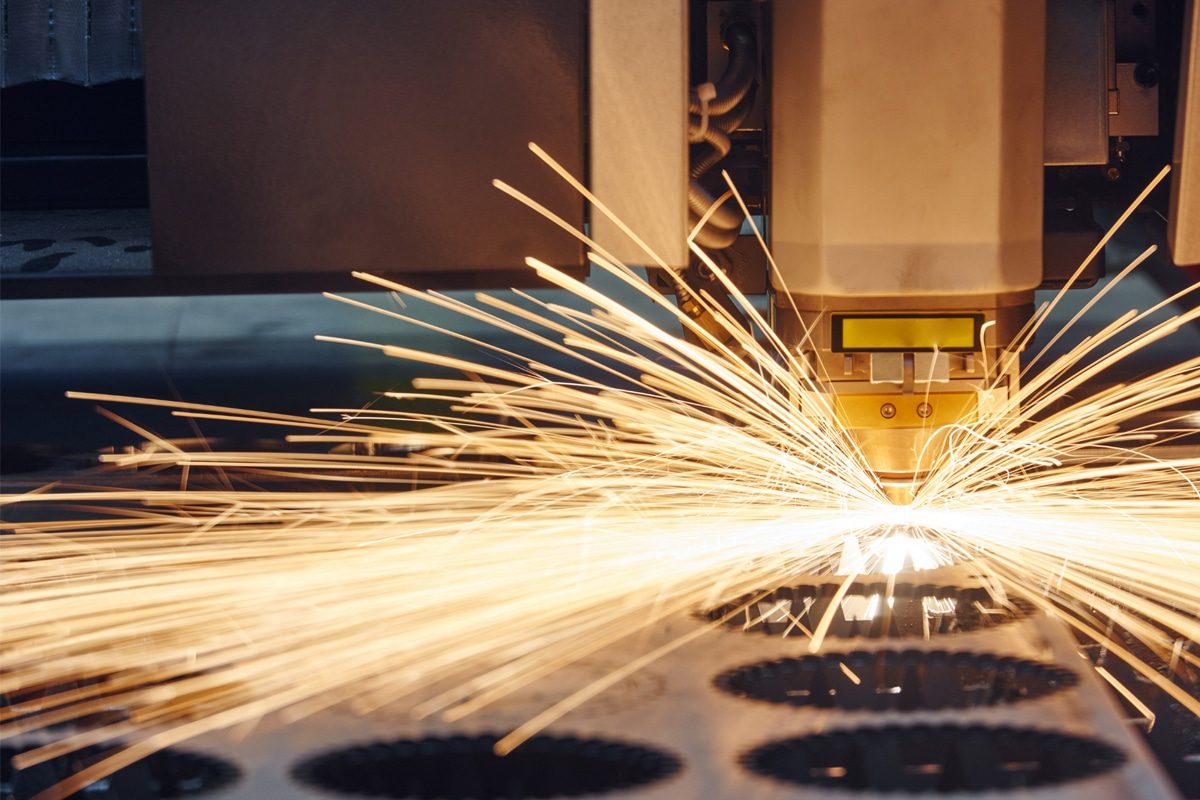
レーザー切断とプラズマ切断: どちらが優れているか
レーザー切断とプラズマ切断は、製造業界で材料を正確に切断するために広く使用されている 2 つの方法です。どちらの技術も独自の利点があり、さまざまな用途に適していますが、切断メカニズム、材料の適合性、コスト効率の点で大きく異なります。レーザー切断では、集束した光線を使用して材料を蒸発または溶解し、高精度で滑らかなエッジを実現するため、複雑なデザインや薄い材料に最適です。一方、プラズマ切断では、電気的にイオン化されたガスを使用して、特に厚い材料の導電性金属を素早く切断します。
レーザー切断とプラズマ切断のどちらを選択するかは、材料の種類、必要な切断速度、精度、全体的な生産コストなどの要因によって異なります。この記事では、これら 2 つの切断方法の主な違いを説明し、特定のニーズにどちらが適しているかを判断するのに役立ちます。速度、精度、コストのどれを優先するかにかかわらず、両方のテクノロジーを理解することで、最適な選択を行うことができます。
目次
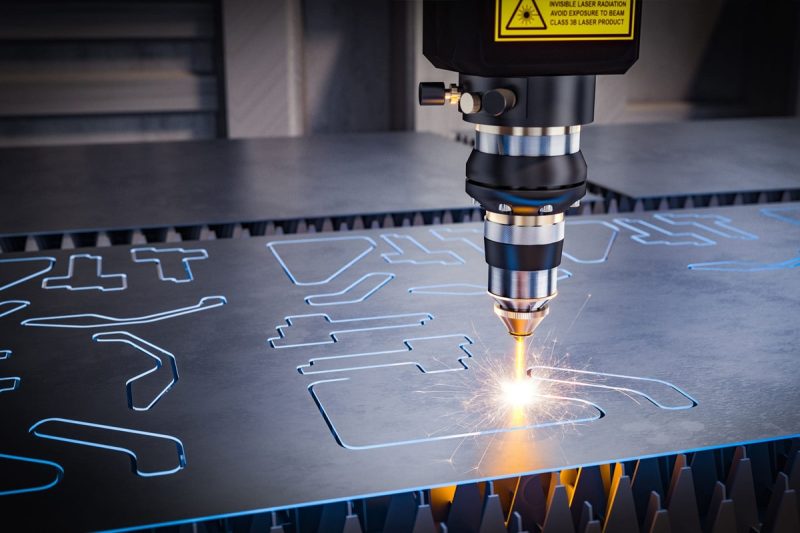
レーザーとプラズマ切断の紹介
レーザー切断とプラズマ切断は、さまざまな材料を精密に切断するために工業製造で使用されている最も一般的な 2 つの方法です。各技術には明確な利点があり、さまざまな用途や業界に適しています。レーザー切断は、その名前が示すように、高度に焦点を絞った光線を使用して材料を溶解または蒸発させ、優れた精度、きれいなエッジ、最小限の材料の無駄を実現します。そのため、複雑な切断、細かいディテール、および電子機器、航空宇宙、自動車業界などの高精度が求められる用途に最適です。
一方、プラズマ切断では、高速のイオン化ガス (プラズマ) の流れを利用して、鋼、アルミニウム、銅などの導電性材料を溶かして切断します。厚い材料を処理できることで知られるプラズマ切断は、大規模な切断作業では一般的に高速であり、建設、造船、金属加工などの高負荷用途で広く使用されています。
どちらの切断方法も現代の製造業では重要な役割を果たしていますが、レーザー切断とプラズマ切断のどちらを選択するかは、材料の種類、厚さ、必要な精度、コストの考慮などの要因によって大きく左右されます。これらの主な違いを理解することで、特定のニーズにどの技術がより適しているかを判断するのに役立ちます。
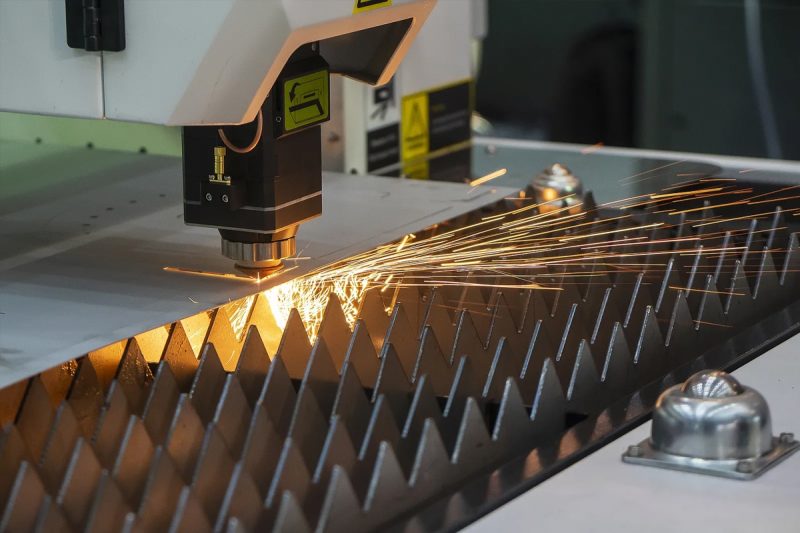
動作原理: レーザー切断とプラズマ切断
レーザー切断とプラズマ切断の基本的な動作原理を理解することは、それらの機能、利点、および限界を理解するために不可欠です。どちらの技術も材料を効率的に切断するように設計されていますが、まったく異なるメカニズムで動作します。
レーザー切断の動作原理
レーザー切断では、高出力の集中光線を利用して、非常に高い精度で材料を切断または彫刻します。「レーザー」という用語は、誘導放出による光増幅を意味します。このプロセスの仕組みは次のとおりです。
- レーザー生成: ファイバー レーザーや CO2 レーザーなどのレーザー ソースは、コヒーレントな単色光ビームを生成します。この光は、レーザー媒体内の原子を励起し、原子が同時に光子を放出することによって生成されます。
- ビームの集束: レーザー ビームは一連のミラーとレンズを通して送られ、材料の表面の非常に小さく正確な点に集束されます。集束機構により、ビームは直径 0.1 mm 程度まで集束され、強度が増します。
- 材料の相互作用: 焦点を絞ったレーザー ビームが材料に当たると、そのエネルギーが吸収され、材料が急速に加熱されます。レーザーの出力と材料の特性に応じて、次のような結果が生じる可能性があります。
- 溶融: 高温により材料が溶けます。
- 気化: 温度が沸点を超えると物質は気化します。
- 燃焼: 場合によっては、特に非金属の場合、材料が燃焼することがあります。
- 補助ガス: 酸素、窒素、圧縮空気などの補助ガスが、ノズルを通してレーザービームと同軸に吹き付けられます。このガスには複数の目的があります。
- 溶融材料の排出:溶融または気化した材料を切断溝から吹き飛ばします。
- 切断速度の向上: 酸素は材料と発熱反応を起こし、切断速度を向上します。
- レンズの保護: 煙や粒子がフォーカスレンズを汚染するのを防ぎます。
