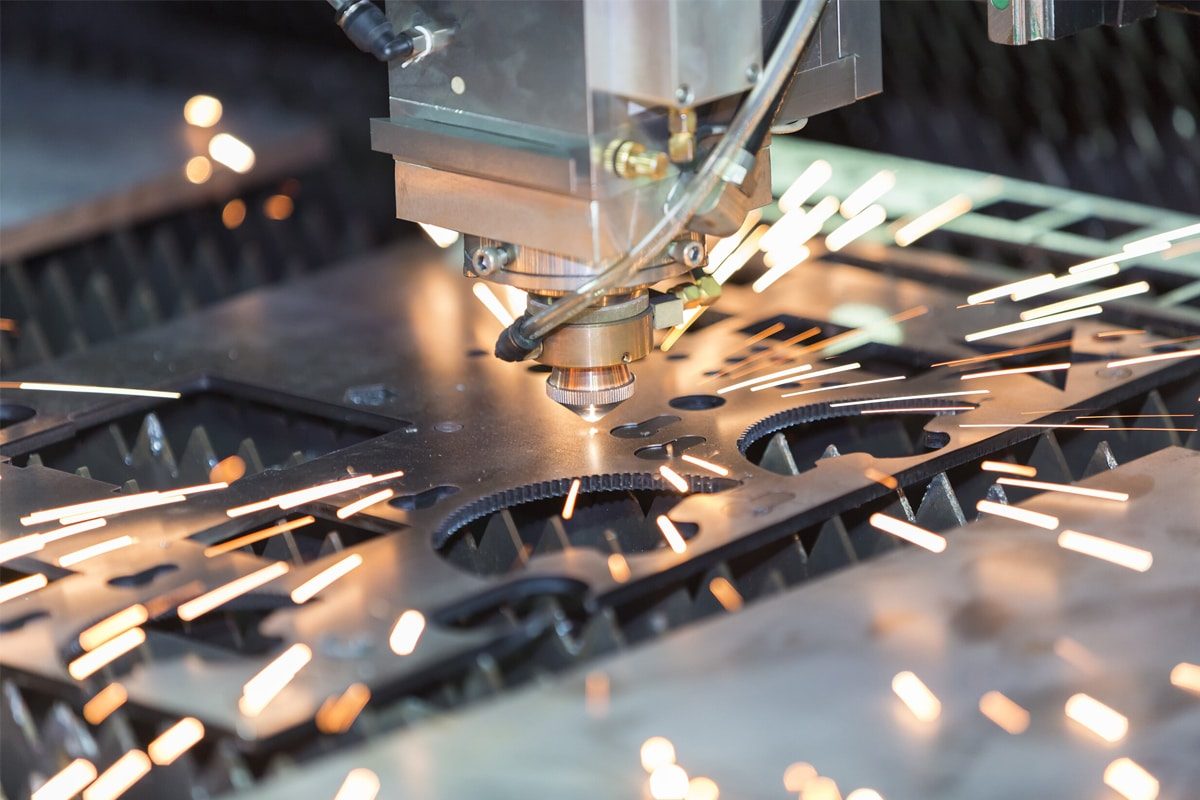
レーザー切断パワーを決定する方法は?
適切なレーザー切断出力を決定することは、さまざまな材料や用途に合わせてレーザー切断プロセスを最適化する上で重要なステップです。レーザー切断出力は、切断速度、エッジ品質、効果的に処理できる材料の範囲に直接影響します。適切な出力設定の選択方法を理解することで、精度、効率、コスト効率に優れた生産が可能になります。材料の種類、厚さ、必要なエッジ品質、切断速度要件などの要素はすべて、この決定において重要な役割を果たします。さらに、CO2、ファイバー、Nd レーザーなどのさまざまなタイプのレーザーには、出力能力に基づいてさまざまな利点と制限があります。
これらの要素を徹底的に評価することで、製造業者も愛好家も、優れた切断結果を達成し、材料の無駄を最小限に抑え、レーザー切断機の寿命を延ばすことができます。この記事では、さまざまな切断作業に必要なレーザー切断パワーを正確に決定し、全体的な生産性と品質を向上させる方法について詳しく説明します。
目次
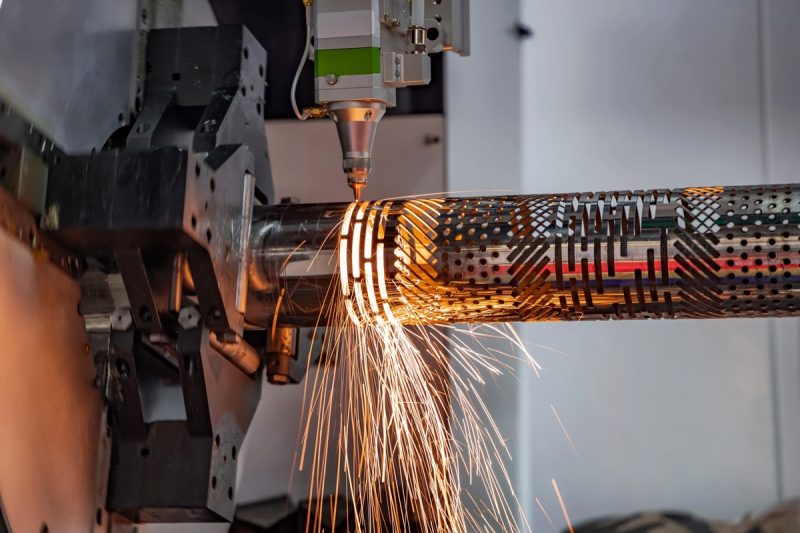
レーザーパワーの理解
レーザーパワーとは何ですか?
