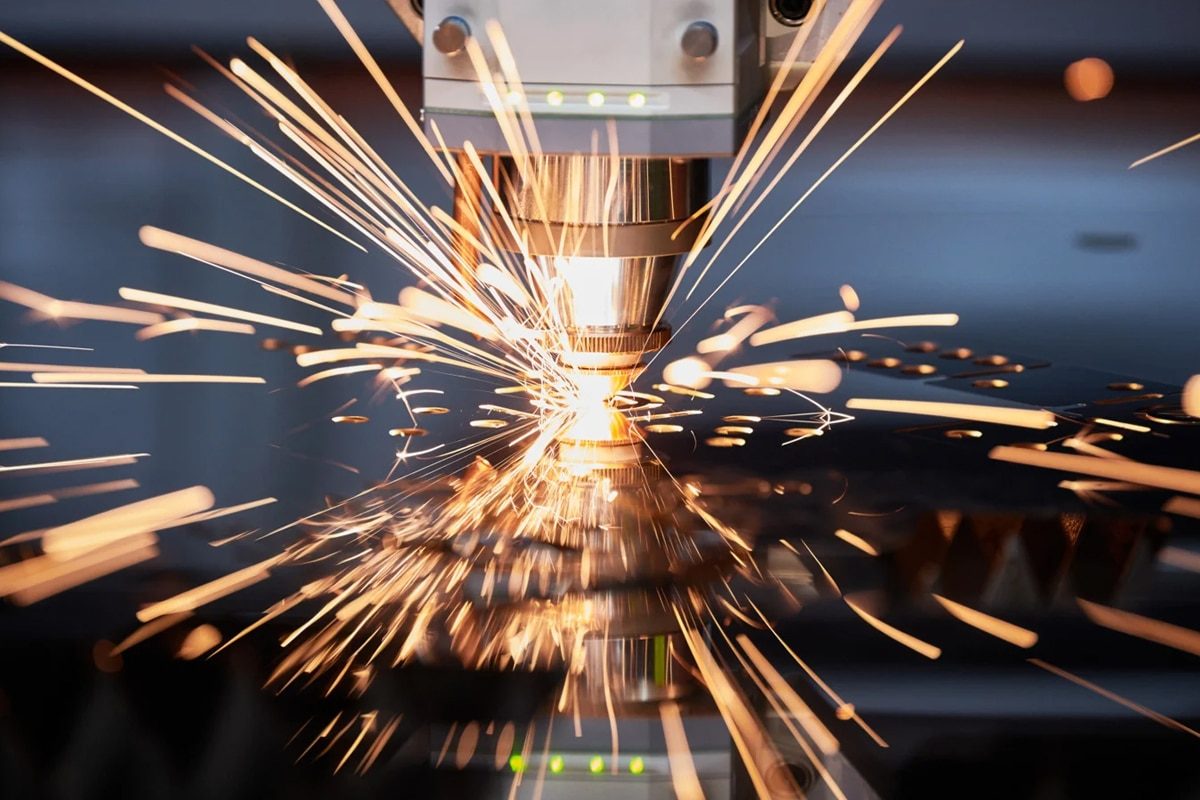
レーザー切断の 3 つの主なタイプとは何ですか?
レーザー切断は、その精度、効率、汎用性により、現代の製造業に不可欠な要素となっています。高出力のレーザービームを集中させて材料を切断または彫刻する技術として、レーザー切断は業界の製造へのアプローチを一変させました。レーザー切断には主に 3 つの種類 (フュージョン切断、フレーム切断、昇華切断) があり、それぞれに明確な利点があり、さまざまな材料や用途に適しています。フュージョン切断は、不活性ガスを使用して酸化物のないきれいな切断面を作るのに優れているため、ステンレス鋼やアルミニウムなどの金属に最適です。フレーム切断は、酸素を利用して発熱反応を起こし、厚い炭素鋼の部分を効率的に処理します。一方、材料を気化させる昇華切断は、薄い材料や非金属の複雑なデザインに優れた精度を提供します。これらの 3 つの切断プロセスを理解することで、メーカーは生産戦略を最適化し、さまざまな用途で最高レベルの品質と効率を実現できます。
目次
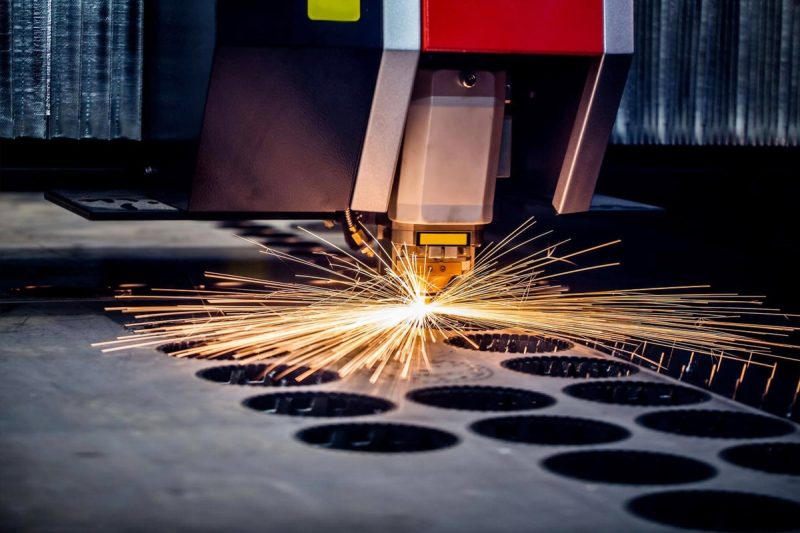
レーザー切断の概要
レーザー切断は製造業に革命をもたらし、さまざまな業界で材料処理のための正確で効率的、かつ多用途な方法を提供しています。レーザー切断では、光学系で焦点を合わせ、CNC (コンピュータ数値制御) システムで誘導する高出力レーザー ビームを使用して、材料を切断、彫刻、または成形します。
レーザー切断の仕組み
レーザー切断は、熱ベースの非接触プロセスであり、焦点を絞ったレーザービームを使用して材料を溶かしたり、燃やしたり、蒸発させたりすることで、きれいで正確な切断面が得られます。このプロセスを段階的に説明します。
- レーザー ソース: レーザー ビームは、密閉されたチャンバー内でレーザー媒体 (通常は CO2、ファイバー、または YAG) を刺激することによって生成されます。
- ビームの伝達: レーザー ビームはミラーまたは光ファイバーを介して導かれ、レンズを使用して材料に集中され、高度に集中した熱源が生成されます。
- 集束および切断ヘッド: レーザー ビームは切断ヘッドに送られます。切断ヘッドには、切断と材料の除去を助ける補助ガス (不活性または反応性) を放出するノズルも含まれています。
- CNC 制御: レーザー ヘッドと材料の動きは CNC システムによって制御され、プログラムされた設計に従ってレーザー パスを正確に誘導します。
- 切断プロセス: 焦点を絞ったビームが材料と相互作用し、材料を溶かしたり、燃焼させたり、蒸発させたりしながら、アシストガスが切断領域から破片や溶融材料を吹き飛ばします。
レーザー切断の利点
- 高精度と正確性: レーザー切断により、複雑で入り組んだ形状を厳しい許容誤差で切断できるため、二次加工の必要性が軽減されます。
- 汎用性:幅広い材料を切断可能。 金属, プラスチック, 木材、セラミックスなど、さまざまな業界に適応できます。
