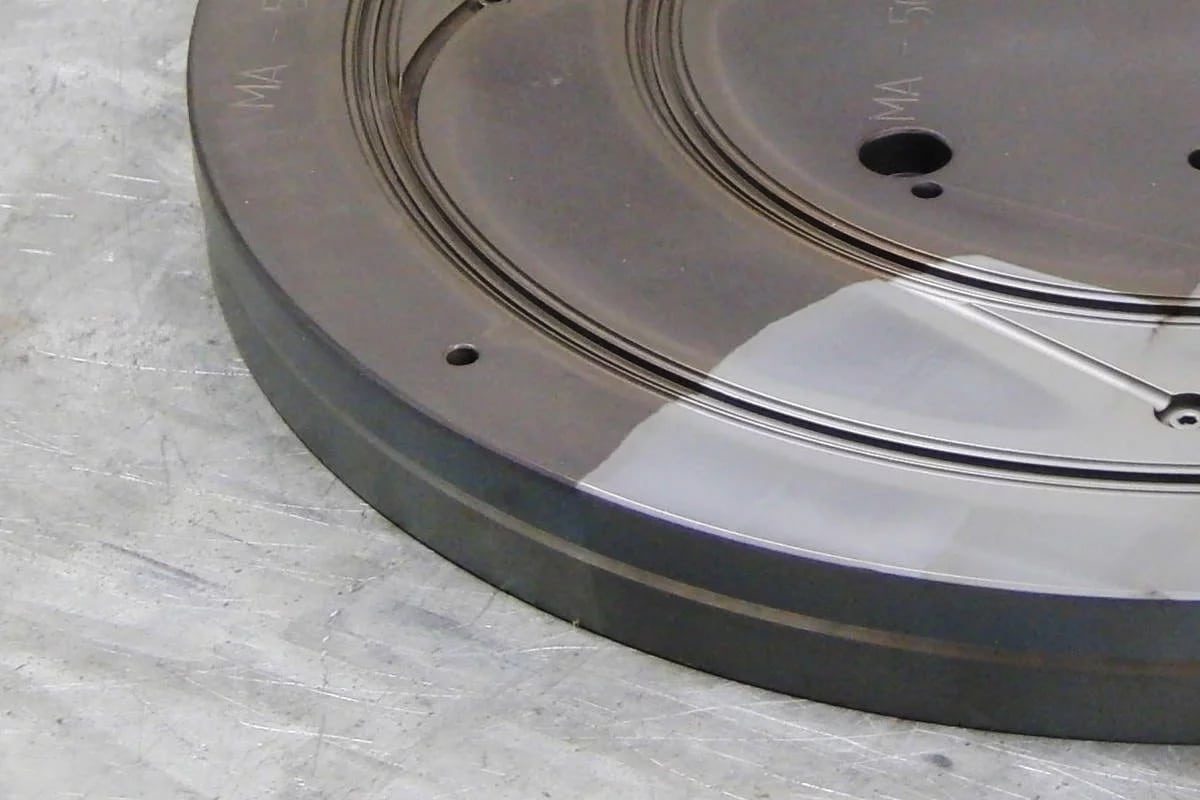
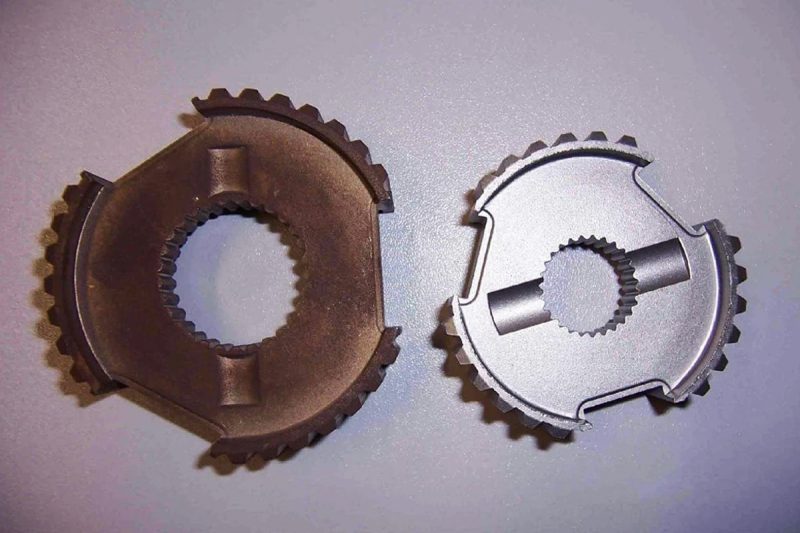
Understanding Pulse Laser Cleaning
Photothermal Ablation
Mechanism:
- The laser pulse delivers energy that is absorbed by the contaminant, leading to a sharp temperature rise.
