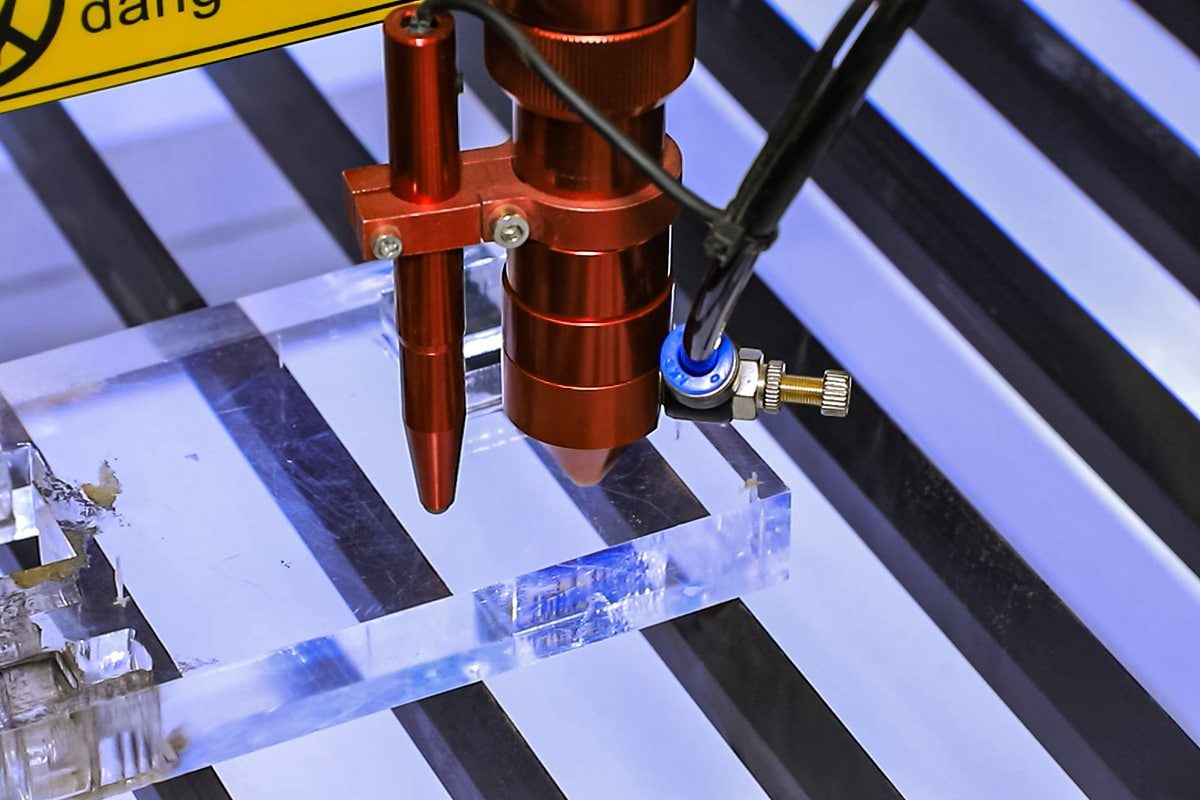
CO2 レーザー切断は高精度の複雑なデザインを実現できますか?
