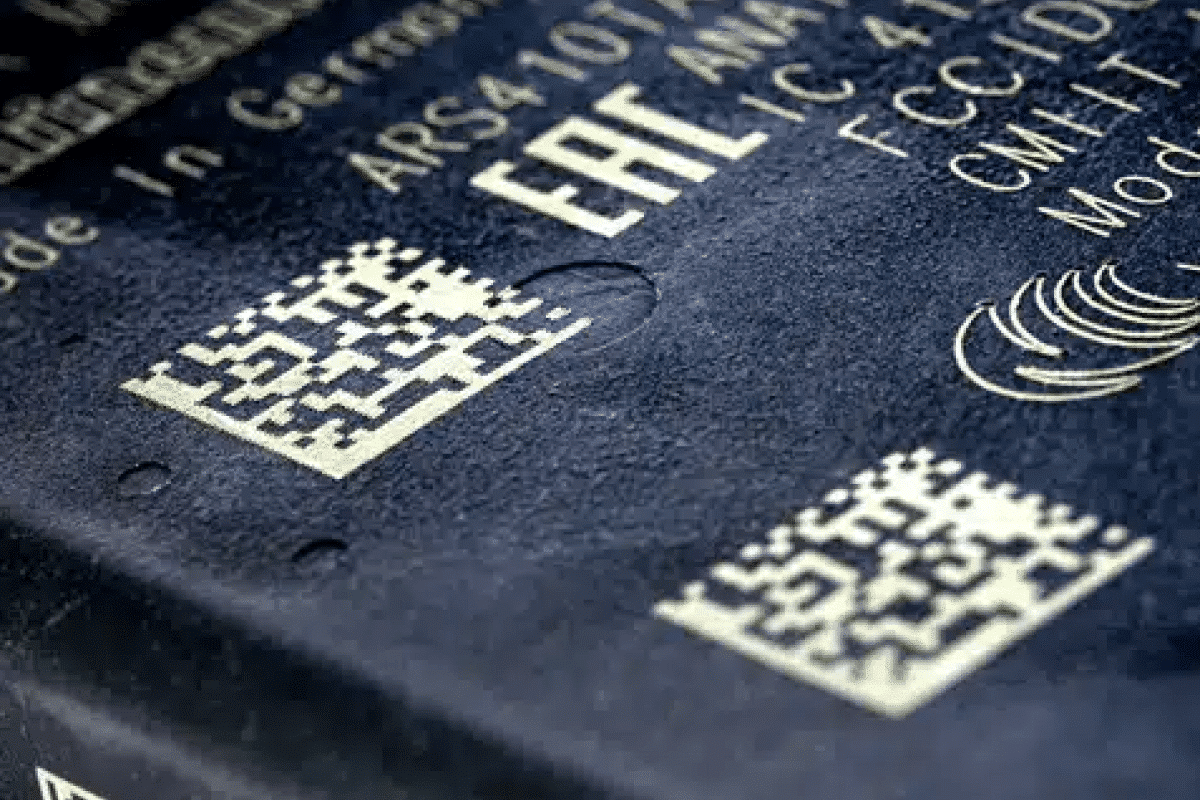
レーザーマーキング VS スクリーン印刷
工業用マーキングは製造業にとって不可欠な部分です。製品の製造プロセスであっても、最終製品の包装やラベル貼りであっても、工業用ラベルは重要な役割を果たします。
現在、工業用マーキングの世界では、レーザー マーキングとスクリーン印刷という 2 つの主な方法がメーカーや顧客に人気があります。どちらのテクノロジーにも利点はありますが、いくつかの制限もあります。この記事では、2 つの産業用マーキング技術について詳しく説明します。 レーザーマーキング とスクリーン印刷の長所と短所を比較し、適切なマーキング技術を選択する方法を検討してください。
目次
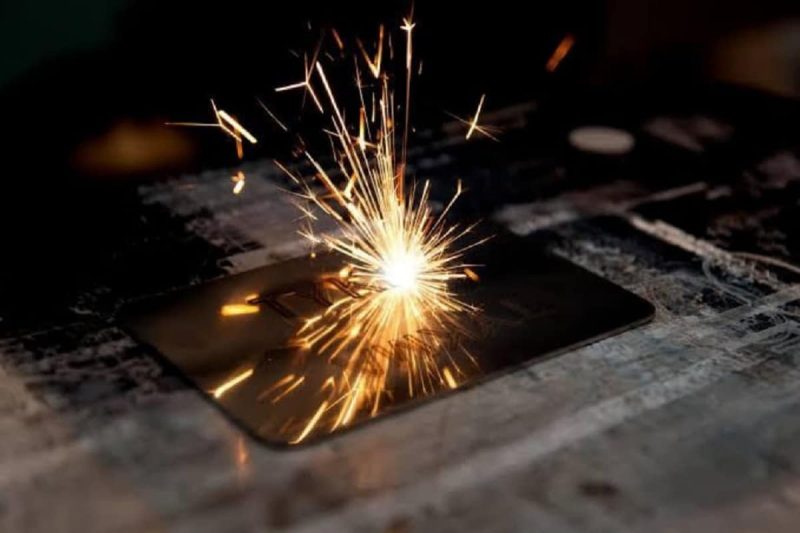
レーザーマーキングとは何ですか?
レーザーマーキングは、レーザービームを通じて物体の表面に直接切り込みを入れる、またはマークを付ける技術です。レーザーの高いエネルギー密度に基づいて、物体の表面に小さな傷や跡が生じることがあります。レーザーマーキングでは通常、レーザー発生器を使用してレーザービームを生成し、レンズやレンズを通してレーザービームをマーキングする必要のある表面に焦点を合わせます。
レーザーマーキングの原理
レーザーマーキングの動作原理は、レーザービームを使用して材料の表面を加工することです。レーザービームの高密度エネルギーは、材料表面の化学的または物理的特性に変化を引き起こします。処理の流れは次のとおりです。
- 適切なレーザー装置を選択する: ターゲット材料の特性と要件に応じて、適切な出力と波長を持つレーザー装置を選択します。さまざまな種類のレーザー (CO2 レーザー、ファイバー レーザー、Nd: YAG レーザーなど) が、さまざまな材料や用途に適しています。
