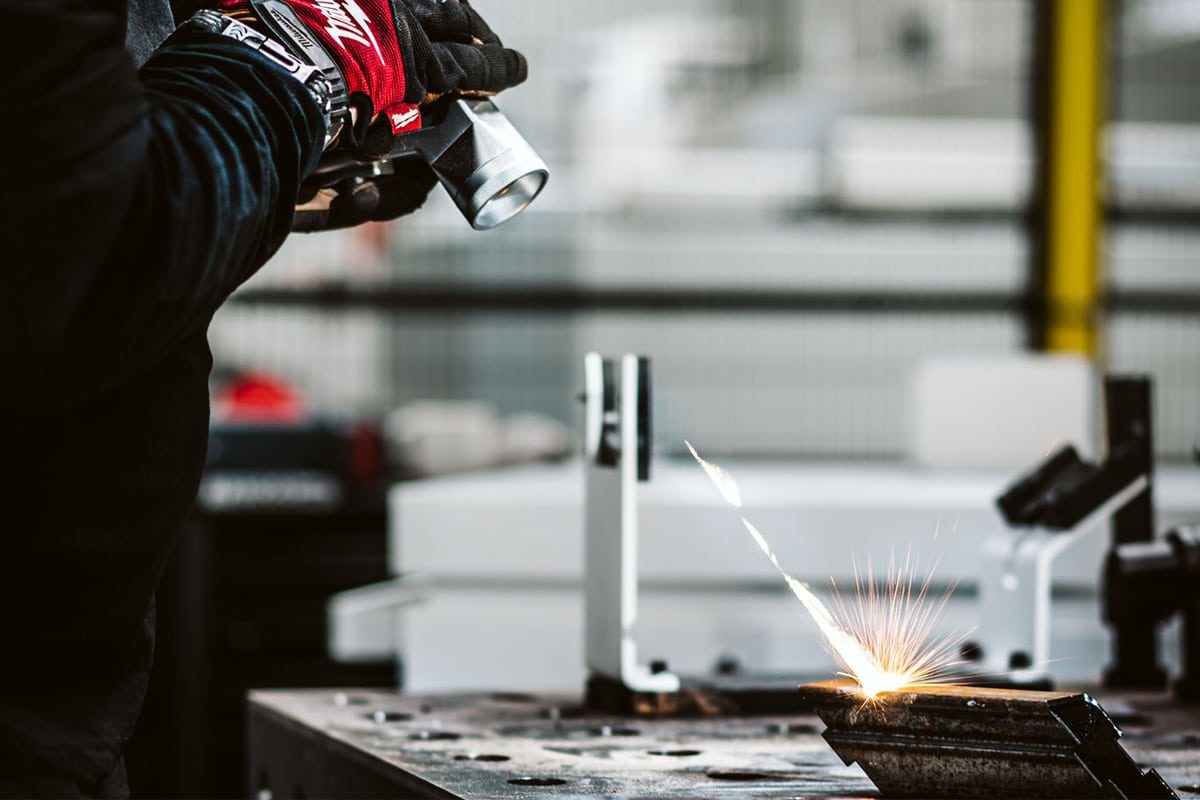
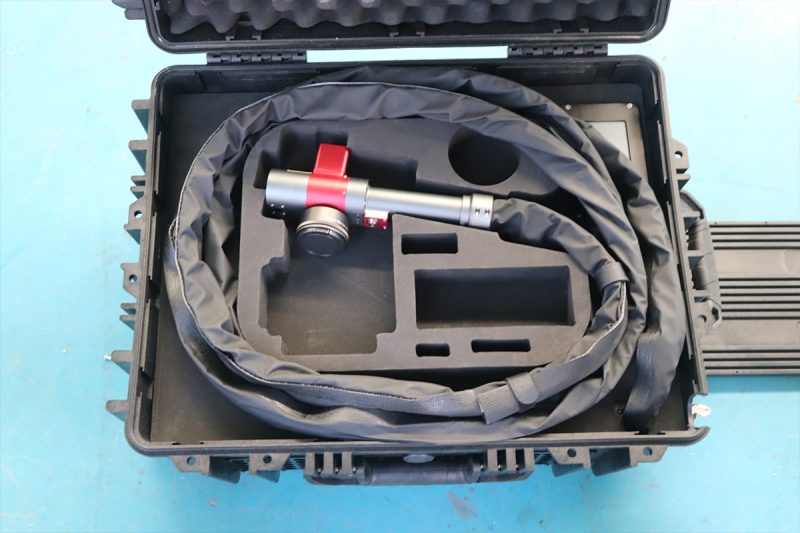
Understanding Rust and Paint Removal
What Is Rust?
Why Are Rust and Paint Removal Important?
