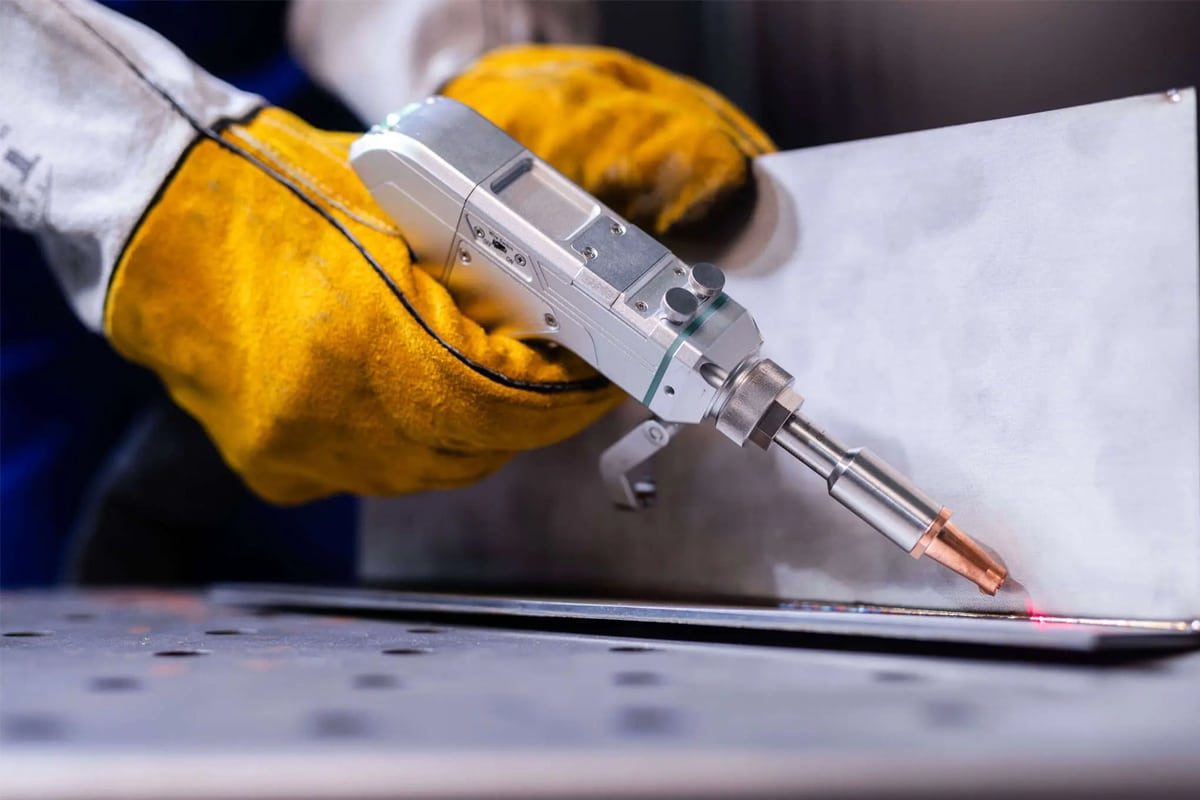
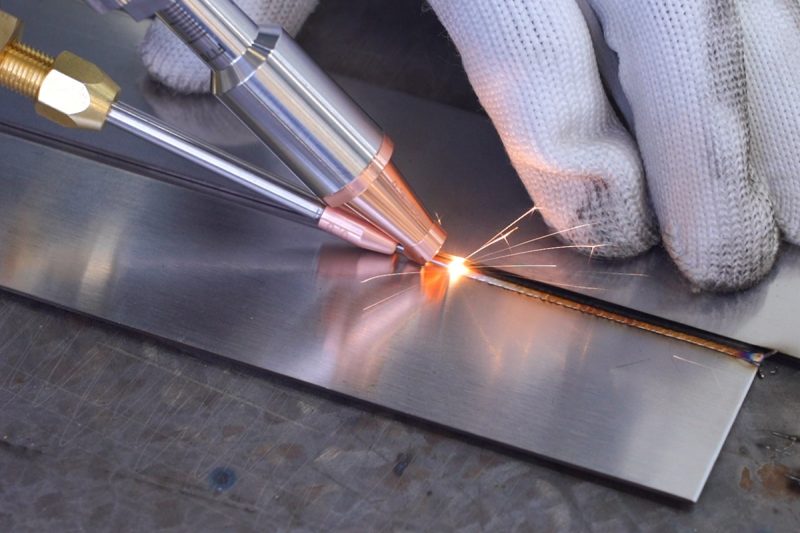
Panoramica della saldatura laser
Cos'è la saldatura laser?