- レーザー照射:レーザー装置を起動し、素材表面の特定の位置にレーザー光の焦点を合わせます。レーザービームの高エネルギーにより、材料の表面に蒸発、酸化、色の変化などの反応が引き起こされ、表面に目的のパターンや文字が残ります。
- 制御とデバッグ: オペレーターは通常、レーザー機器をリアルタイムで監視およびデバッグします。これには、出力、スキャン速度、焦点距離などのレーザー パラメータの調整も含まれ、マーキング効果を制御し、結果として得られるパターンが見えるようにします。
- 閉鎖と清掃: すべてのマーキング作業が完了したら、レーザー装置の電源を切り、材料を作業プラットフォームから取り外します。クーラントなどの補機類を使用している場合は、清掃やメンテナンスも必要です。
レーザーマーキングのメリット
レーザーマーキング技術はスクリーン印刷技術に比べて多くの利点があり、工業用マーキングの分野で人気があります。スクリーン印刷技術と比較したレーザーマーキング技術の主な利点は次のとおりです。
- 非接触:レーザーマーキングの進歩は、レーザー光線が加工材料に直接接触せず、機械的な押し出しや応力を生じず、加工品にダメージを与えないことです。これは、高い表面要件が要求されるアプリケーションにとって非常に重要です。
- 高精度: レーザーマーキングは、テキスト、グラフィックス、バーコードなどを含む非常に細かいマーキングを実現できます。スクリーン印刷では通常不可能な小さな部品に小さなマークを実現できます。
- 高速: レーザーマーキングは高速マーキングプロセスを実現でき、特に大量生産ラインに適しています。通常、スクリーン印刷よりも高速です。
- 低コスト: コンピューターによって自動的に制御されるため、生産プロセス全体が手動介入を必要とせず、人件費を大幅に節約できます。
