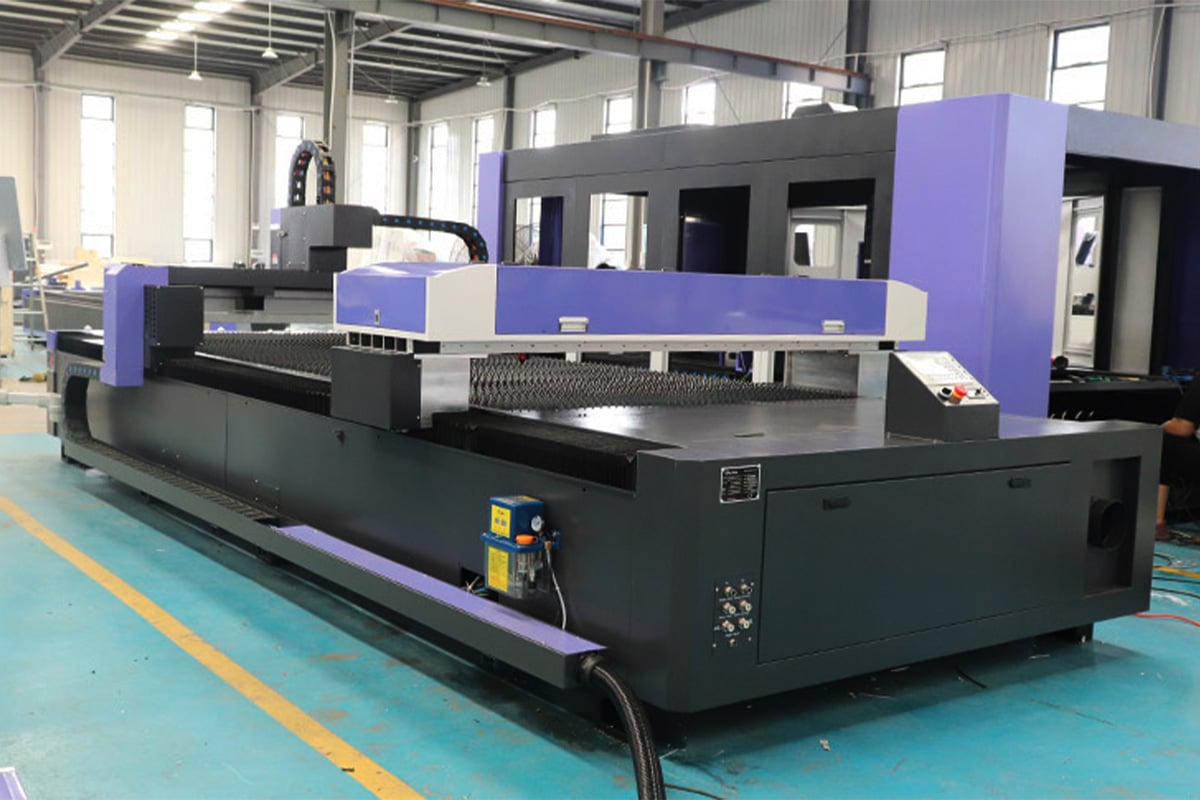
CO2 レーザー切断で最小の切開幅を実現するにはどうすればよいでしょうか?
