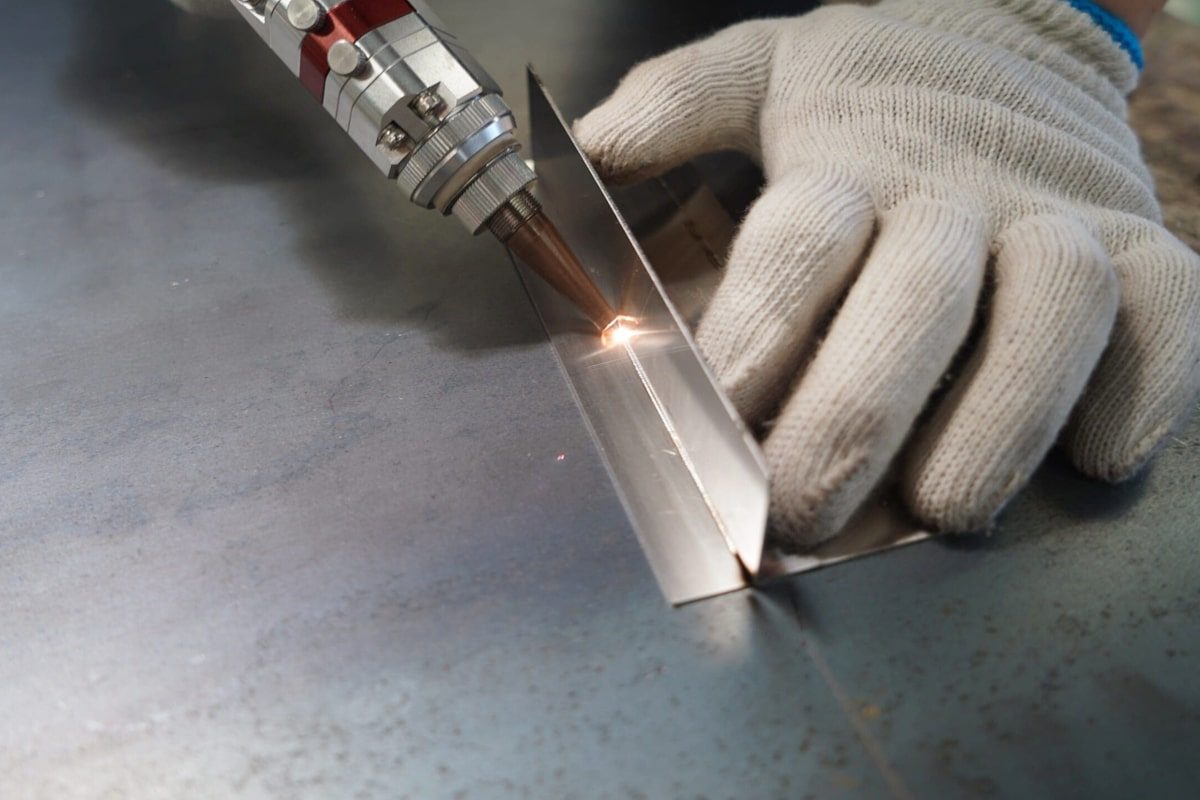
レーザー溶接の溶接性に影響を与える要因は何ですか?
レーザー溶接は、高精度、最小限の熱歪み、従来の方法では溶接が困難な材料の接合を可能にする機能などを提供し、現代の製造業に革命をもたらしました。航空宇宙、自動車、医療機器、電子機器などの業界では、最小限の溶接後処理で高品質で強力な接合部を実現できるスピードと機能のため、レーザー溶接に大きく依存しています。レーザー溶接には数多くの利点がありますが、最適な溶接性を実現するのは必ずしも簡単ではありません。レーザー溶接の成功は、材料特性、レーザーパラメータ、機器の設定、環境条件、溶接後処理など、さまざまな要因によって決まります。これらはすべて、強力で耐久性があり欠陥のない溶接を実現するために慎重に制御する必要があります。
この記事では、レーザー溶接における材料の溶接性に影響を与えるさまざまな要因について詳しく説明します。これらの要因には、ベース材料の組成、接合部の形状、レーザー出力、速度、ビーム品質、および温度や汚染物質などの外部環境要因が含まれます。また、レーザー溶接で発生する一般的な課題と、それらを緩和して可能な限り最高の溶接品質を実現する方法についても説明します。この記事を読み終える頃には、レーザー溶接に関係するさまざまな変数と、優れた溶接結果を得るためにこれらの要因を最適化する方法について、読者は包括的に理解できるようになります。
目次
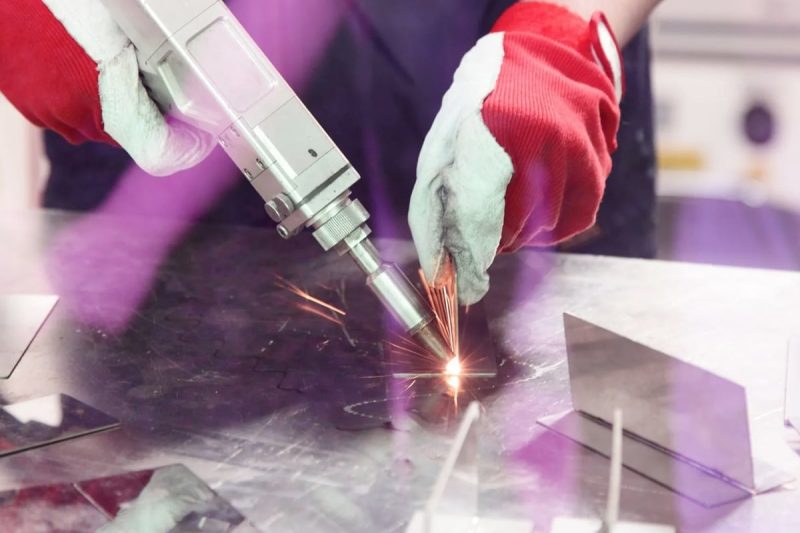
レーザー溶接入門
定義と概要
レーザー溶接は、高集束レーザー ビームを使用して材料 (通常は金属または熱可塑性プラスチック) を溶かして融合する精密溶接技術です。レーザー ソースによって生成されたレーザー ビームは、材料に焦点を絞ったエネルギーを照射し、接合面のベース材料を溶かす局所的な熱領域を作成します。溶けた材料が固まると、溶接部が形成されます。このプロセスは、一定の熱を供給する連続波 (CW) レーザー、または過熱を防ぎ、制御された浸透を提供するために短時間でエネルギーを供給するパルス レーザーのいずれかを使用して実行できます。
レーザー溶接は汎用性が高く、さまざまな材料の種類や厚さに使用できます。溶接速度が速く、熱影響部 (HAZ) が狭く、材料の歪みが最小限で、プロセスを自動化できるため生産効率が向上するなど、数多くの利点があります。レーザー ビームの精度により、狭いスペースや繊細な部品の溶接が可能になり、航空宇宙産業やエレクトロニクス産業などの高精度アプリケーションに最適です。
レーザー溶接における溶接性の重要性
レーザー溶接における溶接性とは、レーザー溶接プロセスを受けたときに、材料が強固で欠陥のない接合部を形成する能力を指します。溶接性の達成は、材料の化学組成、熱特性、接合部の設計、レーザー ビームからの局所的な熱入力に対する反応など、相互に関連するいくつかの要因に依存します。これらの要因が最適化されていない場合、溶接接合部には、多孔性、亀裂、歪み、または弱い結合などの欠陥が生じやすくなります。
