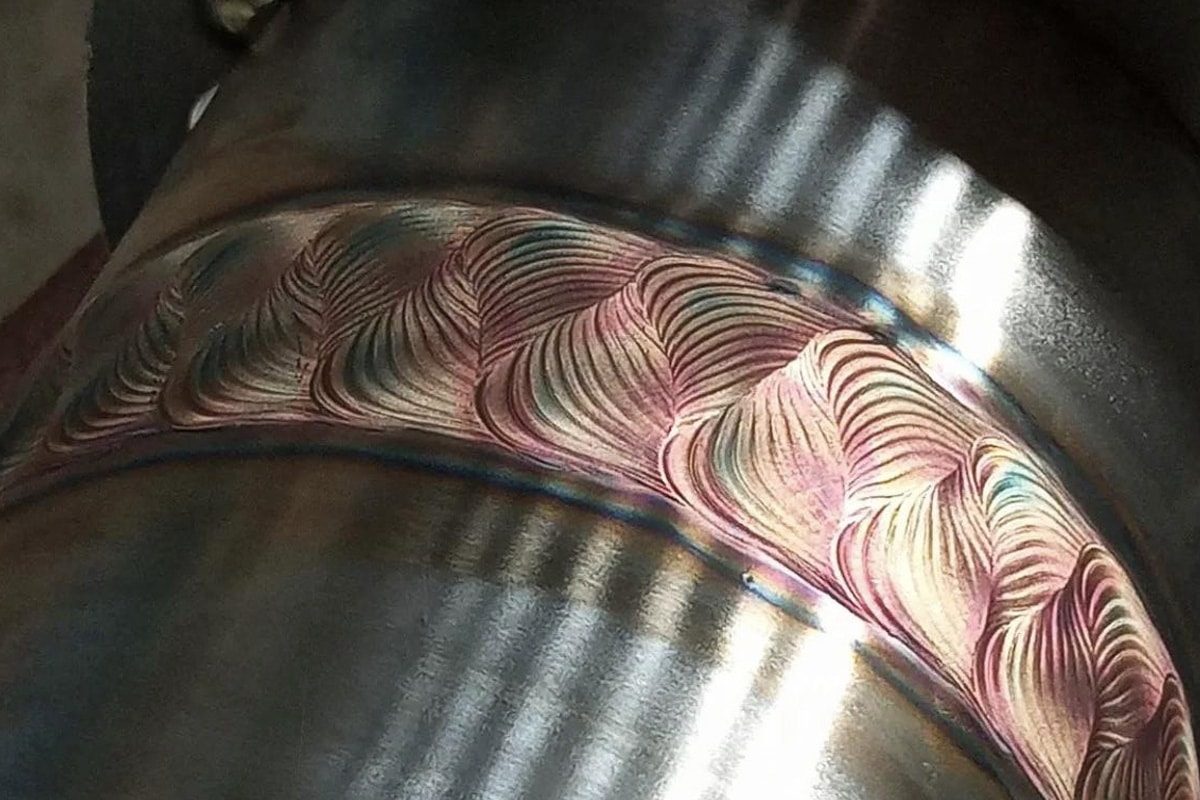
レーザー溶接の歪みと反りを最小限に抑えるにはどうすればよいでしょうか?
