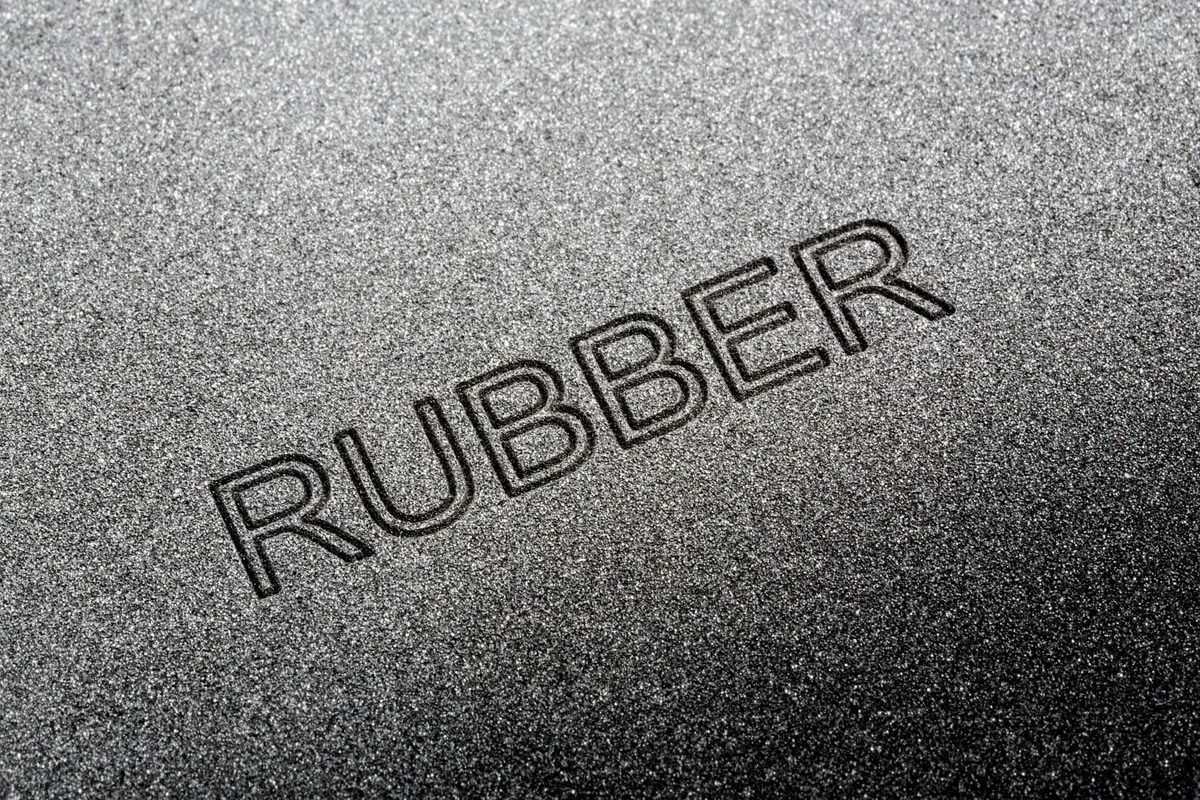
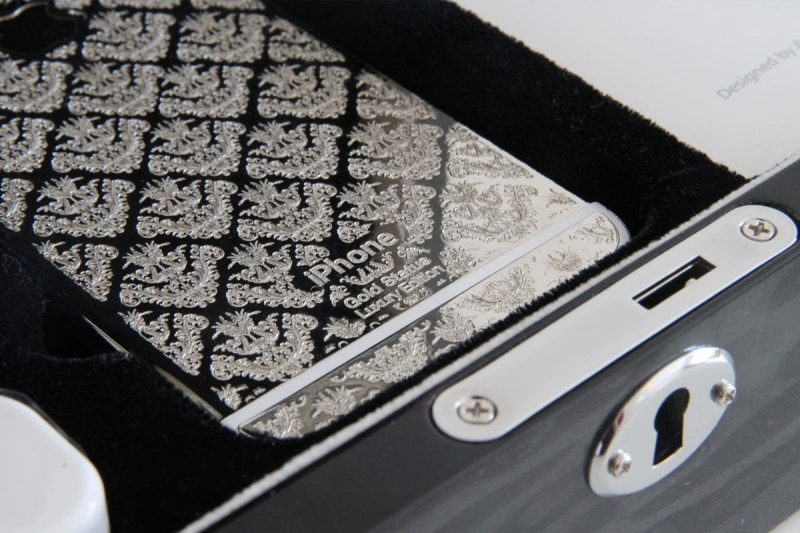
レーザーマーキングマシンとは何ですか?
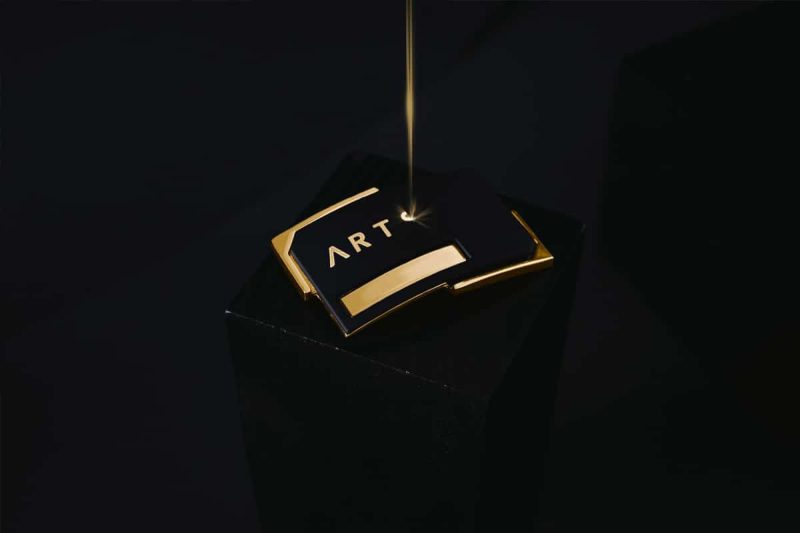
レーザーマーキングマシンはどのように動作するのでしょうか?
