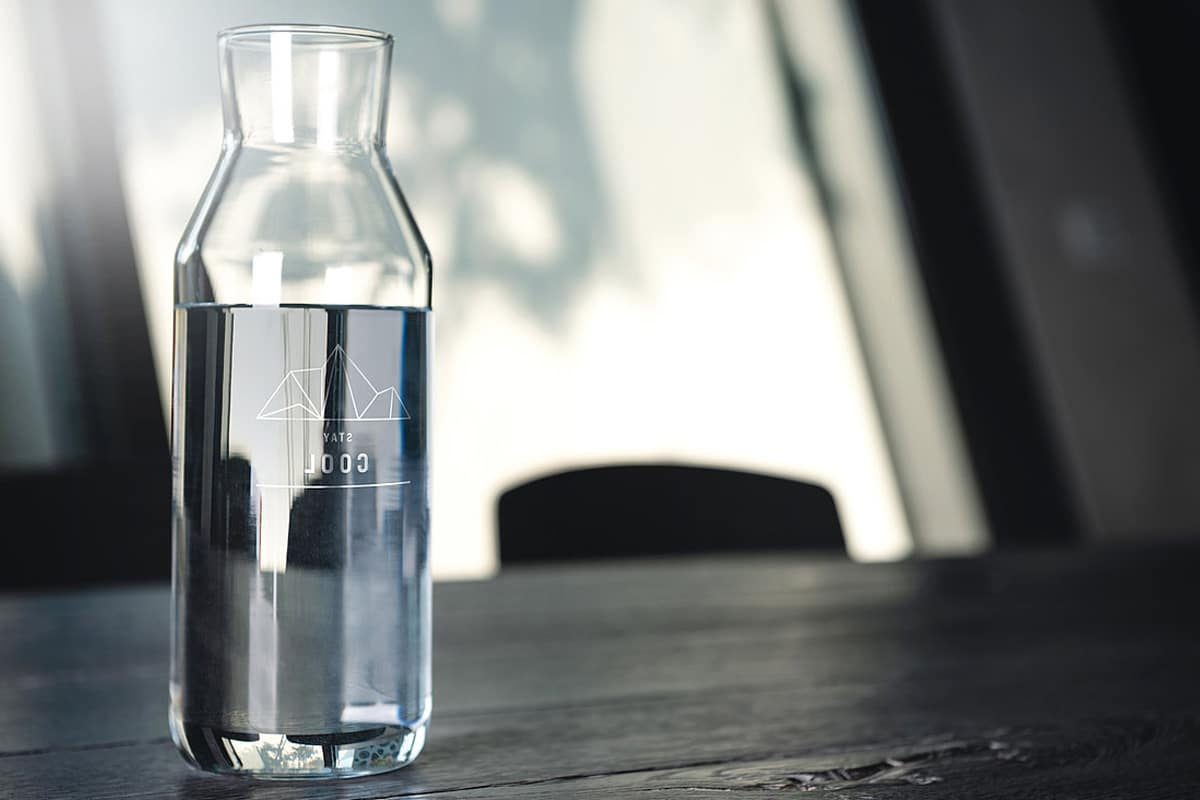
レーザーマーキングの品質に影響を与える要因は何ですか?
レーザーマーキングは、電子、医療、自動車など多くの業界で広く使用されている高精度の加工技術です。材料の表面にレーザービームを作用させて永久的なマークを生成します。従来のマーキング方法と比較して、レーザーマーキングには非接触、無公害、高速、高精度などの利点があります。
しかし、マーキングの品質はレーザー機器自体に依存するだけでなく、多くの要因によっても左右されます。まず、異なるタイプのレーザー光源(ファイバーレーザー、CO2レーザー、UVレーザーなど)は、異なる材料への適応性が異なります。たとえば、ファイバーレーザーは金属材料に適しており、CO2レーザーは非金属材料に適しています。UVレーザーは冷光特性のため、熱に弱い材料に適しています。次に、吸収率、反射率、熱伝導率などの材料の特性がレーザーマーキングの効果に影響します。表面粗さやコーティングの違いも、マーキングの鮮明さに影響します。さらに、レーザーパラメータの設定(出力、マーキング速度など)、環境条件、オペレーターの経験レベルも、マーキングの品質を決定する重要な要素です。これらの要素を総合的に考慮することによってのみ、レーザーマーキングの最良の効果を確保できます。
目次
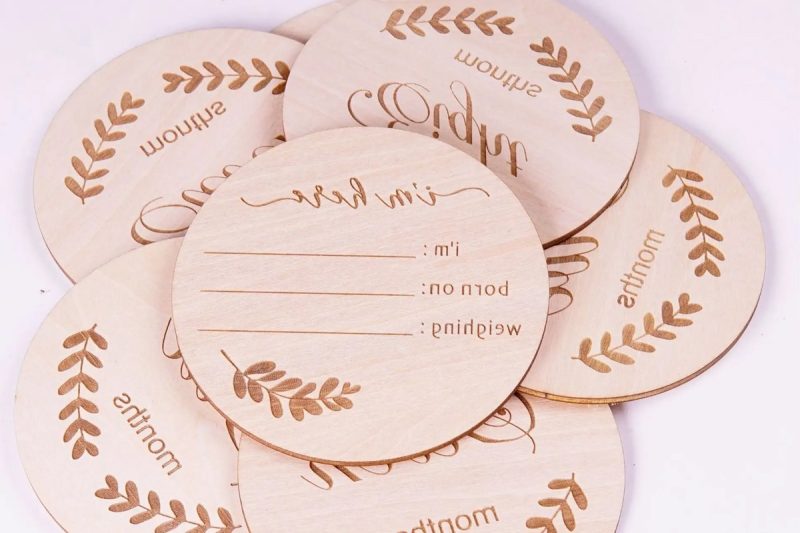
レーザーの種類と光源
レーザーの種類と光源は、レーザー マーキングの品質に影響を与える重要な要素の 1 つです。レーザーの種類によって、材料への適応性やマーキング効果の点で特性が異なります。適切なレーザーの種類を選択すると、マーキングの効率と品質が大幅に向上します。一般的なレーザーの種類には、主に次のものがあります。
- ファイバーレーザー: 高いエネルギー密度と優れた集束特性を備えたファイバーレーザージェネレーターは、金属材料、特に鋼、アルミニウム、銅などの材料のマーキングに非常に適しています。 ファイバーレーザーマーキング 非常に高い精度を実現できるため、電子部品、医療機器、自動車部品のマーキングなど、非常に微細なパターンやテキストを必要とする高精度のアプリケーションでよく使用されます。また、ファイバーレーザーはエネルギー消費量が少なく、耐用年数が長いため、金属マーキングの第一選択肢となっています。
- CO2レーザー:CO2レーザーは主に非金属材料のマーキングに使用され、特に木材、プラスチック、皮革、紙などの材料に使用されます。波長は10.6ミクロンで、非金属材料のエネルギーを効率的に吸収できるため、包装、衣類、手工芸品などの業界で広く使用されています。 CO2レーザーマーキング 広告制作、家具装飾、模型製造にも優れています。
- 紫外線(UV)レーザー:UVレーザーは波長が短い(通常355nm)ため、冷光源と呼ばれます。他のレーザータイプと比較して、UVレーザーは熱影響部が非常に小さいため、マーキングプロセス中に材料の熱変形と損傷が大幅に減少します。これにより、特にガラス、プラスチック、セラミックなどの熱に敏感な材料への微細マーキングに非常に適しています。UVレーザーマーキングは、電子製品、化粧品パッケージ、医薬品ラベルなどの高精度産業でよく使用され、非常に細かく鮮明なマーキング効果を実現できます。
要約すると、適切なレーザーの種類とソースを選択すると、特定の材料とアプリケーションの要件に基づいて、一貫性のある正確なマーキング品質を確保できます。
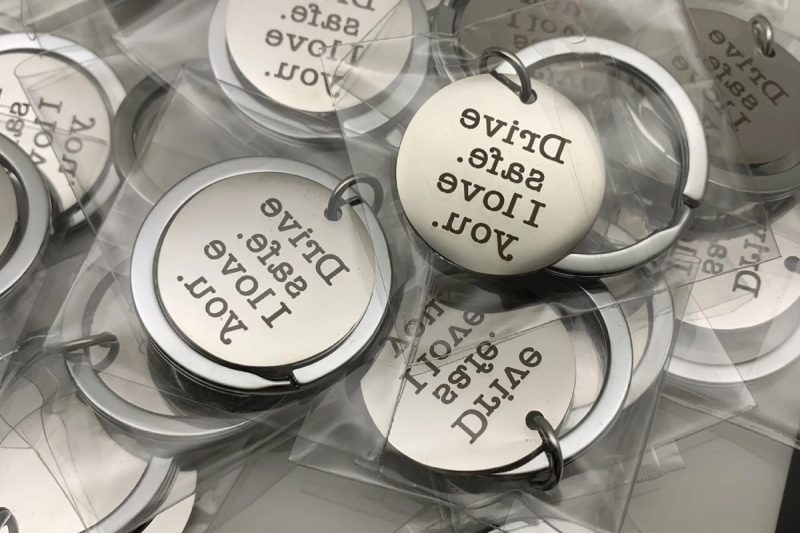
材料特性の影響
材料特性は、レーザー マーキングの効果に影響を与える重要な要素の 1 つです。材料の物理的および化学的特性によって、レーザーの吸収、散乱、反射など、レーザーに対する反応が決まります。以下は、いくつかの主要な材料特性と、それらがレーザー マーキングの品質に及ぼす具体的な影響です。
- 吸収と反射率:材料は、異なる波長のレーザーに対して異なる吸収力と反射力を持っています。吸収率の高い材料はレーザーエネルギーをよりよく吸収し、より良いマーキング効果を生み出しますが、反射率の高い材料は大量のレーザー光を反射し、マーキング効率を低下させます。たとえば、アルミニウムや銅などの金属材料はファイバーレーザーに対して高い反射率を持ち、マーキングが不十分または不明瞭になる可能性があります。このため、これらの高反射率材料にマーキングする場合、理想的なマーキング効果を得るためには、通常、レーザーパラメータを調整するか、特定の波長のレーザーを使用して吸収率を高める必要があります。対照的に、プラスチックやガラスなどの非金属材料は、CO2レーザーやUVレーザーに対して高い吸収率を持ち、マーキングの深さとコントラストを制御しやすくなります。
