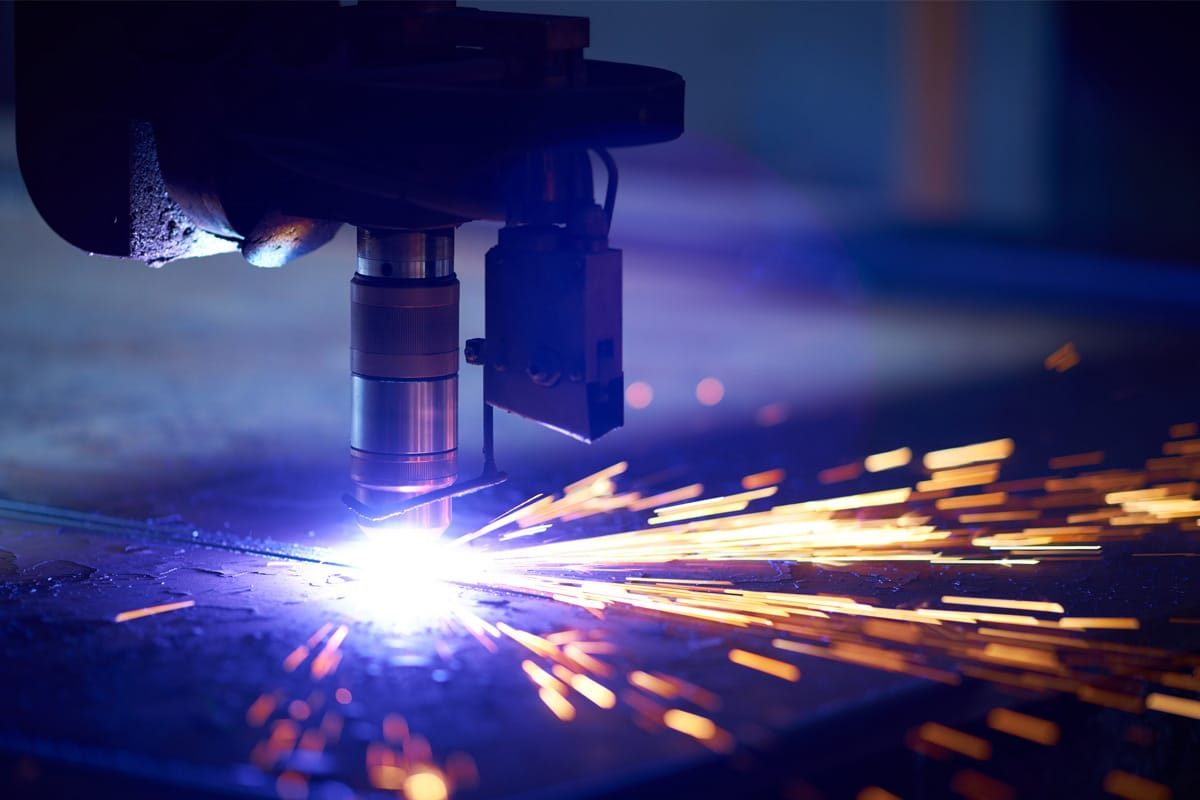
A rostlézeres vágással kapcsolatos gyakori problémák és megoldások
A szálas lézeres vágási technológiát széles körben használják különféle fém- és nemfémes anyagok vágására és megmunkálására, nagy hatékonyságának, nagy pontosságának és rugalmas működésének köszönhetően. Nagy teljesítményű lézersugarat használ a munkadarab felületének besugárzására, hogy megolvadjon vagy elpárologjon, ezáltal a munkadarab precíz vágása érhető el. A gyakorlati alkalmazásokban azonban a szálas lézervágás néhány gyakori problémával és kihívással is szembesül, mint például a csökkent vágási minőség, az alacsony vágási hatékonyság és a gyors berendezésvesztés. Ezeknek a problémáknak a megértése és kezelése nemcsak meghosszabbíthatja a berendezés élettartamát, hanem javíthatja a termelés hatékonyságát és a feldolgozás minőségét is.
Tartalomjegyzék
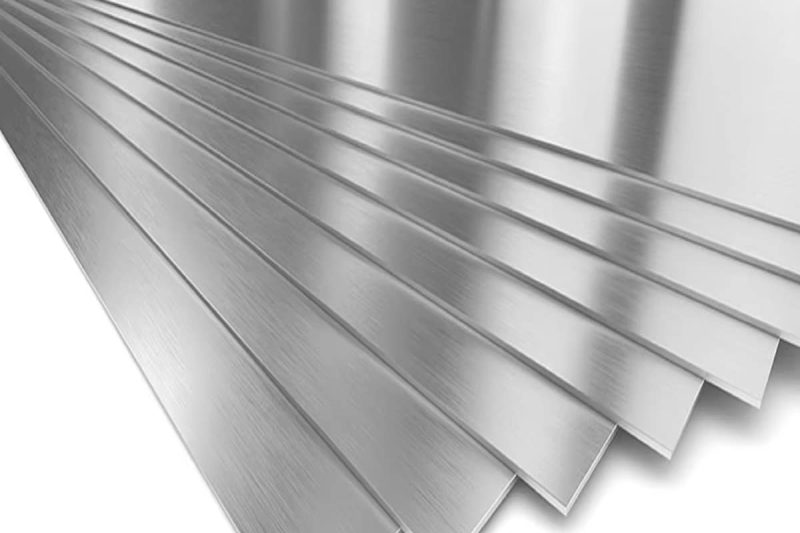
Anyagokkal kapcsolatos kihívások
Reflexiós képesség és vezetőképesség
Minél jobb az anyag vezetőképessége, annál kisebb a lézerenergia elnyelési sebessége. Például az arany, ezüst, réz, alumínium és más anyagok jó vezetőképességgel és gyenge energiaelnyeléssel rendelkeznek, ami szintén a lézer hullámhosszát tükrözi. Ezért minél nagyobb a fém vezetőképessége, annál nagyobb a visszaverő képessége.
Kihívás
- Magas fényvisszaverő képesség: Az olyan fémek, mint az alumínium és a réz, nagy fényvisszaverő képességgel rendelkeznek. Különösen akkor, ha a lézersugár az anyag felületének normálisához közeli szögben esik be, a lézerenergia nagy része visszaverődik a lézergenerátorra vagy a lézerátviteli rendszerre, ami nemcsak a feldolgozási hatékonyságot csökkenti, hanem a lézeres berendezések, például a lencse vagy az optikai szál égetése.
- Nem megfelelő energiaelnyelés: A nagy fényvisszaverő képesség miatt az anyagfelület által elnyelt effektív lézerenergia csökken, ami elégtelen feldolgozási mélységet, lassú vágási sebességet vagy kifogásolható feldolgozási minőséget eredményez.
Megoldás
- Használjon nagy teljesítményű lézereket: A lézergenerátor teljesítményének növelése közvetlenül növelheti az anyag felületére besugárzott lézerenergiát. Még ha az energia egy része visszaverődik is, a maradék energia elegendő a hatékony feldolgozáshoz. Válasszon olyan lézergenerátort, amelynek impulzusszélessége és frekvenciája megfelel bizonyos anyagokhoz az energiaátvitel és a feldolgozási hatások optimalizálása érdekében.
- Reflexiós technológia: A lézersugár alakjának és eltérési szögének beállításával a lézerenergia egyenletesebben oszlik el az anyag felületén, csökkentve a túlzott helyi visszaverődés problémáját. Használjon dinamikusan állítható optikai elemeket (például deformálható tükröket vagy folyadékkristályos térbeli fénymodulátorokat) a lézersugár hullámfront-torzításának valós idejű korrigálására, a lézersugár fókuszálási minőségének javítására, valamint a visszaverődés és a szóródás csökkentésére. Egyes fémek eltérő reflexiós jellemzőkkel rendelkeznek a különböző polarizációs állapotú lézereknél. A lézer polarizációs irányának beállításával a visszaverődési veszteség csökkenthető.