レーザー溶接は現代の製造業に革命をもたらし、業界全体で比類のない精度、効率、汎用性を提供しています。自動車や航空宇宙部品から医療機器や電子機器まで、レーザー溶接は金属を接合するための高速で高品質なソリューションを提供します。しかし、多くの利点があるにもかかわらず、レーザー溶接は歪みや反りなどの一般的な溶接の課題から逃れることはできません。溶接プロセス中の加熱と冷却の不均一性によって引き起こされるこれらの問題は、溶接された部品の寸法精度、機械的完全性、および美観を損なう可能性があります。
歪みと反りを最小限に抑えることは、製品の品質を確保し、材料の無駄を減らし、製造効率を維持するために不可欠です。これを達成するには、熱応力に寄与する要因を深く理解し、最適化された手法と高度なテクノロジーを実装する必要があります。この記事では、レーザー溶接の歪みの原因を探り、メーカーがこれらの課題を軽減して、高性能アプリケーション向けの歪みのない溶接を実現するための実用的な戦略を紹介します。
目次
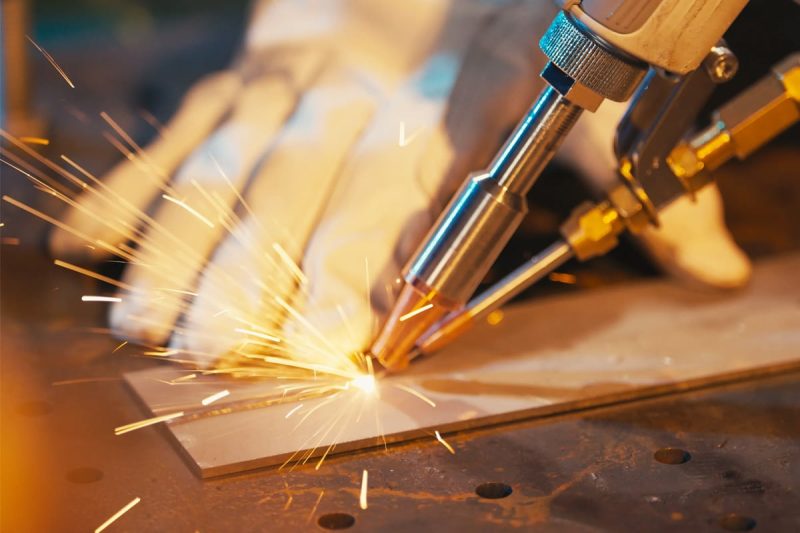
レーザー溶接の歪みと反りを理解する
精度と効率性で知られるレーザー溶接でも、歪みや反りが生じる可能性があり、溶接部品の構造的完全性と品質に問題が生じます。こうした変形は、熱の影響、材料特性、溶接プロセス中に発生する歪みの種類など、さまざまな要因によって生じます。こうした側面を理解することで、歪みを最小限に抑え、高品質の溶接を実現できます。
溶接中の熱の影響
レーザー溶接では、局所的な領域に集中した熱を急速に適用し、急激な温度勾配を作り出します。材料は加熱されると膨張し、冷却されると収縮します。このプロセスの局所的な性質により、不均一な熱膨張と収縮が発生することが多く、材料内に残留応力が生じます。
主な熱の影響は次のとおりです。
- 熱膨張と収縮: 急速な加熱により材料が不均一に膨張し、急速な冷却により収縮力が生じてワークピースが変形します。
- 熱影響部 (HAZ): 溶接部周囲の領域は熱サイクルの影響を受け、微細構造が変化し、多くの場合、追加の応力が発生します。
- 冷却速度: 冷却速度が速いと、急激な熱収縮により、より大きな反りが発生する可能性があります。
歪みに影響を与える材料特性
レーザー溶接中の材料の挙動は、その物理的特性と熱的特性に大きく左右されます。これらの特性によって、熱がどのように吸収、伝導、放散されるかが決まり、歪みや反りの程度に影響します。
主な材料特性は次のとおりです。
- 熱伝導率: アルミニウムなどの熱伝導率の高い材料は熱を素早く放散し、熱勾配を減らしますが、より高いレーザー出力が必要になります。
- 熱膨張係数 (CTE): アルミニウム合金などの CTE が高い材料は、膨張と収縮が大きくなり、歪みが生じる可能性が高くなります。
- 弾性係数: 弾性係数が低い材料は、熱応力下で変形しやすくなります。
- 比熱容量: 熱容量の高い材料は温度が変化する前により多くのエネルギーを吸収し、熱入力の分布に影響を与えます。
溶接における歪みの種類
レーザー溶接中の歪みは、材料、接合部の設計、溶接パラメータに応じて、さまざまな形で現れます。最も一般的なタイプは次のとおりです。
- 縦方向の収縮: 冷却中の収縮により溶接継ぎ目に沿って発生し、材料が縦方向に短くなります。
- 横方向の収縮: これは溶接継ぎ目に対して垂直に発生し、材料が横方向に収縮します。
