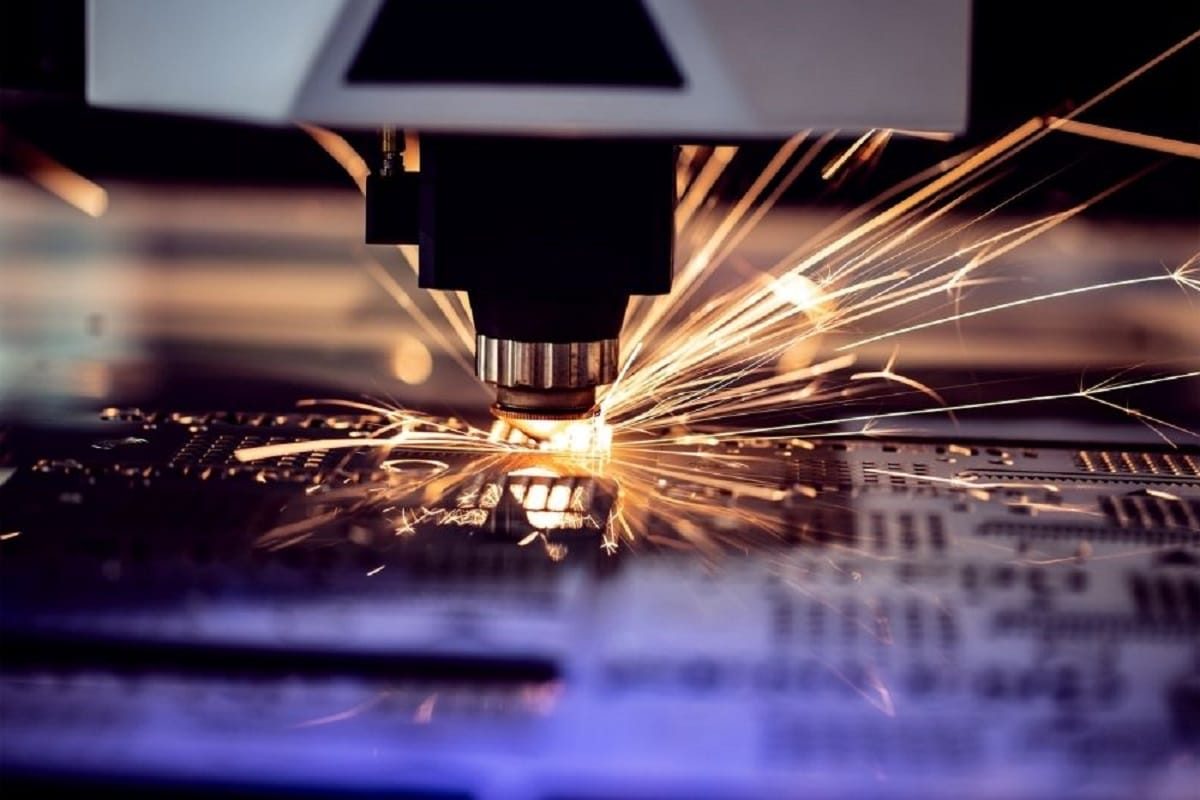
レーザー切断の設計上の考慮事項
レーザー切断 は、製造業から芸術、デザインに至るまで、幅広い業界に応用される多用途かつ精密な技術となっています。同時に、複雑なパターン、詳細なカット、きれいなエッジを作成できるため、多くのプロジェクトで最初に選択されます。ただし、他のプロセスと同様に、レーザー切断にも独自の一連の設計上の考慮事項と制限があり、設計者とエンジニアは、望ましい切断結果を達成するためにこれらを克服する必要があります。この記事では、これらの設計要素について詳しく説明します。
目次
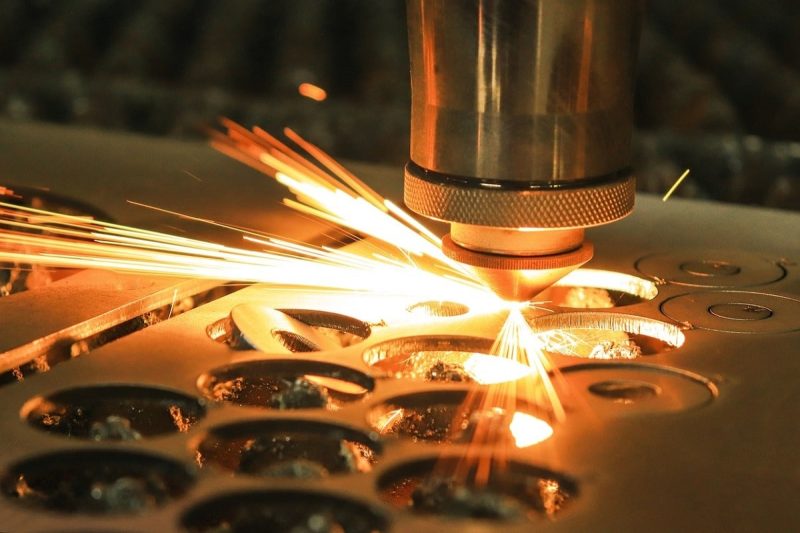
インテリアデザインの考慮事項
レーザー切断技術を使用したインテリア デザインの検討では、デザイン自体の特定の機能、形状、特性に焦点を当てます。これらの考慮事項は、設計がレーザー切断技術に適切に適合していることを確認するのに役立ち、切断プロセスの成功と最終製品の品質に影響を与える可能性があります。レーザー切断を使用する場合のインテリア デザインの重要な考慮事項は次のとおりです。
閉じた形状とミシン目
- レーザー切断は、閉じた形状や輪郭を扱う場合に最も効率的です。これらの形状により、切断プロセス中に材料が安定し、レーザーが正確に追従しやすくなるからです。
- デザインにミシン目(穴)が含まれている場合は、材料の変形や切断の困難を避けるために、ミシン目(穴)が十分な間隔であり、十分な大きさであることを確認する必要があります。材料の厚さとレーザー発生器の能力を考慮してください。
フィーチャの寸法と公差
設計上の特徴は、レーザー発生器の機能および使用される材料の厚さと一致している必要があります。次の側面に焦点を当てる必要があります。
- フィーチャーの寸法: 穴、スロット、カットなどのデザイン内のフィーチャーに細心の注意を払ってください。材料の厚さとレーザー機能に合わせて適切なサイズであることを確認してください。性能特性が達成できない場合や、特殊なレーザー機器が必要な場合があります。
- 公差: レーザー ビームの幅 (カーフ) および潜在的な材料の変動を考慮して、適切な公差を設計に組み込みます。適切な公差により、切断後に部品を正確に組み合わせることができます。
鋭いコーナーと内側の半径
- デザイン内の非常に鋭い角は、レーザー切断に課題を引き起こす可能性があります。レーザービームの直径には限界があるため、若干の丸みが発生する傾向があります。
- 切断精度を向上させるには、デザインに小さなフィレットや丸い角を追加することを検討してください。意図しない切断や材料の除去を避けるために、内側の半径がレーザービームの直径に適合するように設計されていることを確認してください。
材料の適合性
- プロジェクトに選択した材料がレーザー切断プロセスと互換性があることを確認してください。素材が異なれば、吸収特性や切断能力も異なります。
- 選択した材料がレーザー切断条件下でどのように機能するかを理解し、それに応じてデザインを最適化できます。
設計の複雑さ
- レーザー切断は複雑なデザインに最適であり、詳細で正確なパターンをデザインすることでこの機能を活用できます。
- ただし、レーザー切断で非常に微細な細部を実現すること、特にレーザービームの直径 (カーフ) より小さい細部を実現することは困難な場合があります。