- The material undergoes thermal decomposition or evaporation, breaking away from the substrate.
- Minimal energy transfer to the substrate ensures that the underlying material remains unaffected.
Applicazioni:
- Effective for removing rust, oxides, and organic coatings.
- Suitable for applications where heat-sensitive substrates need protection.
Optimization Strategies:
- Use laser wavelengths that are highly absorbed by the contaminant and minimally by the substrate.
- Adjust pulse duration to ensure efficient heating without excessive heat diffusion.
- Implement cooling measures to prevent thermal accumulation.
Photomechanical Ablation
Mechanism:
- The laser pulse induces rapid heating, causing the contaminant to expand abruptly.
- The sudden expansion generates mechanical stress or shock waves within the contaminant layer.
- This stress fractures or lifts the contaminant from the substrate.
Applicazioni:
- Ideal for removing hard contaminants or coatings from durable substrates.
- Used in applications requiring minimal heat transfer to the substrate.
Optimization Strategies:
- Utilize high-intensity pulses to generate sufficient mechanical stress.
- Opt for ultrashort pulse durations (picoseconds or femtoseconds) to maximize the photomechanical effect.
- Tailor laser intensity to match the mechanical properties of the contaminant and substrate.
Photochemical Ablation
Photochemical ablation involves direct interaction between laser photons and the chemical bonds of the contaminant molecules. The high-energy photons break these bonds, resulting in the formation of volatile compounds that are removed from the surface.
Mechanism:
- Laser photons, particularly in the ultraviolet (UV) range, provide enough energy to dissociate chemical bonds in the contaminant.
- The resulting chemical reactions produce gaseous or easily removable byproducts.
- Unlike photothermal and photomechanical mechanisms, photochemical ablation minimizes heat effects.
Applicazioni:
- Suitable for delicate cleaning tasks, such as removing thin films, organic residues, or sensitive coatings.
- Frequently used in industries like electronics, cultural heritage restoration, and precision manufacturing.
Optimization Strategies:
- Use short-wavelength lasers (e.g., UV lasers) to achieve high photon energy for bond dissociation.
- Match the laser parameters to the chemical composition of the contaminant.
- Avoid excessive energy that could alter the substrate chemically.
Synergy Between Ablation Mechanisms
- Photothermal and Photomechanical: Rapid heating can increase mechanical stress, amplifying the photomechanical effect.
- Photothermal and Photochemical: Elevated temperatures can accelerate photochemical reactions, improving efficiency.
- Photomechanical and Photochemical: The combination of mechanical forces and bond-breaking reactions can tackle complex contaminants.
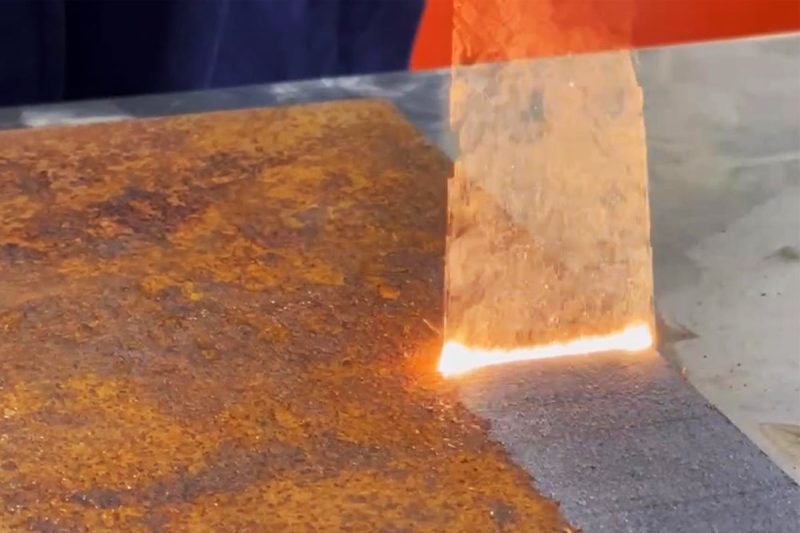
Critical Parameters in Pulse Laser Cleaning
Durata dell'impulso
Pulse duration refers to the length of time that the laser emits energy in a single pulse. It significantly impacts the thermal and mechanical effects on the contaminant and substrate.
