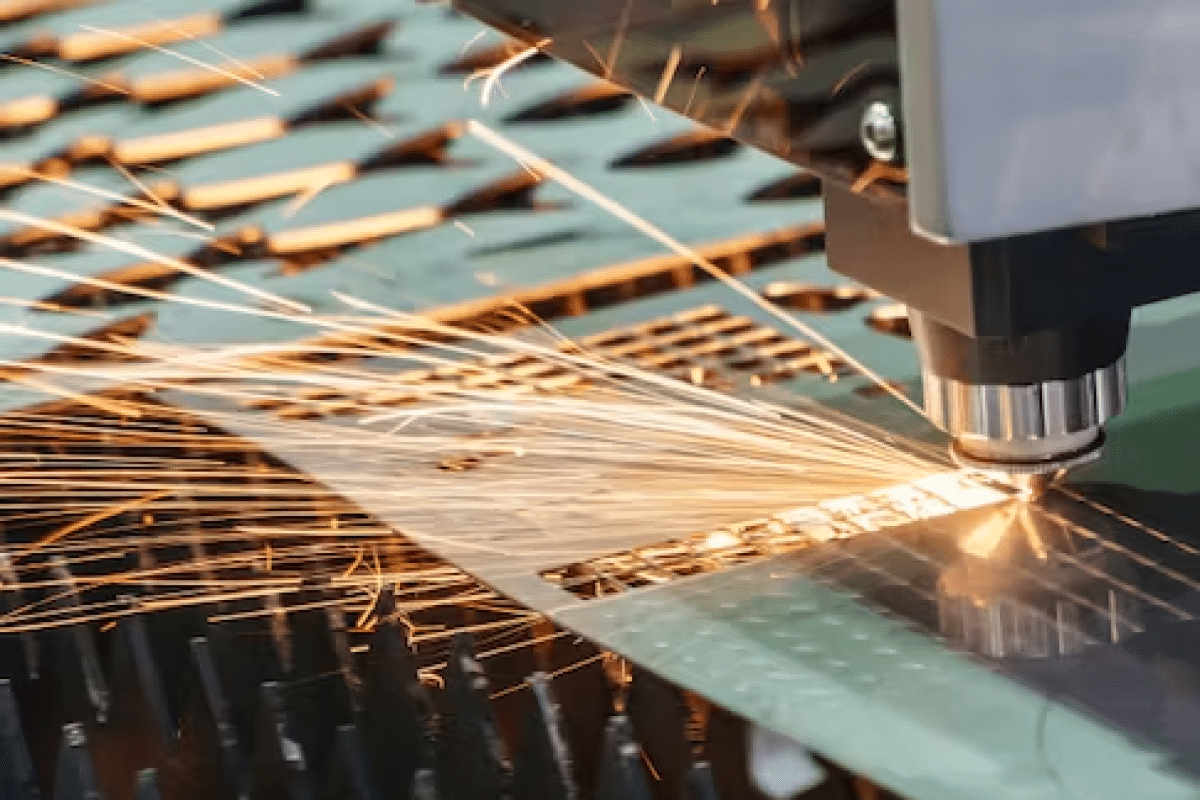
レーザー切断 VS 鋸引き
材料加工は製造業における重要なリンクの 1 つであり、重要なステップとしての切断には常にさまざまな技術が選択されてきました。特定のプロジェクトに最適な方法は、多くの場合、切断される材料の種類、必要な切断の複雑さ、精度のレベルなどのいくつかの要因によって決まります。
この記事では、読者がニーズに合った切断方法をより適切に選択できるように、2 つの主流の切断技術である鋸引きとレーザー切断を詳しく取り上げ、それらがどのように機能するかを理解し、材料加工の分野での長所と短所を比較します。
目次
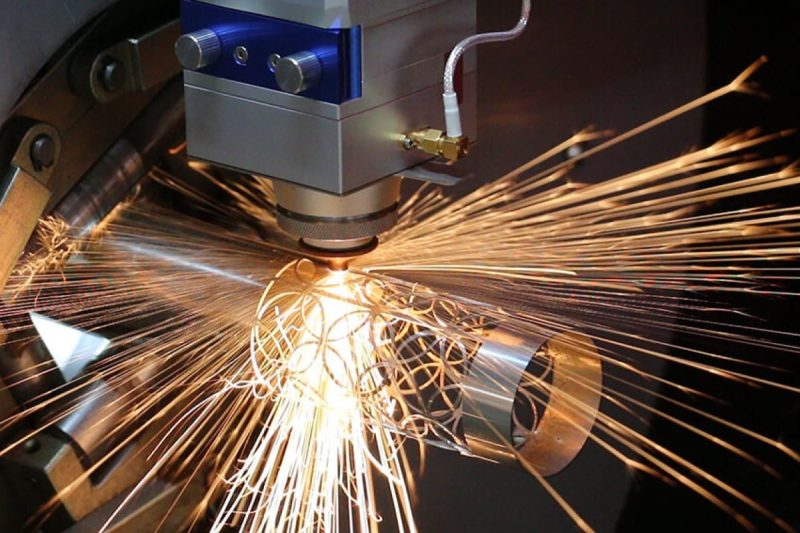
レーザー切断
レーザー切断は、レーザービームを使用して材料を高精度に切断する、高速かつ効率的な材料製造方法です。レーザー切断技術は、その高精度と効率性により広く注目を集めています。
レーザー切断の仕組み
の レーザー切断機 高エネルギーレーザービームを使用して材料を切断する工作機械です。その原理は、電気エネルギーを光エネルギーに変換し、光エネルギーを高エネルギーレーザービームに集中させて、さまざまな材料を切断することです。レーザー切断機の動作方法は、次のように要約できます。
- レーザー放射: レーザー切断機にはレーザー発生器が内蔵されており、高エネルギーのレーザー光線を生成します。
- レーザービームの送信: レンズとレンズシステムを通して、レーザービームは高度に集中した光スポットに集束されます。
- 材料の切断: レーザービームはワークピースの表面に正確に焦点を当て、材料を短時間で蒸発または溶解させるのに十分な温度まで加熱します。制御ソフトウェアはデザインを変換し、レーザー ヘッドの動きをガイドして、希望のパターンのパスをトレースして切断を実現します。
レーザー切断機の主な特徴には、高精度、高速、さまざまな材料 (金属、プラスチック、木材など) への適応性、非接触切断、物理的な工具交換の必要がないことが含まれます。自動車製造、電子製造、金属加工などの分野で幅広く使用されています。
レーザー切断の利点
レーザー切断技術には鋸引きに比べていくつかの利点があり、多くのプロジェクトにとって理想的な製造ソリューションとなっています。主な利点には次のようなものがあります。
- 高精度: レーザー切断技術により、非常に高い切断精度が実現します。レーザー光の径が細いため、材料の表面を精密かつ正確に切断することができます。エレクトロニクス産業や精密部品製造など、切断精度の要求が厳しい用途に適しています。
- 高効率: 従来の鋸引き技術と比較して、レーザー切断は高速です。レーザー光により大量の切断作業を短時間で完了でき、生産効率が向上します。特に大規模生産や自動生産ラインでは、レーザー切断が効率的な選択肢となります。
