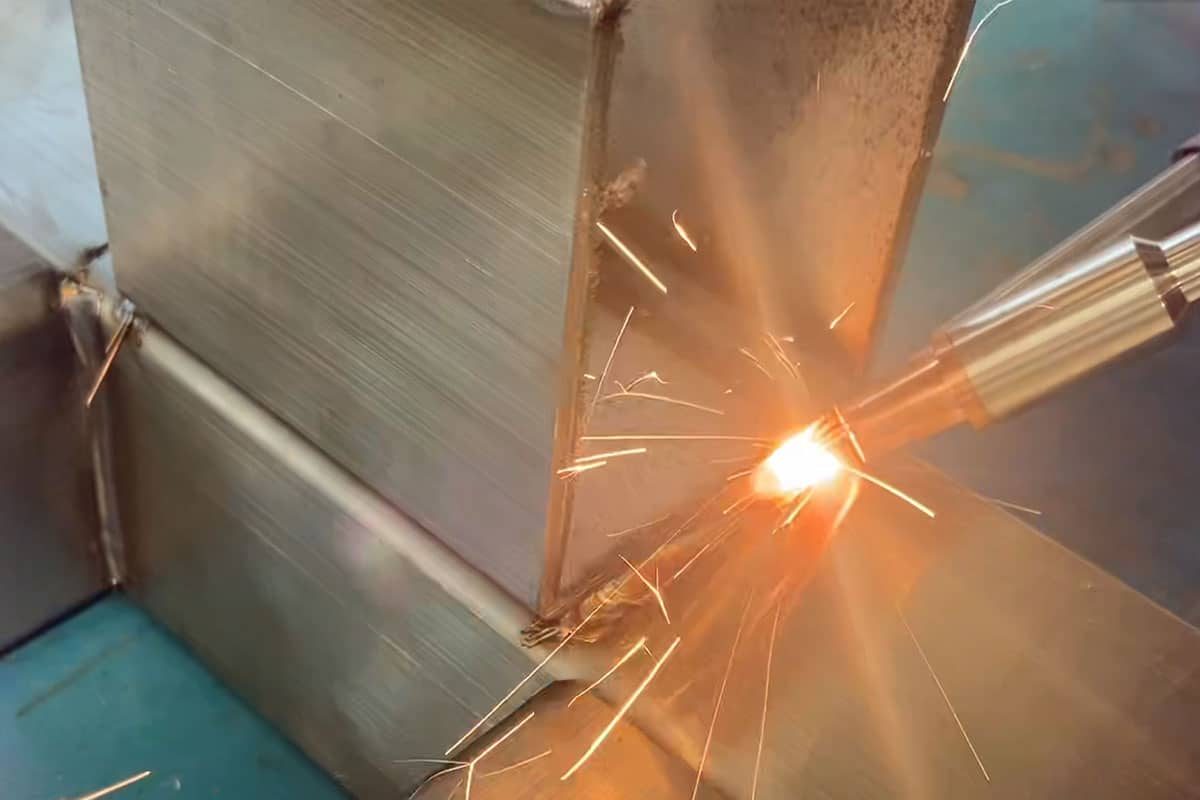
レーザー溶接とミグ溶接の包括的な分析
溶接はさまざまな業界の基本的なプロセスであり、さまざまな溶接技術の選択は、プロジェクトの品質、効率、費用対効果に大きな影響を与える可能性があります。レーザー溶接と MIG (金属不活性ガス) 溶接は、広く使用されている 2 つの著名な方法です。各方法にはそれぞれ独自の長所と短所があるため、溶接工や製造業者は 2 つの方法のどちらかを選択する前に、特定の要件を慎重に検討することが不可欠です。この記事では、ユーザーが特定のニーズに基づいて情報に基づいた意思決定を行えるように、レーザー溶接と MIG 溶接の包括的な分析を提供し、その相違点と類似点を比較します。
目次
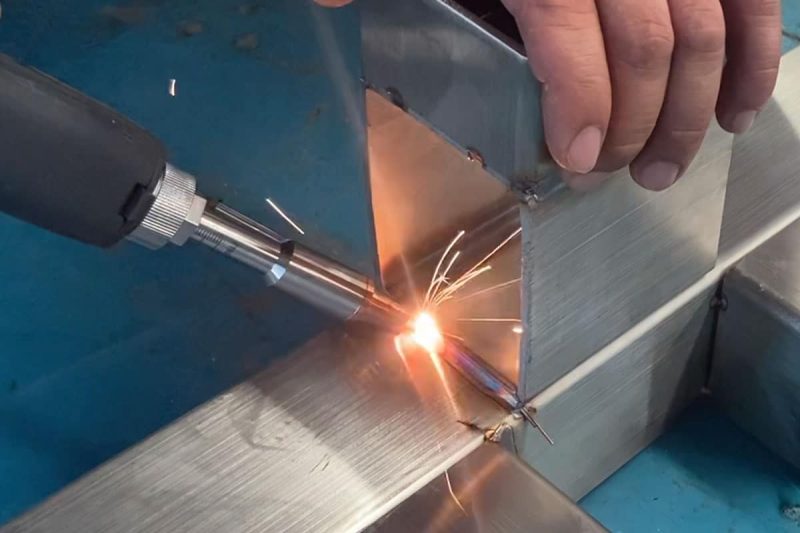
レーザー溶接とは何ですか?