Short Pulse Durations:
- Generate high peak power, which is ideal for breaking down contaminants with minimal thermal diffusion.
- Reduce the risk of heat damage to the substrate, making them suitable for delicate applications.
- Picosecond and femtosecond lasers are particularly effective for precise cleaning.
Longer Pulse Durations:
- Provide more thermal energy, which can help in removing thick or strongly adhered contaminants.
- May lead to heat accumulation and substrate damage if not controlled carefully.
Optimization:
- Match pulse duration to the thermal properties of the contaminant and substrate.
- Use ultrashort pulses for applications requiring minimal heat effects, such as cleaning sensitive surfaces.
Energia impulsiva
Higher Pulse Energy:
- Can remove contaminants more effectively by delivering sufficient energy for ablation.
- May cause substrate damage or excessive material removal if energy exceeds the damage threshold.
Lower Pulse Energy:
- Provides more controlled cleaning, reducing the risk of substrate damage.
- May require multiple passes to achieve thorough cleaning, affecting efficiency.
Optimization:
- Experiment with the minimum energy required for effective contaminant removal without affecting the substrate.
- Adjust energy levels based on the thickness and adhesion strength of the contaminant.
Frequenza di ripetizione
High Repetition Rates:
- Increase cleaning speed by delivering more pulses in a given time.
- This can lead to heat accumulation, especially if the material does not cool sufficiently between pulses.
Low Repetition Rates:
- Allow the surface to cool between pulses, minimizing thermal effects.
- This may result in slower cleaning speeds but provides better control over heat-sensitive substrates.
Optimization:
- Select a repetition rate that balances cleaning speed with thermal management.
- Use cooling systems or intermittent cleaning cycles for high repetition rates to prevent heat buildup.
Lunghezza d'onda
Shorter Wavelengths:
- Provide high photon energy, making them suitable for photochemical ablation.
- Ideal for removing organic contaminants and cleaning delicate surfaces.
Longer Wavelengths:
- More effective for photothermal and photomechanical ablation.
- Commonly used for cleaning metals, oxides, and industrial coatings.
Optimization:
- Match the laser wavelength to the absorption properties of the contaminant while minimizing absorption by the substrate.
- Use tunable laser systems for applications involving multiple contaminant types.
Beam Profile
Gaussian Beam:
- Features a peak intensity at the center and gradual fall-off toward the edges.
- Suitable for applications requiring focused cleaning on small areas.
Top-Hat Beam:
- Delivers uniform intensity across the beam’s cross-section.
- Ideal for cleaning large areas or surfaces with consistent energy requirements.
Optimization:
- Use beam shaping optics to achieve the desired beam profile for specific applications.
- Ensure beam alignment and stability to avoid uneven cleaning results.
Interplay of Parameters
These critical parameters—pulse duration, pulse energy, repetition rate, wavelength, and beam profile—do not act independently. Instead, their interplay defines the overall effectiveness and precision of the cleaning process.
For example:
- Pulse energy and repetition rate: Higher energy combined with an optimal repetition rate can maximize cleaning speed without causing heat accumulation.
- Wavelength and beam profile: A wavelength matched to the contaminant’s absorption properties, paired with a uniform beam profile, ensures efficient and consistent cleaning.
- Pulse duration and substrate sensitivity: Shorter pulses minimize thermal effects, which is essential for cleaning heat-sensitive substrates.
By carefully tuning these parameters to the specific material and cleaning requirements, pulse laser cleaning can achieve superior results in terms of efficiency, precision, and substrate preservation. A thorough understanding of these parameters allows operators to fully harness the potential of pulse laser cleaning technology for diverse industrial and delicate applications.
