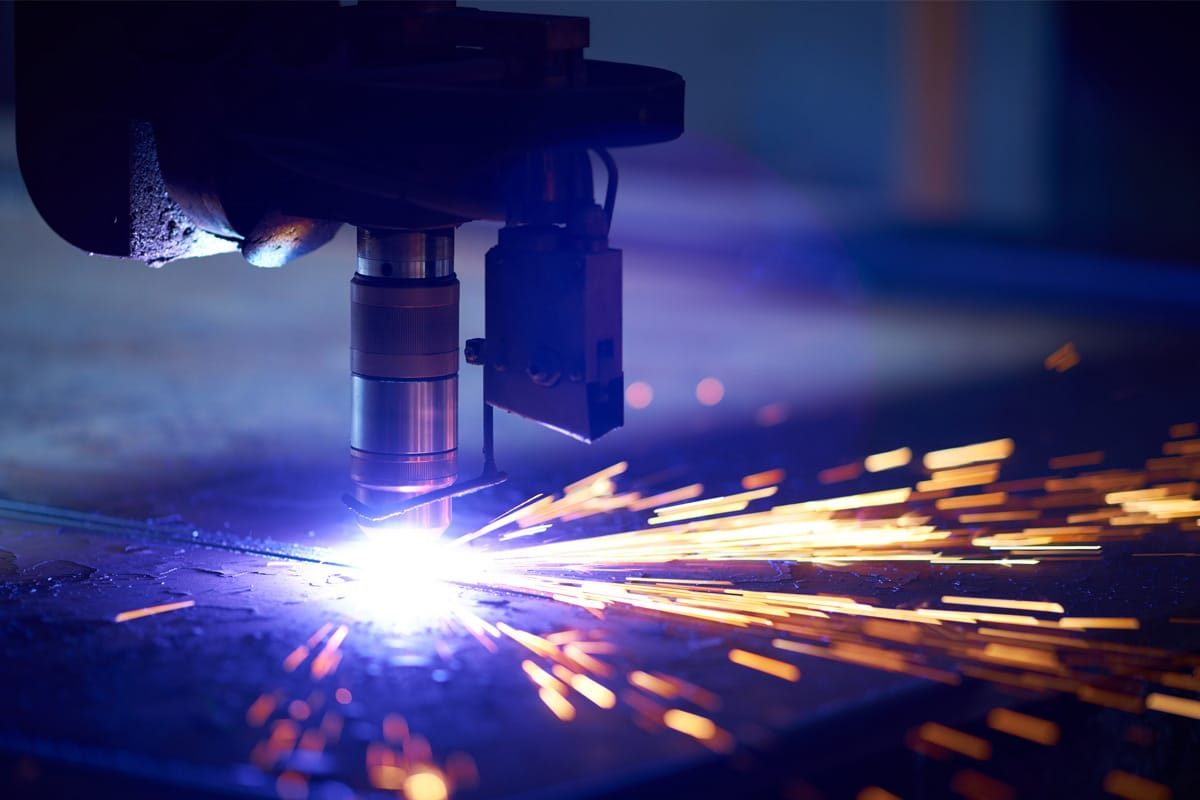
ファイバーレーザー切断の一般的な問題と解決策
ファイバーレーザー切断技術は、高効率、高精度、柔軟な操作性を備えているため、さまざまな金属および非金属材料の切断と加工に広く使用されています。高出力レーザービームを使用してワークピースの表面に照射し、ワークピースを溶融または気化させることで、ワークピースの精密な切断を実現します。ただし、実際のアプリケーションでは、ファイバーレーザー切断は、切断品質の低下、切断効率の低下、機器の急速な損失など、いくつかの一般的な問題と課題にも直面しています。これらの問題を理解して対処することで、機器の寿命を延ばすだけでなく、生産効率と加工品質を向上させることができます。
目次
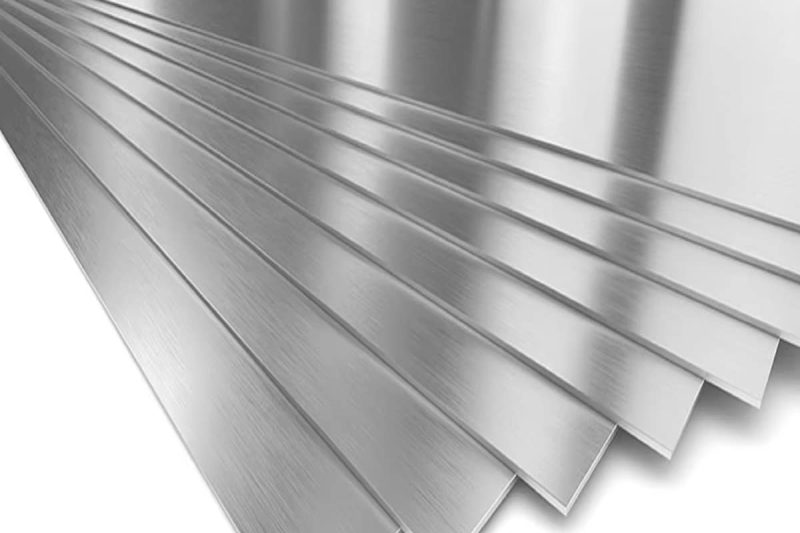
材料関連の課題
反射率と伝導率
材料の導電性が優れているほど、レーザーエネルギーの吸収率は低くなります。たとえば、金、銀、銅、アルミニウムなどの材料は導電性は良好ですが、エネルギー吸収性は低く、レーザー波長を反映するとも言えます。したがって、金属の導電性が高いほど、その反射率は高くなります。
チャレンジ
- 高い反射率:アルミニウムや銅などの金属は反射率が高く、特にレーザービームが材料表面の法線に近い角度で入射すると、レーザーエネルギーの大部分がレーザー発生器またはレーザー伝送システムに反射され、加工効率が低下するだけでなく、レンズや光ファイバーの焼損など、レーザー機器に損傷を与える可能性もあります。
- エネルギー吸収不足: 反射率が高いため、材料表面で吸収される有効なレーザーエネルギーが減少し、加工深さが不十分になったり、切断速度が遅くなったり、加工品質が低下したりします。
解決
- 高出力レーザーを使用する: レーザー発生器の出力を上げると、材料の表面に照射されるレーザーエネルギーを直接増加させることができます。エネルギーの一部が反射されても、残りのエネルギーは効率的な処理に十分です。エネルギー伝達と処理効果を最適化するには、特定の材料に適したパルス幅と周波数のレーザー発生器を選択します。
- 反射防止技術:レーザービームの形状と発散角を調整することで、レーザーエネルギーが材料の表面でより均一に分散され、過度の局所反射の問題が軽減されます。動的に調整可能な光学素子(変形ミラーや液晶空間光変調器など)を使用して、レーザービームの波面歪みをリアルタイムで補正し、レーザービームの集束品質を向上させ、反射と散乱を軽減します。一部の金属は、異なる偏光状態のレーザーに対して異なる反射特性を持っています。レーザーの偏光方向を調整することで、反射損失を減らすことができます。
- 材料表面処理の最適化: 材料の表面にレーザーエネルギーを吸収するコーティングまたはフィルムを塗布して、レーザーエネルギーの吸収率を高め、反射率を低下させます。機械的、化学的、またはレーザーによる前処理により材料表面の粗さを高め、レーザーエネルギーの散乱と吸収を改善し、直接反射を減らします。材料の表面に吸収層を形成するか、表面の化学的性質を変更して、レーザー吸収率を高めます。
- 処理パラメータの調整: レーザービームの入射角を最適化して、レーザービームが材料表面に直接垂直に入射しないようにし、鏡面反射を減らします。レーザー処理の速度、出力、焦点距離などのパラメータを調整して、処理品質と効率を確保するための最適な処理条件を見つけます。
材料の反りと変形
材料の変形は、材料内部の残留応力によって生じる反りによって発生し、材料の幅と長さに沿って不均一に分布します。
チャレンジ
レーザー切断工程では、特に薄板材料の場合、局所的な加熱により材料の変形が生じることがあります。これは、レーザーが切断中に小さな領域に大量の熱エネルギーを集中させ、その領域の温度が急激に上昇し、材料の熱膨張と収縮を引き起こし、最終的に材料が反ったり変形したりするためです。
解決
- レーザー出力を調整する: レーザー出力を下げると熱の集中が減り、材料の熱変形が軽減されます。
- 切断速度を最適化: 切断速度を適切に上げると、レーザーが材料上に留まる時間が短縮され、熱の蓄積が軽減されます。