- 非接触切断: レーザー切断は非接触切断技術です。レーザー光線は物理的接触なしに材料の表面に直接作用します。これは、切断プロセス中に振動や力がかからないことを意味し、材料の変形や損傷を軽減するのに役立ち、材料要件がより高い状況に特に適しています。
- 複数の材料への適応性: レーザー切断技術は、金属、プラスチック、木材、ガラスなどを含むさまざまな材料に優れた適応性を持っています。この複数の材料への適応性により、レーザー切断は幅広い業界や用途で使用できるようになります。
- 工具の交換は不要:材料に応じてさまざまなタイプの鋸刃を交換する必要がある鋸引き技術と比較して、レーザー切断では工具の交換が必要ないため、生産プロセス中のダウンタイムと人件費が削減されます。
- 柔軟性: レーザー切断システムは柔軟性が高く、コンピューター数値制御により正確に制御でき、複雑な形状の切断を実現します。この柔軟性により、レーザー切断はカスタム生産や少量生産に適しています。
レーザー切断のデメリット
レーザー切断技術は多くの点で優れていますが、いくつかの欠点もあります。鋸引き技術と比較したレーザー切断技術の主な欠点は次のとおりです。
- 高い投資コスト: レーザー切断装置は比較的複雑で、高出力レーザー発生器と高度な光学システムを使用するため、装置が高価になります。このため、一部の中小企業や予算が限られている企業にとっては、初期投資が大きな負担となる可能性があります。
- 高い材料要件: レーザー切断には、材料の高い反射率と吸収性が必要です。一部の素材はレーザー切断に適していない場合や、切断するには特別な取り扱いが必要な場合があります。
- メンテナンスと操作のスキルが必要: レーザー切断システムの性能と精度を確保するには、定期的なメンテナンスと校正が必要です。これには専門的なスキルとトレーニングが必要になる場合があり、運用がさらに複雑になります。
- 有害なガスと光放射: レーザー切断プロセス中に窒素酸化物や有機廃ガスなどの有害なガスや煙が発生する可能性があり、これに対処するには効果的な換気システムが必要です。さらに、レーザー切断には潜在的な光放射のリスクが伴うため、適切な保護措置が必要です。
- 切断厚さの範囲が制限されている: 一部の従来の機械切断方法と比較して、レーザー切断は厚い材料を加工する場合に制限がある場合があります。一部の厚い材料の場合、レーザー切断は他の方法ほど効果的ではない場合があります。
- 複雑さと柔軟性のトレードオフ: レーザー切断システムのプログラミングとセットアップは比較的複雑であり、専門知識が必要です。このため、小規模な運用環境では一部のオペレーターが学習曲線に直面し、より長い準備時間が必要になる可能性があります。
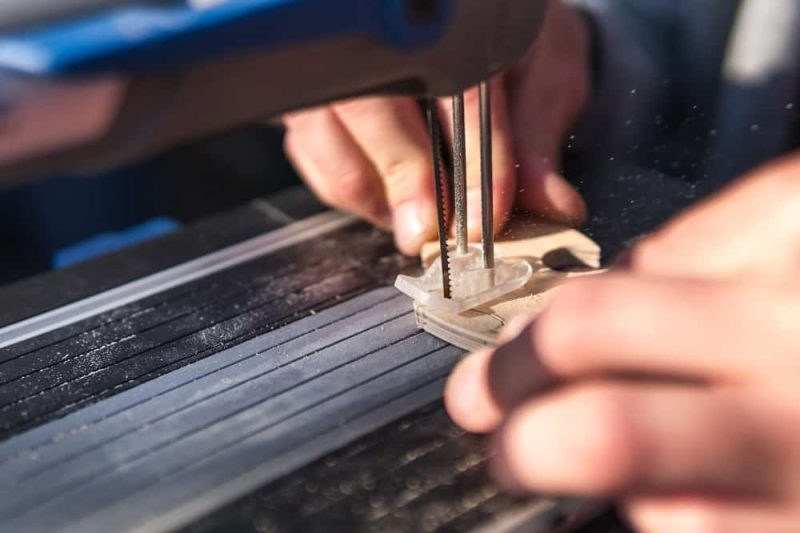
鋸引き