CO2レーザー切断は現代の製造業の基盤技術となり、産業界の材料加工方法に革命をもたらしました。集中したレーザービームの力を利用することで、この技術は金属、プラスチック、複合材など、さまざまな材料を正確に切断することができます。非接触であるため材料の変形が最小限に抑えられ、高精度で複雑なディテールが求められる用途に最適です。 CO2レーザー切断機 工業製造からクリエイティブデザインまで、さまざまな分野での使用が可能になり、その適応性と効率性が実証されています。
CO2レーザー切断は、複雑なデザインにおいて比類のない高精度を発揮し、複雑なパターンや細部を簡単に加工して、厳しい許容差を確保できます。これにより、完成品の品質が向上し、二次加工の必要性が減るだけでなく、コストが大幅に削減され、生産効率も向上します。業界の継続的な革新により、CO2レーザー切断は精密工学と高度な製造の重要な原動力となっています。
目次
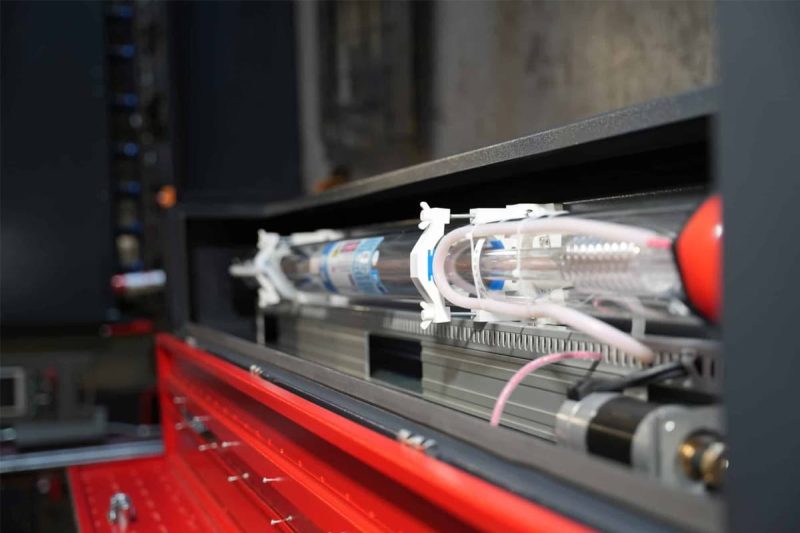
CO2レーザー切断の理解
CO2 レーザー切断は、その高精度と複雑な設計機能により、現代の製造および設計における重要な技術となっています。その原理と機能を深く理解することで、企業はその可能性を最大限に引き出し、多様なアプリケーションのニーズを満たすことができます。
CO2レーザー切断の原理
CO2 レーザー切断では、二酸化炭素レーザー発生器を使用して高エネルギーの赤外線ビームを放射し、極めて高精度で材料を切断、彫刻、エッチングします。その基本原理には、二酸化炭素、窒素、ヘリウムを混合したレーザー媒体を使用してレーザービームを生成する、レンズとレンズを介してビームを材料の表面に焦点を合わせる、CNC などの自動化システムを使用してレーザーヘッドを正確に誘導して複雑なパターンを完成させる、酸素、窒素、空気などの補助ガスを使用して切断効率を向上させ、酸化を防ぎ、スラグを除去する、などがあります。
切削技術と精密加工能力の概要
CO2 レーザー システムの切断プロセスは、レーザー ビームの生成、材料のエネルギー吸収による溶融または気化、溶融材料を除去してきれいなエッジを残すための補助ガスなど、高度に制御された手順を通じて精度と品質を保証します。その精密機能は、高精度 (切断許容範囲は ±0.1 mm)、材料の無駄を減らす狭い切断溝、再現性を保証する自動化システム、金属、アクリル、木材などのさまざまな材料に対する幅広い互換性に反映されています。
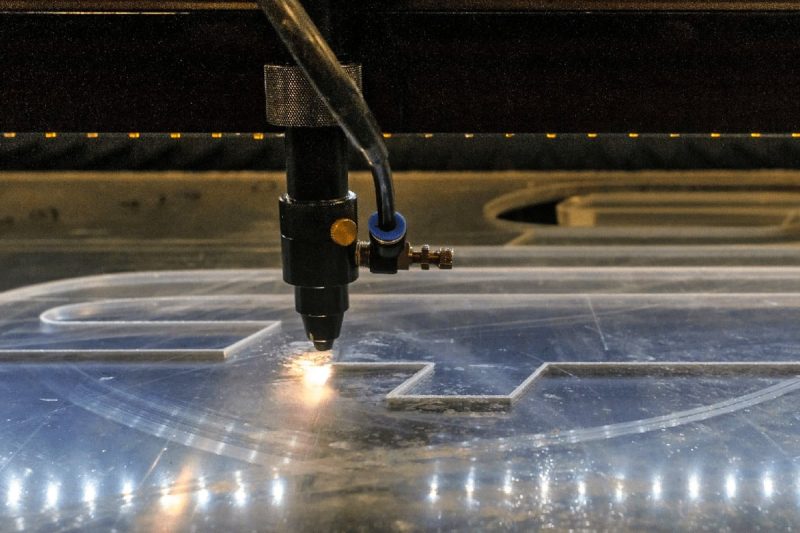
CO2レーザー切断精度に影響を与える主な要因
