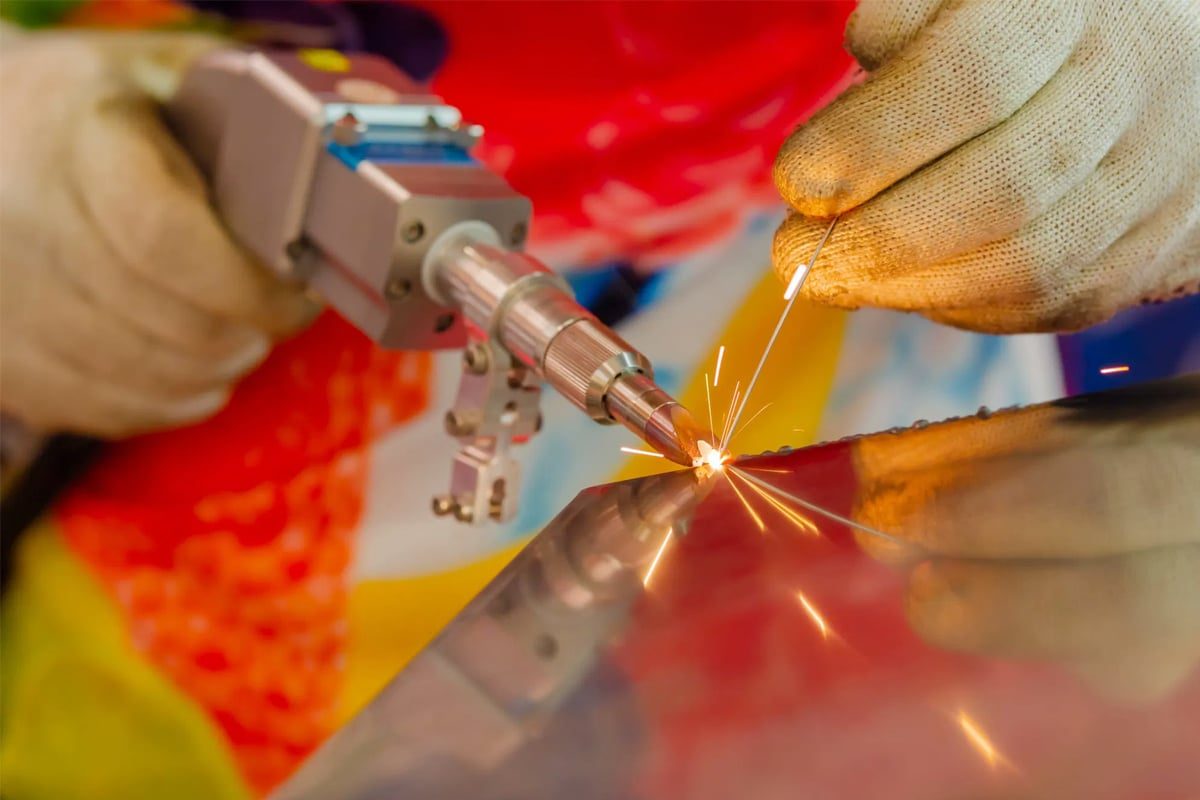
レーザー溶接の厚さに影響を与える要因は何ですか
レーザー溶接では、接合部の強度、耐久性、美観を確保するには、溶接部の厚さを制御することが不可欠です。レーザー溶接部の厚さは、出力、ビームの焦点、速度などのレーザー設定から、溶接される材料の物理的および化学的特性まで、さまざまな要因の影響を受けます。さらに、接合部の設計、シールドガスの選択、作業スペースの環境条件は、レーザーが材料に浸透する深さと全体的な溶接プロファイルを決定する上で重要な役割を果たします。これらの要因を最適化することで、メーカーは正確な溶接部の厚さを実現できます。これは、自動車、航空宇宙、電子機器など、精度と一貫性が極めて重要な業界では特に重要です。この記事では、レーザー溶接の溶接部の厚さに影響を与える多くの変数について説明し、プロセスパラメータと材料の調整が溶接部の深さと品質にどのように影響するかについての洞察を提供します。
目次
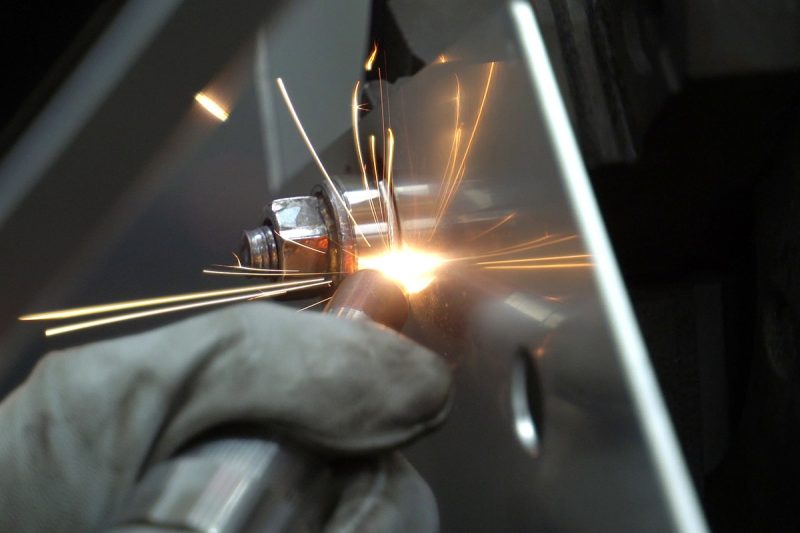
レーザー溶接を理解する
レーザー溶接は、主に金属などの材料を接合するための強力な熱源として、集中したレーザー ビームに依存します。通常、ファイバー、CO2、または固体レーザーなどのレーザー ソースによって生成されるレーザー ビームは、材料の表面に集中します。レーザーからの強力なエネルギーにより、ターゲット領域が急速に加熱されて溶解し、部品を融合する溶融池が形成されます。レーザーが接合部に沿って移動すると、溶融池が凝固し、連続溶接が行われます。
レーザーの高エネルギー密度により、熱影響部 (HAZ) を最小限に抑えながら正確で深い浸透が可能になり、従来の溶接方法と比較して熱変形が低減されます。レーザー溶接は、特定の用途や材料の要件に応じて、真空チャンバー、不活性ガス雰囲気、または大気中など、さまざまな環境で実行できます。この汎用性と精度により、レーザー溶接は複雑な形状やさまざまな熱特性を持つ材料に対して非常に効果的です。
レーザー溶接プロセスの基礎
レーザー溶接プロセスには通常、溶接前の準備、レーザーと材料の相互作用、溶接後の冷却と凝固という 3 つの主要な段階が含まれます。
- 溶接前の準備: 溶接前に、材料の表面は清潔で、汚染物質がなく、適切に整列している必要があります。油、酸化物、破片などの汚染物質は、エネルギー吸収を妨げ、溶接品質を低下させる可能性があります。
- レーザーと材料の相互作用: 溶接中、レーザー ビームはワークピースに集中され、そのエネルギーが表面に吸収されて局所的な溶融を引き起こします。レーザーと材料の相互作用には、主に 2 つのモードがあります。
- 伝導溶接: これはレーザー出力密度が比較的低い場合に発生し、蒸発せずに表面が溶融します。熱が材料に伝導され、浅く広い溶接になります。このモードは、美観と低熱入力を優先するアプリケーションでよく使用されます。
- キーホール溶接: レーザー出力密度が材料を蒸発させるほど高い場合、溶融池内にキーホールまたは蒸気空洞が形成されます。キーホールによりレーザーエネルギーが深く浸透し、高アスペクト比の狭く深い溶接部が形成されます。キーホール溶接は、厚い材料や強力な接合部を必要とする用途に適しています。
- 溶接後の冷却と凝固: レーザーが溶接ジョイントに沿って移動すると、溶融池が凝固し、材料間に連続的な結合が形成されます。適切な冷却速度により、亀裂や残留応力などの欠陥を防ぎ、溶接部の望ましい機械的特性を実現できます。
