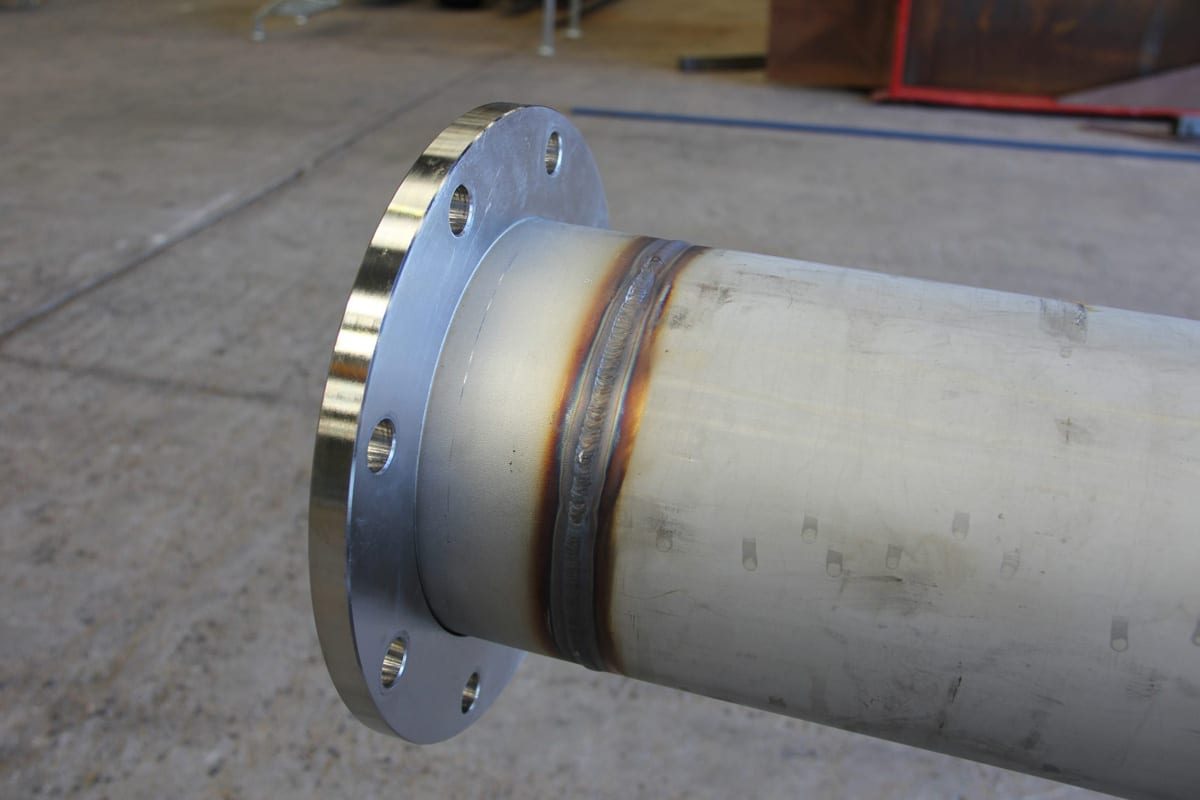
レーザー溶接継手の強度を向上させる方法
レーザー溶接は、低入熱、深溶け込み溶接、優れた自動化機能などにより、効率的で精密な溶接技術として自動車製造、航空宇宙、電子産業で広く使用されています。この技術は、溶接品質を確保しながら生産効率を大幅に向上させ、材料の変形や加工工程を削減できるため、現代の製造業において欠かせない重要な手段となっています。
しかし、溶接継手の強度は、特に高応力や複雑な作業環境にさらされる用途では、製品の性能と信頼性に直接関係しています。材料、プロセス、設計を最適化して溶接継手の強度をさらに向上させる方法は、技術研究開発と産業応用における重要な課題です。この記事では、溶接強度に影響を与える主な要因から始め、強度を向上させるための高度な技術を詳細に分析し、溶接後の処理の重要性を探り、一般的な課題に対する解決策を示します。
目次
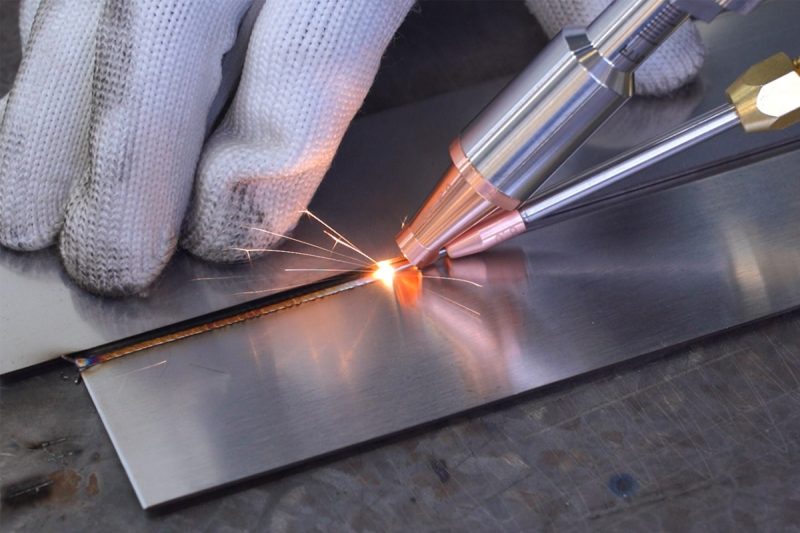
レーザー溶接について学ぶ
レーザー溶接は、高エネルギーレーザービームを熱源として使用し、非常に小さなスポットに集中させることで、低入熱と深い浸透溶接効果を実現します。この技術の独自の利点は、その精度と柔軟性であり、複雑な幾何学的構造、高精度の要件、アクセスが困難な溶接領域に特に適しています。従来の溶接方法と比較して、レーザー溶接は熱変形と残留応力を大幅に低減できるだけでなく、処理速度と生産効率も向上します。
加えて、 レーザー溶接機 溶接は、さまざまな金属や合金材料を含むさまざまな材料の接続に適用でき、特に製造業における軽量で高強度の部品の需要が高まる中で重要な役割を果たしています。しかし、効率的な溶接を実現する一方で、溶接継手の強度は製品の性能と信頼性に影響を与える重要な問題であり続けています。そのため、高水準の産業用途のニーズを満たすために、材料、プロセス、設計を最適化して溶接品質を継続的に改善する必要があります。
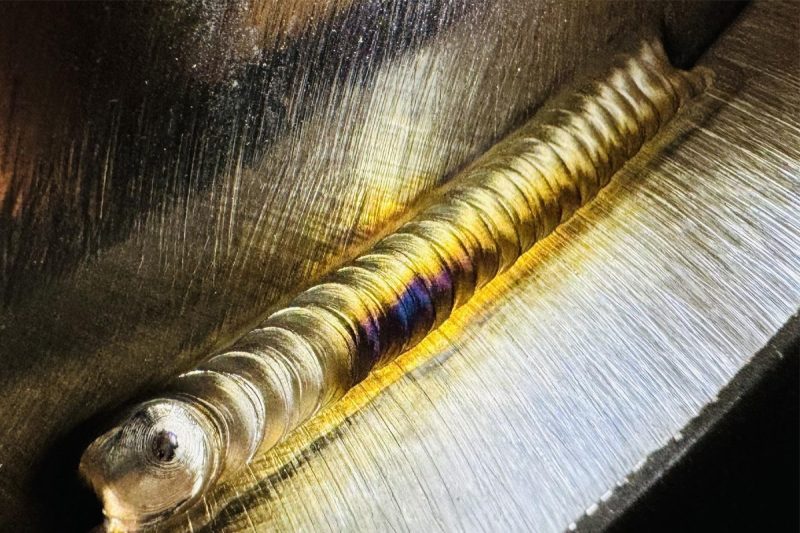
溶接強度に影響を与える要因
レーザー溶接継手の強度は、材料特性、レーザーパラメータ、継手設計、溶接環境などのさまざまな要因の組み合わせによって影響を受けます。高品質の溶接継手を実現するには、これらの要因の具体的な役割と相互影響を深く理解し、実際のアプリケーションで各リンクを最適化する必要があります。以下では、これらの要因を詳細に分析します。
材料特性
材料特性は溶接結果を決定する重要な基礎であり、主に母材の組成、材料の厚さ、表面状態に現れます。