- 熱伝導率:材料の熱伝導率は、マーキングプロセス中の熱分布に直接影響します。銅、アルミニウム、その他の金属などの熱伝導率の高い材料は、マーキングプロセス中に発生した熱をすばやく分散させ、局所的な過熱を減らし、材料表面の溶解や燃焼を回避できます。このような材料では、通常、レーザーマーキング中にレーザー出力を増やすか、マーキング時間を延長して、マーキング領域に十分なエネルギーが適用されるようにします。プラスチックや木材などの熱伝導率の低い材料の場合、熱がすぐに拡散しにくく、マーキングプロセス中に過熱が発生して変形や損傷が発生する可能性があります。したがって、このような材料を加工する場合は、通常、レーザー出力を下げるか、冷却対策を強化して過熱を回避する必要があります。
- 表面状態: 材料の表面状態もマーキング効果に重要な影響を与える可能性があります。滑らかで清潔な表面は、レーザーが均一に作用し、明確で一貫したマーキング パターンを生成します。ただし、粗い表面やコーティングされた表面では、レーザー エネルギーの分布が不均一になり、マーキングが不明瞭になったり、コントラストが不十分になったりする可能性があります。コーティングの厚さと均一性は特に重要です。コーティングが不均一な場合、レーザーは領域ごとに異なる効果を生み出す可能性があり、マーキングに一貫性がなくなります。マーキング前に、クリーニング、研磨、コーティングなどの適切な表面処理を行うと、マーキング効果が大幅に向上します。
つまり、材料の吸収率、反射率、熱伝導率、表面状態は、レーザー マーキングの深さ、鮮明度、コントラストに直接影響します。これらの材料特性を理解し、適切に調整することで、レーザー マーキング プロセスを最適化し、最終的なマーキング品質が期待どおりの効果を達成できるようになります。
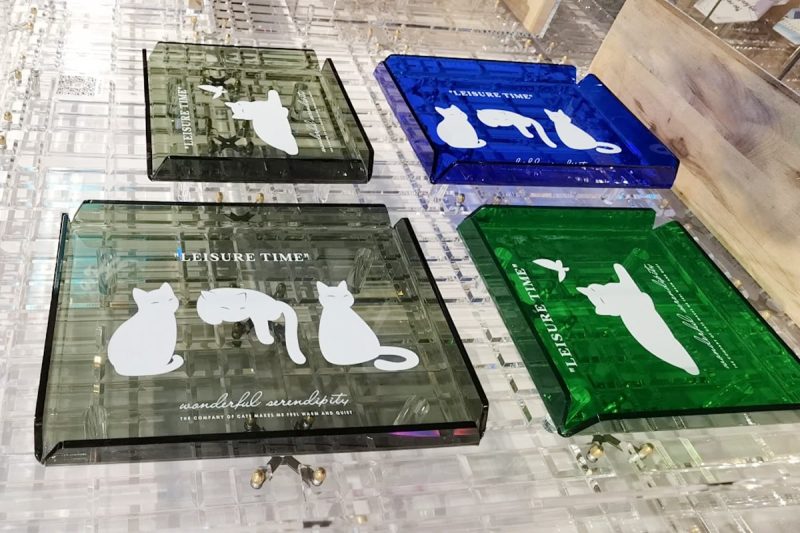
レーザーパラメータの影響
レーザー パラメータの設定は、レーザー マーキングの品質にとって非常に重要です。レーザー パラメータを正しく調整することで、最高のマーキング効果が得られます。これらのパラメータは、マーキング プロセスの速度と効率を決定するだけでなく、マーキングの鮮明度、深さ、コントラストにも直接影響します。次に、いくつかの重要なレーザー パラメータと、マーキングにおけるその役割を示します。
- 出力設定:レーザー出力は、マーキングの深さと効果に影響を与える重要な要素です。出力設定が高すぎると、レーザーエネルギーが大きすぎて、特にプラスチックや薄い金属などの熱に敏感な材料の場合、材料表面の過度のアブレーション、溶融、または変形が簡単に発生する可能性があります。また、出力が高すぎると、マーキングのエッジが粗く不均一になり、全体的な外観に影響を与える可能性があります。出力が低すぎると、レーザーエネルギーが不十分で、材料表面に効果的に作用できず、マーキングが不明瞭になったり、識別が困難になったりします。したがって、材料の特性とマーキングの特定の要件に応じて出力設定を正確に調整し、材料表面を損傷することなく十分なマーキング深さを実現できるようにする必要があります。
- パルス周波数: パルス周波数は、レーザー ジェネレーターが 1 秒間に放出するパルスの数を指し、マーキングの速度と表面品質に重要な影響を及ぼします。パルス周波数が高いほど、レーザー エネルギーがより均等に分散されるため、より滑らかなマーキング表面が生成され、細かいマーキングが必要な用途に適しています。ただし、周波数が高すぎると、レーザー エネルギーが分散しすぎて、マーキングの深さとコントラストに影響する可能性があります。パルス周波数が低いと、レーザー エネルギーがより集中するため、より深いマーキングが必要なシーンに適していますが、表面にわずかな粗さが生じる可能性があります。したがって、さまざまな材料とマーキング要件に応じて、適切なパルス周波数を選択することで、深さと表面仕上げのバランスをとることができます。
- マーキング速度:マーキング速度とは、レーザーが材料の表面を移動する速度を指し、マーキングの深さ、効率、効果に直接影響します。マーキング速度が速いほど生産効率が向上し、大規模な加工ニーズに適しています。ただし、速度が速くなると、レーザーが材料上に留まる時間が短くなり、マーキングの深さも浅くなり、マーキングの鮮明度とコントラストに影響を与える可能性があります。深いマーキングやより高い精度が必要なアプリケーションでは、通常、レーザーが材料と効果的に相互作用するのに十分な時間を確保するために、マーキング速度を下げる必要があります。速度設定では、マーキング要件と材料の特性を総合的に考慮して、効率と品質のバランスをとる必要があります。
- 焦点距離調整:レーザー焦点距離の精度は、マーキングの品質に非常に重要です。焦点距離とは、レーザービームと材料の表面との間の距離を指します。最適な焦点距離ではレーザーエネルギーが集中し、材料の表面に鮮明で正確なマーキング効果を生み出すことができます。焦点距離が正しく調整されていないと、レーザービームのエネルギーが分散され、ぼやけて焦点が合っていないマーキングが発生し、鮮明なパターンやテキストを実現することはできません。特に微細なマーキングでは、焦点距離のわずかなずれでも最終的な効果に大きな影響を与えます。マーキング前に機器の焦点を定期的に調整し、焦点距離の精度を確認することは、マーキング効果の一貫性を確保するための重要なステップです。