レーザー溶接は、高精度、最小限の歪み、そしてきれいで堅牢な接合部を生成する能力を備えています。しかし、望ましい溶接厚さと品質を達成するには、レーザー出力、ビーム焦点、溶接速度、材料特性などの要素を慎重に制御する必要があり、レーザー溶接は現代の製造業にとって複雑で適応性の高いプロセスとなっています。
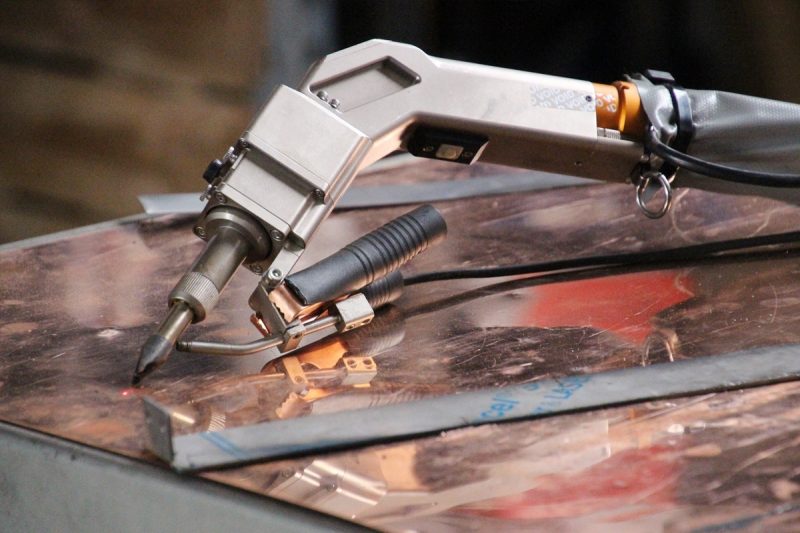
レーザー溶接の用途
レーザー溶接は、その精度、スピード、そして熱変形を最小限に抑えた高品質で一貫した溶接を実現する能力により、多くの業界で基礎技術となっています。製造業の需要が進化するにつれ、レーザー溶接の汎用性と適応性は、今後も非常に貴重なツールとなり続けます。
- 自動車産業: 自動車分野では、レーザー溶接は車体、エンジン部品、トランスミッションギア、排気システム、電気自動車のバッテリーモジュールの組み立てに広く使用されています。このプロセスにより、部品の重量を最小限に抑えながら、強力で高精度の接合が可能になります。レーザー溶接はアルミニウムとスチールなどの異種材料を接合できるため、軽量でエネルギー効率の高い車両設計に特に役立ちます。
- 航空宇宙産業: レーザー溶接は、タービンブレード、構造フレーム、燃料タンクなどの重要な部品に正確で高強度の接合部を作成できるため、航空宇宙産業では不可欠です。熱影響部が最小限であるため、チタン合金や複合材などの軽量で熱に弱い航空宇宙材料の構造的完全性を維持するのに役立ちます。レーザー溶接の精度により、厳格な安全性とパフォーマンスの基準に準拠できます。
- エネルギーと発電: エネルギー分野では、レーザー溶接は風力タービン、ソーラーパネル、石油・ガス設備、原子力発電所の部品の製造に使用されています。強力で欠陥のない溶接を行うことができるため、高圧・高温環境でも信頼性と安全性が確保されます。レーザー溶接は、熱交換器、パイプ、高圧容器の製造にも使用されます。
- 造船および海洋産業: 造船業界は、レーザー溶接の強力で耐腐食性のある溶接部のメリットを享受しています。レーザー溶接は、構造用鋼板、船体部品、内装部品の接合に使用されます。このプロセスにより、船舶の総重量が軽減され、燃料効率が向上し、複雑な設計を高精度でサポートできます。
- 消費者向け電子機器および電化製品: レーザー溶接は、スマートフォン、タブレット、家電製品などの消費者向け電子機器の組み立てに使用されています。レーザー溶接により、金属ケース、コネクタ、バッテリー パックの接合部が信頼性が高く、見た目も美しくなります。このプロセスは自動化された高速生産ラインをサポートし、生産性と一貫性を高めます。
- 食品および飲料業界: 食品および飲料業界では、パイプ、醸造設備、充填機などのステンレス鋼機器の製造にレーザー溶接が使用されています。レーザー溶接によって衛生的でシームレスな溶接が行われるため、細菌の増殖を防ぎ、洗浄プロセスを簡素化できるため、食品グレードの用途に最適です。
- 建設と建築: レーザー溶接は、建設と建築の分野で、強固で美しい金属構造物を作成するために使用されています。構造梁、装飾要素、ファサードなどの製造に使用されます。このプロセスの精度と速度により、カスタム デザインや複雑な形状を作成できます。
- 農業および重機: 農業業界では、鋤、トラクター、ローダーなどの機械や装置の堅牢な部品を製造するためにレーザー溶接が利用されています。レーザー溶接された接合部は、厳しい動作条件に耐える高い強度と耐久性を備えています。
レーザー溶接はさまざまな業界で多様に利用されており、現代の製造業やエンジニアリングにとって重要なツールとしての役割を担っています。溶接部の厚さと品質を正確に制御できるため、レーザー溶接は高性能製品、複雑なアセンブリ、厳格な規制基準の厳しい要求を満たすことができます。