- 基板の構成: 材料によってレーザーの吸収率が異なります。たとえば、反射率の高い金属 (アルミニウムや銅など) はレーザーエネルギーの吸収率が低いため、浸透が不十分になりやすくなります。レーザーパラメータを調整するか、吸収材で表面をコーティングして、溶接効果を向上させる必要があります。
- 材料の厚さ: 材料の厚さはレーザーのエネルギー分布に直接影響します。材料が厚すぎるとレーザーの浸透が不十分になり、不完全な浸透溶接になる可能性があります。一方、材料が薄すぎるとレーザーエネルギーが過剰になり、溶けてしまう傾向があるため、パラメータ設定を慎重に調整する必要があります。
- 表面状態: 材料表面の清浄度、酸化膜、粗さはレーザーの透過と吸収に影響します。表面の汚染や酸化により溶融池の形成が不均一になり、溶接強度が低下する可能性があります。そのため、溶接前の洗浄と適切な表面処理が不可欠です。
レーザーパラメータ
レーザーパラメータは、溶接中の熱入力と溶融池の形成を直接決定します。
- レーザー出力:出力が低すぎると溶け込みが不十分になり、溶接強度が弱まる可能性があります。一方、出力が高すぎると、材料の溶け落ちが起こりやすくなったり、溶融池が大きくなりすぎて、溶接継手の強度が弱まる可能性があります。そのため、材料の特性や厚さに応じて適切な出力レベルを選択する必要があります。
- 溶接速度: 溶接速度が速すぎると溶融池の形成が不十分になり、溶接部に気孔や亀裂が生じる可能性があります。一方、溶接速度が遅すぎると、熱入力が過剰になり、材料が過熱したり、変形したりする可能性があります。
- 焦点位置: レーザー焦点を正確に位置決めすることで、エネルギーの有効利用が最大化され、溶融池の深さと均一性が確保されます。焦点がずれると溶接効率が低下し、品質不良の原因となる可能性があります。
- パルスパラメータ:パルスレーザー溶接の場合、パルス幅と周波数の設定は溶融池の形成と凝固プロセスに直接影響します。パルスパラメータを最適化すると、亀裂や気孔の発生を減らし、溶接強度を向上させることができます。
コネクタ設計
ジョイントの設計は溶接の容易さに影響するだけでなく、溶接の機械的特性と信頼性にも直接関係します。
- ジョイント構成: さまざまなタイプのジョイント (突合せジョイント、重ねジョイントなど) は、さまざまな構造要件と機械的性能要件に適しています。たとえば、突合せジョイントは高強度溶接に適しており、重ねジョイントは薄板溶接に適しています。
- 組み立てと位置合わせ: ジョイントの組み立てが不十分であったり、位置合わせにエラーがあると、溶接プールの移動や溶接欠陥が発生し、溶接強度が低下します。実際の操作では、精密固定具や自動位置合わせシステムを使用すると、組み立て精度が大幅に向上します。