- 制御された動作: CNC (コンピュータ数値制御) システムは、プログラムされた設計に従ってレーザー切断ヘッドを材料の上に誘導し、正確な切断と複雑な形状を保証します。
レーザー切断の主な特徴:
- 精度: ±0.1 mm の厳密な許容差で切断できます。
- エッジ品質: 多くの場合、それ以上の仕上げを必要としない、滑らかできれいなエッジを生成します。
- 汎用性: 金属、プラスチック、木材、ガラスなど、さまざまな材料の切断に適しています (レーザーの種類によって異なります)。
- 最小限の熱影響部: 集中ビームにより周囲の材料の熱による歪みが最小限に抑えられます。
プラズマ切断の動作原理
プラズマ切断は、高温のプラズマのジェットを使用して導電性材料を切断するプロセスです。ここでは、プラズマ切断の仕組みを段階的に説明します。
- 電源とガス: プラズマ カッターは、電源を使用して直流 (DC) アークとプラズマを形成するガス (通常は圧縮空気、窒素、または酸素) を生成します。
- アークの開始: プラズマ カッターは、電極 (トーチ内) とワークピースの間でアークを開始します。これは、次の方法で開始できます。
- 接触開始: トーチの先端をワークピースに接触させて回路を完成させます。
- 高周波始動: 高電圧、高周波回路を使用して、非接触でガスをイオン化します。
- プラズマの形成: ガスはトーチ内の狭いノズルから高速で押し出されます。ガスが電気アークを通過するとイオン化され、高温で電気を伝導するガスであるプラズマに変化します。
- 材料の溶解と除去:
- 溶解: プラズマの温度は最高 30,000℃ (54,000℉) に達し、接触点の金属を瞬時に溶かします。
- 溶融金属の吹き飛ばし: 高速プラズマ流が切断部から溶融金属を吹き飛ばし、切り口を作ります。
- 切断トーチの動き: レーザー切断と同様に、CNC システムはプラズマ トーチの動きを制御して、目的の切断パスに正確に従います。
プラズマ切断の主な特徴:
- 切断速度: レーザー切断に比べて厚い材料の切断速度が速くなります。
- 材料の厚さ: 最大数インチの厚さの金属板を切断するのに効果的です。
- 導電性材料のみ: 鋼、ステンレス鋼、アルミニウム、真鍮、銅など、電気を伝導する材料のみを切断できます。
- より広い切断幅と熱影響部: 切断幅が広くなり、熱の影響を受ける領域が大きくなるため、材料の無駄が増え、反りが発生する可能性があります。
これらの動作原理を理解することは、材料の種類、厚さ、必要な精度、および特定のアプリケーションのニーズに基づいて適切な切断技術を選択するのに役立ちます。
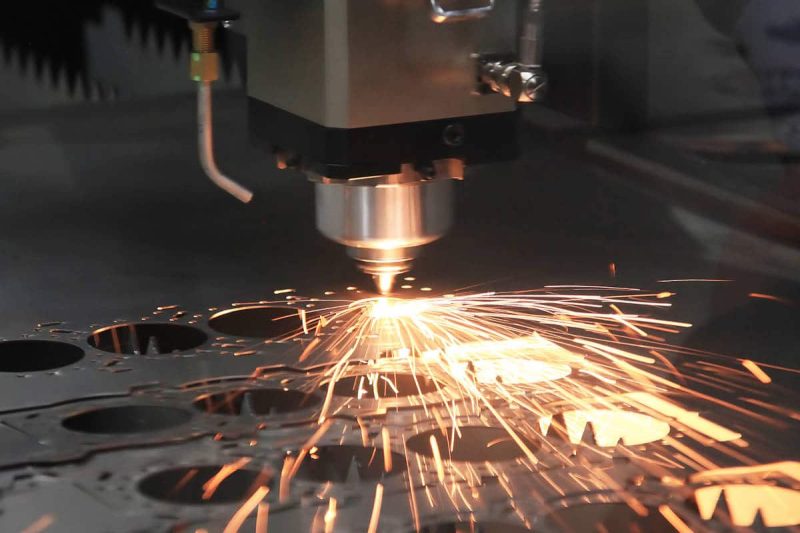
レーザー切断とプラズマ切断の主な違い
レーザー切断とプラズマ切断のどちらを選択するかを決める際、特定の作業にどちらの方法が適しているかはいくつかの重要な要素によって左右されます。以下では、切断メカニズム、材料の適合性、切断速度、切断厚さ、精度、正確さ、熱影響部 (HAZ)、およびエッジ品質に基づいて、これら 2 つの切断技術の主な違いについて説明します。
切断機構
- レーザー切断: レーザー切断は、高出力のレーザー光線を材料の表面に集束させて、材料を溶かしたり、燃やしたり、蒸発させたりすることで機能します。アシストガス (窒素、酸素、圧縮空気など) の流れが、溶融した材料を排出し、きれいな切断面を作ります。レーザー光線は、切断する材料に応じて、ファイバーまたは CO2 レーザー源から生成されます。レーザー切断は比類のない精度を提供し、CNC (コンピュータ数値制御) システムによって制御されるため、複雑で入り組んだデザインを作成できます。
- プラズマ切断: 対照的に、プラズマ切断は、酸素や窒素などのガスを電気的にイオン化することによって生成される高温プラズマのジェットを利用して、鋼鉄やアルミニウムなどの導電性材料を溶かします。プラズマアークは、電気アークを適用しながらガスをノズルに通すことによって生成され、材料を溶かすのに十分な高温の流れを作り出します。プラズマ切断は厚い金属に効果的ですが、レーザー切断と同じレベルの精度は提供しません。
材質の適合性
