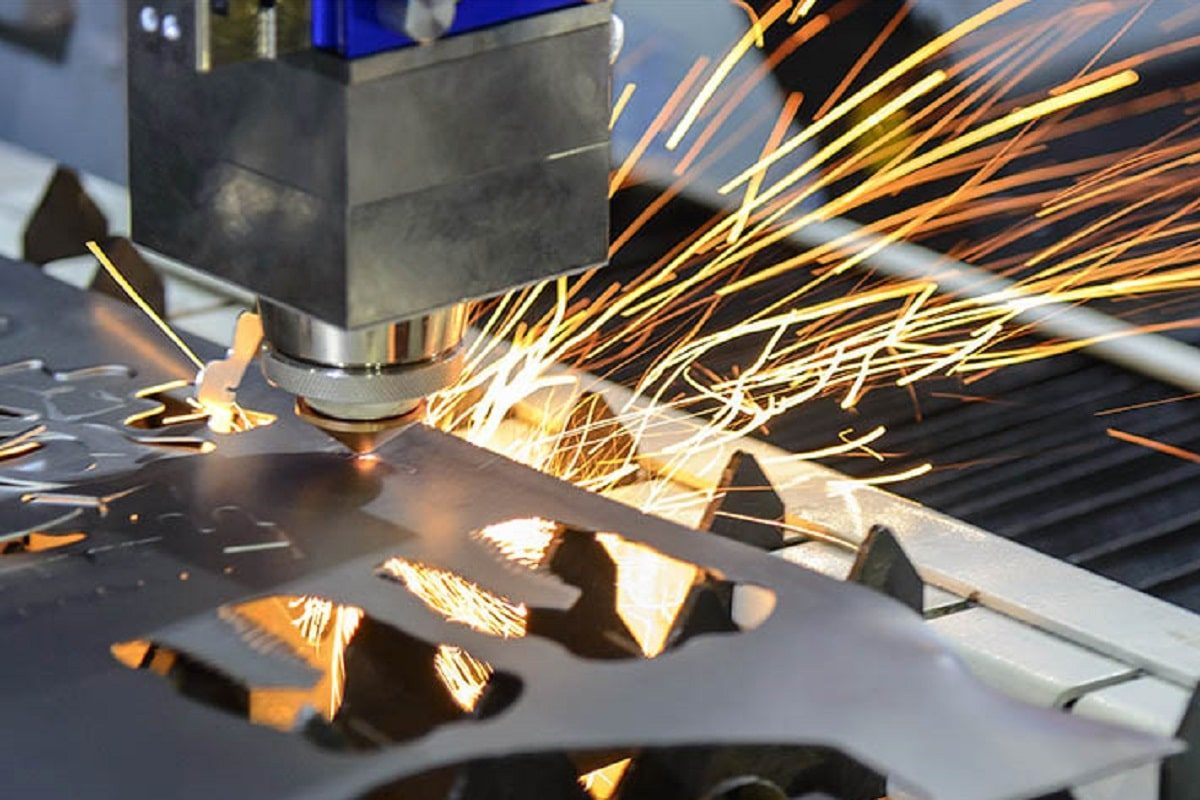
レーザー切断パラメータ: 究極のガイド
レーザー切断は、航空宇宙から宝飾品製造に至るまでの業界でさまざまな素材を高精度に切断するために使用される多用途かつ正確な切断プロセスです。レーザー切断の品質と効率は、いくつかの重要な要素によって決まります。最良のレーザー切断結果を得るには、この切断プロセスに関係する主要なパラメータを直感的に理解し、制御することが重要です。この包括的なガイドでは、レーザー切断操作で最高の切断結果を達成するために役立つこれらのパラメーターの詳細を詳しく説明します。
目次
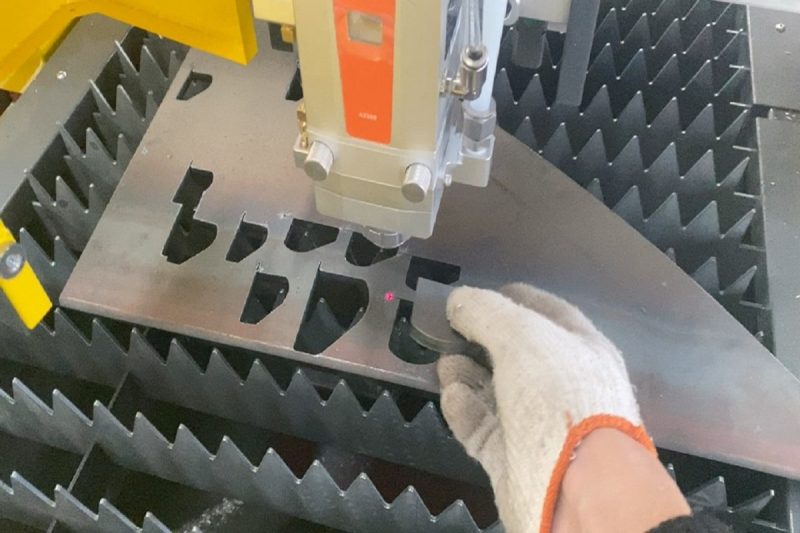
レーザーカットとは?
