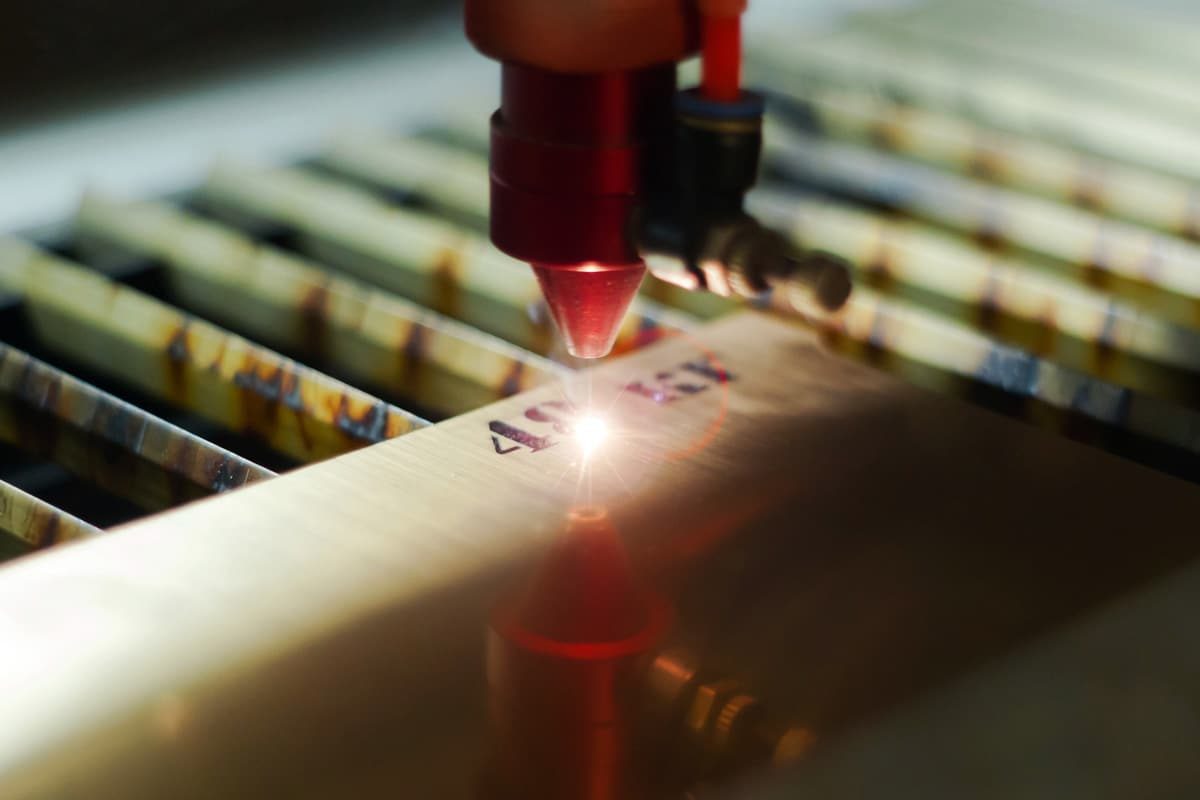
レーザーマーキングで高コントラストを実現する方法
レーザーマーキングは、効率的で正確なマーキング方法として、多くの業界で広く使用されています。特に、電子製造、医療機器、自動車部品、航空宇宙、宝石、包装などの分野で使用されています。製品のシリアル番号、QRコード、ブランドロゴから複雑なグラフィックまで、レーザーマーキング技術はさまざまな材料に永久的なマーキングを実現できます。この技術は、非接触、高速、低コスト、高精度であることから、現代の製造業に欠かせないものとなっています。コントラストは、レーザーマーキングの品質に影響を与える重要な要素です。コントラストが高いと、マークの読みやすさが向上するだけでなく、製品やブランドの視覚効果にも直接影響します。自動バーコード読み取り、ブランドロゴの鮮明さ、複雑な工業用マーキングなど、マークの品質を確保するには、コントラストが重要です。では、レーザーマーキングで高コントラストを実現するにはどうすればよいでしょうか。この記事では、さまざまなアプリケーションシナリオで優れたレーザーマーキング効果を実現できるように、関連するテクノロジーとベストプラクティスを詳細に説明します。
目次
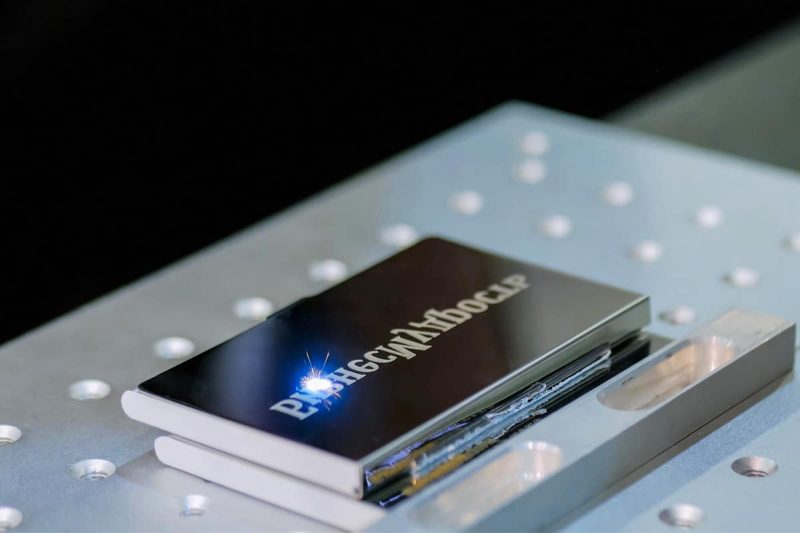
レーザーマーキング技術について学ぶ
レーザーマーキング技術は、非接触、高精度、多様なマーキング方法のため、業界で広く使用されています。マーキング材料とマーキング要件に応じて、彫刻、アニーリング、発泡、アブレーション、カーボンマイグレーションなど、さまざまな方法でレーザーマーキングを実現できます。各技術には異なる動作原理とマーキング効果があり、さまざまなアプリケーションシナリオに適しています。以下では、各マーキング技術を詳細に検討し、その利点とアプリケーション領域を理解していただくお手伝いをします。
彫刻
彫刻とは、高エネルギーレーザーを使用して材料の表面層を除去し、マークを作成する技術です。レーザーの高温により材料が蒸発または溶解し、永久的な凹んだマークが残ります。この技術は、材料に深くまたは永久的にマークを付けるためによく使用され、長期的な耐久性と耐摩耗性が求められる用途に適しています。
- 適用材質:金属、プラスチック、セラミック、木材など
- 利点: 彫刻の深さを制御でき、マーキングの耐摩耗性が非常に高く、自動車部品や工具など、過酷な環境で作業する部品に適しています。
- 適用業界: 自動車製造、電子機器、金属加工、宝飾品、工具識別など。
彫刻技術は、ステンレス鋼やアルミニウム合金などの硬い材料にマーキングするのに特に適しています。耐久性があり鮮明なマークを作成できるため、過酷な条件下でもマークが読み取れるようになります。
アニーリング
アニーリング技術は主に金属材料に使用されます。レーザーは材料の表面を加熱し、表面に酸化反応を引き起こしてさまざまな色のマークを形成します。材料の表面層は材料を除去せずに色を変えるだけなので、アニーリングマークの滑らかな表面は、材料表面に高い要件があるアプリケーションに適しています。
- 適用材質:ステンレス鋼、チタン合金、クロム、その他金属材料。
- 利点: 材料の表面に機械的損傷がなく、表面が滑らかで、医療機器や需要の高い部品に適しています。
- 適用業種:医療機器、外科用器具、航空宇宙部品など
