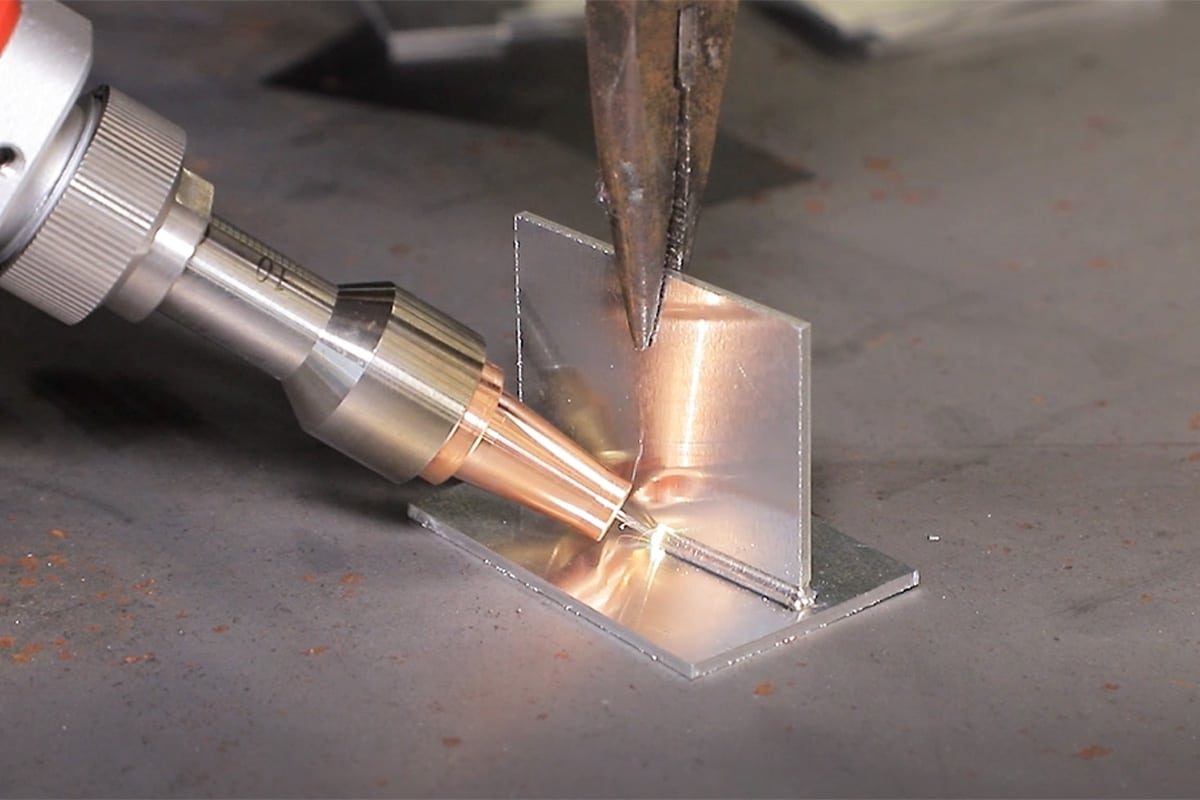
ステンレス鋼のレーザー溶接ガイド
ステンレス鋼は、耐腐食性、強度、耐熱性に優れ、洗浄が容易なため、自動車、航空宇宙、医療、建設など、現代の製造業の多くの分野で広く使用されています。これらの業界では、ステンレス鋼は自動車の排気システムや医療機器など、高温や腐食環境に耐える部品の製造に使用されています。他の材料と比較して、ステンレス鋼は強度と耐酸化性に優れているため、過酷な環境でも長期の安定性と機能性を維持するのに特に適しており、ステンレス鋼製品は日常生活やハイエンドの製造に欠かせないものとなっています。
しかし、ステンレス鋼の溶接には、主に材料の変形、溶接部の酸化、溶接時の入熱制御の面で、いくつかの特定の課題もあります。ステンレス鋼は熱伝導率が低いため、従来の溶接中に局所的な高温によって変形しやすく、溶接精度と溶接品質に影響を与えます。また、ステンレス鋼は高温で非常に酸化しやすく、溶接部の表面に望ましくない酸化層が形成され、外観と耐食性に影響を与える可能性があります。レーザー溶接は、高精度、低熱影響、高効率という利点により、これらの困難をうまく克服し、ステンレス鋼溶接の理想的なソリューションになりました。熱影響部を減らして変形のリスクを減らすだけでなく、効率的で高品質の溶接結果も実現します。
目次
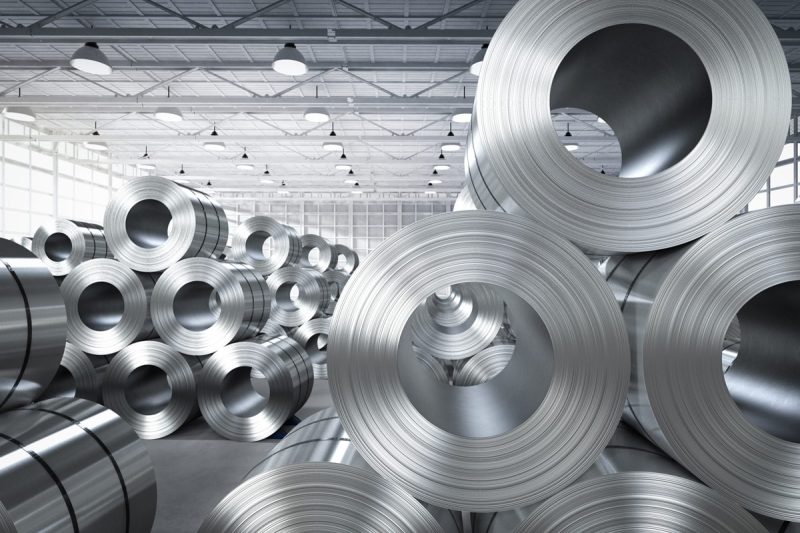
ステンレス鋼の特性
ステンレス鋼は鉄、クロム、ニッケルをベースとした合金で、優れた耐食性と高強度のため、製造業で広く使用されています。用途環境によって要件が異なるため、ステンレス鋼の組成と特性もそれに応じて異なります。これらの違いにより、ステンレス鋼は過酷な環境、特に温度変動、湿度変化、化学腐食に耐える必要がある場所で優れた性能を発揮します。
ステンレス鋼の性能概要
- 耐食性: ステンレス鋼のクロム元素が酸素と接触すると、表面に緻密な不動態膜が形成され、材料の耐食性が大幅に向上します。この特性により、ステンレス鋼は湿気の多い環境や腐食性の化学環境でも使用できます。
- 耐熱性: ステンレス鋼は高温環境でも高い強度と安定性を維持できます。ステンレス鋼の種類によって、組成設計の違いにより、数百度からそれ以上の温度までの動作環境に耐えることができます。
- お手入れが簡単: ステンレス鋼は表面が滑らかでセルフクリーニング効果があるため、お手入れやメンテナンスが簡単です。これは、食品や医薬品など、衛生要件が高い業界では特に重要です。
ステンレス鋼の種類と組成
ステンレス鋼は、微細構造、組成、機械的特性に応じて分類できます。主な種類は次のとおりです。
- オーステナイト系ステンレス鋼:クロム、ニッケル、少量の炭素で構成されており、靭性と可塑性に優れています。オーステナイト系ステンレス鋼には通常、8%以上のニッケルが含まれており、優れた耐酸化性と耐腐食性を備えています。食品加工、医薬品、建築装飾などの業界で広く使用されています。
- フェライト系ステンレス鋼:主にクロムを含み、ニッケルはほとんど含みません。耐食性と磁性に優れています。フェライト系ステンレス鋼は組成がシンプルでコストが低いため、耐食性が求められる自動車の排気システムなど、ストレスの少ない用途に適しています。