- エッジ処理: エッジ処理の品質は溶接効果にとって非常に重要です。エッジが不均一であったりバリがあると、ひび割れや介在物欠陥が発生する可能性があるため、エッジを処理するには精密加工機器が必要です。
溶接環境
溶接環境は、シールドガスの選択や環境条件の制御など、溶接品質に影響を与える外部要因です。
- シールドガス: シールドガスの種類と流量を適切に設定すると、溶融池の酸化を防ぎ、溶接継手の緻密性と耐腐食性を向上させることができます。たとえば、アルゴンとヘリウムは一般的に使用されるシールドガスであり、流量が多すぎたり少なすぎたりすると保護効果に影響します。
- 環境条件: 湿度が高い、ほこりが多い、または温度差が急激な環境は、溶接プロセスに悪影響を及ぼし、溶接の性能が低下する可能性があります。したがって、溶接エリアの環境を良好に管理することは、溶接品質を確保するための重要な対策です。
レーザー溶接継手の強度に影響を与える要因は複雑かつ多様であり、材料特性、レーザーパラメータ、継手設計、溶接環境などあらゆる側面が関係します。実際のアプリケーションでは、これらの要因を総合的に考慮する必要があり、合理的なプロセス最適化と機器調整によって高品質で高強度の溶接継手を実現できます。
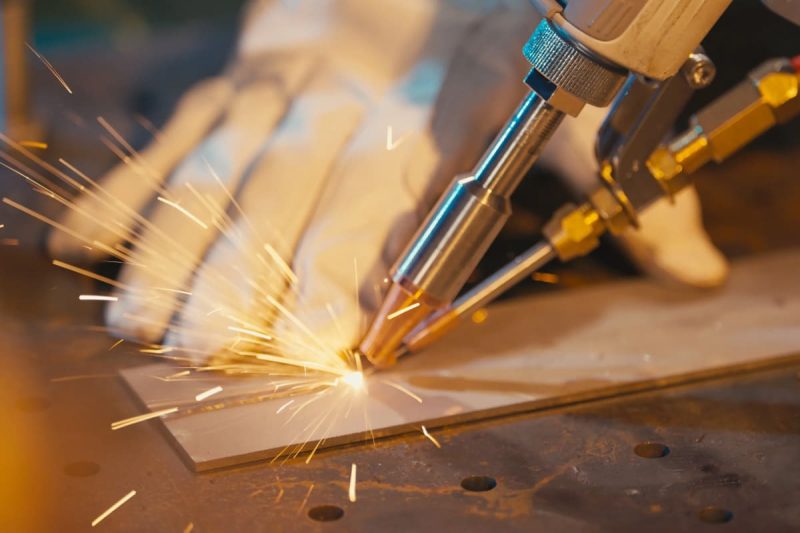
溶接強度向上技術
レーザー溶接継手の強度を向上させるには、材料特性、レーザー技術、溶接プロセス制御、溶接後の処理を最適化する必要があります。これには、溶接材料の選択と準備だけでなく、レーザーパラメータの正確な調整、合理的な接合形状の設計、高度なプロセス制御技術の使用も含まれます。これらのリンクを包括的に最適化することで、溶接の機械的特性と信頼性を大幅に向上させることができます。溶接強度を向上させる具体的な技術的方法については、以下で詳しく説明します。
材料の選択と準備
材料は溶接性能の基礎であり、溶接接合部の強度に重要な役割を果たします。
- 合金の最適化: レーザー溶接に適した高強度材料を選択し、合金の組成を調整することで、溶接結果を大幅に改善できます。たとえば、特定の元素を追加して材料の溶接性と耐疲労性を向上させることで、過酷な環境でも溶接の安定性を維持できます。
- 表面洗浄: 溶接前に材料の表面を徹底的に洗浄して、グリース、酸化層、その他の汚染物質を除去し、レーザー エネルギーの効率的な伝達を確保し、溶接欠陥を減らします。一般的な方法には、機械的洗浄、化学的洗浄、レーザー洗浄などがあります。