アニーリング マーキング技術の大きな利点は、材料表面の完全性を維持しながら高コントラストのマークを提供できる点であり、材料の性能に対する要件が高い業界にとって第一の選択肢となります。
発泡
発泡技術はプラスチックのマーキングによく使用されます。レーザーが材料の表面を加熱し、材料を局所的に蒸発させて小さな泡を形成します。これらの泡は材料の反射特性を変え、顕著な色の違いを生み出します。発泡により、通常、材料の表面がわずかに盛り上がり、マークに立体感が加わります。
- 適用材料:プラスチック、ゴムなどの非金属材料。
- 利点: 発泡マークは鮮明でコントラストが高く、特に暗いプラスチック材料に適しています。
- 適用業種: 電子部品、プラスチック製品、消費財の包装など。
フォームマーキングは、プラスチックの全体構造を変えずに、はっきりとしたマーキングを実現できるため、電子製品、包装材料、消費財の分野でよく使用されます。
アブレーション
アブレーション技術は、高エネルギーレーザーを使用して、材料の表面からコーティングやフィルムを正確に除去します。彫刻とは異なり、アブレーションは下地の材料に影響を与えずに表面層のみを除去します。この技術は、コーティングされた材料に高精度のマーキングを施すためによく使用され、表面コーティングを除去して下地の材料を露出させ、コントラストを生み出します。
- 適用材質:コーティングされた金属、プラスチック、ガラスなど。
- 利点: 高精度のマーキング。外観要件が高く、細かいマーキングが必要な用途に適しています。
- 適用業種:電子部品、家電筐体、計測機器など
アブレーション マーキングは多層材料に適しており、特に電子製品のハウジング、自動車部品、精密機器のマーキングなど、下層の材料を露出させる必要がある用途に適しています。
炭素移動
カーボンマイグレーションは、レーザーを介して材料の炭素含有量を変化させ、材料の表面の色を変えて永久的なマークを形成します。カーボンマイグレーションは主に金属材料、特に炭素を含む材料に使用されます。レーザーエネルギーを正確に制御して、材料内の炭素元素を再分配または昇華させ、色の変化を形成します。
- 適用材料:炭素鋼、ステンレス鋼、チタン、その他炭素含有金属材料。
- 利点: 表面仕上げを損なうことなく非常に高いコントラストを実現できるため、外観に対する要求が高い製品に特に適しています。
- 適用業種: 医療機器、宝飾品、消費財など
カーボンマイグレーションマーキング技術は、材料の表面を傷つけないため、外科用器具や高級品などのステンレス鋼やチタン合金のマーキングに広く使用されています。
さまざまなレーザーマーキング技術は、多様な用途に幅広いオプションを提供します。彫刻技術は深くて耐久性のあるマークを提供し、アニーリング技術は滑らかな金属表面を確保しながら色の変化を実現します。発泡はプラスチック材料に適しており、アブレーションはコーティングされた材料の処理に適しており、カーボンマイグレーションは高コントラストの金属マーキングに比類のない結果を提供できます。材料の種類とマーキング要件に応じて、適切なマーキング方法を選択すると、製品マーキングの品質と読みやすさが大幅に向上します。工業生産では、これらの技術を理解し、特定のアプリケーションシナリオに基づいて選択することが重要です。

レーザーマーキングのコントラストを理解する