- 補助ガスの使用: 適切な補助ガス (窒素や酸素など) を選択し、その流量を調整することで、切断プロセス中に発生する熱を効果的に除去し、材料の変形を減らすことができます。
材料の厚さ
ファイバーレーザー切断プロセスでは、材料の厚さが切断品質、効率、機械性能に直接影響します。材料が薄いほど切断しやすく、速度も精度も高くなりますが、材料が厚いと切断面が粗くなったり、より高い電力と補助ガスが必要になる場合があります。
チャレンジ
厚い材料を切断する場合、レーザーが材料を貫通するのに時間がかかるため、切断が不均一になりやすくなります。厚い材料は熱伝導性が低く、熱が放散されにくいため、切断エッジにスラグや不均一な切断面が生じます。
解決
- 適切なレーザー出力を選択する: 材料の厚さに応じて適切なレーザー出力を選択し、ビームエネルギーが切断領域に集中して最良の切断効果が得られるようにします。
- 切断パラメータを調整します。切断速度、焦点位置、補助ガス圧力などのパラメータが含まれており、切断プロセスの安定性と均一性を確保します。
- 多重切断: 特に厚い材料の場合、複数の切断方法を使用して、毎回厚さの一部を切断し、層ごとに切断することで、熱の蓄積と不均一な切断の問題を軽減できます。
上記の方法により、レーザー切断時の厚い材料の高反射、反り、変形、切断の不均一などの問題を効果的に解決し、切断品質と効率を向上させることができます。
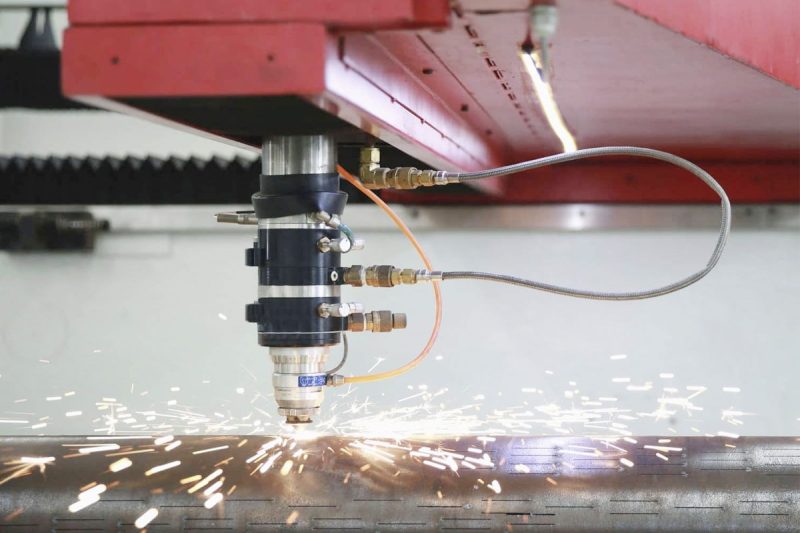
エッジ品質とカーフ幅
切断面の滑らかさとバリの量は、切断精度を評価する上で重要です。レーザーエネルギーが不均一に分散されていたり、切断速度が適切でなかったりすると、切断面が粗くなったりバリができたりすることがあります。スリットの幅は、レーザー焦点の安定性に依存します。焦点が不安定であったり、レーザー出力が変動したりすると、スリットの幅が不均一に変化し、切断精度に影響することがあります。
粗いエッジとバリ
チャレンジ
- レーザー切断の際、エネルギーが不均一であったり、切断速度が速すぎたり遅すぎたりすると、切断面にバリや凹凸が生じることがよくあります。特にレーザービームの出力が不安定な場合は、切断面が局所的に過熱されたり、不均一に溶けたりして、切断面が粗くなることがあります。
- 一部の金属材料(アルミニウム、ステンレス鋼など)では、熱分布が不均一になると熱応力が生じ、さらにバリの形成につながります。
- また、補助ガスの不適切な使用(空気流量不足や圧力不適切)も溶融材料の排出効率に影響し、バリの発生を増加させます。
解決
- レーザーの出力設定と切断速度を最適化することが重要です。レーザー出力が十分に高く、出力が安定して、材料表面の熱分布が均一になるようにしてください。同時に、切断速度は材料の厚さと特性に応じて調整する必要があり、速すぎても(材料の切断が不十分になるのを防ぐため)、遅すぎても(過剰な溶融を防ぐため)いけません。
- 窒素や酸素などの適切な補助ガスを使用すると、切断結果が向上し、切断面がきれいで滑らかになります。窒素は酸化を防ぎ、エッジのバリを減らすためによく使用され、酸素は切断効率と溶解速度の向上に役立ちます。
スリット幅の変化
チャレンジ
- スリット幅が一定でない主な原因は、通常、レーザー焦点の不安定性またはレーザー出力の変動に関連しています。レーザー焦点がずれると、エネルギー集中がそれに応じて変化し、スリット幅が変動します。レーザー出力が不安定な場合、エネルギーの出力変動は切断精度に直接影響し、スリット幅の変化を引き起こします。
- さらに、光学部品の汚れや損傷によってビーム品質が変化し、切断ラインの均一性に影響が出ることもあります。また、ガイドレールやベアリングなどの機械部品の摩耗もレーザーヘッドの移動精度に影響し、スリットの不均一性が生じます。
解決
- レーザーの焦点とエネルギーが安定するように、光学システムを定期的に点検し、メンテナンスしてください。
- ビーム伝送中に不要な屈折や散乱が発生しないように、汚れた光学レンズを清掃または交換してください。
