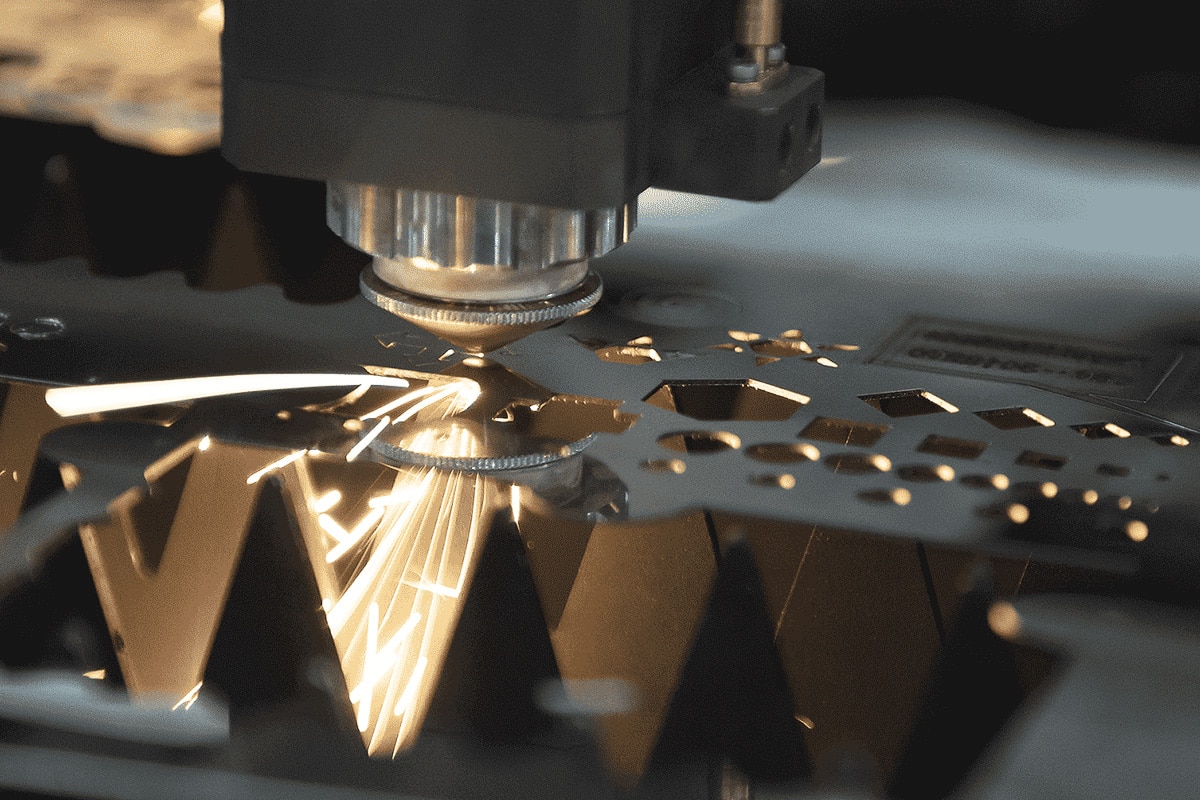
ファイバーレーザー切断機の切断精度に対するオートフォーカスの影響
金属加工産業における重要な設備として、 ファイバーレーザー切断機 様々な製造・加工分野において、切断精度と切断効率は不可欠です。切断精度と切断効率は、ワークの最終品質に影響を与えるだけでなく、生産コストと加工効率にも直接影響します。安定した効率的な切断結果を得るには、装置の焦点調整が不可欠です。従来の手動フォーカス方式は人為的ミスの影響を受けやすく、厚さや種類の異なる材料を加工する際には頻繁な調整が必要となり、生産効率を低下させます。
オートフォーカス技術の導入により、ファイバーレーザー切断機の加工能力は大幅に最適化されました。この技術は、レーザーの焦点位置をリアルタイムで動的に調整し、手動操作なしに材料表面から最適な切断距離を維持します。これにより、切断精度が向上するだけでなく、様々な厚さや材料への適応性も向上し、様々な複雑な加工シナリオにおいて安定した切断品質を維持できます。
目次
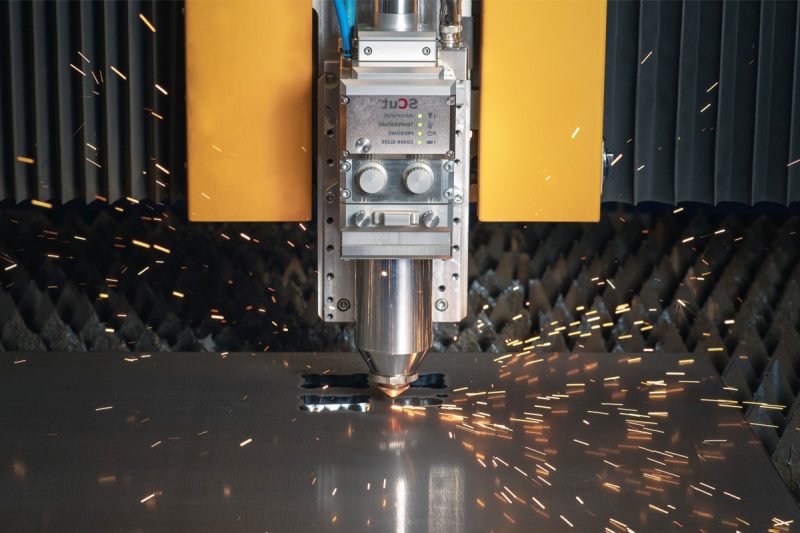
ファイバーレーザー切断におけるオートフォーカスの理解
オートフォーカスの定義と機能
ファイバーレーザー切断において、焦点の精密制御は切断品質と効率に直接影響します。従来の手動フォーカス方式は、時間がかかるだけでなく、人為的ミスによる焦点ずれが発生しやすく、切断精度に影響を与えます。オートフォーカスシステムの登場により、レーザー切断のインテリジェント化レベルは大幅に向上し、材料の厚さや表面状態に応じてレーザー焦点の高さを装置が自動的に調整し、最適な切断条件を確保できるようになりました。
オートフォーカス システムの中核機能は次のとおりです。
- 焦点位置のリアルタイム調整:センサーと制御システムを使用して、材料の表面高さを動的に検出し、焦点位置をリアルタイムで調整することで、レーザービームが常に最適な切断範囲内にあり、高品質の加工を保証します。
- 手動調整エラーの削減: 自動調整により、人的介入による不確実性が排除され、切断精度と一貫性が向上します。これは、大量生産や複雑な処理タスクで特に重要です。
- 異なる材料や厚さの加工効果を最適化: さまざまな金属材料や厚さのばらつきが大きいワークピースを切断する場合、オートフォーカス システムはフォーカスをすばやく調整し、手動調整によるエラーや効率の低下を回避し、機器の適応性と汎用性を向上させます。
インテリジェント製造の発展に伴い、オートフォーカス技術はハイエンドファイバーレーザー切断機の標準機能となりました。その利点は、高速、高精度、多様な加工が求められるアプリケーションにおいて特に顕著です。
