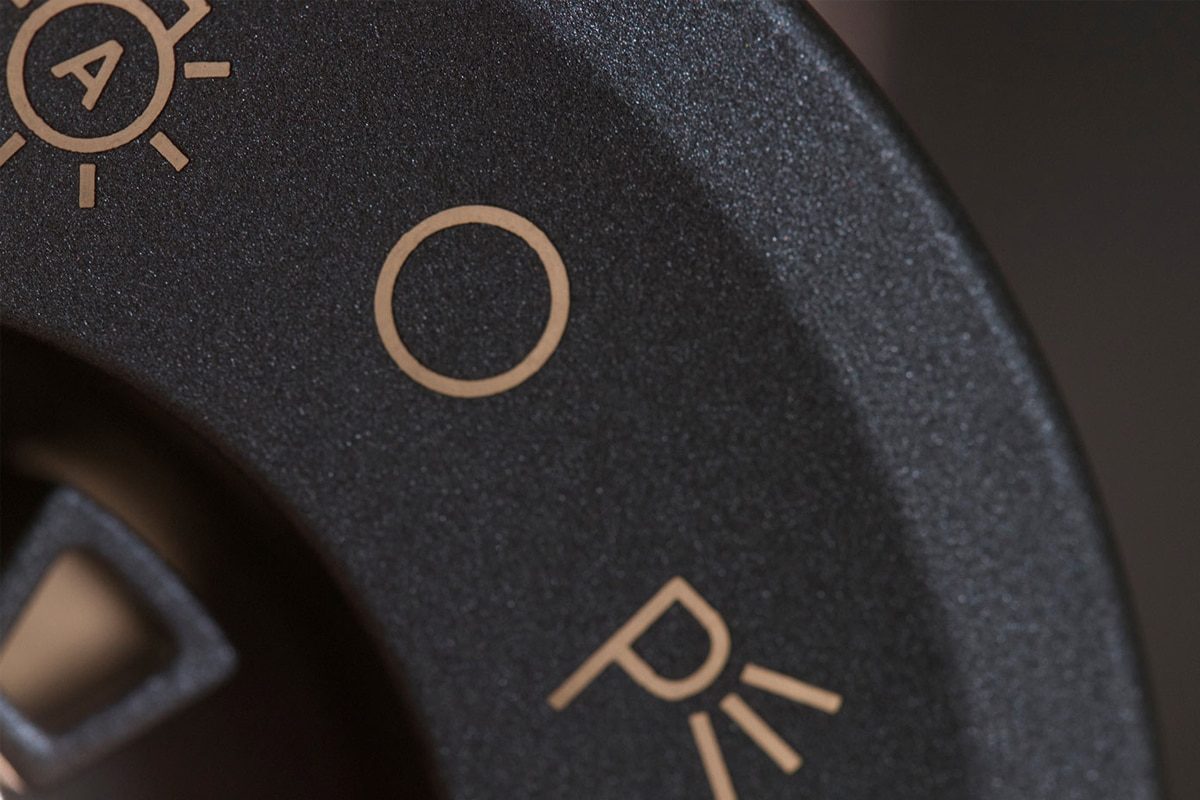
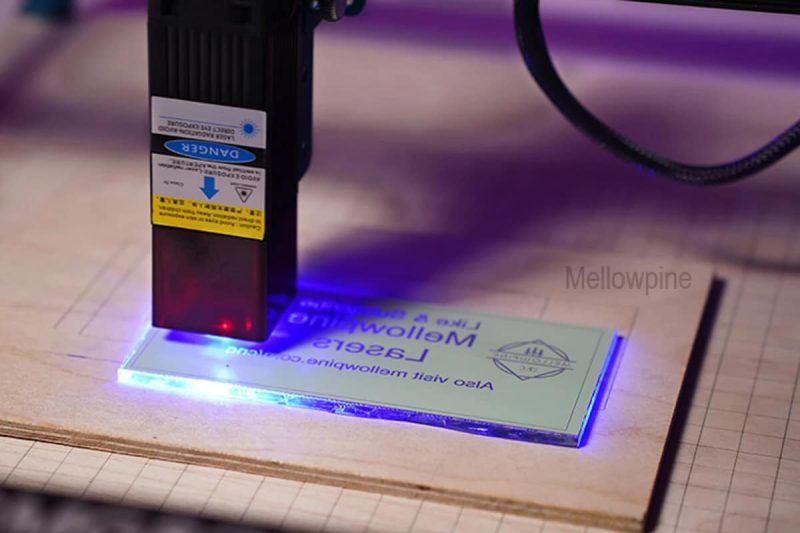
Basic Principles Of Laser Marking Technology
Before understanding how laser marking technology integrates with other manufacturing processes, you need to understand the basic principles of laser marking technology. Laser marking technology uses laser beams to process the surface of workpieces. Its basic principles mainly include the following aspects:
- Laser emission: The laser marking system emits a high-energy, high-consistency laser beam through a laser generator. Commonly used laser generators include carbon dioxide laser generators, fiber laser generators, and semiconductor laser generators.