カット補正
- レーザー ビーム (カーフ) の幅を考慮してデザインを調整します。必要なパーツ サイズを得るためにラインをわずかに内側にカットする必要がある場合があります。
ネストに関する考慮事項
- 1 枚の材料シートに複数のパーツまたはパターンをネストする場合は、切断時の干渉を避けるためにパーツ間に十分な間隔を確保しながら、材料の使用を最適化する方法で設計します。
材料の厚さ
- デザインの特徴は、使用される材料の厚さと一致している必要があります。設計にさまざまな厚さの材料が含まれている場合は、レーザー切断機がこれらの変化に対応できるように適切に設定されていることを確認してください。
材料の木目方向
- 材料、特に木材や特定の金属などの材料の木目の方向を考慮してください。より良い結果を得るには、木目の方向に合わせてデザインを調整または適応させます。
内部の特徴と空洞
- レーザー切断機は材料の内部特徴や空洞にアクセスできない場合があるため、それに応じて設計を計画し、内部切断が必要な場合は代替の製造方法を検討してください。
これらの内部設計の考慮事項に対処することで、レーザー切断設計を最適化し、切断プロセスの効率と精度を向上させ、最終的な切断部品がプロジェクトの要件を確実に満たすことができます。経験豊富なレーザー切断サービスプロバイダーまたはエンジニアと協力することで、設計と材料の選択に関して貴重なガイダンスを得ることができます。

外部設計の考慮事項
レーザー切断の外観デザインの考慮事項は、デザイン自体の外側の要素に焦点を当てますが、切断プロセスの成功と結果の全体的な品質にとって重要です。これらの考慮事項には、プロセス全体、材料の取り扱い、機械の操作に関連する要素が含まれます。レーザー切断を使用する場合の外観設計の重要な考慮事項は次のとおりです。
マテリアルサポート
- 切断中の材料の反り、振動、変形を防ぐために、切断テーブル上で材料を適切に支持してください。サポートが不十分だと、不正確な切断が発生し、切断品質が低下する可能性があります。
マテリアルハンドリングとアライメント
- 切断プロセス中に材料が平らで安定し、確実に配置されるように、切断テーブル上に材料を適切にロードして位置合わせします。
- 材料の位置がずれていたり不安定であると、不正確な切断が発生し、切断品質が低下する可能性があります。
換気と空気の流れ
- 切断する材料によっては、レーザー切断により煙やガスが発生する可能性があります。切断エリアでのこれらの副産物を排除するために、適切な換気とスケジュールを考慮した設計を行ってください。
- 適切な空気の流れは、切断領域から破片を取り除き、明確な切断経路を維持するのに役立ちます。材料に適したガス流量と種類を決定するには、レーザー切断機のメーカーに相談することをお勧めします。
リードインワイヤとリードアウトワイヤ
- リードインパスとリードアウトパスを設計に組み込みます。これらのパスはレーザー ビームの入口と出口のポイントであり、切断プロセスのスムーズな開始と停止を確保するのに役立ちます。
- リードインラインとリードアウトラインにより、切断の開始時と終了時の不要なマークや欠陥を防ぐことができ、切断品質が向上します。
オーバーカットとアンダーカットを避ける
- オーバーカットは、レーザー ビームが意図した切断パスをわずかに超えて伸びると発生し、その結果、材料が過剰に除去されます。
