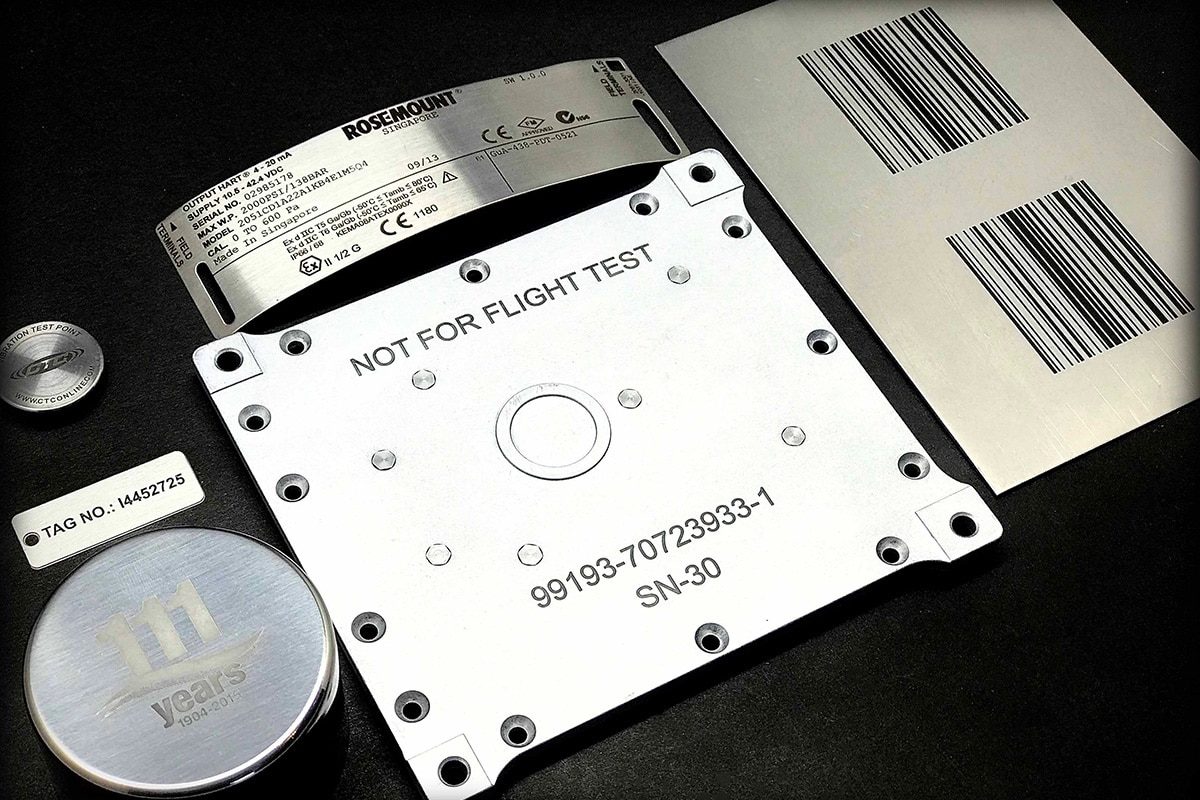
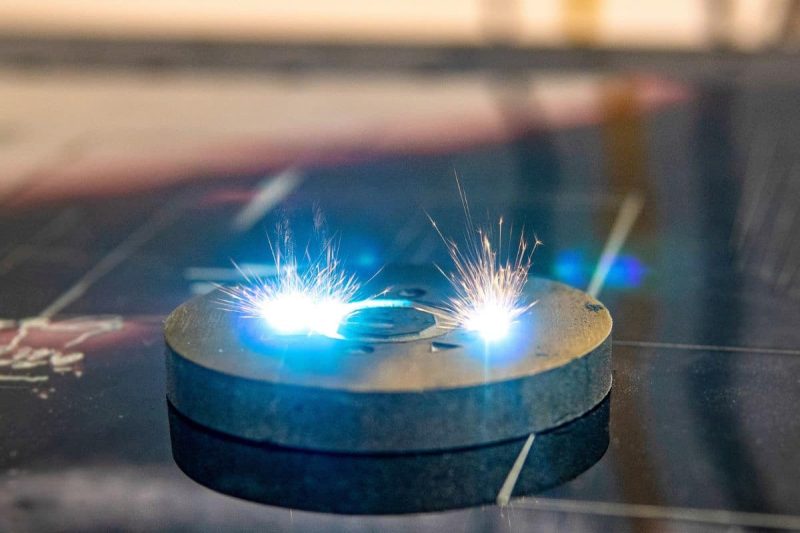
レーザーマーキングの基本
レーザーマーキングのプロセスとアプリケーション
レーザー マーキングは、さまざまな素材に永久的なマークを付けるために使用できる多目的な技術です。このプロセスでは、集中した光線を素材の表面に照射し、物理的または化学的変化を引き起こして目的のマークを作成します。レーザー マーキングには、次のようないくつかの種類があります。
- アニーリング: 主に金属に使用されるこのプロセスは、材料を加熱して、材料を除去することなくマークを作成します。
- エッチング/彫刻: 材料を除去して深みのあるマークを作成するもので、金属やプラスチックに適しています。
- アブレーション: このプロセスでは、材料の層を除去して、対照的な下層を露出させます。このプロセスは、陽極酸化アルミニウムによく使用されます。
- 発泡: 主にプラスチックに使用されるこのプロセスでは、材料内に泡が生成され、それが光を反射して盛り上がったマークが作成されます。
- 炭化: このプロセスは、炭素濃度を高めることによって材料を暗くするもので、木材や皮革などの有機材料によく使用されます。
マーキング能力に影響を与える主要なパラメータ
波長
レーザーの波長によって、さまざまな材料とどのように相互作用するかが決まります。
- ファイバーレーザー (約 1064 nm) は金属や一部のプラスチックに最適です。
- CO2 レーザー (~10.6 µm) は、木材、ガラス、プラスチックなどの非金属に効果的です。
- UV レーザー (約 355 nm) は、繊細で熱に敏感な材料に高精度でマーキングするのに優れています。
パルス持続時間
各レーザーパルスの持続時間はマーキングプロセスに影響します。
- 連続波 (CW) レーザーは、深い彫刻や切断に適した安定したビームを提供します。
- パルスレーザーは短いパルスでエネルギーを供給し、熱の影響を最小限に抑えて精度を高めます。細かい部分や敏感な材料に最適です。
力
レーザーのパワーは、マークの深さと速度に影響します。
- より高出力のレーザーにより、より深いマークとより速い処理時間が可能になります。
- 低出力レーザーは、材料の破壊を最小限に抑える必要がある繊細な用途に適しています。
フォーカスサイズ
レーザービームの焦点の大きさはマークの精度に影響します。
- スポットサイズが小さいほど、細かく詳細なマークを付けることができます。
- より広く、より詳細でないマークには、より大きなスポット サイズが使用されます。
ビーム品質
レーザー ビームの品質は、多くの場合、M² 係数によって定量化され、マークの精度と一貫性に影響します。
- M² 値が低いほどビーム品質が高くなり、より細かく一貫性のあるマークが得られます。
スキャン速度
レーザービームが材料を通過する速度は、マーキングの時間と品質に影響します。