Structural Integrity
Aesthetic Appeal
Functional Efficiency
Safety Compliance
Longevity
Traditional Methods of Rust and Paint Removal
Mechanical Methods
Mechanical methods involve physically removing rust or paint using abrasive force. Common techniques include:
- Sandblasting: Uses high-pressure air to blast abrasive materials (like sand or grit) onto the surface, stripping away rust and paint.
- Grinding and Scraping: Involves using wire brushes, scrapers, or grinders to manually remove contaminants.
Drawbacks:
- Surface Damage: The abrasive nature of these methods can scratch or erode the base material.
- Health Risks: These processes generate dust and debris that can be harmful if inhaled.
- Labor-Intensive: Mechanical removal is time-consuming, especially for large surfaces or intricate parts.
Chemical Methods
Chemical stripping uses solvents or acidic solutions to dissolve rust and paint. These chemicals are applied to the surface and left to act before being wiped or washed away.
- Benefits: Can penetrate complex geometries and hard-to-reach areas.
Drawbacks:
- Environmental Impact: Many chemical strippers contain toxic substances that pose environmental hazards.
- Health Risks: Exposure to these chemicals can cause skin irritation, respiratory problems, and other health issues.
- Material Compatibility: Some chemicals may react with certain metals, causing damage.
Thermal Methods
Thermal methods involve applying heat to loosen or burn off rust and paint.
- Heat Guns and Torches: Used to soften paint, making it easier to scrape away.
- Plasma Cleaning: A more advanced method that uses plasma arcs to remove contaminants.
Drawbacks:
- Risk of Warping: Prolonged or excessive heat can distort or weaken metal substrates.
- Fire Hazards: Working with open flames or high heat increases the risk of fire.
- Incomplete Removal: Some rust or paint residues may remain, requiring further treatment.
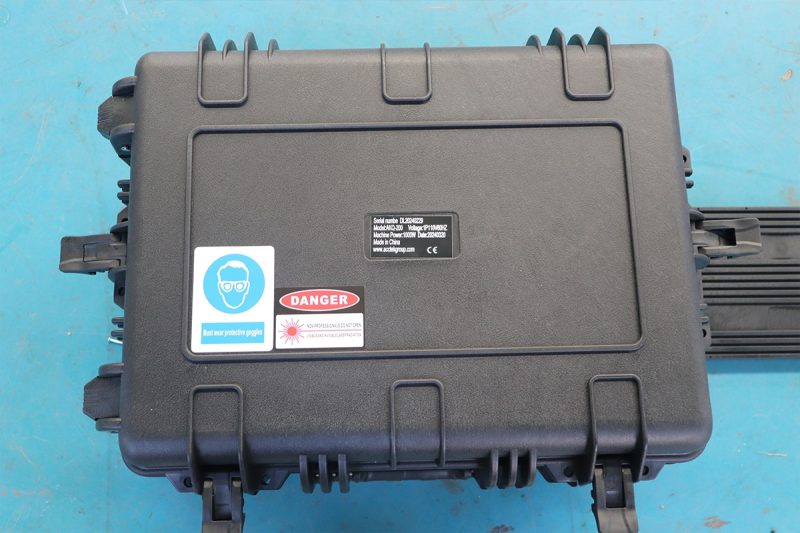
Laser Cleaning Technology
What Is Laser Cleaning?
How Does Laser Cleaning Work?
Key Steps in the Laser Cleaning Process:
- Laser Irradiation: A focused laser beam targets the contaminated surface.
- Contaminant Vaporization: The absorbed energy causes rapid heating and vaporization of rust, paint, or residues.
- Plasma Formation and Shock Waves: High-energy pulses generate a plasma plume and shock waves, further dislodging contaminants.
- Debris Removal: As contaminants vaporize or loosen, the cleaned surface is left free of impurities.
- No Residue: Since no abrasive materials or chemicals are used, the process leaves no secondary waste, making it ideal for clean, precise applications.
Types of Laser Cleaning Systems
Pulsed Lasers
Characteristics:
- Emit short, high-intensity pulses of laser energy at intervals, ensuring precise removal of surface contaminants.
Applications:
- Delicate surfaces that require minimal thermal impact (e.g., historical artifacts, electronics).
- In situations where controlled, precise cleaning is necessary.
Advantages:
- Reduces the risk of heat damage to sensitive surfaces.
- Ideal for fine, detailed cleaning in small or complex areas.
Continuous Wave Lasers
Characteristics:
- Provide a steady, uninterrupted beam of laser energy, suitable for fast and large-scale cleaning tasks.
Applications:
- Heavy-duty industrial applications such as shipbuilding, manufacturing, and automotive parts cleaning.
- Surfaces with thick rust or paint layers that require high energy for complete removal.
Advantages:
- Faster cleaning over large areas.
- Suitable for environments where speed is prioritized over precision.