- レーザー切断: レーザー切断は、材料の適合性に関して非常に汎用性があります。金属材料と非金属材料の両方を切断できます。ファイバーレーザーは主に、鋼鉄、ステンレス鋼、アルミニウム、真鍮、銅などの金属の切断に使用されます。 CO2レーザー切断機一方、ファイバーレーザーは、木材、プラスチック、布地、ガラスなどの非金属の切断に適しています。ただし、ファイバーレーザーは金属の切断に最も効率的であり、レーザー出力と設定を調整しないと、アルミニウムなどの反射率の高い材料を切断することはできません。
- プラズマ切断: プラズマ切断は導電性材料に限られます。これには、炭素鋼、ステンレス鋼、アルミニウム、真鍮、銅、その他の合金などの金属が含まれます。プラスチック、木材、ガラスなどの非導電性材料を切断することはできないため、金属加工業界への適用が制限されます。厚い金属を切断する場合、プラズマ切断はより高速で効率的なオプションを提供します。
切削速度
- レーザー切断: レーザー切断は一般的に、薄い材料を高速かつ正確に切断するのに優れています。厚さが 6 mm 未満の金属の場合、特に高精度の切断が必要な場合、レーザー切断はプラズマ切断よりも大幅に高速です。ただし、材料の厚さが増すにつれて、レーザー切断の切断速度は低下します。レーザー切断は、速度よりも精度が重要な細かい作業に最適です。
- プラズマ切断: 対照的に、厚い材料、特に厚さ 10 mm を超える金属の場合、プラズマ切断はレーザー切断よりも高速です。プラズマ カッターはこれらの厚い材料を高速で切断できるため、造船や建設などの重工業用途に最適です。厚い金属の場合、プラズマ切断はレーザー切断よりも時間効率が高くなります。
切断厚さ
- レーザー切断: レーザー切断は薄い材料に非常に効果的です。高出力ファイバーレーザーを使用する場合、金属の場合、通常厚さ 30 mm まで切断できます。この厚さを超えると、レーザー切断の効率と速度が低下し、電力制限と熱による材料の変形の可能性により、切断が実用的でなくなる可能性があります。
- プラズマ切断: プラズマ切断は、プラズマ カッターのパワーに応じて最大 50 mm 以上の厚い材料を切断する場合に優れています。このため、重工業など、厚い金属を切断する必要がある用途では、プラズマ切断の方が適しています。30 mm を超える材料の場合、プラズマ切断は一般にレーザー切断よりも高速でコスト効率に優れています。
精度と精度
- レーザー切断: レーザー切断の主な利点の 1 つは、その精度です。狭いレーザー ビームと CNC 制御を組み合わせることで、±0.1 mm 以内の厳しい許容誤差で高精度の切断が可能になります。このため、レーザー切断は、複雑な設計、詳細なコンポーネント、航空宇宙、エレクトロニクス、自動車産業など、高精度が不可欠な用途に最適です。切断幅が狭いため、材料の無駄がさらに減ります。
- プラズマ切断: プラズマ切断は厚い材料に効果的ですが、レーザー切断ほど正確ではありません。プラズマ カッターは切り口が広くなるため、細かく複雑な切断が困難になります。多くの産業用途に適していますが、特に細かい作業や薄い材料の場合は、切断品質を向上させてバリを取り除くために、研磨やサンディングなどの後処理が必要になる場合があります。
熱影響区域 (HAZ)
- レーザー切断: レーザー切断では、プラズマ切断に比べて熱影響部 (HAZ) が小さくなります。高集束レーザー ビームは、周囲の領域に大きな影響を与えることなく、材料の小さな部分を溶かします。HAZ が最小限に抑えられるため、熱による歪みが少なくなり、材料が反ったり変形したりするリスクが軽減されます。これは、薄いワークピースや繊細なワークピースの場合に特に重要です。
- プラズマ切断: プラズマ切断では、プラズマアークの高温により、はるかに大きな熱影響部が生成されます。この大きな HAZ により、特に薄い材料を切断する場合に、材料の反りや歪みが生じる可能性が高くなります。厚い金属の場合、HAZ はそれほど問題にならないかもしれませんが、精密な用途や熱による損傷を受けやすい材料の場合は、レーザー切断の方が適しています。
エッジ品質
- レーザー切断: レーザー切断は、滑らかできれいな切断面を実現し、多くの場合それ以上の仕上げを必要としない優れたエッジ品質を実現します。狭い切断面と最小限の熱影響により、バリのない正確なエッジが得られます。これは、美観や高品質の仕上げが求められる用途に特に有利です。