レーザーマーキングマシンの主要コンポーネント
レーザー マーキング マシンの効率、精度、安全性は、いくつかの重要なコンポーネントに依存します。
- レーザー ソース: レーザー ソースは、波長や出力などの特定の特性を持つレーザー ビームを生成します。材料や用途に応じて、さまざまな種類のレーザー ソース (ファイバー、CO2、UV、グリーン) が使用されます。たとえば、ファイバー レーザーは金属に適しており、UV レーザーは熱に弱い材料に最適です。
- ビーム伝送システム: ビーム伝送システムには、ミラー、レンズ、場合によってはビーム エクスパンダーが含まれます。このシステムは、レーザーをソースから材料に正確に導き、エネルギー損失を最小限に抑え、高い焦点を確保します。
- スキャン システム (ガルバノメータ スキャナ): ガルバノメータ スキャナ (または「ガルボ」) は、レーザー ビームの方向を制御する高速ミラーです。プログラムされた設計に従って作業面上でビームを高速に誘導し、迅速かつ正確なマーキングを可能にします。
- 制御ソフトウェア: 制御ソフトウェアを使用すると、マーキングを設計し、レーザー パラメータ (速度や強度など) を調整し、マーキング プロセス全体を管理できます。高度なソフトウェア オプションではリアルタイムの調整もサポートされており、複雑で精巧なデザインが可能になります。
- ワークピース処理システム: このシステムは、マーキング中に材料を配置して固定し、安定性と精度を確保するために使用されます。産業用セットアップでは、大量生産の取り扱いを自動化するためにコンベアやロボット アームが含まれる場合があります。
- 冷却システム: 冷却システムは、レーザー ソースとその他のコンポーネントの最適な動作温度を維持し、過熱を防止します。これは、マシンの寿命を延ばし、一貫したマーキング品質を維持するため、連続マーキングまたは高出力マーキング アプリケーションにとって特に重要です。
- 安全エンクロージャとインターロック: 安全エンクロージャはレーザー放射からオペレータを保護し、インターロック システムにより、エンクロージャが開いている場合はレーザーが動作しないようにします。この設定により、安全な作業環境と安全規制への準拠が保証されます。
レーザーマーキングのプロセス
レーザーマーキングには、設計から品質検査まで、いくつかの正確なステップが含まれます。
- デザインとプログラミング: テキスト、ロゴ、複雑なパターンなどを含むマーキング デザインは、コンピューター ソフトウェアを使用して作成されます。次に、デザインがレーザー マーキング マシンにプログラムされ、レーザー ビームの経路と強度が決定されます。
- 材料の準備: 材料は洗浄され、ワークピース処理システムにしっかりと配置されます。表面の汚染物質はすべて除去され、一貫したマーキング品質が確保されます。
- パラメータ設定: レーザー出力、速度、周波数、パルス持続時間などの主要パラメータは、材料の種類と希望するマーキング効果に基づいて設定されます。このステップは、最適なマーキング品質と耐久性を実現するために不可欠です。
- レーザー ビーム生成: レーザー ソースは、マーキングに適した特定の特性を持つ、コヒーレントで強力な光線を生成します。選択するレーザーの種類 (ファイバー、CO2、UV) は、材料とマーキング要件によって異なります。
- ビームの焦点合わせ: レーザー ビームはレンズを使用して細かいスポット サイズに焦点を合わせられ、高いエネルギー密度が生み出されるため、正確で深いマーキングが可能になります。焦点合わせは高解像度のマーキングを作成するために非常に重要です。
- ビームステアリング: ガルバノメータースキャナーは、プログラムされたパスに沿って材料の表面上で焦点を絞ったビームを高速で移動させ、目的のマーキングパターンを高速で実現します。
- 材料の相互作用: レーザー ビームは材料の表面と相互作用し、加熱、溶融、アブレーションなどの局所的な変化を引き起こします。この相互作用により、材料の色、質感、または表面構造が変化し、目に見えるマークが作成されます。
- 冷却と凝固: レーザーによるマーキングが完了すると、材料は急速に冷却され、マーキングされたパターンが凝固し、永続的で耐久性のある結果が得られます。
- 品質検査: マークが付けられた製品は、マークが明瞭性、精度、耐久性に関する品質基準を満たしていることを確認するための検査を受けます。
レーザーマーキングの背後にある物理学
レーザーマーキングプロセスは、レーザービームと材料の間の基本的な物理的相互作用に依存します。