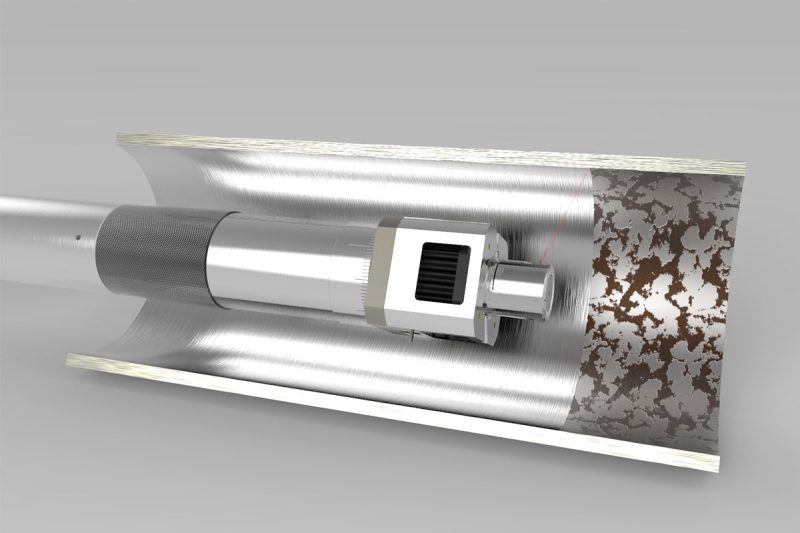
Factors Affecting the Quality of Pulse Laser Cleaning
Proprietà dei materiali
Conduttività termica
- Impact on Cleaning: Materials with high thermal conductivity (e.g., metals like copper and aluminum) dissipate heat quickly, reducing the localized thermal effects of the laser. This can make it challenging to achieve effective ablation, particularly when relying on photothermal mechanisms.
- Optimization: For high-conductivity materials, use higher pulse energy or shorter pulse durations to concentrate thermal effects and enhance ablation efficiency.
Coefficiente di assorbimento
- Impact on Cleaning: The absorption coefficient determines how much laser energy the material absorbs at a specific wavelength. A higher absorption coefficient leads to more efficient energy absorption, improving the cleaning process.
- Optimization: Match the laser wavelength to the material’s absorption spectrum to maximize energy absorption. Materials with low absorption may require wavelength tuning or pre-treatment to improve cleaning efficiency.
Riflettività
- Impact on Cleaning: Reflective materials (e.g., polished metals like stainless steel or aluminum) reflect a significant portion of the laser energy, reducing the energy available for cleaning.
- Optimization: Use anti-reflective coatings or adjust the laser angle to minimize reflection losses. Employ laser wavelengths that are better absorbed by the material to counteract high reflectivity.
Condizioni ambientali
Temperatura ambiente
- Impact on Cleaning: Extreme ambient temperatures can alter the material’s thermal response and the laser system’s performance. High temperatures may increase the risk of unwanted thermal damage, while low temperatures could affect the laser’s efficiency.
- Optimization: Maintain a moderate and stable temperature in the working environment to ensure consistent material response and optimal laser operation.
Umidità
- Impact on Cleaning: High humidity levels can lead to condensation on the material surface or optical components, disrupting the laser beam and reducing cleaning efficiency. Humidity can also accelerate corrosion on certain materials, complicating the cleaning process.
- Optimization: Work in a controlled environment with regulated humidity levels. Use dehumidifiers or enclosed cleaning setups to prevent moisture interference.
Proprietà dei contaminanti
Chemical Composition
- Impact on Cleaning: Different contaminants absorb laser energy differently based on their chemical composition. For example, organic residues absorb UV lasers more effectively, while rust and oxides respond better to mid-infrared lasers.
- Optimization: Select a laser wavelength and pulse energy tailored to the contaminant’s chemical composition to maximize cleaning efficiency.
Spessore
- Impact on Cleaning: Thicker contaminants require more energy or multiple lasers passes for complete removal, while thinner layers may need lower energy to avoid substrate damage.
- Optimization: Adjust pulse energy and repetition rate to match the contaminant’s thickness, ensuring effective removal without excessive substrate exposure.