CO2レーザー切断技術は、高精度、高速、非接触加工などの利点から、金属加工、プラスチック、木材、布地など、様々な材料の切断工程に広く利用されています。カーフ幅とは、切断工程においてレーザービームによって形成される切込みの幅を指します。この指標は、切断の精度と品質に直接影響します。切込み幅が狭いほど、より微細な加工効果が得られ、製品精度の向上、材料の無駄の削減、生産コストの削減につながります。したがって、カーフ幅はレーザー切断品質を測定するための重要な基準です。
切込み幅の制御は、製品品質の向上だけでなく、材料の利用率、後工程の利便性、そして生産効率全体にも密接に関係しています。メーカーにとって、切込み幅の最適化は生産コストの抑制に直結します。特に大規模生産においては、切込み幅が大きすぎると材料の無駄が生じ、後工程の円滑な進行に支障をきたす可能性があります。そのため、切込み幅の正確な制御は、効率的で低コストな生産を実現するための重要な要素となります。
目次
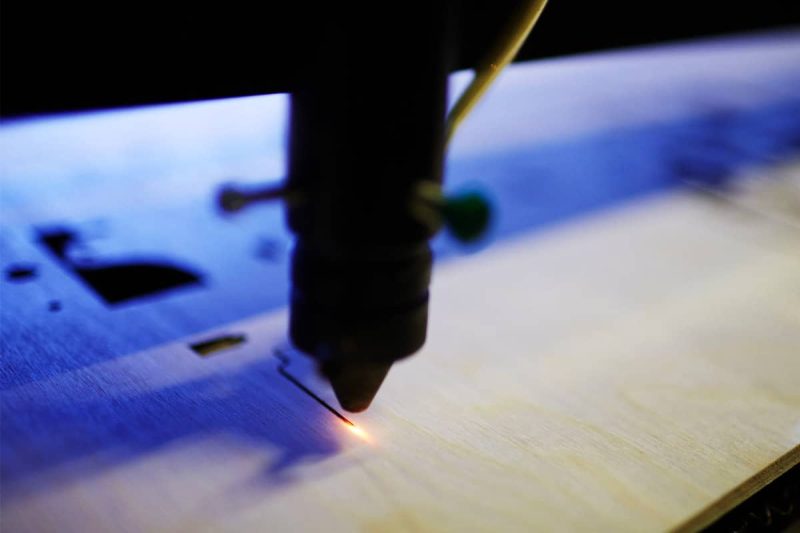
CO2レーザー切断のカーフ幅に影響を与える主な要因
CO2レーザー切断技術の切断効果は多くの要因の影響を受けますが、カーフ幅は最も重要な指標の一つです。これらの要因を適切に調整・最適化することで、メーカーは生産効率を向上させ、材料ロスを削減しながら高精度を確保することができます。以下は、カーフ幅に影響を与える主要な要因とその最適化戦略です。
レーザー焦点サイズ:レーザー焦点サイズはスポット径に直接影響し、スポット径が小さいほど切開幅は狭くなります。焦点精度が高いほど、レーザービームエネルギーの集中度が高くなり、切断精度が向上します。切開幅を最適化するには、適切な焦点距離レンズを選択することが重要です。一般的に、焦点距離の短いレンズは焦点径を小さくできるため、より精密な切断効果が得られます。様々な材料や切断要件に応じて、焦点距離を調整することで焦点サイズを最適化し、最適な切断効果を確保できます。
レーザー出力:レーザー出力はレーザービームの熱エネルギー強度を直接決定し、切断工程における溶融、蒸発、切断効果に影響を与えます。レーザー出力が高すぎると、切込みが広くなりすぎたり、材料を焼き切ってしまう可能性が高くなります。一方、出力が低すぎると、材料を完全に貫通できず、切断が不完全になる可能性があります。材料の厚さや特性に応じて、レーザー出力を最適な値に調整することが重要です。例えば、厚い材料の場合は出力を適切に増加させる必要があり、薄い材料の場合は、切込みが広くなりすぎないように出力を低下させます。出力を正確に調整することで、メーカーは正確で効率的な切断を実現できます。
切断速度:レーザー切断においては、切断速度も重要な役割を果たします。切断速度を適切に上げることで、熱影響部(HAZ)を減らし、溶融材料が切断端面に与える影響を軽減できるだけでなく、生産効率も向上します。しかし、切断速度が速すぎると、レーザー光が材料に十分に浸透できず、切断が不完全になる可能性があります。逆に、速度が遅すぎると、切断幅が広くなりすぎて過剰な溶融物が発生する可能性があります。切断効果を最適化するには、材料の種類と厚さに応じて切断速度を正確に調整し、切断幅を最小限に抑える必要があります。
