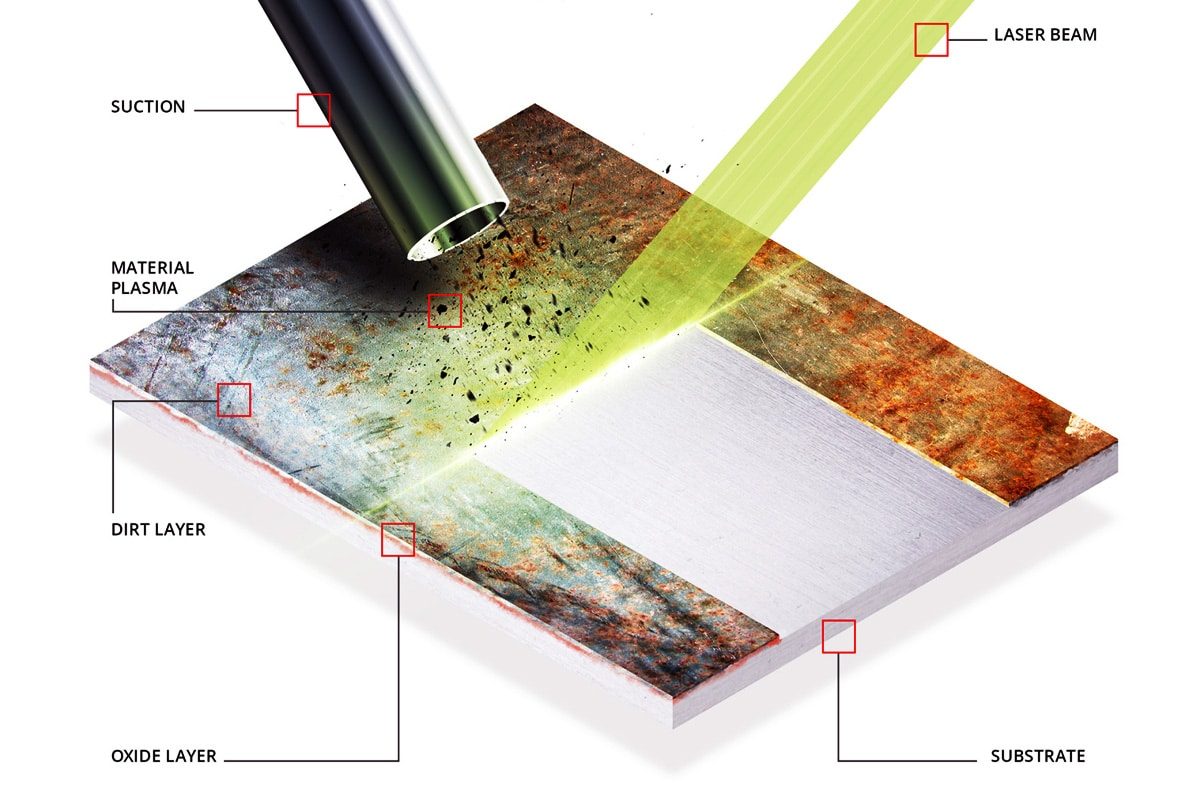
レーザー洗浄後の表面評価に関する総合ガイド
レーザー洗浄技術は、その精度、選択性、環境への配慮、そして非接触プロセスという特長から、多くの業界で広く利用されています。金属加工、自動車製造、航空宇宙、文化遺産の修復など、あらゆる分野で活用されています。 レーザー洗浄機 基材に損傷を与えることなく汚染物質を除去できます。しかし、洗浄を完了するだけでは不十分です。表面の清浄度をどのように評価するかが非常に重要です。これは最終製品の品質に影響を与えるだけでなく、コンプライアンスと長期的な性能にも影響します。
目次
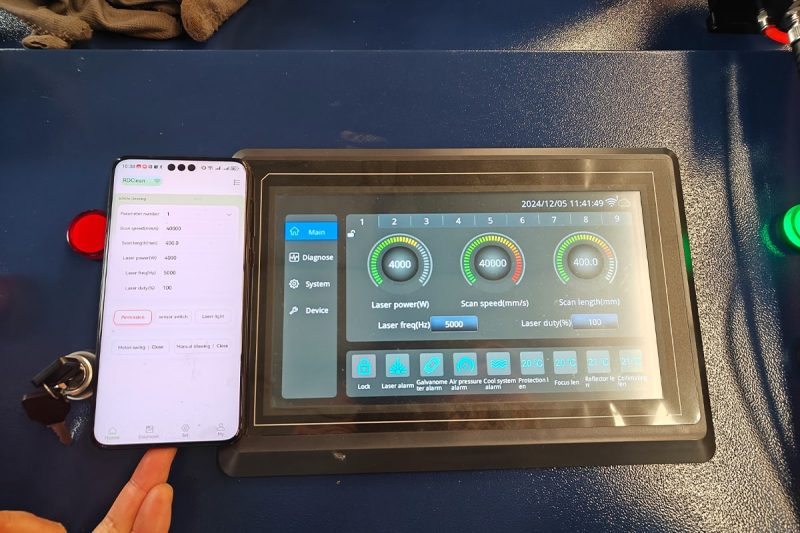
レーザー洗浄について学ぶ
レーザー洗浄は、効率的で精密、かつ環境に優しい表面処理技術であり、金属の錆除去、酸化皮膜除去、コーティング剥離、溶接前処理など、産業用途で広く利用されています。従来の化学洗浄や機械研磨と比較して、レーザー洗浄は基板に損傷を与えることなく汚染物質を除去できるため、プロセスの安定性と製品品質が向上します。以下は、レーザー洗浄の4つの主要な利点です。
精度:レーザー洗浄は、高エネルギーレーザービームを材料表面に集束させ、汚染された領域のみに作用させることで、ミクロンレベルの精密洗浄を実現します。この精密な制御により、汚れ、錆、コーティングを効果的に除去し、従来の洗浄方法によって引き起こされる可能性のある材料の摩耗、変形、化学腐食を回避できます。レーザー洗浄の精度は、表面品質に対する要求が極めて高い航空宇宙、精密電子機器、金型製造などの業界にとって特に重要です。
選択性:化学溶剤洗浄やサンドブラスト洗浄とは異なり、レーザー洗浄は、様々な材質、汚染物質の種類、用途要件に応じてパラメータを正確に調整することで、選択性の高い洗浄を実現します。例えば、コーティング除去プロセスでは、レーザーは基材に影響を与えることなく表面コーティングのみを除去できます。また、文化財修復分野では、レーザーは文化財の本来の素材を保護しながら汚染物質を除去できます。この選択性により、洗浄プロセスの制御性が大幅に向上し、不要な損失を削減できます。