Adhesion to Substrate
- Impact on Cleaning: Contaminants strongly adhered to the substrate may require higher mechanical or thermal energy for removal, while loosely adhered contaminants can be removed with lower energy.
- Optimization: Use higher pulse energy or photomechanical ablation techniques for strongly adhered contaminants. For loosely adhered contaminants, lower energy settings can suffice.
Optical Properties
- Impact on Cleaning: The contaminant’s absorption and reflectivity at the laser wavelength influence how effectively it absorbs laser energy. Highly reflective contaminants can hinder cleaning efficiency.
- Optimization: Use laser wavelengths that align with the contaminant’s absorption peak and consider using absorptive coatings to improve energy absorption for reflective contaminants.
Interplay of Factors
- A material with low absorption and high reflectivity in a humid environment will require precise wavelength selection and environmental control to achieve effective cleaning.
- Thick, strongly adhered contaminants on a high-conductivity substrate may need a combination of higher pulse energy, shorter pulse durations, and optimal beam focusing for efficient removal.
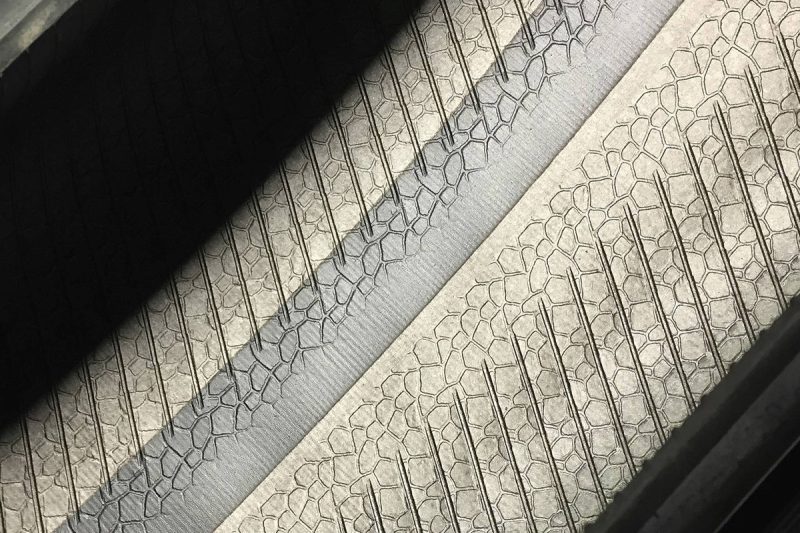
Strategies to Improve the Quality of Pulse Laser Cleaning
Optimal Parameter Selection
Durata dell'impulso
- Shorter Pulses: Use ultrashort pulses (picoseconds or femtoseconds) to minimize thermal diffusion and prevent substrate damage.
- Application-Specific Tuning: Adjust pulse duration to match the contaminant type. For heat-sensitive materials, shorter pulses ensure better results.
Energia impulsiva
- Higher Energy for Stronger Contaminants: Increase pulse energy for thick or strongly adhered contaminants to achieve effective ablation.
- Controlled Energy for Precision: Use energy slightly above the ablation threshold to prevent substrate damage while ensuring contaminant removal.
Frequenza di ripetizione
- Faster Cleaning: Higher repetition rates increase cleaning speed but can lead to heat accumulation if not controlled.
- Balance Efficiency and Safety: Select a rate that allows sufficient cooling between pulses to avoid thermal damage to the substrate.
Wavelength Selection
- Material-Contaminant Compatibility: Choose a wavelength that matches the absorption characteristics of the contaminant for efficient energy absorption.
- Versatile Systems: Utilize lasers with tunable wavelengths for applications involving varying contaminant types.
Beam Profile Optimization
- Uniform Intensity Distribution: Employ top-hat beam profiles for even cleaning across larger areas.
- Precision Cleaning: Use Gaussian profiles for targeted cleaning of small or intricate areas.
- Shaping Optics: Implement beam shaping optics to match the beam profile to specific application requirements.
Advanced Monitoring and Control Systems
Monitoraggio in tempo reale
- Enhanced Precision: Use sensors, cameras, or photodiodes to monitor laser-material interaction in real time.
- Detect Issues Early: Identify incomplete cleaning, overheating, or other issues immediately to avoid defects.