- スキャン速度が速いほどマーキング効率は向上しますが、マークの深さと品質が低下する可能性があります。
- スキャン速度を遅くすると、より深く鮮明なマークを作成できます。
適切なレーザータイプを選択することの重要性
特定のマーキング アプリケーションに適したレーザー タイプを選択すると、最良の結果を得ることができます。適切なレーザーは、高品質のマーキング、効率、およびコスト効率を保証します。適切なレーザー タイプを選択することが重要な理由は次のとおりです。
- 材料の適合性: レーザーの種類によって、材料に対する相互作用が異なります。ファイバー レーザーは金属に最適で、CO2 レーザーは非金属に優れ、UV レーザーは敏感な材料に最適です。間違った種類のレーザーを使用すると、マーキング品質が低下したり、材料が損傷したり、効率が悪くなる可能性があります。
- マーキング精度: 電子機器や医療機器など、細部まで精密にマークする必要があるアプリケーションでは、スポットサイズが小さくビーム品質の高い UV レーザーやファイバー レーザーが役立ちます。一方、CO2 レーザーは、木材やガラスなどの素材に、幅が広く細部まであまり精密でないマークを付けるのに適しています。
- 効率と速度: 生産速度と効率は、産業用途では非常に重要です。ファイバー レーザーは高速マーキング機能で知られており、高スループット環境に最適です。一方、CO2 レーザーは、非金属材料に対して速度と汎用性のバランスを提供します。
- 熱の影響: 電子機器や医療機器のマーキングなどの繊細な用途では、材料の損傷を防ぐために熱の影響が最小限のレーザーが必要です。UV レーザーとそのコールド マーキング プロセスは、これらの用途に最適です。
- コストの考慮: レーザーの種類によって、初期投資と運用コストは異なります。ファイバー レーザー マーキング マシンは初期コストが高くなりますが、寿命が長くメンテナンス コストが低いため、長期的にはコストを節約できます。 CO2レーザーマーキングマシン 初期コストは低くなりますが、より頻繁なメンテナンスが必要になる場合があります。
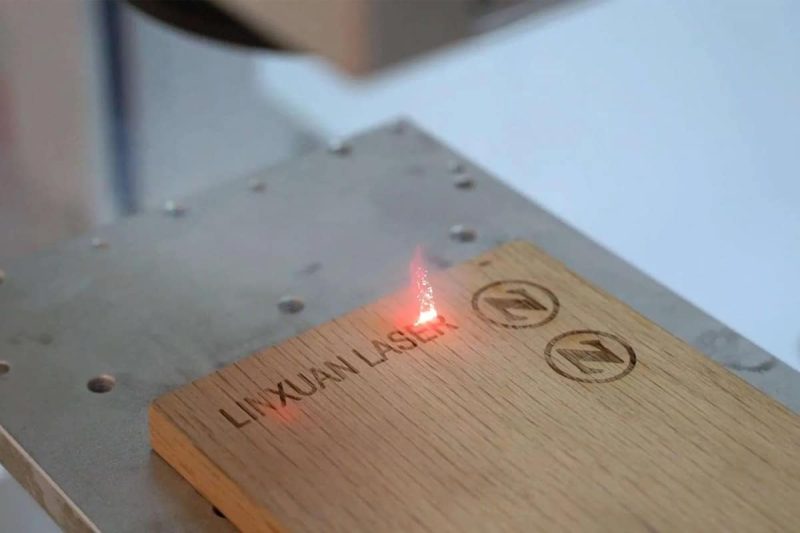
レーザーマーキングで使用されるレーザーの種類
ファイバーレーザー
特徴
- 波長:約1064 nm(近赤外線)。
- ゲイン媒体: イッテルビウム、エルビウム、ネオジムなどの希土類元素がドープされたファイバー。
- レーザータイプ: パルス波または連続波。
- 電力範囲: 通常、数ワットから数百ワットまで。
- 動作: 高品質のビーム、連続波、パルス モード。
パフォーマンス
- 材料の互換性: 金属 (ステンレス鋼、アルミニウム、金、銀)、特定のプラスチック、セラミックに最適です。
- 深さと精度: 高精度で細部まで精細に彫刻でき、金属に深く彫刻できます。
- 速度: 高スループット環境向けの高速マーキング機能。
- ビーム品質: 細かく詳細なマーキングに最適なビーム品質。
アプリケーション
- 電子機器: 回路基板、マイクロチップ、その他の電子部品のマーキング。