- 角度歪み: 接合エッジ間の熱分布が不均一なために発生し、角度変位が生じます。
- 座屈: 薄い材料は過度の熱入力により歪んだり座屈したりして、ワークピースが不安定になることがあります。
- 回転歪み: 熱応力によってねじれが生じる円形または湾曲した部品に発生します。
熱の影響、材料特性、歪みの種類の相互作用を分析して理解することで、製造業者はこれらの課題を軽減し、高品質で歪みのない溶接を製造するための戦略を実行できます。
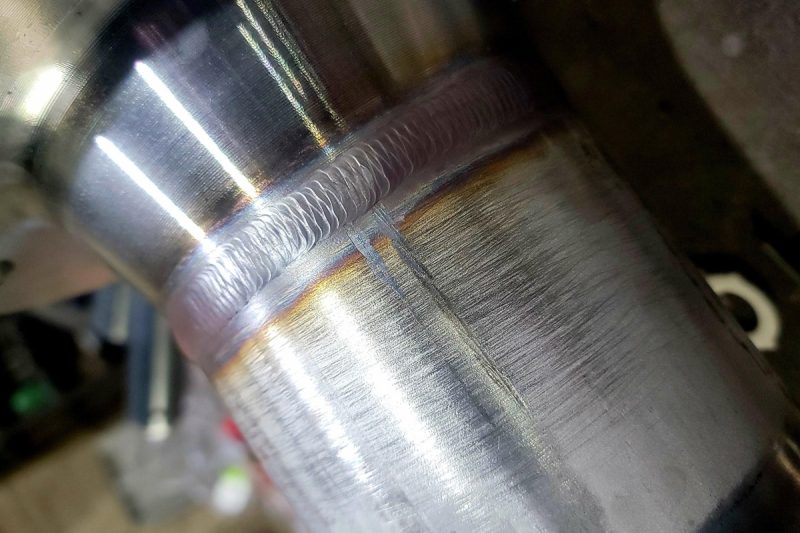
溶接後に歪みや反りが生じやすい材料
レーザー溶接後の歪みや反りの程度は、材料の物理的特性と熱特性によって左右されます。特定の材料は、熱膨張率、伝導性、機械的特性により、本質的に影響を受けやすい場合があります。どの材料が歪みやすいかを理解することで、メーカーはこれらの影響を最小限に抑えるためのカスタマイズされた戦略を採用できます。
アルミニウムおよびアルミニウム合金
アルミニウムは、融点が低く、熱膨張係数 (CTE) が高いため、非常に変形しやすいです。これらの特性により、溶接中に著しい熱膨張が生じ、冷却時に急速な収縮が生じます。さらに、アルミニウムは熱伝導率が高いため、熱が急速に放散され、より高いエネルギー入力が必要となり、熱勾配が悪化して反りが生じる可能性があります。
主な課題:
- CTE が高いと、顕著な膨張と収縮が発生します。
- 薄い部分は特に座屈や角度歪みが発生しやすくなります。
- 急速な熱放散により、熱プロファイルが不均一になります。
最小化戦略:
- 固定具とクランプを使用して動きを制限します。
- 溶接速度とレーザー出力を最適化して熱入力を制御します。
- 温度勾配を減らすためにコンポーネントを予熱します。
ステンレス鋼
ステンレス鋼は、CTE が比較的高く、熱伝導率が低いため、特に薄い部分では歪みが生じやすくなります。材料の放熱性が悪いと、溶接部付近に熱応力が集中し、収縮や角歪みが生じることがよくあります。
主な課題:
- 溶接部に集中した熱により残留応力が増加します。
- 薄い部分では角度や横方向の歪みが発生しやすくなります。
- 熱影響部 (HAZ) の微細構造の変化により、応力が増幅される可能性があります。
最小化戦略:
- レーザー出力と速度のバランスをとって熱入力を制御します。
- 対称的なジョイント設計を使用して熱を均等に分散します。
- パス間の冷却を可能にするために、バックステップまたはスキップ溶接技術を採用します。
高炭素鋼
高炭素鋼は、熱膨張率が高く、溶接中に微細構造が大きく変化する可能性があるため、変形の影響を受けやすくなります。高炭素鋼を急速に冷却すると残留応力が生じ、反りや割れが生じる可能性があります。
主な課題:
- 溶接中に熱膨張と収縮が発生するリスクが高くなります。
- 急速な冷却により残留応力が増加します。
- 微細構造の変化により脆さや反りが生じる可能性があります。
最小化戦略:
- 熱応力を軽減するために予熱し、冷却速度を制御します。
- 熱入力を最小限に抑えるためにパルス溶接技術を使用します。
- ジョイントのフィットアップを最適化して、隙間や加熱の不均一性を減らします。
薄板金属
材料の種類に関係なく、薄い板金は熱応力に耐える剛性がないため、特に歪みが生じやすくなります。レーザー溶接中に最小限の熱入力でも、座屈や波打ちが生じる可能性があります。
主な課題:
