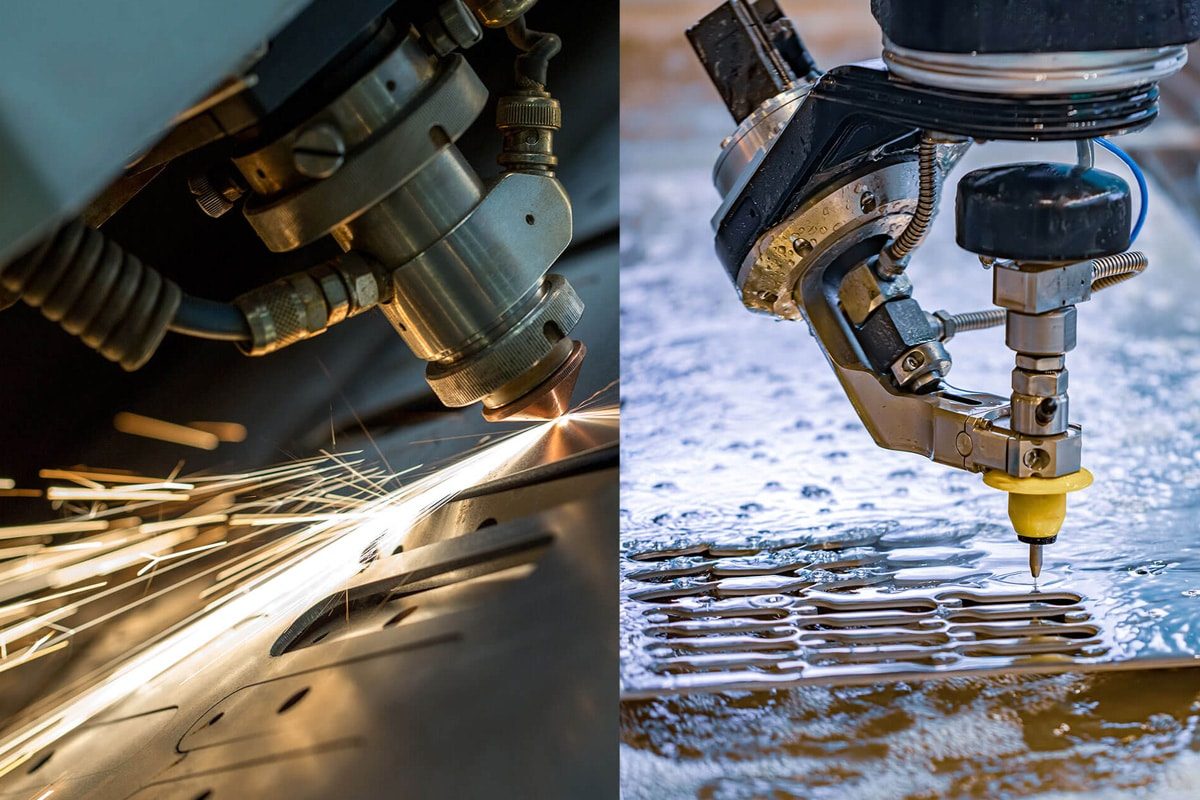
レーザー切断とウォータージェット切断
現代の製造および加工業界では、レーザー切断とウォータージェット切断は、さまざまな業界の複雑な加工ニーズに広く使用されている 2 つの人気の高い高精度切断技術です。両方の技術は、その優れた性能と汎用性により、さまざまな材料を切断するための好ましいソリューションです。各技術には、金属、プラスチック、複合材など、さまざまな材料の切断ニーズを満たすための独自の特性、利点、および制限があります。適切な切断方法を選択すると、処理効率が向上するだけでなく、製品の品質と生産コストにも大きな影響が及ぶ可能性があります。
この記事では、レーザー切断とウォータージェット切断の動作原理を詳細に分析し、切断精度、材料の適応性、運用コスト、環境保護、および適用シナリオの観点から、それぞれの具体的なパフォーマンスを詳しく検討します。これらの重要な要素を比較することで、これら 2 つのテクノロジーの適用シナリオと潜在的な価値をより明確に理解し、実際の生産においてより情報に基づいた選択を行うことができます。
目次
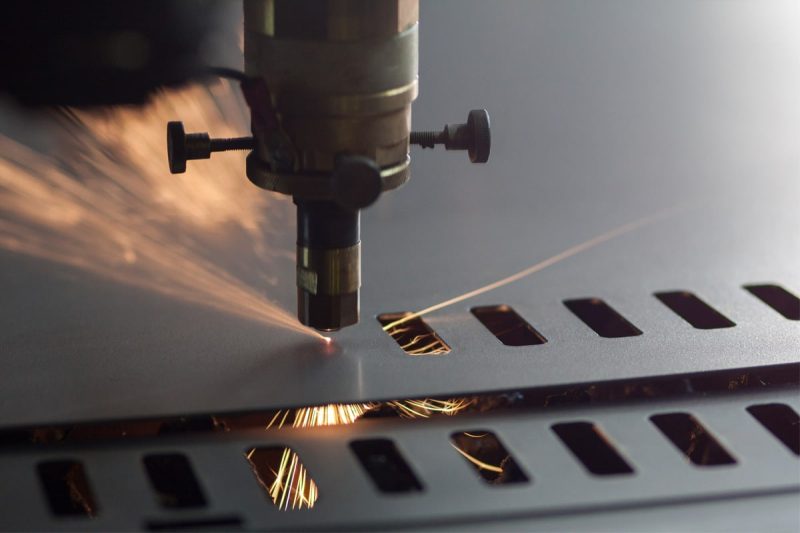
レーザー切断の紹介
レーザー切断は、現代の製造技術において最も先進的で広く使用されている切断プロセスです。高エネルギー密度のレーザービームを使用して材料を高精度に加工し、多くの業界で「見えないナイフ」として知られています。以下では、その動作原理、独自の利点、および制限について説明します。
レーザー切断の原理
レーザー切断はレーザーの高エネルギーと高精度に依存しており、その基本的なプロセスは次の主要なステップに分けられます。
- レーザー生成: レーザー切断の核となるのは、電気エネルギーまたは化学エネルギーを高エネルギービームに変換するレーザー発生器です。一般的なレーザーの種類には、CO2 レーザー発生器、ファイバー レーザー発生器、固体レーザー発生器などがあり、さまざまな種類がさまざまな材料や切断ニーズに適しています。
- ビーム伝送: レーザーは光ファイバーまたは反射鏡を介して切断ヘッドに伝送されます。この伝送プロセスでは、ビーム エネルギーの集中と安定性を確保するために、正確な校正と高品質の光学部品が必要です。
- 集束:レーザーがレンズによって集束された後、エネルギーは材料の表面に高度に集中し、直径が小さく高温のレーザースポットを形成します。この非常に高いエネルギー密度により、材料を局所的に瞬時に溶解または気化させ、切断を実現します。
- 材料の相互作用: 焦点を絞ったレーザービームが材料に接触し、加熱されると材料が急速に溶解、気化、または燃焼する化学反応を起こします。このプロセスにより、切断の深さと経路を正確に制御して、切断品質を確保できます。
- 補助ガス: 補助ガス (酸素、窒素、圧縮空気など) は切断ヘッドから噴射され、レーザービームと連動して機能します。一方では、ガスが溶融物を吹き飛ばして滑らかな切断面を得ることができます。また、酸素が材料と反応して切断効率をさらに向上させることもできます。