- Data Logging: Collect data during the cleaning process for analysis and process optimization.
Feedback Control
- Dynamic Adjustments: Implement closed-loop feedback systems to adjust laser parameters on the fly based on real-time monitoring.
- Consistent Results: Maintain optimal conditions for each pass, even with variations in contaminant thickness or material properties.
- AI Integration: Leverage machine learning algorithms to predict outcomes and fine-tune parameters automatically.
Pre-Cleaning Surface Preparation
Mechanical Pre-Cleaning
- Debris Removal: Use brushes, compressed air, or mild abrasive methods to remove loose dirt, dust, or large particles.
- Improved Laser Interaction: Ensure the laser directly interacts with the contaminant rather than surface debris for consistent cleaning.
Chemical Pre-Treatment
- Selective Treatment: Apply chemicals to soften or dissolve specific contaminants, reducing the energy required for laser ablation.
- Enhanced Absorption: Use absorptive coatings on reflective surfaces to improve laser energy absorption and minimize reflection losses.
- Thorough Rinse: Ensure that chemical residues are rinsed off to avoid interference with the laser cleaning process.
Combining Strategies for Optimal Results
- Parameter Optimization with Monitoring Systems: Fine-tune laser parameters based on real-time feedback to ensure precise cleaning across varying contaminants and surfaces.
- Pre-Cleaning for Consistent Results: Combine surface preparation techniques with optimized parameters to reduce energy loss and improve efficiency.
- Adaptive Technology: Use AI-driven systems for adaptive control, enabling dynamic responses to changes in material or contaminant properties.
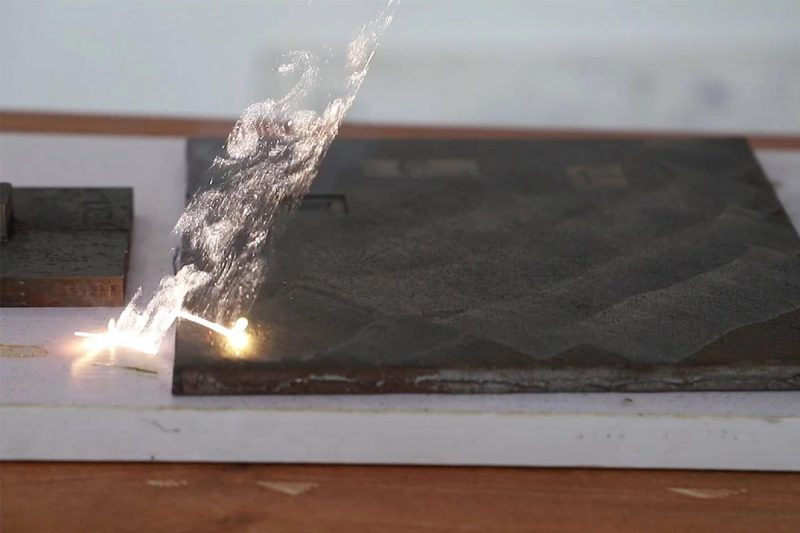
Challenges and Solutions in Pulse Laser Cleaning
Managing Thermal Effects
Soluzioni:
- Optimize Pulse Duration and Energy: Use ultrashort pulse durations (picosecond or femtosecond) to minimize heat diffusion. Adjust pulse energy to stay slightly above the ablation threshold, ensuring contaminant removal without overheating the substrate.
- Control Repetition Rate: Select a repetition rate that allows sufficient cooling time between pulses. Use intermittent cleaning cycles for heat-sensitive materials to avoid cumulative thermal effects.
- Real-Time Monitoring: Incorporate thermal sensors and infrared cameras to monitor surface temperatures during cleaning. Adjust laser parameters dynamically based on feedback to prevent overheating.
- Introduce Cooling Systems: Use external cooling measures such as compressed air or inert gas nozzles to dissipate heat during the cleaning process.
Addressing Material Variability
Soluzioni:
- Material-Specific Parameters: Tailor laser parameters—such as wavelength, pulse duration, and energy—to match the absorption and thermal properties of the material. For example, shorter wavelengths are better for highly reflective materials like metals.
- Layered Cleaning Strategies: For layered contaminants, use a multi-pass approach with gradually increasing energy levels to remove layers without damaging the substrate.
