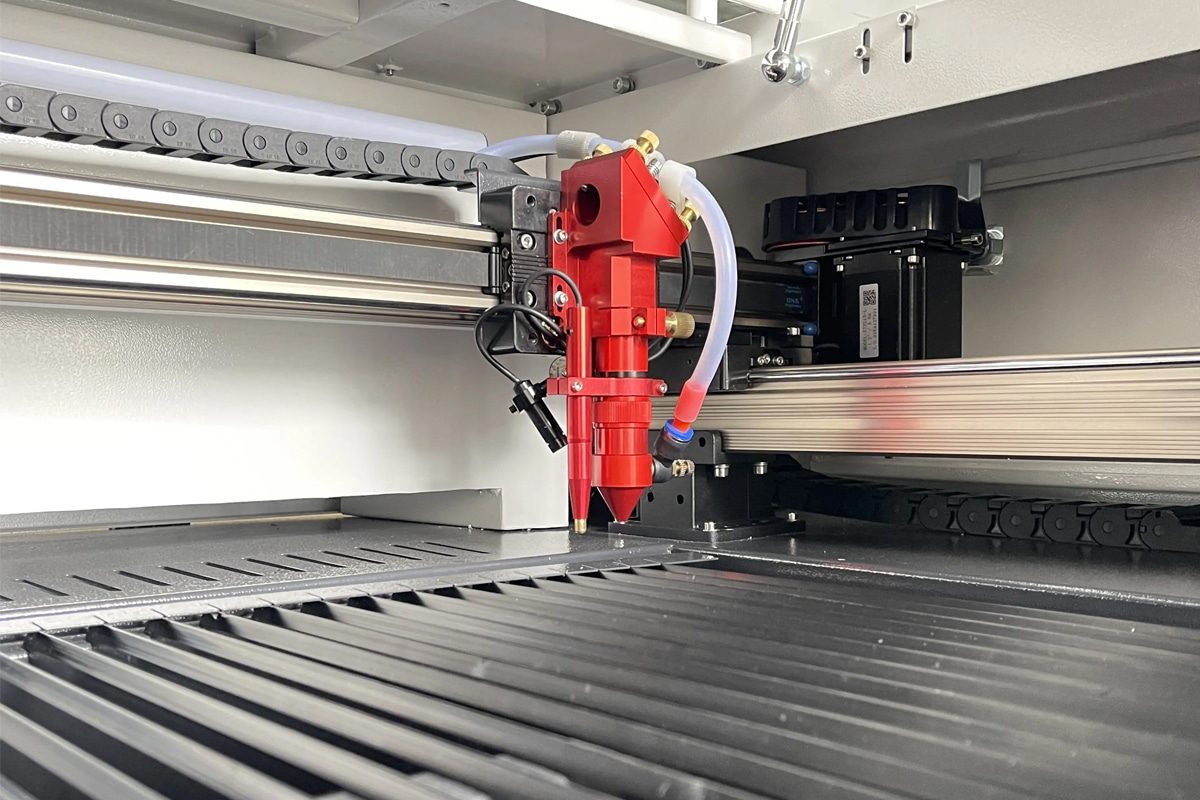
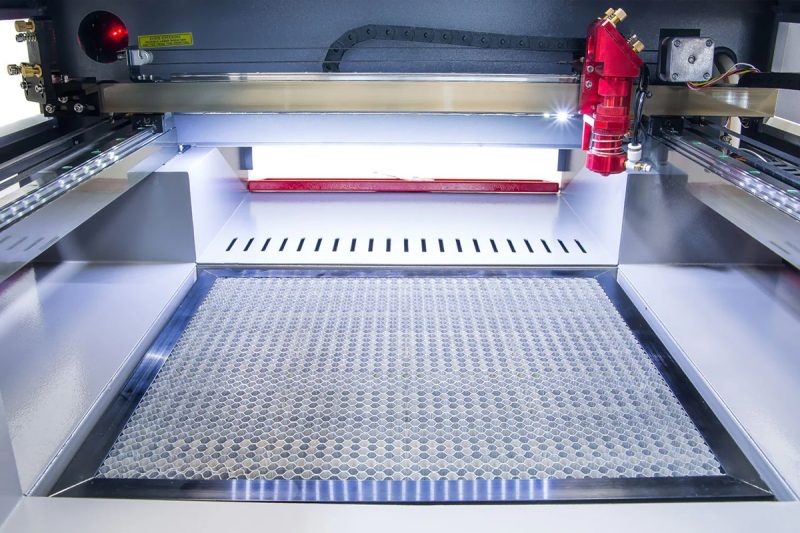
レーザー技術の基礎
レーザーとは何ですか?
