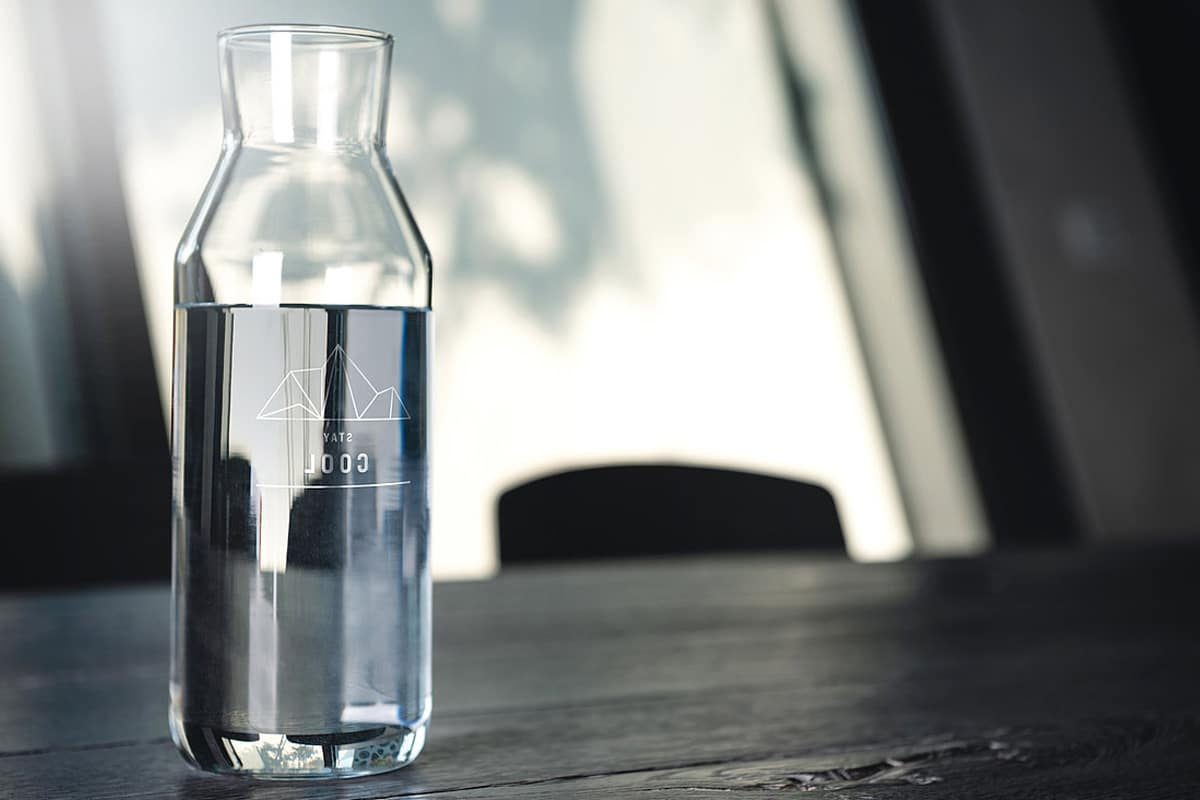
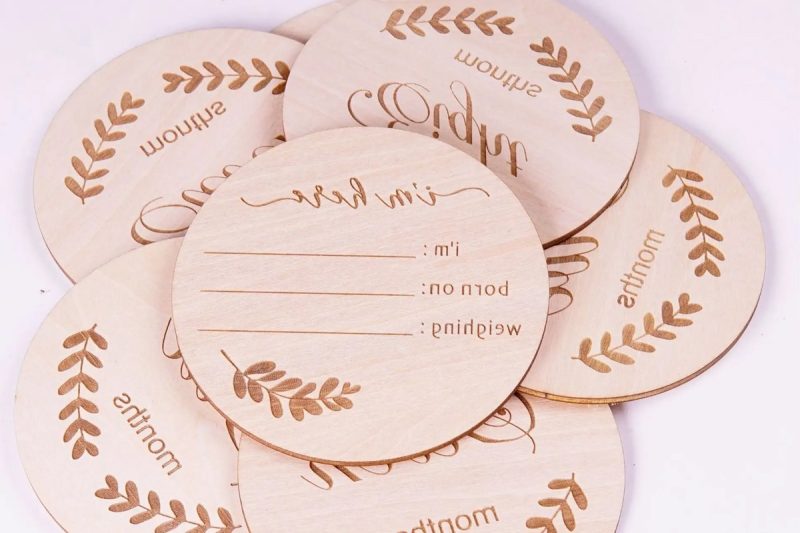
Tipo e sorgente laser
- Laser a fibra: grazie alla loro elevata densità di energia e alle eccellenti caratteristiche di messa a fuoco, i generatori laser a fibra sono particolarmente adatti per la marcatura di materiali metallici, in particolare di materiali come acciaio, alluminio e rame. Marcatura laser fibra può raggiungere una precisione estremamente elevata e viene spesso utilizzato in applicazioni ad alta precisione che richiedono modelli e testo estremamente fini, come la marcatura di componenti elettronici, dispositivi medici e parti di automobili. Inoltre, i laser a fibra hanno un basso consumo energetico e una lunga durata, il che li rende la prima scelta per la marcatura dei metalli.
- Laser CO2: i laser CO2 sono usati principalmente per marcare materiali non metallici, in particolare per materiali come legno, plastica, pelle e carta. Con una lunghezza d'onda di 10,6 micron, può assorbire efficacemente l'energia dei materiali non metallici, quindi è stato ampiamente utilizzato in settori come l'imballaggio, l'abbigliamento e l'artigianato. Le funzioni di taglio e incisione di Marcatura laser CO2 lo rendono inoltre eccezionale nella produzione pubblicitaria, nella decorazione di mobili e nella fabbricazione di modelli.
- Laser ultravioletto (UV): i laser UV sono chiamati sorgenti di luce fredda a causa della loro lunghezza d'onda corta (solitamente 355 nm). Rispetto ad altri tipi di laser, i laser UV hanno una zona termicamente alterata molto piccola, il che significa che la deformazione termica e il danno al materiale saranno notevolmente ridotti durante il processo di marcatura. Ciò lo rende molto adatto per la marcatura fine, specialmente su materiali sensibili al calore come vetro, plastica e ceramica. La marcatura laser UV è spesso utilizzata in settori ad alta precisione come prodotti elettronici, imballaggi cosmetici ed etichette farmaceutiche e può ottenere effetti di marcatura estremamente fini e chiari.