CO2 レーザー切断で高精度を達成するには、いくつかの重要な要素が関係します。これらの要素を理解して最適化することで、切断の精度と効率を高めることができます。
レーザービームの品質:レーザービームの品質は、M2 係数によって測定されます。M2 値が 1 に近いほど、レーザービームは集中しており、切断効果は細かくなります。高品質のレーザービームは、より小さなスポットを提供し、切断精度を向上させ、熱影響領域を減らすことができるため、切断パスの精度が保証されます。
フォーカス設定: フォーカス位置は切断エッジの細かさに影響します。 正しいフォーカス設定により、レーザービームが材料表面に適切なスポットを形成し、正確な切断深さと高品質のエッジが得られます。
システムの安定性:レーザー切断機の安定性が切断精度を決定します。レーザー出力が不安定であったり、機械的な振動があると、精度が変動します。安定したレーザー発生器と精密な動作システムにより、高精度の切断を継続的に行うことができます。
達成可能な許容範囲:CO2 レーザー切断は ±0.1 mm の精度を達成できるため、精密部品や電子製品の加工など、高精度が要求される分野に適しています。
エッジ品質: CO2 レーザー切断により、滑らかな切断エッジが得られます。高品質のレーザー ビームとフォーカス制御により、バリや熱影響部が削減され、切断品質が向上し、二次加工の必要性が減ります。
モーション コントロール システム: 切断機の位置決め精度と動的応答は、特に複雑な設計を扱う場合、切断パスの精度に直接影響します。
材料特性と厚さ: 材料の密度、熱伝導率、厚さはレーザーエネルギーの吸収効率に影響し、切断効果と精度に影響します。
切断速度とパワー: 切断速度が速すぎたりパワーが不十分だと切断が不完全になる可能性があり、パワーが大きすぎると材料が削れたり、エッジの品質に影響が出る可能性があります。
つまり、CO2 レーザー切断は、精密なレーザービーム制御とシステム安定性により、高精度の切断と高品質のエッジ効果を提供し、高精度加工分野で広く使用されています。
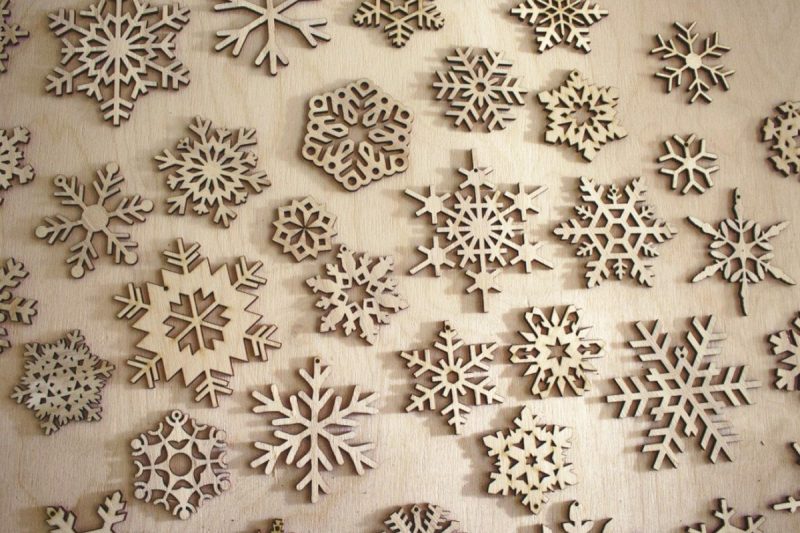
デザインの複雑さ
レーザー切断の分野では、複雑なデザインとは、細かいディテールや複雑なパターンを含み、厳しい許容差が求められるプロジェクトを指します。これらのデザインの実現には、機器の精度、安定性、処理能力に極めて高い要求が課せられ、処理技術にも新たな課題がもたらされます。
レーザー切断における複雑なデザインの定義
複雑な設計とは通常、次のような高い精度と慎重な操作を必要とする設計を指します。