- 材料の無駄が最小限に抑えられます: レーザーの切断幅が狭いため、材料の無駄が最小限に抑えられ、歩留まりが最適化され、コストが削減されます。
- きれいなカットと仕上げの手間の削減: レーザー切断では、バリが最小限に抑えられたきれいなエッジが生成されるため、多くの場合、後処理の必要性がなくなるか、軽減されます。
- 高速処理: 従来の方法と比較して、レーザー切断は作業をより速く完了できるため、生産性が向上し、リードタイムが短縮されます。
- 非接触プロセス: レーザービームは材料に物理的に接触しないため、特に薄い材料や繊細な材料の場合、変形のリスクが少なくなります。
- 自動化との互換性: レーザー切断システムは自動化ソリューションと簡単に統合できるため、生産効率と一貫性が向上します。
レーザー切断は、製造業の可能性の限界を押し広げ続け、比類のない精度、速度、汎用性を提供し、現代の産業の需要に応えています。レーザー切断の仕組みの基本と数多くの利点を理解することで、メーカーはこの技術を利用して生産プロセスを最適化し、優れた結果を達成することができます。
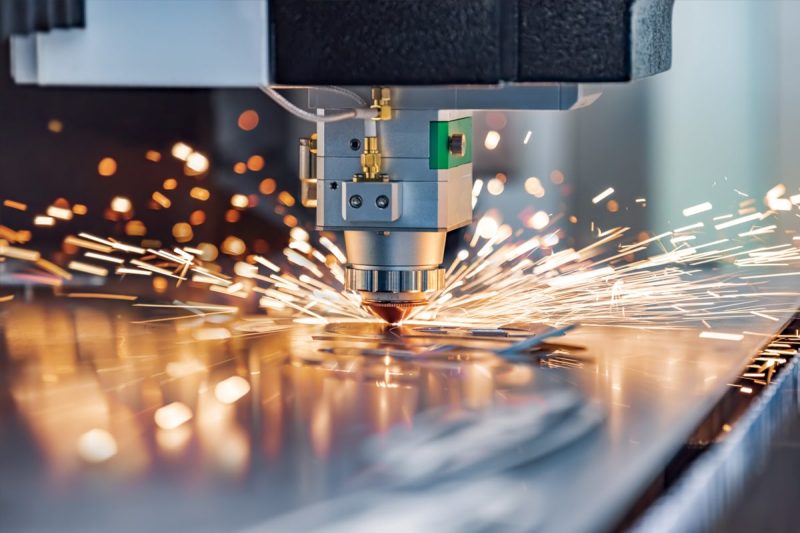
レーザー切断の3つの主な種類
レーザー切断技術には、特定の材料と望ましい結果に合わせて調整された複数の方法があります。主な 3 つのタイプは、フュージョン切断 (メルト アンド ブローとも呼ばれます)、フレーム切断 (反応フュージョン切断)、昇華切断 (気化切断) です。各プロセスのニュアンスを理解することで、特定のアプリケーションに適した技術を選択できます。
溶融切断(メルトアンドブロー)
プロセスの説明
フュージョン切断では、高出力レーザー ビームを使用して材料を溶かし、次に不活性アシスト ガスを使用して切断溝から溶融材料を吹き飛ばします。アシスト ガス (通常は窒素またはアルゴン) は材料と化学反応を起こしません。代わりに、高圧の流れを発生させて切断領域から溶融金属を効率的に除去し、酸化のないきれいで正確な切断を実現します。
溶断の主な手順は次のとおりです。
- 溶解: レーザービームは強力なエネルギーを小さな領域に集中させ、材料を急速に加熱して溶かします。
- 材料の排出: 不活性アシストガスが溶融材料を切断部から吹き飛ばし、再凝固を防ぎ、滑らかなエッジを確保します。
- 連続切断: レーザーが指定されたパスに沿って移動すると、このプロセスが繰り返され、連続切断が作成されます。
溶断に適した材料
フュージョンカットの利点
- 酸化物のないエッジ: 不活性ガスの使用により酸化が防止され、切断後の酸化物除去が不要になります。
- 高精度と高品質: 熱による歪みを最小限に抑え、滑らかできれいなカットを実現します。
- 最小限の後処理: 二次仕上げ作業の必要性を減らします。
- 複雑な形状に適しています: 複雑な形状や細かい部分を正確にカットできます。
フュージョンカットの用途
- 航空宇宙産業: 精度と高品質の仕上げが求められる部品の製造。
- 医療機器製造: 厳格な衛生基準に従って外科用器具やインプラントを製造します。
