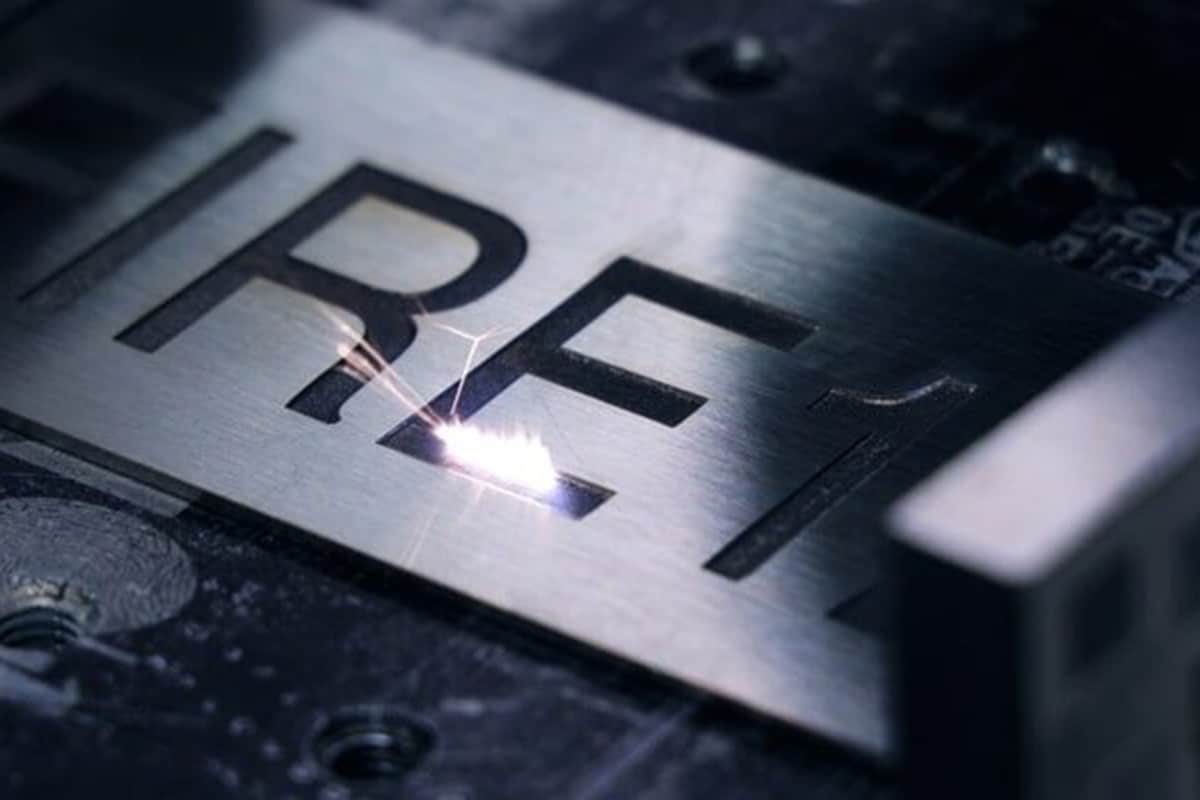
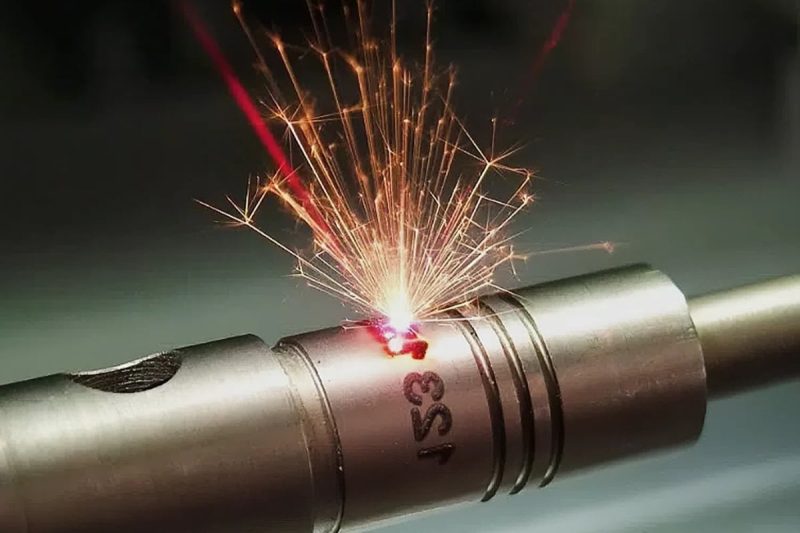
レーザーマーキングの紹介
レーザーマーキングの概要
レーザーマーキングマシンの主なカテゴリー
ファイバーレーザーマーキングマシン
CO2レーザーマーキングマシン
UVレーザーマーキングマシン
レーザーマーキングの種類
レーザーアニーリング
レーザー彫刻
レーザーエッチング
炭素移動
発泡
色の変更
レーザーマーキングに影響を与える要因
レーザーパラメータ
材料特性
環境条件
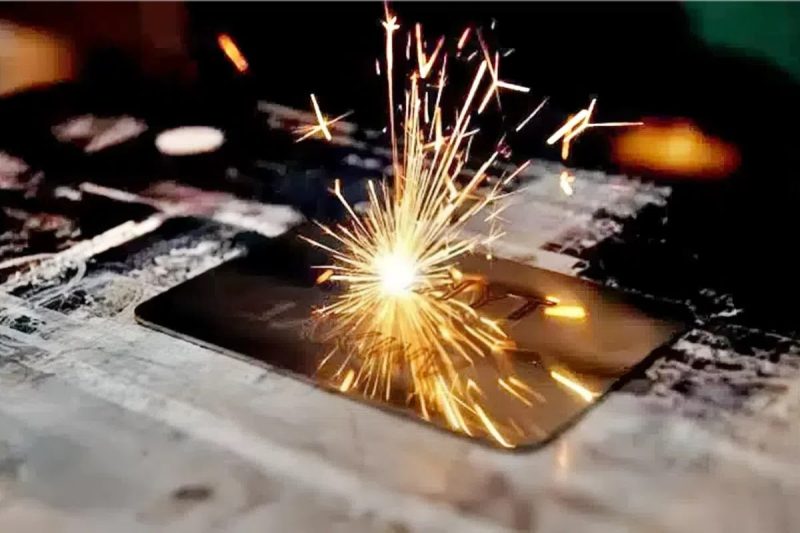
金属へのレーザーマーキングの仕組み
- アニーリングマーキング:アニーリングマーキングは、局所加熱により鉄系金属(鉄、鋼、高級鋼)およびチタン上に酸化物層を形成することです。レーザーアニーリングは、レーザー照射熱を使用して、材料を大幅にアブレーションすることなく局所酸化を誘発するマーキング技術です。
- レーザーエッチング:レーザーエッチングでは、高熱レーザーを使用して金属材料の表面のみを溶かします。エッチングされた部分に酸化が形成される場合があり、マークがよりはっきりと見えるようになります。
- レーザー彫刻: レーザー彫刻は、彫刻プロセス中にレーザーが高熱を発生させ、金属材料を溶かして蒸発させるプロセスです。表面に目に見える溝が形成されます。
さまざまな金属に対するレーザーマーキングの影響
- ステンレス鋼: ステンレス鋼は、耐腐食性と機械的特性に優れているため、広く使用されています。レーザーマーキングは、ステンレス鋼の表面に鮮明で耐久性のあるマークを形成でき、摩耗しにくいです。ただし、レーザーマーキングプロセス中に小さな白い斑点が現れることがあります。これは主に、レーザー出力が高すぎる、マーキング速度が速すぎる、ステンレス鋼の表面が汚れているなどの理由によって発生します。
- アルミニウム: 陽極酸化アルミニウムへのレーザーマーキングは、レーザーが陽極酸化層を除去してその下の金属を露出させ、高いコントラストを実現するため、非常に簡単です。さらに、むき出しのアルミニウムは軽量で耐腐食性のある金属であり、表面に鮮明なマークを形成できます。ただし、アルミニウムは反射率と熱伝導率が高いため、アルミニウム表面でのレーザービームの吸収率が低く、マーキング結果が悪くなるか、より高いレーザー出力が必要になる場合があります。
- 真鍮: 真鍮は、加工性能と美観に優れた銅亜鉛合金です。レーザーマーキングは、真鍮の表面に鮮明で繊細なマークを形成することができ、彫刻の深さを制御するのが容易です。ただし、レーザー出力が高すぎると、真鍮の表面が磨耗したり変形したりする可能性があります。
- 銅: 銅は導電性と熱伝導性に優れた金属です。レーザーマーキング時に反射問題が発生しやすく、マーキング効果に影響します。また、銅の表面酸化もマーキング効果に影響を及ぼす可能性があります。
- チタン: チタンは高強度で耐腐食性に優れた金属です。レーザーマーキングにより、チタンの表面に高品質のマーキングを施すことができます。ただし、チタンは熱伝導率が高いため、チタン表面のレーザービームの熱影響部が大きくなる可能性があり、材料の損傷を避けるためにレーザーパラメータを正確に制御する必要があります。
共通の課題と解決策
反射率
- 反射率の高い金属(アルミニウムや銅など)は、レーザーマーキング中にレーザービームが反射し、マーキング効果に影響を与える可能性があります。
- 反射防止コーティングを採用。
- レーザーの角度を調整します。
熱伝導率
- 熱伝導率の高い金属(アルミニウムやチタンなど)は、レーザーマーキング中に急速な熱拡散を引き起こし、熱影響部が増加して材料損傷のリスクが高まります。
- 過熱すると金属が曲がったり変色したりする可能性があります。
