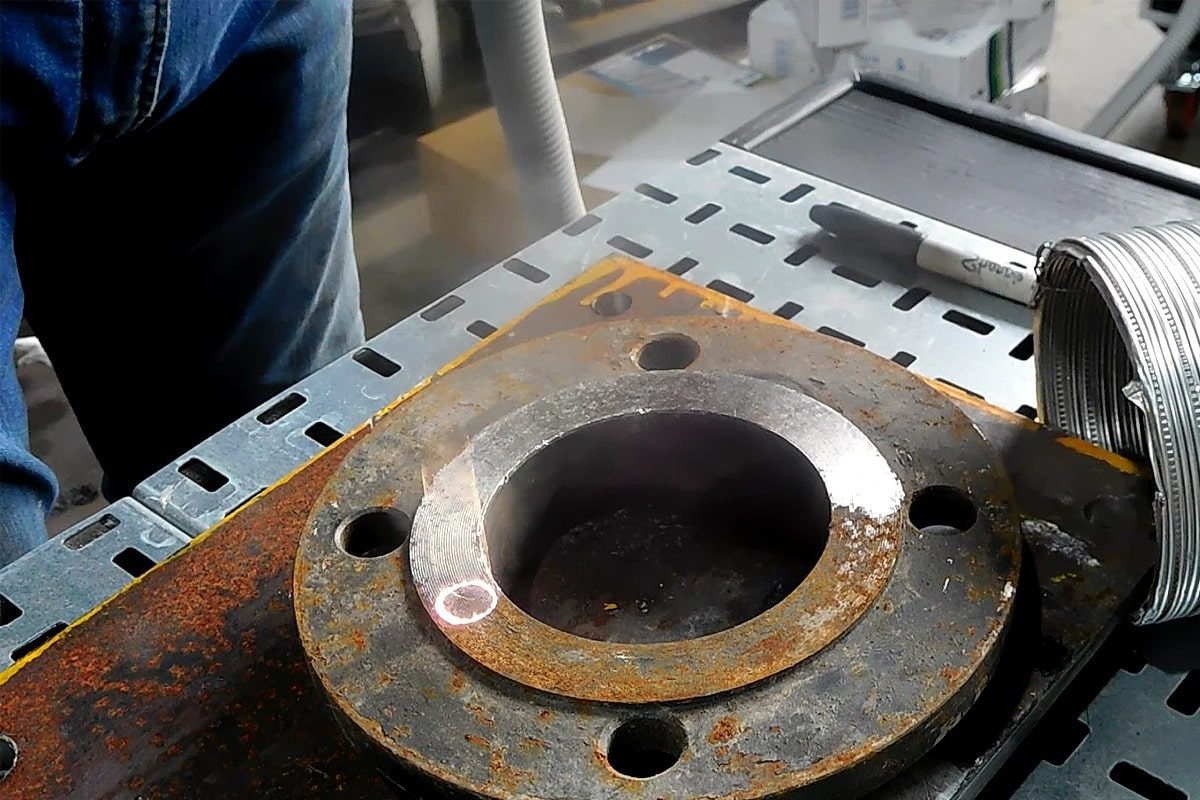
Az impulzuslézeres tisztítógépek előnyei és korlátai
Az ipari gyártási és tisztítási igények folyamatos növekedésével az impulzuslézeres tisztítás fokozatosan forradalmi tisztítási technológiává vált. Az impulzuslézerek nagy energiájának felhasználásával ez a technológia hatékonyan távolíthatja el a különféle szennyeződéseket anélkül, hogy károsítaná a hordozót. A hagyományos tisztítási módszerekkel összehasonlítva az impulzusos lézeres tisztításnak jelentős előnyei vannak, különösen olyan alkalmazásokban, mint a fémfelületek tisztítása, a korróziós réteg eltávolítása és a bevonat eltávolítása. Nemcsak eltávolítja az oxidokat, olajat és rozsdát, hanem precíz folttisztítást is lehetővé tesz, különösen összetett formák és precíziós alkatrészek esetén.
Ez a cikk elemzi az előnyeit és korlátait impulzuslézeres tisztítógépek mélységben, hogy segítsen teljes mértékben megérteni ennek a csúcstechnológiának a jellemzőit és alkalmazási lehetőségeit. Ugyanakkor azt is megvizsgáljuk, hogyan válasszuk ki a legmegfelelőbb impulzuslézeres tisztító megoldást különböző alkalmazási forgatókönyvek esetén, hogy segítsünk optimalizálni a berendezés használati és karbantartási költségeit, miközben biztosítjuk a hatékony tisztítást.