- 熱応力に対抗するために剛性を制限します。
- 角度歪みや座屈の影響を受けやすくなります。
- 急速な熱の吸収と放散により、温度勾配が増大します。
最小化戦略:
- 形状を維持するために、しっかりとしたクランプと固定具を使用します。
- 溶接速度を上げるか、パルスレーザーを使用することで熱入力を減らします。
- ワークピースを安定させるには、バッキングバーまたはヒートシンクを使用します。
チタンおよびチタン合金
チタンは、CTE が比較的高く、熱伝導率が低いため、歪みに対して中程度の感受性を示します。アルミニウムや薄い鋼鉄に比べて反りが発生しにくいですが、溶接中の熱制御が不適切だと、角度や縦方向の歪みが生じる可能性があります。
主な課題:
- 放熱性が低いと局所的な熱応力が増加します。
- 溶接中に酸素と反応すると、反りが悪化する可能性があります。
- 過熱や高温への長時間の暴露に敏感です。
最小化戦略:
- 溶接品質を維持し、熱の影響を最小限に抑えるためにシールドガスを使用します。
- 精密固定具を使用して部品を所定の位置に保持します。
- 熱入力を制御するために溶接パラメータを最適化します。
銅および銅合金
銅は熱伝導率が高いため、熱が急速に放散し、不均一な熱勾配が生じるため、安定した溶接が困難です。ただし、CTE が高いため、熱入力が過剰になると歪みが生じやすくなります。
主な課題:
- 急速な熱放散には高いレーザー出力が必要です。
- CTE が高いと、大幅な膨張と収縮が発生します。
- 加熱が不均一だと、複雑な形状に反りが生じます。
最小化戦略:
- 予熱を使用して温度勾配を減らします。
- レーザーの焦点と出力を最適化して、一貫した熱の適用を保証します。
- リアルタイム監視を使用して熱入力を制御します。
二相ステンレス鋼
二相ステンレス鋼は、オーステナイト系ステンレス鋼よりも剛性が高いため、歪みが生じにくいです。ただし、熱の適用が不均一な場合、特に非対称溶接では、角度や横方向の歪みが生じる可能性があります。
主な課題:
- 冷却が不均一だと残留応力が生じる可能性があります。
- 複雑な形状における角度の歪み。
- 熱サイクルによる微細構造の変化。
最小化戦略:
- 熱を均等に分散させるためにバランスのとれた溶接技術を使用します。
- パス間の温度を制御して、冷却の不均一を防ぎます。
- リアルタイムモニタリングを備えたレーザー溶接を採用し、精度を高めます。
溶接後に歪みが生じやすい材料には、高い熱膨張係数、低い剛性、不均一な加熱に対する敏感さなどの共通の特性があります。これらの課題に対処するには、溶接パラメータ、固定ソリューション、および熱制御技術を慎重に選択する必要があります。熱応力下での各材料の挙動を理解することで、メーカーはカスタマイズされた戦略を実行し、歪みのない溶接を実現し、コンポーネントの完全性を維持できます。
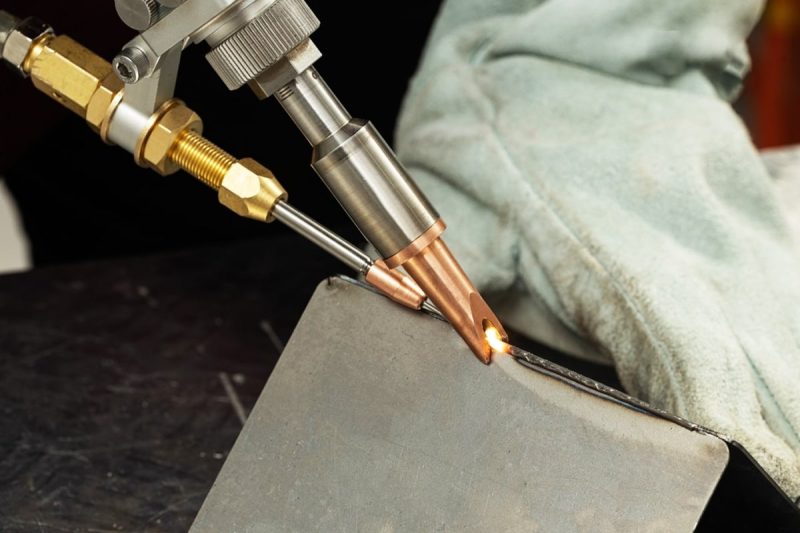
レーザー溶接における歪みと反りに影響を与える要因
レーザー溶接は正確で効率的なプロセスですが、局所的な熱入力と急速な冷却により、歪みや反りが生じる可能性があります。これらの課題の原因となる要因を理解することで、課題を最小限に抑えるための効果的な戦略を実施できます。
熱入力と温度勾配
レーザー溶接中の熱入力とその結果生じる熱勾配は、歪みや反りの程度を決定する上で重要な役割を果たします。
