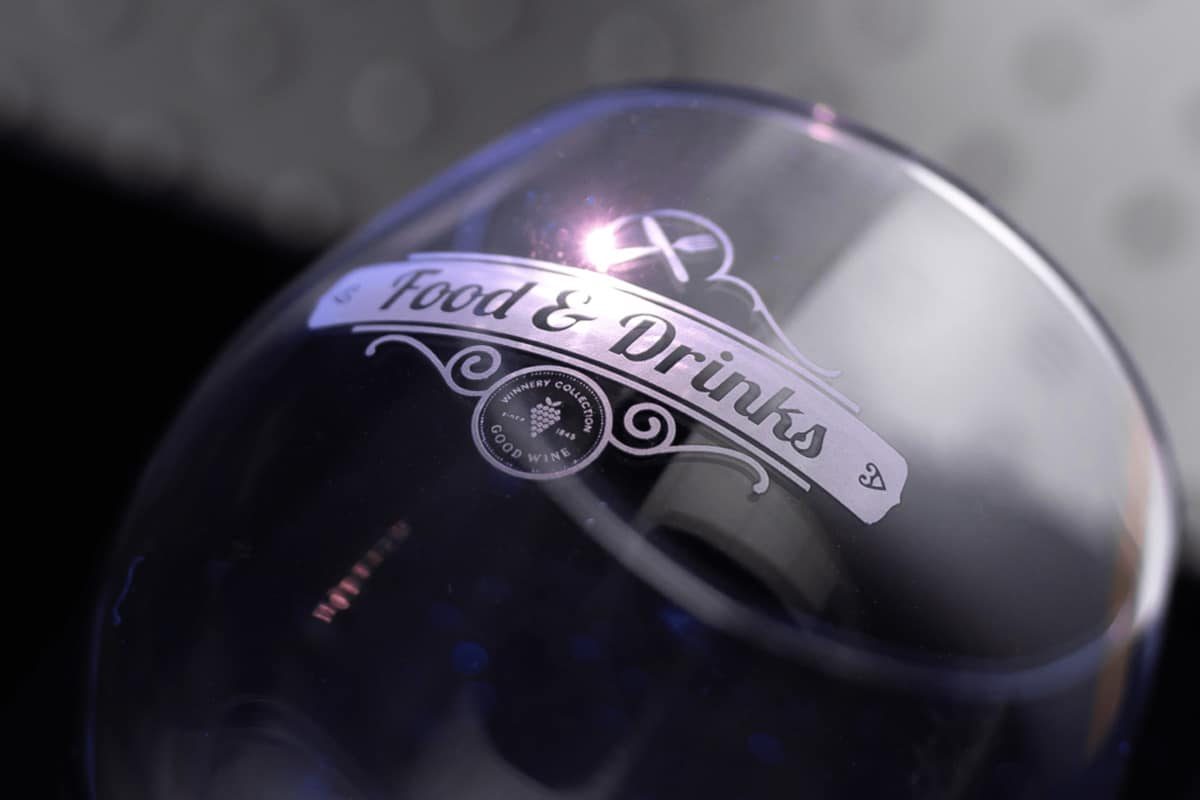
レーザーマーキングの一般的な欠陥は何ですか?
