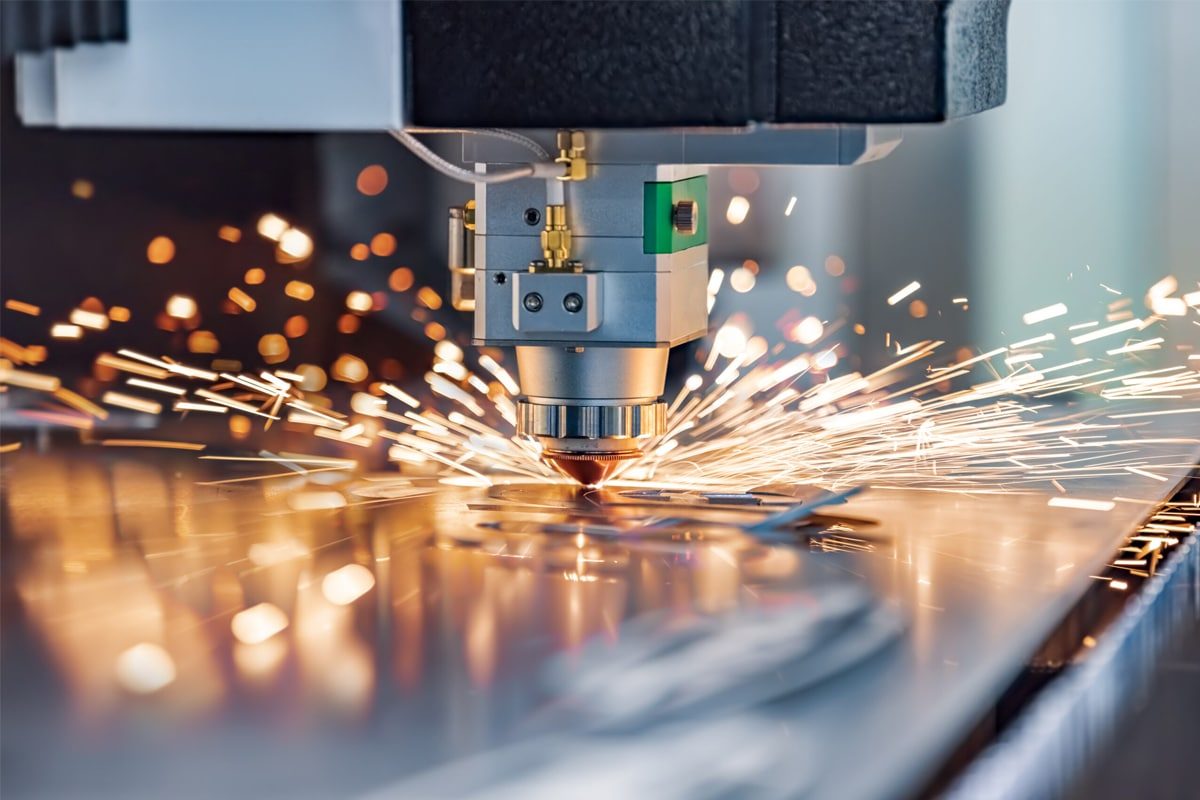
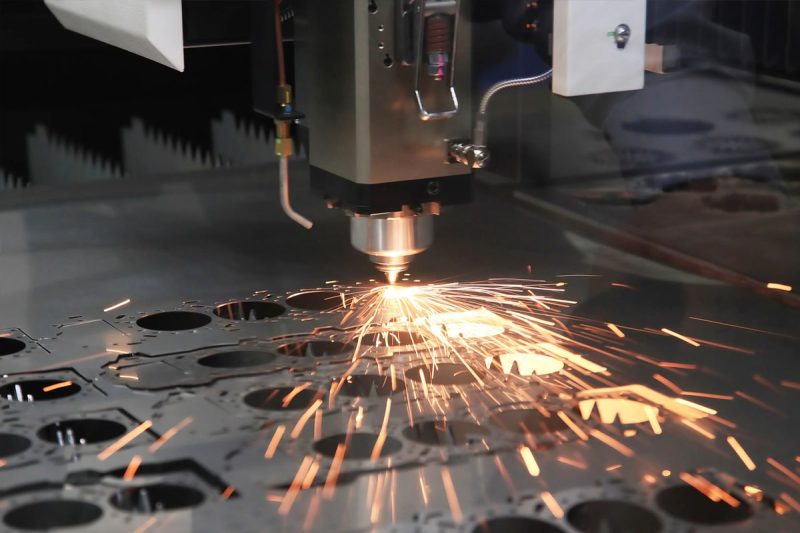
ファイバーレーザー切断の理解
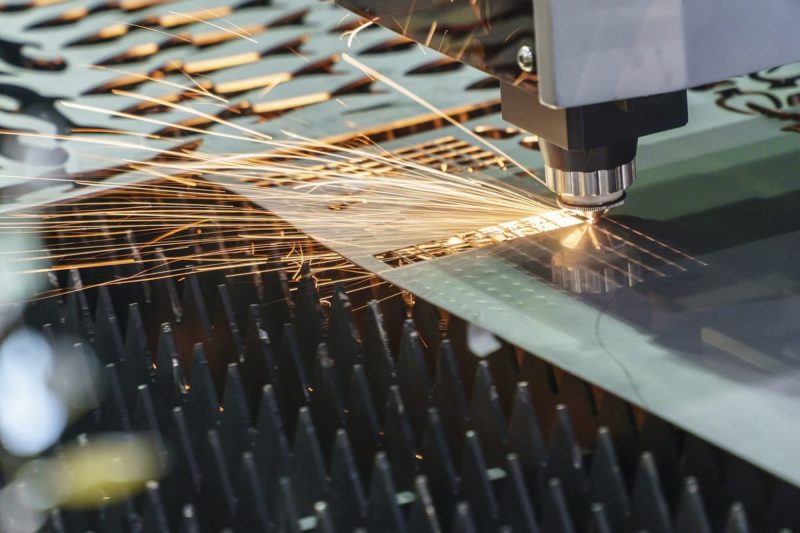
ファイバーレーザー切断の利点
高精度・高精度
スピードと効率
エネルギー効率
低メンテナンス
汎用性
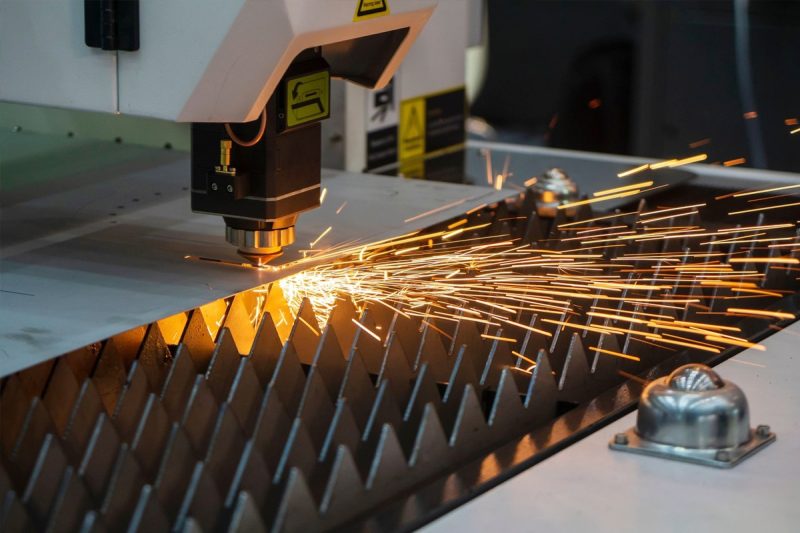
ファイバーレーザー切断に適した金属
炭素鋼
炭素鋼は、その強度、耐久性、汎用性により、ファイバーレーザー切断で最も一般的に使用される金属の 1 つです。自動車や建設など、高いストレスや摩耗に耐えられる堅牢な材料を必要とする業界で広く使用されています。
- 厚さ範囲:ファイバーレーザーは切断可能 炭素鋼 レーザー出力に応じて、非常に薄いシート(0.5 mm)から厚いプレート(25 mm以上)まで対応します。
- 切断品質: ファイバーレーザーは炭素鋼に滑らかでバリのないエッジを生成するため、追加の仕上げの必要性が減り、生産効率が向上します。
- 用途: 炭素鋼は、高い引張強度が重要となる車両部品、構造梁、機械部品、産業機器の製造に不可欠です。
- 利点: ファイバーレーザーの精度と熱影響部が最小限であるため、厚いプレートでも切断の強度と品質が維持されます。切断速度が速いため、大量生産のアプリケーションでもコスト効率に優れています。
ステンレス鋼
ステンレス鋼は耐腐食性と研磨仕上げを備えているため、食品・飲料、医療、建築などの耐久性と外観が重要となる業界に最適です。
- 厚さ範囲:ファイバーレーザーは効果的に切断します ステンレス鋼 薄い箔(0.5 mm)から厚い板(最大20 mm以上)まで。
- 切断品質: ファイバー レーザーはステンレス鋼のエッジをきれいに磨き上げ、美観と完全性を維持します。熱影響部が減少することで切断エッジの酸化が防止され、滑らかで高品質な仕上がりが求められる用途に不可欠です。
- 用途: ステンレス鋼は、衛生設備、医療機器、台所用品、建築備品、装飾要素に広く使用されています。
- 利点: ステンレス鋼の反射特性はファイバーレーザーに適しており、反射を最小限に抑えて正確なカットを可能にします。後処理が不要なため、メーカーは生産を合理化し、時間とリソースの両方を節約できます。
アルミニウムおよびアルミニウム合金
アルミニウムは軽量でありながら強度も備えているため、性能と燃費効率が最優先される航空宇宙産業や自動車産業などでは欠かせない素材となっています。
- 厚さ範囲:ファイバーレーザーは切断可能 アルミニウム 最大 15 mm の厚さまで切断できますが、より厚い部分を切断するには、より高出力のレーザーが必要です。
- 課題: アルミニウムは反射率と熱伝導率が高いため、レーザー光線を反射し、熱を急速に放散するという課題があります。しかし、高度なファイバーレーザー技術では、反射防止コーティングと最適化された切断パラメータにより、これらの問題を克服できます。