- ジュエリーと時計: 貴金属に複雑な模様を彫刻します。
- 自動車: 部品やコンポーネントにシリアル番号とバーコードをマークします。
- 医療機器: 外科用器具や医療用インプラントに正確で永続的なマークを作成します。
利点
- 高精度と高品質: 高精度で細かいマークを生成します。
- スピードと効率: 素早くマーキングでき、大量生産に最適です。
- 耐久性と寿命: メンテナンスが最小限で、通常 100,000 時間を超える長寿命。
- エネルギー効率: 他のタイプのレーザーよりもエネルギー効率が高く、運用コストを削減します。
- 汎用性: 幅広い材料、特に金属にマーキングできます。
制限事項
- 材料の制限: 木材、ガラス、一部のプラスチックなどの非金属材料では効果が低くなります。
- 初期コスト: 初期投資は高くなりますが、長期的な運用コストは低くなります。
- 複雑さ: より複雑なテクノロジーであり、操作と保守には専門知識が必要です。
- 冷却要件: 動作中に発生する熱を管理するために、適切な冷却システムが必要になる場合があります。
CO2レーザー
特徴
- 波長:約10.6µm(遠赤外線)。
- ゲイン媒体: ガス混合物 (CO2、窒素、ヘリウム)。
- レーザータイプ: 連続波またはパルス。
- 電力範囲: 通常、10 ワットから数百ワットの範囲です。
- 動作: 高効率、連続波、パルスモード。
パフォーマンス
- 材質の適合性: 木材、ガラス、プラスチック、布地、皮革、セラミックなどの非金属に最適です。特殊なコーティングを施していない限り、金属への効果は限られます。
- マーキング速度: 材質と希望する深さに応じて中程度。
- 深さと精度: 非金属への深い彫刻と高コントラストのマーキングが可能です。
- ビーム品質: 正確なマーキングのための優れたビーム品質を提供します。
アプリケーション
- 標識と広告: アクリル、木材、その他の素材を使用して複雑な標識を作成します。
- 梱包: 段ボールやプラスチックなどの梱包材に印を付け、切り取ります。
- 織物と布地: 布地と革に模様を彫刻し、切り取ります。
- ガラスと陶器: ガラス瓶、窓、陶器製品にデザインやメッセージを彫刻します。
利点
- 幅広い材料互換性: 幅広い非金属材料で動作します。
- コスト効率: ファイバーレーザーや UV レーザーよりも手頃な価格で、さまざまな用途に使用できます。
- 柔軟性: 切断、彫刻、マーキングなど、複数のタスクを実行できます。
- マーキングの深さ: 深い彫刻や大量の材料除去を必要とする用途に適しています。
制限事項
- 金属に対する精度が低い: 金属に対しては効果が低いため、特殊なコーティングや添加剤が必要になります。
- メンテナンス要件: ファイバーレーザーよりも頻繁なメンテナンスと部品交換が必要です。
- 材質の適合性: 木材、ガラス、プラスチック、布地、皮革、セラミックなどの非金属に最適です。特殊なコーティングを施していない限り、金属への効果は限られます。
- マーキング速度: 材質と希望する深さに応じて中程度。