- アンダーカットは、レーザービームが意図した切断経路に到達しない場合に発生し、材料が切断されないまま残る可能性があります。
- これらの問題は、設計を微調整し、切断パラメータを最適化し、レーザー切断機を適切にメンテナンスすることによって最小限に抑えることができます。
外部サポート体制
- 設計に、切断プロセス中に簡単に動く可能性のある繊細な部品や薄い部品が含まれている場合は、切断プロセスが完了するまで部品を所定の位置に保持するために、外部サポート構造またはタブを追加することを検討してください。
- これらの支持構造は、切断が完了した後に除去できます。
ノズルの位置と焦点
- レーザー切断ノズルが正しく配置され、切断される材料に焦点が合っていることを確認してください。正確なカットを実現するには、適切なノズルの位置合わせと焦点合わせが重要です。
機械の安全対策
- 材料の取り扱いやレーザー切断装置の操作時には安全対策を講じてください。安全ガイドラインに従い、適切な個人用保護具 (PPE) を使用し、適切な換気を提供してオペレーターを保護し、安全な作業環境を維持してください。
機械のメンテナンス
- 最適なパフォーマンスを確保するために、レーザー切断機を定期的にメンテナンスおよび校正してください。適切なメンテナンスは、ビームの位置ずれや出力の変動など、切断品質に影響を与える可能性のある問題を防ぐのに役立ちます。
レーザー光の集光とパワー調整
- 材料と厚さに応じて、レーザービームの焦点と出力設定を調整して、切断プロセスを最適化します。理想的な設定を見つけるには、ある程度の実験とテストが必要になる場合があります。
ノズルの掃除とメンテナンス
- 最適なパフォーマンスを確保するために、レーザー切断ノズルを定期的に清掃およびメンテナンスしてください。きれいなノズルは、一貫した切断品質と精度を維持するのに役立ちます。
廃棄物管理
- 切断プロセス中に発生するスクラップや廃棄物に対処するための廃棄物管理計画を作成します。適切な廃棄物処理は、清潔で安全な作業空間を維持するのに役立ちます。
これらの外部設計上の考慮事項に対処することで、レーザー切断プロセスの成功に貢献し、潜在的な問題や欠陥を最小限に抑え、最終的な切断部品が必要な品質基準を満たすようにすることができます。経験豊富なレーザー切断サービス プロバイダーまたはオペレーターと協力することで、レーザー切断プロジェクトの外部要因を最適化するための貴重なガイダンスも得られます。
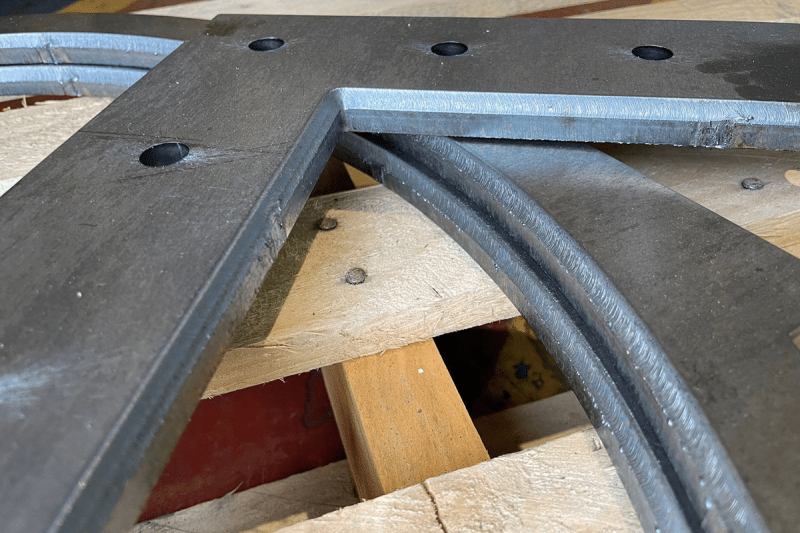
ネストされた最適化
レーザー切断におけるネスティング最適化設計は、最も効率的な方法で材料シート上に部品やパターンを配置し、無駄を最小限に抑え、材料の利用率を最大化します。ネスティングを正しく行うと、コストが大幅に節約され、材料の無駄が減り、生産効率が向上します。レーザー切断のネストされた最適化で最良の結果を得るには、次の重要な考慮事項を考慮してください。
部品の形状と向き
- 部品の形状を分析し、スペース利用率を最大化し、材料の無駄を最小限に抑えるために適切なネストを選択します。
- 部品の向きを最適化して、切断中の材料の動きを減らし、レーザーヘッドの移動時間を最小限に抑えます。
最適なパネルサイズの選択
- パーツまたはパターンの寸法に厳密に一致する材料シート サイズを選択してください。適切なサイズのボードを使用すると、無駄が最小限に抑えられ、材料の利用率が最大になります。必要以上に大きなボードの使用は避けてください。
