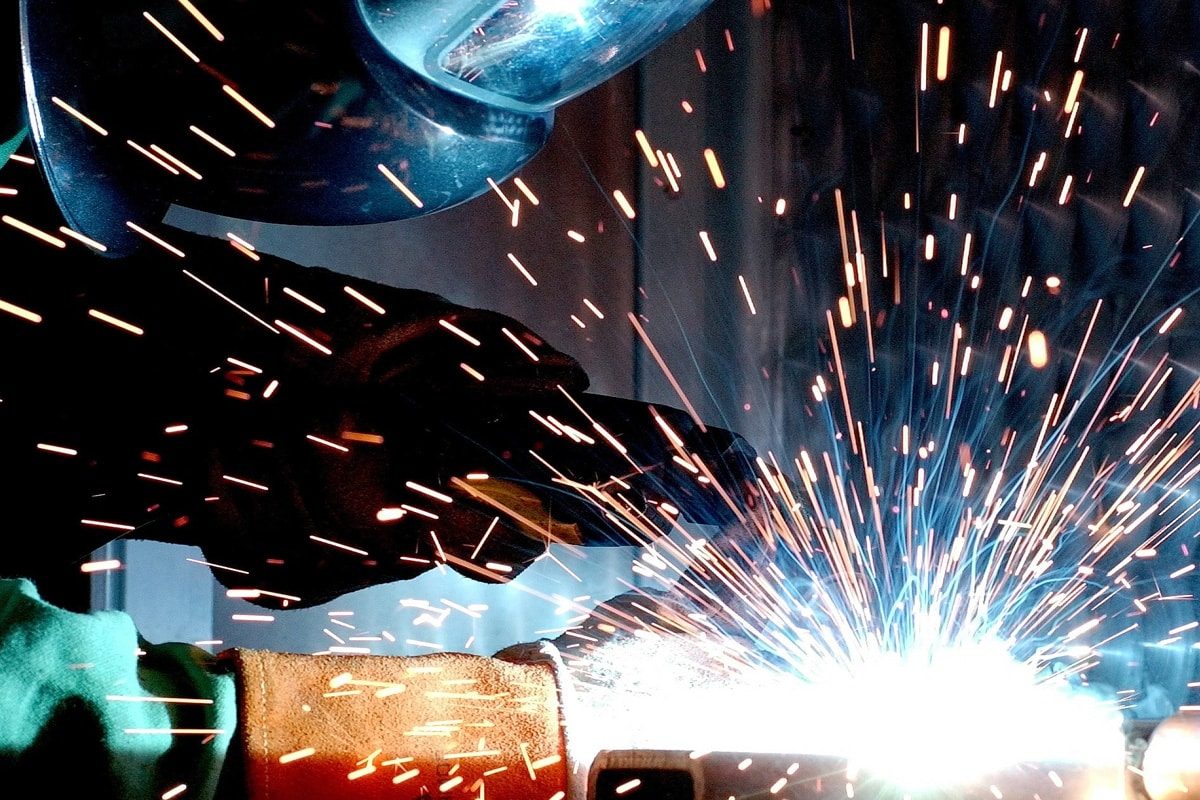
レーザービームの焦点は溶接の品質にどのように影響しますか?
レーザー溶接は、現代の製造業において、非常に正確で効果的なプロセスとなっています。自動車製造、航空宇宙、電子機器製造、医療機器産業など、レーザー溶接は、その高効率、低入熱、優れた溶接品質のため、広く使用されています。ただし、レーザー溶接の品質は、レーザービームの焦点に大きく左右されます。レーザービームの焦点は、レーザー溶接プロセスの効率と有効性に直接影響する重要な要素です。レーザー溶接では、ビームの焦点とは、レーザーエネルギーが最も集中する正確なポイントを指し、焦点は最高の溶接品質を実現するために重要です。焦点を慎重に制御することで、メーカーは、十分な溶け込みの確保、欠陥の最小化、一貫した溶接の実現など、特定の要件を満たすように溶接プロセスを調整できます。レーザービームの焦点合わせのニュアンスを理解することで、入熱、溶接プールのダイナミクス、および全体的なプロセス安定性をより適切に制御できます。これにより、精度が向上し、材料の無駄が削減され、溶接部品の構造的完全性が向上します。産業界がレーザー溶接の精度と効率にますます依存するようになるにつれ、さまざまな用途で高品質の溶接を実現するには、レーザービーム集束技術を習得することが不可欠になります。
目次
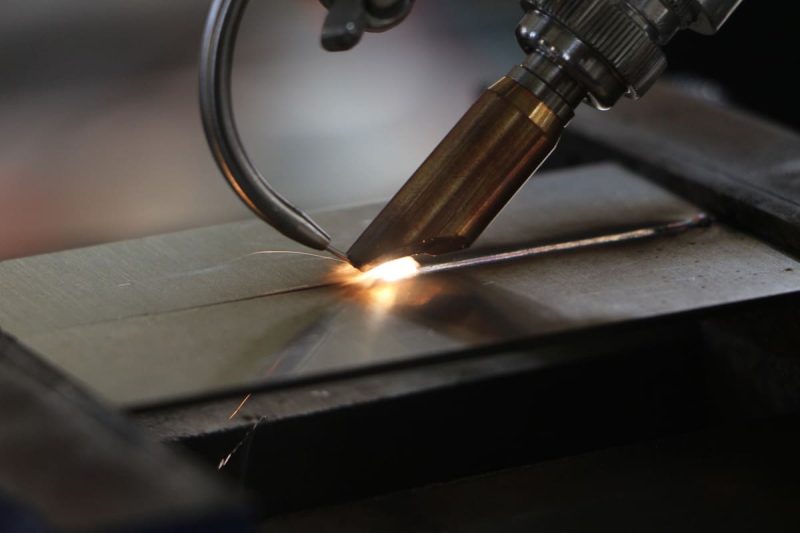
レーザービームの焦点合わせを理解する
レーザービームの焦点と溶接におけるその役割の説明
レーザー ビームの焦点とは、レーザー ビームが最小直径に焦点を合わせられる空間上の点を指します。この焦点は、ワークピース上のレーザー エネルギーの分布を決定するため、レーザー溶接プロセスにおいて重要なパラメータです。レーザー ビームのエネルギー密度は、焦点を合わせた後に最も高くなります。つまり、焦点では、レーザーのパワーが非常に狭い領域に集中し、非常に高い温度になります。この高い温度により、材料は短時間で急速に溶解して融合し、強力な溶接部を形成できます。
実際の作業では、レーザービームの焦点位置は通常、特定の溶接ニーズに応じて調整されます。焦点がワークピースの表面にある場合、レーザーエネルギーは主に材料の表面に集中するため、通常は薄い材料の溶接に適しており、高精度の溶接効果を実現できます。焦点がワークピースの内部にある場合、レーザービームは材料の表面を貫通し、材料の奥深くまで浸透して、より深い溶接を実現できます。これは、厚いワークピースや高強度の接合部を必要とするアプリケーションにとって特に重要です。
また、レーザービームの焦点の位置は、溶接の深さだけでなく、溶接の幅、熱影響部のサイズ、溶接速度にも影響します。適切な焦点設定により、溶接強度を確保しながら、気孔、亀裂、不完全な溶け込みなどの溶接欠陥を減らすことができます。逆に、焦点位置が正しくなく、レーザーエネルギーが不均一に分散されている場合は、溶接品質の低下、溶け込みの浅さ、過熱、または溶接結果の一貫性の欠如につながる可能性があります。
現代のレーザー溶接システムでは、焦点位置の正確な制御が溶接品質を向上させる重要な手段の 1 つになっています。たとえば、適応光学技術は、溶接プロセス中にレーザービームの焦点をリアルタイムで調整して、ワークピースの形状と材料特性に適応させ、レーザーエネルギーが常に最も必要な部分に集中するようにします。さらに、ビーム解析技術により、レーザービームの焦点特性を詳細に解析して、溶接パラメータをさらに最適化し、溶接の安定性と一貫性を向上させることができます。一般に、レーザービームの焦点は溶接プロセスで重要な役割を果たします。焦点位置を正確に制御することで、溶接品質を効果的に向上させ、さまざまな複雑なアプリケーションのニーズを満たすことができます。自動車、航空宇宙、電子機器製造のいずれの場合でも、正しい焦点設定が高品質の溶接を実現するための鍵となります。
焦点サイズと溶接品質の関係
