レーザー溶接機
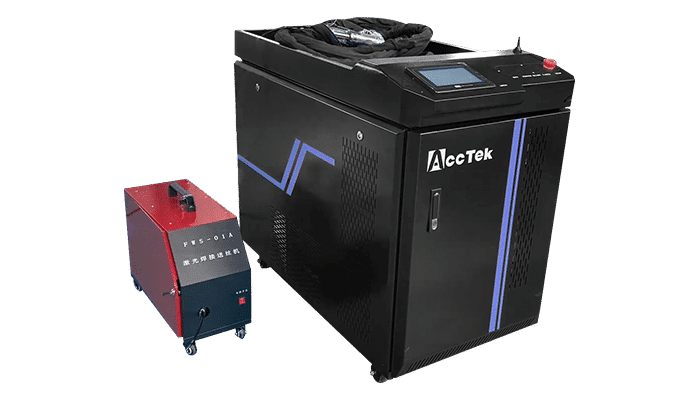
製品ラインナップ
-
ハンドヘルドレーザー溶接機
5段階中5.00の評価$3,900.00 – $8,700.00 オプションを選択 この商品には複数のバリエーションがあります。 オプションは商品ページから選択できます -
ポータブルレーザー溶接機
5段階中4.75の評価$3,800.00 – $8,600.00 オプションを選択 この商品には複数のバリエーションがあります。 オプションは商品ページから選択できます -
ダブルウォブルレーザー溶接機
5段階中4.75の評価$4,400.00 – $9,200.00 オプションを選択 この商品には複数のバリエーションがあります。 オプションは商品ページから選択できます -
自動ワイヤーフィーダーレーザー溶接機
5段階中4.75の評価$3,900.00 – $8,700.00 オプションを選択 この商品には複数のバリエーションがあります。 オプションは商品ページから選択できます -
ポータブル空冷レーザー溶接機
5段階中5.00の評価$4,900.00 – $6,200.00 オプションを選択 この商品には複数のバリエーションがあります。 オプションは商品ページから選択できます -
3 in 1 レーザー溶接切断洗浄機
5段階中4.75の評価$4,200.00 – $9,000.00 オプションを選択 この商品には複数のバリエーションがあります。 オプションは商品ページから選択できます -
レーザー溶接ロボット
5段階中4.75の評価$12,900.00 – $17,700.00 オプションを選択 この商品には複数のバリエーションがあります。 オプションは商品ページから選択できます
レーザー溶接 VS. その他の方法
レーザー溶接とMIG溶接
MIG 溶接は、厚い材料の場合、高速かつコスト効率に優れていますが、発生する熱量が多く、材料の歪みを引き起こし、追加の後処理が必要になる場合があります。一方、レーザー溶接は、熱を最小限に抑えながらより正確な制御が可能で、繊細な材料や薄い材料でも、よりきれいで強力な溶接ができ、仕上げの必要性が少なくなります。
レーザー溶接とTIG溶接
TIG 溶接は、特に薄い材料での溶接品質が高いことで知られています。ただし、処理に時間がかかり、熟練したオペレーターが必要です。それに比べて、レーザー溶接は処理時間が短く、自動化が進み、精度も向上するため、オペレーターのスキルへの依存度が低く、複雑なジョイント設計の大量生産に最適です。
レーザー溶接とスポット溶接
スポット溶接は薄い金属板の接合によく使用されますが、厚い材料の接合には適さず、溶接深さの制御精度も低くなります。レーザー溶接は汎用性が高く、より広範囲の材料と厚さを溶接でき、優れた精度と最小限の熱歪みで、高強度で複雑な溶接に最適です。
AccTekレーザーを選ぶ理由
業界をリードするテクノロジー
当社では最新のレーザー技術を採用し、比類のない精度、速度、効率を機械が実現できるようにしています。AccTek レーザー溶接機は、さまざまな材料に対して熱による歪みを最小限に抑え、溶接強度を最大限に高め、高品質の結果を提供するように作られています。
カスタマイズ可能なソリューション
当社のレーザー溶接機は、カスタマイズ可能な出力設定、レーザーの種類、制御システムを備えており、お客様の特定のニーズに合わせて機器をカスタマイズできます。繊細な部品を扱う場合でも、高負荷のアプリケーションを扱う場合でも、当社はあらゆるプロジェクトに柔軟なソリューションを提供します。
優れた品質
AccTek レーザー マシンは、耐久性と長期的なパフォーマンスを実現するように設計されています。高品質の材料と高度なエンジニアリングで構築された当社のマシンは、厳しい生産環境に耐えるように設計されており、最小限のメンテナンスで信頼性の高い動作を保証します。
精度と精度
AccTek レーザー溶接機は、その優れた精度で知られており、毎回きれいで正確な溶接を保証します。当社の高度な制御システムにより、繊細で複雑な材料でも、厳しい許容差と複雑な溶接形状を簡単に実現できます。
優れた顧客サポート
当社は、最初の相談から設置、アフターサービスまで、優れたカスタマー サポートを提供できることに誇りを持っています。当社の専門家チームが、機械のセットアップ、トレーニング、トラブルシューティングをサポートし、お客様が投資を最大限に活用できるようにします。
競争力のある価格
AccTek Laser では、高性能のレーザー溶接機を競争力のある価格で提供しています。当社は、品質を犠牲にすることなくコスト効率の高いソリューションの必要性を理解しており、当社の機械はあらゆる規模の企業にとって優れた価値を提供します。
よくある質問
レーザー溶接機とは何ですか?