Tartalomjegyzék
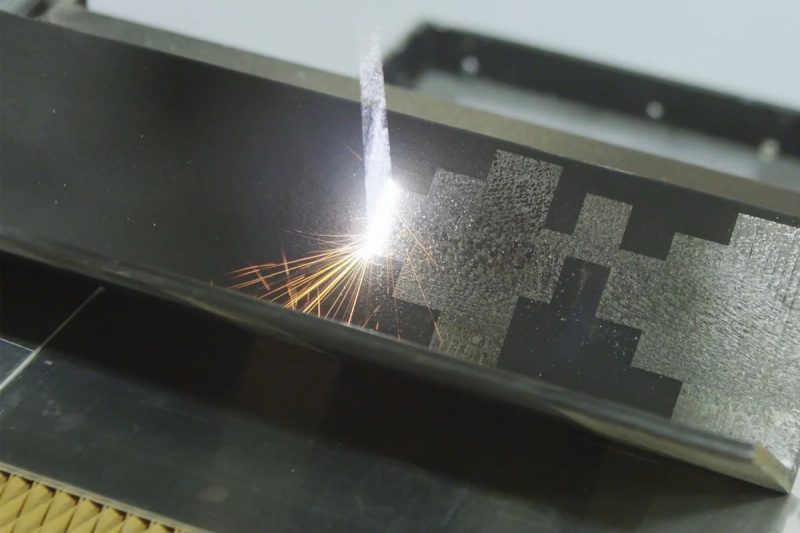
További információ a pulzáló lézeres tisztításról
Az impulzusos lézeres tisztítási technológia egy hatékony és környezetbarát felülettisztítási módszer, amely nagy energiájú lézerimpulzusok segítségével precízen fókuszált lézersugárral sugározza be a tisztítandó anyag felületét. A lézer energiája azonnal felmelegíti a felületet, amitől a szennyeződések (például olaj, rozsda, bevonatok stb.) gyorsan elpárolognak, oxidálódnak vagy felbomlanak, ezáltal tisztító hatás érhető el.
Az impulzusos lézeres tisztításnak jelentős előnye van a hagyományos mechanikai tisztítással, vegyi tisztítással vagy ultrahangos tisztítással szemben. A lézer pontosan tudja szabályozni az energiáját, hogy rövid időn belül befejezze a tisztítási folyamatot, miközben elkerüli a hordozó fizikai károsodását vagy kémiai szennyeződését. Ezzel az érintésmentes tisztítási módszerrel elkerülhető a hagyományos módszereknél megszokott kopás, korrózió vagy oldószeres szennyeződés.
A lézeres tisztítási technológia egyik fő előnye a nagy pontosság. A lézer paramétereinek beállításával bonyolult formák vagy szűk terek nagy energiával történő precíz tisztítása érhető el, ami különösen alkalmas olyan alkalmazásokhoz, mint a rozsda eltávolítása és a fémfelületek régi bevonatainak tisztítása. Emellett a lézeres tisztítás nem igényel kémiai oldószereket, elkerüli a káros hulladékok képződését, és nagyon csekély vízfogyasztást igényel, ami megfelel a modern ipar környezetvédelmi követelményeinek.
Összefoglalva, az impulzuslézeres tisztítás nagy pontosságának, érintésmentességének, nagy hatékonyságának és környezetvédelmének köszönhetően fokozatosan fontos technikai választássá vált a felülettisztítás területén.
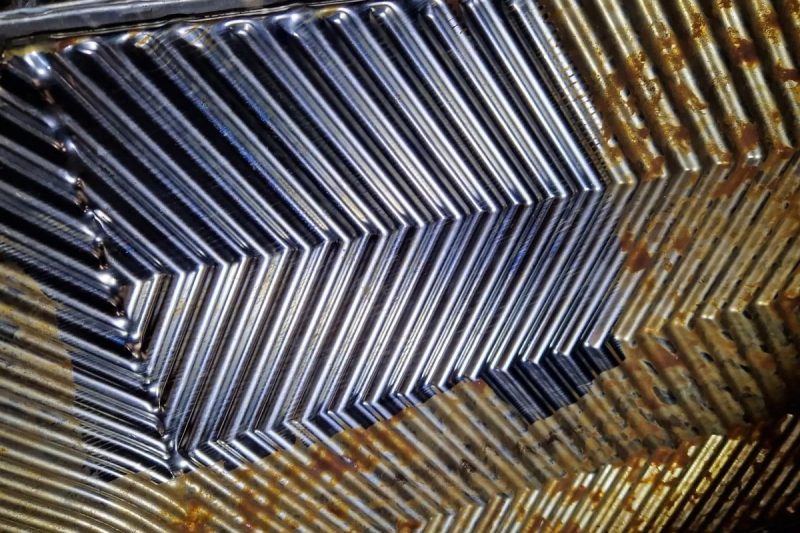
Az impulzuslézeres tisztítógép előnyei
Az impulzuslézeres tisztítási technológia egyedülálló nagy hatékonyságának és környezetbarátságának köszönhetően fokozatosan a modern ipari tisztítás kedvelt módszerévé vált. A hagyományos tisztítási módszerekkel összehasonlítva az impulzuslézeres tisztítógépek nemcsak nagy pontosságú tisztítási hatást biztosítanak, hanem nagymértékben javítják a termelés hatékonyságát és csökkentik a környezetterhelést. Az alábbiakban bemutatjuk az impulzuslézeres tisztítógépek fő előnyeit, amelyek segítenek megérteni, miért érdemes ezt a fejlett technológiát választania, és nagyobb értéket hozzon vállalkozása számára.