オートフォーカスシステムの種類
現在、ファイバーレーザー切断機に広く採用されているオートフォーカスシステムには、主に静電容量式オートフォーカス、非接触式オートフォーカス、そしてインテリジェント制御に基づくオートフォーカスシステムがあります。それぞれのシステムには独自の特徴があり、様々な加工要件に適しています。
静電容量式オートフォーカス
静電容量式オートフォーカスシステムは、ノズルとワーク表面間の静電容量の変化を利用して焦点位置を検出し、レーザーヘッドの高さをリアルタイムで調整します。この技術は電界誘導の原理に基づいており、材料表面の高さの変化に迅速に対応し、加工中に安定した焦点位置を維持することができます。
アドバンテージ:
- 応答速度が速く、特に高速切断アプリケーションに適しており、焦点位置を正確に調整して切断安定性を向上させることができます。
- システム構造が比較的シンプルで、メンテナンスコストが低く、コストパフォーマンスに優れています。
制限:
- セラミックやプラスチックなどの非金属材料などの非導電性材料への適応性が低く、静電容量信号の変化が小さいため、検出感度が低下します。
- 酸化、ほこり、油などの表面汚染の影響を受ける可能性があり、静電容量測定の精度に影響を与え、フォーカス調整エラーを引き起こす可能性があります。
- 極端に薄い材料や厚い材料の制御には一定の制限があり、切断パラメータをさらに最適化する必要があります。
静電容量式オートフォーカス技術は、金属加工、特に大量生産や標準化された加工に適しています。ただし、特殊な材料や過酷な加工環境では、その安定性と適応性をさらに最適化する必要がある場合があります。
非接触オートフォーカス
非接触オートフォーカスは、光学式またはレーザー測距技術を用いて、センサーを通してノズルと材料表面との距離を検出し、焦点位置を動的に調整します。静電容量式フォーカスと比較して、非接触システムは物理的な接触を完全に回避するため、より多くの種類の材料に適しています。
アドバンテージ:
- 物理的な接触を避け、センサーの摩耗を減らし、耐用年数を延ばし、故障率を減らします。
- 非導電性金属、メッキ材料、複合材料など、より多くの材料タイプに適用でき、レーザー切断の応用範囲が拡大します。
- 光学式またはレーザー式の測距技術は、外部汚染の影響を受けにくく、より複雑な環境でも安定して動作し、ワークの表面に油、酸化層、ほこりなどがあっても高い検出精度を維持できます。
- 非接触システムは静電容量フォーカスに比べて検出精度が高く、高精度のマイクロ加工シナリオに特に適しています。