- 局所的な熱入力: レーザー溶接は、小さな領域に強力な熱を集中させ、急激な温度勾配を作り出します。この勾配により、材料の膨張と収縮が不均一になり、残留応力が生じます。
- 過剰な熱入力: レーザー出力が高すぎる場合や溶接速度が遅すぎる場合、過剰な熱入力によって熱影響部 (HAZ) が拡大し、歪みが増幅される可能性があります。
- 急速冷却: レーザー溶接では急速冷却が行われることが多く、急激な温度変化が生じて反りのリスクが高まります。
緩和戦略:
- レーザー出力と溶接速度を最適化して、熱入力のバランスを取り、熱勾配を最小限に抑えます。
- パルス溶接技術を使用して熱伝達を制御し、過度の加熱を減らします。
- 溶接中の温度プロファイルを追跡および調整するには、熱画像またはリアルタイム監視システムを使用します。
材料の厚さとジョイント設計
材料の厚さと溶接継手の設計は、レーザー溶接時の歪み挙動に大きな影響を与えます。
- 材料の厚さ: 薄い材料は、剛性が低く、熱応力に耐えられないため、歪みが生じやすくなります。材料が厚いほど歪みが生じにくくなりますが、より高いレーザー出力が必要になり、HAZ が増加する可能性があります。
- ジョイント設計: 溶接ジョイントの種類とフィットアップは熱分布に影響します。ジョイントの設計が適切でないと、温度勾配が悪化し、膨張と収縮が不均一になる可能性があります。
一般的な関節の種類とその影響:
- 突合せジョイント: 一般的に、適切に位置合わせすると歪みが最小限に抑えられます。
- ラップジョイント: 大きな温度勾配が生じ、反りが生じる可能性があります。
- T ジョイントとコーナー ジョイント: 形状が複雑になると応力が集中し、歪みのリスクが増大する可能性があります。
緩和戦略:
- 対称性を促進し、熱を均等に分散するジョイント設計を選択します。
- 隙間や加熱の不均一さを最小限に抑えるために、しっかりと接合部をフィットさせます。
- 面取りなどのエッジ準備技術を使用して、ジョイントの安定性を向上させ、歪みを軽減します。
クランプと固定
ワークピースを所定の位置に保持し、溶接を歪ませる力に対抗するには、適切なクランプと固定が不可欠です。
- 剛性クランプ: 強力なサポートを提供しますが、過度に拘束すると残留応力が生じる可能性があります。
- フレキシブルクランプ: 応力の蓄積を軽減するためにある程度の動きを許可しますが、反りを完全に防ぐことはできない場合があります。
- ヒートシンク: ヒートシンクとして機能する器具は、熱を放散させ、温度勾配を減らすのに役立ちます。
不適切な固定による影響:
- サポートが不十分だと、溶接中にワークピースが動いたり変形したりする可能性があります。
- 過度に拘束すると応力が固定され、溶接後の反りが発生する可能性があります。
緩和戦略:
- 堅牢な固定具を使用して、過度に拘束することなく部品をしっかりと固定します。
- 熱放散を管理するために、器具にヒートシンクを組み込みます。
- プロセス中の位置合わせを維持するために、タック溶接または連続溶接を使用します。
予熱および冷却速度
予熱と冷却の熱サイクルは、レーザー溶接における歪みと反りの程度に大きな影響を与えます。
- 予熱: 溶接前にワークピースの温度を上げると、材料がより均一に膨張するため、温度勾配が減少します。
- 制御された冷却: 冷却速度を管理することで、残留応力や反りにつながる急激な収縮を防止します。
重要な考慮事項:
- 予熱は、アルミニウムや高炭素鋼など、熱膨張係数の高い材料に特に効果的です。