レーザーの特性
レーザーには、他の光源とは異なる、産業用途に欠かせない次のような独自の特性がいくつかあります。
- コヒーレンス: レーザー光波はコヒーレントであり、一定の位相関係を持ちます。通常の光では放射される波は同期していませんが、レーザーによって生成される光波は同位相です。このコヒーレンスにより、レーザー ビームは長距離にわたって焦点を維持でき、切断やマーキングのプロセスで高い精度を実現します。
- 単色性: レーザーは単一の波長または色の光を放射します。これを単色光といいます。これは、幅広い色スペクトルを生成する従来の光源とは対照的です。レーザーの単色性により、特定の波長にエネルギーを集中させるのに非常に効果的であり、光がさまざまな材料とどのように相互作用するかをより細かく制御できます。
- 指向性: レーザーは、従来の光源に比べて発散が最小限に抑えられた、非常に指向性の高いビームで光を放射します。つまり、レーザー ビームはほとんど拡散せずに長距離を移動できるため、ビームのエネルギーが集中し、正確なカットや複雑なパターンが可能になります。
- 高強度: 光エネルギーを小さな点に集中させることができるため、レーザーは高出力密度を実現し、材料を溶解、蒸発、または除去することができます。この高強度により、熱影響部を最小限に抑えながら高速かつ効率的に材料を処理でき、周囲の材料の構造的完全性を維持できます。
- 偏光: レーザー光は偏光できるため、電界振動の方向を制御できます。この特性は、光の偏光が材料の吸収や挙動に影響を与えるレーザー溶接など、さまざまな用途に役立ちます。
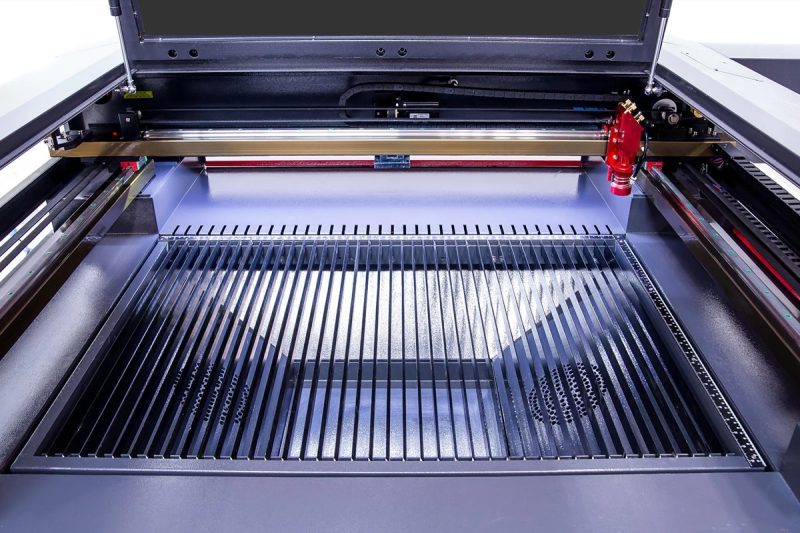
CO2レーザーの基礎
CO2レーザービームの特性
CO2レーザーは遠赤外線領域の光を発するため、次のようなさまざまな材料の加熱や切断に最適です。 金属, プラスチック、繊維、 木材など。以下の特性により、CO2 レーザーは工業用切断に特に効果的です。
- 高出力: CO2 レーザーは、数ワットから数キロワットの範囲の連続波 (CW) 出力を実現できるため、高速精密切断に適しています。
- 単色光: レーザーは特定の波長 (通常 10.6 µm) で光を放射し、幅広い材料による効率的なエネルギー吸収を保証します。
- 優れたビーム品質: ビームを小さなスポット サイズに集中させることができるため、正確で複雑なカットに必要な高い出力密度を実現できます。
- 高効率: CO2 レーザーは、他の種類のレーザーと比較して、電気から光への変換効率が比較的高いです。
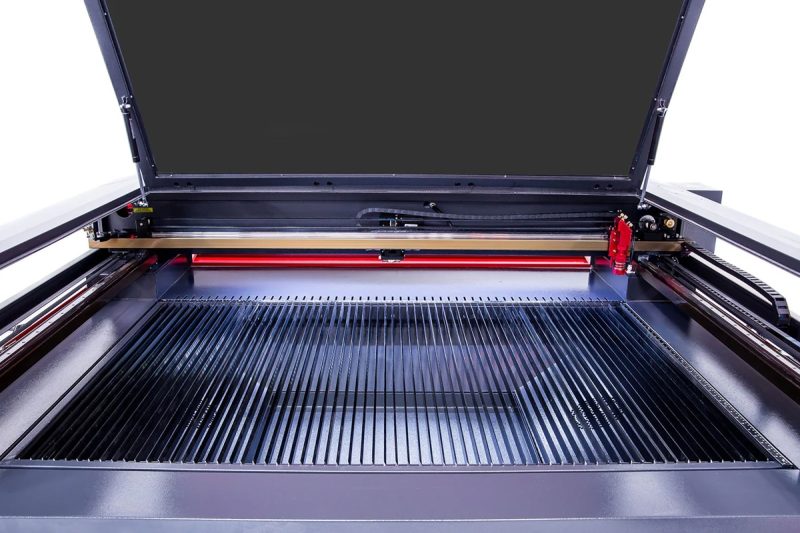
CO2レーザー切断機のコンポーネント
レーザー共振器
カッティングヘッドとフォーカスレンズ
アシストガスシステム
アシストガスは切断ヘッドのノズルから供給され、レーザービームと同軸に流れます。アシストガスは、以下の点で切断プロセスを強化する上で重要な役割を果たします。
- 溶融材料の除去: 溶融材料を切り口 (切断ギャップ) から吹き飛ばして、きれいな切断面を作ります。
- 材料の冷却: 切断部分の周囲を冷却し、熱による歪みを軽減します。
- 材料との反応: 軟鋼などの特定の材料では、酸素などの反応性ガスが発熱反応を起こし、切断速度が上がります。一方、窒素などの不活性ガスは酸化を防ぎ、酸化物のないきれいな刃先を生み出します。