レーザー溶接では、レーザービームの高エネルギー集中が材料の微細構造と機械的特性に重大な影響を与える可能性があるため、溶接性の概念が特に重要です。たとえば、急速な加熱と冷却のサイクルは、特定の材料で残留応力、亀裂、または望ましくない相転移などの問題を引き起こす可能性があります。これらの課題を克服するために、メーカーはレーザー溶接に関係するさまざまなパラメータを慎重に選択して制御する必要があります。
従来の溶接方法との比較
レーザー溶接は精度と効率に優れていることで知られていますが、MIG (金属不活性ガス) 溶接や TIG (タングステン不活性ガス) 溶接などの従来の溶接方法とはいくつかの重要な点で大きく異なります。従来の溶接方法では、電気アークを使用して熱を発生させ、材料のより広い範囲を加熱し、一般的に熱影響部が広くなります。これらの方法では、溶接速度が遅く、材料の歪みが大きくなる傾向があります。一方、レーザー溶接はエネルギービームが非常に集中していることが特徴で、溶接速度が速く、熱影響部が狭く、歪みが最小限に抑えられます。
ただし、レーザー溶接は、従来の方法よりも、材料特性、ジョイント設計、レーザー設定の変化に敏感です。たとえば、従来の方法は、厚い材料や不規則な形状のジョイントを溶接する場合に許容範囲が広いのに対し、レーザー溶接では、レーザー出力、ビーム焦点、溶接速度などのパラメータをより正確に制御する必要があります。そのため、レーザー溶接は、プロセスにとって難しい材料や形状を扱う場合など、すべての用途に最適なソリューションではない可能性があります。
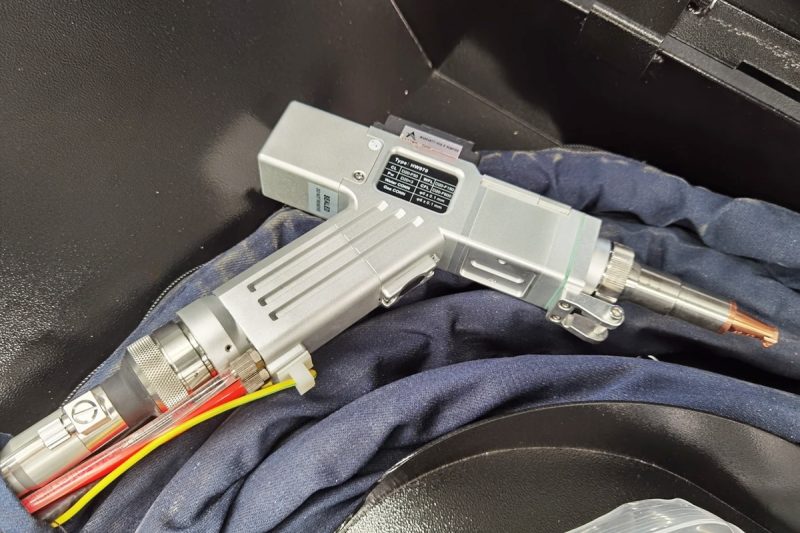
材料特性
溶接される材料は、レーザー溶接作業の成功に重要な役割を果たします。溶接性に影響を与える主な材料特性には、母材の組成、厚さ、形状、融点、熱伝導率、合金元素や添加物の存在などがあります。
ベース材料構成
母材の化学組成は、溶接性に影響を及ぼす最も重要な要因の 1 つです。材料によって融点、熱伝導率、凝固挙動が異なり、これらはすべてレーザー溶接プロセスに影響します。たとえば、高炭素鋼は冷却中に硬くて脆い相を形成する傾向があり、溶接部に亀裂が生じる可能性が高くなります。同様に、クロム、ニッケル、モリブデンなどの特定の合金元素を多く含む材料は相転移の影響を受けやすく、溶接欠陥や機械的特性の低下につながる可能性があります。
いくつかの材料、例えば アルミニウム そして 銅は、熱伝導率が高く、融点が低いため、レーザー溶接で溶接するのが特に困難です。これらの材料は、十分な浸透を得るためにより高いレーザー出力を必要としますが、溶け落ちのリスクもはるかに高くなります。チタン合金などの膨張係数の高い材料は、溶接中に熱変形を起こす可能性があり、レーザーパラメータの正確な制御が必要になります。
最適なレーザーパラメータを決定するには、溶接される材料の組成を理解することが不可欠です。材料に含まれる合金元素や不純物は、材料が熱に反応する方法や溶接の形成に影響を与える可能性があるため、レーザー出力、ビーム焦点、シールドガスなどのパラメータを調整する必要があります。
厚さと形状
材料の厚さと接合部の形状は、溶接に必要なエネルギーと材料内の熱分布に直接影響します。薄い材料の場合、通常はレーザー出力を低くすれば十分ですが、溶け落ちの原因となる過剰な熱入力を避けるためには、慎重な制御が必要です。厚い材料の場合、完全な溶け込みと健全な溶接を確実に行うには、レーザー出力を高くし、溶接速度を遅くする必要があります。