- Optimalizálja az anyag felületkezelését: Vigyen fel egy bevonatot vagy filmet, amely elnyeli a lézerenergiát az anyag felületén, hogy növelje a lézerenergia abszorpciós sebességét és csökkentse a fényvisszaverő képességet. Növelje az anyag felületének érdességét mechanikai, kémiai vagy lézeres előkezeléssel, javítsa a lézerenergia szórását és abszorpcióját, valamint csökkentse a közvetlen visszaverődést. A lézer abszorpciós sebességének növelése érdekében abszorpciós réteget alakítson ki az anyag felületén, vagy változtassa meg a felület kémiai tulajdonságait.
- Állítsa be a feldolgozási paramétereket: Optimalizálja a lézersugár beesési szögét, hogy elkerülje, hogy a lézersugár közvetlenül az anyag felületére merőlegesen essen be, és csökkentse a tükröződést. Állítsa be a lézeres feldolgozás sebességét, teljesítményét, gyújtótávolságát és egyéb paramétereit, hogy megtalálja a legjobb feldolgozási feltételeket a feldolgozás minőségének és hatékonyságának biztosítása érdekében.
Az anyag deformációja és deformációja
Az anyag deformációját a vetemedés okozza, amelyet az anyagon belüli maradék feszültség okoz, és az anyag szélessége és hossza mentén egyenetlenül oszlik el.
Kihívás
A lézeres vágási folyamat során a helyi melegítés anyagdeformációt okozhat, különösen vékony lemezes anyagokon. Ennek az az oka, hogy a lézer nagy mennyiségű hőenergiát koncentrál egy kis területen a vágás során, aminek következtében a terület hőmérséklete gyorsan megemelkedik, ezáltal az anyag hőtágulása és összehúzódása, végső soron pedig az anyag vetemedését és deformálódását okozza.
Megoldás
- A lézerteljesítmény beállítása: A lézerteljesítmény csökkentése csökkentheti a hőkoncentrációt, ezáltal csökkentve az anyag termikus deformációját.
- Optimalizálja a vágási sebességet: A vágási sebesség megfelelő növelése csökkentheti a lézer anyagon való tartózkodási idejét és csökkentheti a hőfelhalmozódást.
- Használjon segédgázt: A megfelelő segédgáz (például nitrogén vagy oxigén) kiválasztásával és áramlási sebességének beállításával hatékonyan eltávolítható a vágási folyamat során keletkező hő, és csökkenthető az anyag deformációja.
Anyagvastagság
A szálas lézeres vágási folyamatban az anyag vastagsága közvetlenül befolyásolja a vágás minőségét, hatékonyságát és a gép teljesítményét. A vékonyabb anyagok könnyebben vághatók, gyorsabban és nagyobb pontossággal, de a vastagabb anyagok durva vágóéleket eredményezhetnek, vagy nagyobb teljesítményt és segédgázt igényelnek.
Kihívás
Vastagabb anyagok vágásakor a lézer hosszabb ideig hatol át az anyagon, ami könnyen egyenetlen vágáshoz vezethet. A vastag anyagok rossz hővezető képességgel rendelkeznek, és a hő nem könnyen elvezethető, ami salakot és szabálytalan vágási felületeket eredményez a vágóélen.
Megoldás
- Válassza ki a megfelelő lézerteljesítményt: Válassza ki a megfelelő lézerteljesítményt az anyag vastagságának megfelelően, hogy a sugár energiája a vágási területen koncentrálódjon a legjobb vágási hatás elérése érdekében.
- Állítsa be a vágási paramétereket: beleértve a vágási sebességet, a fókuszpozíciót és a segédgáz nyomását, hogy biztosítsa a vágási folyamat stabilitását és egyenletességét.
- Többszörös vágás: Különösen vastag anyagok esetén többféle vágási módszer is alkalmazható, minden alkalommal a vastagság egy részét levágva, rétegenként vágva, hogy csökkentse a hőfelhalmozódást és az egyenetlen vágási problémákat.
A fenti módszerekkel hatékonyan megoldható a lézervágás során a vastag anyagok erős visszaverődése, vetemedése, deformációja, egyenetlen vágásának problémája, javítható a vágás minősége és hatékonysága.
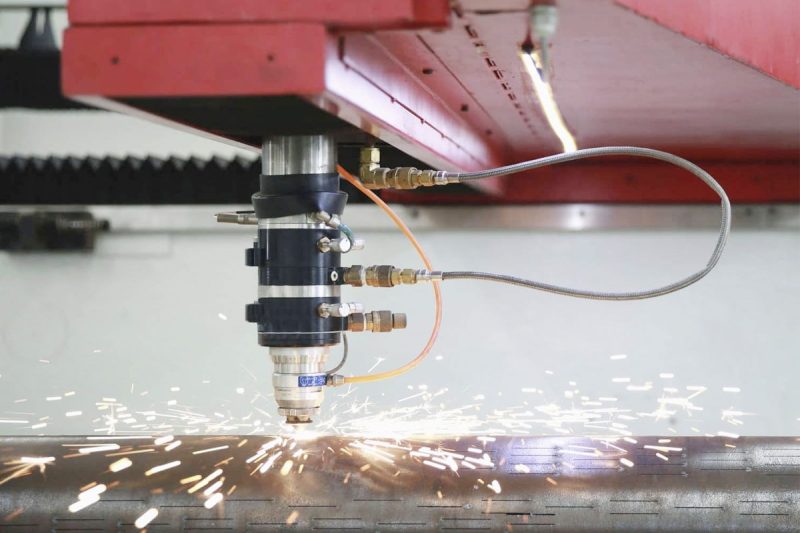
Élminőség és Kerf szélesség
A vágási él simasága és a sorja mennyisége kulcsfontosságú a vágási pontosság értékeléséhez. Ha a lézerenergia egyenetlenül oszlik el, vagy a vágási sebesség nem megfelelő, az él durvának vagy sorjásnak tűnhet. A rés szélessége a lézerfókusz stabilitásától függ. Ha a fókusz instabil, vagy a lézer teljesítménye ingadozik, a rés szélessége következetlenül változhat, ami befolyásolja a vágási pontosságot.
Durva élek és sorja
Kihívás
- Lézeres vágás során, ha az energia egyenetlen, vagy a vágási sebesség túl gyors vagy túl lassú, a vágóél gyakran sorja és egyenetlenség keletkezik. Különösen akkor, ha a lézersugár kimenő teljesítménye instabil, a vágott anyag felülete lokálisan túlmelegedhet vagy egyenetlenül megolvadhat, ami durva éleket eredményezhet.
- Egyes fémanyagok (például alumínium, rozsdamentes acél stb.) esetében az egyenetlen hőeloszlás hőterhelést idéz elő, ami további sorjaképződéshez vezet.
- Ezenkívül a segédgáz nem megfelelő használata (elégtelen légáramlás vagy nem megfelelő nyomás) befolyásolja az olvadt anyag kiürítési hatékonyságát és növeli a sorja számát.
Megoldás
- Kritikus a lézer teljesítménybeállításainak és vágási sebességének optimalizálása. Ügyeljen arra, hogy a lézer teljesítménye elég nagy legyen, és a kimenet stabil legyen az egyenletes hőeloszlás fenntartásához az anyag felületén. Ugyanakkor a vágási sebességet az anyag vastagságának és jellemzőinek megfelelően kell beállítani, sem túl gyorsan (az anyag elégtelen vágásának elkerülése érdekében), sem túl lassan (a túlzott olvadás elkerülése érdekében).