- 深さと精度: 非金属への深い彫刻と高コントラストのマーキングが可能です。
- ビーム品質: 正確なマーキングのための優れたビーム品質を提供します。
UVレーザー
特徴
- 波長:約355 nm(紫外線)。
- ゲイン媒体: 周波数の 3 倍化を利用するソリッド ステートまたはガス システム。
- レーザータイプ: パルス。
- 電力範囲: 通常、数ミリワットから数ワットの範囲です。
- 動作: 短いパルス持続時間で高精度。
パフォーマンス
- 材料の適合性: プラスチック、ガラス、セラミック、金属など、幅広い材料に適しています。
- 深さと精度: 熱の影響を最小限に抑えた超微細マーキングと高コントラストのマーキング。
- 速度: ファイバーレーザーに比べてマーキング速度は遅いですが、精度は高くなります。
- ビーム品質: 細かく詳細なマーキングに最適なビーム品質。
アプリケーション
- 医療および医薬品: 医療機器、器具、パッケージに高精度かつ高コントラストでマーキングします。
- エレクトロニクス:精密電子部品およびマイクロチップの彫刻。
- 航空宇宙: 航空宇宙部品に使用される敏感な材料のマーキング。
- 消費財: ガラス製品、化粧品、その他の消費財に高品質のマークを作成します。
利点
- 精度: 熱の影響を最小限に抑えた超微細マーキング。
- 材料の適合性: 敏感な材料を含む、幅広い材料のマーキング。
- コントラストと品質: 高いコントラストと高品質のマーキングを提供します。
- コールドマーキングプロセス: 熱影響部を減らし、材料の損傷を最小限に抑えます。
- 非破壊: 熱の影響を最小限に抑え、材料の変形が不要なアプリケーションに最適です。
制限事項
- 低電力: 通常は出力が低いため、深い彫刻や高速マーキングには適していません。
- コストが高い: 初期投資とメンテナンスのコストが高くなります。
- 入手の制限: UV レーザー マーキング マシンを製造しているメーカーが少ないため、入手が制限され、部品や修理のリード タイムが長くなる可能性があります。
- 寿命が短い: UV レーザーの寿命はファイバー レーザーよりも短い場合があります。
- 速度: マーキング速度は他のタイプのレーザーに比べて遅くなります。
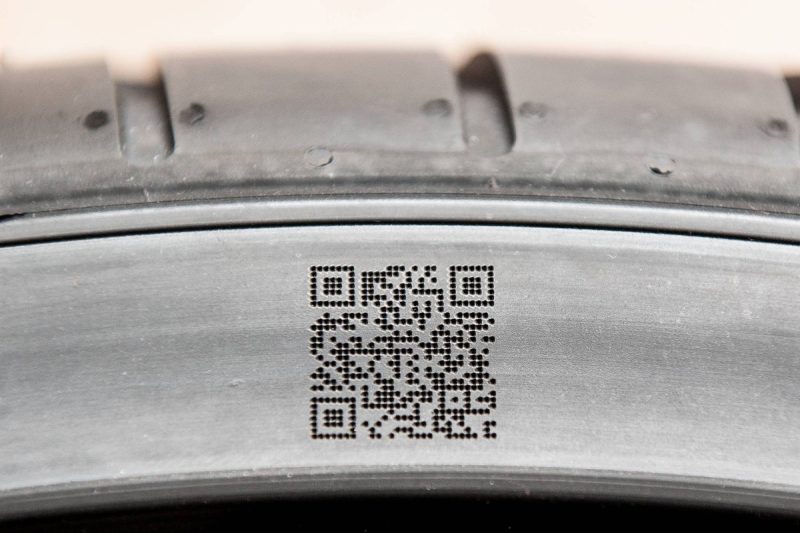
レーザーマーキングにおけるレーザータイプの比較
マーキングのスピードと効率
ファイバーレーザー
- 速度: ファイバー レーザーは高速マーキング機能で知られています。高速マーキング速度を実現できるため、高スループットの生産環境に適しています。
- 効率: ファイバー レーザーはエネルギー効率に優れており、入力エネルギーの大部分を使用可能なレーザー光に変換します。これにより、運用コストとエネルギー消費を削減できます。
CO2レーザー
- 速度: CO2 レーザーは中程度のマーキング速度を提供します。ファイバー レーザーほど高速ではありませんが、多くの産業用途、特に非金属材料を扱う用途には十分です。