- 予熱: 熱に非常に敏感な材料や割れやすい材料の場合、適切な予熱を行うことで溶接プロセス中の熱勾配が低減し、熱応力が軽減されるため、溶接品質が向上します。
レーザー最適化
レーザーパラメータの調整により、溶接の成形品質と機械的特性が直接決まります。
- 出力密度制御: レーザー出力密度を正確に調整して溶融池の均一な分布を確保し、溶接の密度と強度を向上させます。出力密度が低いと溶け込みが不十分になる可能性があり、出力密度が高すぎると溶け落ちや金属の飛散が起こりやすくなります。
- ビーム成形: レーザースポットの形状を最適化すると、溶接プロセス中の熱分布を改善できます。たとえば、円形スポットを楕円形または直線状に分布したビーム形状に変更すると、溶接孔の発生を大幅に減らし、溶接の安定性を向上させることができます。
- 焦点調整: レーザー焦点を正確に位置決めすることが、溶接品質を向上させる鍵となります。焦点が深すぎると溶け込みが不十分になる可能性があり、焦点が浅すぎると表面のアブレーションの問題が発生する可能性があります。そのため、自動焦点または精密な機械調整によって、溶接の最適な溶け込みが確保されます。
プロセス制御
高度なプロセス制御技術により、溶接品質の安定性が強力に保証されます。
- 適応制御システム: リアルタイム監視機器 (カメラやセンサーなど) を使用して溶接プロセスにおける主要なパラメータを監視し、レーザー出力、溶接速度などを自動的に調整して、溶接品質が常に最良の状態になるようにします。
- 閉ループフィードバック: センサーは溶融池の形状や温度などのデータを取得し、リアルタイムで制御システムにフィードバックすることで、溶接パラメータを動的に最適化し、溶接欠陥を削減します。
- 機械学習アルゴリズム:人工知能と機械学習技術を導入して、大量の溶接データを分析し、最適なパラメータの組み合わせを予測し、溶接プロセスをさらに最適化し、自動化のレベルを向上させます。
ジョイントの設計と準備
接合部の設計と端面処理は、溶接接合部の強度に重要な役割を果たします。
- 最適化されたジョイント形状: ジョイント形状は、溶接プロセスと構造要件に応じて設計されます。たとえば、突合せジョイントは高強度溶接に適しており、重ねジョイントは薄板接続に適しています。ジョイント形状を最適化することで、溶接部の機械的特性を大幅に向上させることができます。
- 精密な組み立てと位置合わせ: 高精度の固定具と自動位置決め装置を使用してジョイントの位置合わせ精度を確保し、溶接のオフセットやジョイント不良を回避し、溶接の全体的な強度を向上させます。
- エッジ処理: 精密機器を使用して溶接エッジを加工し、滑らかでバリのない状態にします。これにより、亀裂の発生を効果的に低減し、溶接の一貫性と信頼性を向上させることができます。