レーザー切断の利点
レーザー切断は、その精度と効率性により、さまざまな工業処理ニーズに最適な選択肢です。
- 精度と正確性: レーザー切断は超高精度で有名で、ミクロンレベルの切断許容誤差を実現し、電子機器製造や航空宇宙などの高精度産業の厳しい要件を満たすことができます。レーザーは複雑なパターンや小さな部品の切断にも優れています。
- 切断速度:レーザー切断速度は従来の切断方法に比べて大幅に速く、特に薄板材料の加工においては効率が抜群です。生産サイクルを大幅に短縮し、大量生産環境に特に適しています。
- 汎用性:レーザー切断は金属(スチール、ステンレス、アルミニウム)、非金属(プラスチック、木材、ガラス)など、素材の硬さ、厚さ、形状を問わず、レーザー切断なら簡単に対応できます。
- 材料の無駄が最小限: レーザー ビームの切断スリットは非常に狭く、材料表面への影響が最小限に抑えられるため、材料の無駄が最小限に抑えられます。これにより、生産コストが削減されるだけでなく、環境にも優しくなります。
- 非接触プロセス:レーザー切断は非接触加工プロセスです。切断ヘッドと材料が直接接触しないため、機械的ストレスや切断面の変形が回避され、材料の完全性が保護されます。
- 自動化と柔軟性: レーザー切断技術は CNC システムと互換性があり、高度に自動化された操作を可能にします。大量生産でも小ロットのカスタマイズでも、レーザー切断は柔軟に対応でき、適応性も優れています。
レーザー切断の限界
レーザー切断には多くの利点がありますが、一部のアプリケーション シナリオでは依然として一定の制限があります。
- 熱影響部: レーザー切断は熱処理プロセスであり、高温により材料のエッジが硬化したり変形したりする可能性があります。この問題は薄い材料を切断する場合に特に顕著ですが、レーザー出力や切断速度などのパラメータを最適化することで、熱影響部の影響を効果的に軽減できます。
- 材料の制限: 反射率の高い材料 (銅やアルミニウムなど) の場合、レーザー切断の効率が低下したり、切断が不安定になったりすることがあります。ただし、最新のファイバー レーザー ジェネレーターは、波長とエネルギー制御技術の向上により、この制限を徐々に克服しています。
- 初期コスト: レーザー切断装置の購入および設置コストは、特に中小企業にとっては比較的高額です。しかし、長期的には、運用コストが低く生産性が高いため、この初期投資は通常すぐに回収されます。
- 安全性の問題: レーザーの高エネルギー出力は、目や皮膚への損傷の可能性など、特定の安全上の危険をもたらします。ただし、最新のレーザー切断装置のほとんどには、オペレーターの安全を確保するための厳格な安全ガードが装備されています。
上記の分析から、レーザー切断は、その精度、速度、柔軟性により、工業加工においてかけがえのない重要な技術となっていることがわかります。切断プロセスを選択する場合、レーザー切断は、高効率と精度が求められるシナリオに特に適しています。
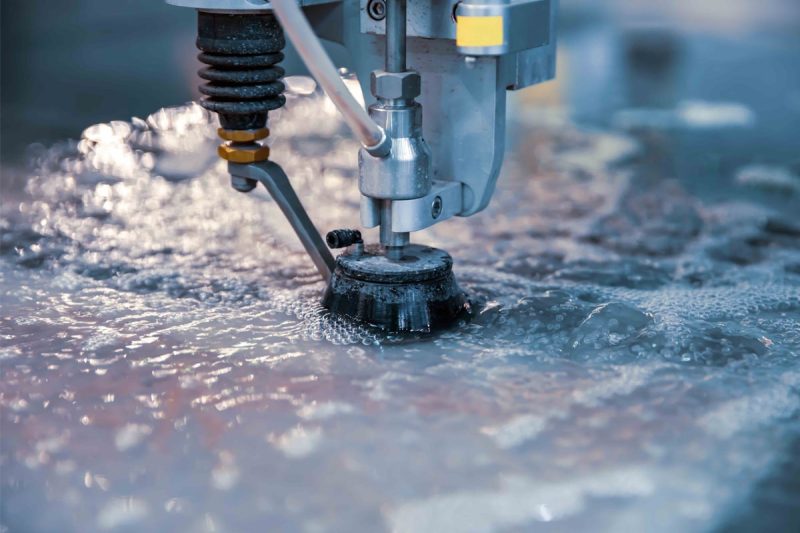
ウォータージェット切断入門