CNC制御システム
冷却システム
排気・濾過システム
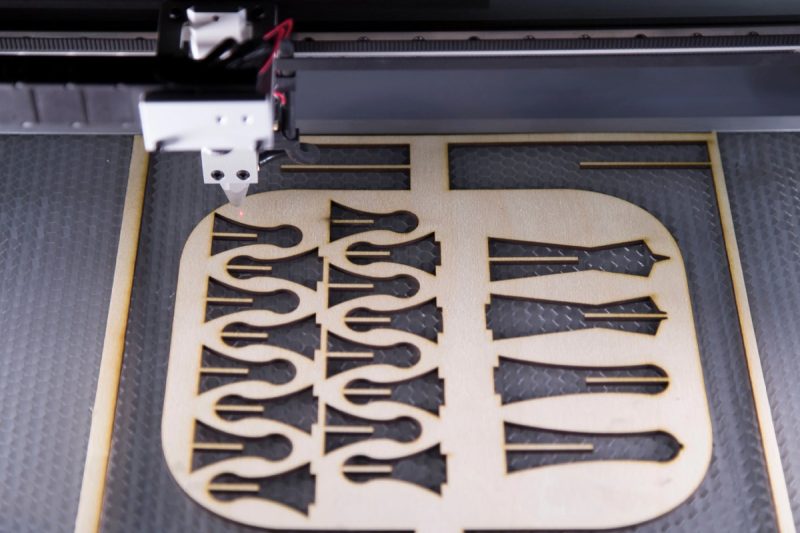
レーザービームの生成
誘導放出プロセス
気体分子の役割
CO2 レーザーの場合、レーザー媒体は主に二酸化炭素 (CO2)、窒素 (N2)、ヘリウム (He) で構成されるガス混合物です。各ガスはレーザー生成プロセスにおいて特定の役割を果たします。
- 二酸化炭素 (CO2): 励起時に光子を放出する活性レーザー媒体。CO2 分子は振動エネルギー状態間を遷移し、工業用切断アプリケーションに適した 10.6 マイクロメートルの波長で光子を放出します。
- 窒素 (N2): エネルギー伝達媒体として機能します。放電によって励起されると、窒素分子は準安定状態に達し、エネルギーを長時間保持します。励起された窒素分子は CO2 分子と衝突し、効率的にエネルギーを伝達して CO2 分子を励起状態にします。
- ヘリウム (He): CO2 分子の脱励起を促進し、システムから熱を放散させて、安定した動作を保証します。
人口逆転の実現
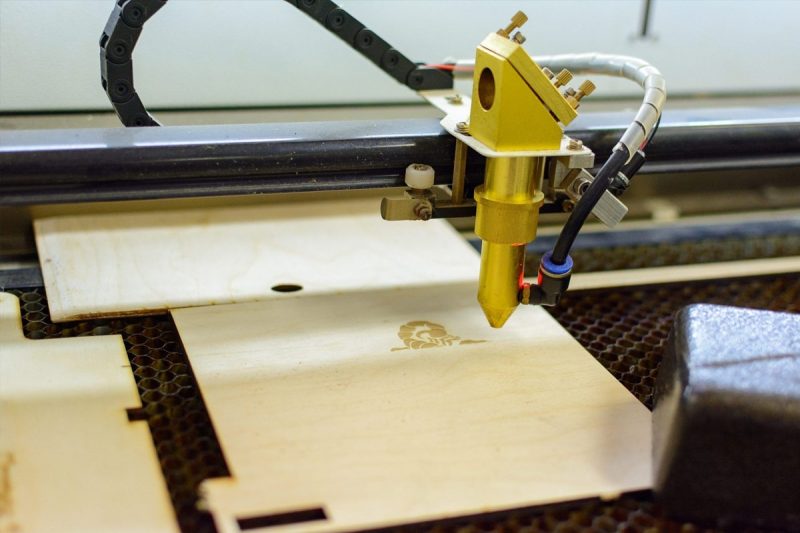
ビームの照射と集束
ビームパスとミラー
フォーカス機構
ビーム品質の重要性
ビーム品質は、CO2 レーザー切断機の性能に影響を与える重要な要素です。ビーム品質が高いと、レーザー ビームをより小さなスポット サイズに集中させることができ、出力密度が高まり、切断精度が向上します。ビーム品質の主な属性は次のとおりです。
- コヒーレンス: 光波が互いに同位相である度合い。コヒーレンスが高いと、明確で集中したビームになります。
- ビーム モード: ビームの断面全体にわたるビームのエネルギー分布を指します。TEM00 (横方向電磁モード) ビームはガウス分布を持ち、対称的なエネルギー プロファイルのため、精密切断に最適であると考えられています。
- 安定性と一貫性: 均一な切断を実現し、材料の無駄を最小限に抑えるには、一貫したビーム出力が不可欠です。
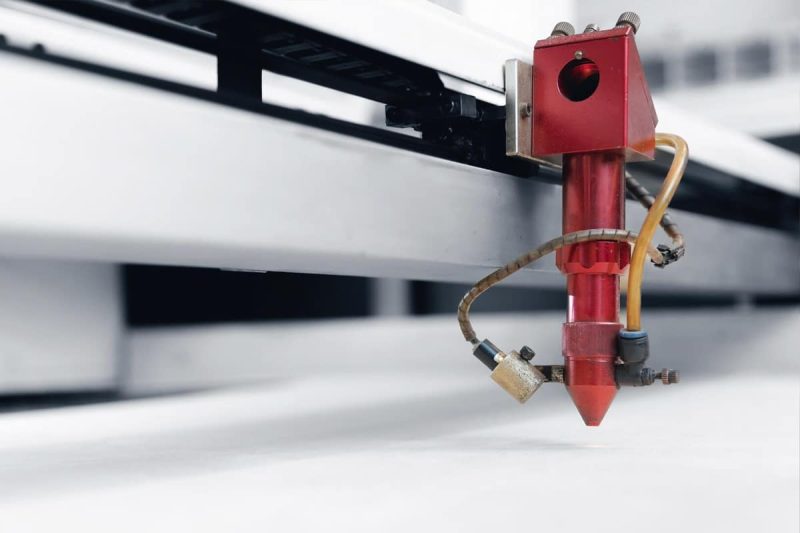
材料との相互作用
レーザーエネルギーの吸収
切断における熱処理
吸収されたレーザーエネルギーは熱に変換され、材料の切断を可能にする一連の熱プロセスを引き起こします。
- 溶融: 集中したレーザー ビームにより材料の温度が急速に上昇し、融点に達します。多くの場合、レーザー ビームは局所的な領域を加熱し、溶融池を形成します。
- 蒸発: 一部の材料では、レーザー エネルギーが十分に強力であるため、材料が直接蒸発し、狭い切り込みまたは切断が形成されます。このプロセスは、薄い材料や、材料の除去を最小限に抑える必要があるアプリケーションに特に役立ちます。
- 材料の除去: 材料が溶融または気化したら、切断を完了するために切断領域から除去する必要があります。この除去は、溶融または気化した材料を切断領域から吹き飛ばすアシストガスによって促進されます。
- 冷却と凝固: 切断プロセスの後、周囲の材料は急速に冷却され、エッジが凝固します。冷却速度と熱影響部 (HAZ) は、エッジの滑らかさや構造の完全性など、切断の品質に影響を与える可能性があります。
アシストガスの役割