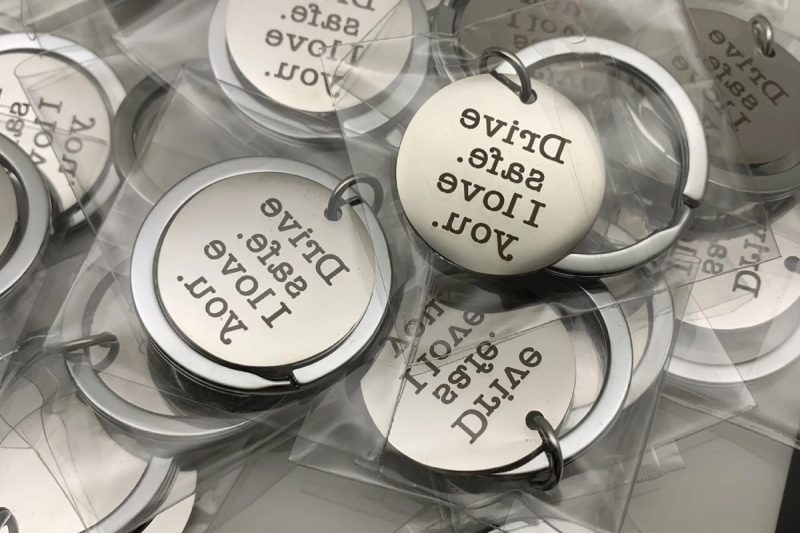
Influenza delle proprietà dei materiali
- Assorbimento e riflettività: i materiali hanno diverse capacità di assorbimento e riflessione per laser di diverse lunghezze d'onda. I materiali con elevato assorbimento possono assorbire meglio l'energia laser e produrre migliori effetti di marcatura, mentre i materiali con elevata riflettività rifletteranno una grande quantità di luce laser e ridurranno l'efficienza di marcatura. Ad esempio, i materiali metallici come alluminio e rame hanno elevata riflettività per i laser a fibra, il che può causare una marcatura insufficiente o poco chiara. Per questo motivo, quando si marcano questi materiali ad elevata riflettività, è solitamente necessario regolare i parametri laser o utilizzare laser di specifiche lunghezze d'onda per migliorare il tasso di assorbimento e ottenere l'effetto di marcatura ideale. Al contrario, i materiali non metallici come plastica o vetro hanno elevati tassi di assorbimento per laser CO2 e UV e la profondità e il contrasto della marcatura sono più facili da controllare.
- Conduttività termica: la conduttività termica del materiale influisce direttamente sulla distribuzione del calore durante il processo di marcatura. I materiali con elevata conduttività termica, come rame, alluminio e altri metalli, possono disperdere rapidamente il calore generato durante il processo di marcatura, ridurre il surriscaldamento locale ed evitare la fusione o la combustione della superficie del materiale. Tali materiali solitamente richiedono una maggiore potenza laser o un tempo di marcatura prolungato durante la marcatura laser per garantire che venga applicata energia sufficiente all'area di marcatura. Per i materiali con bassa conduttività termica, come plastica o legno, il calore è difficile da diffondere rapidamente ed è probabile che si verifichi un surriscaldamento durante il processo di marcatura, con conseguenti deformazioni o danni. Pertanto, quando si elaborano tali materiali, è solitamente necessario ridurre la potenza laser o aumentare le misure di raffreddamento per evitare il surriscaldamento.
- Condizioni della superficie: anche le condizioni della superficie del materiale possono avere un impatto importante sull'effetto di marcatura. Una superficie liscia e pulita assicura che il laser agisca in modo uniforme e produca un motivo di marcatura chiaro e uniforme. Tuttavia, una superficie ruvida o rivestita può causare una distribuzione non uniforme dell'energia laser, con conseguente marcatura poco chiara o contrasto insufficiente. Lo spessore e l'uniformità del rivestimento sono particolarmente importanti. Se il rivestimento non è uniforme, il laser può produrre effetti diversi in aree diverse, con conseguente marcatura non uniforme. Una corretta preparazione della superficie prima della marcatura, come pulizia, molatura o rivestimento, può migliorare significativamente l'effetto di marcatura.
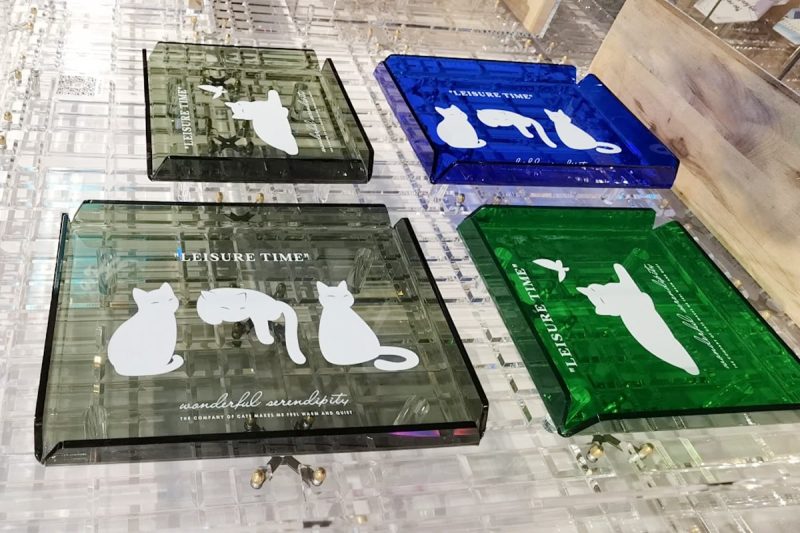
Influenza dei parametri laser
- Impostazione della potenza: la potenza del laser è un fattore importante che influenza la profondità e l'effetto della marcatura. Quando l'impostazione della potenza è troppo alta, l'energia laser è troppo grande, il che può facilmente causare un'ablazione, una fusione o una deformazione eccessive della superficie del materiale, in particolare per materiali sensibili al calore come la plastica o i metalli sottili. Una potenza eccessiva può anche causare bordi ruvidi e irregolari della marcatura, influenzando l'aspetto generale. Quando la potenza è troppo bassa, l'energia laser è insufficiente e non può agire efficacemente sulla superficie del materiale, con conseguenti marcature poco chiare o addirittura difficili da identificare. Pertanto, l'impostazione della potenza deve essere regolata con precisione in base alle caratteristiche del materiale e ai requisiti specifici della marcatura per garantire che sia possibile ottenere una profondità di marcatura sufficiente senza danneggiare la superficie del materiale.
- Frequenza di impulso: la frequenza di impulso si riferisce al numero di impulsi emessi dal generatore laser al secondo, che ha un impatto importante sulla velocità e sulla qualità della superficie della marcatura. Una frequenza di impulso più elevata significa che l'energia laser è distribuita in modo più uniforme, il che aiuta a produrre una superficie di marcatura più liscia ed è adatta per applicazioni che richiedono una marcatura fine. Tuttavia, una frequenza troppo elevata può anche causare una dispersione eccessiva dell'energia laser, influenzando la profondità e il contrasto della marcatura. Una frequenza di impulso inferiore renderà l'energia laser più concentrata, il che è adatto per scene che richiedono una maggiore profondità di marcatura, ma può causare una leggera ruvidità sulla superficie. Pertanto, in base ai diversi materiali e requisiti di marcatura, la scelta della giusta frequenza di impulso può creare un equilibrio tra profondità e finitura superficiale.