接合部の形状も、レーザーが材料とどのように相互作用するかに影響します。単純な突合せ接合は、2 つの表面が直接接続されるため、比較的簡単に溶接できます。ただし、T ジョイント、フィレット ジョイント、ラップ ジョイントなどのより複雑な接合部には、特別な注意が必要です。接合部の角度と配置は、レーザーが材料を適切に貫通して融合する能力に影響します。
形状が複雑な材料の場合、ビームをジョイントに合わせるのが難しいことや、ジョイントに沿った厚さのばらつきがあるため、レーザー溶接にさらなる課題が生じる可能性があります。ジョイント設計を最適化し、レーザー ビームを適切に調整することは、強力で高品質の溶接を実現するための重要なステップです。
融点と熱伝導率
材料の融点によって、材料を溶かすのに必要なエネルギー量が決まります。タングステン、チタン、高合金鋼などの融点の高い材料は、融点に達するまでにかなりのエネルギーが必要で、レーザー出力を慎重に管理する必要があります。一方、アルミニウムや亜鉛などの融点の低い材料は、レーザー ビームの下で溶けやすいため、過度の溶融を防ぐために高速溶接やパルス レーザー技術が必要になる場合があります。
熱伝導率(材料の熱伝導能力)も溶接性に影響します。銅などの熱伝導率の高い材料は熱を素早く放散するため、レーザービームは熱損失を克服して適切な浸透を達成するために十分なエネルギーを供給する必要があります。逆に、銅などの熱伝導率の低い材料は、 ステンレス鋼熱をより効果的に保持しますが、適切に管理しないと、熱影響部 (HAZ) が大きくなり、熱による歪みが発生する可能性があります。
合金元素と添加物
合金元素や添加物の存在は、材料の溶接性に大きな影響を与える可能性があります。マンガン、シリコン、クロムなどの一般的な合金元素は、材料の機械的特性を改善できますが、溶接中に問題を引き起こす可能性もあります。たとえば、マンガンは溶接部の割れを引き起こしやすくし、シリコンが多すぎると溶接部に脆い相が形成される可能性があります。
フラックスなどの添加剤は、表面結合を強化したり、酸化を防いだり、溶接プールの挙動を変更したりするために使用できます。フラックスやその他の添加剤は、溶接の最終的な品質と機械的特性に影響を与える可能性があるため、慎重に選択する必要があります。
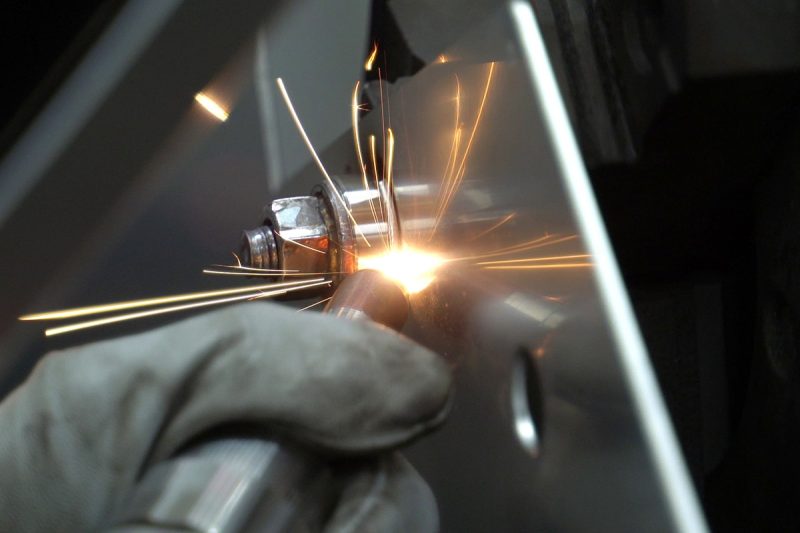
レーザーパラメータ
レーザー出力、焦点、速度、ビーム品質などのレーザーパラメータは、材料の溶接性にとって基本となります。これらのパラメータは、レーザービームが材料とどのように相互作用するか、溶接プールに供給されるエネルギー、および凝固速度を制御します。
レーザーパワー
レーザー出力は、浸透の深さ、溶接速度、およびプロセス中に発生する熱量に直接影響します。レーザー出力が高いほど浸透は深くなりますが、溶け落ちや過度の熱影響部が発生するリスクも高まります。出力設定が低いと、厚い材料に完全に浸透するのに十分なエネルギーが得られず、接合部が弱くなったり、融合が不完全になったりすることがあります。