レーザー マーキング プロセスでは、コントラストはマークの品質を決定する重要な要素の 1 つです。コントラストの高いマークは、特にコントラストの品質が生産効率と製品のパフォーマンスに直接影響する産業用途において、情報の識別と読み取りを容易にします。以下では、レーザー マーキングにおけるコントラストの定義と、さまざまな産業におけるその重要性について詳しく説明します。
コントラストの定義
レーザーマーキングにおけるコントラストとは、マーキングされた部分と周囲のマーキングされていない領域の明暗の差を指します。具体的には、マーキングされた領域の色、明るさ、または反射率が、マーキングされていない領域と鮮明なコントラストを形成し、鮮明な視覚効果を生み出します。コントラストが高いほど、マークが鮮明になり、マーキングされた情報の読み取りやスキャンに重要です。
コントラストの生成は主に以下の要素に依存します。
- 材料表面の特性: さまざまな材料の吸収率と反射率は、レーザーと材料の相互作用に影響し、マークの色と鮮明度に影響します。たとえば、黒いプラスチックへのレーザー マーキングは、白いプラスチックへのマーキングとは大きく異なります。
- レーザーパラメータ: 出力、パルス周波数、スキャン速度などのパラメータは、レーザーマーキングの深さ、色の変化、材料の光沢に影響し、マークのコントラストに直接影響します。
- 環境条件: 温度、湿度、その他の要因も、材料の物理的特性やレーザー マーキングの効果に影響を与える可能性があります。
バーコード、QR コード、テキスト、パターンなど、マーキングが鮮明かどうかは、十分なコントラストによって決まります。特に工業生産においては、マーキングが鮮明かどうかは、製品の追跡可能性と可読性に直接関係します。
高コントラストの重要性
高コントラストのレーザー マーキングは、視覚的に目立つだけでなく、産業オートメーションと手動識別の効率を大幅に向上させます。これは、次の点で特に重要です。
- 読みやすさと認識性の向上: 高コントラストのマーキングにより、さまざまな光、角度、距離で情報を視認できます。特に複雑な産業環境では、強い光、反射、ほこりなどの要因が低コントラストのマーキングの視認性に影響を与える可能性がありますが、高コントラストにより、過酷な状況でも簡単に認識できます。
- 自動化設備の読み取り効率:自動車製造、電子製品、物流、医療機器など、多くの業界では、バーコードやQRコードなどの情報マークは通常、自動化コード読み取り装置によって認識されます。マークのコントラストが不十分な場合、コード読み取り装置は認識エラーを起こしやすくなり、複数回のスキャンが必要になるため、生産効率が低下します。高コントラストのマーキングは、認識エラーや読み取り失敗を減らし、自動化設備の効率を大幅に向上させます。
- 製品のトレーサビリティとコンプライアンスの確保: 電子機器、自動車、医療機器などの高水準の業界では、製品のトレーサビリティは安全性と品質を確保する上で重要な要素です。レーザー マーキングは、これらの業界で部品のマーキングに広く使用されています。高コントラストのマーキングは、製造、輸送、使用中の製品の追跡に役立つだけでなく、業界規制の要件が満たされていることも保証します。
- ブランドと視覚効果の向上: ジュエリー、高級品、携帯電話ケースなどの一部の消費財分野では、ブランド識別のためにレーザーマーキングがよく使用されます。高コントラストのマーキングは、製品の美観を高めるだけでなく、ブランド認知度も高めます。鮮明で耐久性のあるマーキングは、ブランドイメージを強調するだけでなく、消費者に優れた視覚体験を提供します。