- 熱を制御するには、パルスレーザーを使用するか、レーザーのパワーと速度を調整します。
- 各プロセス間で金属を冷却することも、問題の解決に役立ちます。
酸化
- 一部の金属(銅など)は、長時間空気にさらされると酸化されやすく、酸化層が形成され、レーザーマーキングの効果に影響を与える可能性があります。
- マーキングする前に金属表面を洗浄し、脱酸します。
- 適切なレーザーパラメータを選択して、酸化物層を貫通し、金属基板上に明確なマークを形成します。
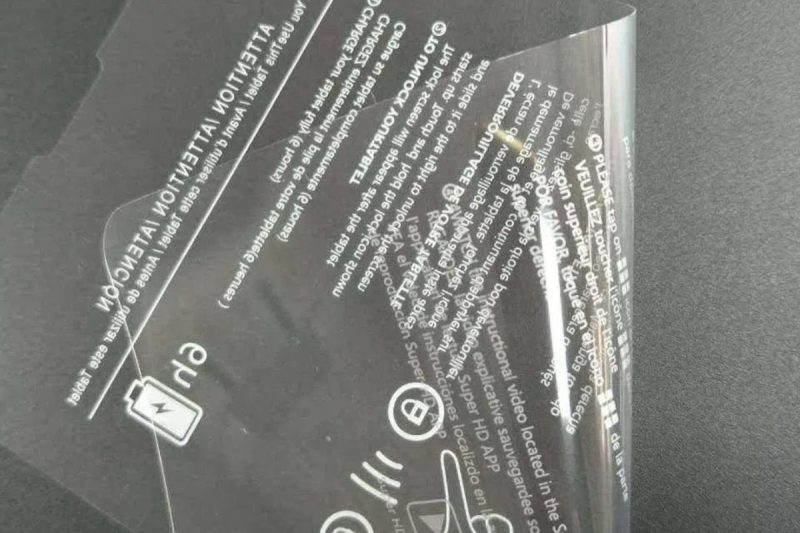
プラスチックへのレーザーマーキングの仕組み
- 泡立ち・変色:プラスチック内の炭素は局所的な加熱により破壊され蒸発し、酸化されて二酸化炭素を形成し、これがプラスチックから放出されて泡の層を形成し、その後これらの材料は冷却されて硬い泡になります。 成分に応じて、変色は明るくなったり暗くなったりします。 暗いプラスチックはマーキングする場所で色が白に変わり、明るいプラスチックは灰色または黒に変わります。
- 炭化:レーザー炭化の場合、プラスチックが破壊され、その中の炭素が放出されます。マーキングされた材料の色は常に暗くなり、その結果生じる変色は灰色から青灰色、黒色までの範囲になります。炭化は、明るい色のプラスチックや有機材料(紙、包装材料、木材、皮革)に使用され、色が明るい色から暗い色に変わります。
さまざまなプラスチックに対するレーザーマーキングの効果
ポリカーボネート(PC)
- 特徴: ポリカーボネートは、高強度、高光透過率、高耐熱性を備えたプラスチックです。
- レーザーマーキング効果: ポリカーボネートは、低強度のレーザービーム照射下でもレーザーマーキング中に炭化され、鮮明なマークが生成されます。これは、ポリカーボネートがレーザーの吸収率が高く、レーザーの作用下で物理的または化学的に変化しやすいためです。レーザーパラメータ (出力、周波数、スキャン速度など) の選択は、マーキング効果にとって重要であることに注意してください。パラメータが高すぎたり低すぎたりすると、マーキング結果が悪くなったり、材料が損傷したりする可能性があります。
アクリロニトリルブタジエンスチレン(ABS)
- 特徴: アクリロニトリルブタジエンスチレン (ABS) は、総合的な特性、優れた機械的特性、耐摩耗性、加工性能を備えた熱可塑性プラスチックです。
- レーザーマーキング効果: アクリロニトリルブタジエンスチレン (ABS) はレーザーに対する応答性が高く、レーザーマーキングマシンで鮮明で持続的なマーキングを実現できます。レーザーマーキングプロセスパラメータ (電流強度、周波数、ステップ長など) を最適化することは、マーキング効果を向上させるために重要です。たとえば、適切なパラメータの下では、アクリロニトリルブタジエンスチレン (ABS) の表面に発泡が発生し、より明るいマーキング効果が得られます。
ポリエチレン(PE)
- 特徴: ポリエチレン (PE) は、優れた耐低温性、化学的安定性、電気絶縁性を備えた、広く使用されている熱可塑性プラスチックです。
- レーザーマーキング効果: レーザーマーキングマシンは、製造日、バッチ番号、仕様モデルなどの鮮明で永続的なマークをポリエチレン (PE) パイプに刻印できます。これらのマークは、製品のトレーサビリティと品質管理に不可欠です。ポリエチレン (PE) 材料のレーザー吸収率は比較的低いため、理想的なマーキング効果を得るには、より高いレーザー出力またはより長い処理時間が必要になる場合があります。
ポリプロピレン(PP)
- 特徴: ポリプロピレン (PP) は、無毒、無臭、低密度、高強度、硬質、耐熱性を備えたプラスチックです。