制限:
- システムコストは高くなります。静電容量式システムと比較して、非接触フォーカスシステムはより複雑な光学またはレーザーセンシング技術を必要とするため、コストが高くなります。
- 高精度なキャリブレーションとメンテナンスが必要です。光学式またはレーザー式計測に依存しているため、長期にわたって安定した焦点検出精度を確保するには、センサーを定期的にキャリブレーションする必要があります。
非接触オートフォーカス技術は、マイクロエレクトロニクス製造、精密機器部品の切断など、高精度かつ高要件が求められる処理シナリオに特に適していますが、一般的な産業処理においてはコスト要因により一定の制限を受ける場合があります。
オートフォーカス制御
オートフォーカス制御は、ソフトウェアアルゴリズム、センサーフィードバック、そしてインテリジェント制御システムを組み合わせた包括的なフォーカス技術です。リアルタイムでフォーカスを調整できるだけでなく、CNCシステムと緊密に統合することで、よりインテリジェントなフォーカス最適化を実現し、さまざまな切削要件に適応します。
アドバンテージ:
- 高度なインテリジェント機能により、さまざまな材質や厚さを自動的に識別し、最適な焦点位置を調整して、手動による介入を減らすことができます。
- CNC 制御システムとシームレスに統合して、完全に自動化された切断を実現し、生産効率と処理の一貫性を向上させます。
- アルゴリズムを通じて切断パラメータを最適化し、さまざまな処理環境で最良の切断品質を維持し、エネルギー消費を削減します。
- 適応性が強く、さまざまな金属材料に適しているだけでなく、さまざまな表面状態に合わせて最適化および調整できるため、切断品質とエッジ仕上げが向上します。
制限:
- ソフトウェアとセンサーの安定性に依存します。システムソフトウェアまたはセンサーに異常がある場合、フォーカス制御の精度に影響が出る可能性があります。
- 環境要因に大きく影響されます。例えば、温度や湿度の変化はセンサーの精度に影響を与える可能性があり、様々な環境に合わせてパラメータを最適化する必要があります。
- オペレーターに対する技術的要件は高く、オートフォーカス システムのパフォーマンスを最大限に引き出すには熟練した技術者がパラメータを調整する必要があります。
オートフォーカス制御技術は、ファイバーレーザー切断の将来の発展方向を象徴しており、特にインテリジェント製造とインダストリー4.0の文脈において、その利点はますます明らかになっています。コストが高く、オペレーターに高度なスキルが求められるものの、高精度でインテリジェントな切断能力により、ハイエンド製造分野における幅広い応用の可能性を秘めています。