La saldatura laser è un processo di giunzione preciso ed efficiente che utilizza un raggio laser altamente focalizzato per riscaldare e fondere i materiali. Il raggio laser genera una fonte di calore concentrata, consentendo saldature strette e profonde con zone termicamente alterate (HAZ) minime. La saldatura laser funziona in due modalità principali, a seconda della densità di potenza e delle proprietà del materiale:
- Saldatura in modalità Keyhole: in questa modalità, un raggio laser ad alta densità di potenza vaporizza il materiale, creando un keyhole stretto e profondo riempito di metallo fuso e vapore. Il keyhole funge da condotto per l'energia laser, consentendo saldature a penetrazione profonda e con elevato rapporto di aspetto. Questa modalità è ideale per applicazioni che richiedono saldature profonde e strette, come nei settori automobilistico e aerospaziale.
- Saldatura in modalità di conduzione: questa modalità si verifica a densità di potenza inferiori rispetto alla saldatura a foro di serratura, in cui il laser riscalda il materiale senza vaporizzarlo. La conduzione del calore dalla superficie crea un bagno di saldatura poco profondo e più ampio. La saldatura in modalità di conduzione è adatta per materiali sottili o quando si desidera una penetrazione e un apporto di calore minimi.
Vantaggi della saldatura laser
La saldatura laser offre diversi vantaggi che la rendono vantaggiosa rispetto ai metodi di saldatura tradizionali:
- Precisione e accuratezza: il raggio laser concentrato consente un controllo preciso, producendo saldature accurate con una distorsione minima.
- Lavorazione ad alta velocità: l'elevata densità di energia del laser consente velocità di saldatura elevate, aumentando la produttività e riducendo i tempi di ciclo.
- Zona minima interessata dal calore: la ridotta diffusione termica riduce al minimo la distorsione, rendendo la saldatura laser adatta a componenti delicati o sottili.
- Capacità di automazione: la saldatura laser può essere facilmente integrata in sistemi automatizzati e bracci robotici, migliorando l'efficienza nella produzione di grandi volumi.
- Versatilità dei materiali: in grado di saldare un'ampia gamma di metalli e leghe, compresi materiali difficili da saldare, come titanio e acciaio inossidabile.
- Processo senza contatto: non è richiesto alcun contatto fisico, il che riduce l'usura degli utensili ed elimina il rischio di contaminazione degli elettrodi.
Applicazioni della saldatura laser
La saldatura laser viene utilizzata in numerosi settori grazie alle sue capacità e alla sua precisione uniche:
- Industria automobilistica: utilizzata per la saldatura di pannelli della carrozzeria, ingranaggi, componenti della trasmissione e sistemi di scarico, dove elevata precisione e velocità sono essenziali.
- Industria aerospaziale: Adatto per la saldatura di componenti leggeri e ad alta resistenza, come pale di turbine, parti strutturali e componenti di motori.
- Industria elettronica: ideale per la microsaldatura di circuiti delicati, connettori e involucri in dispositivi elettronici.
- Produzione di dispositivi medici: utilizzato per la saldatura di dispositivi medici complessi, strumenti chirurgici e componenti impiantabili in cui precisione e pulizia sono fondamentali.
- Gioielleria e arte: consente riparazioni complesse e la fabbricazione di gioielli dal design complesso e di lavorazioni artistiche in metallo.
- Produzione industriale: applicata all'unione di lamiere, tubazioni e componenti strutturali per impieghi gravosi in vari settori industriali.
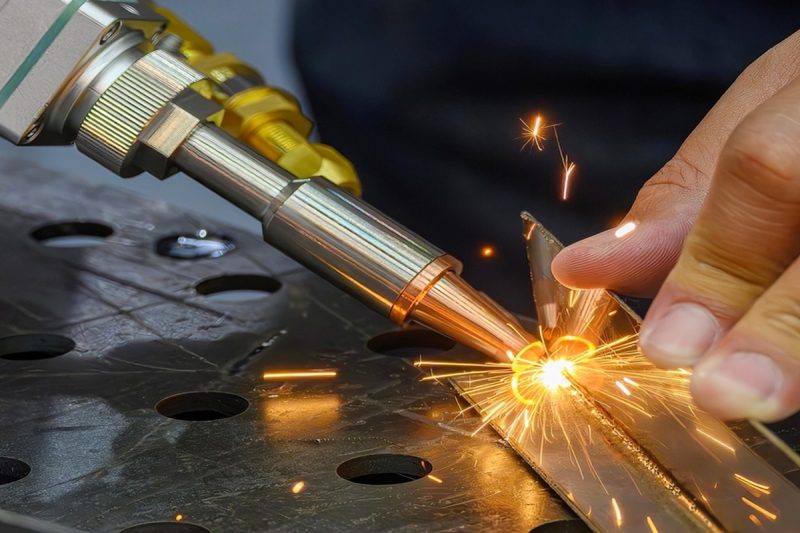
Difetti di saldatura comuni nella saldatura laser
Porosità
Cause
- Contaminazione superficiale: olio, grasso, umidità e ruggine sulla superficie del pezzo in lavorazione possono generare gas quando riscaldati, causando la formazione di bolle intrappolate nella saldatura.