- 微細なディテール: 微細彫刻や装飾パターンなどには、レーザー切断機による安定した高精度の位置決めが必要です。
- 複雑なパターン: 不規則な形状や階層的な幾何学的デザインが含まれる場合、切断パスには複数の調整と効率的な計画が必要です。
- 厳しい許容範囲: 極めて高い精度が求められる製造では、切断偏差をミクロンまたは 0.1 mm の範囲内で制御する必要があります。
これらの設計では、ビーム品質、動作制御、電力安定性など、レーザー切断装置のコア性能に高い要求が課せられます。
複雑なパターンの課題
複雑なパターンの処理は、特に多層または非対称のデザインを正確に再現する場合、レーザー切断技術における大きな課題です。特に顕著な問題は次のとおりです。
- 複雑なパス計画: 複雑なパターンを切断する場合、CNC システムは可変切断パスを最適化して、時間の損失とエラーを削減する必要があります。
- 熱の影響の蓄積: 複雑なパターンを長期間連続して切断すると、局所的に熱が蓄積され、材料の反りや変形を引き起こす可能性があります。
- 一貫性管理: 反復的な処理タスクでは、複雑な設計において各完成品が偏差や欠陥なく一貫性を保つようにする必要があります。
細部への挑戦
微細な切断を実現するには、レーザー切断機の性能に対する要求が高くなります。
- ビーム径の制限: 細い切断線を実現するには、レーザー ビームのスポット径を非常に小さくする必要があり、通常はマイクロメートルの範囲になります。
- 出力安定性: レーザー出力の電力変動は、細部の鮮明度とエッジの品質に直接影響し、切断の不均一やバリの原因となる可能性があります。
- 高い動的応答要件: レーザー ヘッドのモーション コントロールは、細かい領域で複雑な切断を実行するときにパスがオフセットされたり重複したりしないように、迅速に応答する必要があります。
これらの技術的要件により、レーザー切断では細かい部分を処理するのが非常に困難な作業になります。
厳しい許容差の課題
厳しい許容誤差は、特に医療や航空宇宙などの産業におけるハイエンド製造において不可欠な要件です。これらの要件を満たすために、レーザー切断は次のような困難に直面します。
- 高精度の位置決め: レーザー切断機には、切断ヘッドのミクロンレベルの位置決め精度を確保するために、高解像度の位置フィードバック システムを装備する必要があります。
- 熱変形補正:切断工程中に材料が熱により膨張したり変形したりすることがあります。レーザー切断機は、切断サイズを確保するためにリアルタイムで監視し、自動的に調整する必要があります。
- ビーム品質: 高品質の光学部品を使用することで、ビームの散乱と偏差を低減し、切断エッジの明瞭さと精度を確保できます。