一般的に、高品質のレーザー マーキング結果を得るには、レーザー パラメータを正しく設定することが重要です。出力、パルス周波数、マーキング速度、焦点距離を適切に調整することで、マーキングの鮮明度、深さ、コントラストを効果的に向上させることができ、さまざまな材料や用途でレーザー マーキングが最高のパフォーマンスを発揮できるようになります。
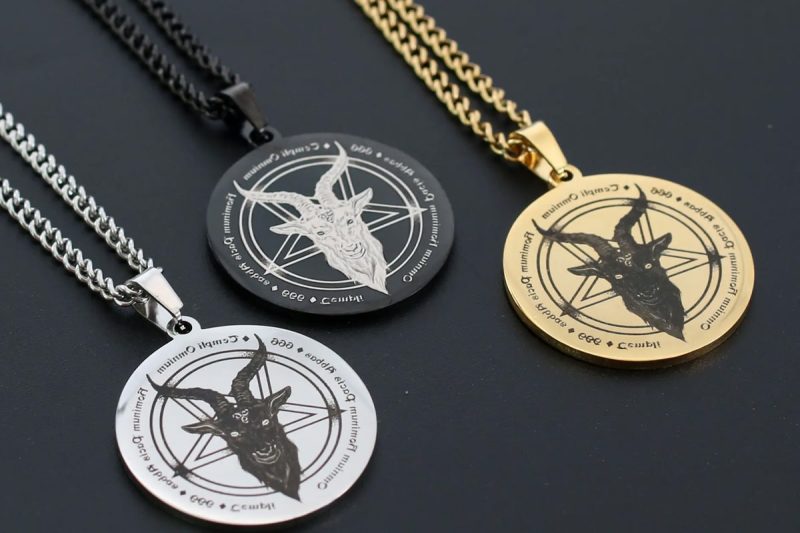
環境条件の影響
レーザーマーキングマシンの性能は外部環境の温度、湿度、清潔さに非常に敏感であるため、環境条件はレーザーマーキングプロセスにおいて重要な役割を果たします。適切な環境条件は、機器の安定性とマーキング効果の品質を確保するのに役立ちますが、不利な環境要因は、マーキングの不安定化や精度の低下などの問題につながる可能性があります。以下は、レーザーマーキングの品質に影響を与える主な環境条件です。
- 温度:周囲温度はレーザーマーキングマシンの動作状態に直接影響します。温度が高すぎると、機器内部、特にレーザー光源と電子部品が過熱する可能性があります。過熱すると、機器の作業効率が低下し、故障や損傷を引き起こすこともあります。また、高温環境ではレーザー発生器の出力が不安定になり、マーキングプロセス中にレーザービームの強度が変動し、マーキングの一貫性と鮮明さに影響する可能性があります。逆に、温度が低すぎると、機器の起動と正常な動作にも影響し、特に寒冷地や寒冷な季節では、レーザー発生器が温まるまでに時間がかかることがあります。したがって、機器の周囲温度をメーカーの推奨範囲(通常は15°C〜30°C)に維持することが、レーザーマーキングマシンの安定した動作を確保するための鍵となります。
- 湿度:過度の湿度は、レーザーマーキング装置の性能に影響を与えるもう一つの大きな隠れた危険です。湿度の高い環境では、レンズ、レンズ、その他の重要な部品など、レーザーマーキングマシンの光学部品が湿気を帯びる可能性があります。これらの光学部品が湿っていると、レーザービームは伝送中に散乱して減衰し、マーキング効果が不明瞭になったりぼやけたりします。また、湿度が高いと、装置内部の酸化や腐食が加速し、装置の寿命が短くなる可能性があります。湿度の問題を回避するには、特に雨季や湿気の多い地域では、湿度管理が良好な環境にマーキング装置を設置する必要があります。光学部品や装置が濡れないように、除湿器などの装置を使用して周囲の湿度を40%〜60%に保つことをお勧めします。
- 清潔さ:作業環境の清潔さは、レーザーマーキングの精度と品質に大きな影響を与えます。ほこり、汚れ、油汚れなどの粒子がマーキング材料の表面や機器の光学部品に付着すると、レーザービームの透過率や焦点距離の精度が妨げられ、マーキングの鮮明度とコントラストが低下します。生産環境、特に工業現場では、空気中に多くのほこり粒子が存在し、レーザービームと材料の表面との相互作用に影響を与え、マーキングが不均一になる可能性があります。最高のマーキング効果を確保するには、機器、特にレンズと光学部品を定期的に清掃し、マーキング材料の表面を清潔でほこりのない状態に保つことをお勧めします。清掃プロセス中は、適切な清掃ツールと方法を使用して、光学部品を傷つけたり、材料の表面を損傷したりしないようにします。
つまり、環境の温度、湿度、清潔さを適切に管理することが、レーザー マーキング マシンの性能とマーキング品質にとって極めて重要です。適切な環境条件下で機器を稼働させ続けることで、マーキングの精度と安定性が向上するだけでなく、機器の耐用年数が延び、生産プロセスの一貫性と信頼性が確保されます。
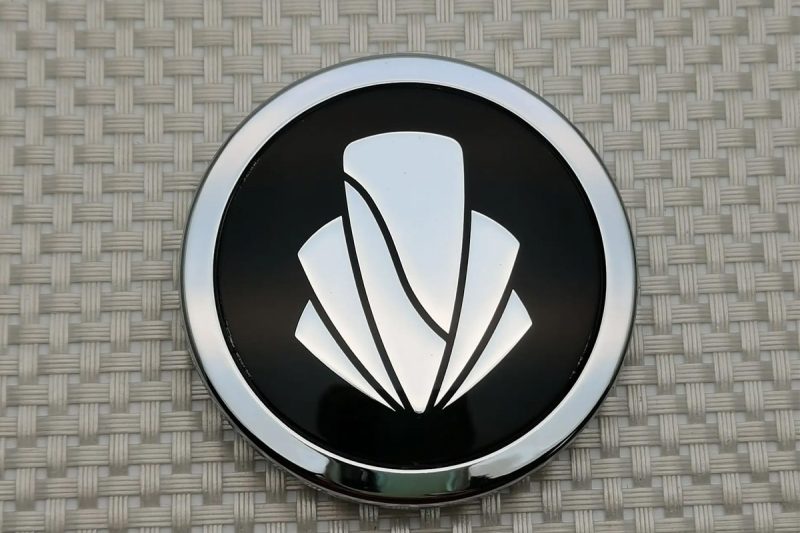
光学部品の影響
光学部品はレーザーマーキングマシンで重要な役割を果たします。光学部品はレーザービームの伝送効率とマーキング品質に直接影響します。高品質の光学部品は、レーザービームが材料表面に最大限の精度と効率で作用することを保証し、鮮明で精細なマーキング効果を実現します。以下は、光学部品がレーザーマーキング品質に与える影響の重要な側面です。
- レンズの品質:レンズはレーザーシステムの中で最も重要な光学部品の一つです。その機能はレーザー光線を集束させ、材料の表面に正確に投影することです。レンズ表面に傷やほこり、不十分な光学性能など、レンズの品質が悪いと、レーザー光線は集束プロセス中に逸れたりエネルギーを失ったりして、マーキングの精度と鮮明さに影響を及ぼします。品質の悪いレンズは、マーキングのぼやけ、焦点が合わない、エネルギー分布が不均一になる可能性があり、特に微細加工が必要な場合、マーキング効果が粗く不均一に見えます。したがって、高品質の光学レンズを選択し、定期的に清掃してメンテナンスし、安定した光学性能を確保することが、マーキング精度を確保するための鍵となります。