- Problemi relativi al gas di protezione: una copertura inadeguata del gas di protezione, basse portate o un tipo di gas inappropriato possono causare contaminazione atmosferica, come l'intrusione di ossigeno e azoto, che forma sacche di gas.
- Composizione del materiale: elevate concentrazioni di idrogeno, zolfo, carbonio o altre impurità nel metallo di base possono causare lo sviluppo di gas durante la saldatura.
- Raffreddamento rapido: la rapida solidificazione della massa fusa può intrappolare il gas prima che fuoriesca.
Soluzioni
- Pulizia delle superfici: pulire accuratamente i pezzi da saldare prima di saldarli, rimuovendo contaminanti come grasso, olio e ruggine.
- Flusso ottimizzato del gas di protezione: utilizzare gas di protezione appropriati, come argon o elio, assicurando la portata e la copertura corrette per proteggere il bagno di saldatura.
- Selezione e preparazione dei materiali: scegliere materiali con basso contenuto di impurità ed eseguire trattamenti pre-saldatura come la degassificazione.
- Regolazione dei parametri: regolare i parametri laser per consentire un raffreddamento controllato, dando ai gas il tempo di fuoriuscire.
Crepatura
Tipi di cracking
- Cracking a caldo: si verifica ad alte temperature durante la solidificazione a causa di sollecitazioni di trazione o segregazione di impurità (ad esempio zolfo).
- Crepe a freddo: si formano dopo il raffreddamento e sono spesso associate a fragilità da idrogeno, sollecitazioni residue o composizione impropria del materiale.
Cause
- Elevati gradienti termici: rapidi cicli di riscaldamento e raffreddamento possono introdurre tensioni residue che favoriscono la formazione di crepe.
- Composizione del materiale: alcune leghe, in particolare quelle ad alto contenuto di zolfo o carbonio, sono più soggette a cricche.
- Impurità: elementi come zolfo e fosforo possono separarsi ai bordi dei grani, indebolendo la struttura.
- Assorbimento di idrogeno: l'idrogeno introdotto attraverso l'umidità, il gas di protezione contaminato o il metallo di base può causare una formazione ritardata di cricche.
Soluzioni
- Preriscaldamento e trattamento termico post-saldatura: preriscaldare il pezzo in lavorazione per ridurre i gradienti termici ed eseguire trattamenti termici post-saldatura per alleviare le sollecitazioni residue.
- Controllo dei materiali: selezionare materiali con bassi livelli di impurità e ottimizzarne la composizione chimica per ridurre la suscettibilità alle crepe.
- Controllo dell'idrogeno: essiccare i materiali e utilizzare processi a basso contenuto di idrogeno, come l'impiego di gas di protezione secchi ed evitando l'umidità.
- Tecniche di riduzione dello stress: utilizzare dispositivi di fissaggio e giunti progettati correttamente per ridurre al minimo la concentrazione dello stress.
Sottosquadro
Cause
- Apporto termico eccessivo: un'elevata potenza laser o basse velocità di spostamento possono causare la fusione localizzata e la perdita di materiale senza un metallo d'apporto sufficiente.
- Angolo del raggio errato: il disallineamento del raggio laser rispetto al giunto può causare la rimozione del materiale anziché la fusione.
- Messa a fuoco non corretta: una messa a fuoco laser non accurata può concentrare l'energia in modo non uniforme.
Soluzioni
- Ottimizzazione dell'apporto di calore: regola la potenza del laser, la velocità di spostamento e il diametro del raggio per controllare la distribuzione del calore.
- Allineamento del raggio: allineare correttamente il raggio laser con il giunto per garantire una fusione e un riempimento uniformi.
- Tecnica di saldatura: regolare l'angolazione e il posizionamento del laser per ridurre la perdita di materiale.
Mancanza di fusione
Cause
- Apporto termico insufficiente: una bassa potenza laser o una velocità di spostamento eccessiva possono impedire la fusione completa dei materiali di base.
- Preparazione non corretta del giunto: un adattamento non corretto, spazi vuoti o disallineamenti tra i pezzi possono impedire la fusione completa.
