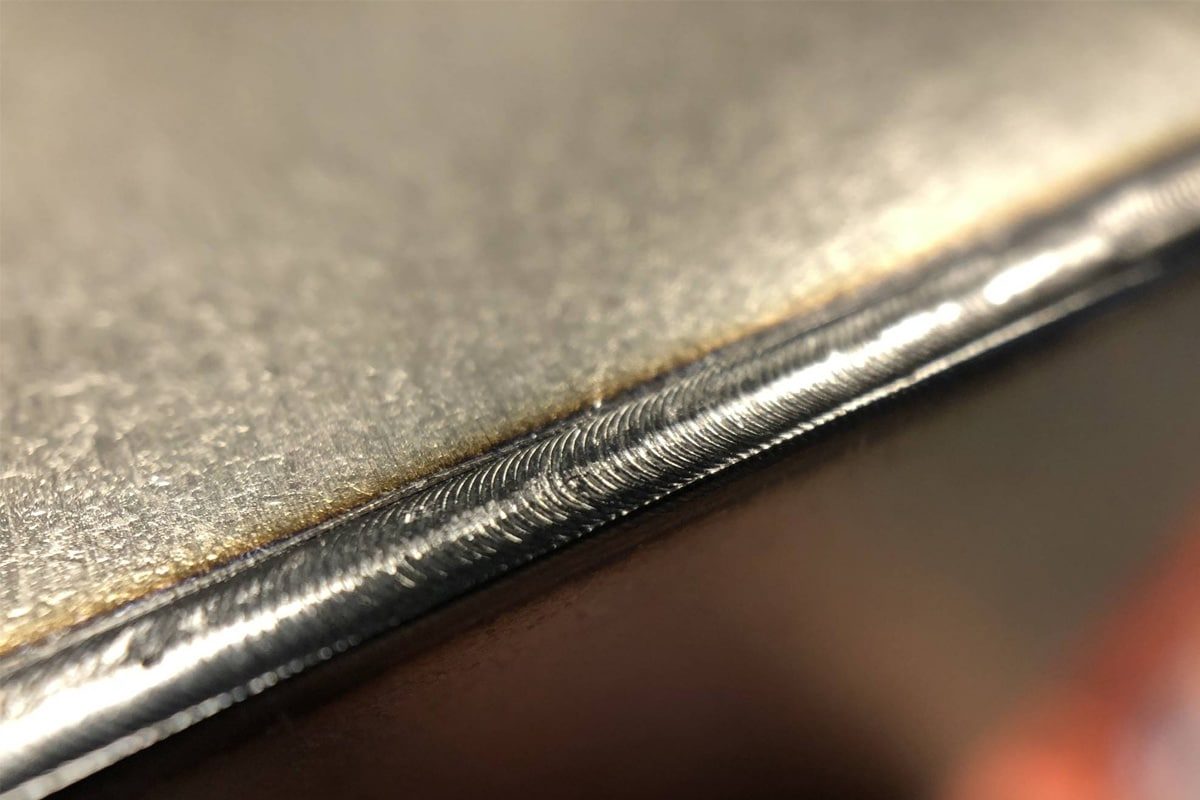
レーザー溶接で最小溶接幅を実現する方法
レーザー溶接は、その高い効率、精度、制御性により、精密溶接技術として、航空宇宙、自動車製造、電子部品、医療機器などで広く使用されています。高エネルギー密度のレーザービームを使用して局所的に加熱して溶融することで、レーザー溶接は、特に溶接サイズに厳しい要件があるシナリオで、高精度の溶接操作を実現できます。
精密製造の分野では、溶接幅の制御が非常に重要です。溶接幅を最小限に抑えることで、熱影響部の範囲を狭め、材料の変形のリスクを軽減し、溶接強度と外観品質を向上させることができます。さらに、溶接幅が狭いほど材料の損失が少なくなり、溶接効率も高くなり、高品質で低コストの生産という現代産業のニーズを満たします。
目次
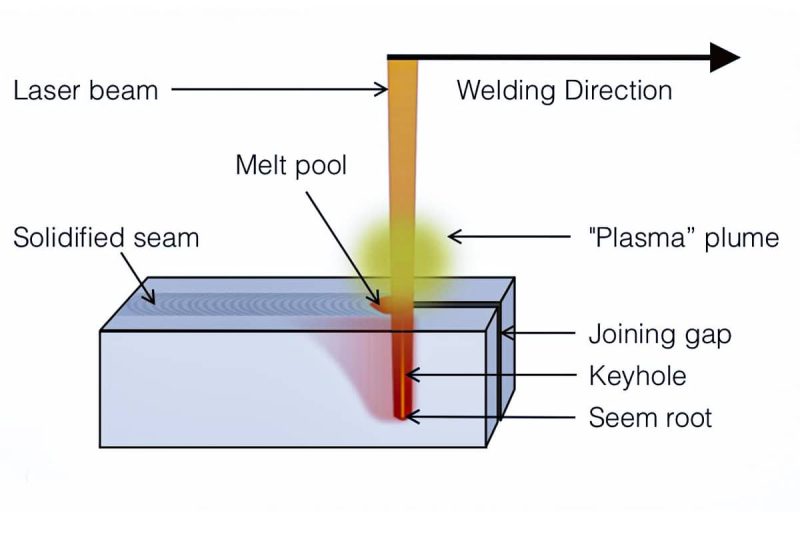
レーザー溶接を理解する
レーザー溶接の基礎
レーザー溶接は、高エネルギー密度のレーザービームを使用して材料を局所的に加熱し、材料の表面を溶かして隣接する領域と素早く結合させる高度な溶接技術です。レーザービームの高出力密度と高精度により、エネルギーを非常に小さな領域に集中させることができ、正確で効率的な溶接を実現します。
この技術は、熱影響部が小さく、材料の変形が起こりにくく、母材本来の特性を良好に保持できるため、薄肉構造物や精密部品の溶接に特に適しています。
レーザー溶接タイプ
レーザー溶接は、連続レーザー溶接とパルスレーザー溶接に分けられます。連続レーザー溶接は厚い材料に適しており、パルスレーザー溶接は薄い材料や、より高い精度が求められる溶接作業に適しています。
- 連続波レーザー溶接:長期の高強度溶接のニーズに適しており、厚い金属板の接続やシーリングに広く使用されています。
- パルスレーザー溶接: 短時間の高エネルギーパルスで材料を加熱し、薄板やマイクロ部品の溶接に適しており、制御精度が高くなります。
さらに、レーザーパラメータ(出力、速度、焦点位置など)を調整することで、溶接領域の熱入力を柔軟に制御し、さまざまな材料や溶接要件を満たすことができ、溶接サイズと溶接品質に影響を与えることができます。この高い適応性により、レーザー溶接は航空宇宙、自動車製造、電子産業で広く使用されています。
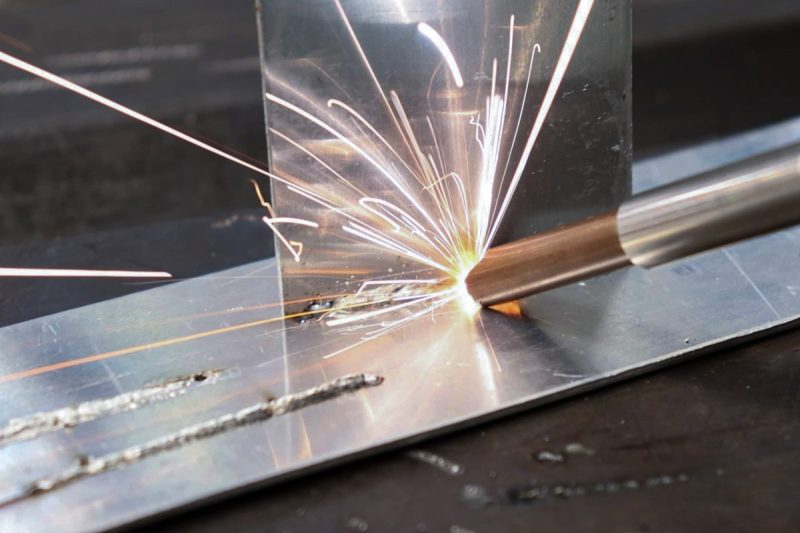
溶接幅に影響を与える要因
溶接幅はレーザー溶接品質の重要な指標の 1 つであり、その大きさは溶接の精度、強度、外観に直接関係します。溶接幅の制御には、主にレーザー パラメータ、材料特性、溶接環境など、複数の要因が関係します。以下は、各要因が溶接幅にどのように影響するかの詳細な分析です。
レーザーパラメータ