最適なレーザー出力設定は、溶接する材料、その厚さ、および望ましい溶接特性によって異なります。一般的には、材料を溶かすのに十分な出力と、ワークピースを変形させる可能性のある過剰な熱を回避することの間でバランスを取る必要があります。
レーザーフォーカス
レーザーの焦点は、レーザー ビームのサイズと強度を制御します。焦点が絞られたビームは、材料上に小さく高エネルギーのスポットを作り、より深い浸透とより狭い溶接を可能にします。ただし、焦点が絞られすぎると、特に薄い材料の場合、溶け落ちのリスクが高まります。対照的に、焦点がぼけたビームは、エネルギーをより広い領域に分散し、溶け落ちのリスクを軽減しますが、浸透は浅くなり、溶接は広くなります。
最適な焦点は、接合部の材質、厚さ、形状によって異なります。精密な制御のために、レーザー システムは通常、焦点を調整できる機能を備えており、オペレーターは特定の溶接要件に応じてビームを微調整できます。
パルス持続時間
パルス レーザー溶接では、レーザー ビームが短時間の強力なエネルギー バーストとして照射されます。これらのパルスの持続時間 (パルス持続時間) は、溶接の浸透深さ、冷却速度、および全体的な品質に大きな影響を与えます。パルスが短いほどエネルギー入力をより制御でき、過熱を防ぐのに役立ちます。一方、パルスが長いほど、より深い浸透のためにより多くのエネルギーが供給されます。
パルス持続時間は、溶接する材料と厚さに基づいて慎重に調整する必要があります。通常、厚い材料には長いパルスが使用され、薄い材料には熱による歪みを避けるために短いパルスが使用されます。
ビーム品質
ビーム品質とは、レーザー ビーム内のエネルギーの分布を指し、レーザーが材料にどれだけ効果的に焦点を合わせられるかを決定する重要な要素です。高品質のビームは均一なエネルギー プロファイルを持ち、一貫したエネルギー供給とより安定した溶接を可能にします。一方、低品質のビームはエネルギー分布が不均一になり、溶接品質が低下し、接合部の形成が不均一になる可能性があります。
ビーム品質の高いレーザー溶接システムは、通常、欠陥が少なく、よりきれいで正確な溶接を実現します。
溶接速度
溶接速度は、レーザーが材料に照射される時間に影響します。通常、溶接速度が速いほど熱入力が低くなり、熱影響部が小さくなり、歪みが減少します。ただし、速度が速すぎると、適切な浸透に十分な時間が取れず、接合部が弱くなる可能性があります。速度が遅いと熱入力が増加し、熱影響部が大きくなり、歪みが大きくなる可能性がありますが、厚い材料を溶接する場合は速度が遅くなる場合があります。
最適な溶接速度は、材料の種類、厚さ、および望ましい溶接特性によって決まります。
シールドガス
シールドガスは、レーザー溶接で溶接プールを周囲の大気による汚染から保護するために使用されます。周囲の大気による汚染は、酸化やその他の欠陥の原因となります。使用されるシールドガスの種類 (アルゴン、窒素、ガス混合物など) は、強度、外観、耐腐食性など、溶接の品質に影響する可能性があります。さらに、シールドガスは溶接プールの熱放散と冷却速度に影響し、溶接の微細構造に影響する可能性があります。
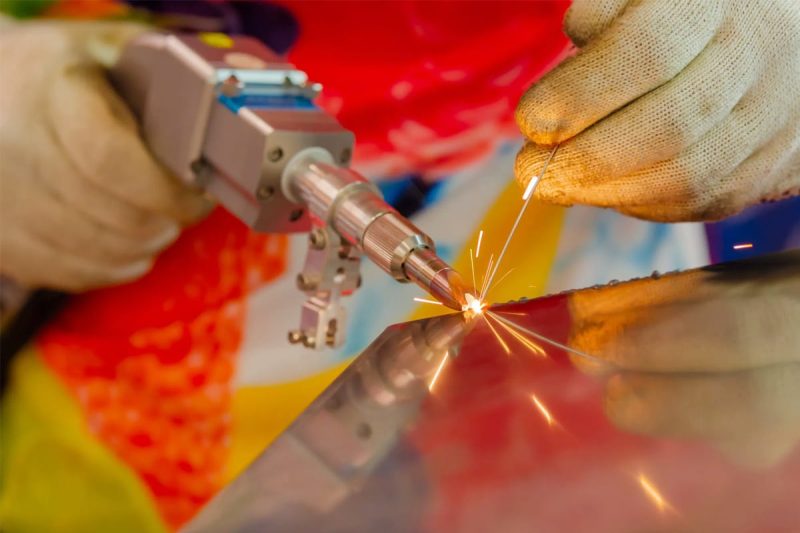