業界における応用例
- 自動車業界: 生産ラインでの追跡可能性と自動コード読み取りの精度を確保するために、部品のシリアル番号、製造日、バッチ番号に高コントラストのマーキングが使用されます。
- エレクトロニクス業界: チップやプリント基板などのコンポーネントのレーザー マーキングでは、通常、高速生産ラインの機器の正確な読み取りを保証するために、細かさと高いコントラストが求められます。
- 医療機器業界: 外科用器具や医療機器の場合、高コントラストのレーザーマーキングにより製品の独自性とトレーサビリティが確保され、製品が厳格な衛生および品質要件を満たしていることが保証されます。
- 航空宇宙: 特殊な材料と過酷な環境のため、高コントラストのマーキングにより、製造、設置、メンテナンス中に部品の明瞭な判読性を確保できます。
高コントラストはレーザーマーキングの品質の象徴であるだけでなく、工業生産効率と製品のトレーサビリティを確保する上で重要な要素でもあります。マーキングの鮮明さに対する要件が厳しい業界では、高コントラストのマーキングを実現することは、自動コード読み取り装置のパフォーマンスの向上、エラーの削減、製品のコンプライアンスの確保に欠かせない役割を果たします。したがって、適切なレーザーパラメータと材料を選択し、マーキングプロセスを最適化することは、高コントラストを実現するための重要なステップです。
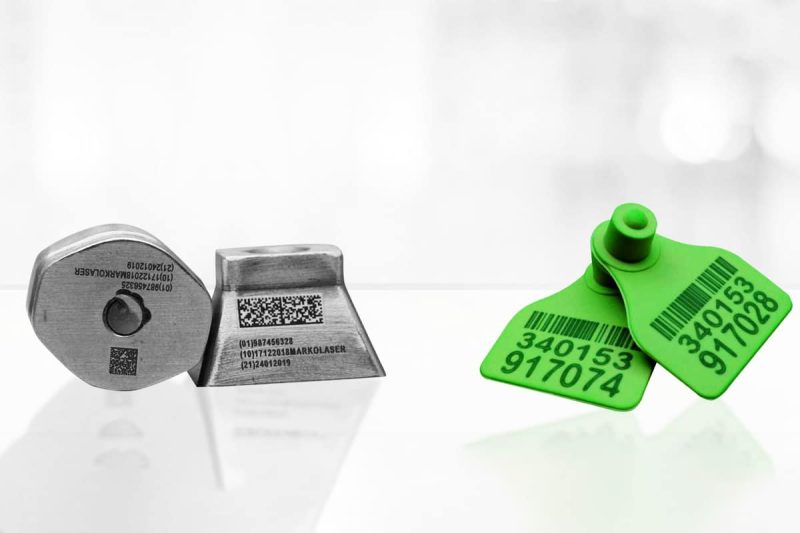
レーザーマーキングのコントラストに影響を与える要因
レーザー マーキングのコントラストは、材料の特性、レーザー パラメータ、環境条件、表面処理など、さまざまな要因の影響を受けます。これらの要因を理解し、それに応じて最適化調整を行うことで、マーキングの鮮明度と品質を大幅に向上させることができます。以下では、さまざまな側面からこれらの要因を制御して、高コントラストのレーザー マーキングを実現する方法について詳しく説明します。
材料特性
材料の物理的および化学的特性はレーザーマーキングの効果に直接影響を及ぼします。特に高コントラストのマーキングを実現する場合、材料の吸収率、反射率、表面の色、表面状態はすべて重要な要素となります。
- 吸収率: 材料によるレーザー エネルギーの吸収率は、マーキング効果を決定する主な要因の 1 つです。吸収率の高い材料は、レーザー エネルギーをより効率的に熱エネルギーに変換できるため、材料表面に明らかな変化が生じます。たとえば、プラスチック、木材、コーティングされた金属などの材料は、通常、レーザー吸収率が高いため、より鮮明なマークが生成されます。ガラスや一部の金属は吸収率が低いため、望ましい効果を得るには、より高い出力や特殊なレーザー波長が必要になる場合があります。
- 反射率: アルミニウム、銀、銅などの反射率の高い素材は、レーザー エネルギーのほとんどを反射する傾向があるため、マーキング効果はわずかです。この種類の素材にマーキングする場合、十分なエネルギー吸収を確保し、マーキングのコントラストを向上させるために、通常、特定の波長のレーザー (ファイバー レーザーやグリーン レーザーなど) を使用する必要があります。適切な表面処理や事前コーティングも、反射率を低減し、マーキングを改善するのに役立ちます。