- プラズマ切断: プラズマ切断は高速ですが、レーザー切断に比べてエッジが粗くなることがよくあります。切断幅が広く HAZ が大きいと、エッジにドロスやスラグ (残留物) が形成される可能性があり、滑らかな仕上がりにするには追加の後処理が必要になります。エッジの品質が重要でない用途では、プラズマ切断は依然として適切なオプションです。
結論: 主な違い
- 切断メカニズム: レーザー切断では集中した光線を使用し、プラズマ切断ではイオン化されたガス (プラズマ) の流れを利用します。
- 材料の適合性: レーザー切断は金属と非金属の両方を扱うことができますが、プラズマ切断は電気伝導性金属に限定されます。
- 切断速度: レーザー切断は薄い材料を切断する方が速いのに対し、プラズマ切断は厚い金属を素早く切断するのに優れています。
- 切断厚さ: レーザー切断は薄い材料に対してより効率的ですが、プラズマ切断は厚い金属に対してより効果的に処理します。
- 精度と正確性: レーザー切断は、よりきれいな切断でより高い精度と正確性を提供しますが、プラズマ切断は精度が低く、後処理が必要になる場合があります。
- 熱影響部 (HAZ): レーザー切断では HAZ が小さくなり、熱による歪みが減少しますが、プラズマ切断では HAZ が大きくなり、反りが発生するリスクが高まります。
- エッジ品質: レーザー切断では滑らかで高品質のエッジが得られますが、プラズマ切断では追加の仕上げが必要となる粗いエッジが生成される場合があります。
これらの重要な違いを理解することで、製造業者やエンジニアは、精度、速度、コスト効率など、特定のアプリケーションのニーズに基づいて適切な切断方法を選択できるようになります。
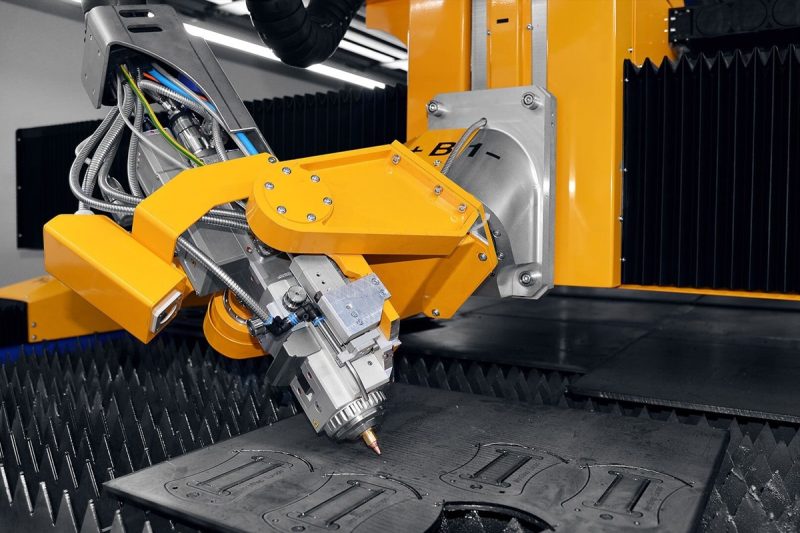
アプリケーション: レーザー切断とプラズマ切断
レーザー切断とプラズマ切断はどちらもさまざまな業界で広く使用されていますが、それぞれの方法には、材料の種類、厚さ、精度、および生産要件に基づいた特定の用途があります。以下では、各技術の理想的な用途について説明し、レーザー切断とプラズマ切断をいつ使用するかを判断するのに役立ちます。
レーザー切断アプリケーション
レーザー切断は、高精度、細かいディテール、きれいなカットで知られており、精度と品質が最も重要視される業界や用途に最適です。レーザー切断は、以下の業界で広く使用されています。
- 航空宇宙: 航空宇宙製造では、部品は極めて高い精度基準を満たす必要があります。レーザー切断は、チタンやアルミニウムなどの軽量金属で作られた複雑な部品を切断したり、許容誤差が最小限の小さくて細かい部品を作成したりするのに好まれる方法です。
- 自動車: レーザー切断は、自動車業界で、板金部品、ダッシュボード パネル、エンジン部品などの複雑な部品の切断に広く使用されています。その精度により、現代の自動車の高性能要件を満たすカスタマイズされた詳細な部品を作成できます。
- エレクトロニクス: エレクトロニクス業界では、プリント基板 (PCB) などの小型部品の繊細で複雑な切断が求められることがよくあります。レーザー切断は薄い材料を扱い、熱による損傷を最小限に抑えながら高精度の切断を実現できるため、このような用途に最適です。
- 医療機器: レーザー切断は、手術器具、インプラント、その他精密な細部加工が求められる精密部品などの医療機器の製造に使用されます。その高い精度により、医療機器は厳しい規制基準を満たすことができます。
- ジュエリーおよびファッション: レーザー切断は、ジュエリーおよびファッション業界での切断や彫刻によく使用されます。高級ジュエリー用の貴金属の切断でも、布地や皮革の複雑な模様の切断でも、レーザー技術は製品の美観を高めるきれいで正確な切断を実現します。
- 繊維および布地の切断: CO2 レーザーは、繊維業界で布地、皮革、合成素材の切断によく使用されます。レーザー切断は、高速で正確な非接触切断を可能にするため、損傷しやすい繊細な素材には不可欠です。
- 標識およびディスプレイの製造: レーザー切断は、アクリル、プラスチック、木材などの素材に詳細なロゴ、複雑なデザイン、文字を作成するために、標識業界でも人気があります。きれいなエッジと正確なカットは、視覚的に魅力的なディスプレイに最適です。
プラズマ切断アプリケーション
プラズマ切断は、そのスピードと、厚くて導電性のある材料を効率的に切断する能力で知られています。通常、精度はそれほど重要ではないが、高速で大規模な切断が求められる重工業で使用されます。プラズマ切断は、次の用途でよく使用されます。