- Laser focusing: The laser beam is focused into a small diameter spot through optical elements such as lenses or mirrors, so that the laser energy is concentrated into a small area, thereby improving the accuracy and efficiency of processing.
- Material absorption: After the laser beam irradiates the surface of the workpiece, the light energy is absorbed by the material, causing the temperature of the local area to increase. Different materials have different absorption rates of laser, so the optical properties of the material need to be considered during the laser marking process.
- Mark formation: The high-energy laser beam causes chemical or physical changes in the surface material of the workpiece to form marks. This change may be surface oxidation, evaporation, or a change in the material structure, thereby forming clear logos, patterns, or text on the surface of the workpiece.
- Control system: The laser marking system is equipped with a sophisticated control system, which can control the movement path and power of the laser beam according to pre-designed patterns or text to achieve precise control of the processing process.
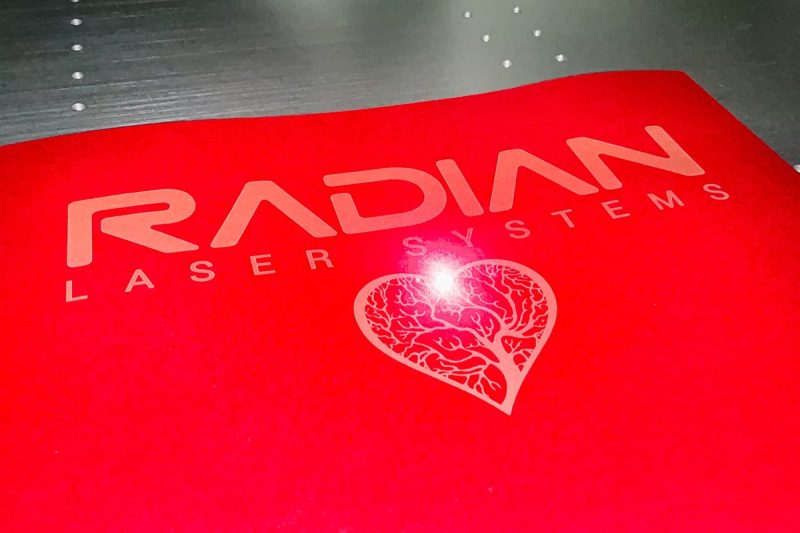
Benefits Of Integrating Laser Marking With Other Manufacturing Processes
The integration of laser marking technology with other manufacturing processes has brought many benefits to the manufacturing industry, including but not limited to the following aspects:
- Improve production efficiency: The integration of laser marking technology with other manufacturing processes can optimize automated production and processing processes, reducing manual intervention and intermediate links, thereby improving production efficiency.
- Enhanced processing accuracy: The high precision of laser marking technology combined with the processing capabilities of other manufacturing processes can achieve precision processing of complex parts, ensuring product quality and accuracy.
- Achieve personalized customization: The integration of laser marking technology 3D printing technology and other manufacturing processes can achieve personalized customization of products to meet the needs of different customers.
- Improve product quality: The integration of laser marking technology and machine vision technology can realize real-time monitoring and detection of product quality, timely discover and solve quality problems in the production process, and improve product consistency and stability.
- Reduce production costs: The integration of laser marking technology with automated assembly technology, intelligent manufacturing systems, etc. can realize the automation and intelligence of the production process, reducing labor costs and production costs.
- Strengthen product traceability and anti-counterfeiting capabilities: Laser marking technology can achieve visible markings on the product surface. Integration with other manufacturing processes can achieve product traceability and anti-counterfeiting, improving product safety and credibility.
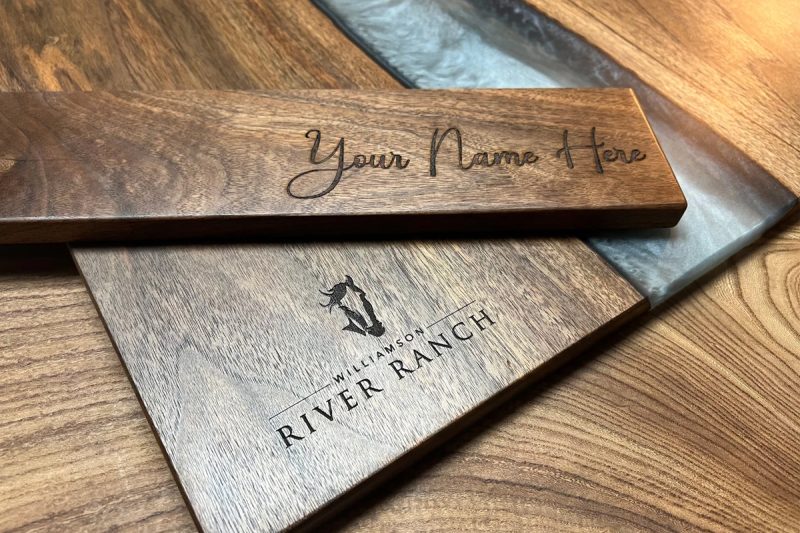
How To Integrate Laser Marking Technology With Other Manufacturing Processes
Laser Marking And CNC Processing Technology
Laser Marking And 3D Printing Technology
Laser Marking And Machine Vision Technology
Integration With Automated Assembly Technology
Integration With Intelligent Manufacturing Systems

Laser Marking Application Cases In Manufacturing Processes
The following are some application cases where laser marking technology is combined with other manufacturing processes:
- Laser marking and automobile manufacturing: In the automobile manufacturing process, laser marking technology is often combined with machine vision technology to mark automobile parts. For example, on the automobile body production line, laser marking can be used to identify information such as body number, production date, etc. By working with a machine vision system, the location of the mark can be ensured to be accurate.
