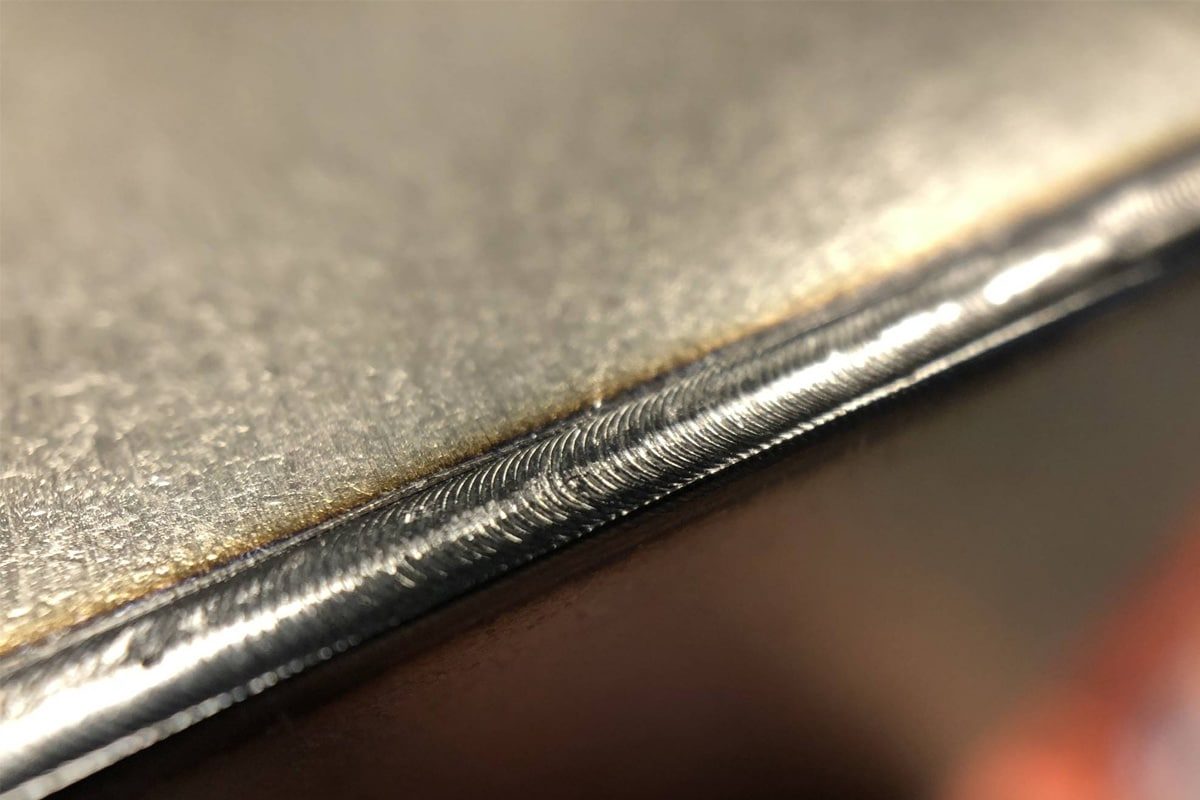
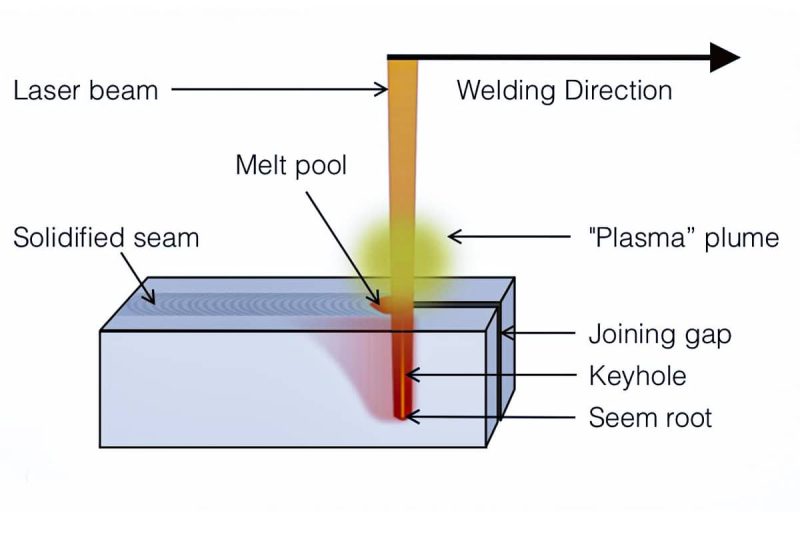
A lézeres hegesztés megértése
A lézeres hegesztés alapjai
Lézeres hegesztés típusa
- Folyamatos hullámú lézerhegesztés: hosszú távú, nagy intenzitású hegesztési igényekre alkalmas, széles körben használják vastag fémlemezek csatlakoztatására és tömítésére.
