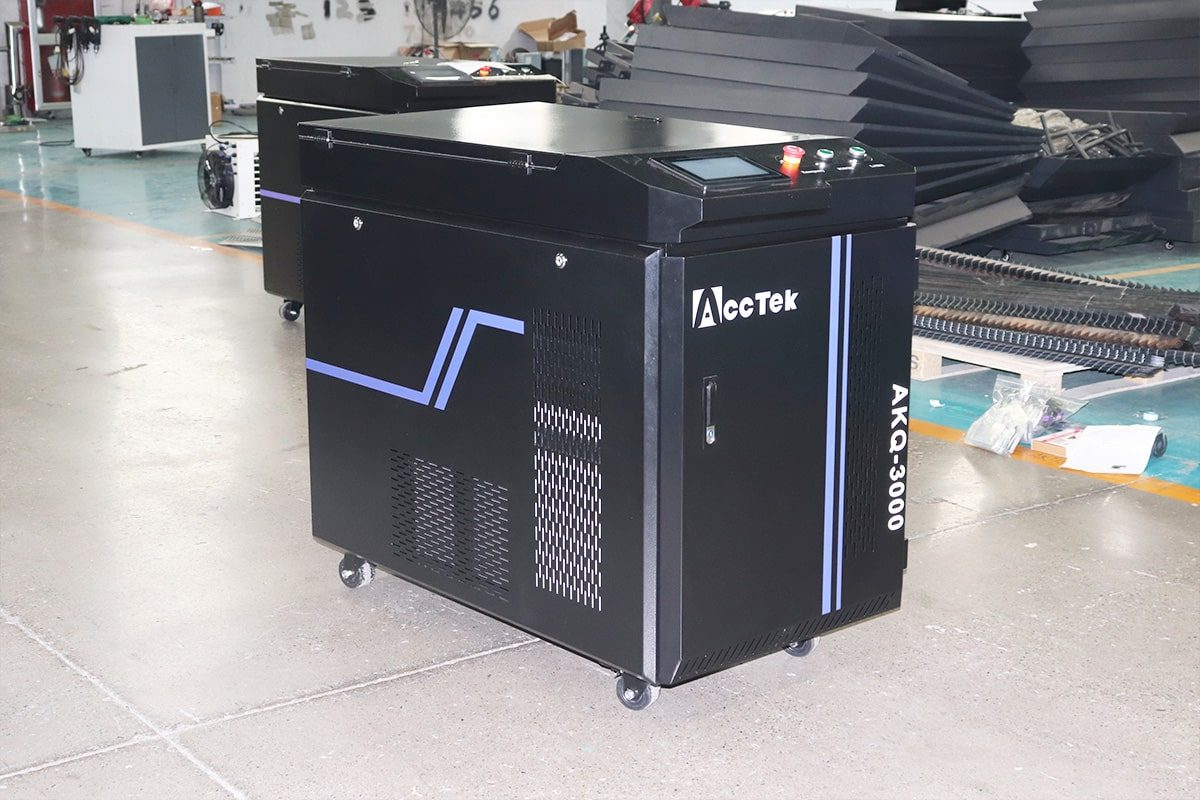
Hogyan válasszuk ki a megfelelő lézeres tisztítórendszert: kulcsfontosságú tényezők
As a non-contact surface treatment technology, lézeres tisztítás systems have been widely used in many industries, including manufacturing, automotive industry, aerospace and cultural heritage protection. Its high efficiency, environmental protection and low maintenance make it an increasingly popular choice for removing rust, paint, oxides and other contaminants from the surface of materials. Compared with traditional cleaning methods (such as chemical cleaning, sandblasting, etc.), laser cleaning has the advantages of no damage to materials, no chemical residue, and precise control.
However, selecting the right laser cleaning system is not simple, as the requirements and materials of each application are different. To ensure optimal performance and benefits, users must consider a variety of key factors when selecting a system, including laser source type, power range, cooling system, and safety compliance. By comprehensively analyzing these factors, users can find the solution that best suits their specific application.