Precizitás és kontroll
Finomhangolási paraméterek: Az impulzuslézeres tisztítási technológia egyik legnagyobb tulajdonsága a precíz vezérlési képesség. Az olyan paraméterek finombeállításával, mint a lézerimpulzus energia, időtartama és frekvencia, a lézeres tisztítás rugalmasan állítható a különböző tisztítási igényekhez. Legyen szó finom szennyeződések eltávolításáról vagy a kényes részek felületének tisztításáról, a lézeres tisztítás kiváló pontosságot biztosít. Ezzel a vezérlési funkcióval a tisztítási folyamat mikron pontosságú lehet, elkerülve a munkadarab felületének szükségtelen károsodását. A nagy pontosságú tisztítást igénylő iparágakban, mint például a repülőgépipar, az autóipar és a nagy pontosságú berendezések gyártása, az impulzusos lézeres tisztítási technológia ideális megoldás.
Minimális sérülés: A hagyományos mechanikai vagy vegyi tisztítási módszerekkel ellentétben az impulzusos lézeres tisztítás érintésmentes tisztítási technológia. Ez azt jelenti, hogy a lézersugár csak a szennyeződésekkel érintkezik, a hordozóval nem, elkerülve az érintkezési tisztítás által okozott károkat. Ez különösen fontos precíziós alkatrészek és összetett felületek esetén, mert biztosítja, hogy magának az anyagnak a szerkezete és tulajdonságai nem változnak. Legyen szó fém felületről, műanyagról, kerámiáról vagy más anyagról, a lézeres tisztítás megőrzi az alapfelület épségét, és elkerüli a hagyományos tisztítási módszerek által okozott kopást vagy sérülést.
Környezetbarát és nem mérgező
Nincs vegyi hulladék: A hagyományos tisztítási módszerek általában nagy mennyiségű vegyi oldószer használatát teszik szükségessé, ami veszélyes hulladékok képződését eredményezi. Ezzel szemben az impulzusos lézeres tisztítás egy teljesen környezetbarát tisztítási technológia, amely egyáltalán nem támaszkodik vegyszerekre vagy tisztítószerekre. Ez nemcsak a vegyi hulladék képződését csökkenti, hanem a hulladék ártalmatlanításának és tárolásának költségeit is. A lézeres tisztítás lézerimpulzusokkal közvetlenül távolítja el a szennyeződéseket, elkerülve a vegyi anyagok használatát, és megfelel az egyre szigorúbb környezetvédelmi előírásoknak.
Csökkentett vízfogyasztás: A hagyományos tisztítási módszerek általában sok vízforrást igényelnek, ami különösen a vízhiányos területeken jelent problémát. Az impulzusos lézeres tisztítás nagymértékben csökkenti a vízfogyasztást és csökkenti a vízfogyasztást a tisztítási folyamat során. A vállalatok számára ez azt jelenti, hogy hatékony tisztítási eredményeket tudnak biztosítani a vízforrások pazarlása nélkül, és megfelelnek a fenntartható termelés követelményeinek. A vízfelhasználás csökkentésével a vállalatok költséget takaríthatnak meg és csökkenthetik a környezetre nehezedő terhelést.
A kezelők biztonsága: A lézeres tisztítási eljárás során nem keletkeznek káros vegyi gázok, szennyvíz vagy por, így biztosítva a kezelők biztonságát. A vegyszeres tisztításhoz képest a kezelőket nem kell mérgező vegyszereknek kitenni, csökkentve ezzel az egészségügyi kockázatokat. Ezenkívül az impulzuslézeres tisztítóberendezések általában fejlett kipufogógáz-kezelő rendszerekkel és szűrőberendezésekkel vannak felszerelve, amelyek hatékonyan távolítják el a tisztítási folyamat során esetlegesen keletkező apró részecskéket és füstöt, így tovább védik a kezelők légúti egészségét. A biztonság és a környezetvédelem ideális választássá teszi a lézeres tisztítást az ipari tisztításhoz, különösen az olyan iparágakban, amelyek magas követelményeket támasztanak a munkakörnyezet és az alkalmazottak egészsége tekintetében.
Hatékonyság és sebesség
Nagy áteresztőképesség: Az impulzusos lézeres tisztítási technológia rendkívül magas tisztítási hatékonyságot biztosít. Mivel a lézerimpulzusok azonnal nagy energiát szabadítanak fel és gyorsan eltávolítják a felületi szennyeződéseket, a teljes tisztítási folyamat nagyon rövid idő alatt elvégezhető. Ez azt jelenti, hogy a vállalatok több tisztítási feladatot tudnak rövidebb idő alatt elvégezni, és javítják a gyártósor hatékonyságát. A nagyüzemi gyártás során az impulzuslézeres tisztítás nagymértékben javíthatja a termelési teljesítményt. Különösen a kötegelt gyártási környezetben jelentősen lerövidítheti a gyártási ciklust és növelheti a teljes termelési kapacitást.
Minimális állásidő: A hagyományos mechanikus tisztítási módszerek általában hosszú előkezelést és várakozást igényelnek, míg az impulzuslézeres tisztítás nagy hatékonyságának köszönhetően jelentősen lerövidítheti az állásidőt. A gyártási folyamatban a berendezések állásideje közvetlenül befolyásolja a kimeneti és szállítási ciklust. Az impulzuslézeres tisztítás gyorsan befejezheti a tisztítási feladatot, és csökkentheti a gyártósor állásidejét, ami nagy előnyökkel jár a gyors szállítást és hatékony gyártást igénylő iparágak számára, mint például az autóipar, az elektronika, a repülés stb. Az állásidő csökkentése azt jelenti, hogy a vállalatok általánosságban javíthatnak a termelés hatékonyságát, ezáltal csökkentve a termelési költségeket.