- 電子機器: 精度が最も重要となる電子機器の部品の切断。
- 自動車産業: 組み立てと美観のために高品質のエッジを必要とする部品の製造。
技術的な考慮事項
- レーザー出力: 特に厚い部分の場合、材料を効率的に溶かすには十分な出力が必要です。
- 補助ガス圧力: 溶融材料を効果的に除去するには高圧不活性ガスが不可欠です。
- 焦点位置: 正確な焦点合わせにより、最適なエネルギー集中と切断効率が保証されます。
- ノズルの設計: 適切なノズルを選択すると、ガスの流れが強化され、切断品質が向上します。
- 材料の反射率: アルミニウムなどの反射率の高い材料では、ビームの反射を防ぐために特殊なレーザーやコーティングが必要になる場合があります。
火炎切断(反応溶融切断)
プロセスの説明
炎切断は、反応性溶融切断またはレーザー酸素切断とも呼ばれ、レーザーの熱と化学反応を組み合わせて切断プロセスを強化します。この方法では、酸素が補助ガスとして使用されます。レーザーは材料を発火温度まで加熱し、酸素は金属 (通常は鋼鉄) と発熱反応を起こし、切断を助ける追加のエネルギーを放出します。
火炎切断における重要な手順:
- 加熱: レーザービームが材料を燃焼温度まで加熱します。
- 発熱反応: 酸素が加熱された金属と反応し、燃焼して余分な熱が発生します。
- 材料の除去: 溶融酸化物が酸素流によって吹き飛ばされ、切断が作成されます。
火炎切断に適した材料
炎切断は、次のような酸化する可能性のある鉄金属に最も効果的です。
- 炭素鋼: 酸素との反応性があるため、火炎切断の主材料となります。
- 低合金鋼: 合金元素の含有量が少ない鋼。
- 軟鋼: 建設や製造によく使用されます。
火炎切断の利点
- 切断厚さ: 同じレーザー出力で、溶融切断に比べて厚い材料を切断できます。
- レーザー電力要件の削減: 発熱反応によりレーザーが補完され、より低い電力で効率的な切断が可能になります。
- 切断速度の向上: 厚い鋼材に特に効果的です。
- コスト効率が高い: 酸素は窒素やアルゴンなどの不活性ガスよりも安価です。
火炎切断の用途
- 重工業: 梁やプレートなどの構造部品の製造。
- 造船:船体やその他の構造物用の大型鋼材を切断します。
- 建設機械:重機部品の製造。
- スチールサービスセンター:さまざまな産業向けの鋼板や鋼板の加工。
技術的な考慮事項
- 切断エッジの酸化: このプロセスにより切断エッジが酸化されるため、きれいな切断エッジが必要な場合は、研磨やサンドブラストなどの後処理が必要になる場合があります。
- 熱影響部 (HAZ): 他の切断方法に比べて HAZ が大きく、切断箇所付近の材料の機械的特性に影響を与える可能性があります。
- 補助ガス純度: 高純度酸素により、カットの一貫性と品質が向上します。
- レーザーの焦点と位置合わせ: 発熱反応を開始し維持するために重要です。
- 材料の厚さ: 発熱反応が最大の効果を発揮する厚い材料に最適です。
昇華切断(気化切断)
プロセスの説明