アシストガスは、CO2 レーザー切断プロセスに不可欠な要素です。アシストガスは、切断ヘッドのノズルを通ってレーザービームと同軸に流れ、いくつかの重要な役割を果たします。
- 材料除去: アシストガスは、溶融および気化した材料を切断面から排出し、クリーンかつ連続的な切断を保証します。これは、厚い材料や密度の高い材料の場合に特に重要であり、溶融材料を迅速に除去することで再凝固を防ぎ、切断品質を向上させます。
- 化学反応: 一部のアプリケーションでは、酸素 (O2) などの反応性ガスがアシストガスとして使用されます。酸素は材料と反応して発熱反応を起こし、切断プロセスに熱を加え、切断速度と効率を高めます。これは通常、軟鋼の切断に使用されます。
- 酸化防止: 対照的に、ステンレス鋼やアルミニウムを切断する場合など、酸化を最小限に抑える必要がある場合は、窒素 (N2) やアルゴン (Ar) などの不活性ガスが使用されます。これらのガスは酸化を防ぐ保護雰囲気を作り出し、きれいで酸化物のない切断面を実現します。
- 冷却: アシストガスは材料とその周囲を冷却し、熱影響部 (HAZ) のサイズを縮小して熱変形を防ぐこともできます。
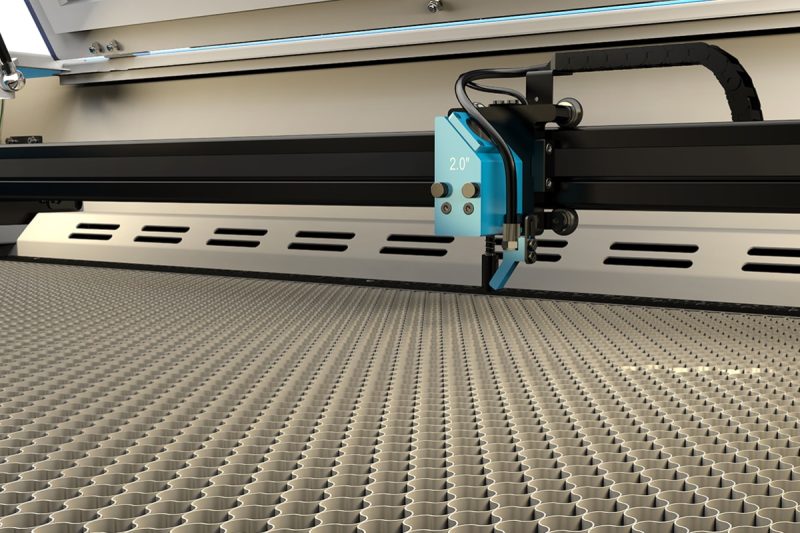
切断工程管理
CNCプログラミング
CO2 レーザー切断における CNC プログラミングの主な側面は次のとおりです。
- 切断パスの定義: CNC プログラムは、材料を切断するためにレーザー ビームがたどる正確なパスを指定します。このパスは、目的の形状と寸法を実現するために重要です。
- 切断パラメータの設定: プログラムは、レーザー出力、送り速度、焦点位置、アシストガス流量などのさまざまなパラメータを制御します。これらのパラメータは、材料の種類、厚さ、および必要なエッジ品質に基づいて調整できます。
- ピアシング戦略: 厚い材料の場合、CNC システムは、切断を続行する前に、特定のピアシング戦略を使用して最初の穴を作成する場合があります。これにより、最初から効率的できれいな切断が保証されます。
モーションコントロールシステム
モーション制御システムの主な機能は次のとおりです。
- 同期: 切断ヘッドの動きをレーザー ビームのオン/オフ状態と調整して、必要なときにのみ切断が行われるようにします。
- 加速と減速の制御: 切断ヘッドの速度を最適化して、方向転換時のスムーズな移行を実現し、急激な動きを防ぎ、一貫した切断品質を維持します。
- リアルタイム調整: 材料の厚さの変化や複雑な形状などの切断条件に基づいて、切断ヘッドの速度と位置を調整します。
監視とフィードバック
監視およびフィードバック メカニズムの例には次のものがあります。
- 高さ検知: 高さセンサーは、切断ヘッドと材料表面の間の距離を継続的に監視します。切断ヘッドの位置を調整して最適な焦点距離を維持し、一貫した切断深さとエッジ品質を確保します。
- レーザー出力とビーム安定性の監視: センサーはレーザーの出力とビーム安定性を追跡し、一貫したエネルギー供給を維持するための調整を可能にします。
- アシストガスの圧力と流量の監視: アシストガスの圧力と流量を監視することで、ガスが一貫して供給されるようになり、きれいな切断と適切な材料除去に貢献します。