環境保護:従来の洗浄方法は、通常、化学溶剤や研磨材を使用しており、有害な廃液、有毒ガス、粉塵汚染が発生し、環境や作業者の健康を脅かす可能性があります。レーザー洗浄は、レーザーエネルギーのみを用いて汚染物質を気化または分解する、純粋に物理的なプロセスです。化学試薬の使用を必要とせず、二次汚染も発生しません。現代産業の環境保護と持続可能な開発の要件を完全に満たしています。そのため、レーザー洗浄は、自動車製造、医療機器、食品加工機器など、清潔さと環境保護基準に対する厳しい要件を持つ業界で広く利用されています。
非接触プロセス:レーザー洗浄のもう一つの注目すべき特徴は非接触動作です。つまり、洗浄プロセス中に基板に直接接触する必要がないため、摩擦、圧力、機械的損傷による材料の摩耗を回避できます。この利点は、精密機器、マイクロエレクトロニクス部品、半導体チップ、精密金型などの壊れやすい材料の洗浄に特に適しています。さらに、非接触洗浄は自動化にも対応しており、ロボット、CNCシステム、組立ライン操作と組み合わせることで、効率的で安定した産業用洗浄プロセスを実現できます。
レーザー洗浄は、その精度、選択性、環境への配慮、そして非接触プロセスという利点から、現代の産業洗浄分野における主流技術の一つとなりつつあります。従来の洗浄方法と比較して、レーザー洗浄は洗浄品質の向上だけでなく、環境汚染の低減、メンテナンスコストの削減にもつながり、様々な複雑な応用シナリオにも適応します。技術の継続的な進歩に伴い、レーザー洗浄はより多くの業界でその優位性を発揮し、企業により効率的で持続可能な洗浄ソリューションを提供するでしょう。
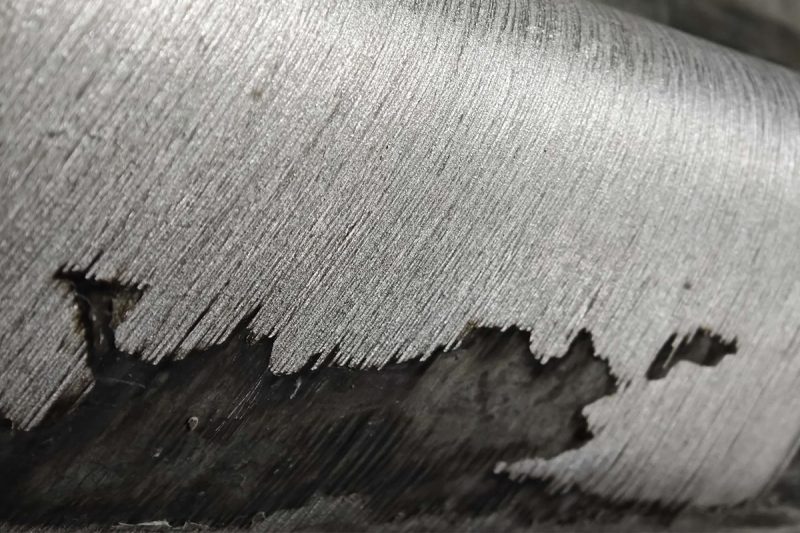
清潔さの評価を理解する
レーザー洗浄は、効率的な表面処理技術として、金属製造、電子産業、自動車修復、航空宇宙、文化遺産の修復など、多くの分野で広く利用されています。しかし、洗浄効果の測定は目視観察だけに頼るのではなく、体系的な清浄度評価が必要です。このプロセスには、汚染物質の特定、表面感度、規制遵守、性能検証など、複数の側面が含まれており、洗浄された表面が業界標準およびアプリケーション要件を満たしていることを確認します。
汚染物質の特定:清浄度評価における最初のステップは、汚染物質の種類と分布を正確に特定することです。様々な材料の表面に存在する汚染物質には、酸化物層、錆、グリース、コーティング残留物、ほこり、化学残留物などがあり、それぞれの汚染物質は洗浄プロセスへの適応性が異なります。
