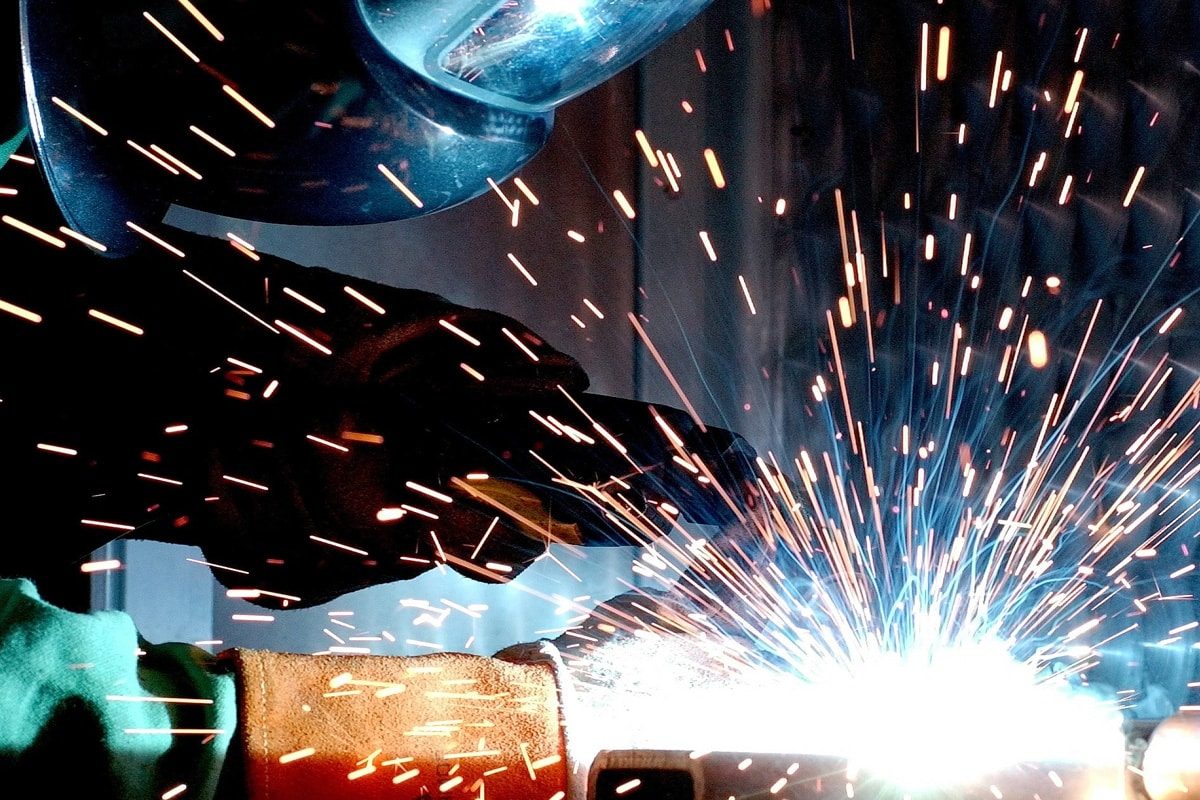
In che modo il punto focale del raggio laser influisce sulla qualità della saldatura?
La saldatura laser è diventata un processo altamente accurato ed efficace nella produzione moderna. Che si tratti di produzione automobilistica, aerospaziale, produzione di elettronica o industria dei dispositivi medici, la saldatura laser è ampiamente utilizzata per la sua elevata efficienza, il basso apporto di calore e l'eccellente qualità di saldatura. Tuttavia, la qualità delle saldature laser è fortemente influenzata dalla messa a fuoco del raggio laser. La messa a fuoco del raggio laser è un fattore chiave che influenza direttamente l'efficienza e l'efficacia del processo di saldatura laser. Nella saldatura laser, la messa a fuoco del raggio si riferisce al punto preciso in cui l'energia laser è più concentrata e la messa a fuoco è fondamentale per ottenere la migliore qualità di saldatura. Controllando attentamente la messa a fuoco, i produttori possono adattare il processo di saldatura per soddisfare requisiti specifici, come garantire una penetrazione sufficiente, ridurre al minimo i difetti e ottenere saldature coerenti. Comprendere le sfumature della messa a fuoco del raggio laser può controllare meglio l'apporto di calore, le dinamiche del bagno di saldatura e la stabilità complessiva del processo. Ciò a sua volta può aumentare la precisione, ridurre lo spreco di materiale e migliorare l'integrità strutturale dei componenti saldati. Poiché le industrie fanno sempre più affidamento sulla precisione e l'efficienza della saldatura laser, padroneggiare la tecnologia di focalizzazione del raggio laser è essenziale per produrre saldature di alta qualità in una varietà di applicazioni.
Sommario
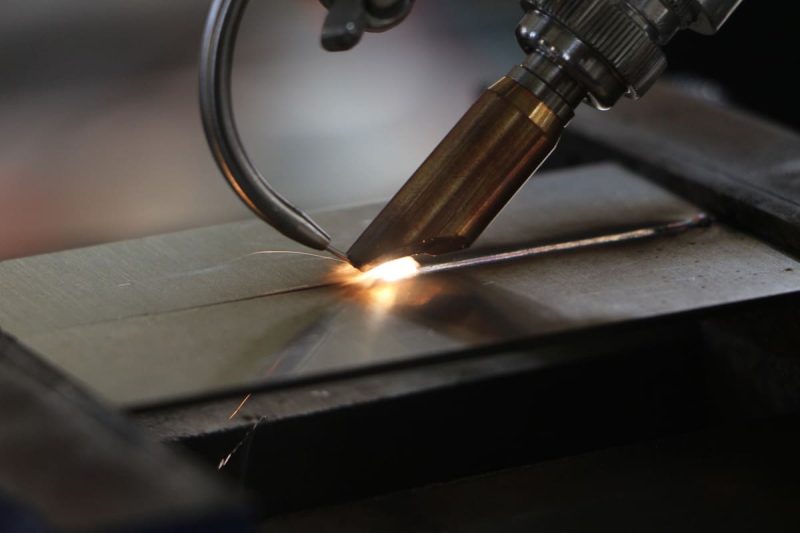
Comprensione della messa a fuoco del raggio laser
Spiegazione della messa a fuoco del raggio laser e del suo ruolo nella saldatura
La messa a fuoco di un raggio laser si riferisce al punto nello spazio in cui il raggio laser è focalizzato al diametro minimo. Questa messa a fuoco è un parametro critico nel processo di saldatura laser perché determina la distribuzione dell'energia laser sul pezzo in lavorazione. La densità di energia del raggio laser è più alta dopo che è focalizzato, il che significa che alla messa a fuoco, la potenza del laser è concentrata in un'area molto piccola, con conseguenti temperature estremamente elevate. È questa temperatura elevata che consente al materiale di fondersi e fondersi rapidamente in un breve periodo di tempo per formare una saldatura forte.