- レーザー出力:レーザー出力は、溶接結果に影響を与える最も重要なパラメータの1つです。レーザー出力が大きいほど、発生する熱が多くなり、熱影響部と溶融池の体積も増加し、溶接幅が広くなります。逆に、出力が低すぎると、材料を溶かすのに十分なエネルギーを提供できず、溶接継手が不十分になり、溶接幅が狭くなったり、溶接が不完全になったりする可能性があります。したがって、最適な溶接幅を実現するには、材料の厚さ、種類、溶接速度に応じてレーザー出力を合理的に選択する必要があります。
- 溶接速度:溶接速度は入熱に重要な影響を及ぼします。溶接速度が遅いと、レーザーが溶接領域に長く留まるため、母材への熱伝達が多くなり、溶融池と熱影響部が大きくなり、溶接幅が広くなります。逆に、溶接速度が速すぎると入熱が少なくなり、溶接が不完全になったり、溶接幅が狭すぎたり、溶接が弱くなったりする可能性があります。したがって、溶接速度を適切に制御することが、適切な溶接幅を確保するための鍵となります。
- 波長:レーザーの波長によって、レーザーが材料とどのように相互作用するかが決まります。短波長レーザー(ファイバーレーザー発生器から放射されるものなど)は、エネルギー集中度が高く、より狭い領域でより多くのエネルギーを提供できるため、金属材料によく吸収され、溶接効率が向上し、溶接部が狭くなります。相対的に言えば、長波長レーザー(CO2レーザー管から放射されるものなど)は金属材料の吸収が悪く、溶接中のエネルギー分布が比較的広く、溶接幅が大きくなりやすいです。したがって、短波長レーザーは高精度溶接に適しています。
- パルス持続時間: パルスレーザー溶接には、パルス持続時間を調整することで溶接を最適化できるという独自の利点があります。パルス持続時間が短いほど、レーザーの熱入力時間が短くなり、熱影響部の拡大が抑えられ、より小さな溶接部が形成されます。パルス持続時間が長いほど、熱入力が多くなり、溶接部が広くなります。パルス成形技術により、レーザーのパルス幅と間隔を正確に制御して、溶接中の熱分布と溶接形態を最適化できます。
- ビーム品質: レーザービームの品質と焦点制御は、溶接精度にとって重要です。ビーム品質の優れたレーザーは焦点サイズが小さく、エネルギーがより集中しているため、より高精度の溶接を実現できます。ビーム品質が高いほど熱拡散が減り、溶接領域に熱がより集中して溶接幅が狭くなります。ビーム品質が悪いと、レーザーエネルギーの分布が不均一になり、溶接幅が広くなります。
材料特性
- 吸収率:材料のレーザーに対する吸収率は、溶接効果に直接影響します。金属材料の吸収率は通常高く、特に短波長レーザーが金属に適合すると、吸収率がさらに向上します。レーザー溶接プロセスでは、吸収率が高いほど、レーザーエネルギーを効果的に熱エネルギーに変換できるため、溶接が小さくなります。逆に、材料の吸収率が低いと、レーザーエネルギーの有効利用率が悪く、溶接が広すぎたり不完全になったりする可能性があります。