補助ガスの種類と圧力:補助ガスはレーザー切断において重要な役割を果たします。一般的に使用される補助ガスは、酸素、窒素、空気です。酸素は切断工程中の燃焼反応を促進するため、鉄鋼などの材料の切断に適しています。窒素は酸化を抑えるため、ステンレス鋼などの材料に適しています。空気は経済性が高いため、さまざまな材料に広く使用されています。ガスの種類に加えて、ガス圧力も切断品質に影響します。適切なガス圧力は、溶融物を除去し、切断端への付着を防ぐのに役立ち、それによって切断幅を狭めることができます。ガス圧力が低いと、溶融物を効果的に除去できず、切断幅が広がる可能性があるため、切断効果を最適化するには、適切なガス圧力とタイプを選択する必要があります。
材料特性:異なる材料の特性は、レーザー切断の精度に大きな影響を与える可能性があります。吸収率、熱伝導率、融点などの材料特性は、レーザー光線の透過効率と切断品質に直接影響します。反射率の高い材料(アルミニウム、銅など)は、レーザー光線の反射・散乱を引き起こし、切断効果を低下させる傾向があります。これらの材料の場合、レーザーパラメータを最適化し、特にパワー密度を高めて、レーザーが材料に効果的に浸透できるようにする必要があります。一方、鋼鉄などの反射率の低い材料は切断が容易です。異なる材料を切断する場合、メーカーは材料特性に応じて切断パラメータを調整し、最高の切断品質と最小の切開幅を確保する必要があります。
切断パスの最適化:切断パスの最適化は、切開幅を制御する上で非常に重要です。滑らかな切断パスは、レーザービームの方向転換時の誤差を低減し、不規則な切開を回避します。特に複雑な形状を切断する場合、パスを合理的に設計し、旋回や緊急停止を減らすことで、切断精度を大幅に向上させることができます。さらに、送りと引き戻しの戦略を最適化することで、材料のアブレーションを低減し、過度の加熱による切開部の変形を防ぐこともできます。パスを設計する際には、急な旋回や不均一な経路を可能な限り避け、切断プロセス中のエネルギーが均等に分散されるようにすることで、切開幅を制御する必要があります。
これらの重要な要素を正確に制御および最適化することで、メーカーは生産コストを削減し、材料の利用率を向上させ、高精度の切断を保証しながら生産効率を高めることができます。
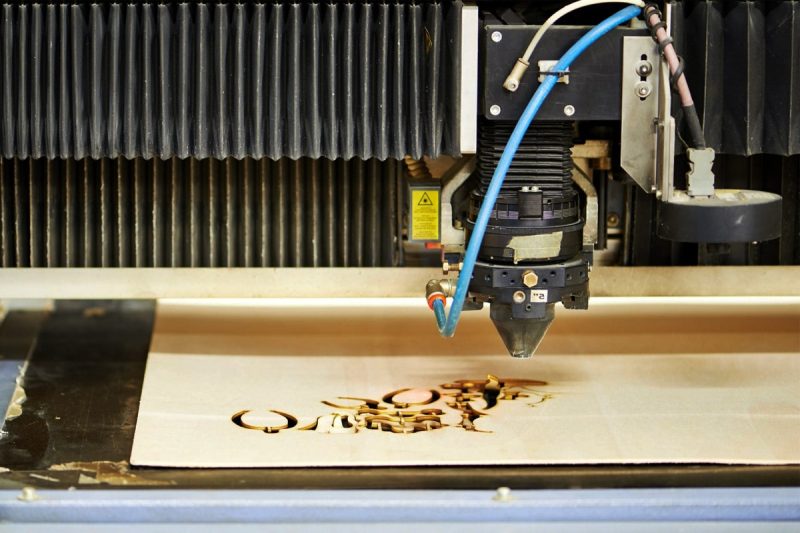
最小カーフ幅を実現するための最適化戦略
CO2レーザー切断において最小カーフ幅を実現するには、複数の最適化戦略を検討する必要があります。これらの戦略は、切断精度を向上させるだけでなく、材料の無駄を効果的に削減し、生産効率を向上させることができます。以下は、最小カーフ幅を実現するための主要な最適化手法です。