焦点サイズとは、焦点におけるレーザー ビームの直径を指し、通常はミクロン単位で測定されます。焦点のサイズは、レーザー エネルギーの分布と溶接の最終的な効果に直接影響します。レーザー溶接では、焦点サイズが小さいほど、レーザー エネルギーがより集中し、単位面積あたりのエネルギー密度が高くなります。この高いエネルギー密度により、材料が急速に溶解し、溶接の浸透が増加するため、より深い溶接が可能になります。これは、厚板溶接や重要な構造部品の溶接など、高い強度と溶接の深さを必要とする用途で大きな利点となります。
ただし、焦点サイズが小さすぎると、限界もあります。エネルギーが非常に集中するため、溶接の幅が非常に狭くなる可能性があり、より広い溶接を必要とする一部のアプリケーションには適さない場合があります。さらに、焦点サイズが小さすぎると、溶接プロセス中の不安定性が増し、特に処理対象材料の表面が不均一であったり不純物が含まれていたりする場合に、溶接品質が一定しなくなる可能性があります。
一方、焦点サイズが大きいと、レーザーエネルギーがより広い領域に分散され、単位面積あたりのエネルギー密度が低下します。これにより溶接の浸透深さが減少する可能性がありますが、表面接合やシール溶接など、より広い溶接ビードを必要とする用途では、焦点サイズが大きい方が適しています。この場合、溶接の深さは減少する可能性がありますが、溶接の範囲は広くなり、材料の表面接続の完全性が確保されます。
したがって、焦点サイズの選択は溶接品質と密接に関係しており、特定の溶接ニーズに応じて最適化する必要があります。実際のアプリケーションでは、溶接エンジニアは、ワークピースの材質、厚さ、形状、溶接要件に基づいて適切な焦点サイズを選択し、溶接幅、深さ、強度の最適なバランスを実現する必要があります。適切な焦点サイズの設定により、溶接の安定性が向上し、欠陥が削減され、最終的に溶接の全体的な品質が向上します。
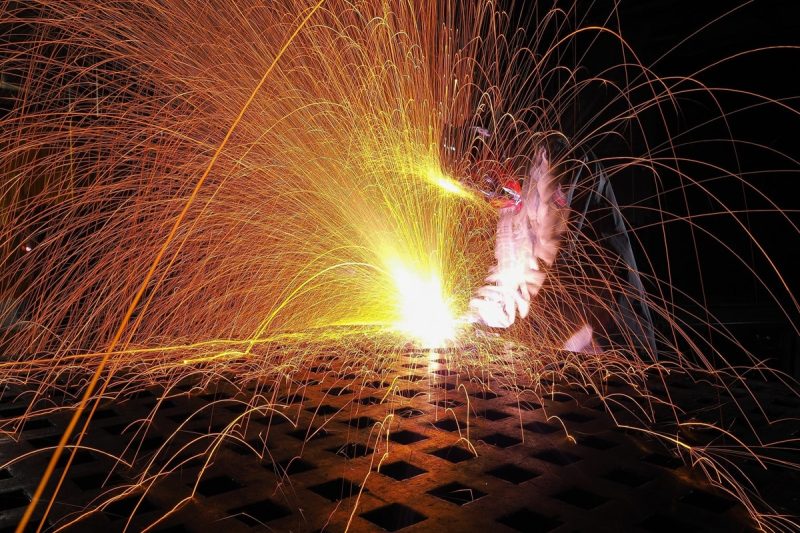
レーザービームの焦点に影響を与える要因
レーザービームの焦点合わせはレーザー溶接の重要なステップであり、溶接の効果と品質を直接決定します。レーザービームの焦点合わせに影響を与える要因には、レンズの選択、ビーム径、焦点距離、ビーム品質などがあります。これらの要因を正しく理解して最適化することで、溶接のパフォーマンスと精度を効果的に向上させることができます。
レンズの選択
レンズはレーザービームの集束プロセスにおいて重要な役割を果たし、ビームの収束能力に影響を与える主要なコンポーネントです。レンズの設計と材料が異なると、レーザービームの集束性能に大きな影響を与えます。たとえば、焦点距離の短いレンズはレーザービームをすばやく集束できるため、焦点スポットのサイズが小さくなります。この高エネルギー密度の集束は、マイクロエレクトロニクス部品の溶接や高精度の薄板溶接など、細かい制御が必要な溶接作業に適しています。これらのアプリケーションでは、焦点が小さいほど溶接精度が高くなり、溶接幅が狭くなります。
ただし、短焦点レンズの欠点は、浸透能力が限られているため、厚い材料や深い溶接作業には適していないことです。このタイプの用途には、より長い焦点距離のレンズの方が適しています。長い焦点距離のレンズは、レーザービームをより深く焦点合わせし、より大きな焦点スポットサイズとより長い焦点深度を生み出し、それによって溶接深度を増加させます。このレンズは、厚板溶接や重工業の構造部品など、深い浸透を必要とする溶接作業によく使用されます。
さらに、レンズの材質もレーザービームの伝送効率と焦点品質に影響を与えます。高品質のレンズ材質は、レンズを通過する際のレーザーのエネルギー損失を減らし、レーザービームの焦点がより鮮明で安定していることを保証します。適切なレンズ材質と設計を選択することは、レーザービームの焦点を最適化するための第一歩であり、溶接品質に直接関係しています。
ビーム径
レーザー ビーム径は、焦点を合わせるのに影響を及ぼすもう 1 つの重要な要素です。これは、焦点を合わせていないときのレーザー ビームの幅を指します。ビーム径のサイズによって、焦点を合わせた後のレーザー ビームの焦点サイズが決まります。ビーム径が大きいほど、通常は焦点サイズも大きくなり、より広い溶接を必要とする用途に適しています。たとえば、広い接触領域をカバーしたり、表面接続を作成したりする必要がある溶接作業では、焦点サイズが大きいほど、材料の安定した接続を確保するのに十分な範囲をカバーできます。