ネスティングソフトウェア
- 専用のネスティング ソフトウェアまたは設計ソフトウェアの機能を利用して、ネスティング プロセスを自動化します。これらのツールは、デザイン、材料シートの寸法、および切断パラメータを分析して、ネスティングを自動的に最適化します。
材料効率
- パーツを重ならないように近接して配置することで、材料の効率的な利用を優先します。部品間の過度の間隔を避けることで、無駄を減らし、生産コストを削減できます。
重複したカットを避ける
- さまざまなパーツの切断パスが重ならないようにしてください。カットが重なると、エッジが不均一になり、材料が無駄になる可能性があります。ネスティング ソフトウェアを使用すると、パーツが重ならないように自動的に配置されます。
材料の厚さの一貫性
- 均一な切断品質を維持し、ネスティングに影響を与える可能性のある変動を避けるために、材料の厚さがシート全体で一貫していることを確認してください。さらに、材料の厚さにばらつきがあると、切断結果が不均一になる可能性があります。
パネル使用率の最適化
- ネスティング ソフトウェアを使用すると、不規則な形状や材料特性を考慮して、シート材料上にパーツを配置する最も効率的な方法を計算できます。ソフトウェアによっては、無駄を最小限に抑えるためにパーツを回転させることもできます。
- 場合によっては、特定の要件に従ってパーツを手動で配置した方が、自動ネスティング ソフトウェアのみに依存するよりも良い結果が得られる場合があります。さまざまな配置を試して、最適な配置を見つけてください。
部品の切断順序の優先順位
- 材料の変形や部品間の干渉のリスクを最小限に抑えるために、部品を切断する順序を考慮してください。最初に小さなフィーチャまたは内部フィーチャを切断すると、材料の安定性を維持できます。
等高線のネスティング
- 輪郭ネスティング技術を使用して、同様の形状のパーツを互いに密接にネストすることで、無駄をさらに削減し、材料の使用を最適化します。
動的ネスト
- 一部の高度なネスティング ソフトウェアは、設計や利用可能な材料の変更に基づいてパーツの配置をリアルタイムで動的に調整できます。この柔軟性により、カスタムまたはオンデマンド製造での材料の使用が最適化されます。
廃棄物管理
- 可能な限り廃棄物を管理し、再利用するための戦略を策定します。以前の切断からの小さな残骸には、小さな部品に使用できるセクションがまだある場合があります。
要約する
レーザー切断は比類のない精度と柔軟性を提供しますが、その可能性を最大限に引き出すには、設計上の考慮事項と制限事項を深く理解する必要があります。適切な材料を選択し、設計を最適化し、レーザー切断技術の機能を尊重することで、設計者とエンジニアは、潜在的な落とし穴を回避しながら、この革新的な製造プロセスのパワーを解き放つことができます。経験豊富なレーザー切断機メーカーまたは専門家と協力することで、特定のプロジェクト要件に合わせた貴重な洞察が得られ、レーザー切断作業を成功させることができます。
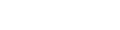
連絡先
- [email protected]
- [email protected]
- +86-19963414011
- No. 3 ゾーン A、Lunzhen 工業地帯、玉城市、山東省。
レーザー ソリューションを入手する