ウォータージェット切断は、高圧水流と研磨剤を組み合わせて材料を分離する冷間切断プロセスです。効率的で環境に優しい加工技術として、ウォータージェット切断は、複数の材料の精密加工と切断を必要とする業界で広く使用されています。以下では、その原理、利点、制限について詳しく紹介します。
ウォータージェット切断の原理
- 水加圧:高圧ポンプはウォータージェット切断の核心設備の一つで、普通の水を3000~4000バール、あるいはそれ以上の圧力に加圧して超高圧水流を形成します。この強い圧力が切断工程の基礎となります。
- 研磨剤の追加: 切断プロセスでは、切断能力を高めるために、通常、研磨剤 (ザクロ砂など) が水流に追加されます。研磨剤の追加により、ウォーター ジェットは金属、ガラス、石などのより硬い材料を切断できるようになります。
- ノズル伝達: 高圧水流がノズルから非常に高速で噴射され、高速切断ジェットを形成します。これらのノズルは、耐久性と安定性を確保するために、耐摩耗性材料 (タングステンカーバイドやダイヤモンドなど) で作られています。
- 材料の相互作用:高速水流と研磨剤が共同で材料の表面に衝突し、水流の運動エネルギーと研磨剤の研削作用により材料が素早く除去され、切断が完了します。
- CNC 制御: CNC システムと組み合わせたウォーター ジェット切断により、切断経路と速度を正確に制御できるため、曲線、特殊形状のパターン、高精度部品の加工など、複雑な切断ニーズに適応できます。
ウォータージェット切断の利点
ウォータージェット切断は、その独自のプロセス特性により、多くのアプリケーションシナリオで優れたパフォーマンスを発揮します。
- 冷間切断プロセス: レーザー切断やプラズマ切断とは異なり、ウォータージェット切断では高温が発生しないため、材料に熱影響部がありません。切断によって材料の物理的特性 (硬度や靭性など) が変化することはないため、熱に敏感な材料の加工に非常に適しています。
- 汎用性: ウォータージェット切断は、金属 (鋼鉄、アルミニウムなど)、非金属 (ガラス、石、セラミックなど)、複合材料 (炭素繊維など) など、ほぼすべての材料に適しています。柔らかい材料でも硬い材料でも、ウォータージェットで切断できます。
- 厚さの対応能力: ウォータージェット切断の厚さの対応能力は印象的です。30 cm を超える厚さの材料を切断することができ、特に極厚材料の加工においては他の切断プロセスとは比べものにならないほどです。
- 環境上の利点:ウォータージェット切断は主に水と天然研磨剤を媒体として使用し、有害なガスや化学廃棄物を生成せず、環境に優しい処理方法です。また、処理後の廃水をリサイクルできるため、環境への影響がさらに軽減されます。
- エッジ品質: ウォータージェット切断の切断面は滑らかでバリがなく、通常は追加の後処理は必要ありません。これにより、生産効率が向上し、生産コストが削減されます。
- 非接触プロセス:ウォータージェット切断は、材料に機械的ストレスを与えない非接触加工方法であるため、材料の変形や機械的損傷を回避し、切断精度と品質を保証します。