逆に、ビーム径が小さいほど焦点も小さくなり、エネルギー密度と溶接精度が高くなります。これは、マイクロ溶接や精密機械加工など、細かい制御が必要な溶接作業では特に重要です。溶接エンジニアはビーム径を調整することで、焦点サイズと溶接精度の最適なバランスを見つけ、溶接品質を最適化できます。
焦点距離
焦点距離とは、レンズからレーザー ビームの焦点までの距離を指し、レーザー ビームの集束能力を決定する重要なパラメータです。焦点距離の選択は、焦点のサイズとビームの集束深度に直接影響します。焦点距離の短いレンズを使用すると、レーザー ビームをより短い距離に素早く集束でき、焦点サイズが小さくなります。この構成は一般にエネルギー密度が高く、レーザーが材料を素早く溶かすことができるため、高精度で高速な溶接を必要とする用途に適しています。
ただし、焦点距離が短いと、焦点が材料の表面または表面近くに集中するため、溶接の深さが制限され、深い溶け込みを実現するのが難しくなります。より深い溶接が必要な作業には、焦点距離の長いレンズの方が適しています。焦点距離の長いレンズは、レーザービームをより長い距離に焦点を合わせることができ、焦点サイズが大きくなって、より深い溶け込みが可能になります。ただし、この場合、エネルギー密度が低下し、溶接精度にも影響が出る可能性があります。したがって、溶け込みと溶接精度の最適なバランスを実現するには、特定の溶接ニーズに応じて焦点距離を選択する必要があります。
ビーム品質
ビーム品質は、レーザー ビームの集束能力の重要な指標である M² 係数で表現されることがよくあります。M² 係数が 1 に近いほど、ビーム品質は向上し、レーザー ビームをより適切に集束して、より小さく集中した焦点を作成できます。高品質のビームは、エネルギー密度が高く、より正確な制御が可能であることを意味し、高精度部品の溶接や複雑な形状のワークピースの溶接など、要求の厳しい溶接作業に適しています。
逆に、ビーム品質の悪いレーザー ビームは焦点が大きくなり、エネルギー分布が不均一になるため、溶接の精度と品質が低下します。溶接が不均一に見え、気孔、亀裂、溶接不良などの欠陥が生じることもあります。したがって、ビーム品質を改善することは、溶接品質を改善するための重要な手段です。レーザー ジェネレータの設計を最適化し、高品質の光学系を使用することで、溶接エンジニアはビーム品質を大幅に改善し、溶接の信頼性と一貫性を高めることができます。
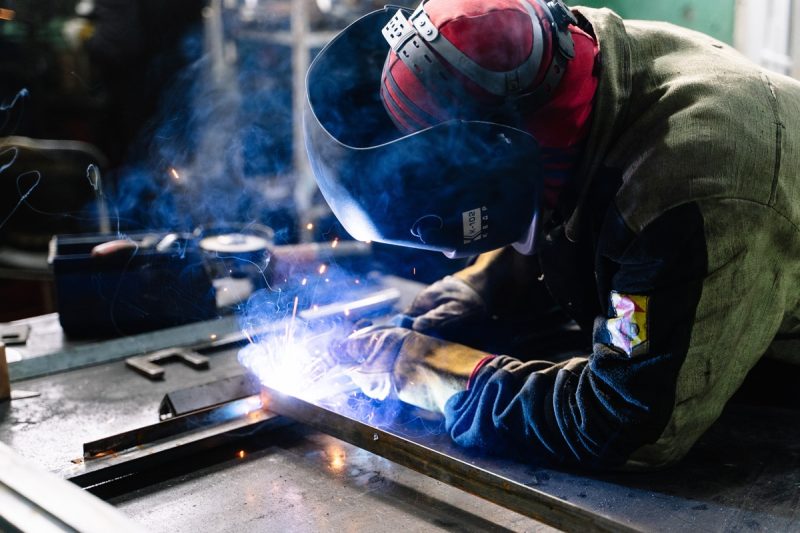
レーザービームの集束が溶接品質に与える影響
レーザービームの焦点設定は溶接プロセスにおいて重要な役割を果たし、溶け込み深さ、溶接幅、入熱、溶接速度、欠陥の最小化など、溶接のいくつかの重要なパラメータに直接影響します。レーザービームの焦点を正確に制御することで、溶接品質を大幅に向上させ、さまざまなアプリケーションのニーズを満たすことができます。
浸透深度
レーザービームの焦点を正しく設定することは、溶接の溶け込み深さに直接影響します。溶け込み深さとは、レーザービームが材料に効果的に浸透して強力な接合部を形成できる深さを指します。レーザー溶接では、焦点をワークピースの表面または内部に設定すると、レーザービームのエネルギーがその場所に集中し、レーザーが材料をすばやく溶かして浸透します。この高エネルギー密度の集中により、深い溶接が可能になります。これは、厚いワークピースの場合に特に重要です。焦点を正しく設定すると、溶接の完全な浸透が保証され、不完全な浸透の現象が回避されるため、溶接継手の強度と信頼性が確保されます。
厚板の溶接や重工業部品の溶接など、特定の用途では、溶け込み深さの要件が非常に高くなります。焦点位置を正確に調整することで、エンジニアは溶け込み深さを最適化し、溶接継手の内部構造が均一で欠陥がないことを確認できます。この正確な制御により、溶接の強度が向上するだけでなく、実際の用途での継手の耐久性と安全性も向上します。
溶接幅
焦点設定も溶接の幅に重要な影響を及ぼします。溶接幅とは、レーザー溶接プロセス中に溶融材料によって形成される溶接の横幅を指します。一般的に、焦点サイズが小さいほど溶接幅が狭くなり、細かい溶接を必要とする用途に適しています。たとえば、マイクロエレクトロニクス部品の溶接や精密機器の製造では、溶接幅を狭くすることで材料の無駄を減らし、溶接部分の美観と機能性を高めることができます。
