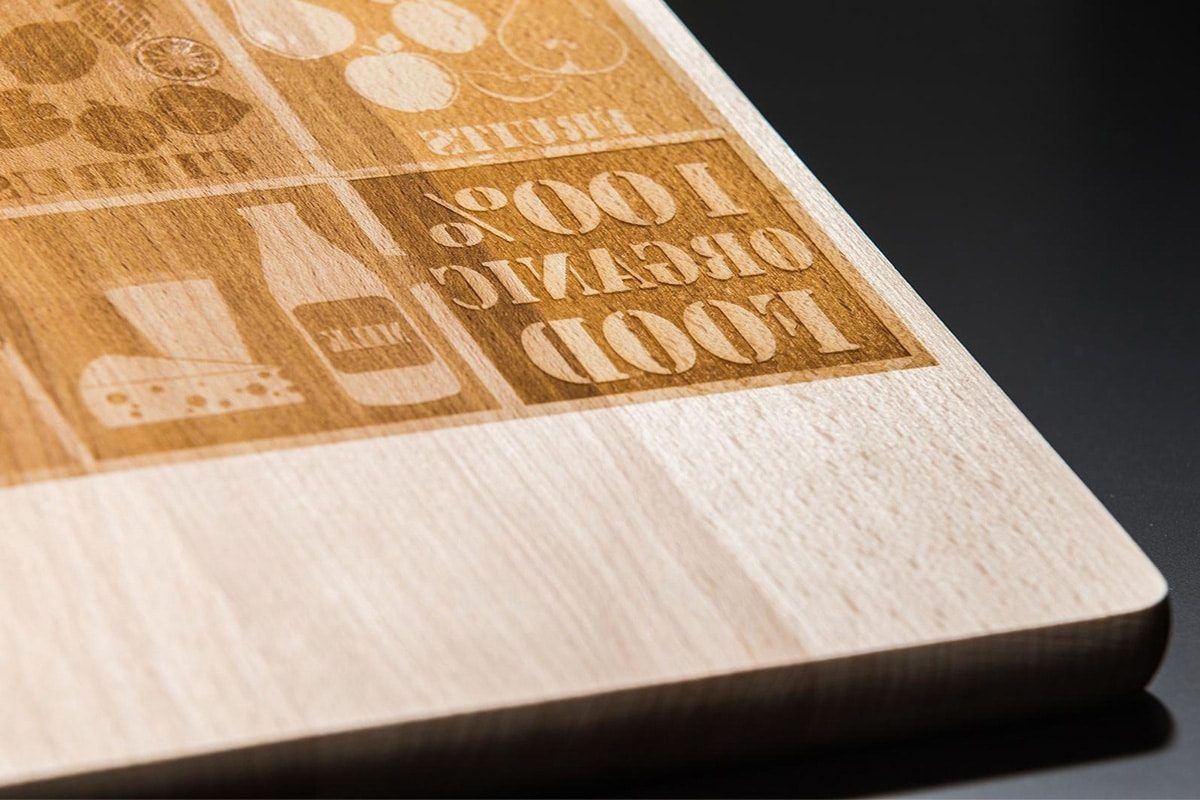
How to Remove Laser Markings
Laser marking technology is widely used in many industries due to its high precision and durability, from the numbering of electronic components to the identification of medical devices to the tracking codes of industrial parts. It can generate clear and durable marks on the surfaces of various materials such as metal, plastic, glass, etc., ensuring that the information can be preserved for a long time in harsh environments. However, in some special cases, it becomes necessary to remove these marks. For example, it is particularly important to remove marks when there are incorrect marks generated during the production process, old labels need to be replaced, or when the surface of the product is reprocessed.
Removing laser marks is not only about aesthetics but also about ensuring that the surface is not damaged. While shallow marks or annealed marks such as color changes are relatively easy to remove, deep engraved or etched marks are more challenging. The characteristics of each material and the depth of the mark determine the appropriate removal method, so these factors need to be carefully evaluated. This article will comprehensively analyze the durability of laser marks and the various situations in which they can be removed. It will provide you with detailed removal methods – including mechanical, chemical, and thermal treatments, and explain the safety and material protection considerations that need to be considered during the removal process. In addition, this article will summarize the best practices for laser mark removal to help you achieve mark removal in your operation efficiently and safely while maintaining surface finish.