- レーザーマーキングの効果:レーザーマーキングマシンは、洗面器、樽、鮮度保持箱、家具、フィルム、織り袋などのポリプロピレン(PP)プラスチック製品の生産ラインでよく使用されます。UVレーザーは、焦点が非常に小さく、熱影響部が小さいため、PPなどのプラスチックの超微細マーキングに特に適しています。UVレーザーマーキングは、材料に熱による損傷を与えることなく、高速で高精度な加工を実現できます。
ポリ塩化ビニル(PVC)
- 特徴: ポリ塩化ビニル (PVC) は、フリーラジカル重合メカニズムによって形成されるポリマーであり、優れた耐薬品性、絶縁性、難燃性を備えています。
- レーザーマーキング効果:ポリ塩化ビニル(PVC)材料もレーザーマーキング中に鮮明なマークを生成できます。ただし、ポリ塩化ビニル(PVC)材料の特殊な特性(熱に敏感、分解しやすいなど)により、材料の損傷や有害ガスの発生を避けるために、適切なレーザーパラメータと処理戦略を選択する必要があります。紫外線レーザーは、操作が簡単で、マークが消えにくく、環境保護と無公害であるため、ポリ塩化ビニル(PVC)材料のマーキングに広く使用されています。
課題と解決策
熱による損傷
- 高強度レーザー照射による材料の過度な炭化を避けるために、機械のパワーを下げることもできます。
- 冷間加工マーキング装置を使用します:UVレーザーマーキングマシン。
添加物
- 一般的な樹脂、ABS、PP、PEなどの材料など、一部のプラスチック製品にレーザーマーキングする場合、レーザーマーキングマシンは彫刻できないか、不明瞭になります。また、レーザーマーキング中にプラスチックの表面に気泡が発生し、マーキングが不明瞭になることがあります。
- レーザーパウダー(レーザー彫刻パウダーまたはレーザー添加剤)を原材料に添加することができます。レーザーパウダーの主な機能は、レーザーエネルギーを吸収し、レーザービームを熱エネルギーに変換し、添加剤自体の変色による熱、炭化、蒸発、化学反応を発生させ、製品の表面にマーキングパターンを形成することです。
煙
- レーザーマーキングマシンから発生する煙は、ワークピースによって決まります。一部の金属製品は煙を放出しにくいです。単純な金属製品であれば、これらの煙はほとんど無臭です。プラスチック製品やその他の製品の場合は、臭いが発生する場合があります。したがって、レーザーマーキングマシンの臭いと煙は、レーザー加工中にワークピースが揮発することによって発生します。レーザーマーキングマシンのレーザー自体は煙を放出しないため、煙の発生源はこれらのワークピースにあります。
- 作業者は防毒マスクを着用できます。また、レーザーマーキングマシンには排気システムを装備することができ、レーザーマーキングプロセス中に発生する煙を効果的に処理できます。AccTek Laserの完全密閉型レーザーマーキングマシンを選択することもできます。これにより、作業環境へのほこりや煙の侵入を防ぎ、作業者の安全を確保できます。マシンはマーキングプロセス中に発生する煙を自動的に排出するため、吸入や汚染のリスクを最小限に抑えることができます。完全密閉型設計は、マーキングプロセス中の事故を防ぐのにも役立ち、多くの業界にとって優れた選択肢となります。
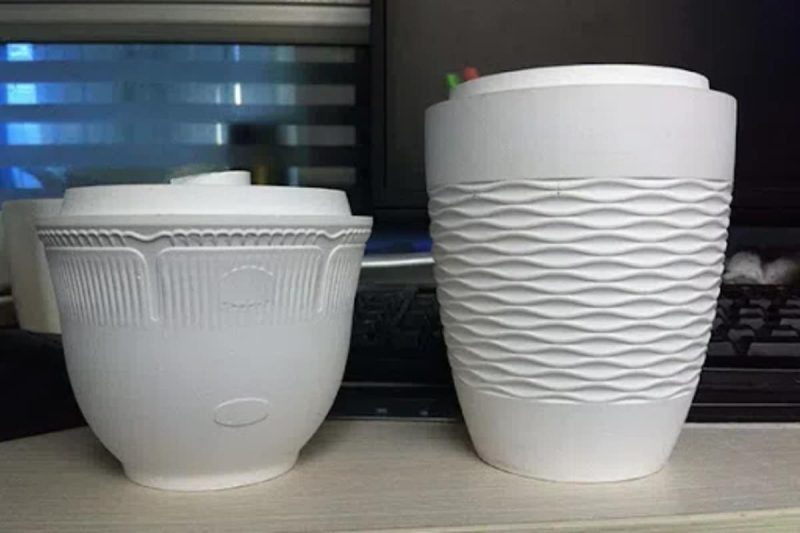
セラミックスへのレーザーマーキングの仕組み
さまざまなセラミックに対するレーザーマーキングの影響
レーザーマーキングがさまざまなセラミックに与える影響は、その材料特性とレーザーパラメータによって異なります。以下は、アルミナセラミック、ジルコニアセラミック、ガラスセラミックなどの一般的なセラミックの詳細な分析です。
- アルミナ: レーザーマーキングは、アルミナセラミックに鮮明で耐久性のあるマークを作成できます。レーザーのエネルギー密度が高いため、セラミックの表面に局所的に照射することができ、表面の材料が蒸発したり変色したりして、はっきりとしたマークが形成されます。