対照的に、焦点サイズが大きいほど溶接幅が広くなり、より大きな接触面積やより高い強度を必要とする構造部品の溶接に適しています。たとえば、船舶の建造や大型機械設備の製造では、溶接幅が広いほど溶接接触面積が大きくなり、溶接部の強度と安定性が向上します。したがって、レーザービームの焦点サイズを調整することで、溶接幅を柔軟に制御してさまざまな溶接要件を満たすことができ、溶接品質とプロセスパフォーマンスを最適化できます。
入熱量
レーザービームの焦点位置は、溶接プロセス中の入熱に直接影響します。入熱とは、溶接プロセス中にレーザーによって材料に伝達されるエネルギーを指し、材料の溶融度と熱影響部(HAZ)のサイズを直接決定します。熱影響部とは、溶接プロセス中に加熱されるが溶融しない材料の領域を指し、通常は熱変形または性能低下が発生します。
レーザービームの焦点が溶接領域に集中すると、エネルギー密度が高く、入熱が集中するため、材料が急速に溶けて溶接を完了できます。この精密な熱制御は、熱影響部のサイズを縮小するのに役立ち、それによって溶接中の熱変形のリスクを軽減し、薄肉材料や複雑な構造の溶接など、高精度と低入熱を必要とする溶接作業に特に適しています。これらのアプリケーションでは、熱影響部を最小限に抑えることで、材料の完全性と機械的特性を維持し、溶接継手の品質を確保できます。
溶接速度
レーザービームの焦点設定は、溶接速度に重要な影響を及ぼします。溶接速度とは、レーザービームがワークピースの表面を移動する速度を指し、通常はミリメートル/秒 (mm/s) で測定されます。適切な焦点設定により、レーザーエネルギーの利用効率が向上し、溶接プロセス中にレーザービームが材料をより速く安定して溶融できるようになり、溶接速度が速くなります。溶接速度が速いと、生産効率が向上するだけでなく、材料が高温にさらされる時間が短縮され、熱変形や材料損傷のリスクがさらに軽減されます。
しかし、焦点設定が間違っていると、エネルギーが分散し、溶接領域に完全に焦点が合わず、溶接速度が低下する可能性があります。溶接速度の低下は、生産効率に影響を与えるだけでなく、溶接の不均一や溶融池の制御の困難など、溶接品質の不安定化につながる可能性があります。したがって、溶接技術者は焦点設定を最適化することで、溶接速度を上げながら溶接品質の一貫性と信頼性を維持することができます。
欠陥を最小限に抑える
レーザービームの焦点設定を最適化することは、溶接欠陥を減らすために重要です。溶接プロセス中によく見られる欠陥には、気孔、亀裂、不完全な溶け込み、溶接不良などがあります。これらの欠陥は溶接継手の強度を低下させるだけでなく、構造上の欠陥や安全上の危険につながる可能性もあります。レーザービームの焦点位置を正確に調整することで、これらの欠陥の発生を効果的に減らすことができます。
焦点設定を正しく行うことで、溶接の均一性と一貫性が確保され、内部応力の蓄積が軽減されるため、溶接プロセス中に亀裂や気孔が発生するリスクが軽減されます。さらに、適切な焦点位置により、溶融池の形成と凝固プロセスが改善され、溶接不良の発生を防ぐことができます。レーザービームの焦点設定を最適化することで、溶接エンジニアは溶接品質の安定性と信頼性を大幅に向上させ、長期間の使用でも溶接継手の耐久性を確保できます。
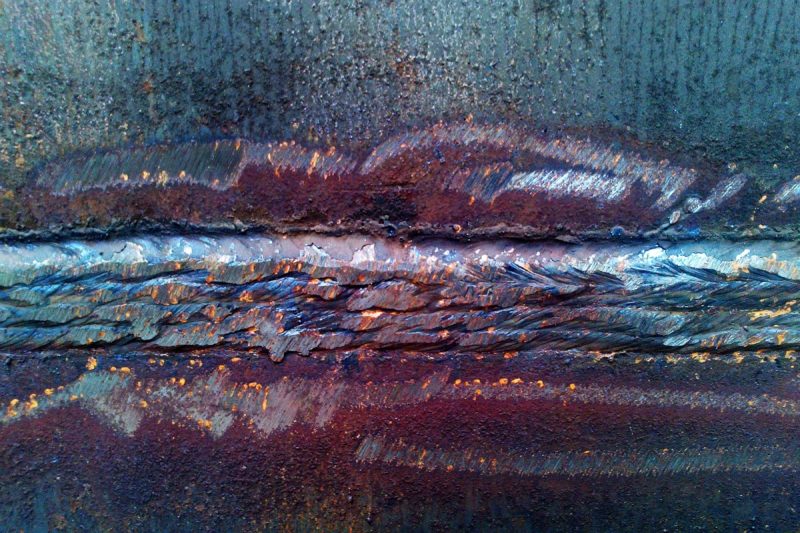
誤ったフォーカス設定の影響
レーザー溶接プロセスでは、正確な焦点設定が重要です。ただし、焦点が正しく設定されていないと、溶接品質と生産効率に一連の悪影響が生じます。焦点設定が間違っていると、次のような問題が発生することがあります。
浅い浸透
レーザービームの焦点が正しく設定されていない場合、特に焦点位置が高すぎたり低すぎたりすると、レーザービームがワークピースを効果的に貫通できない可能性があります。 この場合、レーザーエネルギーは溶接される領域に十分に集中できず、溶接深さが不十分になります。 この浅い溶け込み現象は、溶接継手の強度と堅固さに直接影響します。 浅い溶け込みの溶接継手は、使用中に応力に耐えられず、構造の早期故障や破損につながる可能性があり、特に航空宇宙、自動車製造、重機など、高強度と高信頼性が求められる産業用途では、実際の用途の要件を満たすことができません。 そのため、浅い溶け込みは溶接継手の性能を低下させるだけでなく、重大な安全上の危険をもたらす可能性があります。