Table of Contents
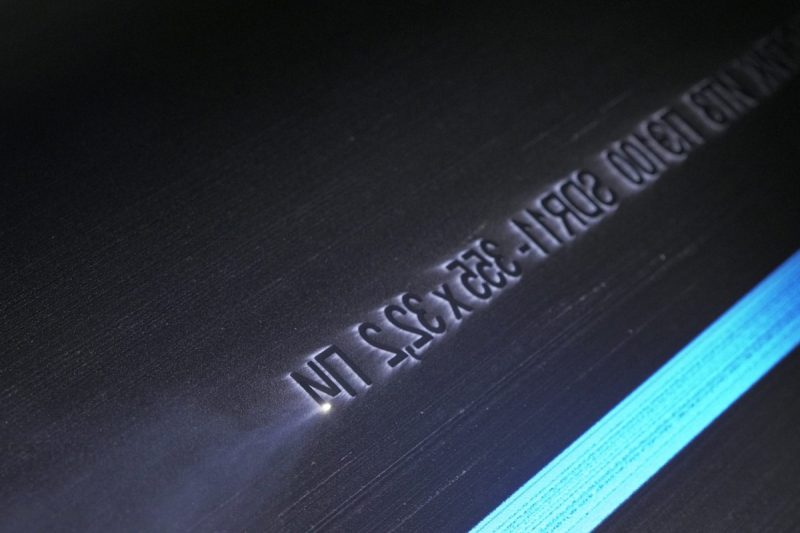
Learn About Laser Marking
Laser marking is a technology that uses high-energy lasers to create permanent marks on the surface of materials. It is non-contact, precise, and fast, and can achieve clear and durable markings on a variety of materials such as metals, plastics, glass, etc. Laser marking is widely used in industries such as electronics, medical, and automotive. It can not only improve product recognition but also ensure that information is visible in harsh environments. Different types of laser marking, such as engraving, etching, annealing, etc., are suitable for different materials and needs, making them popular in industrial production.
Laser Marking Process and Durability
Laser marking is a precision process that uses a high-energy laser beam to generate localized heating on the surface of a material, causing physical or chemical changes in the surface material to form a permanent mark with a specific color, texture, or bump. The principle of this process is to concentrate the laser energy in a very small area and induce oxidation, melting, or evaporation of the material through high temperature to achieve a specific marking effect. Laser marking is flexible and diverse, including engraving, etching, annealing, and foaming, each with different marking effects and durability. For example, engraving and etching remove the surface material and leave a groove or raised pattern, while annealing changes the surface color through heat without damaging the material itself.
Since laser marking machines do not need to contact the surface of the material during marking, the marking is very precise and can maintain good adhesion and clarity on many materials. Laser marking is highly durable, especially on metals and certain heat-resistant plastics. Even when exposed to extreme conditions such as wear, chemicals, moisture and high temperature, the marking remains clear and intact. Compared with traditional marking methods such as inkjet or printing, laser marking is not only more anti-counterfeiting, but also more wear-resistant and corrosion-resistant. Therefore, it is widely used in industries with demanding identification requirements, such as medical equipment, aerospace, electronic parts and automotive manufacturing, to ensure that information can be continuously tracked and identified throughout the product life cycle.
Types of Laser Marking
Laser marking technology can be divided into many types according to application requirements and material characteristics, each type achieves different marking effects through unique processes. The following are the main types of laser marking and their characteristics:
Engraving
Engraving is a deep marking method that uses a high-energy laser beam to remove the surface of the material, leaving a recessed pattern or text. The depth of the engraved mark can be adjusted according to the laser intensity and material thickness, and it is usually more wear-resistant and permanent. This method is suitable for hard materials such as metals, ceramics, and glass. It is widely used in industrial parts, tools, and accessories that require deep marking. Engraving can leave a clear touch on the surface of the material and is not easy to erase, making it very suitable for use in harsh environments.
Etching
Etching laser marking mainly uses laser energy to generate an oxide layer on the surface of the material or change the texture of the material surface to form marks. Unlike engraving, etching marks usually do not result in a noticeable loss of material, but rather a color change or subtle texture on the surface that creates a visual effect. Etching is suitable for metals and some plastic materials and is often used in electronic product casings, precision instruments, and other occasions that require high marking accuracy. Etched markings are particularly effective on smooth surfaces, without compromising structural strength and resisting wear and corrosion.
Annealing
Annealing is a laser marking method specifically for metal materials. This technology uses low-energy lasers to heat the surface of the material to generate a thin oxide film, which makes the marked area appear in different colors (such as black, dark gray, brown, etc.). This method does not remove the material itself but uses the color change of the material after heating and oxidation to form a mark, and the surface remains smooth and intact. Annealing marking is widely used for marking materials such as stainless steel and titanium due to its fine coloring effect, such as watches, medical devices, and accessories, which are both beautiful and durable.
Foaming
Foaming is a laser marking method that creates a bubble-like texture on the surface of non-metallic materials such as plastics. The laser heats the surface of the material, forming tiny bubbles that create a white or light-colored mark on the surface. Foaming marks have a bright color and high contrast, making them ideal for marking dark plastics such as keyboard keys and electronic product housings. Because the foaming mark is located on the surface of the material, it does not affect the structural strength of the substrate but provides good wear resistance and durability.
Each laser marking type has its unique application areas and advantages. Engraving is suitable for deep and durable marks, etching is suitable for high precision needs, annealing is suitable for metal surfaces that require subtle colors, and foaming is suitable for bright marks on non-metallic materials. Choosing the right laser marking type depends not only on the material but also on the durability, fineness, and desired effect of the mark.