- 効率: CO2 レーザーは、ガス媒体の性質上、一般にファイバー レーザーよりも効率が低くなりますが、それでも多くの用途で妥当な効率を提供します。
UVレーザー
- 速度: UV レーザーはファイバー レーザーよりもマーキングが遅くなります。速度は、高精度と最小限の熱効果の必要性によって制限されます。
- 効率: UV レーザーは出力が低いため、エネルギー使用の面では効率が低くなりますが、速度がそれほど重要でない精密アプリケーションでは優れています。
マーキングの精度と品質
ファイバーレーザー
- 精度: ファイバーレーザーは高精度で細かいディテールを実現できるため、金属や一部のプラスチックへの複雑なマーキングに適しています。
- 品質: マーキング品質は優れており、シャープな線、最小限の熱歪み、幅広い材料に対する一貫した結果が得られます。
CO2レーザー
- 精度: CO2 レーザーは非金属材料に対しては優れた精度を発揮しますが、特殊なコーティングが施されていない金属に対しては精度が低くなります。
- 品質: 非金属へのマーキング品質は高く、深く目立つ彫刻を作成できます。
UVレーザー
- 精度: UV レーザーは波長が短く、熱の影響が最小限であるため、3 つのレーザーの中で最も精度が高く、非常に細かいマークを作成できます。
- 品質: UV レーザー マーキングの品質は優れており、コントラストと鮮明度が高くなっています。コールド マーキング プロセスにより、材料へのダメージが最小限に抑えられます。
多用途性とさまざまな素材との互換性
ファイバーレーザー
- 汎用性: ファイバーレーザーは非常に汎用性が高く、金属、プラスチック、セラミックなど、さまざまな材料にマーキングできます。
- 互換性: ステンレス鋼、アルミニウム、金、銀などの金属や、工業用途で使用される特定のプラスチックのマーキングに優れています。
CO2レーザー
- 汎用性: CO2 レーザーも非常に汎用性がありますが、非金属材料に重点を置いています。さまざまな物質にマーキング、彫刻、切断を行うことができます。
- 適合性: 木材、ガラス、アクリル、プラスチック、布地、皮革、セラミックには特に効果的ですが、特別な処理を施さない限り金属には効果が低くなります。
UVレーザー
- 汎用性: UV レーザーは非常に汎用性が高く、繊細な材料の高精度加工を必要とする用途に特に役立ちます。
- 互換性: プラスチック、ガラス、セラミック、金属など、さまざまな材料にマーキングできます。UV レーザーは、熱の影響を最小限に抑える必要がある敏感な材料に最適です。
コスト効率とメンテナンスの考慮
ファイバーレーザー
- コスト効率: ファイバー レーザー マーキング システムへの初期投資は高額になる可能性がありますが、寿命が長く、メンテナンスの必要性が低いため、長期的にはコスト効率が高くなります。
- メンテナンス: ファイバー レーザーはメンテナンスの必要性が最小限で、通常はダウンタイムを最小限に抑えながら 100,000 時間以上稼働します。これにより、メンテナンス コストと生産中断が削減されます。