過度の熱入力
焦点設定が不適切だと、特に材料の表面に焦点が集中しすぎると、過剰な熱入力につながる可能性があります。この場合、レーザービームのエネルギーは材料の深層に効果的に分散されず、表面に集中し、局所的に熱が過剰に蓄積されます。
これにより、いくつかの問題が発生します。まず、熱影響部(HAZ)が拡大し、材料構造が結晶粒の粗大化や相変態などの悪影響を被り、材料の機械的特性に影響を与える可能性があります。次に、過剰な入熱によりワークピースの熱変形が誘発され、特に電子部品や精密機器の溶接など、高精度と小さな公差が求められる製造プロセスでは、ワークピースの寸法精度が低下します。さらに、過剰な熱は材料の表面酸化や燃焼などの問題も引き起こし、溶接部の品質と美観をさらに低下させる可能性があります。したがって、入熱を制御することは、材料の構造的完全性と溶接部の品質を維持するために非常に重要です。
溶接品質のばらつき
焦点設定が不適切だと溶接品質にばらつきが生じ、実際の生産では深刻な問題となります。レーザービームの焦点を溶接パスに正確に合わせることができないと、同じワークピースでも溶接部の幅、深さ、形態が大きく異なることがあります。このばらつきにより溶接部の機械的特性にばらつきが生じ、溶接継手の全体的な強度と耐久性に影響します。さらに、溶接部のばらつきは製品の外観品質にも影響を及ぼします。特に、溶接部の滑らかさと均一性が重要な、家電製品や医療機器の製造など、高い外観品質が求められる用途では顕著です。溶接品質にばらつきがあると、追加の研磨、修理、検査の手順が必要になるなど、後続の処理が複雑になり、生産コストと時間が増加することもあります。
効率の低下
焦点設定が間違っていると、溶接効率が大幅に低下する可能性があります。レーザービームがワークピースの重要な領域に完全に焦点を合わせることができない場合、エネルギー利用率が低下し、溶接速度が低下します。溶接速度が低下し、生産サイクルが長くなると、生産ライン全体の効率が低下するだけでなく、単位時間あたりの生産コストも増加します。特に大規模生産では、効率が低下すると会社の生産能力と納期に悪影響を及ぼし、注文の遅延や顧客満足度の低下につながる可能性があります。さらに、不適切な焦点設定から生じる溶接欠陥により手直し率が上昇し、生産コストと時間の無駄がさらに増加する可能性があります。したがって、焦点設定が正しいことを確認することは、効率的な生産プロセスを維持し、生産コストを管理するために重要です。
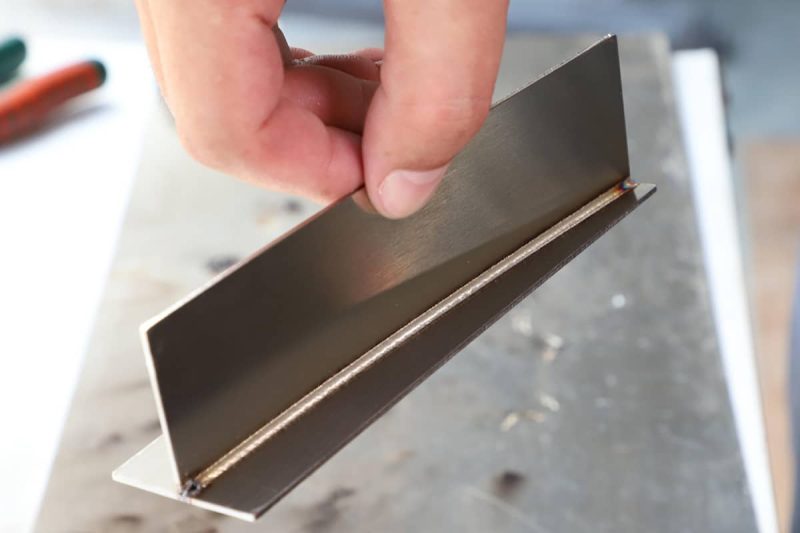
高品質の溶接のためにレーザービームの焦点を最適化
レーザー溶接時に高品質の溶接結果を得るには、レーザービームの集束性能を最適化する必要があります。レーザービームの集束を最適化するには、ビーム分析、プロセスパラメータ調整、高度な適応光学など、多くの技術の側面が関係します。これらの方法は互いに補完し合い、レーザービームエネルギーの有効利用を保証し、溶接品質と生産効率を向上させます。
ビーム解析
ビーム解析は、レーザー ビームの集束性能を最適化するための最初のステップです。レーザー ビームの主要パラメータを詳細に測定および解析することで、溶接プロセス中のレーザー ビームの動作をより深く理解できます。ビーム解析には通常、次の重要な側面が含まれます。
- ビーム径測定: さまざまな位置でレーザー ビームの直径を測定すると、レンズを通過した後にレーザー ビームがどのように焦点を合わせるかを判断するのに役立ちます。ビーム径が小さいほど、エネルギー密度が高くなり、深い浸透と高精度の溶接を実現するために重要です。
- 焦点位置測定: レーザー ビームの焦点の位置を測定することで、レーザー ビームがワークピースの特定の部分に正確に焦点を合わせていることを確認できます。焦点位置を正確に制御することで、溶接の深さと溶接品質を最適化し、溶け込みが浅い、熱が過剰に入るなどの問題を回避できます。