- 過熱により HAZ が増加し、望ましくない冶金学的変化が生じる可能性があります。
- 制御されていない冷却は応力集中を悪化させ、歪みを増加させる可能性があります。
緩和戦略:
- 温度差を減らすために、オーブンまたは誘導加熱を使用してワークピース全体を均一に予熱します。
- 溶接後の熱処理または徐冷法で冷却速度を制御します。
- 一貫性を確保するために、熱電対または赤外線センサーを使用して予熱および冷却中の温度を監視します。
レーザー溶接における歪みと反りを最小限に抑えるには、入熱、材料の挙動、接合部の設計、熱管理に影響を与える要因に細心の注意を払う必要があります。これらのパラメータを最適化し、効果的なクランプと予熱技術を組み込むことで、メーカーは歪みのリスクを大幅に軽減し、より高い溶接品質と寸法精度を確保できます。
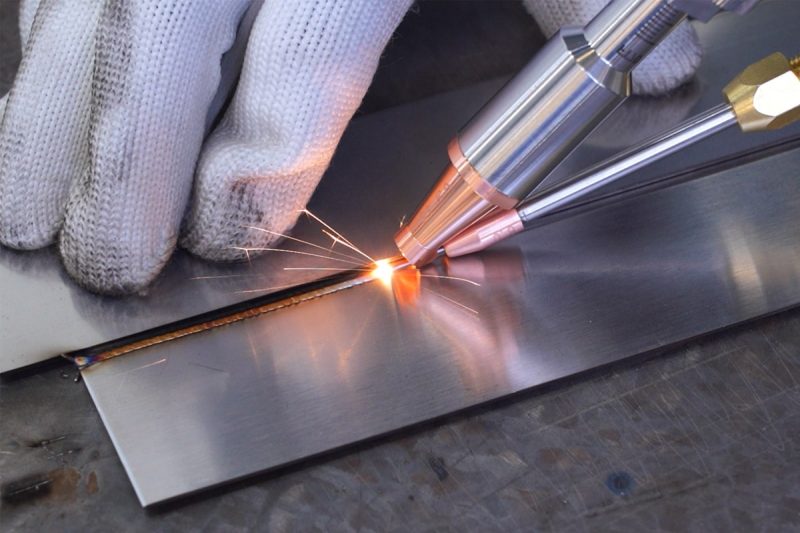
レーザー溶接における歪みと反りを最小限に抑える方法
レーザー溶接における歪みと反りを最小限に抑えるには、熱管理、接合部の設計、材料の準備、溶接技術を考慮した戦略的なアプローチが必要です。
溶接パラメータの最適化
熱入力を制御し、熱勾配を最小限に抑え、歪みを減らすには、溶接パラメータを適切に調整することが不可欠です。
- レーザー出力の調整: レーザー出力が高いと、熱入力が過剰になり、熱影響部 (HAZ) が大きくなる可能性があります。レーザー出力を最適化して、不必要な加熱を最小限に抑えながら十分な浸透を実現します。
- 溶接速度の制御: 溶接速度が遅いと熱入力が増加し、歪みが大きくなります。速度が速いと熱勾配は減少しますが、完全な融合を確実にするために注意が必要です。
- パルスレーザーと連続波レーザーの使用: パルスレーザーは断続的な熱伝達を可能にし、全体的な熱入力を減らし、歪みを最小限に抑えます。連続波レーザーは高速アプリケーションに適していますが、追加の冷却戦略が必要になる場合があります。
実用的なヒント:
- 試運転を使用して、特定の材料に最適な電力と速度の設定を特定します。
- 溶接中の熱分布を監視するために熱画像を使用します。
- 薄い材料や歪みが生じやすい材料には、低出力とパルスレーザーモードを組み合わせます。
ジョイント設計の考慮事項
溶接継手の設計と準備は、熱分布と応力集中に大きな影響を与えます。
- 適切なジョイント タイプの選択: 突き合わせジョイントなどの対称ジョイントは、熱を均等に分散し、歪みを軽減するのに役立ちます。ラップ ジョイントとコーナー ジョイントは、特定の用途では必要ですが、ストレスを管理するために慎重な取り扱いが必要です。
- エッジの準備: 面取りや機械加工などの適切なエッジの準備により、しっかりとしたフィットアップと一貫した熱の適用が保証され、不均一な加熱や反りのリスクが軽減されます。
実用的なヒント:
- 均一な熱の流れを促進するジョイント設計を使用します。
- 精密な加工によりジョイントの隙間を最小限に抑えます。
- 隙間を埋めて溶接品質を向上させるために、充填材を選択的に使用することを検討してください。
材料の選択と準備
適切な材料を選択し、溶接の準備を整えることで、歪みを大幅に減らすことができます。
- 材料の適合性: 熱応力を最小限に抑えるために、熱膨張係数 (CTE) が低い材料または熱伝導率が高い材料を使用します。
