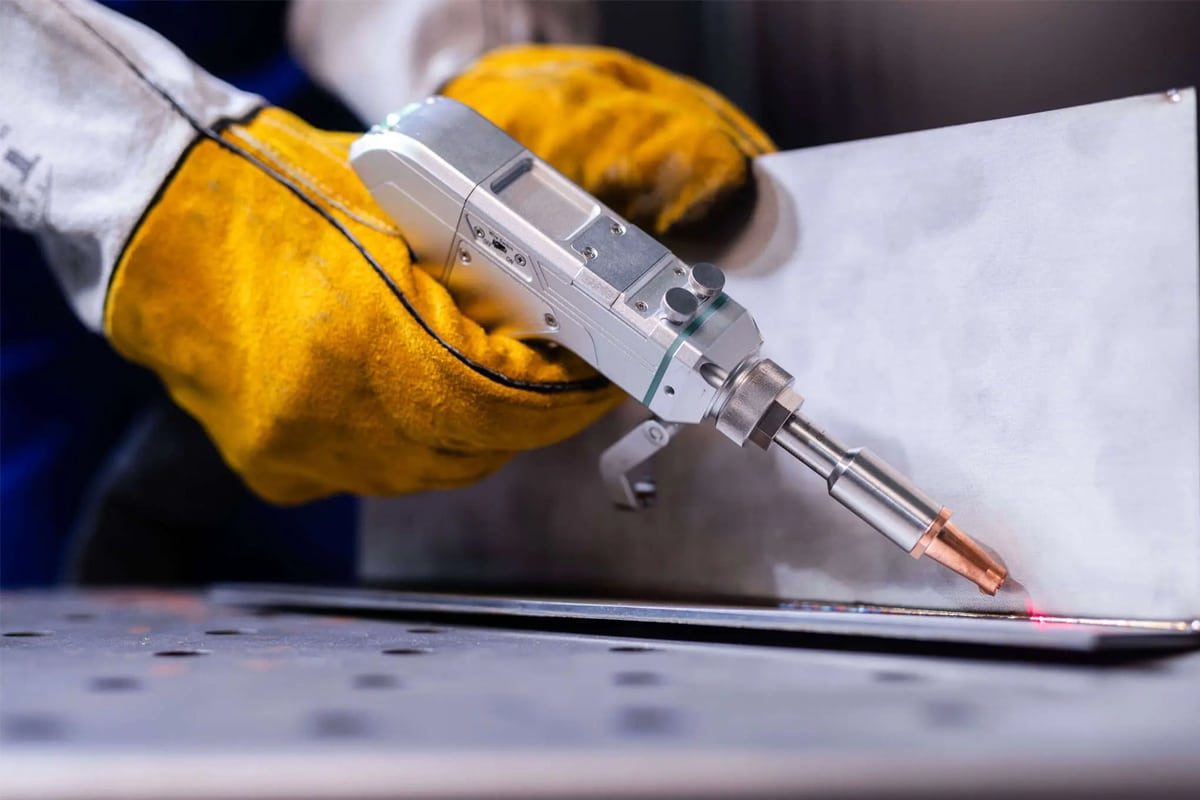
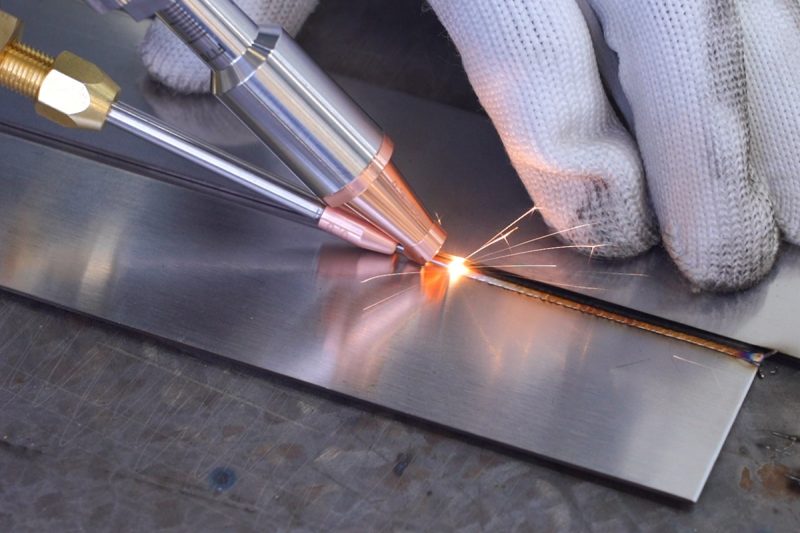
レーザー溶接の概要
レーザー溶接とは何ですか?