- M² 係数分析: M² 係数はレーザービームの品質の重要な指標であり、レーザービームの集束能力を反映します。M² 係数を分析することで、レーザービームの集束性能が優れているかどうかを評価できます。M² 係数が低いほど、レーザービームの品質が高く、より効果的に集束できるため、溶接の精度と品質が向上します。
ビーム分析はレーザー溶接の科学的根拠を提供し、オペレーターが特定の溶接ニーズに基づいて調整を最適化できるようにします。ビームを通した分析により、焦点のずれやビーム品質の低下などの潜在的な問題を特定して解決できるため、レーザー ビームが常に最適な状態になり、溶接の全体的な品質が向上します。
プロセスパラメータ
ビーム自体の最適化に加えて、溶接プロセスパラメータを正しく設定することも、レーザービームの集束効果を確保する上で重要な要素です。プロセスパラメータには、レーザー出力、溶接速度、シールドガス流量などがあり、これらが組み合わさってレーザービームのエネルギー入力と伝送効率を決定します。以下は、主要なプロセスパラメータの重要な最適化ポイントです。
- レーザー出力:レーザー出力は溶接時のエネルギー入力に直接影響します。出力が高すぎると熱入力が過剰になり、ワークピースの変形や材料の焼損を引き起こす可能性があります。出力が低すぎると、溶接が不完全になったり、溶け込みが浅くなったりする可能性があります。したがって、材料の特性と溶接要件に応じてレーザー出力を正確に調整することが、溶接品質を確保する鍵となります。
- 溶接速度: 溶接速度はレーザー出力と密接に関係しており、レーザー出力によってワークピース上のレーザービームの滞留時間が決まります。溶接速度が遅いと浸透深さは深くなりますが、熱影響部が拡大する可能性があります。一方、溶接速度が速いと熱変形が減り、生産効率が向上します。溶接速度とレーザー出力のバランスをとることで、最高の溶接効果が得られます。
- シールドガス流量: レーザー溶接中、アルゴンや窒素などのシールドガスを使用すると、溶接部分の酸化や汚染を防ぐことができます。シールドガス流量の調整は、溶接の品質を維持するために不可欠です。ガス流量が高すぎたり低すぎたりすると、溶接の形成と品質に影響を与える可能性があるため、材料とプロセスの要件に応じて正確に調整する必要があります。
プロセスパラメータを最適化することで、レーザービームのエネルギーが最大限に活用され、気孔、亀裂、不完全な溶け込みなどの溶接欠陥が低減され、溶接継手の強度と一貫性が向上します。
プロセスパラメータ
適応光学は、レーザービームの焦点位置とビーム形状をリアルタイムで最適化できる高度な光学調整技術です。適応光学は、溶接プロセス中にレーザービームを動的に調整し、さまざまなワークピースや溶接条件に対応するためにレーザービームが常に最適な焦点位置にあるようにします。以下は、レーザー溶接における適応光学の具体的な用途です。
- リアルタイム焦点調整: 適応光学は、レーザービームの焦点位置をリアルタイムで監視し、ワークピースの表面形態と溶接パスに応じて焦点を調整できます。この動的な調整機能により、複雑な溶接作業中、特に不規則な形状やさまざまな厚さのワークピースを扱う場合に、レーザービームは高精度の焦点を維持できます。
- ビーム形態の最適化: 焦点位置に加えて、適応光学技術は、ビームのスポット形状やエネルギー分布の変更など、レーザービームの形態を調整することもできます。この調整により、特に多層材料や複合材料の溶接において、溶接の形態と品質を最適化し、溶接欠陥を減らすことができます。
- 自動補正システム: 適応光学システムには、通常、光学部品や環境の変化によって生じるビームの偏差を検出して補正できる自動補正機能が装備されています。この機能により、レーザー ビームの安定性と一貫性が確保され、長時間の溶接や複雑なプロセス条件でも高品質の溶接結果が維持されます。
適応光学技術の導入により、レーザー溶接の柔軟性と精度が大幅に向上し、レーザー溶接がより複雑で多様な応用シナリオに適応できるようになりました。たとえば、自動車製造では、適応光学技術を使用して車体構造部品を溶接することができ、航空宇宙産業では、異なる材料と厚さの接合部の溶接ニーズに対応できます。したがって、適応光学は溶接品質を向上させるだけでなく、生産効率とプロセス安定性も向上させます。