- Impulzuslézeres hegesztés: rövid távú, nagy energiájú impulzusokkal melegíti fel az anyagot, alkalmasabb vékony lemezek vagy mikroelemek hegesztésére, nagyobb szabályozási pontossággal.
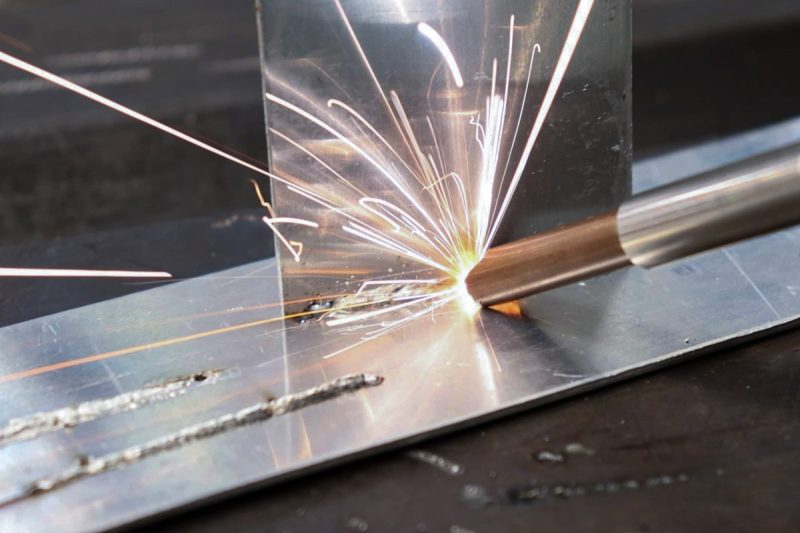
A hegesztési varrat szélességét befolyásoló tényezők
Lézer paraméterek
- Lézerteljesítmény: A lézerteljesítmény az egyik legkritikusabb paraméter, amely befolyásolja a hegesztési eredményeket. Minél nagyobb a lézerteljesítmény, annál több hő keletkezik, és megnő a hőhatászóna és az olvadt medence térfogata is, ami növeli a hegesztési varrat szélességét. Ezzel szemben, ha a teljesítmény túl alacsony, nem tud elegendő energiát biztosítani az anyag megolvasztásához, és a hegesztési kötés is elégtelen lehet, ami szűk hegesztést vagy hiányos hegesztést eredményezhet. Ezért a lézerteljesítményt ésszerűen meg kell választani az anyag vastagsága, típusa és hegesztési sebessége szerint, hogy elérjük a varrat optimális szélességét.