レーザー出力は、レーザー ビームのエネルギー出力の尺度で、通常はワット (W) またはキロワット (kW) で表されます。これは、単位時間あたりにレーザーから放出されるエネルギーの量を表します。このエネルギーは、材料を高精度に切断、彫刻、エッチングするために焦点を絞ることができる細いビームに集中します。レーザーの出力によって、さまざまな材料を貫通して切断する能力が決まります。レーザー出力が高いほど、材料に伝達されるエネルギーが多くなり、切断の効率と速度が向上しますが、材料を損傷しないように注意深く制御する必要もあります。
レーザー出力が切断プロセスに与える影響
レーザー出力はレーザー切断プロセスにおいて重要な役割を果たし、いくつかの重要な側面に影響を及ぼします。
- 切断速度: レーザー出力が高いほど、切断速度が速くなります。これは、材料を溶かしたり、気化させたり、燃やしたりするために利用できるエネルギーが増えるため、切断速度が速くなるためです。高い生産性が重要な産業用途では、レーザー出力を高くすると、生産時間を大幅に短縮できます。
- エッジ品質: 切断エッジの品質はレーザー出力によって左右されます。最適な出力設定により、バリや熱歪みを最小限に抑えながら、滑らかできれいなエッジが得られます。ただし、出力が高すぎると、エッジの焼け、過剰な溶融、熱影響部 (HAZ) の拡大が発生し、エッジ品質が損なわれる可能性があります。
- 材料の貫通: レーザー出力によって、さまざまな厚さの材料を切断できる能力が決まります。厚い材料の場合は、レーザー ビームが材料の深さ全体に貫通できるように、より高い出力が必要です。薄い材料の場合は、低い出力設定で十分な場合が多く、不要な熱の蓄積や材料の損傷を防ぐことができます。
- 材料除去率: 材料除去率はレーザー出力によって影響を受けます。出力が高いほど材料除去率も高くなります。これは厚い材料には有利ですが、薄い材料の場合は過剰に溶けたり燃えたりする可能性があります。
- 精度と詳細: 複雑なデザインや細かいディテールの場合は、レーザー出力を低くする方がよい場合が多くあります。これにより、レーザー ビームを正確に制御でき、過剰カットのリスクが軽減され、詳細な特徴が正確にレンダリングされます。
- 熱の影響: レーザー出力が高すぎると、特に熱に敏感な材料では、反りや変色などの顕著な熱の影響が生じる可能性があります。適切な出力調整を行うことで、これらの悪影響を最小限に抑えることができます。
適切なレーザー出力を選択するには、材料の特性と希望する切断結果を理解する必要があります。レーザー出力、材料の種類、厚さのバランスをとることで、最適な切断性能を実現できます。材料と切断作業の特定の要件に合わせてレーザー出力を慎重に調整することで、オペレーターは高品質の切断、効率的な生産、材料の無駄を最小限に抑えることができます。
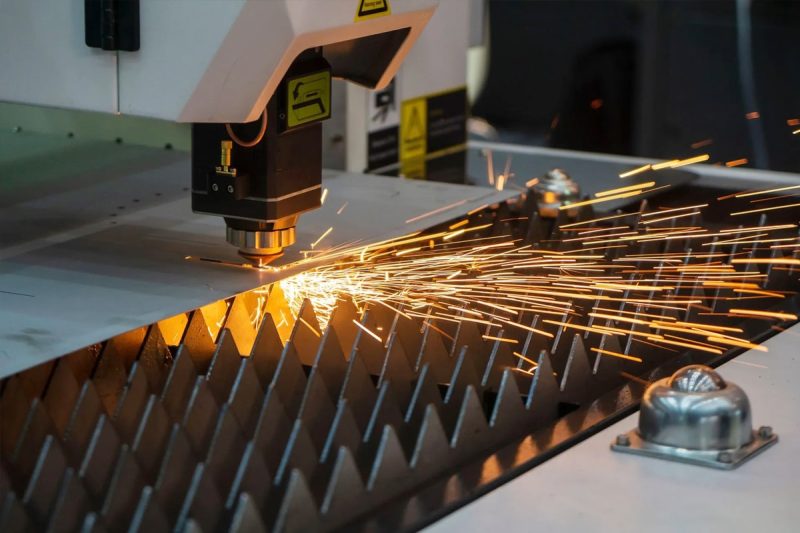
レーザー切断機の種類
アプリケーションに適したレーザー切断出力を決定するには、利用可能なレーザー切断機の種類を理解する必要があります。各レーザー タイプには、電力要件に影響を与える独自の特性とアプリケーションがあります。レーザーには、ファイバー レーザー、CO2 レーザー、Nd レーザーの 3 つの主要なタイプがあります。各タイプについて詳しく見ていきましょう。
ファイバーレーザー切断機
ファイバーレーザー切断機 高効率、高精度、多用途性で知られています。これらの機械は固体レーザー源を使用しており、レーザービームは一連のダイオードによって生成され、光ファイバーを介して伝送されます。光ファイバーはビームを増幅し、切断ヘッドに導きます。
主な特徴
- 波長: 通常は約 1.06 ミクロンで、金属の切断に最適です。
- 効率: 高い電気光学効率 (通常 30% 以上) により、運用コストとエネルギー消費が削減されます。
- ビーム品質: 優れたビーム品質により、特に薄い材料をより細かく、より正確に切断できます。
- メンテナンス: レーザー ソースには可動部品がないため、メンテナンスの必要性が低くなります。
アプリケーション
- 材質: 鋼、ステンレス鋼、アルミニウム、真鍮、銅などの金属の切断に最適です。
- 厚さ:薄物から中厚物の高精度切断に適しています。
- 業界: 航空宇宙、自動車、電子機器、金属製造業界で広く使用されています。
利点
- 速度: 特に薄い材料を切断する場合、CO₂レーザーやNdレーザーに比べて切断速度が速くなります。
- 精度: 細いビームにより高精度と高エッジ品質を実現。
- 高い電気光学効率: 効率が高くなり、エネルギー消費と運用コストが削減されます。
- コスト効率: 耐用年数が長く、メンテナンスの必要性が低い。
短所
- 初期コスト: CO2 レーザー発生器に比べて初期投資が高くなります。
- 材料の制限: 木材やプラスチックなどの非金属材料では効果が低くなります。
CO2レーザー切断機
CO2レーザー切断機 産業用途で最も広く使用されているレーザーの 1 つです。レーザー ビームを生成するために、ガス混合物 (通常は二酸化炭素、窒素、ヘリウム) を使用します。
主な特徴
