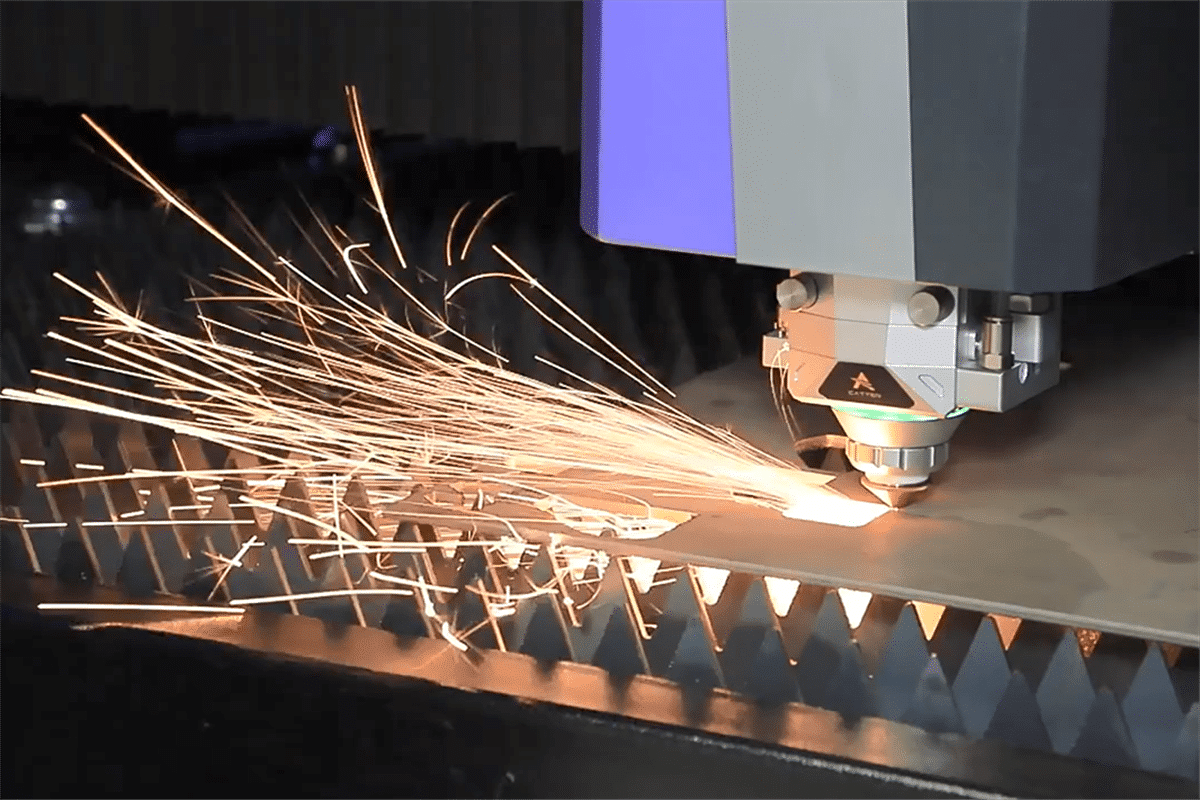
ファイバーレーザー切断 VS 従来の金属切断
レーザー切断機 1960 年代から産業運営の一部となってきました。レーザー技術の発展により、高精度、高速、多用途性がレーザー切断プロセスの主要な利点となり、産業分野におけるレーザー切断の重要性がますます高まっています。ファイバーレーザー切断技術が登場する以前は、さまざまな伝統的な金属切断プロセスが存在し、それぞれが独自の特徴を持ってさまざまな分野で重要な役割を果たしていました。では、ファイバーレーザー切断技術の開発が徐々に成熟するにつれ、金属切断プロジェクトに直面する際に、適切な切断装置をどのように選択すればよいのでしょうか?ここでは高度なファイバーレーザー切断技術を紹介し、他の 3 つの主要な従来の金属切断プロセスと比較します。これらの金属切削加工の特徴を理解することで、プロジェクトに適した切削工具を選択することができます。
目次
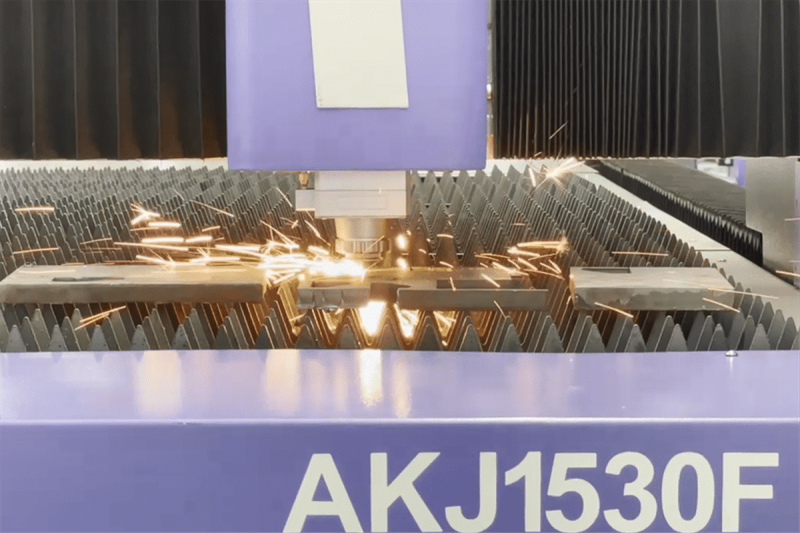
ファイバーレーザー切断技術を理解する
ファイバーレーザー切断は、高出力レーザーを使用して金属材料を高精度に切断する技術です。その精度、スピード、多用途性により人気を集めています。他の伝統的な金属切削プロセスと比較する前に、まずこの高度なプロセスを理解しましょう。ファイバーレーザー切断技術を理解するのに役立ついくつかの重要な側面を以下に示します。
ファイバーレーザー切断はどのように機能しますか?
ファイバーレーザー発生器は、ポンプダイオードからエネルギーを収集する特別に設計されたグラスファイバーを使用してビームを増幅します。この強力なレーザーが材料の表面に当たると、高強度の光が吸収されて熱に変換され、表面が溶けます。レーザービームと平行な高速気流を使用して溶融材料を吹き飛ばし、それによってワークピースを切断します。
ファイバーレーザービームと材料との最初の接触点は、その後の相互作用よりも強くなければなりません。この最初の接触では材料を単に切断するのではなく貫通する必要があり、これには高出力パルスビームの使用が必要となるためです。通常、ファイバーレーザー切断機はコンピューター数値制御技術を使用しており、コンピューター支援設計ワークステーションから切断データを受信できます。これらの技術は、材料の表面またはレーザー自体を制御して、特定のパターンやデザインを生成するのに役立ちます。
ファイバーレーザー切断加工で加工できる材質は何ですか?
ファイバーレーザー切断機 は、特にさまざまな金属材料の切断における高い効率と多用途性で知られています。ファイバーレーザー切断機の高出力密度により、これらの金属を正確かつ迅速に切断できます。