厳しい許容誤差を満たしながら高い処理効率を維持する必要があるため、切断プロセスはさらに複雑になります。
これらの課題に対処することで、レーザー切断技術は複雑なデザインを実現するための不可欠なツールとなり、精密製造の世界に新たな可能性をもたらしました。
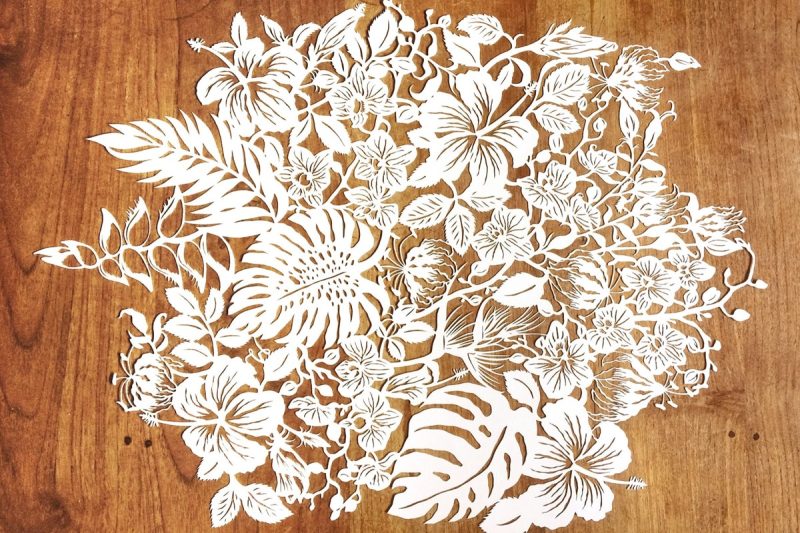
レーザー切断精度向上技術
レーザー切断の分野は常に進化しており、技術の進歩により精度、効率、汎用性が大幅に向上しています。これらの技術革新は、特に複雑なデザインやさまざまな材料の種類を扱う際の精度と一貫性に関する課題に対処します。以下では、CO2 レーザー切断における 3 つの重要なブレークスルーである、自動フォーカス調整、リアルタイム監視システム、CAD/CAM 統合について説明します。
オートフォーカス調整: さまざまな素材の精度を向上
自動フォーカス調整は、CO2 レーザー切断システムの革新的な機能です。この機能により、レーザーはさまざまな材料の厚さや表面の輪郭に合わせて動的に調整され、レーザー ビームが最適な焦点に留まるようになります。これは精密切断に不可欠です。
- さまざまな材質に対応: 金属、プラスチック、ガラスなど、さまざまな材質をきれいに切断するには、特定の焦点設定が必要です。自動フォーカスにより、手動で調整する必要がなくなり、ダウンタイムと人的エラーの両方が削減されます。
- エッジ品質の向上: 正しい焦点距離を維持することで、オートフォーカスは、特に複雑なパターンにおける、粗いエッジ、不完全なカット、または材料の焼けなどの問題を最小限に抑えます。
- 効率の向上: 自動調整により切断プロセスが合理化され、特に材料の切り替えや多層デザインでの作業時に、切断プロセスがより高速かつ信頼性が高まります。
リアルタイム監視システム: ライブ調整による一貫性の確保
リアルタイム監視システムにより、CO2 レーザー切断機は切断プロセス全体にわたって精度と一貫性を維持できます。これらのシステムは、センサーとフィードバック ループを使用して、出力、ビームの位置合わせ、材料の相互作用などのパラメータを監視します。
- 動的調整: 監視システムは、材料密度の変化や予期しない不規則性を考慮して、レーザー出力や切断速度などの設定を自動的に調整できます。
- 欠陥の最小化: 熱による歪みやビームのずれなどの問題をリアルタイムで検出することで、欠陥が発生する前に防止し、より高品質な結果を保証します。
- 生産性の向上: 継続的なフィードバックにより、カット後の検査ややり直しの必要性が減り、スループットとコスト効率が向上します。