- 用途: アルミニウムは、航空宇宙部品、自動車のボディパネル、電子機器の筐体、装飾用途に使用されます。
- 利点: ファイバー レーザーを使用すると、アルミニウムの歪みや熱による変形を起こさずに、正確で詳細な切断を行うことができます。また、軽量で複雑な航空宇宙および自動車部品に不可欠な、複雑なデザインを作成するためのソリューションも提供します。
銅と真鍮
銅と真鍮は導電性と外観が高く評価されており、電気分野や装飾分野での用途に最適です。ただし、これらの金属は反射性と導電性が非常に高いため、特別な取り扱いが必要です。
チタンおよびチタン合金
チタンは優れた強度対重量比と耐腐食性で知られており、航空宇宙、医療、スポーツ用品製造などの業界で高く評価されています。
- 厚さの範囲: ファイバーレーザーは最大 10 mm の厚さのチタンとその合金を切断できますが、それよりも厚い材料には強力なレーザーが必要です。
- 切断品質: ファイバー レーザーは、ドロスを最小限に抑えてきれいな切断を実現し、チタンの高品質な表面仕上げを維持します。熱入力が低いため、金属の構造的完全性と特性が損なわれることはありません。
- 用途: チタンは、航空宇宙部品、医療用インプラント、義肢、高性能スポーツ用品などに広く使用されています。
- 利点: ファイバー レーザーを使用すると、熱による歪みを起こさずにチタンを切断できるため、金属の望ましい特性が維持されます。このため、耐久性と重量の両方が重要となる高ストレスのアプリケーションに最適です。
ニッケル合金(インコネル、モネル)
インコネルやモネルなどのニッケルベースの合金は、極度の耐熱性と耐腐食性が求められる厳しい環境で使用されます。これらの合金は、航空宇宙、海洋、化学処理業界でよく使用されます。
- 厚さの範囲: ファイバーレーザーは最大 10 mm の厚さのニッケル合金を切断できますが、その強度を保つには正確なレーザー制御が必要です。
- 切断品質: ファイバー レーザーは高精度の切断を実現します。これは、高ストレス条件下で動作する必要があるコンポーネントに不可欠です。ニッケル合金の耐久性と高い融点は、ファイバー レーザー切断に最適です。
- 用途: ニッケル合金は、タービンブレード、排気システム、化学処理装置、海洋部品に使用されます。
- 利点: ファイバーレーザーにより、これらの強靭な合金を効率的に処理できるため、材料の無駄が減り、金属の強度と耐腐食性を維持しながら、きれいで正確な切断が可能になります。
亜鉛めっき鋼
亜鉛メッキ鋼には保護用の亜鉛コーティングが施されているため、腐食に強く、屋外や構造用途に適しています。ただし、このコーティングは切断時に特別な考慮が必要です。
- 課題: レーザー切断中に亜鉛層が蒸発して煙が発生し、切断品質に影響を与える可能性があるため、適切な換気が必要になります。
- 用途: 亜鉛メッキ鋼は、HVAC システム、屋根材、自動車部品、建築フレームワークに広く使用されています。
- 利点: 適切なパラメータ調整と換気により、ファイバーレーザーは亜鉛メッキ鋼を効果的に処理し、追加の後処理なしで材料の保護特性を維持する切断を実現できます。
工具鋼