- 熱および振動センサー: 切断精度に影響を与える可能性のある過度の熱や振動を検出します。システムは、欠陥や損傷を防ぐために切断プロセスを遅くしたり一時停止したりできます。
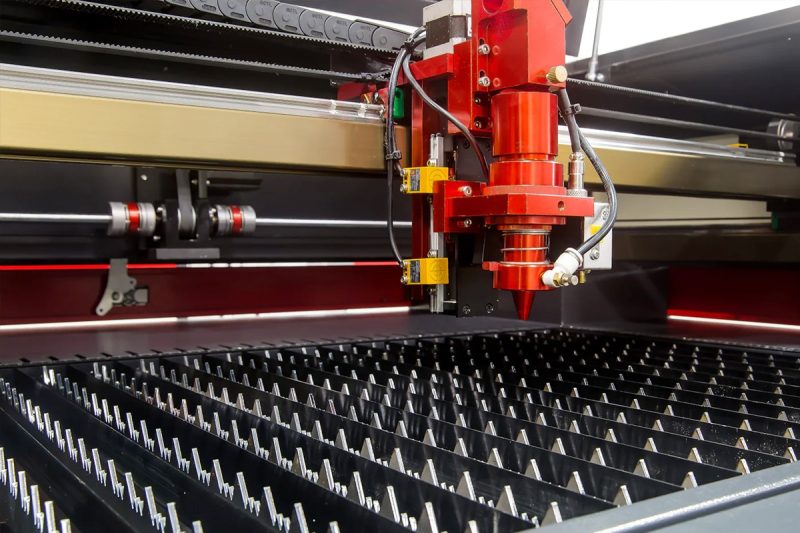
CO2レーザー切断に適した材料
非金属材料
CO2 レーザーは、レーザーの赤外線波長をより効率的に吸収する非金属材料の切断に特に効果的です。このため、CO2 レーザー切断機は繊維、木工、看板などの業界に非常に適しています。
- 木材CO2 レーザーは、木材の切断、彫刻、マーキングに広く使用されています。きれいな切断面と複雑なデザインを実現できるため、家具、装飾品、模型製作などの用途に最適です。
- アクリル: 看板やディスプレイの製造によく使用されるアクリルは、CO2 レーザーで滑らかに切断され、追加の仕上げ工程なしで、磨かれた炎仕上げのエッジを作成します。
- プラスチック: さまざまなタイプのプラスチック、例えば ポリカーボネート、ポリエステル、 ポリプロピレンCO2 レーザーで切断できます。レーザー切断は、包装、電子機器、自動車業界でカスタムプラスチック部品に使用されています。
- 革と 生地CO2 レーザーは、皮革や合成繊維、天然繊維の正確な切断とほつれの最小化を実現します。ファッション、室内装飾、履物業界でよく使用されています。
- ゴム: 特定のゴムは、ガスケット製造やその他の工業用途に加工できます。レーザーにより、残留物が最小限に抑えられ、きれいな切断が行えます。
有機材料
CO2 レーザー切断機は、熱による歪みを最小限に抑えながら材料を気化できるため、さまざまな有機材料を切断することもできます。これらの材料には次のものが含まれます。
- フォーム: 薄いフォームシートをカットして、梱包用挿入物、カスタムパッド、その他の精密フォーム製品を作ることができます。
- 紙と段ボール: CO2 レーザーは紙製品の精密切断に非常に効果的であり、包装、招待状、アート用途に適しています。
金属(制限あり)
複合材料
ラミネートやコーティングされた繊維などの特定の複合材料は、CO2レーザーで加工できます。ただし、レーザーカット時に有害な煙を放出する材料を避けることが重要です。 PVC およびいくつかの繊維複合材料。
- ラミネートシート: CO2 レーザーは、家具、インテリアデザイン、電子機器など、高精度が求められる業界でラミネート材料の切断によく使用されます。
- コーティングされた生地: レーザー切断により、室内装飾品、アウトドア用品、カスタム衣料によく使用されるコーティングされた生地に複雑なパターンを作成できます。
CO2レーザー切断に適さない材料
CO2 レーザーは多用途ですが、有毒ガスの放出や過度の溶解の可能性があるため、一部の材料はレーザー加工に適していません。これには次のものが含まれます。
- グラスファイバーとカーボンファイバー: これらの材料は燃えて有害な煙を放出する傾向があるため、CO2 レーザー切断には適していません。
- 反射性金属: 銅や真鍮などの厚くて反射率の高い金属は、レーザーエネルギーの多くを反射し、切断が非効率的になり、機器が損傷する可能性があるため、CO2 レーザーには適していません。
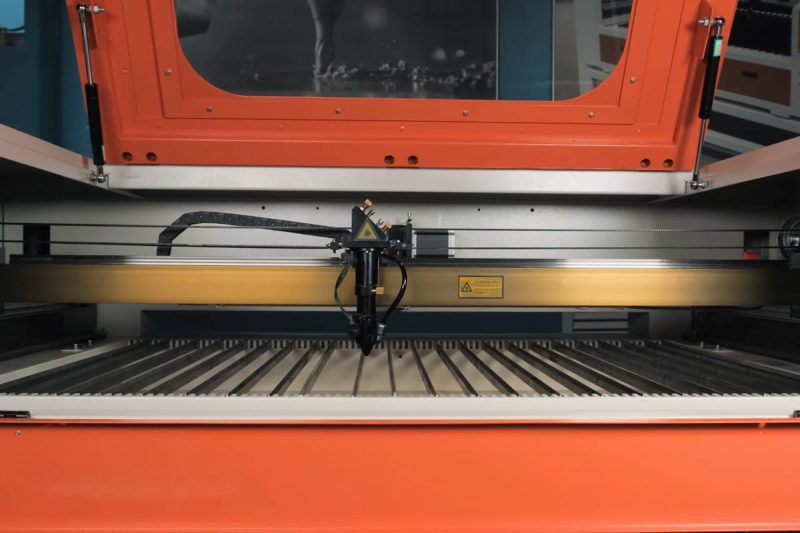
CO2レーザー切断の利点と限界