Sokoldalúság
Anyagkompatibilitás: Az impulzuslézeres tisztítás nemcsak a rozsda- és olajfoltokat képes hatékonyan eltávolítani a fémfelületekről, hanem számos különböző anyag felületét is meg tudja dolgozni, beleértve a műanyagokat, kerámiákat stb. , lézeres tisztítással ideális tisztítási eredmény érhető el. Az anyagkompatibilitásnak ez a széles skálája a lézeres tisztítást a preferált tisztítási módszerré teszi számos iparágban, különösen azokban, amelyek több anyag gyártását és feldolgozását foglalják magukban.
Szennyezőanyagok eltávolítása: A lézeres tisztítás hatékonyan távolíthatja el a különböző típusú szennyeződéseket, beleértve a rozsdát, olajat, oxidrétegeket, bevonatokat stb. A hagyományos tisztítási módszerek gyakran sok időt és munkát igényelnek, míg az impulzusos lézeres tisztítás rövid időn belül pontosan eltávolítja ezeket a szennyeződéseket az anyag felületének károsodása nélkül. A lézeres tisztítás különösen bizonyos tisztítási feladatoknál, amelyek nagy pontosságot igényelnek, kiváló teljesítményt nyújthat. Például a repülőgépgyártás, az autógyártás stb. területén a lézeres tisztítással teljesen eltávolíthatók a precíziós alkatrészek felületéről a szennyeződések, így biztosítva a berendezés nagy teljesítményét és hosszú távú stabilitását.
Felületkezelés
A tapadás javítása: A tisztítás mellett az impulzusos lézeres tisztítás javíthatja az anyagok felületi tulajdonságait is. A lézerrel eltávolíthatók a rozsda, oxidrétegek és a régi bevonatok a fémfelületekről, javítva a későbbi bevonatok tapadását. A bevonatot, hegesztést vagy ragasztást igénylő anyagok esetében az impulzusos lézeres tisztítás ideálisabb felületet hozhat létre, javíthatja a bevonatok vagy ragasztók tapadását, valamint javítja a termék minőségét és tartósságát. A fémfelület-kezelés során a lézeres tisztítás nemcsak a felületi szennyeződéseket távolítja el, hanem hatékonyan javítja a felület mikroszerkezetét is, ideális alapot biztosítva a későbbi folyamatokhoz.
Továbbfejlesztett felületi tulajdonságok: Az impulzuslézeres tisztítás jelentősen javíthatja az anyagok felületi tulajdonságait, például javíthatja a korrózióállóságot, a kopásállóságot stb. Az oxidrétegek és a felesleges bevonatok eltávolításával a lézeres tisztítás simábbá és egyenletesebbé teheti az anyagfelületeket. Ez a felületkezelési képesség különösen alkalmas olyan iparágakban, ahol szigorú anyagteljesítmény-követelmények vannak, mint például a repülőgépipar, az autógyártás, az elektronikai berendezések stb. Az anyagok felületi minőségének javításával a lézeres tisztítás meghosszabbíthatja a termékek élettartamát és csökkentheti a karbantartási költségeket.
Az impulzuslézeres tisztítógép ideális választássá vált a modern ipari tisztításhoz nagy pontosságának, környezetkímélésének és nem toxikusságának, nagy hatékonyságának és sokoldalúságának köszönhetően. Pontosan tudja eltávolítani a szennyeződéseket az aljzat károsítása nélkül, és alkalmas különféle anyagok és összetett felületek tisztítási igényeire. A lézeres tisztítás nemcsak vegyszeres hulladékot nem tartalmaz, és csökkenti a környezetszennyezést, hanem nagymértékben javítja a termelés hatékonyságát és csökkenti a költségeket. A technológia folyamatos fejlődésével az impulzuslézeres tisztítógépek egyre több ipari területen kapnak majd szerepet, és válnak a vállalati termelés nélkülözhetetlen eszközeivé. Az impulzuslézeres tisztítás választása nagyobb tisztítási hatékonyságot és jobb gazdasági hasznot hoz vállalata számára.
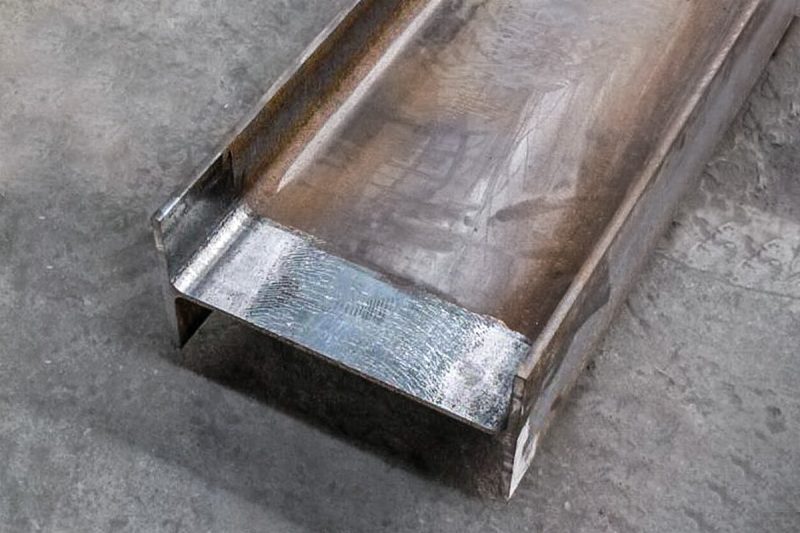
Az impulzuslézeres tisztítószerek korlátai
Míg az impulzusos lézeres tisztításnak számos jelentős előnye van, vannak korlátai is. A lézeres tisztítás használatának kiválasztásakor fontos megérteni ezeket a korlátozásokat, hogy megalapozottabb döntést hozhasson.