- 反射率: 反射率の高い材料 (アルミニウムや銅など) はレーザーの反射が大きく、レーザーエネルギーの吸収効率が低下します。これにより溶接品質に影響し、溶接幅が広くなる可能性があります。この問題を克服するには、反射率の高い材料に適したレーザー タイプ (短波長レーザーの使用など) を選択するか、レーザー出力を上げて反射損失を補うことができます。また、焦点を絞ったビームと適切なレーザー波長を使用すると、反射性材料のレーザー吸収率を高めることもできます。
溶接環境
- シールドガス:シールドガスはレーザー溶接において重要な役割を果たします。溶接中の酸化や汚染を防ぐだけでなく、ガスの流れを制御することで熱伝導や溶接幅にも影響を及ぼします。たとえば、アルゴンや窒素はレーザー溶接のシールドガスとしてよく使用されます。これらは熱影響部の範囲を効果的に縮小し、過剰な溶接部の発生を回避できます。シールドガスの選択と制御は、特定の材料と溶接要件に応じて調整する必要があります。
- 環境条件: 温度や湿度などの環境要因もレーザー溶接の効果に一定の影響を与えます。低温環境では金属材料の熱伝導率が変化する可能性があり、溶接時の熱管理に影響します。また、湿度の高い環境ではレーザーエネルギーが散乱し、溶接品質に影響する可能性があります。安定した環境条件は、レーザービームの安定性を維持し、溶接時の溶接幅の一貫性を確保するのに役立ちます。
レーザー溶接における溶接幅の制御には、レーザーパラメータ、材料特性、溶接環境などの複数の要因の複合的な影響が関係します。最小溶接幅を得るには、実際の用途に応じてこれらの要因を細かく調整し、合理的に選択する必要があります。レーザー出力、溶接速度、ビーム品質などのパラメータを適切に最適化し、材料の吸収率、熱伝導率、反射率を考慮することで、溶接精度を効果的に向上させ、溶接の狭さと品質を確保できます。実際の用途では、高い反射率や難しい熱管理などの問題を解決することが、高精度の溶接を実現するための鍵となります。
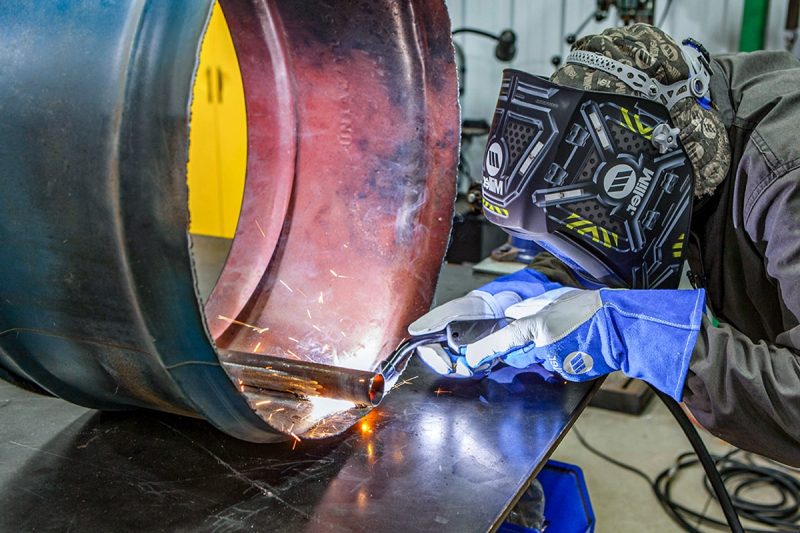
最小溶接幅を実現する技術
レーザー溶接で最小溶接幅を実現するには、レーザータイプの選択、レーザーパラメータの最適化、材料の準備、高度な溶接技術など、多くの面で最適化と調整を行う必要があります。これらの技術により、入熱を効果的に制御し、熱影響部を減らし、溶接の精度と狭さを確保できます。
レーザータイプの選択
適切なレーザー タイプを選択することが、最小溶接幅を実現するための基本です。レーザー ジェネレーターのタイプによって金属の溶接時の性能が異なり、適切な溶接タスクも異なります。