- 有機汚染物質(油、樹脂、潤滑剤など)を除去するには、通常、高エネルギー短パルスレーザー蒸発が必要です。
- 無機汚染物質(酸化物、錆、金属残留物など)は、レーザーの高温蒸発に依存します。
- 粒子汚染(ほこりや微粒子など)の場合、二次汚染を防ぐために真空吸着や気流補助が必要になることがあります。
汚染物質を正確に特定することで、洗浄パラメータを最適化できるだけでなく、洗浄後の残留物が製品の品質に影響を与えるのを防ぐための清浄度評価の精度も確保できます。
表面感受性:材料によって洗浄プロセスに対する感受性は異なります。レーザー洗浄では、基板に損傷を与えることなく汚染物質を効果的に除去するために、材料の特性に応じて出力、波長、走査速度などのパラメータを調整する必要があります。
- 反射率の高い材料(アルミニウムや銅など)はレーザー吸収率が低いため、特定の波長または高いパルスエネルギーを持つレーザー発生器を使用する必要があります。
- 脆い材料(セラミックやガラスなど)は熱衝撃により割れる場合があり、熱影響部を減らすために低出力の短パルスレーザーを使用する必要があります。
- 精密部品(半導体や電子回路など)には、敏感な回路や絶縁層へのレーザーによる損傷を避けながら、極めて高い清浄度基準が必要です。
清浄度評価において重要な点は、洗浄後の材料表面が元の物理的・化学的特性を維持しているかどうかを確認することです。例えば、金属表面には洗浄後の微小亀裂や過度の表面粗さがあってはなりません。そうでないと、その後のコーティング、溶接、組み立てに影響を及ぼす可能性があります。
規制遵守:業界によって表面清浄度に関する厳格な基準や規制が定められています。製品が品質検査にスムーズに合格するためには、清浄度評価は関連する業界仕様および品質管理システムに準拠する必要があります。
- 航空宇宙: NASA および FAA の規定により、宇宙船コンポーネントの表面には、接着や腐食に影響を及ぼす可能性のある汚染物質が残ってはなりません。
- 自動車: ISO 16232 (VDA 19) 規格では、エンジンや燃料システムなどの主要コンポーネントに汚染物質がないことを確認するための自動車部品の清浄度テスト方法を規定しています。