Magas kezdeti költség
- Tőkebefektetés: Az impulzuslézeres tisztítógép kezdeti beszerzési költsége viszonylag magas. A lézeres berendezések kutatás-fejlesztése, gyártása és műszaki integrációja sok befektetést igényel, ezért a cégeknek tőkebefektetést kell figyelembe venniük vásárláskor. Emiatt az impulzuslézeres tisztítóberendezések általában alkalmasak nagyüzemi gyártásra vagy csúcskategóriás alkalmazásokra, míg a kis- és középvállalkozások esetében előfordulhat, hogy a költségvetés alapján gondosan meg kell vizsgálni.
- Karbantartási költségek: Maga a berendezés magas költsége mellett a lézeres tisztítógépek karbantartása és javítása is költséges. A lézeres berendezések rendszeres kalibrálást és karbantartást igényelnek az optimális teljesítmény fenntartásához, amely magában foglalhatja a kulcsfontosságú alkatrészek, például a lézerforrás és a tisztítórendszer cseréjét. A nem megfelelő karbantartás vagy a nem megfelelő tartozékok használata a berendezés meghibásodásához vezethet, ami tovább növeli az üzemeltetési költségeket.
Energia fogyasztás
- Üzemeltetési költségek: Az impulzuslézeres tisztítógépek energiafogyasztása magas, különösen hosszú ideig tartó vagy nagy intenzitású munkavégzés esetén, és az energiafogyasztás az üzemeltetési költségeik fontos részét képezi. A hagyományos tisztítási módszerekkel összehasonlítva a lézeres tisztítás erősebb energiát igényel a nagy teljesítményű lézersugarak előállításához, ami hosszú távú használat esetén magas energiaköltséget eredményezhet. Ezért a vállalatoknak figyelembe kell venniük az energiahatékonysági szempontokat a beruházások során, különösen a magas energiaköltségű területeken.
- Környezeti hatás: A magas energiafogyasztás nemcsak gazdasági előnyökkel jár, hanem bizonyos hatásokkal is járhat a környezetre. Bár a lézeres tisztítás csökkenti a vegyi tisztítószerek szükségességét és csökkenti a vegyi hulladék kibocsátását, a magas energiafogyasztás továbbra is olyan tényező, amelyet figyelembe kell venni. A technológia fejlődésével a lézeres tisztítógépek energiahatékonysága javult, de továbbra is energiaellátást igényel, és folyamatos nagy terhelés mellett bizonyos környezetterhelést okozhat.
Korlátozott anyagkompatibilitás
- Fényvisszaverő felületek: A lézeres tisztítás kevésbé hatékony az erősen fényvisszaverő anyagokon. Például az olyan fémek, mint a réz és az alumínium erősen visszaverő felülettel rendelkeznek, ami megnehezíti a lézerenergia hatékony elnyelését, ami viszont befolyásolja a tisztító hatást. Ebben az esetben a tisztítási folyamat további teljesítményt és bonyolultabb technikai eszközöket igényelhet a kívánt tisztítási hatás eléréséhez.
- Átlátszó anyagok: A pulzáló lézeres tisztítási technológia hatékonyabb átlátszó anyagokon, például üvegen és műanyagon. Mivel az átlátszó anyagok fényelnyelési aránya alacsony, a lézer nem tud hatékonyan hatni a felületre, ami nagymértékben csökkenti a tisztítási hatékonyságot. Az ilyen anyagok esetében a lézeres tisztítás nem feltétlenül a legalkalmasabb tisztítási módszer.
- Vékony vagy törékeny anyagok: A lézeres tisztítás a nagyon vékony vagy törékeny anyagokra is korlátozódik. A lézer rövid időn belül sok energiát szabadít fel, ami túlmelegedést vagy felületi károsodást okozhat vékony anyagokon, különösen helytelen paraméterbeállítások esetén. Ezért az ilyen anyagok tisztítása különös gondosságot igényel, és további műszaki támogatást igényelhet.
biztonsági kérdés
- Szem- és bőrkárosodás: A lézeres tisztítás során a lézersugár nagy energiája károsíthatja a kezelő szemét és bőrét. A nagy teljesítményű lézerek, ha nem megfelelően működnek vagy nincsenek megfelelően védve, súlyos biztonsági baleseteket okozhatnak. Ezért a kezelőknek speciális védőszemüveget és védőruházatot kell viselniük a személyes biztonság érdekében.
