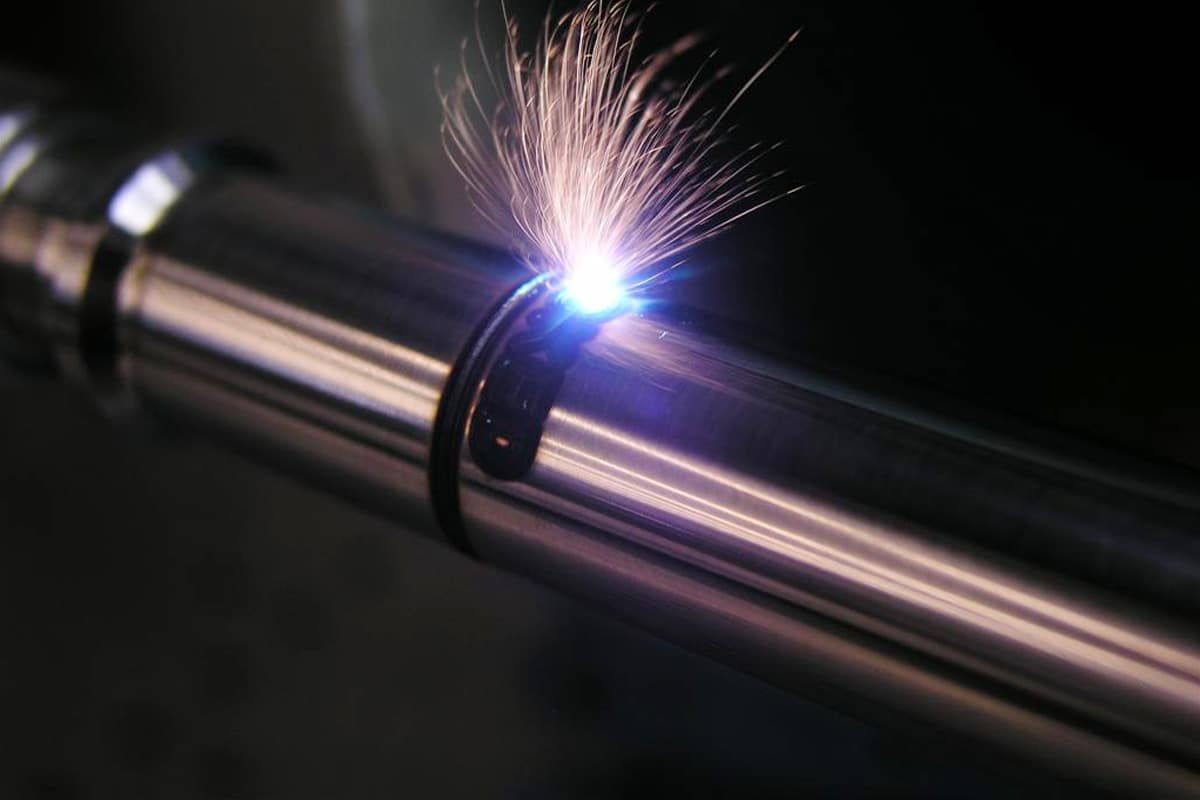
レーザーマーキングの設計上の考慮事項と制限
レーザーマーキング技術の幅広い応用は、現代の工業生産に欠かせないものとなっています。しかし、マーキングや彫刻の精度と柔軟性が高いにもかかわらず、実際のアプリケーションでは、設計者は最良の結果を確保するためにさまざまな要素を慎重に考慮する必要があります。材料の選択からレーザーパラメータの調整、安全性の考慮まで、これらはすべてレーザーマーキングを設計する際に注意する必要がある重要な要素です。同時に、レーザーマーキング技術には、特定の材料が不適切であったり、表面処理要件が制限されたりするなど、いくつかの制限もあります。
この記事では、これらの設計上の考慮事項と制限について検討し、レーザー マーキング技術の基礎、方法、およびこれらの制限に対処するための革新の概要も紹介して、読者がレーザー マーキング技術をよりよく理解して適用できるようにします。
目次
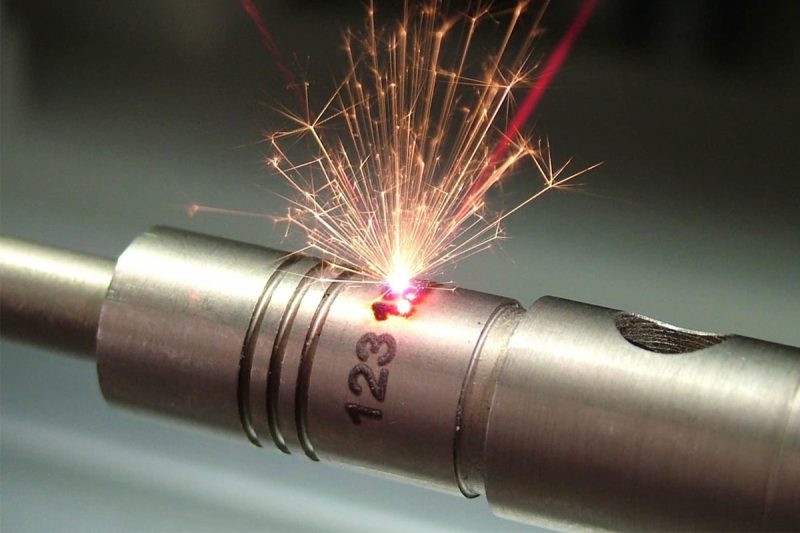
レーザーマーキング技術の基本原理
レーザーマーキング技術は、レーザービームを使用して材料の表面にエッチング、マーキング、または切断を行う加工方法です。基本的な原理は次のとおりです。
- レーザー生成: レーザー マーキング システムでは通常、ガス レーザー ジェネレーター、固体レーザー ジェネレーター、または半導体レーザー ジェネレーターがレーザー ソースとして使用されます。これらのレーザー ジェネレーターは、高度に集中したレーザー ビームを生成します。
- レーザー ビームの集束: レンズやミラーなどの光学素子を通してレーザー ビームを非常に小さな焦点に集束させ、高エネルギー密度のスポットを形成します。
- レーザーエネルギーの役割:レーザービームが材料の表面に照射されると、その高いエネルギー密度により材料が局所的に加熱され、溶融または気化温度に達し、エッチングまたは蒸発を引き起こします。
- 材料の反応: 材料によってレーザー光に対する反応は異なります。金属は通常、吸収率が高く、表面で蒸発や酸化が起こりやすいのに対し、非金属材料は熱化学反応やアブレーションを起こす可能性があります。
- 制御システム: レーザーマーキングシステムには高度な制御システムが装備されており、設計書に従ってレーザービームの位置、出力、移動経路を制御し、正確なマーキングや切断を実現します。
- マーキング効果:レーザーマーキングは、永久的で高精細かつ高精度のマークを生成できるため、さまざまな材料や複雑なパターンの加工に適しています。
以上のステップにより、レーザーマーキング技術は材料表面の精密な加工を実現し、工業生産、医療機器、電子機器などで広く使用されています。