材料の厚さとジョイント設計
レーザー溶接では、材料の厚さと接合部の形状が溶接プロセス、必要なエネルギー、そして最終的には溶接の品質に大きな影響を与えます。これらの要素を深く理解することは、欠陥を最小限に抑えた最適な溶接を実現するために不可欠です。
材料の厚さ
溶接される材料の厚さは、レーザー溶接プロセスに直接影響します。厚い材料では、完全な浸透と強力な結合を実現するために、より高いレーザー出力が必要です。厚い材料を溶接する場合は、過熱や歪みを防ぐために熱入力を慎重に管理する必要があります。出力設定を高くすると、より深い浸透が可能になりますが、熱影響部 (HAZ) のサイズも大きくなり、ベース材料の機械的特性に影響を与える可能性があります。
薄い材料の場合、溶けるのに必要なエネルギーが少ないため、溶け落ちを防ぐために通常はレーザー出力を低くします。薄い材料をレーザーで溶接する際の主な課題は、材料を損傷することなく十分な浸透を達成しながら、過剰な熱入力を避けるためにレーザー出力のバランスをとることです。レーザー溶接の高速冷却速度は、薄い材料の熱影響部を最小限に抑えるのに役立ちます。
ジョイント形状
突合せ継手、T 継手、重ね継手、すみ肉継手などの継手の形状は、レーザー溶接の成功に重要な役割を果たします。レーザー溶接は、通常、突合せ継手で最もうまく機能します。これは、材料の端を直接整列させることで、一貫した溶接プールが確保されるためです。ただし、重ね継手や T 継手などのより複雑な継手では、材料間に存在する可能性のある隙間を含め、継手のすべての側面にレーザーが確実に浸透する必要があるため、ビームの慎重な調整が必要です。
ジョイント形状が複雑な形状であったり、材料の厚さにばらつきがあったりする場合は、溶接パラメータの調整が必要です。たとえば、重ね継ぎの場合は、上部の材料が下部の材料と効果的に融合するように、レーザーの焦点とビーム角度を正確に制御する必要があります。また、すみ肉溶接の場合は、角度と材料の近接性が熱分布に影響を与える可能性があるため、レーザー ビームとジョイントの表面との相互作用を慎重に制御する必要があります。
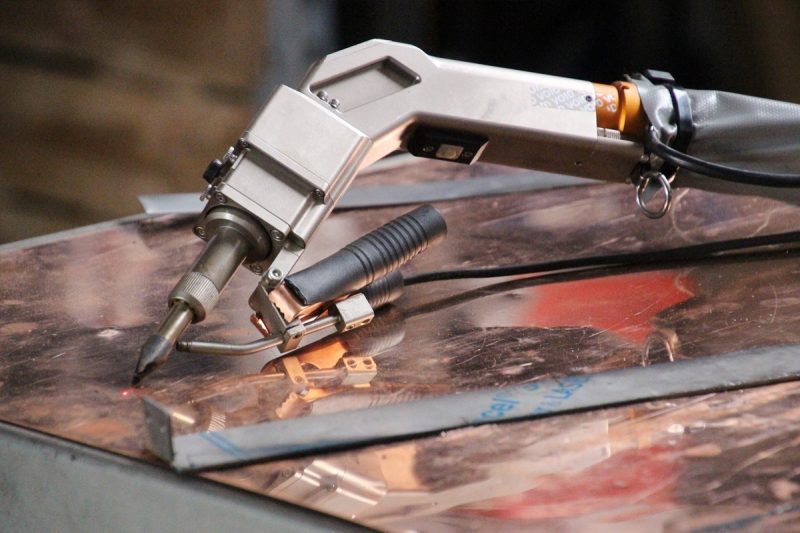
熱管理と冷却速度
レーザー溶接では、材料特性を制御し、歪みを最小限に抑え、溶接欠陥を防ぐために、効果的な熱管理が不可欠です。熱管理の重要な側面には、熱影響部 (HAZ) と冷却速度が含まれます。
熱影響区域 (HAZ)
熱影響部 (HAZ) は、溶接中の高温により溶融しないものの微細構造が変化する材料の領域です。HAZ のサイズと範囲は、レーザー出力、溶接速度、材料の種類によって決まります。レーザー溶接では、レーザー ビームの熱が集中するため、従来の溶接方法に比べて HAZ が小さくなる傾向があります。ただし、特に高強度鋼や熱サイクルに敏感な材料の場合、小さな HAZ でも材料特性に影響を与える可能性があります。
特定の材料、例えば 高炭素鋼 またはチタン合金の場合、HAZ が大きくなると、脆性挙動や応力腐食割れなどの機械的特性が低下する可能性があります。そのため、接合界面で十分な融合を達成しながら HAZ を最小限に抑えるには、レーザー パラメータ、特に出力と速度を慎重に制御することが不可欠です。