- Contaminazione: ossidi superficiali, sporcizia o altri contaminanti possono fungere da barriere alla fusione.
Soluzioni
- Aumentare l'apporto di calore: utilizzare una potenza laser sufficiente o ridurre la velocità di spostamento per ottenere una fusione adeguata.
- Migliora l'adattamento dei giunti: assicura il corretto allineamento e adattamento tra i pezzi in lavorazione per una penetrazione uniforme della saldatura.
- Pulizia delle superfici: rimuovere ossidi, oli e altri contaminanti dalle superfici di saldatura.
Penetrazione incompleta
Cause
- Bassa potenza laser: apporto di energia insufficiente per fondere completamente lo spessore del materiale.
- Elevata velocità di spostamento: il laser si muove troppo rapidamente per riscaldare e fondere completamente il giunto.
- Messa a fuoco non corretta del raggio: una messa a fuoco non corretta del laser può causare una penetrazione superficiale.
Soluzioni
- Aumentare la potenza del laser: regolare le impostazioni di potenza per garantire la penetrazione completa attraverso l'articolazione.
- Ridurre la velocità di spostamento: lasciare più tempo al laser per riscaldarsi e fondere il materiale.
- Messa a fuoco corretta del raggio: mettere a fuoco correttamente il laser per ottenere una profondità di penetrazione costante.
Schizzi
Cause
- Potenza laser eccessiva: impostazioni di potenza elevate possono causare una violenta ebollizione della massa fusa.
- Contaminanti: le impurità superficiali possono reagire con il calore, provocando una rapida vaporizzazione.
- Gas di protezione non idoneo: una protezione inadeguata può favorire l'ossidazione, causando schizzi.
Soluzioni
- Regola i parametri laser: riduci la potenza del laser e ottimizza le impostazioni degli impulsi per evitare un apporto energetico eccessivo.
- Pulizia delle superfici: assicurarsi che le superfici siano prive di contaminanti prima di procedere alla saldatura.
- Ottimizzazione del gas di protezione: utilizzare il gas di protezione appropriato e mantenere le portate corrette.
Irregolarità del cordone di saldatura
Cause
- Velocità di viaggio non uniforme: le fluttuazioni di velocità determinano un apporto di calore non uniforme.
- Variabilità della potenza laser: variazioni nella potenza in uscita possono causare una fusione non uniforme.
- Messa a fuoco del fascio non corretta: una messa a fuoco non allineata provoca una distribuzione non uniforme dell'energia.
Soluzioni
- Mantenere una velocità di avanzamento costante: garantire una velocità uniforme durante l'intero processo di saldatura.
- Stabilizzare la potenza di uscita: utilizzare una fonte di alimentazione stabile per mantenere un'uscita laser costante.
- Regola la messa a fuoco del raggio: assicurati che il raggio sia allineato correttamente e che la messa a fuoco sia rivolta verso un'erogazione uniforme dell'energia.
Bruciare
Cause
- Apporto termico eccessivo: un'elevata potenza laser o basse velocità di spostamento possono causare una fusione eccessiva.
- Materiale sottile: i fogli sottili sono più inclini a bruciare.
- Messa a fuoco del raggio errata: concentrare l'energia in un'area piccola può aggravare la fusione.
Soluzioni
- Ridurre l'apporto di calore: ridurre la potenza del laser o aumentare la velocità di spostamento.
- Amplia la messa a fuoco del raggio: distribuisce l'energia laser in modo più uniforme.
- Utilizzare lo spessore appropriato del materiale: adattare lo spessore del materiale ai requisiti di saldatura.
Deformazione e distorsione
Cause
- Stress termici: rapidi cicli di riscaldamento e raffreddamento causano espansione e contrazione.
- Materiali sottili: più soggetti a deformazioni e flessioni.
- Apporto termico eccessivo: un apporto energetico elevato può causare gravi distorsioni.
Soluzioni
- Ottimizzazione dell'apporto di calore: utilizzare parametri laser controllati per ridurre al minimo il calore eccessivo.
- Fissaggio e serraggio: tenere fermi i pezzi in lavorazione con dispositivi di fissaggio per ridurne il movimento.
- Saldatura bilanciata: utilizzare tecniche che bilanciano il riscaldamento e riducono al minimo lo stress.
Ossidazione e scolorimento
Cause
- Gas di protezione inadeguato: un flusso di gas basso o una copertura insufficiente possono esporre il bagno di saldatura all'aria.
- Composizione del gas non corretta: la scelta errata del gas di protezione potrebbe non riuscire a prevenire l'ossidazione.
- Contaminanti: le impurità superficiali possono reagire e causare ossidazione.
Soluzioni
- Garantire una schermatura adeguata: utilizzare un flusso adeguato di gas di protezione per proteggere il bagno di saldatura.