- 医療機器: ISO 13485 では、患者の安全に影響を与える可能性のある汚染物質を避けるために、医療機器は厳格な清浄度基準を満たす必要があると規定されています。
- エレクトロニクス業界: IPC 規格では、短絡やはんだ付け不良を防ぐために、はんだ付け前に回路基板の表面が極めて高い清浄度に達することが要求されています。
清浄度評価プロセスでは、企業は関連基準に基づいてテストを実施し、洗浄結果を記録してコンプライアンス要件を満たし、製品の市場競争力を向上させる必要があります。
性能検証:レーザー洗浄では、汚染物質を除去するだけでなく、洗浄された表面が後続工程や最終使用の要件を満たしていることを確認する必要があります。そのため、性能検証は清浄度評価において重要なポイントであり、以下の側面が含まれます。
- 表面完全性テスト: 洗浄後に、微細な亀裂や表面粗さの変化など、材料に微細な損傷がないことを確認します。
- 接着テスト: 洗浄後の表面をコーティング、塗装、または溶接する必要がある場合は、表面の汚染による接着力の低下を避けるために、新しい接着部分の接着強度をテストする必要があります。
- 耐食性評価:一部の金属材料は洗浄後に酸化や腐食のリスクにさらされる可能性があり、塩水噴霧試験などの耐食性評価が必要です。
- 光学顕微鏡分析: 顕微鏡、走査型電子顕微鏡 (SEM)、または X 線分光法 (XPS) を使用して微細な汚染物質を検出し、洗浄後に表面に残留物がないことを確認します。
体系的な性能検証を通じて、さまざまなアプリケーションシナリオにおけるレーザー洗浄技術の信頼性を確保し、顧客の品質要件を満たすことができます。
清浄度評価は、レーザー洗浄の品質を保証するための中核的な要素であり、汚染物質の特定、表面感度、規制遵守、性能検証という4つの主要な側面を網羅しています。汚染物質を正確に特定し、様々な材料に合わせて洗浄パラメータを最適化し、業界標準に準拠し、厳格な性能検証を実施することで、企業は洗浄効果が産業用途のニーズを満たすことを保証できます。洗浄技術の継続的な進歩に伴い、レーザー洗浄はますます多くの業界で好まれる表面処理ソリューションとなり、ハイエンド製造業にとってより効率的で環境に優しい洗浄ソリューションを提供するでしょう。
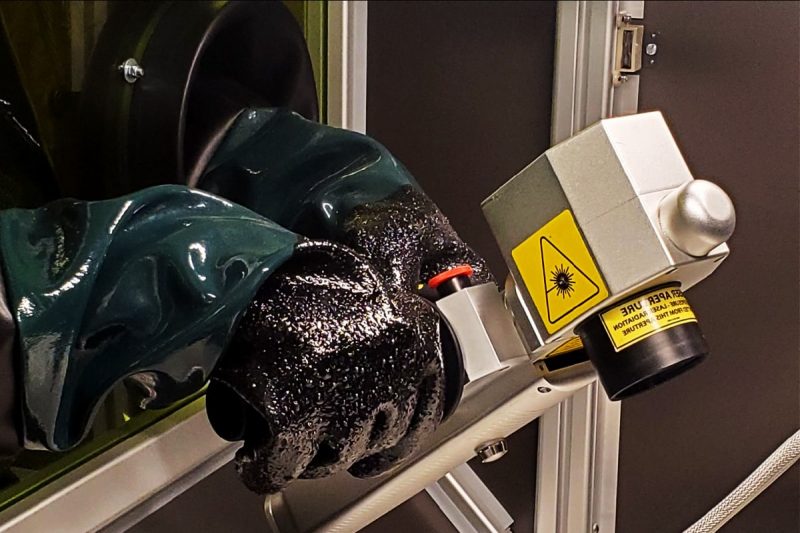
レーザー洗浄後の清浄度評価の重要性