- ビーム伝送システム: ビーム伝送システムは、レーザーをレーザー光源からマーキング材料の表面に伝送する役割を担っています。このプロセスでは、レーザーのエネルギーは、エネルギー損失やビーム散乱なしに効率的に伝送されなければなりません。伝送プロセス中に損失があると、レーザーの強度と集束効果に影響し、マーキング深度が不十分になったり、鮮明度が低下したりします。ビーム伝送の効率を確保するには、反射鏡や伝送光ファイバーなど、伝送システムのさまざまなコンポーネントを非常に清潔で無傷に保つ必要があります。光学コンポーネントにほこりや汚れ、損傷があると、ビームが散乱して反射が悪くなり、マーキング結果に影響します。効率的で損失のないビーム伝送システムは、マーキングプロセスの安定性と一貫性を確保し、毎回理想的な効果を達成できるようにします。
- ガルバノスキャナ:ガルバノスキャナは、レーザービームの高速移動と正確な位置決めを制御する重要なコンポーネントであり、マーキングパターンの速度、精度、一貫性を直接決定します。ガルバノスキャナは、高速リフレクタを介してレーザービームの方向を調整し、材料の表面に必要なパターンまたは文字を描画します。そのスキャン速度と精度は、マーキング効果にとって特に重要です。高精度のガルバノスキャナは、複雑なパターンや小さなパターンでレーザービームを正確に配置して、線やパターンの偏差を回避できます。高速ガルバノスキャナはマーキング効率を向上させることができ、大量生産のニーズに適しています。ただし、スキャン速度が速すぎると、エネルギー分布が不均一になり、マーキングの深さとコントラストに影響を与える可能性があります。したがって、速度を確保しながら、ガルバノメータの精度が妥当な範囲内にとどまるようにすることも必要です。ガルバノスキャナの品質と性能は、マーキング効果の安定性に不可欠です。したがって、高速スキャンでも正確なマーキング効果を維持できるように、高性能のガルバノメータ システムを選択して校正し、定期的にメンテナンスする必要があります。
一般的に、光学部品の品質と性能は、レーザーマーキングの最終的な効果を直接決定します。高品質のレンズ、ロスレスビーム伝送システム、および精密なガルバノメータースキャナーは、レーザーマーキングプロセスの精度と効率を保証するための重要な要素です。これらの光学部品を維持および最適化することで、企業はさまざまな材料やアプリケーションの微細マーキングのニーズを満たす一貫した高品質の出力を確保できます。
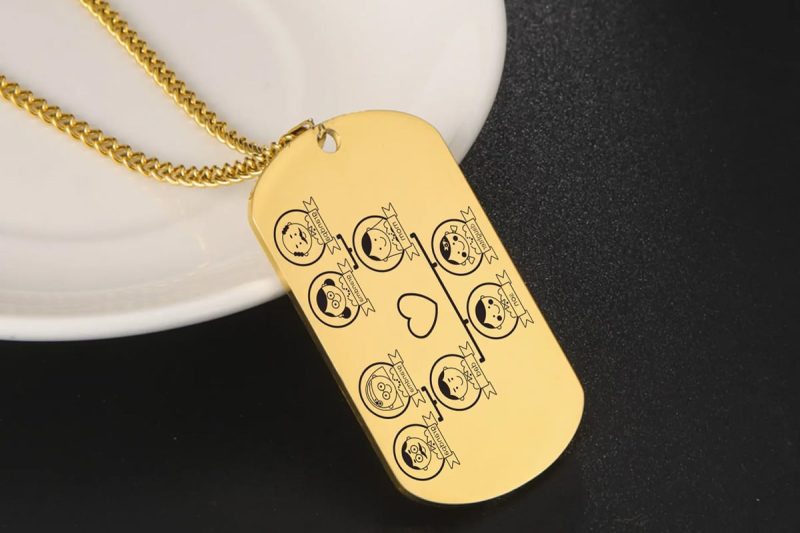
ソフトウェアと制御システムの影響
ソフトウェアと制御システムはレーザー マーキング プロセスで中心的な役割を果たし、マーキングの精度、効率、一貫性を確保するための鍵となります。高品質のマーキング ソフトウェアと高度な制御システムは、オペレーターがレーザー ジェネレーターのさまざまなパラメーターを正確に制御し、効率的な自動化生産プロセスを実現するのに役立ちます。ソフトウェアと制御システムがレーザー マーキングの品質に与える具体的な影響は次のとおりです。
- マーキングソフトウェア:マーキングソフトウェアは、レーザーマーキング機器を制御するための重要なツールです。レーザー出力、マーキング速度、パルス周波数などのレーザージェネレータパラメータの設定と調整を担当します。高品質のソフトウェアは、これらの重要なパラメータを正確に制御できるだけでなく、パターン設計、フォント選択、バーコードとQRコードの生成などの豊富なマーキング機能も提供できます。さらに、マーキングソフトウェアは、金属、プラスチック、ガラスなどの材料への高精度で異なる深さのマーキングなど、マルチレベルのマーキングを実現し、さまざまな材料のさまざまな処理要件をサポートできます。高度なマーキングソフトウェアは通常、ユーザーフレンドリーなインターフェイスを備えており、操作プロセスを簡素化し、オペレーターがシステムをすばやく理解して習得できるようにし、人為的な操作エラーを減らし、生産効率とマーキング品質を向上させます。同時に、ソフトウェアのアップグレード可能性も非常に重要です。技術の発展と市場の需要の変化に伴い、マーキングソフトウェアは新しいマーキング要件に適応するために継続的に更新および最適化する必要があります。
- モーションコントロールシステム:モーションコントロールシステムは、レーザーマーキングマシンでレーザーヘッドとワークピースの協調動作を制御するために使用されるコアコンポーネントです。マーキングプロセス中に、レーザーヘッドと処理対象のワークピースを正確に同期させ、レーザービームが設定された軌道に従って材料表面上を移動できるようにします。この同期は、マーキングパターンの一貫性と精度を実現するために不可欠です。モーションコントロールシステムには、通常、モーター、センサー、コントローラーなどのハードウェアが含まれ、マーキングソフトウェアと連携してリアルタイムの監視と調整を行います。高精度のマーキングでは、特に複雑なパターンを材料の広い領域にマーキングする必要がある場合、モーションコントロールシステムの精度と応答速度が特に重要です。モーションコントロールシステムの感度が十分でない場合、レーザーマーキングヘッドがずれて、パターンの変形や線の不均一などの問題が発生する可能性があります。したがって、安定した効率的なモーションコントロールシステムは、レーザーマーキングの一貫性と鮮明さを確保するための重要な要素の1つです。