- Selezionare la composizione del gas appropriata: scegliere un gas di protezione che prevenga efficacemente l'ossidazione (ad esempio, argon).
- Pulizia delle superfici: pulire accuratamente le superfici del pezzo da lavorare per ridurre al minimo le reazioni durante la saldatura.
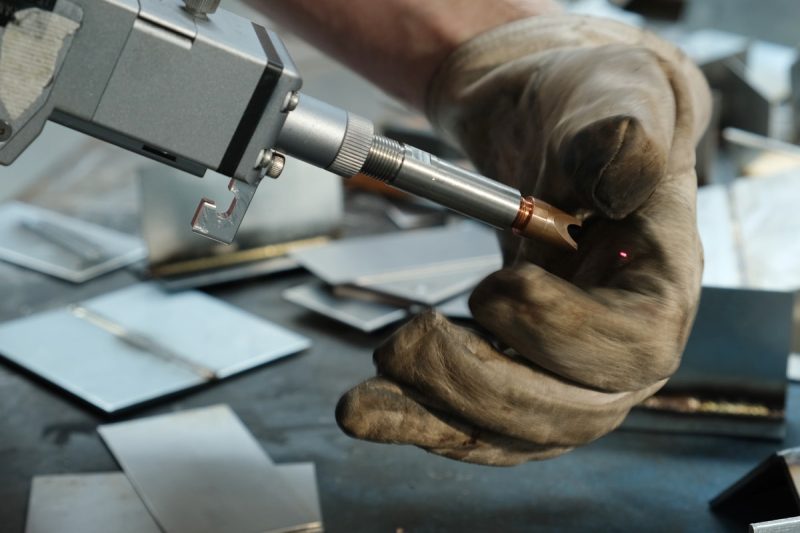
Fattori che influenzano i difetti di saldatura
Proprietà dei materiali
Le proprietà dei materiali saldati svolgono un ruolo significativo nel determinare la qualità della saldatura e la probabilità di difetti.
- Conduttività termica: i materiali con elevata conduttività termica, come l'alluminio, tendono a dissipare rapidamente il calore, richiedendo una maggiore potenza laser o velocità di spostamento più lente per ottenere penetrazione e fusione sufficienti. Un controllo insufficiente può portare a difetti come mancanza di fusione o penetrazione incompleta.
- Punto di fusione: materiali con punti di fusione variabili richiedono parametri laser diversi. Ad esempio, il titanio ha un punto di fusione elevato e richiede un maggiore apporto di energia, mentre materiali con un punto di fusione basso come lo zinco possono subire bruciature se non gestiti con attenzione.
- Riflettività: i materiali altamente riflettenti, come il rame e alcune leghe di alluminio, possono riflettere una parte dell'energia laser, riducendo l'effettivo apporto di calore. Ciò può causare una fusione incompleta, una penetrazione incoerente o spruzzi, poiché l'energia riflessa può influenzare le aree circostanti.
- Composizione del materiale e impurità: elementi come zolfo, fosforo e idrogeno nel materiale possono aumentare la probabilità di difetti come porosità e cricche. Ad esempio, un elevato contenuto di idrogeno può causare porosità, mentre zolfo e fosforo aumentano il rischio di cricche a caldo. La selezione di materiali con bassi livelli di impurità o l'esecuzione di trattamenti pre-saldatura può aiutare ad attenuare questi problemi.
Parametri di saldatura
La selezione e il controllo adeguati dei parametri di saldatura laser sono essenziali per prevenire i difetti. I parametri chiave includono:
- Potenza laser: una potenza laser adeguata è essenziale per ottenere una penetrazione e una fusione complete. Una potenza insufficiente può portare a una mancanza di fusione o a una penetrazione incompleta, mentre una potenza eccessiva può causare bruciature, schizzi e deformazioni.
- Velocità di spostamento: la velocità di spostamento influisce sull'apporto di calore per unità di lunghezza della saldatura. Una velocità troppo elevata può impedire al materiale di riscaldarsi adeguatamente, causando difetti come mancanza di fusione e penetrazione incompleta. Al contrario, una velocità troppo lenta può causare un apporto di calore eccessivo, causando bruciature e distorsioni.
- Messa a fuoco del fascio: la corretta messa a fuoco del fascio è essenziale per la concentrazione di energia. Un disallineamento o una posizione focale non corretta possono portare a una penetrazione insufficiente, profili di cordone irregolari e porosità della saldatura. Per una penetrazione profonda, è necessario un fascio focalizzato con una piccola dimensione dello spot, mentre un fascio defocalizzato può essere adatto per saldature più ampie e poco profonde.
