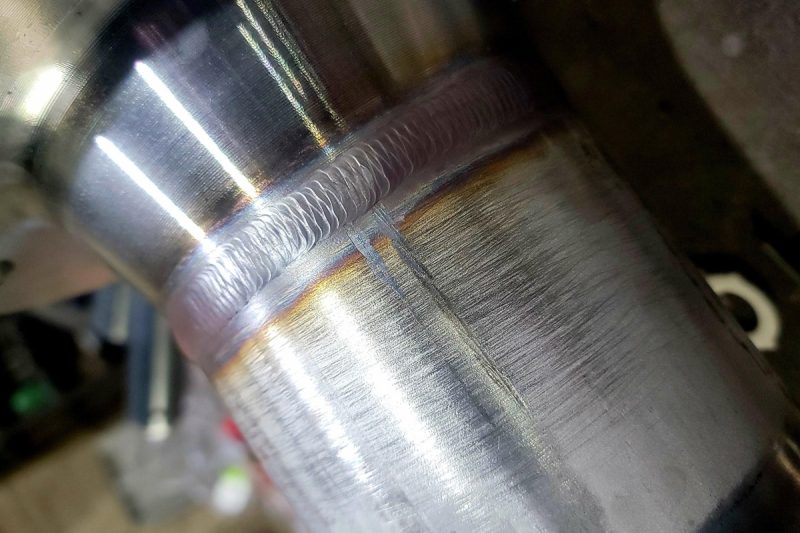
Materials Prone to Distortion and Warpage After Welding
The extent of distortion and warpage after laser welding is influenced by the material’s physical and thermal properties. Certain materials are inherently more susceptible due to their thermal expansion rates, conductivity, and mechanical characteristics. Understanding which materials are prone to distortion helps manufacturers adopt tailored strategies to minimize these effects.
Aluminum and Aluminum Alloys
Aluminum is highly prone to distortion due to its low melting point and high coefficient of thermal expansion (CTE). These characteristics lead to significant thermal expansion during welding and rapid contraction upon cooling. Additionally, aluminum’s high thermal conductivity dissipates heat quickly, requiring higher energy input, which can exacerbate thermal gradients and lead to warpage.
Key Challenges:
- High CTE causes pronounced expansion and contraction.
- Thin sections are particularly prone to buckling or angular distortion.
- Rapid heat dissipation leads to uneven thermal profiles.
Minimization Strategies:
- Use fixtures and clamps to restrain movement.
- Optimize welding speed and laser power to control heat input.
- Preheat components to reduce thermal gradients.
Stainless Steel
Stainless steel’s relatively high CTE and low thermal conductivity can make it prone to distortion, especially in thin sections. The material’s poor heat dissipation often results in concentrated thermal stresses near the weld zone, leading to shrinkage and angular distortion.
Key Challenges:
- Concentrated heat in the weld zone increases residual stresses.
- Susceptible to angular and transverse distortion in thin sections.
- Changes in microstructure in the heat-affected zone (HAZ) can amplify stresses.
Minimization Strategies:
- Balance laser power and speed to control heat input.
- Use symmetrical joint designs to distribute heat evenly.
- Employ backstepping or skip welding techniques to allow for cooling between passes.
High-Carbon Steels
High-carbon steels are susceptible to distortion due to their high thermal expansion and the potential for significant changes in microstructure during welding. The rapid cooling of high-carbon steels can introduce residual stresses, resulting in warpage or cracking.
Key Challenges:
- High risk of thermal expansion and contraction during welding.
- Rapid cooling increases residual stresses.
- Microstructural changes can lead to brittleness and warping.
Minimization Strategies:
- Preheat and control cooling rates to reduce thermal stresses.
- Use pulse welding techniques to minimize heat input.
- Optimize joint fit-up to reduce gaps and uneven heating.
Thin Sheet Metals
Regardless of the material type, thin sheet metals are particularly prone to distortion because they lack the stiffness to resist thermal stresses. Even minimal heat input during laser welding can cause buckling or waviness.