レーザー溶接は、焦点を絞ったレーザー ビームを使用して 2 つ以上の材料を接合する溶接プロセスです。レーザー ビームは集中した熱源を提供し、さまざまな金属材料を正確かつ効率的に溶接できます。このプロセスでは、接触点で材料を溶かし、固化させて強力な結合を形成します。
レーザー溶接の動作原理
レーザー溶接は、高エネルギーのレーザービームを使用して金属材料を接合するプロセスです。汎用性が高く、高精度な溶接方法です。レーザー溶接の背後にある基本原理には、高度に集束したレーザー ビームを材料の表面に集中させ、局所的な溶融ゾーンを作成することが含まれます。この溶融領域で溶接が行われ、冷却すると強力な結合が形成されます。電気アークや火炎を使用する従来の溶接方法とは異なり、レーザー溶接はレーザーによって発生する高熱に依存します。
レーザー溶接はどのような材質に使用できますか?
レーザー溶接は、さまざまな業界のさまざまな材料に使用できる多用途の溶接プロセスです。レーザー溶接の適合性は、材料の特性と用途の特定の要件によって異なります。レーザー溶接で一般的に使用される材料をいくつか紹介します。
- 鋼: レーザー溶接は、炭素鋼やステンレス鋼を含むさまざまな種類の鋼の溶接に広く使用されています。
- アルミニウム:アルミニウムとその合金の接合にはレーザー溶接が効果的です。
- チタン: レーザー溶接は、チタン部品の溶接に航空宇宙産業や医療産業で使用されています。
- 銅と真鍮: レーザー溶接は、銅や真鍮などの非鉄金属に使用できます。
- ステンレス鋼合金: レーザー溶接は、ステンレス鋼製の医療機器の組み立てに一般的に使用されます。
- 貴金属: レーザー溶接は、金やプラチナなどの貴金属を溶接するために宝飾品業界で広く使用されています。
- さまざまな金属および合金: レーザー溶接は、自動車業界でさまざまな金属部品を接合するために使用されています。
レーザー溶接の強みの 1 つは、さまざまな材料との互換性です。異種材料を溶接できる機能は、特定の用途では特に価値があります。たとえば、自動車産業では、鋼とアルミニウムの部品を接合するためにレーザー溶接が使用されます。材料の適合性は、材料の融点、熱伝導率、その他の物理的特性によって決まります。レーザー溶接の成功は、材料の厚さ、組成、用途の特定の要件などの要因に依存することに注意することが重要です。さらに、材料や用途に応じて、伝導モード溶接やキーホールモード溶接など、さまざまなタイプのレーザー溶接技術が好ましい場合があります。
レーザー溶接にはどのような種類がありますか?