- Tunable Laser Systems: Use lasers with adjustable wavelengths to accommodate a wider range of materials. This flexibility allows for precise cleaning of mixed materials or surfaces with variable properties.
- Pre-Testing: Conduct material-specific tests before the cleaning process to determine optimal parameters for each substrate and contaminant type.
Ensuring Consistency
Soluzioni:
- Beam Profile Optimization: Ensure a uniform beam profile (e.g., top hat) for consistent energy distribution across the cleaning area. Use beam-shaping optics to maintain uniformity, especially for large or intricate surfaces.
- Automated Systems: Integrate automated scanning systems, such as galvanometer scanners or robotic arms, to maintain precise and consistent laser movement. This ensures even cleaning across the entire surface.
- Real-Time Feedback and Adjustments: Employ advanced monitoring systems to detect inconsistencies in cleaning. Use feedback control to adjust parameters dynamically and maintain consistent quality.
- Controlled Environment: Conduct cleaning in a stable environment with controlled temperature and humidity to minimize external factors affecting the process. Enclosed workspaces can reduce the impact of environmental variability.
Holistic Approach to Overcoming Challenges
- Dynamic Parameter Adjustment: Real-time monitoring systems combined with adaptive controls ensure that thermal effects are managed, material variability is addressed, and consistency is maintained.
- Operator Training: Ensure operators are well-trained in using laser cleaning systems and understand material-specific requirements. Skilled operators can identify and rectify potential issues quickly.
- Regular Equipment Maintenance: Maintain laser systems and associated optics regularly to ensure consistent beam quality and performance.
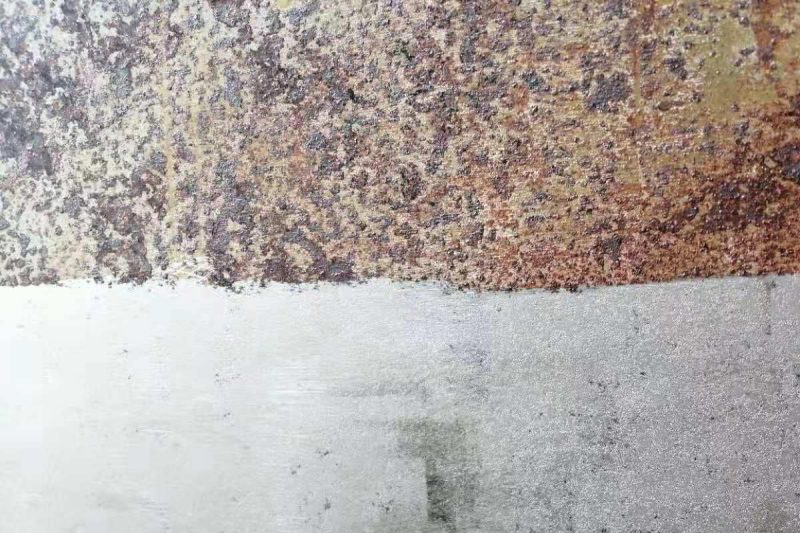
Safety and Environmental Considerations in Pulse Laser Cleaning
Fume Extraction
Soluzioni:
- Install Fume Extraction Systems: Use high-efficiency fume extractors with HEPA and activated carbon filters to capture and neutralize harmful particles and gases.
- Positioning of Extraction Units: Place fume extraction units close to the cleaning area to ensure effective capture of airborne contaminants.
- Ventilation: Ensure the workspace has adequate ventilation to prevent the accumulation of hazardous fumes, particularly in enclosed environments.
- Regular Maintenance: Maintain and replace filters regularly to ensure the continuous efficiency of the fume extraction system.
Equipaggiamento protettivo
Soluzioni:
- Laser Safety Goggles: Use laser safety goggles designed for the specific wavelength of the laser being used to protect against direct or reflected laser radiation.
- Respiratory Protection: Provide operators with suitable respirators or masks, particularly in environments with insufficient fume extraction.
- Protective Clothing: Equip operators with gloves, face shields, and flame-resistant clothing to protect against ejected debris and accidental exposure to the laser beam.
- Safety Enclosures: Where possible, conduct laser cleaning within a fully enclosed system to minimize exposure to radiation and fumes.