鋸引き技術は、鋸刃を使用して材料を切断する一般的な切断方法です。主に木材や金属など様々な素材の加工に用いられる切断方法です。鋸引きは、手動のこぎり、電動のこぎり、さらにはプロの工業用のこぎりを使用して行うことができます。
鋸引きの仕組み
鋸引きの動作原理は、鋸刃の回転運動に基づいており、鋸歯を通して材料を切断します。一般的な鋸引きの仕組みは次のとおりです。
- 鋸刃の選択: 粗い鋸歯や細かい鋸刃など、さまざまな材質や切断要件に応じて、さまざまな種類の鋸刃を選択できます。
- 回転運動: 鋸刃は通常、回転シャフトに取り付けられており、手動で操作することも、電気モーターで駆動することもできます。鋸刃の回転運動により、その歯が切断対象の材料に入り込み、切断することができます。
- 鋸歯切断: 回転中に鋸歯が継続的に材料に入ります。鋸歯の切断動作により、材料は必要な形状とサイズに分割されます。
- 送り動作: 一部の自動鋸引きシステムでは、通常、切断プロセス中にワークピースが固定パスに沿って移動します。これは送り動作と呼ばれます。これにより、切断プロセス全体を通じて材料が均一に切断されることが保証されます。
鋸引き技術は、家庭装飾や木工プロジェクトから工業生産における金属切断に至るまで、幅広い用途に使用されています。鋸引きが見られます。
鋸引き技術の利点
レーザー切断と比較して、鋸引き技術には、特に特定の用途シナリオや材料加工ニーズの下で、いくつかの独自の利点があります。レーザー切断と比較した鋸引き技術の利点のいくつかを以下に示します。
- 低コスト: 鋸引き装置は比較的シンプルで、レーザー切断装置に比べて投資コストとメンテナンスコストが低くなります。これにより、予算が限られている一部の企業や個人の職人にとって、鋸引き技術がより実用的になります。
- 大きくて厚い材料に適しています: 鋸引き技術は、大きくて厚い材料を加工する場合に一定の利点があります。一部の木材または金属材料では、鋸引き技術により切断作業が容易になります。
- 操作が簡単であること: 鋸引き装置は通常、比較的シンプルで操作が簡単です。対照的に、レーザー切断技術はより複雑なセットアップと操作を必要とする場合があるため、一部の専門家以外のオペレーターにとっては鋸引きの方が使いやすいです。
- さまざまな素材に使用可能: 鋸引き技術は、木材、金属、プラスチックなど、さまざまな種類の素材に幅広く適用できます。レーザー切断では材料に対する要求が比較的高いのに対し、ソーイング技術はこの点でより柔軟です。
- 一部の非常に厚い材料に適しています: 一部の非常に厚い材料には、鋸引き技術の方が適している場合があります。非常に厚い材料を扱う場合、レーザー切断にはいくつかの制限がある場合があります。
- 技術的な敷居が低い: 鋸引き装置の操作は比較的簡単で、過剰な専門スキルやトレーニングは必要ありません。これにより、一部の中小企業や家庭作業場でのこぎり技術の適用が容易になります。
鋸引き技術の欠点