レーザーマーキングは、高エネルギー密度のレーザービームを使用して材料の表面に非接触加工を行う技術です。集束されたレーザービームにより、材料の表面が急速に加熱または蒸発し、永久的なマークが形成されます。このマーキング方法は、金属、プラスチック、セラミック、ガラスなど、幅広い材料を処理できるため、高精度、柔軟性、汎用性が高く知られています。従来のマーキングマシンと比較して、 レーザーマーキングマシン 消耗品が不要で、マーキング効果はより正確かつ安定しています。
目次
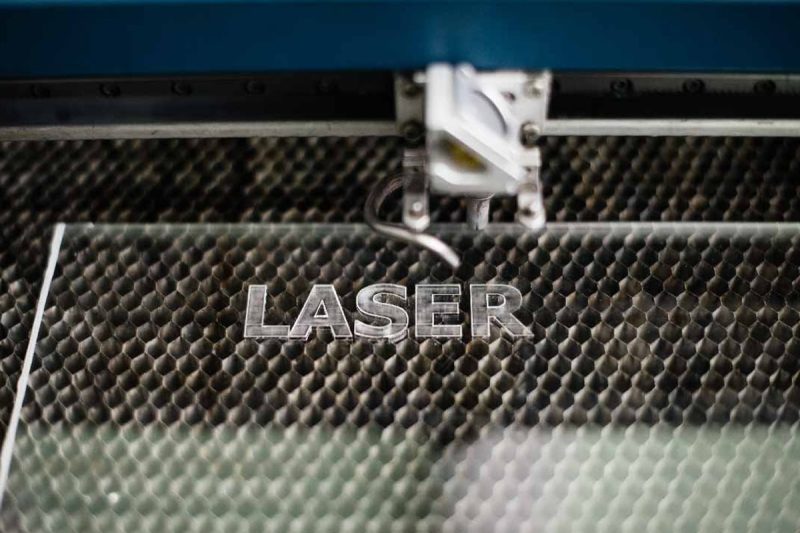
レーザーマーキングシステムの概要
レーザーマーキング技術の核心は、さまざまな種類のレーザー発生器にあり、材料の特性と処理要件に応じて適切なレーザーシステムが選択されます。一般的なレーザーの種類には、ファイバーレーザーと CO2 レーザーがあり、応用分野と性能に大きな違いがあります。
ファイバーレーザーとCO2レーザーの主な違い
ファイバーレーザー
- レーザータイプ: ファイバーレーザージェネレーターは光ファイバーを通じてレーザーを励起し、高いビーム品質と高いエネルギー変換効率を実現します。
- 波長: ファイバーレーザーの波長は通常 1.06 ミクロンで、金属や一部の硬質材料の加工に適しています。
利点
- 高いエネルギー変換効率と低いエネルギー損失。
- レーザービームは品質が良く、集束効果が強いため、精密加工に適しています。
- 金属材料(ステンレス、アルミニウム、銅など)や一部のプラスチック、セラミックのマーキングや切断に適しています。
CO2レーザー
- レーザーの種類: CO2 レーザー発生器は二酸化炭素ガスを使用して、通常 10.6 ミクロンの長い波長のレーザーを励起します。
- 波長: ファイバーレーザーと比較して、CO2レーザーは波長が長く、非金属材料の加工に適しています。
利点
- 有機材料に対して強い吸収力を発揮し、非金属材料の加工に適しています。
- このシステムは比較的成熟しており、さまざまな生産環境で広く使用されています。
ファイバーレーザーと CO2 レーザーは、レーザーマーキングにおいてそれぞれ利点があります。ファイバーレーザーは金属や高精度のマーキングに適しており、CO2 レーザーは非金属材料や大規模な加工に利点があります。加工要件や材料の種類に応じて適切なレーザーシステムを選択すると、生産効率と製品品質が向上します。
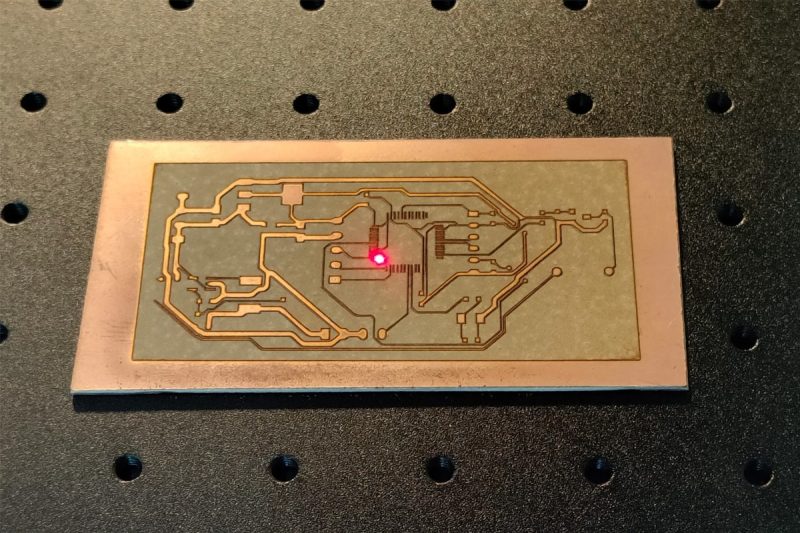
レーザーマーキングによく使われる材料
一般的なレーザーマーキング材料には、金属、プラスチック、セラミック、ガラス、複合材料などがあります。各材料の特性と適切なレーザー技術を理解することで、マーキング品質の向上だけでなく、生産効率の最適化にも役立ちます。