Applicable Marking Materials
Laser marking technology is widely applicable and can achieve clear and durable marks on a variety of materials. Different materials absorb and react to lasers to different degrees, which determines the effect, depth and durability of the mark. The following are several commonly used laser marking materials and their characteristics:
Metal Materials
Metal is one of the main applications of laser marking. Common metal materials include stainless steel, carbon steel, aluminum, copper, and titanium. Metals absorb laser energy more, so they can form clear and lasting marks. For materials such as stainless steel and titanium, laser annealing can produce marks of different colors, while engraving and etching techniques can produce deep marks that are wear-resistant and corrosion-resistant. Metal laser marking is widely used in industries such as automotive manufacturing, aerospace, electronic components, and medical devices to ensure that the information on key components can be maintained for a long time in extreme environments.
Plastic Material
Laser marking is also widely used on plastics. Commonly used materials include ABS, polycarbonate (PC), polypropylene (PP), etc. Plastics are sensitive to laser energy. By adjusting the laser wavelength and energy intensity, a contrasting mark can be generated on the plastic surface. For dark plastics, foaming marking can form light-colored marks, while etching marking is suitable for fine marking of light-colored plastics. Plastic laser marking is commonly used for marking the housings of consumer electronics, automotive interior trims, and medical devices.
Glass
Laser marking can form permanent and visually appealing marks on glass surfaces. The high hardness and transparency of glass place high demands on the laser wavelength and pulsed lasers are usually used to avoid glass cracks. By properly adjusting the laser parameters, a fine etching effect can be formed on the glass, which is often used for marking containers such as wine bottles and medicine bottles, as well as decorative patterns and QR code markings. The advantage of glass marking is that it does not change the surface smoothness, which is suitable for applications that require visual clarity but do not affect the touch.
Ceramics
Ceramic is a material with high hardness that can withstand high-energy lasers. Through laser etching or engraving, clear patterns or text can be generated on the ceramic surface. Ceramic marking is suitable for high-temperature and chemical corrosion environments, so it is often used to identify industrial parts and laboratory equipment. The ceramic mark after marking has extremely high durability and can maintain the marking effect for a long time in harsh environments.
Other Materials
Laser marking is also suitable for organic materials such as wood, leather, and fiber fabrics. Wood will produce carbonization during laser marking, forming dark marks, which are suitable for the personalized design of signs and crafts. Flexible materials such as leather and fabrics can generate clear patterns without damaging the fibers through low-energy laser marking, which is widely used in the customized processing of leather goods and clothing.
Different materials have a great influence on the effect of laser marking. It is necessary to select the appropriate marking type and laser parameters according to the material characteristics to ensure the best marking effect and durability. The applicability of laser marking on various materials makes it an ideal choice for marking in many industries, taking into account durability, aesthetics, and fineness.
Factors Affecting Laser Marking Permanence
The durability of laser marking is affected by many factors, including material type, marking depth, marking method, and subsequent use and processing environment. These factors directly determine the mark’s wear resistance, corrosion resistance, and retention under extreme conditions. The following is a detailed analysis of these key factors:
Material Type
The durability of laser marking depends largely on the properties of the material. Different materials have different absorption and reaction capabilities to lasers, resulting in different marking depths and effects. For example, metal (such as stainless steel, and aluminum) markings usually have high wear resistance and durability and can maintain the integrity of the marking in extreme temperatures or corrosive environments. On the other hand, markings on non-metallic materials such as plastics and glass are relatively more fragile and are more affected by physical wear or chemicals. Therefore, the selection of marking materials is particularly critical when used in environments with high confrontation requirements.
Marking Depth
The depth of the laser mark has a direct impact on its durability. Deeply engraved marks can penetrate the surface of the material, are more resistant to scratches and abrasion, are generally more difficult to remove, and can maintain the clarity of the mark even in heavy wear environments. In contrast, shallow marking (such as annealing marking) mainly forms an oxide layer or slight color change on the surface of the material. Although the visual effect is good, it is easily subject to physical wear or external force because the mark does not penetrate deep into the material. Therefore, deep marking has a more durable effect under harsh environmental conditions and long-term use.
Marking Method
The laser marking method will also affect the durability of the mark, and different methods are suitable for different application scenarios. Engraving and etching marks are usually formed by removing materials or changing the material structure. They have extremely high wear resistance and are suitable for parts that need to be used for a long time. Although annealing marks have good visual effects, the oxide film formed on the metal surface is relatively fragile. It is suitable for surfaces that require high aesthetics but are not susceptible to frequent physical contact. In addition, foaming marks are mainly used on plastic surfaces and are usually not resistant to high temperatures or chemical erosion, so they are not suitable for applications that require high durability.