- ファイバーレーザー発生器: ファイバーレーザー発生器は、レーザー溶接で最も広く使用されているレーザー源の 1 つです。高出力、高ビーム品質、優れた集束能力を備えています。ファイバーレーザー発生器のビームは、非常に小さな領域に正確に集束できるため、溶接幅が小さくなり、薄板材料を効率的に処理できます。ファイバーレーザー発生器は、高精度で高速な溶接作業に非常に適しており、高品質の小さな溶接を実現し、材料の熱影響部 (HAZ) の拡大を減らすことができます。
- CO2 レーザー管: CO2 レーザー管は、金属溶接によく使用される別のレーザー源です。CO2 レーザー管のビーム品質は、一般的にファイバー レーザー ジェネレーターほど良くはありませんが、より大きなパワーと深い浸透深度を提供できるため、厚い材料の溶接に適しています。ファイバー レーザーほど正確ではありませんが、適切なパワー調整と最適化された溶接速度により、比較的狭い溶接幅を実現できます。
レーザー波長の選択
レーザー発生器の波長が異なれば、材料によって吸収率が異なります。CO2 レーザーは波長が長く、一般に非鉄金属 (アルミニウムや銅など) の吸収効率は低くなります。ファイバー レーザーは波長が短く、一般に金属材料による吸収率が高く、溶接効率が高く、溶接幅が狭くなります。したがって、レーザー発生器を選択するときは、出力と材料の厚さを考慮するだけでなく、材料の光学特性とレーザーの波長の適合性も考慮する必要があります。
レーザーパラメータの最適化
- レーザー出力調整:レーザー出力は溶接入熱に影響を与える主な要因です。出力が高すぎると、周囲に過剰な熱が広がり、溶接部が広がり、溶接欠陥の原因にもなります。出力を適切に下げると、特に薄板材料を溶接する場合、入熱を減らして溶接幅を狭くすることができます。ただし、出力が低すぎると、溶接が不十分になる可能性があります。したがって、材料特性、溶接速度、溶接要件に合わせてレーザー出力を適切に調整すると、正確な溶接を実現し、溶接幅を効果的に制御できます。
- パルス成形技術:パルスレーザー溶接技術は、レーザーパルスの周波数、持続時間、エネルギーを調整することで、溶接中の入熱を正確に制御できます。パルス幅が短いほど、入熱時間が短くなり、溶接領域に蓄積される熱が少なくなり、溶接部が狭くなります。また、パルス周波数とエネルギーを調整することで、溶接速度と溶融池の形態を制御でき、溶接部の幅に影響を与えます。パルス成形技術を使用すると、特にマイクロ溶接では、各パルスの熱分布を正確に制御して、最小溶接幅を効果的に達成できます。
- ビーム焦点制御:レーザー溶接の精度と溶接幅は、ビームの焦点位置に密接に関係しています。レーザービームの焦点が小さいほど、エネルギー密度が高くなり、溶接領域に集中できるため、狭く細かい溶接部を生成できます。したがって、レーザー焦点制御は非常に重要です。焦点位置を調整することで、レーザービームのエネルギーを溶接領域に集中させ、周囲への熱拡散を回避し、溶接幅を狭くすることができます。