CAD/CAM統合: 精密な設計と実行
コンピュータ支援設計 (CAD) およびコンピュータ支援製造 (CAM) ソフトウェアと CO2 レーザー切断システムの統合により、設計を物理的なコンポーネントに変換する方法が一変しました。この相乗効果により、シームレスな設計の実行と最適化が可能になります。
- 正確なパス プランニング: CAD/CAM ソフトウェアは正確な切断パスを生成し、最も複雑な設計でも完璧に実行できるようにします。これは、航空宇宙や医療機器製造など、厳しい許容誤差が求められる業界にとって非常に重要です。
- 材料の最適化: 高度なソフトウェアが切断経路と材料の使用をシミュレートし、無駄を減らしてコスト効率を高めます。
- カスタマイズ可能なパラメータ: オペレーターはソフトウェア内でレーザー ジェネレータの設定 (電力や切断速度など) を事前に定義できるため、複数の生産実行と材料間で一貫性を確保できます。
- 自動化とスケーラビリティ: CAD/CAM 統合により自動化されたワークフローがサポートされ、精度や品質を損なうことなくスケーラブルな生産が可能になります。
自動焦点調整、リアルタイム監視、CAD/CAM 統合の組み合わせにより、CO2 レーザー切断精度の新たな基準が確立されました。これらの技術の進歩により、切断精度が向上するだけでなく、効率が向上し、材料の無駄が減り、運用コストも削減されます。これらを組み合わせることで、メーカーは複雑な設計に取り組むことができ、幅広い用途にわたって優れた一貫性を実現できます。
これらの最先端技術を採用することで、企業は CO2 レーザー ジェネレーターの潜在能力を最大限に引き出し、現代の産業のニーズを満たす高品質の結果を提供できます。複雑なジュエリー デザイン、精密な医療部品、自動車部品など、これらの技術の進歩はレーザー切断ソリューションの未来への道を切り開いています。
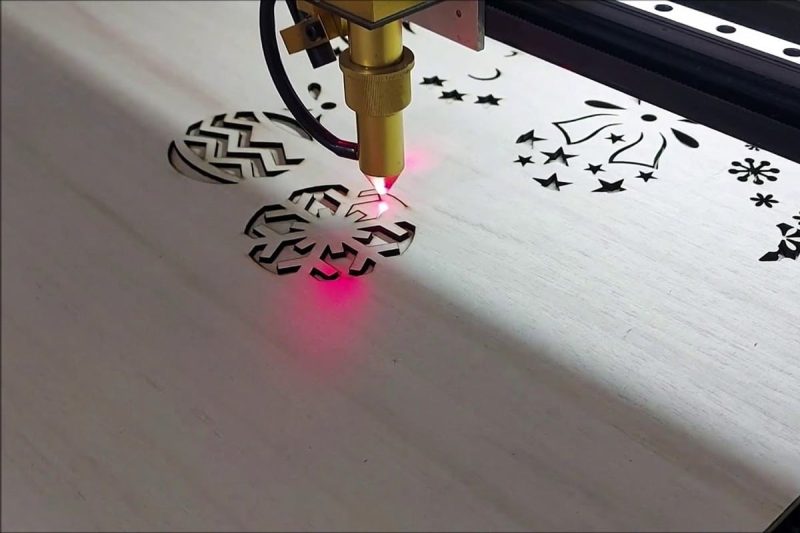
高精度CO2レーザー切断の利点
部品の品質と一貫性の向上
高精度 CO2 レーザー切断は、優れた表面仕上げと均一性を実現します。この技術により、大量生産でもカスタムメイドの部品でも、すべての製品でサイズと形状の一貫性が維持されます。従来の切断方法と比較して、CO2 レーザー切断は人為的エラーや機械精度の問題による偏差を大幅に削減し、製品の一貫性と品質を大幅に向上させます。特に自動車、航空宇宙、医療機器製造などの厳しい表面品質要件がある業界では、レーザー切断により、バリや不規則な形状が少なく、より滑らかなエッジが生成されます。