- Durata dell'impulso (nella saldatura laser pulsata): la durata dell'impulso influisce sulla quantità di energia erogata in ogni impulso. Gli impulsi brevi riducono l'apporto di calore e minimizzano il rischio di deformazione, rendendoli ideali per materiali delicati o sensibili al calore. Gli impulsi più lunghi consentono una maggiore penetrazione ma possono aumentare il rischio di difetti come schizzi e porosità.
Progettazione congiunta
La progettazione e la preparazione del giunto possono influenzare notevolmente la qualità della saldatura e la probabilità di difetti.
- Tolleranza di adattamento: un corretto adattamento del giunto è essenziale per ottenere una qualità di saldatura uniforme. Fessure o disallineamenti tra i pezzi possono causare una mancanza di fusione, porosità o penetrazione incoerente. Gli adattamenti stretti consentono un migliore controllo della pozza fusa e riducono al minimo il rischio di difetti.
- Tipo di giunto: diversi tipi di giunto (ad esempio, testa a testa, sovrapposizione, raccordo) richiedono tecniche e parametri di saldatura laser diversi. Ad esempio, giunti testa a testa con allineamento scadente possono causare sottosquadri o mancanza di fusione, mentre giunti sovrapposti con sovrapposizione eccessiva possono causare schizzi e fusione insufficiente.
- Accessibilità: nelle strutture complesse, l'accesso limitato al giunto può limitare la portata del raggio laser, portando a una fusione incompleta o a una formazione irregolare di granuli. Per i giunti con accessibilità limitata sono necessari un fissaggio e un allineamento laser adeguati.
- Preparazione e pulizia: la corretta preparazione e pulizia dell'area di giunzione sono fondamentali, poiché i contaminanti superficiali possono causare porosità, crepe e schizzi. La pulizia rimuove ossidi, oli e altre impurità che possono interferire con la fusione e introdurre difetti.
Fattori ambientali
Le condizioni ambientali nell'area di saldatura possono influenzare direttamente la qualità della saldatura e il verificarsi di difetti.
- Temperatura ambiente: la saldatura a temperature estreme, sia troppo fredde che troppo calde, può influire sulla velocità di raffreddamento della saldatura e portare a stress termico e cricche. Gli ambienti freddi, ad esempio, possono causare un raffreddamento rapido, portando a saldature fragili e cricche.
- Umidità e condensa: l'umidità nell'ambiente può introdurre idrogeno nel bagno di saldatura, aumentando il rischio di porosità e cricche indotte dall'idrogeno. Per saldature di alta qualità è essenziale saldare in un ambiente asciutto e controllato o adottare precauzioni per prevenire l'esposizione all'umidità.
- Qualità e flusso del gas di protezione: il gas di protezione protegge il bagno di saldatura fuso dalla contaminazione atmosferica. Un flusso di gas di protezione inadeguato o l'uso di gas poco puri possono causare ossidazione, porosità e scolorimento. Inoltre, gas di protezione come argon ed elio devono essere utilizzati in base ai requisiti del materiale per prevenire la contaminazione.
- Vibrazioni e movimento: le vibrazioni ambientali o il movimento nell'impostazione di saldatura possono portare a cordoni di saldatura incoerenti e altri difetti. Fissaggi stabili e riduzione al minimo dei movimenti esterni sono essenziali per garantire risultati coerenti.
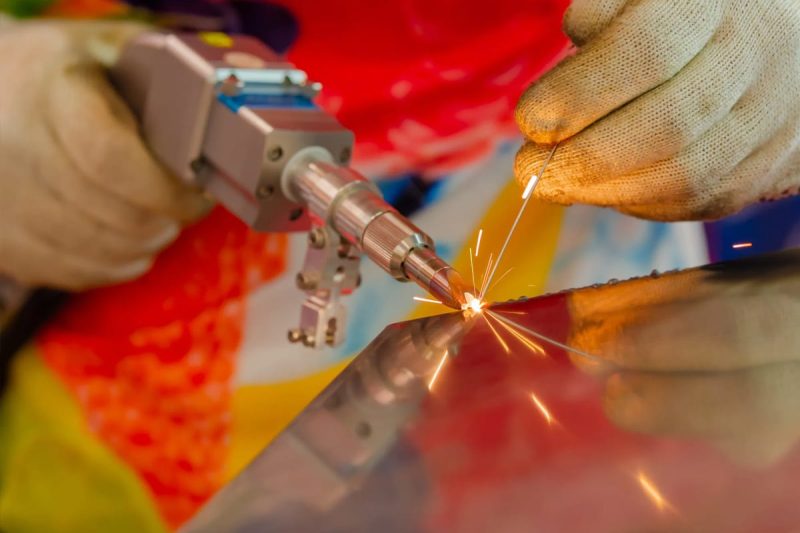
Ulteriori considerazioni e best practice
Selezione corretta del materiale
La scelta dei materiali giusti per la saldatura laser è essenziale per ottenere saldature di alta qualità e ridurre al minimo i difetti.