- 表面の清浄度: 油、酸化物、汚れなどの汚染物質は熱吸収に影響し、加熱が不均一になります。表面を清浄にすると、溶接の一貫性が向上し、歪みが減少します。
実用的なヒント:
- 同様の熱特性と機械特性を持つベース材料とフィラーを組み合わせます。
- 化学的または機械的な洗浄方法を使用して表面を準備します。
- 熱膨張率の高い材料を予熱して、熱勾配を減らします。
固定具とクランプの使用
適切な固定とクランプ技術により、溶接中の動きが防止され、熱放散が効果的に管理されます。
- 適切なクランプ技術: 歪みを防ぐためにワークピースをしっかりと固定しますが、残留応力の原因となる過剰な拘束は避けてください。
- バッキング バーとヒート シンクの使用: バッキング バーは溶接領域をサポートし、材料を安定させることで歪みを軽減します。一方、ヒート シンクは余分な熱を放散して温度勾配を制御します。
実用的なヒント:
- 特定のワークピースの形状に合わせてカスタム固定具を設計します。
- サポートを損なうことなく柔軟性を確保するために、調整可能なクランプを組み込みます。
- 放熱を管理するには、バッキングバーまたはヒートシンクに熱伝導率の高い材料を使用します。
予熱と溶接後熱処理
溶接前後の熱管理により、残留応力と歪みが大幅に減少します。
- 制御された予熱: ワークピースを予熱すると、特にアルミニウムや高炭素鋼などの材料の場合、熱勾配が減少します。
- 溶接後の熱処理: 溶接後の徐冷または応力緩和焼鈍により残留応力が軽減され、材料が安定します。
実用的なヒント:
- オーブン、トーチ、または誘導加熱装置を使用してワークピースを均一に予熱します。
- 急激な収縮を防ぐために、断熱ブランケットや熱処理で冷却速度を制御します。
- 一貫した熱管理のために熱電対を使用して温度を監視します。
溶接シーケンス計画
溶接シーケンスを戦略的に計画することで、熱を均等に分散し、応力の蓄積を管理することができます。
- バランス溶接: ワークピースの反対側を交互に溶接することで、熱入力のバランスが取れ、反りが最小限に抑えられます。
- スキップ溶接技術: 断続的にセクションを溶接し、溶接間の冷却を可能にして、特定の領域に過度の熱が蓄積されるのを防ぎます。
実用的なヒント:
- 中間冷却を可能にするために、大きな溶接部分を小さなセクションに分割します。
- 低応力領域から溶接を開始し、徐々に高応力領域へ移動します。
- ソフトウェア ツールを使用して応力分布をシミュレートし、溶接シーケンスを最適化します。
高度な技術の採用
革新的な溶接技術により、歪みや反りを最小限に抑える高度なソリューションが提供されます。
- ハイブリッドレーザー溶接: レーザー溶接とアーク溶接などの他の技術を組み合わせて、熱分散を改善し、歪みを軽減します。
- アダプティブ レーザー溶接: センサーとフィードバック システムを使用して、材料とプロセス条件に基づいて溶接パラメータをリアルタイムで調整します。
- リアルタイムの監視と制御: 熱画像、レーザー出力フィードバック、変形センサーを組み込んで、最適な溶接条件を維持します。
実用的なヒント:
- 複雑なアプリケーションや許容度の高いアプリケーションにはハイブリッド システムに投資してください。
- リアルタイム監視システムを使用して、逸脱を即座に検出し修正します。
- 一貫した溶接パラメータを維持するために閉ループ制御システムを実装します。