- レーザー エネルギーの吸収: レーザー ビームが材料に当たると、表面がそのエネルギーを吸収し、局所的に加熱されます。吸収率は材料とレーザーの波長によって異なります。たとえば、金属は赤外線レーザー エネルギーを効果的に吸収しますが、UV レーザーはプラスチックに適しています。
- 局所的な加熱: 吸収されたエネルギーによって局所的に強い熱が発生し、材料の構造が変化します。プロセスと材料によっては、この熱によって酸化、色の変化、表面の溶解が起こる場合があります。
- 材料除去 (アブレーション): 彫刻などの一部のマーキング プロセスでは、レーザー エネルギーが材料を蒸発させるほど強力で、溝やくぼみが作成されます。このアブレーションは非接触方式であるため、マーキング ツールの摩耗を防ぎ、複雑で精密なデザインが可能になります。
- 化学反応: レーザーによって発生した熱は、酸化などの化学変化を引き起こし、材料を除去することなく材料の色を変えます。たとえば、ステンレス鋼へのアニーリング マーキングでは、酸化を利用して黒または暗い色のマークを作成します。
- 相変化: 一部の材料は、レーザー マーキング中に固体から気体など相変化を起こします。この急速な変化は材料の質感と外観に影響を与え、明瞭で耐久性のあるマーキングを可能にします。
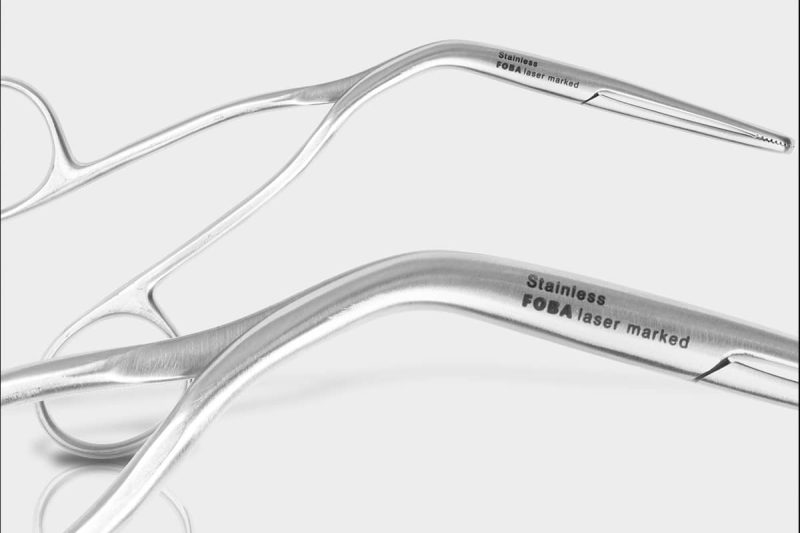
レーザーマーキングプロセスの種類
アニーリングマーキング
アニーリング マーキングでは、金属表面を加熱して酸化を誘発し、素材を一切除去せずに色を変えます。このプロセスにより、通常、暗いマークが生成され、酸化レベルに応じて茶色から黒までさまざまな色になります。
- 材料: 主にステンレス鋼、チタン、その他の合金などの金属に使用されます。
- 用途: 表面の完全性が重要となる医療機器や外科用器具、自動車部品や航空宇宙部品によく使用されます。
- 利点: 焼きなましでは材料が除去されないため、表面が維持され、滑らかで耐腐食性のある仕上げが必要な用途に最適です。
エッチング/彫刻
エッチングと彫刻は、レーザーで表面から材料を除去するプロセスです。エッチングでは表面が浅く除去されますが、彫刻では材料の奥深くまで浸透します。
- 材質: 金属、プラスチック、セラミックに適しています。
- 用途: 自動車、宝石、電子機器業界など、耐久性と耐摩耗性に優れたマーキングを必要とする業界で広く使用されています。
- 利点: 手荒な取り扱いや過酷な条件への暴露にも耐えられる、耐久性の高い触覚マークを生成します。また、マーキングの深さにより、追跡可能性と偽造防止の目的でセキュリティも強化されます。
炭素移動
カーボンマイグレーションは、金属表面を加熱して炭素を表面に引き寄せ、暗くコントラストの高いマークを作成するプロセスです。レーザーは材料を除去するのではなく、分子の変化を引き起こし、目に見えるマークを作成します。
- 材料: 鋼合金などの炭素含有金属によく使用されます。
- 用途: 金属に暗いマークを作成するのに最適で、ツールや部品の識別など、高いコントラストと耐久性が求められる用途に最適です。
- 利点: 材料を除去することなく高コントラストの永久マークを生成できるため、視覚的なインパクトが強いきれいな表面を必要とする用途に最適です。
発泡
発泡は、主にプラスチックや一部の金属に使用されるレーザー マーキング技術です。レーザーは材料を溶かし、冷却時に材料内に閉じ込められた小さな気泡を生成します。このプロセスにより、泡のような外観を持つ、盛り上がった明るい色のマークが生成されます。
- 材質: 暗い色のプラスチックや特定の金属に最も効果的です。
- 用途: 包装、消費財、電子部品などのプラスチックへの高コントラストのマーキングによく使用されます。
- 利点: 発泡部分と非発泡部分のコントラストにより、マークがはっきりと見えるため、暗い色の素材でも読みやすくなります。
色の変更
色を変えるプロセスは、レーザーを利用して、表面の質感に影響を与えずに材料内の分子または化学的な変化を引き起こします。この技術は、変形せずに材料の色を変えることができるため、プラスチックに特に有効です。
- 材質: プラスチックや一部の金属によく使用されます。
- 用途: 回路基板、医療機器、家電製品など、目立たないながらも鮮明なマークが必要なアイテムに最適です。
- 利点: 材料の表面を損傷することなく高コントラストのマークを作成できるため、繊細な部品や美観を重視するマーキングの用途に適しています。
表面アブレーション
表面アブレーションでは、レーザーを使用して塗料、陽極酸化コーティング、その他の表面処理などの薄い材料層を除去し、下にある基板を露出させます。このプロセスは、異なる材料層を露出させることでコントラストを作成するのに効果的です。