レーザー溶接方法にはいくつかの種類があり、それぞれに独自の利点と用途があります。レーザー溶接技術の選択は、材料の特性、厚さ、生産速度、望ましい溶接特性などの要因によって異なります。メーカーは多くの場合、特定の要件と接合される材料の特性に基づいて最適な方法を選択します。一般的なレーザー溶接のいくつかを次に示します。
- 伝導モード溶接: 伝導モード溶接では、レーザー エネルギーは主に材料の表面で吸収されます。このモードは薄い材料の溶接に適しており、溶け込み深さが浅いのが特徴です。熱影響部を最小限に抑える必要がある用途に一般的に使用されます。
- キーホール モード溶接: キーホール モード溶接では、レーザーを集中させて材料に深いキーホールを作成します。この技術は厚い材料の溶接に適しており、より深い溶け込みが得られます。キーホール溶接は、強力で深い溶接が必要な場合によく使用されます。
- パルス レーザー溶接: パルス レーザー溶接では、レーザー エネルギーをパルスで供給します。この方法は、入熱を制御し、熱歪みを最小限に抑え、薄い材料を溶接するのに適しています。パルスレーザー溶接は、溶接プロセスの正確な制御が不可欠な用途で一般的に使用されます。
- 連続波 (CW) レーザー溶接: 連続波レーザー溶接では、パルスなしで一定のレーザー ビームが使用されます。この方法は高速溶接用途によく使用され、特定の材料と厚さに対して良好な結果が得られます。
- レーザーマイクロ溶接: レーザーマイクロ溶接は、小さくて繊細な部品の溶接に使用される特殊な技術です。これは、精度と最小限の熱入力が重要であるエレクトロニクスや医療機器などの業界で一般的に適用されます。
- レーザーハイブリッド溶接: レーザーハイブリッド溶接は、レーザー溶接とガスメタルアーク溶接 (GMAW) やタングステン不活性ガス (TIG) 溶接などの別の溶接プロセスを組み合わせたものです。このアプローチは両方のプロセスの利点を活用しており、自動車業界や造船業界でよく使用されています。
- レーザー シーム溶接: レーザー シーム溶接は、重なった材料の長さに沿って連続的な溶接シームを作成するために使用されます。この技術は薄いシートを接合するのに適しており、自動車およびエレクトロニクス産業で一般的に適用されています。
- レーザー スポット溶接: レーザー スポット溶接では、レーザー エネルギーを小さなスポットに集中させ、局所的な溶接を作成します。この方法は、宝飾品の製造や電子部品の組み立てなどの用途での精密溶接によく使用されます。
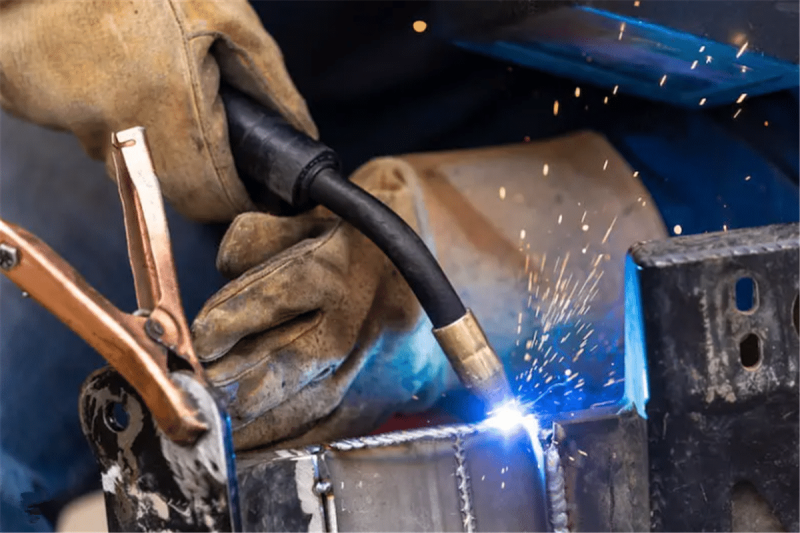
MIG溶接とは何ですか?
MIG 溶接 (金属不活性ガス溶接) は、連続した消耗品のワイヤ電極を使用して 2 つ以上の金属片を接合する一般的な溶接プロセスです。このプロセスはガスメタルアーク溶接 (GMAW) としても知られており、ワイヤ電極とワークピースの間に電気アークが形成され、溶接に必要な熱が発生するという事実を反映しています。 MIG溶接とレーザー溶接を比較する前に、まずこの溶接プロセスについて詳しく理解しましょう。
MIG溶接の動作原理
ワイヤ電極はスプールから溶接ガンを通して連続的に供給されます。ワイヤが前進すると、ワイヤとワークピースの間に電気アークが発生します。アークによって発生する熱によりワイヤとワークピースの両方が溶け、溶融池が形成されます。同時にシールドガスがノズルから放出され、欠陥の原因となる大気ガスから溶接部を保護します。
MIG溶接はどのような材質に使用できますか?