Advantages of Laser Cleaning Over Traditional Methods
Non-Abrasive and Non-Contact
- Unlike sandblasting or grinding, laser cleaning does not wear down or damage the base material.
- It preserves the original structure and appearance of the substrate, which is crucial for sensitive or valuable components.
Environmentally Friendly
- Laser cleaning eliminates the need for chemicals or abrasives, reducing environmental impact and waste.
- It does not generate hazardous residues, making it a sustainable option for industries aiming to meet environmental regulations.
High Precision and Selectivity
- The laser can be adjusted to target specific areas, leaving surrounding surfaces untouched.
- This level of precision is particularly valuable in applications such as aerospace and electronics manufacturing.
Increased Efficiency and Productivity
- Laser cleaning reduces downtime by offering fast, effective cleaning, especially for complex surfaces or equipment with intricate geometries.
- It requires minimal setup and eliminates the need for consumables, further improving efficiency.
Enhanced Safety
- Reduces worker exposure to dust, chemicals, and noise associated with traditional methods.
- With proper safety protocols in place, laser cleaning offers a safer working environment.
Versatility Across Materials and Industries
- Laser cleaning is suitable for various substrates, including steel, aluminum, copper, plastics, and composites.
- It finds applications in industries such as automotive, aerospace, shipbuilding, and cultural heritage restoration.
Lower Maintenance and Operating Costs
- With fewer consumables and minimal wear on equipment, laser cleaning systems require less maintenance.
- The long service life of laser sources contributes to reduced operational costs over time.
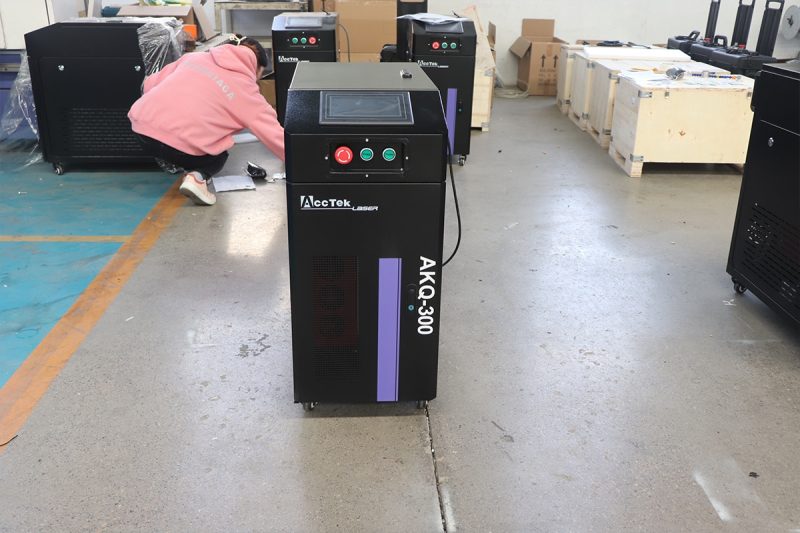
How to Remove Rust and Paint Using Laser Cleaning
Step-by-Step Guide
Surface Assessment
Proper assessment ensures that the cleaning process is optimized for the specific surface and contaminants.
- Identify the Material: Determine if the substrate is compatible with laser cleaning (e.g., steel, aluminum, copper).
- Analyze the Contaminants: Assess the thickness and type of rust or paint to select the appropriate laser settings.
- Inspect Surface Conditions: Check for coatings, cracks, or other surface features that could affect the cleaning process.
Equipment Selection
Choosing the right equipment is critical to achieving effective and safe cleaning.
- Select the Laser Type:
- Pulsed Lasers: For delicate surfaces requiring precision.
- Continuous Wave Lasers: For heavy-duty cleaning with large surface areas.
- Consider Mobility Needs: Decide between a portable unit for on-site cleaning or a stationary system for workshop use.
- Choose Accessories: Some applications may require special nozzles or optics to enhance performance.
Parameter Configuration
Fine-tuning the laser settings ensures effective contaminant removal without damaging the substrate.
- Set Laser Power: Higher power is ideal for thick rust or paint layers; lower power is used for delicate surfaces.
- Adjust Pulse Frequency and Scanning Speed: Higher frequency and speed improve coverage but may require multiple passes.
- Focus the Laser Beam: Correct focusing ensures optimal energy absorption by contaminants for efficient cleaning.
Safety Measures
Following safety protocols is essential to protect workers and the environment.
- Personal Protective Equipment (PPE): Use laser safety goggles, gloves, and protective clothing.
- Area Preparation: Establish barriers to control access and prevent laser exposure to unauthorized personnel.
- Training: Ensure operators are well-trained in laser safety and equipment operation.
- Ventilation: Install fume extraction systems to remove vaporized materials from the workspace.