ソーイング技術は特定の用途では利点がありますが、レーザー切断と比較していくつかの欠点もあります。鋸引き技術の主な欠点のいくつかを以下に示します。
- 比較的低い切断精度: 鋸引き技術による切断精度は、特にレーザー切断と比較した場合、比較的低いことがよくあります。電子部品の製造や精密機械部品の切断など、高い精度が要求される用途には適さない場合があります。
- 遅い切断速度: 鋸引きの切断速度は、特に大きくて厚い材料の場合、比較的遅くなります。これは生産効率に影響を与える可能性があり、高スループットが必要な一部の産業環境では鋸引きが適さなくなります。
- 加工中により多くの廃棄物が発生する: 鋸引きプロセスでは、鋸歯の特性により、切断された小さな破片や削りくずなど、より多くの廃棄物が発生する可能性があります。これにより、スクラップのクリーンアップと廃棄のコストが増加し、実稼働環境に追加の作業負荷が生じる可能性があります。
- 制限された形状を切断する能力が弱い: 鋸引き技術は、レーザー切断ほど複雑な形状や曲線を切断する能力が劣ります。レーザー切断は非接触であるため、複雑な形状をより簡単に切断できますが、鋸引きにはこの点で一定の制限があります。
- 一部の特殊な材料には適さない: 鋸引き技術は、複合材料、プラスチック、ガラスなどの一部の特殊な材料には適さない場合があります。一方、レーザー切断技術は、より幅広い種類の材料に適用できます。
- 摩耗とメンテナンス: 鋸刃 (鋸刃) は摩耗しやすいため、定期的に交換する必要があります。これは運用コストを増加させるだけでなく、生産の中断を引き起こす可能性もあります。
- 騒音と振動:鋸引き工程中に発生する騒音と振動は比較的大きく、作業環境や作業者の健康に一定の影響を与える可能性があります。それに比べて、レーザー切断は一般に静かです。
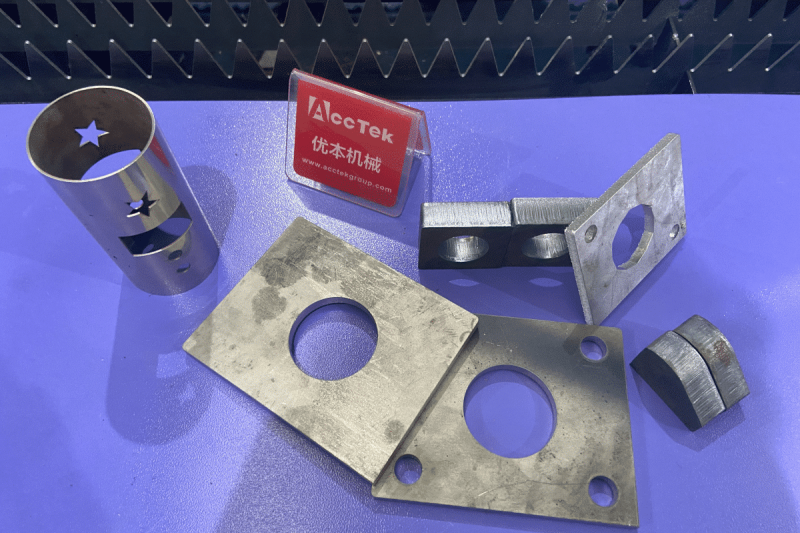
鋸切断VSレーザー切断技術:選択方法
鋸引き技術とレーザー切断技術のどちらを選択するかは、材料の種類、処理要件、予算、生産効率など、いくつかの要因によって決まります。ここでは、2 つの技術のどちらを選択するかを決める際に役立つ提案をいくつか紹介します。
材料の種類
- 鋸引き: 木材、大きな金属片など、比較的厚い、大きい、または複合材料に適しています。
- レーザー切断: 板金、プラスチック、ガラスなどの薄くて精密な材料に適しています。
切断精度の要件
- 鋸引き: 切断精度の要件が特に高くなく、予算が限られている場合は、鋸引きが適切なオプションになる可能性があります。
- レーザー切断: 電子部品製造、精密機械など、高精度の切断が必要なシナリオでは、レーザー切断が要件をよりよく満たすことができます。
生産性とスピード
- 鋸引き: 大きくて厚い材料を扱う場合は鋸引き速度が遅くなることがありますが、より強力な鋸引き装置を使用することで生産性を高めることができます。