冷却速度
冷却速度、つまり溶融池が凝固する速度は、溶接の最終的な微細構造と機械的特性を決定する重要な要素です。レーザー溶接では、熱影響部が小さく、溶融池が急速に凝固するため、通常、冷却速度が非常に速くなります。冷却速度が速いほど微細構造が細かくなり、溶接の強度が向上する可能性があります。ただし、この急速な冷却によって残留応力も生じ、高炭素鋼などの高硬化性材料では特に、ひび割れや歪みが生じる可能性があります。
冷却速度を遅くすると、割れのリスクは減りますが、より大きな粒子が形成され、溶接全体の強度が低下する可能性があります。冷却速度を管理することは、これらの要素のバランスをとるために不可欠です。溶接後の熱処理(アニーリングなど)などの技術を使用して、残留応力を緩和し、最終的な材料特性を向上させることができます。
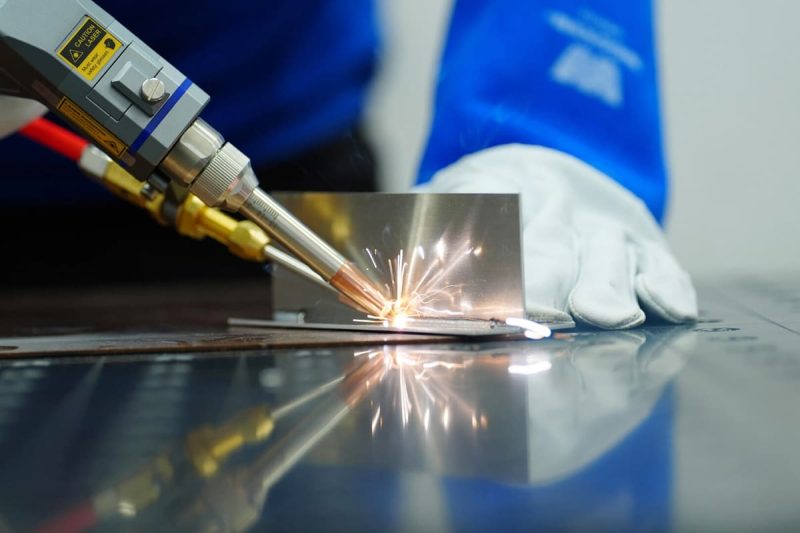
レーザー溶接装置とセットアップ
レーザー溶接の品質は、レーザー溶接装置の種類と構成に大きく影響されます。装置の主要コンポーネントには、レーザー光源、集束レンズ、光学系、溶接ヘッドなどがあります。
レーザー光源タイプ
溶接プロセスで使用されるレーザーの種類は、ビームの品質、出力、焦点など、作業のさまざまな側面に影響します。溶接によく使用されるレーザーの種類には、CO2 レーザー、ファイバー レーザー、ディスク レーザーなどがあります。
- CO2 レーザー: 高出力と多用途性のため、工業溶接で最も広く使用されているレーザーです。CO2 レーザーは厚い材料の溶接に最適で、安定したビーム品質を提供します。
- ファイバーレーザー: これらのレーザーは、ビーム品質と効率性が高いことで知られており、特に薄板金属の溶接に効果的です。ファイバーレーザーは、特に熱伝導率の低い材料では、CO2 レーザーよりも溶接速度が速く、より高い精度を実現できます。
適切なレーザー光源の選択は、材料の種類、厚さ、およびアプリケーションの要件によって異なります。
集束レンズと光学系
希望する溶接サイズと溶け込みを実現するには、レーザー ビームをワークピースに焦点を合わせる必要があります。焦点合わせレンズと光学系の品質と調整は、ビームの精度と溶接品質に重要な役割を果たします。高品質の光学システムにより、レーザー ビームが安定して焦点が合った状態が保たれます。これは、高精度のアプリケーションでは特に重要です。
レンズの焦点距離、絞りサイズ、レンズの位置はすべて、材料の表面全体にエネルギーがどのように分散されるかに影響します。光学系の調整が不十分だと焦点がぼけ、エネルギーの伝達が不安定になり、溶接が弱くなったり欠陥が生じたりする可能性があります。
溶接ヘッドと集光光学系
溶接ヘッドは、レーザー光線を材料に照射する役割を担っています。位置、傾き、動きなどの溶接ヘッドの設定は、溶接の均一性と品質に影響します。溶接ヘッドは、溶接プロセス全体を通じてレーザー光線が接合部に焦点を合わせ続けるように、材料と正確に位置合わせする必要があります。
溶接ヘッドに加えて、ビームを形作り、方向付ける集束光学系も適切に保守および調整する必要があります。これらの光学系の位置ずれや劣化は、ビームの照射に一貫性がなくなり、溶接品質の低下につながる可能性があります。