CO2レーザー切断の利点
- 高精度と正確性: CO2 レーザー切断機は、非常に高い精度と正確性を備えており、厳しい許容誤差で複雑で詳細な切断が可能です。レーザー ビームは正確に制御できるため、意図した切断パスからの逸脱を最小限に抑え、きれいで鋭いエッジが得られます。このため、CO2 レーザーは、標識、電子機器、自動車製造など、複雑な形状と細かいディテールが求められる業界に最適です。
- 滑らかできれいな切断: CO2 レーザーは、バリ取りや研磨などの二次仕上げ工程を必要とせずに、滑らかできれいなエッジを生成します。レーザー切断の非接触性により、機械的な変形が最小限に抑えられ、欠けたりほつれたりする可能性のある材料でも高品質の仕上がりが保証されます。
- さまざまな材料に対応できる汎用性: CO2 レーザー切断機は汎用性が高く、木材、プラスチック、繊維、皮革、ガラス、アクリル、薄い金属など、さまざまな材料を加工できます。この汎用性により、製造や加工からクリエイティブや芸術の用途まで、さまざまな業界にとって貴重なツールとなります。
- 高速切断: 従来の切断方法と比較して、CO2 レーザーは、特に薄い非金属材料に対して高速切断を実現できます。これにより、産業環境での生産性が向上し、サイクル時間が短縮され、出力が増加します。
- 非接触プロセス: レーザー切断は非接触プロセスです。つまり、ツールと材料の物理的な接触はありません。これにより、ツールの摩耗のリスクがなくなり、メンテナンス コストが削減され、材料への機械的ストレスが最小限に抑えられます。その結果、CO2 レーザー切断は、デリケートな材料や敏感な材料に特に有利です。
- 材料の無駄の削減: CO2 レーザー切断機は、狭い切断幅 (切断幅) を生成するため、材料の無駄が削減され、1 枚の材料から切断できる部品の数を最大限に増やすことができます。高度なネスティング ソフトウェアにより、材料の使用をさらに最適化できるため、コスト削減に貢献します。
- 自動化および統合機能: CO2 レーザー切断機は自動化された生産ラインに簡単に統合できるため、効率が向上し、人件費が削減されます。自動ロード/アンロード システム、CNC 制御、リアルタイム監視などの機能により、生産性が向上し、複雑で大規模な製造プロセスが可能になります。
- 最小限の熱影響部 (HAZ): 集中したレーザー ビームにより、切断部分の周囲の熱影響部が最小限に抑えられ、熱による歪みが軽減され、材料の構造的完全性が維持されます。これは、精度と最小限の変形が重要な用途では特に重要です。
CO2レーザー切断の潜在的な欠点
- 金属切断能力の制限: CO2 レーザーは薄い金属を切断できますが、アルミニウム、真鍮、銅などの厚い金属や反射率の高い金属を切断する場合、一般的にファイバー レーザーほど効果的ではありません。これらの材料はレーザー エネルギーを反射するため、切断が非効率的になり、機器が損傷する可能性があります。
- 高いエネルギー消費: CO2 レーザーは動作に大量の電力を必要とするため、他の切断技術に比べてエネルギー コストが高くなる可能性があります。エネルギー消費を抑えるには、冷却システムと電気システムを適切にメンテナンスする必要があります。