CO2レーザー
- コスト効率: CO2 レーザー マーキング マシンは、一般的に初期費用は安価ですが、頻繁なメンテナンスや部品交換により、長期的にはコストが高くなる可能性があります。
- メンテナンス: ガスの補充やミラーの交換など、定期的なメンテナンスが必要であり、時間の経過とともに運用コストが増加する可能性があります。
UVレーザー
- コスト効率: UV レーザー マーキング マシンは、特殊な技術と低い出力のため、初期コストと運用コストが最も高くなります。
- メンテナンス:より頻繁なメンテナンスが必要で、寿命は ファイバーレーザーマーキングマシン ただし、超高精度のマークを作成できる能力は、精度が重要となるアプリケーションでは、より高いコストを正当化します。
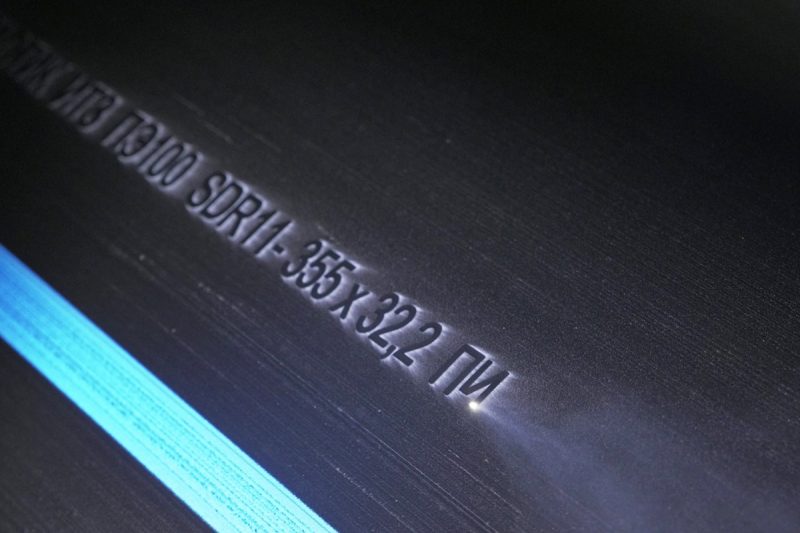
レーザータイプの選択に影響する要因
材料の種類と特性
マーキングする材料の種類は、適切なレーザーの種類を選択する上で最も重要な要素の 1 つです。さまざまなレーザーがさまざまな方法で材料と相互作用し、マーキング プロセスの品質と効率に影響を与えます。
- ファイバーレーザー: 金属 (鋼鉄、アルミニウム、銅、真鍮) および一部のプラスチック用。ファイバーレーザーは、エネルギー密度が高く波長が短いため、硬い材料に優れたマーキング品質を提供します。
- CO2 レーザー: 木材、ガラス、セラミック、プラスチック、皮革、繊維などの非金属材料用。CO2 レーザーはこれらの材料がよく吸収する長い波長を持っているため、有機材料の切断や彫刻に最適です。
- UV レーザー: 熱影響部を最小限に抑えた、細かく詳細なマーキングが必要な材料に適しています。特に、高精度と熱影響の最小化が求められる用途で、ガラス、セラミック、プラスチック、一部の金属のマーキングに最適です。
マーキング要件
深さ、コントラスト、解像度、耐久性などの特定のマーキング要件も、レーザー タイプの選択に影響します。
- ファイバーレーザー: 高いコントラスト、耐摩耗性、耐腐食性を備えた永久マーキングを提供します。高い鮮明度が求められるバーコード、シリアル番号、ロゴに最適です。
- CO2 レーザー: 特に深さと質感が重要な場合に、幅広い材料にマーキングできる柔軟性を提供します。複雑なデザインを必要とする彫刻や切断の用途でよく使用されます。
- UV レーザー: 熱の影響を最小限に抑えながら高精度のマークを生成します。電子機器や医療機器など、繊細な素材や細かいディテールが求められる用途に最適です。
スループットと速度の要件
スループットと速度の要件によって、特定のアプリケーションに対する特定のレーザー タイプの効率と適合性が決まります。
- ファイバーレーザー: マーキング速度と効率が高いことで知られており、大量生産環境に適しています。高速でも高品質を維持できるため、自動車や航空宇宙などの業界でメリットがあります。