これらの方法を実施することで、メーカーはレーザー溶接プロセスにおける歪みや反りを効果的に最小限に抑えることができます。溶接パラメータの最適化、適切な接合部の設計、材料の準備、適切な固定具の使用、熱サイクルの管理、高度な技術の活用はすべて、高品質で歪みのない溶接の実現に貢献します。これらの戦略は、溶接部品の寸法精度を高めるだけでなく、生産効率を改善し、材料の無駄を減らし、信頼性が高くコスト効率の高い製造結果を保証します。
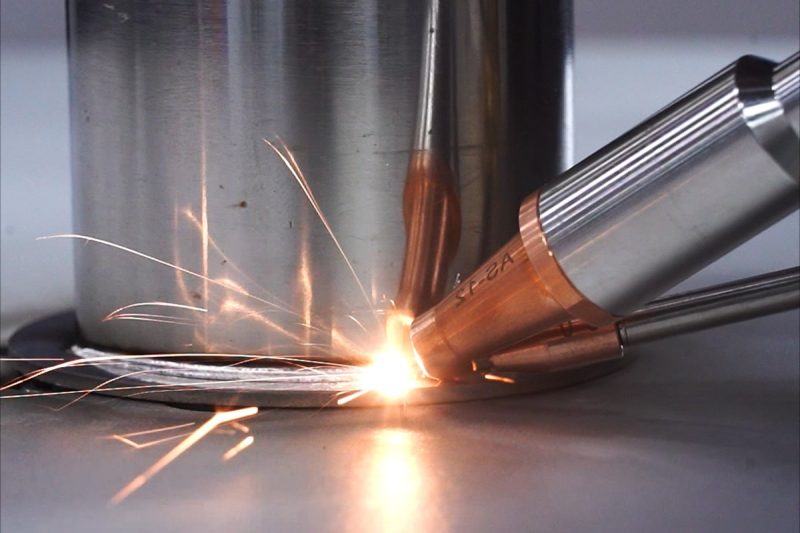
まとめ
レーザー溶接における歪みと反りを最小限に抑えることは、高品質の溶接を実現し、部品の構造的完全性を維持するために不可欠です。歪みは不均一な加熱と冷却によって発生し、残留応力によって材料が変形します。熱入力、材料特性、接合部設計、熱管理などの重要な要素に対処することで、メーカーはこれらの課題を効果的に軽減できます。
レーザー出力、速度、パルスまたは連続波レーザーの使用など、溶接パラメータを最適化することは、熱入力を制御するために不可欠です。適切なジョイント設計、材料の選択、表面処理により、均一な熱分布が確保され、熱応力が軽減されるため、溶接品質がさらに向上します。効果的なクランプ、バッキングバーとヒートシンクの使用、戦略的な予熱と溶接後の熱処理も重要な役割を果たします。ハイブリッドレーザー溶接、リアルタイム監視、適応制御システムなどの高度な技術は、歪みを最小限に抑えるための追加のツールを提供します。
これらの戦略を統合することで、メーカーは歪みのない、正確で信頼性の高い溶接を実現し、効率と製品のパフォーマンスを向上させることができます。
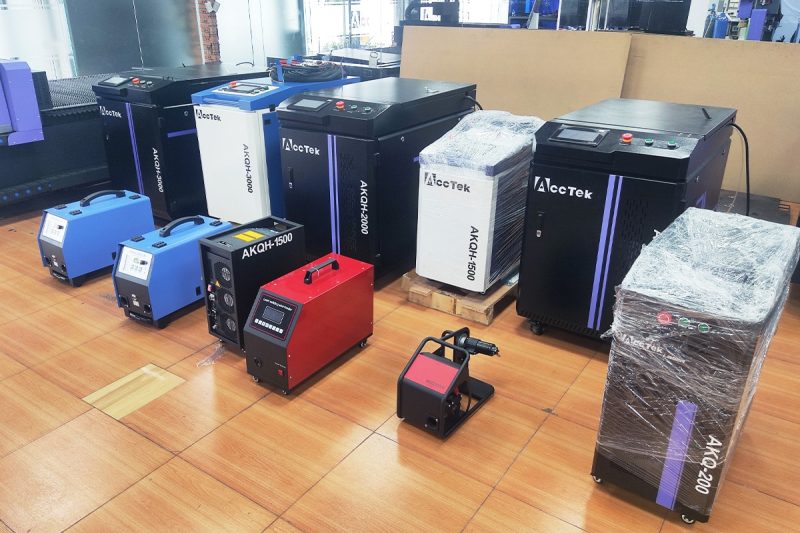
レーザー溶接ソリューションを入手
で AccTek レーザーレーザー溶接時の歪みや反りを最小限に抑えるためにメーカーが直面する課題を当社は理解しています。 レーザー切断機, レーザー溶接機, レーザー洗浄機、 と レーザーマーキングマシン当社は、お客様のニーズに合わせた最先端のソリューションを提供することに尽力しています。当社の高度なレーザー溶接機は、正確な熱制御を保証するように設計されており、最も要求の厳しい用途でも歪みのない溶接が可能です。
AccTek Laser のマシンは、最適化されたレーザー出力設定、リアルタイム監視システム、アダプティブ溶接テクノロジーなど、さまざまなカスタマイズ可能な機能を備えており、比類のないパフォーマンスと信頼性を提供します。繊細な素材や複雑な形状を扱う場合でも、当社の専門家がお客様の特定の要件に最適な構成の選択をお手伝いします。
AccTek Laser と提携して、溶接の課題を克服し、生産効率を高めましょう。包括的なコンサルティング、技術サポート、業界をリードするレーザー溶接ソリューションへのアクセスについては、今すぐお問い合わせください。あらゆる溶接で完璧な仕上がりを実現するお手伝いをいたします。
ワークピースを所定の位置に保持し、溶接を歪ませる力に対抗するには、適切なクランプと固定が不可欠です。
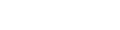
連絡先
- [email protected]
- [email protected]
- +86-19963414011
- No. 3 ゾーン A、Lunzhen 工業地帯、玉城市、山東省。
レーザー ソリューションを入手する