材料の準備
- 表面の清浄度: 溶接材料の表面の清浄度は、レーザー溶接の効果に直接影響します。表面の酸化物、油、錆、その他の汚染物質はレーザーの吸収率に影響し、溶接領域に熱を効果的に集中させることができなくなり、溶接品質に影響を与え、溶接幅が広くなります。溶接表面が清潔で汚染がないことを確認することは、溶接品質を最適化するための前提条件です。表面の汚染物質は通常、化学洗浄、機械洗浄、またはレーザー洗浄によって除去できます。
- 表面コーティング:場合によっては、特に溶接が難しい材料の場合、表面コーティングによりレーザーの吸収効率が大幅に向上します。コーティング材料(銅メッキ、亜鉛メッキなど)は、レーザーと材料の相互作用を改善し、溶接領域の熱蓄積を強化し、溶接プロセス中に溶接幅を正確に制御するのに役立ちます。さらに、特殊なコーティングにより、溶接中の溶融池の安定性が向上し、溶接中の欠陥も減少します。
高度な溶接技術
- ハイブリッドレーザー溶接:ハイブリッドレーザー溶接技術は、レーザーと従来の溶接方法(TIG溶接やMIG溶接など)の利点を組み合わせ、異なる熱源の利点を組み合わせることで熱入力と溶接精度を向上させます。レーザーと従来の溶接方法を組み合わせることで、特に厚い材料を溶接する場合に、溶接幅を効果的に減らすことができます。ハイブリッドレーザー溶接技術は、溶融池の安定性を高め、熱影響部を小さくすることで、より洗練された溶接効果を実現します。
- マイクロ溶接技術:マイクロレーザー溶接は、超小型溶接部を処理するための高精度溶接技術であり、特に小型部品の接続に適しています。マイクロ溶接技術は、細かく制御されたレーザーパルスを使用して、非常に小さな溶接領域で効率的なエネルギー伝達を実現し、非常に狭い溶接部の形成を保証します。マイクロ溶接は、電子機器、精密機器、医療機器などの業界で一般的に使用されており、高い溶接精度を実現し、溶接領域への熱の影響を最小限に抑えることができます。
最小溶接幅を実現するための鍵は、レーザーの種類、レーザーパラメータ、材料の準備から高度な溶接技術まで、複数の要素を総合的に調整することにあります。各リンクには細かい設計と調整が必要です。適切なレーザーの種類を選択し、レーザー出力とパルス形状を最適化し、ビームの焦点位置を制御し、材料の準備と表面処理を改善することで、溶接幅を大幅に縮小できます。同時に、ハイブリッドレーザー溶接とマイクロ溶接技術の適用により、高精度で狭い溶接を実現するための可能性が広がります。これらの技術の組み合わせと革新により、レーザー溶接は高精度の要件を満たしながら溶接効率と品質を向上させることができます。
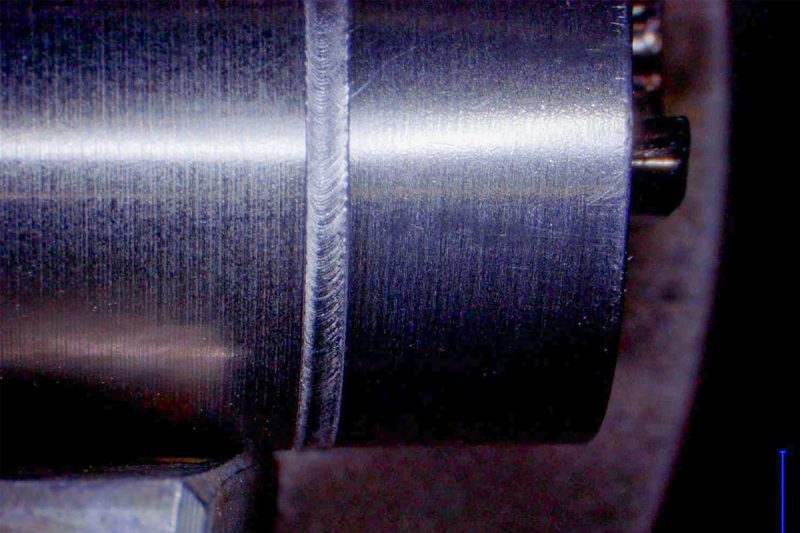
課題と解決策