レーザー溶接機は溶接ワイヤを使用しますか?
- 隙間を埋める: 溶接する部品の間に大きな隙間がある場合は、接合部を埋めてより強力な結合を確保するためにフィラーワイヤを追加できます。
- 薄い材料の溶接: 非常に薄い材料や繊細な部品を溶接する場合、溶接ワイヤを使用して制御性を高め、接合部の強度を向上させることができます。
- 特殊合金: 一部の先進材料または合金では、溶接の構造的完全性またはベース材料との適合性を確保するために充填材が必要になる場合があります。
レーザー溶接機の運用コストはいくらですか?
- 電力消費: レーザー溶接機は、レーザー発生器、冷却システム、およびその他のコンポーネントに電力を供給するために電力を必要とします。エネルギー消費量は、レーザー発生器の出力、デューティ サイクル、動作時間などの要因によって異なります。
- レーザー消耗品: レーザー溶接では通常、充填材などの消耗品は必要ありませんが、レーザー光学系、保護窓、一部のタイプのレーザーのガス部品など、レーザー システム内の特定のコンポーネントは定期的な交換が必要になる場合があります。
- メンテナンスと維持: 定期的なメンテナンスと維持により、レーザー溶接機を効率的に稼働させ、耐用年数を確保できます。これには、光学系のクリーニング、摩耗した部品の交換、レーザー ビームの調整、冷却システムの修理などが含まれます。メンテナンス コストは、使用頻度と機械の複雑さに応じて異なります。
- ガス消費量: 一部のレーザー溶接プロセスでは、溶接プールを大気汚染から保護するために、アルゴンやヘリウムなどのシールド ガスの使用が必要になる場合があります。これらのガスのコストは、全体的な運用費用に影響を及ぼす可能性があります。
- オペレーターのトレーニングと人件費: レーザー溶接機を効率的かつ安全に使用するには、オペレーターが適切なトレーニングを受ける必要があります。機械の操作に関連する人件費と、セットアップ、プログラミング、品質管理に必要な追加の労働力を考慮する必要があります。
- 施設コスト: レーザー溶接機を操作するには、適切な換気、安全対策、環境制御を備えた適切な施設が必要です。賃貸料、光熱費、保険などの施設コストが全体の運営費を構成します。
- 消耗品: 用途によっては、フィラーワイヤやフラックスなどの追加の消耗品が必要になる場合があり、運用コストが増加します。
- 減価償却: レーザー溶接機は時間の経過とともに減価償却されるため、減価償却を計算すると、実際の所有コストがわかります。
レーザー溶接機の欠点は何ですか?