- 酸化ジルコニウム: レーザーマーキング技術は、レーザービームを使用してジルコニアセラミックの表面に鮮明なグラフィックまたはテキストマークを形成します。ジルコニアセラミックは高硬度と高耐摩耗性の特性を備えているため、レーザーマーキングはこれらの材料に高精度のマーキングを実現し、マークの鮮明さと耐久性を確保します。
- ガラスセラミック: レーザーマーキングは、高エネルギー密度のレーザービームを使用して、ガラスセラミック材料の表面酸化反応や蒸発などの物理的および化学的変化を起こし、パターンやテキストをマーキングします。この技術により、ガラスセラミックに鮮明で詳細なマークが作成され、非常に耐久性があり、摩耗や色あせに強いです。
課題と解決策
脆さ
- レーザーパラメータを最適化: レーザー出力、パルス幅、スキャン速度などのパラメータを調整することで、セラミック材料への熱衝撃と機械的ストレスを軽減し、亀裂のリスクを軽減します。
- 低応力レーザーマーキング技術の使用:紫外線レーザーマーキング技術は、その短パルスと高エネルギー密度の特性により、セラミック材料の熱影響部を減らすことができ、それによって亀裂の可能性を減らすことができます。
- 適切なセラミック材料とプロセスを選択する: 可能であれば、脆性が低く、処理性能に優れたセラミック材料を選択し、粒子の微細化や気孔の減少などのセラミックの準備プロセスを最適化して、耐亀裂性を向上させます。
表面仕上げ
- セラミック表面を前処理する: マーキングする前にセラミック表面を洗浄して磨き、表面の欠陥や汚れを除去し、表面仕上げを改善します。
- 高精度レーザーマーキング装置を使用する: 精密ガルバノメータスキャンシステムを使用する装置など、セラミック表面に微細なマーキングを実現し、マークの鮮明度とエッジ精度を向上させることができる高精度のレーザーマーキング装置を選択します。
- レーザービームの品質を制御する: 伝送中にレーザービームが拡散したり変形したりしてマーキング効果に影響が出ないように、レーザービームの品質と安定性が良好であることを確認します。
材料のばらつき
- 原材料の品質管理の強化:セラミック原材料の品質を厳密に管理し、原材料の含有量、粒度分布などのパラメータが標準要件を満たし、材料のばらつきを低減することを保証します。
- レーザーマーキングプロセスデータベースの確立: 多数の実験とデータ分析を通じて、さまざまなセラミック材料のレーザーマーキングプロセスデータベースを確立し、実際の生産に信頼性の高いプロセスパラメータと参照ベースを提供します。
- リアルタイム監視と調整:生産プロセス中のレーザーマーキング効果をリアルタイムで監視し、実際の状況に応じてレーザーパラメータとプロセス条件をタイムリーに調整して、マーキング効果の一貫性と安定性を確保します。
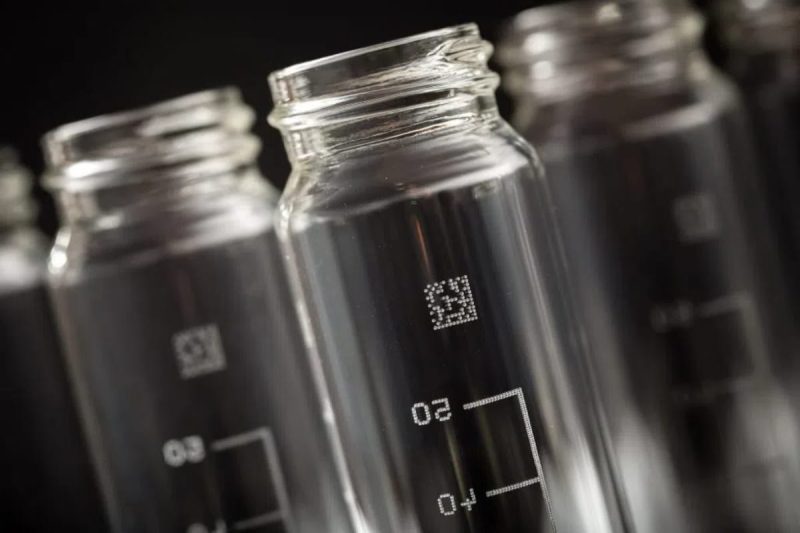
ガラスへのレーザーマーキングの仕組み
レーザーマーキングは、高エネルギー密度のレーザーを使用してガラスの局所的な表面に照射します。マーキングには、彫刻と表面改質の 2 つの主な種類があります。種類によって効果は異なり、必要な効果に応じてレーザーを調整できます。
- 彫刻: レーザー光線をガラスの表面または内部で正確に制御して、目的のパターンまたは形状を形成する彫刻プロセス。
- 表面改質: レーザービームをガラス表面に照射して表面特性を変更する表面改質プロセス。
さまざまなガラスに対するレーザーマーキングの影響
ソーダ石灰ガラス
- 特徴: ソーダ石灰ガラスは最も一般的なガラスで、全ガラス生産量の約 90% を占めています。ソーダ石灰ガラスは SLS ガラスとも呼ばれ、約 70% S (二酸化ケイ素)、15% S (酸化ナトリウム)、9% L (酸化カルシウム) のほか、清澄剤や色の制御に使用される少量の化合物で構成されています。