- 建設: プラズマ切断は、厚い鋼板、構造梁、金属補強材の切断に建設業界で広く使用されています。厚い材料を素早く切断できるため、橋梁、建物、その他のインフラストラクチャなどの大規模プロジェクトに最適です。
- 造船: 造船業界では、船の建造に使用される厚い鋼板を切断するためにプラズマ切断が不可欠です。プラズマ切断はスピードとコスト効率に優れているため、船体やフレームなどの大型金属部品を製造するための頼りになる方法です。
- 金属加工: プラズマ切断は、金属加工工場で厚い金属板、パイプ、フレームを切断するのによく使用されます。加工業者は、特にステンレス鋼やアルミニウムなどの高強度材料を扱う作業において、プラズマ切断のスピードとパワーを高く評価しています。
- 自動車の修理とカスタマイズ: レーザー切断は自動車部品の製造によく使用されますが、厚い金属を素早く切断する必要がある自動車修理工場にはプラズマ切断が最適です。プラズマ カッターは、車両フレーム、排気システム、カスタム金属加工の修理によく使用されます。
- 重機製造: 鉱業、農業、産業機器などの重機を製造する業界では、これらの機械を構成する厚い鋼鉄や金属部品の取り扱いにプラズマ切断を利用することがよくあります。プラズマ切断は厚い材料を切断できるため、耐久性の高い部品の製造に非常に効果的です。
- パイプライン建設: 石油・ガス業界では、厚い金属パイプの切断と成形にプラズマ切断が使用されています。厚い材料を高速で切断する能力は、輸送システム用の大型パイプや金属部品の取り扱いに精度が求められる業界にとって不可欠です。
結論: アプリケーション
- レーザー切断は、精度、細かいディテール、高品質の仕上げを必要とする用途に最適です。精度ときれいなエッジが重要となる航空宇宙、自動車、電子機器、医療機器製造などの業界で優れています。
- プラズマ切断は、厚い材料を迅速かつ効率的に切断する必要がある高負荷用途に最適です。建設、造船、金属加工などの業界では、特に精度がそれほど重要でない場合に、プラズマ切断の速度とコスト効率のメリットを享受できます。
レーザー切断とプラズマ切断のどちらを選択するかは、最終的には、材料の種類、厚さ、精度、生産速度など、プロジェクトの特定の要件によって決まります。各技術の長所を理解することで、メーカーはアプリケーションのニーズに最適な切断方法を選択できます。
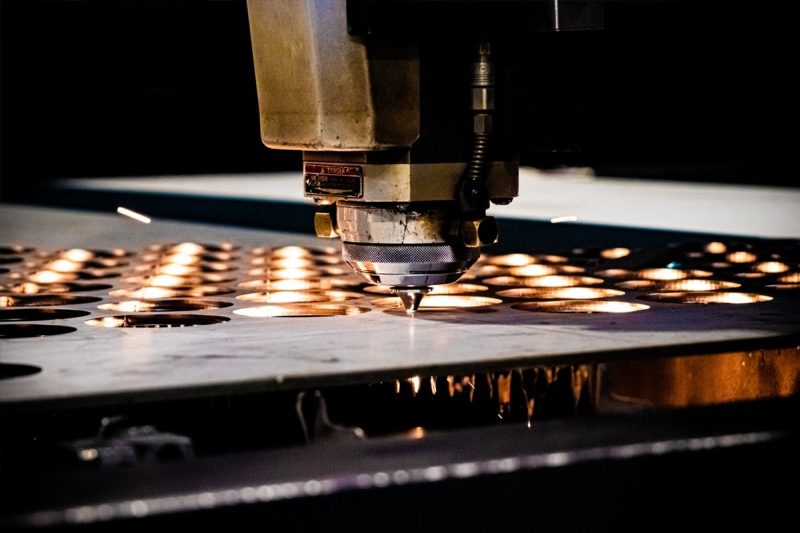
コスト比較: レーザー切断 VS プラズマ切断
産業ニーズに合わせてレーザー切断とプラズマ切断のどちらを選択するかを決める場合、コストは考慮すべき重要な要素です。総所有コストには、初期投資だけでなく、継続的な運用コスト、メンテナンス、エネルギー消費も含まれます。以下では、両方の切断技術に関連するコストを比較し、特定の用途でどちらの方法の方がコスト効率が高いかを判断するのに役立ちます。
初期投資
- レーザー切断: レーザー切断機の初期投資は、プラズマ切断機に比べて一般的に高くなります。レーザー切断機、特にファイバーレーザーは、その精度と高度な技術で知られていますが、価格も高くなります。 ファイバーレーザー切断機 価格は、電力、機能、カスタム構成に応じて、$15,000 から $500,000 を超える範囲になります。たとえば、金属加工に使用される高出力の産業用レーザー切断システムは、薄い材料や小規模生産向けに設計された基本的な機械よりも大幅に高価になる可能性があります。
- プラズマ切断: 対照的に、プラズマ切断機は初期費用が低く抑えられます。標準的なプラズマ カッターの価格は、機械のパワーと処理できる材料のサイズによって異なりますが、通常 $15,000 ~ $100,000 です。ハイエンドのプラズマ カッターでも、一般的にレーザー カッターよりも手頃な価格です。この低価格により、厚い金属を切断する必要があるものの、レーザー切断ほどの高精度は必要としない中小企業にとって、プラズマ切断はより利用しやすくなります。
運用コスト
- レーザー切断:初期費用は レーザー切断機 コストが高いほど、運用コストは長期的には低くなります。レーザー切断は、特に効率的なファイバーレーザーを使用する場合、動作中に消費する電力が少なくなります。補助ガス(窒素、酸素、圧縮空気など)などの消耗品は比較的安価で、機械の全体的な効率に貢献します。さらに、レーザー切断では正確できれいな切断ができるため、後処理が不要になることが多く、仕上げ作業に関連する人件費が削減されます。