Tartalomjegyzék
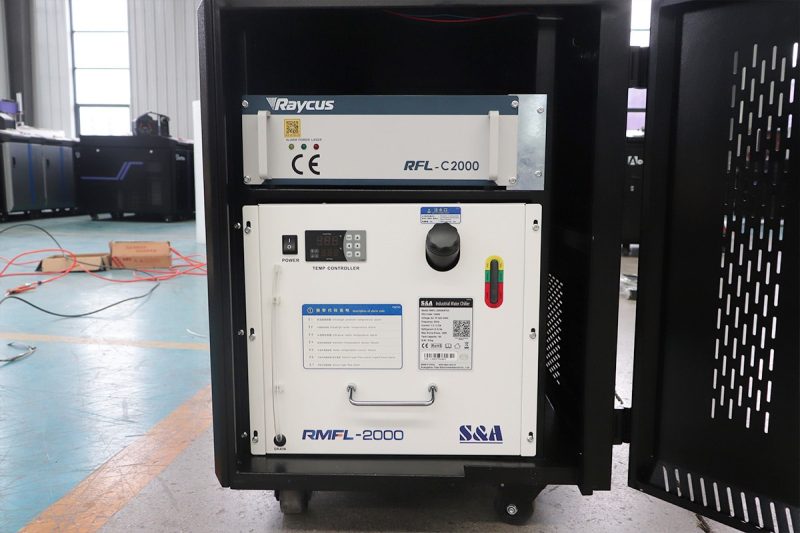
Learn About Laser Cleaning Systems
Laser cleaning systems are made up of several key parts, each of which plays a vital role in system performance and application results. To select the most suitable laser cleaning system, it is necessary to have a deep understanding of how these components work together to provide the best cleaning results.
Lézerforrás
The laser source is the core of the laser cleaning system, which determines the system’s output power, wavelength and processing capabilities. Common types of laser sources include fiber lasers and CO2 lasers, each of which has its own advantages and applicable fields.
- Fiber lasers usually emit near-infrared light with a wavelength of 1064 nm, which is suitable for cleaning metal surfaces, such as removing rust and oxides. Fiber laser generators have the advantages of high beam quality, high efficiency, and long life, and are widely used in the precision processing of metals in industrial production.
- CO2 laser mainly emits 10.6 μm far-infrared light waves, which are suitable for processing non-metallic materials such as rubber, plastic, and glass surfaces. Its wavelength makes it more effective on these materials and provides precise cleaning effects.
Optikai rendszer
The main task of the optical system is to accurately guide the laser beam to the target surface, ensuring high precision and high efficiency during the cleaning process. The most critical parts of the optical system are the lens and focusing device, which determine the size, shape and focus point of the laser beam. Good optical design can ensure that the beam evenly covers the cleaning area and avoids local over-treatment or under-treatment.
- The quality of the beam directly affects the cleaning efficiency. The more concentrated the beam is, the higher the energy density is, and the pollutants can be removed more quickly and effectively.
- Focus control ensures that the laser can achieve the best cleaning effect on different surfaces by adjusting the focus position, which is especially important for processing complex shapes and materials.
Vezérlő rendszer
The control system is the “brain” of the laser cleaning system. It is responsible for adjusting the laser’s output power, scanning speed, pulse frequency, and other parameters to ensure the system’s flexibility and adaptability in different cleaning tasks.
- The multifunctional operation interface allows users to customize the laser output mode, such as pulse mode, continuous mode, etc., to suit different cleaning requirements.
- Automatic control and intelligent parameter adjustment make cleaning of complex surfaces and different materials more precise and efficient.
Hűtőrendszer
During the laser cleaning process, the laser generator generates a lot of heat, which must be dissipated in time through the cooling system to prevent overheating.
- The air cooling system is suitable for medium and low-power laser generators. It has a simple structure and low cost, but its heat dissipation capacity is relatively weak.
- The water cooling system is used for high-power laser generators, which can more effectively remove the heat generated by the laser generator during operation, ensuring the stability and reliability of long-term continuous operation. The performance of the cooling system directly affects the service life and working efficiency of the laser cleaning system, so it is very important to choose a suitable cooling solution.