Subsequent Processing and Use Environment
Subsequent processing and the use environment will further affect the durability of the mark. For example, marks that are frequently exposed to chemicals are susceptible to corrosion, and marks that are exposed to high temperatures, high humidity, or strong acid and alkali environments for a long time may also fade or become damaged. To ensure the long-term durability of the mark, in some cases, surface treatments such as coating protection or surface encapsulation can be added to improve the wear and corrosion resistance of the mark. In addition, the marking of outdoor equipment needs to consider the impact of sunlight and ultraviolet rays, and it is crucial to choose the right materials and marking methods.
In summary, the durability of laser marking is not fixed but is affected by multiple factors. According to different marking requirements and environmental conditions, the reasonable selection of materials and marking methods, as well as the appropriate depth and post-processing methods can maximize the durability of the marking and ensure that the marking is still clearly visible under harsh conditions.
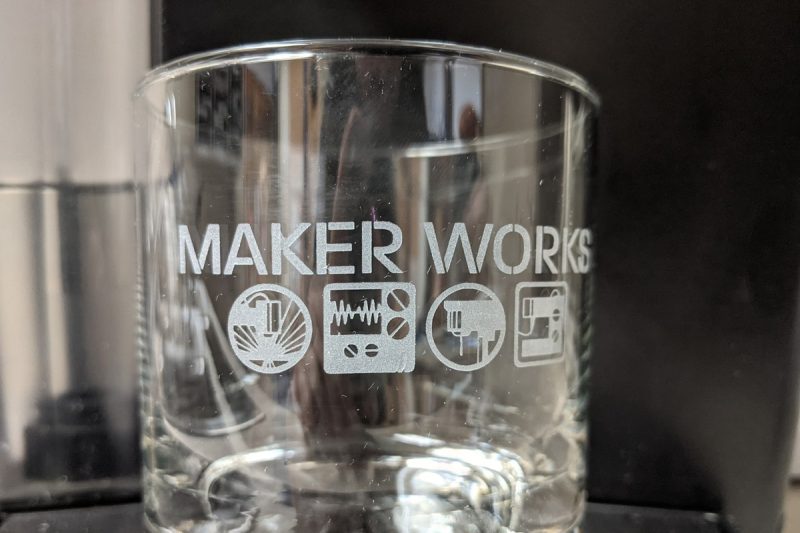
Can Laser Markings Be Removed?
The removability of laser marking is a relatively complex topic that is affected by many factors. Although laser markings are generally highly durable and long-lasting, there are situations where laser marking removal becomes necessary, such as reprocessing, product recycling, or replacement of markings. Whether a mark can be removed depends on many aspects, such as the type of mark, its depth, the material used, and the choice of removal method.
Laser Marking Permanence and Removability
The durability of laser marking depends mainly on the working principle of the laser and how it reacts to the material. For example, engraving and etching-type marks usually penetrate deep into the surface of the material, forming a relatively strong mark, which makes them difficult to remove. In contrast, annealing or foaming-type marks are usually formed by producing an oxide layer or bubble-like effect on the surface, which is shallower and relatively easier to remove. However, even deep marks can be removed under the right conditions, but it takes more time and appropriate technical means.
Factors Affecting Laser Marking Removability
The difficulty of laser marking removal is mainly affected by the following factors:
- Marking Type: Engraving and foaming marks are deep and difficult to remove because they change the surface structure of the material. Annealing and superficial etching marks are shallow and easier to remove.
- Material Type: Marks on soft materials (such as plastics) are easy to remove, while marks on hard materials (such as steel) are difficult to remove, especially deep marks.
- Marking Depth: The deeper the mark, the more difficult it is to remove; shallow marks are relatively simple to remove.
- Surface Finish Requirements: The removal process may leave scratches or abrasions, which may be more challenging for surfaces that require a high finish.
Types of Laser Markings That Can and Cannot Be Removed
Although laser markings can be removed in theory, there are some challenges in practice. The removal process, especially for deep marks, is often difficult to do without affecting the integrity of the substrate, which may cause surface damage or unevenness. In addition, removing laser marks usually requires special equipment and techniques, and the method needs to be adjusted according to the characteristics of the material. For example, engraved marks on metal surfaces may require stronger chemical or mechanical methods, while plastic or glass surfaces may use milder laser ablation or chemical solvents.
The removability of a mark depends on the mark type, material, and process. Shallow marks, such as annealed marks and foamed marks, are easier to remove, while deep engraved or etched marks are more challenging. Some metal or glass marks may not be able to restore the original surface after removal, and may even cause permanent damage. Therefore, when choosing laser marking, the feasibility and cost of post-processing must be considered to ensure that the mark meets the requirements of use and subsequent removal is feasible.