- Velocità di marcatura: la velocità di marcatura si riferisce alla velocità a cui il laser si muove sulla superficie del materiale, che ha un impatto diretto sulla profondità, l'efficienza e l'effetto della marcatura. Velocità di marcatura più elevate possono migliorare l'efficienza della produzione e sono adatte per esigenze di elaborazione su larga scala. Tuttavia, all'aumentare della velocità, il laser rimane sul materiale per un tempo più breve e anche la profondità di marcatura diminuisce, il che può influire sulla chiarezza e sul contrasto della marcatura. Per applicazioni che richiedono marcature profonde o maggiore precisione, è solitamente necessario ridurre la velocità di marcatura per garantire che il laser abbia abbastanza tempo per interagire efficacemente con il materiale. L'impostazione della velocità deve considerare in modo completo i requisiti di marcatura e le caratteristiche del materiale per raggiungere un equilibrio tra efficienza e qualità.
- Regolazione della lunghezza focale: la precisione della lunghezza focale del laser è fondamentale per la qualità della marcatura. La lunghezza focale si riferisce alla distanza tra il raggio laser e la superficie del materiale. L'energia laser alla lunghezza focale ottimale è concentrata, il che può produrre effetti di marcatura chiari e precisi sulla superficie del materiale. Se la lunghezza focale non viene regolata correttamente, l'energia del raggio laser verrà dispersa, con conseguente marcatura sfocata e fuori fuoco, ed è impossibile ottenere motivi o testo chiari. Soprattutto nella marcatura fine, anche una leggera deviazione nella lunghezza focale avrà un impatto significativo sull'effetto finale. La calibrazione regolare della messa a fuoco dell'apparecchiatura e la conferma della precisione della lunghezza focale prima della marcatura sono passaggi fondamentali per garantire la coerenza dell'effetto di marcatura.
In generale, l'impostazione corretta dei parametri laser è fondamentale per ottenere risultati di marcatura laser di alta qualità. Regolando correttamente la potenza, la frequenza degli impulsi, la velocità di marcatura e la lunghezza focale, la chiarezza, la profondità e il contrasto della marcatura possono essere migliorati in modo efficace, assicurando che la marcatura laser funzioni al meglio in diversi materiali e applicazioni.
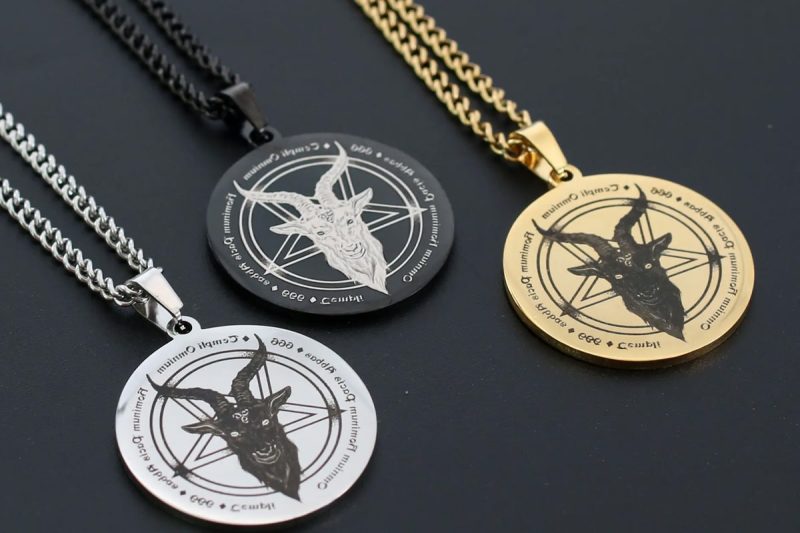
Influenza delle condizioni ambientali
- Temperatura: la temperatura ambiente ha un impatto diretto sullo stato operativo della macchina per marcatura laser. Una temperatura eccessiva può causare surriscaldamento all'interno dell'apparecchiatura, in particolare della sorgente laser e dei componenti elettronici. Il surriscaldamento ridurrà l'efficienza di lavoro dell'apparecchiatura e causerà persino guasti o danni. Inoltre, la potenza di uscita del generatore laser potrebbe diventare instabile in un ambiente ad alta temperatura, con conseguenti fluttuazioni nell'intensità del raggio laser durante il processo di marcatura e compromettendo la coerenza e la chiarezza della marcatura. Al contrario, una temperatura troppo bassa potrebbe anche compromettere l'avvio e il normale funzionamento dell'apparecchiatura, in particolare in aree o stagioni fredde, in cui il generatore laser potrebbe impiegare più tempo per riscaldarsi. Pertanto, mantenere la temperatura ambiente dell'apparecchiatura entro l'intervallo consigliato dal produttore (solitamente da 15 °C a 30 °C) è la chiave per garantire il funzionamento stabile della macchina per marcatura laser.
- Umidità: l'eccessiva umidità è un altro importante pericolo nascosto che influisce sulle prestazioni delle apparecchiature di marcatura laser. Un ambiente con elevata umidità può causare l'umidità dei componenti ottici della macchina per marcatura laser, come lenti, lenti e altri componenti chiave. Se questi componenti ottici sono umidi, il raggio laser si disperderà e si attenuerà durante la trasmissione, con conseguenti effetti di marcatura poco chiari o sfocati. Inoltre, un'elevata umidità può accelerare l'ossidazione e la corrosione all'interno dell'apparecchiatura e ridurne la durata. Per evitare problemi di umidità, l'apparecchiatura di marcatura deve essere installata in un ambiente con un buon controllo dell'umidità, specialmente nelle stagioni piovose o nelle aree umide. Si consiglia di utilizzare apparecchiature come deumidificatori per mantenere l'umidità ambientale tra 40%-60% per evitare che i componenti ottici e l'apparecchiatura si bagnino.
- Pulizia: la pulizia dell'ambiente di lavoro ha un impatto significativo sulla precisione e sulla qualità della marcatura laser. Particelle come polvere, sporcizia e macchie d'olio possono depositarsi sulla superficie del materiale di marcatura o sui componenti ottici dell'apparecchiatura, interferendo con la trasmissione del raggio laser e la precisione della lunghezza focale, riducendo così la chiarezza e il contrasto della marcatura. In un ambiente di produzione, in particolare in un sito industriale, ci sono molte particelle di polvere nell'aria, che possono influenzare l'interazione tra il raggio laser e la superficie del materiale, con conseguente marcatura irregolare. Per garantire il miglior effetto di marcatura, si consiglia di pulire regolarmente l'apparecchiatura, in particolare la lente e i componenti ottici, per mantenere la superficie del materiale di marcatura pulita e priva di polvere. Durante il processo di pulizia, utilizzare strumenti e metodi di pulizia appropriati per evitare di graffiare i componenti ottici o danneggiare la superficie del materiale.