By fully understanding the functions and roles of laser sources, optical systems, control systems, and cooling systems, users can better select equipment that suits their specific cleaning needs. The synergy of these components makes laser cleaning technology widely used in various industries and can effectively cope with the cleaning challenges of different materials and surfaces.
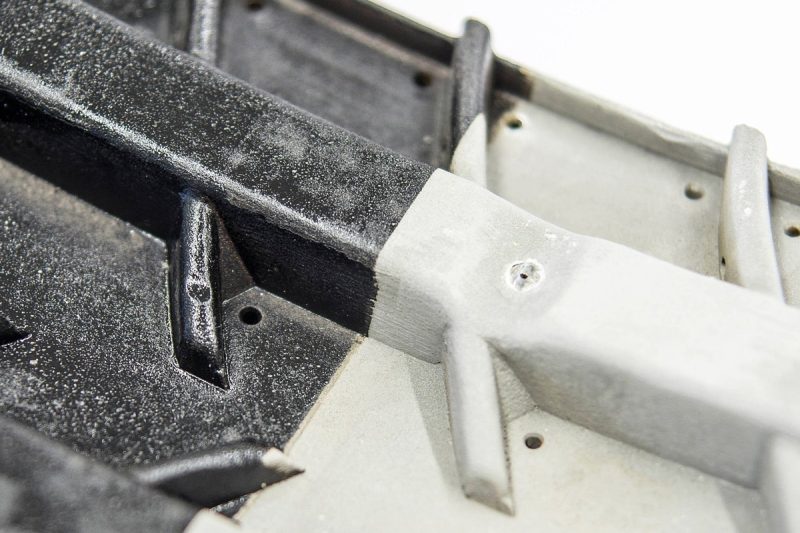
Key Factors to Consider When Selecting a Laser Cleaning System
When choosing the right laser cleaning system, it’s important to understand the key factors that influence its performance. This not only ensures the equipment meets your specific application needs but also optimizes cleaning results and operational efficiency. Here are a few areas to focus on to help you make an informed choice.
jelentkezési követelmények
The first step in selecting a laser cleaning system is to identify your specific cleaning task.
- Material type: Are you dealing with metals (such as steel, and aluminum) or non-metals (such as plastics, and rubber)?The effectiveness of a laser cleaning system depends on how efficiently the material absorbs the laser, and different materials have different requirements for wavelength and power. For example, metal materials usually require a fiber laser system, while non-metal materials are more suitable for a CO2 laser system.
- Contaminant type: Do you need to remove rust, oxides, paint, or dirt? Heavy contamination that is more difficult to remove requires a higher-power laser generator, while light contamination or delicate cleaning can use a lower-power device.
Laser Power and Wavelength
- Power: Laser power determines the speed and efficiency of cleaning. High-power laser generators are more suitable for cleaning large, heavily contaminated surfaces, but may over-clean or even damage the material when used in smaller or delicate areas. Low-power lasers are more suitable for delicate cleaning tasks and reduce thermal effects on the material.
- Wavelength: Wavelength directly affects the interaction between the laser and the material. For example, the wavelength of a fiber laser generator is usually around 1070 nm, which is suitable for metal cleaning. The wavelength of a CO2 laser generator is 10.6 µm, which is more suitable for cleaning non-metallic materials such as plastics, wood, or rubber. The choice of different wavelengths depends on the material’s absorption efficiency of the laser energy.
Impulzus időtartama és gyakorisága
- Pulse duration: Short pulse duration allows high-precision cleaning without damaging the substrate. It reduces the thermal impact on the surrounding area by releasing laser energy quickly, which is suitable for high-precision applications such as cleaning electronic components or mold surfaces.
- Frequency: The frequency of the laser pulse determines the repetition rate of the pulse. High-frequency pulses are suitable for quickly processing large surfaces, but they also generate more heat and may damage some materials. The choice of frequency should be adjusted according to the specific cleaning needs and material characteristics.