レーザー溶接は、高度に焦点を絞ったレーザー ビームを使用して材料を加熱して融合する、正確で効率的な接合プロセスです。レーザー ビームは集中した熱源を生成するため、熱影響部 (HAZ) を最小限に抑えた狭く深い溶接が可能になります。レーザー溶接は、電力密度と材料特性に応じて、主に 2 つのモードで動作します。
- キーホール モード溶接: このモードでは、高出力密度のレーザー ビームが材料を蒸発させ、溶融金属と蒸気で満たされた狭く深いキーホールを作成します。キーホールはレーザー エネルギーの導管として機能し、深い浸透と高アスペクト比の溶接を可能にします。このモードは、自動車産業や航空宇宙産業など、狭く深い溶接を必要とする用途に最適です。
- 伝導モード溶接: このモードはキーホール溶接に比べて低い電力密度で行われ、レーザーは材料を蒸発させずに加熱します。表面からの熱伝導により、浅く広い溶接プールが形成されます。伝導モード溶接は、薄い材料や、最小限の浸透と熱入力が求められる場合に適しています。
レーザー溶接の利点
レーザー溶接には、従来の溶接方法に比べて有利ないくつかの利点があります。
- 精度と正確性: 集中したレーザービームにより精密な制御が可能になり、歪みを最小限に抑えた正確な溶接を実現します。
- 高速処理: レーザーの高エネルギー密度により、溶接速度が速くなり、生産性が向上し、サイクル時間が短縮されます。
- 最小限の熱影響部: 熱拡散が低減されるため、歪みが最小限に抑えられ、レーザー溶接は繊細な部品や薄い部品に適しています。
- 自動化機能: レーザー溶接は自動化システムやロボットアームに簡単に統合できるため、大量生産の効率が向上します。
- 材料の多様性: チタンやステンレス鋼などの溶接が難しい材料を含む、幅広い金属や合金の溶接が可能です。
- 非接触プロセス: 物理的な接触が不要なため、ツールの摩耗が軽減され、電極の汚染のリスクが排除されます。
レーザー溶接の用途
レーザー溶接は、その独自の機能と精度により、さまざまな業界で使用されています。
- 自動車産業: 高精度と高速性が重要となる車体パネル、ギア、トランスミッション部品、排気システムの溶接に使用されます。
- 航空宇宙産業: タービンブレード、構造部品、エンジン部品などの軽量で高強度の部品の溶接に適しています。
- エレクトロニクス産業: 電子機器の繊細な回路、コネクタ、筐体のマイクロ溶接に最適です。
- 医療機器製造: 精度と清潔さが最も重要となる複雑な医療機器、外科用器具、インプラント部品の溶接に使用されます。
- ジュエリーおよびアート: 複雑なジュエリー デザインや芸術的な金属細工の精巧な修理および製作を可能にします。
- 工業製造: さまざまな産業分野における金属板、配管、および頑丈な構造部品の接合に適用されます。
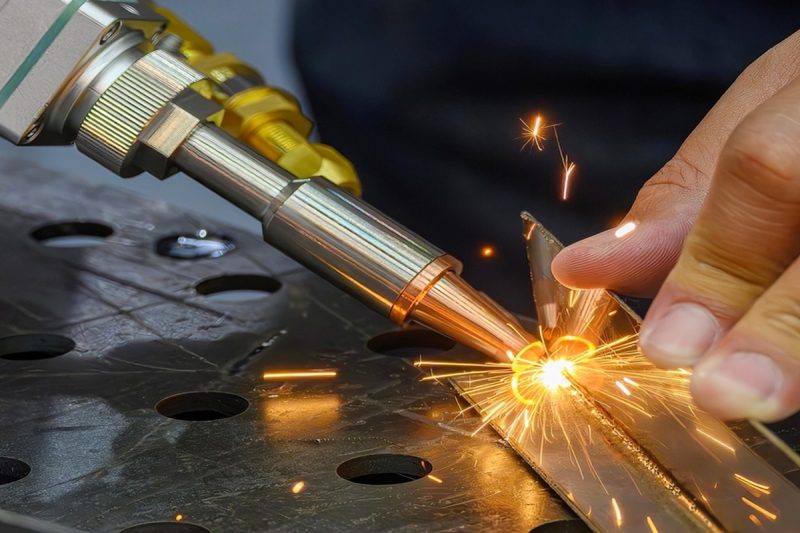
レーザー溶接における一般的な溶接欠陥
気孔率
原因
- 表面汚染: ワークピースの表面にある油、グリース、水分、錆は、加熱されるとガスを発生し、溶接部内に気泡が閉じ込められる原因となります。