Cleaning Process
Executing the process correctly ensures thorough and efficient contaminant removal.
- Positioning the Laser Head: Hold or mount the cleaning head at the correct distance and angle.
- Perform a Test Run: Start with a small section to ensure the parameters are correct.
- Scan the Surface: Move the laser head evenly over the surface with overlapping passes to ensure full coverage.
- Monitor the Process: Continuously observe the surface to prevent substrate damage or incomplete cleaning.
Post-Cleaning Procedures
Post-cleaning inspection and maintenance ensure quality results and equipment longevity.
- Inspect the Surface: Check for any remaining contaminants or damage to the substrate.
- Apply Protective Coatings: If needed, apply coatings to prevent re-oxidation or corrosion.
- Cleanup: Remove any dust or debris and ensure the workspace is clean.
- Document Results: Record the settings and outcomes for future reference.
Tips for Optimal Results
Multiple Passes
- For thick rust or paint layers, multiple cleaning passes may be necessary.
- Adjust parameters between passes to improve cleaning efficiency.
Cooling Intervals
- Allow time for the substrate to cool between passes to prevent heat buildup and avoid damaging the surface.
Parameter Optimization
- Continuously monitor and fine-tune laser power, scanning speed, and pulse frequency for the best results.
- Use test runs to adjust parameters before full-scale cleaning.
Maintenance
- Regularly clean and inspect the optics, cables, and laser head to maintain optimal performance.
- Check the cooling system to prevent overheating during extended operations.
Documentation
- Maintain detailed records of laser settings, outcomes, and any adjustments made during the cleaning process.
- Use these records to refine procedures and improve efficiency for future tasks.
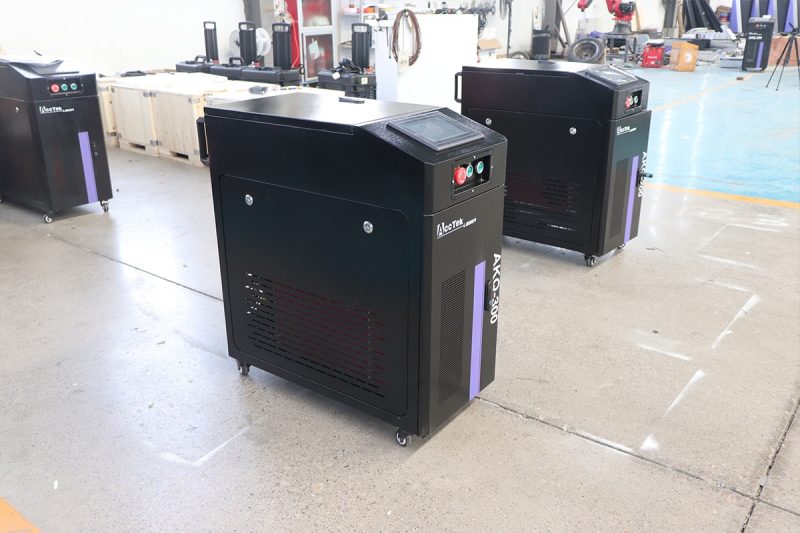
Applications of Laser Cleaning
Automotive Industry
- Restoration: In the automotive restoration sector, removing rust and old paint from classic and vintage cars is critical to preserving their structural integrity and appearance. Laser cleaning offers a gentle yet effective solution for removing contaminants without damaging the underlying metal, allowing for precise cleaning of delicate components like chassis, frames, and body panels.
- Manufacturing: Laser cleaning is increasingly used in automotive manufacturing to prepare parts for coating, bonding, or welding. By removing oxides, grease, or residues from engine parts, brake components, and other critical systems, laser cleaning enhances product quality and ensures proper adhesion of protective coatings.
- Maintenance: For ongoing maintenance, laser cleaning provides an efficient solution for removing rust, corrosion, and buildup on automotive components such as exhaust systems, engine blocks, and suspension parts. The precise nature of laser cleaning allows for targeted removal, helping to extend the life of automotive components while minimizing downtime.
Aerospace Industry
- Component Cleaning: In the aerospace industry, components like turbine blades, landing gear, and structural parts must be meticulously cleaned before maintenance or inspection. Laser cleaning is ideal for removing surface contaminants such as rust, carbon deposits, and oxidation from critical aerospace components, ensuring they meet stringent safety and performance standards.
- Surface Preparation: Before components are coated, welded, or bonded, laser cleaning is used to remove contaminants that could compromise the integrity of these processes. This method ensures that surfaces are thoroughly cleaned and prepared for further treatment, improving the quality and durability of aerospace components.
- Deburring: In precision aerospace manufacturing, laser cleaning is often used to remove sharp edges, burrs, or residues left from machining processes. The non-contact nature of laser cleaning prevents surface damage, ensuring components meet the exacting tolerances required in the aerospace industry.