- 幅広い用途: レーザーマーキングマシンシステムは、金属、プラスチック、ガラス木材、セラミック、革、石などの適切なキャリア上にデザインを復元できます。このプロセスは非常に正確です。
- 耐久性: レーザーマーキングされたマークは通常、非常に耐久性があり、摩耗、化学的攻撃、環境変化に対して耐性があります。これは、長期的な識別が必要なアプリケーションで非常に役立ちます。
レーザーマーキングのデメリット
スクリーン印刷技術と比較すると、レーザーマーキング技術には潜在的な欠点もいくつかあります。
- 高い初期コスト: レーザー マーキング装置は一般に比較的高価であるため、一部の中小企業やアプリケーションにとっては手頃な価格ではない可能性があります。それに比べて、スクリーン印刷装置は通常より安価です。
- 適用範囲の制限: レーザーマーキングには、さまざまな種類の材料や表面への適用に関して一定の制限があります。一部の材料はレーザー光の吸収能力が限られており、マーキングには高出力のレーザー源が必要になる場合があります。この点において、スクリーン印刷技術はより柔軟であり、より広い適用範囲を持っています。
- 環境要因: レーザーマーキングプロセスでは高エネルギーのレーザービームが生成されるため、追加の冷却システムと慎重に設計された作業環境が必要になる場合があります。レーザーマーキング中に煙、臭気、または有害なガスが発生する場合もあるため、適切な換気と排気ガス処理が必要です。
- 安全性と目の保護: レーザーマーキングに使用されるレーザー光線は潜在的に危険であり、オペレーターの目に脅威を与える可能性があります。したがって、リスクを軽減するために保護メガネが必要です。
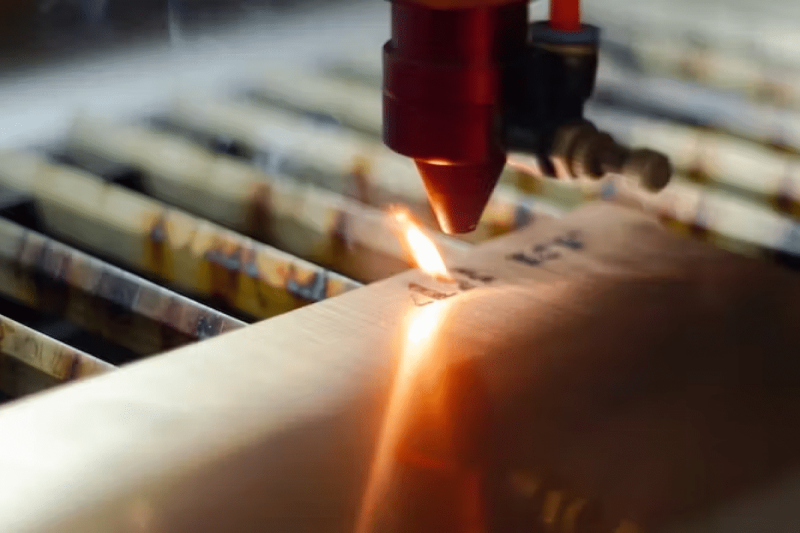
スクリーン印刷とは何ですか?