産業用途において、レーザー洗浄後の清浄度を評価することは非常に重要です。これは製品の品質を決定づけるだけでなく、後続工程の信頼性にも影響します。清浄度評価の4つのコアバリューは以下のとおりです。
- 業界標準への準拠:航空、自動車、電子機器、医療など、様々な業界では表面清浄度に関する厳しい要件が定められています。ISO、VDA、IPCなどの規格への準拠を確保することで、製品がスムーズに品質認証を取得し、市場競争力を高めることができます。
- 最適な性能と信頼性:洗浄後も表面に汚染物質が残っていると、その後の溶接、コーティング、接合に影響を及ぼす可能性があります。部品の長期使用において最適な性能を維持し、故障リスクを低減するために、清浄度を正確に評価する必要があります。
- 品質保証:清潔さは製品の一貫性と耐久性に直接関係します。科学的な評価方法により、製造ミスを削減し、製造品質全体を向上させ、お客様の高い基準を満たすことができます。
- 費用対効果: 効果的な清浄度評価により、汚染による繰り返しの洗浄や手直し、廃棄、修理コストを回避できるほか、ダウンタイムが短縮され、生産効率が向上し、全体的な運用コストも削減されます。
清浄度評価は品質管理の一部であるだけでなく、生産の安定性を確保し、プロセスフローを最適化し、経済的利益を向上させるための重要な要素でもあります。

清浄度評価のための評価技術
レーザー洗浄後の表面が理想的な状態に到達するためには、清浄度を検出するための様々な評価技術が必要です。一般的な方法には以下が含まれます。
- 目視検査: 肉眼または拡大鏡を使用して予備検査を実施し、表面に明らかな汚染物質や欠陥があるかどうかを迅速に判断します。
- 表面プロファイル分析: 粗さ計を使用して表面の微細構造の変化を検出し、洗浄後に後続の処理やコーティングに影響がないことを確認します。
- 表面分析: X 線分光法 (XPS) またはエネルギー分散分光法 (EDS) を使用して表面組成を分析し、残留酸化物や有機汚染物質があるかどうかを検出します。
- 化学分析: 滴定、蛍光検出、またはガスクロマトグラフィー (GC-MS) を使用して表面の化学残留物を分析し、業界の洗浄基準に準拠していることを確認します。
- 光学顕微鏡:ミクロンレベルの汚染物質を拡大して観察します。特に電子機器や医療機器などの精密製造分野に適しています。