- 表面の色と構成: 素材の色もレーザー マーキングのコントラストに大きな影響を与えます。暗い色の素材 (黒のプラスチックや黒の金属コーティングなど) は、通常、レーザー エネルギーをより効率的に吸収するため、コントラストが顕著になる可能性が高くなります。逆に、白いプラスチックや銀色の金属などの明るい色の素材では、理想的なコントラストを実現するために、より高いレーザー出力やより細かいパラメータ調整が必要になる場合があります。
- 表面状態: 材料表面の滑らかさや粗さは、レーザーと材料の相互作用に直接影響します。滑らかな表面は通常、レーザー光をより均一に反射するため、コントラストが高くなりますが、表面が粗すぎるとレーザーエネルギーが散乱し、マーキング効果が低下する可能性があります。ただし、適度に粗い表面はレーザーエネルギーの吸収を促進し、マーキング効果を向上させることができます。つまり、材料とアプリケーションの要件に応じて、適切な表面粗さを選択すると、コントラストの向上にもプラスの影響を与える可能性があります。
レーザーパラメータ
レーザーマーキングでは、レーザー機器のパラメータ設定がマーキングの品質、精度、コントラストに重要な役割を果たします。レーザー出力、速度、パルス周波数、フォーカスを最適化することで、マーキング効果を向上させ、マーキングのコントラストを高めることができます。
- 出力: レーザーの出力によって、材料の表面に照射されるエネルギーの量が決まります。出力が低すぎると、マーキングが不明瞭になり、コントラストが不十分になる場合があります。一方、出力が高すぎると、材料が過度に燃えたり溶けたり、材料の表面が損傷したりする場合があります。高コントラストのマーキングを実現するには、レーザー エネルギーが材料の特性に一致するように出力を正確に調整し、材料を損傷することなく鮮明なマーキングを実現する必要があります。
- 速度: レーザーヘッドの移動速度は、レーザーが材料の表面に作用する時間に影響します。速度が遅いほど、レーザーが材料の表面に長く留まり、熱エネルギーの蓄積が増加し、マーキングの深さとコントラストが向上します。ただし、速度が遅すぎると、材料が過熱し、マークの鮮明度に影響を与える可能性があります。したがって、最高のマーキング効果を得るには、速度調整を電力と併せて検討する必要があります。
- パルス周波数: レーザー パルス周波数は、レーザー繰り返し率、つまり単位時間あたりのレーザー パルス数を決定します。高周波レーザー パルスは、短時間でより広い領域をカバーできるため、繊細で複雑なパターンのマーキングに適しています。一方、低周波レーザー パルスは、深いマーキングに適しています。高コントラストのマーキングを実現するには、適切なパルス周波数を選択すると、材料表面に均一で鮮明なマークを作成できます。
- フォーカス: レーザーのフォーカスを正確にすると、レーザー エネルギーが材料表面の特定の領域に集中し、最も効率的なエネルギー伝達が実現します。フォーカスが正確でないと、レーザー エネルギーが分散し、マークの鮮明度とコントラストに影響する可能性があります。レーザー フォーカスを調整することで、マークされた領域が最大のレーザー エネルギーを取得し、コントラストを向上させることができます。
環境条件
レーザーマーキングの際の環境条件もマーキング効果に影響します。作業環境の温度、湿度、清潔さによって材料の物理的特性やレーザーエネルギーの伝達効率が変化し、コントラストに影響します。