レーザー切断は、高度に集束したレーザー ビームを使用して、金属、プラスチック、木材などのさまざまな材料を正確かつきれいに切断する製造プロセスです。レーザー ビームによって生成される強烈な熱により、プログラムされた経路に沿って材料が蒸発、溶解、または焼き尽くされます。 、切削工具との物理的な接触を必要とせずに、正確で複雑な切断を可能にします。レーザー切断は、その精度、速度、幅広い用途における多用途性で知られています。
レーザー切断の精度により、複雑なデザインや細かいディテールが可能となり、小規模生産と大量生産の両方に適しています。金属、プラスチック、木材、繊維など、さまざまな素材を切断できる多用途性で知られています。レーザー切断は、熱の影響を受ける部分が最小限に抑えられるため、周囲の素材への歪みや損傷が最小限に抑えられるという点で好まれています。
レーザー切断は、精密部品の製造、複雑なアートワークの作成、産業用途での材料の成形に使用されるかどうかに関係なく、高品質でカスタマイズされた結果を卓越した精度で実現するための重要なテクノロジーです。
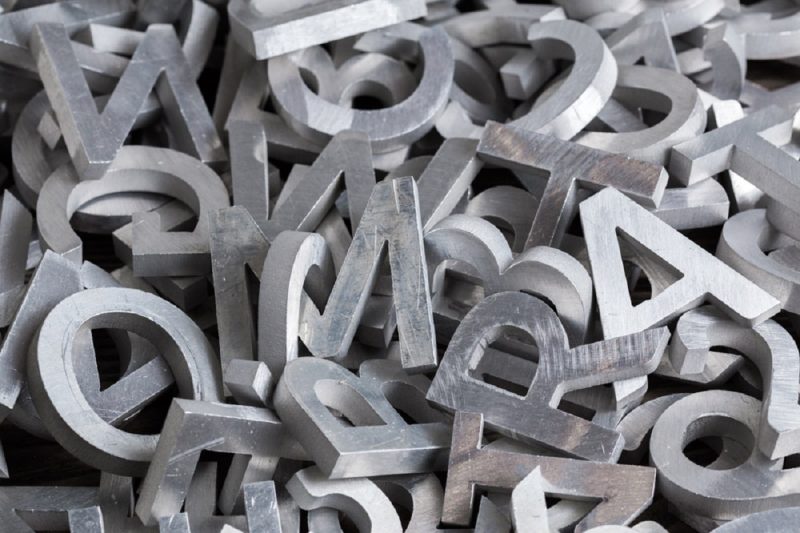
レーザー切断で制御すべき最も重要なパラメータは何ですか?
レーザー切断は、材料加工において比類のない精度と多用途性を提供する革新的な切断技術です。この最先端テクノロジーの可能性を最大限に活用するには、そのパフォーマンスを制御する主要なパラメーターを理解し、操作する必要があります。レーザー切断の基本パラメータを詳しく見て、その重要性と最終結果に与える影響を理解しましょう。
レーザーパワー
- 意味: レーザー出力は通常、ワット (W) で測定され、レーザー ビームの強度と材料を透過する能力が決まります。
- 注: レーザー出力が高いほど、より厚い材料をより速く切断できますが、レーザー出力が高すぎると、不要な熱影響ゾーンや不正確なエッジが作成される可能性があります。逆に、より低いレーザー出力は、複雑な細部やより薄い材料に最適です。材料の厚さに基づいてレーザー出力を正確に調整することで、最適な結果を得ることができます。
切断速度
- 意味: 切断速度は、1 秒あたりのミリメートル (mm/s) または 1 分あたりのインチ (in/min) で測定され、レーザー ヘッドが材料の表面に沿って移動する速度を決定します。
- 注: 通常、速度が遅いほど、エッジが滑らかになり、精度が高くなります。逆に、材料が薄い場合や生産性が高い場合には、より速い速度が使用されます。切断速度の選択は、材料の厚さと要求される品質によって異なります。
焦点/ビーム径
- 意味: 焦点またはビーム直径は、材料と相互作用するレーザービームの幅を指し、切断精度に直接影響します。適切な焦点合わせにより、きれいで正確なカットが保証されます。
- 注: 正確な焦点により、一貫した高品質の切断結果が得られます。焦点が正しくないと、切断品質が変化し、熱発生が増加する可能性があります。最適な切断パフォーマンスを得るには、材料の種類と機械の厚さに基づいて焦点を慎重に調整する必要があります。
補助ガスの圧力と種類
- 意味: 酸素、窒素、空気などの補助ガスは、溶融した材料を切断領域から除去し、きれいな切断を維持する上で重要な役割を果たします。
- 注: 特定の材料と厚さには、正確なアシストガスの種類と圧力設定が必要です。たとえば、炭素鋼の切断には通常酸素が使用されますが、非鉄金属やプラスチックには窒素が好まれます。適切なアシストガスを選択すると、効率的な切断が保証され、酸化が最小限に抑えられます。
材料の厚さ
- 意味: 材料の厚さは、出力、速度、アシストガス設定などのさまざまなレーザー切断パラメータに影響を与える重要な要素です。
- 注: 正確で最適な結果を得るには、材料の厚さに基づいてレーザー設定をカスタマイズする必要があります。メーカーのガイドラインやテストカットの作成は、正しい切断パラメータを決定するのに役立ちます。
パルス周波数または連続波モード
- 意味: パルス周波数 (ヘルツ (Hz) で測定) はレーザー パルスの周波数を決定しますが、連続波モードは連続レーザー ビームを提供します。