Nel funzionamento effettivo, la posizione di messa a fuoco del raggio laser viene solitamente regolata in base alle specifiche esigenze di saldatura. Se la messa a fuoco è sulla superficie del pezzo in lavorazione, l'energia laser è principalmente concentrata sulla superficie del materiale, che è solitamente adatta per la saldatura di materiali sottili e può ottenere effetti di saldatura ad alta precisione. Quando la messa a fuoco è all'interno del pezzo in lavorazione, il raggio laser può penetrare la superficie del materiale e penetrare in profondità nel materiale, ottenendo così una saldatura più profonda. Ciò è particolarmente importante per pezzi in lavorazione più spessi o applicazioni che richiedono giunti ad alta resistenza.
Inoltre, la posizione del fuoco del raggio laser non influisce solo sulla profondità della saldatura, ma anche sulla larghezza della saldatura, sulla dimensione della zona interessata dal calore e sulla velocità di saldatura. Un'impostazione corretta del fuoco può ridurre i difetti di saldatura come pori, crepe e penetrazione incompleta, garantendo al contempo la resistenza della saldatura. Al contrario, se la posizione del fuoco non è corretta e l'energia laser è distribuita in modo non uniforme, ciò può portare a una scarsa qualità della saldatura, penetrazione superficiale, surriscaldamento o risultati di saldatura incoerenti.
Nei moderni sistemi di saldatura laser, il controllo preciso della posizione di messa a fuoco è diventato uno dei mezzi importanti per migliorare la qualità della saldatura. Ad esempio, la tecnologia dell'ottica adattiva può regolare la messa a fuoco del raggio laser in tempo reale durante il processo di saldatura per adattarsi alla forma e alle proprietà del materiale del pezzo, assicurando che l'energia laser sia sempre concentrata sulla parte più necessaria. Inoltre, attraverso la tecnologia di analisi del raggio, le caratteristiche di messa a fuoco del raggio laser possono essere analizzate in modo approfondito per ottimizzare ulteriormente i parametri di saldatura e migliorare la stabilità e la coerenza della saldatura. In generale, la messa a fuoco del raggio laser svolge un ruolo fondamentale nel processo di saldatura. Controllando con precisione la posizione di messa a fuoco, la qualità della saldatura può essere efficacemente migliorata per soddisfare le esigenze di varie applicazioni complesse. Che si tratti di produzione automobilistica, aerospaziale o elettronica, l'impostazione corretta della messa a fuoco è la chiave per ottenere una saldatura di alta qualità.
Dimensione della messa a fuoco e la sua relazione con la qualità della saldatura
La dimensione della messa a fuoco si riferisce al diametro del raggio laser nel punto focale, solitamente misurato in micron. La dimensione della messa a fuoco influisce direttamente sulla distribuzione dell'energia laser e sull'effetto finale della saldatura. Nella saldatura laser, la dimensione della messa a fuoco più piccola significa che l'energia laser è più concentrata e la densità di energia per unità di area è maggiore. Questa elevata densità di energia fonde rapidamente il materiale e aumenta la penetrazione della saldatura, consentendo saldature più profonde. Ciò presenta vantaggi significativi nelle applicazioni che richiedono elevata resistenza e profondità di saldatura, come la saldatura di lamiere spesse o la saldatura di parti strutturali critiche.
Tuttavia, anche una dimensione di messa a fuoco troppo piccola ha i suoi limiti. Poiché l'energia è così concentrata, la larghezza della saldatura può diventare molto stretta, il che potrebbe non essere l'ideale per alcune applicazioni che richiedono una saldatura più ampia. Inoltre, una dimensione di messa a fuoco troppo piccola può aumentare l'instabilità durante il processo di saldatura, con conseguente qualità di saldatura incoerente, specialmente quando la superficie del materiale lavorato è irregolare o contiene impurità.
D'altro canto, una dimensione di messa a fuoco maggiore distribuirà l'energia laser su un'area più ampia, riducendo la densità di energia per unità di area. Mentre questo può ridurre la profondità di penetrazione della saldatura, per applicazioni che richiedono un cordone di saldatura più ampio, come la giunzione superficiale o la saldatura di tenuta, una dimensione di messa a fuoco maggiore è più adatta. In questo caso, sebbene la profondità della saldatura possa essere ridotta, la copertura della saldatura è maggiore, garantendo l'integrità della connessione superficiale dei materiali.
Pertanto, la scelta della dimensione della messa a fuoco è strettamente correlata alla qualità della saldatura e deve essere ottimizzata in base alle specifiche esigenze di saldatura. Nelle applicazioni pratiche, gli ingegneri di saldatura devono selezionare la dimensione della messa a fuoco appropriata in base al materiale, allo spessore, alla forma e ai requisiti di saldatura del pezzo in lavorazione per ottenere il miglior equilibrio tra larghezza, profondità e resistenza della saldatura. Attraverso impostazioni ragionevoli della dimensione della messa a fuoco, è possibile migliorare la stabilità della saldatura, ridurre i difetti e, in definitiva, migliorare la qualità complessiva della saldatura.
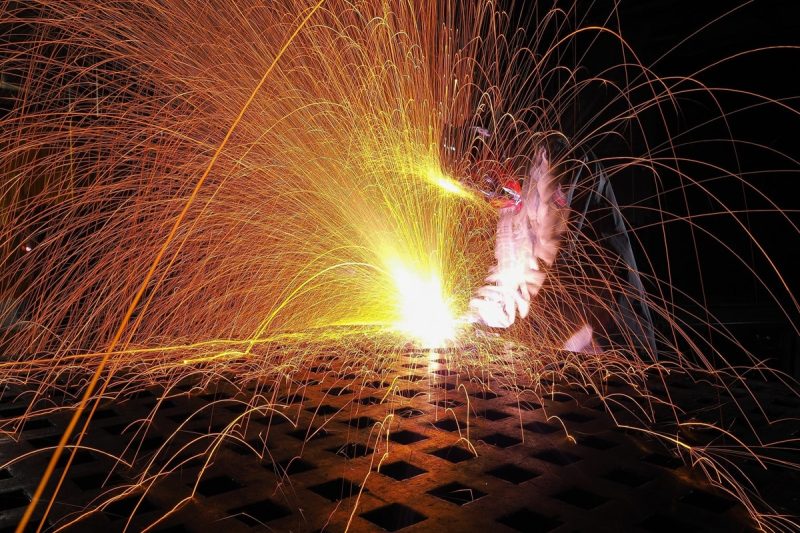
Fattori che influenzano la messa a fuoco del raggio laser
La focalizzazione del raggio laser è un passaggio cruciale nella saldatura laser, che determina direttamente l'effetto e la qualità della saldatura. I fattori che influenzano la focalizzazione del raggio laser includono la selezione della lente, il diametro del raggio, la lunghezza focale e la qualità del raggio. La corretta comprensione e ottimizzazione di questi fattori può migliorare efficacemente le prestazioni e la precisione della saldatura.
Selezione dell'obiettivo
La lente svolge un ruolo chiave nel processo di focalizzazione del raggio laser ed è il componente principale che influenza la capacità di convergenza del raggio. Diversi design e materiali delle lenti hanno un impatto significativo sulle prestazioni di focalizzazione del raggio laser. Ad esempio, una lente con lunghezza focale corta può focalizzare rapidamente il raggio laser, con conseguente riduzione delle dimensioni del punto focale. Questa focalizzazione ad alta densità di energia è adatta per attività di saldatura che richiedono un controllo preciso, come la saldatura di componenti microelettronici o la saldatura di piastre sottili ad alta precisione. In queste applicazioni, più piccola è la messa a fuoco, maggiore è la precisione della saldatura e più stretta è la saldatura.