- Laser marking and aerospace manufacturing: In the field of aerospace manufacturing, laser marking technology is often used in combination with 3D printing technology. For example, when manufacturing aero-engine parts, 3D printing technology can be used to manufacture complex components, and then laser marking technology can be used to mark key information such as part numbers and serial numbers on the surface of the parts.
- Laser marking and electronic product manufacturing: In electronic product manufacturing, laser marking technology is often combined with automated assembly technology. For example, in mobile phone production lines, laser marking can be used to identify the brand, model, and other information on the back panel of the mobile phone. Combined with the automated assembly system, it can realize automatic marking of mobile phone back panels and improve production efficiency.
- Laser marking and medical device manufacturing: In the field of medical device manufacturing, laser marking technology is often used in combination with precision machining technology. For example, when producing medical devices, laser marking can be used to identify the batch number, production date, and other information about the device. Combined with precision machining technology, the clarity and durability of the logo can be ensured.
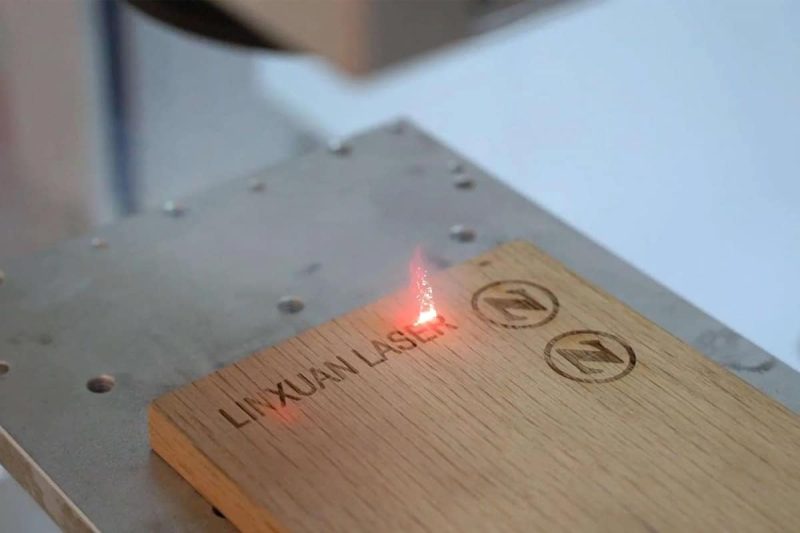
Challenges And Trends Brought About By Future Integration
The challenges and trends faced by the integration of laser marking technology with other manufacturing processes in the future include the following aspects:
- Technology integration challenges: The integration of laser marking technology with other manufacturing processes will face the challenge of increasing the difficulty of technology integration. Data exchange, collaboration, and control between different technologies need to be more efficient and precise, so in-depth research and innovative technology integration solutions are required.
- Need for interdisciplinary cooperation: Integration with other manufacturing processes requires interdisciplinary cooperation involving mechanical engineering, optical engineering, electronic engineering, computer science, and other fields. It requires experts from different disciplines to work together to jointly solve problems in technology integration.
- Safety and environmental protection challenges: Laser marking technology will produce a certain amount of light pollution and heat pollution during the processing process, and its integration with other manufacturing processes may increase the complexity of safety and environmental protection risks. Therefore, it is necessary to strengthen the management and supervision of safety and environmental protection in the manufacturing process in the future.
- Demand for intelligence and automation: The integration of laser marking technology with other manufacturing processes also needs to develop in the direction of intelligence and automation. The future trend is to realize intelligent manufacturing processes and automated control and optimization of manufacturing processes through technologies such as artificial intelligence and big data.
- Standardization and normalization requirements: As the integration of laser marking technology with other manufacturing processes becomes more and more widely used, the requirements for standardization and normalization will also become higher and higher. Standardize the integration process of laser marking technology and other manufacturing processes to ensure product quality and safety.
Summarize
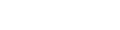
- [email protected]
- [email protected]
- +86-19963414011
- No. 3 Zone A, Lunzhen Industrial Zone,Yucheng City , Shandong Province.