- Hegesztési sebesség: A hegesztési sebesség fontos hatással van a hőbevitelre. Ha a hegesztési sebesség alacsony, a lézer hosszabb ideig marad a hegesztési területen, ami több hőátadást eredményez az alapanyag felé, nagyobb olvadékmedencét és hőhatászónát képezve, ezáltal megnő a hegesztési szélesség. Ezzel szemben a túl nagy hegesztési sebesség csökkenti a hőbevitelt, ami nem teljes hegesztést, túl keskeny varratokat és esetleg gyenge varratokat eredményez. Ezért a hegesztési sebesség ésszerű szabályozása a kulcs a megfelelő hegesztési szélesség biztosításához.
- Hullámhossz: A lézer hullámhossza határozza meg, hogy a lézer hogyan lép kölcsönhatásba az anyaggal. A rövid hullámhosszú lézereket (például a szálas lézergenerátorok által kibocsátottakat) jobban el tudják nyelni a fémanyagok, mert nagyobb az energiakoncentrációjuk, és kisebb területen is több energiát tudnak biztosítani, ezáltal javul a hegesztés hatékonysága és keskenyebb a varrat. Viszonylagosan elmondható, hogy a hosszú hullámhosszú lézerek (például a CO2 lézercsövek által kibocsátottak) a fémanyagokat rosszul abszorbeálják, és a hegesztés közbeni energiaeloszlás viszonylag széles, ami könnyen nagyobb hegesztési szélességhez vezet. Ezért a rövid hullámhosszú lézerek alkalmasabbak nagy pontosságú hegesztésre.
- Impulzus időtartama: Az impulzusos lézerhegesztés egyedülálló előnye, hogy az impulzus időtartamának beállításával optimalizálja a hegesztést. Minél rövidebb az impulzus időtartama, annál rövidebb a lézer hőbeviteli ideje, ami segít csökkenteni a hőhatás zóna tágulását és kisebb hegesztést képez. A hosszabb impulzus időtartamok nagyobb hőbevitelt és szélesebb hegesztést eredményeznek. Az impulzusalakító technológiával a lézer impulzusszélessége és intervalluma pontosan szabályozható, így optimalizálható a hőeloszlás és a hegesztési morfológia a hegesztés során.
- Sugárminőség: A lézersugár minősége és fókuszszabályozása kritikus fontosságú a hegesztési pontosság szempontjából. A jobb sugárminőségű lézerek kisebb fókuszmérettel és koncentráltabb energiával rendelkeznek, ami nagyobb pontosságú hegesztést tesz lehetővé. A jobb sugárminőség csökkenti a hő diffúziót, így a hő jobban koncentrálódik a hegesztési területen, és kisebb lesz a hegesztési szélesség. Ha a sugár minősége rossz, az a lézerenergia egyenetlen eloszlását okozza, ami növeli a hegesztési varrat szélességét.
Anyagtulajdonságok
- Abszorpciós sebesség: Az anyagnak a lézerhez való abszorpciós sebessége közvetlenül befolyásolja a hegesztési hatást. A fémanyagok abszorpciós sebessége általában magas, különösen, ha a rövid hullámhosszú lézert a fémhez illesztjük, az abszorpciós sebesség tovább javul. A lézeres hegesztési eljárásban a nagyobb abszorpciós sebesség azt jelenti, hogy a lézerenergia hatékonyan hőenergiává alakítható, ami kisebb hegesztést eredményez. Ezzel szemben, ha az anyag abszorpciós sebessége alacsony, a lézerenergia effektív kihasználtsága gyenge, ami a hegesztés túl szélességét vagy hiányosságát okozhatja.
- Hővezető képesség: Az anyag hővezető képessége befolyásolja a hő diffúziós sebességét az aljzatban. Magasabb hővezető képességű anyagok (pl réz és alumínium) gyorsan eloszlatja a hőt, ami túlzott hőeloszlást eredményez a hegesztési területen és szélesebb hegesztési varratokat. Ezzel szemben az alacsonyabb hővezető képességű anyagok (pl rozsdamentes acél) több hőt tud koncentrálni a hegesztési területen, keskenyebb varratot képezve. Ezért a különböző hővezető képességű anyagok hegesztésekor a hegesztési paramétereket a termikus tulajdonságaik szerint kell beállítani, hogy a hegesztési szélesség megfelelő legyen.