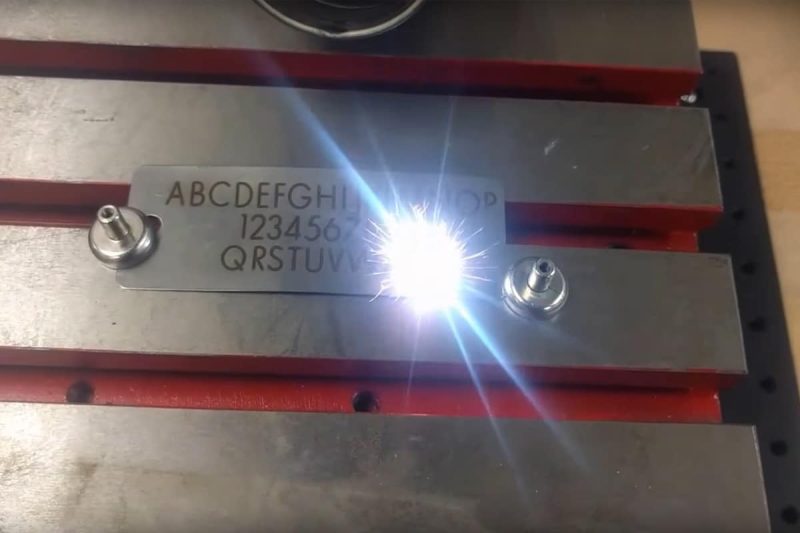
レーザーマーキングにおける具体的な設計上の考慮事項
レーザーマーキング技術は、工業生産などの分野で広く使用されている高精度加工技術です。ただし、レーザーマーキング技術を使用する場合、設計者はマークの品質、安全性、効率を確保するために、いくつかの特定の設計上の考慮事項に注意する必要があります。以下は、レーザーマーキングにおける特定の設計上の考慮事項です。
材料の選択と互換性
レーザーマーキングに適した材料を選択する際には、材料の吸収特性と反射特性を考慮する必要があります。金属などの一部の材料は一般に吸収率が高く、レーザーマーキングに適しています。反射率が高い一部の非金属材料(プラスチックやガラスなど)の場合、良好な結果を得るには高出力のレーザーが必要になる場合があります。また、有機材料などの一部の特殊材料は、レーザーマーキングプロセス中に有毒ガスを生成する可能性があるため、追加の保護対策が必要です。
レーザーパラメータの調整
レーザー マーキングの効果は、レーザー出力、周波数、パルス幅、焦点距離などのレーザー パラメータによって左右されます。これらのパラメータを適切に調整することで、最高のマーキング効果が得られます。出力が低すぎるとマーキングが不明瞭になり、出力が高すぎると材料が溶けたり損傷したりする可能性があります。周波数とマーキング速度の調整も、最終的なマーキングの品質と速度に影響します。
表面処理要件
レーザーマーキングでは通常、マーキング効果を得るために材料表面に一定の温度または化学反応が必要です。したがって、レーザーマーキングの前に、油汚れ、酸化層、コーティングを除去するなど、材料表面を適切に処理して、最高のマーキング効果を確保する必要があります。さらに、材料によっては、マーキングのコントラストを高めるために特殊なマーキング剤を塗布するなどの前処理が必要になる場合があります。
セキュリティ上の問題
レーザーマーキング装置から発せられるレーザー放射は人体や環境に有害であるため、レーザーマーキング装置を使用する際には安全規則を厳守する必要があります。作業員は専門的な訓練を受け、レーザー安全メガネや保護シールドなどの適切な保護具を使用して、レーザー放射による人体への損傷を軽減する必要があります。また、レーザーマーキング装置は専用の操作エリアに設置し、予期しない事態に対処するために緊急停止ボタンや安全警告標識を装備する必要があります。
設計ファイルの準備
レーザーマーキングの前に、設計者は設計ファイルを準備し、それが レーザーマーキング装置正しい設計ファイル形式とパラメータ設定により、最終的なマーキングの品質と精度を確保できます。さらに、設計ドキュメント内のパターンとテキストは、レーザーマーキングプロセス中に確実に表示されるように、特定のサイズと比率を持つ必要があります。