Key Challenges:
- Limited rigidity to counteract thermal stresses.
- Higher susceptibility to angular distortion and buckling.
- Rapid heat absorption and dissipation amplify thermal gradients.
Minimization Strategies:
- Employ rigid clamping and fixturing to maintain shape.
- Reduce heat input by increasing welding speed or using pulsed lasers.
- Use backing bars or heat sinks to stabilize the workpiece.
Titanium and Titanium Alloys
Titanium exhibits moderate susceptibility to distortion due to its relatively high CTE and low thermal conductivity. While it is less prone to warpage compared to aluminum or thin steel, improper heat control during welding can lead to angular or longitudinal distortion.
Key Challenges:
- Low heat dissipation increases localized thermal stresses.
- High reactivity with oxygen during welding can exacerbate warpage.
- Sensitive to overheating and prolonged exposure to high temperatures.
Minimization Strategies:
- Employ shielding gas to maintain weld quality and minimize thermal effects.
- Use precision fixturing to hold parts in place.
- Optimize welding parameters for controlled heat input.
Copper and Copper Alloys
Copper’s high thermal conductivity makes it challenging to weld consistently, as heat rapidly dissipates, creating uneven thermal gradients. However, its high CTE makes it susceptible to distortion when heat input is excessive.
Key Challenges:
- Rapid heat dissipation requires high laser power.
- High CTE causes significant expansion and contraction.
- Uneven heating leads to warpage in complex geometries.
Minimization Strategies:
- Use preheating to reduce the thermal gradient.
- Optimize laser focus and power to ensure consistent heat application.
- Employ real-time monitoring to control heat input.
Duplex Stainless Steel
Duplex stainless steels are less prone to distortion than austenitic stainless steels due to their higher stiffness. However, uneven heat application can still lead to angular and transverse distortion, particularly in asymmetrical welds.
Key Challenges:
- Uneven cooling can lead to residual stresses.
- Angular distortion in complex geometries.
- Microstructural changes due to thermal cycling.
Minimization Strategies:
- Use balanced welding techniques to evenly distribute heat.
- Control interpass temperatures to prevent uneven cooling.
- Employ laser welding with real-time monitoring for precision.
Materials prone to distortion after welding share common traits such as high thermal expansion coefficients, low stiffness, and sensitivity to uneven heating. Addressing these challenges requires careful selection of welding parameters, fixturing solutions, and thermal control techniques. By understanding the behavior of each material under thermal stress, manufacturers can implement tailored strategies to achieve distortion-free welds and maintain the integrity of their components.
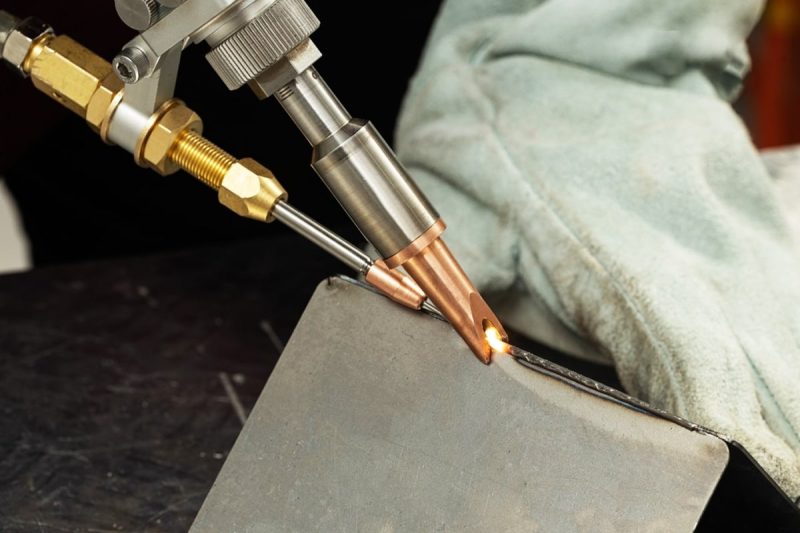
Factors Influencing Distortion and Warpage in Laser Welding
Laser welding is a precise and efficient process, but its localized heat input and rapid cooling can cause distortion and warpage. Understanding the factors that contribute to these challenges can help implement effective strategies to minimize them.