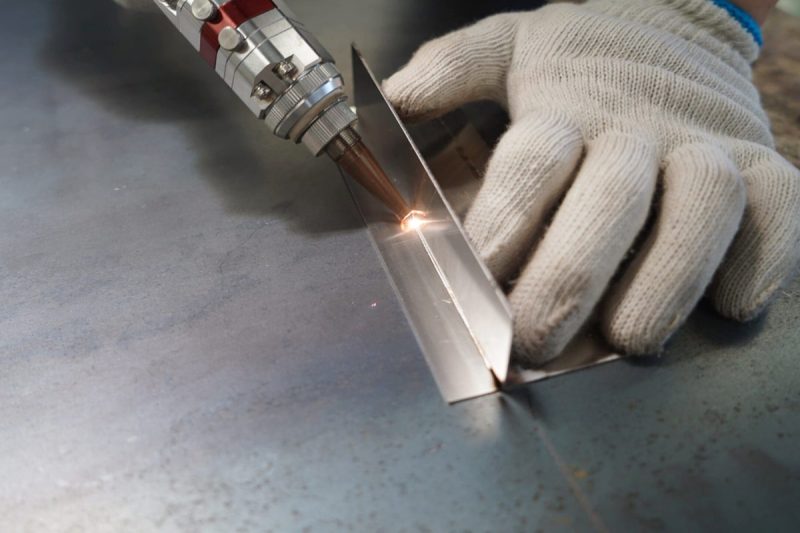
レーザー溶接の厚さに影響を与える要因
レーザー溶接で希望の厚さを実現することは、数多くの要因の影響を受ける複雑なプロセスです。これらの要因はそれぞれ、溶接の浸透深さ、品質、完全性に直接影響します。これらの変数を理解することで、メーカーは最適な厚さ、強度、精度が得られるようにレーザー溶接プロセスをカスタマイズできます。
レーザーパワー
- 溶接厚さへの影響: レーザー出力は、溶接厚さを決定する最も重要な要素の 1 つです。レーザー出力が高いほどエネルギー入力が増加し、より深い浸透とより厚い溶接が可能になります。逆に、出力レベルが低いと溶接は浅くなり、薄い材料や最小限の熱入力が必要な用途に適している場合があります。
- 最適化: 材料の厚さと必要な浸透深さに応じてレーザー出力を調整することで、エネルギーを効果的に利用することができます。厚い材料や深い溶接の場合、過度の熱影響部 (HAZ) を生じさせることなく必要な浸透を達成するために十分な出力を適用する必要があります。
溶接速度
- 溶接厚さへの影響: 溶接速度、つまりレーザーが接合部に沿って移動する速度は、溶接厚さに大きく影響します。溶接速度が遅いほど、より多くのレーザーエネルギーが材料に吸収され、溶接が厚く深くなります。逆に、速度が速いと熱入力が減り、溶接が浅くなります。
- 最適化: 希望の厚さを達成するには、溶接速度とレーザー出力のバランスをとることが不可欠です。速度が遅すぎると過熱や欠陥が発生する可能性があり、速度が速いと不完全な融合や浸透不足が発生する可能性があります。
焦点位置
- 溶接厚さへの影響: レーザー ビームの焦点位置は、エネルギーがワークピースのどこに集中するかに影響します。ビームを材料の表面上またはわずかに下に正確に焦点を合わせると、溶け込み深さが増し、より厚い溶接が可能になります。焦点の位置がずれると、溶け込みが不均一になったり不十分になったりする可能性があります。
- 最適化: 材料の厚さと溶接モード (伝導またはキーホール) に応じて焦点を調整することで、製造業者はより制御された溶接厚さを実現できます。正確な焦点合わせにより、エネルギーの集中が改善され、一貫した深さが確保されます。
ビーム品質とモード
- 溶接厚さへの影響: ビーム品質とモード (TEM00、TEM01 など) は、作業領域全体にレーザー エネルギーがどのように分散されるかに影響します。高品質のシングル モード ビーム (TEM00) は、より集中した強力なスポットを提供し、より深い浸透とより厚い溶接を可能にします。一方、マルチ モード ビームは、エネルギーの拡散により、より広く浅い溶接につながる可能性があります。
- 最適化: 適切なビーム品質とモードのレーザーを選択すると、溶接厚さの制御が向上します。深く狭い溶接が必要な用途には、高品質のシングルモード レーザーが最適です。
材料特性
- 溶接厚さへの影響: 熱伝導率、融点、反射率などの特性に基づいて、材料ごとにレーザー エネルギーに対する反応が異なります。たとえば、アルミニウムや銅などの熱伝導率の高い金属は熱を急速に放散するため、必要な浸透を達成するにはより高いレーザー出力が必要になります。反射率の高い材料はエネルギー吸収も低下し、厚さに影響を与える可能性があります。
- 最適化: 特定の材料特性を理解することは、目標の厚さを達成するためにレーザーパラメータを調整するのに役立ちます。たとえば、反射性材料は、吸収を向上させる表面処理の恩恵を受けるか、効果的な浸透のためにより高い出力を必要とする場合があります。