スクリーン印刷は、穴のメッシュを持つスクリーンを使用してインクまたはインクを印刷物に転写する伝統的な印刷技術です。この技術は、スクリーンの穴を使用してインクの転写を制御し、印刷物上に目的のパターンを作成します。
スクリーン印刷の原理
スクリーン印刷プロセスの印刷原理は、スクリーンを使用してインクまたはインクを転写し、印刷物に目的のパターンまたはマークを作成することに基づいています。スクリーン印刷プロセスの印刷プロセスは次のとおりです。
- 材料の準備: インクまたはインクをスクリーンの一方の端に置きます。印刷物 (紙、布、ガラス、プラスチックなど) を画面の下に置きます。
- 印刷するには: スキージまたはスキージを使用してスクリーンの上部をこすり、インクまたはインクをスクリーンの開口部に転写します。スクリーンのメッシュには一定の開口部があるため、インクまたはインクは開口部を通って印刷材料にのみ転写され、目的のパターンまたは文字が形成されます。
- 乾燥と硬化: 印刷が完了したら、パターンがにじんだり消えたりしないように、インクを乾燥して硬化する必要があります。これは、自然乾燥、またはオーブン、UV ランプなどの機器を使用して行うことができます。
- 繰り返し印刷: マルチカラー印刷またはマルチレイヤー印刷の場合は、毎回異なるスクリーンとインクの色を使用して上記の手順を繰り返し、カラフルなパターンをレイヤーごとに構築できます。
スクリーン印刷のメリット
スクリーン印刷はいくつかの点でレーザーマーキングほど優れていませんが、特定のアプリケーションシナリオでは非常に価値のある利点がいくつかあります。その利点のいくつかを以下に示します。
- 幅広い適用性: スクリーン印刷は、紙、プラスチック、ガラス、布地など、さまざまな種類の材料に適用できます。
- 低コスト: レーザーマーキング装置と比較して、スクリーン印刷装置は通常コストが低く、小規模および中規模の生産に適しています。
- 大面積印刷: スクリーン印刷は、看板、ポスター、大型パッケージなど、より大きな表面に印刷する必要がある用途に適しています。大型サイズの印刷業務にも対応できます。
- マルチカラー印刷: スクリーン印刷では複数の色のインクを使用して、カラフルな印刷効果を実現できます。
- 耐久性: スクリーン印刷されたマーカーは一般にある程度の耐久性があり、特に適切なインクとコーティングが使用されている場合、ある程度の摩耗や環境の影響に耐えることができます。
- 柔軟性: スクリーン印刷技術は、広告、包装、繊維、エレクトロニクス、ガラス製造などを含むさまざまな業界で使用できるため、柔軟性が高くなります。
スクリーン印刷のデメリット
レーザーマーキング技術と比較すると、スクリーン印刷技術には明らかな欠点がいくつかあり、さまざまな用途シナリオでの選択に影響を与える可能性があります。
- 解像度の制限: スクリーン印刷の解像度は比較的低いため、スクリーン印刷では印刷された細部や小さなオブジェクトに鮮明なマークやパターンが表示されない場合があります。
- 限られた色のオプション: スクリーン印刷には色ごとに個別のスクリーンが必要で、複数の色で印刷する場合は複数の印刷と位置合わせが必要になる場合があり、複雑さとコストが増加します。
- 製版コスト:スクリーン印刷ではスクリーンやスクリーンを作成する必要があり、製版コストが高額になります。印刷パターンや印刷内容を頻繁に変更する必要がある場合、製版コストが負担となることがあります。