- ステンレス鋼: ファイバーレーザーは、優れたエッジ品質と最小限の熱歪みでさまざまなグレードのステンレス鋼を切断でき、自動車、航空宇宙、建設業界でよく使用されます。
- 軟鋼: ファイバー レーザー切断は、さまざまな構造用途や一般的な製造で一般的に使用される、さまざまな厚さの軟鋼シートやプレートに最適です。
- アルミニウム: ファイバーレーザー切断プロセスは、航空宇宙や自動車の用途でよく使用されるアルミニウムシートや合金の切断に最適です。
- 銅: 銅は導電性の高い金属であり、ファイバーレーザージェネレータを使用して効果的に切断できるため、電気部品、パイプ、装飾部品の製造および加工に適しています。
- 真鍮: ファイバーレーザーは、装飾用途で知られる金属合金である真鍮を正確に切断できます。
- 亜鉛メッキ鋼: ファイバー レーザー ジェネレーターは、建設や製造で一般的に使用される亜鉛メッキ鋼を切断できます。
- チタン: ファイバーレーザー発生器は、航空宇宙産業や医療産業で使用される軽量で強力な金属であるチタンを切断できます。
- その他の金属合金: ファイバーレーザー切断プロセスは、特殊な用途で使用されるさまざまな金属合金を切断することができ、さまざまな業界での用途を拡大します。
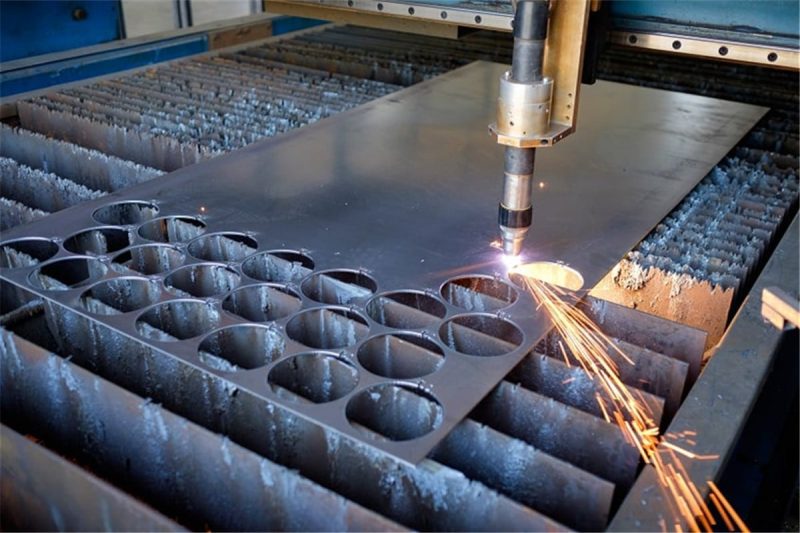
伝統的な金属切断プロセスとは何ですか?
ファイバーレーザー切断技術が広く使用されるようになる前は、いくつかの従来の金属切断プロセスが製造の基礎となっていました。ここでは、一般的な従来の金属切断技術を 3 つ紹介します。
プラズマ切断
プラズマ切断は、プラズマ アークを使用して金属を溶かして切断する熱切断プロセスです。このプロセスでは、ワークピース上にイオン化ガス (プラズマ) の高速ジェットを使用し、制御された集中的な切断アークを作成します。プラズマ切断システムは、プラズマ ジェットが通過するノズルを備えたプラズマ切断トーチで構成されます。トーチには、プラズマ アークの制御と安定化に役立つ電極とボルテックス リングも含まれています。プラズマ切断は、鋼、ステンレス鋼、アルミニウム、銅、その他の金属を含むさまざまな導電性材料の切断に広く使用されています。
ウォータージェット切断
ウォータージェット切断は、高圧の水流、または水と研磨材の混合物を使用して、さまざまな材料を切断する加工プロセスです。この技術は、レーザーやプラズマ切断などの他の方法で発生する高温に敏感な材料の精密切断によく使用されます。ウォータージェット切断には主に 2 つのタイプがあります。
- ピュア ウォータージェット切断: この方法では、集中した水流を使用して、ゴム、フォーム、特定のプラスチックなどの柔らかい材料を切断します。純粋なウォータージェット切断は、研磨粒子による追加の切断力を必要としない材料に最適です。