- 材料: コーティングされた金属やプラスチックに適しています。
- 用途: バックライトが必要なボタンやスイッチの「昼夜」マーキングや、塗装面への永久マークの作成に広く使用されています。
- 利点: 異なる層を露出させることで、正確でコントラストの高いマーキングが可能になり、自動車の内装、コントロール パネル、さまざまな照明下で判読可能なマーキングが必要なあらゆるアプリケーションに役立ちます。
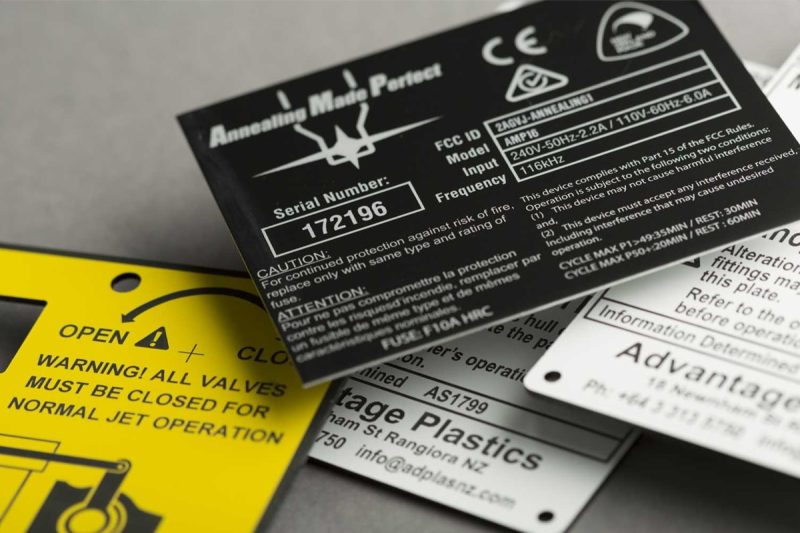
マーキングマシンで使用されるレーザー光源の種類
ファイバーレーザー
ファイバーレーザーは、イッテルビウムなどの希土類元素を添加した光ファイバーを使用して、高強度のレーザービームを生成します。効率性が高く、メンテナンスの必要性を最小限に抑えながら、安定した連続動作を実現できます。
- 波長: 約1064 nm (赤外線)。
- マーキング可能な材料: ファイバー レーザーは、ステンレス鋼、アルミニウム、銅、真鍮、その他の合金などの金属に特に効果的です。また、一部の種類のプラスチックにもマーキングできます。
- 用途: 自動車部品、電子部品、工具、医療機器などのマーキングに広く使用されています。金属の彫刻、エッチング、焼きなましに最適です。
- 利点:
- 高いビーム品質: ファイバーレーザーは、細かく高解像度のマークを生成するため、複雑なデザインや小さなテキストに適しています。
- 長寿命: ファイバーレーザーは堅牢で、最小限のメンテナンスで最大 100,000 時間使用できます。
- 効率: 高いエネルギー効率により運用コストが削減されます。
- 非接触で高速なマーキング: 物理的な接触なしで高速マーキングを実現し、機械の摩耗を抑えます。
CO2レーザー
CO2 レーザーは、主に二酸化炭素、窒素、ヘリウムからなるガス混合物を励起してレーザー ビームを生成します。CO2 レーザーは遠赤外線スペクトルで動作し、非金属および有機材料のマーキングに最適です。
- 波長:約10,600 nm(遠赤外線)。
- マーク可能な素材: 木材、ガラス、紙、繊維、皮革、ゴム、アクリル、特定のプラスチックなどの非金属に効果的です。
- 用途: 包装、標識、繊維加工、木工など、有機材料を扱う業界でよく使用されます。CO2 レーザーは、彫刻、切断、表面マーキングを必要とする用途に適しています。
- 利点:
- 非金属に対する汎用性: CO2 レーザーは、他のレーザーでは困難な非金属材料のマーキングと切断に優れています。
- 切断と彫刻に高いパワーを発揮: 厚い有機材料のマーキングと切断の両方に使用できます。
- 所有コストが低い: CO2 レーザーは一般に初期コストが低く、メンテナンスも比較的簡単です。
- 最小限の熱影響: 熱の影響を受ける領域が制限されたきれいなマークが生成されるため、反りが発生しやすい材料に適しています。
UVレーザー
UV レーザーは短波長で動作し、「冷たい」レーザー マーキング効果を生み出します。短波長により材料に伝わる熱量が減少するため、高精度と最小限の熱影響が求められる用途に最適です。
- 波長:約355 nm(紫外線)。
- マーキング可能な素材: プラスチック、ガラス、セラミック、特定の金属などの敏感な素材に非常に効果的です。また、正確で高コントラストのマーキングが必要な熱に敏感な素材や表面にも効果的です。
- 用途: UV レーザーは、電子機器業界、医療機器製造、化粧品業界でのマーキングによく使用されます。回路基板、プラスチック部品、ガラス瓶、医療用パッケージのマーキングに最適です。
- 利点:
- 熱影響部が最小限: UV レーザーは冷たいマーキング効果を生み出し、繊細な素材への損傷を防ぎます。
- 精度と鮮明さ: 高解像度の高コントラスト マーク。複雑なグラフィック、小さなフォント、シリアル番号に適しています。
- 低熱変形: 溶解、変色、損傷のリスクがなく、熱に敏感な材料に適しています。
- プラスチックへの高い吸収率: UV 波長はプラスチックに非常に吸収されるため、鮮明でコントラストの高いマークを作成できます。
緑色レーザー
緑色レーザーは可視スペクトルの波長で動作するため、赤外線レーザーではマーキングが難しい反射性材料のマーキングに非常に効果的です。緑色レーザーは優れた浸透性と精度を備えており、特定の金属や透明材料に特に有効です。
- 波長:約532 nm(緑)。
- マーキング可能な材料: 銅、銀、金などの反射性金属、および特定の種類のプラスチック、セラミック、ガラスに適しています。