- メンテナンス要件: CO2 レーザー切断機は、固体レーザーに比べてメンテナンスが複雑です。最適なパフォーマンスを維持するには、レーザー共振器、光学系 (ミラーとレンズ)、補助ガス システムを定期的にクリーニング、調整、交換する必要があります。これにより、ダウンタイムが発生し、追加の運用コストが発生する可能性があります。
- 煙やガスの排出: 切断プロセス中、特定の材料から煙や潜在的に危険なガスが排出されることがあります。作業者の安全を確保し、環境規制に準拠するには、効果的な排気システムと濾過システムが必要です。換気が不十分であったり濾過が不十分だと、有害な暴露につながる可能性があります。
- 厚い材料の切断効率が低い: 厚い材料を切断する場合、CO2 レーザーでは低速と高出力設定が必要になることがあり、全体的な切断効率が低下する可能性があります。これは、厚い金属をより高速かつ効率的に切断できるファイバー レーザーと比較すると大きな欠点です。
- 初期投資コスト: CO2 レーザー切断機の購入と設置には、多額の初期投資が必要です。長期的なメリットは初期コストを上回ることが多いですが、中小企業では導入に経済的な障壁が立ちはだかる場合があります。
- 反射性材料の課題: CO2 レーザーは、研磨された金属などの反射率の高い材料では扱いにくい場合があります。これらの材料はレーザー光線を光学部品に反射し、損傷を引き起こしたり、切断効率を低下させたりする可能性があります。特殊なコーティング、より高い出力レベル、または代替レーザー ソース (ファイバー レーザーなど) が必要になる場合があります。
- セットアップとプログラミングの複雑さ: CO2 レーザー切断機を操作するには、CNC プログラミング、材料の選択、およびパラメータの最適化に関する専門知識が必要です。複雑なジョブでは詳細なプログラミングと微調整が必要になる場合があり、特にカスタムまたは小バッチの実行ではセットアップ時間が長くなる可能性があります。
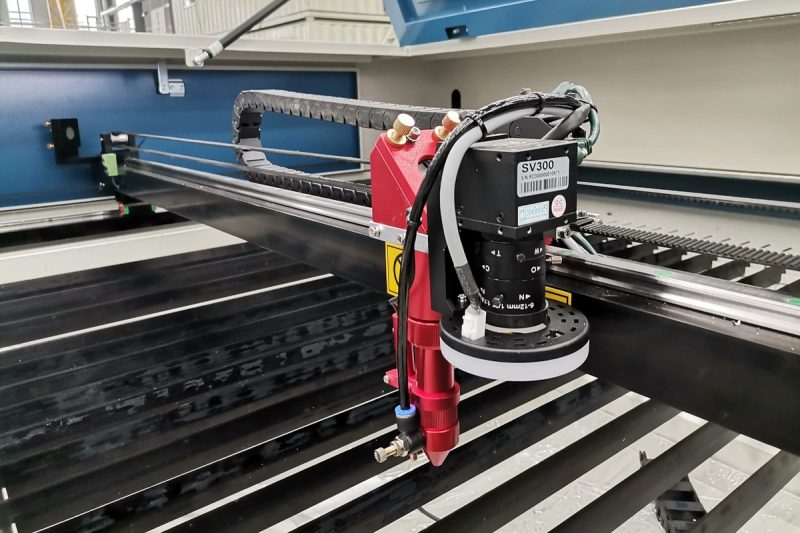
安全上の考慮事項
レーザーの安全対策
CO2 レーザーは、さまざまな材料を切断できる高出力のビームを生成するため、安全性が最優先されます。次の対策は、レーザー操作に伴う潜在的なリスクを軽減するのに役立ちます。
- レーザー安全ゴーグル: オペレーターおよび付近の作業員は、CO2 レーザーの特定の波長 (10.6 マイクロメートル) から保護するように設計された適切なレーザー安全ゴーグルを着用する必要があります。これにより、直接または反射されたレーザー光線による目の損傷を防ぐことができます。
- 密閉された作業エリア: CO2 レーザー切断機には、レーザー光線を封じ込めて偶発的な被爆を防ぐため、完全に密閉された作業エリアまたは部分的に密閉された作業エリアが備えられていることがよくあります。安全インターロックにより、エンクロージャが開いている場合は機械が作動しないようになっています。
- レーザー警告標識: 高出力レーザーが使用されていることを示す適切な標識を機械の周囲に表示する必要があります。これにより、作業員に潜在的な危険を警告し、レーザー領域への不正アクセスを制限します。
- 定期的なビーム パスの位置合わせチェック: レーザー ビームの位置合わせがずれると、意図しない反射が発生し、重大な危険が生じる可能性があります。ミラーと光学コンポーネントを定期的に検査して位置合わせすると、このリスクを軽減できます。