Tuttavia, lo svantaggio delle lenti a corta lunghezza focale è che hanno capacità di penetrazione limitate e non sono adatte a materiali spessi o a lavori di saldatura profonda. Per questo tipo di applicazione, sono più adatte lenti a lunga lunghezza focale. Le lenti a lunga lunghezza focale focalizzano il raggio laser più in profondità, producendo una dimensione del punto focale maggiore e una maggiore profondità di messa a fuoco, aumentando così la profondità di saldatura. Questa lente è spesso utilizzata per lavori di saldatura che richiedono una penetrazione profonda, come la saldatura di lamiere spesse o parti strutturali nell'industria pesante.
Inoltre, il materiale della lente influirà anche sull'efficienza di trasmissione e sulla qualità della messa a fuoco del raggio laser. Un materiale di alta qualità per lenti può ridurre la perdita di energia del laser quando passa attraverso la lente, assicurando che la messa a fuoco del raggio laser sia più chiara e stabile. La scelta del materiale e del design della lente appropriati è il primo passo per ottimizzare la messa a fuoco del raggio laser, che è direttamente correlata alla qualità della saldatura.
Diametro del fascio
Il diametro del raggio laser è un altro fattore importante che influenza la messa a fuoco. Si riferisce alla larghezza del raggio laser quando non è messo a fuoco. La dimensione del diametro del raggio determina la dimensione focale del raggio laser dopo che è stato messo a fuoco. Un diametro del raggio più grande generalmente si traduce in una dimensione focale più grande, che è adatta per applicazioni che richiedono una saldatura più ampia. Ad esempio, nelle attività di saldatura che richiedono la copertura di un'ampia area di contatto o la creazione di connessioni superficiali, una dimensione focale più grande può fornire una copertura sufficiente per garantire una connessione stabile dei materiali.
Al contrario, un diametro del fascio più piccolo può formare un punto focale più piccolo, fornendo così una maggiore densità di energia e precisione di saldatura. Ciò è particolarmente importante per le attività di saldatura che richiedono un controllo preciso, come la microsaldatura o la lavorazione di precisione. Regolando il diametro del fascio, gli ingegneri di saldatura possono trovare il miglior equilibrio tra dimensione focale e precisione di saldatura per ottimizzare la qualità della saldatura.
Lunghezza focale
La lunghezza focale si riferisce alla distanza dalla lente al punto focale del raggio laser ed è un parametro importante che determina la capacità di messa a fuoco del raggio laser. La scelta della lunghezza focale influisce direttamente sulla dimensione del punto focale e sulla profondità di messa a fuoco del raggio. Una lente con lunghezza focale corta consente di mettere a fuoco rapidamente il raggio laser su una distanza più breve, formando una dimensione focale più piccola. Questa configurazione generalmente fornisce una maggiore densità di energia, consentendo al laser di fondere rapidamente il materiale, ed è adatta per applicazioni che richiedono elevata precisione e saldatura veloce.
Tuttavia, una lunghezza focale corta può anche limitare la profondità di saldatura perché la messa a fuoco è concentrata sulla superficie del materiale o vicino alla superficie, rendendo difficile ottenere una penetrazione profonda. Per attività che richiedono una saldatura più profonda, è più adatta una lente con lunghezza focale lunga. Una lente con lunghezza focale lunga può focalizzare il raggio laser su una distanza maggiore, formando una dimensione focale maggiore, fornendo così capacità di penetrazione più profonde. Tuttavia, in questo caso, la densità di energia può diminuire e anche la precisione della saldatura può essere influenzata. Pertanto, la scelta della lunghezza focale deve essere ponderata in base alle specifiche esigenze di saldatura per ottenere il miglior equilibrio tra penetrazione e precisione della saldatura.
Qualità del raggio
La qualità del raggio è spesso espressa in termini di fattore M², che è una misura fondamentale della capacità di messa a fuoco di un raggio laser. Più il fattore M² è vicino a 1, migliore è la qualità del raggio e il raggio laser può essere messo a fuoco meglio, creando una messa a fuoco più piccola e concentrata. Un raggio di alta qualità significa maggiore densità di energia e controllo più preciso, adatto per attività di saldatura impegnative, come la saldatura di componenti ad alta precisione o la saldatura di pezzi lavorati di forma complessa.
Al contrario, un raggio laser con scarsa qualità del raggio causerà un aumento della messa a fuoco e una distribuzione irregolare dell'energia, riducendo così la precisione e la qualità della saldatura. Le saldature possono apparire irregolari e persino produrre difetti come pori, crepe o saldature scadenti. Pertanto, migliorare la qualità del raggio è un mezzo importante per migliorare la qualità della saldatura. Ottimizzando la progettazione del generatore laser e utilizzando ottiche di alta qualità, gli ingegneri di saldatura possono migliorare significativamente la qualità del raggio, aumentando così l'affidabilità e la coerenza della saldatura.
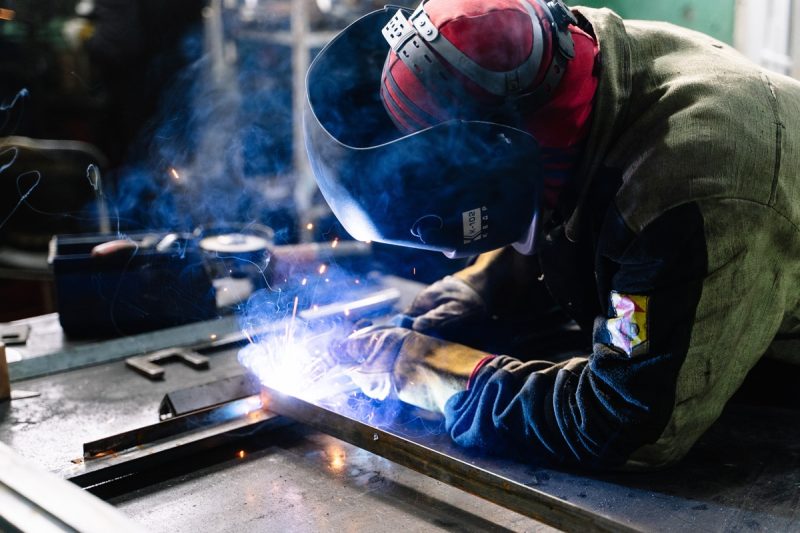
L'influenza della focalizzazione del raggio laser sulla qualità della saldatura
L'impostazione della messa a fuoco del raggio laser svolge un ruolo fondamentale nel processo di saldatura, influenzando direttamente diversi parametri chiave della saldatura, come profondità di penetrazione, larghezza della saldatura, apporto di calore, velocità di saldatura e minimizzazione dei difetti. Attraverso un controllo preciso della messa a fuoco del raggio laser, la qualità della saldatura può essere notevolmente migliorata per soddisfare le esigenze di diverse applicazioni.