- 用途: 緑色レーザーは、電子機器、宝石、医療機器など、反射材に細かいディテールを施す必要がある業界で使用されています。回路基板のマーキングや宝石のカスタマイズなど、熱伝達を最小限に抑える必要がある用途に最適です。
- 利点:
- 反射性材料に効果的: 赤外線エネルギーの吸収が少ない、難しい高反射性材料にマーキングできます。
- 高精度: 小さなフォントや複雑なデザインに適した、きめ細かいマークを生成します。
- 熱の影響を低減: ワークピースへの熱による損傷のリスクを軽減し、材料特性を維持します。
- 熱に弱い素材へのコールドマーキング: 割れや欠けがなく、ガラスなどの素材に高品質のマーキングを保証します。
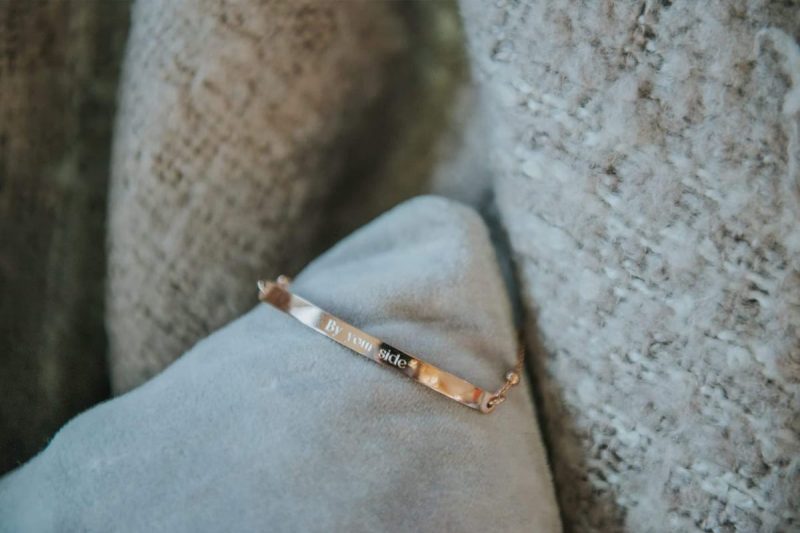
レーザーマーキングマシンの用途
自動車産業
自動車業界では、精度と追跡可能性が極めて重要です。レーザー マーキング マシンは、エンジン部品、ブレーキ システム、VIN (車両識別番号) プレートなど、さまざまなコンポーネントにマーキングするために使用されます。これらの永久的なマーキングにより、各部品がライフサイクル全体にわたって追跡可能になり、メンテナンス、リコール プロセス、偽造防止に役立ちます。
- 一般的なマーキング: シリアル番号、バーコード、部品番号、ロゴ。
- 利点: トレーサビリティを強化し、安全性を向上させ、業界の規制に準拠します。
エレクトロニクスおよび半導体
電子機器や半導体の製造では、プリント基板 (PCB)、コネクタ、チップなどの繊細な部品のラベル付けにレーザー マーキングが広く使用されています。レーザー マーキングは、繊細な電子部品を損傷することなく高いコントラストを実現し、製品の完全性を維持しながら明確な識別を保証します。
- 一般的なマーキング: QR コード、シリアル番号、小さな英数字。
- 利点: 在庫管理と品質管理に不可欠な、小型コンポーネントへの正確でコントラストの高いマーキングが可能になります。
医療機器
レーザー マーキングは、精度と安全性が最も重要視される医療機器業界では欠かせません。医療用ツール、手術器具、インプラントには、固有デバイス識別 (UDI) コード、バッチ番号、ロゴが付けられます。レーザー マーキングは生体適合性と耐腐食性を備えているため、医療分野の厳格な規制基準を満たしています。
- 一般的なマーキング: UDI、バッチ番号、会社のロゴ。
- 利点: 滅菌プロセスに耐える永久的な滅菌マーキングを提供し、医療規制への準拠を保証し、患者の安全性を向上させます。
航空宇宙産業
航空宇宙産業では、重要な部品が過酷な条件にさらされることが多いため、これらの部品には耐久性のあるマーキングが必要です。レーザー マーキングにより、航空機部品のマーキングが判読可能かつ永続的に維持され、信頼性の高い追跡とメンテナンスが可能になります。タービン ブレード、ファスナー、構造部品などの航空宇宙部品には、シリアル番号と追跡コードが付けられています。
- 一般的なマーキング: シリアル番号、部品 ID、追跡コード。
- 利点: 過酷な環境や厳格な品質基準に耐えられる、耐久性と耐摩耗性に優れたマーキングを提供します。
ジュエリーおよび高級品
レーザー マーキングは、貴金属、宝石、高級品に複雑なデザイン、パーソナライズ、ブランド化を加えるために、ジュエリーや高級品業界で広く使用されています。これにより、宝石商は貴重な素材の完全性を損なうことなく、高品質で詳細なマークを作成できます。
- 一般的なマーキング: カスタム デザイン、ロゴ、シリアル番号、刻印。
- 利点: 物理的な接触なしにエレガントで詳細なカスタマイズ可能なマーキングを提供し、高級製品に価値と偽造防止対策を追加します。
ツール製造
レーザー マーキングは、仕様、ブランド ロゴ、シリアル番号でツールを識別するためにツール製造に不可欠です。これにより、顧客はツールをすばやく識別でき、メーカーは品質管理の目的で製品バッチを追跡できます。
- 一般的なマーキング: モデル番号、寸法、ロゴ、バッチ番号。
- 利点: 乱暴な取り扱いや摩耗に耐える耐久性のあるマーキングが可能になり、トレーサビリティと品質保証が向上します。
包装業界
包装業界では、レーザー マーキングを使用して、包装材料に有効期限、バッチ番号、バーコードを作成します。これにより、トレーサビリティ、在庫管理、規制遵守に役立ちます。レーザー マーキングは非接触でクリーンなため、さまざまな包装材料にマーキングするのに最適です。
- 一般的なマーキング: 有効期限、バーコード、バッチ番号。
- 利点: 環境ストレス下でも規制基準を満たし、品質を維持する、明確で永続的なマーキングを提供します。
消費財