- 温度:周囲温度は、材料の物理的特性とレーザーエネルギーの伝達に一定の影響を及ぼします。高温環境では、特にプラスチックなどの熱に敏感な材料では、材料の吸収率が低下する可能性があります。高温により、材料が事前に軟化または変形し、マーキング効果に影響を与える可能性があります。したがって、高温環境でレーザーマーキングを実行する場合は、レーザー出力を下げるか、他のパラメータを最適化する必要がある場合があります。
- 湿度: 湿度は、特にプラスチックや木材などの特定の材料のレーザー マーキング効果に大きな影響を与えます。湿度の高い環境では、水蒸気が材料の表面に凝縮し、レーザー エネルギーの伝達に影響を与え、マークの鮮明度が低下する可能性があります。湿度の高い環境では、マークのコントラストを確保するため、材料の表面が乾燥していることを確認するのが最善です。
- 清潔さ: 材料の表面のほこり、グリース、酸化物、その他の汚染物質は、レーザーエネルギーの伝達を妨げ、エネルギーの分散を引き起こし、マーキング効果に影響を与えます。特に、高精度が求められるレーザーマーキングの場合、材料の表面が清潔であることを確認することが重要です。レーザーマーキングの前に材料の表面を清掃すると、マークのコントラストが大幅に向上します。
表面処理
レーザーマーキングの前に、材料の表面処理が最終的なマークの品質とコントラストに直接影響します。適切な表面洗浄、粗さの調整、および必要な前処理により、レーザーエネルギーが材料の表面に効率的に伝達され、鮮明なマークが生成されます。
- クリーニング: マーキングする前に、材料の表面を徹底的にクリーニングして、レーザー マーキングの効果に影響を与える可能性のあるほこり、グリース、酸化層、その他の汚染物質を除去する必要があります。溶剤、ブラシ、または超音波洗浄装置を使用すると、表面に残留物が残らないようにすることができ、レーザー マーキングのコントラストが向上します。
- 表面粗さ: 適切な表面粗さは、特に反射率の高い材料の場合、材料がレーザーエネルギーをよりよく吸収するのに役立ちます。表面粗さを大きくすると反射率が低下し、マーキング効果が向上します。ただし、高精度の医療機器や電子部品など、滑らかな表面を必要とするアプリケーションでは、より良いマーキング結果を得るために表面の滑らかさを確保する必要があります。
- 前処理: レーザーマーキング効果を最大限に発揮させるために、一部の材料では前処理が必要になる場合があります。たとえば、金属材料は研磨またはコーティングすることができ、プラスチック材料は表面化学処理を施すことができます。これらの手順により、材料表面によるレーザーエネルギーの吸収が改善され、コントラストが向上します。
レーザーマーキングのコントラストに影響を与える要因は、材料の特性、レーザー機器のパラメータ、環境条件、表面処理など、複雑で多様です。これらの要因を的確に調整することで、レーザーマーキングのコントラストを効果的に向上させ、マーキング効果が明確で耐久性があることを保証できます。これにより、工業生産におけるトレーサビリティと識別の要件を満たすだけでなく、ブランド識別などのアプリケーションでより優れた視覚効果を実現できます。
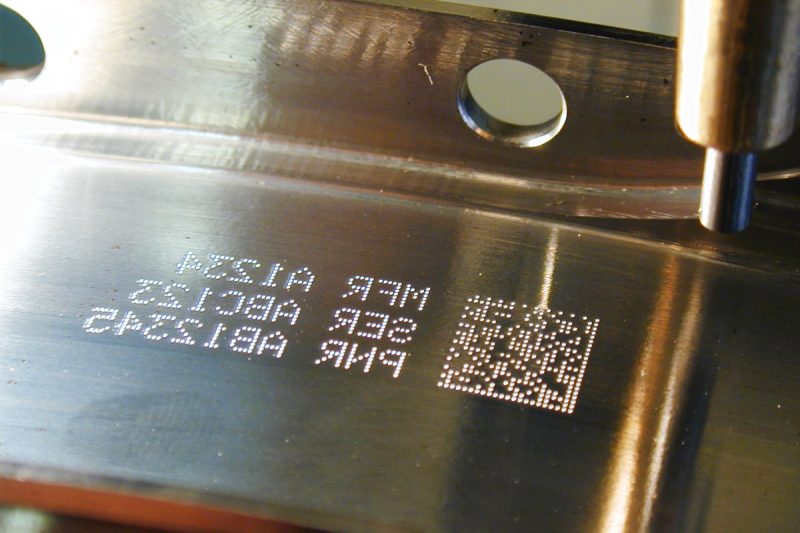
高コントラストを実現するための7つの重要な実践