- Reflexiós képesség: A nagy fényvisszaverő képességű anyagok (például alumínium és réz) jobban visszaverik a lézert, és csökkentik a lézerenergia abszorpciós hatékonyságát, ezáltal befolyásolják a hegesztés minőségét, és a hegesztési szélesség növekedését okozhatják. Ennek a problémának a megoldására választhat olyan lézertípust, amely alkalmas erősen visszaverő anyagokhoz (például rövid hullámhosszú lézer használata), vagy növelheti a lézerteljesítményt a visszaverődési veszteség kompenzálására. Ezen túlmenően a fókuszált sugár és a megfelelő lézerhullámhossz használata hozzájárulhat a visszaverő anyagok lézerelnyelési sebességének növeléséhez.
Hegesztési környezet
- Védőgáz: A védőgáz fontos szerepet játszik a lézeres hegesztésben. Nemcsak az oxidációt és a szennyeződést akadályozza meg a hegesztés során, hanem a gázáramlás szabályozásával befolyásolja a hővezetést és a hegesztési varrat szélességét is. Például az argont és a nitrogént gyakran használják védőgázként a lézeres hegesztésben. Hatékonyan csökkenthetik a hőhatás zóna hatótávolságát, és elkerülhetik a túlzott hegesztési varratok kialakulását. A védőgáz kiválasztását és szabályozását az adott anyagokhoz és hegesztési követelményekhez kell igazítani.
- Környezeti feltételek: A környezeti tényezők, például a hőmérséklet és a páratartalom szintén befolyásolják a lézerhegesztés hatását. Alacsony hőmérsékletű környezetben a fémanyagok hővezető képessége megváltozhat, ami befolyásolja a hegesztés során a hőgazdálkodást. Ezenkívül a magas páratartalmú környezet a lézerenergia szórását okozhatja, és ronthatja a hegesztés minőségét. A stabil környezeti feltételek segítenek megőrizni a lézersugár stabilitását és biztosítják a hegesztési szélesség állandóságát a hegesztés során.
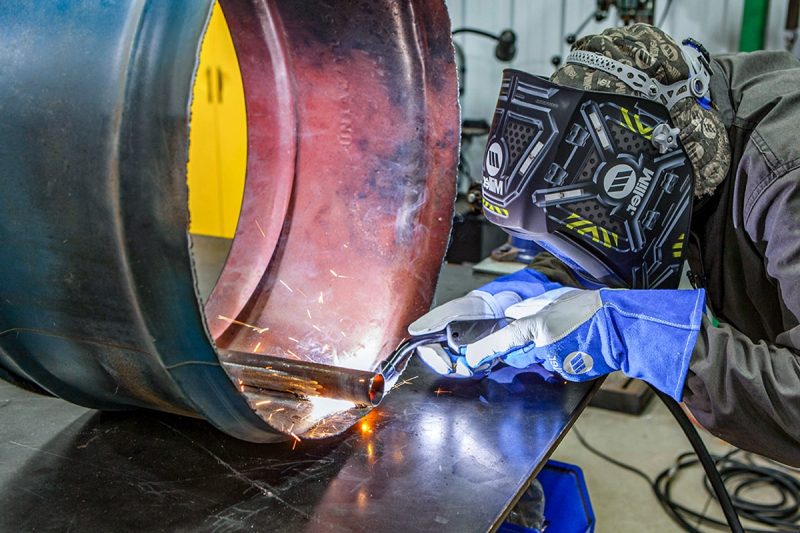
Technológia a minimális hegesztési szélesség elérésére
Lézer típus kiválasztása
- Szálas lézergenerátor: A szálas lézergenerátor az egyik legszélesebb körben használt lézerforrás a lézerhegesztésben. Nagy teljesítményű, kiváló sugárminőséggel és kiváló fókuszáló képességgel rendelkezik. A szálas lézergenerátor sugara nagyon kis területre precízen fókuszálható, így a hegesztési varrat szélessége kisebb és vékony lemezanyagok hatékony feldolgozására képes. A szálas lézergenerátorok kiválóan alkalmasak a nagy pontosságú és gyors hegesztési feladatokra, és kiváló minőségű kis hegesztéseket tesznek lehetővé, és csökkentik az anyag hőhatászónájának (HAZ) tágulását.