溶接後処理
溶接後の処理により、溶接残留応力をさらに解放し、溶接部の機械的特性と耐用年数を向上させることができます。
- 熱処理:焼鈍または焼き戻しにより溶接応力を解放し、溶接部および周囲の材料の微細構造を改善し、材料の靭性と強度を向上させます。
- 表面仕上げ:研削または研磨により溶接面の粗い部分や欠陥を除去し、疲労耐性と美観を向上させます。
- 非破壊検査: 超音波検査や放射線検査などの非破壊検査方法を使用して、溶接部内に亀裂や気孔などの隠れた危険がないことを確認し、製品の信頼性をさらに向上させます。
- 機械加工:ショットピーニングなどの方法により溶接面の残留応力分布を改善し、圧延技術を使用して機械的圧力により溶接部の密度と疲労耐性を向上させます。これらの機械加工方法は、溶接部に追加の強化手段を提供できます。
レーザー溶接継手の強度を向上させるには、材料の選択と準備からレーザーパラメータの正確な調整、高度なプロセス制御と溶接後の処理まで、多くの側面を総合的に最適化する必要があり、各リンクが重要です。科学的で合理的なプロセスの組み合わせにより、溶接継手の機械的特性が向上するだけでなく、全体的な溶接品質と信頼性も向上し、高水準の産業用途を強力にサポートします。
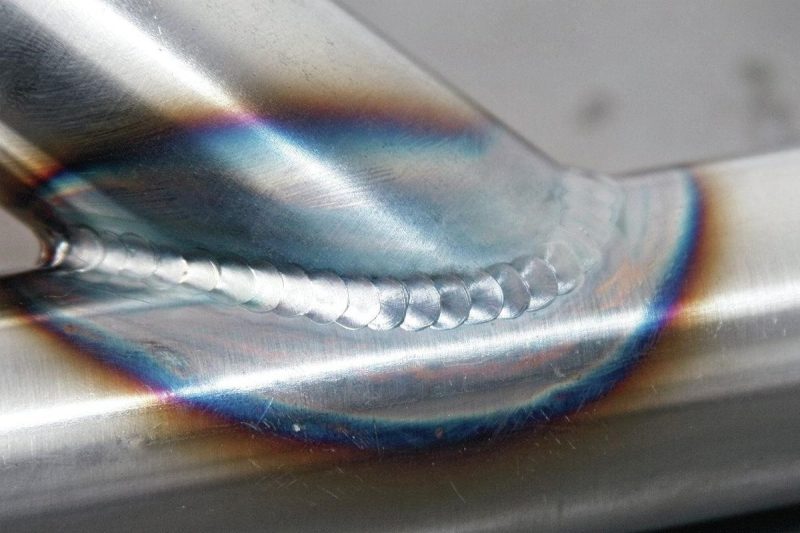
課題と解決策
レーザー溶接プロセスでは、技術の効率と精度が多業種への応用に強力なサポートを提供していますが、実際の応用には依然としていくつかの課題があり、溶接継手の品質と安定性に直接影響します。これらの課題に対処するために、効果的なソリューションは溶接品質を向上させるだけでなく、レーザー溶接の適用範囲を広げることもできます。以下では、熱管理、材料適合性、プロセス安定性の3つの主要な課題とその解決策について詳しく説明します。
熱管理
熱管理は、レーザー溶接中に対処する必要がある重要な問題です。レーザー溶接では、集中した熱入力により材料が局所的に過熱しやすく、変形、熱亀裂、残留応力などの原因となり、溶接接合部の強度と寿命が低下する可能性があります。
課題分析
- 高入熱環境では、特に薄い材料や精密部品の溶接において、材料の不均一な膨張と収縮により変形が生じる可能性があります。
- 温度が高すぎると溶接部に亀裂や粒界腐食が発生し、溶接性能に影響を及ぼす可能性があります。
解決
- 溶接パスの最適化:コンピュータ支援設計(CAD)により溶接パスを最適化し、入熱を分散し、熱蓄積領域の温度を下げます。
- 冷却装置:溶接時に冷却水設備や空冷設備を導入することで、溶接部の入熱強度を効果的に制御し、熱変形や亀裂の発生確率を低減できます。