工具鋼は耐久性に優れ、摩耗にも耐えられるため、長持ちする金型、ダイ、切削工具を必要とする業界では不可欠です。
- 切断品質: ファイバーレーザーは工具鋼をきれいかつ正確に切断するため、多くの場合、追加の機械加工や仕上げが不要になります。
- 用途: 工具鋼は、製造業や機械加工業における機械部品、金型、鋳型、さまざまな工具の作成に使用されます。
- 利点: ファイバーレーザーの精度により、工具鋼コンポーネントが正確な仕様を満たすことが保証され、メーカーは廃棄物を最小限に抑えながら高品質の工具や機械部品を製造できます。
銀と金
銀と金は、細かいディテールと高品質の仕上げが不可欠な電子機器や宝飾品によく使用される貴金属です。これらの素材は反射率が高く価値が高いため、特別な取り扱いが必要です。
- 課題: 銀と金は反射性があるため、レーザー効率が低下し、無駄を避けるために正確なパラメータ制御の必要性が高まります。
- 用途: 銀と金は、電子機器、複雑な宝飾品、カスタム装飾品に使用されます。
- 利点: ファイバーレーザーを使用すると、これらの貴金属を細かく切断できるため、ジュエリー製造と電子機器製造の両方における高精度のアプリケーションに適しています。
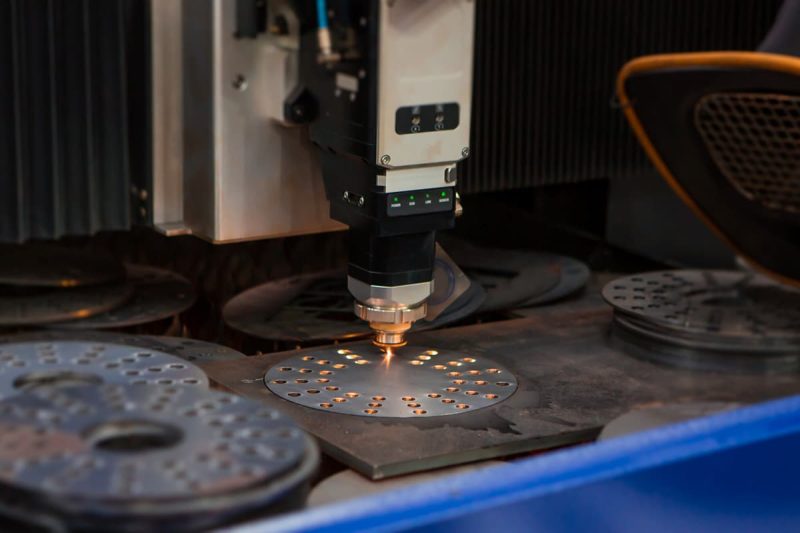
切断能力に影響を与える要因
レーザーパワー
レーザー出力は、さまざまな種類の材料や厚さを切断する機械の能力に直接影響します。通常、レーザー出力が高いほど、切断が速くなり、より厚い材料を処理できるようになります。
- 低電力 (1,500W – 3,000W): 薄い材料 (最大 15 mm) に適しており、複雑なデザインや細かいディテールの精密切断に最適です。
- 中出力 (3,000W – 6,000W): 中程度の厚さの金属 (最大 25 mm) を扱い、一般的な製造に適したバランスの取れた速度と品質を提供します。
- 高出力 (12,000W 以上): 重工業用途や大型構造部品など、厚い材料 (50 mm 以上) に適しています。
材料の厚さ
材料の厚さは、ファイバーレーザー切断の有効性と品質を決定する最も影響力のある要因の 1 つです。材料が厚いほど、効果的に貫通して切断するために必要なエネルギーが大きくなります。
- 薄い材料 (10 mm 未満): ファイバー レーザーは、薄いシートを高精度かつ熱による歪みを最小限に抑えて切断するのに優れているため、細かいディテールが求められる用途に最適です。
- 中程度の厚さ (12 mm ~ 25 mm): 厚い材料の場合、速度と切断品質のバランスをとるために、中程度のレーザー出力と最適化された設定が必要になることがよくあります。
- 厚い材料 (25 mm 以上): 厚い金属を切断するには、滑らかなエッジで完全に切断するために、より高い電力とより遅い切断速度が必要です。ドロスの除去とエッジの仕上げにも重点を置く必要がある場合があります。
材質の反射率
金属の反射率は、ファイバー レーザー切断との互換性において重要な役割を果たします。アルミニウム、銅、真鍮、銀、金などの反射率の高い金属は、レーザー ビームを機械に反射して問題を引き起こし、レーザー ソースや光学系に損傷を与える可能性があります。