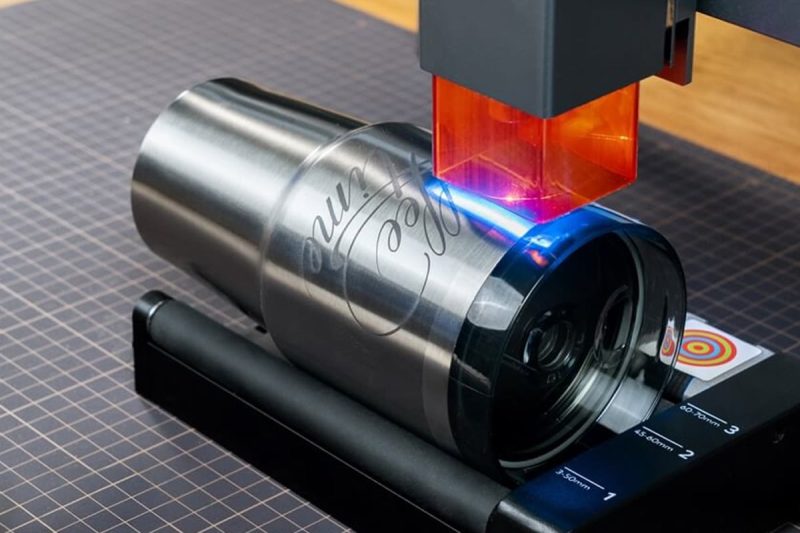
Methods for Removing Laser Markings
Laser mark removal involves a variety of methods, including mechanical, chemical, thermal, and specialized techniques. Different methods are suitable for different mark types, materials, and mark depths. The following is a detailed introduction to common laser mark removal methods:
Mechanical Methods
Mechanical methods are usually suitable for cases where the surface marking is light, and the marking is removed by physical means, but it may cause slight damage to the substrate surface. Common mechanical removal methods include:
- Grinding is the gradual removal of superficial laser marks by rubbing the surface of the material with sandpaper or a grinding wheel. It is suitable for situations where the surface marks are shallow or small. Although grinding can effectively remove the marks, it may leave fine scratches and requires special care to avoid affecting the appearance of the material.
- Sanding is the processing of the metal surface using a polisher or grinder to remove the laser mark. This method is suitable for metal materials, especially when the marks are shallow. The polishing process removes a layer of metal surface, which can effectively remove the marks, but it may also cause micro-damage to the substrate, especially for materials with high surface requirements.
- Polishing is a fine grinding method suitable for removing slight laser marks, especially on metal and plastic surfaces. Through meticulous polishing, shallow marks can be removed and the surface gloss can be restored. Although polishing can effectively remove marks, if it is not done properly, it may cause tiny surface scratches and affect the surface quality.
Chemical Methods
Removing laser markings by chemical reaction is suitable for situations where mechanical damage to the substrate is undesirable. Common chemical removal methods include:
- Solvents and cleaners can be used to remove light laser markings, especially for plastics, films, or certain soft materials. By using specific solvents, the surface material at the mark can be dissolved, thus removing the laser mark. Since the chemical reaction is mild, no significant damage to the substrate is caused.
- Etching agents dissolve the surface of the material through chemical reactions, removing the laser mark. It is suitable for surface removal of materials such as metals and ceramics, and usually requires the selection of suitable chemicals to ensure that the substrate is not damaged. The reaction time and temperature should be carefully controlled during the etching process to avoid excessive corrosion of the material or changing its properties.
Thermal Method
Thermal methods mainly use heat energy to process laser markings. It is suitable for metals and some special materials and can remove deeper marks or change the surface appearance. Common thermal removal methods include:
- Laser ablation removes laser marks by heating the marked surface with another laser. This method uses a different laser wavelength and power than the laser used to mark the original mark to ensure that no new damage is caused to the substrate during the removal process. The advantage of laser ablation is that it can remove marks very accurately, but special care must be taken to control the heating temperature and duration to avoid excessive damage to the surface.
- Heat treatment is to change the surface state of the metal by heating it, thereby covering or removing the laser mark. A common method is to heat the metal surface at a high temperature to cause an oxidation reaction, change the color, and cover the mark. This method is suitable for some metal surfaces and can effectively remove or cover the mark, especially to improve the surface appearance without affecting the material properties.
Specialized Methods
In addition to conventional mechanical, chemical, and thermal methods, there are also specialized removal methods that are highly effective in removing laser marks and are suitable for specific materials and marking situations.
- Plasma cleaning uses plasma to clean surfaces and can remove minor laser marks. This method is suitable for shallow marks on the surface, especially on plastic, metal, or ceramic materials. Plasma cleaning can effectively remove organic matter, but it is necessary to ensure that the energy and time during the process do not damage the substrate.
- Ultrasonic cleaning uses high-frequency vibration to hit the tiny bubbles of liquid medium onto the surface of the object, thereby removing the laser mark. Ultrasonic cleaning is suitable for smaller parts, especially materials with high surface finish requirements. This method is effective for fine markings, but it also requires precise control to avoid damage to the material surface due to excessive vibration.