- マルテンサイト系ステンレス鋼:クロムを含み、炭素含有量が高い。ナイフ、タービンブレードなど、高強度と耐摩耗性が求められる用途に適しています。マルテンサイト系ステンレス鋼は硬度が高いため、機械的衝撃に耐える必要がある用途に適していますが、耐食性はオーステナイト系ステンレス鋼よりもわずかに低くなります。
ステンレス鋼の溶接の課題
ステンレス鋼には多くの利点がありますが、溶接時にいくつかの課題も発生するため、次の問題には特に注意する必要があります。
- 亀裂の形成: ステンレス鋼は、溶接中、特に急速加熱または急速冷却中に、高温亀裂または低温亀裂が発生しやすい傾向があります。これらの亀裂により、溶接の強度と信頼性が大幅に低下する可能性があります。
- 変形制御:ステンレス鋼の熱伝導率は低く、溶接プロセス中に溶接部付近で熱が集中し、局所的な温度が高くなります。冷却後に変形しやすく、ワークピースの寸法精度に影響を与えます。
- 溶接色の変化:ステンレス鋼の溶接プロセスでは、ステンレス鋼の酸化傾向が顕著であり、溶接部の表面に酸化変色が発生し、溶接部の色が青、茶色、黒に変わります。これは溶接部の外観に影響を与えるだけでなく、溶接部の耐腐食性能を低下させる可能性もあります。
- 酸化層保護:高温溶接中、ステンレス鋼の表面に酸化層が形成されやすく、溶接部の耐食性が弱まります。そのため、溶接部をアルゴン、窒素などの保護ガスで覆い、酸素が溶接面に接触するのを防ぎ、溶接部の品質を確保する必要があります。
これらの課題を解決するには、ステンレス鋼を溶接する際に、溶接パラメータを最適化し、適切な溶接プロセスを選択し、効果的な保護対策を講じる必要があります。
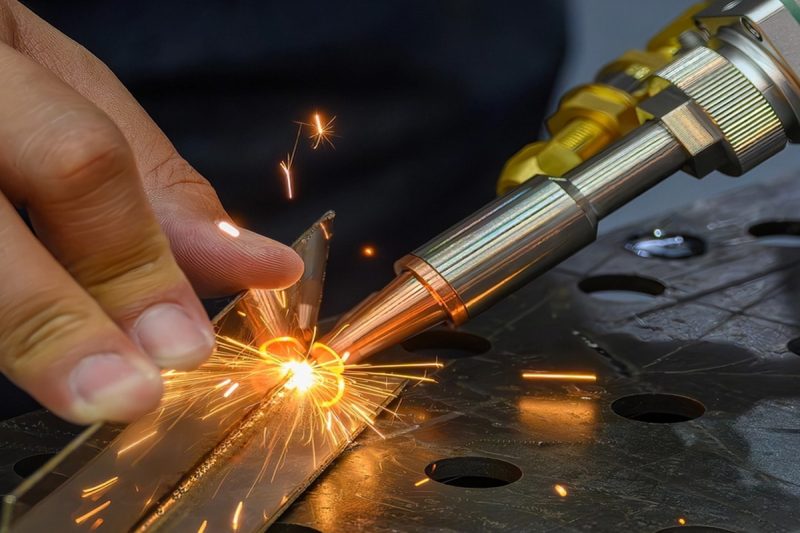
ステンレス鋼のレーザー溶接の原理
レーザー溶接は、高エネルギーのレーザービームを集中させてステンレス鋼材料を溶かし、急速冷却によって安定した接合を実現する、効率的で精密な溶接技術です。レーザー溶接は、熱影響部が小さく、精度が高いため、ステンレス鋼などの熱に弱い材料の溶接に特に適しています。溶接の厚さと用途の要件の違いにより、レーザー溶接は主に熱伝導溶接と深溶け込み溶接の 2 つのモードに分けられ、薄いステンレス鋼板と厚いステンレス鋼板の接合に適しています。
レーザー溶接プロセス
- 熱溶接:熱溶接のエネルギーは材料の表面に集中し、熱伝導によって材料に拡散します。通常、薄い材料の溶接に使用されます。この溶接モードは、溶接面の滑らかさと細かさに対する要件が高く、電子部品や精密機器の溶接に適しています。
- 深溶け込み溶接:深溶け込み溶接では、レーザーがステンレス鋼の表面で急速に溶け、小さな溶融池を形成して材料を貫通します。レーザービームによって生成された高温により、溶接部に小さなチャネル(「キーホール」と呼ばれる)が形成され、レーザーエネルギーがチャネルに集中して、溶接の深さが大きくなります。この溶接方法は、より厚いステンレス鋼板に適しており、自動車製造や圧力容器などの高強度溶接の場面で広く使用されています。
レーザーとステンレス鋼の相互作用
- エネルギー浸透:レーザービームがステンレス鋼と相互作用すると、その高いエネルギー密度がステンレス鋼の表面を素早く浸透し、局所的な材料を瞬時に融点または気化温度まで加熱します。溶融したステンレス鋼金属は溶融池内で液体を形成し、レーザーによって生成された小さな穴構造と連携して、高強度の溶接効果を確保します。