Heat Input and Thermal Gradients
The heat input during laser welding and the resulting thermal gradients play a critical role in determining the extent of distortion and warpage.
- Localized Heat Input: Laser welding focuses intense heat on a small area, creating steep temperature gradients. These gradients cause uneven expansion and contraction of the material, leading to residual stresses.
- Excessive Heat Input: If the laser power is too high or the welding speed too slow, excessive heat input can enlarge the heat-affected zone (HAZ) and amplify distortion.
- Rapid Cooling: Laser welding often involves rapid cooling, which can create abrupt temperature changes and increase the risk of warpage.
Mitigation Strategies:
- Optimize laser power and welding speed to balance heat input and minimize thermal gradients.
- Use pulse welding techniques to control heat delivery and reduce excessive heating.
- Employ thermal imaging or real-time monitoring systems to track and adjust temperature profiles during welding.
Material Thickness and Joint Design
The thickness of the material and the design of the weld joint significantly affect distortion behavior during laser welding.
- Material Thickness: Thin materials are more prone to distortion due to their low stiffness and inability to resist thermal stresses. Thicker materials are less susceptible but may require higher laser power, increasing the HAZ.
- Joint Design: The type and fit-up of the weld joint influence heat distribution. Poorly designed joints can exacerbate thermal gradients and lead to uneven expansion and contraction.
Common Joint Types and Their Impact:
- Butt Joints: Generally minimize distortion when properly aligned.
- Lap Joints: Can create significant thermal gradients, leading to warpage.
- T-Joints and Corner Joints: More complex geometries may concentrate stresses, increasing distortion risks.
Mitigation Strategies:
- Select joint designs that promote symmetry and distribute heat evenly.
- Ensure tight joint fit-up to minimize gaps and uneven heating.
- Use edge preparation techniques, such as beveling, to improve joint stability and reduce distortion.
Clamping and Fixturing
Proper clamping and fixturing are essential to hold the workpiece in place and counteract the forces that distort welding.
- Rigid Clamping: Provides strong support but may introduce residual stresses if over-restrained.
- Flexible Clamping: Allows some movement to reduce stress accumulation but may not fully prevent warpage.
- Heat Sinks: Fixtures that act as heat sinks can help dissipate heat, reducing thermal gradients.
Effects of Inadequate Fixturing:
- Insufficient support allows the workpiece to move or deform during welding.
- Over-constraining can lock in stresses, leading to post-weld warpage.
Mitigation Strategies:
- Use robust fixturing to hold parts firmly in place without over-restraining.
- Incorporate heat sinks into fixtures to manage heat dissipation.
- Employ tack welding or sequential welding to maintain alignment during the process.
Preheating and Cooling Rates
The thermal cycle of preheating and cooling has a significant impact on the extent of distortion and warpage in laser welding.
- Preheating: Raising the temperature of the workpiece before welding reduces thermal gradients, as the material expands more uniformly.
- Controlled Cooling: Managing the cooling rate prevents abrupt contractions that lead to residual stresses and warpages.
Key Considerations:
- Preheating is particularly beneficial for materials with high thermal expansion coefficients, such as aluminum or high-carbon steels.
- Overheating can increase the HAZ and introduce unwanted metallurgical changes.
- Uncontrolled cooling can exacerbate stress concentrations and increase distortion.
Mitigation Strategies:
- Preheat the entire workpiece uniformly using ovens or induction heating to reduce temperature differences.
- Control cooling rates with post-weld heat treatments or slow cooling methods.
- Monitor temperatures during preheating and cooling with thermocouples or infrared sensors to ensure consistency.
Minimizing distortion and warpage in laser welding requires careful attention to the factors influencing heat input, material behavior, joint design, and thermal management. By optimizing these parameters and incorporating effective clamping and preheating techniques, manufacturers can significantly reduce distortion risks, ensuring higher weld quality and dimensional accuracy.