- 高反射金属: 銅や真鍮などの材料では、レーザー システムの損傷を防ぐために、特殊なレーザー設定や反射防止技術が必要です。レーザー出力を高め、正確に調整することで、切断効率が向上し、反射の問題を最小限に抑えることができます。
- 非反射性金属: 炭素鋼とステンレス鋼は反射率が低く、ファイバーレーザーの波長をより効果的に吸収するため、標準設定で切断しやすくなります。
アシストガス
アシストガスの選択とその圧力は、ファイバーレーザーの切断品質と速度に重要な役割を果たします。アシストガスは、切断経路から溶融材料を除去し、光学系を保護し、場合によっては切断反応を強化するために使用されます。
- 酸素 (O2): 酸素は発熱反応を起こして切断速度を上げるため、炭素鋼の切断によく使用されます。ただし、切断端が酸化する可能性があり、追加の仕上げが必要になる場合があります。
- 窒素 (N2): 窒素は酸化を防ぐ不活性ガスで、ステンレス鋼、アルミニウム、その他きれいな切断面が不可欠な高品質の用途の切断によく使用されます。高品質の切断を実現しますが、酸素に比べて切断速度が遅くなる可能性があります。
- エア: エアは、エッジの品質がそれほど重要でない薄い材料を切断する場合にコスト効率の高いオプションになりますが、エッジが酸化される可能性があります。
ビーム品質
レーザー ビームの品質は、多くの場合 M2 値で測定され、切断の精度、効率、滑らかさに大きく影響します。M2 値が低いほど、ビームの品質が高く、より小さなスポット サイズに焦点を合わせることができ、材料に高い電力密度を供給できます。
- M2 値: 高品質のビーム (M2 値が低い) により、より小さく細かいカットをより正確に行うことができるため、複雑なデザインや厳しい許容誤差に最適です。
- フォーカス制御: ダイナミックフォーカスシステムにより、切断プロセス全体にわたって最適な焦点距離を維持するための調整が可能になります。これは、厚い材料や複雑な形状の場合に特に重要です。
- オートフォーカス システム: これらのシステムは、フォーカス位置を自動的に調整し、セットアップ時間を短縮し、異なる材料や厚さ間の移行を迅速化することで効率を高めます。
切削速度
切断速度は、ファイバーレーザー切断の品質、効率、仕上がりに直接影響します。理想的な切断速度は、材料の種類、厚さ、望ましいエッジ品質などの要素のバランスによって決まります。
- 高速: 切断速度が速すぎると、特に厚い材料の場合、切断が不完全になったり、切断面が粗くなったり、切断品質が低下したりする可能性があります。
- 低速: 切断速度が遅すぎると熱入力が増加し、特に薄い材料では、反りや切り口が広くなる可能性があります。
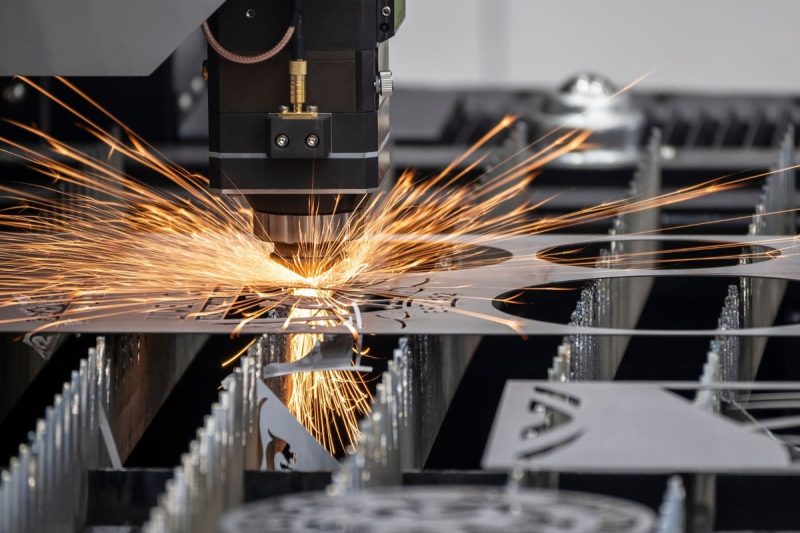
さまざまな業界への応用
自動車産業
アプリケーション
- ボディパネル: 車両の外部および内部パネルの精密な切断により、均一性ときれいなエッジが確保され、スムーズにフィットします。