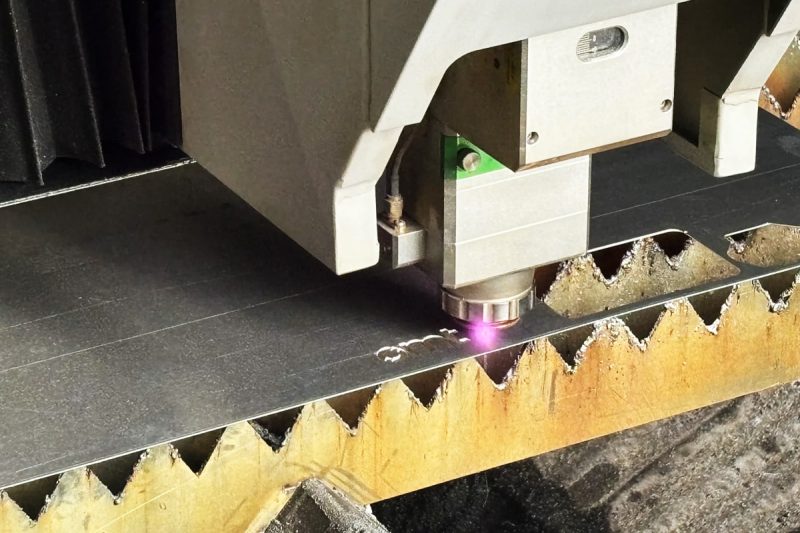
切断精度に影響を与える要因
ファイバーレーザー切断の精度に影響を与える要因には、主に材料特性、ビーム品質、ノズル距離、機械の安定性、ソフトウェア制御などがあります。
材料特性:様々な材料は、レーザー吸収率、熱伝導率、溶融特性によって切断精度に直接影響を及ぼします。例えば、ステンレス鋼はレーザー吸収率が高いため、通常はより滑らかな切断面が得られますが、アルミニウム合金やアルミニウム合金などの反射率の高い材料は、より滑らかな切断面が得られます。 銅 レーザー光を反射し、エネルギー吸収に影響を与え、切断が不安定になる可能性があります。さらに、材料の厚さもレーザー焦点の調整に影響します。厚い材料では、正確な切断を行うために、通常、より高いレーザー出力とより遅い切断速度が必要になります。
ビーム品質:レーザービームのパターンと品質は、スポットのサイズとエネルギー密度を決定し、切断精度に影響を与えます。高品質のビームは通常、焦点が絞られたスポットが小さく、レーザーエネルギーがより集中するため、切断精度が向上し、熱影響部が低減します。ビームパターンが不安定であったり、出力分布が不均一だったりすると、切断面が粗くなったり、スラグ残渣が不均一になったりする可能性があります。
ノズル距離:ノズルとワーク表面との距離は、補助ガスの流れと切断安定性に影響を与えます。ノズル距離が大きすぎると補助ガスの圧力が不足し、スラグ残留量が過剰になる可能性があります。一方、ノズル距離が小さすぎると乱気流が発生し、切断精度に影響を与える可能性があります。そのため、切断工程では、ノズル距離を正確に調整することでガスの流れを最適化し、切断欠陥を低減し、切断面の品質を向上させる必要があります。
機械の安定性:ファイバーレーザー切断機の構造安定性は、切断軌跡の精度に直接影響します。高精度のガイドレール、リードスクリュー、サーボシステムにより、切断工程のスムーズな動作を維持し、振動による誤差を低減できます。機械の剛性が不十分であったり、長期間の運転で部品が緩んでいたりすると、切断偏差が発生し、最終的な加工効果に影響を与える可能性があります。そのため、機械の安定性を定期的に保守・点検することが不可欠です。
ソフトウェア制御:高度なソフトウェア制御システムは、切断経路を最適化し、レーザー出力と速度を調整することで、様々な材料や厚さの加工ニーズに対応します。インテリジェントソフトウェアは、材料特性に基づいて誤差を自動的に補正し、切断の一貫性を向上させます。さらに、リアルタイム監視およびフィードバックシステムにより、パラメータを適時に調整し、切断品質を最適化します。ソフトウェア制御の精度が低い場合、または動作パラメータが適切に設定されていない場合、切断偏差や不要な材料の無駄が発生する可能性があります。