- シールドガスの問題: シールドガスの適用範囲が不十分、流量が低い、またはガスの種類が不適切であると、酸素や窒素の侵入などの大気汚染が発生し、ガスポケットが形成される可能性があります。
- 材料組成: 母材に高濃度の水素、硫黄、炭素、その他の不純物が含まれていると、溶接中にガスが発生する可能性があります。
- 急速冷却: 溶融池を急速に凝固させることで、ガスが逃げる前に閉じ込めることができます。
ソリューション
- 表面洗浄: 溶接前にワークピースを徹底的に洗浄し、グリース、油、錆などの汚染物質を除去します。
- 最適化されたシールド ガス フロー: アルゴンやヘリウムなどの適切なシールド ガスを使用して、正しい流量と範囲を確保し、溶接プールを保護します。
- 材料の選択と準備: 不純物含有量の少ない材料を選択し、ガス抜きなどの溶接前処理を実行します。
- パラメータ調整: レーザーパラメータを調整して冷却を制御し、ガスが逃げる時間を確保します。
クラッキング
ひび割れの種類
- 高温割れ: 引張応力または不純物の偏析 (硫黄など) により、凝固中に高温で発生します。
- 冷間割れ: 冷却後に発生し、多くの場合、水素脆化、残留応力、または不適切な材料組成に関連します。
原因
- 高い温度勾配: 急速な加熱と冷却のサイクルにより残留応力が生じ、ひび割れが促進される可能性があります。
- 材料構成: 特定の合金、特に硫黄や炭素を多く含む合金は、ひび割れが発生しやすくなります。
- 不純物: 硫黄やリンなどの元素が粒界に偏析し、構造を弱める可能性があります。
- 水素吸収: 湿気、汚染されたシールドガス、またはベースメタルを通じて水素が導入されると、遅延割れが発生する可能性があります。
ソリューション
- 予熱と溶接後の熱処理: ワークピースを予熱して温度勾配を減らし、溶接後の熱処理を実行して残留応力を軽減します。
- 材料管理: 不純物レベルの低い材料を選択し、その化学組成を最適化して、亀裂の発生可能性を低減します。
- 水素制御: 乾燥した材料を使用し、乾燥したシールドガスの使用や湿気の回避など、低水素プロセスを使用します。
- 応力緩和技術: 固定具と適切なジョイント設計を使用して、応力の集中を最小限に抑えます。
アンダーカット
原因
- 過度の熱入力: レーザー出力が高かったり移動速度が遅かったりすると、十分な充填金属がないと局所的に溶融し、材料が失われる可能性があります。
- ビーム角度が正しくない: 接合部に対するレーザー ビームの位置がずれていると、融合ではなく材料の除去につながる可能性があります。
- 不適切な焦点: レーザーの焦点が不正確だと、エネルギーが不均一に集中する可能性があります。
ソリューション
- 熱入力を最適化: レーザー出力、移動速度、ビーム径を調整して熱分布を制御します。
- ビームの位置合わせ: 均一な溶融と充填を確実に行うために、レーザー ビームをジョイントに適切に位置合わせします。
- 溶接技術: レーザーの角度と位置を調整して材料の損失を減らします。
融合の欠如
原因
- 熱入力不足: レーザー出力が低い、または移動速度が速すぎると、ベース材料が完全に融合されない可能性があります。