- レーザーマーキング効果: ガラスのレーザーマーキングは、CO2 レーザーでガラスの表面を加熱することで行うことができます。これにより、一連の表面の微小亀裂が生成され、つや消しの外観を持つ均一なマークが形成されます。他のガラスマーキング方法と比較して、ガラスのレーザーマーキングは、より繊細で複雑なデザイン効果を生み出すことができます。
ホウケイ酸ガラス
- 特徴: ホウケイ酸ガラスは、高温に耐え、強度が高いガラスの一種です。化学的安定性と熱的安定性は、通常のソーダ石灰ガラスよりも優れています。
- レーザーマーキング効果:レーザーはガラス表面に適度な突出高さで、鮮明でひび割れのないマークを形成できます。この加工方法は、ガラスの光学特性と物理的特性を損なわずに維持できます。実験器具、調理器具、光学部品などの製造によく使用されます。
強化ガラス
- 特徴:強化ガラスは加熱と急冷により作られるガラスの一種で、耐熱性と耐衝撃性に優れています。表面に圧縮応力層が形成され、内部に引張応力層が生成されることで、ガラスの強度と安定性が向上します。
- レーザーマーキングの効果:レーザーマーキングは強化ガラスに鮮明で耐久性のあるマークを形成できます。これらのマークは強化ガラスの物理的特性と強度に影響を与えません。同時に、レーザーマーキングの刻印は高度な偽造防止と追跡可能性を備えており、高いセキュリティが求められるアプリケーションシナリオに適しています。
課題と解決策
クラッキング
- レーザーエネルギーの調整:ガラスの厚さと密度に応じて、レーザーエネルギーを適切に設定および調整し、彫刻プロセス中にレーザーが材料を損傷しないようにします。レーザーエネルギーが高すぎてガラスが割れる場合は、レーザーエネルギーを適切に減らすことができます。
- 適切なガラス素材を選択してください: 薄すぎるガラスの使用は避け、レーザーによる損傷に対する耐性を高めるために厚いガラスを選択してください。
- パターン設計を最適化: シンプルなパターンを設計し、過度に複雑で繊細な彫刻を避けて、ガラス素材へのダメージを減らします。
表面反射
- 表面処理: サンドペーパーで研磨したり、化学試薬で腐食させたりしてガラスの表面を粗くし、反射率を下げます。また、黒色塗料や特殊コーティングなどの光吸収材料の層でガラスの表面をコーティングすることも検討できます。
- レーザーパラメータの調整:レーザーマーカーのパワー、速度、周波数などのパラメータを調整することで、反射の問題を改善します。パワーを適切に上げ、マーキング速度を下げ、周波数を上げると、光の反射が減り、マーキングの精度が向上します。
- レンズを清掃する: ほこりやその他の不純物が反射率に影響を与えないように、レーザー マーカーのレンズを定期的に清掃してください。
一貫性
- 高精度の機器を選択する: マーキング プロセスの安定性と精度を確保するために、高精度で安定したレーザー マーキング 機器を選択します。
- 操作プロセスの最適化: 標準化された操作手順を開発し、オペレーターに専門的なトレーニングを提供し、各マーキング操作が標準プロセスに従って実行されるようにします。
- 環境制御:温度、湿度、光などのマーキング環境の安定性を維持し、環境要因がマーキング結果に与える影響を軽減します。
- 機器を定期的に校正する: 機器の精度と安定性を確保するために、レーザー マーキング機器を定期的に校正およびメンテナンスします。
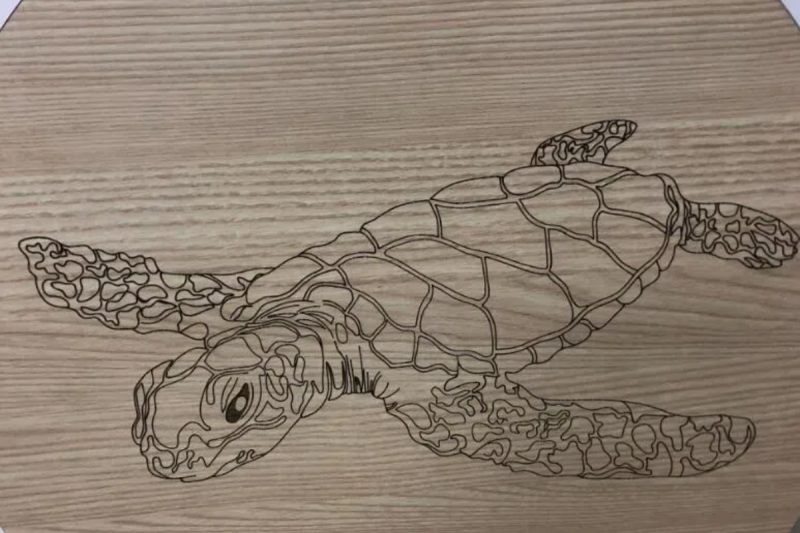
木材へのレーザーマーキングの仕組み
さまざまな種類の木材に対するレーザーマーキングの影響
広葉樹
- 特徴: 広葉樹は硬度と密度が高いです。
- レーザーマーキングの効果:レーザーマーキングは、鮮明で永続的なマークを形成できます。レーザービームは、広葉樹の表面の材料を正確に除去し、細かいグラフィックマークを残します。高精度のレーザーマーキングマシン(UVレーザーなど)は、広葉樹に細かいパターンやテキスト印刷を実現し、製品の美しさと認識性を向上させます。
コルク
- 特徴: コルクは密度が低く、柔らかい質感です。