- 波長:約10.6ミクロン、非金属を含む幅広い材料の切断に最適です。
- 効率: ファイバーレーザーに比べて電気効率が低くなります。
- ビーム品質: 優れたビーム品質で、幅広い切断および彫刻作業に適しています。
- メンテナンス: ガスの補充やミラーの調整など、定期的なメンテナンスが必要です。
アプリケーション
- 材料: 金属、木材、アクリル、ガラス、繊維、プラスチックなど、幅広い材料を切断できます。
- 厚さ:薄い材料から厚い材料まで切断するのに効果的です。
- 業界: 標識、包装、木工、自動車、繊維業界で使用されます。
利点
- 汎用性: 金属に加えて、幅広い材料を切断できます。
- コスト: ファイバーレーザーに比べて初期コストが低い。
- 可用性: 成熟したテクノロジーで、さまざまなモデルと構成で利用できます。
短所
- 速度: ファイバーレーザーに比べて金属の切断速度が遅くなります。
- メンテナンス: ガスの補充や定期的なミラーの調整など、メンテナンスの要件は高くなります。
- エネルギー消費: 電気効率が低いため、エネルギー消費が高くなります。
Ndレーザー切断機
Nd (ネオジム添加) レーザー発生器は、レーザー媒体として結晶を使用する固体レーザー発生器です。これらのレーザーは、高いピーク出力とパルス動作で知られています。
主な特徴
- 波長: 約 1.064 ミクロン、ファイバーレーザーに似ており、金属切断に適しています。
- 動作モード: 連続波 (CW) モードとパルス モードの両方で動作できるため、切断や彫刻のアプリケーションに柔軟性を提供します。
- ビーム品質: 精密な切断と穴あけのための高品質のビーム。
- メンテナンス: 通常、メンテナンスが少なく、頑丈な設計で、長寿命です。
アプリケーション
- 材質: 金属、セラミック、一部のプラスチックの切断に適しています。
- 厚さ:薄い材料の精密切断や穴あけに適しています。
- 業界: 電子機器、医療機器製造、宝石、航空宇宙産業でよく使用されます。
利点
- 精度: 高精度で、細かいディテールを生成できます。
- パルス操作: パルス操作が可能で、穴あけや細かい彫刻に最適です。
- 材料適合性: 硬質材料や脆性材料を含む幅広い材料に効果的です。
短所
- 速度: ファイバーレーザージェネレータに比べて切断速度が遅くなります。
- コスト: CO2 レーザーに比べて初期コストが高く、効率が低い。
- 冷却要件: 熱放散を管理するために効率的な冷却システムが必要です。
各タイプのレーザー切断機(ファイバー、CO2、Nd)には、それぞれ長所、短所、適切な用途があります。特定の用途に必要なレーザー切断出力を決定する際には、これらの違いを注意深く理解する必要があります。ファイバーレーザーは金属を高速かつ高精度に切断するのに優れており、CO2レーザーは幅広い材料に適しており、Ndレーザーは微細な切断と穴あけの精度を提供します。適切なタイプのレーザー切断機を選択することで、 レーザー切断機、レーザー切断プロセスのパフォーマンス、効率、品質を最適化できます。
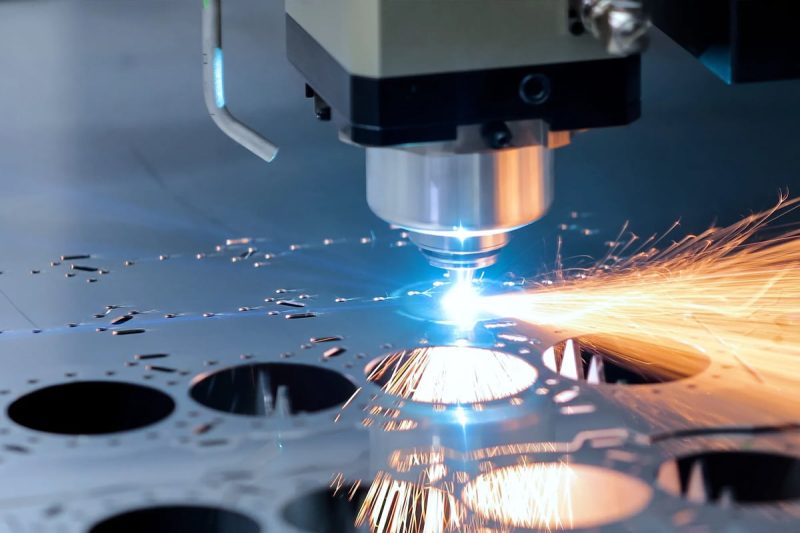
レーザー出力に影響を与える要因
適切なレーザー切断出力を決定することは、さまざまな材料を効率的かつ高品質に切断するための重要なステップです。必要なレーザー出力には複数の要因が影響し、それぞれの要因が切断プロセスの全体的なパフォーマンスに影響します。材料の種類、材料の厚さ、切断速度の要件、必要な切断品質、設計の複雑さなど、これらの主要な要因について見ていきましょう。
材料の種類
切断する材料の種類は、必要なレーザー出力に影響を与える最も重要な要因の 1 つです。材料によって反射率、熱伝導率、融点などの特性が異なり、レーザー ビームとの相互作用に影響します。
金属
- 鋼: 融点が高いため、通常はより高いレーザー出力が必要です。軟鋼、ステンレス鋼、その他の鋼合金では、必要な出力が異なる場合があります。
- アルミニウム: 反射率と熱伝導率が高いため、高いレーザー出力が必要です。
- 銅と真鍮: これらの材料は反射性と導電性が高く、効率的な切断を確実に行うには、より高い出力レベルまたはファイバー レーザー ジェネレーターなどの特殊なレーザー ジェネレーターが必要です。
非金属
- プラスチックとアクリル: 一般的に金属よりも低い電力が必要です。必要な電力はプラスチックの種類と厚さによって異なります。
- 木材: 中程度のパワーが必要ですが、木材の種類や水分含有量によって必要なパワーは大きく異なります。
- 布地と紙: これらの素材は薄くて可燃性であるため、切断時に必要な電力は低くなります。
熱伝導率や反射率などの材料の特定の特性を知ることは、適切なレーザー出力を選択するのに役立ちます。
材料の厚さ
材料の厚さは、必要なレーザー出力に正比例します。厚い材料を切断するには、レーザーをより深く浸透させてより多くの材料を除去する必要があるため、より多くの出力が必要です。
- 薄い材料 (≤ 1 mm): 低い出力レベルで十分です。出力が低いほど、高精度で細かいディテールを実現できます。