- 不適切な接合準備: ワークピース間のフィットアップ不良、隙間、または位置ずれにより、完全な融合が妨げられる可能性があります。
- 汚染: 表面の酸化物、汚れ、その他の汚染物質は、融合の障壁として機能する可能性があります。
ソリューション
- 熱入力の増加: 適切な融合を実現するために、十分なレーザー出力を使用するか、移動速度を下げます。
- ジョイントのフィットアップを改善: ワークピース間の適切な位置合わせとフィットを確保し、一貫した溶接の浸透を実現します。
- 表面洗浄: 溶接表面から酸化物、油、その他の汚染物質を除去します。
不完全な浸透
原因
- レーザー出力が低い: 材料の厚さを完全に溶かすためのエネルギー入力が不十分です。
- 移動速度が速い: レーザーの移動速度が速すぎるため、接合部を完全に加熱して溶かすことができません。
- 不適切なビーム焦点: レーザーの焦点を誤って合わせると、貫通が浅くなる可能性があります。
ソリューション
- レーザー出力を上げる: ジョイントを完全に貫通するように出力設定を調整します。
- 移動速度を下げる: レーザーが材料を加熱して溶かす時間を長くします。
- 正しいビーム焦点: レーザーを適切に焦点を合わせて、一貫した浸透深度を実現します。
スパッタ
原因
- 過剰なレーザー出力: 出力設定を高くすると、溶融池が激しく沸騰する可能性があります。
- 汚染物質: 表面の不純物が熱と反応して急速に蒸発する可能性があります。
- 不適切なシールドガス: シールドが不十分だと酸化が起こり、飛散の原因になります。
ソリューション
- レーザー パラメータの調整: レーザー出力を減らし、パルス設定を最適化して、過剰なエネルギー入力を防ぎます。
- 表面洗浄: 溶接前に表面に汚染物質がないことを確認します。
- シールドガスの最適化: 適切なシールドガスを使用し、適切な流量を維持します。
溶接ビードの不規則性
原因
- 移動速度の不一致: 速度の変動により熱入力が不均一になります。
- レーザー出力の変動: 出力の変化により、溶融が不均一になる可能性があります。
- ビーム焦点が正しくない: 焦点がずれていると、エネルギー分布が不均一になります。
ソリューション
- 一定の移動速度を維持する: 溶接プロセス全体を通じて均一な速度を確保します。
- 電力出力の安定化: 安定した電源を使用して、一貫したレーザー出力を維持します。
- ビーム焦点の調整: ビームの位置合わせと焦点が正しいことを確認して、均一なエネルギー供給を実現します。
バーンスルー
原因
- 過度の熱入力: レーザー出力が高かったり移動速度が遅かったりすると、過剰な溶融が発生する可能性があります。
- 薄い素材: 薄いシートは焼け落ちやすくなります。
- ビームの焦点が不適切: エネルギーを狭い領域に集中させると、溶解が悪化する可能性があります。
ソリューション
- 熱入力を減らす: レーザー出力を下げるか、移動速度を上げます。
- ビーム焦点を広げる: レーザーエネルギーをより均等に分散します。
- 適切な材料の厚さを使用する: 材料の厚さを溶接要件に合わせてください。