- 動作中の精度を確保するために、レーザー機器の焦点と出力を定期的に調整してください。
- 機械の摩耗による切断エラーを減らすために、レーザー ヘッドのスムーズで障害のない動きを確保するために、機器の機械部品をメンテナンスします。
要約すると、パラメータを正しく設定し、光学系を定期的にメンテナンスすることで、エッジ品質を効果的に改善し、カーフ幅を制御することができます。
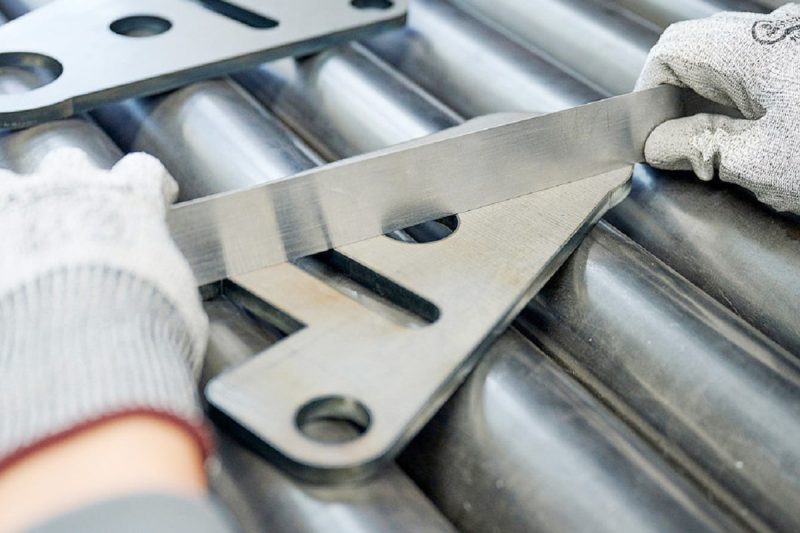
プロセス関連の課題
プロセス関連の課題は、主にファイバーレーザー切断プロセス中に発生する可能性のある技術的な問題です。一般的なプロセス関連の課題にはスラグの蓄積が含まれます。これはファイバーレーザー切断プロセスでよく発生する課題で、特に厚い材料や切断が難しい材料を切断する場合によく発生します。通常、スラグの蓄積は、材料が完全に溶融または蒸発しなかったり、補助ガスの供給が不十分で溶融材料を切断領域から時間内に吹き飛ばせないことが原因で発生します。
スラグの蓄積
チャレンジ
- レーザーエネルギーが不十分であったり、レーザービームの焦点がずれていると、材料表面が溶融または蒸発する温度に達することができず、切断端に材料が残ってしまいます。特に厚板の加工では、レーザーエネルギーが材料の厚さ全体に浸透するほど強力である必要があります。
- 溶融材料を切断領域から吹き飛ばすために、酸素や窒素などの補助ガスがよく使用されます。ガス圧が低すぎて溶融材料を効果的に除去できない場合は、切断エッジにスラグが蓄積します。
- 切断速度が速すぎると、レーザーが同じ領域に作用し続けなくなり、材料が完全に溶けなかったり、ガスが時間内に残留物を排出できず、スラグが蓄積することになります。
解決
- 溶融材料を効果的に除去し、スラグの蓄積を防ぐために、十分なガス圧が供給されていることを確認してください。窒素は非酸化性材料に適していますが、酸素は切断速度を加速できますが、より高いガス圧が必要です。
- 材料の厚さと特性に応じて切断速度を最適化し、レーザーエネルギーが切断領域に十分に作用できるようにします。レーザー出力と切断速度を適切に組み合わせることで、不要な熱影響領域を減らし、材料の不完全な溶融の問題を回避できます。
- レーザー発生器の光学部品が最良の状態にあり、必要なレーザー出力を安定して出力できることを確認して、切断プロセスの一貫性を確保します。
これらのパラメータを総合的に調整することで、スラグ蓄積の問題を大幅に軽減し、切断品質を向上させ、その後の研磨および洗浄作業を削減できます。
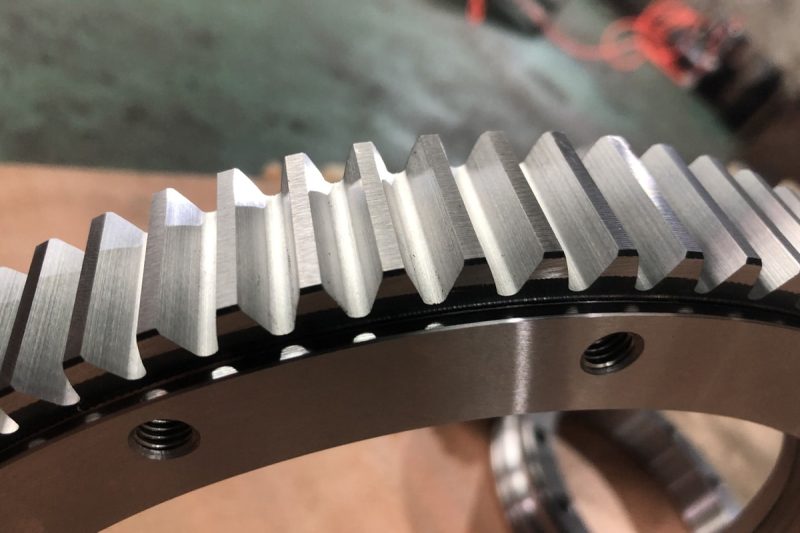
パンクと始動の問題
ファイバーレーザー切断プロセスでは、特に厚い材料や反射率の高い材料を扱う場合、穿孔と起動の問題が一般的な課題となります。穿孔プロセスはレーザー切断の出発点であり、その安定性と効率は切断プロセス全体の効果に直接影響します。穿孔時間が長すぎたり失敗したりすると、材料の無駄や機器の摩耗につながり、切断品質にも影響する可能性があります。起動プロセスの不安定さは、スリットの不均一や切断品質の低下につながり、完成品の精度と外観に影響を与えます。
ピアシングの遅延と失敗
チャレンジ
ピアシングの遅延は通常、レーザー ビームが材料を貫通するのに十分なエネルギーをすばやく集中できず、ピアシングに長い時間がかかることが原因で発生します。ピアシングの遅延は、厚い材料や反射性材料 (アルミニウムや銅など) で特に顕著で、ピアシングの失敗を引き起こすこともあります。ピアシングの失敗の原因としては、レーザー出力の不足、レーザー フォーカスの不正確さ、補助ガスの不足、ガスの選択の不適切などが挙げられます。これにより、切断の開始が不均一になったり、切断が失敗したり、材料が無駄になったり、レーザー機器が損傷する可能性があります。
解決
- 特に厚い板材では、穿孔に高いエネルギーが必要となるため、レーザー出力を素早く集中させる必要があります。レーザーの焦点を調整して、材料の表面に集中させ、エネルギーの分散を減らし、穿孔時間を短縮します。
- 短パルスモードでのピアシングにより、材料の過熱と変形が軽減され、ピアシングが失敗する可能性も減ります。この技術は、厚い材料や反射率の高い材料に特に適しています。
