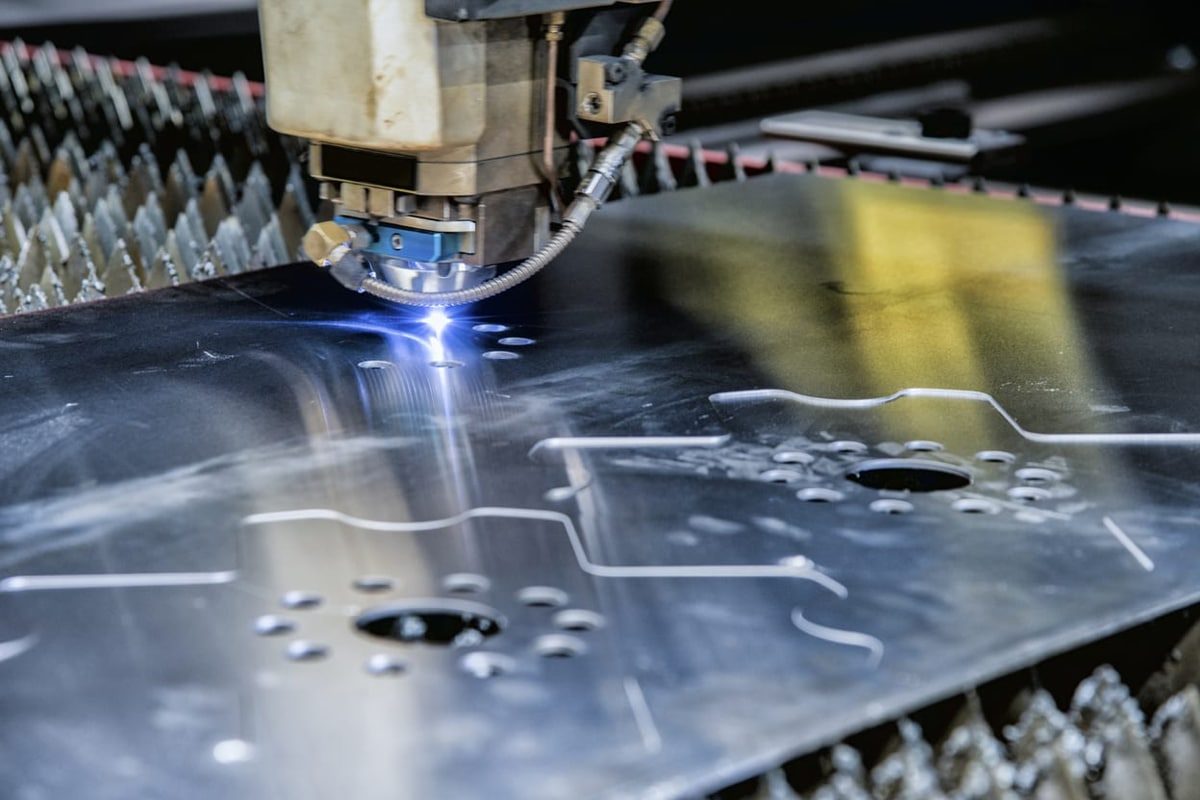
レーザー切断:材料の最適化と精密な生産
現代の製造業では、製造の精度が非常に重要です。レーザー切断技術は、材料を最適化し、製造プロセスを合理化する画期的な技術です。レーザー切断は精度が高いため、さまざまな材料に複雑なパターンや形状を作成できます。金属から木材、プラスチックまで、レーザー切断の汎用性は従来の製造方法を完全に変革し、前例のないレベルの有効性と効率性を実現しました。この記事では、レーザー切断の世界を深く掘り下げ、その無数の用途、利点、精密製造の未来を形作る上での重要な役割を探ります。レーザー切断の変革力と、材料の最適化と精密製造の水準向上への影響を探ります。
目次
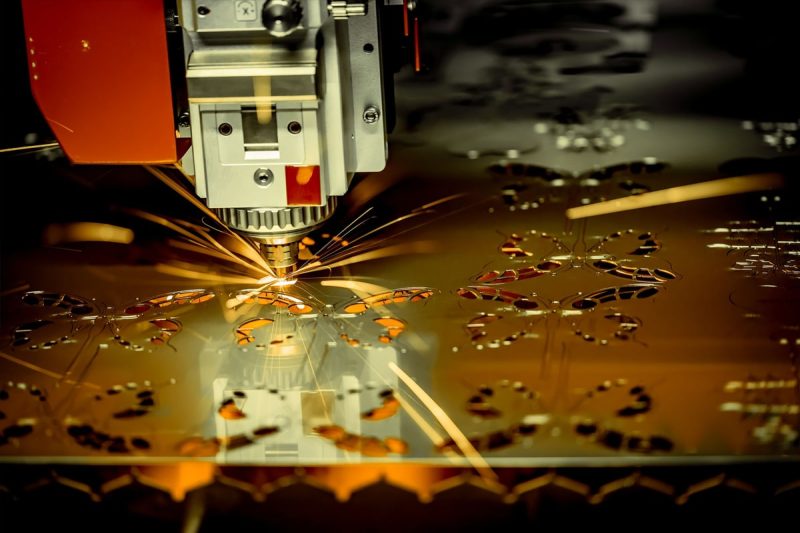
レーザー切断技術の紹介
わずかな偏差でも品質が損なわれる可能性がある精密製造の世界では、レーザー技術の精度が非常に重要です。 レーザー切断 この技術は、焦点を絞ったレーザー光線が材料を正確に切断または彫刻するという原理に基づいています。このプロセスには、レーザー光源、焦点合わせミラー、切断材料、レーザー光線の動きを誘導するコンピューター制御システムなど、いくつかの主要なコンポーネントが関係します。レーザー切断技術の基本原理は次のとおりです。
- 集束ビーム: レーザー切断は、高度に集束されたビームを材料の表面に照射することで機能します。集束により、レーザー発生器は指定された切断経路に沿って材料を溶解、燃焼、または蒸発させる強力な熱を発生させることができます。
- 材料の相互作用: 材料によってレーザー ビームとの相互作用の仕方は異なります。金属は通常レーザー エネルギーを吸収しますが、非金属材料はレーザー エネルギーを反射したり部分的に吸収したりします。この多様性により、金属やプラスチックから木材や布地まで、さまざまな材料を切断できます。
- コンピュータ制御の精度: レーザー切断は、コンピュータ支援設計 (CAD) ソフトウェアによって制御されるデジタル制御プロセスです。ソフトウェアは切断パスとパラメータを正確に決定し、複雑なデザインや形状を無駄を最小限に抑えて正確に再現します。
- 非接触切断: 鋸引きやフライス加工などの従来の方法とは異なり、レーザー切断は非接触プロセスです。レーザービームは材料に機械的な力を加えないため、歪みや損傷のリスクが軽減され、複雑で繊細な部品の製造が可能になります。
- 熱影響部を最小限に抑える: レーザー切断では、熱の影響により材料の特性が変化する可能性のある周囲の領域である熱影響部 (HAZ) を最小限に抑えます。これにより、熱による損傷を受けやすい材料に適した、きれいで正確な切断が可能になります。