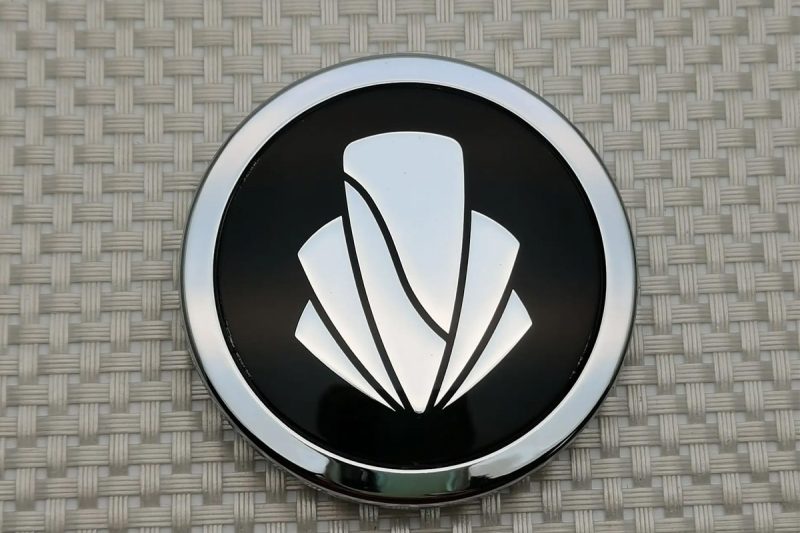
L'influenza dei componenti ottici
- Qualità della lente: la lente è uno dei componenti ottici più importanti nel sistema laser. La sua funzione è quella di focalizzare il raggio laser e proiettarlo con precisione sulla superficie del materiale. Se la qualità della lente è scarsa, ad esempio graffi, polvere o prestazioni ottiche insufficienti sulla superficie della lente, il raggio laser devierà o perderà energia durante il processo di messa a fuoco, il che influirà sulla precisione e sulla chiarezza della marcatura. Lenti di scarsa qualità possono causare marcature sfocate, fuori fuoco o distribuzione non uniforme dell'energia, specialmente in occasioni in cui è richiesta una lavorazione fine, l'effetto di marcatura apparirà ruvido e irregolare. Pertanto, la scelta di lenti ottiche di alta qualità e la loro regolare pulizia e manutenzione per garantire le loro prestazioni ottiche stabili sono la chiave per garantire la precisione della marcatura.
- Sistema di trasmissione del raggio: il sistema di trasmissione del raggio è responsabile della trasmissione del laser dalla sorgente laser alla superficie del materiale di marcatura. Durante questo processo, l'energia del laser deve essere trasmessa in modo efficiente senza alcuna perdita di energia o dispersione del raggio. Qualsiasi perdita durante il processo di trasmissione influirà sull'intensità e sull'effetto di messa a fuoco del laser, con conseguente profondità di marcatura insufficiente o riduzione della chiarezza. Per garantire l'efficienza della trasmissione del raggio, i vari componenti del sistema di trasmissione, come riflettori e fibre ottiche di trasmissione, devono essere mantenuti estremamente puliti e intatti. Qualsiasi polvere, sporcizia o danno ai componenti ottici causerà la dispersione e la scarsa riflessione del raggio, influenzando così i risultati della marcatura. Un sistema di trasmissione del raggio efficiente e senza perdite può garantire la stabilità e la coerenza del processo di marcatura, assicurando che l'effetto ideale possa essere ottenuto ogni volta.
- Scanner galvanometrico: lo scanner galvanometrico è un componente chiave che controlla il movimento rapido e il posizionamento preciso del raggio laser, che determina direttamente la velocità, la precisione e la coerenza del modello di marcatura. Lo scanner galvanometrico regola la direzione del raggio laser attraverso un riflettore ad alta velocità per disegnare il modello o il carattere richiesto sulla superficie del materiale. La sua velocità di scansione e la sua precisione sono particolarmente importanti per l'effetto di marcatura. Gli scanner galvanometrici ad alta precisione possono garantire il posizionamento preciso del raggio laser in modelli complessi o minuscoli per evitare deviazioni in linee o modelli. Gli scanner galvanometrici ad alta velocità possono migliorare l'efficienza di marcatura e sono adatti alle esigenze di produzione di massa. Tuttavia, una velocità di scansione troppo elevata può causare una distribuzione irregolare dell'energia, influenzando la profondità e il contrasto della marcatura. Pertanto, pur garantendo la velocità, è anche necessario garantire che la precisione del galvanometro rimanga entro un intervallo ragionevole. La qualità e le prestazioni dello scanner galvanometrico sono fondamentali per la stabilità dell'effetto di marcatura. Pertanto, un sistema galvanometrico ad alte prestazioni dovrebbe essere selezionato, calibrato e sottoposto a manutenzione regolare per garantire che possa mantenere effetti di marcatura accurati anche con la scansione ad alta velocità.
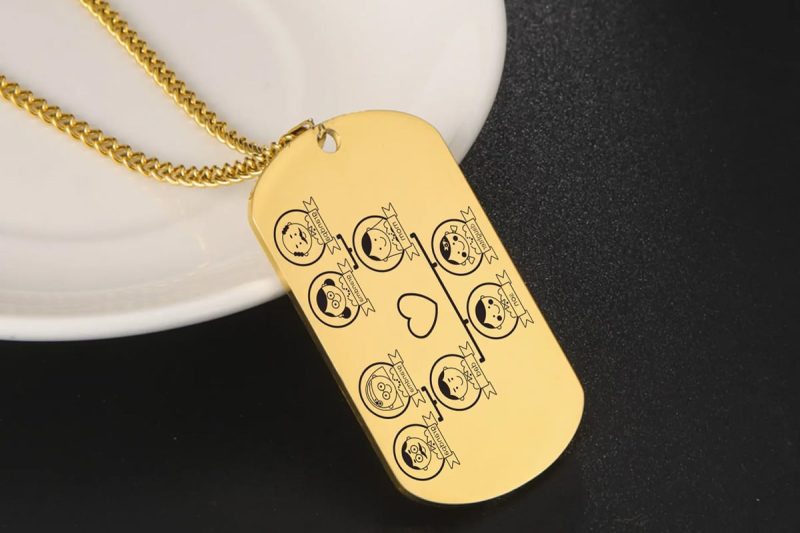
L'impatto del software e dei sistemi di controllo
- Software di marcatura: il software di marcatura è uno strumento importante per il controllo delle apparecchiature di marcatura laser. È responsabile dell'impostazione e della regolazione dei parametri del generatore laser, come potenza laser, velocità di marcatura, frequenza degli impulsi, ecc. Un software di alta qualità non solo può controllare accuratamente questi parametri chiave, ma fornisce anche funzioni di marcatura avanzate, come progettazione di pattern, selezione di font, generazione di codici a barre e QR, ecc. Inoltre, il software di marcatura può ottenere una marcatura multilivello e supportare vari requisiti di elaborazione di materiali diversi, come marcatura ad alta precisione e diversa profondità su metallo, plastica, vetro e altri materiali. Un software di marcatura avanzato di solito ha un'interfaccia intuitiva, semplifica il processo operativo, consente agli operatori di familiarizzare e padroneggiare rapidamente il sistema, riduce gli errori operativi umani e quindi migliora l'efficienza della produzione e la qualità della marcatura. Allo stesso tempo, anche l'aggiornabilità del software è molto importante. Con lo sviluppo della tecnologia e i cambiamenti nella domanda del mercato, il software di marcatura deve essere costantemente aggiornato e ottimizzato per adattarsi ai nuovi requisiti di marcatura.