- 窒素と酸素の使用は、穿孔プロセスに大きな影響を与えます。酸素は穿孔プロセスを高速化できますが、材料の酸化を引き起こす可能性があるため、材料の特性に基づいて適切なガスと圧力を選択する必要があります。
- 非常に厚い材料の場合、一度にすべてではなく層ごとに材料を貫通する多段階穿孔技術を使用できます。この方法により、穿孔の失敗と過度の熱の影響を効果的に回避できます。
不安定な起動
チャレンジ
不安定な起動は、主にレーザー切断の開始時に不均一なカーフ幅と不良なエッジ品質として現れ、切断プロセスの失敗につながることもあります。これは通常、不安定なレーザーエネルギー、ガス流量の変化、材料表面特性の不一致(酸化やコーティングなど)などによって引き起こされます。不安定な起動は、特に精密切断アプリケーションでは、初期部分の切断品質の低下につながる可能性があり、この不安定性は完成品の精度と一貫性に影響します。
解決
- 特に反射率の高い材料の場合は、作業を始める前に材料の表面を予熱しておくことができます。これによりレーザーの反射が抑えられ、切断プロセスがスムーズになります。
- レーザー出力の増加率と補助ガスの流量を調整することで、レーザー発生器が起動時に速やかに安定状態に達するようにします。これにより、起動時のエネルギー変動を効果的に回避できます。
- 表面に酸化物層やその他の不純物がある材料の場合、起動前に簡単な表面洗浄またはコーティング除去を実行することで、起動プロセス中のレーザー反射と不安定性を軽減できます。
- リアルタイム監視システムを使用して、特に起動フェーズ中に切断プロセスを監視し、パラメータを調整することで切断プロセスの安定性と一貫性を確保します。
一般的に、レーザーパラメータを最適化し、適切な補助ガスを選択し、パルス穿孔技術を使用し、開始前に前処理することで、穿孔の遅延、失敗、不安定な開始などの問題を大幅に軽減し、切断効率と品質を向上させることができます。これらのソリューションは、運用効率を向上させるだけでなく、機器の長期にわたる安定した動作を保証します。
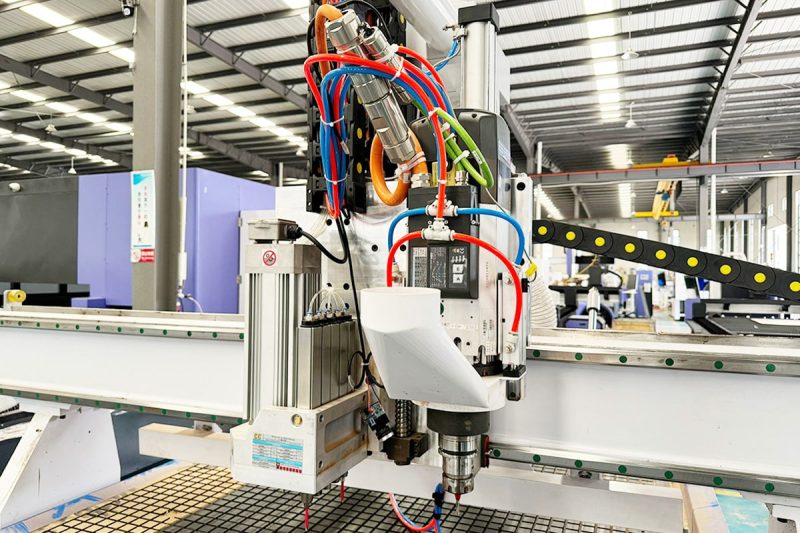
機械関連の課題
ファイバーレーザー切断では、機械の性能が切断品質と効率に直接影響します。機械自体のビーム伝送システムと機械部品は、長期間の使用後にさまざまな問題が発生する可能性があり、レーザー切断の精度と安定性に影響を与えます。
ビーム伝送システムの問題
チャレンジ
ビーム伝送システムは、レーザー光源のエネルギーを切断ヘッドに伝送するコアシステムです。その性能は、レーザービームのエネルギー安定性と切断品質を直接決定します。ビーム伝送システムを定期的に検査および保守しないと、ほこり、不純物、または機械的摩耗によって光学部品が損傷し、システムの効率がさらに低下する可能性があります。
解決
- 光学レンズやファイバーレーザー切断システムのレンズは、ほこりや油が蓄積されやすい傾向があります。定期的に清掃することで、レーザービームの伝送効率の低下を防ぎ、ビームの安定性を確保できます。
- ファイバー コネクタの安定性とレーザー ビームの正確な位置合わせを確保することで、エネルギー損失を削減できます。ファイバー接続を定期的にチェックして、緩みや摩耗がないことを確認してください。
- ビームの不安定性の問題が頻繁に発生する場合は、適応光学技術を使用してビーム伝送システムをリアルタイムで調整し、最高のビーム品質を確保することを検討してください。
- ビーム伝送中の熱蓄積はビーム品質に影響を与えるため、冷却システムを効率的に稼働させることが重要です。冷却システムを定期的にチェックして、正常に熱を放散し、ビーム伝送中の熱の影響を軽減できることを確認してください。
機械的摩耗
チャレンジ
ガイドレール、サーボモーター、駆動システムなど、ファイバーレーザー切断機の機械部品は、集中的に使用すると時間の経過とともに徐々に摩耗します。機械の摩耗は、切断ヘッドの動きが不安定になるだけでなく、切断経路の精度、ひいては完成品の品質にも影響を与える可能性があります。特に、高速かつ高精度の切断が求められる場合、機械の摩耗により機器の老朽化が加速し、メンテナンスコストとダウンタイムが増加します。さらに、振動や騒音の増加も機械の摩耗の一般的な症状です。