- CO2 lézercső: A CO2 lézercső egy másik fémhegesztéshez általánosan használt lézerforrás. Bár a CO2 lézercsövek sugárminősége általában nem olyan jó, mint a szálas lézergenerátoroké, nagyobb teljesítményt és mélyebb behatolási mélységet tud biztosítani, ami vastagabb anyagok hegesztésére alkalmas. Bár nem olyan pontos, mint a szállézer, viszonylag kis hegesztési szélesség érhető el ésszerű teljesítményszabályozással és optimalizált hegesztési sebességgel.
Lézeres hullámhossz kiválasztása
Lézeres paraméterek optimalizálása
- Lézerteljesítmény beállítása: A lézerteljesítmény a fő tényező, amely befolyásolja a hegesztési hőbevitelt. A túlzott teljesítmény túlzott hő terjedését okozza a környező területen, ezáltal kiszélesíti a hegesztést, és akár hegesztési hibákat is okozhat. A teljesítmény megfelelő csökkentésével csökkenthető a hőbevitel és szűkíthető a hegesztési szélesség, különösen vékony lemezanyagok hegesztésekor. A túl alacsony teljesítmény azonban nem megfelelő hegesztést eredményezhet. Ezért a lézerteljesítmény ésszerű beállításával, hogy az megfeleljen az anyag tulajdonságainak, a hegesztési sebességnek és a hegesztési követelményeknek, precíz hegesztés érhető el, és hatékonyan szabályozható a hegesztési szélesség.
- Impulzus-alakító technológia: Az impulzuslézeres hegesztési technológia a lézerimpulzus frekvenciájának, időtartamának és energiájának beállításával pontosan szabályozhatja a hegesztés közbeni hőbevitelt. Minél rövidebb az impulzus szélessége, annál rövidebb a hőbeviteli idő, és annál kevesebb hő halmozódik fel a hegesztési területen, ami szűkebbé teszi a hegesztést. Ezenkívül az impulzusfrekvencia és az energia beállításával szabályozható a hegesztési sebesség és az olvadt medence morfológiája, ami viszont befolyásolja a varrat szélességét. Az impulzusalakító technológia használatával, különösen a mikrohegesztésnél, minden impulzus hőeloszlása pontosan szabályozható a minimális hegesztési szélesség hatékony elérése érdekében.
- Sugárfókusz szabályozás: A lézeres hegesztés pontossága és hegesztési szélessége szorosan összefügg a sugár fókuszpozíciójával. Minél kisebb a lézersugár fókusza, annál nagyobb az energiasűrűség, amely a hegesztési területen koncentrálódik, így keskeny és finom varrat keletkezik. Ezért a lézeres fókuszvezérlés nagyon fontos. A fókuszpozíció beállításával a lézersugár energiája jobban koncentrálható a hegesztési területen, elkerülve a hő diffúzióját a környező területre, és ezáltal csökkentve a hegesztési varrat szélességét.
Anyag előkészítés
- Felületi tisztaság: A hegesztőanyag felületi tisztasága közvetlenül befolyásolja a lézerhegesztés hatását. A felületen lévő oxidok, olaj, rozsda és egyéb szennyeződések befolyásolják a lézer abszorpciós sebességét, ami azt eredményezi, hogy nem tudja hatékonyan koncentrálni a hőt a hegesztési területen, ami befolyásolja a hegesztés minőségét és növeli a varrat szélességét. A hegesztési felület tisztaságának és szennyeződésmentességének biztosítása a hegesztési minőség optimalizálásának előfeltétele. A felületi szennyeződések általában vegyszeres tisztítással, mechanikai tisztítással vagy lézeres tisztítással távolíthatók el.