一般的に、高精度のファイバーレーザー切断を実現するには、上記の要素を総合的に考慮し、微調整と最適化された制御を通じて加工品質の安定性と一貫性を確保する必要があります。
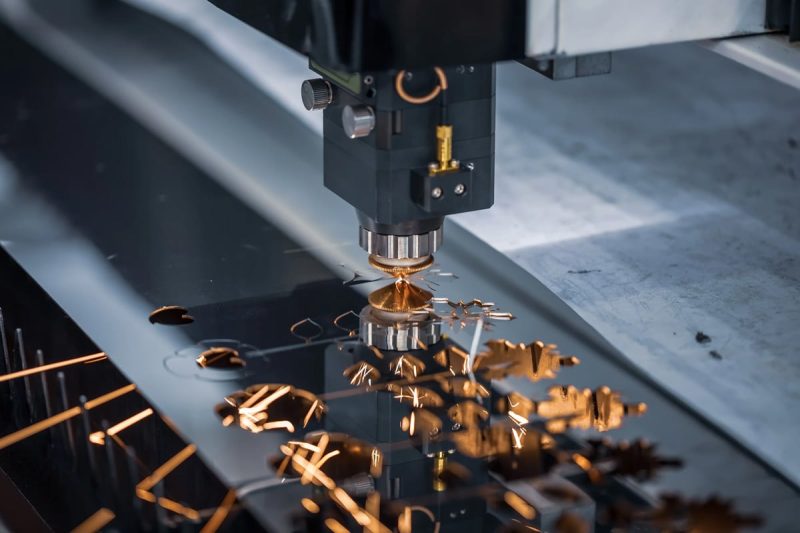
オートフォーカスが切断精度に与える影響
オートフォーカス技術は、ファイバーレーザー切断の精度と処理効率に重要な役割を果たしており、主に以下の側面に反映されます。
精度と安定性:オートフォーカスシステムは、材料の厚さと表面状態に応じて焦点位置をリアルタイムで調整し、レーザーが常に最適な焦点領域に作用することを保証します。これにより、切断精度が向上するだけでなく、量産時における安定した加工効果を維持し、手動調整による誤差を低減し、製品の安定性を向上させます。
準備時間の短縮:従来の手動フォーカス調整では、異なる厚さや材質の切断時にオペレーターが頻繁に調整する必要があり、時間がかかり、ミスが発生しやすいという問題がありました。オートフォーカスシステムは、フォーカス調整を迅速に完了できるため、生産準備時間を大幅に短縮し、特に多品種少量生産の加工シナリオにおいて、全体的な加工効率を向上させます。
材料変更への適応性:材料によってレーザー吸収率や切断条件は異なります。オートフォーカスシステムは、材料特性に応じて焦点を自動的に最適化します。ステンレス鋼からアルミニウム合金、高反射材料まで、様々な金属材料に切断パラメータを適応させることで、常に安定した切断品質を確保し、材料変更に伴うデバッグコストを削減します。
刃先品質への影響:正確なフォーカス制御は熱影響部(HAZ)の低減に役立ち、刃先をより滑らかで垂直に仕上げ、バリやスラグ残留物を低減します。特に高精度加工や、溶接やコーティングが必要なワークピースにおいては、オートフォーカス技術により切断品質を大幅に向上させ、二次加工の必要性を低減できます。
オートフォーカスシステムにより、ファイバーレーザー切断機はより高い加工精度を実現できるだけでなく、生産効率を向上させ、人的介入によるエラーを減らし、切断プロセスをよりインテリジェントかつ効率的にすることができます。
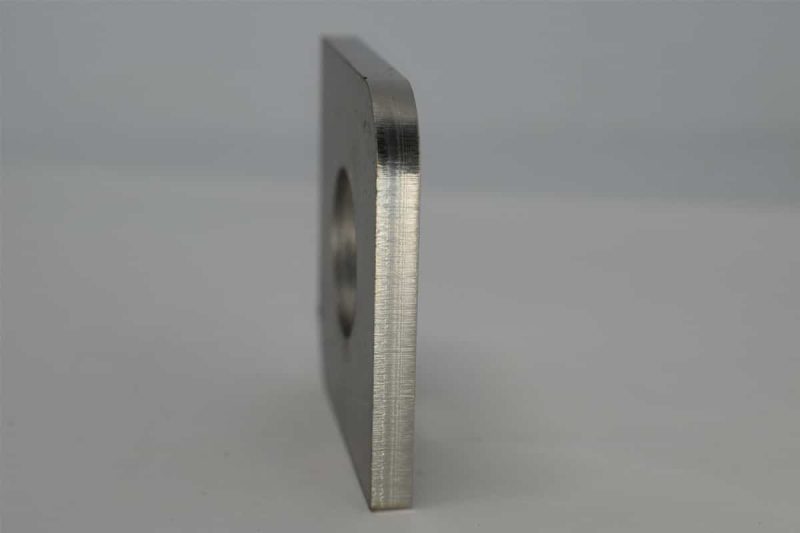
課題と解決策
オートフォーカス技術はファイバーレーザー切断の精度と効率を大幅に向上させましたが、実用化においては依然としていくつかの課題に直面しています。オートフォーカスシステムの安定した動作を確保するには、以下の主要な課題に対する効果的な解決策を講じる必要があります。