- 自動化:高度に自動化されたレーザーマーキングシステムは、生産効率を大幅に向上させ、人的操作のエラーを減らし、製品の各バッチが一貫したマーキング効果を得られることを保証できます。自動化された制御システムを導入することで、レーザーマーキング装置を生産ラインにシームレスに接続し、バッチおよび連続マーキング操作を実現できます。たとえば、自動化システムは、ワークピースを自動的に識別して配置し、レーザーマーキングヘッドの高さと焦点距離を調整し、各マーキングが最適な条件で実行されるようにします。自動化システムは、人間の介入なしに異なるバッチのマーキングパターンとパラメータを自動的に変更することもできるため、生産の柔軟性が大幅に向上します。さらに、自動化システムを他の工場管理システムに接続して、生産データのリアルタイム監視と分析を実現し、企業が生産プロセスを最適化し、製品の品質を向上させ、コストを削減するのに役立ちます。自動化されたマーキングシステムは、特に需要が高く大量生産の環境では、オペレーターの関与を減らし、人件費を削減することもできます。
一般的に、ソフトウェアと制御システムはレーザーマーキング装置の「頭脳」であり、マーキングの精度、効率、操作性に直接影響します。高品質のマーキングソフトウェアは、細かい制御と豊富なマーキング機能を提供できるだけでなく、操作を簡素化し、自動化の程度を向上させることができます。同時に、高度なモーション制御システムはレーザーマーキングの精度と一貫性を確保し、自動化技術は生産効率を大幅に向上させ、人間の介入のリスクを軽減します。ソフトウェアと制御システムを最適化することで、企業は複雑なマーキングのニーズにうまく対応し、全体的な生産性と製品品質を向上させることができます。
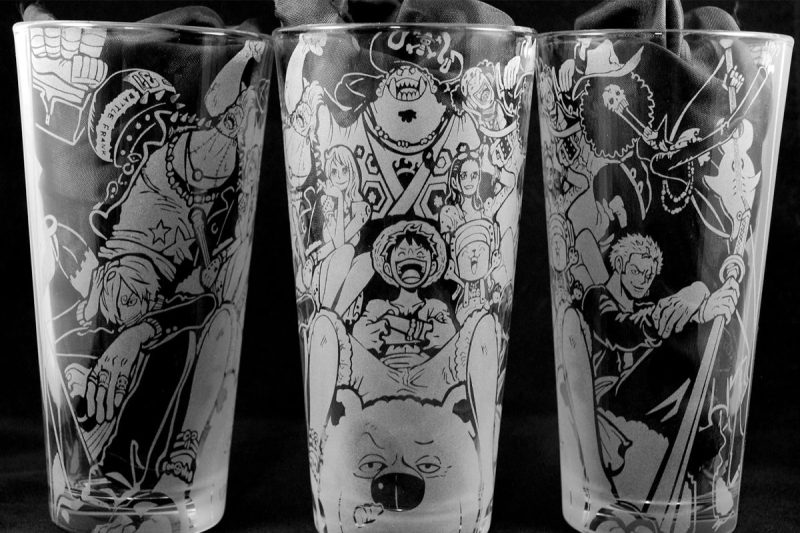
冷却システムの効果
冷却システムはレーザーマーキング装置において重要な役割を果たします。冷却システムは装置の全体的な安定性に影響を与えるだけでなく、装置の耐用年数と性能にも直接関係します。レーザーマーキングマシン、特に高出力レーザージェネレーターは動作中に大量の熱を発生します。熱がタイムリーかつ効果的に放散されない場合、装置が過熱し、マーキング精度やレーザー出力の安定性に影響を与え、装置が損傷する可能性もあります。したがって、適切な冷却システムを選択することは、装置の正常な動作にとって非常に重要です。
- 空冷:空冷システムは、一部の小型ファイバーレーザーマーキングマシンなどの低出力レーザー機器によく使用されます。この冷却方法は、ファンなどの空気循環装置を介してレーザージェネレーターやその他の主要コンポーネントから熱を取り除きます。空冷システムは構造がシンプルでメンテナンスコストが低いため、放熱要件が低いアプリケーションシナリオに適しています。空冷システムは、設置面積が小さく、設計がコンパクトであるという利点があります。通常、外部冷却装置を必要とせずに機器に統合されます。そのため、容積が限られた小型レーザーマーキングマシンで広く使用されています。ただし、空冷の放熱効果は比較的弱く、高出力レーザージェネレーターによって発生する大量の熱に対処できません。高出力機器を空気で冷却すると、熱が蓄積され、レーザージェネレーターの性能と寿命に影響を与える可能性があります。したがって、空冷システムは主に、低出力で放熱要件が低いレーザー機器に適しています。
- 水冷システム:空冷と比較して、水冷システムは高出力レーザーマーキング装置に適しており、特に長期連続運転が必要な場合、より効果的な放熱を提供できます。水冷システムは、水ポンプを介して冷却剤(通常は水または冷却剤)をレーザー発生器およびその他の発熱部品の近くに循環させ、水の効率的な熱伝達によって熱をすばやく除去します。空冷と比較して、水冷システムは熱容量と伝導効率が高く、高温環境または高強度作業条件で装置が安定した動作を維持できることを保証し、レーザー発生器の過熱による出力減衰またはマーキング品質の低下を回避できます。さらに、水冷システムは温度変動を制御し、レーザー発生器が常に最適な温度範囲内で動作することを保証できるため、装置の耐用年数が延びます。
水冷システムは放熱性能の点で空冷システムより優れていますが、構造が比較的複雑で、追加の水タンク、ポンプ、パイプなどの設備が必要であり、また、定期的な冷却剤の交換とメンテナンスも必要です。そのため、水冷システムのコストとメンテナンス要件は比較的高くなります。ただし、高精度で高強度のマーキングが必要なシナリオでは、水冷システムが機器の長期にわたる安定した動作を確保するための最良の選択です。高出力ファイバーレーザー発生器やCO2レーザー発生器などのマーキング機器でよく使用されます。特に金属マーキングや大面積マーキングのタスクでは、水冷システムによりレーザーマーキングの効果と効率が大幅に向上します。
一般的に、冷却システムはレーザーマーキング装置の不可欠な構成要素であり、装置の動作性能と耐用年数に直接影響します。空冷システムは低電力でコンパクトな装置に適していますが、水冷システムは高電力装置用に設計されており、高強度の作業条件下でより効率的な放熱を提供できます。レーザーマーキング装置を選択する場合、企業はマーキング要件と装置の電力に応じて適切な冷却システムを選択し、装置が理想的な状態で動作し、最高のマーキング効果が得られるようにする必要があります。