Profondità di penetrazione
La corretta impostazione della messa a fuoco del raggio laser ha un impatto diretto sulla profondità di penetrazione della saldatura. La profondità di penetrazione si riferisce alla profondità alla quale il raggio laser può penetrare efficacemente il materiale e formare un giunto forte. Nella saldatura laser, quando la messa a fuoco è impostata sulla superficie del pezzo in lavorazione o al suo interno, l'energia del raggio laser è concentrata in quella posizione, consentendo al laser di fondersi rapidamente e penetrare il materiale. Questa concentrazione ad alta densità di energia consente una saldatura profonda, che è particolarmente importante per pezzi in lavorazione più spessi. La corretta impostazione della messa a fuoco assicura la penetrazione completa della saldatura ed evita il fenomeno della penetrazione incompleta, garantendo così la resistenza e l'affidabilità del giunto saldato.
In alcune applicazioni specifiche, come la saldatura di piastre spesse o la saldatura di componenti industriali pesanti, i requisiti di profondità di penetrazione sono molto elevati. Regolando con precisione la posizione di messa a fuoco, gli ingegneri possono ottimizzare la profondità di penetrazione e garantire che la struttura interna del giunto saldato sia uniforme e priva di difetti. Questo controllo preciso non solo migliora la resistenza della saldatura, ma aumenta anche la durata e la sicurezza del giunto nell'applicazione effettiva.
Larghezza di saldatura
L'impostazione della messa a fuoco ha anche un impatto importante sulla larghezza della saldatura. La larghezza della saldatura si riferisce alla larghezza laterale della saldatura formata dal materiale fuso durante il processo di saldatura laser. In genere, una dimensione di messa a fuoco più piccola produce una saldatura più stretta, adatta per applicazioni che richiedono una saldatura fine. Ad esempio, nella saldatura di componenti microelettronici o nella fabbricazione di strumenti di precisione, una saldatura più stretta può ridurre lo spreco di materiale e migliorare l'estetica e la funzionalità della parte saldata.
Al contrario, una dimensione di messa a fuoco più grande determina una saldatura più ampia, adatta per saldare parti strutturali che richiedono un'area di contatto più ampia o una resistenza maggiore. Ad esempio, nella costruzione di navi o nella fabbricazione di grandi apparecchiature meccaniche, una saldatura ampia può fornire un'area di contatto di saldatura più ampia e migliorare la resistenza e la stabilità della parte saldata. Pertanto, regolando la dimensione di messa a fuoco del raggio laser, la larghezza della saldatura può essere controllata in modo flessibile per soddisfare diversi requisiti di saldatura, ottimizzando così la qualità della saldatura e le prestazioni del processo.
Apporto termico
La posizione focale del raggio laser influenza direttamente l'apporto di calore durante il processo di saldatura. L'apporto di calore si riferisce all'energia trasferita dal laser al materiale durante il processo di saldatura, che determina direttamente il grado di fusione del materiale e la dimensione della zona termicamente alterata (HAZ). La zona termicamente alterata si riferisce all'area del materiale che viene riscaldata ma non fusa durante il processo di saldatura e solitamente si verifica una deformazione termica o un degrado delle prestazioni.
Quando la messa a fuoco del raggio laser è concentrata sull'area di saldatura, la densità di energia è elevata e l'apporto di calore è concentrato, così il materiale può fondersi rapidamente e completare la saldatura. Questo controllo preciso del calore aiuta a ridurre le dimensioni della zona interessata dal calore, riducendo così il rischio di deformazione termica durante la saldatura ed è particolarmente adatto per attività di saldatura che richiedono elevata precisione e basso apporto di calore, come la saldatura di materiali a pareti sottili o strutture complesse. In queste applicazioni, la riduzione al minimo della zona interessata dal calore può mantenere l'integrità e le proprietà meccaniche del materiale e garantire la qualità del giunto saldato.
Velocità di saldatura
L'impostazione della messa a fuoco del raggio laser ha un'influenza importante sulla velocità di saldatura. La velocità di saldatura si riferisce alla velocità alla quale il raggio laser si muove sulla superficie del pezzo, solitamente misurata in millimetri al secondo (mm/s). L'impostazione corretta della messa a fuoco può migliorare l'efficienza di utilizzo dell'energia laser, consentendo al raggio laser di fondere il materiale più velocemente e più stabilmente durante il processo di saldatura, accelerando così la velocità di saldatura. Velocità di saldatura più elevate non solo migliorano l'efficienza produttiva, ma riducono anche il tempo in cui il materiale è esposto ad alte temperature, riducendo ulteriormente il rischio di deformazione termica e danni al materiale.
Tuttavia, impostazioni di messa a fuoco non corrette possono causare dispersione di energia e non riuscire a mettere a fuoco completamente l'area di saldatura, riducendo così la velocità di saldatura. La diminuzione della velocità di saldatura non solo influisce sull'efficienza produttiva, ma può anche portare a una qualità di saldatura instabile, come saldature irregolari e un difficile controllo del bagno fuso. Pertanto, ottimizzando l'impostazione di messa a fuoco, gli ingegneri di saldatura possono mantenere coerenza e affidabilità della qualità di saldatura aumentando al contempo la velocità di saldatura.
Ridurre al minimo i difetti
L'ottimizzazione delle impostazioni di messa a fuoco del raggio laser è fondamentale per ridurre i difetti di saldatura. Durante il processo di saldatura, i difetti comuni includono pori, crepe, penetrazione incompleta e saldatura scadente. Questi difetti non solo riducono la resistenza del giunto saldato, ma possono anche causare cedimenti strutturali o pericoli per la sicurezza. Regolando con precisione la posizione di messa a fuoco del raggio laser, il verificarsi di questi difetti può essere ridotto in modo efficace.
L'impostazione corretta della messa a fuoco assicura uniformità e coerenza della saldatura e riduce l'accumulo di stress interno, riducendo così il rischio di crepe e pori durante il processo di saldatura. Inoltre, la posizione di messa a fuoco appropriata può anche migliorare il processo di formazione e solidificazione del bagno fuso ed evitare il verificarsi di una saldatura scadente. Ottimizzando le impostazioni di messa a fuoco del raggio laser, gli ingegneri di saldatura possono migliorare significativamente la stabilità e l'affidabilità della qualità della saldatura, garantendo la durata dei giunti saldati per lunghi periodi di utilizzo.