レーザーマーキングで高いコントラストを実現するには、レーザータイプの選択から環境制御、後処理技術の適用まで、一連のベストプラクティスを採用する必要があります。合理的な操作と調整により、さまざまな材料に鮮明で耐久性のあるマーキング効果が得られます。
適切なレーザータイプを選択する
レーザーの波長は材料によって吸収率が異なるため、適切なレーザーの種類を選択することが重要です。ファイバーレーザージェネレーターは、ステンレス鋼、アルミニウム、銅などの金属材料に適しており、鮮明なマークを作成できます。CO2レーザーは、プラスチック、有機材料、木材、皮革などの一部の非金属材料に適しています。材料の特性に合ったレーザージェネレーターを選択すると、より高いエネルギー吸収が保証され、マーキングのコントラストが向上します。
材料の準備
材料表面の準備は、マーキングの結果に直接影響します。レーザーエネルギーが均等に分散され吸収されるように、表面は清潔で平らである必要があります。材料によっては、マーキングを妨げる可能性のある不純物を取り除くために、研磨、サンドブラスト、化学洗浄などの前処理が必要になる場合があります。このような準備は、レーザーの透過効果を最適化し、マークのコントラストと鮮明さを向上させるのに役立ちます。
レーザーパラメータの最適化
レーザーパラメータの設定は、高いコントラストを実現するために重要です。パワー、速度、パルス周波数などのパラメータは、材料の特性に応じて調整する必要があります。一般的に、パワーが高いほどマークの深さは深くなりますが、パワーが高すぎると材料が焼けたり、過剰に加工されたりする可能性があります。マーキング速度が遅いほど、レーザーと材料の相互作用が高まり、コントラストが向上します。一連の実験テストを通じて、さまざまな材料に最適なレーザー設定を見つけ、最高のマーキング効果を確保できます。
制御された環境条件
環境の温度、湿度、清潔さは、レーザー マーキングの安定性に影響します。過度の温度や湿度は、材料の物理的特性を変化させ、レーザーの吸収効率や伝導効率に影響を与える可能性があります。特に湿気に敏感な材料にレーザー マーキングする場合は、環境条件を一定に保つことで、一貫したマーキング結果を確保できます。作業エリアを定期的に清掃して、マーキング プロセスを妨げるほこりや不純物を避け、高コントラストのマーキング品質を確保してください。
備品と資材の取り扱い
マーキングプロセス中、材料は安定して動かないようにする必要があります。少しでも動くと、マーキングが不明瞭になったり、エラーが発生したりします。高精度の固定具と材料固定具を使用すると、マーキング位置の安定性と一貫性が確保され、処理の繰り返しやマーキングのぼやけを回避できます。特に、広い領域や複雑なパターンをマーキングする場合、安定した固定具を使用すると、全体的なマーキング品質が向上します。
ソフトウェアと制御システム
現代のレーザー マーキング システムには、レーザーの出力、パス、マーキング速度を正確に管理できる、高度にインテリジェントな制御ソフトウェアが搭載されています。これらの機能を適切に使用することで、パラメータの自動調整が可能になり、操作効率が向上します。さらに、ソフトウェアはさまざまな材料に最適なパラメータ設定を記録して、その後の操作を容易にし、各マーキングが理想的なコントラストを実現できるようにします。
後処理技術