- 中程度の厚さ (1 ~ 5 mm): 中程度の電力レベルが必要です。必要な正確な電力は、材料の種類と希望する切断速度によって異なります。
- 厚い材料 (> 5 mm): 完全な貫通と効率的な切断を確実に行うには、高出力が必要です。非常に厚い材料の場合、マルチパス アプローチまたは専用の高出力レーザー ジェネレーターが必要になることがあります。
通常、材料の厚さが増すと、切断効率と品質を維持するためにレーザー出力もそれに応じて増加する必要があります。
切断速度要件
希望する切断速度は、レーザー出力の選択に大きく影響します。切断速度が速いほど、切断品質を維持し、不完全な切断や過剰なバリを防ぐために、通常、より高い出力が必要になります。
- 高速切断: 大量生産など、速度が重要な用途では、より高いレーザー出力が必要です。出力が高ければ、品質を犠牲にすることなく、レーザーが材料を素早く切断できるようになります。
- 中速切断: 切断速度がそれほど重要でないシナリオでは、中程度の電力設定を使用できます。これは、小ロット生産やカスタム製造の場合によく使用されます。
- 低速切断: 非常に細かい部分や複雑な部分を切断する場合は、切断速度を遅くし、電力設定を低くすることができます。これにより、精度と制御性が向上します。
切断速度とレーザー出力のバランスをとることで、望ましい切断品質を維持しながら効率的な生産を実現できます。
必要なカット品質
必要なカット品質もレーザー出力設定に影響します。アプリケーションによって、エッジ品質、精度、仕上げの基準が異なります。
- 高品質の切断: 滑らかなエッジ、高品質、最小限の後処理を必要とするアプリケーションでは、通常、より高いレーザー出力とより遅い切断速度が必要です。これにより、ドロスとバリが最小限に抑えられたきれいな切断が保証されます。
- 標準品質の切断: 小さな欠陥が許容される用途では、中程度の出力レベルで十分です。これは、速度が美観品質よりも優先される重工業用途でよく見られます。
- 荒削り: 刃先の品質よりも速度が主な懸念事項である場合、より高い出力とより速い切削速度を採用できます。このアプローチは、予備的な切削段階や、さらに加工される材料によく使用されます。
特定の品質要件を満たすようにレーザー出力を調整すると、切断プロセスと最終製品を最適化できます。
デザインの複雑さ
カットするデザインやパターンの複雑さも、必要なレーザー出力に影響します。複雑で詳細なデザインでは、通常、レーザーをより正確に制御する必要があり、それが出力設定に影響します。
- 複雑なデザイン: 鋭角、小さな穴、細かい特徴を持つ複雑なパターンでは、レーザー出力の正確な制御が必要です。低出力設定と低速を組み合わせることで、高精度を実現し、材料の過熱や変形を防ぐことができます。
- 中程度のデザイン: 中程度の複雑さのデザインは、バランスの取れた出力設定でカットできます。これらのデザインには曲線やさまざまな線の太さが含まれる場合がありますが、極度の精度は必要ありません。
- シンプルなデザイン: シンプルな形状や直線など、細部が最小限の単純なカットは、より高い電力設定とより速い速度で実行できます。
レーザー出力をデザインの複雑さに合わせて調整することで、材料の完全性を損なうことなく、複雑な細部を正確にカットできます。
適切なレーザー切断出力を決定するには、材料の種類、材料の厚さ、切断速度の要件、望ましい切断品質、設計の複雑さなど、複数の要因を慎重に考慮する必要があります。これらの要因がレーザー切断プロセスにどのように影響するかを理解することで、オペレーターは、精密製造、高速生産、複雑な設計作業など、最良の結果を得るために設定を最適化できます。これらの要因を適切にバランスさせることで、各プロジェクトの特定のニーズに合わせた効率的で高品質のレーザー切断操作が保証されます。
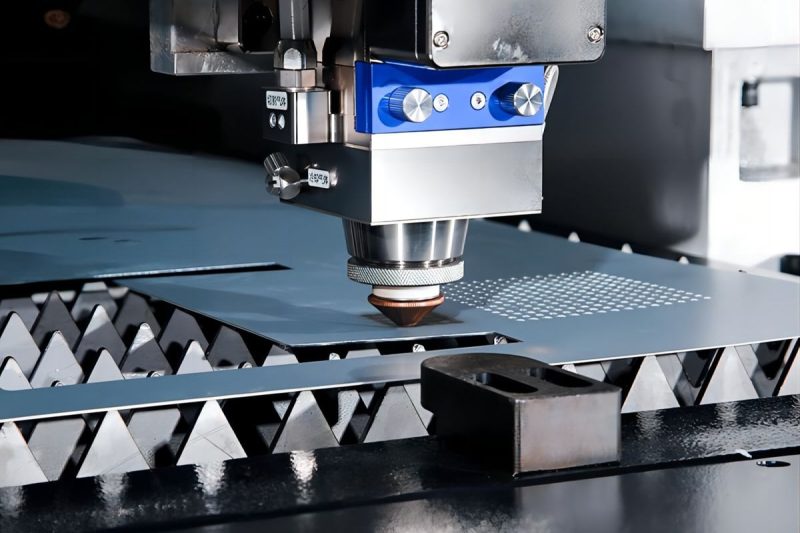
さまざまな材料に対するレーザー出力範囲
適切なレーザー切断出力を選択すると、さまざまな材料で最高の切断結果を得ることができます。材料によって必要なレーザー出力設定は異なり、使用するレーザーの種類によって大きく異なります。このセクションでは、金属、非金属、複合材に推奨されるレーザー出力範囲と、適切なレーザーの種類 (ファイバー レーザーと CO2 レーザー) について詳しく説明します。
金属
金属は、その密度と熱伝導率のため、一般的に高いレーザー出力を必要とします。ファイバーレーザーは、高精度かつ効率的に金属を切断するのに最も効果的です。
軟鋼
- 薄板(厚さ3mmまで):1,000~2,000ワット
- 中厚(3~6 mm):2,000~4,000ワット
- 厚板(6~12 mm):4,000~8,000ワット
- 極厚プレート(厚さ12mm以上):8,000~12,000ワット
ステンレス鋼
- 薄板(厚さ2mmまで):1,000~2,000ワット
- 中厚(2~5 mm):2,000~4,000ワット
- 厚板(5~10 mm):4,000~6,000ワット
- 極厚プレート(厚さ10mm以上):6,000~12,000ワット
アルミニウム
- 薄板(厚さ2mmまで):1,000~2,000ワット