予熱
- 溶接厚さへの影響: 溶接前に材料を予熱すると、熱勾配が低減され、よりスムーズな溶け込みとより厚い溶接が可能になります。また、高炭素鋼などの熱応力を受けやすい材料の割れのリスクも最小限に抑えられます。
- 最適化: 予熱は、特に急速な冷却によって欠陥が発生する可能性がある厚い部分で、一定の厚さを実現するのに役立ちます。過度の熱入力を防ぐために、予熱の程度を制御する必要があります。
表面状態
- 溶接厚さへの影響: 清潔さや酸化などの材料の表面状態は、エネルギーの吸収と浸透に影響します。油、酸化物、汚れなどの汚染物質はレーザーエネルギーの吸収を低下させ、厚さの不均一や溶接の弱化につながる可能性があります。
- 最適化: 溶接前に表面を洗浄して準備することで、レーザー エネルギーが効果的に吸収され、厚さが制御されます。研磨やサンドブラストなどの表面処理によっても、溶接品質が向上します。
シールドガスと補助ガス
- 溶接厚さへの影響: シールド ガス (アルゴン、ヘリウム、窒素など) は、大気汚染から溶接プールを保護し、溶接の溶け込みと厚さに影響を与える可能性があります。ガスの種類によって熱特性が異なり、熱入力と溶接特性に影響します。切断によく使用される補助ガスも、安定した溶接プールを維持する役割を果たします。
- 最適化: 適切なシールド ガスを選択すると、溶接の溶け込みが向上します。たとえば、熱伝導率の高いヘリウムは溶け込みを増やし、溶接の厚さに影響を及ぼします。ガスの流量を調整することで、乱流や欠陥を生じさせることなく、十分なシールドを確保できます。
溶接モード(伝導溶接とキーホール溶接)
- 溶接厚さへの影響: レーザー溶接は伝導モードまたはキーホール モードで実行できますが、それぞれが達成可能な溶接厚さに影響します。伝導溶接では、表面レベルの用途に適した広くて浅い溶接が生成されますが、キーホール溶接では、厚い材料に最適な深くて狭い溶接が生成されます。
- 最適化: 適切な溶接モードを選択すると、厚さを正確に制御できます。伝導モードは、美しい表面溶接が必要な場合に使用され、キーホール モードは、より深い浸透深度が求められる用途に最適です。
ジョイント構成
- 溶接厚さへの影響: 突合せ、重ね、T ジョイントなどのジョイントの構成は、レーザー エネルギーが材料とどのように相互作用するかに影響し、達成可能な厚さを決定します。たとえば、突合せジョイントでは完全な溶け込み溶接が可能ですが、重ねジョイントでは同等の深さを得るためにより多くのレーザー出力が必要になる場合があります。
- 最適化: 材料の厚さとアプリケーション要件に基づいて適切なジョイント構成を選択すると、効果的なエネルギー分散と溶接厚さが保証されます。
レーザー波長
- 溶接厚さへの影響: レーザーの波長は、材料がエネルギーを吸収する効率に影響します。たとえば、ファイバー レーザーなどの短い波長は、CO2 レーザーの長い波長よりも金属によく吸収され、溶け込み深さと溶接厚さに影響します。
- 最適化: 材料の吸収特性に一致する波長のレーザーを選択すると、効率的なエネルギー使用が保証され、最適な溶接厚さが可能になります。
溶接前後の処理
- 溶接前処理: 溶接前の表面処理、洗浄、位置合わせにより、レーザーのエネルギー吸収が改善され、厚さが一定になります。汚染物質や位置ずれがあると、欠陥や浸透の不均一が生じる可能性があります。
- 溶接後処理: 熱処理や制御された冷却などの溶接後処理は、溶接構造と安定性に影響します。制御された冷却速度は、残留応力や反りを防ぎ、均一な厚さを維持するのに役立ちます。