MIG (メタルイナートガス) 溶接は、ガスメタルアーク溶接 (GMAW) とも呼ばれ、さまざまな材料に使用できる多用途の溶接プロセスです。 MIG 溶接で最も一般的な材料は次のとおりです。
- 炭素鋼: MIG 溶接は炭素鋼の溶接によく使用されます。薄い部分にも厚い部分にも適用可能です。
- ステンレス鋼: MIG 溶接はステンレス鋼に適しており、耐食性が重要な産業で広く使用されています。
- アルミニウム: MIG 溶接はアルミニウムに使用できますが、スプール ガンやプッシュプル システムを使用して柔らかいアルミニウム ワイヤを絡ませることなく送るなど、特別な配慮が必要です。
- ニッケル合金: MIG 溶接は、航空宇宙や化学処理などの産業で一般的に使用されるニッケル合金の溶接に使用されます。
- 銅および銅合金: MIG 溶接は銅および銅合金の溶接に使用できますが、特別な技術と装置が必要な場合があります。
- その他の合金: MIG 溶接は、使用する特定の溶接ワイヤとシールド ガスに基づいて、さまざまな合金に適応できます。
最適な結果を得るには、材料が異なると特定の溶接ワイヤとシールドガスが必要になる場合があることに注意することが重要です。さらに、材料の厚さと種類に基づいて、溶接パラメータ (電圧、ワイヤ送給速度、移動速度など) を調整する必要がある場合があります。
MIG溶接にはどのような種類がありますか?
MIG 溶接には、さまざまな用途や材料に合わせてさまざまな技術とバリエーションが含まれています。 MIG 溶接技術の選択は、材料の厚さ、接合部の構成、溶接位置、および必要な溶接特性などの要因によって異なります。溶接工は多くの場合、溶接プロジェクトの特定の要件に基づいて適切なモードを選択します。一般的な MIG 溶接のいくつかを次に示します。
- 短絡移行: このモードでは、溶接ワイヤが溶接溜まりに触れ、短絡が発生します。これにより、アーク全体にわたる小さな液滴の制御された移動が実現します。短絡転写は、薄い材料の溶接に適しており、自動車や板金用途でよく使用されます。
- 球状転写: 球状転写では、溶融金属の大きな滴がアークを横切って移動し、より顕著なアークとスパッタを生成します。通常、より厚い材料の溶接に使用され、より高い電圧設定が必要になる場合があります。
- スプレー転写: スプレー転写では、小さな溶融液滴の安定した流れがスプレー パターンでアーク全体に転写されます。このモードは、より厚い材料をより高いアンペア数で溶接する場合に使用され、より良い溶け込みとより高い溶着速度を実現します。
- パルス MIG 溶接: パルス MIG 溶接は、スプレー転写と短絡転写の利点を組み合わせたものです。パルス電流を使用して入熱を制御し、熱の影響を受けるゾーン全体を減らします。パルス MIG は、薄い材料、位置外溶接、および正確な制御が必要な用途に適しています。
- 表面張力転写 (STT): 表面張力転写は、低電圧と高電流を利用する短絡転写の一種です。特に薄い材料を溶接する場合に、溶接プロセスをより適切に制御できるように設計されています。
- コールド メタル トランスファー (CMT): コールド メタル トランスファーは、入熱と歪みを最小限に抑える低熱伝達プロセスです。薄い材料の溶接によく使用され、精密な制御が重要な用途に適しています。