- 中厚(2~6mm):2,000~4,000ワット
- 厚板(6~10 mm):4,000~8,000ワット
- 極厚プレート(10mm以上):8,000~12,000ワット
銅と真鍮
- 薄板(厚さ1mmまで):1,000~2,000ワット
- 中厚(1~3 mm):2,000~4,000ワット
- 厚板(3~6 mm):4,000~6,000ワット
- 極厚プレート(6mm以上):6,000~8,000ワット
金属の場合、特に材料の厚さが増すにつれて、きれいで正確な切断を確実に行うために高い電力設定が必要になります。
非金属
非金属は、プラスチック、木材、アクリルなどの非金属材料を CO2 レーザーで切断するのが一般的です。これらのレーザーは、非金属の切断作業に十分なパワーと精度を提供します。
プラスチック(例:ポリカーボネート、ポリプロピレン、PVC)
- 薄板(厚さ2mmまで):25~40ワット
- 中厚(2~5 mm):40~100ワット
- 厚いシート(5~10 mm):100~150ワット
- 極厚シート(厚さ10mm以上):200~600ワット
アクリル
- 薄板(厚さ2mmまで):60~100ワット
- 中厚(2~5 mm):100~200ワット
- 厚いシート(5~10 mm):200~400ワット
- 極厚シート(厚さ10mm以上): 400~600ワット
木材(例:合板、MDF、硬材)
- 薄板(厚さ3mmまで):100~150ワット
- 中厚(3~6 mm):150~300ワット
- 厚いシート(6~12×12mm):300~500ワット
- 極厚シート(12 mm以上): 500~600 ワット
繊維・皮革
- 薄型および中型: 60~150 ワット
- 厚い材料: 150~300 ワット
非金属は金属よりも少ない電力を必要としますが、必要な正確な電力は材料の厚さと密度によって異なります。
複合材料
炭素繊維強化ポリマー(CFRP)やガラス繊維強化ポリマー(GFRP)などの複合材料は、その不均質な構造のため、慎重な考慮が必要です。特定の複合材料に応じて、CO2レーザーを使用して切断できます。
炭素繊維強化ポリマー(CFRP)
- 薄板(厚さ1mmまで):100~200ワット
- 中厚(1~3 mm):200~400ワット
- 厚板(3~6 mm):400~600ワット
ガラス繊維強化ポリマー(GFRP)
- 薄板(厚さ1mmまで):100~200ワット
- 中厚(1~3 mm):200~400ワット
- 厚板(3~6 mm):400~600ワット
その他の複合材料(例:ケブラー、ホウ素複合材料)
- 薄板(厚さ1mmまで):100~200ワット
- 中厚(1~3 mm):200~400ワット
- 厚板(3~6 mm):400~600ワット
複合材料の構造的完全性を損なうことなく正確な切断を行うには、電力設定を慎重に調整する必要があります。
さまざまな材料に必要なレーザー出力範囲と適切なレーザー タイプを理解することで、レーザー切断プロセスを最適化することができます。金属の場合は通常、より高い出力設定が必要で、ファイバー レーザーが特に効果的です。非金属の場合は通常、より低い出力設定が必要で、そのような材料を切断する際の効率性から CO2 レーザーが好まれます。複合材料には、レーザー タイプと出力設定を慎重に検討する必要がある独特の課題があります。これらのガイドラインに従うことで、適切なレーザー出力を選択し、切断作業の効率、品質、精度を確保できます。
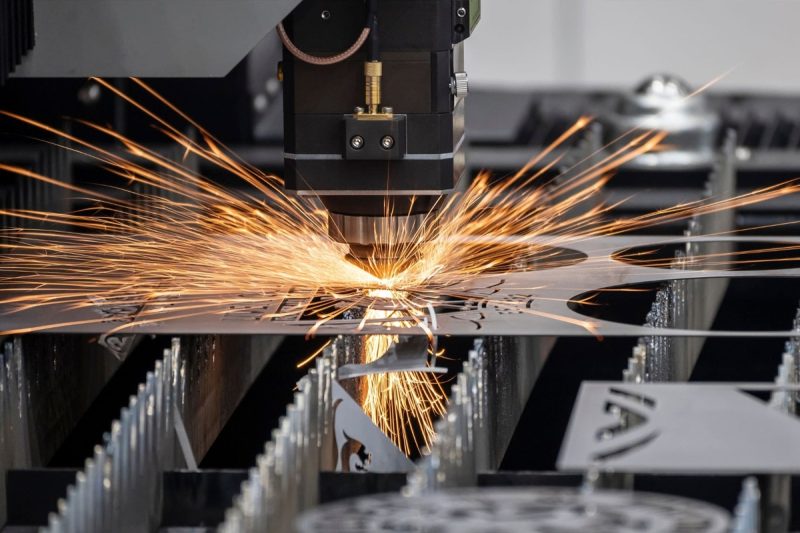
レーザー出力を決定する方法
特定の用途に適したレーザー切断パワーを決定するには、ツール、テクニック、リソースを組み合わせる必要があります。主な方法としては、材料適合性チャートの使用、材料テストの実施、メーカーの推奨事項の遵守などがあります。各方法の詳細な説明は次のとおりです。
材料適合性チャート
材料適合性チャートは、さまざまな材料に必要なレーザー出力設定に関する一般的なガイダンスを提供する貴重なリソースです。
- 目的: これらのチャートは、材料の種類と厚さに基づいて、さまざまな材料の開始電力設定をユーザーがすばやく識別するのに役立ちます。
- 構造: 互換性チャートでは通常、材料が 1 つの列にリストされ、その後に推奨される電力設定、切断速度、およびその他の関連パラメータが続きます。
- 出典: これらのチャートは、ユーザー マニュアル、レーザー切断ソフトウェア、および製造元の Web サイトにあります。
利点
- クイック リファレンス: 膨大な計算や実験を必要とせずに、すぐにガイダンスを提供します。
- 標準化された設定: 業界のベスト プラクティスに基づいて標準化された電源設定を提供します。
短所
- 一般情報: 材料の品質や環境条件の特定の変動を考慮していない可能性があります。
- 開始点のみ: これは、さらなる調整と最適化のベースラインとして機能する必要があります。
材料試験
材料テストでは、特定の材料や用途に合わせてレーザー出力設定を微調整するために実際のテストを実施します。
- 初期設定: 材料の互換性チャートまたは製造元のガイドに記載されている推奨設定から始めます。