- Felületi bevonat: Bizonyos esetekben, különösen a nehezen hegeszthető anyagok esetében, a felületbevonat jelentősen javíthatja a lézer abszorpciós hatékonyságát. A bevonóanyagok (például rézbevonat, horganyzás stb.) javíthatják a lézer és az anyag közötti kölcsönhatást, és fokozhatják a hőfelhalmozódást a hegesztési területen, ezáltal segítve a hegesztési folyamat során a hegesztési varrat szélességének pontos szabályozását. Ezenkívül a speciális bevonatok javíthatják az olvadt medence stabilitását a hegesztés során, és csökkenthetik a hegesztés során fellépő hibákat.
Fejlett hegesztési technológia
- Hibrid lézeres hegesztés: A hibrid lézeres hegesztési technológia egyesíti a lézeres és a hagyományos hegesztési módszerek (például AWI-hegesztés vagy MIG-hegesztés) előnyeit, és javítja a hőbevitelt és a hegesztési pontosságot a különböző hőforrások előnyeinek kombinálásával. A lézeres és a hagyományos hegesztési módszerek kombinációja hatékonyan csökkentheti a varrat szélességét, különösen vastagabb anyagok hegesztésekor. A hibrid lézeres hegesztési technológia nagyobb olvadékmedence-stabilitást és kisebb hőhatású zónákat biztosít, ezáltal finomabb hegesztési hatásokat érhet el.
- Mikrohegesztési technológia: A mikrolézeres hegesztés egy nagy pontosságú hegesztési technológia ultra-kis varratok feldolgozására, különösen alkalmas apró alkatrészek összekapcsolására. A mikrohegesztési technológia finoman szabályozott lézerimpulzusokat használ a hatékony energiaátvitel érdekében nagyon kis hegesztési területen, biztosítva a nagyon keskeny hegesztési varratok kialakulását. A mikrohegesztést általában olyan iparágakban használják, mint az elektronika, a precíziós műszerek és az orvosi eszközök, és nagy hegesztési pontosságot érhet el, és minimálisra csökkentheti a hegesztési terület hőhatását.
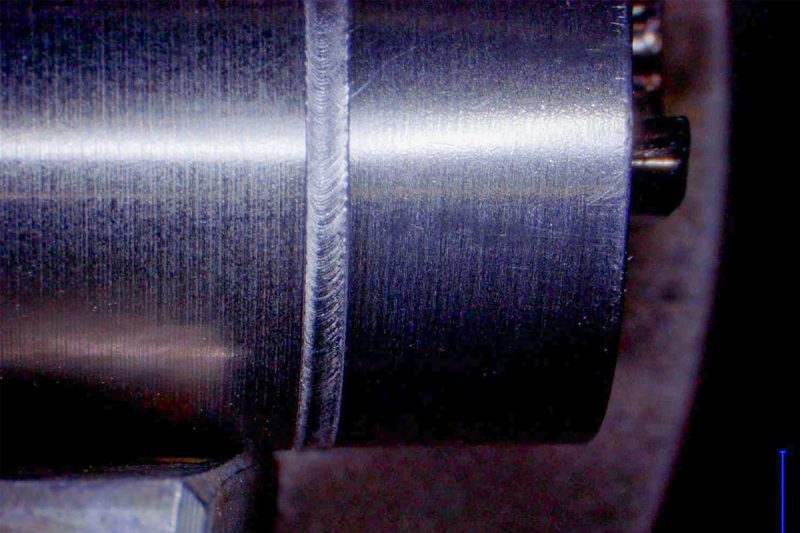
Kihívások és megoldások
Hőkezelés
Kihívás
Megoldás
- Használjon segédgázos hűtést: Megfelelő védőgáz vagy segédgáz (például argon, nitrogén vagy oxigén) használatával nem csak a hegesztési terület oxidációját akadályozhatja meg, hanem hatékonyan távolítja el a hegesztés során keletkező felesleges hőt, ezáltal csökkenti a hőhatás zóna tágulását. A legjobb hűtőhatás biztosítása érdekében a segédgáz áramlási sebességét és nyomását a hegesztőanyag, a hegesztési sebesség és a lézerteljesítmény szerint optimalizálni kell.