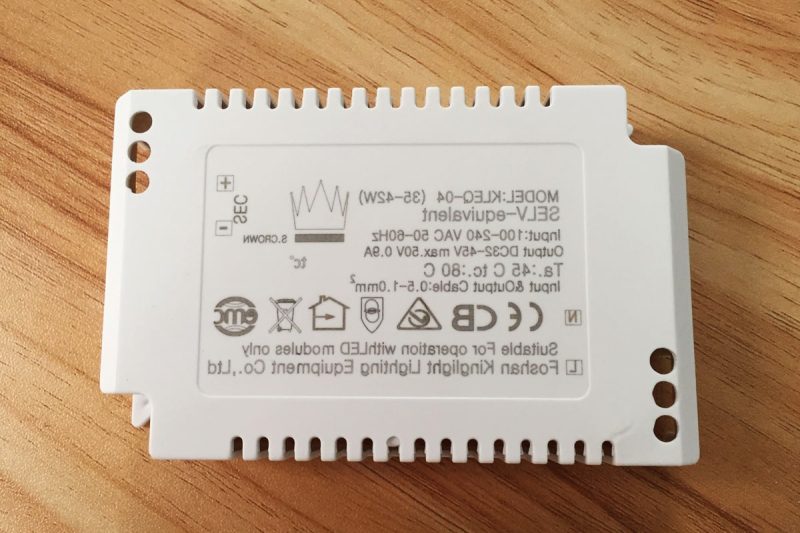
オペレーターのスキルとトレーニング
オペレーターのスキルレベルとトレーニングは、レーザーマーキングプロセスにおいて重要な役割を果たし、マーキングの精度、効率、最終効果に直接影響します。レーザーマーキングマシンの技術はますます進歩し、自動化の程度は徐々に向上していますが、オペレーターの専門知識と操作スキルは、機器の効率的な操作と安定したマーキング品質を確保するための重要な要素です。オペレーターのスキルとトレーニングがマーキング品質に与える具体的な影響は次のとおりです。
- 専門知識:レーザーマーキングのオペレーターは、確かな専門知識、特にさまざまな材料特性とレーザーパラメータに関する知識を持っている必要があります。材料によってレーザーの吸収率、反射率、熱伝導率が異なるため、オペレーターは材料の特性に応じて、レーザー出力、マーキング速度、パルス周波数などのレーザーパラメータを適切に調整する必要があります。たとえば、金属材料には通常、より高出力のファイバーレーザージェネレータが必要ですが、プラスチックやガラスなどの非金属材料には、UVレーザーまたはCO2レーザージェネレータの方が適している場合があります。オペレーターが材料特性とレーザージェネレータの種類に関する十分な知識を持っていない場合、満足のいくマーキング結果が得られなかったり、深さが不均一になったり、ぼやけたり、焼けたりする可能性があります。体系的なトレーニングを通じて、オペレーターはさまざまな材料のマーキング要件を習得し、各マーキングで最良の結果が得られるようにすることができます。
- 校正とメンテナンス:レーザーマーキング装置は、長期使用中にレンズ、ガルバノメーター、ビーム伝送システムなどの主要部品の摩耗や偏差が発生する可能性があります。したがって、装置のビーム品質とマーキング精度が常に最良の状態になるようにするには、定期的な装置の校正とメンテナンスが不可欠です。オペレーターは、問題を迅速に検出して解決するために、装置の日常的な検査と簡単なトラブルシューティングを実行する能力を持っている必要があります。たとえば、レーザージェネレーターの電力減衰、ガルバノメータースキャンの精度の低下、光学部品の汚染は、マーキング効果に影響を与えます。十分に訓練されたオペレーターは、定期的に装置を校正して、レーザーマーキング装置の安定した動作を確保し、装置の故障やパラメータの偏差による生産停滞や品質低下を減らすことができます。さらに、メンテナンスは装置の耐用年数を延ばすだけでなく、予期しないダウンタイムや重大な故障を回避し、修理コストを削減することもできます。
- 操作の熟練度と安全意識:レーザーマーキング装置の操作は簡単になりましたが、装置を効率的に操作するには、オペレーターが一定レベルの熟練度を持っている必要があります。オペレーターは、マーキングパスの設定、焦点距離の調整、適切なマーキング速度とパワーの選択など、職場でのさまざまなマーキングタスクの操作手順を習得する必要があります。熟練したオペレーターは、さまざまなマーキングニーズに合わせてパラメータをすばやく判断して調整できるため、生産効率が向上します。さらに、オペレーターは一定レベルの安全意識も持っている必要があります。レーザー装置は、操作中にレーザー放射や発熱など、特定の安全上の危険を伴う場合があります。専門的なトレーニングを受けたオペレーターは、不適切な操作による安全上の問題を効果的に回避し、生産環境の安全を確保できます。
- 継続的な学習と技術の更新:レーザーマーキング技術は絶えず更新されており、新しいマーキング機器やソフトウェア機能もリリースされています。そのため、オペレーターは新しい技術を継続的に学習して適応し、トレーニングを通じて新しいレーザージェネレーターとマーキングソフトウェアの操作を習得し、最新のプロセス改善を理解する必要があります。オペレーターの継続的な学習は、企業が競争力を維持し、マーキングの効率と製品品質を向上させ、変化する市場の需要を満たすのに役立ちます。
つまり、レーザーマーキング装置の安定した操作とマーキング品質を確保するには、オペレーターのスキルレベルとトレーニングが重要です。専門的なトレーニングを通じて、オペレーターはさまざまな材料のマーキングパラメータ設定を習得できるだけでなく、装置の日常的な校正とメンテナンスを実行して、品質の問題と生産のダウンタイムを削減できます。高度なスキルを持つオペレーターは、レーザーマーキング装置の潜在能力を最大限に引き出し、生産効率を向上させ、運用コストを削減しながら、製品品質の安定性と一貫性を確保できます。
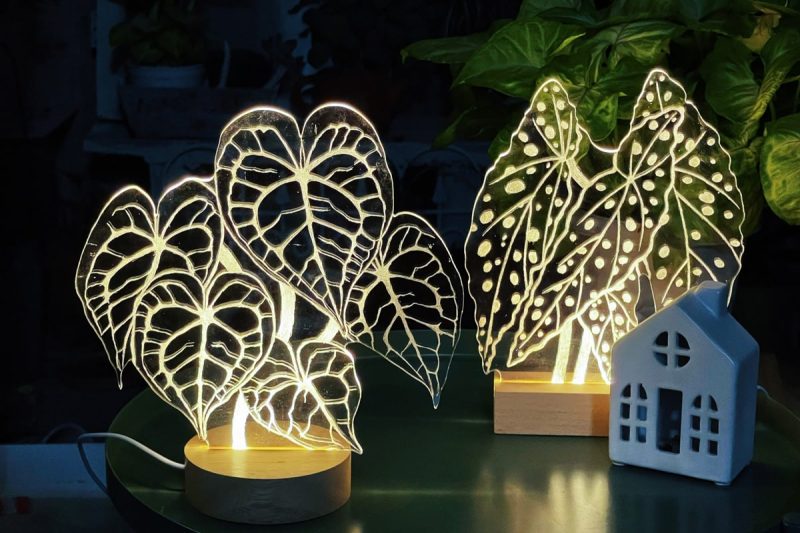
材料の取り扱いと固定の影響
レーザーマーキングプロセスでは、材料の取り扱いと固定具の設計が最終的なマーキング効果に大きな影響を与えます。ワークピースの安定性、材料表面の清潔さ、一貫したバッチ処理の確保は、高品質のマーキングを実現するための重要な要素です。