キャリブレーションとメンテナンス:オートフォーカスシステムは高精度なセンサーとアクチュエータに依存しています。長期間使用したり、メンテナンスが不十分だったりすると、フォーカスのずれが生じ、切断品質に影響を与える可能性があります。そのため、オートフォーカス装置を定期的にキャリブレーションすることが非常に重要です。企業は、センサー感度のチェック、光学部品のクリーニング、フォーカスパラメータの修正などを含む厳格なメンテナンス計画を策定し、装置が常に最良の動作状態を維持できるようにする必要があります。さらに、ソフトウェアシステムの更新も怠ってはなりません。アルゴリズムと補正戦略を最適化することで、オートフォーカスの精度をさらに向上させることができます。
環境要因:ファイバーレーザー切断機の動作環境も、オートフォーカスシステムの安定性に一定の影響を与えます。例えば、埃、煙、温度、湿度などの要因は、センサーの検出精度に影響を与える可能性があります。切断環境に埃や油分が多いと、レンズやセンサーが汚染され、フォーカス検出に異常が生じる可能性があります。そのため、装置の周囲に適切な排煙・除塵システムを設置し、センサーや光学部品を定期的に清掃することをお勧めします。同時に、一定の温度と湿度の作業環境を維持することで、熱膨張・収縮がレーザー光路やフォーカス精度に与える影響を軽減できます。
オペレーターのトレーニングとスキル:オートフォーカス技術は手動介入を削減しますが、異常発生時にフォーカスパラメータを迅速に調整・最適化するためには、オペレーターが一定の専門知識を有する必要があります。熟練していない操作はフォーカス設定を誤る可能性があり、切断効果に影響を与える可能性があります。そのため、企業はオペレーターに対して体系的なトレーニングを実施し、オートフォーカスシステムの動作原理、一般的な障害の特定とトラブルシューティング、そして様々な材料に応じた適切なフォーカスモードの調整方法を習得させる必要があります。さらに、インテリジェントモニタリングシステムと組み合わせることで、オペレーターはデータフィードバックを通じて切断戦略を最適化し、全体的な生産効率を向上させることができます。
定期的な校正とメンテナンス、作業環境の最適化、オペレーターのスキル向上を通じて、実際のアプリケーションにおけるオートフォーカス技術の課題を効果的に解決し、ファイバーレーザー切断機が常に高精度で高安定性の処理能力を維持できるようにします。
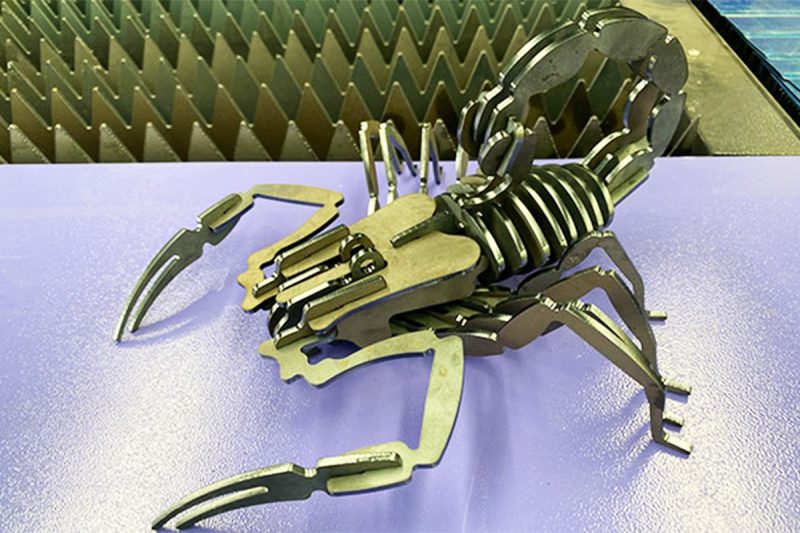
要約する