二次加工の必要性の削減
CO2 レーザー ジェネレータの精密切断機能により、切断後の調整の必要性が大幅に軽減されます。従来の切断方法では、切断エッジを微調整したり寸法を調整したりするために、複数の二次操作が必要になることがよくあります。対照的に、高精度レーザー切断では、1 回のパスで目的の切断結果を達成できるため、その後の調整にかかる時間とコストを節約できます。この利点は、精密ツール、航空宇宙部品、電子ハウジングなどの複雑な部品や精密部品の製造に特に役立ち、人件費と製造時間を削減します。
コスト削減と生産性の向上
高精度 CO2 レーザー切断は、二次加工を最小限に抑え、切断プロセスを最適化することで、生産効率を大幅に向上させます。レーザー ジェネレーターは、最小限の人的介入で効率的な切断を実行できるため、生産サイクルが短縮され、部品の品質が一定に保たれ、手直しや材料の無駄が減ります。この自動化された高精度な生産方法は、運用コストを削減するだけでなく、スループットも向上させ、ビジネス全体の生産性を向上させます。大規模メーカーにとって、高精度 CO2 レーザー切断は、生産プロセスを合理化し、競争力を高めるための重要なツールです。
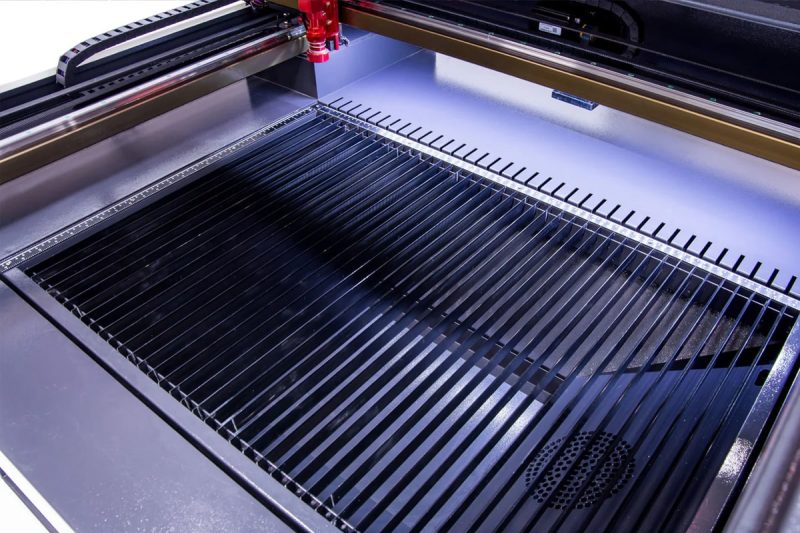
高精度切断を必要とする用途
高精度切断は幅広い分野で使用されており、主な用途には次のようなものがあります。
航空宇宙部品:航空宇宙産業では、部品の性能と安全性を確保するために、極めて高い切断精度が求められます。たとえば、エンジン部品、構造フレーム、精密部品の製造には、各部品がサイズ、形状、強度の点で厳しい要件を満たしていることを確認するためにレーザー切断技術が必要です。わずかな偏差でも全体の性能や安全性に影響を与える可能性があるため、高精度の切断技術が不可欠です。
エレクトロニクスとマイクロエレクトロニクス: 電子機器が小型化されるにつれて、マイクロエレクトロニクス部品の精度要件はますます厳しくなっています。チップのパッケージング、PCB ボードの切断、センサーの製造などのアプリケーションでは、レーザー切断により極めて高い精度を実現し、各回路とコンポーネントが正しく接続されるようにすることで、電子機器の信頼性とパフォーマンスを確保できます。
医療機器: 医療機器や装置、特に低侵襲手術器具やインプラントには、非常に高い切断精度が求められます。これらの機器は複雑な形状や極小サイズであることが多く、レーザー切断では金属、プラスチック、その他の生体適合性材料を極めて微細な精度で切断できるため、機能と安全性の面で機器が厳格な医療基準を満たすことが保証されます。