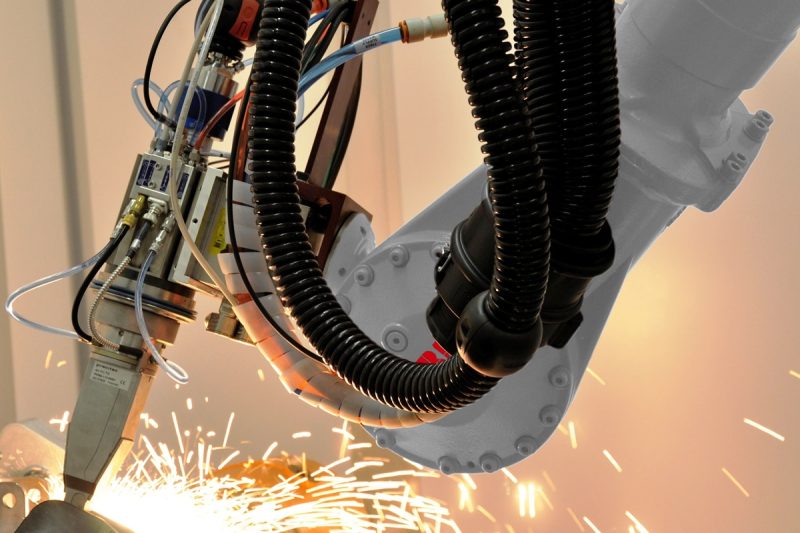
環境条件
レーザー溶接が行われる環境条件は、溶接の品質と一貫性に大きな影響を与える可能性があります。考慮すべき重要な環境要因には、周囲温度と気流が含まれます。
周囲温度
極端な温度は、レーザー溶接プロセスに対する材料の反応に影響を与える可能性があります。たとえば、材料は低温では脆くなり、溶接中に割れる可能性が高くなります。逆に、周囲温度が高いと、材料の過度の歪みや熱膨張が発生し、ジョイントの位置合わせや溶接の一貫性に影響を与える可能性があります。材料が溶接プロセスに予想どおりに反応するには、安定した周囲温度を維持することが重要です。
空気の流れと汚染物質
ほこり、油、湿気、煙などの汚染物質が存在すると、溶接プロセスにさまざまな影響が及ぶ可能性があります。空気中の汚染物質はレーザーエネルギーの一部を吸収し、プロセスの効率を低下させる可能性があります。さらに、材料表面の不純物は、酸化、腐食、その他の欠陥を引き起こし、溶接の品質を損なう可能性があります。
適切な換気、清潔な表面、密閉された溶接室などを通じて溶接環境を制御すると、汚染のリスクを軽減し、より一貫した溶接を実現できます。

溶接後処理
レーザー溶接プロセスが完了したら、機械的特性を改善し、残留応力を緩和し、溶接が必要な仕様を満たしていることを確認するために、溶接後の処理が必要になる場合があります。
アニーリング
アニーリングは、溶接された材料を特定の温度まで加熱し、その後ゆっくりと冷却する熱処理プロセスです。このプロセスは、溶接プロセスの急速加熱および冷却段階で生じた可能性のある残留応力を緩和するために使用されます。アニーリングは、材料の延性を回復し、割れのリスクを軽減するのに役立ちます。
レーザー溶接では、急速な冷却速度を経験する材料は脆化を防ぎ、溶接の靭性を向上させるために焼きなましが必要になる場合があります。正確な焼きなまし温度と時間は、材料の種類と溶接の特定の要件によって異なります。
表面仕上げと洗浄
溶接後、溶接面には除去する必要のある酸化物、スケール、その他の汚染物質が付着している場合があります。溶接面の洗浄と仕上げは、滑らかで欠陥のない外観を確保し、溶接部分の耐腐食性を高めるために不可欠です。
洗浄には、機械研磨、化学酸洗、研磨ブラストなどの技術が用いられることがあります。医療機器や家電製品など、溶接の美観と材料の完全性が最優先される業界では、適切な表面仕上げが特に重要です。
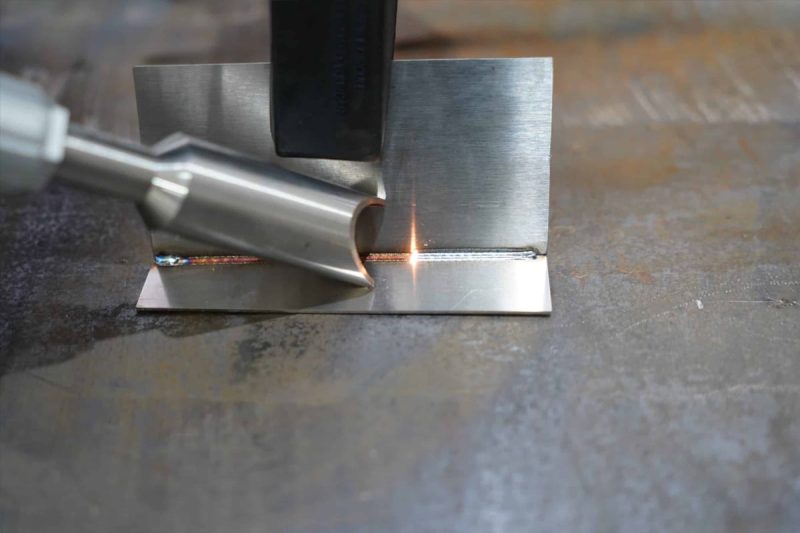
レーザー溶接の課題
レーザー溶接には多くの利点がありますが、独自の課題も伴います。一般的な問題としては、多孔性、亀裂、歪み、溶接品質の不一致などがあります。
気孔率
気孔は、溶接プール内にガスポケットが形成され、溶接部に空隙が生じる場合に発生します。これは、凝固プロセス中に閉じ込められた窒素や酸素などの閉じ込められたガスによって発生することがよくあります。気孔があると溶接部が弱くなり、その性能に影響する可能性があります。適切なシールドガス、溶接パラメータの慎重な制御、溶接前のきれいな表面の確保により、気孔を最小限に抑えることができます。