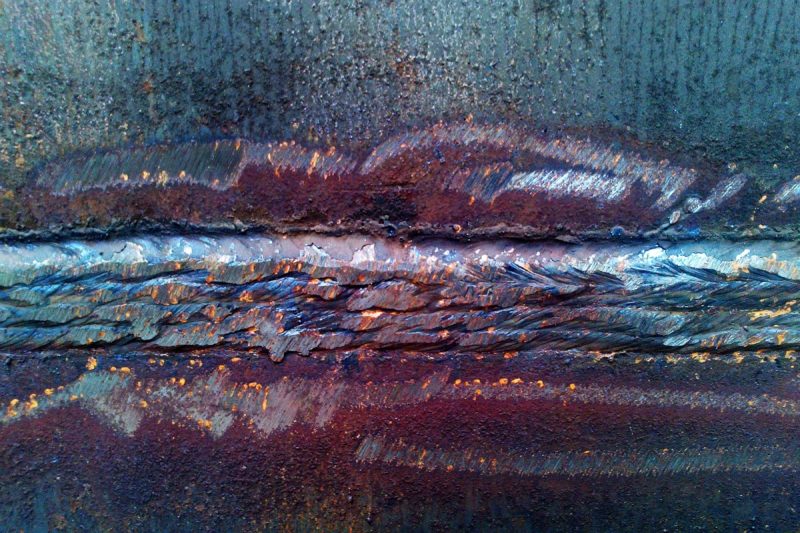
Effetti di un'impostazione di messa a fuoco errata
Nel processo di saldatura laser, l'impostazione precisa della messa a fuoco è fondamentale. Tuttavia, se la messa a fuoco non è impostata correttamente, avrà una serie di effetti negativi sulla qualità della saldatura e sull'efficienza della produzione. Di seguito sono riportati alcuni problemi specifici che possono essere causati da un'impostazione della messa a fuoco non corretta:
Penetrazione superficiale
Quando la messa a fuoco del raggio laser non è impostata correttamente, specialmente quando la posizione di messa a fuoco è troppo alta o troppo bassa, il raggio laser potrebbe non essere in grado di penetrare efficacemente il pezzo in lavorazione. In questo caso, l'energia laser non può essere completamente concentrata nell'area da saldare, con conseguente profondità di saldatura insufficiente. Questo fenomeno di penetrazione superficiale influisce direttamente sulla resistenza e la fermezza del giunto saldato. I giunti saldati a penetrazione superficiale potrebbero non essere in grado di resistere allo stress durante l'uso, con conseguente guasto o frattura prematura della struttura, e non possono soddisfare i requisiti delle applicazioni pratiche, specialmente nelle applicazioni industriali che richiedono elevata resistenza e alta affidabilità, come l'industria aerospaziale, la produzione automobilistica e i macchinari pesanti. Pertanto, la penetrazione superficiale non solo riduce le prestazioni del giunto saldato, ma può anche comportare gravi rischi per la sicurezza.
Eccessivo apporto di calore
Un'impostazione di messa a fuoco non corretta può anche portare a un apporto di calore eccessivo, specialmente quando la messa a fuoco è troppo concentrata sulla superficie del materiale. In questo caso, l'energia del raggio laser non può essere dispersa efficacemente nello strato profondo del materiale ma è concentrata sulla superficie, con conseguente accumulo eccessivo di calore in aree locali.
Ciò causerà diversi problemi: in primo luogo, la zona termicamente alterata (HAZ) si allarga e la struttura del materiale potrebbe subire cambiamenti avversi, come l'ingrossamento della grana o la trasformazione di fase, che a loro volta influenzano le proprietà meccaniche del materiale. In secondo luogo, un apporto di calore eccessivo indurrà una deformazione termica del pezzo, con conseguente diminuzione della precisione dimensionale del pezzo, in particolare nei processi di produzione che richiedono elevata precisione e piccole tolleranze, come la saldatura di componenti elettronici e strumenti di precisione. Inoltre, il calore eccessivo potrebbe anche causare problemi come l'ossidazione superficiale e la bruciatura del materiale, riducendo ulteriormente la qualità e l'estetica della saldatura. Pertanto, il controllo dell'apporto di calore è fondamentale per mantenere l'integrità strutturale del materiale e la qualità della saldatura.
Qualità di saldatura incoerente
Un'impostazione di messa a fuoco non corretta può portare a incoerenza nella qualità della saldatura, il che è un problema serio nella produzione effettiva. Quando la messa a fuoco del raggio laser non può essere allineata con precisione con il percorso di saldatura, la larghezza, la profondità e la morfologia della saldatura possono variare in modo significativo sullo stesso pezzo. Questa incoerenza determina proprietà meccaniche irregolari della saldatura, che influiscono sulla resistenza e sulla durata complessive del giunto saldato. Inoltre, l'incoerenza delle saldature può anche influire sulla qualità dell'aspetto del prodotto, specialmente in applicazioni che richiedono un'elevata qualità visiva, come l'elettronica di consumo e la produzione di dispositivi medici, dove la scorrevolezza e l'uniformità delle saldature sono fondamentali. Una qualità di saldatura incoerente può anche aumentare la complessità della lavorazione successiva, come la necessità di ulteriori fasi di rettifica, riparazione e ispezione, aumentando così i costi e i tempi di produzione.
Efficienza ridotta
Impostazioni di messa a fuoco errate possono ridurre significativamente l'efficienza della saldatura. Quando il raggio laser non riesce a concentrarsi completamente sull'area critica del pezzo, il tasso di utilizzo dell'energia diminuisce e la velocità di saldatura diminuisce. Man mano che la velocità di saldatura rallenta e il ciclo di produzione si estende, ciò non solo riduce l'efficienza complessiva della linea di produzione, ma aumenta anche il costo di produzione per unità di tempo. Soprattutto nella produzione su larga scala, una ridotta efficienza può danneggiare la capacità produttiva e i tempi di consegna di un'azienda, il che può portare a ritardi negli ordini e a una ridotta soddisfazione del cliente. Inoltre, i tassi di rilavorazione possono aumentare a causa di difetti di saldatura che possono derivare da impostazioni di messa a fuoco errate, aumentando ulteriormente i costi di produzione e lo spreco di tempo. Pertanto, garantire che le impostazioni di messa a fuoco siano corrette è fondamentale per mantenere un processo di produzione efficiente e controllare i costi di produzione.
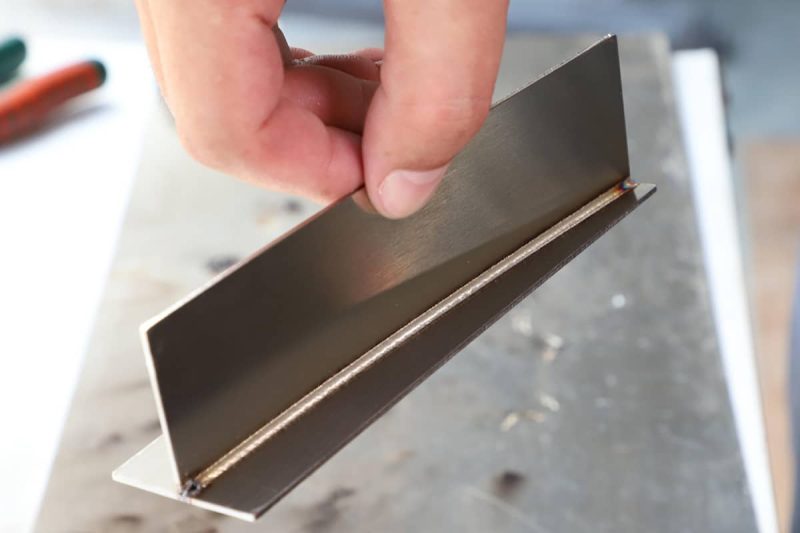
Ottimizzare la messa a fuoco del raggio laser per una saldatura di alta qualità
Per ottenere risultati di saldatura di alta qualità durante la saldatura laser, è necessario ottimizzare le prestazioni di messa a fuoco del raggio laser. L'ottimizzazione della messa a fuoco del raggio laser coinvolge molti aspetti della tecnologia, tra cui l'analisi del raggio, la regolazione dei parametri di processo e l'ottica adattiva avanzata. Questi metodi si completano a vicenda e aiutano a garantire l'uso efficace dell'energia del raggio laser, migliorando così la qualità della saldatura e l'efficienza della produzione.