Shipbuilding and Marine Industry
- Hull Cleaning: Rust and biofouling accumulate on ship hulls over time, leading to increased drag and higher fuel consumption. Laser cleaning provides an efficient, non-abrasive method for removing these contaminants, restoring the hull’s surface without damaging the metal or coatings. This method is particularly useful in shipyards where environmental regulations require eco-friendly cleaning solutions.
- Component Maintenance: Laser cleaning is used to maintain valves, pipes, and mechanical parts exposed to harsh marine environments. By removing corrosion, salt deposits, and old paint, laser cleaning helps prolong the lifespan of marine components and ensures that ships and other vessels operate at peak performance.
- Corrosion Prevention: Regular laser cleaning of marine structures and equipment prevents corrosion from spreading, which is vital for maintaining the safety and functionality of ships, offshore platforms, and dock facilities. Laser cleaning offers a precise and controlled way to clean metal surfaces, enabling the application of protective coatings that guard against future corrosion.
Manufacturing and Heavy Industry
- Tool and Die Cleaning: In the manufacturing sector, tools and dies accumulate rust, grease, and contaminants that can affect the quality of production. Laser cleaning provides an efficient way to clean these surfaces without causing wear or deformation, ensuring that manufacturing processes run smoothly and that the final products meet high-quality standards.
- Weld Preparation: Before welding, laser cleaning is used to remove contaminants like oxides, rust, or old coatings from metal surfaces, ensuring strong, reliable welds. The precision of laser cleaning allows for selective removal in areas that require welding, improving the integrity and quality of weld joints.
- Surface Texturing: Laser cleaning can also be used to create specific surface textures or finishes in metal components. By carefully controlling the laser’s intensity and focus, manufacturers can achieve desired surface characteristics, which may improve the performance or aesthetics of their products.
Cultural Heritage and Art Restoration
- Artifact Preservation: When it comes to preserving historical artifacts, traditional cleaning methods can cause irreversible damage. Laser cleaning, on the other hand, offers a gentle, controlled method for removing corrosion, dirt, and pollutants from metal, stone, or wood artifacts. This non-invasive process preserves the integrity of delicate surfaces while effectively cleaning them.
- Delicate Materials: For items made from sensitive materials, such as ancient metals, textiles, or fragile artworks, laser cleaning is ideal because it precisely targets contaminants without harming the original structure. This is particularly useful in the restoration of sculptures, monuments, and museum pieces, where conservation is a top priority.
Electronics Industry
- Circuit Board Cleaning: In the electronics industry, laser cleaning is used to remove oxides, solder residues, and contaminants from circuit boards and other electronic components. The precision and non-contact nature of laser cleaning makes it perfect for cleaning sensitive electronic devices without risking damage to the circuitry.
- Precision Cleaning: Laser cleaning is also used for high-precision cleaning tasks in the manufacturing of electronic devices, semiconductors, and other micro-scale components. The ability to selectively clean targeted areas without affecting adjacent parts makes it an essential tool in electronics production, where precision is key.
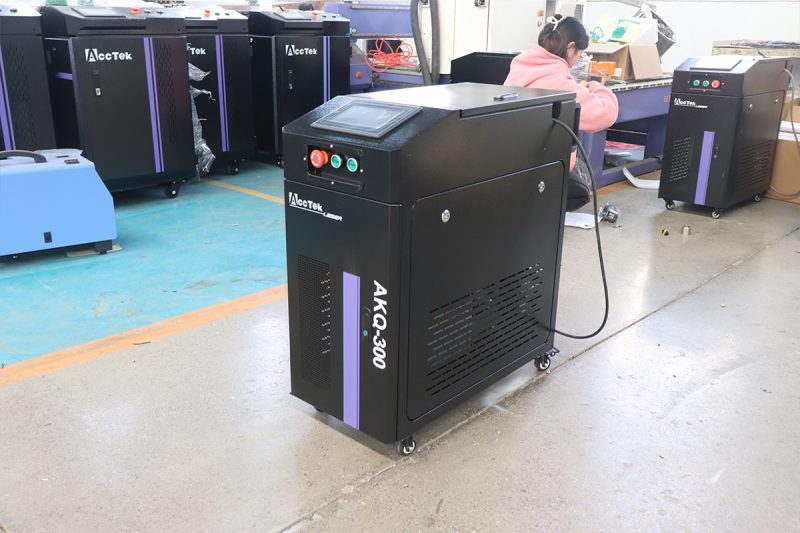
Choosing the Right Laser Cleaning Machine
Power Requirements
The power of a laser cleaning machine directly impacts its ability to remove contaminants and the speed of the cleaning process. Machines with higher power are suitable for heavy-duty tasks, while lower-power models are ideal for delicate applications.