- Compatibilità dei materiali: assicurarsi che i materiali di base siano compatibili con la saldatura laser. Materiali diversi rispondono in modo diverso all'energia laser a causa di variazioni nei punti di fusione, conduttività termica e riflettività. Ad esempio, materiali riflettenti come l'alluminio potrebbero richiedere misure speciali per ridurre la riflessione e ottimizzare l'assorbimento del calore.
- Purezza del materiale: utilizzare materiali con bassi livelli di impurità, come zolfo e fosforo, che possono contribuire alla porosità, alle crepe e ad altri difetti.
- Spessore del materiale: tenere in considerazione lo spessore dei materiali da saldare, poiché influisce sulla potenza laser richiesta e sull'apporto termico.
Tipo di laser e impostazioni
La scelta del tipo di laser appropriato e la messa a punto delle sue impostazioni sono fattori critici per la riuscita della saldatura laser.
- Tipo di laser: scegli tra laser a onda continua (CW) e laser pulsati in base all'applicazione. I laser CW sono ideali per la saldatura ad alta velocità, mentre i laser pulsati sono adatti per componenti delicati o sensibili al calore.
- Impostazioni di potenza e velocità: ottimizza la potenza del laser, la velocità di spostamento e la durata dell'impulso per ottenere la penetrazione desiderata, ridurre al minimo difetti come schizzi o porosità e controllare l'apporto di calore.
- Messa a fuoco e posizionamento del raggio: il corretto allineamento e la corretta messa a fuoco del raggio sono essenziali per una distribuzione uniforme dell'energia e saldature uniformi.
Progettazione e montaggio dei giunti
Una progettazione e un montaggio adeguati dei giunti garantiscono una qualità di saldatura costante e riducono la probabilità di difetti quali mancanza di fusione, porosità e disallineamento.
- Tolleranze di adattamento: assicurarsi che i giunti abbiano adattamenti stretti e uniformi, riducendo al minimo gli spazi che potrebbero causare una fusione irregolare o porosità.
- Accessibilità alle giunzioni: progettare le giunzioni in modo da consentire un facile accesso al raggio laser, riducendo al minimo il rischio di fusione incompleta o di microsfere irregolari.
- Preparazione del giunto: pulire e preparare adeguatamente le superfici del giunto per rimuovere contaminanti come oli, ossidi e altre impurità.
Selezione del gas di protezione
Il gas di protezione protegge il bagno di saldatura fuso dalla contaminazione atmosferica, prevenendo l'ossidazione, la porosità e altri difetti.
- Tipo di gas: selezionare i gas di protezione appropriati, come argon, elio o miscele, in base al materiale di base e alle caratteristiche di saldatura desiderate. Ad esempio, l'argon è spesso utilizzato per l'acciaio inossidabile, mentre l'elio può migliorare la penetrazione per materiali più spessi.
- Portata: assicurarsi che la portata del gas di protezione sia sufficiente a coprire il bagno di saldatura senza turbolenze o copertura inadeguata.
- Purezza: utilizzare gas di protezione ad elevata purezza per evitare contaminazioni.
Trattamenti pre-saldatura e post-saldatura
I trattamenti pre-saldatura e post-saldatura possono ridurre significativamente la probabilità di difetti e migliorare la qualità complessiva della saldatura.
- Pulizia pre-saldatura: pulire accuratamente i pezzi da lavorare per rimuovere contaminanti, come oli, ruggine e umidità, che possono causare porosità, crepe e altri difetti.
- Preriscaldamento: il preriscaldamento dei materiali, in particolare di quelli soggetti a crepe, può ridurre i gradienti termici e minimizzare le sollecitazioni residue.
- Trattamento termico post-saldatura: eseguire trattamenti termici post-saldatura, come ricottura o distensione, per ridurre le sollecitazioni residue e migliorare le proprietà meccaniche della saldatura.
Formazione degli operatori
Gli operatori qualificati svolgono un ruolo fondamentale nel garantire saldature laser costanti e di alta qualità.
- Formazione tecnica: formare gli operatori sulla corretta gestione delle apparecchiature di saldatura laser, inclusi posizionamento, controllo della velocità e regolazione dei parametri.
- Identificazione dei difetti: insegnare agli operatori a riconoscere i difetti più comuni, le loro cause e come apportare le modifiche necessarie per evitarne il ripetersi.