- CO2 レーザー: 多用途ですが、特定の大量生産アプリケーションではファイバー レーザーの速度に匹敵しない場合があります。ただし、非金属材料の切断や彫刻が必要なアプリケーションでは優れています。
- UV レーザー: 通常はファイバー レーザーや CO2 レーザーよりも低速ですが、比類のない精度を提供します。電子機器や医療業界など、速度よりも品質と詳細が重要となるアプリケーションに最適です。
生産環境と制限
選択したレーザー タイプが最適に機能することを保証するには、動作環境と潜在的な制限を考慮する必要があります。
- ファイバーレーザー: 一般的に頑丈で、メンテナンスの必要性が少なく、過酷な産業環境に適しています。コンパクトな設計で、さまざまな生産ラインに統合できます。
- CO2 レーザー: 汚染物質がレーザー光学系に影響を与えないように、クリーンな環境が必要です。レーザー チューブと関連機器のサイズが大きいため、より多くのスペースが必要になる場合があります。
- UV レーザー: 環境条件に敏感で、最適なパフォーマンスを得るにはクリーンルーム環境が必要です。精度が高いため、半導体製造などの制御された環境での用途に最適です。
予算の制限とコストの考慮
適切なレーザーの種類を選択する上で、コストは常に重要な要素です。これには初期投資、運用コスト、メンテナンスが含まれます。
- ファイバーレーザー: 一般的に初期コストは高くなりますが、エネルギー効率が高く耐用年数が長いため運用コストは低くなります。大量生産のアプリケーションでは投資収益率が高くなります。
- CO2 レーザー: 一般的に、特に低出力システムの場合、初期費用は比較的安価です。ただし、補給ガスと頻繁なメンテナンスが必要なため、運用コストとメンテナンス コストが高くなる可能性があります。
- UV レーザー: 複雑さと精度のため、一般的に最も高価です。精度と材料への影響を最小限に抑えることが重要な特殊な用途では、コスト効率に優れています。
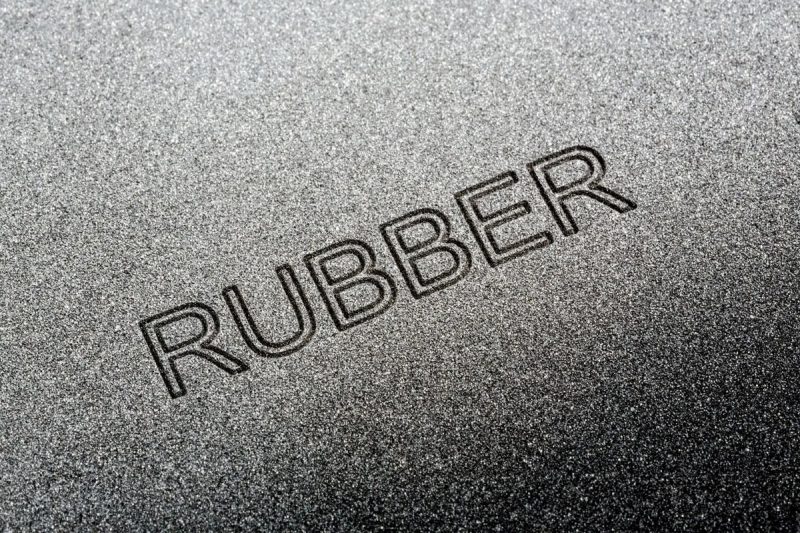
適切なレーザータイプを選択するためのベストプラクティス
材料の適合性とマーキング要件を評価する
適切なレーザー タイプを選択するための最初のステップは、使用する材料と特定のマーキング要件を評価することです。
- 材料の適合性: マーキングする材料の種類を決定します。ファイバー レーザーは金属や特定のプラスチックに適しており、CO2 レーザーは木材やガラスなどの非金属に適しており、UV レーザーは繊細で敏感な材料に最適です。サンプル材料をテストして、各レーザー タイプが材料とどのように相互作用するかを観察します。
- マーキング要件: 深さ、コントラスト、解像度、耐久性などのマーキング仕様を定義します。たとえば、繊細な表面に高コントラストの詳細なマーキングが必要な場合は、UV レーザーが適しています。金属に深く永久的なマーキングをする場合は、ファイバー レーザーが最適です。大量生産が必要な場合は、マーキング速度を考慮してください。
レーザーメーカーや専門家に相談する