ひび割れと歪み
レーザー溶接では、特に炭素含有量が多い材料や延性の低い材料では、割れが大きな問題となります。レーザー溶接の急速な冷却速度によって高い残留応力が生じ、特に熱影響部で割れが生じる可能性があります。
歪みは、加熱と冷却の不均一性によっても発生し、材料が反ったり変形したりする原因となります。最適なレーザー パラメータを使用して熱入力を管理し、クランプ技術を使用すると、歪みを軽減できます。
溶接品質の不一致
溶接品質の不一致は、材料特性、レーザー パラメータ、または環境要因の変動によって発生することがあります。レーザー出力や焦点の変動、ジョイントのずれ、シールド ガス フローの変化はすべて、溶接の不一致の原因となります。これらの不一致を最小限に抑えるには、溶接プロセスを厳密に管理し、定期的に機器を調整してすべての溶接の均一性を確保することが不可欠です。
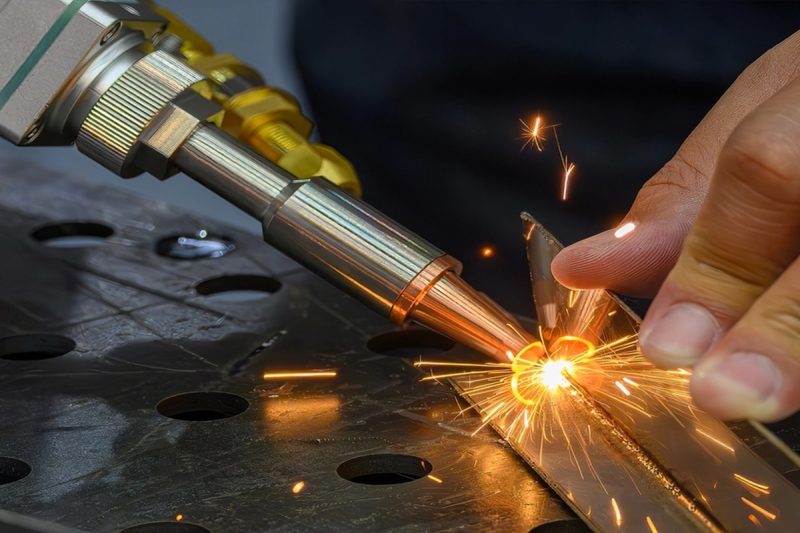
まとめ
レーザー溶接では、材料の溶接性は、材料の組成や厚さからレーザーパラメータや外部環境条件まで、さまざまな要因に依存します。これらの要因を理解して最適化することで、メーカーは強度、耐久性、外観に関する厳しい要件を満たす高品質の溶接を実現できます。溶接プロセス中に多孔性、亀裂、歪みなどの問題が発生する可能性がありますが、溶接パラメータ、装置、溶接後の処理を慎重に制御および選択することで、これらの問題を軽減し、さまざまな材料や用途にわたるレーザー溶接の一貫性と信頼性を向上させることができます。
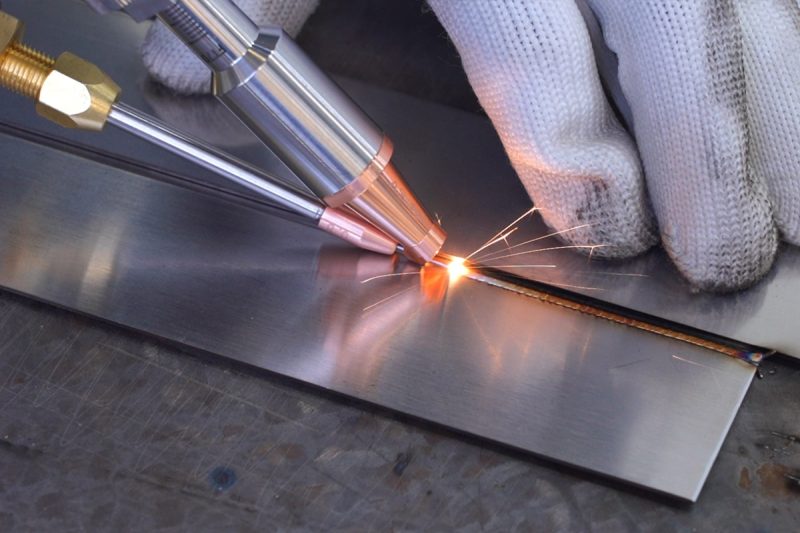
レーザー溶接ソリューションを入手
高品質で信頼性の高い溶接を求める企業のために、AccTek Laser は、多様な産業ニーズを満たすように設計された最先端のレーザー溶接ソリューションを提供しています。レーザー切断、溶接、洗浄、マーキング マシンの専門メーカーである AccTek Laser は、溶接性を最適化するようにカスタマイズされた最先端の機器を提供しています。金属、プラスチック、複合材のいずれを扱う場合でも、当社のレーザー溶接マシンは、最も困難な用途でも精度、速度、効率を提供します。
AccTekレーザーの レーザー溶接機 さまざまな材料や厚さに対応できるように設計されており、レーザー出力、パルス持続時間、焦点、溶接速度の設定をカスタマイズできるため、最高水準の溶接が確実に行えます。当社の専門家チームは、適切な機器の選択、特定のニーズに合わせたシステムの構成、生産プロセス全体を通じて最適なパフォーマンスを確保するための継続的なサポートを提供します。
AccTek Laser を選択すると、高度なテクノロジーと、溶接の品質と生産性の向上に取り組むパートナーにアクセスでき、最終的には毎回完璧で耐久性のある溶接を実現できるようになります。
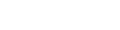
連絡先
- [email protected]
- [email protected]
- +86-19963414011
- No. 3 ゾーン A、Lunzhen 工業地帯、玉城市、山東省。
レーザー ソリューションを入手する