- 修正された短絡伝達: 修正された短絡伝達のバリエーションには、位置溶接や特定の材料の厚さなど、特定の用途のパフォーマンスを最適化するための溶接パラメータの調整が含まれます。
- 軸方向スプレー移動: 軸方向スプレー移動は、アークが軸方向に向けられるスプレー移動の一種で、結果として貫通力と制御が向上します。
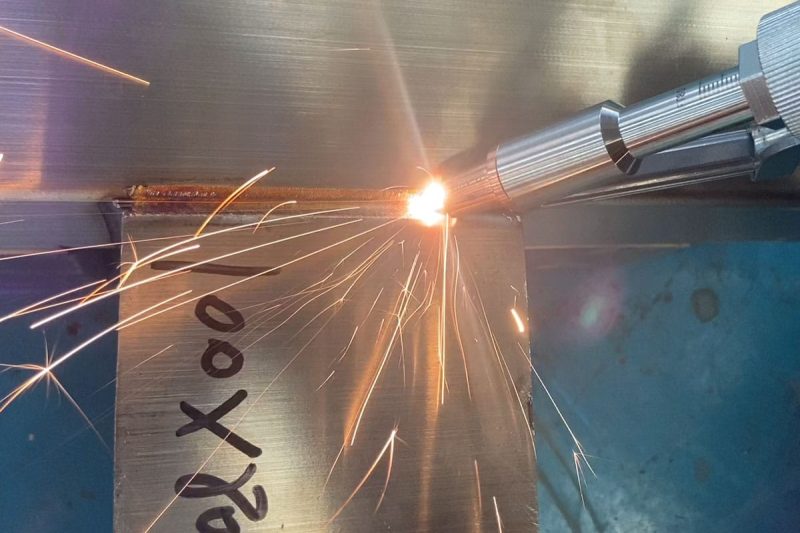
レーザー溶接 VS MIG 溶接
レーザー溶接と MIG (金属不活性ガス) 溶接は 2 つの異なる溶接プロセスであり、それぞれに独自の利点と用途があります。以下は、これら 2 つの溶接プロセスの比較分析であり、その性能、用途、利点、制限に関連するさまざまな要素をカバーしています。
溶接工程
- レーザー溶接: 熱源として高度に集束されたレーザービームを利用します。レーザービームは正確に制御され、溶接領域に照射されます。正確かつ集中的な熱を提供し、さまざまな材料の微細な溶接を可能にします。
- MIG 溶接: 消耗品のワイヤ電極とシールドガスを使用して、熱源として電気アークを生成します。浸透性が良く、厚手の材料に適しています。
精度と精度
- レーザー溶接: 高い精度と精度を実現し、繊細で複雑な溶接に適しています。熱影響部を最小限に抑え、溶接プロセスを正確に制御する必要がある用途に最適です。
- MIG 溶接: 一般に溶け込みは良好ですが、熱影響範囲が広くなる場合があります。厚い材料に適しており、構造用途や耐久性の高い用途に最適です。
溶接品質
- レーザー溶接: 通常、歪みが最小限に抑えられ、熱影響を受けるゾーンが狭い高品質の溶接が行われます。溶接の品質と美観が重要な用途に最適です。
- MIG 溶接: 強力で構造的に健全な溶接を行うことができますが、レーザー溶接に比べて熱の影響を受けるゾーンが大きくなり、特定の用途ではより大きな歪みが発生する可能性があります。高強度の溶接が不可欠な用途に適しています。
スピード能力
- レーザー溶接: レーザービームの集中した熱源により、特にシーム溶接やスポット溶接などの用途で、溶接速度の高速化が可能になります。溶接速度の高速化は、生産効率の向上に貢献する可能性があります。
- MIG 溶接: これは、特に速度が重要な用途では、比較的高速なプロセスとなる可能性があります。高い被覆率と迅速な溶接に適しています。
自動化能力
- レーザー溶接: 大量生産のための自動化システムに簡単に統合できます。自動化と精度が重要な産業用途に最適です。
- MIG 溶接: ある程度自動化できますが、レーザー溶接ほど簡単に自動化できない場合があります。手動プロセスと半自動プロセスの両方に多用途に使用できます。
機械コスト
- レーザー溶接機: 一般に初期コストは MIG 溶接機よりも高価であり、中小企業や個人の溶接業者にとっては障壁となる可能性があります。
- MIG溶接機:通常、 レーザー溶接システムより幅広いユーザーが利用できるようになります。
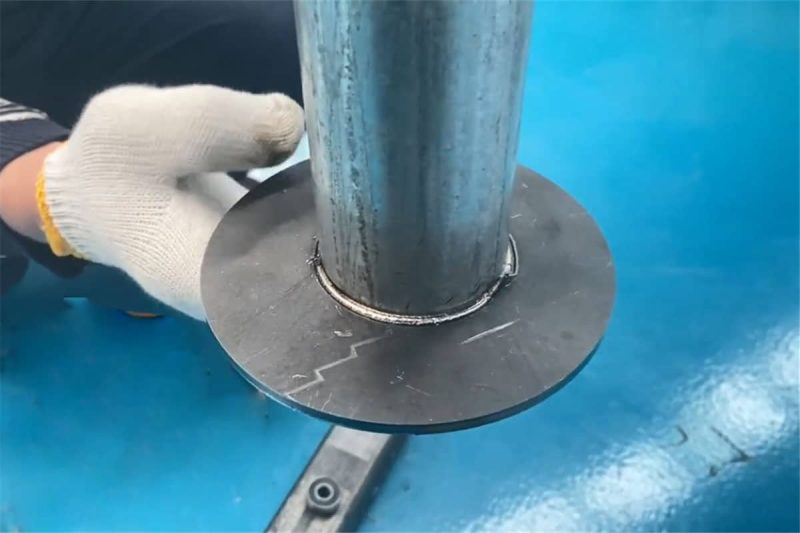
適切な溶接プロセスを選択する方法
レーザー溶接と MIG 溶接の技術的な違いを理解することで、必要な溶接プロセスを適切に選択することができます。適切な溶接プロセスを選択する際に考慮すべき要素は次のとおりです。
素材の種類と厚さ