- パルスレーザーモード: 連続レーザー溶接の代わりにパルスレーザー溶接を使用すると、熱入力をより適切に制御し、熱影響領域の範囲を縮小して、溶接品質を向上させることができます。
材質の適合性
工業生産において、鋼とアルミニウム、銅とステンレス鋼など、異種材料の溶接はますます一般的になっています。これらの材料の物理的特性と化学的特性の違いにより、溶接が困難になる可能性があります。
課題分析
- 異種材料の溶接では、融合不良、脆性相、または界面亀裂が発生しやすく、溶接継手の強度と信頼性に重大な影響を及ぼします。
- 材料間の膨張係数の差により、冷却中に溶接部に大きな残留応力が生じ、割れのリスクが高まります。
解決
- 適合合金の選択:材料配合を最適化することで、ベース材料として適合性の高い合金を選択し、融合不良や亀裂の発生を低減します。
- フィラー材料の使用: 溶接プロセス中に特定のフィラー材料 (マスター合金や溶接ワイヤなど) を追加すると、2 つの材料の融合性能が向上し、界面反応の複雑さが軽減されます。
- レーザーパラメータの最適化: レーザー出力、溶接速度、焦点位置を正確に調整して、異種材料溶接の特定のニーズを満たし、溶融プールの安定性と均一性を確保します。
プロセスの安定性
レーザー溶接は、パラメータに大きく依存するプロセスです。溶接パラメータの変動は溶接品質の不一致につながり、生産効率や製品性能に影響を与える可能性があります。
課題分析
- レーザー出力や溶接速度が不安定だと、溶接の深さ、幅、強度が不均一になる可能性があります。
- 溶接装置の振動や材料の締め付けが緩いと、融合不足、多孔性、オフセットの問題などの溶接欠陥が発生する可能性があります。
解決
- 適応制御: インテリジェントな適応制御システムを導入し、リアルタイムで監視される溶接パラメータ (温度、溶融池の形状など) に応じてレーザー出力と溶接速度を動的に調整し、プロセスの高い安定性を確保します。
- 閉ループフィードバックシステム:高精度センサーを使用して溶接プロセスの重要なデータを収集し、そのデータを制御システムにフィードバックして自動調整します。たとえば、溶融池の形状変化をリアルタイムで監視して焦点位置を動的に調整し、溶接の一貫性を確保します。
- 人工知能最適化:機械学習に基づくアルゴリズムを導入し、ビッグデータ分析とパラメータ予測を通じてレーザー溶接プロセスの自動最適化を実現し、パラメータ変動の影響を軽減し、溶接の信頼性と再現性を向上させます。