- Sistema di controllo del movimento: il sistema di controllo del movimento è il componente principale utilizzato nella macchina per marcatura laser per controllare il movimento coordinato tra la testa laser e il pezzo in lavorazione. Garantisce che durante il processo di marcatura, la testa laser e il pezzo in lavorazione da lavorare possano essere sincronizzati con precisione, in modo che il raggio laser si muova sulla superficie del materiale secondo la traiettoria impostata. Questa sincronizzazione è essenziale per ottenere coerenza e accuratezza del modello di marcatura. I sistemi di controllo del movimento solitamente includono hardware come motori, sensori e controller e collaborano con il software di marcatura per il monitoraggio e la regolazione in tempo reale. Nella marcatura ad alta precisione, specialmente quando è necessario marcare modelli complessi su ampie aree di materiali, la precisione e la velocità di risposta del sistema di controllo del movimento sono particolarmente importanti. Se il sistema di controllo del movimento non è sufficientemente sensibile, la testa di marcatura laser potrebbe deviare, causando problemi come deformazione del modello e linee irregolari. Pertanto, un sistema di controllo del movimento stabile ed efficiente è uno dei fattori chiave per garantire la coerenza e la chiarezza della marcatura laser.
- Automazione: un sistema di marcatura laser altamente automatizzato può migliorare significativamente l'efficienza produttiva, ridurre gli errori nelle operazioni umane e garantire che ogni lotto di prodotti possa ottenere effetti di marcatura coerenti. Introducendo un sistema di controllo automatizzato, l'apparecchiatura di marcatura laser può essere collegata senza soluzione di continuità alla linea di produzione per ottenere operazioni di marcatura in batch e continue. Ad esempio, il sistema automatizzato può identificare e localizzare automaticamente il pezzo, regolare l'altezza e la lunghezza focale della testa di marcatura laser e garantire che ogni marcatura venga eseguita in condizioni ottimali. Il sistema automatizzato può anche modificare automaticamente il modello di marcatura e i parametri di diversi lotti senza intervento umano, migliorando notevolmente la flessibilità della produzione. Inoltre, il sistema di automazione può essere collegato ad altri sistemi di gestione della fabbrica per ottenere il monitoraggio e l'analisi in tempo reale dei dati di produzione, aiutando le aziende a ottimizzare i processi di produzione, migliorare la qualità del prodotto e ridurre i costi. Il sistema di marcatura automatizzato può anche ridurre il coinvolgimento dell'operatore e ridurre i costi di manodopera, specialmente in ambienti di produzione ad alta richiesta e ad alto volume, dove i suoi vantaggi sono particolarmente evidenti.
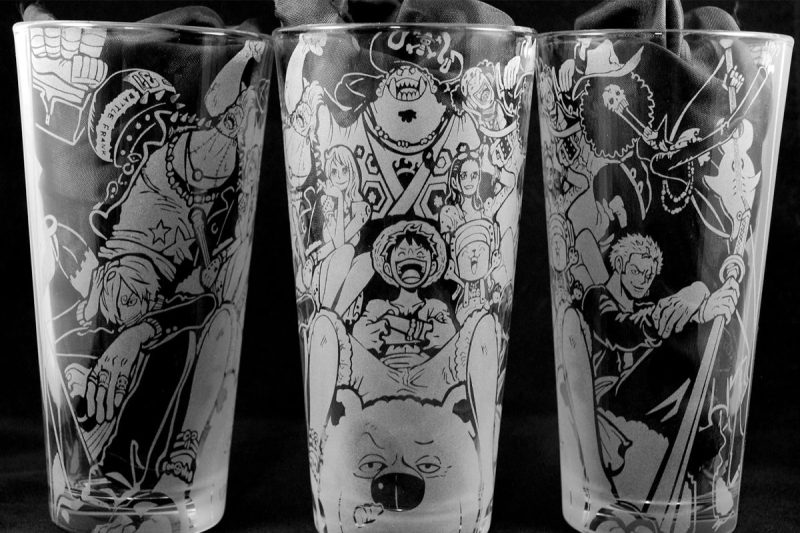
Effetto del sistema di raffreddamento
- Raffreddamento ad aria: i sistemi di raffreddamento ad aria sono spesso utilizzati per apparecchiature laser a bassa potenza, come alcune piccole macchine per marcatura laser a fibra. Questo metodo di raffreddamento rimuove il calore dal generatore laser e da altri componenti chiave tramite dispositivi di circolazione dell'aria come ventole. Grazie alla struttura semplice e ai bassi costi di manutenzione del sistema di raffreddamento ad aria, è adatto per scenari applicativi con bassi requisiti di dissipazione del calore. Il sistema di raffreddamento ad aria presenta i vantaggi di un ingombro ridotto e di un design compatto. Di solito è integrato nell'apparecchiatura senza la necessità di apparecchiature di raffreddamento esterne. Pertanto, è ampiamente utilizzato in piccole macchine per marcatura laser con volume limitato. Tuttavia, l'effetto di dissipazione del calore del raffreddamento ad aria è relativamente debole e non riesce a far fronte alla grande quantità di calore generata dai generatori laser ad alta potenza. Se l'apparecchiatura ad alta potenza viene raffreddata ad aria, potrebbe verificarsi un accumulo di calore, che influisce sulle prestazioni e sulla durata del generatore laser. Pertanto, il sistema di raffreddamento ad aria è principalmente adatto per apparecchiature laser con bassi requisiti di potenza e bassa dissipazione del calore.