- シャーシ コンポーネント: フレームやブラケットなどの構造部品には耐久性のある切断が必要ですが、ファイバー レーザーを使用すると材料の無駄を最小限に抑えて切断できます。
- 排気システム: ステンレス鋼とチタンを切断できるため、ファイバーレーザーで排気部品を精密に製造でき、仕上げの必要性が減ります。
利点
- 高スループット: ファイバーレーザーは、切断時間を短縮し、大規模生産を可能にすることで生産性を向上させます。
- 設計の柔軟性: 自動車メーカーは、燃費向上に不可欠な複雑な設計と軽量構造を実現できます。
航空宇宙産業
アプリケーション
- 航空機構造: 構造部品用のアルミニウム、チタン、高強度合金を切断することで、耐久性と精度を確保します。
- エンジン部品: ファイバーレーザーは、タービンブレードや排気システムに必要な複雑な形状や厳しい許容誤差に対応できます。
- 宇宙船部品: 衛星やロケットでは、熱の影響を最小限に抑えながらアルミニウムなどの軽量金属を切断する能力が不可欠です。
利点
- 精度と一貫性: ファイバーレーザーは、過酷な条件に直面するコンポーネントに必要な厳格な基準を提供します。
- 材料効率: 高価値の航空宇宙部品に不可欠な高価な合金の無駄を削減します。
医療産業
アプリケーション
- 外科用器具: メスの刃、鉗子、その他の器具の製造には、正確な切断と研磨された刃先が必要です。
- 医療用インプラント: ファイバーレーザーにより、骨プレートや関節置換などのインプラント用のチタンを精密に切断できます。
- 機器コンポーネント: MRI 装置や患者モニターなどの医療機器の部品には、高い精度と信頼性の高い性能が求められます。
利点
- 生体適合性: ステンレス鋼とチタンのきれいな酸化のない切断により、医療用途に不可欠な材料特性が維持されます。
- カスタマイズ: 正確な仕様で患者固有のインプラントを生産する機能。
エレクトロニクス産業
アプリケーション
- 回路基板:プリント回路基板用の銅やアルミニウムなどの金属基板を高精度に切断します。
- エンクロージャとケース: スマートフォン、ラップトップ、産業機器などのデバイス用の金属ケースを製造します。
- ヒートシンク: 放熱を管理するコンポーネント用のアルミニウムおよび銅材料の精密切断。
利点
- 高精度: 小型電子機器に必要な小型で精密な部品を作成するために不可欠です。
- 生産性の向上: 高速切断速度により大量生産が可能になり、エレクトロニクス市場の急速な需要に対応できます。
建設と建築
アプリケーション
- 構造部品: 建物や橋梁の鉄骨構造の梁、柱、ブラケットを切断します。
- 装飾要素: カスタムデザインのファサード、手すり、金属製の備品を複雑なパターンで作成できます。
- HVAC システム: 暖房、換気、空調システム用の金属ダクトおよびコンポーネントの製造。
利点
- カスタマイズと柔軟性: 建築家や設計者は、独自の詳細な金属細工を建物に組み込むことができます。
- 耐久性: ファイバーレーザー切断により、長期間にわたる構造上の要求に耐える、きれいで強力なエッジが生成されます。
再生可能エネルギー