- Low-Power Lasers (100W – 300W):
- Best for light rust or thin paint layers.
- Suitable for delicate surfaces, including electronics and historical artifacts.
- Medium-Power Lasers (500W – 1000W):
- Offers a balance of precision and speed.
- Ideal for automotive maintenance, aerospace components, and general manufacturing applications.
- High-Power Lasers (1500W and above):
- Suitable for thick rust and heavy-duty paint removal in industries like shipbuilding and manufacturing.
- Best for large-scale or high-volume applications requiring quick turnaround.
Material Compatibility
Different materials respond uniquely to laser cleaning, so it is essential to select a machine compatible with your target surfaces.
- Metals: Steel, aluminum, copper, brass, and titanium can all be effectively cleaned using laser technology.
- Non-Metals: Some plastics, composites, and coatings can be cleaned with the right laser configuration.
- Surface Sensitivity: For delicate surfaces such as thin metals or historical artifacts, pulsed lasers are more suitable due to their precise control and minimal thermal impact.
Surface Geometry
The shape and complexity of the surface being cleaned influence the type of laser cleaning machine needed.
- Flat Surfaces: Large flat areas, such as sheet metal or ship hulls, benefit from high-power continuous wave lasers for rapid cleaning.
- Complex or Intricate Shapes: Pulsed lasers are ideal for intricate designs, corners, or small components that require precise cleaning.
- Hard-to-Reach Areas: Laser cleaning systems with adjustable nozzles and handheld options provide greater flexibility for irregular geometries and inaccessible spaces.
Mobility
Mobility is a critical consideration, especially for on-site cleaning tasks or when working with large equipment.
- Portable Laser Cleaning Machines:
- Lightweight and easy to move.
- Ideal for fieldwork, automotive repairs, or maintenance in remote locations.
- Stationary Laser Cleaning Systems:
- Suitable for workshops or production lines.
- Offers higher power and larger working areas for high-volume applications.
- Hybrid Solutions: Some machines offer both stationary and portable configurations to provide maximum flexibility.
Budget and Cost of Ownership
Laser cleaning machines represent a significant investment, so it is essential to assess both the upfront costs and long-term savings.
- Initial Investment: Higher-power systems may have a higher purchase price but offer faster cleaning speeds, reducing labor costs.
- Operating Costs: Laser cleaning has low operating costs since it requires no chemicals or abrasives. Routine maintenance is minimal compared to traditional cleaning methods.
- Efficiency and ROI: Faster cleaning and minimal downtime translate into long-term savings. Calculate the return on investment (ROI) to determine the cost-effectiveness of the machine over its lifespan.
Regulatory Compliance
Laser cleaning technology must meet industry-specific safety and environmental standards to ensure safe and responsible operation.
- Laser Safety Standards: Ensure that the machine complies with international safety regulations such as IEC 60825-1. Operators should receive proper training and use personal protective equipment (PPE) to prevent accidents.
- Environmental Regulations: Laser cleaning produces no hazardous waste or emissions, making it environmentally friendly. Machines with proper fume extraction systems help maintain air quality in compliance with environmental standards.
- Industry-Specific Guidelines: Some industries, like aerospace and medical manufacturing, have stringent requirements for cleaning processes. Make sure the chosen laser machine meets these standards for regulatory compliance.
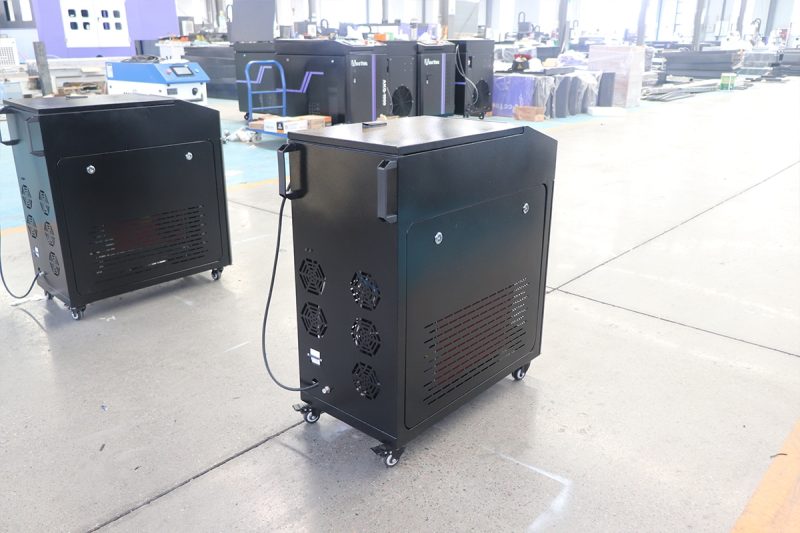
Safety Considerations
Laser Safety
Laser cleaning machines use high-powered lasers that can pose risks if not properly managed. It is crucial to understand laser safety measures to protect operators and bystanders.