- 初期コスト: レーザー溶接機は、従来の溶接装置に比べて初期コストが高くなる傾向があります。初期投資には、機械自体の購入、設置、およびオペレーターのトレーニングが含まれます。
- 材料の制限: レーザー溶接は、鋼、アルミニウム、チタンなどの光吸収特性に優れた金属に最も効果的です。反射率の高い金属や非金属材料などの特定の材料をレーザー溶接で溶接することは、困難であったり、非現実的であったりする場合があります。
- ジョイントのアクセス性: レーザー溶接では溶接エリアへの視線が必要となるため、複雑な形状や閉じた形状の接合には適さない場合があります。アクセスが制限されると、追加の固定や操作を行わずに特定の部品を溶接することが困難になる場合があります。
- 熱感受性: レーザー溶接は局所的に高熱を発生させ、特に薄い材料や熱に敏感な部品が近くにある部品では熱変形を引き起こす可能性があります。この問題を軽減するには、パルス溶接や充填材の使用などの適切な熱管理技術が必要になる場合があります。
- スキルとトレーニングの要件: レーザー溶接機の操作には、複雑なセットアップ、プログラミング、および安全上の考慮事項があるため、専門的なトレーニングと専門知識が必要です。熟練したオペレーターは、高品質の溶接を実現し、機器の効率を最大限に高めます。
- メンテナンスとダウンタイム: レーザー溶接機は、最適なパフォーマンスと信頼性を確保するために定期的なメンテナンスが必要です。メンテナンスや修理のためのダウンタイムは生産スケジュールに影響を与える可能性があり、ワークフローの継続性を維持するために別の溶接方法が必要になる場合があります。
- 安全性の問題: レーザー溶接では高エネルギーのレーザー光線を使用するため、誤った使用をすると作業者に安全上のリスクが生じる可能性があります。事故や怪我のリスクを最小限に抑えるには、安全柵、レーザー安全メガネ、適切なトレーニングなどの保護対策を講じる必要があります。
- 溶接速度: レーザー溶接は、一部の用途では従来の溶接方法よりも高速であることが多いですが、特に厚い材料や大きな部品の場合は、必ずしも最速のオプションとは限りません。厚い材料に深く浸透するには、複数のパスが必要になる場合があり、サイクル時間が長くなります。
レーザー溶接にはガスが必要ですか?
- ガスシールド: 一部のレーザー溶接プロセス、特に金属を扱うプロセスでは、シールドガスを使用して溶接プールを大気汚染から保護することがあります。一般的なシールドガスには、アルゴン、ヘリウム、窒素、またはこれらのガスの混合物があります。シールドガスの選択は、溶接する材料や必要な溶接特性などの要因によって異なります。
- ガスアシスト: プラスチックやセラミックなどの特定の材料のレーザー溶接では、溶接の品質を向上させるためにガスをアシストガスとして使用することがあります。アシストガスは、溶接プロセスの特定の要件に応じて、破片の除去、熱放散の制御、または浸透深度の強化に役立ちます。
- ガス不要オプション: ただし、ガスを必要としないレーザー溶接プロセスもあります。たとえば、特定のプラスチックのレーザー溶接や特殊な金属溶接アプリケーションでは、ガスは不要であるか、プロセスに悪影響を与える可能性があります。
レーザー溶接機はどのようにして最小の熱影響部を作り出すのでしょうか?
- 高エネルギー密度: レーザー溶接は、大量のエネルギーを小さなスポット サイズに集中させるため、溶接ポイントでのエネルギー密度が非常に高くなります。この強力な熱により、溶接ゾーンの材料が急速に加熱され、溶解され、周囲への熱伝達が最小限に抑えられます。
- 相互作用時間が短い: レーザー加熱の持続時間は非常に短く、通常は数ミリ秒程度です。相互作用時間が短いということは、少量の材料のみが強い熱にさらされ、隣接する領域への熱拡散が最小限に抑えられることを意味します。
- 精密制御: レーザー溶接機は、レーザー出力、パルス持続時間、パルス周波数、ビーム焦点などのパラメータを正確に制御できます。オペレーターはこれらのパラメータを調整して溶接ゾーンへのエネルギー供給を最適化し、十分な浸透深さを確保しながら周囲の材料の過熱を最小限に抑えることができます。
- 集束ビーム: レーザー ビームは、レンズやミラーなどの光学部品を使用して、しっかりと集束できます。レーザー ビームを小さなスポット サイズに集束させることで、エネルギーが集中し、ワークピースの奥深くまで浸透しながら、隣接領域への熱の拡散を制限できます。
- 非接触プロセス: レーザー溶接は非接触プロセスです。つまり、熱源 (レーザー ビーム) とワークピースの間に物理的な接触はありません。これにより、ガス メタル アーク溶接 (GMAW) やシールド メタル アーク溶接 (SMAW) などのプロセスで見られるような、直接接触によって生じる熱影響領域を収容するための熱影響部が不要になります。
- 最小限のエネルギー入力: レーザー溶接は、従来の溶接方法と比較して最小限の熱入力で、高度に制御された方法でワークピースにエネルギーを供給します。これにより、材料への全体的な熱の影響が軽減され、熱影響領域が小さくなります。
レーザー溶接は安全ですか?