- A megfelelő segédgáz, például nitrogén vagy oxigén használata javíthatja a vágási eredményeket, és tiszta és sima vágási felületet biztosít. A nitrogént gyakran használják az oxidáció megelőzésére és az élsorja csökkentésére, míg az oxigén segít növelni a vágási hatékonyságot és az olvadási sebességet.
A résszélesség változása
Kihívás
- Az inkonzisztens résszélesség fő oka általában a lézerfókusz instabilitása vagy a lézerteljesítmény ingadozása. Ha a lézerfókusz el van tolva, az energiakoncentráció ennek megfelelően változik, ami a résszélesség ingadozását eredményezi. Ha a lézer teljesítménye instabil, az energia kimeneti ingadozása közvetlenül befolyásolja a vágási pontosságot, és változásokat okoz a résszélességben.
- Ezenkívül az optikai alkatrészek szennyeződése vagy sérülése a sugár minőségének változását is okozhatja, ezáltal befolyásolva a vágási vonal egyenletességét. A berendezés mechanikus részeinek, például a vezetősínek és a csapágyak kopása szintén befolyásolja a lézerfej mozgási pontosságát, ami következetlen réseket eredményez.
Megoldás
- Rendszeresen ellenőrizze és tartsa karban az optikai rendszert a stabil lézerfókusz és energia biztosítása érdekében.
- Tisztítsa meg vagy cserélje ki a szennyezett optikai lencséket, hogy elkerülje a szükségtelen fénytörést vagy szóródást a sugárátvitel során.
- Rendszeresen kalibrálja a lézerberendezés fókuszát és teljesítményét, hogy biztosítsa pontosságát működés közben.
- Karbantartsa a berendezés mechanikus részeit, hogy biztosítsa a lézerfej zökkenőmentes és akadálytalan mozgását a mechanikai kopás okozta vágási hibák csökkentése érdekében.
Összefoglalva, a paraméterek helyes beállításával és az optikai rendszer rendszeres karbantartásával hatékonyan javítható az élminőség és szabályozható a bevágás szélessége.
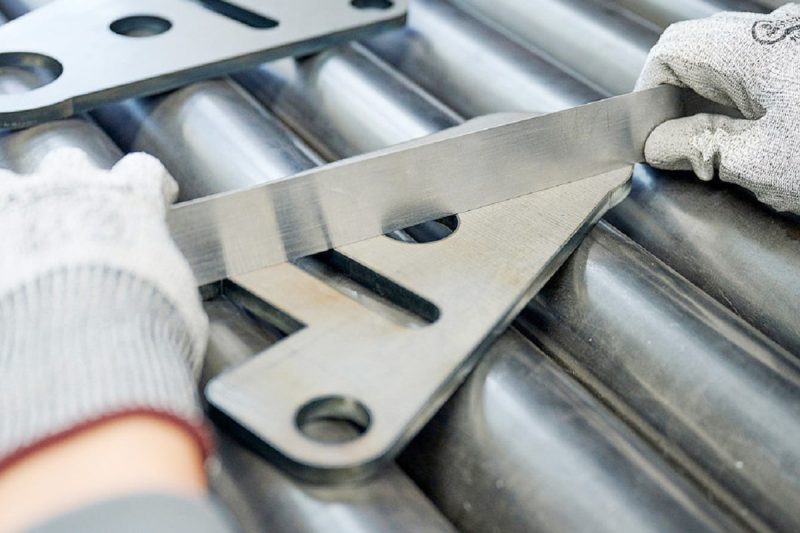
Folyamathoz kapcsolódó kihívások
A folyamattal kapcsolatos kihívások főként a szállézeres vágási folyamat során felmerülő műszaki problémákat érintik. A folyamatokkal kapcsolatos gyakori kihívások közé tartozik a salak felhalmozódása, amely gyakori kihívás a szálas lézeres vágási folyamatban, különösen vastagabb vagy nehezen vágható anyagok vágásakor. A salak felhalmozódását általában az okozza, hogy az anyag nem olvad meg teljesen, vagy nem tud elpárologni, vagy a segédgáz nem elegendő ahhoz, hogy az olvadt anyagot időben elfújja a vágási területről.
Salak felhalmozódása
Kihívás
- Ha a lézerenergia nem elegendő, vagy a lézersugár fókusza eltolt, az anyag felülete nem éri el azt a hőmérsékletet, hogy megolvadjon vagy elpárologjon, aminek eredményeként némi anyag a vágóélen marad. Különösen vastag lemezek megmunkálásánál a lézerenergiának elég erősnek kell lennie ahhoz, hogy a teljes anyagvastagságon áthatoljon.
- Segédgázokat, például oxigént vagy nitrogént gyakran használnak az olvadt anyag elfújására a vágási területről. Ha a gáznyomás túl alacsony, és az olvadt anyagot nem lehet hatékonyan eltávolítani, salak halmozódik fel a vágóélen.
- A túl nagy vágási sebesség azt eredményezi, hogy a lézer nem működik tovább ugyanazon a területen, az anyag nem olvad meg teljesen, vagy a gáz nem tudja időben eltávolítani a maradékot, ami salak felhalmozódását eredményezi.
Megoldás
- Győződjön meg arról, hogy elegendő gáznyomás áll rendelkezésre az olvadt anyag hatékony eltávolításához és a salak felhalmozódásának elkerüléséhez. A nitrogén nem oxidáló anyagokhoz alkalmas, míg az oxigén felgyorsíthatja a vágási sebességet, de nagyobb gáznyomást igényel.
- Optimalizálja a vágási sebességet az anyag vastagságának és jellemzőinek megfelelően, hogy a lézerenergia teljes mértékben hatni tudjon a vágási területre. A lézerteljesítmény és a vágási sebesség megfelelő kombinációja csökkentheti a szükségtelen hőhatásnak kitett zónákat, ezáltal elkerülhető az anyagok tökéletlen olvadása.
- Győződjön meg arról, hogy a lézergenerátor optikai alkatrészei a legjobb állapotban vannak, és stabilan ki tudják adni a szükséges lézerteljesítményt a vágási folyamat következetességének biztosítása érdekében.
Ezen paraméterek átfogó beállításával a salak felhalmozódási problémái jelentősen csökkenthetők, a vágás minősége javul, és az ezt követő csiszolási és tisztítási munka csökkenthető.
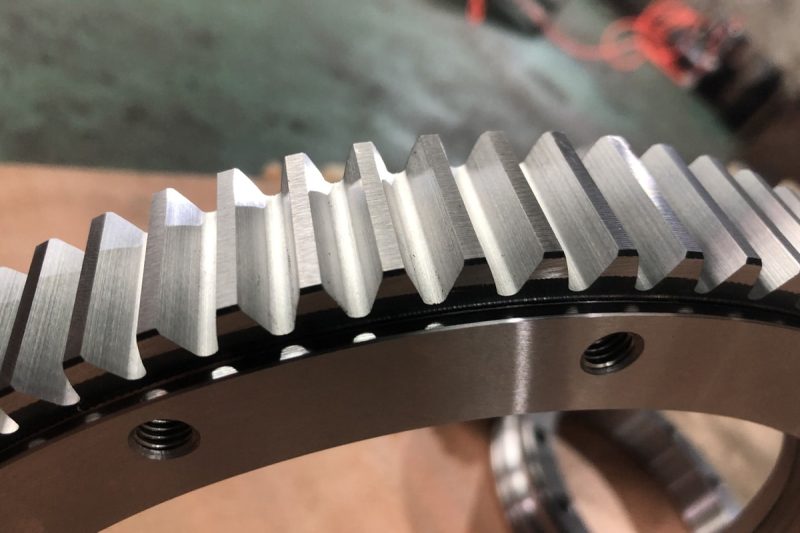
Szúrási és indítási problémák
A szálas lézeres vágási folyamat során a perforáció és az indítási problémák gyakori kihívást jelentenek, különösen vastagabb vagy erősen tükröződő anyagok esetén. A perforációs eljárás a lézervágás kiindulópontja, stabilitása és hatékonysága közvetlenül befolyásolja a teljes vágási folyamat hatását. Ha a perforálási idő túl hosszú vagy meghiúsul, az anyagpazarláshoz és a berendezés kopásához vezethet, és még a vágás minőségét is befolyásolhatja. Az indítási folyamat instabilitása egyenetlen résekhez és gyenge élvonalbeli minőséghez vezet, ami befolyásolja a késztermék pontosságát és megjelenését.