デジタル設計ファイルを調整してコンピュータ制御システムをガイドすることで、広範囲の切断深さと複雑さを実現し、レーザー切断で効果的かつ正確な製造プロセスを実現できます。この記事では、これらの原理をさらに詳しく説明します。
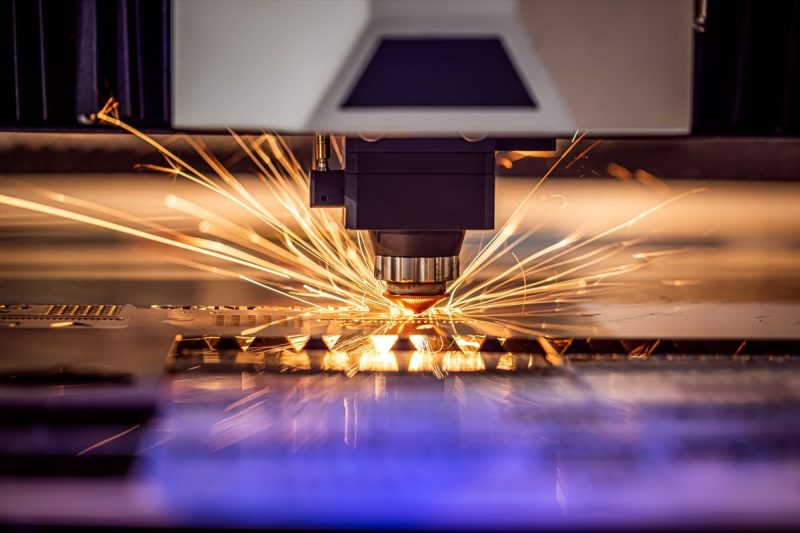
レーザー切断の主な利点は材料の無駄を減らすことです
レーザー切断技術は、精度と正確さ、ネスト最適化、切開幅の縮小、材料の柔軟性、迅速な生産と設計、材料処理の削減(材料損傷の可能性の低減)、プロトタイプの設計とテストの点でどのように機能しますか?材料の無駄を減らしますか?以下について説明します。
精密な切断
レーザー切断機 高出力レーザーを使用して、信じられないほどの精度で材料を正確に切断します。この精度により、最小のマージンまたはカーフ幅が可能になります。カーフ幅とは、切断プロセスで除去される材料の幅を指します。レーザー切断では、切断幅を数千分の1インチまで小さくできるため、鋸引きやせん断などの従来の切断方法と比較して、材料の無駄を大幅に削減できます。この精度により、材料を効率的に使用し、無駄を最小限に抑え、生産を最適化できます。
ネストされた最適化
ネスト最適化ソフトウェアは、切断する部品の形状を分析し、部品の形状、サイズ、数量、材料の制約など、材料シート上で部品を最も効率的に配置する方法を決定します。部品をインテリジェントにネストして部品間のスペースを最小限に抑えることで、ボードの表面積全体を効率的に使用できます。これは、部品間の未使用スペースを減らすように部品を戦略的に配置することで実現され、無駄な材料の量を減らします。
カーフ幅の縮小
レーザー切断のカーフ幅を狭めるには、ノッチ幅を狭める必要があり、その結果、より細かく、より正確な切断が可能になります。各パスで除去される材料の量を最小限に抑えることで、レーザー切断は材料の利用効率を高めます。ノッチ幅を狭めると、より多くの原材料が保存され、切断プロセス中の廃棄物の発生が大幅に減少します。
素材の柔軟性
レーザー切断における材料の柔軟性は、廃棄物の削減に不可欠です。レーザー切断は、幅広い材料に対応することで、リソースの使用を最適化し、セットアップ時間を最小限に抑え、材料間の精度を維持し、カスタマイズとプロトタイプ作成を容易にします。この包括的なアプローチにより、製造プロセス全体を通じて効率的な生産、エラーの削減、廃棄物の発生の最小化が保証されます。
迅速な生産と設計