- プラズマ切断: プラズマ切断機はレーザー切断機に比べて運用コストが高くなります。これは主に、プラズマアークを生成して維持するために必要なエネルギー消費量が大きいためです。プラズマ切断では電極やノズルなどの消耗品が早く消耗するため、より頻繁に交換する必要があります。切断にガス (酸素、窒素、アルゴンなど) を使用すると、継続的な運用コストも増加します。さらに、プラズマ切断された材料は、粗いエッジを滑らかにするために、研削や研磨などの二次仕上げが必要になることが多く、人件費が増加します。
メンテナンス費用
- レーザー切断: レーザー切断機は、レーザー光源やその他のコンポーネントの寿命を確保するために定期的なメンテナンスが必要です。ただし、ファイバー レーザーは、古い CO2 レーザーに比べて寿命が長く、メンテナンスの必要性が低いことで知られています。最も一般的なメンテナンス作業は、光学系のクリーニングと、摩耗したレンズやミラーの交換ですが、これらの作業は一般的に低コストで、頻繁に行う必要もありません。適切にメンテナンスすれば、ファイバー レーザーは、稼働寿命全体にわたってダウンタイムを最小限に抑え、メンテナンス費用を比較的低く抑えることができます。
- プラズマ切断: プラズマカッターは設計がシンプルですが、時間の経過とともにメンテナンスコストが高くなる傾向があります。電極、ノズル、シールドなどの消耗部品は、プラズマアークによる摩耗のため、定期的に交換する必要があります。さらに、厚い材料を高出力で切断する場合、これらの部品はより早く摩耗する可能性があります。交換頻度により、長期的なメンテナンスコストが増加します。部品あたりのコストは低いかもしれませんが、頻繁に交換する必要があるため、時間の経過とともにコストが上昇する可能性があります。
エネルギー消費
- レーザー切断: レーザー切断の最大の利点の 1 つは、エネルギー効率です。特にファイバー レーザー切断機は、薄い材料を切断する場合、プラズマ カッターよりも大幅に少ない電力を消費します。高度に焦点を絞ったレーザー ビームにより、過剰な電力を必要とせずに効率的な切断が可能になります。エネルギー フットプリントと運用コストを削減したい企業にとって、特に長期使用の場合、レーザー切断は多くの場合、より良い選択肢となります。
- プラズマ切断: プラズマ切断機は厚い材料を切断するのに効率的ですが、より多くのエネルギーを消費する傾向があります。ガスをイオン化してプラズマアークを生成するプロセスには、特に厚い材料を高アンペアで切断する場合、かなりの電力が必要です。プラズマ切断機のエネルギー消費量はファイバーレーザーカッターの 2 ~ 3 倍になる可能性があり、長期的には運用コストが高くなります。
結論: コスト比較
- 初期投資: レーザー切断機は初期費用が高くなりますが、精度と機能が優れています。プラズマ切断機は初期費用が手頃なので、極度の精度を必要とせず厚い材料を扱う企業に最適です。
- 運用コスト: レーザー切断は、消耗品が少なく、エネルギーの使用効率が高く、後処理の必要性が最小限であるため、運用コストが低くなります。プラズマ切断は購入コストは安いですが、消耗品の交換が頻繁に必要で、エネルギー消費量が多いため、運用コストが高くなります。
- メンテナンス コスト: レーザー切断は一般的にメンテナンスが少なくて済みます。特に耐久性の高いファイバー レーザーの場合はその傾向が顕著です。プラズマ切断はシンプルですが、部品の交換が頻繁に必要になるため、長期的なメンテナンス コストが高くなります。
- エネルギー消費: レーザー切断、特にファイバーレーザーによる切断は、動作に多くの電力を必要とするプラズマ切断よりもはるかにエネルギー効率に優れています。
精度、効率、長期的なコスト削減を優先する場合は、初期コストが高くてもレーザー切断の方が適しています。厚い材料が使用され、細かいディテールを必要としないプロジェクトの場合、特に重工業用途に重点を置く企業にとって、プラズマ切断はより手頃で迅速なソリューションを提供します。
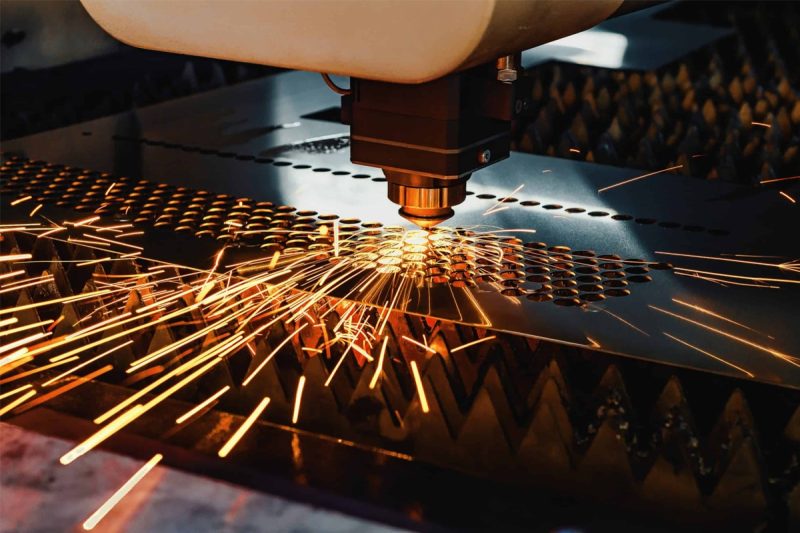
環境への影響: レーザー切断とプラズマ切断