- 溶融池の形成: レーザーの作用により、金属溶融池はレーザーによって継続的に加熱され、液体金属領域を形成します。溶接プロセス中に液体金属が互いに浸透し、強力な接合領域が生成されます。溶融池内の液体金属は冷却され、高い機械的ストレスに耐えられる固体溶接部を形成します。
- 溶接品質:レーザー溶接はエネルギー密度が高く、穴が小さいため、溶接部の高密度接続が実現でき、溶接強度は母材の強度に近くなります。また、レーザー溶接の熱影響部が小さいため、溶接後のワークピースの変形が小さく、高温下でのステンレス鋼材料の酸化損失が低減されます。
溶接に影響を与える主要なパラメータ
ステンレス鋼のレーザー溶接プロセスでは、溶接効果はいくつかの重要なパラメータによって影響を受けます。
- レーザー出力:レーザー出力は溶接熱量を決定し、溶接深さと溶接幅に直接影響します。レーザー出力が高いほど溶接の溶け込みが深くなり、厚板材料の溶接に適していますが、材料の過剰溶融や割れを引き起こす過剰な出力を避ける必要があります。
- 焦点位置:レーザーの焦点位置は溶接品質にとって非常に重要です。適切な焦点位置は溶接部分にエネルギーを集中させ、溶接強度と深さを向上させることができます。通常、最良の溶接効果を得るために、焦点はワークピースの内側にわずかに調整されます。
- 溶接速度: 溶接速度は溶接効率と入熱量に直接影響します。溶接速度が速すぎると溶接が不完全になったり強度が不十分になったりし、逆に溶接速度が遅すぎると入熱量が多すぎたり材料が変形したり気孔ができたりします。通常、溶接速度は材料の厚さとレーザー出力に応じて最適化され、理想的な溶接が得られます。
- シールドガス:ステンレス鋼をレーザー溶接する場合、溶接部が空気中の酸素と接触するのを防ぎ、溶接部の酸化を防ぐために、シールドガス(アルゴンや窒素など)を使用して溶接部を覆う必要があります。シールドガスの流量と選択も溶接の品質に影響します。適切なシールドガスは、溶接部の酸化を効果的に防止し、溶接部の強度と外観を確保します。
これらのパラメータを最適化することで、安定したレーザー溶接効果を実現し、さまざまな用途シナリオにおけるステンレス鋼の品質と性能の要件を満たすことができます。

ステンレス鋼のレーザー溶接の準備
ステンレス鋼をレーザー溶接する前に、適切な準備を行うことが溶接の品質と効率を確保するための重要なステップです。材料の選択、ジョイントの設計、溶接前の表面洗浄は、最終溶接の強度、外観、耐久性に影響します。慎重に準備することで、溶接欠陥を減らし、溶接結果の安定性を向上させることができます。
材料の選択と準備
- 適切なステンレス鋼材料を選択する: 溶接に使用するステンレス鋼材料は、溶接中に起こり得る品質問題を減らすために、優れた耐熱性と耐腐食性を備えている必要があります。一般的に使用されるステンレス鋼材料には、オーステナイト系ステンレス鋼 (304、316 など) とフェライト系ステンレス鋼 (430 など) があります。溶接の適用シナリオと構成要件に応じて、適切な材料を選択できます。
- 材料の品質を確保する: 溶接中に溶融池が不安定になったり、亀裂が拡大したりしないように、材料の表面が平らで、亀裂や気孔がないことを確認するために、高品質のステンレス鋼を選択します。材料を選択するときは、不純物が多すぎる材料は避けてください。そうしないと、溶接強度に影響する可能性があります。