変形と歪み
原因
- 熱応力: 急速な加熱と冷却のサイクルにより膨張と収縮が発生します。
- 薄い素材: 反りや曲がりが発生しやすくなります。
- 過度の熱入力: 高いエネルギー入力は深刻な歪みを引き起こす可能性があります。
ソリューション
- 熱入力を最適化: 制御されたレーザー パラメータを使用して過剰な熱を最小限に抑えます。
- 固定具とクランプ: 固定具を使用してワークピースを所定の位置に保持し、動きを抑えます。
- バランス溶接: 加熱のバランスを取り、ストレスを最小限に抑える技術を使用します。
酸化と変色
原因
- シールドガスが不十分: ガス流量が低い、またはカバー範囲が狭いと、溶接プールが空気にさらされる可能性があります。
- 不適切なガス組成: シールドガスの選択を誤ると、酸化を防止できない場合があります。
- 汚染物質: 表面の不純物が反応して酸化を引き起こす可能性があります。
ソリューション
- 適切なシールドを確保する: 溶接プールを保護するために、適切なシールドガス流量を使用します。
- 適切なガス組成を選択する: 酸化を効果的に防ぐシールドガス (アルゴンなど) を選択します。
- 表面洗浄: 溶接中の反応を最小限に抑えるために、ワークピースの表面を徹底的に洗浄します。
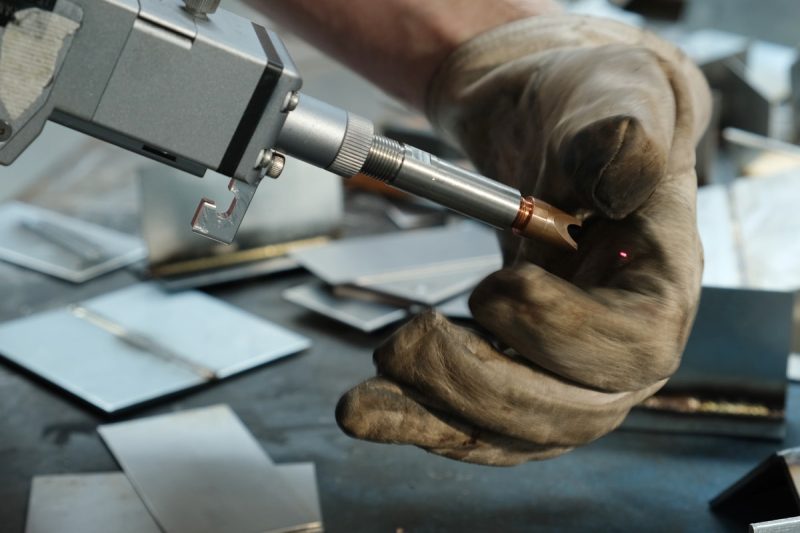
溶接欠陥に影響を与える要因
材料特性
溶接される材料の特性は、溶接の品質と欠陥の可能性を決定する上で重要な役割を果たします。
- 熱伝導率: アルミニウムなどの熱伝導率の高い材料は熱を急速に放散する傾向があるため、十分な浸透と融合を実現するには、より高いレーザー出力またはより遅い移動速度が必要になります。制御が不十分だと、融合不足や不完全な浸透などの欠陥が発生する可能性があります。
- 融点: 融点が異なる材料には、異なるレーザー パラメータが必要です。たとえば、チタンは融点が高く、より大きなエネルギー入力が必要ですが、亜鉛などの融点の低い材料は、慎重に管理しないと焼け落ちてしまう可能性があります。
- 反射率: 銅や特定のアルミニウム合金などの反射率の高い材料は、レーザー エネルギーの一部を反射し、有効な熱入力を低下させる可能性があります。反射エネルギーが周囲の領域に影響を与える可能性があるため、不完全な融合、不均一な浸透、または飛散が発生する可能性があります。
- 材料の組成と不純物: 材料に含まれる硫黄、リン、水素などの元素は、多孔性や割れなどの欠陥の可能性を高める可能性があります。たとえば、水素含有量が多いと多孔性が生じ、硫黄とリンは高温割れのリスクを高めます。不純物レベルの低い材料を選択するか、溶接前の処理を実施すると、これらの問題を軽減できます。
溶接パラメータ
レーザー溶接パラメータの適切な選択と制御は、欠陥を防ぐために非常に重要です。主なパラメータは次のとおりです。
- レーザー出力: 完全な浸透と融合を実現するには、適切なレーザー出力が不可欠です。出力が不十分だと、融合が不十分になったり、浸透が不完全になったりする可能性があります。一方、出力が過剰だと、溶け落ち、飛び散り、変形が生じる可能性があります。