- 最適化: 適切な溶接前および溶接後の処理により溶接品質が向上し、一貫した溶接厚さと機械的特性が実現します。
これらの各要素は、レーザー溶接の厚さと品質を決定する上で重要な役割を果たします。各変数を慎重に調整して最適化することで、メーカーは希望する溶接厚さを実現し、レーザー溶接がさまざまな産業用途の厳しい要件を満たすことを保証できます。
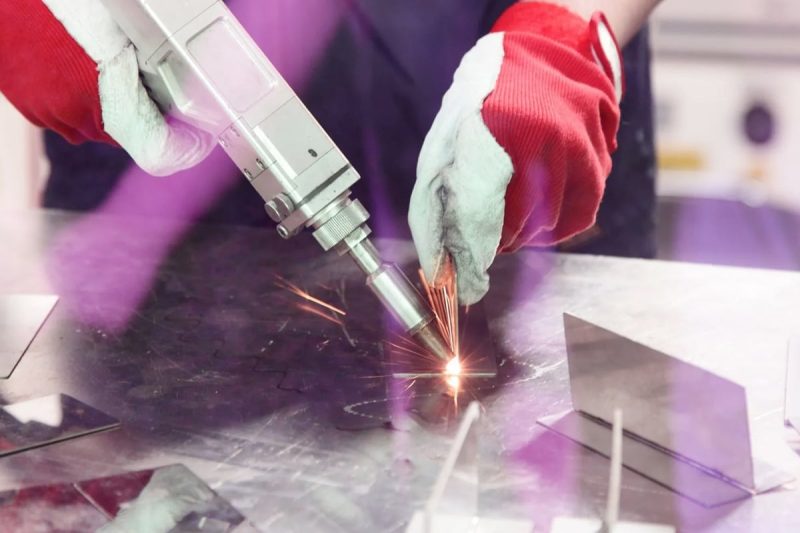
溶接厚さの最適化
レーザー溶接の厚さを最適化するには、複数のプロセス パラメータを慎重にバランスさせ、正確な制御のための戦略を採用する必要があります。目的の溶接厚さを実現することは、溶接強度を確保し、欠陥を最小限に抑え、設計仕様を満たすために不可欠です。
プロセスパラメータの調整
レーザー出力調整
- 影響: レーザー出力は、溶け込みの深さと溶接の厚さに直接影響します。出力を上げると、溶接プールに供給されるエネルギーが増加し、より深く厚い溶接が可能になります。一方、出力を下げると、溶け込みは浅くなります。
- 最適化戦略: 最適な溶接厚さを実現するには、材料特性、接合部の構成、厚さの要件に基づいてレーザー出力を慎重に調整する必要があります。出力が高すぎると、多孔性や過剰な溶融などの欠陥が発生する可能性があるため、浸透を最大化しながら望ましくない影響を最小限に抑えるバランスを見つけることが重要です。
溶接速度制御
- 影響: 溶接速度によって、レーザーが材料と相互作用する時間の長さが決まります。速度が遅いとエネルギー吸収量が増加し、溶接部はより深く厚くなります。一方、速度が速いと熱入力が減り、溶接部はより薄くなります。
- 最適化戦略: レーザー出力と連動して溶接速度を調整することで、厚さを一定に保つことができます。材料が厚い場合や、浸透が深い場合は速度を遅くすることができますが、過熱や過度の熱影響部を防ぐために速度を制御する必要があります。
焦点位置調整
- 影響: 材料表面に対するレーザー焦点の位置は、エネルギーの集中に影響します。表面上または表面よりわずかに下に焦点を合わせたビームは、浸透を最大化し、溶接の厚さを増やしますが、焦点の位置が誤っていると、結果に一貫性がなくなる可能性があります。
- 最適化戦略: 焦点を正確に調整することで、ワークピースへの一貫したエネルギー供給が保証され、溶接の厚さが増します。望ましい結果を得るには、異なる材料やジョイント構成に応じて焦点位置の調整が必要になる場合があります。
ビーム品質とモードの最適化
- 影響: 安定したモード構造を持つ高品質のレーザー ビームにより、エネルギー集中が向上し、より深く制御された溶接が可能になります。
- 最適化戦略: 高品質のビームを使用し、適切なビーム モードを選択することで、正確で一貫した溶接厚さを実現できます。定期的な機器メンテナンスによって安定したレーザー出力とビーム品質を維持することが重要です。
シールドとアシストガスフロー
- 影響: シールド ガスの種類と流量は、溶接プールの安定性と浸透に影響します。適切なシールドは汚染を防ぎ、エネルギー吸収を高めることができ、アシスト ガスは安定した溶接環境を維持するのに役立ちます。
- 最適化戦略: 適切なシールド ガス (アルゴン、ヘリウム、窒素など) を選択し、流量を調整して、最適な溶接溶け込みと厚さを確保します。シールド ガスの効果を最大化するには、材料と溶接条件に合わせてシールド ガスを調整する必要があります。
予熱および冷却速度
- 影響: 材料を予熱すると、熱勾配が減少し、エネルギーの吸収と浸透が改善されます。冷却速度は凝固プロセスと溶接構造に影響します。