There are many different methods for removing laser marks, suitable for different materials, mark types, and mark depths. Mechanical methods are suitable for removing superficial marks, chemical methods can gently remove minor marks, and thermal methods and specialized technologies such as laser ablation and plasma cleaning are suitable for more complex mark removal. When choosing a removal method, it is necessary to select the most appropriate treatment method based on the characteristics of the material, the depth of the mark, and the subsequent surface requirements.
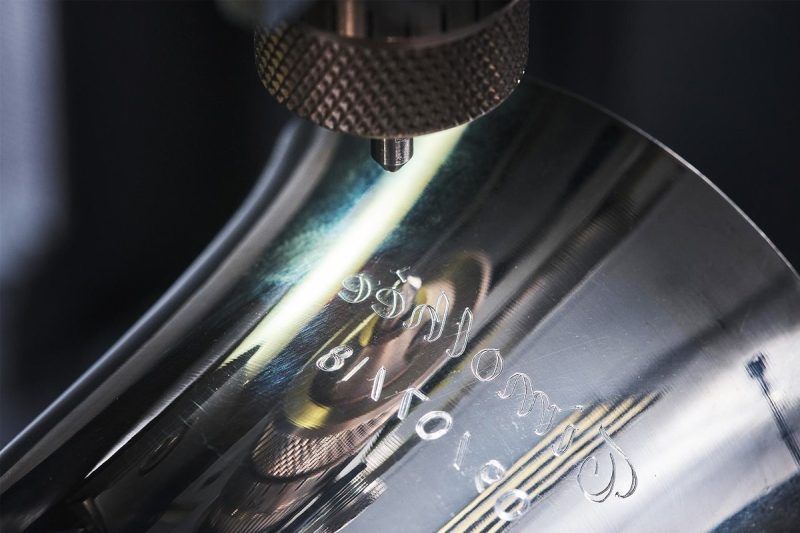
Precautions When Removing Laser Markings
Laser marking removal is not just a simple physical or chemical process, but a complex operation that requires consideration of multiple factors. To ensure the removal effect and protect the integrity of the material, the following are the main considerations when removing laser markings:
Type of Material Being Marked
Different materials respond differently to the methods used to remove laser marks, so choosing the right removal technology is critical.
- Laser markings are relatively easy to remove from soft materials such as plastics, rubber, and films. Soft materials are usually shallow and can be removed by mechanical grinding, solvent cleaning, or mild chemical reactions. These materials are not susceptible to excessive wear, so gentler removal methods can be used.
- Hard materials such as steel, aluminum, and ceramics are relatively difficult to remove, especially deep engraved marks. When working with these materials, overly aggressive removal methods (such as excessive grinding or strong chemical reactions) should be avoided to prevent damage to the substrate surface. For metal materials, more precise removal methods such as laser ablation, fine polishing, or plasma cleaning are often used to ensure that the properties of the substrate are not affected.
- Glass markings require special care when removing because glass is inherently fragile and any excessive mechanical or thermal treatment may cause cracking. Common methods are ultrasonic cleaning and laser ablation, which remove the mark in a gentle way without damaging the substrate.
Depth and Type of Laser Marking
The depth and type of laser mark are key factors affecting removal effectiveness. Deep marks are generally more difficult to remove than shallow marks, especially when engraved or etched.
- Annealing marks, foaming marks, or slight etching marks are usually easier to remove. These marks generally do not penetrate deep into the material and the surface reaction is relatively mild, so milder removal methods such as polishing, chemical cleaning, or ultrasonic cleaning can usually effectively remove them.
- Deep engraved or etched marks are more difficult to remove. Deep marks usually involve the removal of a large area of material on the surface of the material, and more care must be taken during removal to avoid damaging the substrate. More precise equipment such as laser ablation, mechanical grinding, and strong chemical solvents may be required. These methods require precise control of force and time to avoid over-removal, resulting in rough or deformed surfaces.
- Different types of marks (such as engraving, etching, and annealing) will have different effects during the removal process. Engraved marks are usually deep and require a large area of material to be removed; while annealed marks are usually shallow and relatively easy to remove. Understanding the type of mark can help choose the appropriate removal technology and avoid unnecessary operational complexity.
Surface Finish After Removal
The finish of the target surface is critical to the selection and effectiveness of the removal process. Many removal methods, especially mechanical methods, may affect the surface to varying degrees.
- When removing laser marks from materials that require an extremely high finish (such as pearlescent, mirror-like metals or plastics), special care must be taken. For example, polishing and grinding methods may leave fine scratches or damage that affect the appearance of the material. Therefore, when removing laser marks, it is important to ensure that the removal method selected has the least impact on the surface, and it is best to choose a gentler technique (such as chemical cleaning, ultrasonic cleaning, etc.).
- When removing deeply engraved marks, if the operation is not done properly, it may result in an uneven or uneven surface. This will not only affect the removal effect, but may also have an adverse effect on subsequent machining, spraying or other surface treatments. Therefore, excessive grinding or scratching should be avoided during the removal process to maintain the smoothness of the surface.