Analisi del fascio
L'analisi del raggio è il primo passo per ottimizzare le prestazioni di messa a fuoco del raggio laser. Misurando e analizzando in dettaglio i parametri chiave del raggio laser, è possibile ottenere una comprensione più approfondita del comportamento del raggio laser durante il processo di saldatura. L'analisi del raggio solitamente include i seguenti aspetti importanti:
- Misurazione del diametro del raggio: la misurazione del diametro del raggio laser in diverse posizioni può aiutare a determinare come il raggio laser viene focalizzato dopo essere passato attraverso la lente. Un diametro del raggio più piccolo generalmente significa una maggiore densità di energia, che è fondamentale per ottenere una penetrazione profonda e una saldatura ad alta precisione.
- Misurazione della posizione di messa a fuoco: misurando la posizione della messa a fuoco del raggio laser, puoi assicurarti che il raggio laser sia accuratamente focalizzato su una parte specifica del pezzo in lavorazione. Il controllo preciso della posizione di messa a fuoco aiuta a ottimizzare la profondità e la qualità della saldatura, evitando problemi come penetrazione superficiale o eccessivo apporto di calore.
- Analisi del fattore M²: il fattore M² è un indicatore importante della qualità del raggio laser, che riflette la capacità di messa a fuoco del raggio laser. Analizzando il fattore M², è possibile valutare se il raggio laser ha buone prestazioni di messa a fuoco. Un fattore M² inferiore indica generalmente che il raggio laser è di migliore qualità e può essere messo a fuoco in modo più efficace, migliorando così la precisione e la qualità della saldatura.
L'analisi del raggio fornisce una base scientifica per la saldatura laser, consentendo agli operatori di ottimizzare le regolazioni in base alle specifiche esigenze di saldatura. L'analisi del raggio passante consente di identificare e risolvere potenziali problemi come lo spostamento della messa a fuoco o il degrado della qualità del raggio, assicurando che il raggio laser sia sempre in condizioni ottimali, migliorando così la qualità complessiva della saldatura.
Parametri di processo
Oltre all'ottimizzazione del raggio stesso, anche la corretta impostazione dei parametri del processo di saldatura è un fattore importante per garantire l'effetto di focalizzazione del raggio laser. I parametri di processo includono potenza laser, velocità di saldatura, flusso di gas di protezione, ecc., che insieme determinano l'immissione di energia e l'efficienza di trasmissione del raggio laser. Di seguito sono riportati alcuni punti chiave di ottimizzazione per i parametri di processo chiave:
- Potenza laser: la potenza laser influisce direttamente sull'apporto energetico durante la saldatura. Una potenza troppo elevata può portare a un apporto di calore eccessivo, causando la deformazione del pezzo o la bruciatura del materiale; una potenza troppo bassa può portare a una saldatura incompleta o a una penetrazione superficiale. Pertanto, una regolazione accurata della potenza laser è la chiave per garantire la qualità della saldatura in base alle caratteristiche del materiale e ai requisiti di saldatura.
- Velocità di saldatura: la velocità di saldatura è strettamente correlata alla potenza laser, che determina il tempo di residenza del raggio laser sul pezzo in lavorazione. Una velocità di saldatura più lenta può aumentare la profondità di penetrazione, ma può causare l'espansione della zona interessata dal calore; una velocità maggiore aiuta a ridurre la deformazione termica e a migliorare l'efficienza produttiva. Il miglior effetto di saldatura può essere ottenuto bilanciando la velocità di saldatura e la potenza laser.
- Flusso di gas di protezione: durante la saldatura laser, l'uso di gas di protezione come argon o azoto può prevenire l'ossidazione e la contaminazione dell'area di saldatura. La regolazione del flusso di gas di protezione è essenziale per mantenere la qualità della saldatura. Un flusso di gas troppo alto o troppo basso può influire sulla formazione e sulla qualità della saldatura, quindi deve essere regolato con precisione in base ai requisiti del materiale e del processo.
Ottimizzando i parametri di processo è possibile garantire che l'energia del raggio laser venga sfruttata appieno, riducendo così i difetti di saldatura quali pori, crepe e penetrazione incompleta e migliorando la resistenza e la consistenza del giunto saldato.
Parametri di processo
L'ottica adattiva è una tecnologia avanzata di regolazione ottica che può ottimizzare la posizione focale e la forma del raggio laser in tempo reale. L'ottica adattiva regola dinamicamente il raggio laser durante il processo di saldatura per garantire che il raggio laser sia sempre nella posizione focale ottimale per far fronte a diversi pezzi e condizioni di saldatura. Di seguito sono riportate applicazioni specifiche dell'ottica adattiva nella saldatura laser:
- Regolazione della messa a fuoco in tempo reale: l'ottica adattiva può monitorare la posizione focale del raggio laser in tempo reale e regolarla in base alla morfologia della superficie del pezzo e al percorso di saldatura. Questa capacità di regolazione dinamica consente al raggio laser di mantenere una messa a fuoco ad alta precisione durante attività di saldatura complesse, in particolare quando si ha a che fare con pezzi con forme irregolari o spessori variabili.
- Ottimizzazione della morfologia del raggio: oltre alla posizione focale, la tecnologia dell'ottica adattiva può anche regolare la morfologia del raggio laser, ad esempio modificando la forma del punto o la distribuzione dell'energia del raggio. Questa regolazione può aiutare a ottimizzare la morfologia e la qualità della saldatura e a ridurre i difetti di saldatura, in particolare nella saldatura di materiali multistrato o materiali compositi.
- Sistema di correzione automatica: i sistemi di ottica adattiva sono solitamente dotati di funzioni di correzione automatica in grado di rilevare e compensare le deviazioni del raggio causate da cambiamenti nei componenti ottici o nell'ambiente. Questa funzione garantisce la stabilità e la coerenza del raggio laser, mantenendo risultati di saldatura di alta qualità anche in condizioni di saldatura a lungo termine o di processo complesse.
L'introduzione della tecnologia di ottica adattiva ha notevolmente migliorato la flessibilità e la precisione della saldatura laser, rendendo possibile l'adattamento della saldatura laser a scenari applicativi più complessi e diversificati. Ad esempio, nella produzione automobilistica, la tecnologia di ottica adattiva può essere utilizzata per saldare parti strutturali della carrozzeria e, nell'industria aerospaziale, può gestire le esigenze di saldatura di giunti di materiali e spessori diversi. Pertanto, l'ottica adattiva non solo migliora la qualità della saldatura, ma migliora anche l'efficienza della produzione e la stabilità del processo.