- レーザーマーキング効果:レーザービームは表面材料をより簡単に除去できます。マーキングプロセスは比較的速く、マーキング品質は良好です。また、松、モミなどのさまざまなコルク材料にも適しています。柔軟な処理方法により、さまざまな形状とサイズのコルク製品のマーキングニーズを満たすことができます。
合板
- 特徴: 変形が小さい、サイズが大きい、施工が簡単、反りがない、横方向の引張機械的特性が良好、など。
- レーザーマーキングの効果:合板へのレーザーマーキングの効果は、無垢材への効果と同様です。レーザービームは合板の表面を貫通し、内部の材料にマーキングすることができます。合板の内部構造を損傷しないように、彫刻の深さが深すぎないように注意してください。レーザーマーキングマシンは、さまざまなタイプと厚さの合板に適しています。その効率的な処理方法は、合板の大量生産のマーキングニーズを満たすことができます。
中密度繊維板(MDF)
- 特徴:中密度繊維板は無垢材に比べて加工性が安定しており、変形や割れなどのトラブルが発生しにくいです。
- レーザーマーキングの効果:レーザーマーキングは中密度繊維板に良い効果をもたらします。レーザービームは表面から材料を正確に除去し、鮮明で長持ちするマークを作成します。レーザーマーキングマシンは、さまざまな種類と厚さの中密度繊維板製品に広く使用されています。その効率的な処理方法は、中密度繊維板の大量生産のマーキングニーズを満たすことができます。
課題と解決策
燃焼と炭化
- オペレーターは、レーザー出力や切断速度などのレーザー設定に細心の注意を払う必要があります。レーザー設定、特に速度と出力の設定が正確性と炭化防止の適切なバランスを保つのに役立ちます。
- 適切な換気は、切断中に発生する煙を拡散させ、火傷の可能性を減らし、より安全な作業環境を確保するのに役立ちます。
- さらに、使用時には材料の選択が重要です。樹脂含有量の少ない木材を選択すると、木材に含まれる揮発性化合物が発火するリスクを軽減できます。
一貫性のないテクスチャ
- 木材を前処理する: レーザーマーキングの前に、木材を研磨して表面を平らで滑らかにし、より一貫したマーキング効果を実現します。
- レーザー パラメータの調整: 木材のテクスチャ特性に応じて、レーザー出力、速度、スキャン パスなどのパラメータを調整し、さまざまな領域のテクスチャの変化に適応します。
- 画像処理技術の使用: レーザーマーキング ソフトウェアに画像処理技術を導入して、木材のテクスチャを識別および分析し、テクスチャの変化に合わせてレーザー パラメータを自動的に調整します。
接着剤
- 適切な接着剤を選択する: 合板などの製品を製造する場合は、レーザーマーキングへの影響が少ない接着剤を選択してください。
- レーザーパラメータの調整: 接着剤を含む木製品の場合、レーザー出力、速度、走査パスなどのパラメータを適切に調整して、接着剤がマーキング効果に与える影響を軽減します。
- 後処理: レーザーマーキング後、研磨、洗浄などのマーキング領域の後処理を行い、気泡やぼやけたエッジを除去してマーキング品質を向上させます。
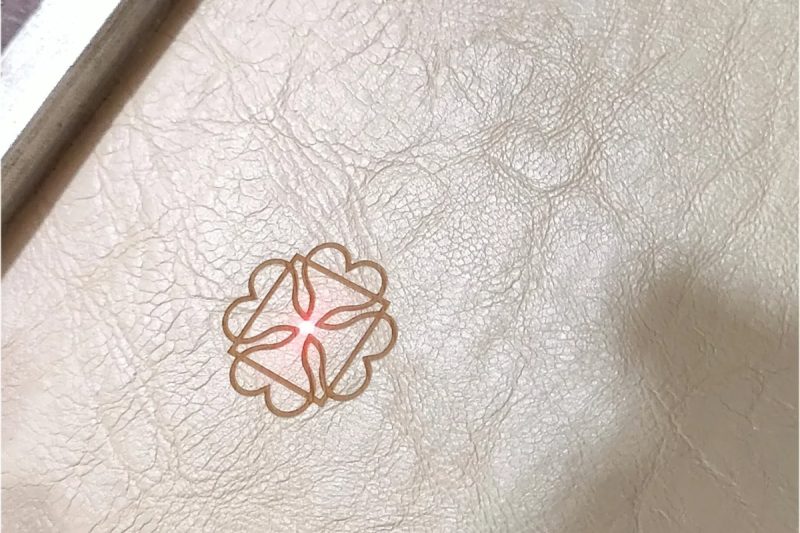
繊維へのレーザーマーキングの仕組み
レーザーの強度と素材の特性に応じて、織物を切断したり、一定の深さの模様を彫刻したり、織物の色を変えるだけで模様を変えたりすることも可能です。
- 色の変化: 一部の繊維は CO2 レーザー ビームにさらされると色や色合いが変わりますが、表面の外観は変化しますが、素材は除去されません。レーザー マーキングを使用すると、繊維の表面に目に見えるパターンやデザインを作成できます。
- 彫刻: 天然繊維と合成繊維はどちらも CO2 レーザー ビームのエネルギーを容易に吸収します。レーザーによって生成される高エネルギー レーザー ビームは、繊維を瞬時に溶かしたり、蒸発させたりします。CO2 レーザー ビームのパワーは、特定の深さまで材料を除去 (彫刻) できるように制限できます。