昇華切断は気化切断とも呼ばれ、材料を液体状態を経ずに固体から気体に直接変換します。レーザー ビームは材料を気化温度まで加熱し、蒸発させます。切断溝から気化した材料を除去するために、補助ガス (通常は窒素などの不活性ガス) が使用されます。
昇華カットの重要な手順:
- 気化: レーザービームは材料を沸点まで急速に加熱し、気化させます。
- 材料排出: アシストガスは気化した材料を切断領域から排出します。
- 精密切断: 溶融材料がないため、熱の影響が最小限で精密な切断が可能です。
昇華カットに適した素材
昇華カットの利点
- 高精度と細部の表現: 切り込み幅が最小限に抑えられているため、複雑なデザインや細部の表現に最適です。
- きれいなカット: バリや溶融残留物のない滑らかなエッジを生成します。
- 熱による損傷を最小限に抑える: 熱入力が低減されるため、熱の影響を受ける領域が最小限に抑えられます。
- 汎用性: 幅広い非金属材料を加工できます。
- 非接触プロセス: 繊細な材料にかかる機械的ストレスを排除します。
昇華切断の応用
- エレクトロニクス産業: プリント回路基板 (PCB) の切断と穴あけ。
- 標識とディスプレイ: 高品質のディスプレイ用にアクリルとプラスチックを正確に切断します。
- 医療機器: 正確な寸法ときれいなエッジを必要とするコンポーネントの製造。
- ファッションとテキスタイル: 端がほつれないように衣類やアクセサリー用の生地を裁断します。
- 美術と工芸: 木材、紙、その他の材料で詳細なデザインを作成します。
技術的な考慮事項
- レーザー出力密度: 特に気化温度が高い材料の場合、気化を達成するには高い出力密度が必要です。
- 材料の厚さ: 薄い材料に最適です。厚い材料では、より多くのエネルギーが必要になります。
- 補助ガスの選択: 不活性ガスは不要な化学反応を防ぎ、気化した物質の除去に役立ちます。
- 換気要件: 気化により煙が発生するため、適切な抽出およびろ過システムが必要になる場合があります。
- 材料特性: 燃焼や焦げ付きを防ぐためには、材料の熱特性を理解することが重要です。
レーザー切断の 3 つの主な種類 (溶融切断、火炎切断、昇華切断) を総合的に理解することで、製造業者やエンジニアは特定の用途に最も適した方法を選択できます。各技術には独自の利点があり、特定の材料や要件に適しているため、レーザー切断は現代の製造プロセスにおいて多目的なツールとなっています。
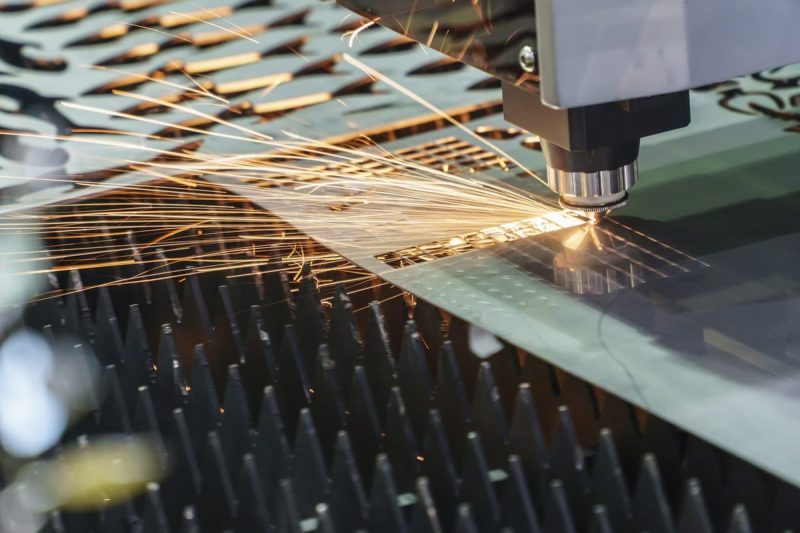
3つの切断方法の比較
レーザー切断の主な 3 つのタイプ、すなわち溶融切断 (メルト アンド ブロー)、炎切断 (反応溶融切断)、昇華切断 (気化切断) を考えると、それぞれの方法には独自の利点があり、特定の用途に適しています。
プロセスメカニズム
- フュージョン カッティング (メルト アンド ブロー): この方法では、レーザーを使用して材料を溶かし、不活性補助ガス (窒素やアルゴンなど) で溶融金属を吹き飛ばします。この方法では、酸化物のないきれいなエッジが生成され、精密なカッティングに最適です。