金属材料のレーザーマーキング特性
レーザーマーキングは金属材料、特にステンレス鋼、アルミニウム、銅、チタンなどの一般的な金属材料に広く使用されており、細かくて長持ちするマーキングを実現できます。
プラスチック材料のレーザーマーキング効果
プラスチックへのレーザーマーキングの適用は比較的複雑です。プラスチック材料によって熱反応性と吸収性が大きく異なるため、マーキング効果も異なります。一般的なプラスチック材料には、ポリカーボネート(PC)、ポリオキシメチレン(POM)、アクリル酸(PMMA)などがあります。
陶磁器とガラス
セラミックやガラスは壊れやすい素材なので、レーザーマーキング中に素材が破損しないように特別な注意が必要です。これらの素材はレーザーの吸収率が低いですが、レーザーのパワー、周波数、パルス幅を正確に制御することで、非常に高品質のマーキングを実現できます。
複合材料: 複雑な材料に対する特別な要件
複合材料は 2 つ以上の異なる材料から作られ、航空宇宙、自動車、建設などのハイエンド製造業界で一般的に使用されています。複合材料のレーザーマーキングでは、異なる材料の熱膨張や化学反応によって生じるマーキングの不均一性を回避するために、各材料の特性に応じてレーザーパラメータを正確に調整する必要があります。
さまざまな材料へのレーザー マーキング技術の適用は広範囲かつ複雑です。各材料のマーキング特性と要件を理解することは、適切なレーザー システムを選択する上で非常に重要です。レーザー パラメータを最適化し、適切なレーザー タイプを選択することで、より効率的で正確かつ持続的なマーキング効果が得られ、さまざまな業界のマーキング品質と精度の要件を満たすことができます。
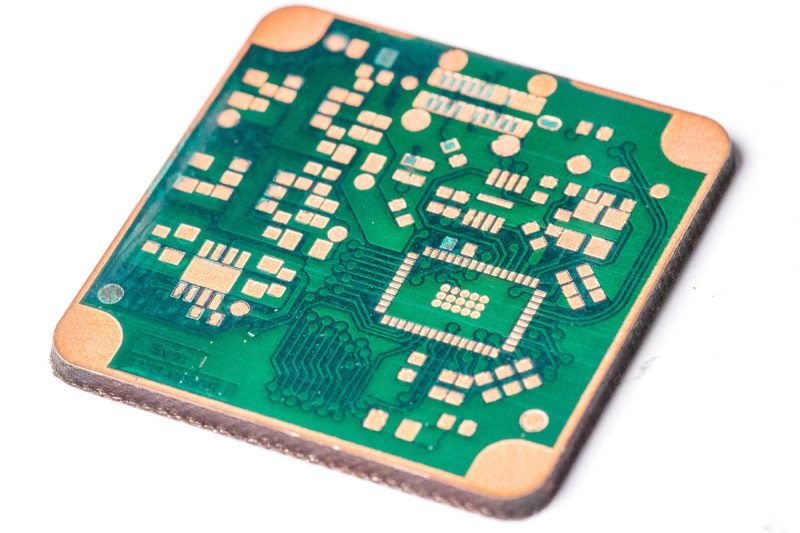
レーザーマーキングの欠陥の概要
レーザーマーキングの欠陥は、主に機器の問題、不適切なパラメータ設定、不十分な材料の選択と準備によって発生します。レーザー出力の不安定さやビームモードのずれなどの機器の問題は、マーキングの品質に影響を与える可能性があります。機器の定期的な校正、光学部品の清掃、老朽化した部品の交換により、これらの問題を防ぐことができます。出力が高すぎる、速度が遅すぎるなどの不適切なパラメータ設定は、マーキングの不均一につながる可能性があります。パラメータは、材料とプロセスの要件に応じて最適化する必要があります。材料の吸収率と表面状態もマーキング効果に影響を与えます。レーザー波長と互換性のある材料を選択し、表面がきれいであることを確認することで、欠陥を回避できます。
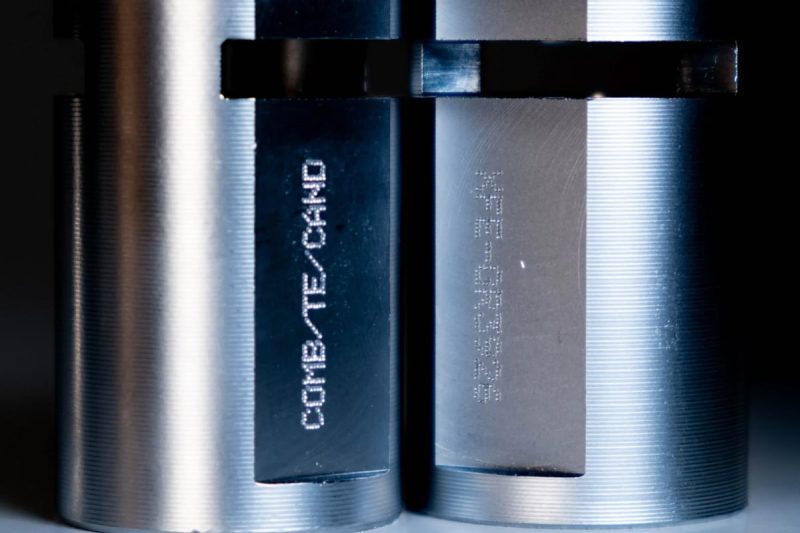