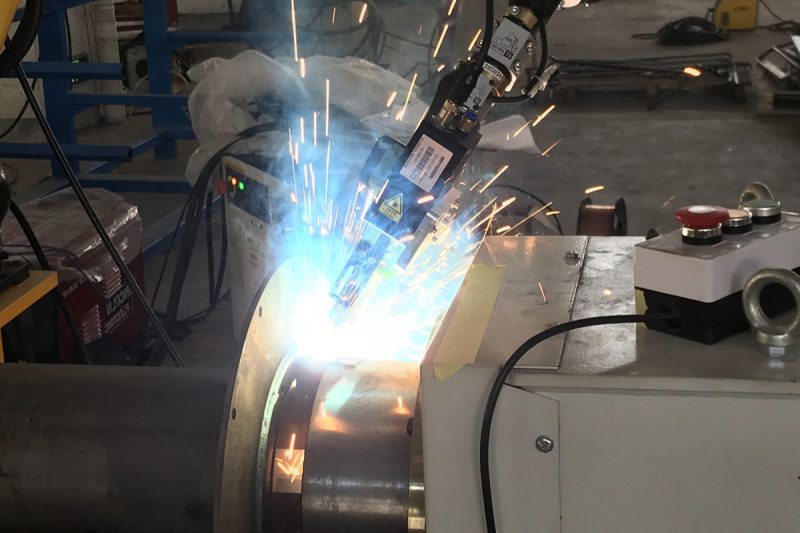
Considerazioni specifiche sull'applicazione
La saldatura laser è ampiamente utilizzata in molteplici settori, ognuno dei quali ha i suoi standard e le sue sfide specifiche per la qualità della saldatura e i requisiti del raggio laser. Di seguito sono riportate considerazioni specifiche per diverse aree di applicazione:
Industria automobilistica
Nella produzione automobilistica, la saldatura laser è ampiamente utilizzata per collegare carrozzerie, telai e parti del motore. Le parti delle auto hanno solitamente forme complesse e severi requisiti di resistenza, quindi la precisione e l'affidabilità della saldatura laser sono cruciali.
- Posizione di messa a fuoco e ottimizzazione delle dimensioni: la saldatura di parti automobilistiche di solito coinvolge una varietà di materiali e spessori. L'impostazione di messa a fuoco corretta può garantire la resistenza e la stabilità della saldatura. La posizione di messa a fuoco deve essere regolata con precisione per soddisfare i requisiti di connessione di diverse parti. Una dimensione di messa a fuoco più piccola può ottenere una saldatura ad alta precisione, ma è anche necessario garantire che la profondità e la resistenza della saldatura soddisfino gli standard di sicurezza della produzione automobilistica.
- Resistenza ed estetica della saldatura: le saldature delle parti automobilistiche non devono solo avere una resistenza sufficiente per sopportare il carico operativo del veicolo, ma devono anche soddisfare i requisiti estetici dell'aspetto. L'elevata precisione della saldatura laser aiuta a ridurre i difetti di saldatura come schizzi e saldature irregolari, migliorando così l'aspetto e la qualità delle parti automobilistiche.
- Compatibilità dei materiali: la produzione automobilistica comporta la connessione di molti materiali diversi, come acciaio, alluminio e materiali compositi. La saldatura laser può gestire le attività di saldatura di questi diversi materiali, ma la posizione di messa a fuoco e le dimensioni del raggio laser devono essere ottimizzate per i diversi materiali per garantire la fermezza e la durata del giunto saldato.
Industria aerospaziale
L'industria aerospaziale ha requisiti estremamente elevati per la qualità della saldatura, specialmente nella fabbricazione di parti strutturali di motori e fusoliere. Quando la saldatura laser viene applicata in questo campo, si dovrebbe prestare particolare attenzione ai seguenti punti:
- Controllo preciso della messa a fuoco: i componenti aerospaziali sono spesso sottoposti a condizioni ambientali estreme, come alte temperature e alte pressioni. Pertanto, l'impostazione della messa a fuoco della saldatura laser deve essere molto precisa per garantire la qualità e la resistenza strutturale della saldatura. L'ottimizzazione della posizione e delle dimensioni della messa a fuoco aiuta a evitare difetti di saldatura, garantendo così la sicurezza e l'affidabilità del giunto saldato.
- Analisi del fascio e ottica adattiva: nella produzione aerospaziale, è spesso necessario saldare geometrie complesse e materiali di spessori diversi. Le tecnologie avanzate di analisi del fascio e di ottica adattiva possono regolare la messa a fuoco del raggio laser in tempo reale per garantire prestazioni ottimali durante il processo di saldatura. Queste tecnologie aiutano a ottenere saldature ad alta precisione e a ridurre i rischi per la sicurezza del volo causati da difetti di saldatura.
- Controllo dei materiali e dell'ambiente: i componenti aerospaziali utilizzano spesso materiali ad alte prestazioni come leghe di titanio e leghe ad alta temperatura. La saldatura di questi materiali richiede parametri di saldatura laser speciali e controllo ambientale per garantire che le proprietà del materiale non vengano influenzate durante il processo di saldatura. L'ottimizzazione della posizione di messa a fuoco e delle dimensioni del raggio laser può ridurre la zona interessata dal calore e garantire l'integrità strutturale del materiale.
Produzione elettronica
Nella produzione di componenti elettronici, la saldatura laser viene utilizzata principalmente per collegare componenti minuscoli come chip, fili e connettori. Poiché questi componenti sono estremamente sensibili al calore, la saldatura laser richiede un'attenzione particolare ai seguenti aspetti:
- Impostazione precisa della messa a fuoco: le parti elettroniche sono molto piccole, quindi l'impostazione della messa a fuoco del raggio laser deve essere molto precisa. Le piccole dimensioni della messa a fuoco possono fornire un'elevata densità di energia, che aiuta a ottenere una saldatura fine. Tuttavia, il controllo della messa a fuoco deve essere molto preciso per evitare un apporto eccessivo di calore alle parti minuscole, che può causare danni o degradazione delle prestazioni.
- Elevata qualità del fascio: la saldatura nella produzione elettronica richiede un'uniformità e una qualità delle saldature estremamente elevate. La saldatura laser con elevata qualità del fascio può fornire una messa a fuoco stabile, ottenendo così giunti saldati di alta qualità. L'ottimizzazione della qualità del fascio può ridurre la deformazione termica e i difetti dei giunti causati dalla saldatura e migliorare l'affidabilità complessiva dei prodotti elettronici.
- Gestione del calore: nella produzione elettronica, il calore generato dalla saldatura laser deve essere rigorosamente controllato per evitare il surriscaldamento dei componenti elettronici sensibili. L'impostazione della messa a fuoco del raggio laser deve garantire un controllo preciso dell'apporto di calore per proteggere le parti dai danni da surriscaldamento, garantendo al contempo la fermezza e la stabilità della saldatura.
Produzione elettronica
Nella produzione di dispositivi medici, la saldatura laser viene utilizzata per collegare materiali ad alta precisione come acciaio inossidabile e leghe di titanio. La saldatura di questi materiali è estremamente impegnativa e comporta le seguenti considerazioni chiave:
- Posizione e dimensione di messa a fuoco precise: i dispositivi medici spesso coinvolgono componenti ad alta precisione come strumenti chirurgici e impianti. L'ottimizzazione della posizione di messa a fuoco e delle dimensioni del raggio laser è fondamentale per garantire l'accuratezza e l'affidabilità del giunto saldato. Una dimensione di messa a fuoco più piccola aiuta a ottenere una saldatura delicata, garantendo la sicurezza e la funzionalità dei dispositivi medici.