- 炎切断(反応性溶融切断):炎切断では、酸素を補助ガスとして使用します。酸素は加熱された材料と反応して発熱反応を起こし、プロセスに熱を加えます。これにより、炭素鋼などの厚い材料を効率的に切断できます。ただし、酸化したエッジが残ります。
- 昇華切断(気化切断):このプロセスでは、レーザー ビームの熱を使用して材料を直接気化させ、気化した材料を排出するために不活性ガスを使用します。薄い非金属材料の精密な切断に適しています。
材質の適合性
- フュージョン切断: ステンレス鋼、アルミニウム、非鉄金属などの金属を中心に、幅広い材料に適しています。高品質で酸化のない切断を実現します。
- 炎切断: 酸化反応を利用するため、主に炭素鋼や低合金鋼などの鉄系金属の切断に使用されます。
- 昇華カット: 木材、プラスチック、繊維、セラミック、特定の金属など、精密で複雑なカットが必要な薄い素材に最適です。
エッジ品質
- フュージョンカット: バリが最小限に抑えられ、酸化のないきれいで滑らかなエッジを実現し、後処理の必要性を減らします。
- 炎切断: エッジが酸化されるため、きれいな表面が必要な場合は、研磨などの追加仕上げを行って酸化層を除去する必要がある場合があります。
- 昇華切断: 熱による歪みやバリを最小限に抑え、非常にきれいなエッジを生成するため、エッジの品質が最も重要となる用途に最適です。
切断速度と厚さの能力
- フュージョンカット:薄~中厚の材料に高精度で効果的ですが、材料の厚さが厚くなるにつれて切断速度が低下します。
- 火炎切断: 酸素との発熱反応により厚い材料を高速で切断できるため、重量物の製造や構造部品に効果的です。
- 昇華切断: 蒸発に必要なエネルギーが大きいため、薄い材料に最適です。高精度ですが、厚い部分では効率的でない場合があります。
ガス使用補助
- フュージョン切断: 窒素やアルゴンなどの不活性ガスを使用して酸化を防ぎ、きれいな切断面を作ります。
- 炎切断: 酸素を利用し、金属と反応して発熱反応を起こし、切断プロセスを強化します。
- 昇華切断: 気化した材料を排出するために、材料に応じて不活性ガスを使用するか、またはガスを使用しないことが多いです。
熱影響区域 (HAZ)
- 溶融切断: 追加の反応なしで溶融することに重点を置いているため、比較的小さな熱影響部が生成されます。
- 火炎切断: 発熱反応により熱影響部が大きくなり、切断端付近の材料特性が変化する可能性があります。
- 昇華切断: 急速な蒸発により熱影響部を最小限に抑え、周囲の材料の完全性を維持します。
アプリケーション
- フュージョン カッティング: 航空宇宙、医療、電子産業など、高精度で酸化のないエッジが重要なアプリケーションに最適です。
- 火炎切断: 重工業、建設、造船、および厚い鋼材の切断を必要とするその他の用途で一般的に使用されます。
- 昇華カッティング: 電子機器、繊維、アート、デザイン業界など、薄い素材や繊細な素材の細かい作業に最適です。
コストと効率の考慮
- フュージョン切断: より高い電力とより高価な不活性ガスが必要ですが、優れたエッジ品質と精度が得られます。