備品
- ワークピースの安定性を確保: 正確なクランプと固定により、マーキング プロセス中にワークピースがわずかに動くのを防ぎ、マーキング パターンの正確な位置決めと一貫性を確保します。これは、小さな文字や複雑なパターンのマーキングなど、高精度のマーキング タスクにとって特に重要です。
- エラーの削減: 安定した治具は、ワークピースの位置の変化によって生じるマーキング エラーを効果的に削減し、製品の一貫性と品質を向上させます。特に大規模生産では、一貫した治具設定により、各ワークピースが同じ条件でマーキングされることを保証できます。
- さまざまなワークピースに適応: 固定具の設計では、さまざまな形状やサイズのワークピースを考慮して、さまざまな生産タスクに柔軟に適用できるようにする必要があります。固定具には、オペレーターがさまざまなワークピースの要件に応じて設定できるように、クイック調整機能が必要です。これにより、生産効率が向上します。
材料の準備
- クリーニング: マーキングの前に、材料の表面を清潔にすることが重要です。汚れ、グリース、ほこりなどの不純物はレーザー光線の透過を妨げ、マーキング パターンがぼやけて不均一になる可能性があります。超音波洗浄や化学洗浄などの適切な洗浄方法を使用すると、表面の汚れを効果的に除去し、レーザー マーキングの鮮明さと一貫性を確保できます。
- 処理: 材料によっては、表面仕上げとレーザー接着性を向上させるために、研磨、サンドブラスト、化学処理などの追加の表面処理が必要になる場合があります。これらの処理手順により、材料表面の凹凸が軽減され、特に高い滑らかさが求められるアプリケーション シナリオでマーキング効果が向上します。
- 検査: マーキングする前に、材料の表面を検査して、マーキング要件を満たしていることを確認する必要があります。明らかな欠陥や表面の凹凸がある材料では、最終的なマーキング効果に悪影響を与えないように、追加の処理が必要になる場合があります。
バッチ処理
- 標準化: 大量生産で一貫したマーキング結果を維持するには、標準化された操作手順と固定具の設計を採用する必要があります。標準化により、操作の違いやワークピースの位置の不一致によって発生するマーキング エラーを削減できます。
- 自動化: 大量生産では、自動化システムを適用することで、生産効率と一貫性を大幅に向上できます。自動化システムは、大量のワークピースのマーキング作業を迅速かつ効率的に完了し、各ワークピースが同じ条件で処理されることを保証できるため、人為的エラーや生産の変動が軽減されます。
- 品質管理: 大量生産する場合は、定期的な検査やテストなど、厳格な品質管理措置を実施して、各バッチの製品が品質基準を満たしていることを確認する必要があります。マーキング効果をリアルタイムで監視することで、潜在的な問題を迅速に検出して修正し、製品の一貫性と安定性を確保できます。
要約すると、治具の設計、材料の準備、バッチ処理はすべて、レーザーマーキングの品質に影響を与える重要な要素です。治具の安定性を最適化し、材料表面の清潔さと一貫性を改善し、バッチ生産の標準化と自動化を実施することで、企業はマーキングプロセスの高精度、高効率、高品質を確保できます。
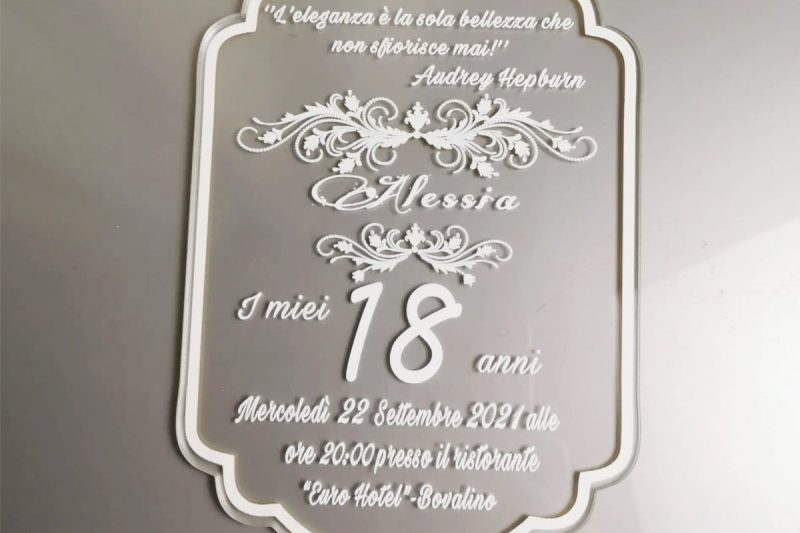
アプリケーション固有の要因の影響
レーザー マーキング プロセスでは、さまざまなアプリケーション シナリオの特定のニーズに応じて、マーキング品質に対する要件が異なります。次に、アプリケーション固有の重要な要因と、それらがマーキング品質に与える影響をいくつか示します。
マーキング深さ
マーキングの深さとは、レーザーが材料の表面に到達できる深さを指します。アプリケーション シナリオによって、マーキングの深さの要件は異なります。
- 深さの要件: 製造や工業部品などの特定の用途では、長期間の使用でもマークの耐久性と判読性を維持するために、より深いマークが必要になる場合があります。たとえば、航空宇宙部品やツールでは、摩擦が多く過酷な環境でも判読性を維持するために、より深いマークが必要になることがよくあります。深いマークは、マークの耐久性を向上させるだけでなく、摩耗に対する耐性も高めます。
- 表面マーキング: 一方、消費者向け製品のラベルや装飾マーキングなど、表面マーキングのみを必要とするアプリケーションでは、より浅いマークの深さで十分です。この場合、マークの深さを浅くすると、マークの可読性の要件を満たしながら、材料の損失と処理コストを削減できます。
コントラストのマーキング
マーキングのコントラストとは、マークと材料表面の色の違いを指します。高コントラストのマーキングは、特に正確な識別が求められるシナリオで、読みやすさを向上させるのに役立ちます。
- QR コードとバーコード: QR コードやバーコードなどの機械読み取り可能なマークには、高コントラストが不可欠です。高コントラストのマークにより、スキャン デバイスが情報を正確に読み取ることができ、マークのぼやけやコントラスト不足による読み取りエラーを回避できます。適切なレーザー パラメータと材料処理技術を使用することで、マークのコントラストを高め、信頼性の高い情報伝達を実現できます。