レーザー溶接プロセスにおける課題は、主に熱管理、材料の反射率、およびプロセスの安定性に反映されます。これらの問題を考慮すると、対応するソリューションを採用することで、溶接品質を効果的に向上させ、溶接幅を縮小し、溶接プロセスの制御性と一貫性を確保できます。
熱管理
チャレンジ
レーザー溶接では、入熱量が多すぎると溶接部が過熱し、溶接幅が大きくなりすぎ、熱亀裂や変形などの一連の溶接欠陥が発生する可能性があります。また、熱影響部(HAZ)が大きいと、材料特性に悪影響を与える可能性もあります。入熱を合理的に制御し、過度の熱拡散を回避する方法は、精密溶接を実現する上で重要な課題となっています。
解決
- 補助ガス冷却の使用:適切なシールドガスまたは補助ガス(アルゴン、窒素、酸素など)を使用すると、溶接領域の酸化を防ぐだけでなく、溶接中に発生する余分な熱を効果的に除去し、熱影響部の拡大を減らすことができます。最高の冷却効果を確保するには、溶接材料、溶接速度、レーザー出力に応じて補助ガスの流量と圧力を最適化する必要があります。
- 溶接速度の最適化: 溶接速度を適切に上げると、単位時間あたりの熱入力が減り、材料の加熱時間が短縮され、溶接領域の過熱を効果的に回避できます。溶接速度が速いほど、熱がより広い領域に急速に広がり、局所的な温度上昇が抑えられ、溶接幅と熱影響部を制御できます。
- 熱源の調整: レーザー出力を調整するか、パルスレーザーを使用することで、溶接プロセス中の熱入力を正確に制御できます。特にパルス溶接では、短いパルスと高いパルス周波数により、熱が溶接領域に素早く集中して分散され、熱拡散を防ぐことができます。
材質の反射率
チャレンジ
多くの金属材料、特に非鉄金属(例えば アルミニウム、銅など)は光の反射率が高いです。反射率の高い材料は大量のレーザーエネルギーを反射するため、エネルギーの有効利用が低下し、溶接効率が制限され、溶接時に不完全な溶接や溶接幅の増加を引き起こす可能性があります。
解決
- 短波長レーザーを使用する: 短波長レーザー (ファイバー レーザー ジェネレーターによって生成されるものなど) は、反射率の高い材料に対する吸収率が高くなります。短波長レーザーは材料によく吸収され、反射を減らし、溶接プロセスでより多くのレーザー エネルギーが効果的に使用されるようにすることで、溶接効率を向上させ、溶接幅を縮小します。長波長 CO2 レーザーと比較して、ファイバー レーザー ジェネレーターは反射率の高い材料の加工に適しています。
- レーザー出力調整: 反射率の高い材料の場合、レーザー出力を適切に下げることで、過剰なエネルギー反射を回避できます。出力設定を低くすると、反射が減り、エネルギーの無駄が回避されるため、溶接幅を効果的に制御し、溶接品質を最適化できます。