- In some cases, it may be necessary to sacrifice a portion of the surface finish in order to remove the mark. This usually occurs when removing deep engravings or more stubborn etched marks. In this case, it is necessary to evaluate the importance of the finish to the end use effect and adopt an appropriate balance strategy.
Environmental and Safety Considerations
When removing laser markings, environmental and safety factors cannot be ignored. Different removal methods may involve harmful chemicals, temperature changes, noise, etc., and relevant safety regulations need to be followed.
- When using chemical solvents or etchants, you must ensure that the environment is well-ventilated and wear appropriate personal protective equipment (such as gloves, goggles, etc.). Some chemicals may be corrosive or irritating. When using them, you should strictly follow the operating instructions to avoid contact with skin or eyes.
- During mechanical grinding and polishing, flying chips or dust may be generated, which may cause damage to operators or equipment. Wear dust masks and goggles during operation and take appropriate protective measures to avoid scratches or eye injuries.
- During laser ablation, due to high temperatures, heat radiation or sparks may be generated. Fire prevention measures need to be taken and ensure that the operating environment is suitable. In addition, when using laser equipment, laser safety standards must be followed to avoid direct exposure to the laser beam.
When removing laser markings, in addition to choosing the appropriate removal method, you also need to consider many factors, such as material type, marking depth, surface finish, and safety protection during operation. Each removal method has its advantages and disadvantages. Understanding these considerations can help choose the best removal strategy to ensure removal results while maximizing material integrity and surface quality.
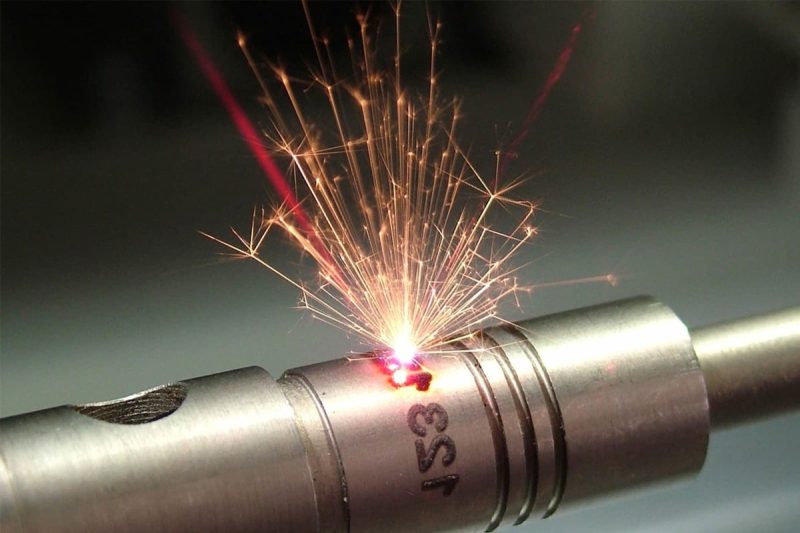
Best Methods for Laser Marking Removal
When removing laser markings, ensuring that the substrate is not damaged and the best results are achieved requires a comprehensive consideration of methods, equipment, and subsequent processing. The following are suggestions on how to effectively remove laser markings:
Avoid Substrate Damage
Laser marking removal can cause damage to the substrate, especially in the case of hard materials and deep markings. To ensure substrate integrity during the removal process, here are some effective precautions:
- When using grinding, polishing, or other physical removal methods, it is recommended to test from low intensity to gradually increase the intensity to gradually find the most appropriate removal intensity. This can avoid excessive wear or uneven surface damage to the substrate. Especially for more fragile materials such as metals and plastics, avoid using too rough grinding tools or too high pressure.
- For soft materials such as plastics, rubbers or films, solvent cleaning or low-abrasion methods are usually more effective. Appropriate chemical solvents (such as solvent-based cleaners) can be selected to dissolve the laser mark without damaging the surface of the substrate. Solvent cleaning methods have less impact on the material surface and are therefore more suitable for soft materials.
- When choosing a mechanical removal method, fine-grained sandpaper, soft cloth or low-abrasion polishing materials can be used to remove the mark while maintaining the integrity of the material surface to the greatest extent. This is especially suitable for materials that require a high surface finish.
Use Proper Equipment and Safety Precautions
During the laser marking removal process, it is very important to use appropriate equipment and take necessary safety precautions to ensure a safe operating environment and effectively avoid potential damage to the human body and equipment.
- Specialized equipment, such as laser cleaning machines, ultrasonic cleaning equipment, etc., can provide efficient and accurate mark removal. With specialized equipment, the force and temperature during the removal process can be precisely controlled to ensure that the substrate is not overly damaged. Specialized equipment can also improve removal efficiency and reduce manual operation errors.