レーザー マーキングは、携帯電話、ラップトップ、アクセサリなどの製品にアイテムをパーソナライズしたり、ブランド ロゴを追加したり、固有の識別子を刻印したりするために、消費財分野で広く使用されています。レーザー マーキングの柔軟性により、メーカーはさまざまな材料に高品質で詳細なデザインを追加できます。
- 一般的なマーキング: ロゴ、バーコード、シリアル番号、装飾要素。
- 利点: 耐久性と高品質のパーソナライゼーション オプションを提供し、ブランド価値を高め、偽造を防止します。
防衛と軍事
防衛および軍事分野では、レーザー マーキングは、機器、銃器、その他の資産のマーキングと追跡に不可欠です。永続的で高コントラストのマークは、在庫管理、資産管理、軍事規格への準拠に役立ちます。
- 一般的なマーキング: シリアル番号、バーコード、資産識別子。
- 利点: 過酷な条件に耐える堅牢なマーキングを提供し、信頼性と軍事規制への準拠を保証します。
広告と看板
レーザー マーキングは、高品質のグラフィックやテキストを使用してカスタマイズされた看板、ディスプレイ、販促品を作成するのに最適です。この技術により、アクリル、金属、木材などの素材に精巧なディテールを刻むことができ、広告素材の視覚的な魅力を高める鮮明で長持ちするマークを作成できます。
- 一般的なマーキング: ロゴ、グラフィック、装飾テキスト。
- 利点: 目を引く詳細で高コントラストのマーキングを提供するため、ブランディングやプロモーションに最適です。
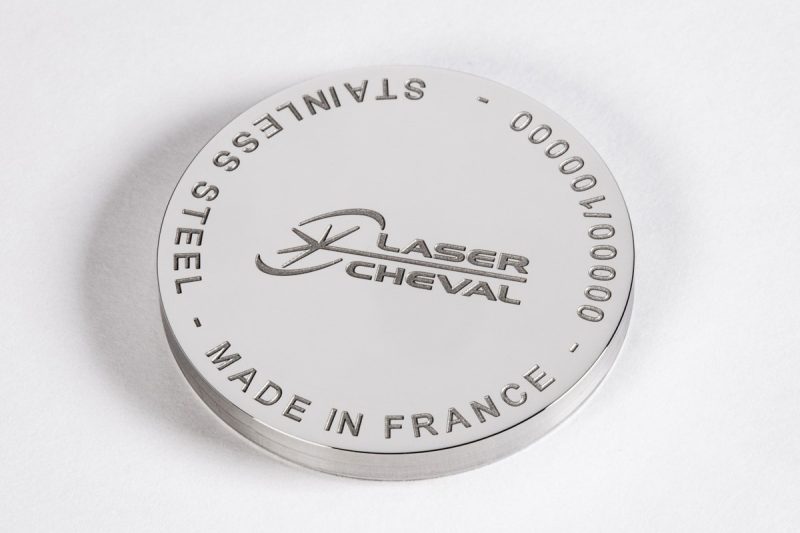
レーザーマーキングマシンの利点
レーザー マーキング マシンは従来のマーキング方法に比べて多くの利点があり、さまざまな業界の現代の製造業にとって不可欠なツールとなっています。
- 高精度と高品質: レーザー マーキングは比類のない精度と詳細さを提供し、メーカーは複雑なデザイン、小さなフォント、高解像度のグラフィックを非常に鮮明に作成できます。レーザー ビームは高度に焦点が絞られているため、一貫性のある正確なマーキングが保証され、読みやすさと美的品質が向上します。この精度は、電子部品や医療機器などの小さなコンポーネントに詳細なロゴ、バーコード、シリアル番号が必要なアプリケーションに特に役立ちます。
- 高速性と効率性: レーザー マーキング マシンは高速で動作するため、時間が重要な生産環境に最適です。数秒以内に製品をマーキングできるため、生産性とスループットが大幅に向上します。メンテナンスに必要なダウンタイムが最小限に抑えられるため、レーザー マーキング マシンは効率的で継続的な操作をサポートし、リード タイムを短縮して製造プロセスを最適化します。
- 永久的で耐久性のあるマーク: レーザー マーキングによって作成されたマークは永久的で耐久性が高く、過酷な環境、摩耗、化学物質への暴露に耐えることができます。この耐久性により、シリアル番号やバッチ コードなどの識別マークが製品のライフサイクル全体にわたってそのまま残ります。この利点は、コンポーネントの追跡可能性と品質保証が不可欠な自動車、航空宇宙、医療機器などの業界では特に重要です。
- 非接触プロセス: レーザー マーキングは非接触プロセスです。つまり、レーザー ビームは物理的に材料に触れることなく材料と相互作用します。このアプローチにより、機械とワークピースの両方の摩耗が最小限に抑えられ、デリケートな材料や敏感な材料の完全性が維持されます。レーザー マーキングの非接触性により、材料の変形のリスクも軽減されるため、壊れやすい材料や薄い材料に最適です。
- 汎用性: レーザー マーキング マシンは汎用性が高く、金属、プラスチック、セラミック、ガラス、木材、繊維など、さまざまな素材にマーキングできます。ファイバー、CO2、UV、グリーン レーザーなどのさまざまなレーザー ソースにより、硬質素材と軟質素材の両方に同じ精度でマーキングできます。この汎用性により、メーカーは単一の生産ライン内でさまざまなマーキング ニーズに対応できます。
- 柔軟性: レーザー マーキング マシンは、設計と操作の両方で柔軟性を提供します。コンピューター制御のソフトウェアを使用すると、ツールや設定を変更することなく、さまざまなデザイン、ロゴ、テキストを簡単に切り替えることができます。この機能は、小ロット生産やパーソナライズされたマーキングに役立ち、企業はさまざまな顧客の要求や製品仕様に迅速に対応できます。
- 低い運用コスト: レーザー マーキング マシンは、一度設置すると、継続的なコストが最小限で済みます。従来の方法とは異なり、レーザー マーキングではインク、化学薬品、彫刻ツールなどの消耗品が不要なため、長期的には大幅な節約につながります。さらに、可動部品が少ないため、レーザー マーキング マシンのメンテナンスは最小限で済み、長期的な運用コストの削減につながります。