- 移動速度: 移動速度は、溶接の単位長さあたりの熱入力に影響します。速度が速すぎると、材料が適切に加熱されず、融合不足や不完全な溶け込みなどの欠陥が生じる可能性があります。逆に、速度が遅すぎると、熱入力が過剰になり、溶け落ちや歪みが生じる可能性があります。
- ビーム フォーカス: エネルギーを集中させるには、ビームのフォーカスが正確であることが不可欠です。焦点の位置がずれていたり、焦点の位置が間違っていると、溶け込みが不十分になったり、ビード プロファイルが不規則になったり、溶接部に多孔性が生じたりすることがあります。深い溶け込みには、スポット サイズの小さい焦点ビームが必要ですが、広くて浅い溶接には、焦点をずらしたビームが適している場合があります。
- パルス持続時間 (パルス レーザー溶接): パルス持続時間は、各パルスで供給されるエネルギー量に影響します。短いパルスは熱入力を減らし、変形のリスクを最小限に抑えるため、繊細な材料や熱に敏感な材料に最適です。長いパルスは浸透が大きくなりますが、スパッタや多孔性などの欠陥のリスクが増す可能性があります。
ジョイントデザイン
接合部の設計と準備は、溶接の品質と欠陥の可能性に大きな影響を与える可能性があります。
- フィットアップ許容範囲: 適切なジョイント フィットアップは、一貫した溶接品質を実現するために不可欠です。ワークピース間の隙間や位置ずれは、融合不足、多孔性、または不均一な溶け込みの原因となります。フィットアップがきつく締められると、溶融池をより適切に制御でき、欠陥のリスクを最小限に抑えることができます。
- ジョイント タイプ: ジョイント タイプ (突合せ、重ね合わせ、すみ肉など) によって、必要なレーザー溶接技術とパラメータが異なります。たとえば、突き合わせジョイントの位置合わせが悪いと、アンダーカットや融合不足が生じる可能性があり、重ね合わせジョイントの重なりが多すぎると、スパッタや融合不足が生じる可能性があります。
- アクセス性: 複雑な構造では、ジョイントへのアクセスが制限されるとレーザー ビームの到達範囲が制限され、不完全な融合や不規則なビード形成につながる可能性があります。アクセス性が制限されているジョイントでは、適切な固定とレーザーの位置合わせが必要です。
- 準備と洗浄: 表面の汚染物質は多孔性、ひび割れ、飛散の原因となる可能性があるため、接合部を適切に準備して洗浄することが重要です。洗浄により、融合を妨げ、欠陥を引き起こす可能性のある酸化物、油、その他の不純物が除去されます。
環境要因
溶接エリアの環境条件は、溶接品質と欠陥の発生に直接影響を与える可能性があります。
- 周囲温度: 極端に低いまたは高い温度での溶接は、溶接部の冷却速度に影響を与え、熱応力や割れの原因となります。たとえば、低温環境では急速な冷却が起こり、溶接部の脆化や割れの原因となります。
- 湿度と水分: 環境中の水分により溶接プールに水素が入り込み、多孔性と水素誘起割れのリスクが高まります。高品質の溶接を行うには、乾燥した管理された環境で溶接するか、湿気への曝露を防ぐための予防措置を講じることが不可欠です。