一般的なレーザーマーキングの欠陥と解決策
レーザーマーキング技術は、その高精度と高効率により、多くの業界で広く使用されています。しかし、実際の操作では、機器、パラメータ設定、材料の準備などの影響により、いくつかの一般的なマーキング欠陥が発生する可能性があります。これらの欠陥はマーキング効果に影響を与えるだけでなく、製品の品質と顧客満足度に悪影響を与える可能性もあります。これらの欠陥の根本原因を理解し、適切な解決策を適用することで、マーキング品質を大幅に向上させることができます。
火傷の跡
欠陥の説明: 焼け跡は通常、高出力または不適切なフォーカス条件で発生し、特に金属、プラスチック、一部のセラミック材料に発生します。これらの跡は通常、焦げた表面または過熱された領域として発生し、外観に影響を与えるだけでなく、材料の構造にも影響を与える可能性があります。
理由
- レーザー出力が高すぎるため、材料の表面が過熱します。
- 焦点設定が不適切だと、レーザービームが過度に集中したり分散したりして、特定のポイントに過度の熱が蓄積されます。
解決
- 出力と速度を調整する: レーザー出力を下げるか、スキャン速度を上げて熱の蓄積を減らします。
- 焦点を調整する: レーザーの焦点が材料の表面に合っていることを確認し、焦点が合いすぎないようにします。材料に適切な焦点設定を使用すると、過熱を防ぐことができます。
不完全なマーク
欠陥の説明: 不完全なマーキングは、通常、ビームの位置合わせが不正確であるか、レーザー スキャン速度の設定が不適切であることが原因で発生します。これにより、マークが不均一になったり、部分的に欠落したりして、マークの完全性と読みやすさに影響します。
理由
- ビームが正しく調整されていないため、レーザーが目的の場所を正確に照らすことができません。
- レーザースキャン速度が速すぎるか遅すぎるため、マーキング領域が不完全または不均一になります。
解決
- ビームの位置合わせを校正する: レーザー ビームがマーキング領域に正確に焦点を合わせられるように、レーザー ジェネレータの位置合わせを定期的に確認および校正します。
- スキャン速度の調整: 材料とマーキングの要件に応じて、レーザーのスキャン速度を適切に調整し、速度が速すぎたり遅すぎたりしてマーキング効果に影響しないようにします。
- プロセス パスの最適化: 複雑なグラフィックやテキストをマークする場合は、適切なパス プランニングを選択して、各領域が完全にカバーされるようにします。
色の変化とコントラストの低下
欠陥の説明: 変色やコントラストの低下は、特にプラスチックやコーティングされた金属表面でのレーザー マーキング中によく見られる問題です。これらの欠陥により、マークが不明瞭になり、識別が困難になることもあります。