- 切断: レーザー出力が十分に高ければ、レーザー ビームは繊維を完全に貫通します。レーザーで切断すると、ほとんどの繊維はすぐに蒸発し、熱影響部が小さい滑らかで真っ直ぐなエッジになります。場合によっては、レーザー切断によってエッジが密閉され、繊維がほつれるのを防ぎます。
さまざまな種類の繊維に対するレーザーマーキングの影響
天然繊維
綿、麻、絹、ウールなどの天然繊維には、それぞれ独特の物理的、化学的特性があります。
- 綿繊維:綿繊維はレーザーの吸収力が強く、レーザーマーキング時に表面に鮮明なマークを形成しやすいです。ただし、綿繊維は燃えやすいため、過度の燃焼や炭化を防ぐために、レーザー加工中にエネルギー密度を厳密に制御する必要があります。
- 麻繊維:麻繊維は綿繊維に似ており、レーザー反応に敏感です。レーザーマーキングは麻繊維の表面に明らかなパターンや文字を形成できますが、焼けを防ぐことも必要です。
- シルク繊維(絹など):シルク繊維の表面は滑らかで繊細です。レーザーマーキングは繊維構造を損傷することなく微細なマークを形成できます。ただし、シルク繊維の耐熱性は比較的低いため、レーザーパラメータの選択はより正確に行う必要があります。
- ウール繊維(ウールなど):ウール繊維のレーザーマーキング効果は、その特定の種類と処理方法によって異なります。一部のウール繊維は、レーザーの作用によりわずかに焦げた臭いや煙を発生する場合がありますが、適切なレーザーパラメータ設定により、この効果を軽減できます。
合成繊維
ポリエステル、ナイロン、スパンデックスなどの合成繊維は、優れた物理的特性と化学的安定性を備えています。
- ポリエステル: ポリエステル繊維はレーザーによく反応し、レーザーマーキングにより表面に鮮明で永続的なマークを形成できます。ポリエステルは耐熱性に優れており、燃えたり変形したりしにくいです。
- ナイロン:ナイロン繊維はポリエステルに似ており、レーザー加工性能も優れています。レーザーマーキングはナイロンの表面に細かい模様や文字を形成することができ、マーキング品質は安定しています。
- スパンデックス:スパンデックスは、衣類の伸縮部分によく使用される伸縮性繊維です。スパンデックスに対するレーザーマーキングの影響は比較的小さいですが、繊維の弾性特性を損なわないようにレーザーエネルギーを制御する必要があります。
混合繊維
課題と解決策
燃焼と溶解
- レーザーパラメータを正確に制御: 繊維の材質、厚さ、必要なマーキングの深さに応じて、レーザー出力、波長、パルス幅などのパラメータを正確に調整し、レーザーエネルギーが制御可能な範囲内にあることを確認します。
- 冷却システムを導入する: レーザーマーキングマシンに水冷装置や空冷装置などの冷却システムを装備し、レーザーマーキングプロセス中に発生した熱を適時に放散し、繊維表面の温度を下げます。
- マーキング経路と速度を最適化: レーザービームの移動経路とマーキング速度を最適化することで、繊維表面におけるレーザーの滞留時間が短縮され、焼けや溶解のリスクが軽減されます。
消耗
- 適切なレーザーを選択する: 繊維の材質と特性に応じて、適切なレーザー波長と出力を選択し、繊維表面の摩耗を軽減します。
- マーキングの深さを調整する: レーザー マーキングの深さを制御して、マーキングが深すぎることによる繊維の内部構造の損傷や表面の摩耗を回避します。
- 補助材料の使用: レーザーマーキングの前に、耐熱性および耐摩耗性のコーティングやフィルムなどの補助材料の層を繊維の表面に塗布して、繊維の表面を摩耗から保護することができます。
色の一貫性
- サンプルテスト: マーキングする前に、レーザーマーキングでサンプルをテストし、最適なレーザーパラメータとマーキング効果を決定します。さまざまなパラメータでのマーキング効果を比較することで、生産に最適な色の一貫性を持つソリューションを選択します。