その後の処理と検査
レーザー マーキングが完了したら、通常はその後のマークの処理と検査が必要です。フォローアップ処理には、洗浄や除塵のほか、耐久性を高めるためにマーキングに保護コーティングや表面処理を施すことが含まれます。検査は目視検査または光学顕微鏡などの機器を使用して実行し、マークの品質と精度が要件を満たしていることを確認します。
まとめると、レーザーマーキングは工業生産において重要な応用価値を持っていますが、設計者はレーザーマーキング技術を使用する際に、最終的なマーキングの品質、安全性、効率性を確保するために、いくつかの特定の設計事項に注意を払う必要があります。高品質のレーザーマーキング処理は、材料の合理的な選択、レーザーパラメータの調整、表面処理、安全規制の厳格な遵守、適切な設計文書の作成を通じて実現できます。
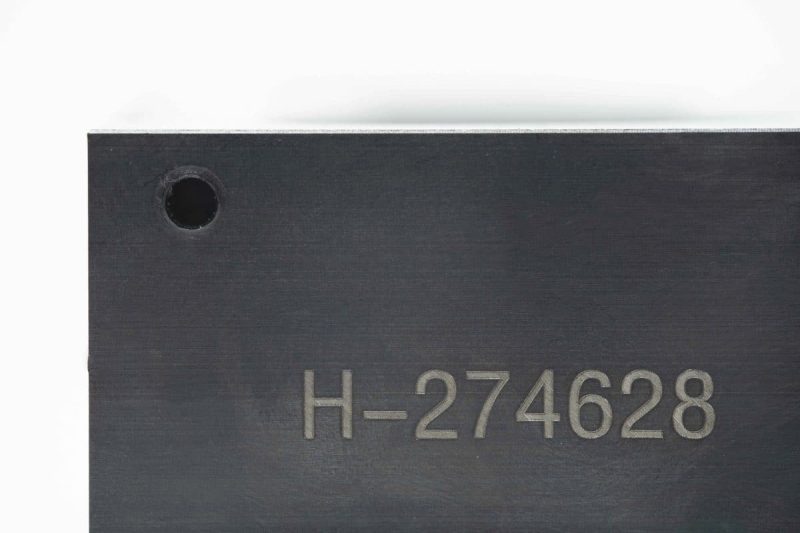
レーザーマーキングにおける特定の設計上の制限
レーザーマーキングの適用可能な材料の範囲には一定の制限があります。レーザーマーキングは金属、プラスチック、ガラス、セラミックなどの多くの一般的な材料に適していますが、一部の高反射率金属、透明材料、光学ガラスなどの特殊な材料では、レーザーエネルギーの吸収と反射が十分でない場合があります。理想的ではないため、明確なマーキング効果を得ることが困難です。
素材の制限
レーザーマーキングの適用可能な材料の範囲には一定の制限があります。レーザーマーキングは金属、プラスチック、ガラス、セラミックなどの多くの一般的な材料に適していますが、一部の高反射率金属、透明材料、光学ガラスなどの特殊な材料では、レーザーエネルギーの吸収と反射が十分でない場合があります。理想的ではないため、明確なマーキング効果を得ることが困難です。
表面処理要件
レーザー マーキングでは通常、マーキング効果を確実にするために材料表面を適切に処理する必要があります。材料によっては、レーザーと材料の相互作用を高めるために、酸化物層、コーティング、その他の汚染物質を除去する必要がある場合があります。ただし、表面処理によって、特に大量生産の場合、生産コストと複雑さが増す可能性があります。
マーキングサイズと深さの制限
レーザーマーキングのサイズと深さには制限があります。レーザーマークは材料の表面を局所的に加熱してマーキングするため、マークの深さは通常浅くなり、深い加工を実現するのは困難です。また、レーザービームの焦点サイズと焦点深度によって、マーキングされたマーカーの最小サイズと精度も制限されます。
複雑なパターンと詳細