- 最適化戦略: 制御された予熱と溶接後の冷却を実施することで、均一な厚さが確保され、ひび割れや反りなどの欠陥のリスクが最小限に抑えられます。
制御戦略
プロセスマッピングとシミュレーション
レーザーパラメータ(出力、速度、焦点位置など)と溶接厚さを相関させるプロセスマップを作成すると、さまざまな材料や接合部構成に最適な設定を特定するのに役立ちます。溶接シミュレーションソフトウェアは、パラメータの変更が溶接厚さに与える影響を予測するのにも役立ち、コストのかかる試行錯誤の必要性を減らします。
リアルタイム監視およびフィードバックシステム
レーザー溶接中にセンサーと監視システムを実装すると、溶接の溶け込み、厚さ、品質に関するリアルタイムのデータが得られます。自動フィードバック システムは、溶接環境の変化に応じてパラメータを調整し、一貫した溶接厚さを確保します。
適応制御システム
高度なレーザー溶接システムは、リアルタイムのフィードバックに基づいて、レーザー出力、速度、およびその他のパラメータを自動的に調整できます。この機能により、変動が最小限に抑えられ、複雑な形状やさまざまな材料条件にわたって均一な溶接厚さが確保されます。
表面処理と材料調整
洗浄や調整などの適切な表面処理により、エネルギー吸収と溶接の一貫性が向上します。研磨、サンドブラスト、表面コーティングなどの方法により、レーザー エネルギーの相互作用が改善され、より一貫した厚さが得られます。
ジョイント設計とフィットアップの最適化
隙間を最小限に抑え、コンポーネントの正確な位置合わせを確実にすることで、エネルギー伝達と溶接厚さの一貫性が向上します。適切なクランプと固定技術を使用すると、溶接中に最適な接合状態を維持できます。
プロセスの検証とテスト
レーザー溶接プロセスの定期的なテストと検証を行うことで、特定のアプリケーションに最適なパラメータ設定を特定できます。継続的なプロセス改善により、溶接厚さが望ましい許容範囲内に保たれます。
主要なプロセス パラメータを調整し、効果的な制御戦略を実装することで、メーカーは最適な溶接厚さを実現し、接合部の品質を向上させ、レーザー溶接操作の全体的な効率を高めることができます。これらの実践により、レーザー溶接は、さまざまな産業用途において信頼性が高く、多用途なソリューションであり続けることが保証されます。
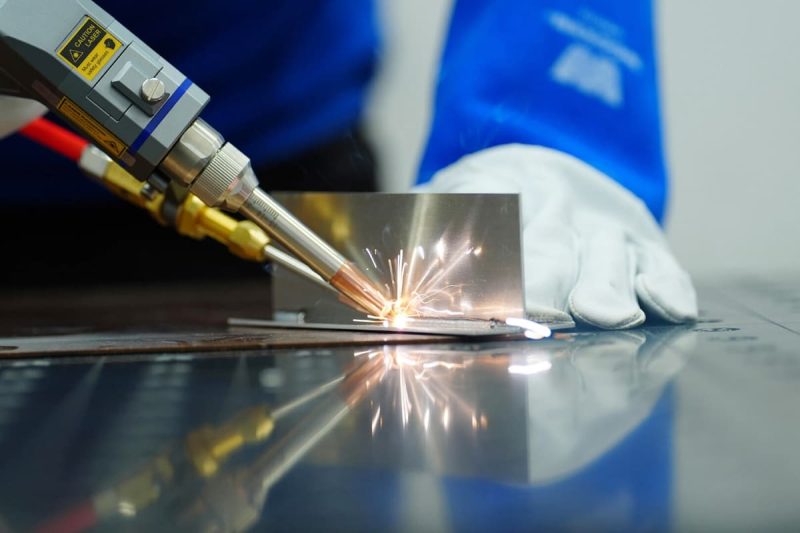
課題と考慮事項
レーザー溶接の厚さを最適化することは、課題がないわけではありません。さまざまな要因が溶接の一貫性、品質、パフォーマンスに影響を与える可能性があります。一般的な問題を理解し、堅牢な品質管理対策を実施することで、メーカーはプロセスを改善し、信頼性の高い溶接を確保できます。
よくある問題
浸透深さの不一致
- 課題: レーザー出力、ビーム焦点、材料の厚さ、または接合部の位置合わせのばらつきにより、溶け込み深さが一定でなくなり、溶接部の厚さに影響する可能性があります。このばらつきにより、接合部の弱化、融合不足、または構造上の欠陥が生じ、溶接の完全性が損なわれる可能性があります。
- 考慮事項: レーザー光源の定期的な校正、ビーム焦点の監視、および溶接パラメータの正確な制御は、一貫した溶け込みと溶接厚さを実現するために不可欠です。
熱影響部(HAZ)
- 課題: 過剰な熱入力により、大きな熱影響部が形成され、材料の微細構造が変化し、溶接部付近の機械的特性が低下する可能性があります。これにより、特に熱応力に敏感な材料では、反り、残留応力、または亀裂が発生する可能性があります。
- 考慮事項: レーザー出力と溶接速度を最適化し、適切なシールドガスを使用することで、熱影響部を最小限に抑え、一貫した溶接厚さを維持できます。