- シールドガスの品質と流量: シールドガスは溶融溶接プールを大気汚染から保護します。シールドガスの流量が不十分であったり、純度の低いガスを使用したりすると、酸化、多孔性、変色が生じる可能性があります。さらに、汚染を防ぐために、材料の要件に基づいてアルゴンやヘリウムなどのシールドガスを使用する必要があります。
- 振動と動き: 溶接セットアップにおける環境の振動や動きにより、溶接ビードの不一致やその他の欠陥が発生する可能性があります。安定した固定具を使用し、外部の動きを最小限に抑えることが、一貫した結果を確保する上で不可欠です。
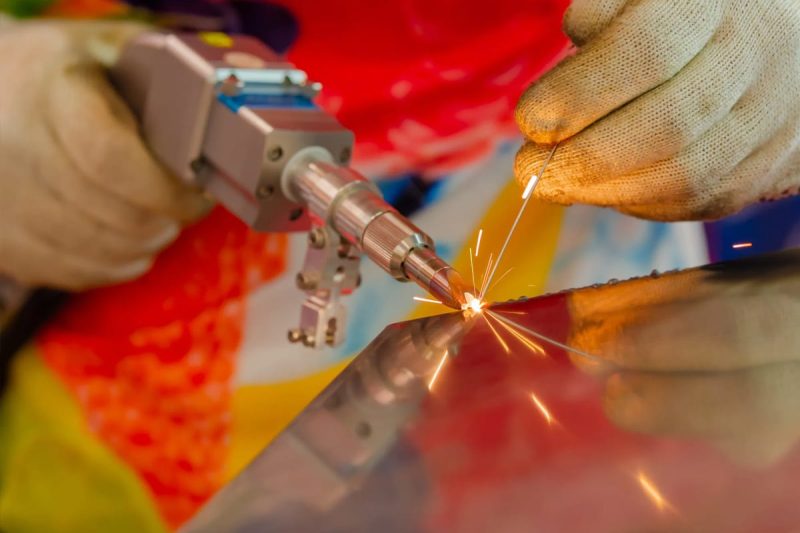
追加の考慮事項とベストプラクティス
適切な材料の選択
高品質の溶接を実現し、欠陥を最小限に抑えるには、レーザー溶接に適した材料を選択することが不可欠です。
- 材料の適合性: ベース材料がレーザー溶接に適合していることを確認します。材料によって融点、熱伝導率、反射率が異なるため、レーザー エネルギーに対する反応は異なります。たとえば、アルミニウムなどの反射性材料では、反射を減らして熱吸収を最適化するために特別な対策が必要になる場合があります。
- 材料の純度: 多孔性、ひび割れ、その他の欠陥の原因となる硫黄やリンなどの不純物の含有量が少ない材料を使用します。
- 材料の厚さ: 溶接する材料の厚さは必要なレーザー出力と熱入力に影響するため、考慮してください。
レーザーの種類と設定
適切なレーザーの種類を選択し、その設定を微調整することが、レーザー溶接を成功させる上で重要な要素です。
- レーザー タイプ: 用途に応じて、連続波 (CW) レーザーとパルス レーザーを選択します。CW レーザーは高速溶接に最適で、パルス レーザーは繊細な部品や熱に敏感な部品に適しています。
- 出力と速度の設定: レーザー出力、移動速度、パルス持続時間を最適化して、必要な浸透を実現し、飛散や多孔性などの欠陥を最小限に抑え、熱入力を制御します。
- ビームの焦点と位置決め: 均一なエネルギー分散と一貫した溶接には、適切なビームの位置合わせと焦点が不可欠です。
ジョイント設計とフィットアップ
適切なジョイント設計とフィットアップにより、一貫した溶接品質が確保され、融合不足、多孔性、位置ずれなどの欠陥の可能性が低減されます。
- フィットアップ許容範囲: ジョイントのフィットアップがしっかりと一貫していることを確認し、不均一な融合や多孔性につながる可能性のある隙間を最小限に抑えます。
- ジョイントのアクセス性: レーザー ビームが簡単にアクセスできるようにジョイントを設計し、不完全な融合や不規則なビーズが発生するリスクを最小限に抑えます。
- ジョイントの準備: ジョイント表面を適切に洗浄して準備し、油、酸化物、その他の不純物などの汚染物質を除去します。
シールドガスの選択
シールドガスは溶融溶接プールを大気汚染から保護し、酸化、多孔性、その他の欠陥を防止します。
- ガスの種類: ベース材料と必要な溶接特性に基づいて、アルゴン、ヘリウム、または混合物などの適切なシールド ガスを選択します。たとえば、アルゴンはステンレス鋼によく使用されますが、ヘリウムは厚い材料の浸透を改善できます。