レーザーメーカーや業界の専門家の知識と経験を活用することで、貴重な洞察が得られます。
- メーカーへの相談: レーザー メーカーに連絡して、具体的なニーズについてご相談ください。メーカーは、さまざまなタイプのレーザーの機能に関する詳細な情報を提供し、材料やマーキングの要件に基づいて最適なオプションを推奨します。
- 専門家のアドバイス: さまざまなレーザー マーキング アプリケーションの経験を持つ業界の専門家に相談してください。彼らは、実際のアプリケーションとパフォーマンスに基づいて実用的な洞察と推奨事項を提供できます。
長期的な運用コストとメンテナンス要件を考慮する
コスト効率を確保するには、レーザー システムの長期的な運用コストとメンテナンス要件を考慮することが重要です。
- 初期コストと運用コスト: ファイバー レーザーは初期コストが高くなる場合がありますが、耐久性がありメンテナンスの必要性が最小限であるため、一般的に長期的な運用コストは低くなります。CO2 レーザーでは、より頻繁なメンテナンスと消耗品の交換が必要になる場合があり、全体的なコストに影響する可能性があります。
- メンテナンス要件: 各レーザー タイプのメンテナンス スケジュールと要件を評価します。ダウンタイムを回避し、一貫したパフォーマンスを確保するために、定期的なメンテナンスを実行するために必要なリソースと機能があることを確認します。
- エネルギー効率: 各レーザー タイプのエネルギー消費量を考慮してください。これは、長期にわたって運用コストに大きな影響を与える可能性があります。
マーキングプロセスを定期的に評価し、最適化する
マーキング プロセスを継続的に評価および最適化することで、効率が向上し、より良い結果が得られます。
- プロセス評価: レーザー マーキング システムのパフォーマンスを定期的に評価します。マーキング速度、品質、一貫性などのパラメータを監視して、改善の余地がある領域を特定します。
- 最適化戦略: 評価に基づいて最適化戦略を実行します。これには、レーザー設定の調整、コンポーネントのアップグレード、さらにはマーキングの改善が必要な場合は別のタイプのレーザーへの切り替えなどが含まれる場合があります。
- トレーニングと開発: チームがレーザー システムの操作と保守について十分にトレーニングされていることを確認します。定期的なトレーニング セッションにより、全員がベスト プラクティスと新しいテクニックを常に把握し、機器をより効果的に使用できるようになります。
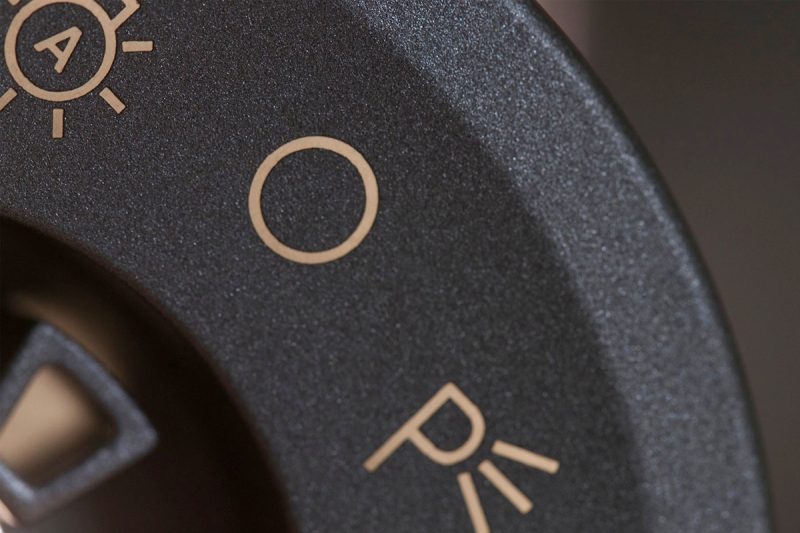
まとめ
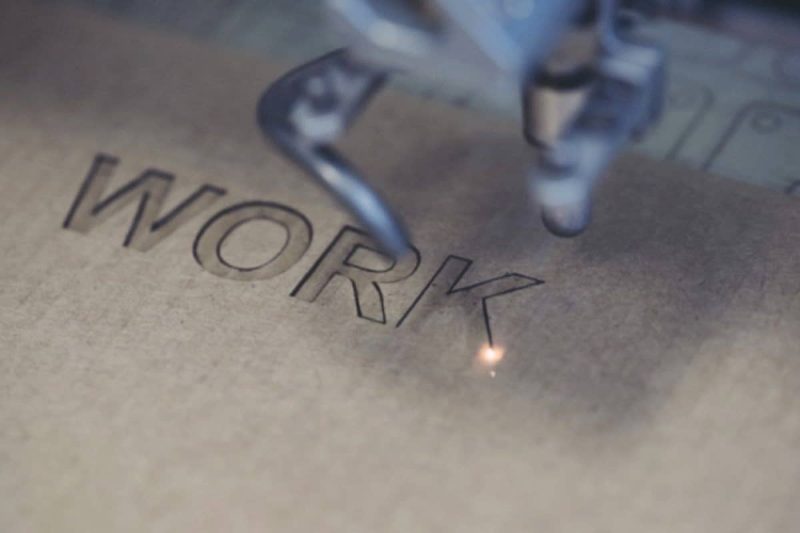
レーザーマーキングソリューションを入手
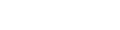
- [email protected]
- [email protected]
- +86-19963414011
- No. 3 ゾーン A、Lunzhen 工業地帯、玉城市、山東省。