- 均一な材料の厚さを確保: 厚さが不均一な材料を溶接すると、レーザー エネルギーの分布が不均一になり、溶接品質に影響します。均一な材料の厚さを確保すると、一貫した溶け込み深さと溶接形状が得られます。
コネクタ設計の考慮事項
- 突合せジョイント: 突合せジョイントは、平行で隣接する材料のエッジに適しており、薄いステンレス鋼の接続によく使用されます。突合せジョイントは、より高い溶接強度を提供できますが、溶接の連続性を確保するために、より高い位置合わせ精度が必要です。
- 重ね継ぎ: 重ね継ぎは、重ね合わせた材料の溶接に適しており、通常は厚板や高荷重の部品に使用されます。重ね継ぎは溶接強度と靭性を向上させることができますが、溶接熱が過剰になって変形が生じるのを避けるために、重ね合わせ領域のサイズを適切にする必要があります。
- フィレットジョイント:フィレットジョイントは、2 つの材料エッジを直角に溶接するために使用され、構造部品やフレームの溶接で広く使用されています。ステンレス鋼の溶接では、溶接後の強度と外観の一貫性を確保するために、フィレットジョイントの溶接角度を考慮する必要があります。
- 溶接ギャップと溶接幅: 適切に設計された溶接ギャップと溶接幅により、均一なレーザーエネルギー分布が確保され、材料の変形や溶接収縮を引き起こす過度の熱集中を回避できます。厚いステンレス鋼の場合、熱変形を減らすために、通常は溶接ギャップを小さくします。
表面洗浄と溶接前処理
ステンレス鋼の表面の清浄度は、レーザー溶接の安定性と品質に大きく影響します。表面が清浄でないと、不純物や酸化物が発生し、溶融池の形成や溶接の強度に影響する可能性があります。
- 酸化層を除去する: ステンレス鋼の表面には酸化層があることが多く、これがレーザーの有効吸収に影響し、溶接効果を低下させます。レーザー洗浄剤または化学洗浄剤を使用して酸化層を除去し、レーザーエネルギーが材料の表面に十分に作用できるようにします。
- 油分や不純物の除去: 油分や不純物は溶接の不均一や気孔の原因になります。表面の汚染物質を除去するには、無水アルコールまたは特殊な洗浄剤が必要です。食品や医療など、清浄度が要求される溶接部品に使用する場合は、溶接前の洗浄が特に重要です。
- 機械洗浄: 表面の汚れがひどい場合は、研磨やサンドペーパー処理などの機械洗浄方法を使用して、滑らかな表面を確保できます。機械洗浄では、ステンレス鋼の表面に傷が残らないように注意する必要があります。傷が残ると、溶接の美しさと強度に影響します。
- 適切なシールドガスの使用: 溶接前処理では、材料の特性に応じて適切なシールドガス (アルゴン、窒素など) を選択する必要があります。これにより、溶接中の酸化や気孔が効果的に防止され、溶接の品質と強度が確保されます。
上記の準備作業により、レーザー溶接されたステンレス鋼の安定性と溶接効果が大幅に向上し、さまざまな適用環境における溶接の耐久性と美観が確保されます。
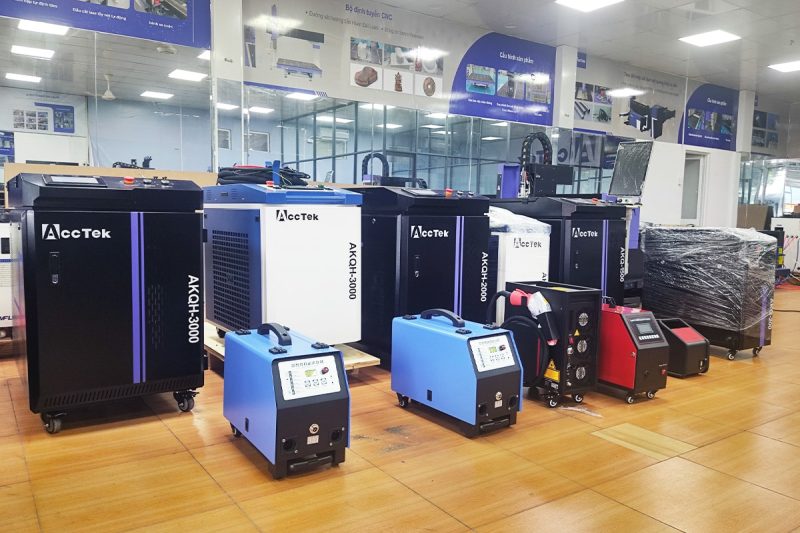
ステンレス鋼レーザー溶接機
レーザー溶接機 現代の製造業、特にステンレス鋼の溶接用途において重要な役割を果たしています。効率的で正確な溶接ソリューションを提供し、自動車、航空宇宙、医療機器、その他の業界で広く使用されています。適切なレーザー溶接機を選択すると、溶接品質と生産効率が大幅に向上します。
ステンレス鋼用レーザー溶接システムの種類
市場には主に 2 種類のレーザー溶接システムがあり、それぞれステンレス鋼のさまざまな溶接ニーズに適しています。