- Sistema di raffreddamento ad acqua: rispetto al raffreddamento ad aria, il sistema di raffreddamento ad acqua è adatto per apparecchiature di marcatura laser ad alta potenza, soprattutto quando è richiesto un funzionamento continuo a lungo termine, può fornire una dissipazione del calore più efficace. Il sistema di raffreddamento ad acqua fa circolare il refrigerante (solitamente acqua o refrigerante) nelle vicinanze del generatore laser e di altri componenti che generano calore attraverso una pompa dell'acqua e rimuove rapidamente il calore attraverso l'efficiente trasferimento di calore dell'acqua. Rispetto al raffreddamento ad aria, il sistema di raffreddamento ad acqua ha una maggiore capacità termica ed efficienza di conduzione, che possono garantire che l'apparecchiatura possa mantenere un funzionamento stabile in ambienti ad alta temperatura o condizioni di lavoro ad alta intensità ed evitare l'attenuazione di potenza o il degrado della qualità di marcatura causati dal surriscaldamento del generatore laser. Inoltre, il sistema di raffreddamento ad acqua può controllare le fluttuazioni di temperatura e garantire che il generatore laser funzioni sempre entro l'intervallo di temperatura ottimale, prolungando così la durata utile dell'apparecchiatura.
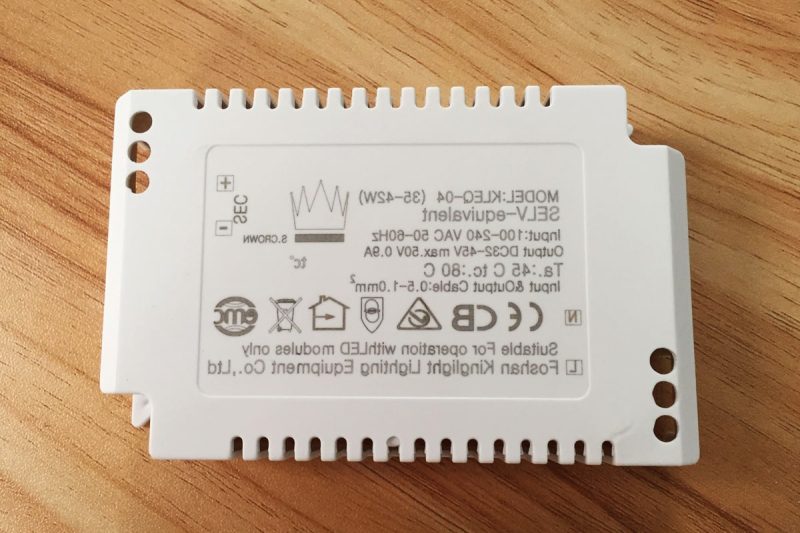
Abilità e formazione degli operatori
- Competenza: gli operatori di marcatura laser devono avere solide competenze, in particolare la conoscenza delle diverse proprietà dei materiali e dei parametri laser. Materiali diversi hanno diversi tassi di assorbimento, riflettività e conduttività termica dei laser, quindi gli operatori devono ragionevolmente regolare i parametri laser come potenza laser, velocità di marcatura, frequenza degli impulsi, ecc. in base alle caratteristiche dei materiali. Ad esempio, i materiali metallici di solito richiedono generatori laser a fibra ad alta potenza, mentre materiali non metallici come plastica o vetro possono essere più adatti per laser UV o generatori laser CO2. Se l'operatore non ha una conoscenza sufficiente delle proprietà dei materiali e dei tipi di generatori laser, ciò potrebbe portare a risultati di marcatura insoddisfacenti, profondità irregolare, sfocatura e bruciatura. Attraverso una formazione sistematica, gli operatori possono padroneggiare i requisiti di marcatura di diversi materiali e garantire che ogni marcatura possa ottenere i migliori risultati.
- Calibrazione e manutenzione: le apparecchiature di marcatura laser possono subire usura o deviazioni di componenti chiave come lenti, galvanometri e sistemi di trasmissione del raggio durante l'uso a lungo termine. Pertanto, la calibrazione e la manutenzione regolari delle apparecchiature sono essenziali per garantire che la qualità del raggio e la precisione della marcatura dell'apparecchiatura siano sempre nelle migliori condizioni. Gli operatori devono essere in grado di eseguire ispezioni giornaliere e una semplice risoluzione dei problemi dell'apparecchiatura per rilevare e risolvere tempestivamente i problemi. Ad esempio, l'attenuazione di potenza del generatore laser, la ridotta precisione della scansione del galvanometro e la contaminazione dei componenti ottici influenzeranno l'effetto di marcatura. Gli operatori ben formati possono calibrare regolarmente l'apparecchiatura per garantire il funzionamento stabile dell'apparecchiatura di marcatura laser e ridurre la stagnazione della produzione o il degrado della qualità causato da guasti dell'apparecchiatura o deviazione dei parametri. Inoltre, la manutenzione può non solo estendere la durata utile dell'apparecchiatura, ma anche evitare tempi di fermo imprevisti o guasti importanti e ridurre i costi di riparazione.
- Competenza operativa e consapevolezza della sicurezza: sebbene il funzionamento delle apparecchiature di marcatura laser sia diventato semplice, gli operatori devono comunque avere un certo livello di competenza per utilizzare l'apparecchiatura in modo efficiente. Gli operatori devono padroneggiare le procedure operative di varie attività di marcatura sul lavoro, come l'impostazione del percorso di marcatura, la regolazione della lunghezza focale e la selezione della velocità e della potenza di marcatura appropriate. Gli operatori qualificati possono valutare e regolare rapidamente i parametri per soddisfare diverse esigenze di marcatura, migliorando così l'efficienza della produzione. Inoltre, gli operatori devono anche avere un certo livello di consapevolezza della sicurezza. Le apparecchiature laser possono presentare determinati rischi per la sicurezza durante il funzionamento, come radiazioni laser e generazione di calore. Gli operatori che hanno ricevuto una formazione professionale possono evitare efficacemente i problemi di sicurezza causati da un funzionamento improprio e garantire la sicurezza dell'ambiente di produzione.
- Apprendimento continuo e aggiornamenti tecnologici: la tecnologia di marcatura laser è costantemente aggiornata e vengono lanciate anche nuove apparecchiature di marcatura e funzioni software. Pertanto, gli operatori devono continuare ad apprendere e adattarsi alle nuove tecnologie, padroneggiare il funzionamento di nuovi generatori laser e software di marcatura tramite formazione e comprendere gli ultimi miglioramenti dei processi. L'apprendimento continuo degli operatori può aiutare le aziende a mantenere la competitività, migliorare l'efficienza di marcatura e la qualità del prodotto e soddisfare le mutevoli richieste del mercato.