- 視覚マーキング: 製品番号、ブランド ロゴなど、手動で識別する必要がある一部のアプリケーションでは、高コントラストも同様に重要です。明確なマーキングにより、認識効率と精度が向上し、誤認の可能性が減ります。このような場合、マーキング マシンは、マークの明瞭性と読みやすさを確保するために、さまざまな材料の特性に応じてパラメータを調整する必要があります。
マーキングの耐久性
マーキングの耐久性は、特に過酷な環境におけるマーキング品質を測定するためのもう 1 つの重要な基準です。
- 過酷な環境: 一部の産業用途では、マーキングは高温、化学腐食、紫外線などの過酷な環境に耐える必要があります。たとえば、自動車部品や機械設備は使用中にさまざまな外部要因にさらされるため、マーキングには高い耐久性と耐損失性が求められます。適切なレーザー タイプと材料処理プロセスを選択すると、マーキングの耐久性が向上し、長期間の使用でもマーキングが鮮明で読みやすい状態を維持できます。
- 長期使用: 電子部品のシリアル番号や医療機器のロゴなど、長期間保存する必要がある一部のマーキングでは、耐久性も同様に重要です。レーザーマーキングマシンは、長期使用でマーキングが色あせたり、摩耗したり、失われたりしないように、レーザーパラメータを調整して、元の状態と機能を維持する必要があります。
つまり、アプリケーション シナリオによって、レーザー マーキングの深さ、コントラスト、耐久性に対する要件が異なります。これらのアプリケーション固有の要因を理解し、ニーズに応じてレーザー マーキングのパラメーターとプロセスを調整することで、マーキングの品質が期待される基準を満たすことが保証され、さまざまな実際のアプリケーションのニーズを満たすことができます。
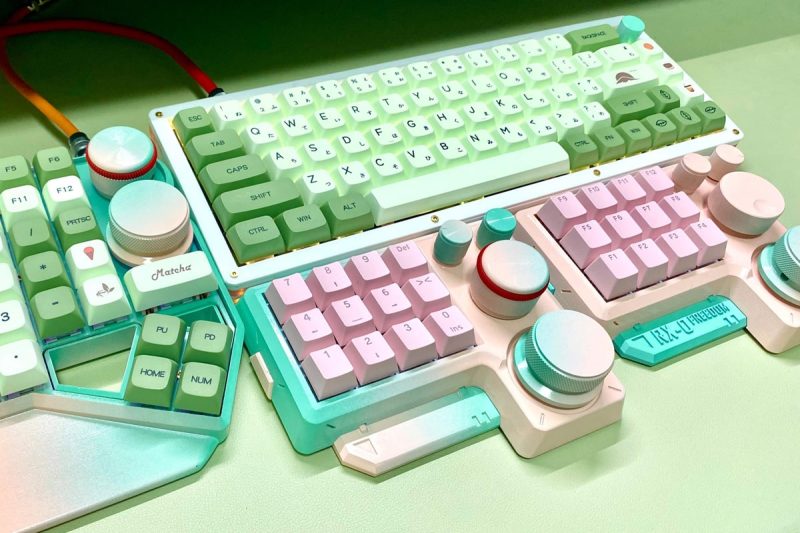
要約する
レーザーマーキング技術は高精度の加工方法であり、そのマーキング品質は、レーザーの種類、材料特性、レーザーパラメータ、環境条件、光学部品、ソフトウェアと制御システム、冷却システム、オペレーターのスキル、材料の取り扱いと固定具の設計、アプリケーション固有の要因など、多くの要因の影響を受けます。各要因は、マーキングの最終的な効果にさまざまな程度で影響します。
- レーザー光源の選択によって、適用可能な材料とマーキング結果が直接決まります。たとえば、ファイバーレーザーは金属材料に適しており、CO2 レーザーは非金属材料に適しており、紫外線 (UV) レーザーは微細なマーキングが必要な用途に適しています。
- 吸収、反射率、表面状態などの材料特性は、レーザー光線の透過率と最終的なマーキング効果に影響します。材料の取り扱いと表面処理もマーキングの品質に直接影響します。
- レーザー パラメータには、電力設定、パルス周波数、マーキング速度、焦点距離調整などがあり、明確で準拠したマーキングを確実に行うには、これらを正確に設定する必要があります。
- 温度、湿度、清潔さなどの環境条件は、機器の安定性とレーザービームの品質に影響を与えます。
- レンズの品質、ビーム伝送システム、ガルバノメータ スキャナーなどの光学コンポーネントのパフォーマンスも、マーキングの精度と一貫性に直接関係します。
- ソフトウェアと制御システムの品質によって、マーキングの精度と操作のしやすさが決まります。優れたソフトウェアと自動化システムは、マーキングの効率と品質を向上させることができます。
- 冷却システムはレーザー機器の安定した動作に不可欠です。効率的な冷却システムは機器の寿命を延ばし、機器の性能を維持することができます。
- オペレーターのスキルとトレーニングは、マーキング品質を確保するための基礎です。プロのオペレーターは、機器のパラメータを正しく設定し、定期的なメンテナンスを実行して、機器の最高のパフォーマンスを確保できます。
- 材料の取り扱いと治具の設計もマーキング効果に影響を与える重要な要素です。安定した治具と適切な材料の取り扱いにより、マーキングの一貫性と精度が向上します。
- マーキングの深さ、コントラスト、耐久性などのアプリケーション固有の要素は、アプリケーションの要件に応じて異なり、マーキングの品質基準も異なります。
これらの影響要因を理解して最適化することで、企業は理想的なレーザー マーキング結果を達成できます。当社のチームは、さまざまなアプリケーション要件を満たすカスタマイズされたレーザー ソリューションを提供することに尽力しています。当社の製品やサービスにご興味がある場合、またはさらに技術サポートが必要な場合は、お気軽にお問い合わせください。当社は、レーザー マーキング プロセスが最高の結果を達成できるように、専門的なコンサルティングとソリューションを心を込めて提供いたします。
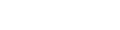
連絡先
- [email protected]
- [email protected]
- +86-19963414011
- No. 3 ゾーン A、Lunzhen 工業地帯、玉城市、山東省。
レーザー ソリューションを入手する