アプリケーション
- ソーラーパネル フレーム: ソーラー設備に耐久性と安定性を提供するアルミ フレームとマウント システムを切断します。
- 風力タービン部品: 構造サポートやタービンブレードなどの部品を製造します。
- バッテリーエンクロージャ:電気自動車やエネルギー貯蔵に使用されるバッテリー用のケースとエンクロージャの製造。
利点
- 精度と強度: 屋外環境や温度変動にさらされるコンポーネントに不可欠です。
- 効率性: 大量かつ複雑な形状を処理できるため、再生可能エネルギー機器の製造に最適です。
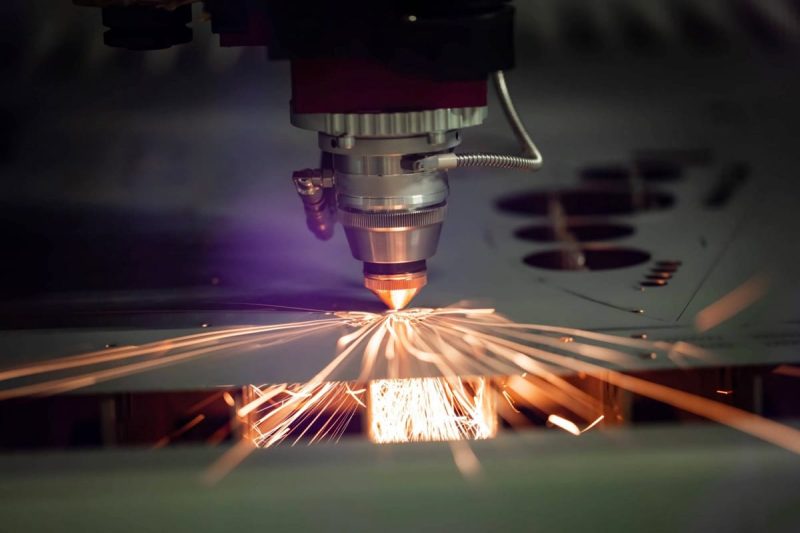
ファイバーレーザー切断の限界
金属反射率
アルミニウム、銅、真鍮、銀、金などの反射率の高い金属は、ファイバー レーザー切断において問題となる可能性があります。これらの金属はレーザー ビームを切断ヘッドに反射する傾向があり、レーザー ソースと光学系を損傷する可能性があります。この反射によって切断効率が低下し、切断が不安定になることもあります。
- 課題: 反射面はレーザーエネルギーの吸収を低下させ、切断の深さと品質に影響を与える可能性があります。また、反射により機械内に熱が蓄積されるため、追加の冷却または保護対策が必要になる場合があります。
- 解決策: 高度なファイバー レーザー システムには、反射性金属をより効果的に処理するための反射防止技術や光学系のコーティングが組み込まれている場合があります。さらに、レーザー出力、焦点距離、補助ガスなどのパラメータを調整することで、切断性能を向上させることができます。ただし、反射性金属の切断には、レーザー システムを保護するために細心の注意とより頻繁なメンテナンスが必要です。
厚さの制限
ファイバーレーザーは薄い金属から中程度の厚さの金属を切断するのに非常に効率的ですが、効果的に切断できる最大の厚さには実際的な制限があります。
- 薄~中厚金属(0.5 mm~25 mm):ファイバーレーザーは、薄~中厚金属を高精度かつ高速に切断するのに最適です。
- 厚い金属 (25 mm 以上): ファイバー レーザーは厚い金属を切断できますが、厚さが増すにつれてパフォーマンスが低下します。非常に厚い材料 (50 mm 以上) を切断するには、より高いレーザー出力とより遅い切断速度が必要になり、生産時間と運用コストが増加する可能性があります。さらに、厚い切断ではドロスが多く発生する可能性があり、きれいな仕上がりのために後処理が必要になります。
初期投資
ファイバー レーザー切断機は、多額の資本投資を必要とします。ファイバー レーザーのコストは、高度な技術、高出力レーザー、特殊な光学系が使用されるため、一般的に CO2 レーザーやその他の従来の切断装置よりも高くなります。
- コスト要因: 高品質のファイバー レーザー切断機には、レーザー ソース、切断ヘッド、CNC 制御、冷却システム、安全機能など、かなりの価格が伴います。エネルギー効率が高く、メンテナンスの必要性が少ないため運用コストは低くなりますが、小規模な企業や予算が限られている企業にとっては初期投資が障壁となる場合があります。