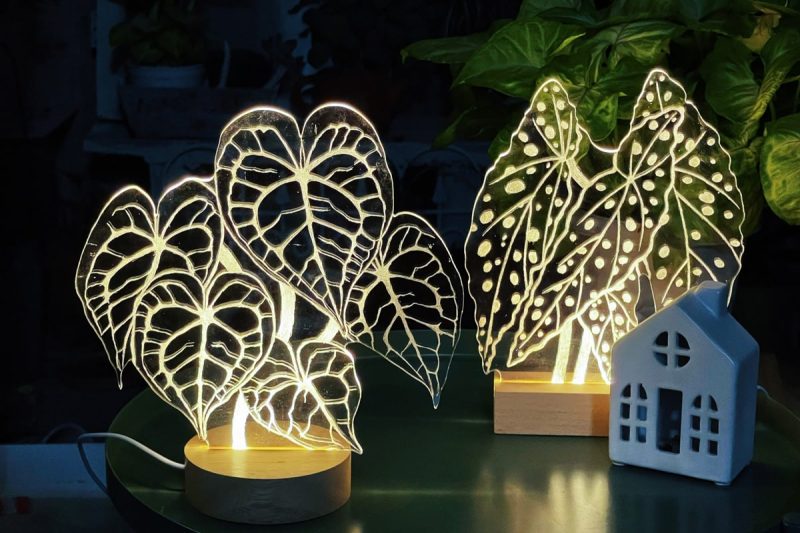
L'influenza della movimentazione e dell'attrezzatura dei materiali
Fissaggio
- Garantire la stabilità del pezzo: il serraggio e il fissaggio precisi impediscono al pezzo di muoversi leggermente durante il processo di marcatura, garantendo così un posizionamento accurato e la coerenza del modello di marcatura. Ciò è particolarmente importante per attività di marcatura ad alta precisione, come la marcatura di caratteri minuscoli o modelli complessi.
- Riduzione degli errori: un dispositivo stabile può ridurre efficacemente gli errori di marcatura causati da cambiamenti nella posizione del pezzo, migliorando la coerenza e la qualità del prodotto. Soprattutto nella produzione su larga scala, impostazioni di dispositivi coerenti possono garantire che ogni pezzo venga marcato nelle stesse condizioni.
- Adattarsi a diversi pezzi: il design dell'attrezzatura dovrebbe tenere conto di pezzi di diverse forme e dimensioni in modo che possa essere applicato in modo flessibile in varie attività di produzione. L'attrezzatura dovrebbe avere una funzione di regolazione rapida per facilitare l'operatore a impostarla in base ai diversi requisiti del pezzo, migliorando così l'efficienza della produzione.
Preparazione del materiale
- Pulizia: prima della marcatura, la pulizia della superficie del materiale è fondamentale. Impurità come sporco, grasso e polvere possono interferire con la trasmissione del raggio laser, dando origine a motivi di marcatura sfocati e irregolari. Utilizzando metodi di pulizia appropriati, come la pulizia a ultrasuoni o la pulizia chimica, è possibile rimuovere efficacemente la contaminazione superficiale e garantire la chiarezza e la coerenza della marcatura laser.
- Trattamento: alcuni materiali potrebbero richiedere un trattamento superficiale aggiuntivo, come molatura, sabbiatura o trattamento chimico, per migliorare la finitura superficiale e l'adesione laser. Questi passaggi di trattamento possono ridurre l'irregolarità della superficie del materiale e migliorare l'effetto di marcatura, specialmente in scenari applicativi in cui è richiesta un'elevata levigatezza.
- Ispezione: prima della marcatura, la superficie del materiale deve essere ispezionata per assicurarsi che soddisfi i requisiti di marcatura. I materiali con difetti evidenti o superfici irregolari potrebbero richiedere un trattamento aggiuntivo per evitare di influire negativamente sull'effetto di marcatura finale.
Elaborazione in lotti
- Standardizzazione: per mantenere risultati di marcatura coerenti nella produzione di massa, è necessario adottare procedure operative standardizzate e progetti di attrezzature. La standardizzazione può ridurre gli errori di marcatura causati da differenze operative o posizioni incoerenti del pezzo.
- Automazione: nella produzione di massa, l'applicazione di sistemi di automazione può migliorare significativamente l'efficienza e la coerenza della produzione. I sistemi automatizzati possono completare in modo rapido ed efficiente il compito di marcatura di un gran numero di pezzi e garantire che ogni pezzo venga elaborato nelle stesse condizioni, riducendo così l'errore umano e le fluttuazioni nella produzione.
- Controllo qualità: quando si produce in grandi quantità, è necessario implementare rigide misure di controllo qualità, tra cui ispezioni e test regolari, per garantire che ogni lotto di prodotti soddisfi gli standard qualitativi. Il monitoraggio in tempo reale dell'effetto di marcatura può rilevare e correggere tempestivamente potenziali problemi per garantire la coerenza e la stabilità del prodotto.
In sintesi, la progettazione dell'attrezzatura, la preparazione del materiale e l'elaborazione in batch sono tutti fattori importanti che influenzano la qualità della marcatura laser. Ottimizzando la stabilità dell'attrezzatura, migliorando la pulizia e la consistenza della superficie del materiale e implementando la standardizzazione e l'automazione nella produzione in batch, le aziende possono garantire elevata precisione, elevata efficienza e alta qualità del processo di marcatura.
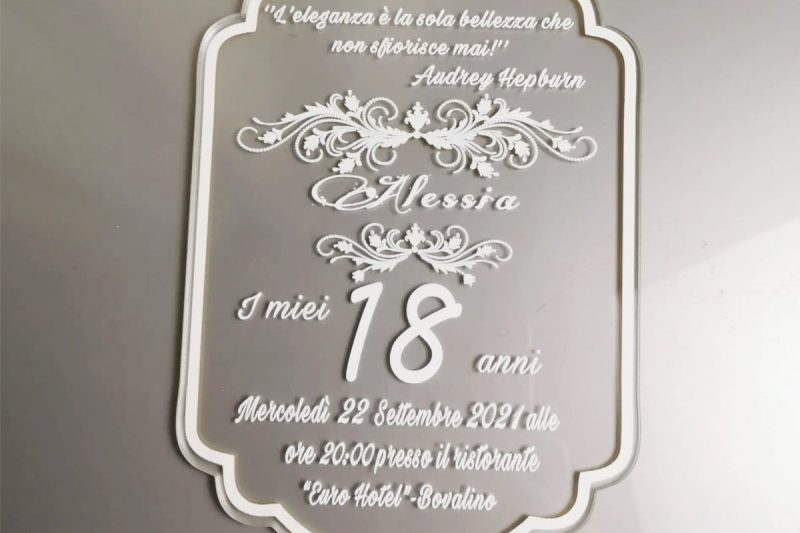
Impatto dei fattori specifici dell'applicazione
Profondità di marcatura
- Requisiti di profondità: in alcune applicazioni specifiche, come parti di produzione e industriali, potrebbe essere necessario un marchio più profondo per garantire che il marchio sia durevole e rimanga leggibile per un uso a lungo termine. Ad esempio, parti e utensili aerospaziali spesso richiedono un marchio più profondo per rimanere leggibili in ambienti ad alto attrito e difficili. I marchi profondi non solo aiutano a migliorare la durata del marchio, ma ne migliorano anche la resistenza all'usura.