- 色管理: レーザー マーキング マシンで色調整と色合わせを実行する色管理システムを確立し、異なる時間や異なるデバイスでのマーキングの色の一貫性を確保します。
- 適切なレーザー タイプを選択する: 繊維の色特性とマーキング要件に応じて、適切なレーザー タイプ (ファイバー レーザー、CO2 レーザーなど) を選択して、より優れた色の一貫性とマーキング効果を実現します。
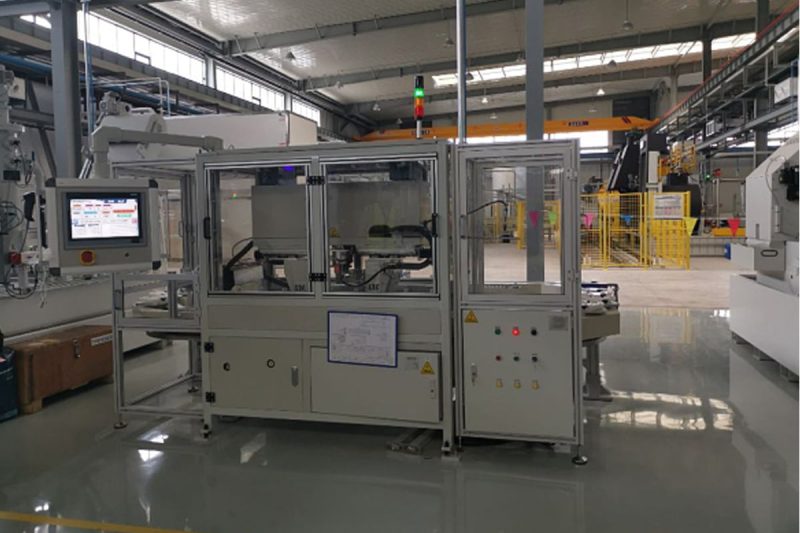
環境と安全に関する考慮事項
材料の安全性
煙と粒子
- 排気システムを使用して、発生した煙や粒子を作業エリアから速やかに排出してください。
- 排気システムが効果的に機能するように、定期的に点検およびメンテナンスを行ってください。
- 作業者は防塵マスクや呼吸器などの個人用保護具を着用する必要があります。
熱効果
- 過剰なエネルギー入力を避けるために、出力、パルス幅などのレーザーパラメータを正確に制御します。
- 材料の表面温度を下げるために、水冷や空冷などの冷却システムを導入します。
- 冷却システムが正常に動作するように定期的に点検およびメンテナンスしてください。
レーザーの安全性
レーザーレベル
- 操作する前に、レーザー機器のレベルと潜在的な危険性を理解する必要があります。
- レーザー機器の安全操作手順を厳守してください。
保護具
- オペレーターは、レーザー保護メガネや保護服などの適切な個人用保護具を着用する必要があります。
- レーザーマーキングマシンは、操作者以外の人による意図しない接触を防ぐために、専用の作業エリアに設置する必要があります。
- レーザーマーキングマシンの安全システムを定期的に点検し、メンテナンスしてください。
環境への影響
エネルギー消費
- エネルギー効率の高いレーザーマーキングマシンモデルを選択してください。
- 設備のアイドル時間を削減するために生産計画を合理的に調整します。
- 機器が最良の動作状態を保つように、定期的に保守およびメンテナンスを実施してください。
廃棄物管理
- 発生した廃棄物を分類して収集し、処理します。
- 有害廃棄物の発生を減らすために、環境に優しい材料をマーキングに使用します。
- 地域の環境保護法および規制を遵守し、有害廃棄物は指定された処理機関に送って処理します。
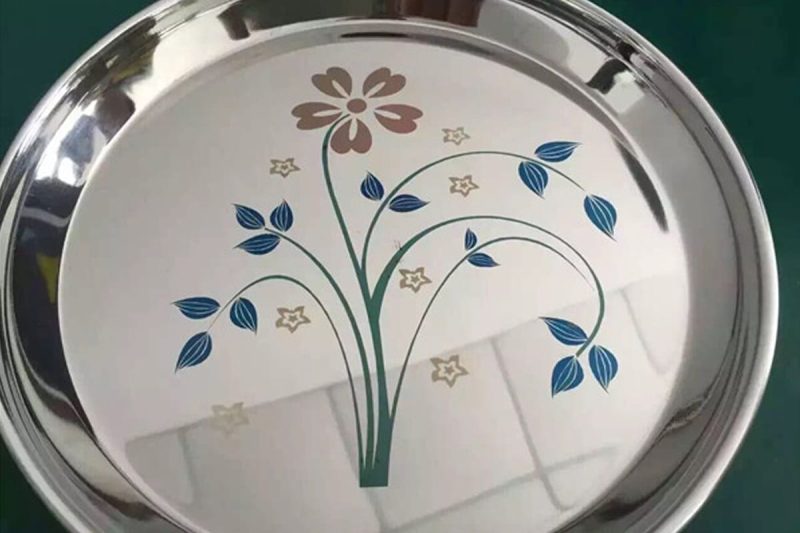
まとめ
レーザー ソリューションを入手する
AccTek Laser は、プロフェッショナル レーザー マーキング テクノロジーの大手サプライヤーであり、さまざまな業界のニーズに合わせた包括的なソリューションを提供しています。当社は安全性と効率性を重視し、各オペレーターが高度なレーザー クリーニング機器の操作を習得できるよう十分なトレーニングを受けています。当社のトレーニング プログラムは、レーザー テクノロジーの理解、機械コンポーネントの習得、厳格な安全プロトコルの順守など、重要な分野をカバーしています。AccTek Laser と提携することで、企業は専門家によるトレーニングとサポートに支えられた最先端のレーザー マーキング テクノロジーを利用できるようになります。これにより、マーキング プロセスの有効性が最大化されるだけでなく、オペレーターの安全性と規制基準への準拠も保証されます。AccTek Laser は、業界の特定のニーズを満たす、信頼性が高く、効率的で安全なレーザー マーキング ソリューションを提供します。
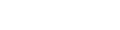
- [email protected]
- [email protected]
- +86-19963414011
- No. 3 ゾーン A、Lunzhen 工業地帯、玉城市、山東省。