- 研磨ウォータージェット切断: このプロセスでは、研磨粒子 (通常はガーネット) を水流に混ぜて切断力を高めます。これにより、研磨ウォータージェットは金属、石、セラミック、複合材などのより硬い材料を切断できます。ウォータージェット内の研磨粒子は、材料を侵食して切断する働きをします。この記事では、金属切断用のこのタイプの研磨ウォータージェット切断について説明します。
ウォータージェット切断システムの基本コンポーネントには、高圧ポンプ、ノズル、混合チャンバー (研磨ウォータージェット用)、および CNC (コンピューター数値制御) システムが含まれます。 CNC システムはウォータージェット ノズルの動きを制御して特定の切断パスに沿って移動し、正確で複雑な形状を作成します。
火炎切断
酸素燃料切断としても知られる火炎切断は、ガスと酸素の燃焼によって発生する熱を使用して金属を切断する熱切断プロセスです。特に鉄金属の切断に適しており、手動で使用することも、CNC システムを使用して自動切断することもできます。フレームカットプロセスには次の手順が含まれます。
- 予熱: 金属は融点直下の温度まで予熱されます。これは、炎を金属表面に向けることによって行われます。予熱により、切断プロセスに必要な酸素の量が減少します。
- 切断: 金属が適切に予熱されると、酸素のジェットが予熱された金属に向けられます。高圧酸素ジェットが金属と反応して、酸化鉄またはスラグを形成します。発熱反応により追加の熱が放出され、金属が溶解します。溶けた金属は酸素ジェットの力で吹き飛ばされ、切り込みが生じます。
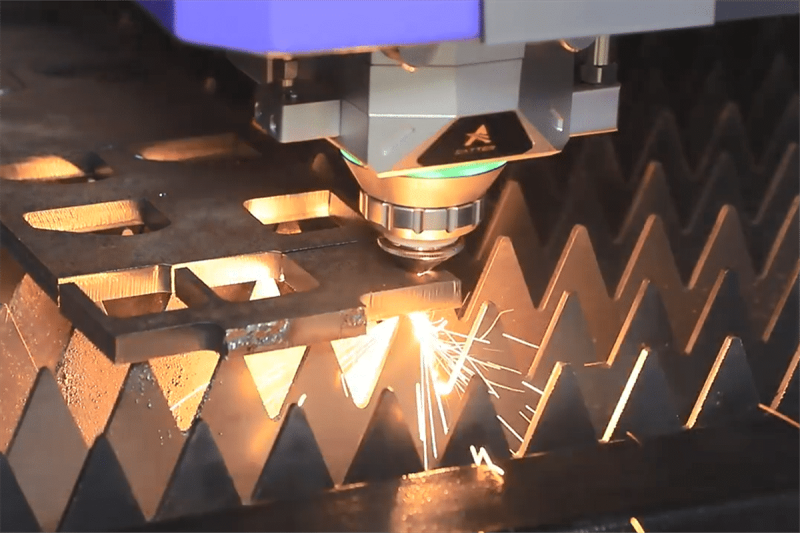
ファイバーレーザー切断 VS 従来の金属切断プロセス
ファイバーレーザー切断と、プラズマ切断、ウォータージェット切断、火炎切断などの従来の金属切断プロセスには、コスト、効率、精度、適用範囲の点で明確な違いがあります。以下は、ファイバーレーザー切断と従来の金属切断プロセスの比較です。
動作原理
- ファイバーレーザー切断: このプロセスには、ファイバーレーザー源によって生成された高出力レーザービームの使用が含まれます。レーザービームは焦点を合わせて切断対象の材料に照射し、所定の切断経路に沿って材料を溶融または蒸発させます。
- プラズマ切断: イオン化ガス (プラズマ) の高速ジェットを使用して材料を溶かして除去します。プラズマは、ガスに電気アークを通すことによって生成されます。
- ウォーター ジェット切断: ウォーター ジェット切断では、高圧の水流 (ガーネットなどの研磨材と混合される場合もあります) を利用して材料を切断します。研磨ウォーター ジェットは、溶融ではなく浸食によってさまざまな材料を切断できます。
- 火炎切断: 高温の火炎 (通常は酸素燃料) を利用して材料を発火点まで加熱します。次に、酸素の流れが加熱された材料に向けられ、材料が酸化され、スラグとして吹き飛ばされます。