Piercing késések és kudarcok
Kihívás
A piercing késését általában az okozza, hogy a lézersugár nem képes gyorsan fókuszálni elég energiát ahhoz, hogy áthatoljon az anyagon, ami hosszú átszúrási időt eredményez. Az átszúrás késése különösen vastagabb anyagokon vagy fényvisszaverő anyagokon (például alumínium és réz) észlelhető, és még az átszúrási hibákat is okozhatja. A piercing meghibásodásának oka lehet az elégtelen lézerteljesítmény, a pontatlan lézerfókusz, az elégtelen segédgáz vagy a nem megfelelő gázválasztás. Ez egyenetlen vagy sikertelen vágásindítást, anyagveszteséget okozhat, és károsíthatja a lézeres berendezést.
Megoldás
- Gondoskodjon arról, hogy a lézer teljesítménye gyorsan koncentrálható legyen, különösen vastag lemezanyagoknál, ahol nagyobb energia szükséges a perforációhoz. Állítsa be a lézer fókuszát úgy, hogy az az anyag felületére összpontosuljon, csökkentve az energia diszperziót és lerövidítve a perforáció idejét.
- Rövid impulzus üzemmódban történő átszúrással csökkenthető az anyag túlmelegedése és deformációja, miközben csökken a szúrás meghibásodásának esélye. Ez a technika különösen alkalmas vastagabb anyagokhoz és erősen tükröződő anyagokhoz.
- A nitrogén és az oxigén használata jelentős hatással van a piercing folyamatára. Az oxigén felgyorsíthatja a perforálási folyamatot, de az anyag oxidációját okozhatja, ezért a megfelelő gázt és nyomást az anyagjellemzők alapján kell kiválasztani.
- Nagyon vastag anyagoknál többlépcsős perforációs technikák alkalmazhatók, amelyek nem egyszerre, hanem rétegenként hatolnak át az anyagon. Ezzel a módszerrel hatékonyan elkerülhető a defekt és a túlzott hőhatás.
Instabil indítás
Kihívás
Az instabil indítás főként a lézervágás elején egyenetlen vágásszélességben és rossz élminőségben nyilvánul meg, sőt a vágási folyamat meghibásodásához is vezethet. Ennek oka általában az instabil lézerenergia, a gázáramlási sebesség változása, az anyag felületi jellemzőinek (például oxidáció vagy bevonat) inkonzisztenciája, stb. Az instabil indítás a kezdeti rész rossz vágási minőségéhez vezethet, különösen precíziós vágási alkalmazásoknál. az instabilitás befolyásolja a késztermék pontosságát és konzisztenciáját.
Megoldás
- Indítás előtt az anyagfelület előmelegíthető, különösen erősen tükröződő anyagokon. Ez segít csökkenteni a lézervisszaverődést, és simábbá teszi a vágási folyamatot.
- Győződjön meg arról, hogy a lézergenerátor gyorsan eléri a stabil állapotot indításkor a lézerteljesítmény növekedési sebességének és a segédgáz áramlási sebességének beállításával. Ezzel hatékonyan elkerülhetők az energiaingadozások indításkor.
- Azon anyagok esetében, amelyek felületén oxidrétegek vagy egyéb szennyeződések találhatók, egyszerű felülettisztítás vagy bevonateltávolítás végezhető az indítás előtt, hogy csökkentse a lézervisszaverődést és az instabilitást az indítási folyamat során.
- Használjon valós idejű felügyeleti rendszert a vágási folyamat figyelésére, különösen az indítási szakaszban, és biztosítsa a vágási folyamat stabilitását és konzisztenciáját a paraméterek beállításával.
Általánosságban elmondható, hogy a lézerparaméterek optimalizálásával, megfelelő segédgáz kiválasztásával, impulzusperforációs technológia alkalmazásával, indítás előtti előfeldolgozással jelentősen csökkenthető a perforáció késleltetése, meghibásodása, instabil indítási problémája, javítható a vágás hatékonysága és minősége. Ezek a megoldások nemcsak a működési hatékonyságot javítják, hanem a berendezések hosszú távú stabil működését is biztosítják.
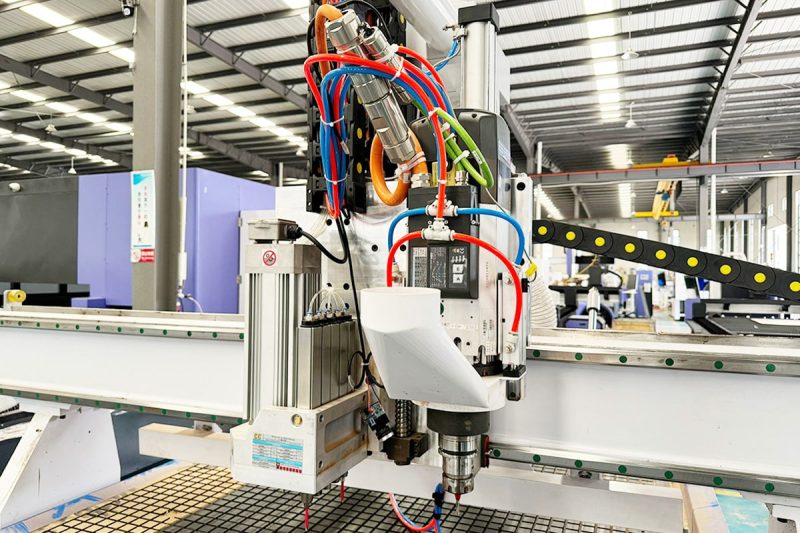
Géppel kapcsolatos kihívások
Szállézeres vágásnál a gép teljesítménye közvetlenül befolyásolja a vágás minőségét és hatékonyságát. Maga a gép sugárátviteli rendszere és mechanikai alkatrészei hosszú távú használat után különféle problémákat okozhatnak, amelyek befolyásolják a lézervágás pontosságát és stabilitását.
Gerenda szállítási rendszer problémái
Kihívás
A sugárátviteli rendszer az a magrendszer, amely a lézerforrás energiáját továbbítja a vágófejnek. Teljesítménye közvetlenül meghatározza a lézersugár energiastabilitását és a vágás minőségét. Ha a sugárátviteli rendszert nem ellenőrzik és karbantartják rendszeresen, a por, szennyeződések vagy mechanikai kopás is károsíthatja az optikai alkatrészeket, tovább csökkentve a rendszer hatékonyságát.
Megoldás
- Az optikai lencsék és a szálas lézervágó rendszerek lencséi hajlamosak a por és az olaj felhalmozódására. A rendszeres tisztítás elkerülheti a lézersugár átviteli hatékonyságának csökkenését és biztosítja a sugár stabilitását.