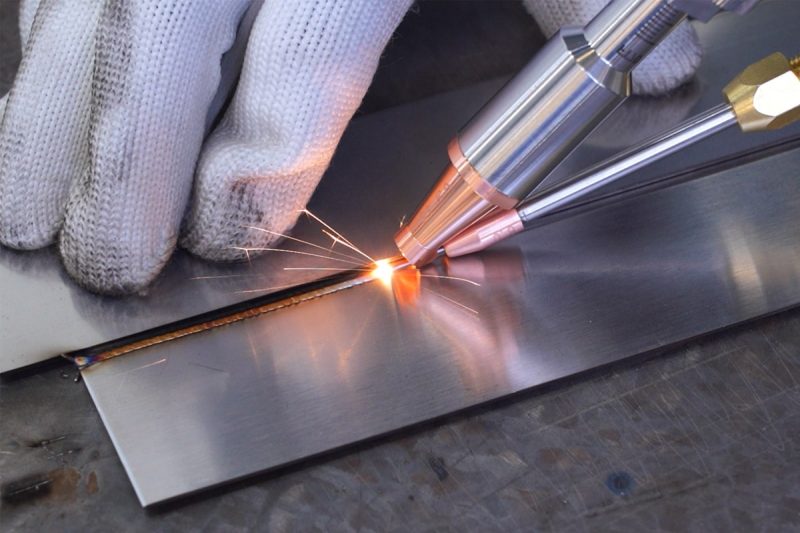
Methods to Minimize Distortion and Warpage in Laser Welding
Minimizing distortion and warpage in laser welding requires a strategic approach that addresses heat management, joint design, material preparation, and welding techniques.
Optimizing Welding Parameters
Proper adjustment of welding parameters is essential to control heat input, minimize thermal gradients, and reduce distortion.
- Adjusting Laser Power: High laser power can lead to excessive heat input and larger heat-affected zones (HAZ). Optimize laser power to achieve sufficient penetration while minimizing unnecessary heating.
- Controlling Welding Speed: Slow welding speeds increase heat input, leading to greater distortion. Faster speeds reduce thermal gradients, but care must be taken to ensure complete fusion.
- Using Pulse vs. Continuous Wave Lasers: Pulsed lasers allow for intermittent heat delivery, reducing overall heat input and minimizing distortion. Continuous-wave lasers are better suited for high-speed applications but may require additional cooling strategies.
Practical Tips:
- Use trial runs to identify optimal power and speed settings for specific materials.
- Employ thermal imaging to monitor heat distribution during welding.
- Combine lower power with pulsed laser modes for thin or distortion-prone materials.
Joint Design Considerations
The design and preparation of weld joints significantly influence heat distribution and stress concentrations.
- Choosing the Right Joint Type: Symmetrical joints, such as butt joints, help distribute heat evenly and reduce distortion. Lap joints and corner joints, while necessary for certain applications, require careful handling to manage stress.
- Edge Preparation: Proper edge preparation, such as beveling or machining, ensures tight fit-ups and consistent heat application, reducing the risk of uneven heating and warpage.
Practical Tips:
- Use joint designs that promote uniform heat flow.
- Minimize joint gaps through precise machining.
- Consider using filler materials selectively to bridge gaps and improve weld quality.
Material Selection and Preparation
Selecting appropriate materials and ensuring their readiness for welding can greatly reduce distortion.
- Material Compatibility: Use materials with lower coefficients of thermal expansion (CTE) or high thermal conductivity to minimize thermal stresses.
- Surface Cleanliness: Contaminants like oils, oxides, or dirt affect heat absorption and cause uneven heating. Clean surfaces ensure better weld consistency and reduce distortion.
Practical Tips:
- Match base materials and fillers for similar thermal and mechanical properties.
- Use chemical or mechanical cleaning methods to prepare surfaces.
- Preheat materials with high thermal expansion to reduce thermal gradients.