- 炎切断: 酸素を使用するため、厚い炭素鋼を切断する場合のコスト効率は高くなりますが、後処理でコストが増加する可能性があります。
- 昇華切断: 厚い材料ではエネルギーを大量に消費するため、薄い材料を使用する特殊な用途に適しています。
概要表
特徴 | フュージョンカット | 火炎切断 | 昇華カッティング |
プロセスメカニズム | 材料を溶かし、不活性ガスが溶解物を除去する | 発熱反応に酸素を使用する | 物質を蒸発させる |
材料 | ステンレス鋼、アルミニウムなどの金属 | 炭素鋼、低合金鋼 | 薄い金属、非金属、プラスチック |
エッジ品質 | クリーン、酸化物フリー | 酸化しているため、仕上げが必要な場合があります | クリーンで正確 |
切断厚さ | 薄手〜中程度 | 厚い素材 | 薄い素材 |
アシストガス | 不活性ガス(窒素、アルゴンなど) | 酸素 | 不活性ガスまたはなし |
危険 | 小さい | 大きい | 最小限 |
アプリケーション | 航空宇宙、エレクトロニクス、医療 | 構造部品、重工業 | 電子機器、繊維、アート |
コスト効率 | コストは高いが精度は高い | 厚切りでもコスト効率が良い | 高精度、薄型材料 |
これらのレーザー切断方法はそれぞれ、現代の製造業において特定の目的を果たします。フュージョン切断、フレーム切断、昇華切断の長所と限界を理解することで、メーカーは材料と希望する結果に最も適したプロセスを選択し、コストとパフォーマンスの両方を最適化できます。
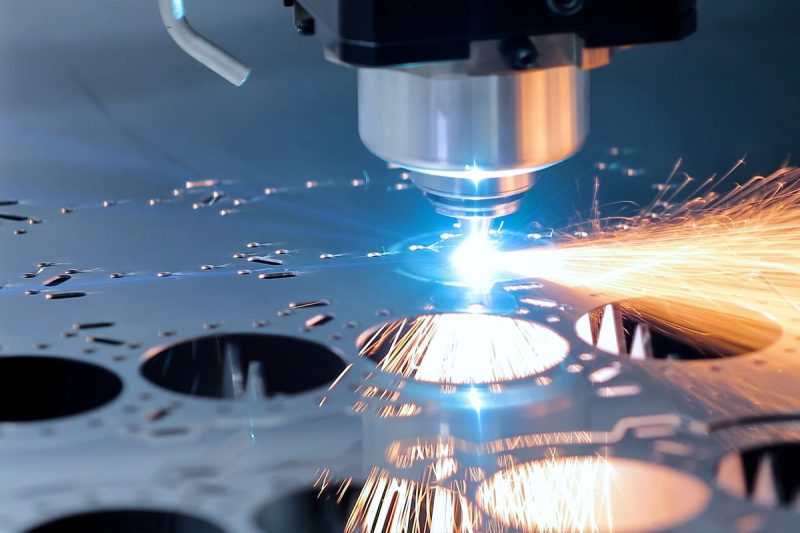
適切な切断方法の選択
適切なレーザー切断方法を選択することは、品質、効率、コスト効率の点で最適な結果を得るために重要です。レーザー切断の 3 つの主な種類、つまり溶融切断 (メルト アンド ブロー)、火炎切断 (反応溶融切断)、昇華切断 (気化切断) の中から選択する場合、材料の特性、必要なエッジ品質、厚さ、速度、生産要件など、いくつかの要素を考慮する必要があります。
材料の種類と特性
- 金属材料: ステンレス鋼、アルミニウム、その他の非鉄金属など、きれいで酸化物のない切断面を必要とする金属の場合、フュージョン切断が最適な選択肢となることがよくあります。不活性ガスを使用することで酸化を防ぎ、高品質で正確な切断を実現します。
- 鉄金属: 炭素鋼やその他の鉄材料を切断する場合、酸素を使用して発熱反応を起こす炎切断は優れたパフォーマンスを発揮します。この方法では厚い材料を効率的に切断できますが、端面が酸化される可能性があります。
- 非金属および薄い素材: 昇華カットは、プラスチック、木材、セラミック、繊維などの非金属素材に最適です。特に薄い素材の場合、複雑なデザインや正確なカットに最適です。
望ましいエッジ品質
- きれいで酸化物のないエッジ: 高品質で酸化のないきれいなエッジがアプリケーションにとって重要である場合は、切断プロセス中に酸化を防ぐ不活性ガスを使用するため、フュージョン切断が推奨されます。