多孔性とガス閉じ込め
- 課題: 溶接プール内に閉じ込められたガスは多孔性を引き起こし、溶接部の機械的強度を低下させ、溶接部の厚さにばらつきを生じさせる可能性があります。多孔性は、汚染物質、不十分なシールド ガス、または不適切なプロセス設定によって発生する可能性があります。
- 考慮事項: 溶接前に表面を洗浄し、シールドガスの流れを最適化し、汚染物質を減らすことで、多孔性を最小限に抑えることができます。リアルタイムの監視により、プロセスの早い段階で多孔性の問題を検出し、対処することができます。
材料の反射率
- 課題: アルミニウムや銅などの反射率の高い材料は、レーザー エネルギーの大部分を反射するため、十分な浸透と一定の厚さを実現することが困難になります。これらの材料では、エネルギー吸収を高めるために特別な考慮が必要になる場合があります。
- 考慮事項: コーティングやテクスチャリングなどの表面処理や、より短い波長のレーザーの使用により、反射材料のエネルギー吸収と一貫性を向上させることができます。
関節のずれと隙間
- 課題: 接合部の位置がずれていたり、コンポーネント間の隙間があると、レーザーの均一な浸透能力が低下します。これにより、アンダーカット、不完全な融合、溶接厚さのばらつきが生じる可能性があります。
- 考慮事項: 適切な固定、位置合わせ、およびフィットアップ制御により、一貫したジョイント状態が確保され、欠陥の可能性が低減します。
熱変形と応力
- 課題: 不均一な熱分布と急速な冷却により、熱変形、残留応力、反りが発生し、溶接部の厚さと接合部の完全性に影響を及ぼす可能性があります。
- 考慮事項: 予熱、冷却制御、および最適化された溶接速度は、熱応力を軽減し、一貫した溶接寸法を維持するのに役立ちます。
品質管理措置
リアルタイムプロセス監視
- 測定: リアルタイム監視システムを実装すると、レーザー出力、溶接速度、溶け込み深さなどの主要なパラメータに関するフィードバックが得られます。これにより、即時の調整が可能になり、溶接厚さのばらつきが減り、全体的な一貫性が向上します。
- 考慮事項: プロセスの安定性を維持するために使用できるツールの例としては、光学センサー、温度モニター、レーザー フィードバック システムなどがあります。
溶接前の表面処理
- 対策: ワークピースの表面が清潔で、汚染物質がなく、適切に準備されていることを確認することは、一貫したエネルギー吸収と溶接品質を実現するために重要です。
- 考慮事項: 研磨、脱脂、コーティングの適用などの表面処理は、エネルギー伝達を妨げる可能性のある汚染物質を最小限に抑えるのに役立ちます。
機器の校正とメンテナンス
- 測定: レーザー ソース、光学系、およびその他のシステム コンポーネントを定期的に校正およびメンテナンスすることで、安定したビーム品質、出力、精度が確保されます。
- 考慮事項: 定期的なチェックにより、溶接の厚さや全体的な品質に影響を及ぼす可能性のあるパフォーマンスの低下を防ぐことができます。
非破壊検査(NDT)
- 測定: 超音波検査、放射線検査、目視検査などの技術は、部品を損傷することなく溶接品質を評価するのに役立ちます。非破壊検査法は、多孔性、亀裂、不完全な融合などの問題を検出します。
- 考慮事項: NDT 手順を実装すると、溶接の一貫性と仕様への準拠を検証するのに役立ち、製品障害の可能性が低減します。
シールドガスとアシストガスの使用
- 対策: シールドガスの適切な選択と流量制御により、溶接プールを大気汚染から保護し、溶接の溶け込みに影響を与えます。