- Protocolli di sicurezza: assicurarsi che gli operatori siano formati sulle procedure di sicurezza laser per proteggere se stessi e l'ambiente di lavoro.
Manutenzione dell'equipaggiamento
La manutenzione regolare delle apparecchiature di saldatura laser è essenziale per garantire prestazioni costanti e prevenire difetti.
- Pulizia delle ottiche: pulire regolarmente lenti, specchi e altri componenti ottici per mantenere la qualità e la precisione del fascio.
- Calibrazione: calibrare periodicamente i sistemi laser per garantire potenza di uscita, allineamento del raggio e messa a fuoco precisi.
- Ispezione dei componenti: ispezionare e sostituire i componenti usurati o danneggiati, come ugelli e lenti, per mantenere la coerenza della saldatura.
Monitoraggio del processo
Il monitoraggio e il controllo del processo sono essenziali per ottenere saldature uniformi e prive di difetti.
- Monitoraggio in tempo reale: utilizzare sensori e sistemi di monitoraggio per rilevare e correggere in tempo reale le deviazioni nei parametri di saldatura, come fluttuazioni di potenza, velocità di spostamento e messa a fuoco del raggio.
- Registrazione dei dati: registra i parametri e i risultati della saldatura per analizzare le tendenze, identificare le cause principali dei difetti e implementare misure di miglioramento continuo.
- Controlli di qualità: effettuare ispezioni regolari, compresi metodi di prove non distruttive (NDT), per verificare la qualità della saldatura.
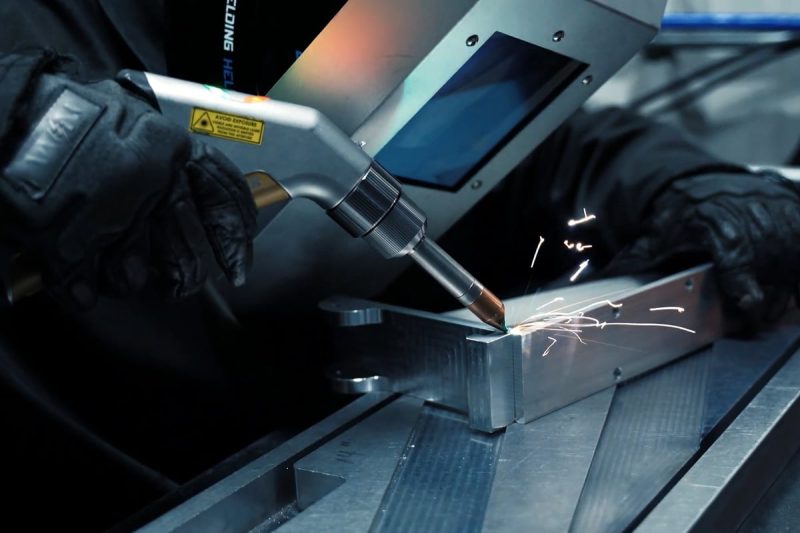
Riepilogo
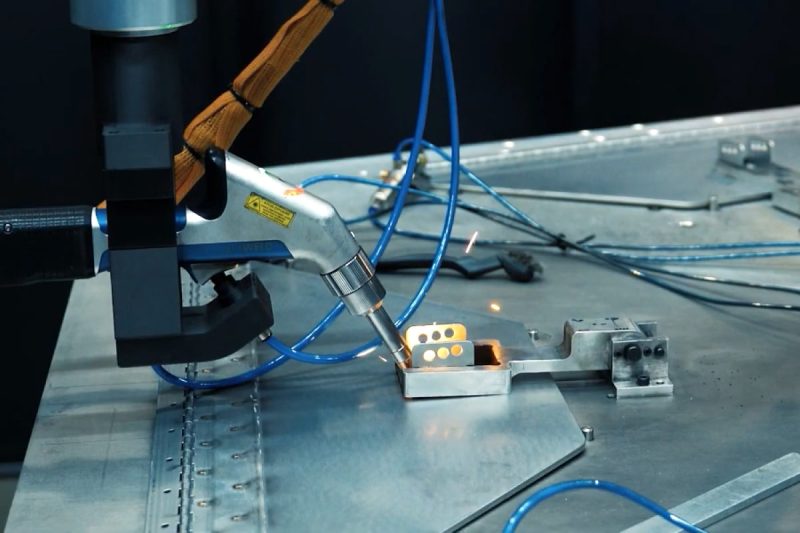
Ottieni soluzioni di saldatura laser
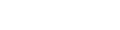
- [email protected]
- [email protected]
- +86-19963414011
- N. 3 Zona A, zona industriale di Lunzhen, città di Yucheng, provincia di Shandong.