- 目の保護: レーザー光線によって生成される強烈な光に直接さらされると、網膜損傷や失明などの目の損傷を引き起こす可能性があります。オペレーターおよびレーザー溶接エリアの近くにいる人は、レーザーによって放射される特定の波長を遮断するために、適切な光学濃度の適切なレーザー安全メガネを着用する必要があります。
- 皮膚の保護: レーザー光線に皮膚がさらされると、火傷や組織の損傷を引き起こす可能性があります。皮膚損傷のリスクを最小限に抑えるため、作業者は不燃性素材で作られた長袖の衣服、手袋、エプロンなどの適切な保護服を着用する必要があります。
- 換気と煙の排出: レーザー溶接では、溶接する材料に応じて煙、ガス、蒸気が発生することがあります。空気中の汚染物質を溶接エリアから除去して蓄積を防ぎ、作業者にとって安全な作業環境を確保するために、適切な換気と煙の排出システムを設置する必要があります。
- 火災安全: レーザー溶接は熱を発生し、特に可燃性材料を扱っている場合や可燃性物質を含む環境で作業している場合、火災の原因となる可能性があります。火災事故のリスクを軽減するために、防火壁、消火器、適切なハウスキーピング対策などの火災予防対策を講じる必要があります。
- 電気安全: レーザー溶接機は動作に電気を必要とするため、感電や感電死などの電気的危険を防ぐために予防措置を講じる必要があります。機械は適切に接地し、電気接続に損傷や摩耗の兆候がないか定期的に点検する必要があります。
- トレーニングと監督: オペレーターは、機器の適切な操作、レーザーの危険性の取り扱い、緊急時の対応手順など、レーザーの安全手順に関する包括的なトレーニングを受ける必要があります。訓練を受けた人員による監督により、安全なレーザー溶接手順が常に遵守されます。
- 制御: レーザーの危険性を最小限に抑えるために、エンジニアリング制御、管理制御、および個人用保護具 (PPE) を実装する必要があります。これには、機器の安全インターロック、レーザー領域へのアクセス制限、レーザー放射を封じ込めるための障壁または囲いの使用などが含まれます。
レーザー溶接機にはどのようなメンテナンスが必要ですか?
- 光学部品のクリーニング: レンズやミラーなどのレーザー光学部品は、ビームの品質や効率に影響を与える可能性のあるほこりや汚れ、その他の汚染物質を除去するために定期的にクリーニングする必要があります。光学部品に傷や損傷を与えないように、適切な洗浄液と糸くずの出ない素材を使用して慎重にクリーニングする必要があります。