- Hegesztési sebesség optimalizálása: A hegesztési sebesség megfelelő növelésével csökkenthető az időegységenkénti hőbevitel és az anyag melegítési ideje, ezáltal hatékonyan elkerülhető a hegesztési terület túlmelegedése. Nagyobb hegesztési sebesség esetén a hő gyorsan terjedhet nagyobb területre, csökkentheti a helyi hőmérséklet-emelkedést, és így szabályozható a hegesztési szélesség és a hőhatás zóna.
- Hőforrás szabályozás: A lézerteljesítmény beállításával vagy impulzuslézer használatával a hőbevitel pontosan szabályozható a hegesztési folyamat során. Különösen az impulzushegesztésnél a rövid impulzusok és a magasabb impulzusfrekvenciák biztosíthatják a hő gyors fókuszálását és eloszlását a hegesztési területen a hő diffúzió elkerülése érdekében.
Anyagvisszaverő képesség
Kihívás
Megoldás
- Használjon rövid hullámhosszú lézereket: A rövid hullámhosszú lézerek (például a szálas lézergenerátorok által előállított lézerek) nagyobb abszorpciós rátával rendelkeznek a nagy fényvisszaverő anyagok esetén. A rövid hullámhosszú lézereket jobban elnyelik az anyagok, csökkentik a visszaverődést, és biztosítják, hogy a hegesztési folyamat során több lézerenergiát hasznosítsanak, ezáltal javul a hegesztési hatékonyság és csökken a hegesztési szélesség. A hosszú hullámhosszú CO2 lézerekhez képest a szálas lézergenerátorok alkalmasabbak nagyobb visszaverőképességű anyagok feldolgozására.
- Lézerteljesítmény beállítása: Nagy fényvisszaverő képességű anyagok esetén a lézerteljesítmény megfelelő csökkentésével elkerülhető a túlzott energiavisszaverődés. Az alacsonyabb teljesítmény-beállítások segítenek csökkenteni a tükröződést és elkerülni az energiapazarlást, ezáltal hatékonyan szabályozzák a hegesztési varrat szélességét és optimalizálják a hegesztési minőséget.
- Használjon bevonatos anyagokat: Egyes erősen fényvisszaverő fémanyagok, például alumínium és réz, bevonási technológiát alkalmazhatnak, mint például az alumínium bevonat bevonása, a rézbevonat és más felületkezelési módszerek. Ezeknek a bevonatoknak kisebb a visszaverő képessége, ami javíthatja a lézer abszorpciós hatékonyságát, és csökkentheti a hegesztési folyamatra gyakorolt visszaverődés interferenciáját, ezáltal jobban szabályozható a hegesztési szélesség.
Folyamatstabilitás
Kihívás
Megoldás
- Fejlett lézervezérlő rendszer: Fejlett lézeres vezérlőrendszerek használatával az olyan kulcsparaméterek, mint a lézerteljesítmény, hegesztési sebesség, sugárfókusz stb., valós időben figyelhetők és állíthatók, hogy biztosítsák a lézerparaméterek konzisztenciáját minden hegesztési folyamat során. A modern lézeres hegesztőrendszerek általában nagy pontosságú érzékelőkkel és automatikus beállítási funkciókkal vannak felszerelve, amelyek valós időben képesek érzékelni a hegesztési terület hőmérsékletét, az olvadt medence morfológiáját és a sugár helyzetét, és automatikusan beállítják a lézerkimenetet a hegesztési folyamat stabilitásának megőrzése érdekében.