- 考慮事項: シールドガスの種類と流量を調整することで、酸化、多孔性、溶接厚さの不均一性を最小限に抑えることができます。
溶接プロセスの最適化
- 測定: レーザーパラメータ (出力、速度、焦点位置など) と溶接厚さを相関させるプロセスマップを作成することで、さまざまな材料や接合部構成に最適な設定が保証されます。
- 考慮事項: テストとシミュレーションに基づく継続的なプロセス改善により、溶接厚さの制御が強化され、変動性が低減されます。
トレーニングと熟練オペレーター
- 対策: レーザー溶接のパラメータ、材料、および技術を深く理解している熟練したオペレーターは、溶接の一貫性と品質の維持に大きく貢献します。
- 考慮事項: 継続的なトレーニングとスキル開発により、オペレーターは問題を迅速に特定して解決できるようになり、プロセス制御が向上します。
一般的な課題に対処し、堅牢な品質管理対策を実施することで、製造業者はレーザー溶接プロセスを最適化し、一貫した溶接厚さ、高い構造的完全性、優れた品質を実現できます。

まとめ
レーザー溶接の厚さは、溶接ジョイントの強度、精度、および全体的な性能に影響を与える重要な要素です。最適な厚さを実現するには、レーザー出力、溶接速度、ビーム品質、焦点位置、材料特性、シールドガスなど、さまざまな要素を深く理解する必要があります。これらのパラメータを調整することで、正確なエネルギー入力と一貫した溶け込みが保証され、高品質で欠陥のない溶接が実現します。溶接前後の処理、ジョイントの構成、表面状態も、溶接の結果に影響を与えます。一貫性のない溶け込み、多孔性、熱変形などの一般的な課題に対処することで、メーカーは溶接の厚さを最適化し、全体的なプロセスの信頼性を高めることができます。リアルタイムの監視、適切な機器のキャリブレーション、オペレーターのトレーニングなどの堅牢な品質管理対策を実施することで、一貫性のある信頼性の高い結果が保証されます。これらの洞察により、レーザー溶接は、精度、強度、および高い生産性を要求する業界にとって不可欠なソリューションであり続けています。
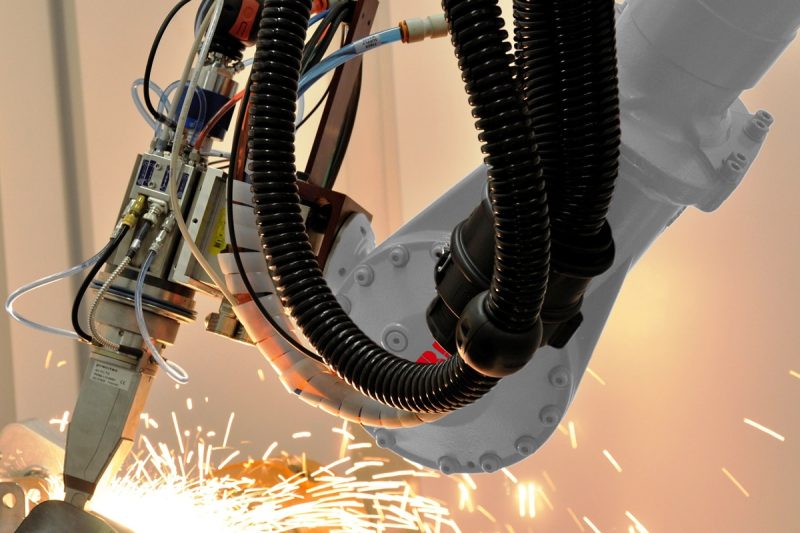
レーザー溶接ソリューションを入手
レーザー溶接の厚さを最適化することは、さまざまな用途で正確で強力かつ信頼性の高い溶接を実現するために不可欠です。AccTek Laserでは、お客様の業界特有の要求を満たすようにカスタマイズされた高度なレーザー溶接ソリューションを提供しています。当社の最先端のレーザー溶接システムは、レーザー出力、ビームフォーカス、溶接速度などの重要なパラメータを優れた方法で制御し、一貫した浸透と高品質の結果を保証します。当社の専門家チームは、お客様が適切なものを選択するのをお手伝いします。 レーザー溶接機 材料の種類、ジョイント構成、特定のアプリケーションのニーズに基づいて設計します。
薄くて繊細な部品や厚い構造部品を溶接する必要がある場合でも、AccTek Laser のソリューションは優れた精度、最小限の熱影響部、比類のない効率を実現します。販売前のコンサルティング、システム統合、トレーニング、メンテナンスなどの包括的なサポートにより、溶接プロセスを最適化し、比類のないパフォーマンスを実現できます。 お問い合わせ 生産要件に最適なレーザー溶接ソリューションを今すぐ見つけてください。
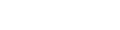
連絡先
- [email protected]
- [email protected]
- +86-19963414011
- No. 3 ゾーン A、Lunzhen 工業地帯、玉城市、山東省。
レーザー ソリューションを入手する