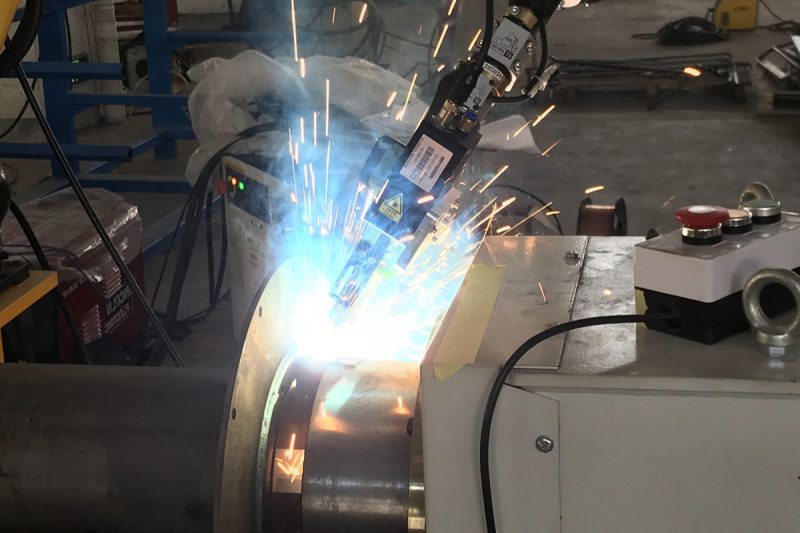
アプリケーション固有の考慮事項
レーザー溶接はさまざまな業界で広く使用されていますが、各業界では溶接品質とレーザー ビームの要件に関して独自の基準と課題があります。以下は、さまざまなアプリケーション分野に固有の考慮事項です。
自動車産業
自動車製造では、車体、シャーシ、エンジン部品の接合にレーザー溶接が広く使用されています。自動車部品は通常、形状が複雑で強度要件が厳しいため、レーザー溶接の精度と信頼性が非常に重要です。
- 焦点位置とサイズの最適化:自動車部品の溶接には通常、さまざまな材料と厚さが関係します。焦点を正しく設定することで、溶接の強度と安定性を確保できます。さまざまな部品の接続要件を満たすには、焦点位置を正確に調整する必要があります。焦点サイズが小さいほど高精度の溶接を実現できますが、溶接の深さと強度が自動車製造の安全基準を満たしていることも確認する必要があります。
- 溶接部の強度と美観: 自動車部品の溶接部は、車両の動作負荷に耐える十分な強度を備えているだけでなく、外観の美観要件も満たす必要があります。レーザー溶接の高精度により、スパッタや溶接の不均一などの溶接欠陥が軽減され、自動車部品の外観と品質が向上します。
- 材料の適合性: 自動車の製造には、鋼、アルミニウム、複合材料など、さまざまな材料の接合が伴います。レーザー溶接は、これらのさまざまな材料の溶接作業に対応できますが、溶接接合部の強度と耐久性を確保するには、レーザー ビームの焦点位置とサイズをさまざまな材料に合わせて最適化する必要があります。
航空宇宙産業
航空宇宙産業では、特にエンジンや機体構造部品の製造において、溶接品質に対する要求が非常に高くなっています。この分野でレーザー溶接を適用する場合、以下の点に特に注意する必要があります。
- 正確な焦点制御: 航空宇宙部品は、高温や高圧などの過酷な環境条件にさらされることがよくあります。そのため、レーザー溶接の焦点設定は、溶接の品質と構造強度を確保するために非常に正確でなければなりません。焦点の位置とサイズを最適化すると、溶接欠陥を回避でき、溶接継手の安全性と信頼性を確保できます。
- ビーム解析と適応光学: 航空宇宙製造では、複雑な形状や異なる厚さの材料を溶接する必要があることがよくあります。高度なビーム解析と適応光学技術により、レーザー ビームの焦点をリアルタイムで調整して、溶接プロセス中に最適なパフォーマンスを確保できます。これらの技術は、高精度の溶接を実現し、溶接欠陥による飛行安全上の危険を軽減するのに役立ちます。
- 材料と環境の制御: 航空宇宙部品には、チタン合金や耐熱合金などの高性能材料がよく使用されます。これらの材料の溶接には、溶接プロセス中に材料特性が影響を受けないようにするための特別なレーザー溶接パラメータと環境制御が必要です。レーザービームの焦点位置とサイズを最適化すると、熱影響部が減り、材料の構造的完全性が確保されます。
電子機器製造
電子機器の製造において、レーザー溶接は主にチップ、ワイヤ、コネクタなどの小さな部品を接続するために使用されます。これらの部品は熱に非常に敏感であるため、レーザー溶接では以下の点に特別な注意を払う必要があります。
- 正確な焦点設定: 電子部品は非常に小さいため、レーザー ビームの焦点設定は非常に正確でなければなりません。焦点サイズが小さいとエネルギー密度が高くなり、精密な溶接を実現できます。ただし、小さな部品への過度の熱入力を回避するために焦点制御は非常に正確でなければならず、過度の熱入力は損傷や性能低下の原因となる可能性があります。
- 高いビーム品質: 電子機器製造における溶接では、極めて高い均一性と溶接品質が求められます。ビーム品質の高いレーザー溶接は安定した焦点を提供し、高品質の溶接接合部を実現します。ビーム品質を最適化することで、溶接による熱変形や接合部の欠陥を軽減し、電子製品の全体的な信頼性を向上させることができます。
- 熱管理: 電子機器の製造では、レーザー溶接によって発生する熱を厳密に制御して、敏感な電子部品の過熱を防ぐ必要があります。レーザービームの焦点設定により、熱入力を正確に制御して、部品を過熱による損傷から保護すると同時に、溶接の堅牢性と安定性を確保する必要があります。