理由
- 材料の表面の汚れや油はレーザーの反射に影響を与え、マークがぼやけたり変色したりします。
- レーザーパラメータの設定が不適切(出力が低すぎる、速度が速すぎるなど)な場合、マークのコントラストが不十分になり、識別が困難になります。
解決
- 材料表面の洗浄: マーキングする前に、レーザービームが材料表面に効果的に作用できるように、材料表面に油、ほこり、その他の汚染物質がないことを確認してください。
- レーザー パラメータを最適化します。材料の特性に応じてレーザー出力、スキャン速度、焦点距離、その他のパラメータを調整し、マークのコントラストと鮮明さを確保します。
- コーティングまたはエンハンサーを使用する: 一部のプラスチック材料では、特定のレーザー マーキング コーティングを使用して、コントラストとマーキング効果を向上させることができます。
表面損傷と熱影響部
欠陥の説明: 熱に弱い材料 (プラスチック、木材など) を加工する場合、レーザーの過度の熱により表面損傷や熱影響部 (HAZ) が発生する可能性があります。このような欠陥は通常、焦げ、変色、変形として現れます。
理由
- レーザー出力が高すぎるか、スキャン速度が遅すぎるため、過度の加熱が発生します。
- 熱に敏感な材料は、加熱されると物理的または化学的変化を起こします。
解決
- レーザー出力とスキャン速度を調整します。出力を低くし、速度を高くすることで、熱の蓄積を減らし、熱に敏感な材料の過熱を防ぎます。
- 適切な材料を選択する: 材料を選択するときは、レーザーマーキングに適した熱安定性に優れた材料を優先するか、前処理された材料を使用します。
- 加熱制御システム: 気流または冷却システムを使用して、レーザーマーキング中に発生する熱を制御し、熱影響部の拡大を抑えます。
ゴースト、影、マーキングの深さの不一致
欠陥の説明: ゴーストや影は通常、レーザー ビームの発散または機器の光学システムのエラーによって発生します。マーキングの深さの不一致は、レーザー ジェネレーターの焦点距離の変化、ビームの発散、またはエネルギー出力の不均一によっても発生する可能性があります。
理由
- レーザービームの発散または不安定性により、マークにゴーストや影が発生します。
- レーザー発生器の光学系が適切に調整されていないため、レーザービームが焦点を合わせられず、マークの均一性に影響を及ぼします。
- レーザーエネルギー出力が不均一なため、マークの深さが一定ではありません。
解決
- レーザー ジェネレータを定期的に校正する: ビームの不安定性を回避するために、レーザー ジェネレータの光学系と焦点距離を定期的にチェックし、校正してください。
- 光学システムの設定を調整する: 材料の特性とマーキング要件に応じて、レーザーの焦点距離とエネルギー出力を調整します。