Use of Fixtures and Clamping
Proper fixturing and clamping techniques prevent movement during welding and manage heat dissipation effectively.
- Proper Clamping Techniques: Securely hold the workpiece in place to prevent distortion but avoid over-restraining, which can cause residual stresses.
- Use of Backing Bars and Heat Sinks: Backing bars support the weld area and reduce distortion by stabilizing the material, while heat sinks dissipate excess heat to control thermal gradients.
Practical Tips:
- Design custom fixtures to suit specific workpiece geometries.
- Incorporate adjustable clamps for flexibility without compromising support.
- Use materials with high thermal conductivity for backing bars or heat sinks to manage heat dissipation.
Preheating and Post-Weld Heat Treatment
Thermal management before and after welding significantly reduces residual stresses and distortion.
- Controlled Preheating: Preheating the workpiece reduces thermal gradients, particularly for materials like aluminum and high-carbon steel.
- Post-Weld Heat Treatment: Gradual cooling or stress-relief annealing after welding reduces residual stresses and stabilizes the material.
Practical Tips:
- Preheat workpieces uniformly using ovens, torches, or induction heaters.
- Control cooling rates with insulating blankets or heat treatments to prevent abrupt contractions.
- Monitor temperatures using thermocouples for consistent thermal management.
Welding Sequence Planning
Strategic planning of the welding sequence helps distribute heat evenly and manage stress buildup.
- Balanced Welding: Alternating welds on opposite sides of the workpiece balances heat input and minimize warpage.
- Skip Welding Techniques: Weld intermittent sections, allowing cooling between welds to prevent excessive heat accumulation in any one area.
Practical Tips:
- Divide large welds into smaller sections to allow intermediate cooling.
- Begin welding in low-stress areas and gradually move to high-stress regions.
- Use software tools to simulate stress distribution and optimize welding sequences.
Employing Advanced Techniques
Innovative welding technologies offer advanced solutions to minimize distortion and warpage.
- Hybrid Laser Welding: Combines laser welding with other techniques like arc welding to improve heat distribution and reduce distortion.
- Adaptive Laser Welding: Uses sensors and feedback systems to adjust welding parameters in real time based on material and process conditions.
- Real-Time Monitoring and Control: Incorporates thermal imaging, laser power feedback, and deformation sensors to maintain optimal welding conditions.
Practical Tips:
- Invest in hybrid systems for complex or high-tolerance applications.
- Use real-time monitoring systems to detect and correct deviations instantly.
- Implement closed-loop control systems to maintain consistent welding parameters.
By implementing these methods, manufacturers can effectively minimize distortion and warpage in laser welding processes. Optimizing welding parameters, designing appropriate joints, preparing materials, using proper fixtures, managing thermal cycles, and leveraging advanced technologies all contribute to achieving high-quality, distortion-free welds. These strategies not only enhance the dimensional accuracy of welded components but also improve production efficiency and reduce material waste, ensuring reliable and cost-effective manufacturing outcomes.
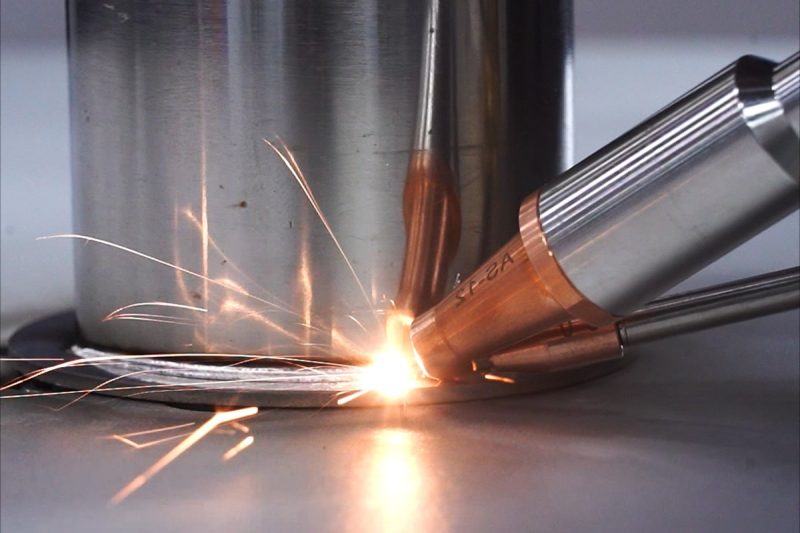
Summary
Minimizing distortion and warpage in laser welding is critical to achieving high-quality welds and maintaining the structural integrity of components. Distortion arises from uneven heating and cooling, leading to residual stresses that deform the material. By addressing key factors such as heat input, material properties, joint design, and thermal management, manufacturers can effectively mitigate these challenges.