レーザー溶接アプリケーションでは、熱管理、材料の適合性、およびプロセス安定性が、溶接品質に影響を与える 3 つの重要な課題です。これらの問題は、最適化された溶接パス、適合合金、フィラー材料、およびインテリジェント制御テクノロジを採用して溶接部の機械的特性とプロセス安定性を改善することで効果的に解決できます。これらのソリューションは、現在の工業生産の高い要件を満たすだけでなく、レーザー溶接技術のさらなる発展のための強固な基盤も提供します。
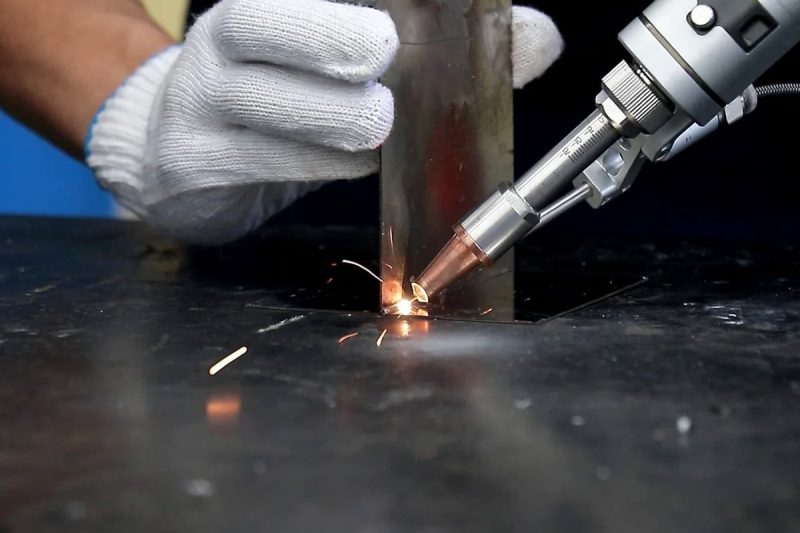
要約する
効率的で精密な溶接方法として、レーザー溶接技術は接合部の強度を向上させる大きな可能性を秘めています。材料の選択、レーザーパラメータ、接合部の設計、溶接後の処理を最適化することで、溶接継手の強度と信頼性を効果的に向上させることができます。溶接中の正確なレーザー出力制御、適切な表面洗浄、適切な接合部形状の設計、溶接後の熱処理は、熱変形を減らし、溶接継手の疲労耐性を高めるのに役立ちます。さらに、プロセス制御技術、特に機械学習と適応制御システムの応用の進歩により、レーザー溶接の安定性と品質がこれまでにないほど保証されています。これらすべての技術を統合することで、レーザー溶接は産業用途でより競争力が高まり、さまざまな業界に効率的で信頼性の高い溶接ソリューションをもたらします。
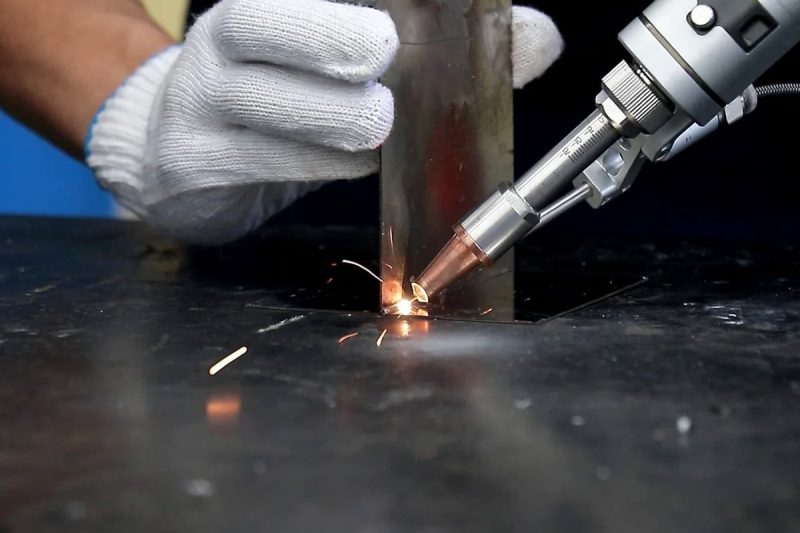
レーザー ソリューションを入手する
レーザー溶接分野のリーダーとして、 AccTek レーザー レーザージェネレーターは、優れた性能と精密技術を備えた高強度で高安定性の溶接ソリューションを提供します。当社は、各デバイスがお客様の特定のニーズに完全に適応できるように、お客様に合わせたソリューションに重点を置いています。材料の適合性、溶接プロセスの制御、溶接後の処理など、当社のレーザー技術は、最高の溶接効果を実現し、生産効率と製品品質を向上させるのに役立ちます。当社は、お客様の溶接プロセスが常に業界のトップレベルになるように、すべてのお客様に包括的な技術サポートとソリューションを提供することに尽力しています。レーザー溶接技術についてご質問やご要望がございましたら、お気軽にお問い合わせください。当社は、レーザー溶接への道を成功に導くために、最も専門的なコンサルティングとサービスを提供します。
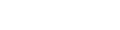
連絡先
- [email protected]
- [email protected]
- +86-19963414011
- No. 3 ゾーン A、Lunzhen 工業地帯、玉城市、山東省。
レーザー ソリューションを入手する