- 高精度レーザー ジェネレーターを使用する: マーキングの深さとパターンの鮮明さを確保するために、安定性と精度の高いレーザー ジェネレーターを選択します。
レーザーマーキングの一般的な欠陥とその原因を理解することで、マーキングプロセスを最適化し、マークの品質を向上させるための的を絞った対策を講じることができます。レーザー機器の定期的な検査と調整、パラメータ設定の最適化、適切な材料の選択、表面処理方法はすべて、マーキングの品質を確保するための鍵です。微調整と制御により、欠陥を最小限に抑え、生産効率を向上させ、顧客満足度を確保できます。
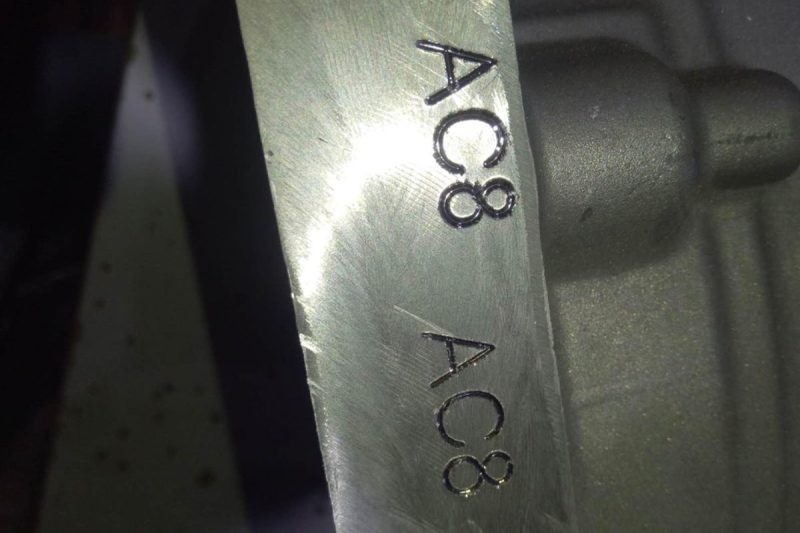
予防策と最適化の提案
パラメータの最適化
電源設定
- 電力が高すぎると材料が過熱し、焼けや変形などの欠陥が発生する可能性があります。
- 出力が低すぎると、マーキングが不明瞭になったり、効果的なマーキングがまったく行われない可能性があります。
速度設定
- 速度が遅すぎると熱影響部が拡大し、熱による損傷のリスクが高まります。
- 速度が速すぎると、マーキングが不完全になったり、表面が不均一になったりする可能性があります。
フォーカス調整
- 焦点距離を正確に設定することで、レーザービームが焦点を合わせられ、広がりすぎたり焦点が合いすぎたりすることがなくなり、マーキングの鮮明さと一貫性が向上します。
最適化の提案
- さまざまな材料やアプリケーションシナリオに応じて、定期的に電力と速度を調整して最適なパラメータを設定します。
- 複数のテストと実験データを使用して、レーザー出力と速度の最適な組み合わせを見つけ、安定した正確なマーキングを実現します。
材料の準備
表面洗浄
- マーキングする前に、レーザービームの正確な動作に影響を与える可能性のある油、ほこり、その他の汚染物質を除去するために、材料の表面を完全に洗浄する必要があります。
- 化学洗浄、ブラッシング、ブローなどの適切な洗浄方法を使用して、表面に障害物がないことを確認します。
材質の適合性
- 材質によってレーザー吸収率が異なるため、レーザー波長に適合する材質を選択してください。アルミニウムや銅などの反射率の高い材質では、出力とフォーカスの設定に特別な注意が必要です。
- レーザー出力が高すぎるとひび割れや損傷が発生する可能性があるため、脆い材料(セラミックやガラスなど)には特に注意してください。
最適化の提案
- マーキングを開始する前に材料テストを実行して、材料がレーザーのエネルギーに耐えられることを確認し、材料の不適合による欠陥を回避します。
- レーザーとの互換性が高い材料を使用し、表面が複雑または不安定な材料は避けてください。
設備保全