- Füst- és részecskekibocsátás: A felületi szennyeződések eltávolításakor a lézeres tisztítás füstöt és apró részecskéket bocsáthat ki. Ezek a kibocsátások potenciális veszélyt jelenthetnek a kezelő légzőrendszerére és egészségére. Ezért a lézeres tisztítórendszert hatékony kipufogórendszerrel és füstelszívó berendezéssel kell felszerelni a káros anyagoknak való kitettség csökkentése érdekében.
Készségek és képzési követelmények
- Műszaki szakértelem: Az impulzuslézeres tisztítógépek üzemeltetése bizonyos műszaki szakértelmet igényel. A különböző anyagok, szennyeződések és tisztítási feladatok a lézerparaméterek pontos beállítását igénylik (például impulzus időtartama, energia, frekvencia stb.), és a kezelőknek megfelelő készségekkel és ismeretekkel kell rendelkezniük a legjobb tisztítási hatás biztosításához. A kezelők számára ezekben a készségekben való jártasság előfeltétele a lézeres tisztítógépek normál működésének.
- Képzési költségek: Az impulzusos lézeres tisztítógépek magas működési követelményei miatt a vállalatoknak időt és erőforrásokat kell befektetni az alkalmazottak képzésébe. Ezek a képzések általában a lézeres berendezések üzemeltetésével, biztonsági előírásaival, karbantartásával és vészhelyzeti elhárításával foglalkoznak. A képzési folyamat munkaerő- és időköltségét is figyelembe kell venni a vállalat teljes költségvetésében.
Bár az impulzusos lézeres tisztítógépeknek számos előnye van, korlátaik, például a magas kezdeti költség, az energiafogyasztási problémák, az anyagkompatibilitási korlátozások és a működési biztonsági követelmények továbbra is potenciális kihívást jelentenek. A lézeres tisztítási technológia kiválasztásakor a vállalatoknak átfogóan értékelniük kell ezeket a tényezőket, mérlegelni kell azok hosszú távú gazdasági hasznát és alkalmazhatóságát, és biztosítaniuk kell, hogy a termelési igényeiknek leginkább megfelelő tisztítási megoldást válasszák.
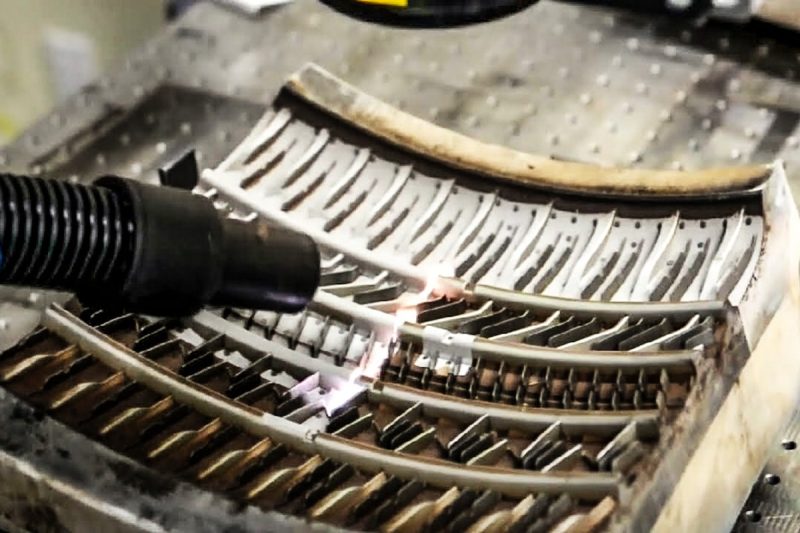
Hogyan lehet optimalizálni a pulzáló lézeres tisztítást
Az impulzuslézeres tisztítási technológia egy hatékony és környezetbarát tisztítási módszer, amelyet széles körben alkalmaznak különféle anyagok, például fémfelületek, műanyagok, kerámiák stb. tisztítására. Azonban az impulzuslézeres tisztítási hatás optimális biztosítása és a szolgáltatás kiterjesztése érdekében a berendezés élettartamát, a tisztítási folyamatot hatékonyan optimalizálni kell. Az impulzuslézeres tisztítás optimalizálása nemcsak javíthatja a tisztítási hatékonyságot és csökkentheti a berendezés meghibásodását, hanem a kezelők biztonságát is biztosítja. Az alábbiakban bemutatjuk, hogyan optimalizálhatja az impulzuslézeres tisztítási technológiát.
Paraméter optimalizálás
Az impulzuslézeres tisztítás hatékonysága szorosan összefügg a lézer különböző paramétereivel, beleértve az impulzus időtartamát, az impulzus energiáját, az ismétlési gyakoriságot és a hullámhossz kiválasztását. A tisztítási feladattól és az anyagtulajdonságoktól függően ezeknek a paramétereknek az optimalizálása kulcsfontosságú.
- Impulzus időtartama: Az impulzus időtartama az az időtartam, ameddig a lézerimpulzus felszabadul. A rövidebb impulzus időtartamok javíthatják a tisztítási hatékonyságot, mivel rövid időn belül nagy energiát szabadítanak fel, és gyorsan eltávolítják a szennyeződéseket. A hosszabb impulzus időtartamok olyan helyzetekben megfelelőek, amikor hosszabb időt vesz igénybe a szennyeződések eltávolítása vagy a szennyeződések vastag rétegeinek kezelése. A megfelelő impulzusidőtartam megválasztásával elkerülhető a túlzott hőfelhalmozódás, ami megakadályozhatja az aljzat károsodását.