- 注: パルス周波数が高いと切断速度と精度が向上しますが、発熱量も多くなります。連続波モードは一定のビームを提供しますが、より多くの熱を発生する可能性があります。モードの選択は、特定の切断要件と材料特性によって異なります。
ノズル径とノズル間隔
- 意味: ノズル直径はレーザービームの集束と材料との相互作用に影響を与えますが、分離距離はノズルと材料表面の間のギャップを指します。
- 注:材質や用途に応じて適切なノズルサイズを選択する必要があります。小さいノズルは細かい作業に適しており、大きいノズルはより速い切断をもたらす可能性があります。さらに、切断効率と品質を最適化するには、分離距離を調整する必要があります。
前処理と後処理
- 意味: 前処理には表面のクリーニングやマスキングなどのタスクが含まれ、後処理にはバリ取りやクリーニングなどの作業が含まれます。どちらも切断を成功させるために重要です。
- 注: 材料を洗浄すると、最良の切断結果が得られます。適切な前処理により、切断前に材料に汚染物質が付着していないことが保証されます。一方、所望の最終製品を得るには、バリ取りや洗浄などの後処理ステップが必要になることが多く、確実に研磨された表面を確保します。

最適なレーザー切断パラメータを見つけるにはどうすればよいですか?
最適なレーザー切断パラメータを見つけるには、望ましい切断品質、速度、精度を達成するためにさまざまな要素を最適化する必要があるため、体系的かつ系統的なアプローチが必要です。ここでは、特定の材料と用途に最適なレーザー切断パラメータを決定する方法について、詳細なステップバイステップ ガイドを示します。
- 材料の評価: 切断する必要がある材料を徹底的に理解することから始めます。組成、厚さ、および放射率、熱伝導率、硬度などの固有の特性に関する情報を収集します。材料の特性を理解すると、正しいレーザー切断パラメータを選択するのに役立ちます。
- メーカーのガイドラインを参照する: レーザー カッターのメーカーの推奨事項とガイドラインを参照してください。これらのガイドラインは、多くの場合、材料の種類と厚さに基づいてパラメータを設定するための開始点を提供し、安全性と機械の互換性を確保するのに役立ちます。
- 制御された環境をセットアップする: 材料がレーザー カッター内にしっかりと保持され、正しく配置されていることを確認しながら、実験を安全に実施できる制御されたテスト環境を作成する必要があります。
- テスト計画を作成する: テストするパラメーターと炭酸化する各パラメーターの値の範囲の概要を示し、実験用に構造化されたテスト計画を作成します。
- 重要なパラメータを決定する: 特定の用途にとってどのレーザー切断パラメータが最も重要かを決定します。通常、主なパラメータには、レーザー出力、切断速度、焦点/ビーム直径、補助ガスの種類と圧力、ノズル直径が含まれます。
- レーザー出力の実験: 他のパラメータを一定に保ちながら、レーザー出力を変化させることから実験を開始します。材料の予想される出力要件を満たす範囲の出力設定から開始し、切込み深さ、熱影響ゾーン、切断端の外観などの要素に注意しながら、材料がさまざまな出力設定にどのように反応するかを観察します。材料に過度のダメージを与えることなく、必要な切断品質を実現できる出力設定を探してください。
- 切断速度を調整する: 最適な出力設定を決定したら、レーザー出力を一定に保ちながら切断速度を調整して実験を開始します。エッジの滑らかさ、精度、歪みの兆候に注意を払い、さまざまな切断速度が切断品質に及ぼす影響を評価します。
- 焦点とビーム直径の最適化: 焦点とビーム直径の設定を微調整します。焦点を調整して、レーザービームが材料と最も効果的に相互作用するスイートスポットを見つけます。焦点とビーム直径の変化が切断品質、特に切り口の幅と熱の影響を受けるゾーンに及ぼす影響を評価し、きれいで正確な切断を実現する設定を探します。