材質の適合性
- ファイバーレーザー切断: 多用途で、鋼、アルミニウム、銅、真鍮などの金属を含む幅広い材料の切断に適しています。特に薄肉から中厚の金属に効果的です。
- プラズマ切断: 鉄金属や非鉄金属を含むさまざまな導電性材料に適しています。特に厚い材料の切断に威力を発揮します。
- ウォータージェット切断: 多用途で、金属、プラスチック、複合材料、石、ガラス、セラミックなどの幅広い材料を切断できます。
- 火炎切断: より厚い金属、特に炭素鋼の切断に一般的に使用されます。アルミニウムやステンレス鋼などの非鉄金属の切断にはあまり効果がありません。
精度の高い能力
- ファイバーレーザー切断: 特に複雑で詳細な切断に高い精度と精度を提供します。集束されたレーザービームにより、切断プロセスを細かく制御できるため、微細な公差が可能になり、滑らかなエッジが得られます。
- プラズマ切断: 一般に精度は良好ですが、特にエッジの滑らかさと細部の点で、切断品質はレーザー切断ほど高くない場合があります。
- ウォータージェット切断:特に厚い材料の場合、良好な精度が得られますが、精度は材料の厚さや切断速度などの要因に影響される可能性があります。
- フレーム切断: 一般に、レーザー切断に比べて精度が低くなります。構造用鋼の製造など、精度が重要な要件ではない用途に最適です。
速度性能
- ファイバーレーザー切断: 一般に、特に薄い素材から中程度の厚さの素材の場合、多くの従来の方法よりも高速です。レーザー切断速度は、レーザー出力や材料の種類などの要因に影響されます。
- プラズマ切断: プラズマ切断は、特に厚い材料の場合は高速ですが、レーザー切断と比較すると速度の点で制限がある場合があります。
- ウォータージェット切断:特に厚い材料の場合、レーザー切断よりも時間がかかります。切断速度は、材料の種類や厚さなどの要因に影響されます。
- フレーム切断: 特に厚い材料の場合、レーザー切断に比べて時間がかかります。切断速度は材料の厚さによって異なります。
厚さの能力
- ファイバーレーザー切断: 薄い材料と厚い材料の両方に効果的ですが、非常に厚い部分では制限がある場合があります。
- プラズマ切断: 厚い金属を切断できることでよく知られており、高い切断力を必要とする用途に最適です。
- ウォータージェット切断: 厚い金属を効果的に切断できますが、具体的な能力は材料の特性によって異なります。材料が厚い場合は、適切な貫通を確保するために切断速度を遅くする必要がある場合があります。
- 火炎切断:材質が限られており、厚い炭素鋼の切断に最も効果的です。
熱影響区域 (HAZ)
- ファイバーレーザー切断: 従来の方法と比較して熱影響を受けるゾーンが小さくなり、材料の歪みや反りのリスクが最小限に抑えられます。