解決
- ガイドレールと伝動システムは、摩擦を減らして機械部品の耐用年数を延ばすために定期的に潤滑する必要があります。同時に、潤滑システムを点検して正常に動作していることを確認し、潤滑不足による部品の過度の摩耗を防ぐ必要があります。
- ガイド レール、ギア、またはその他の部品が摩耗またはオフセットしていることが判明した場合は、機械の精度と安定性を確保するために、損傷した部品を適時に交換する必要があります。
- 高精度な加工では、振動により切削精度が損なわれることがあります。防振装置を設置したり、機械の設置位置を最適化することで、機械部品への振動の影響を軽減し、摩耗を遅らせることができます。
- モダンな ファイバーレーザー切断機 機械部品の状態をリアルタイムで監視し、データ分析を通じて事前に故障を予測し、機械の摩耗による突然のダウンタイムを回避する監視システムを装備することができます。
ビーム伝送システムと機械部品の定期的なメンテナンスと最適化により、ファイバーレーザー切断機の性能と安定性が大幅に向上し、切断効果の継続性と高品質が保証されます。
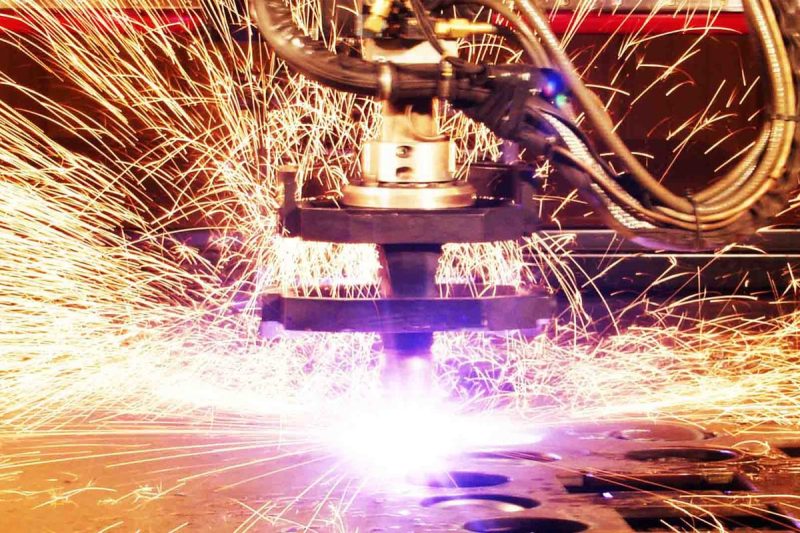
テーパーと角度偏差
テーパーと角度偏差は、ファイバーレーザー切断プロセスにおける 2 つの一般的な精度上の課題です。テーパーの問題は通常、切断エッジの上部と下部の幅が一定でないことで現れますが、角度偏差はレーザービームと材料の間の垂直性が欠如していることを意味し、その結果、切断面が傾きます。これらの問題は、特に高精度の切断作業において、最終的なワークピースの品質と外観に影響を及ぼします。
テーパー
チャレンジ
テーパー現象は通常、厚い材料を切断するときに発生し、切断刃の上部が狭く、下部が広い、または上部が広く、下部が狭いという形で現れます。これは、レーザービームが材料を通過するときにエネルギー分布が不均一になるためです。切断深さが大きいほど、レーザーエネルギーの減衰が顕著になり、切断刃の上部と下部の幅に差が生じます。テーパーは、特に高精度の組み立ての場合、ワークピースの精度に影響を与えます。テーパーは組み立てを困難にし、ワークピースをスクラップにすることさえあります。さらに、不適切な補助ガス圧力と不安定なレーザー出力もテーパー現象を悪化させます。
解決
- テーパーの問題は、レーザー焦点の深さと位置を最適化することで効果的に軽減できます。焦点を材料の表面ではなく中央に配置すると、切断厚さ全体にわたってレーザー エネルギーが均等に分散されます。
- より厚い材料の場合、高出力のレーザー発生器を使用すると、切断プロセス中に安定したエネルギー出力を維持し、レーザー減衰によって発生するテーパーの問題を軽減できます。
- 補助ガスの圧力を適切に調整し、切断領域を清潔に保ち、刃先を効果的に冷却することで、テーパーを減らすことができます。特に厚い材料の切断では、補助ガスの役割が重要です。
- 光学システムに少しでも問題があると、レーザービームのエネルギー分布が不均一になります。そのため、光学部品を定期的にメンテナンスしてクリーニングし、レーザービームの品質を確保することで、テーパーを効果的に低減できます。
角度偏差
チャレンジ
角度偏差とは、レーザー ビームが材料に対して垂直でなくなり、切断エッジが傾くことを意味します。これは、レーザー ヘッドの取り付けが不安定、ビームの位置合わせが不正確、または機械システムの精度が不十分なことが原因で発生することがあります。角度偏差により、ワークピースの切断面が不均一になり、特にワークピースを直角に切断する必要がある場合に、精度と外観に影響を及ぼします。
解決
- レーザー ヘッドがしっかりと取り付けられ、材料に対して垂直になっていることを確認することが、角度偏差の問題を解決するための第一歩です。レーザー ヘッドと機械システムを定期的に調整することで、切断中にレーザー ビームが常に正しい角度を維持できるようになります。