- 段階的調整: 結果を監視しながら、レーザー出力、速度、その他のパラメータを徐々に調整します。
- 評価: カット品質、エッジの滑らかさ、材料の劣化や過熱の兆候を評価します。
利点
- 精度: 特定の材料特性と切断要件に基づいた正確な調整が可能になります。
- 最適化: 最適な切断パフォーマンスを実現するための微調整が可能になり、効率と品質が向上します。
短所
- 時間がかかります: 複数のテストと評価を実行するには時間とリソースが必要です。
- 材料の廃棄: テスト中に何らかの材料を使用することになります。
メーカーの推奨事項
製造元の推奨事項に従うことは、適切なレーザー切断出力を決定するための重要な方法です。
- 出典: 推奨事項は、ユーザー マニュアル、技術サポート ドキュメント、およびレーザー切断機メーカーからの公式通知に記載されています。
- 内容: これらのガイドには通常、広範なテストと実際のアプリケーションに基づいた詳細な電力設定、切断速度、その他のパラメータが含まれています。
利点
- 信頼性: メーカーの推奨事項は包括的なテストに基づいており、レーザー切断機の特定の機能に合わせて調整されています。
- サポート: ご質問やご不明な点がある場合は、メーカーからテクニカル サポートを受けることができます。
短所
- 一般的な推奨事項: これらの推奨事項は信頼できるものですが、特定のユースケースや材料条件に基づいて微調整する必要がある場合があります。
- 依存性: 製造元の推奨事項に過度に依存すると、固有のアプリケーションに最適な設定の探索が制限される可能性があります。
適切なレーザー切断パワーを決定するには、材料適合性チャートの使用、材料テストの実施、およびメーカーの推奨事項の遵守を組み合わせる必要があります。材料適合性チャートは、クイックリファレンスと開始点を提供し、材料テストは正確な最適化を可能にし、メーカーの推奨事項は広範な研究に基づいた信頼できるガイダンスを提供します。これらの方法を組み合わせることで、特定の材料とアプリケーションに必要なレーザー切断パワーを正確に決定し、効率的で高品質かつ高精度の切断プロセスを確保できます。
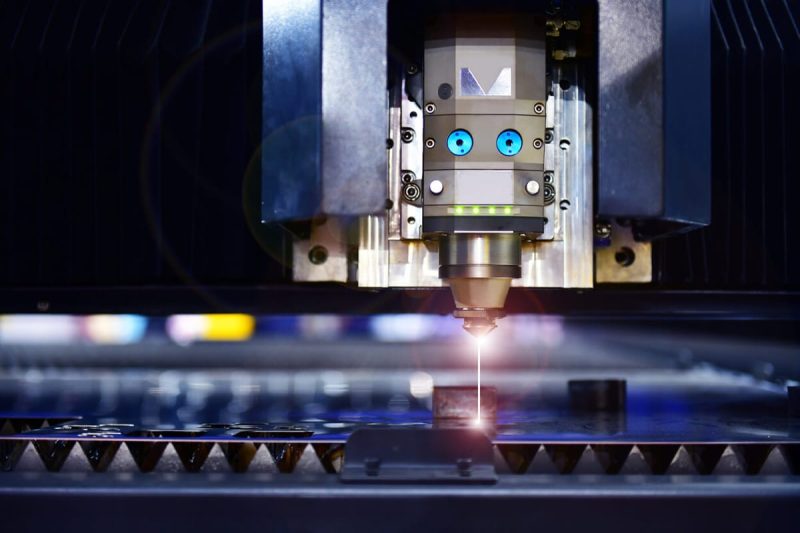
レーザー切断パワーを選択するための実用的な考慮事項
アプリケーションに適したレーザー切断出力を決定する際には、材料特性と切断要件に加えて、いくつかの実際的な要素を考慮する必要があります。これらの要素には、機械の仕様、コストとエネルギー効率、メンテナンスとダウンタイムが含まれます。これらの考慮事項を理解することで、レーザー切断操作を最適化し、最良の結果を得ることができます。
機械仕様
レーザー切断機の仕様は、適切なレーザー出力設定を決定する上で重要な役割を果たします。各機械には、考慮しなければならない固有の機能と制限があります。
最大および最小出力
- 範囲: マシンが材料に必要な電力設定に対応できることを確認します。ファイバー レーザーは通常 1,000 ~ 12,000 ワット (金属の場合) の範囲で、CO2 レーザーは 60 ~ 600 ワット (非金属の場合) の範囲です。
- 柔軟性: 幅広い出力範囲を備えたマシンは、さまざまな材料や厚さを切断するための柔軟性が向上します。
ビーム品質
- 焦点サイズ: レーザー ビームの品質は、カットの精度に影響します。ビームの品質が高く、焦点サイズが小さいほど、より細かく、より正確なカットが可能になります。
- 安定性: 一貫したビーム品質により、均一なカットが保証され、頻繁な調整の必要性が軽減されます。
切削速度と加速
- 速度機能: レーザー出力が高ければ切断速度も速くなりますが、機械の機械部品は精度を損なうことなくこれらの速度をサポートする必要があります。
- 加速: 高い加速能力を備えたマシンは、切断方向の急激な変化に対応できるため、複雑なデザインの実現に役立ちます。
制御システム
- ソフトウェア: 高度な制御ソフトウェアにより、切断パスと電力設定を最適化し、効率と品質を向上させることができます。
- 統合: 制御システムを他の生産設備やソフトウェアとシームレスに統合して操作を簡素化できるようにします。
コストとエネルギー効率
運用コストとエネルギー効率のバランスをとることで、収益性と持続可能性を維持できます。
運用費用
- 電力消費: レーザー出力設定が高いほど、消費電力も大きくなります。さまざまな出力レベルに関連するエネルギー要件と運用コストを評価します。
- 補助ガス: 使用される補助ガスの種類と量 (酸素、窒素、圧縮空気など) は、総コストに影響する可能性があります。パワー設定が高いほど、カット品質を維持するために補助ガスの使用量が増える可能性があります。補助ガスについて詳しく知りたい場合は、「補助ガスの選択がレーザー切断に与える影響" 記事。
初期投資と長期貯蓄
- 初期コスト: より高出力のレーザー切断機は、通常、より高い初期投資が必要です。ただし、切断速度と効率が向上するため、長期的には節約になります。
- 効率性の向上: より強力なレーザーを使用すると、切断時間が短縮され、生産スループットが向上し、労力と運用コストが節約されます。