- 薄い材料: レーザー溶接は薄い材料を高精度に溶接するのに優れているため、電子機器などの用途に最適です。
- 厚い材料: MIG 溶接は熱入力が高いため、建設業や重工業でよく見られる厚い材料に適しています。
コストに関する考慮事項
- 初期投資: レーザー溶接装置は初期コストが高くなる傾向があるため、MIG 溶接は特定の溶接ニーズに対してコスト効率の高いソリューションとなります。
- 運用コスト: 各溶接方法の長期的な運用コストを評価する際には、消耗品コスト、エネルギー効率、メンテナンスなどの要素を考慮する必要があります。
生産速度と効率
- 大量生産: レーザー溶接は溶接速度が速く、自動化機能を備えているため、効率が重要となる大量生産に適しています。
- カスタマイズとプロトタイピング: MIG 溶接は、汎用性とコスト効率に優れているため、速度よりも柔軟性が重視されるカスタマイズやプロトタイピングに適しています。
産業と用途
- 航空宇宙: レーザー溶接の精度と最小限の歪みにより、厳しい公差と高品質の溶接が重要となる航空宇宙用途に適しています。
- エレクトロニクス: 小さくて繊細な部品を溶接できるため、レーザー溶接はエレクトロニクス業界で好まれる選択肢となっています。
- 医療機器: レーザー溶接は、その精度と生体適合性材料を扱える能力により、医療機器の製造に広く使用されています。
- 自動車: MIG 溶接は、その多用途性と、さまざまな材料や厚さに対応できるため、自動車業界で一般的に使用されています。
- 建設: MIG 溶接は費用対効果と多用途性により、構造用鋼を含む建設プロジェクトに最適な方法となっています。
- 一般的な製造: MIG 溶接は、使いやすさと幅広い用途への適合性から、一般的な製造工場で広く採用されています。
要約する
まとめると、レーザー溶接と MIG 溶接にはそれぞれ長所があり、さまざまな用途に適しています。レーザー溶接は精度と速度に優れていますが、MIG 溶接は多用途性と厚い材料への適性で知られています。どちらを選択するかは、材料の種類と厚さ、精度、速度、予算の考慮事項など、溶接プロジェクトの特定のニーズによって異なります。溶接業者と製造業者はこれらの要素を慎重に評価して、情報に基づいた決定を下し、溶接用途で最適な結果を達成する必要があります。技術は進歩し続けるため、選択した方法が業界の進化するニーズに確実に適合するように、レーザー溶接と MIG 溶接の両方の最新の開発情報を常に最新の状態に保つことが重要です。
AccTek Laser では、ユーザーにレーザー溶接機と ロボットレーザー溶接装置。これらの最新の溶接プロセスは、企業が人件費を削減し、工場での溶接効率を向上させるのに役立ちます。オンラインで連絡するか、[email protected] に直接メールでニーズを伝えてください。当社の専門販売チームは、お客様の特定の溶接用途に基づいた完全なソリューションを提供し、詳細な価格情報を提供します。
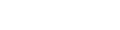
連絡先
- [email protected]
- [email protected]
- +86-19963414011
- No. 3 ゾーン A、Lunzhen 工業地帯、玉城市、山東省。
レーザー ソリューションを入手する