- 酸化エッジ: 強力な発熱反応が必要であり、酸化エッジが許容されるか後処理できる場合は、炎切断が適切なオプションです。
- 高精度で滑らかなエッジ: 電子機器や美術品など、熱による歪みを最小限に抑えながら極めて高い精度と滑らかなエッジが求められる用途には、昇華カッティングが最適です。
材料の厚さ
- 薄から中程度の厚さ: フュージョン カッティングは薄から中程度の厚さの材料に優れており、精密で高品質のエッジを提供します。
- 厚い材料: 炎切断は、発熱反応によりレーザー出力要件が低く、効率的な切断が可能になるため、厚い材料に適しています。
- 非常に薄い素材: 昇華カッティングは非常に薄い素材に最適で、複雑なパターンや形状を高精度に表現できます。
切断速度と効率
- 高速生産: 特に厚い鋼板を切断する場合など、速度が優先される場合、酸素ベースの発熱反応により炎切断が非常に効率的です。
- 速度よりも精度: 速度よりも精度が重要なアプリケーションでは、フュージョン カッティングと昇華カッティングが優れた結果をもたらします。
- バッチ生産とカスタム作業: 生産の性質を考慮してください。フュージョン カッティングは高精度のバッチ処理に適しており、昇華カッティングは複雑な詳細を必要とするカスタム作業に最適です。
コストに関する考慮事項
- 補助ガスのコスト: フュージョン切断では窒素やアルゴンなどの不活性ガスを使用しますが、これはフレーム切断で使用される酸素よりも高価になる場合があります。ただし、優れたエッジ品質が得られます。
- 消費電力: 昇華切断は厚い材料ではエネルギーを大量に消費しますが、薄い部分では効率的です。炎切断では酸素反応によって熱が発生するため、必要なレーザー出力が低く、厚い部分の切断ではコスト効率が高くなります。
- 後処理の要件: 後処理の必要性 (例: 火炎切断における酸化物の除去) により全体的なコストが増加する可能性があるため、決定の際に考慮する必要があります。
申請要件
- 精度が重要な用途: 精度ときれいなエッジが重要な航空宇宙、電子機器、医療機器製造などの業界では、フュージョン カッティングと昇華カッティングが好まれます。
- 重工業の製造: 火炎切断は、構造部品、重機、および厚い金属の切断を必要とするその他の用途に最適です。
- 複雑なデザイン: 特に非金属素材で細かいディテールや複雑なカットが必要な場合は、昇華カットが最適なオプションです。
機器とセットアップに関する考慮事項
- レーザー出力とタイプ: 選択したレーザー システムが適切な出力を持ち、選択した切断方法と互換性があることを確認します。たとえば、反射率の高い金属の場合、フュージョン切断では特殊なレーザー ソースが必要になることがあります。
- 補助ガスの可用性: 補助ガスの可用性とコストを考慮してください。火炎切断では通常酸素が使用されますが、溶融切断では不活性ガスが必要です。
- 自動化と統合: レーザー切断を自動化生産ラインに統合する場合、精密切断機能により、フュージョン切断と昇華切断の方が互換性が高くなることがよくあります。