定期的な校正
- レーザー機器の光学システムは、ビームの精度と一貫性を確保するために定期的に校正する必要があります。特に焦点距離、ビームのコリメーション、出力などの領域では、定期的な校正によってエラーを大幅に削減できます。
- ビームの偏向によって不完全なマークやぼやけたマークが発生しないように、専門的な機器とツールを使用して校正してください。
部品の検査と洗浄
- レーザー レンズ、反射鏡、集束レンズなどの光学部品は、ほこりや汚染物質がレーザーの伝送やマーキング効果に影響を与えないように清潔に保つ必要があります。
- レーザー機器の動作状態を定期的にチェックし、機械的な摩耗やその他の故障がないことを確認してください。
定期的な校正
- 毎月または四半期ごとにレーザー機器の包括的な検査を実行し、機器のすべての部品が最適な動作状態にあることを確認します。
- 機器の使用中は、機器を清潔に保ち、光学部品を定期的に清掃してください。
オペレータートレーニング
スキル向上
- オペレーターは、レーザー マーキングに関する知識の確固たる基礎を持ち、レーザーの動作原理、材料特性、さまざまな一般的な問題の解決策を理解している必要があります。
- シミュレーショントレーニングや実際の操作を通じて、オペレーターの障害診断能力が向上し、生産上の問題に迅速に対応できるようになります。
業務標準化
- オペレーターが作業の一貫性と標準化を守れるように、明確な操作手順と標準操作手順 (SOP) を確立します。
- オペレーターは定期的に操作マニュアルを確認し、機器の操作を継続的に学習する必要があります。
最適化の提案
- オペレーターが最新のレーザーマーキング技術と操作スキルを習得できるように、定期的なトレーニングとスキル向上コースが開催されます。
- 各オペレーターが厳格なスキル評価を受けることを保証するために、オペレーター資格認定制度を導入します。
環境管理
温度と湿度の制御
- 周囲温度が高すぎたり低すぎたりすると、レーザーの安定性に影響し、マーキング効果に影響します。湿度が高すぎると、機器の故障や材料表面の損傷を引き起こす可能性があります。
- レーザー マーキング スタジオでは、レーザー ジェネレータと材料が理想的な動作状態になるように、安定した温度と湿度を維持する必要があります。
清潔に保つ
- 作業環境は、ほこり、油、または破片が機器に入らないように、清潔で整頓された状態に保つ必要があります。作業場、特に光学部品が配置されているエリアを定期的に清掃し、マーキングの品質に影響を与える汚染物質がないことを確認してください。
最適化の提案
- 作業場に温度と湿度を制御するシステムを設置し、環境条件を定期的にチェックして、温度と湿度を推奨範囲内に保ってください。