- Impulzusenergia: A lézerimpulzus energiája határozza meg a tisztítási folyamat során a szennyeződések eltávolításának hatékonyságát. A magasabb impulzusenergiák alkalmasak a makacsabb szennyeződések (például vastag rozsda- vagy olajrétegek) eltávolítására, míg az alacsonyabb impulzusenergiák kényes tisztításra vagy olyan helyzetekre alkalmasak, ahol nem kívánatos az alapfelület károsodása. A különböző szennyeződések természetétől függően az impulzusenergia optimalizálásával a legjobb tisztítóhatás érhető el, miközben elkerülhető a túlzott tisztítás, amely károsíthatja az aljzatot.
- Ismétlési gyakoriság: Az ismétlési gyakoriság az egységnyi idő alatt kibocsátott lézerimpulzusok gyakoriságára vonatkozik. A nagyobb ismétlési arányok gyorsan, rövid időn belül eltávolíthatják a szennyeződéseket, és alkalmasak nagyméretű tisztítási feladatokra. Az alacsonyabb ismétlési arányok alkalmasak a kényes részek tisztítására, ami csökkentheti a hőfelhalmozódást és elkerülheti az aljzat károsodását. Az impulzus ismétlési gyakoriságának beállításával a tisztítási hatás és a tisztítási sebesség optimalizálható a különböző alkalmazási követelményeknek megfelelően.
- Hullámhossz kiválasztása: A lézer hullámhossza határozza meg a lézer kölcsönhatását különböző anyagokkal. A különböző anyagok eltérő abszorpciós jellemzőkkel rendelkeznek a különböző hullámhosszú lézereknél. A megfelelő hullámhossz megválasztásával javítható a lézeres tisztítás hatékonysága. Például egyes fémanyagok magasabb abszorpciós sebességgel rendelkeznek egy adott hullámhosszú lézereknél, amelyek hatékonyabban távolítják el a felületi szennyeződéseket. A hullámhossz optimalizálásával javítható a tisztítási hatás és csökkenthető a tisztítási idő.
Karbantartás és kalibrálás
Annak érdekében, hogy az impulzuslézeres tisztítógép optimális teljesítményt tartson fenn hosszú távú működés során, elengedhetetlen a rendszeres karbantartás és kalibrálás. A jó karbantartás nemcsak a berendezés élettartamát hosszabbítja meg, hanem egyenletes tisztítási eredményeket is biztosít.
- Rendszeres karbantartás: A lézertisztító berendezések rendszeres karbantartása magában foglalja a lézerforrás állapotának, a hűtőrendszer működésének ellenőrzését, az optikai alkatrészek tisztítását és az egyéb mechanikai alkatrészek karbantartását. Ezek a karbantartási intézkedések hatékonyan megakadályozhatják a berendezés por, szennyeződés vagy kopás miatti teljesítményromlását. Például a lézeroptikai lencse szennyezett lehet a lézerimpulzus nagy energiája miatt, és ezen részek rendszeres tisztítása segít megőrizni a tisztítóhatás stabilitását. Emellett a kopó alkatrészek rendszeres cseréje és az elektromos rendszer ellenőrzése is fontos intézkedés a berendezés normál működésének biztosításához.
- A rendszer kalibrálása: A kalibrálás kulcsfontosságú lépés a lézeres tisztítógép kimeneti stabilitásának biztosításához. Hosszabb ideig tartó használat után a lézerberendezések kimeneti teljesítménye, impulzusfrekvenciája stb. eltéréseket mutathat. Ezért nagyon fontos a lézerrendszer rendszeres kalibrálása. A kalibrációval gondoskodjon arról, hogy a lézersugár különféle paraméterei, mint például a teljesítmény, az impulzusfrekvencia, a hullámhossz stb. megfeleljenek a tervezési szabványoknak, ezáltal biztosítva a tisztítóhatás stabilitását és konzisztenciáját. Az egyes eszközök kalibrációs ciklusa változhat, és általában a berendezés használatának gyakoriságától és a munkakörnyezettől függően kerül meghatározásra.
Biztonsági intézkedések
Az impulzusos lézeres tisztítás során a lézersugár magas energiajellemzői miatt kritikus fontosságú a kezelő és a környezet biztonságának biztosítása. Íme néhány általános biztonsági intézkedés:
- Védőfelszerelés: Impulzuslézeres tisztítógép használatakor a kezelőnek speciális védőfelszerelést kell viselnie. A legfontosabb védőfelszerelés a lézeres védőszemüveg, amely hatékonyan gátolja a lézersugarak szemkárosodását. A szemvédelem mellett védőruházatot, kesztyűt stb. is kell viselni, hogy megvédje a testet a lézersugárzástól vagy az esetleges hőkárosodástól. Győződjön meg arról, hogy minden kezelő részt vett a szigorú biztonsági képzésen, megértette a lézeres berendezések veszélyeit, és elkerülheti a helytelen működés által okozott baleseteket.