- A szálas csatlakozók stabilitásának és a lézersugarak pontos beállításának biztosítása csökkentheti az energiaveszteséget. Rendszeresen ellenőrizze a szálcsatlakozásokat, hogy ne legyen laza vagy kopás.
- Ha gyakori sugárinstabilitási problémák lépnek fel, fontolja meg az adaptív optika technológia használatát a sugárátviteli rendszer valós idejű beállításához a legjobb sugárminőség biztosítása érdekében.
- A sugárátvitel során felhalmozódó hő befolyásolja a sugár minőségét, ezért kulcsfontosságú a hűtőrendszer hatékony működése. Rendszeresen ellenőrizze a hűtőrendszert, hogy megbizonyosodjon arról, hogy az megfelelően tudja-e elvezetni a hőt, és csökkenti a hőhatást a sugárátvitel során.
Mechanikai kopás
Kihívás
A szállézeres vágógépek mechanikai alkatrészei, beleértve a vezetősíneket, szervomotorokat és meghajtórendszereket, az intenzív használat során idővel fokozatosan elhasználódnak. A mechanikai kopás nemcsak a vágófej instabil mozgását okozza, hanem befolyásolhatja a vágási út pontosságát és végső soron a késztermék minőségét is. Különösen a nagy sebességű és nagy pontosságú vágási követelmények mellett a mechanikai kopás felgyorsítja a berendezések öregedését, és növeli a karbantartási költségeket és az állásidőt. Emellett a megnövekedett vibráció és zaj is gyakori tünete a mechanikai kopásnak.
Megoldás
- A vezetősíneket és az erőátviteli rendszereket rendszeresen kenni kell a súrlódás csökkentése és a mechanikus alkatrészek élettartamának meghosszabbítása érdekében. Ugyanakkor ellenőrizni kell a kenési rendszert, hogy biztosítsa a normál működését, és elkerülje az alkatrészek elégtelen kenés miatti túlzott kopását.
- Ha a vezetősínek, fogaskerekek vagy más alkatrészek elkoptak vagy elmozdultak, a sérült részeket időben ki kell cserélni a gép pontosságának és stabilitásának biztosítása érdekében.
- Nagy pontosságú műveleteknél a vibráció ronthatja a vágási pontosságot. Rezgéscsillapító eszközök beépítésével vagy a gép beépítési helyzetének optimalizálásával csökkenthető a rezgés hatása a mechanikai alkatrészekre, ezáltal késleltetve a kopást.
- Modern szálas lézervágó gépek felszerelhető felügyeleti rendszerrel, amely valós időben figyeli a mechanikai alkatrészek állapotát, adatelemzéssel előre jelzi az esetleges meghibásodásokat, és elkerüli a mechanikai kopás okozta hirtelen leállásokat.
A sugárátviteli rendszer és a mechanikai alkatrészek rendszeres karbantartásával és optimalizálásával a szálas lézervágó gép teljesítménye és stabilitása jelentősen javítható, biztosítva a vágási hatás folytonosságát és magas minőségét.
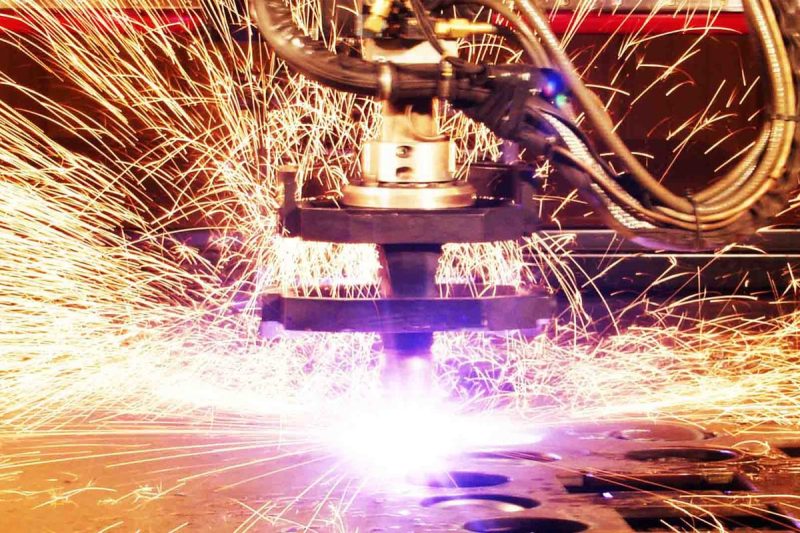
Kúp és szögeltérés
A kúposság és a szögeltérés két gyakori precíziós kihívás a szálas lézeres vágási folyamatban. A kúpos problémák általában a vágott él felső és alsó szélességében mutatkoznak meg, míg a szögeltérés a lézersugár és az anyag közötti merőlegesség hiányára utal, ami ferde vágási felületet eredményez. Ezek a problémák befolyásolják a kész munkadarab minőségét és megjelenését, különösen a nagy pontosságú vágási feladatoknál.
Kúpos
Kihívás
A kúpos jelenség általában vastag anyagok vágásakor jelentkezik, és abban nyilvánul meg, hogy a vágóél felül keskeny, alul széles, vagy felül széles, alul keskeny. Ennek az az oka, hogy a lézersugár energiaeloszlása az anyagon való áthaladáskor egyenetlen. Minél nagyobb a vágási mélység, annál nyilvánvalóbb a lézerenergia csillapítása, ami különbséget eredményez a vágóél felső és alsó szélességében. A kúposodás befolyásolja a munkadarab pontosságát, különösen nagy pontosságú összeszerelés esetén. A kúpos szerelési nehézségeket okoz, sőt a munkadarabot selejtezi. Ezenkívül a nem megfelelő segédgáznyomás és az instabil lézerteljesítmény szintén súlyosbítja a kúpos jelenséget.
Megoldás
- A kúpos problémák hatékonyan csökkenthetők a lézerfókusz mélységének és helyzetének optimalizálásával. Ha a fókuszt az anyag közepére helyezi a felület helyett, segít fenntartani a lézerenergia egyenletes eloszlását a teljes vágási vastagságban.
- Vastagabb anyagok esetén a nagyobb teljesítményű lézergenerátor használatával stabilabb energiakibocsátás tartható fenn a vágási folyamat során, és csökkenthető a lézercsillapítás okozta kúpos problémák.
- A kúposodás csökkenthető a segédgáz nyomásának megfelelő beállításával, a vágási terület tisztán tartásával és a vágóél hatékony hűtésével. Különösen vastag anyag vágásánál a segédgáz szerepe döntő.
- Az optikai rendszerrel kapcsolatos bármilyen kisebb probléma a lézersugár egyenetlen energiaeloszlását okozza. Ezért az optikai alkatrészek rendszeres karbantartása és tisztítása a lézersugár minőségének biztosítása érdekében hatékonyan csökkentheti a kúposodást.
Szögeltérés
Kihívás
A szögeltérés a lézersugár anyaghoz viszonyított függőlegességének hiányára utal, ami ferde vágóélt eredményez. Ennek oka lehet a lézerfej instabil beszerelése, a sugár nem megfelelő beállítása vagy a mechanikai rendszer nem megfelelő pontossága. A szögeltérés miatt a munkadarab vágási felülete egyenetlen lesz, ami befolyásolja a pontosságot és a megjelenést, különösen akkor, ha a munkadarabot derékszögben kell vágni.
Megoldás
- A szögeltérés probléma megoldásának első lépése annak biztosítása, hogy a lézerfej szilárdan rögzítve legyen és merőlegesen az anyagra. A lézerfej és a mechanikai rendszer rendszeres kalibrálása biztosítja, hogy a lézersugár mindig a megfelelő szöget tartsa a vágás során.