レーザーマーキングは高精度のマーキング効果を実現できますが、複雑なパターンや細部を処理する場合には一定の制限があります。たとえば、非常に小さなサイズや複雑な構造のパターンを処理する場合、レーザーマーキングはビームの焦点合わせや制御精度によって制限され、満足のいくラベリング効果が得られないことがあります。
生産効率の限界
レーザーマーキングは通常、効率的な加工方法と考えられていますが、大量処理の場合は生産効率の制限に直面する可能性があります。レーザーマーキング速度は、レーザー出力、材料特性、マーキング深さなどの要因によって影響を受けます。したがって、実際のアプリケーションでは、品質と生産効率の関係が必要になる場合があります。
要約すると、レーザーマーキング技術には多くの利点がありますが、実際のアプリケーションでは特定の設計と制限がいくつかあります。設計者はこれらの制限を十分に考慮し、設計と製造プロセスで対応する対策を講じて、レーザーマーキング技術の利点を最大限に引き出し、起こり得る問題を解決する必要があります。
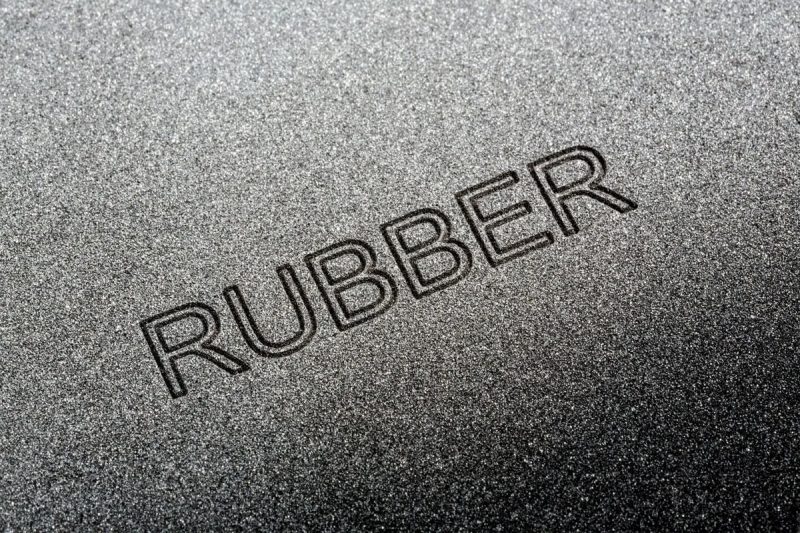
ソリューションとイノベーション
レーザー マークの特定の設計上の注意事項と制限については、次のソリューションとイノベーションを採用できます。
材料適応性イノベーション
- レーザーと特定の材料との相互作用を強化し、マーキング効果を向上させる新しいレーザーマーキングマシンまたは添加剤を開発します。
- 多波長レーザーシステムの使用を検討し、レーザー波長の吸収に関するさまざまな材料の吸収特性に適応し、レーザーマーキングの対象となる材料の範囲を拡大します。
- 表面処理技術を開発し、素材表面の吸収・反射を改善し、レーザーマークの効率と精度を向上させます。
レーザーパラメータ最適化イノベーション
- 高度なレーザー制御技術を活用して、レーザーパラメータの動的な調整と最適化を実現し、さまざまな材料やマーキング要件に適応します。
- ディープラーニングと人工知能技術を活用してレーザーパラメータ設定を自動的に最適化し、レーザーマーキングの効率と精度を向上させます。
- マルチビームまたは複合レーザー システムを開発して、複数のパラメータを同時に制御し、レーザー マーキングの柔軟性と多様性を向上させます。
セキュリティ保護イノベーション
- レーザー光線監視システムや自動緊急停止装置などのインテリジェントな安全装置を設計して使用し、レーザー放射による危険を迅速に検出して回避します。
- より快適なレーザー安全メガネや通気性に優れた保護服など、より効率的で快適なレーザー安全保護具を開発します。
- より厳格な安全基準と操作手順を策定し、レーザーマーキング作業者のトレーニングと監督を強化し、職場の安全性と環境保護レベルを向上させます。
マーク品質最適化イノベーション
- レーザーマーキングのエネルギー密度と安定性を高め、マーキングの品質と一貫性を向上させるために、高出力で安定性の高いレーザーデバイスと光学システムを開発します。