- Laser Classification: Most industrial laser cleaning systems are classified as Class 4 lasers, which are the highest-risk category. Direct or reflected exposure to the laser beam can cause serious harm to the skin and eyes.
- Personal Protective Equipment (PPE): Operators must wear laser safety goggles that are rated for the specific wavelength of the laser being used. Protective clothing should also be worn to shield against accidental exposure to the laser beam. PPE helps prevent burns, eye injuries, and other laser-related accidents.
- Laser Beam Control: Always ensure that the laser cleaning system is equipped with safety features such as beam enclosures or barriers to prevent accidental exposure. Proper laser alignment and focusing are essential to minimize unintended reflections that could pose a risk.
- Training and Certification: Only trained personnel should operate laser cleaning machines. Operators must be familiar with laser safety protocols, including emergency shutdown procedures and the proper use of protective equipment.
Environmental Safety
Laser cleaning is an environmentally friendly process compared to chemical stripping or sandblasting, but there are still environmental factors to consider.
- Fume Extraction Systems: During laser cleaning, contaminants such as rust, paint particles, and vaporized material are released into the air. A proper fume extraction system is essential to remove these particulates and ensure clean air quality in the workspace. This not only protects workers but also helps maintain compliance with environmental regulations.
- Waste Management: Unlike chemical cleaning, laser cleaning does not produce hazardous liquid waste. However, the fine dust and particulates generated during the process must be properly collected and disposed of according to local regulations to prevent contamination.
- Energy Efficiency: Laser cleaning machines are energy-efficient, but it’s important to ensure that the equipment is running optimally to minimize energy consumption. Regular maintenance helps keep machines performing efficiently, reducing the environmental impact.
Operational Safety
Operational safety involves creating a secure working environment and establishing protocols that prevent accidents and ensure smooth operations.
- Controlled Access to the Laser Area: The laser cleaning workspace should be a controlled area, with restricted access to only authorized personnel. Clear signage should be displayed to warn of the presence of high-powered lasers. This reduces the risk of accidental exposure to bystanders.
- Emergency Shutoff Systems: All laser cleaning machines should be equipped with easily accessible emergency shutoff buttons. In the event of equipment malfunction or unexpected exposure, operators must be able to quickly power down the system to prevent injury or damage.
- Monitoring and Maintenance: Regular monitoring of laser cleaning equipment is necessary to ensure that all safety systems are functioning correctly. Routine inspections should be conducted to check for any wear and tear on protective covers, cables, or optics. This helps prevent breakdowns or laser malfunctions that could endanger workers.
- Operational Protocols: Establishing clear operating procedures is key to maintaining safety. Operators should be required to follow standard operating procedures (SOPs) for starting, operating, and shutting down the machine. This includes pre-checks to verify that all safety features are active and post-cleaning protocols to ensure proper storage and care of the equipment.
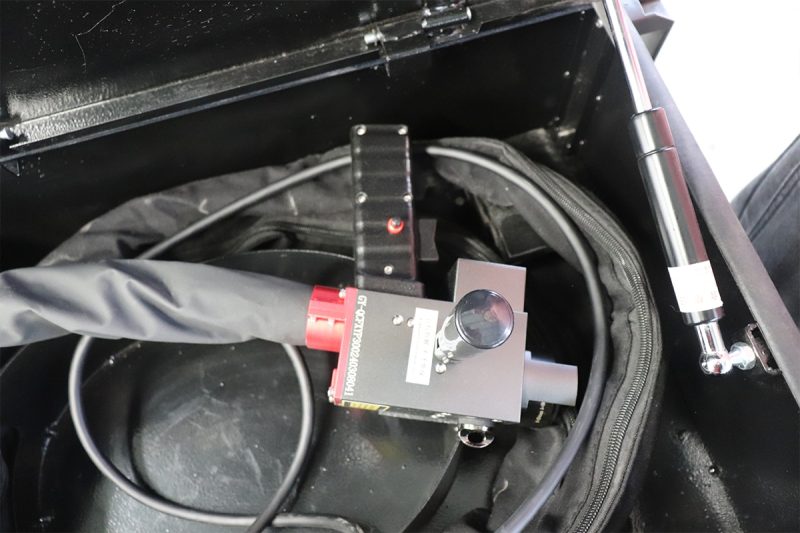
Maintenance and Care of Laser Cleaning Machine
Regular Maintenance Tasks
Cleaning Optics
Checking Laser Cables and Connectors
Monitoring the Cooling System
Laser Calibration
Lubrication of Moving Parts
Scheduled Servicing
Professional Inspections
Component Replacement
Software Updates
Troubleshooting Common Issues
Inconsistent Cleaning Results
- Cause: This may be due to dirty optics, misalignment of the laser beam, or incorrect parameter settings.