- A vágási sebesség, a kimeneti teljesítmény és a segédgáz beállításai mind befolyásolják a szögeltérést. Ezen paraméterek optimalizálásával a lézersugár stabilan tartható vágás közben, ezáltal csökkenthető a szögeltérés.
- Az adaptív optika valós időben tudja beállítani a lézersugár terjedési útvonalát és fókuszát, így biztosítva, hogy a vágás során mindig a megfelelő szöget betartsa az anyaggal, ezáltal csökkentve a szögeltérést.
- A külső tényezők, például a hőmérséklet- és páratartalom-változások és a rezgések befolyásolhatják a lézervágás szögpontosságát. A szögeltérés tovább csökkenthető a vágási környezet stabilitásának megőrzésével, például a vibráció csökkentésével, a hőmérséklet és páratartalom szabályozásával stb.
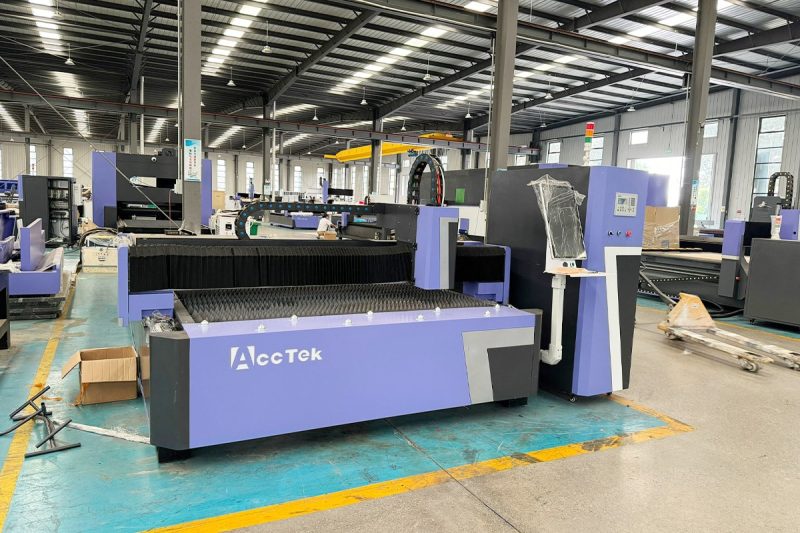
Környezeti tényezők
A környezeti tényezők közvetlen hatással vannak a szállézeres vágási folyamat stabilitására és minőségére. A hőmérséklet és a páratartalom ingadozása, valamint a levegő minőségének változása negatívan befolyásolhatja a lézerrendszer teljesítményét, a vágás minőségét és a gép élettartamát. Ezeknek a környezeti tényezőknek a megértése és ellenőrzése biztosíthatja, hogy a berendezés a lehető legjobban működjön, csökkentve a szükségtelen meghibásodásokat és a karbantartási igényeket.
Hőmérséklet és páratartalom ingadozása
Kihívás
A hőmérséklet és a páratartalom ingadozása komoly kihívást jelent a lézervágási folyamatban. A lézergenerátor és az optikai rendszer nagyon érzékeny a hőmérséklet és a páratartalom változásaira. Például a túl magas hőmérséklet a lézergenerátor túlmelegedését okozhatja, ami befolyásolja a lézersugár minőségét és stabilitását; míg a túl alacsony hőmérséklet azt okozhatja, hogy a lézergenerátor nem éri el a szükséges üzemi hőmérsékletet, ami befolyásolja a teljesítményt. A túl magas páratartalom páralecsapódást okozhat az optikai alkatrészeken, ami befolyásolja a lézersugár átviteli hatékonyságát, sőt az optikai eszközöket is károsíthatja. A túl alacsony páratartalom növelheti a statikus elektromosság kockázatát, ami megzavarhatja az elektronikus alkatrészek normál működését.
Megoldás
- A hőmérséklet- és páratartalom-ingadozások megbirkózása érdekében ajánlatos speciális környezetszabályozó rendszereket, például klíma- és páramentesítő berendezéseket telepíteni a vágóműhelybe. Ezek a rendszerek állandó hőmérsékletet és páratartalmat tudnak fenntartani a műhelyben annak érdekében, hogy a lézerberendezés optimális körülmények között működjön.
- Szereljen fel hőmérséklet- és páratartalom-érzékelőket a vágóberendezés köré, hogy valós időben figyelje a környezeti feltételeket. Ha rendellenességet észlel, a környezeti vezérlőrendszer automatikusan beállítható, vagy szükség esetén a vágási folyamat felfüggeszthető a berendezés károsodásának elkerülése érdekében.
- Száraz környezetben növelje a levegő páratartalmát a statikus elektromosság kockázatának csökkentése érdekében, és használjon antisztatikus padlót és a berendezés földelését a biztonságos működés érdekében.
Levegőminőség
Kihívás
A levegő minőségének a lézeres vágási folyamatra gyakorolt hatását nem lehet figyelmen kívül hagyni. A levegőben lebegő por, olajköd és egyéb szennyező anyagok bejuthatnak a lézergenerátor optikai rendszerébe vagy vágási területére, befolyásolva a lézersugár átvitelét és fókuszálását. A levegőben lévő szennyező anyagok a vágási folyamat során is reagálhatnak a lézersugárral, ami rossz vágási eredményeket vagy akár a munkadarab felületének károsodását is eredményezheti. Ezenkívül a rossz minőségű levegőnek való hosszú távú kitettség növeli a gép karbantartásának gyakoriságát és lerövidíti a berendezés élettartamát.
Megoldás
- Telepítsen légtisztító rendszert a lézervágó műhelyben, hogy kiszűrje a levegőben lévő részecskéket és szennyező anyagokat a tiszta levegő biztosítása érdekében. Különösen bizonyos anyagok (például műanyag és fa) vágásakor ezek az anyagok káros gázokat bocsáthatnak ki a lézeres vágási folyamat során, ezért különösen fontos a hatékony légtisztító rendszer.
- Még légtisztító rendszer esetén is szükséges a lézergenerátor optikai rendszerének rendszeres tisztítása. Távolítsa el a port és a szennyeződéseket, amelyek felhalmozódhatnak, hogy biztosítsák a lézersugár minőségét és a vágási hatást.
- Egyes kulcsfontosságú berendezésekben vagy területeken túlnyomás elleni védelmi intézkedéseket lehet bevezetni, vagyis szűrt levegő bevezetésével a területen a levegőnyomást a külsőnél magasabban tartják, hogy megakadályozzák a szennyező anyagok bejutását.
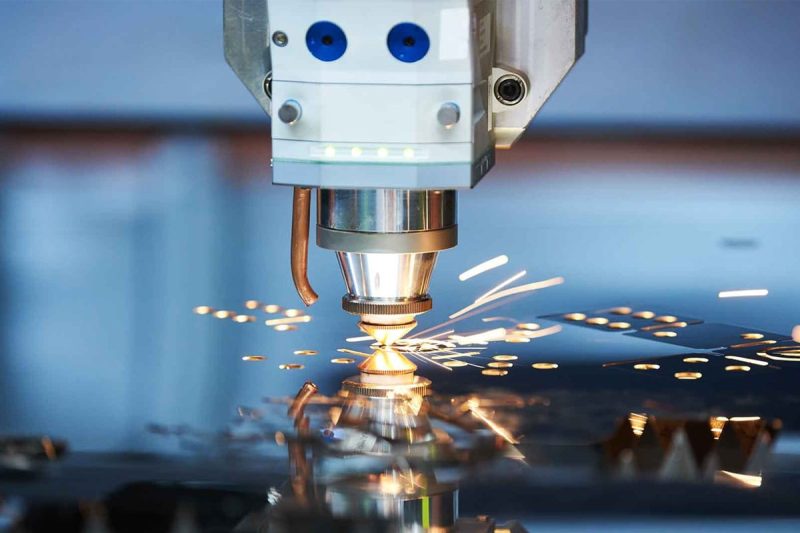
Üzemeltetővel kapcsolatos kihívások
A szállézeres vágás minőségét és hatékonyságát a környezeti tényezők mellett a kezelő képzettségi szintje és munkahatékonysága is közvetlenül befolyásolja. A képzettség és a szakértelem hiánya vagy a nem hatékony munkafolyamat helytelen működéshez, megnövekedett hibaarányokhoz, sőt berendezések károsodásához vagy biztonsági balesetekhez vezethet. Ezért a kezelő professzionalizmusának javítása és a munkafolyamat optimalizálása fontos láncszemek a vágási minőség és a termelés hatékonyságának biztosításához.