ファイバーレーザー溶接機
- ファイバーレーザー溶接機は、エネルギー利用率が高く、ビーム伝送効率が優れているため、広く使用されています。ファイバーレーザー発生器は、レーザービームを溶接点に正確に焦点を合わせることができるため、より強力な溶接効果が得られます。
- このタイプのレーザー発生器は、溶接時に発生する熱影響部が小さく、溶接変形のリスクが低減されるため、精密溶接や薄板溶接に適しています。
CO2レーザー溶接機
- CO2 レーザー溶接機は、主に厚いステンレス鋼板の溶接に適しています。ファイバーレーザー溶接機よりもエネルギー効率は若干劣りますが、特定の用途には依然として理想的な選択肢です。
- この溶接システムの操作には、ガス流量とレーザー調整の高度な制御が必要であり、大規模生産に適しています。
レーザー光源とパラメータの選択
適切なレーザー光源を選択し、溶接パラメータを調整することが、ステンレス鋼溶接の品質を確保するための鍵となります。
レーザー光源の選択
- より高出力のファイバーレーザージェネレーターの使用をお勧めします。レーザー出力が高いほど、溶接速度と深さが効果的に増加し、溶接効果がより理想的になります。
- レーザー発生器を選択する際には、さまざまな厚さのステンレス鋼の溶接要件を満たすことができることを確認するために、適切な材料の厚さを考慮する必要があります。
パラメータ調整
- ステンレス鋼板の厚さに応じて、溶接速度とレーザー出力を調整します。ステンレス鋼板が薄い場合は、過度の熱入力による変形を避けるために、溶接速度を速くし、出力を低くする必要があります。
- 厚いステンレス鋼板の場合、溶接速度を下げてレーザー出力を上げると、良好な溶接外観を維持しながら溶接の深さと強度を確保できます。
補助装置および付属品
補助装置と付属品はレーザー溶接プロセスにおいて重要な役割を果たし、溶接効果と品質をさらに向上させることができます。
保護ガス
- アルゴンまたは窒素をシールドガスとして使用すると、溶接中の酸化やその他の悪影響を防ぐことができます。シールドガスによって形成されるガスバリアは溶融池を保護し、溶接の清潔さと品質を確保します。
- ガスの流量と種類を適切に選択することで、溶接雰囲気を制御し、溶接欠陥の発生を減らすことができます。
冷却システム
- 冷却システムは、溶接プロセス中に発生する温度を制御し、過熱による材料の変形や溶接の劣化を防ぐために使用されます。
- 適切な冷却により、機器の耐用年数が延び、溶接プロセスの安定性と安全性が向上します。
固定具および位置決め装置
- 固定具と位置決め装置は、溶接ワークピースを固定して、溶接プロセス中の正確なドッキングと安定性を確保するために使用されます。これは、高精度の溶接に不可欠です。
- 柔軟で調整可能な固定具設計により、さまざまな形状やサイズのステンレス鋼ワークピースに適応でき、生産効率が向上します。
レーザー溶接機とその補助装置を合理的に選択することで、ステンレス鋼の溶接において効率的で高品質の溶接効果を実現し、現代の製造業のニーズを満たすことができます。
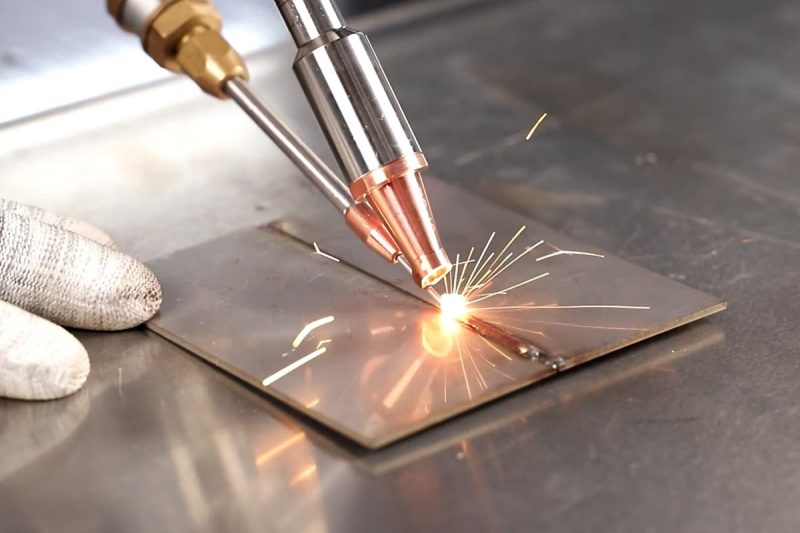
ステンレス鋼のレーザー溶接の応用
レーザー溶接技術は、その優れた溶接効果と幅広い適用性により、多くの業界で広く使用されています。以下は、ステンレス鋼のレーザー溶接の主な応用分野と、それぞれの利点と特徴です。