迅速な生産と設計は、効率的なプロトタイピング、オンデマンド製造、カスタマイズ、最適化された生産工程、合理化された設計反復を促進し、レーザー切断による材料の無駄を最小限に抑える上で重要な役割を果たします。この包括的なアプローチにより、ギャップ幅が効果的に削減され、さまざまな製造プロセスにわたって材料の利用率が向上し、無駄が削減されます。
材料処理の削減
レーザー切断では材料の取り扱いが少なくなるため、材料が損傷する可能性が減り、廃棄物の削減に役立ちます。切断プロセス中に材料を移動または操作する必要性が最小限に抑えられるため、レーザー切断では材料の無駄につながる偶発的な損傷やエラーのリスクが軽減されます。この合理化されたアプローチにより、製造プロセス全体を通じて材料が無傷のまま損傷を受けず、材料の有用性が最大限に高まり、廃棄物の発生が最小限に抑えられます。
プロトタイプの設計とテスト
プロトタイプ作成とテストの側面の概要は、反復的な設計サイクルの促進、スクラップの最小化、カスタマイズの実現、生産プロセスの合理化、およびリソース利用の最適化によって、レーザー切断による材料の無駄の削減をサポートします。この包括的なアプローチにより、材料の効率的な使用が保証され、無駄のない無駄の削減に貢献します。
要約すると、レーザー切断は、製造における材料の無駄を最小限に抑え、生産プロセスを合理化する多面的なアプローチを提供します。これらの利点を組み合わせることで、最終的には材料の効率的な使用が可能になり、レーザー切断は製造廃棄物を削減するための効果的なツールになります。
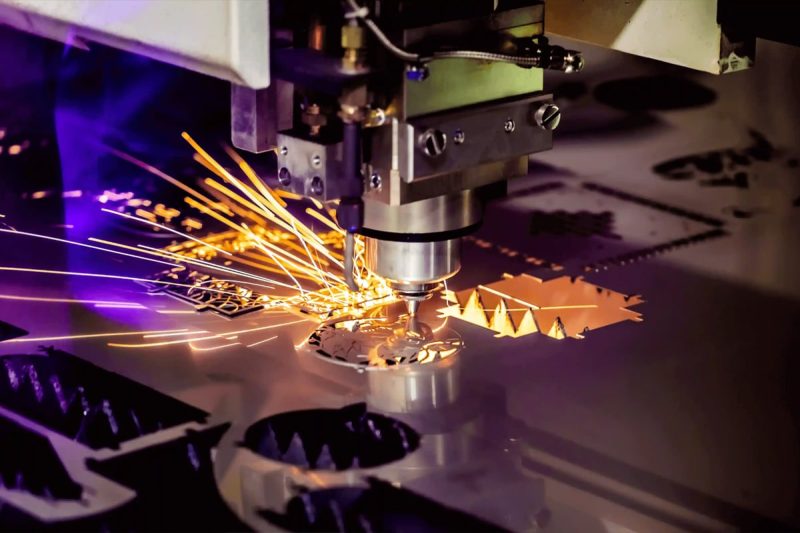
材料利用におけるレーザー切断のその他の利点
材料使用に関する上記の利点に加えて、レーザー切断技術には、複雑な設計が可能、熱影響領域が最小、ツールの摩耗が少ない、複数の材料を処理できるなどの利点もあります。詳細は次のとおりです。
複雑な設計機能
レーザー切断は、複雑な形状や幾何学的形状を高精度に切断するのに優れており、極めて高精度に曲線を切断できます。この機能により、デザイナーは複雑なデザインを作成でき、滑らかな曲線や有機的な形状を必要とする複雑なデザインに特に役立ちます。レーザー切断は、デザインの輪郭に正確に従い、利用可能な材料を最大限に活用することで、直線切断や手作業による成形に伴う材料の無駄を最小限に抑えます。
最小の熱影響エリア
レーザー切断技術では熱影響部が最小限に抑えられ、材料の構造的完全性が維持され、後処理の必要性が最小限に抑えられます。プラズマ切断や火炎切断などの従来の切断方法では、大量の熱が発生し、切断部分の周囲で材料が反ったり変形したりします。レーザー切断の熱影響部が最小限に抑えられるため、この反りが最小限に抑えられ、追加の仕上げや改良を最小限にとどめ、材料が元の形状とサイズを維持できます。