- 切断速度、出力、補助ガスの設定はすべて角度偏差に影響します。これらのパラメータを最適化することで、切断中にレーザービームを安定させ、角度偏差を減らすことができます。
- 適応光学は、レーザービームの伝播経路と焦点をリアルタイムで調整し、切断中に材料との正しい角度が常に維持されるようにすることで、角度の偏差を低減します。
- 温度や湿度の変化、振動などの外的要因は、レーザー切断の角度精度に影響を与える可能性があります。振動の低減、温度や湿度の制御など、切断環境の安定性を維持することで、角度偏差をさらに低減できます。
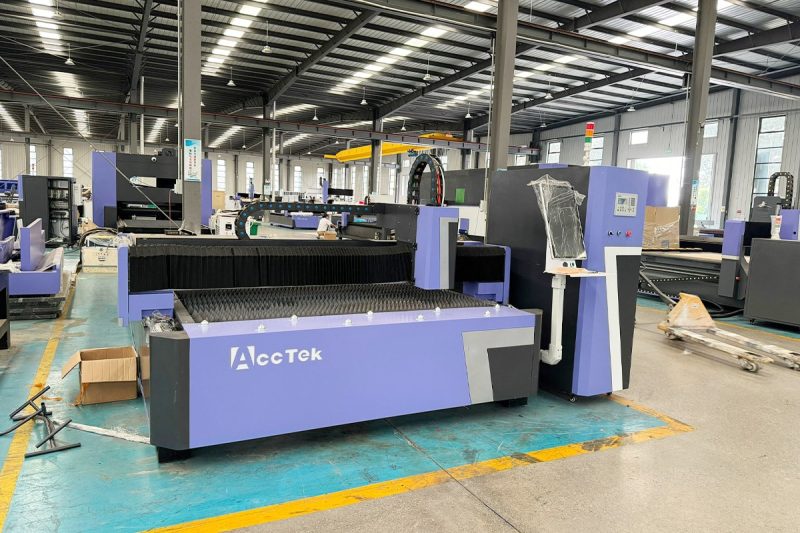
環境要因
環境要因は、ファイバー レーザー切断プロセスの安定性と品質に直接影響します。温度と湿度の変動、および空気の質の変化は、レーザー システムのパフォーマンス、切断の品質、および機械の寿命に悪影響を及ぼす可能性があります。これらの環境要因を理解して制御することで、機器が最高の状態で動作し、不要な故障やメンテナンスの必要性が軽減されます。
温度と湿度の変動
チャレンジ
温度と湿度の変動は、レーザー切断プロセスにおける大きな課題です。レーザー発生器と光学システムは、温度と湿度の変化に非常に敏感です。たとえば、温度が高すぎるとレーザー発生器が過熱し、レーザービームの品質と安定性に影響する可能性があります。一方、温度が低すぎると、レーザー発生器が必要な動作温度に到達できず、出力に影響する可能性があります。湿度が高すぎると、光学部品に結露が発生し、レーザービームの伝送効率に影響し、光学デバイスが損傷することもあります。湿度が低すぎると、静電気のリスクが高まり、電子部品の正常な動作を妨げる可能性があります。
解決
- 温度と湿度の変動に対処するために、切断作業場に空調や除湿装置などの専用の環境制御システムを設置することをお勧めします。これらのシステムにより、作業場の温度と湿度を一定に保ち、レーザー装置が最適な状態で動作することを保証します。
- 切断装置の周囲に温度と湿度のセンサーを設置し、環境条件をリアルタイムで監視します。異常が検出されると、環境制御システムを自動的に調整したり、必要に応じて切断プロセスを一時停止して、装置の損傷を回避したりできます。
- 乾燥した環境では、空気の湿度を高めて静電気のリスクを軽減し、安全な操作を確保するために静電気防止床と機器の接地対策を講じてください。
空気の質
チャレンジ
空気の質がレーザー切断プロセスに与える影響は無視できません。空気中に浮遊するほこり、オイルミスト、その他の汚染物質がレーザー発生器の光学系や切断領域に入り込み、レーザービームの伝送と集束に影響を与える可能性があります。また、空気中の汚染物質は切断プロセス中にレーザービームと反応し、切断結果が悪くなったり、ワークピースの表面が損傷したりすることもあります。さらに、質の悪い空気に長期間さらされると、機械のメンテナンス頻度が増加し、機器の耐用年数が短くなります。
解決
- レーザー切断作業場に空気清浄システムを設置して、空気中の粒子状物質や汚染物質を除去し、きれいな空気を確保します。特に、特定の材料(プラスチックや木材など)を切断する場合、レーザー切断プロセス中にこれらの材料から有害なガスが放出される可能性があるため、効果的な空気清浄システムが特に重要です。
- 空気清浄システムを使用していても、レーザー発生器の光学システムを定期的に清掃する必要があります。レーザービームの品質と切断効果を確保するために、蓄積する可能性のあるほこりや汚染物質を除去します。
- 一部の重要な設備またはエリアでは、正圧保護対策を採用することができます。つまり、ろ過された空気を導入することで、そのエリア内の空気圧を外部よりも高く維持し、汚染物質の侵入を防ぎます。
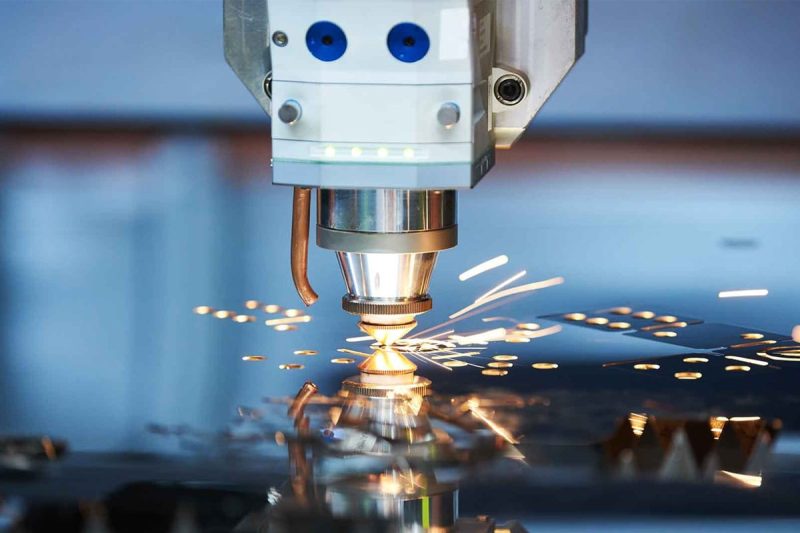
オペレータ関連の課題
環境要因に加えて、オペレーターのスキルレベルと作業効率もファイバーレーザー切断の品質と効率に直接影響します。トレーニングと専門知識の不足、または非効率的なワークフローは、不適切な操作、エラー率の増加、さらには機器の損傷や安全事故につながる可能性があります。したがって、オペレーターの専門性を向上させ、ワークフローを最適化することは、切断品質と生産効率を確保するための重要なリンクです。