- 生産速度が遅い: レーザーマーキングに比べて、スクリーン印刷の生産速度は一般的に遅くなります。これは、高スループットと迅速な生産を必要とするアプリケーションには十分な効率が得られない可能性があります。
- 利用可能な材料の制限: スクリーン印刷は幅広い材料に利用できますが、場合によっては制限がある場合があります。たとえば、曲面や凹凸のある表面などの一部の特殊な素材では、スクリーン印刷では均一な印刷効果が得られない場合があります。
- 環境への配慮: 一部の印刷インキには有害な物質が含まれている場合があり、環境に悪影響を与える可能性があるため、特定の対策が必要です。
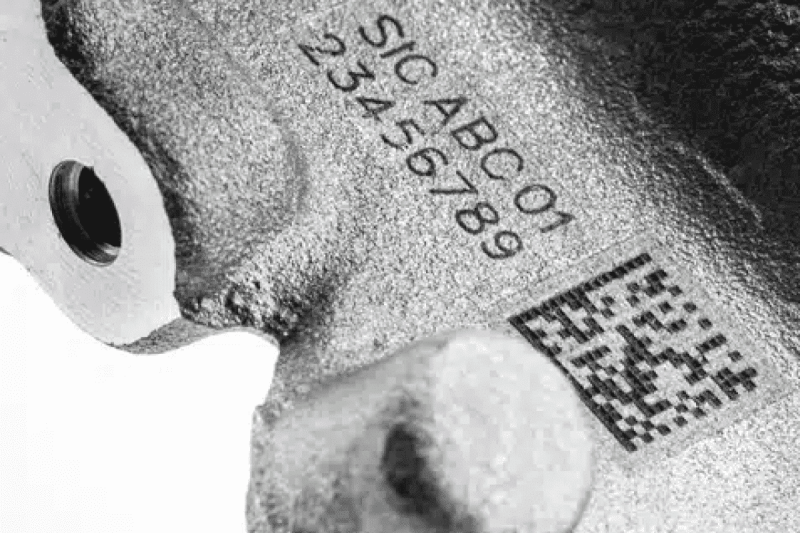
レーザーマーキングとスクリーン印刷: どちらの技術を選択すべきか
マーキング技術を選択する際には、選択した技術が特定のアプリケーション シナリオに最適であることを確認するために、いくつかの要素を考慮する必要があります。レーザー マーキングまたはスクリーン印刷技術を選択する際に考慮すべき主な要素は次のとおりです。
精度と分解能
マークする必要があるパターンまたはテキストの精度要件を考慮してください。非常に細かいマーキングが必要な場合は、多くの場合、解像度と精度が高いレーザーマーキング技術の方が適しています。
耐久性
マーカーの耐久性のニーズを考慮してください。自動車部品や医療機器など、マークが長期間にわたって判読できる必要がある場合、多くの場合、レーザー マーキングの方が耐久性が高くなります。
スピードと生産性
生産ラインの速度と生産量の要件に基づいて、テクノロジーの生産効率を検討します。レーザーマーキングは一般に高速であり、大量生産環境に適しています。
アプライドマテリアルズ
材料の種類に応じて、異なるマーキング技術が適しています。どのテクノロジーがより適しているかを判断するには、マーキングが必要な材料を検討してください。スクリーン印刷は一般にさまざまな材料に適していますが、レーザーマーキングは一部の特殊な材料に限定される場合があります。
製版費用
コストの見積もりは重要な要素です。レーザー機器は一般に高価であり、メンテナンス費用も高くなります。従来の溶接技術は、特に小規模なプロジェクトや予算が限られている企業にとっては、より安価なことがよくあります。
材料の厚さ
ワークの厚みを考慮してください。レーザー溶接は薄い材料に適していますが、厚い材料の場合は複数のパスが必要になる場合があります。従来の溶接は一般に、さまざまな厚さの材料に適しています。
環境および安全要件
作業環境と安全要件を考慮してください。レーザー溶接では、オペレータの安全を保護するために、より厳格な環境管理と安全対策が必要となる場合があります。
要約する
従来の溶接方法にも利点はありますが、レーザー溶接は金属を接合するための一般的な選択肢であり、その精度、制御、繊細な金属部品や薄い金属部品を溶接できるため、複数の部品製造業界で人気が高まっています。適切な溶接方法の選択は、特定の用途のニーズ、コスト、品質基準によって異なります。
レーザー溶接機をお探しならぜひご検討ください。 AccTek レーザー。当社にはレーザー溶接の分野での実績のある経験があります。当社のレーザー溶接能力に関する情報が必要な場合は、当社を訪問し、お問い合わせください。
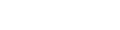
連絡先
- [email protected]
- [email protected]
- +86-19963414011
- No. 3 ゾーン A、Lunzhen 工業地帯、玉城市、山東省。
レーザー ソリューションを入手する