- コーティングされた材料を使用する: アルミニウムや銅などの反射率の高い金属材料には、コーティング技術 (コーティング アルミニウム メッキ、銅メッキ、その他の表面処理方法など) を使用できます。これらのコーティングは反射率が低いため、レーザーの吸収効率が向上し、溶接プロセスでの反射の干渉が減少し、溶接幅をより適切に制御できます。
プロセスの安定性
チャレンジ
レーザー溶接中の安定性は重要な要素です。プロセスが不安定になると、溶接品質の変動、溶接幅の変化、さらには溶接欠陥(気孔、溶接オフセットなど)につながる可能性があります。一貫した溶接結果を得るには、レーザー溶接プロセスの安定性を確保し、パラメータの変動による溶接品質の問題を回避する必要があります。
解決
- 高度なレーザー制御システム:高度なレーザー制御システムを使用することで、レーザー出力、溶接速度、ビーム焦点などの主要なパラメータをリアルタイムで監視および調整し、各溶接プロセス中のレーザーパラメータの一貫性を確保できます。現代のレーザー溶接システムは通常、高精度センサーと自動調整機能を備えており、溶接領域の温度、溶融池の形態、ビームの位置をリアルタイムで検出し、レーザー出力を自動的に調整して溶接プロセスの安定性を維持します。
- リアルタイムフィードバックと閉ループ制御:リアルタイムフィードバックと閉ループ制御技術を使用すると、溶接プロセス中にパラメータをリアルタイムで調整して、材料特性と溶接環境の変化に対応できます。たとえば、センサーは溶融池のサイズ、形状、温度を監視し、システムはレーザー出力と溶接速度を自動的に調整して、溶接品質の一貫性を維持できます。この技術により、溶接プロセスの信頼性が大幅に向上し、プロセス変動による溶接の問題を回避できます。
- 溶接パスの最適化: 溶接プロセス中、レーザーパス計画を最適化することは、プロセスの安定性を向上させるもう 1 つの重要な方法です。溶接パスと溶接シーケンスを正確に制御することで、材料の変形や熱影響部の変化を軽減し、各溶接プロセス中の一貫した温度分布を確保して、安定した溶接結果を実現できます。
熱管理、材料反射率、プロセス安定性は、レーザー溶接における3つの大きな課題であり、溶接幅、溶接品質、生産効率に影響します。これらの課題は、適切な冷却方法、短波長レーザー、レーザー出力調整、高度なレーザー制御システム、最適化された溶接パス、その他の技術を採用して溶接プロセスの精度と安定性を向上させることで効果的に解決できます。これらのソリューションは、最小溶接幅の達成に役立つだけでなく、レーザー溶接技術の広範な応用を強力にサポートします。
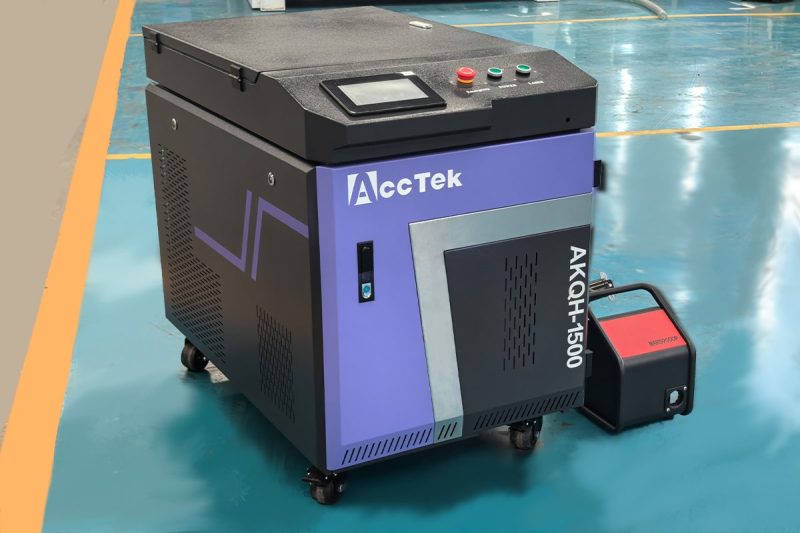
要約する