トレーニングと専門知識の不足
チャレンジ
ファイバーレーザー切断は高精度の技術であり、オペレーターは高度な専門知識とスキルを必要とします。しかし、一部の企業では、オペレーターが十分なトレーニングを受けておらず、レーザー切断の複雑さを完全に理解して習得できない場合があります。この状況により、オペレーターは技術的な問題や複雑なワークピースに直面したときに効果的に対応できず、切断品質に影響を与え、機器の摩耗を増加させ、安全上の危険を引き起こす可能性があります。さらに、機器のメンテナンスとケアには特定のスキルと知識が必要です。オペレーターの知識不足により、機器が迅速にメンテナンスおよびケアされず、機器の耐用年数が短くなる可能性があります。
解決
- 企業は、レーザー切断の基本原理、機器の操作ガイド、トラブルシューティング、一般的な問題の解決策などを含む体系的なトレーニングをオペレーターに提供する必要があります。定期的なトレーニングを通じて、オペレーターが常に最新の技術と操作仕様を習得できるようにします。
- オペレーターの操作認証システムを確立し、認証を受けた人だけがレーザー切断装置を操作できるようにします。これにより、オペレーターの責任感が向上するだけでなく、操作の品質と安全性も確保されます。
- 専門の技術コンサルティング部門を設置したり、技術専門家を雇用して定期的に指導し、オペレータが日常業務で問題を解決できるように支援するなど、オペレータに強力な技術サポートを提供します。
非効率的なワークフロー
チャレンジ
ワークフローの効率は、生産全体の効率とレーザー切断の品質に直接影響します。一部の企業では、ワークフローの設計が不合理であったり、調整が不十分であったりするため、作業者がタスクの切り替え、機器のデバッグ、材料の取り扱いに時間がかかりすぎることがあります。このような非効率的なワークフローは、時間とリソースを浪費するだけでなく、作業者の疲労を引き起こし、エラーの可能性を高める可能性があります。さらに、企業がワークフローを速やかに最適化しないと、注文量が増えるにつれて、非効率的なプロセスが顕著になり、生産能力と企業の競争力に深刻な影響を及ぼします。
解決
- 現在のワークフローを分析・評価することで、ボトルネックや非効率なリンクを特定し、ターゲットを絞った最適化を行うことができます。たとえば、タスクの順序を合理的に整理し、機器の試運転や材料の取り扱いにかかる時間を短縮し、作業効率を向上させることができます。
- 自動積み込み・積み下ろしシステムやインテリジェントな組版ソフトウェアなどの自動化技術を導入することで、手作業による時間と精度の誤差を大幅に削減し、ワークフロー全体の効率を向上させることができます。
- 無駄を削減し、リソースの割り当てを最適化するために、リーン生産方式の原則を適用します。継続的な改善と従業員の参加を通じて、効率的で柔軟なワークフローを確立し、レーザー切断プロセスの効率と高品質を確保できます。
これらの環境およびオペレータ関連の課題に対処することで、企業はファイバーレーザー切断の効率と品質を大幅に向上させ、市場競争で優位に立つことができます。
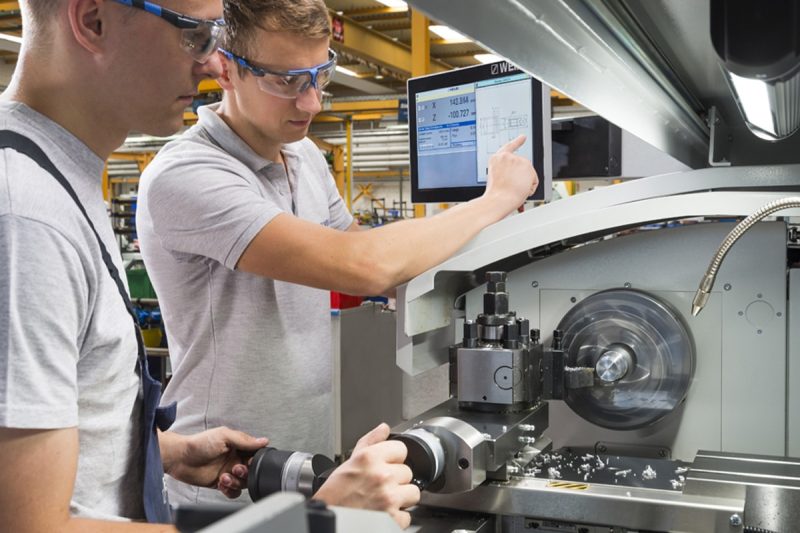
注意事項とベストプラクティス
ファイバーレーザー切断の効率的な運用を継続的に確保するには、予防措置とベストプラクティスを講じることが重要です。定期的な機械メンテナンス、パラメータの最適化、オペレーターのトレーニング、継続的な改善を通じて、企業は故障率を効果的に低減し、切断品質を向上させ、機器の寿命を延ばすことができます。
定期的な機械メンテナンス
チャレンジ
レーザー切断装置を長期間使用すると、光学部品の汚染、レーザーヘッドの摩耗、冷却システムの故障につながる可能性があります。定期的なメンテナンスが不足すると、これらの問題がレーザー発生装置のパフォーマンスに影響を与え、生産停止時間の増加、さらには装置の故障を引き起こす可能性があります。
解決