建築モデルとプロトタイプ: 建築設計とプロトタイプ作成では、レーザー切断技術を使用して複雑な建築モデルと繊細なコンポーネントを作成します。木材、プラスチック、金属などのさまざまな材料を正確に切断して、設計検証とサンプル製造を行うことができます。これは、設計コンセプトの実証、エンジニアリングソリューションのテスト、顧客とのコミュニケーションに非常に重要です。
これらのアプリケーションは、厳しい許容誤差と複雑な設計要件を満たし、製品の性能と品質を保証する高精度切削技術がさまざまな分野で重要な役割を果たしていることを実証しています。
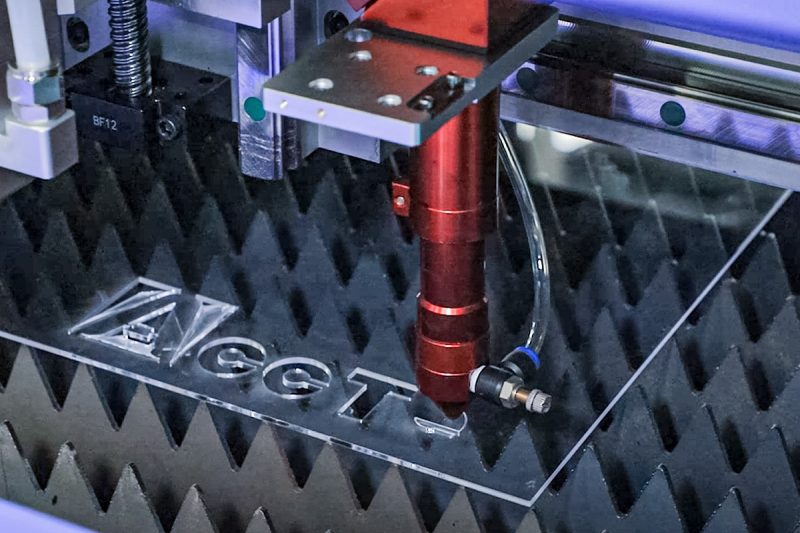
要約する
CO2レーザー切断技術は、高精度と優れた適応性を備え、複雑な設計と厳しい許容誤差の分野で比類のない利点を実証しています。レーザービームの品質から自動化機能まで、あらゆる側面で高精度切断の実現をサポートしています。航空宇宙の主要部品であれ、マイクロエレクトロニクスや医療機器の精密ニーズであれ、CO2レーザー切断は部品の一貫性と品質を向上させるだけでなく、二次加工コストを大幅に削減し、全体的な生産効率を向上させます。
将来を見据えると、技術の継続的な革新により、CO2レーザー切断はより多くの分野でその可能性を発揮し、製造業における精密加工や複雑な設計のためのより効率的で経済的なソリューションを提供します。この技術は、ハイエンド製造業の中核ツールであるだけでなく、業界をより正確で効率的な未来へと導き続けます。
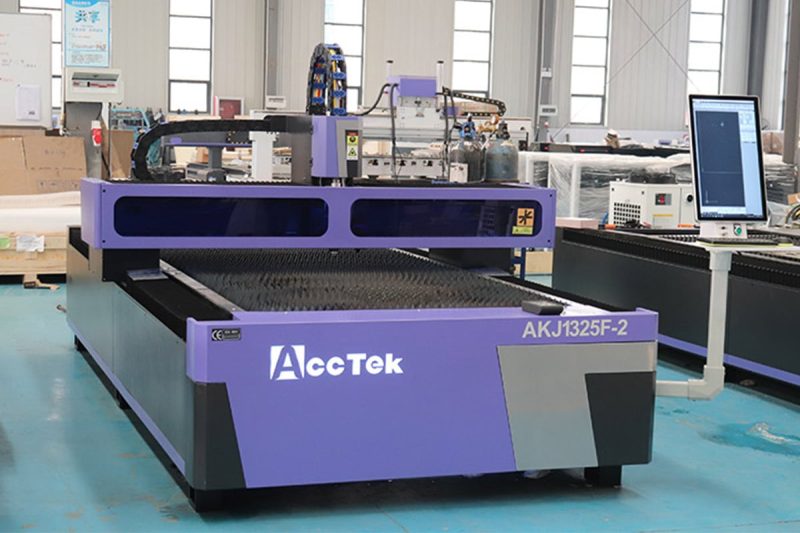
レーザー ソリューションを入手する
複雑なデザインを高精度にカットしたいですか? AccTek レーザー 完璧なソリューションを提供します。レーザー技術の専門家として、当社は、精密製造におけるさまざまなニーズを満たす高性能で信頼性の高い CO2 レーザー切断機をお客様に提供することに重点を置いています。航空宇宙部品から電子機器の微細加工まで、当社の切断装置は、優れた精度と安定性で複雑な設計上の課題に簡単に対応するのに役立ちます。今すぐ当社に連絡して、カスタマイズされたレーザー切断ソリューションを入手し、製造プロセスをより効率的かつ優れたものにしましょう。
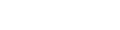
連絡先
- [email protected]
- [email protected]
- +86-19963414011
- No. 3 ゾーン A、Lunzhen 工業地帯、玉城市、山東省。
レーザー ソリューションを入手する