ウォータージェット切断の限界
ウォータージェット切断には多くの利点がありますが、特定の条件下では一定の制限があります。
- 速度が遅い: ウォータージェット切断の切断速度は、特に薄い材料を加工する場合、レーザー切断よりも遅くなります。この違いは特に顕著です。したがって、高効率生産が求められるシナリオでは、ウォータージェット切断は最適な選択肢ではない可能性があります。
- 研磨材コスト: 研磨材 (ガーネットなど) の消費は、ウォータージェット切断における大きな運用コストの 1 つです。特に硬い材料を切断する場合、研磨材の使用量が大幅に増加し、総処理コストが増加します。
- 材料処理: 高圧水切断中に発生する廃水には研磨剤や切断屑が含まれることが多く、排出またはリサイクルする前に特別な処理が必要です。このプロセスにより、設備コストと運用コストが増加します。
- 精度: レーザー切断と比較すると、ウォータージェット切断の精度はわずかに低くなります。特に複雑なパターンや小さな部品を加工する場合、レーザー切断の精度を達成するのは難しい場合があります。しかし、ほとんどの日常的な加工ニーズに対しては、ウォータージェットの精度で十分です。
ウォータージェット切断は、環境保護、冷間切断、汎用性により、工業加工において重要な位置を占めています。特に厚い材料や熱に弱い材料を切断する必要がある場合、ウォータージェット切断はかけがえのない技術選択肢となります。切断パラメータと材料処理方法を最適化することで、ウォータージェット切断は効率と適用性をさらに向上させ、現代の製造業にさらなる可能性を提供します。
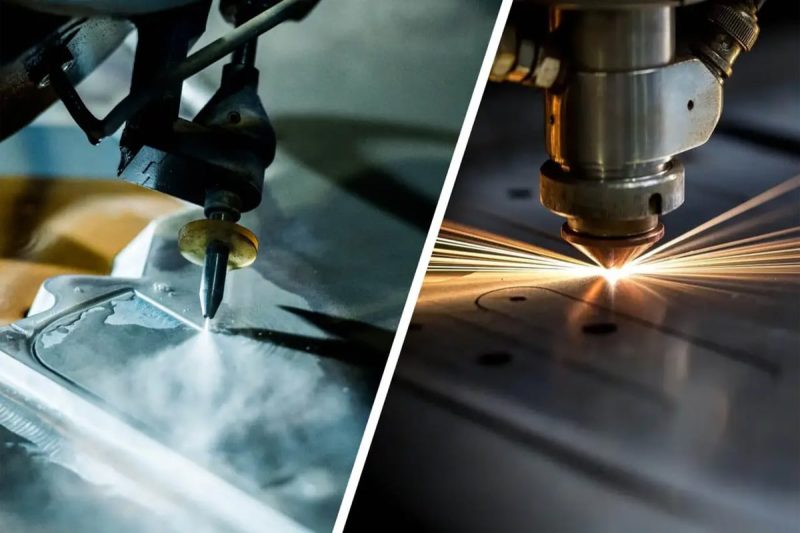
比較解析
このセクションでは、精度、切断速度、材料の汎用性、コスト、環境への影響、エッジ品質など、いくつかの重要な側面におけるレーザー切断とウォータージェット切断の違いについて詳しく説明します。
精度と正確性: レーザー切断は高精度で知られており、航空宇宙、電子機器製造、宝石加工など、精密加工が必要な分野に特に適しています。切断精度はミクロンレベルに達するため、複雑なパターンや詳細なデザインを簡単に完成できます。この機能により、高精度と再現性が求められる用途で優位に立っています。ウォータージェット切断も高精度ですが、切断ジェットの物理的特性により、素晴らしいディテールや複雑なパターンを加工する場合、レーザー切断よりも効果がわずかに劣ります。したがって、より高い精度が求められる作業にはレーザー切断の方が適しています。
切断速度と効率:レーザー切断の速度は、薄い材料や中程度の厚さの材料を切断する際に大きな利点があります。その効率的な切断能力は、特に大量生産において生産効率を大幅に向上させることができます。比較すると、ウォータージェット切断は、冷間切断プロセスと、特に薄い材料を切断する場合に研磨剤を追加する必要があるため、速度が遅くなります。ただし、ウォータージェットの切断能力は、非常に厚い材料を処理する場合に適していますが、これは特定のシナリオにのみ適しています。ほとんどの産業用途では、レーザー切断の方が効率的です。