ファイバーレーザー切断機へのオートフォーカス技術の適用により、切断精度と生産効率が大幅に向上しました。様々なタイプのオートフォーカスシステムにはそれぞれ利点があり、適切な選択と最適化により、切断の一貫性を効果的に向上させ、手作業による調整時間を短縮し、様々な材料や厚さへの適応性を高め、より高品質な加工結果を保証します。この技術の適用により、レーザー切断はよりインテリジェントになり、人的ミスが削減され、生産の安定性と精度が向上します。
しかし、オートフォーカスシステムは、実際の使用において、校正メンテナンス、環境への影響、操作スキル要件など、依然としていくつかの課題に直面しています。センサーの精度、外部環境要因、オペレーターの技術レベルは、システムの安定性と切断効果に影響を与えます。そのため、企業は合理的な設備メンテナンス計画を策定し、作業環境を最適化し、オペレーターのトレーニングを強化することで、オートフォーカスシステムの最高のパフォーマンスを確保し、全体的な加工品質と生産競争力をさらに向上させる必要があります。
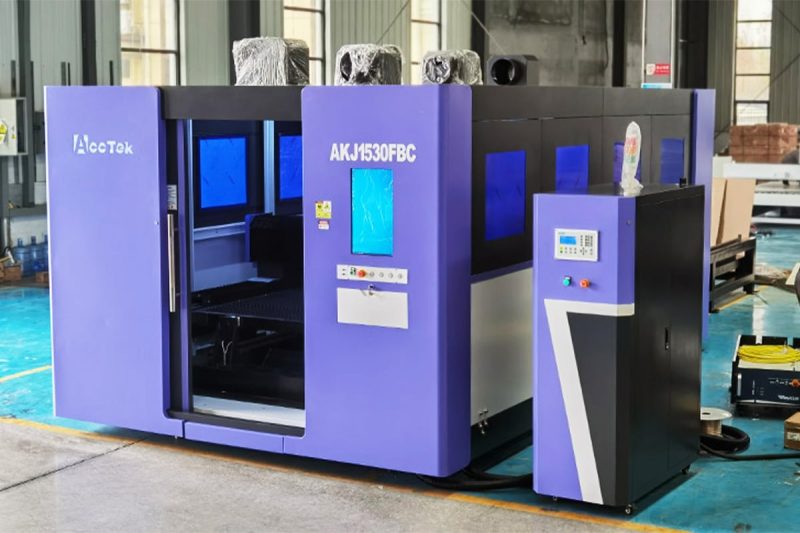
レーザー ソリューションを入手する
AccTek レーザー は、世界中のユーザーに高度なファイバーレーザー切断ソリューションを提供することに尽力しています。当社のオートフォーカス技術は、レーザー焦点を常に最適な位置に維持するためのリアルタイムの精密調整を実現し、切断精度と加工品質を大幅に向上させます。異なる厚さの金属材料を加工する場合でも、複雑な切断要件に対応する場合でも、当社のインテリジェントなオートフォーカスシステムは、生産プロセスの最適化、効率向上、人的ミスの削減に役立ちます。
当社のレーザー切断装置は、板金加工、自動車製造、航空宇宙、電子機器などの業界で幅広く利用されており、優れた安定性と効率的な性能により、世界中のお客様から信頼を得ています。オートフォーカス技術と高精度レーザー切断の応用についてさらに詳しく知りたい場合、または生産ニーズに適したレーザー切断ソリューションをお探しの場合は、お気軽にお問い合わせください。 お問い合わせ! 当社の専門チームが詳細なコンサルティングと技術サポートを提供し、お客様のビジネスをより高いレベルに引き上げるお手伝いをいたします。
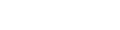
連絡先
- [email protected]
- [email protected]
- +86-19963414011
- No. 3 ゾーン A、Lunzhen 工業地帯、玉城市、山東省。
レーザー ソリューションを入手する