適切なレーザー切断方法の選択は、材料の特性、希望する切断品質、厚さ、コストの制約、および特定のアプリケーション要件によって異なります。フュージョン切断は、薄から中程度の厚さの金属を高精度で酸化のない切断するのに最適です。フレーム切断は厚い鉄材料を効率的に切断するのに優れており、昇華切断は薄い材料や複雑なデザインに優れた精度を提供します。これらの要素を慎重に評価することで、レーザー切断プロセスを最適化して効率と品質を最大限に高め、生産ニーズに最適な結果を得ることができます。
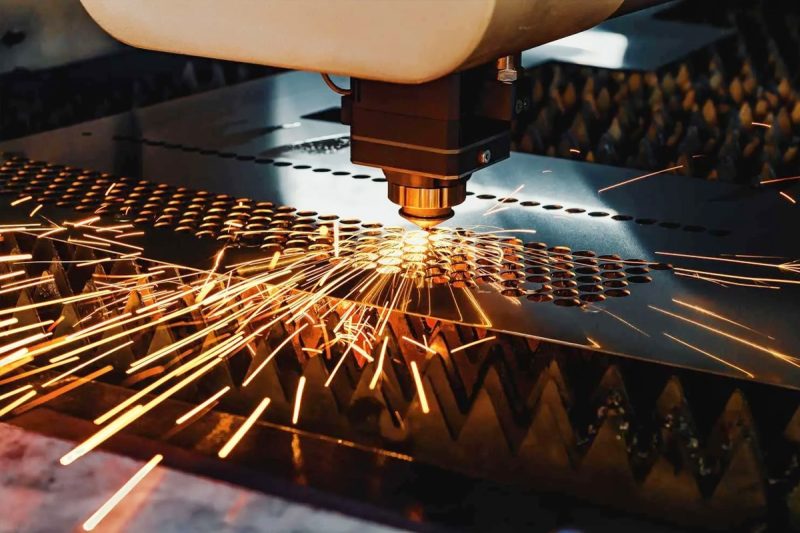
まとめ
レーザー切断は現代の製造業に欠かせない技術となり、幅広い用途で精度、汎用性、効率性を提供しています。レーザー切断には主に 3 つの種類 (フュージョン切断、フレーム切断、昇華切断) があり、それぞれ目的が異なります。フュージョン切断では不活性ガスを使用して、高品質で酸化物のない切断面が得られるため、ステンレス鋼やアルミニウムなどの金属に最適です。フレーム切断では酸素を使用して発熱反応を起こし、厚い鉄材料を効率的に切断できるため、特に耐久性の高い製造に適しています。昇華切断では材料を直接蒸発させるため、非金属や特殊な金属部品などの複雑なデザインや薄い材料に優れた精度が得られます。各切断方法の機能と用途を理解することで、メーカーはプロセスを最適化して優れた品質とコスト効率を実現し、レーザー切断を活用して多様な産業ニーズに対応できます。
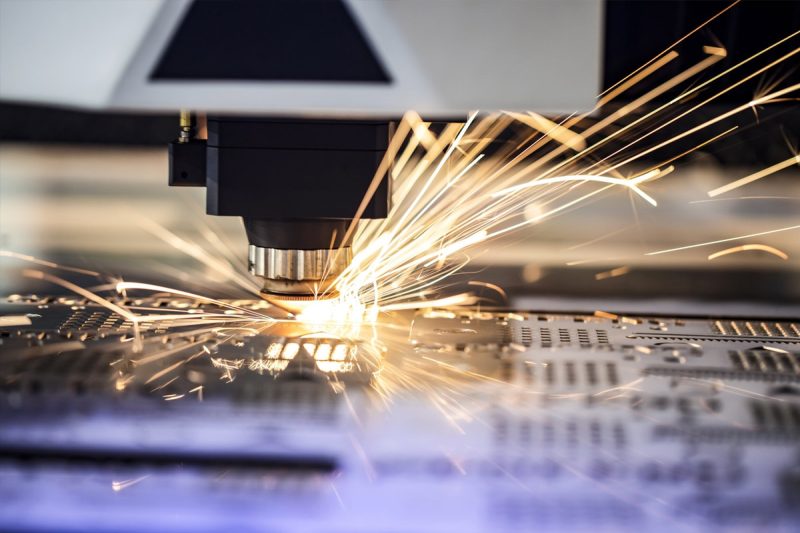
レーザー切断ソリューションを入手
製造業務において最適な精度、効率、生産性を実現するには、適切なレーザー切断方法を選択することが不可欠です。金属のクリーンで酸化のない切断、厚い材料の効率的な処理、非金属基板の複雑なデザインなど、AccTek Laserはお客様のニーズにぴったり合うレーザー切断ソリューションを提供します。フュージョン切断、フレーム切断、昇華切断技術の専門知識を持つ当社の レーザー切断機 多様なアプリケーションや業界で優れたパフォーマンスを提供します。当社の高度なシステムは、高精度、材料の無駄を最小限に抑え、運用効率を最大限に高めるように設計されており、生産目標に対して最高の結果を保証します。
AccTek Laser の切断ソリューションには、販売前のコンサルティング、カスタム構成オプション、信頼性の高いアフターサービスなど、包括的なサポートが付属しています。生産能力の強化や既存のプロセスの最適化をお考えの場合でも、AccTek Laser は最先端のレーザー技術と専門家のガイダンスを提供します。 お問い合わせ あなたのビジネスに最適なレーザー切断ソリューションを今すぐ見つけてください。
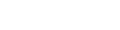
連絡先
- [email protected]
- [email protected]
- +86-19963414011
- No. 3 ゾーン A、Lunzhen 工業地帯、玉城市、山東省。
レーザー ソリューションを入手する