材料の多様性: ウォータージェット切断は、材料の適応性において大きな利点があり、反射率の高い金属、ガラス、セラミック、複合材など、ほぼすべての種類の材料を切断できます。これにより、非常に用途の広い切断ツールになります。ただし、レーザー切断も材料の多様性に優れており、金属 (鋼、ステンレス鋼、アルミニウムなど) や非金属 (プラスチック、木材、繊維など) を簡単に切断できます。レーザー切断では、反射率の高い材料 (銅やアルミニウムなど) を処理する際に追加の調整が必要ですが、最新のレーザー技術 (ファイバー レーザー ジェネレーターなど) の開発により、これらの材料の切断効率と品質が大幅に向上しました。全体として、レーザー切断は、ほとんどの金属および一般的な材料の加工ニーズに対して、より効率的で経済的な選択肢です。
コスト:レーザー切断設備、特に高出力の工業用レーザー発生器への初期投資は高くなりますが、処理能力が速く、運用コスト(エネルギー消費やメンテナンス費用など)が低いため、長期的に使用すると経済的です。また、レーザー切断は自動化の度合いが高く、CNCシステムとの互換性が高いため、人件費をさらに削減できます。比較すると、ウォータージェット切断設備の初期投資はわずかに低くなりますが、研磨材のコストが高くなります。特に大規模生産では、研磨材の継続的な消費により運用費用が大幅に増加します。したがって、全体として、レーザー切断は長期大量生産を必要とする企業に適しています。
環境への影響:レーザー切断はある程度の熱を発生し、追加の排気処理装置が必要になる場合がありますが、現代の産業設備には通常、熱の影響と有害ガスの排出を最小限に抑えるための完全な濾過システムが装備されています。対照的に、ウォータージェット切断は冷間切断プロセスであるため、熱を発生せず、材料の物理的特性に影響を与えないため、環境性能の面でより多くの利点があります。ただし、ウォータージェット切断中に生成される廃水と研磨残留物は特別な処理が必要であり、そうしないと環境汚染を引き起こす可能性があります。このため、レーザー切断は現代の産業グリーン製造、特に環境保護とクリーン生産に重点を置く業界でより顕著になっています。
エッジ品質:レーザー切断とウォータージェット切断はどちらも切断エッジ品質に優れていますが、レーザー切断はビームの焦点が非常に細かく、切断軌道を高度に制御できるため、非常に滑らかなエッジを実現できます。これは、高い美観が求められる精密部品や加工要件に適しています。ウォータージェット切断には熱影響部がないため、切断エッジは比較的滑らかで、追加の加工は必要ありません。ただし、高速と高精度という2つの要件の下では、レーザー切断の方が、特に中薄材料や高精度部品の加工において優れた性能を発揮します。
熱の影響:レーザー切断中に発生する高温により、切断エッジに熱影響部(HAZ)が形成され、材料エッジの硬化や変形を引き起こす可能性があります。現代のレーザー機器は、切断パラメータ(電力、速度、ガス流量など)を最適化することでこの影響を大幅に軽減し、ほとんどの材料の処理に熱の影響がほとんどないようにすることができます。ウォータージェット切断には熱の影響がまったくないため、ガラス、セラミック、複合材などの熱に敏感な材料を処理する場合にさらに有利になります。ただし、ほとんどの金属材料や工業用途では、レーザー切断の効率と精度の方が適しています。