Képzés és szakértelem hiánya
Kihívás
A szálas lézervágás egy nagy pontosságú technológia, amely magas szakmai tudást és készségeket követel meg a kezelőktől. Egyes vállalatoknál azonban előfordulhat, hogy a kezelők nem rendelkeznek megfelelő képzettséggel, és nem tudják teljesen megérteni és elsajátítani a lézervágás összetettségét. Ez a helyzet azt eredményezheti, hogy a kezelők nem tudnak hatékonyan reagálni, ha olyan műszaki problémákkal vagy összetett munkadarabokkal szembesülnek, amelyek befolyásolhatják a vágás minőségét, növelhetik a berendezés kopását, és akár biztonsági kockázatokat is okozhatnak. Ezenkívül a berendezés karbantartása és gondozása speciális készségeket és ismereteket igényel. Az üzemeltető ismereteinek hiánya azt eredményezheti, hogy a berendezést nem karbantartják és nem gondozzák azonnal, ami lerövidíti a berendezés élettartamát.
Megoldás
- A vállalatoknak szisztematikus képzést kell nyújtaniuk a kezelők számára, beleértve a lézervágás alapelveit, a berendezés kezelési útmutatóját, a hibaelhárítást és a gyakori problémák megoldását stb. Rendszeres képzéssel biztosítsák, hogy a kezelők mindig elsajátítsák a legújabb technológiát és működési előírásokat.
- Hozzon létre egy működési tanúsítási rendszert a kezelők számára, és csak minősített személyzet kezelheti a lézervágó berendezéseket. Ez nemcsak a kezelő felelősségérzetét javítja, hanem a működés minőségét és biztonságát is biztosítja.
- Erős technikai támogatást nyújt az üzemeltetőknek, például egy speciális műszaki tanácsadó részleg felállítása, vagy műszaki szakértők felvétele rendszeres útmutatásra, hogy segítsenek az üzemeltetőknek megoldani a napi működés során felmerülő problémákat.
Nem hatékony munkafolyamat
Kihívás
A munkafolyamat hatékonysága közvetlenül befolyásolja a gyártás általános hatékonyságát és a lézervágás minőségét. Egyes vállalatoknál az ésszerűtlen munkafolyamat-tervezés vagy az elégtelen koordináció miatt a kezelők túl sok időt tölthetnek a feladatok váltásával, a berendezések hibakeresésével vagy az anyagok kezelésével. Ez a nem hatékony munkafolyamat nemcsak időt és erőforrásokat pazarol, hanem a kezelőt is elfáradhat, és növelheti a hibák lehetőségét. Ezen túlmenően, ha a vállalat nem tudja azonnal optimalizálni a munkafolyamatot, a rendelési mennyiség növekedésével a nem hatékony folyamat egyre hangsúlyosabbá válik, ami súlyosan érinti a termelési kapacitást és a vállalati versenyképességet.
Megoldás
- A jelenlegi munkafolyamat elemzésével és értékelésével azonosítani tudjuk a szűk keresztmetszeteket és a nem hatékony kapcsolatokat, és célzott optimalizálásokat hajthatunk végre. Például ésszerűen rendezhetjük a feladatok sorrendjét, csökkenthetjük a berendezések üzembe helyezésének és anyagmozgatásának idejét, javíthatjuk a munka hatékonyságát.
- Az automatizálási technológiák, mint például az automatikus be- és kirakodó rendszerek és az intelligens szedőszoftver bevezetése jelentősen csökkentheti a kézi műveletek idő- és precíziós hibáit, és javíthatja a teljes munkafolyamat hatékonyságát.
- Alkalmazza a karcsú termelési elveket a hulladék csökkentése és az erőforrás-elosztás optimalizálása érdekében. Folyamatos fejlesztésekkel és munkatársak részvételével hatékony és rugalmas munkafolyamatot alakíthatunk ki a lézervágási folyamat hatékonyságának és magas minőségének biztosítása érdekében.
E környezeti és üzemeltetői kihívások kezelésével a vállalatok nagymértékben javíthatják a szálas lézervágás hatékonyságát és minőségét, ezáltal előnyhöz juthatnak a piaci versenyben.
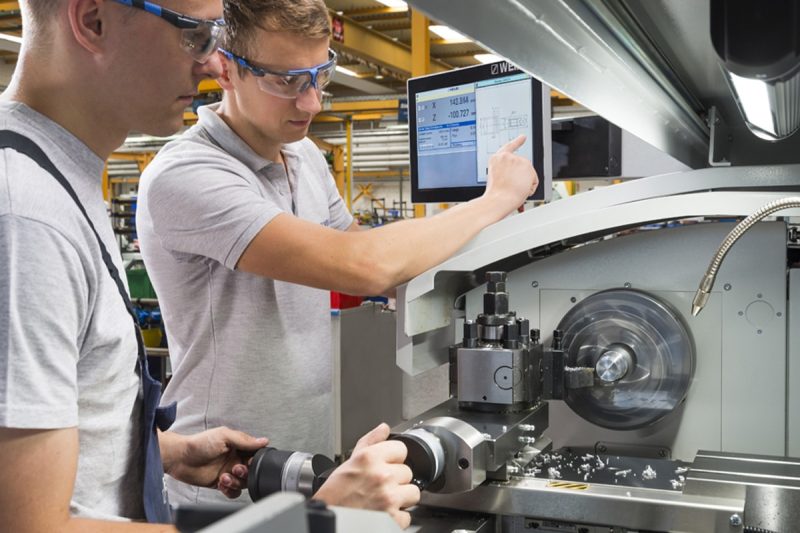
Óvintézkedések és bevált gyakorlatok
A szálas lézervágás folyamatos hatékony működésének biztosítása érdekében kritikus fontosságú a megelőző intézkedések és a legjobb gyakorlatok megtétele. A gépek rendszeres karbantartásával, a paraméterek optimalizálásával, a kezelői képzéssel és a folyamatos fejlesztéssel a vállalatok hatékonyan csökkenthetik a meghibásodási arányt, javíthatják a vágás minőségét és meghosszabbíthatják a berendezések élettartamát.
Rendszeres gépkarbantartás
Kihívás
A lézervágó berendezések hosszú távú működése az optikai alkatrészek szennyeződését, a lézerfej kopását és a hűtőrendszer meghibásodását okozhatja. Ha hiányzik a rendszeres karbantartás, ezek a problémák befolyásolhatják a lézergenerátor teljesítményét, növelhetik a termelési leállást, és akár berendezés meghibásodását is okozhatják.
Megoldás
- A lézersugár átviteli hatékonyságának biztosítása érdekében rendszeresen tisztítsa meg az optikai rendszert.