レーザー溶接における最小溶接幅の実現は、溶接品質の向上の鍵となるだけでなく、材料の無駄を減らし、生産効率を高め、コストを削減するための重要なステップでもあります。製造業における精密溶接技術の需要が高まるにつれ、溶接工程中に熱入力、溶接幅、溶接品質を正確に制御する方法に注目する企業が増えています。レーザー溶接では、レーザーパラメータ(出力、溶接速度、パルス成形、ビーム焦点など)を正確に制御し、適切な材料と溶接技術を選択することで、溶接効果を効果的に最適化し、理想的な溶接品質を実現し、不必要な材料の無駄を減らし、製品の一貫性と信頼性を向上させることができます。
しかし、実際の生産アプリケーションでは、レーザー溶接は依然として一連の技術的課題に直面しています。たとえば、過度の熱入力により溶接が広くなりすぎる可能性があり、材料の反射率もレーザーエネルギーの有効な伝達に影響します。これらの課題は、高度な技術的手段とプロセスの改善によって解決する必要があります。たとえば、適切な冷却方法の使用、短波長レーザーの選択、レーザー出力の最適化、効率的なレーザー制御システムの使用により、これらの問題をある程度解決できます。技術の継続的な進歩により、レーザー溶接の精度と安定性は向上し続け、より幅広く高度な産業用途のニーズを満たすことができます。
このプロセスでは、私たちの レーザー溶接機 は、優れた技術と革新的な設計により、業界のリーダーとなっています。当社のレーザー溶接機は最新のファイバーレーザー技術を採用しており、溶接プロセス中に正確な温度制御を確保しながら効率的な溶接を実現し、溶接幅を効果的に制御し、熱影響部を減らします。当社の溶接設備は、高精度のレーザービーム調整機能を備えているだけでなく、溶接プロセス中にパラメータを自動的に調整できる高度な温度制御システムも装備されており、溶接効果を最適化し、各溶接ポイントで安定した一貫した品質を確保します。
加えて、 AccTekレーザーの 溶接機は、さまざまな金属材料や複雑なプロセスに広く適用でき、高精度で狭い溶接に対するさまざまな業界のニーズを満たすことができます。電子機器製造、自動車産業、精密機器製造のいずれの場合でも、当社のレーザー溶接装置は信頼性の高いソリューションを提供できます。優れた製品品質と安定性により、レーザー溶接の分野で多くのお客様の信頼を獲得しています。レーザー溶接技術の継続的な進化に伴い、AccTek Laserは革新と技術の最適化に引き続き取り組み、製品の性能を継続的に向上させ、より効率的で正確で信頼性の高い溶接ソリューションをお客様に提供し、お客様が激しい市場競争で有利な立場を占めるのに役立ちます。
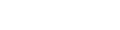
連絡先
- [email protected]
- [email protected]
- +86-19963414011
- No. 3 ゾーン A、Lunzhen 工業地帯、玉城市、山東省。
レーザー ソリューションを入手する