- 環境に優しい: レーザー マーキングは、有害な化学物質を含まず、大量の廃棄物も出さないクリーンなプロセスです。インク、溶剤、その他の消耗品が不要になることで、レーザー マーキングは環境への影響を軽減し、持続可能な製造方法に適合します。また、このプロセスでは騒音やほこりも最小限に抑えられるため、マーキングのニーズに対してより安全で環境に優しいソリューションとなります。
- 自動化と統合: レーザー マーキング マシンは自動化された生産ラインに簡単に統合できるため、大量生産に適しています。多くのレーザー マーキング システムはロボット ハンドリング システムやプログラマブル ロジック コントローラー (PLC) と互換性があり、シームレスな操作と一貫したマーキング品質を実現します。自動化されたワークフローとの互換性により、大量生産がサポートされ、一貫性が向上し、メーカーは効率的に拡張できます。
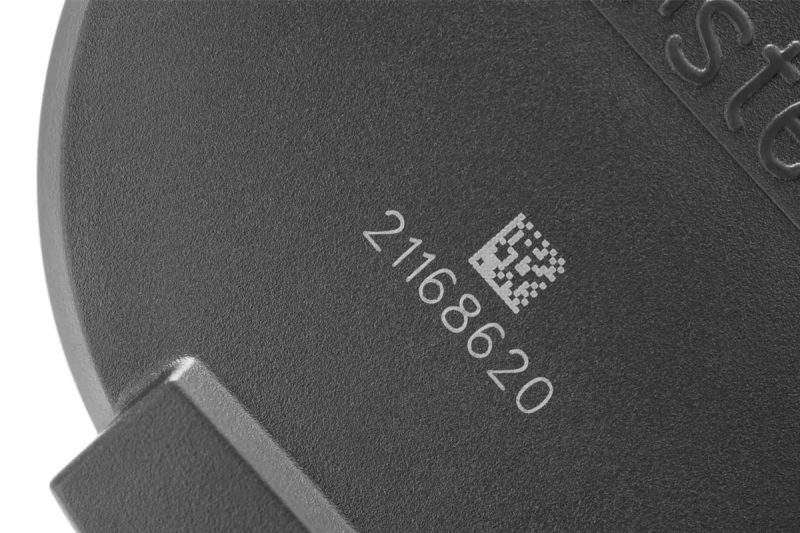
制限と課題
レーザー マーキング マシンには数多くの利点がありますが、一定の制限や課題もあります。これらを理解することで、メーカーは情報に基づいた決定を下し、レーザー マーキングを生産プロセスに組み込む前に必要な検討事項を準備することができます。
- 初期投資: レーザー マーキング マシンは、インクジェット印刷やスタンプなどの従来のマーキング方法に比べて、かなりの初期投資が必要です。高品質のレーザー マーキング システム、特にファイバー レーザーや UV レーザーなどの高度な機能を備えたシステムは、かなりのコストがかかる場合があります。この初期費用には、マシンだけでなく、セットアップ、ソフトウェア、オペレーターのトレーニングも含まれます。小規模な企業や予算が限られている企業にとっては、コストが導入の障壁となる可能性があります。ただし、運用コストが低く、メンテナンスが最小限であることから得られる長期的なコスト削減により、初期投資を相殺できる場合がよくあります。
- 材料の制限: レーザー マーキング マシンは幅広い材料に対応できますが、特定の材料はレーザー マーキングが難しいか、レーザー マーキングと互換性がありません。たとえば、銅や金などの反射性金属には、グリーン レーザーなどの特定の種類のレーザーが必要であり、コストが増加する可能性があります。さらに、一部の熱可塑性プラスチックなどの熱に敏感な材料は、低エネルギー設定でもレーザー マーキングにさらされると変形したり変色したりする可能性があります。このような場合、レーザー パラメータの調整や別のマーキング方法が必要になることがあります。
- 安全上の考慮事項: レーザー マーキング マシンは高エネルギー ビームを発するため、適切に管理しないと安全上のリスクが生じる可能性があります。オペレーターやその場にいる人は、目や皮膚に傷害を負う可能性のあるレーザー照射から保護する必要があります。リスクを最小限に抑えるには、保護エンクロージャー、インターロック、レーザー安全メガネの使用などの安全対策が不可欠です。また、特定の材料のレーザー マーキングでは煙や微粒子が発生する可能性があるため、空気の質を維持しオペレーターの安全を確保するために適切な換気システムまたは煙抽出システムが必要です。
- 技術的専門知識: レーザー マーキング マシンを操作して最適な結果を得るには、ある程度の技術的専門知識が必要です。材料や希望するマーキング効果に応じてレーザー パラメータ (出力、周波数、速度など) を調整するのは複雑で、専門知識が必要になる場合があります。さらに、複雑なグラフィックや高精度のテキストなどのマーキングを設計およびプログラミングするには、レーザー マーキング ソフトウェアに精通している必要があります。必要なトレーニングと専門知識がなければ、企業はレーザー マーキング マシンの機能を十分に活用できず、最適なマーキングが得られなかったり、生産時間が長くなったりする可能性があります。
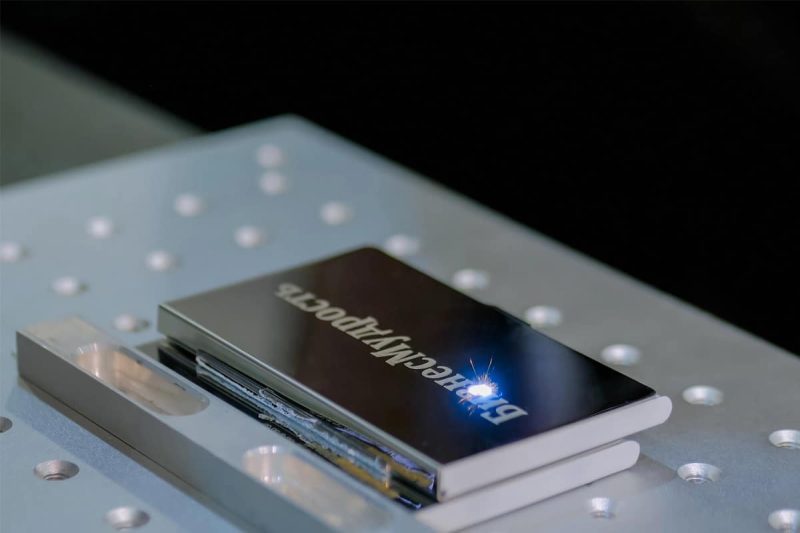
レーザーマーキングマシンを選択する際の考慮事項
適切なレーザー マーキング マシンを選択することは、生産ニーズ、品質基準、予算を満たすために不可欠です。意思決定プロセスを導くための重要な考慮事項は次のとおりです。
- 材料の種類: さまざまなレーザーの種類は、さまざまな材料に適しています。たとえば、ファイバー レーザーは金属に最適ですが、CO2 レーザーは木材、プラスチック、ガラスなどの有機材料に最適です。生産ラインに複数の材料が使用されている場合は、さまざまな基材を効率的に処理するために、多目的レーザー マーキング マシンまたは複数のレーザー ソースが必要になる場合があります。