光学系の最適化:光学系の品質はレーザービームの集光効果に直接影響し、ひいては切開の細かさに影響します。高品質の光学レンズを選択することで、レーザービームが対象材料の表面に均一に焦点を合わせることができ、安定した精密な切断効果が得られます。短焦点レンズ(焦点距離2.5インチなど)の使用は、レーザービームの集光を最適化するための重要な戦略です。短焦点レンズはより小さなスポット径を集光できるため、レーザービームの拡散が減少し、切開幅が大幅に減少します。スポット径が小さいほど、切断精度が向上するだけでなく、材料への熱影響も軽減され、切断工程中の安定性も確保できます。
レーザー出力と速度を正確に調整する:レーザー出力と切断速度は、切開幅に影響を与える2つの重要な要素です。レーザー出力と速度の組み合わせを正確に調整することで、最高の切断効果を得ることができます。パルスモードを使用すると、連続加熱時間を短縮できるため、熱影響部(HAZ)が減少し、切開端の溶融現象が軽減されます。パルスモードは、レーザーエネルギー分布をより均一にし、高出力連続出力による過熱の問題を回避します。同時に、材料の厚さと組み合わせてレーザー出力を調整することで、レーザービームが材料を完全に貫通し、切開幅を制御できるようになります。材料が薄い場合は、過度の熱蓄積を避けるために適切に出力を下げます。材料が厚い場合は、切断品質を確保するために適切に出力を上げますが、切開幅の制御にも注意してください。
補助ガスパラメータの調整:補助ガスはCO2レーザー切断において重要な役割を果たします。切断中に発生する溶融物を除去するだけでなく、ガス圧力を最適化することで切断品質を制御します。ガス圧力を適切に高めることで、切断中に発生するスラグを効果的に除去し、切断端へのスラグの付着を防ぎ、狭い切断幅を維持できます。補助ガスを選択する際に、窒素は特に酸化を抑え、切断仕上がりを向上させる必要がある材料によく使用されるガスの1つです。窒素は材料表面の酸化を効果的に抑制するだけでなく、切断中の切断面の滑らかさを維持し、より高品質な切断効果をもたらします。
ソフトウェアとCNCパラメータの最適化:高精度CNCシステムは、レーザー切断の精度を効果的に向上させ、機械的な誤差による切断偏差を低減するのに役立ちます。高度なCNCシステムを使用することで、切断経路を最適化し、レーザービームの方向変化による誤差を低減できます。正確な経路計画は、切断中の曲がりや不均一な経路による誤差を低減するのに役立ちます。さらに、自動焦点システムの使用も、切開幅を最適化するための重要な戦略です。自動焦点システムは、材料の厚さ、形状、切断要件に応じてレーザーの焦点位置を自動的に調整し、レーザービームが常に最適な位置に焦点を合わせられるようにすることで、焦点位置の誤りによる不均一な切断や幅が広すぎる切断を回避します。
熱影響部(HAZ)の低減:HAZの大きさは、レーザー切断工程における熱蓄積と密接に関係しています。過剰な熱は材料表面の過剰な溶融を引き起こし、それによって切断幅が拡大し、切断品質に影響を与える可能性があります。熱影響部を低減するために、高速切断は効果的な戦略です。高速切断はレーザービームの移動を加速し、それによって材料表面への熱蓄積を減らし、溶融と切断エッジの拡大を回避できます。ただし、高速切断を使用する場合は、レーザービームのエネルギーが材料を貫通するのに十分であることを確認する必要があります。切断品質をさらに最適化するために、スプレー冷却やデュアルガス注入などの冷却技術を組み合わせることで、切断領域の温度を効果的に下げ、過熱を回避し、より正確で安定した切断効果を確保できます。