- Proprietà dei materiali: i dispositivi medici utilizzano spesso leghe ad alte prestazioni e acciai inossidabili, che hanno requisiti molto rigorosi per la saldatura. L'impostazione della messa a fuoco del raggio laser deve tenere conto della conduttività termica e della reattività termica del materiale per evitare danni termici e cambiamenti strutturali durante la saldatura.
- Requisiti di igiene per giunti saldati: i giunti saldati dei dispositivi medici devono soddisfare rigorosi requisiti di igiene e sterilità. Il controllo preciso della messa a fuoco del raggio laser può ridurre i difetti nei giunti saldati e garantire la sicurezza e l'igiene del prodotto durante l'uso.
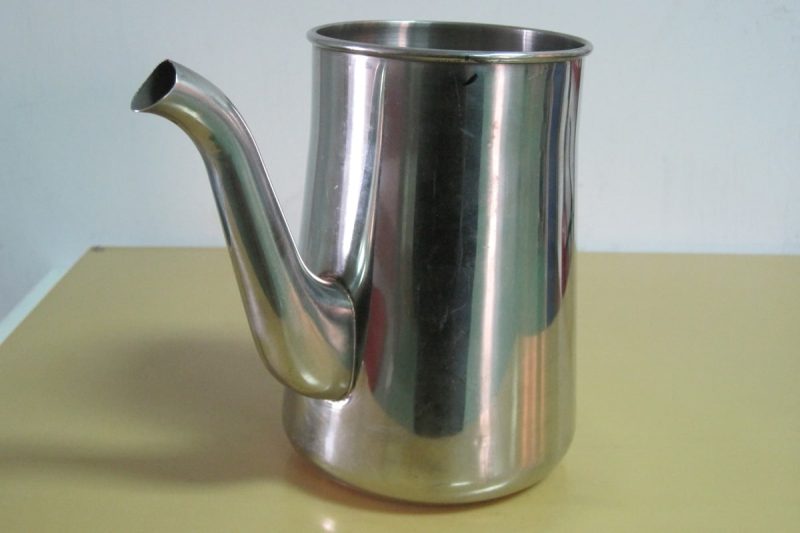
Riassumere
L'impostazione della messa a fuoco del raggio laser ha un profondo impatto sulla qualità della saldatura. La corretta selezione delle lenti e la regolazione del diametro del raggio, della lunghezza focale e della qualità del raggio possono migliorare significativamente la profondità, la larghezza e la coerenza delle saldature, riducendo così i difetti di saldatura. Attraverso un'impostazione precisa della messa a fuoco, non solo è possibile ottenere una penetrazione più profonda e saldature più ampie, ma è anche possibile migliorare l'uniformità del processo di saldatura, garantendo una qualità costante in ogni giunto saldato. Questa coerenza è particolarmente importante nelle applicazioni che richiedono standard elevati, come la produzione di dispositivi aerospaziali e medici.
Inoltre, l'ottimizzazione delle impostazioni di messa a fuoco può ridurre efficacemente i difetti di saldatura come porosità, crepe e penetrazione incompleta. Il controllo preciso della messa a fuoco del raggio laser può ridurre le dimensioni della zona interessata dal calore e ridurre la deformazione termica, migliorando così la stabilità della qualità della saldatura. Allo stesso tempo, impostazioni di messa a fuoco accurate possono aiutare a evitare surriscaldamento e danni ai materiali, garantendo l'integrità e la resistenza dei giunti saldati. Questa ottimizzazione nel processo di saldatura non solo migliora la qualità della saldatura, ma migliora anche l'efficienza della produzione e riduce i costi di produzione.
Man mano che la tecnologia laser continua ad avanzare, lo fa anche la tecnologia di ottimizzazione della messa a fuoco. Analisi avanzata del raggio, tecnologia ottica adattiva e miglioramenti nei parametri di processo promuoveranno ulteriormente l'applicazione della tecnologia di saldatura laser. In futuro, la tecnologia di saldatura laser sarà in grado di gestire attività di saldatura più complesse, soddisfare le esigenze di più settori e svolgere un ruolo sempre più importante nell'industria manifatturiera. Lo sviluppo continuo della tecnologia di ottimizzazione della messa a fuoco promuoverà l'innovazione e il progresso nel settore della saldatura, ottenendo una qualità superiore e una produzione più efficiente.
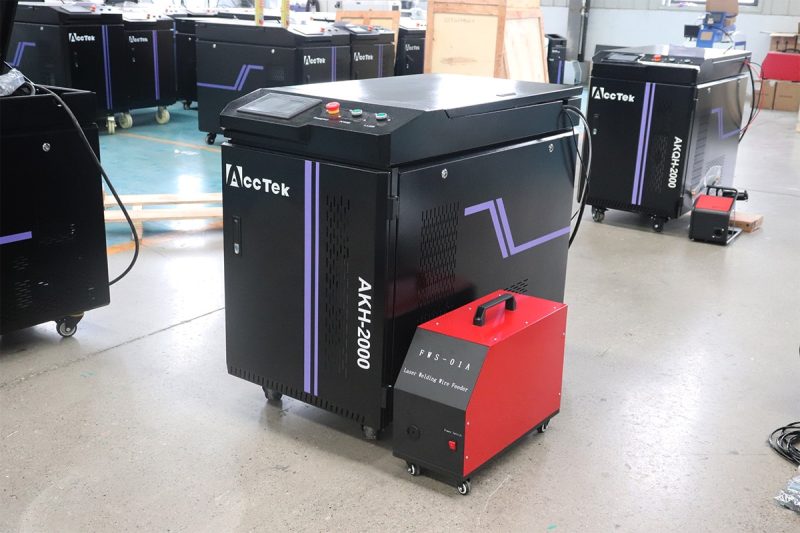
Ottieni soluzioni laser
La scelta della giusta impostazione di messa a fuoco del raggio laser è fondamentale per ottimizzare la qualità della saldatura. Quando lavori con un fornitore affidabile, puoi ottenere supporto tecnico avanzato, consulenza professionale e servizio continuo. In AccTek Laser, offriamo una vasta gamma di apparecchiature di saldatura laser per una varietà di esigenze del settore. I nostri esperti ti aiuteranno a ottimizzare i parametri di messa a fuoco, garantire una qualità di saldatura stabile e massimizzare l'efficienza della produzione. Forniamo anche funzionalità avanzate come la regolazione di precisione della messa a fuoco e sistemi di monitoraggio intelligenti per garantire coerenza e accuratezza della saldatura. Inoltre, il nostro team tecnico fornisce regolare manutenzione delle apparecchiature e supporto tecnico per garantire che le tue apparecchiature funzionino sempre al meglio. Lavorando con AccTek Laser, otterrai una qualità di saldatura efficiente e stabile, ridurrai i rischi di produzione e migliorerai la competitività. Contattaci ora per saperne di più sulle nostre innovative soluzioni di saldatura per aiutare la tua attività a decollare.
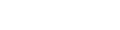
Informazioni sui contatti
- [email protected]
- [email protected]
- +86-19963414011
- N. 3 Zona A, zona industriale di Lunzhen, città di Yucheng, provincia di Shandong.
Ottieni soluzioni laser