- マーキング要件: 深い彫刻、高コントラストのマーキング、または細い線の作業など、必要なマーキングの種類を決定します。アプリケーションによっては、エッチングや彫刻が必要な場合もあれば、表面のマーキングや色の変更のみが必要な場合もあります。特定のマーキング要件を理解することで、適切なレーザー出力、波長、および処理機能を選択して、希望する結果を得ることができます。
- 生産量: 大量生産では、速度と効率が重要です。レーザー マーキング マシンにはさまざまな速度と機能があり、高速バッチ処理用に作られたものもあれば、細かくて低速のマーキング用に設計されたものもあります。品質や速度を犠牲にすることなく生産量を処理できるマシンを選択してください。自動処理システムも大量生産環境での効率を向上させることができます。
- 精度と詳細: 複雑なデザイン、小さなフォント、高精度のマークが必要なアプリケーションの場合は、高解像度のマーキング機能を備えたマシンが必要です。ビーム品質、フォーカス精度、スキャン速度はすべて、達成できる詳細レベルに影響します。医療、電子機器、高級品分野のアプリケーションでは、多くの場合、この高い精度が求められます。
- 統合と自動化: レーザー マーキング マシンを既存の生産ラインに統合する必要があるかどうかを検討してください。多くのレーザー マーキング システムは、プログラマブル ロジック コントローラー (PLC) による自動化をサポートしており、ロボット アームやコンベアと互換性があります。大規模または大量の操作の場合、自動化された統合によってプロセスが合理化され、エラーが削減され、一貫したマーキング品質が維持されます。
- ソフトウェア機能: レーザー マーキング マシンは、デザインの作成、パラメータ調整、自動化機能を管理する制御ソフトウェアを介して操作されます。ソフトウェアがユーザー フレンドリであり、デザインに必要なファイル形式 (DXF、PLT、BMP など) をサポートしていることを確認してください。高度なソフトウェアでは、リアルタイムの調整、シリアル化、さらには動的なマーキングのニーズに対応するデータベース システムとの統合も可能になります。
- コストと予算: レーザー マーキング マシンのコストは、レーザーの種類、出力、機能によって大きく異なります。初期購入価格だけでなく、メンテナンスやエネルギー消費などの継続的な運用コストも考慮して、現実的な予算を設定してください。ハイエンド モデルは高度な機能を備えている場合もありますが、これらの機能が生産目標に合致し、明確な投資収益率をもたらすかどうかを評価することが不可欠です。
- アフターセールス サポートとサービス: 信頼性の高いアフターセールス サポートは、特に複雑なレーザー機器を操作する場合に非常に役立ちます。設置、トレーニング、トラブルシューティング、メンテナンスなどの包括的なサポート サービスを提供するメーカーまたはサプライヤーを選択してください。質の高いアフターセールス サービスにより、マシンが最適な状態に保たれ、問題が発生した場合のダウンタイムが短縮されます。
- 規制コンプライアンス: 業界によっては、レーザー マーキングされた製品に特定の規制基準が適用される場合があります。たとえば、医療機器には固有デバイス識別 (UDI) マーキングが必要であり、自動車部品には標準化された識別コードが必要になることがよくあります。選択したマシンが業界固有の規制を満たし、健康と安全の基準に準拠していることを確認してください。
- 将来の拡張: ビジネスが成長するにつれて、生産ニーズが高まり、より強力で多用途なマーキング機能が必要になる場合があります。アップグレード オプションやモジュール設計を備えたマシンを探してください。これにより、必要に応じて新しい機能を追加したり、パワーを増強したりできます。拡張性のあるマシンに投資することで、完全な交換を必要とせずに将来の需要を満たすことができます。
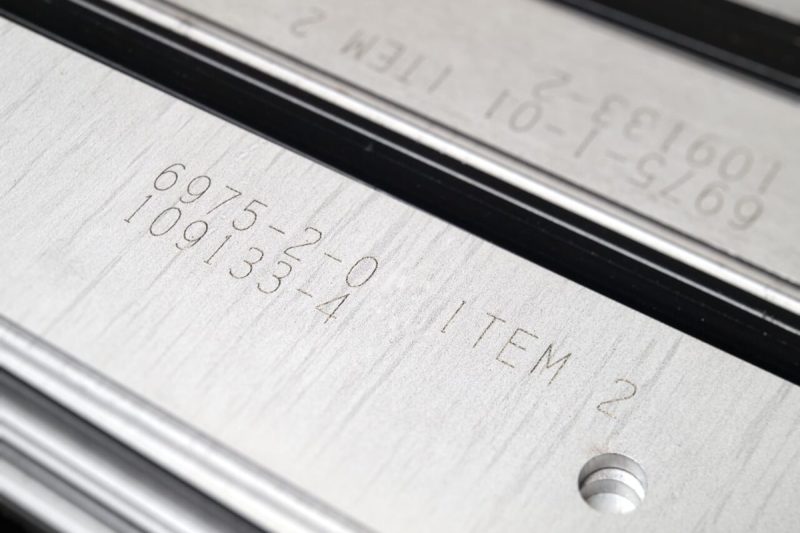
まとめ
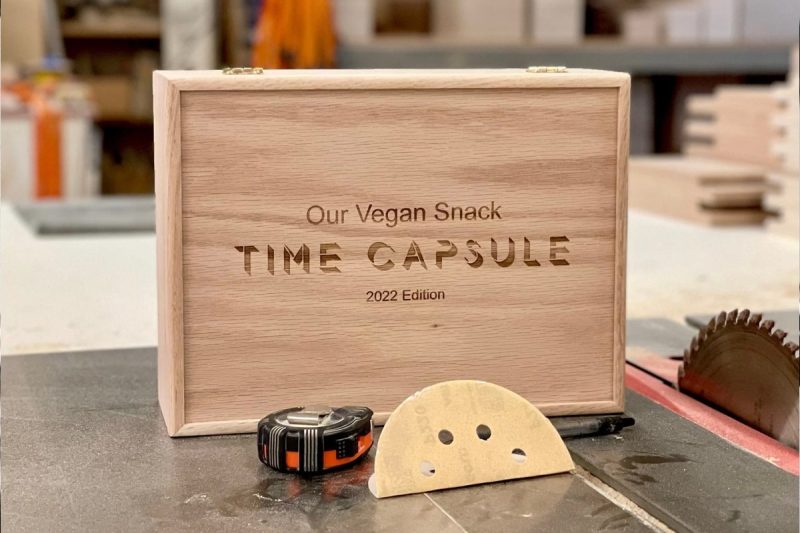
レーザーマーキングソリューションを入手
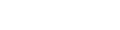
- [email protected]
- [email protected]
- +86-19963414011
- No. 3 ゾーン A、Lunzhen 工業地帯、玉城市、山東省。