自動車産業
応用分野
自動車業界では、レーザー溶接は自動車の排気システム、燃料タンク、車体構造、シートフレーム、およびさまざまな付属品の溶接に広く使用されています。これらの部品の溶接には、さまざまな運転条件下での自動車の性能を確保するために、高い強度と耐腐食性が求められます。
利点
- 高強度溶接: レーザー溶接は、高圧と衝撃力に耐える強力な溶接接合部を提供し、過酷な条件下でも構造の完全性を保証します。
- 耐食性:ステンレス鋼自体は優れた耐食性を備えており、レーザー溶接の溶接部も効果的に腐食に耐えることができ、車の耐用年数を延ばし、メンテナンスコストを削減します。
- 軽量設計: レーザー溶接の精度と溶接のサイズが小さいため、設計者は重量を増やすことなくより強力な構造を設計でき、車の燃費が向上します。
航空宇宙
応用分野
航空宇宙産業では、航空機の胴体、タービンブレード、エンジン部品、その他の複雑な構造物の溶接にレーザー溶接が使用されています。これらの部品は過酷な条件と高い強度要件に耐える必要があるため、レーザー溶接は理想的な選択肢です。
利点
- 高精度: レーザー溶接は、航空宇宙部品にとって非常に重要なミクロンレベルの溶接精度を実現し、高負荷および高ストレス環境下での性能を確保できます。
- 熱影響部が小さい: レーザー溶接時の熱影響部が小さいため、材料の変形や応力が軽減され、溶接後の変形の問題を効果的に回避できます。
- 小さくてきれいな溶接: レーザー溶接の溶接は従来の溶接よりも小さくてきれいで、追加の表面処理工程を減らすことができます。
医療機器
応用分野
医療機器で溶接が必要となることが多い部品には、外科用メス、インプラント、医療機器ハウジングなどがあります。これらの部品は、厳格な衛生基準と性能基準を満たす必要があります。
利点
- クリーンな溶接: レーザー溶接は汚染のない環境で実行でき、溶接は滑らかで欠陥がなく、医療業界の厳しいクリーンさの要件を満たしています。
- 高精度:レーザー溶接の高精度により、医療機器の製造精度が保証され、使用の安全性と有効性が向上します。
- パーソナライズとカスタマイズ: レーザー溶接は、さまざまな複雑な形状やサイズの溶接に適しており、パーソナライズされた医療機器のニーズを満たすことができます。
食品・飲料業界
応用分野
食品・飲料業界では、タンク、コンベア、貯蔵タンク、加工装置の溶接にステンレス鋼の溶接が広く使用されています。これらの溶接は、食品の安全性を確保するために高い衛生基準を満たす必要があります。
利点
- 耐腐食性: ステンレス鋼材料はさまざまな腐食に効果的に耐え、食品加工機器の長期にわたる安全な動作を保証します。
- 清掃が簡単: レーザー溶接の溶接部は平らで滑らかなので、細菌の増殖のリスクが軽減され、機器の清掃が容易になり、食品衛生基準を満たします。
- 高品質の溶接: レーザー溶接による溶接は強度が高く、見た目も美しいため、機器の全体的な品質と市場競争力を向上させることができます。
建設と装飾
応用分野
ステンレス鋼は建設業界や装飾業界で広く使用されており、レーザー溶接技術はステンレス鋼の手すり、ドアや窓、家具、その他の装飾部品の溶接に使用されています。
利点
- 滑らかな溶接: レーザー溶接により滑らかな溶接面が確保され、従来の溶接でよく見られる欠陥が回避され、全体的な美観が向上します。