場合によっては、レーザーマーキング後の後処理によってコントラストをさらに向上させることができます。たとえば、金属表面を酸化したり、保護層をスプレーしたりして、マーキング効果を高めることができます。場合によっては、マーキング後の洗浄ステップでマーキングプロセスの残留物を除去し、マークをより鮮明で耐久性のあるものにすることもできます。これらの後処理技術は、さまざまな材料やアプリケーションシナリオに応じて柔軟に使用でき、レーザーマーキングの全体的な品質を向上させることができます。
適切なレーザー タイプを選択し、パラメータを微調整し、環境条件を制御し、後処理技術を使用することで、高コントラストのレーザー マーキングを実現できます。これらのベスト プラクティスは、マークの鮮明度と耐久性を向上させ、さまざまな材料でマークが適切に機能することを保証します。
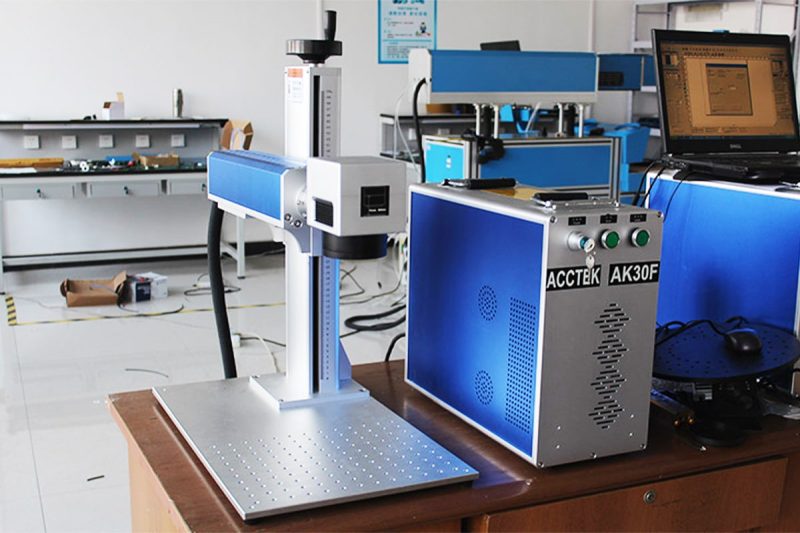
要約する
高コントラストのレーザーマーキングを実現するには、材料、レーザーパラメータ、環境など、さまざまな要素を考慮する必要があります。レーザーの種類を適切に選択し、マーキング設定を最適化し、材料の清潔さを維持することで、企業はマーキング品質を大幅に向上させ、より美しく実用的なマーキング効果をもたらすことができます。
材料の準備に関しては、材料によって吸収率や反射率が異なるため、適切なレーザー発生器を選択することが重要です。 ファイバーレーザーマーキングマシン AccTekが提供するレーザーマーキングマシンは、ステンレス鋼やアルミニウムなどの金属材料に特に適していますが、CO2レーザーマーキングマシンはプラスチックや有機材料に適しています。研磨や洗浄など、材料の特性に応じた適切な前処理により、レーザーエネルギーが均等に吸収され、マーキングのコントラストがより鮮明になります。
レーザーパラメータの調整も同様に重要です。マーキングの際、当社のレーザー機器は柔軟なパラメータ調整をサポートし、パワー、速度、周波数に基づいて最適な設定を見つけることができます。金属への深いマークでも、プラスチックへの浅いマークでも、高コントラスト効果が保証されます。反射率の高い素材でも、AccTek のファイバーレーザーマーキングマシンは簡単に処理できます。
環境条件の制御も無視できないステップです。マーキング環境を乾燥して清潔に保つことで、ほこりや湿気がマーキング効果に影響を与えるのを効果的に防ぐことができます。当社の機器はさまざまな産業環境で優れた性能を発揮し、安定性も高いため、さまざまな条件下で一貫したマーキング結果を得ることができます。日常業務では、当社のレーザーマーキングマシンは設計がシンプルでメンテナンスも簡単です。当社のレーザーマーキングマシンを合理的に使用することで、お客様は迅速かつ正確なマーキングを実現し、製品の全体的な品質とブランドイメージを向上させることができます。これらの取り組みにより、製品をより美しくできるだけでなく、お客様が当社のレーザーマーキングソリューションに興味を持ち、注文の増加を促進できます。
当社のレーザーマーキングマシンにご興味がございましたら、お気軽にお問い合わせください。貴社のビジネスに適したカスタマイズされたソリューションについて詳しくご説明いたします。
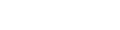
連絡先
- [email protected]
- [email protected]
- +86-19963414011
- No. 3 ゾーン A、Lunzhen 工業地帯、玉城市、山東省。
レーザー ソリューションを入手する