- 接着試験: 引き剥がし試験またはテープ剥離試験により表面コーティング、溶接、または接着の接着強度を評価し、後続のプロセスの品質を確保します。
複数の評価手法を組み合わせることで、洗浄結果をより正確に判断し、レーザー洗浄が業界標準とアプリケーション要件を満たしていることを確認できます。
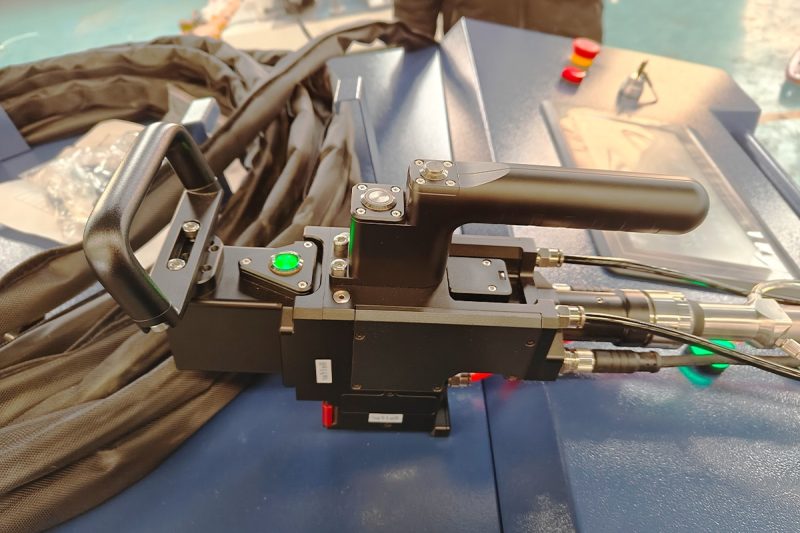
清潔さの評価に関するベストプラクティス
レーザー洗浄後の一貫した信頼性の高い表面品質を確保するために、企業は一連のベスト プラクティスに従って、評価の精度と一貫性を向上させる必要があります。
- 明確な基準を確立する: 業界仕様 (ISO、VDA、IPC など) に基づいて清浄度基準を策定し、すべての製品が品質要件を満たし、さまざまなアプリケーション シナリオに適していることを確認します。
- 複数の技術を活用する:単一の検出方法には限界があります。目視検査、表面分析、化学試験、顕微鏡観察、接着試験など、複数の技術を組み合わせることで、より包括的な評価結果を得ることができます。
- 機器の校正: 測定データの精度を確保し、機器の偏差による評価エラーを回避するために、テスト機器を定期的に校正します。
- 標準化された手順: 統一された清浄度検出プロセスを確立して、すべてのオペレーターが同じ手順に従い、人的エラーを削減し、データの比較可能性を向上させます。
- 担当者のトレーニング: 汚染物質、テスト方法、およびデータ解釈を識別する能力を向上させ、評価結果の信頼性を確保するために、テスト担当者に定期的に専門的なトレーニングを提供します。
- 結果の記録: 汚染物質の種類、テスト方法、機器のパラメータ、最終結果など、各清浄度評価のデータを詳細に記録し、追跡と分析を行って洗浄プロセスを最適化し、品質管理要件を満たします。
これらのベストプラクティスを通じて、企業は清浄度評価の精度と一貫性を向上させ、レーザー洗浄プロセスの信頼性を確保し、それによって製品の品質と市場競争力を向上させることができます。
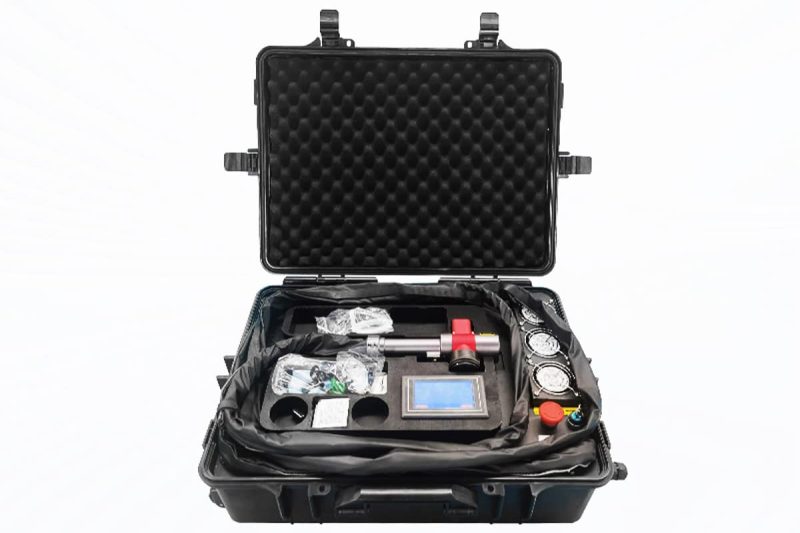
要約する