Optimizing welding parameters, including laser power, speed, and the use of pulsed or continuous wave lasers, is essential to control heat input. Proper joint design, material selection, and surface preparation further enhance weld quality by ensuring uniform heat distribution and reducing thermal stresses. Effective clamping, the use of backing bars and heat sinks, and strategic preheating and post-weld heat treatments also play pivotal roles. Advanced techniques like hybrid laser welding, real-time monitoring, and adaptive control systems provide additional tools to minimize distortion.
By integrating these strategies, manufacturers can produce distortion-free, precise, and reliable welds, enhancing efficiency and product performance.
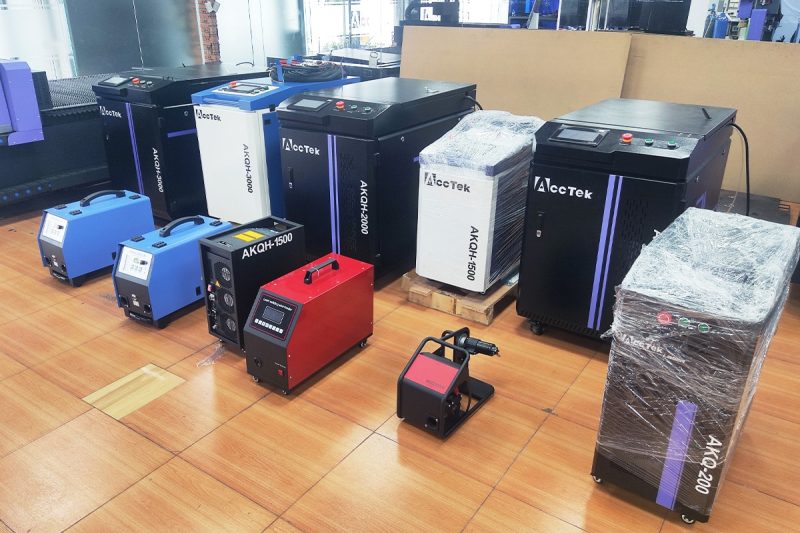
Get Laser Welding Solutions
At AccTek Laser, we understand the challenges manufacturers face in minimizing distortion and warpage during laser welding. As a professional manufacturer of laser cutting machines, laser welding machines, laser cleaning machines, and laser marking machines, we are committed to delivering cutting-edge solutions tailored to your needs. Our advanced laser welding machines are designed to ensure precise heat control, enabling distortion-free welding even in the most demanding applications.
With a range of customizable features, including optimized laser power settings, real-time monitoring systems, and adaptive welding technologies, AccTek Laser’s machines provide unmatched performance and reliability. Whether you’re working with delicate materials or complex geometries, our experts can guide you in selecting the best configuration for your specific requirements.
Partner with AccTek Laser to overcome welding challenges and enhance your production efficiency. Contact us today for comprehensive consultation, technical support, and access to industry-leading laser welding solutions. Let us help you achieve perfection in every weld.
Proper clamping and fixturing are essential to hold the workpiece in place and counteract the forces that distort welding.
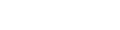
Contact information
- [email protected]
- [email protected]
- +86-19963414011
- No. 3 Zone A, Lunzhen Industrial Zone,Yucheng City , Shandong Province.
Get Laser Solutions