- Marcatura superficiale: al contrario, per alcune applicazioni che richiedono solo la marcatura superficiale, come etichette di prodotti di consumo o marcature decorative, è sufficiente una profondità di marcatura più bassa. In questo caso, una profondità di marcatura più bassa può ridurre la perdita di materiale e i costi di lavorazione, soddisfacendo al contempo i requisiti di leggibilità della marcatura.
Contrassegno di contrasto
- Codici QR e codici a barre: un contrasto elevato è essenziale per i marchi leggibili dalle macchine, come i codici QR e i codici a barre. I marchi ad alto contrasto assicurano che i dispositivi di scansione possano leggere accuratamente le informazioni ed evitare errori di lettura dovuti a marchi sfocati o contrasto insufficiente. Utilizzando parametri laser appropriati e tecnologia di elaborazione dei materiali, il contrasto del marchio può essere migliorato per garantire una trasmissione affidabile delle informazioni.
- Marcatura visiva: un contrasto elevato è ugualmente importante in alcune applicazioni che richiedono l'identificazione manuale, come numeri di prodotto, loghi di marchi, ecc. Una marcatura chiara può migliorare l'efficienza e l'accuratezza del riconoscimento e ridurre la possibilità di identificazione errata. In questi casi, la macchina di marcatura deve regolare i parametri in base alle caratteristiche dei diversi materiali per garantire la chiarezza e la leggibilità del marchio.
Durata della marcatura
- Ambienti difficili: in alcune applicazioni industriali, la marcatura deve resistere ad ambienti difficili come alte temperature, corrosione chimica e radiazioni ultraviolette. Ad esempio, i componenti automobilistici e le apparecchiature meccaniche sono esposti a vari fattori esterni durante l'uso, il che richiede che la marcatura abbia un'elevata durata e resistenza alla perdita. La scelta del tipo di laser e del processo di lavorazione del materiale giusti può migliorare la durata della marcatura e garantire che la marcatura rimanga chiara e leggibile durante l'uso a lungo termine.
- Utilizzo a lungo termine: per alcune marcature che devono essere conservate a lungo, come i numeri di serie sui componenti elettronici o i loghi sui dispositivi medici, la durata è ugualmente importante. La macchina per marcatura laser deve regolare i parametri laser per garantire che la marcatura non sbiadisca, non si usuri o non si perda con l'utilizzo a lungo termine, per mantenere il suo stato e la sua funzione originali.
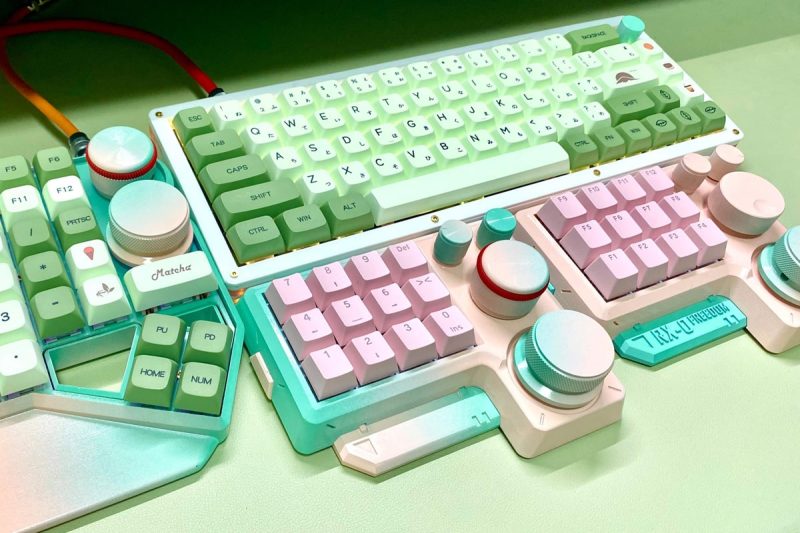
Riassumere
- La scelta della sorgente laser determina direttamente i materiali applicabili e i risultati della marcatura. Ad esempio, i laser a fibra sono adatti per materiali metallici, i laser a CO2 sono adatti per materiali non metallici e i laser ultravioletti (UV) sono adatti per applicazioni che richiedono una marcatura fine.
- Le proprietà dei materiali come assorbimento, riflettività e condizioni della superficie influenzeranno la trasmissione del raggio laser e l'effetto di marcatura finale. Anche la movimentazione dei materiali e la preparazione della superficie hanno un impatto diretto sulla qualità della marcatura.
- I parametri laser includono impostazioni di potenza, frequenza degli impulsi, velocità di marcatura e regolazione della lunghezza focale, che devono essere impostati con precisione per garantire una marcatura chiara e conforme.
- Condizioni ambientali quali temperatura, umidità e pulizia influiranno sulla stabilità dell'apparecchiatura e sulla qualità del raggio laser.
- Anche le prestazioni dei componenti ottici, quali la qualità delle lenti, il sistema di emissione del raggio e lo scanner galvanometrico, sono direttamente correlate alla precisione e alla coerenza della marcatura.
- La qualità del software e dei sistemi di controllo determina l'accuratezza della marcatura e la facilità di funzionamento. Software eccellenti e sistemi di automazione possono migliorare l'efficienza e la qualità della marcatura.
- Il sistema di raffreddamento è fondamentale per il funzionamento stabile delle apparecchiature laser. Un sistema di raffreddamento efficiente può prolungare la durata delle apparecchiature e mantenerne le prestazioni.
- Le competenze e la formazione dell'operatore sono la base per garantire la qualità della marcatura. Un operatore professionista può impostare correttamente i parametri dell'attrezzatura ed eseguire una manutenzione regolare per garantire le migliori prestazioni dell'attrezzatura.
- Anche la movimentazione dei materiali e la progettazione degli impianti sono fattori importanti che influenzano l'effetto di marcatura. Impianti stabili e una corretta movimentazione dei materiali possono migliorare la coerenza e l'accuratezza della marcatura.
- Anche i fattori specifici dell'applicazione, come la profondità di marcatura, il contrasto e la durata, variano a seconda dei requisiti applicativi. Anche gli standard di qualità della marcatura variano.
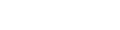
- [email protected]
- [email protected]
- +86-19963414011
- N. 3 Zona A, zona industriale di Lunzhen, città di Yucheng, provincia di Shandong.