- Training: Train operators on the correct use of protective equipment and safe handling of laser cleaning systems.
Complying with Regulations
Soluzioni:
- Laser Safety Standards: Follow guidelines such as those outlined in ISO 11553 for laser safety. Ensure the classification of the laser system is appropriate for the application and workspace setup.
- Fume Emission Regulations: Adhere to environmental regulations concerning air quality, such as permissible emission levels of particulate matter and toxic substances.
- Operator Certification: Ensure that operators are certified or trained according to applicable safety standards, such as OSHA requirements in the U.S. or equivalent local standards.
- Waste Management: Properly dispose of collected contaminants, filters, and other waste products by hazardous waste disposal regulations.
- Periodic Audits: Conduct regular audits of safety practices, equipment, and environmental controls to ensure ongoing compliance with regulations.
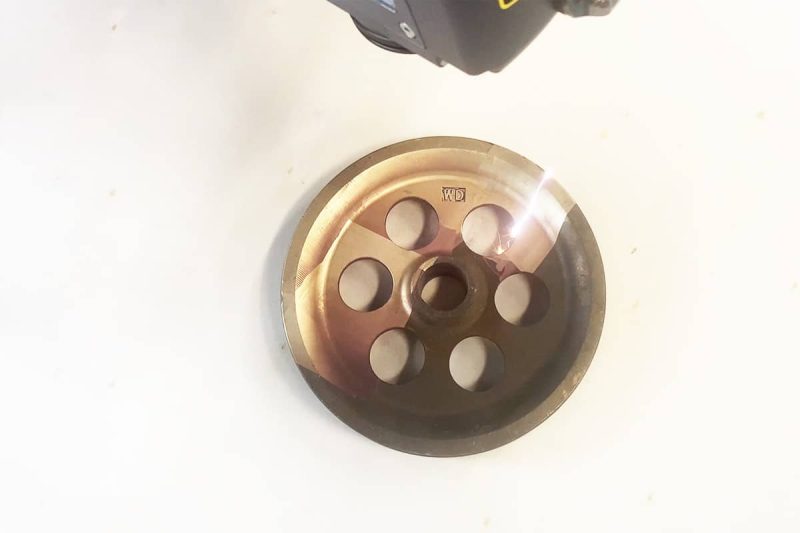
Riepilogo
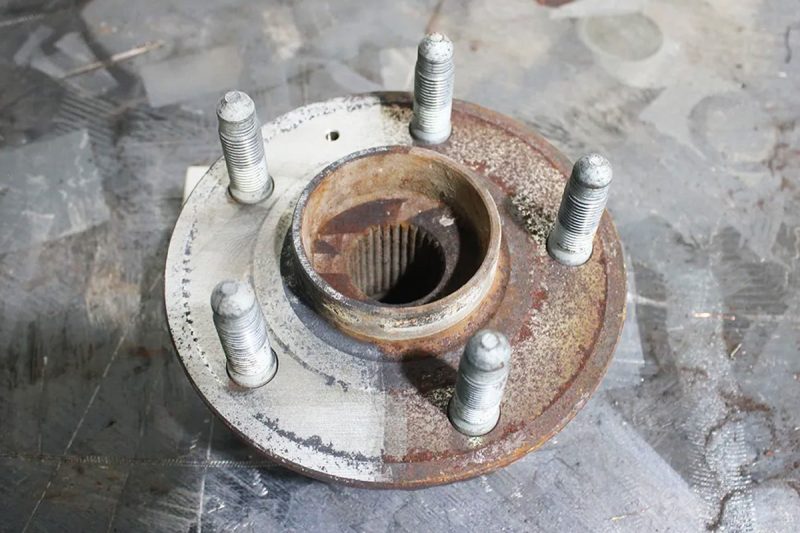
Ottieni soluzioni di pulizia laser
Photochemical ablation involves direct interaction between laser photons and the chemical bonds of the contaminant molecules. The high-energy photons break these bonds, resulting in the formation of volatile compounds that are removed from the surface.
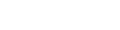
- [email protected]
- [email protected]
- +86-19963414011
- N. 3 Zona A, zona industriale di Lunzhen, città di Yucheng, provincia di Shandong.