- 美観: 溶接後の表面処理が少ないため、ステンレス鋼製品は顧客にとって見た目がより魅力的になり、建築デザインの高い美観要件を満たします。
- 耐久性: ステンレス鋼素材は耐腐食性と耐摩耗性に優れており、レーザー溶接の堅牢性により、さまざまな環境での建物や装飾品の長期使用が保証されます。
レーザー溶接ステンレス鋼技術の広範な応用は、さまざまな業界の製品の品質と性能を向上させるだけでなく、製造技術の進歩を継続的に促進してきました。正確で効率的なレーザー溶接技術を通じて、高品質と高効率に対する現代の製造業の切実なニーズを満たすことができます。
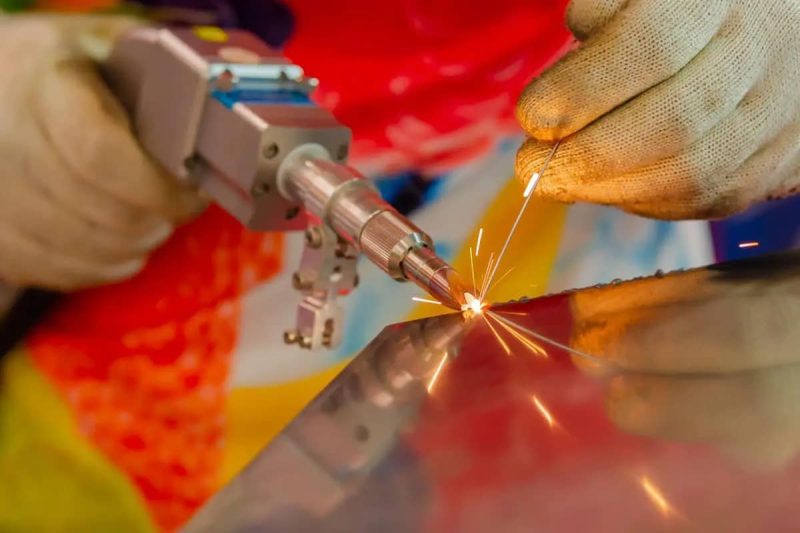
ベストプラクティスとヒント
ステンレス鋼をレーザー溶接する場合、溶接品質を向上させるだけでなく、溶接プロセスをスムーズにするためにも、ベスト プラクティスとヒントに従うことが重要です。ここでは、溶接プロセスに関する重要なベスト プラクティスとヒントをいくつか紹介します。
ステンレス鋼の適切な取り扱いと保管
材料保管
- ステンレス鋼材料は、湿気や汚染を避けるために、乾燥した換気の良い環境で保管する必要があります。
- 湿気の侵入を防ぐために、木製のラックまたはプラスチック製のパッドを使用して、地面との直接接触を避けてください。
- ステンレス鋼の表面を保護するためにカバー(プラスチックフィルムなど)を使用しますが、湿気がたまらないように通気性のある素材を使用してください。
マテリアルハンドリング
- 溶接する前に、ステンレス鋼材の表面に傷や錆などの欠陥がないことを確認してください。
- 溶接品質を確保するために、糸くずの出ない布と適切なクリーナー(アルコールや特殊なクリーナーなど)を使用して表面を徹底的に清掃し、油、酸化物、不純物を取り除きます。
- ワイヤーブラシや鉄製の工具など、ステンレス鋼の表面を汚染する可能性のある工具の使用は避けてください。
溶接パラメータの最適化
レーザー出力と溶接速度
- さまざまな厚さのステンレス鋼板の場合、溶接出力と速度を最適化することが重要です。厚いステンレス鋼板 (例: 3 mm 以上) では、十分な溶融と浸透を確保するために、通常、より高いレーザー出力とより遅い溶接速度が必要です。
- 最適な溶接速度とレーザー出力の組み合わせは実験的に決定でき、小規模なテストを通じてパラメータ設定を最適化できます。
フォーカス位置
- 溶接時には、レーザービームの焦点位置も溶接の品質に影響します。最良の溶接効果を確保するには、焦点をワークピースの表面よりわずかに下に配置する必要があります。
- 溶接不良を防ぐために、レーザーの焦点を定期的に確認して調整し、常に最適な位置にあることを確認してください。
溶接後処理・仕上げ技術
溶接後処理
- 溶接後、溶接部には酸化物や汚れが残ることがあるため、溶接後処理を行う必要があります。一般的な処理方法としては、研削、研磨、酸洗いなどがあります。
- 研磨: グラインダーと適切な研磨剤を使用して溶接部を丁寧に研磨し、表面の欠陥を除去して溶接部の滑らかさを確保します。
- 酸洗い:酸洗い液を使用して溶接部の表面の酸化物を除去し、ステンレス鋼の光沢を回復し、外観と耐食性を向上させます。
表面処理
- 要求度の高い製品の場合、美観と耐腐食性を向上させるために、研磨やサンドブラストなどの追加の表面処理を施すことができます。
- 溶接部品を定期的に点検し、メンテナンスすることで、長期間にわたって良好な性能と外観を維持できます。