- 流量: シールドガスの流量が、乱流や不十分なカバーなしに溶接プールをカバーするのに十分であることを確認します。
- 純度: 汚染を避けるために高純度シールドガスを使用します。
溶接前および溶接後の処理
溶接前および溶接後の処理により、欠陥の可能性を大幅に低減し、全体的な溶接品質を向上させることができます。
- 溶接前の洗浄: 多孔性、ひび割れ、その他の欠陥の原因となる油、錆、湿気などの汚染物質を除去するために、ワークピースを徹底的に洗浄します。
- 予熱: 特にひび割れが発生しやすい材料を予熱すると、温度勾配が減少し、残留応力を最小限に抑えることができます。
- 溶接後熱処理: 残留応力を低減し、溶接部の機械的特性を向上させるために、アニーリングや応力緩和などの溶接後熱処理を実行します。
オペレータートレーニング
熟練したオペレーターは、一貫した高品質のレーザー溶接を保証する上で重要な役割を果たします。
- 技術トレーニング: 位置決め、速度制御、パラメータ調整など、レーザー溶接装置の適切な取り扱いについてオペレーターをトレーニングします。
- 欠陥の特定: 一般的な欠陥とその原因を認識し、再発を防ぐために必要な調整を行う方法をオペレーターに教育します。
- 安全プロトコル: オペレーターが自分自身と作業環境を保護するためにレーザー安全手順のトレーニングを受けていることを確認します。
設備保全
レーザー溶接装置の定期的なメンテナンスは、一貫したパフォーマンスを確保し、欠陥を防ぐために不可欠です。
- 光学部品のクリーニング: ビームの品質と精度を維持するために、レンズ、ミラー、その他の光学部品を定期的にクリーニングします。
- キャリブレーション: レーザー システムを定期的にキャリブレーションして、正確な出力、ビームの位置合わせ、および焦点を確保します。
- コンポーネント検査: ノズルやレンズなどの摩耗または損傷したコンポーネントを検査して交換し、溶接の一貫性を維持します。
プロセス監視
プロセスの監視と制御は、一貫性のある欠陥のない溶接を実現するために不可欠です。
- リアルタイム監視: センサーと監視システムを使用して、電力変動、移動速度、ビーム焦点などの溶接パラメータの偏差をリアルタイムで検出し、修正します。
- データ ロギング: 溶接パラメータと結果を記録して傾向を分析し、欠陥の根本原因を特定し、継続的な改善策を実施します。
- 品質検査: 非破壊検査 (NDT) 方法を含む定期的な検査を実施して、溶接品質を確認します。
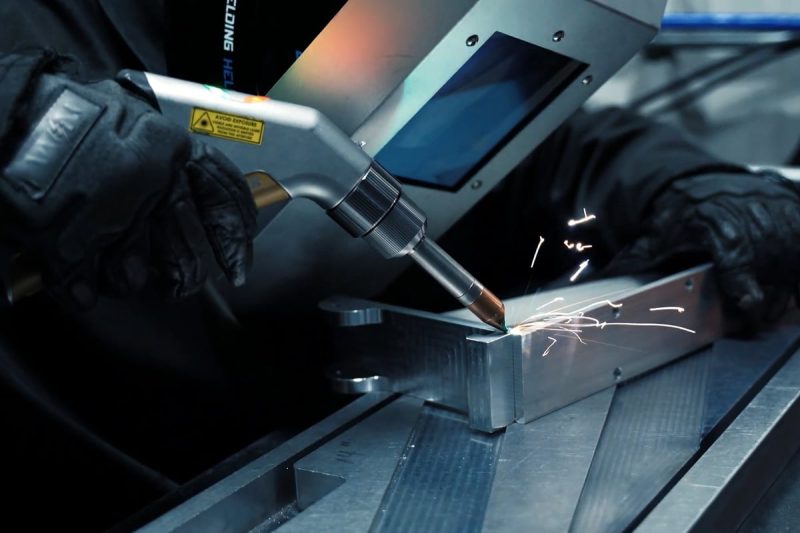
まとめ
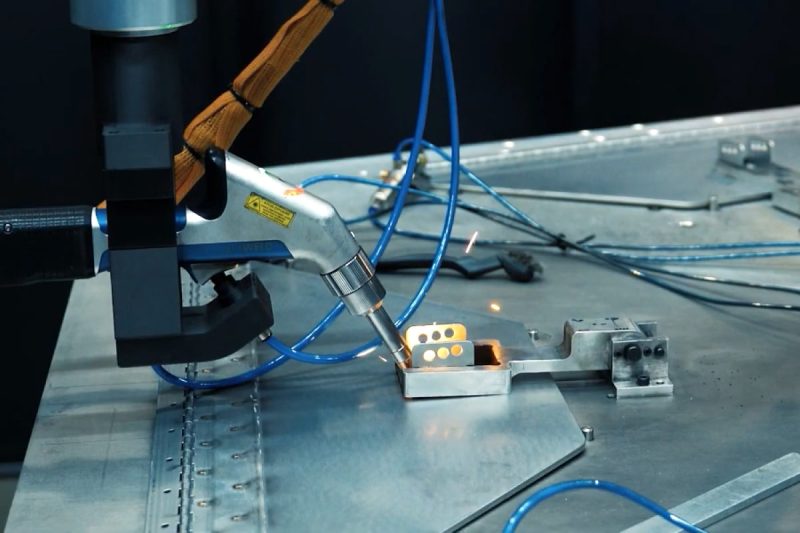
レーザー溶接ソリューションを入手
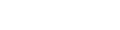
- [email protected]
- [email protected]
- +86-19963414011
- No. 3 ゾーン A、Lunzhen 工業地帯、玉城市、山東省。