ツールの摩耗を軽減
レーザー切断は、刃やドリルなど、使用すると劣化する物理的なツールに依存しないため、切断装置の寿命が大幅に延びます。ツールの寿命が長くなると、ツールの交換頻度が減り、廃棄または摩耗したツールに関連する材料の無駄が最小限に抑えられます。ツールの摩耗が最小限に抑えられるため、欠けや鈍化などのツール関連の欠陥のリスクが軽減され、各切断が材料の無駄を最小限に抑えながら最終製品に貢献することが保証されます。
複数の材料の加工
レーザー切断技術は、金属、プラスチック、木材、ガラス、複合材など、さまざまな材料を切断できます。この汎用性により、メーカーは 1 台のマシンでさまざまな材料を切断できるため、材料の種類ごとに個別の切断装置を用意する必要がなくなります。切断プロセスを 1 台のマシンに統合することで、メーカーはセットアップ時間、ツールの変更、複数のマシンのメンテナンスに伴う材料の無駄を最小限に抑えることができます。
これらの機能により、厳しい許容誤差を伴う複雑な設計を高速化し、材料の完全性を維持し、ツールの寿命を延ばし、さまざまな材料タイプに適応して材料の利用率を向上させることができます。したがって、レーザー切断はさまざまな業界で材料の使用効率を最大化し、コストを節約し、製品の品質を向上させるのに役立ちます。
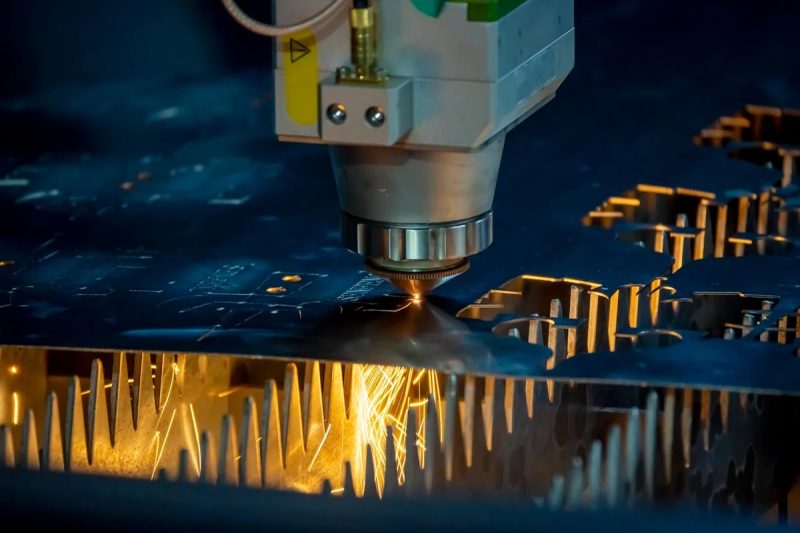
レーザー切断の異業種への応用
レーザー切断技術は、その精度、汎用性、効率性により、さまざまな業界で多種多様な用途に使用されています。以下にいくつか例を挙げます。
- 製造と加工: レーザー切断は、金属 (鋼鉄、アルミニウム、チタン)、プラスチック、複合材などのさまざまな材料を切断して成形するための製造と加工で広く使用されています。自動車部品、航空宇宙部品、機械、家電製品などを生産する業界で採用されています。
- 自動車業界: レーザー切断は、自動車業界で複雑な部品やコンポーネントの製造に利用されています。車体、シャーシ、排気システム、エンジン部品、内装部品の板金切断に使用されます。レーザー切断された部品は、後処理が最小限で済むことが多く、製造時間とコストを削減できます。
- 航空宇宙および防衛: 航空宇宙および防衛の用途では、レーザー切断技術を使用して、軽量で複雑な部品を高精度に製造します。航空機部品、ミサイル システム、防衛機器用のアルミニウム、チタン、炭素繊維複合材などの材料を切断するために使用されます。