よくある課題とトラブルシューティング
溶接部の酸化
- 溶接中に溶接部に酸化が発生した場合、シールドガスの流量が不十分または不適切である可能性があります。アルゴンの流量を調整してシールドガスの適用範囲を広げ、溶接部の清浄度を確保してください。
- 酸化のリスクを減らすために、より純度の高いシールドガスの使用も検討できます。
溶接変形
- 溶接中の変形は、通常、レーザー出力が高すぎるか、溶接速度が速すぎることに関係しています。溶接パラメータを再評価し、レーザー出力を適切に下げるか、溶接速度を上げる必要があります。
- 溶接中の変形のリスクを軽減するために、セクションごとに溶接するか、適切な固定具を使用してワークピースを固定することを検討してください。
溶接強度不足
- 溶接強度不足は、溶接速度が速すぎるか、レーザー出力が不十分なことが原因で発生する場合があります。これは、溶接パラメータを調整することで改善できます。
- 溶接品質が期待される基準を満たしていることを確認するために、溶接引張試験とせん断試験を定期的に実行し、必要に応じて再溶接します。
上記のベストプラクティスとヒントに従うことで、溶接プロセスはステンレス鋼レーザー溶接の品質と効率を効果的に向上させ、一般的な問題の発生確率を減らし、溶接構造の長期的な信頼性を確保することができます。
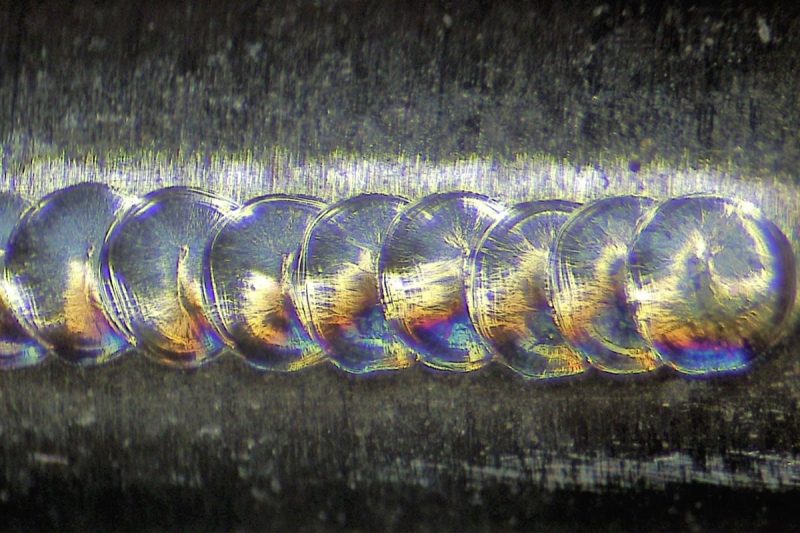
要約する
ステンレス鋼のレーザー溶接は、あらゆる製造業に信頼性の高い溶接ソリューションを提供する革新的な技術です。この溶接方法では、高エネルギーレーザービームを正確に制御して、溶接中にステンレス鋼材料をすばやく溶かし、高強度で美しい溶接部を形成します。従来の溶接方法と比較して、レーザー溶接は熱影響が小さく、変形が少なく、効率が高いという利点があり、精密製造の第一選択肢となっています。このため、レーザー溶接は現代の産業でますます使用され、自動車、航空宇宙、医療機器などの多くの分野をカバーしています。
ステンレス鋼を溶接する場合、適切な材料を選択し、溶接パラメータを正確に制御し、必要な溶接後の処理を行うことが、溶接品質を確保するための重要な要素です。溶接前に、材料の表面が清潔で乾燥していることを確認し、溶接欠陥を回避します。溶接プロセス中に、レーザー出力と溶接速度を適切に調整すると、溶接部の強度と外観が大幅に向上します。溶接後、研磨や酸洗いなどの適切な処理と仕上げにより、酸化物が除去され、溶接部の滑らかさと耐腐食性が向上し、製品の耐用年数が延びます。
業界をリードするレーザー機器メーカーである AccTek は、さまざまな業界に適したレーザー溶接機を提供し、お客様の多様なニーズを満たすことを目指しています。当社の機械は優れた性能と耐久性で知られており、お客様が使用中にタイムリーなサポートと支援を受けられるように、包括的なアフターサービスも提供しています。製造ニーズをサポートし、生産効率を向上させる当社のレーザー溶接機器について詳しく知りたい場合は、ぜひお問い合わせください。
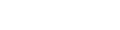
連絡先
- [email protected]
- [email protected]
- +86-19963414011
- No. 3 ゾーン A、Lunzhen 工業地帯、玉城市、山東省。
レーザー ソリューションを入手する