- ビームの位置合わせをチェックする: ビームの位置合わせを定期的にチェックすることで、レーザー ビームが適切に焦点を合わせられ、ワークピースに向けられていることを確認できます。位置合わせがずれていると、溶接の品質と効率が低下する可能性があります。ずれが検出された場合は、ビームの位置合わせを再度行うために調整が必要になる場合があります。
- 冷却システムのメンテナンス: レーザー溶接機には通常、動作中に発生する熱を放散するための冷却システムが備わっています。ポンプ、フィルター、熱交換器などの冷却コンポーネントを定期的にメンテナンスすることで、過熱を防ぎ、適切な冷却性能を確保できます。
- 消耗部品の検査と交換: レーザー光学系、保護窓、ガス フィルターなど、レーザー システム内の特定のコンポーネントは、時間の経過とともに摩耗し、交換が必要になる場合があります。最適なパフォーマンスを維持するために、定期的に検査を行って摩耗または損傷した部品を特定し、必要に応じて交換する必要があります。
- ガス供給システムの確認: レーザー溶接プロセスでシールドガスや補助ガスを使用する必要がある場合は、ガス供給システムに漏れ、詰まり、その他の問題がないか定期的に確認する必要があります。最適な溶接条件を維持するために、ガスの流量と圧力を必要に応じて調整する必要があります。
- ビーム品質の確認: レーザー出力のビーム品質を監視および評価することで、レーザーシステムの問題を示す可能性のある偏差や異常を検出できます。ビーム品質のチェックは、適切な診断ツールと手順を使用して定期的に実行する必要があります。
- ソフトウェアの更新とキャリブレーション: レーザー溶接機には、溶接パラメータを制御し、パフォーマンスを監視するソフトウェアが搭載されている場合があります。定期的なソフトウェアの更新とキャリブレーション チェックにより、正確な操作と進化する業界標準との互換性が確保されます。
- 安全検査: 安全基準と規制に準拠していることを確認するために、安全検査を定期的に実施する必要があります。これには、事故を防止し、オペレーターを保護するための緊急停止システム、インターロック、安全柵、その他の安全機能のチェックが含まれます。
関連リソース
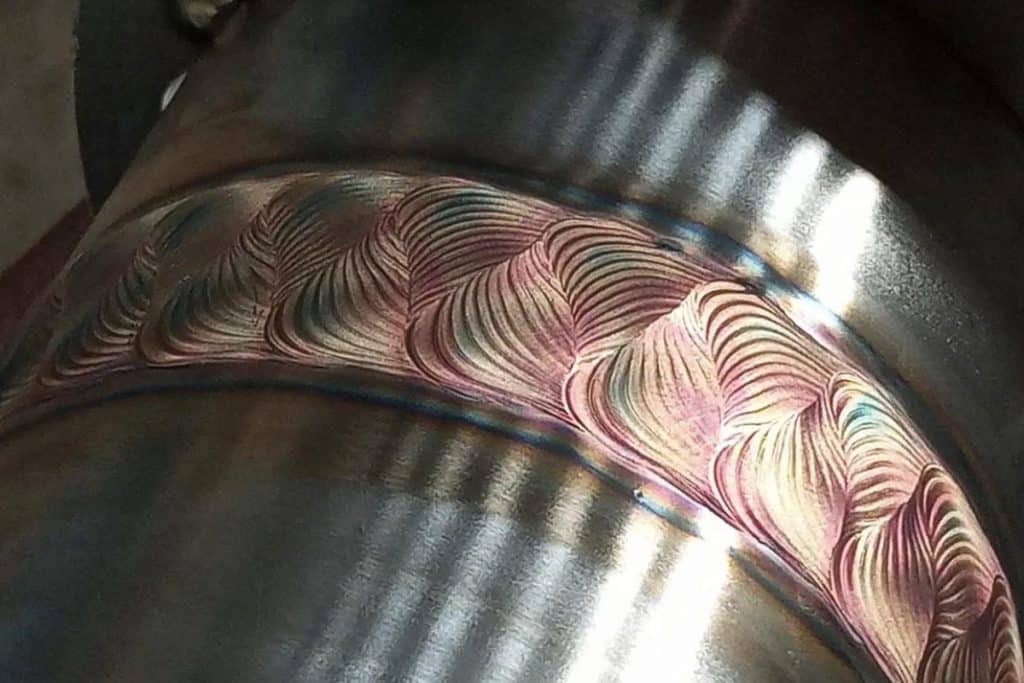
レーザー溶接の歪みと反りを最小限に抑えるにはどうすればよいでしょうか?