上記の最適化戦略を組み合わせることで、メーカーはCO2レーザー切断における最小カーフ幅を効果的に達成できます。技術の継続的な進歩と設備の継続的な最適化により、これらの戦略は切断精度のさらなる向上、材料の無駄の削減、生産効率の向上に役立ちます。
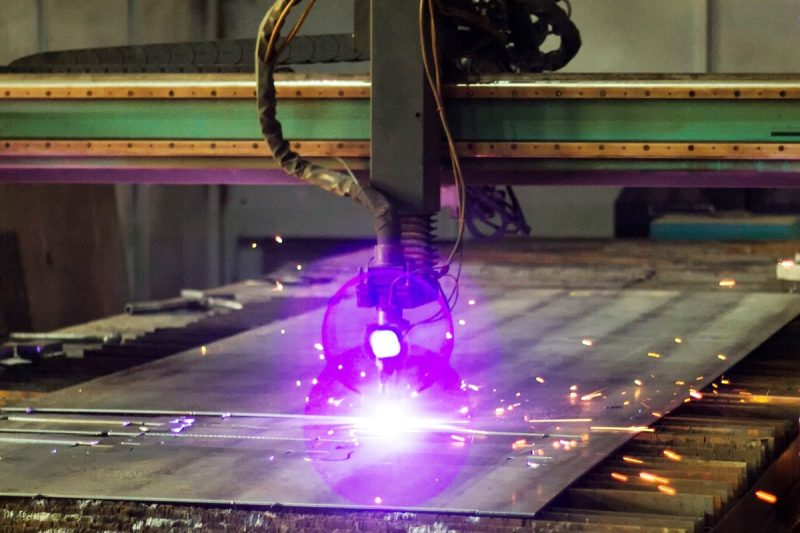
要約する
最小カーフ幅の実現は、単純なパラメータ調整ではなく、多くの要素を総合的に考慮するプロセスです。レーザー焦点、出力設定、切断速度、補助ガスの種類と圧力、ソフトウェア制御を正確に最適化することで、メーカーは生産効率を最大化し、材料の無駄を減らしながら切断品質を確保できます。レーザー焦点を正確に調整することで、切断エリアのスポットサイズを確保し、切断プロセス中に過度の熱影響部を回避し、細かく滑らかな切断を確保できます。出力と切断速度の正確な組み合わせは、過度の熱蓄積を回避し、溶融物が切断幅に与える影響を軽減します。適切な補助ガスはスラグを除去するだけでなく、酸化を防ぎ、切断品質をさらに向上させます。同時に、高度なCNCソフトウェアと自動フォーカス技術を使用することで、切断パスとレーザービームの焦点を継続的に最適化し、切断効果の安定性と一貫性を確保できます。
技術の継続的な発展に伴い、CO2レーザー切断機の性能と制御精度も向上しています。メーカーは、上記の要素を継続的に調整・最適化し、光学技術、自動制御システム、効率的な冷却技術の継続的な進歩と組み合わせることで、より正確な切断効果を実現できます。最終的に、最小の切込み幅を達成することは、切断精度を向上させるだけでなく、生産効率を高め、材料コストを削減し、長期使用における生産ラインの経済的メリットを大幅に向上させます。そのため、CO2レーザー切断機のユーザーにとって、 CO2レーザー切断機これらの最適化戦略を継続的に学習し、習得することが、全体的な生産能力と競争力を向上させる鍵となります。
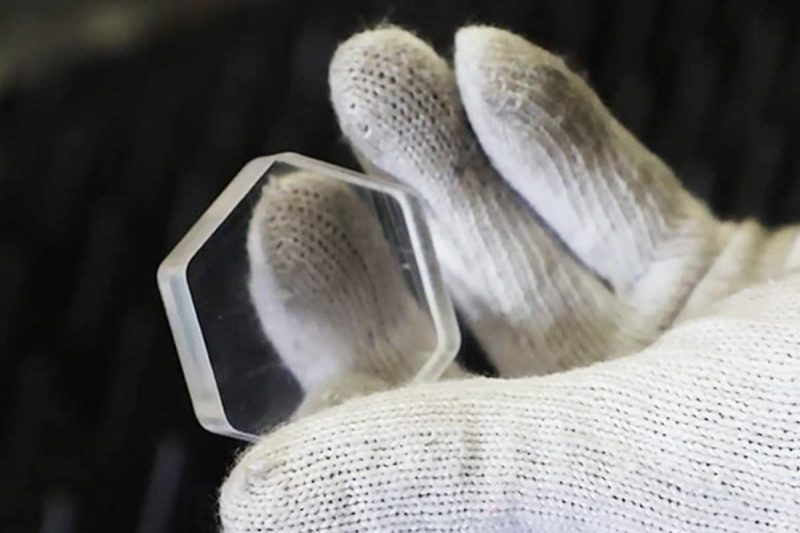
レーザー ソリューションを入手する
AccTek レーザー インテリジェントなフォーカス、自動パス最適化、効率的な補助ガス制御をサポートし、最小の切開幅を確保して精密な加工を実現する高精度 CO2 レーザー切断装置を提供します。 お問い合わせ カスタマイズされたレーザー切断ソリューションを入手して、生産効率と処理精度を向上させましょう。
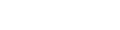
連絡先
- [email protected]
- [email protected]
- +86-19963414011
- No. 3 ゾーン A、Lunzhen 工業地帯、玉城市、山東省。
レーザー ソリューションを入手する