- Füst elszívás: A lézeres tisztítási folyamat során a szennyező anyagok eltávolítása füst, részecskék vagy gázok képződését okozhatja, amelyek veszélyt jelenthetnek a kezelő egészségére. Ezért kulcsfontosságú, hogy hatékony füstelvezető rendszerrel rendelkezzünk. A rendszer azonnal eltávolítja a tisztítási folyamat során keletkező káros anyagokat, így biztosítva a működési környezet tisztaságát és biztonságát. Ezenkívül rendszeresen ellenőrizze a füstelvezető rendszert, hogy megbizonyosodjon arról, hogy megfelelően működik, és csökkenti a káros anyagoknak való kitettséget.
- Képzés és oktatás: A fizikai biztonsági felszerelések mellett a kezelő biztonságtudatossága és technikai felkészültsége is döntő jelentőségű. Rendszeres képzéssel és oktatással javítsa a kezelők megértését az impulzuslézeres tisztítóberendezésekről, és tegye lehetővé számukra a megfelelő működési módszerek és biztonsági előírások elsajátítását. A képzés tartalmának tartalmaznia kell a berendezések üzemeltetését, hibaelhárítását, biztonsági védelmi intézkedéseket, vészhelyzeti kezelési eljárásokat stb. A szisztematikus képzéssel csökkenthetők az üzemeltetési hibák, és elkerülhetők a biztonsági balesetek.
Az impulzusos lézeres tisztítási technológia optimalizálása nemcsak javítja a tisztítási eredményeket, hanem meghosszabbítja a berendezés élettartamát és csökkenti a karbantartási költségeket is. A lézerparaméterek, például az impulzus időtartama, az energia, az ismétlési sebesség és a hullámhossz optimalizálásával precíz tisztítási megoldások biztosíthatók a különböző tisztítási igényeknek és anyagtulajdonságoknak megfelelően. Ugyanakkor a berendezés rendszeres karbantartása és kalibrálása, valamint a szigorú biztonsági intézkedések biztosítják a berendezés stabilitását és üzembiztonságát hosszú távú használat során. Az átfogó optimalizálás révén az impulzusos lézeres tisztítási technológia maximalizálja a benne rejlő lehetőségeket, és magasabb termelési hatékonyságot és jobb gazdasági előnyöket biztosít a vállalkozások számára.

Összesít
Az impulzuslézeres tisztítógépek kiemelkedően nagy pontosságuk, nagy hatékonyságuk és környezetbarát tulajdonságaik miatt egyre fontosabb tisztítóeszközökké váltak a modern iparban. A hagyományos tisztítási módszerekkel összehasonlítva az impulzuslézeres tisztítás nemcsak precízebb és hatékonyabb tisztítási eredményeket biztosít, hanem érintésmentes és vegyszermentes tulajdonságainak köszönhetően nagymértékben csökkenti a környezetterhelést is. Emiatt az impulzuslézeres tisztítás az előnyben részesített tisztítási módszer számos iparágban (beleértve az autógyártást, a repülőgépgyártást, az elektronikát, a fémfeldolgozást stb.).
Természetesen, mint minden fejlett technológia, az impulzuslézeres tisztítógépek kezdeti beruházási és üzemeltetési költségei is viszonylag magasak. A lézeres berendezések beszerzése, karbantartása és üzemeltetése mind-mind bizonyos mértékű beruházást igényel, különösen a berendezések kezdeti telepítése és üzembe helyezése során a cégeknek szükségük lehet bizonyos tőkeköltségvetésre. De éppen a hatékony, precíz és sérülésmentes tisztítási teljesítménye miatt tapasztalta sok cég, hogy az impulzusos lézeres tisztítógépek nemcsak javítják a termelés hatékonyságát és csökkentik a hosszú távú karbantartási költségeket, hanem sok esetben az előnyöket és az időmegtakarítást is. hoz nem lehet figyelmen kívül hagyni. Ezért a speciális, nagy pontosságú és igényes ipari alkalmazásokban az impulzusos lézeres tisztítógépekbe való befektetés gyakran megéri.
A technológia folyamatos innovációjával és fejlődésével az impulzuslézeres tisztítógépek alkalmazási területe tovább bővül. A jövőben, ahogy a berendezések egyre érettebbek és a költségek fokozatosan csökkennek, az impulzuslézeres tisztítás várhatóan egyre több iparágban fog megjelenni, és egyre több vállalat számára válik a preferált tisztítási megoldássá. Manapság, amikor a környezetvédelem egyre nagyobb figyelmet kap, az impulzuslézeres tisztítás környezeti előnyei a jövőbeli fejlődés fontos irányvonalává is teszik.
Ha bármilyen kérdése van az impulzuslézeres tisztítógépek alkalmazásával vagy a teljesítményük optimalizálásával kapcsolatban, vagy szeretne többet megtudni AccTek Laser lézeres tisztító megoldások, kérjük, forduljon hozzánk bizalommal. Csapatunk készséggel áll rendelkezésére professzionális tanácsokkal, hogy megtalálja az Ön igényeinek leginkább megfelelő tisztítási megoldást. Akár érdekli a berendezés, akár többet szeretne megtudni a technológia mögött meghúzódó alapelvekről, részletes válaszokat adunk Önnek, hogy segítsen a legmegfelelőbb választásban.
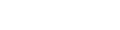
Elérhetőség
- [email protected]
- [email protected]
- +86-19963414011
- No. 3 A zóna, Lunzhen ipari zóna, Yucheng város, Shandong tartomány.
Szerezzen lézeres megoldásokat