エネルギー効率
- レーザー効率: ファイバー レーザー ジェネレーターは、一般的に CO2 レーザー ジェネレーターよりもエネルギー効率に優れています。電力設定を選択するときは、レーザー ジェネレーターの種類のエネルギー効率を考慮してください。
- 冷却システム: 効率的な冷却システムはエネルギー消費を削減し、レーザー発生器の寿命を延ばすことができます。
メンテナンスとダウンタイム
定期的なメンテナンスとダウンタイムの最小化により、安定したパフォーマンスを確保し、レーザー切断機の寿命を延ばすことができます。
定期メンテナンス
- 頻度: 電力設定を高くすると、機械部品の摩耗が早まります。定期的なメンテナンス スケジュールを作成し、必要に応じて部品を検査して交換してください。
- 部品: レンズ、ミラー、ノズルなどの重要なコンポーネントは、最適なパフォーマンスを維持するために頻繁に清掃および交換する必要があります。
ダウンタイム管理
- 計画されたダウンタイム: 計画されたダウンタイム中にメンテナンス活動を計画して、生産の中断を最小限に抑えます。
- 予防保守: 機械の故障を引き起こす前に潜在的な問題を特定して解決するための予防保守戦略を実装します。
メーカーサポート
- サービス契約: メーカーが提供するサービス契約とサポート パッケージを検討してください。これにより安心が得られ、ダウンタイムが長引くリスクを軽減できます。
- 技術サポート: マシンのパフォーマンスのトラブルシューティングと最適化を行うために、技術サポートにアクセスできるようにします。
適切なレーザー切断出力を選択するには、機械の仕様、コストとエネルギー効率、メンテナンスとダウンタイムなど、さまざまな実際的な要素を考慮する必要があります。これらの要素を理解してバランスをとることで、レーザー切断操作を最適化し、高品質の結果を達成し、効率的でコスト効率の高い生産プロセスを維持できます。定期的なメンテナンスと慎重な運用コスト管理により、レーザー切断装置のパフォーマンスと寿命がさらに向上します。
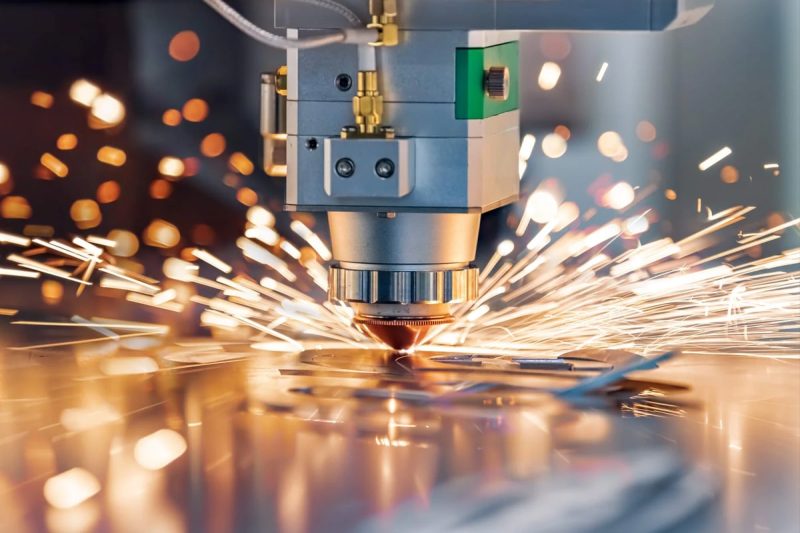
レーザー出力の問題のトラブルシューティング
適切なレーザー切断出力を決定すると、最良の結果を得ることができます。ただし、最適な設定であっても、切断中に問題が発生する場合があります。このセクションでは、一般的なレーザー出力の問題について説明し、切断深さが十分でない、過度の燃焼または溶解、切断結果の一貫性がない、といったそれぞれのトラブルシューティングのヒントを示します。
十分に深く切っていない
レーザーが十分な深さまで切断しない場合、切断が不完全となり、追加のパスや手動介入が必要になる場合があります。考えられる原因と解決策は次のとおりです。
電力不足
- 原因: レーザー出力の設定が低すぎて材料を切断できない可能性があります。
- 解決策: レーザー出力を徐々に上げ、希望の深さに達するまでテストカットを行います。出力レベルがマシンの安全な動作範囲内であることを確認します。
切断速度が速すぎる
- 原因: 切断速度が速すぎて、レーザーが材料に完全に浸透する時間が足りない可能性があります。
- 解決策: 切断速度を下げて、より多くのエネルギーを材料に集中させます。速度と電力の設定のバランスをとって、切断の深さを最適化します。
フォーカスを逃した
- 原因: レーザービームが材料表面に適切に焦点を合わせられず、切断効率が低下している可能性があります。
- 解決策: 焦点の高さを調整して、レーザー ビームが材料に適切に焦点を合わせるようにします。マシンのフォーカス ツールを使用するか、必要に応じて手動で調整します。
材料の厚さ
- 原因: 材料が予想よりも厚いため、より多くの電力または複数回のパスが必要になる可能性があります。
- 解決策: 材料の厚さを確認し、それに応じて出力設定を調整します。非常に厚い材料の場合は、複数回のパスまたは高出力のレーザーの使用を検討してください。
過度の燃焼または溶解
過度の燃焼や溶解は、切断品質を低下させ、材料を損傷する可能性があります。 根本的な原因を特定して修正することで、良好な切断品質を維持することができます。
過剰な電力
- 原因: 切断する材料に対してレーザー出力設定が高すぎる可能性があります。
- 解決策: 焼けや溶解が最小限に抑えられるまで、レーザー出力を徐々に下げます。出力設定が材料に適切であることを確認します。
切断速度が遅い
- 原因: 切断速度が遅すぎるため、過度の熱が蓄積され、焼けてしまう可能性があります。
- 解決策: 切断速度を上げて熱にさらされる時間を短縮します。速度とパワーの適切なバランスを見つけて、焼けることなくきれいに切断します。
焦点が間違っている
- 原因: レーザーの焦点が集中しすぎて、狭い領域で過熱が発生する可能性があります。
- 解決策: レーザー エネルギーが切断領域全体に均等に分散されるように焦点の高さを調整します。ビームが適切に調整され、焦点が合っていることを確認します。
材料感度
- 原因: 一部の素材は熱に敏感で、燃えたり溶けたりする傾向があります。