- 光学イメージングと 3 次元スキャン技術を使用して、マーキング プロセスのリアルタイム監視とフィードバックを実現し、マーキング プロセスの問題をタイムリーに発見して修正し、マーキングの品質と精度を向上させます。
- フェムト秒レーザーマーキングや超高速レーザー加工などの新しいレーザーマーキング技術の使用を検討し、特定の材料の超高精度およびマイクロナノスケールのマーキングを実現します。
生産効率向上イノベーション
- インテリジェントなレーザーマーキング システムを設計および適用して、自動化された生産と効率的な処理を実現し、生産効率とコスト効率を向上させます。
- レーザーマーキング技術を使用して大量カスタマイズ生産を実現し、顧客のニーズに応じて生産パラメータとマーキングパターンをリアルタイムで調整し、生産の柔軟性と応答速度を向上させます。
- レーザーマーキングとレーザー切断、レーザー溶接などの加工技術を統合したソリューションを開発し、多工程ジョイント加工を実現し、生産効率と加工品質を向上させます。
レーザーマーキング技術と関連機器およびプロセスの継続的な革新と改善を通じて、レーザーマーキングにおける特定の設計上の考慮事項と制限に効果的に対処し、レーザーマーキングの適用範囲、効率、品質を向上させることができます。
要約する
レーザーマーキング技術の応用においては、特定の設計上の考慮事項と制限を真剣に考慮する必要があります。材料の選択からレーザーパラメータの調整、安全性の考慮まで、これらの要素はレーザーマーキングの有効性と安全性に直接影響します。設計者は、これらの制限を克服し、レーザーマーキング技術の開発と応用を促進するための方法と技術革新を常に模索する必要があります。レーザーマーキング技術の特性を深く理解し、革新的なソリューションと組み合わせることで、レーザーマーキングの応用分野をさらに拡大し、生産効率と製品品質を向上させることができます。
したがって、レーザー マーキングには特定の設計上の考慮事項と制限がありますが、革新と改善に努め続ける限り、レーザー マーキング技術は現代の工業生産における重要なツールとなり、あらゆる分野にさらなる可能性と開発の機会をもたらします。レーザー マーキングとレーザー彫刻のプロセスについてさらに詳しく知りたい場合は、AccTek Laser の専門家にお問い合わせください。
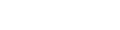
連絡先
- [email protected]
- [email protected]
- +86-19963414011
- No. 3 ゾーン A、Lunzhen 工業地帯、玉城市、山東省。
レーザー ソリューションを入手する