- 作業場の空気を新鮮に保ち、ほこりがたまらないように作業場を定期的に清掃してメンテナンスしてください。
レーザーマーキングの品質は多くの要因の影響を受けます。パラメータの最適化、材料の正確な準備、定期的な機器メンテナンス、オペレーターのトレーニング、厳格な環境管理により、欠陥を減らし、生産効率と顧客満足度を向上させることができます。これらの最適化対策により、マーキングプロセスの高い精度と長期的な安定性を確保し、企業が競争から際立つことに役立ちます。
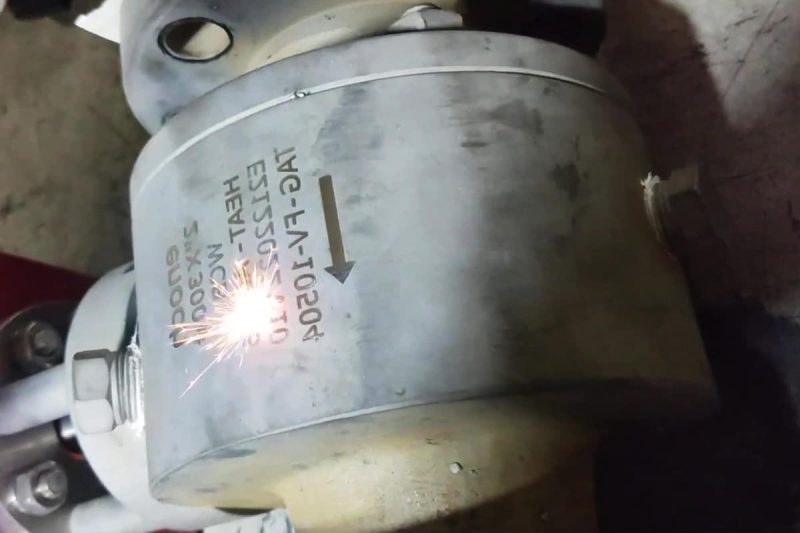
要約する
レーザーマーキング技術は現代の製造業で重要な役割を果たしていますが、実際の応用では、焼け跡、不完全なマーキング、表面損傷などの欠陥によく遭遇します。これらの問題は、レーザー機器の選択を最適化し、パラメータ設定を調整し、定期的にメンテナンスを行い、オペレーターを専門的にトレーニングすることで効果的に軽減できます。合理的な機器の選択と正確なパラメータ設定により、一般的な欠陥を回避できるだけでなく、マーキングの品質を向上させ、各製品の外観とロゴが明確で一貫していることを保証し、ブランドイメージと市場競争力を高めることができます。
これらの最適化措置により、レーザーマーキングの品質が向上し、製品の外観が向上するだけでなく、顧客満足度も効果的に向上します。高品質のレーザーマーキングは、製品の魅力を高めるだけでなく、顧客のブランドロイヤルティを強化し、企業が激しい市場競争で際立って、より多くの顧客と市場シェアを獲得するのに役立ちます。
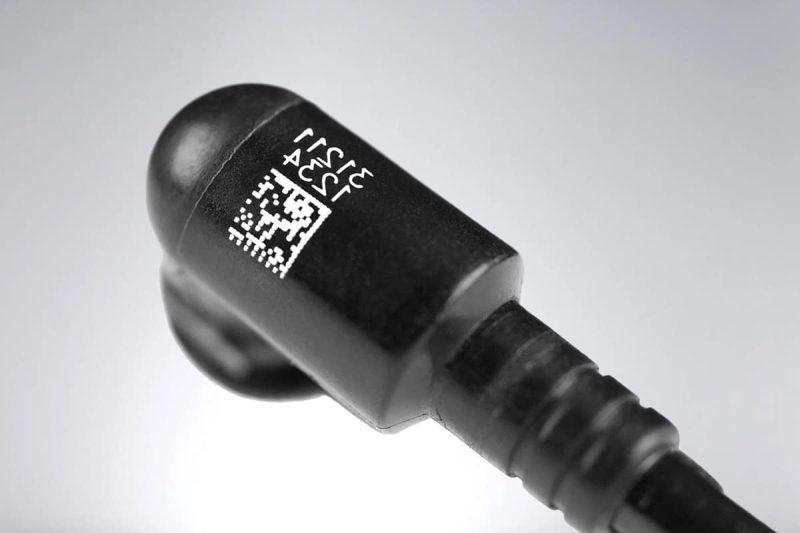
レーザー ソリューションを入手する
効率的なレーザーソリューションをお探しなら、 AccTek レーザー は、お客様の独自のニーズを満たすために、専門的なレーザー技術コンサルティングとカスタマイズされたサービスを提供しています。機器の選択、パラメータの最適化、特定のアプリケーションケースの参照など、当社の専門家チームは、最良の処理結果を達成するための詳細なガイダンスを提供できます。
レーザー マーキング、レーザー溶接、その他のレーザー アプリケーションについて詳しくは、今すぐお問い合わせください。当社のコンサルティング サービスでは、レーザー テクノロジーの応用において貴社の競争力を維持するためのカスタマイズされたソリューションをご提供します。
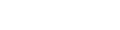
連絡先
- [email protected]
- [email protected]
- +86-19963414011
- No. 3 ゾーン A、Lunzhen 工業地帯、玉城市、山東省。
レーザー ソリューションを入手する