Scanning System and Control Software
- Scanning system: An efficient scanning system ensures that the laser beam moves quickly and evenly over a large surface area, improving cleaning speed and efficiency. High-precision and high-speed scanning systems are particularly important because they can greatly improve production efficiency and ensure the uniformity of the cleaning process.
- Control software: The control system determines the operational flexibility and degree of automation of the laser generator. Advanced control software allows users to adjust various parameters (such as power, scanning mode, pulse frequency, etc.) to ensure the applicability of the system in different applications. A user-friendly human-machine interface can simplify operations, reduce the learning curve, and improve the overall user experience.
Security Features and Compliance
- Safety interlock: The laser cleaning system should be equipped with a safety interlock function to prevent the laser beam from accidentally firing when not in operation, ensuring the safety of the operator.
- Compliance: Laser equipment must comply with local and international safety standards and regulations, such as ISO 11553 and CE certification. This not only ensures the safe and legal use of the equipment but also improves the compliance and reputation of the company.
Karbantartás és támogatás
- Maintenance requirements: Choosing a system that is easy to maintain can reduce daily operating costs. Some laser systems require regular replacement of key components such as lenses and filters, while some systems are designed for low maintenance, reducing downtime.
- Technical support: Reliable after-sales technical support is essential to the long-term stability of the equipment. Whether it is remote support or on-site repair services, whether the supplier can provide comprehensive technical support is one of the key factors to consider when selecting equipment.
Cost and Return on Investment (ROI)
- Initial cost: The initial investment in a laser cleaning system is high, so when choosing, you should consider its performance, brand, and application requirements, and choose a cost-effective device. Laser cleaning systems of different powers, wavelengths, and configurations vary greatly in price.
- Operating costs: In addition to the initial purchase cost, long-term operating expenses also need to be considered. Energy-efficient laser systems can significantly reduce power consumption, consumables, and maintenance costs, which will help improve the overall return on investment in the long run.
- Return on investment (ROI) analysis: When investing in equipment, it is crucial to evaluate the ROI of the equipment. By evaluating factors such as the equipment’s operating efficiency, labor cost savings, and cleaning effects, you can better predict the long-term value-added that the equipment will bring to your business.

Összesít
When choosing a laser cleaning system, it is important to conduct a comprehensive evaluation from multiple perspectives to ensure that the selected equipment can meet business needs and bring the greatest benefits. First, it is necessary to clarify the specific application requirements. Different types of laser cleaning systems perform differently when processing different materials and cleaning different types of contaminants (such as rust, coatings, oxides, etc.). It is crucial to choose the right laser power and wavelength based on the materials and application scenarios you need to process.
Secondly, the performance of the equipment is an important factor in determining the selection. The efficiency, accuracy, and processing speed of the laser cleaning system will directly affect production efficiency and process effects. For example, high-power laser cleaning systems are generally suitable for large-area, heavily polluted cleaning needs, while low-power equipment may be more suitable for delicate operations. Therefore, it is important to choose the right performance specifications based on the specific needs of the project.
Maintenance requirements are also an important consideration. Although laser cleaning systems generally have a long service life and low daily maintenance requirements, different equipment may vary in terms of maintenance frequency, operating costs, etc. Choosing equipment that is easy to maintain and has an adequate supply of spare parts can effectively reduce downtime and increase equipment utilization.
In addition, safety regulations are an important part of any industrial equipment selection. Laser cleaning equipment involves high-energy laser beams, and improper operation may cause safety hazards. Therefore, choosing equipment that meets international safety standards, is equipped with complete safety protection measures, and ensures that operators are fully trained to ensure the safe use of the equipment and the safety of the environment.
In short, choosing a suitable laser cleaning system requires comprehensive consideration of application requirements, equipment performance, maintenance requirements, and safety regulations. By fully evaluating these key factors, you will be able to choose the equipment that best meets your business needs, ensure that it performs at its best in long-term use, and bring sustainable return on investment to your business.
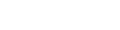
Elérhetőség
- [email protected]
- [email protected]
- +86-19963414011
- No. 3 A zóna, Lunzhen ipari zóna, Yucheng város, Shandong tartomány.
Szerezzen lézeres megoldásokat