- 電子機器および消費財: レーザー切断は、電子機器の筐体、スマートフォンケース、ラップトップのコンポーネント、装飾品などに使用される PCB (プリント回路基板)、アクリル、プラスチックなどのさまざまな材料の切断や彫刻に電子機器業界で利用されています。レーザー切断は、複雑なデザインでも正確な切断とマーキングが可能です。
- 医療機器: レーザー切断技術は、医療機器業界で、手術器具、インプラント、医療機器、診断機器の精密部品の製造に使用されています。医療用途に不可欠な、厳密な許容誤差を持つ小型で複雑な部品の製造を可能にします。
- 繊維およびアパレル: レーザー切断は、繊維およびアパレル業界で、布地、皮革、合成素材を高精度に切断するために使用されています。これにより、衣類、履物、アクセサリー、室内装飾品に複雑なパターン、デザイン、カスタマイズを施すことができます。
- 建築とインテリア デザイン: レーザー カッティングは、建築とインテリア デザインで、装飾要素、標識、建築モデル、建物のファサード、壁パネル、家具、照明器具の複雑なパターンを作成するために利用されています。これにより、デザイナーは複雑なデザインを精密でカスタマイズされた製品に変換できます。
- 芸術と工芸: レーザー切断技術は、複雑な芸術作品、彫刻、宝石、装飾品を作成するために、芸術と工芸のコミュニティで人気があります。アーティストや職人は、レーザー切断を使用して、木材、アクリル、紙、ガラスなどのさまざまな材料を加工し、正確なディテールと複雑なデザインを実現します。
これらは、さまざまな業界でレーザー切断技術が幅広く応用されている例のほんの一部です。その汎用性と精度により、レーザー切断技術はさまざまな分野で生産性、効率性、創造性を高める貴重なツールとなっています。
要約する
レーザー切断技術の将来は、大きな進歩を遂げるのに役立ちます。これは、ドライバーが材料の使用を最適化し、精密な生産能力を向上させることに常に注力しているためです。業界の需要の効率、柔軟性、持続可能性が高まるにつれて、レーザー切断はこれらの継続的な開発ニーズを満たす上で重要な役割を果たすことが期待されます。
材料の最適化と正確な生産により、パフォーマンスを最大化し、コストを最小限に抑えることができます。レーザー切断機の選択をお手伝いする必要がある場合は、いつでもお客様のアプリケーションに最適な切断ソリューションをご提供いたします。お問い合わせ AccTek レーザー 今すぐ始めましょう!
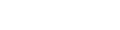
連絡先
- [email protected]
- [email protected]
- +86-19963414011
- No. 3 ゾーン A、Lunzhen 工業地帯、玉城市、山東省。
レーザー ソリューションを入手する