この記事では、溶接パラメータ、ジョイント設計、材料の準備、高度な技術など、レーザー溶接の歪みと反りを最小限に抑える実用的な方法について説明します。
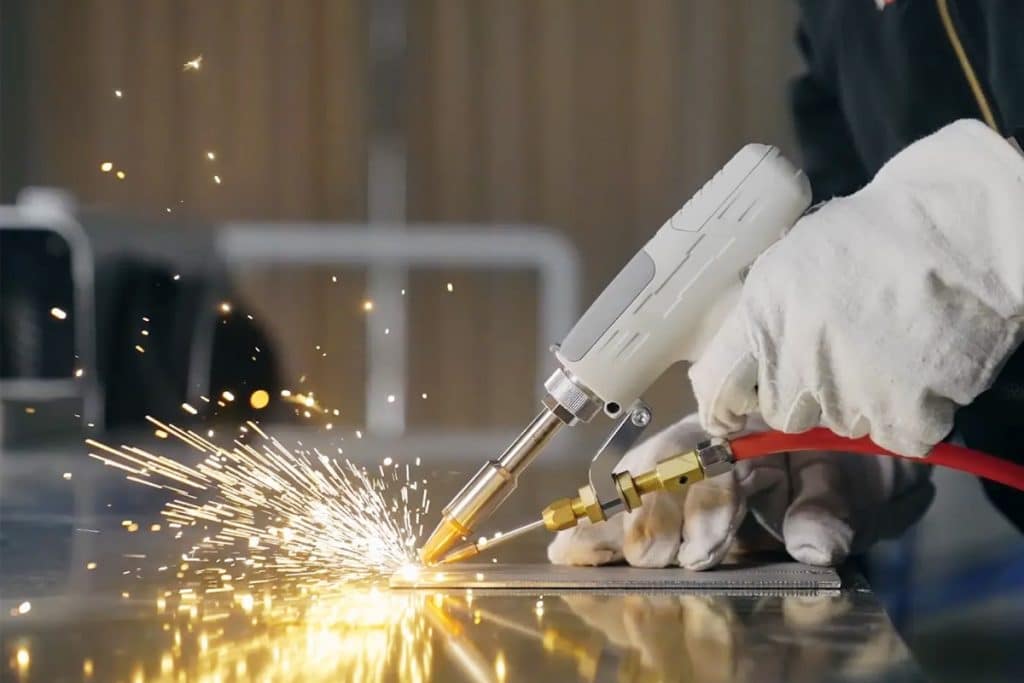
レーザー溶接はどれくらい高温になりますか?
この記事では、レーザー溶接プロセスにおける温度の重要性について、その動作原理、影響要因、温度範囲、さまざまな業界での応用と最適化の方法などを中心に紹介します。
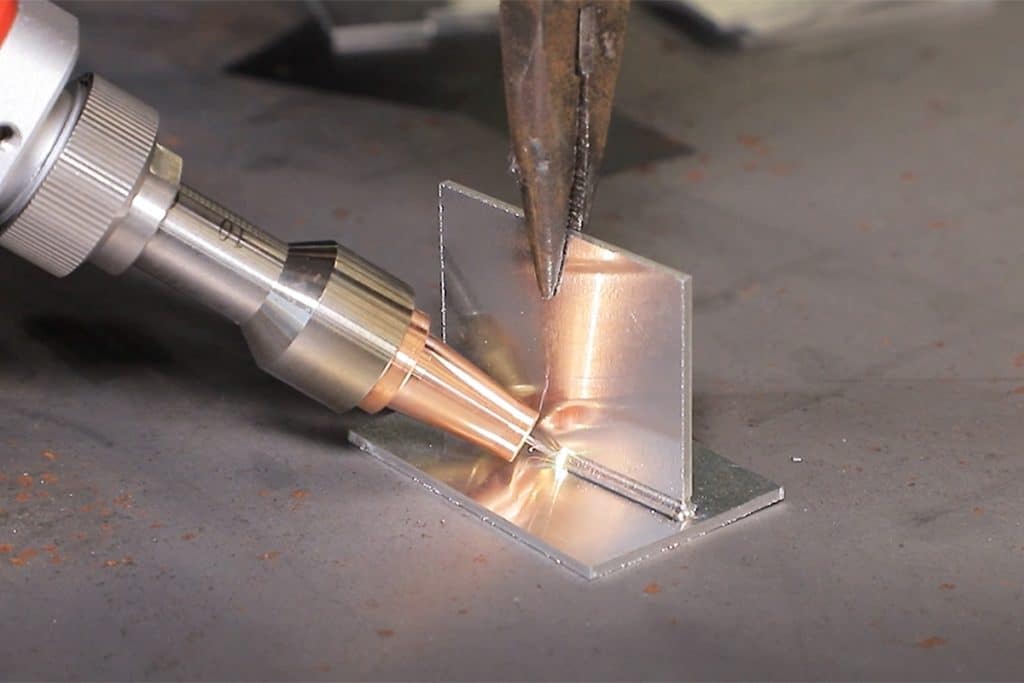
ステンレス鋼のレーザー溶接ガイド
この記事では、ステンレス鋼の産業上の利点と溶接の課題、およびステンレス鋼のレーザー溶接の利点に焦点を当てています。