最先端技術を評価する際、持続可能性に重点を置く企業にとって、環境への影響を考慮することがますます重要になっています。レーザー切断とプラズマ切断はどちらも、エネルギー消費、排出、廃棄物の発生、全体的な資源の使用に関連する環境への影響がそれぞれ異なります。これらの要因を理解することで、メーカーはより環境に優しいオプションを選択できます。
エネルギー効率
- レーザー切断: レーザー切断、特にファイバーレーザーは、エネルギー効率が高いことで知られています。ファイバーレーザーは、無駄を最小限に抑えながら電気エネルギーを光に変換し、必要な切断力を生成するために使用する電力が少なくなります。エネルギー消費が減るため、レーザー切断は、特に薄手から中程度の厚さの材料を切断する場合に、より環境に優しいものになります。さらに、レーザー切断の正確で制御された性質により、材料の無駄が減り、より持続可能な生産プロセスに貢献します。
- プラズマ切断: プラズマ切断は厚い材料の切断には効果的ですが、一般的にレーザー切断に比べてエネルギー効率は低くなります。プラズマアークを生成して維持するプロセスでは、特に厚い金属板を切断する場合、大量の電力を消費します。この高いエネルギー需要により二酸化炭素排出量が大きくなり、エネルギー消費の点ではプラズマ切断は環境に優しい選択肢とは言えません。
排出ガスと大気質
- レーザー切断: レーザー切断では、通常、作業中に発生する有害な排出物が少なくなります。切断プロセスでは窒素や酸素などのガスが使用されますが、重大な汚染物質は排出されません。特にファイバー レーザーは、空気の質に関して環境への影響が最小限です。ただし、プラスチックや複合材などの特定の材料を切断する場合、レーザー切断によって煙が放出される可能性があり、作業員を保護し、大気汚染を軽減するために適切な換気システムまたは濾過システムが必要になります。
- プラズマ切断: プラズマ切断では、切断プロセス中に酸素、窒素、アルゴンなどのガスがイオン化されるため、より多くの汚染物質が排出されます。プラズマ切断によって発生する熱は、特にコーティングまたは処理された金属を切断する場合に、有害な煙の放出を引き起こす可能性があります。これらの煙には、窒素酸化物 (NOx) などの有害な粒子やガスが含まれている可能性があり、大気汚染の原因となり、作業者の健康を害する可能性があります。したがって、プラズマ切断では、空気の質への影響を軽減するために、通常、より堅牢な換気および濾過システムが必要です。
材料廃棄物
- レーザー切断: レーザー切断の主な環境的利点の 1 つは、材料の無駄を最小限に抑えられることです。レーザー切断の精度により、許容誤差が小さくなり、切断幅が小さくなるため、切断プロセスで失われる材料が少なくなります。これにより、スクラップの量が減るだけでなく、材料の使用効率も向上し、特に高価な材料の場合、レーザー切断はより持続可能な選択肢になります。
- プラズマ切断: プラズマ切断では、切断幅が広く、切断後の端が粗いため、材料の無駄が多くなる傾向があります。熱影響部 (HAZ) が大きいと、変形や反りが発生し、材料の無駄が増えることもあります。さらに、プラズマ切断された部品は、バリや粗い端を取り除く後処理が必要になることが多く、材料の損失がさらに増えます。これにより、プラズマ切断の効率が低下し、原材料の使用という点で無駄が増える可能性があります。
消耗品とリソースの使用
- レーザー切断: レーザー切断、特にファイバー レーザーでは、消耗品の要件が比較的低くなります。ファイバー レーザーでは、電極やノズルなどのコンポーネントを頻繁に交換する必要がないため、長期的に見て環境的に持続可能になります。レーザー切断で使用される補助ガス (窒素または酸素) も広く入手可能であり、プラズマ切断で使用されるガスに比べて環境への影響が低くなります。
- プラズマ切断: プラズマ切断は、電極、ノズル、シールドなどの消耗品に大きく依存しており、これらは摩耗により定期的に交換する必要があります。消耗部品が頻繁に必要になることで、運用コストが増加するだけでなく、資源の消費と廃棄物の発生も増加します。摩耗した部品の廃棄は、特に適切にリサイクルされない場合、プラズマ切断の環境フットプリントに影響を及ぼします。
騒音公害
- レーザー切断: レーザー切断は、他の工業用切断方法に比べて比較的静かに動作します。切断プロセスでは発生する騒音が最小限に抑えられるため、より安全で快適な作業環境が実現します。騒音公害の軽減は、特に騒音規制が厳しい都市部や住宅地では、環境上の利点でもあります。