環境と安全に関する考慮事項:レーザー切断ではレーザー放射の安全性に特別な注意が必要ですが、現代のレーザー機器には通常、操作の安全性を確保するための包括的な安全保護対策 (保護カバーや放射線遮蔽など) が装備されています。一方、ウォーター ジェット切断では、廃水と研磨残留物を適切に処理する必要があります。そうしないと、環境汚染を引き起こす可能性があります。現代の製造業では環境保護への関心が高まっているため、この機能によりウォーター ジェット技術の適用が制限される可能性があります。
レーザー切断とウォータージェット切断を総合的に比較すると、レーザー切断は精度、切断速度、効率の面で明らかな利点があり、高精度の要件と大量生産のシナリオに特に適していることがわかります。ウォータージェット切断は複雑な材料を処理し、熱の影響を回避するという独自の利点がありますが、レーザー切断は高速、効率的、費用対効果が高いため、現代の製造業で広く使用されています。適切な切断技術の選択は、特定のアプリケーション要件と材料特性に基づく必要があります。レーザー切断は、精度と効率を追求する多くの業界にとって間違いなく好ましいソリューションです。
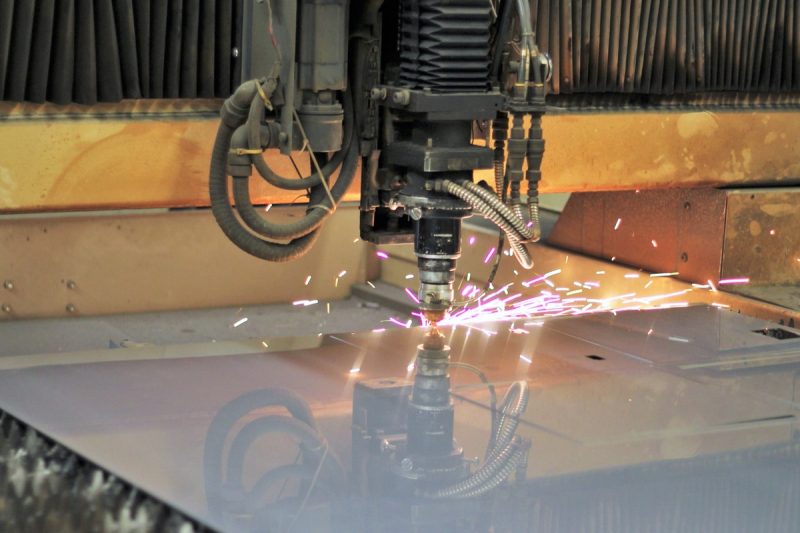
要約する
レーザー切断とウォータージェット切断はそれぞれ独自の利点と制限があり、さまざまな産業ニーズに適しています。切断技術を選択するときは、特定の処理要件に基づいて判断することが重要です。特に薄い材料を切断する場合に高精度と高速切断を求める場合、レーザー切断は間違いなく最も効率的な選択です。レーザー切断は極めて高い精度を提供するだけでなく、生産効率を向上させ、材料の無駄を減らします。
一方、より厚い材料を切断する必要がある場合、または材料の物理的特性を保護するために熱の影響を回避する必要がある場合は、ウォーター ジェット切断がより適切なソリューションです。ウォーター ジェット切断は、より幅広い材料に適しており、冷間切断特性により、熱に敏感な材料への損傷を回避できます。
AccTek レーザー は、さまざまな業界の生産ニーズを満たす優れた性能と信頼性を備えた、先進的でコスト効率の高いレーザー切断機器を顧客に提供することに尽力しています。レーザー切断を選択すると、生産効率が向上するだけでなく、より洗練された処理結果を実現できます。機器に関する詳細情報や専門的なアドバイスについては、お気軽にお問い合わせください。オーダーメイドのソリューションを提供します。
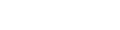
連絡先
- [email protected]
- [email protected]
- +86-19963414011
- No. 3 ゾーン A、Lunzhen 工業地帯、玉城市、山東省。
レーザー ソリューションを入手する