- Valós idejű visszacsatolás és zárt hurkú vezérlés: A valós idejű visszacsatolás és a zárt hurkú vezérlési technológia valós időben állíthatja be a paramétereket a hegesztési folyamat során, hogy megbirkózzanak az anyagtulajdonságok és a hegesztési környezet változásaival. Például az érzékelők figyelhetik az olvadt medence méretét, alakját és hőmérsékletét, és a rendszer automatikusan beállíthatja a lézer teljesítményét és a hegesztési sebességet a hegesztési minőség állandóságának megőrzése érdekében. Ezzel a technológiával jelentősen javítható a hegesztési folyamat megbízhatósága és elkerülhetőek a folyamatingadozások okozta hegesztési problémák.
- Hegesztési út optimalizálása: A hegesztési folyamat során a lézerút tervezésének optimalizálása egy másik fontos módja a folyamatstabilitás javításának. A hegesztési út és hegesztési sorrend pontos szabályozásával csökkenthető az anyag deformációja és a hőhatászónában bekövetkező változások, így biztosítható az egyenletes hőmérsékleteloszlás minden hegesztési folyamat során, és ezáltal stabil hegesztési eredmény érhető el.
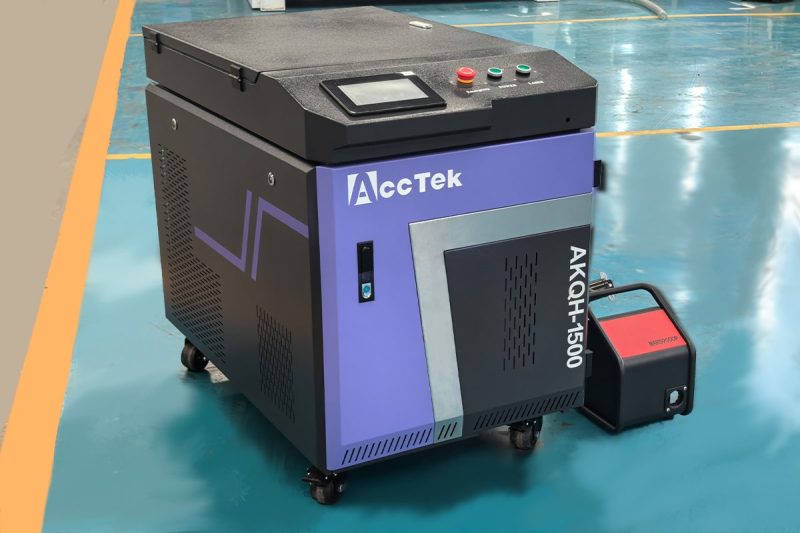
Összesít
Ebben a folyamatban a mi lézeres hegesztőgépek kiváló technológiájukkal és innovatív kialakításukkal az iparág vezetőivé váltak. Cégünk lézeres hegesztőgépei a legújabb szállézeres technológiát alkalmazzák, mellyel hatékony hegesztés érhető el, miközben a hegesztési folyamat során pontos hőmérsékletszabályozást biztosítanak, ezáltal hatékonyan szabályozzák a varrat szélességét és csökkentik a hőhatászónát. Hegesztőberendezéseink nemcsak nagy pontosságú lézersugár-beállítási lehetőségekkel rendelkeznek, hanem fejlett hőmérséklet-szabályozó rendszerrel is fel vannak szerelve, amely automatikusan be tudja állítani a paramétereket a hegesztési folyamat során, ezáltal optimalizálja a hegesztési hatást, és stabil és állandó minőséget biztosít minden hegesztési ponton.
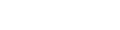
- [email protected]
- [email protected]
- +86-19963414011
- No. 3 A zóna, Lunzhen ipari zóna, Yucheng város, Shandong tartomány.