- レーザービームの伝送効率を確保するために、光学システムを定期的に清掃してください。
- 切断ノズル、レーザー レンズ、フィルター システムなどの脆弱な部品を点検し、交換します。
- レーザー発生器の過熱を防ぐために、冷却システムを定期的に点検し、適切に機能していることを確認してください。
パラメータの最適化
チャレンジ
異なる材料や厚さには、異なるレーザー出力、切断速度、ガス圧が必要です。パラメータ設定が不適切だと、バリが増えたり、切断幅が広すぎたり狭すぎたりするなど、切断品質が低下する可能性があります。
解決
- パワーと速度の正確な一致を確保するために、さまざまな材料の詳細な切断パラメータ テーブルを作成します。
- 安定したパワーとフォーカスを確保するために、機器のレーザー出力を定期的にテストしてください。
- 補助ソフトウェアを使用してパラメータを自動最適化し、切断効率と品質を向上させます。
オペレータートレーニング
チャレンジ
オペレーターの専門知識やスキルが不足していると、操作ミスが発生し、故障率が上昇し、切断効果に影響する可能性があります。
解決
- オペレーターに定期的に技術トレーニングを提供し、レーザー機器の操作仕様を習得できるようにします。
- 詳細な機器操作マニュアルを提供し、日常的な問題を解決するための技術サポート チームを設置します。
- 資格のある人だけが機器を操作できるように、オペレーター認証システムを導入します。
継続的な改善
チャレンジ
テクノロジーと市場の急速な変化により、企業は競争力を維持するために生産プロセスとテクノロジーを継続的に最適化する必要があります。
解決
- リーン生産コンセプトを導入し、生産プロセスを継続的に分析および最適化し、無駄を削減し、効率を向上させます。
- レーザー切断技術の開発動向を追跡し、機器とソフトウェアを迅速に更新します。
- 生産データを収集し、パフォーマンス指標を分析し、切断パラメータと操作手順を継続的に改善します。
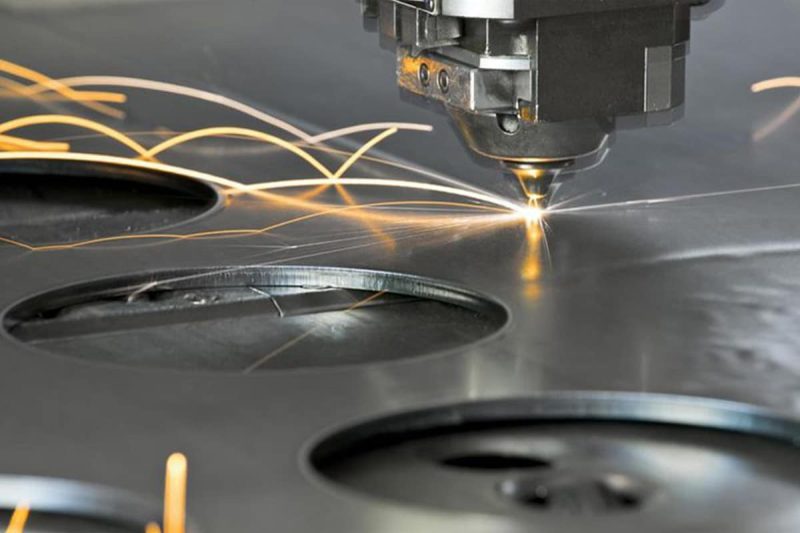
要約する
ファイバーレーザー切断の課題には、材料特性、機器の性能、環境条件など、多くの側面が関係します。定期的なメンテナンス、パラメータの最適化、トレーニングの強化、高度な技術の使用により、切断の品質と効率を大幅に向上できます。切断プロセスの安定性を向上させ、機械のダウンタイムとメンテナンスコストを削減するには、ケースバイケースでソリューションを実装する必要があります。
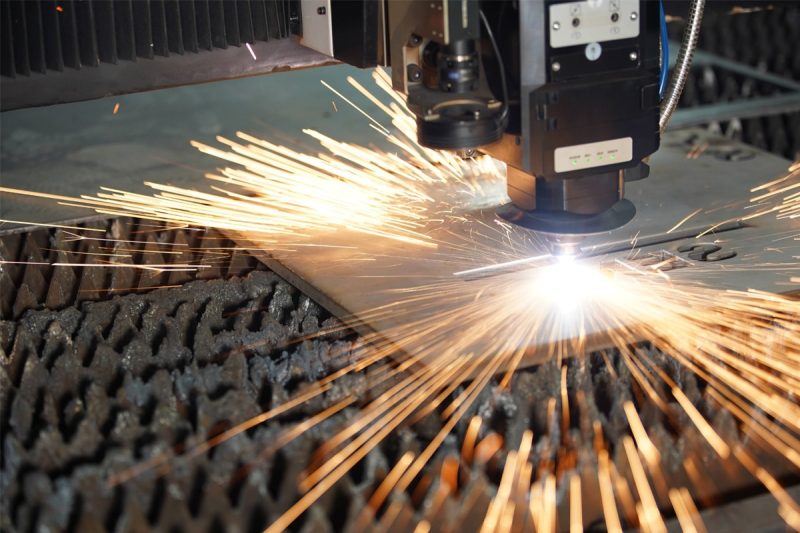
レーザー ソリューションを入手する
適切なファイバーレーザー切断機を選択すると、電力消費を最適化し、高い運用効率を実現できます。信頼できるサプライヤーと協力することで、高度なテクノロジー、カスタマイズされたアドバイス、継続的なサポートを利用できます。AccTek Laser では、さまざまな産業ニーズを満たすように設計された包括的なファイバーレーザー切断機機器を提供しています。当社の専門家は、材料の種類、厚さ、生産量などの要素を考慮して、最もエネルギー効率の高いモデルと構成を選択するお手伝いをします。また、高効率レーザージェネレーター、インテリジェント冷却システム、エネルギー管理ソフトウェアなどの最先端の機能を提供し、パフォーマンスを最大化し、エネルギー使用量を最小限に抑えます。さらに、当社のチームは定期的なメンテナンスサービスと技術サポートを提供し、機器を最高の効率に保ちます。当社と協力することで、大幅なエネルギー節約、運用コストの削減、持続可能性への取り組みの強化を実現できます。ご質問がある場合は、すぐにご連絡ください。AccTek Laser は、すべてのお客様に完璧なレーザーソリューションを提供することに尽力しています。
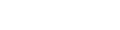
連絡先
- [email protected]
- [email protected]
- +86-19963414011
- No. 3 ゾーン A、Lunzhen 工業地帯、玉城市、山東省。
レーザー ソリューションを入手する