- Solution: First, clean the optics and check the laser calibration to ensure the beam is focused correctly. Review the cleaning parameters, including power level, pulse frequency, and scanning speed, to ensure they are set appropriately for the material and contaminant being removed.
Laser Power Fluctuations
- Cause: Power fluctuations could be caused by a faulty power supply, dirty optics, or an overheating laser source due to cooling system failure.
- Solution: Check the power supply and connections for any loose or damaged components. Clean the optics to ensure optimal laser transmission. Inspect the cooling system for proper function and ensure that it is maintaining the correct temperature.
Overheating Issues
- Cause: Overheating can occur if the cooling system is malfunctioning or if airflow is blocked.
- Solution: Check the cooling system, including coolant levels and air vents, and ensure they are functioning properly. Clean or replace air filters if needed and make sure there is adequate ventilation around the machine.
Machine Fails to Start
- Cause: This could be due to an electrical issue, such as a tripped circuit breaker or a problem with the power supply.
- Solution: Check all electrical connections and the power supply. Reset the circuit breaker if necessary. If the issue persists, consult a professional technician for further diagnosis.
Unexpected Shutdowns
- Cause: A sudden shutdown could be triggered by overheating, a power surge, or a malfunction in the laser control system.
- Solution: Inspect the cooling system for blockages or failures and ensure the machine is properly ventilated. Check for any electrical issues, such as power surges, and restart the machine. If the problem continues, contact a service technician.
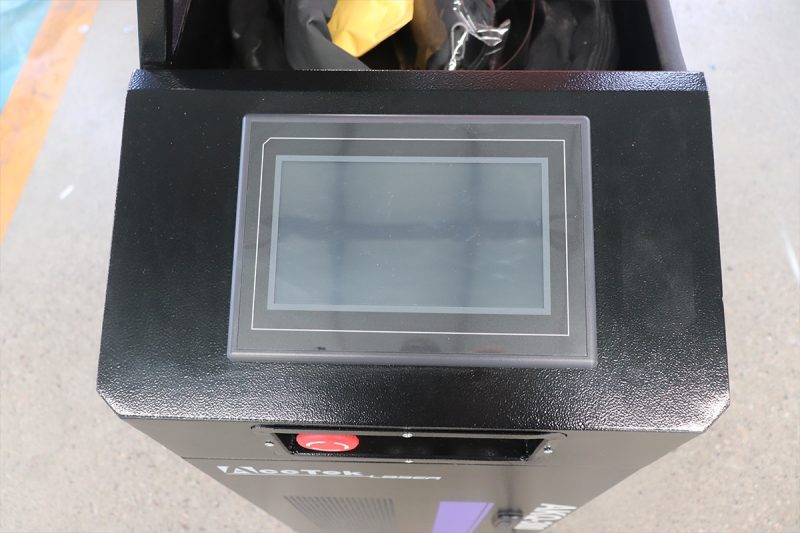
Summary
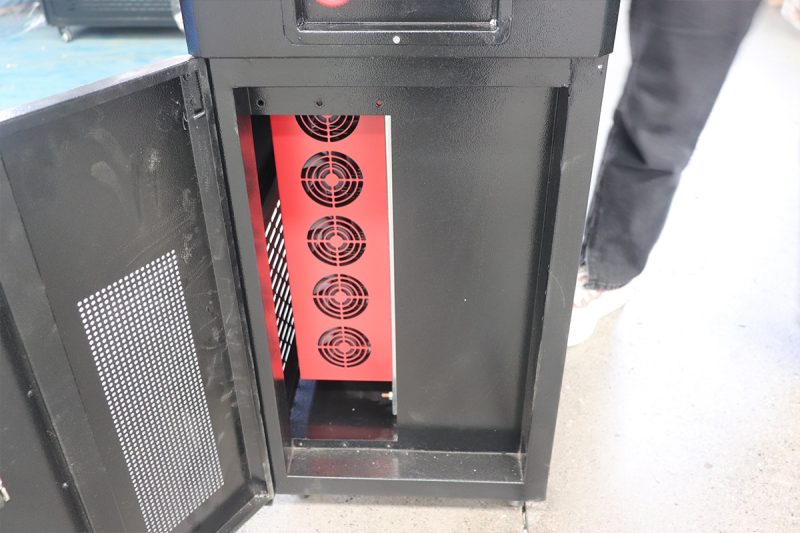
Get Laser Cleaning Solutions
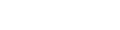
- [email protected]
- [email protected]
- +86-19963414011
- No. 3 Zone A, Lunzhen Industrial Zone,Yucheng City , Shandong Province.