- プラズマ切断: 一般に、HAZ が大きくなり、特に薄い部分で材料の特性に影響を与える可能性があります。
- ウォータージェット切断: 滑らかなエッジが残りますが、切断面はわずかに先細りになる場合があります。このプロセスは冷間切断とみなされ、熱の影響を受ける部分が最小限に抑えられます。
- 火炎切断: より大きな熱影響ゾーンが生成され、より重大な熱歪みが発生する可能性があります。
運用費用
- ファイバーレーザー切断: 初期投資コストは高くなりますが、エネルギー効率と最小限の消耗品により、長期的には通常運用コストが低くなります。
- プラズマ切断: 通常、初期コストは低くなりますが、電極やガスなどの消耗品の継続コストが高くなる場合があります。
- ウォータージェット切断: これは、特に高圧ウォーターポンプと研磨材により、運用コストの点でより高価になる可能性があります。
- 火炎切断: 初期投資は低く抑えられますが、燃料ガスの消費により運用コストが高くなる可能性があります。
要約する
ファイバーレーザー切断機は、高度な切断ツールとして、その精度、速度、さまざまな材料や厚さに対する多用途性により好まれており、多くの分野で従来の金属切断装置を徐々に置き換え始めています。ただし、これは従来の切断プロセスが完全に市場を失うことを意味するものではありません。各方法には独自の利点があります。
ファイバーレーザー切断は、薄肉から中厚の材料の精度、速度、多用途性に優れる傾向があり、プラズマ切断は、高精度を必要としない厚い金属ワークの加工に適しており、ウォータージェット切断は、最小限の熱影響部が必要なワークの加工に適しています。火炎切断は、より厚い炭素鋼セクションに適している場合があります。ファイバーレーザー切断技術を使用する場合、多くの場合、企業は効率と精度を重視します。従来の切断プロセスを使用する場合、精度は主な考慮事項ではなく、コストの考慮が重要な役割を果たします。最終的に、どちらを選択するかは、特定の要件、材料の種類、予算の考慮事項によって決まります。
で AccTek レーザー、当社は、金属プレートレーザー切断機、チューブレーザー切断機、プレート&チューブレーザー切断機など、1KW〜30KWの電力オプションを備えたさまざまなタイプのファイバーレーザー切断装置をユーザーに提供します。さまざまな用途シナリオの切断ニーズを満たすためのオプションのアクセサリも多数あります。ファイバーレーザー切断ソリューションの詳細については、今すぐお問い合わせください。
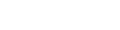
連絡先
- [email protected]
- [email protected]
- +86-19963414011
- No. 3 ゾーン A、Lunzhen 工業地帯、玉城市、山東省。
レーザー ソリューションを入手する