- レーザー切断: ほとんどの場合、レーザー切断の方が高速であり、高スループットを必要とする生産環境に特に適しています。
投資コスト
- 鋸引き: 鋸引き装置は通常シンプルで、投資コストが比較的低く、予算が限られている状況に適しています。
- レーザー切断: レーザー切断装置は一般に高価であり、多額の初期投資が必要です。
材料廃棄物
- 鋸引き: 鋸歯の特性により、鋸引き中にさらに多くの廃棄物が発生する可能性があります。材料廃棄物の要件が高い一部の環境では、慎重な考慮が必要です。
- レーザー切断: レーザー切断は非接触切断方法であるため、一般にスクラップの発生が少なくなります。
運用・保守の難しさ
- 鋸引き: 操作は比較的単純で、オペレーターに要求されるスキルは比較的低いです。メンテナンスは主に鋸刃の交換と装置の清掃です。
- レーザー切断: 操作とプログラミングにはより高いスキル レベルが必要な場合があり、機器のメンテナンスと校正の要件は複雑です。
安全性と環境への影響
- 鋸引き: 鋸引きでは、機械的な動きが伴うため、騒音や振動が発生する可能性があります。作業環境やオペレーターの健康に関する要件がある場合には、これらの要素を考慮する必要があります。
- レーザー切断: 通常、発生する騒音は少ないですが、レーザー放射と排気ガスが環境やオペレーターに及ぼす影響に注意を払う必要があります。
要約する
鋸引き技術とレーザー切断技術にはそれぞれ独自の利点と制限があり、さまざまな用途シナリオで適切な切断方法を選択することが重要です。ソーイング技術はコスト重視で高精度を必要としない一部のシーンに適していますが、レーザー切断技術は高精度と効率が必要な領域で優れた性能を発揮します。鋸引きとレーザー切断技術の詳細な比較を通じて、読者はこれら 2 つの切断方法の特徴と適用範囲をより包括的に理解し、実際の生産において適切な切断技術を選択するための参考になると思います。科学技術の継続的な発展に伴い、鋸引きとレーザー切断技術は常に革新され、改善されています。将来的には、変化する製造ニーズに対応するために、より高度な切削技術が登場すると予想されます。
AccTek レーザー は、顧客の多様なニーズに応える包括的なレーザー切断ソリューションを提供します。当社の最先端のレーザー切断技術により、金属、プラスチック、複合材料などのさまざまな材料の正確かつ複雑な切断が可能になります。お客様のプロジェクトに合わせたカスタマイズされたアプローチについて当社にご相談ください。当社の完全なレーザー切断ソリューションの利点を体験してください。
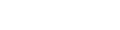
連絡先
- [email protected]
- [email protected]
- +86-19963414011
- No. 3 ゾーン A、Lunzhen 工業地帯、玉城市、山東省。
レーザー ソリューションを入手する