- When performing laser mark removal, appropriate personal protective equipment, such as protective glasses, gloves, masks, etc., should be worn, especially when mechanical or chemical removal is performed. Laser protective glasses should be worn during laser operation to avoid direct exposure to the laser beam. In addition, chemical-resistant gloves and goggles should be used during chemical cleaning to prevent chemical agents from damaging the skin or eyes.
- When using chemicals (such as cleaning solvents or etchants), it is necessary to ensure that the operating environment is well-ventilated to avoid the accumulation of toxic gases or vapors. When operating in an enclosed space, an exhaust system or local ventilation equipment should be used to ensure that there is no risk to the health of the operator during the cleaning process.
Surface Treatment After Removal
After laser marking is removed, some minor damage or loss of finish may occur on the material surface. Appropriate post-processing is required to restore the appearance and functionality of the material.
- After laser marking is removed, especially when mechanical methods are used, the surface may be left with fine scratches or wear marks. To restore the finish and beauty, the surface can be further polished. Through fine polishing, these marks can be effectively removed and the surface smoothness can be restored to improve the appearance.
- Passivation can effectively enhance the corrosion resistance and durability of metal surfaces, which is especially important for materials such as stainless steel. After the mark is removed, passivation treatment can not only improve the surface’s antioxidant capacity but also prevent the metal layer that may be exposed during the removal process from being affected by the external environment, thereby extending the service life of the material.
- For some materials, after laser marking is removed, a protective layer or film can be considered to be applied to further improve the surface wear resistance, corrosion resistance, etc. Especially on materials that are susceptible to environmental influences (such as metals, plastics, etc.), the use of protective coatings can effectively avoid scratches or wear on the surface during later use, maintaining the long-term beauty and performance of the material.
When removing laser markings, it is critical to choose the right methods, equipment, and techniques. By gradually testing the strength of the removal, using specialized equipment, safety precautions, and post-removal surface treatment, you can ensure that the removal is both efficient and does not damage the substrate. During the treatment process, especially on materials that require a fine surface finish, special attention should be paid to the meticulousness of the operation to maintain the integrity and functionality of the material.
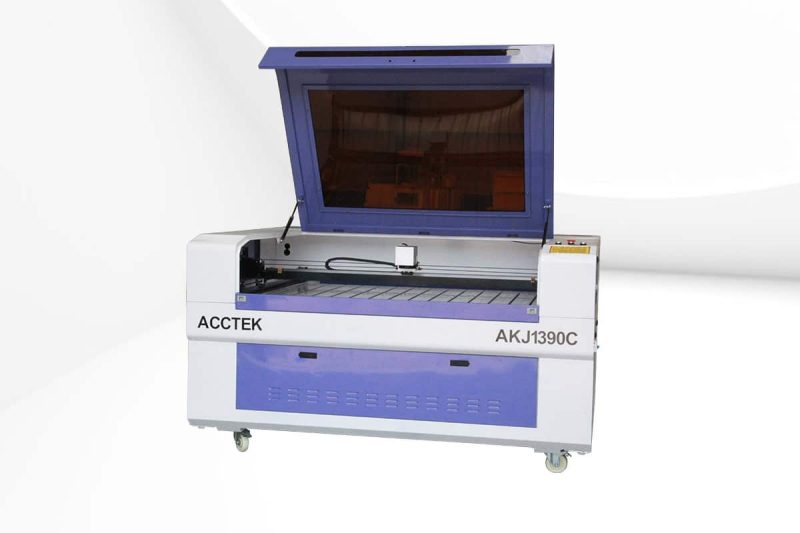
Summarize
Laser mark removal is a complex process that requires a comprehensive consideration of the depth of the mark, the type of material, the surface finish required, and the equipment and methods used. Different types of laser marks, such as engraving, foaming, annealing, or superficial etching, have a great impact on the ease of removal. Deep marks are generally more challenging and require precision mechanical, chemical, or laser ablation methods to handle. The hardness and surface characteristics of the material will also determine the choice of removal method. For example, for soft materials, solvents or low-abrasion methods may be selected, while hard materials may require more stringent physical or chemical removal methods. Selecting the right removal method is critical to ensuring removal results and material surface integrity.
In addition, during the laser marking removal process, operational safety and precise control of the equipment are equally important. The use of professional cleaning equipment, reasonable safety protection measures, and a well-ventilated environment can effectively reduce risks in operation and ensure the quality of the marking after removal. During the removal process, especially for materials with high surface requirements, polishing or other surface treatment may be required to restore the smoothness and durability of the material. Overall, although laser marking removal is feasible, to achieve the best results, it is necessary to carefully select methods, equipment, and operating strategies, and flexibly adjust them according to different situations to ensure that the removal process is both efficient and does not damage the material.
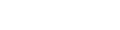
Contact information
- [email protected]
- [email protected]
- +86-19963414011
- No. 3 Zone A, Lunzhen Industrial Zone,Yucheng City , Shandong Province.
Get Laser Solutions