電子機器製造
医療機器の製造では、ステンレス鋼やチタン合金などの高精度材料を接合するためにレーザー溶接が使用されます。これらの材料の溶接は非常に要求が厳しく、以下の重要な考慮事項が含まれます。
- 正確な焦点位置とサイズ: 医療機器には、手術器具やインプラントなどの高精度の部品が含まれることがよくあります。レーザービームの焦点位置とサイズを最適化することは、溶接接合部の精度と信頼性を確保する上で重要です。焦点サイズが小さいほど繊細な溶接が可能になり、医療機器の安全性と機能性が確保されます。
- 材料特性: 医療機器では高性能合金やステンレス鋼が使用されることが多く、溶接の要件は非常に厳しいです。レーザービームの焦点設定では、溶接中の熱損傷や構造変化を避けるために、材料の熱伝導率と熱反応性を考慮する必要があります。
- 溶接接合部の衛生要件: 医療機器の溶接接合部は、厳格な衛生および無菌要件を満たす必要があります。レーザービームの焦点を正確に制御することで、溶接接合部の欠陥を減らし、使用中の製品の安全性と衛生を確保できます。
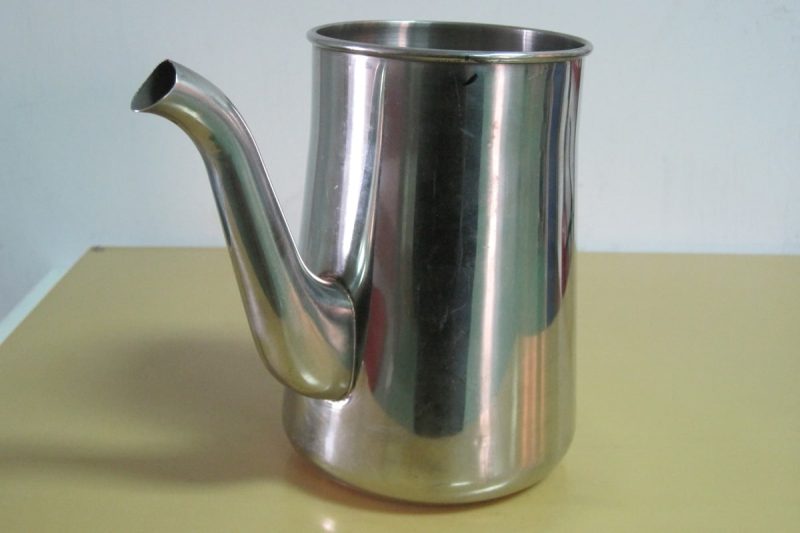
要約する
レーザー ビームの焦点設定は、溶接品質に大きな影響を与えます。レンズを適切に選択し、ビーム径、焦点距離、ビーム品質を調整することで、溶接の深さ、幅、一貫性を大幅に改善し、溶接欠陥を減らすことができます。正確な焦点設定により、より深い溶け込みとより広い溶接を実現できるだけでなく、溶接プロセスの均一性も向上し、すべての溶接ジョイントで一貫した品質を確保できます。この一貫性は、航空宇宙や医療機器の製造など、高い基準が求められる用途では特に重要です。
さらに、焦点設定を最適化することで、気孔、亀裂、不完全な溶け込みなどの溶接欠陥を効果的に減らすことができます。レーザービームの焦点を正確に制御することで、熱影響部のサイズを縮小し、熱変形を減らすことができ、溶接品質の安定性が向上します。同時に、正確な焦点設定は過熱や材料の損傷を回避し、溶接継手の完全性と強度を確保するのに役立ちます。溶接プロセスのこの最適化は、溶接品質を向上させるだけでなく、生産効率を向上させ、生産コストを削減します。
レーザー技術が進歩し続けるにつれて、焦点最適化技術も進歩しています。高度なビーム分析、適応光学技術、プロセスパラメータの改善により、レーザー溶接技術の応用がさらに促進されます。将来、レーザー溶接技術はより複雑な溶接タスクを処理できるようになり、より多くの業界のニーズを満たし、製造業でますます重要な役割を果たすようになります。焦点最適化技術の継続的な開発は、溶接業界の革新と進歩を促進し、より高い品質とより効率的な生産を実現します。
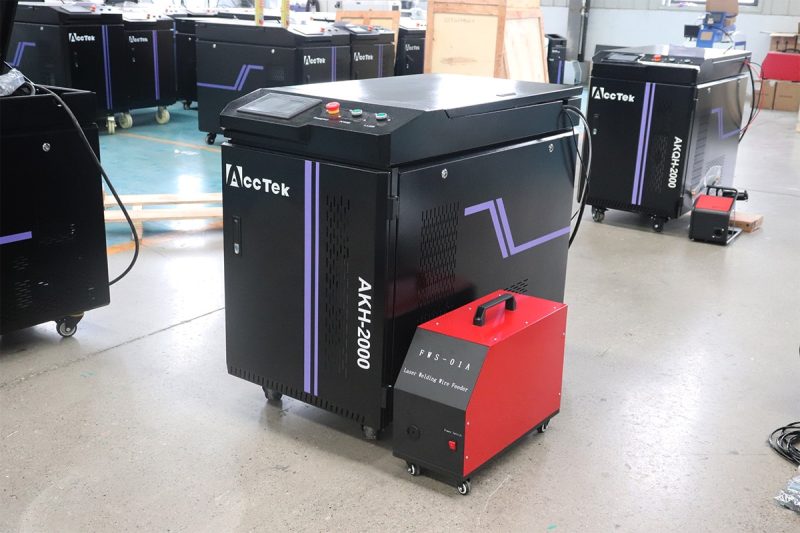
レーザー ソリューションを入手する
適切なレーザー ビームの焦点設定を選択することが、溶接品質を最適化する鍵となります。信頼できるサプライヤーと協力すれば、高度な技術サポート、専門家のアドバイス、継続的なサービスを受けることができます。AccTek Laser では、さまざまな業界のニーズに対応する多様なレーザー溶接機器を提供しています。当社の専門家が、焦点パラメータの最適化、安定した溶接品質の確保、生産効率の最大化をお手伝いします。また、溶接の一貫性と精度を確保するために、精密焦点調整やインテリジェント モニタリング システムなどの高度な機能も提供しています。さらに、当社の技術チームは、機器が常に最高の状態で稼働するように、定期的な機器メンテナンスと技術サポートを提供しています。AccTek Laser と協力することで、効率的で安定した溶接品質が得られ、生産リスクが軽減され、競争力が高まります。今すぐ当社に連絡して、ビジネスの成功に役立つ当社の革新的な溶接ソリューションの詳細をご確認ください。
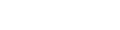
連絡先
- [email protected]
- [email protected]
- +86-19963414011
- No. 3 ゾーン A、Lunzhen 工業地帯、玉城市、山東省。
レーザー ソリューションを入手する