- プラズマ切断: プラズマ切断は、特に厚い材料を高出力で切断する場合、より多くの騒音を発生します。プラズマアークと溶融金属の噴出によって発生する騒音は、作業場の騒音公害の一因となる可能性があり、作業者は聴覚保護具を着用する必要があります。過度の騒音レベルは周囲の環境を乱す可能性があり、騒音に敏感なエリアでのプラズマ切断は望ましくありません。
結論: 環境への影響
- エネルギー効率: レーザー切断、特にファイバーレーザーによる切断はプラズマ切断よりもエネルギー効率が高く、より環境に優しい選択肢となります。
- 排出物: プラズマ切断では、特にコーティングまたは処理された金属を切断する場合、より多くの有害な煙や粒子が排出されます。レーザー切断では排出物は少なくなりますが、特定の材料では適切な換気が必要になる場合があります。
- 材料の無駄: レーザー切断は精度が高いため無駄が少なくなりますが、プラズマ切断ではスクラップが多くなり、追加の後処理が必要になる場合があります。
- 消耗品: プラズマ切断ではより多くの消耗品が必要になるため、資源の使用量と廃棄物が増加しますが、レーザー切断では消耗品の使用量が少なくなります。
- 騒音公害: レーザー切断は、騒音の大きいプラズマ切断プロセスに比べて静かで、騒音公害も少なくなります。
レーザー切断は、エネルギー効率、排出量の低さ、材料の無駄の少なさ、消耗品の必要性の少なさから、一般的に環境に優しい選択肢です。プラズマ切断は厚い材料には効果的ですが、エネルギー消費量、排出量、材料の無駄が多いため、環境への影響が大きくなります。持続可能性を重視する企業にとって、レーザー切断はより環境に優しいソリューションを提供します。
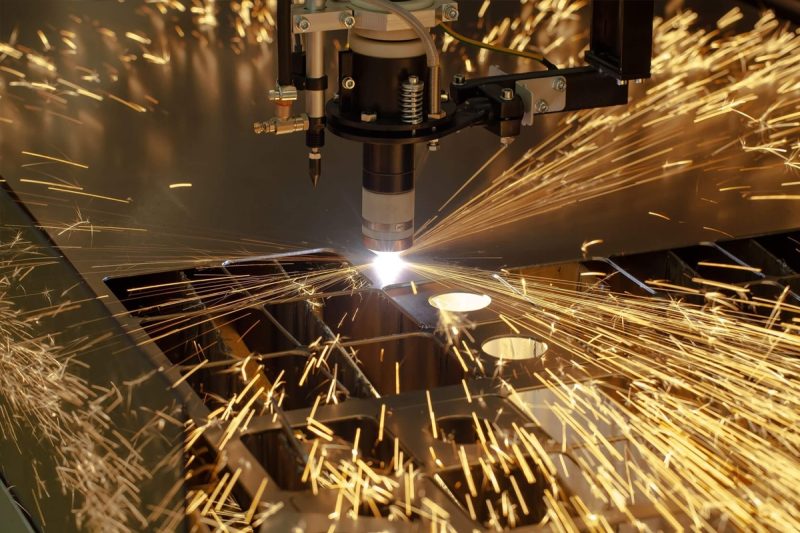
まとめ
レーザー切断とプラズマ切断のどちらを選ぶかは、特定のアプリケーションのニーズによって決まります。レーザー切断は、精度、正確性、きれいで滑らかなエッジの生成に優れているため、複雑なディテールと高品質の仕上げが不可欠な航空宇宙、自動車、電子機器などの業界に最適です。また、薄い材料にも適しており、長期的には運用コストとメンテナンス コストが低くなります。ただし、初期投資は高く、厚い金属の切断にはそれほど効率的ではない場合があります。
一方、プラズマ切断は、より厚く導電性のある金属を切断する場合、より高速でコスト効率に優れています。プラズマ切断は、細かい部分よりも速度と材料の厚さが優先される建設業や金属加工業などの重工業で広く使用されています。プラズマ切断は初期費用が低いですが、材料の無駄が多くなり、エネルギー消費量が多くなり、メンテナンスも必要になる傾向があります。
結局のところ、レーザー切断は精度に優れており、プラズマ切断は高速で厚い金属を切断するのに最適です。
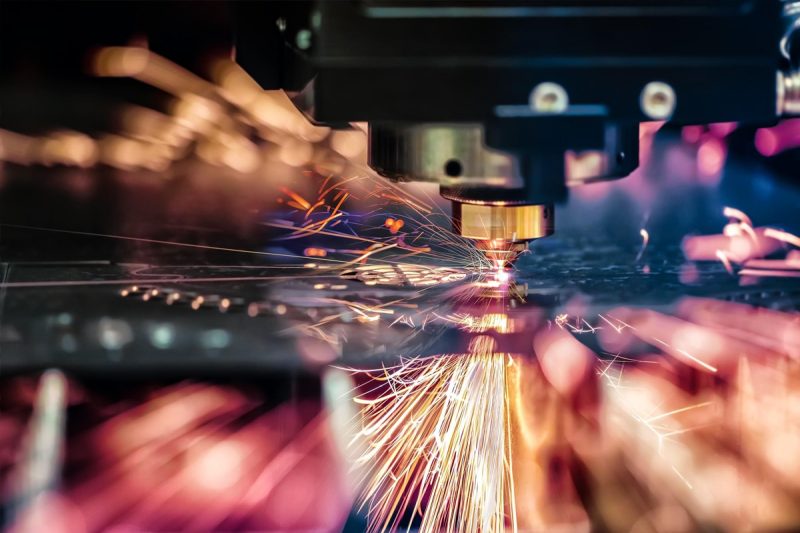
AccTekレーザーでレーザーソリューションを入手
精密切断に関しては、AccTek Laser はお客様の製造ニーズに合わせた高度なソリューションを提供します。レーザー切断機の大手メーカーとして、当社はさまざまな材料で高精度、きれいなエッジ、優れた性能を実現する最先端の技術を提供しています。薄い金属を扱う場合でも、複雑なデザインを作成する必要がある場合でも、当社のファイバー レーザー切断機は、正確で効率的、かつコスト効率の高い生産を保証します。
AccTek Laser では、専門家によるコンサルティング、カスタマイズ可能なマシン構成、堅牢なアフターサービスなど、包括的なサポートも受けられます。当社のマシンは、材料の無駄を最小限に抑え、エネルギー消費を減らし、運用効率を高めるように設計されています。レーザー切断に加えて、レーザー溶接、クリーニング、マーキングマシンのフルラインナップも提供しており、レーザーベースのすべての製造プロセスに対するワンストップソリューションを提供します。
次のプロジェクトには AccTek Laser を選択し、レーザー技術の優れた利点を体験してください。
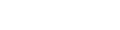
連絡先
- [email protected]
- [email protected]
- +86-19963414011
- No. 3 ゾーン A、Lunzhen 工業地帯、玉城市、山東省。
レーザー ソリューションを入手する