- 防火設備: 高エネルギーのレーザー光線は熱を発生し、可燃性物質や粉塵に引火する可能性があります。消火器、防火ブランケット、その他の防火設備をすぐに利用できるようにしておく必要があります。作業者は可燃性物質のない清潔な作業スペースを維持する必要があります。
- 換気と煙の除去: CO2 レーザーで特定の材料を切断すると、煙、煙、潜在的に危険なガスが発生します。切断エリアからこれらの副産物を除去し、オペレーターの安全を確保し、環境規制に準拠するには、堅牢な換気および煙の除去システムが不可欠です。
ガスおよび電気部品の取り扱い
ガスの取り扱い
- 補助ガスの安全性: CO2 レーザー切断機は、切断プロセスを補助するために酸素、窒素、圧縮空気などの補助ガスを使用します。これらのガスは、不適切な使用や漏れによって火災、爆発、窒息などの安全上のリスクが生じる可能性があるため、慎重に取り扱うことが重要です。
- 適切な保管: ガスボンベは、熱源、火花、直射日光を避け、換気の良い場所に安全に保管する必要があります。
- 圧力調整: 機器を損傷したり安全上の危険を生じさせたりする可能性がある過剰な圧力を防ぐために、ガス圧力を監視および調整する必要があります。
- 漏れ検出: 石鹸水や特殊なガス検知器などの承認された検出方法を使用して、ガス管、バルブ、接続部に漏れがないか定期的に検査します。
- 排気および換気システム: 排気システムが適切に保守され、切断中に発生する有毒ガス、煙、粒子を除去するように機能していることを確認します。これにより、有害物質の蓄積を防ぎ、作業場の空気の質を維持します。
電気部品の取り扱い
- 高電圧の安全性: CO2 レーザー切断システムは高電圧で動作するため、電気の安全性が極めて重要です。電気のメンテナンス、修理、調整は、訓練を受けた有資格者のみが行う必要があります。
- ロックアウト/タグアウト (LOTO): ロックアウト/タグアウト手順を実装して、電気システムの電源が切断され、メンテナンス中に誤って再通電されないようにします。
- 電気検査: 電気接続、ケーブル、コンポーネントに摩耗、損傷、腐食の兆候がないか定期的に検査します。電気的な危険を防ぐために、問題があればすぐに対処してください。
- 接地と絶縁: 感電やショートを防ぐために、すべての電気部品は適切に接地および絶縁する必要があります。接地は、迷走電流を安全に迂回させるのに役立ちます。
- コントロール パネルの安全性: オペレーターは、コントロール パネル、緊急停止ボタン、インターロック システムの適切な使用方法についてトレーニングを受ける必要があります。緊急時には、これらのシステムによりレーザーを即座にシャットダウンして、怪我や機器の損傷を防ぐことができます。
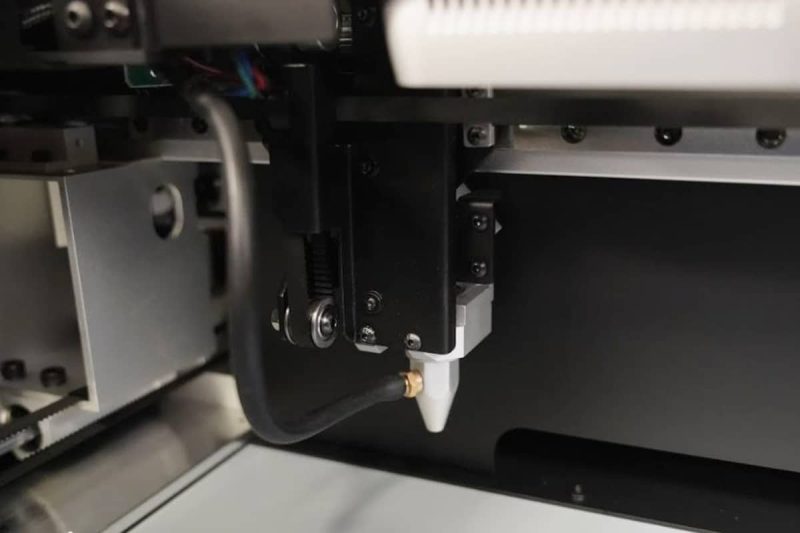
まとめ
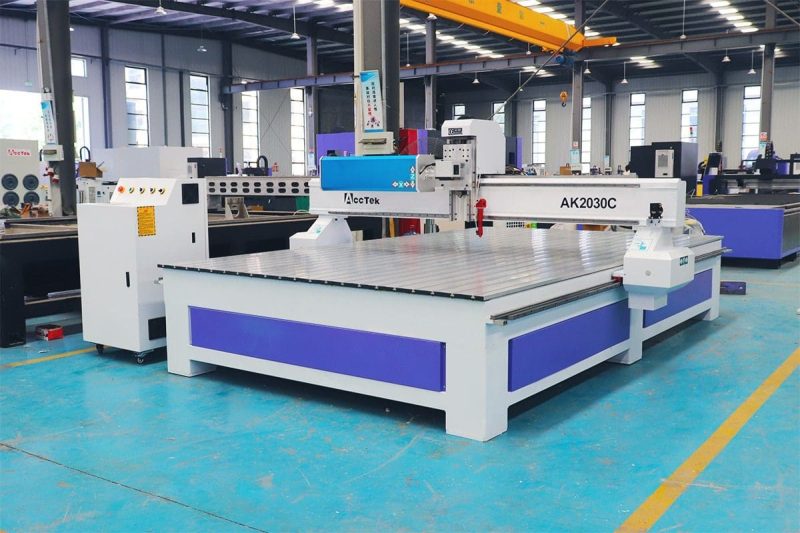
レーザー切断ソリューションを入手
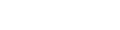
- [email protected]
- [email protected]
- +86-19963414011
- No. 3 ゾーン A、Lunzhen 工業地帯、玉城市、山東省。