レーザー洗浄は、表面汚染物質の除去だけでなく、製造品質の向上とプロセスフローの最適化にも重要な役割を果たします。徹底的に清浄で基準を満たした表面は、後続のコーティング、溶接、接合などの工程をスムーズに進め、残留汚染物質による製品不良を回避します。正確な清浄度評価を通じて、企業はレーザー洗浄の効果を定量化し、各ワークピースが業界基準を満たしていることを保証し、製品の安定性と耐用年数を向上させることができます。さらに、厳格な清浄度管理は、手直しやスクラップ率の削減、生産コストの最適化、そして全体的な製造効率の向上にも役立ちます。
競争の激しい市場環境において、科学的な評価技術、標準化されたプロセス、そして効率的な試験方法を活用することで、製品の品質向上だけでなく、企業の市場における評判と顧客からの信頼を高めることができます。したがって、レーザー洗浄後の清浄度評価は、品質管理における重要なステップであるだけでなく、長期的な製造の最適化と業界リーダーシップの達成にとって重要な保証となります。
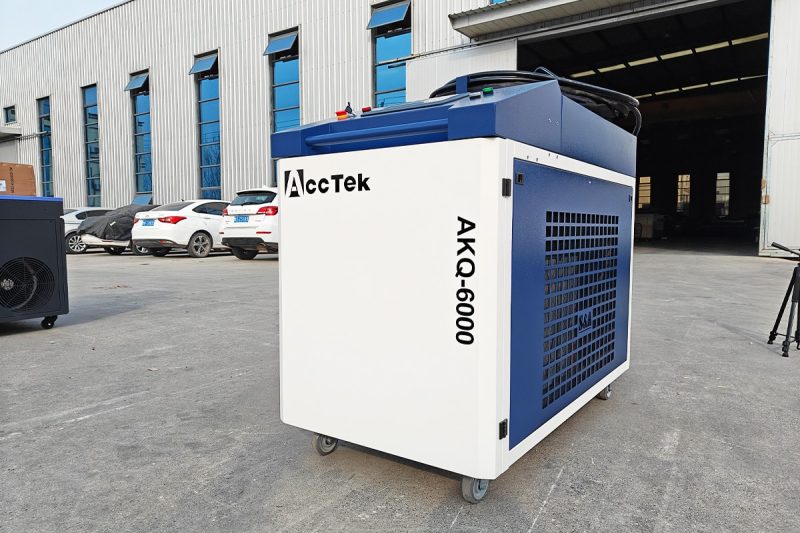
レーザー ソリューションを入手する
AccTek レーザー は、自動車製造、航空宇宙、電子産業、金属加工、文化遺産の修復など、多くの分野で広く使用されている、効率的で正確かつ安全なレーザー洗浄機の提供を専門としています。当社のレーザー洗浄技術は、酸化膜、油汚れ、コーティング、錆などの表面汚染物質を効果的に除去し、環境に優しくメンテナンスコストが低いまま、部品の高品質な加工を保証します。
信頼性の高いレーザー洗浄ソリューションをお探しなら、当社の専門チームがお客様のニーズに合わせてカスタマイズしたソリューションをご提供いたします。お客様の生産プロセスに最適な装置をご提案し、作業効率の向上と運用コストの削減を実現します。大規模な産業用途から精密部品の洗浄まで、AccTek Laserは高度な技術サポートと万全のアフターサービスをご提供いたします。
ようこそ お問い合わせ 専門家によるコンサルティング、製品デモンストレーション、詳細な技術ソリューションについては、お気軽にお問い合わせください。レーザー洗浄技術が貴社の生産基準向上に貢献します。
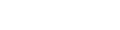
連絡先
- [email protected]
- [email protected]
- +86-19963414011
- No. 3 ゾーン A、Lunzhen 工業地帯、玉城市、山東省。
レーザー ソリューションを入手する