- 長期的な ROI: 大量生産環境では、エネルギー効率、メンテナンスの低減、処理速度の高速化によるコスト削減が、多くの場合、投資を正当化します。ただし、少量生産アプリケーションでは、初期費用が高いため、ファイバー レーザー切断は他の方法に比べて魅力が薄れる可能性があります。
安全性の懸念
ファイバーレーザーは、非常に集中した波長で高強度のレーザービームを放射するため、適切に管理しないと安全上のリスクが生じる可能性があります。また、切断プロセスでは煙や微粒子が発生する可能性があり、作業者と環境を保護するために慎重に取り扱う必要があります。
- レーザー放射: 強力なレーザー光線は、皮膚や目に直接触れると重傷を負う可能性があります。ファイバー レーザーには、偶発的な照射を防ぐために安全筐体とインターロック システムが必要です。
- 煙と粒子の排出: 特定の金属、特に亜鉛メッキ鋼のようなコーティングが施された金属を切断すると、有害な煙や粒子が放出される可能性があります。安全な作業環境を維持するには、適切な換気と煙排出システムが不可欠です。
- 火災の危険性: 切断中に発生する高温により可燃性物質が発火し、特に換気の悪い場所や雑然とした場所では火災の危険が生じます。これらのリスクを軽減するには、定期的な機器メンテナンスや消火システムなどの安全プロトコルが必要です。
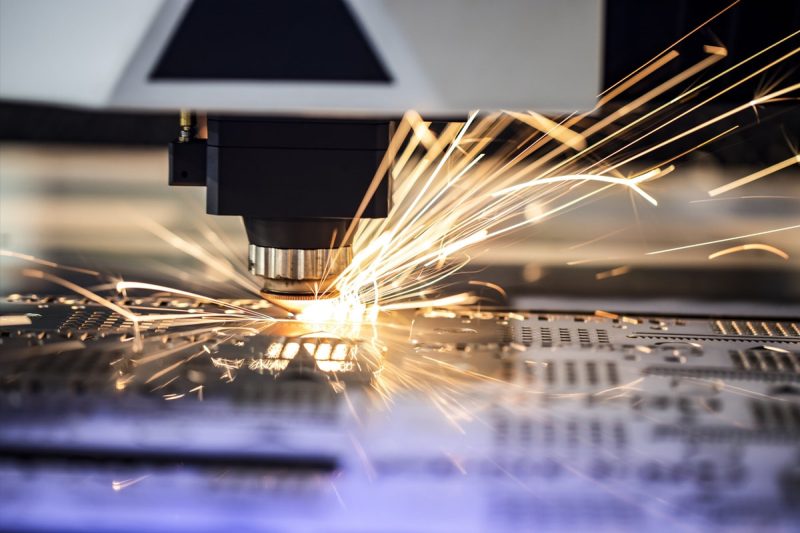
安全上の考慮事項
保護具
潜在的なレーザーの危険からオペレータを保護するために、ファイバー レーザー切断機の近くで作業するときは常に適切な個人用保護具 (PPE) を使用する必要があります。
- レーザー安全メガネ: 作業者は、ファイバー レーザーの波長 (通常、約 1.064 マイクロメートル) に適したレーザー安全メガネを着用する必要があります。このメガネは、直接または反射されたレーザー ビームによる目の損傷を防ぎます。
- 防護服: 耐火性の服と手袋は、作業者を火花、熱い金属粒子、火傷から保護します。これは、切断中に熱を発生する厚い金属や導電性の高い金属を扱う場合に特に重要です。
- 聴覚保護: ファイバーレーザー切断機は、特に高出力または高生産環境において、聴覚保護が必要となるレベルの騒音を発生する場合があります。
機械の安全機能
ファイバーレーザー切断機には、事故を防ぎ、オペレーターと機器の両方を保護するように設計されたいくつかの組み込み安全機能が装備されています。
- 安全エンクロージャ: エンクロージャは、レーザー放射からオペレータを保護し、レーザー光線への偶発的な露出を防止します。これらの保護バリアはレーザー光を封じ込め、指定された切断領域にのみ影響を与えるようにします。
- インターロック システム: インターロック メカニズムは、エンクロージャが開かれたとき、または不正なアクセス ポイントが検出されたときに、レーザーを自動的にシャットダウンします。この機能により、レーザー ビームへの偶発的な露出が防止され、安全性がさらに高まります。