- 解決策: 可能な限り、耐熱性に優れた材料を使用します。また、切断領域周辺の酸素を排除することで燃焼を軽減できる窒素などの補助ガスの使用も検討してください。
一貫性のない切断結果
切断結果が一定でないと、切断品質と精度にばらつきが生じ、最終製品の完全性に影響を及ぼす可能性があります。不一致の原因を特定して解決することが重要です。
可変出力
- 原因: レーザー発生器の出力が変動し、切断性能が一定でなくなる可能性があります。
- 解決策: レーザー ジェネレーターの安定性の問題をチェックし、正しく動作していることを確認します。定期的なメンテナンスと調整により、一貫した出力を維持できます。
素材のバリエーション
- 原因: 厚さや組成などの材料特性のばらつきにより、切断が不安定になることがあります。
- 解決策: 材料の一貫性を確保するために、高品質で均一な材料を使用します。さまざまなバッチの材料でテストカットを実行し、必要に応じて設定を調整します。
不適切な機械の校正
- 原因: 機械が適切に調整されていないため、切断の精度と一貫性に影響が出る可能性があります。
- 解決策: 製造元のガイドラインに従って、レーザー切断機を定期的に調整します。切断性能に影響を与える可能性のある機械的な問題や位置ずれがないか確認します。
汚れや損傷した光学部品
- 原因: 光学部品が汚れていたり損傷していると、レーザー光線が散乱し、切断結果が一定しなくなる可能性があります。
- 解決策: 定期的に光学系を清掃し、損傷がないか検査します。損傷したコンポーネントがあれば交換して、最適なビーム品質と一貫性を確保します。
環境要因
- 原因: 周囲の温度、湿度、または空気の流れの変化が切断プロセスに影響を与える可能性があります。
- 解決策: レーザー切断機の環境を管理します。温度と湿度のレベルを一定に保ち、環境要因が切断プロセスに与える影響を軽減します。
レーザー出力の問題を解決するには、不十分な切断深さ、過度の燃焼または溶解、一貫性のない切断結果など、一般的な問題の根本原因を理解する必要があります。レーザー出力、切断速度、焦点、補助ガス設定を調整し、清潔で安定した切断環境を維持することで、レーザー切断機のパフォーマンスを最適化し、一貫性のある高品質の結果を得ることができます。定期的なメンテナンスとメーカーの推奨事項の順守も、これらの問題を効果的に防止および解決するための鍵となります。
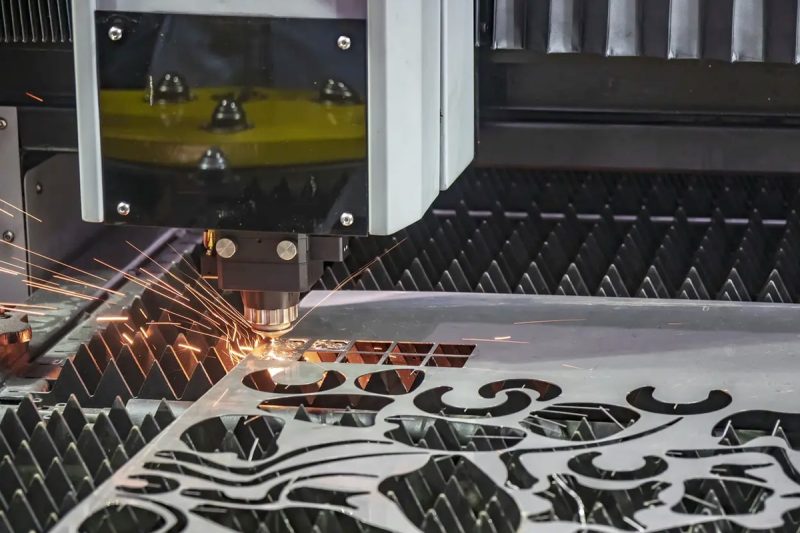
まとめ
適切なレーザー切断出力を決定することで、レーザー切断作業で最適なパフォーマンスと高品質の結果を得ることができます。考慮すべき主な要因には、材料の種類、厚さ、切断速度の要件、望ましい切断品質、設計の複雑さなどがあります。材料適合性チャートの使用、材料テストの実行、メーカーの推奨事項の遵守は、適切な出力設定を選択するための効果的な方法です。機械の仕様、コストとエネルギー効率、メンテナンスの必要性などの実際的な考慮事項も、レーザー出力の最適化において重要な役割を果たします。不十分な切断深さ、過剰な燃焼、一貫性のない結果などの一般的な問題に対処することで、効率的な操作を継続できます。これらの問題を理解して対処することで、オペレーターは情報に基づいた決定を下し、生産性を高め、さまざまな材料を正確かつ効率的に切断できます。定期的なメンテナンスとベストプラクティスの順守は、レーザー切断システムの寿命をさらに延ばし、信頼性を向上させるのに役立ちます。
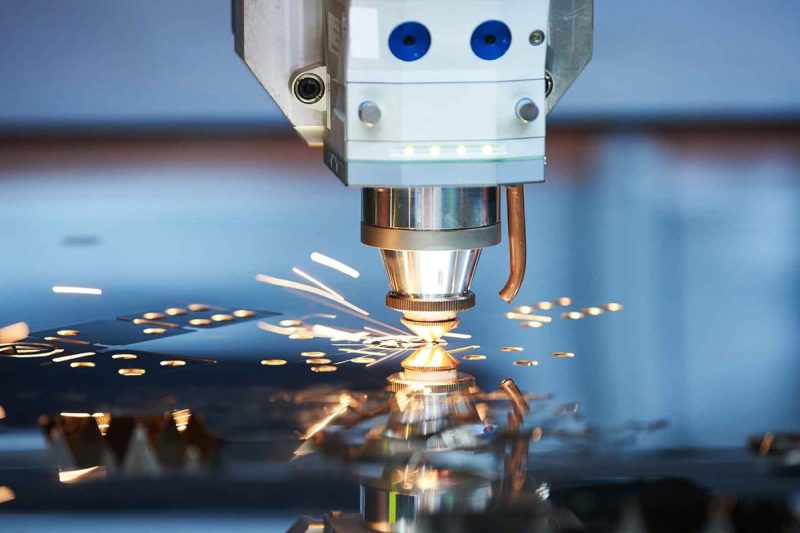
レーザー切断ソリューションを入手
で AccTek レーザー弊社は、優れた切断性能と効率性を実現するために、適切なレーザー切断出力を選択することが極めて重要であることを理解しています。プロ仕様のレーザー切断機の大手プロバイダーとして、弊社はお客様の特定のニーズに合わせた包括的なソリューションを提供します。弊社の高度なレーザー システムは、さまざまな材料を正確かつ確実に処理できるように設計されています。金属、非金属、複合材のいずれを切断する場合でも、弊社の専門家がお客様と緊密に連携して、お客様の用途に最適な出力設定を決定します。
当社のチームは、詳細な材料適合性チャートを提供し、徹底した材料テストを実施し、お客様が最良の結果を確実に得られるよう、個別の推奨事項を提供します。さらに、機械の仕様、コストとエネルギー効率、メンテナンス戦略に関する専門的なガイダンスを提供し、お客様の投資を最大限に活用できるようサポートします。
お客様独自の要件を満たすカスタマイズされたレーザー切断ソリューションについては、最先端のテクノロジーと比類のないサポートを提供する AccTek Laser にお任せください。 お問い合わせ 当社のレーザー切断ソリューションが貴社の生産能力をどのように向上できるかをぜひ今日ご確認ください。
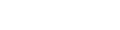
連絡先
- [email protected]
- [email protected]
- +86-19963414011
- No. 3 ゾーン A、Lunzhen 工業地帯、玉城市、山東省。
レーザー ソリューションを入手する