- Ellenőrizze és cserélje ki a sérülékeny részeket, például vágófúvókákat, lézerlencséket és szűrőrendszereket.
- A lézergenerátor túlmelegedésének elkerülése érdekében rendszeresen ellenőrizze a hűtőrendszert, hogy megbizonyosodjon arról, hogy megfelelően működik.
Paraméter optimalizálás
Kihívás
A különböző anyagok és vastagságok eltérő lézerteljesítményt, vágási sebességet és gáznyomást igényelnek. A nem megfelelő paraméterbeállítások a vágási minőség romlását, például megnövekedett sorjaképződést, vagy túl széles vagy túl keskeny bevágásokat eredményezhetnek.
Megoldás
- Készítsen részletes vágási paramétertáblázatokat a különböző anyagokhoz, hogy biztosítsa a teljesítmény és a sebesség pontos illeszkedését.
- Rendszeresen tesztelje a berendezés lézerkimenetét a stabil teljesítmény és fókusz biztosítása érdekében.
- Használjon segédszoftvert az automatizált paraméteroptimalizáláshoz a vágás hatékonyságának és minőségének javítása érdekében.
Kezelői képzés
Kihívás
A kezelő szakértelmének vagy jártasságának hiánya működési hibákhoz vezethet, növelheti a meghibásodási arányt és befolyásolhatja a vágási hatást.
Megoldás
- Rendszeresen biztosítson műszaki képzést a kezelőknek, hogy elsajátítsa a lézeres berendezések működési előírásait.
- Részletes berendezés kezelési útmutatókat készít, és műszaki támogatási csoportot állít fel a napi problémák megoldására.
- Vezessen be egy kezelői tanúsítási rendszert annak biztosítására, hogy a berendezést csak szakképzett személyek kezelhessék.
Folyamatos fejlesztés
Kihívás
A technológia és a piacok gyors változásai megkövetelik a vállalatoktól, hogy folyamatosan optimalizálják a gyártási folyamatokat és technológiákat, hogy versenyképesek maradjanak.
Megoldás
- Lean termelési koncepciók bevezetése, a termelési folyamatok folyamatos elemzése és optimalizálása, a hulladék csökkentése és a hatékonyság javítása.
- Kövesse nyomon a lézervágási technológia fejlődési trendjét, és azonnal frissítse a berendezéseket és szoftvereket.
- Gyűjtsön gyártási adatokat, elemezze a teljesítménymutatókat, és folyamatosan javítsa a forgácsolási paramétereket és működési eljárásokat.
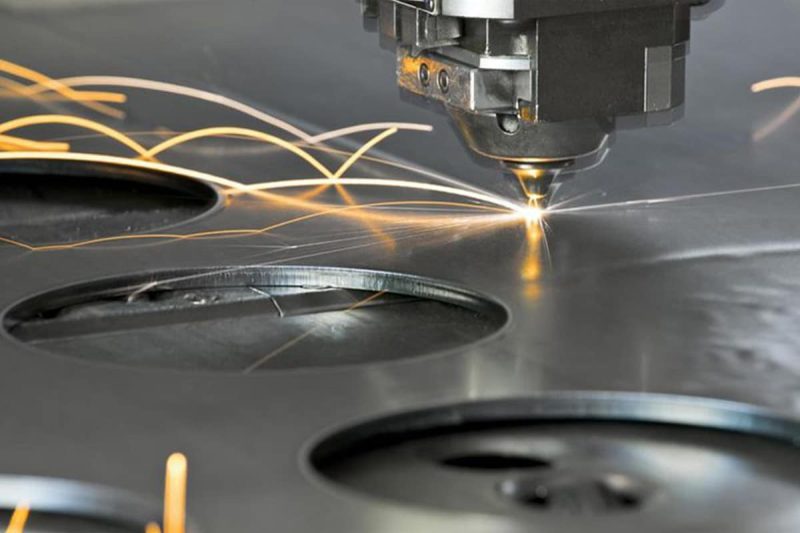
Összesít
A szálas lézervágás kihívásai számos szempontot érintenek, beleértve az anyagtulajdonságokat, a berendezés teljesítményét, a környezeti feltételeket stb. Rendszeres karbantartással, optimalizált paraméterekkel, továbbfejlesztett képzéssel és a fejlett technológia alkalmazásával a vágás minősége és hatékonysága jelentősen javítható. A megoldásokat eseti alapon kell megvalósítani a vágási folyamat stabilitásának javítása, valamint a gép állásidejének és karbantartási költségeinek csökkentése érdekében.
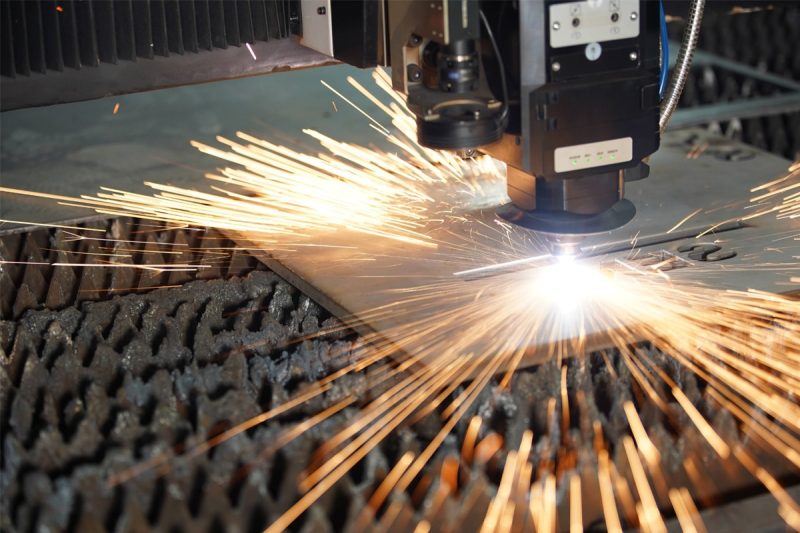
Szerezzen lézeres megoldásokat
A megfelelő szálas lézervágó gép kiválasztása segíthet az energiafogyasztás optimalizálásában és a magas működési hatékonyság elérésében. A megbízható beszállítóval való együttműködés biztosítja a hozzáférést a fejlett technológiához, a személyre szabott tanácsadáshoz és a folyamatos támogatáshoz. Az AccTek Lasernél a szálas lézervágó gépek átfogó választékát kínáljuk, amelyeket különféle ipari igények kielégítésére terveztek. Szakértőink segítenek kiválasztani a leginkább energiahatékony modellt és konfigurációt, figyelembe véve az olyan tényezőket, mint az anyagtípus, a vastagság és a gyártási mennyiség. Olyan élvonalbeli szolgáltatásokat is kínálunk, mint a nagy hatékonyságú lézergenerátorok, intelligens hűtőrendszerek és energiagazdálkodási szoftverek a teljesítmény maximalizálása és az energiafelhasználás minimalizálása érdekében. Ezen kívül csapatunk rendszeres karbantartási szolgáltatásokat és műszaki támogatást is nyújt, hogy berendezései a lehető legjobban működjenek. Ha velünk dolgozik, jelentős energiamegtakarítást érhet el, csökkentheti a működési költségeket és fokozhatja fenntarthatósági törekvéseit. Ha kérdése van, forduljon hozzánk időben, az AccTek Laser elkötelezett amellett, hogy minden vásárló számára tökéletes lézeres megoldásokat kínáljon!
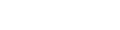
Elérhetőség
- [email protected]
- [email protected]
- +86-19963414011
- No. 3 A zóna, Lunzhen ipari zóna, Yucheng város, Shandong tartomány.
Szerezzen lézeres megoldásokat