- 緊急停止ボタン: 緊急停止ボタンはマシン上に戦略的に配置されており、故障や緊急事態が発生した場合にオペレーターがレーザー切断プロセスを即座に停止できます。
- センサーとアラーム: 高度なファイバー レーザー マシンには、過熱、過剰な反射、またはシステムの誤動作を検出するセンサーとアラームが装備されていることが多く、問題が深刻化する前にオペレーターに潜在的な問題を警告します。
環境制御
ファイバーレーザー切断では、特に亜鉛メッキ鋼などのコーティングが施された金属を切断する場合、煙、微粒子、さらには可燃性の粉塵が発生することがあります。空気の質を維持し、火災の危険を防ぎ、安全な作業環境を確保するには、適切な環境管理が不可欠です。
- 換気と煙の除去: 特定の金属を切断すると、有毒な煙や微粒子が放出されることがあります。煙の除去システムと適切な換気により、作業スペースから有害物質が除去され、作業者の呼吸器系の健康が保護され、空気の質が確保されます。
- 集塵システム: 可燃性粉塵が発生する金属を切断する場合、集塵システムは蓄積を防ぎ、火災や爆発のリスクを軽減するために不可欠です。これらのシステムの定期的な清掃とメンテナンスも、安全な操作を継続するために不可欠です。
- 温度と湿度の制御: 安定した温度と湿度レベルを維持すると、レーザーのパフォーマンスを妨げ、電気的危険のリスクを高める可能性のある結露を防ぐことができます。
トレーニングと手順
適切なトレーニングと厳格な操作手順は、ファイバー レーザー切断機を安全かつ効率的に使用するための基本です。すべてのオペレーターは、機械の取り扱い、安全プロトコル、緊急時の対応に関する包括的なトレーニングを受ける必要があります。
- オペレーターのトレーニング: すべてのオペレーターは、機械の起動と停止、パラメータの調整、補助ガスの使用、材料の取り扱いなど、ファイバー レーザー切断機の操作について徹底的にトレーニングを受ける必要があります。トレーニングでは、保護具の正しい使用方法や安全プロトコルに従うことの重要性についても説明する必要があります。
- 安全プロトコル: 安全ガイドラインを確立し、すべての担当者に伝達する必要があります。これらのプロトコルには、適切な起動およびシャットダウン プロセス、メンテナンス スケジュール、緊急事態や機器の故障に対処する手順が含まれます。
- 緊急手順: オペレーターは、レーザーの故障、火災、煙の蓄積などの緊急事態に対応し、必要に応じてその場所から安全に避難する方法を習得するためのトレーニングを受ける必要があります。定期的な安全訓練と緊急時プロトコルの見直しは、これらの手順を強化するのに役立ちます。
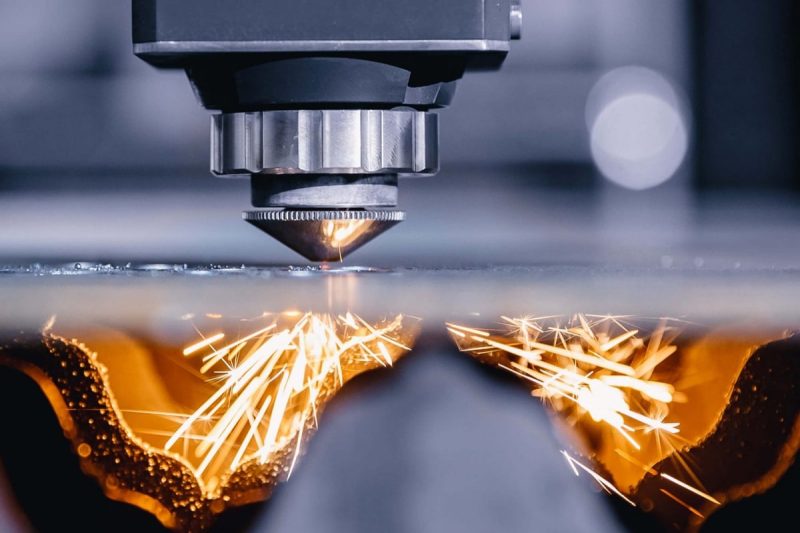
まとめ
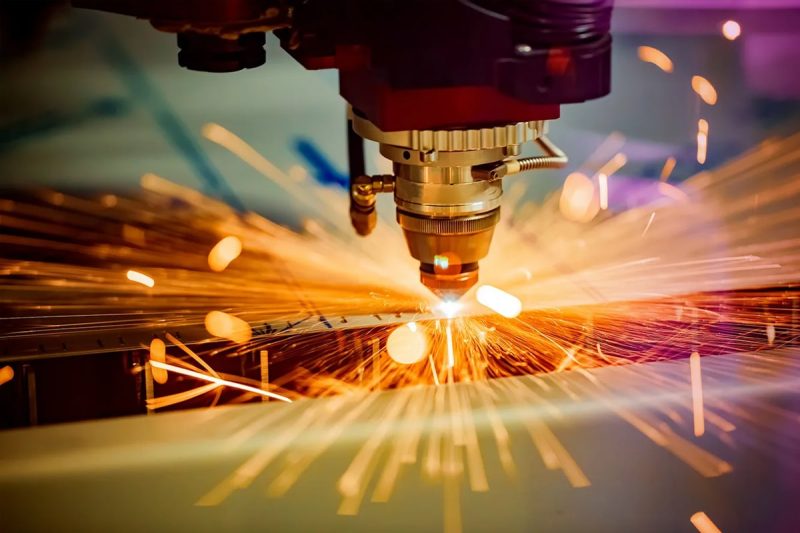
レーザー切断ソリューションを入手
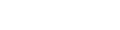
- [email protected]
- [email protected]
- +86-19963414011
- No. 3 ゾーン A、Lunzhen 工業地帯、玉城市、山東省。