- アシストガスパラメータを調べる: さまざまな種類のアシストガス (酸素、窒素、圧縮空気など) をテストし、圧力設定を調整します。アシストガスとその圧力の選択は、切断プロセスに大きな影響を与える可能性があります。アシストガスが材料の除去にどのように役立つか、またそれが最終的な切断品質にどのような影響を与えるかを評価します。
- パルス周波数または連続波モードをテストする: さまざまなパルス周波数または連続波モード設定をテストして、切断速度と精度のバランスを見つけます。材料や厚さが異なれば、必要なパルス周波数も異なる場合があるため、より高速な切断と潜在的な発熱とのトレードオフを考慮してください。
- ノズルの直径と分離距離: ノズルの直径とノズルから材料までの分離距離を調整して、ビームの焦点と材料の相互作用を最適化します。エッジの滑らかさや速度などの要素を考慮して、これらのパラメータの変更が切断品質に及ぼす影響を評価します。
- 後処理評価: テストカットのたびに、カット品質を慎重に評価します。エッジの滑らかさ、バリの有無、材料の歪みを確認し、正確な測定を行って、必要な許容範囲と比較します。
- 記録と分析: 各テストの詳細な記録を保管し、使用した特定のパラメーター、観察された切断品質、および発生した注目すべき観察や問題を記録します。このデータを使用して、最適なパラメーターの組み合わせにつながる傾向とパターンを特定します。
- 反復と調整: 観察と評価に基づいてパラメータ設定を調整し、必要に応じて段階的に調整を行い、特定の品質と効率の要件に合わせてパラメータの最適な組み合わせを達成することを目指します。さらに、アプリケーションに必要な切断品質、効率、精度が達成されるまで、プロセスを評価および改善するために継続的な実験が必要です。
- 安全性と機械の制限を考慮する: テストプロセス全体を通じて安全性を限定的に考慮し、レーザーカッターが機器や人員に害を及ぼさずに選択されたパラメータを処理できることを確認する必要があります。
- 専門家のアドバイスとリソースを求める: 問題が発生した場合、または具体的な質問がある場合は、経験豊富なレーザー オペレーター、エンジニア、またはレーザー切断技術の専門家に遠慮なくアドバイスを求めてください。さらに、レーザー切断専用のオンライン フォーラム、コミュニティ、リソースを探索することをお勧めします。これらは、一般的な課題に対する貴重な洞察や解決策を提供することがよくあります。
- 検証と生産: 最適なレーザー切断パラメータを決定したら、追加のテスト切断を実行してそれらを検証し、一貫性と信頼性を確保します。次に、最適化されたパラメータを生産プロセスに適用し、定期的に監視および保守します。 レーザー切断機 パフォーマンスを維持するために。
最適なレーザー切断パラメータを見つけるには、忍耐と細部への注意が必要な、細心の注意を払って反復的なプロセスが必要です。これらの手順に従い、徹底的な実験を行うことで、特定の材料や用途に合わせて正確、効率的、高品質のレーザーカットを行うための最適なパラメータを決定できます。
要約する
まとめると、レーザー切断パラメータをマスターすることは、正確で高品質の切断を実現するのに役立ちます。通常、特定の材料や用途に合わせてこれらのパラメータを微調整するには、実験とテストが必要です。レーザー切断パラメータを調整するときは、安全性と最適な結果を確保するために、常にメーカーの推奨事項とガイドラインに従ってください。レーザー切断の専門知識には経験が必要です。そのため、このプロセスに不慣れな場合は、当社の専門家チームに遠慮なくお問い合わせください。AccTek Laserの専門家チームは、お客様の要件に基づいて適切なパラメータ設定を推奨します。もちろん、無料の校正サービスも提供しています。必要な場合は、 お問い合わせ いつでも。
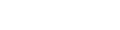
連絡先
- [email protected]
- [email protected]
- +86-19963414011
- No. 3 ゾーン A、Lunzhen 工業地帯、玉城市、山東省。
レーザー ソリューションを入手する